Zero USV Oceanus12
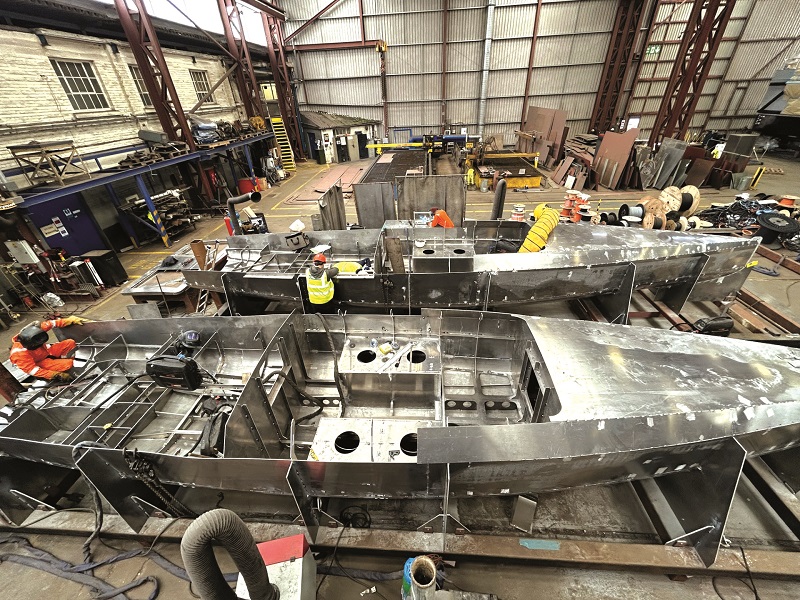
Rory Jackson reports on a company set on making great regulatory strides for USVs
The future of uncrewed systems hinges on the future of their regulation. Many anticipate that establishing common rules for design, engineering and maintenance will create a solid platform for producing safe, efficient and competitive autonomous vehicles across countless industries.
Great strides are being made for the largest and most advanced oceangoing autonomous vessels, such as the Mayflower (see Issue 42), which crossed the Atlantic fully autonomously in 2022. However, the most recent USV regulations published across Europe and elsewhere only dictate standards for remotely operated boats, so the path to certification remains elusive.
As Matthew Ratsey, founder and managing director of UK-headquartered Zero USV (and CEO of Marine AI), says: “I know a lot of commercial USV developers who became frustrated with regulations and as a result either pulled the plug on their operation or moved it away from Britain so they didn’t have to deal with UK regulators.”
Ratsey and his colleagues – including Brett Phaneuf, CEO of the Mayflower and of MSubs, who gives significant technical consultation to Zero – were undeterred, however, in their collective ambition to create a mission-agnostic, fully autonomous and certified USV capable of BVLOS industrial applications.
“Most players are working under remote control, and doing so close to shore or a mothership. We wanted to offer a cost-effective USV, fully capable of over-the-horizon, oceangoing work in scientific, hydrographic, bathymetric and other roles you can name,” Ratsey says.
“Our first offering, the Oceanus12, is a roughly 12 m vessel, which keeps its costs manageable and enables it to be shipped from Britain to Australia in a standard, 40 ft container within six weeks, or to the US in two weeks.”
The Oceanus12 features a monohull design with a 2.33 m beam and 4 t displacement, a hybrid-electric powertrain enabling a top speed of 10 knots, and a number of software, sensors and electronics powering its marine autonomy. But it was the aluminium hull and structure that took most of Zero’s attention, particularly to solve the riddle of how an autonomous industrial vessel could be certified for maritime operations.
Construction standards
When Ratsey and his team began developing their first USV, there was no guidance on the right standard codes to adhere to, so advice was sought from the managing director of MECAL, a certifying body for the UK’s Maritime and Coastguard Agency (MCA) with responsibility for boats under 24 m.
“From what he could see, in the MCA Workboat Code Edition 3, or other guidelines for ‘remotely operated, unmanned vessels’, there was no real way to code an autonomous vessel, but he confirmed that Oceanus12 could absolutely be certified to Hull Construction standards if we followed the related guidelines,” Ratsey recounts.
The Oceanus12 has been designed and built to ISO12215, a standard recognised in the MCA Workboat Code. Its design – including scantlings (a naval term for the geometrical dimensions of the structural system) – has been witnessed by a third-party naval architect and its construction by a third-party surveyor, both appointed by MECAL.
“We do a load of non-destructive testing, including dye penetrant testing and X-raying, and based on hull construction standards we’re allowed to do one shot of the latter per metre of boat length, meaning 12 X-rays per unit,” Ratsey says.
“It’s quite an expensive thing to do, but it gives us full confidence to look customers in the eye and tell them our boat is tough, and built to a known industrial standard. That’s important because after that almost everything we put in the boat is bleeding-edge tech, vital to it being a high-end, autonomous USV. There’s no accommodation or seating onboard; it’s meant to be a completely uncrewed vessel.
“We’ve aimed to meet the regulatory requirements by using established industry standards, and where possible using Type-approved materials, exhausts, batteries, fuel lines and so on. It’s not easy; not everything being developed for use on USVs today is Type-approved – that’s just a fact.”
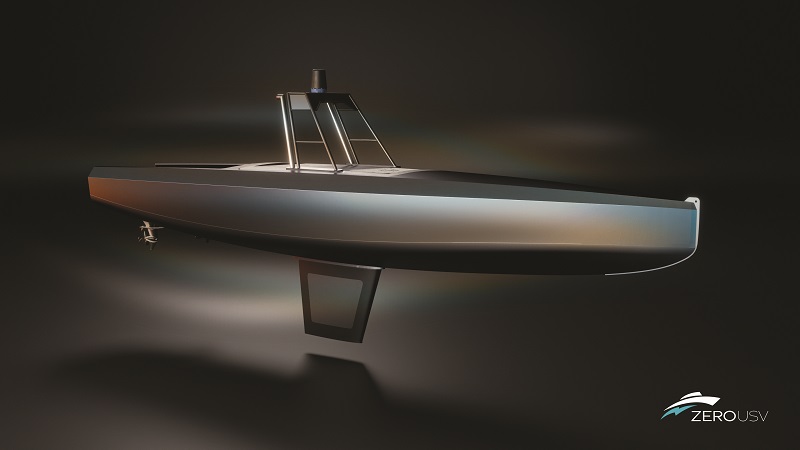
Fibre glass to aluminium
In its original drawings (made in early 2023), Oceanus12 was designed as a glass fibre-reinforced plastic (GRP) vessel. After obtaining quotes on raw materials and tooling for GRP-based production, and finding the tally was significantly more expensive than expected, Zero questioned whether they were using the right material.
“Around August last year, we decided to switch to aluminium, which required quite a bit of re-engineering, but we found a partner [undisclosed] who could take the GRP design and remake it into an aluminium, kit-built vessel,” Ratsey recounts.
“Getting that to production-level drawings was quite a bit of work, lasting until January, but it’s a truism that spending more time in the design phase – especially for these kinds of boats – saves you absolute tons of money and time in production down the line.”
Doing so meant that the vessel kit assembled perfectly at Manor Marine, Zero’s chosen shipyard in Weymouth, UK. Notably, Ratsey adds that Manor Marine described Oceanus12’s components as “one of the best kits they’ve ever had”, including both the first version of the USV and the second, latest one (which incorporated 10 minimally-tuned parts – a low number in boatbuilding).
“As well as having a competitive price, Manor are basically just up the road from our facility in Plymouth, which is vital for getting the initial build right, ensuring supply chains are working and getting the regulatory oversight in place as needed,” Ratsey says.
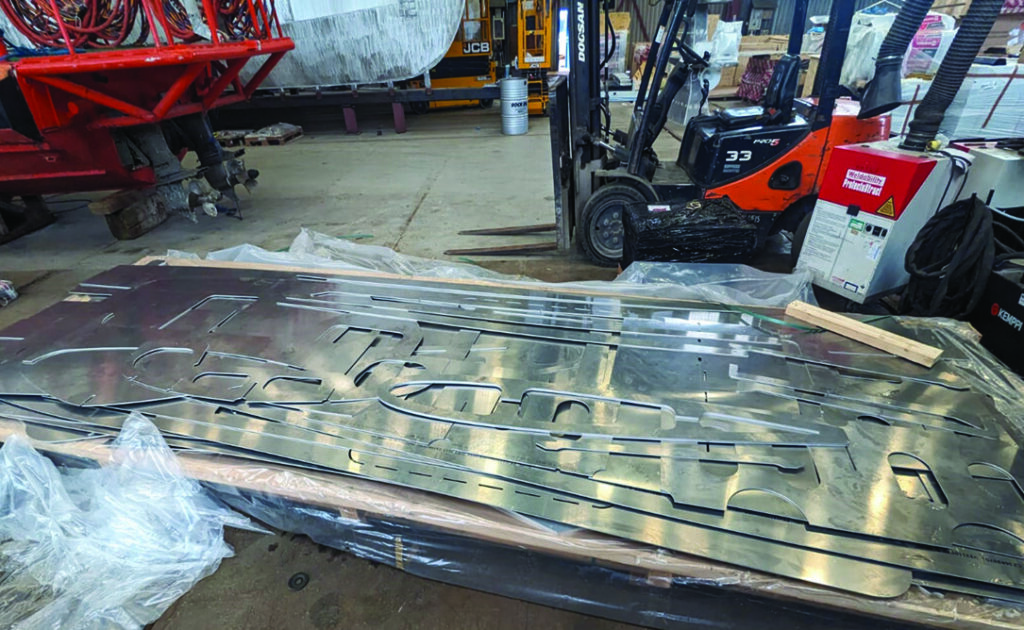
Kit-built hull
Vessels today can be constructed from a flat-packed kit, in which the parts for the hull shape, frames, stringers, deck plating and shell plating are all cut from metal and stacked in a crate.
“Back in the late 1990s, I worked with someone called Jim Moore, who came up with this system for producing self-jigging steel or aluminium kits, such that boats could be put together like a Lego kit,” Ratsey says.
“The frames will largely feature positive tabs that come out, so that when you put the shell plating on it slots through. They will also have been cut with slots for inserting and holding the stringers, and all the other detailed holes and grooves you need are pre-cut, so that an Oceanus12 can be assembled and tag-welded together in a matter of days.
“It really came about with the advent of advanced design software for visualising these sorts of components, as well as laser-cutting for precision, time-efficient metalwork of kit components. Laser machinery also lets us etch serial numbers on the frames, as well as other clever things, so you can really make quite a sophisticated kit.”
Overseas manufacturing of Oceanus12 USVs can be arranged by simply sharing the design files with laser-equipped CNC houses for them to use in producing kits or by shipping the kits in containers. Snijtech in the Netherlands cuts, stacks and supplies the Oceanus12 kits (as well as sourcing the recycled aluminium they are made from) for Zero.
“Snijtech’s leadership as a vessel kit manufacturer is one of the worst kept secrets in modern naval architecture,” Ratsey muses. “Basically, everyone is using Snijtech for their aluminium laser-cut kits, and we can get kits fully cut and formed from the recycled aluminium, readied for assembly in Holland, and then delivered to the UK, all cheaper than buying aluminium in the UK, thanks to Snijtech’s volume, efficiency and know-how.”
Monohull hydrodynamics
Snijtech’s very large metal-forming and bending machinery has enabled the assembled Oceanus12’s shell plating to be made from large pieces of aluminium. Those feature soft, hydrodynamic curves rather than sharp corners across the boat’s length.
“Getting a shipyard to do that costs a fortune, because they will have someone with a hammer slamming and bending metal manually, but doing it in a large machine with MDF templates means we can have some quite large sections bent and pre-formed, so the boats move efficiently and look good at a cost-effective price,” Ratsey says.
Both software simulation and towing-tank tests of hull prototypes have gone into optimisation of the USV’s hydrodynamics, as have lessons from the Mayflower, despite it having a trimaran hull.
“The build costs of a trimaran and other multihulls aren’t necessarily justified by the benefits,” Ratsey explains. “There’s some stability gained over a monohull in places, but with serious exceptions to that general rule. If you’re going over or down a wave, the trimaran can very easily and suddenly decide to do a hard left or right, possibly then capsizing.”
Hence, a narrow, slender monohull became the preferred approach for Oceanus12, especially after simulating both hull types in the company’s trusted in-house software.
As a result of the monohull’s efficiency and safety, at 6-7 knots, Oceanus12’s two 750 litre fuel tanks give a range of roughly 2500 miles (4023 km). If a survey speed of 3-4 knots is maintained, close to 1000 miles may be added to the range between refuelling stints. More fuel tanks can be added or mothership refuelling arranged if required.
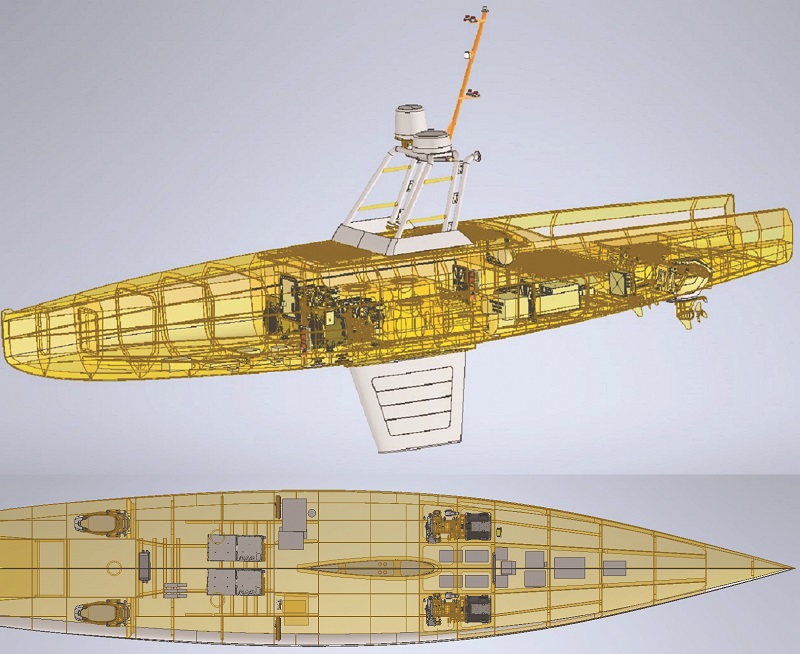
Hull balancing
Zero has distributed Oceanus12’s subsystems across its structure, principally to maintain the centres of gravity and buoyancy, thereby minimising the degree of pitching caused by payload mass and making the vessel’s trim as easy to control as possible.
“There is a collision bulkhead right at the front, with a fairly large void space behind that is going to carry quite a bit of electronics and computer power, as well as two day tanks,” Ratsey explains.
The fuel system has two main tanks, collectively storing 750 litres of diesel, which pump into two day tanks of 100 litres each. The generators then draw fuel from the day tanks. This approach reduces the risk of fuel being contaminated (by water or another substance) in the main tanks and those contaminants reaching the powertrain.
“Further back, we reach the main mid-section in which you see there’s two generators – one each side, port and starboard, as well as a fuel tank each side,” Ratsey says. “We also have our battery chargers and motor inverters in that section.
“Then there’s another bulkhead, beyond which the boat splits into a payload deck above and a battery deck below, and then behind those we’ve got the RAD electric drives. They are a little bit like Volvo IPS drives; their shafts are able to rotate 180° and they can run in forward or reverse mode. That gives an effective, 360° rotation capability and also makes them somewhat like azipod thrusters, though with azipods you can rotate 360° but you don’t get a reverse-thrust setting – you just have to rotate 180° and thrust forwards, whereas we can do both and we get the same effect.”
Beneath the vessel, the keel functions as a sensor strut, integrating survey payloads below the waterline, as well as cooling systems. While Zero was tempted to use the Mayflower’s pumped-seawater cooling approach, a conventional, closed-loop, water-glycol arrangement was found to bring greater reliability than the former’s impellers or raw water pumps.
“Since we needed a functioning water-glycol system onboard for our batteries and some other systems anyway, it made sense to share it among the other systems,” Ratsey notes.
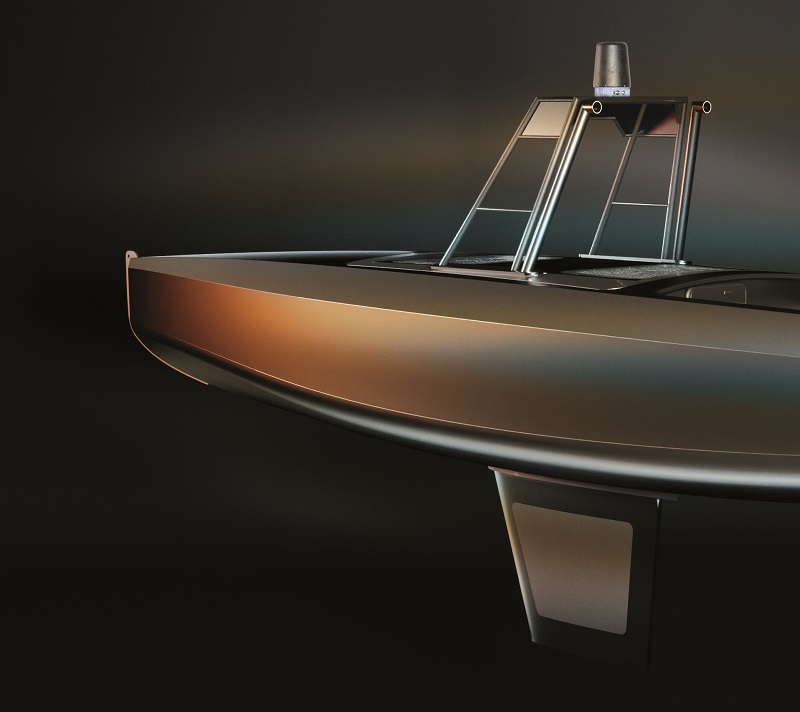
Maritime electronics
Above deck, an A-frame arrangement houses sensors for the autonomy system. As well as cameras, W-band and X-band radars are installed. The former detects objects at normal amplitude and distance, while the latter gives close-up, high-definition resolution data.
The radars were chosen over Lidar as the latter induces reflections and hence distorted images off almost any source of water, including waves, rain or splashes. Radar, by contrast, will operate in any realistic environmental condition.
“Range is a key distinguisher. Radars provide for great obstacle detection at long range, whereas even with high-quality Lidar you’ll struggle to get more than 200 m out of them,” Ratsey says.
A Simrad HALO20+ device serves as the W-band radar, purchased COTS but tuned to function with Zero’s autonomy software. The hi-res X-band system, supplied by NavTech, can distinguish between fishing traps, small mooring buoys and swimmers within 1000 m of the USV.
“It allows us to navigate among close-range objects, giving 3D information correlating very strongly with what we’re seeing on the cameras, and possibly of superior value over the vision data if visibility is poor,” Ratsey says.
The cameras are COTS bullet-type cameras from IRIS, selected for their cost-effectiveness and field of view, by which five units installed concentrically around the USV give 360° visibility.
Also installed above deck are meteorology stations for tracking weather, an AIS receiver, and a high accuracy, survey-grade GNSS-INS from Veripos. Together, the sensors provide data for a comprehensive picture of everything the USV requires to navigate.
“The autonomy system works by ingesting all this sensor information, and grades each individual packet of data with a probability score before fusing that probability data, and outputting what it feels to be the best assessment and decision for the operational situation it is being presented with,” Ratsey says.
“Say you pick up an AIS target, but neither the camera nor radars see it, the autonomy system will almost certainly judge ‘that AIS signal is old and therefore not something we should worry about’.
“Conversely, if the AIS doesn’t pick up a target, but the radars and camera all clearly see something at a given position, the main computer will judge that as a target with maybe 98% probability, and start taking its heading, velocity and so forth into account.”
The system has been designed to track multiple targets at once, as vessels rarely encounter one at a time, especially in ports. When one target is within range of the USV, there will almost always be at least two to four others on the water nearby.
Marine AI (headed by Ratsey and Phaneuf) supplies the autopilot computer, which was developed from the ground up to suit the Oceanus12, with capabilities such as low-level PLC access, and fine control over the motor steering and throttle.
“We don’t need constant monitoring or comms; nor do we rely on an unreliable and costly always-on satellite connection to operate, as many USVs do,” Ratsey says.
“That said, we do have an Iridium-based system, which we’ve found very reliable, even with low bandwidths. While things like Starlink have only come along in the last two years or so, we’ll leverage that for live streams of camera, radar and survey payload data at some point in the future.”
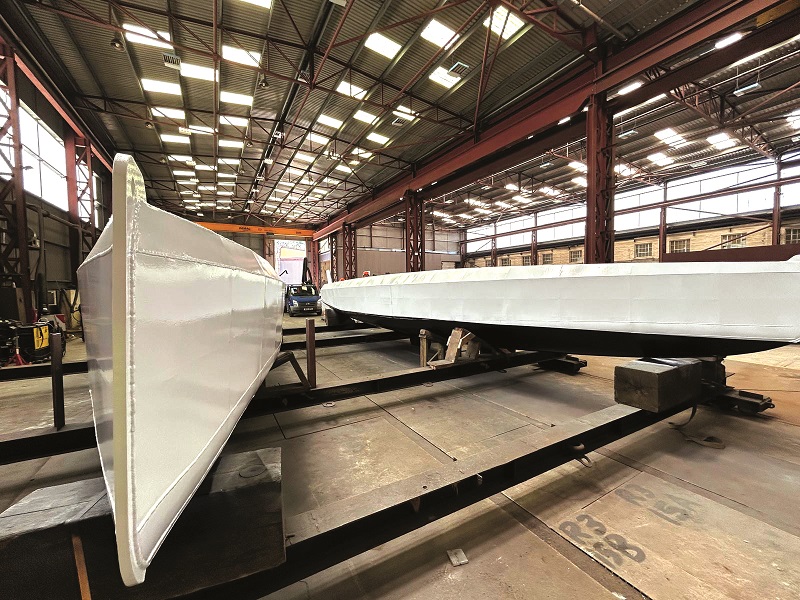
Powertrain
The main tanks are built into the Oceanus12’s aluminium structure, while the day tanks are COTS plastic vessels, and a further bladder tank may be installed within the USV’s payload space.
Two pumps, one on each side, deliver fuel to the day tank (then it is gravity fed to the generators), both pumps being COTS. For onboard fuel security, multiple redundant fuel lines and a PLC-managed valving system enable the port main tank to feed the starboard day tank, and vice versa, so operations can continue safely if a hose, connector or tank show signs of a fault.
Identical pairs of generators, inverters, chargers and drives follow, and much like the fuel tanks, they are arranged in port-starboard configurations, and each one can be isolated via the control software in the event of a malfunction.
“Regulators think that advanced software and other new tech is full of bugs or untested functions, and those are the problems they need to regulate for,” Ratsey says.
“In reality, it’s the engineering and mechanical parts that need to catch up with the level of reliability needed for fully and persistently uncrewed systems. Before Mayflower went off on its first attempt at a transatlantic crossing, I said, ‘It’s going to be a $20 part that causes us to fail’ and that turned out to be true.
“That first attempt came to a halt off the Azores for two reasons. First, a battery isolation switch had been mis-specified by that USV’s generator supplier and, second, the raw water-cooling pump died.
“An onboard engineer could fix either problem in an hour, but, for a USV, it means a five-day boat-recovery operation, thanks to less than $150 of equipment, all because they’d been used in a vehicle design that contained single points of failure. That’s why redundancy is so critical for industrial USVs.”
The generators are three-phase, 480 V systems, outputting 23 kW each, with Zero forgoing higher voltages to prevent the need for huge cables onboard. Beta Marine’s generators were chosen for their compactness, cost-effectiveness and strong fuel economy, while the alternators were purchased from Mecc Alte in Italy.
The batteries through to the motor drives are 400 V systems, provided by RAD Propulsion. Each of the two packs stores up to 21 kWh, with one designated as the master unit and the other the slave. Each drive produces up to 40 kW of thrust.
Ratsey says that as RAD Propulsion was founded by Dan Hook (previously from ASV Ltd and L3Harris ASV), the company understands the integration requirements of USVs, and has thus designed its products for transparent interfacing, digital feedback and control-by-wire.
“The RAD system isn’t Type-approved yet, but RAD is working very intensively on that. There are alternative drives that are already Type-approved, but, honestly, they just aren’t as good as RAD’s,” he says. “We’d rather use this system, especially since it will be compliant in due course.
“It’s taken a lot of tuning and bespoke work, as well as pulling together five or so different companies to talk to each other, to align specifications across the generators, chargers, batteries, inverters and drives. But the result has been a powertrain we think will be successful, with the necessary functionality and redundancy for extended work at sea.”
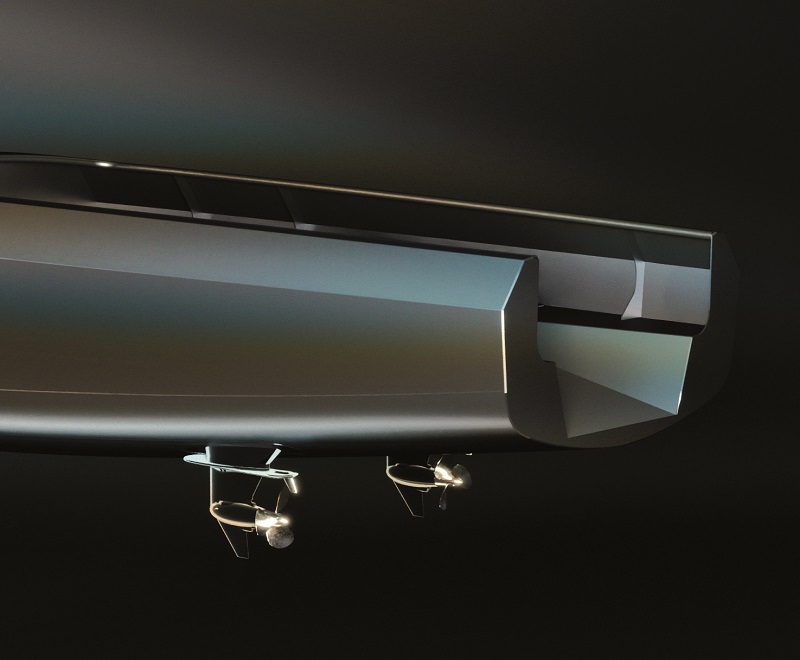
The future
For the first markets for the Oceanus12, Ratsey and his team have analysed the construction and cost targets of the global offshore wind industry. They concluded that the only realistic way these can be achieved is through having fleets of autonomous USVs, making detailed seabed maps pre-construction, and then routinely monitoring wind farms during construction or in operation.
“We’ve got a package that is built on proven technology and is genuinely turnkey, such that surveyor customers can take our USV, send it out and start making money from day one,” Ratsey says.
Going forwards from today, Zero anticipates building up the fleet of 12 m USVs over the next 18 months, with a target of 12 vessels being on the water by December 2025.
It will also keep a weather eye on the potential benefits of going bigger, with increased payloads and range, which a hypothetical Oceanus18 and Oceanus24 would allow. To start with, 12 m has been chosen, capable of deep ocean sailing.
“Right now, we’re fully able to build these USVs as fast as the market can order them,” Ratsey says.
“I think five years from now, we’ll see a lot of USVs – ours especially, we hope – in fleets of different sizes, because USV fleets will make a real and huge difference for industry.
“Imagine a survey field and place six USVs with multibeam echosounders on it – suddenly you’re able to map in swaths of 2.5 km instead of 400 m. That’s going to change everything.”
Key specifications
- Oceanus12
- Monohull
- Aluminium kit construction
- Diesel-electric
- Twin electric outboard drives
- Self-righting
- Hull length: 11.55 m
- Waterline length: 11.4 m
- Max beam: 2.33 m
- Displacement: 4 t
- Max speed: 10 knots
- Operating speed: 7 knots
- Nominal range: 2500 miles (4023 km)
Key suppliers
- Laser cutting: Snijtech
- Construction kits: Snijtech
- Generator: Beta Marine
- Alternator: Mecc Alte
- Thrusters: RAD Propulsion
- Autopilot: MarineAI
- GPU: nVidia
- GNSS: Veripos
- Cameras: IRIS
- Radars: Navtech
- Radars: Simrad
- Satcom: Iridium
- Satcom: Thales
UPCOMING EVENTS
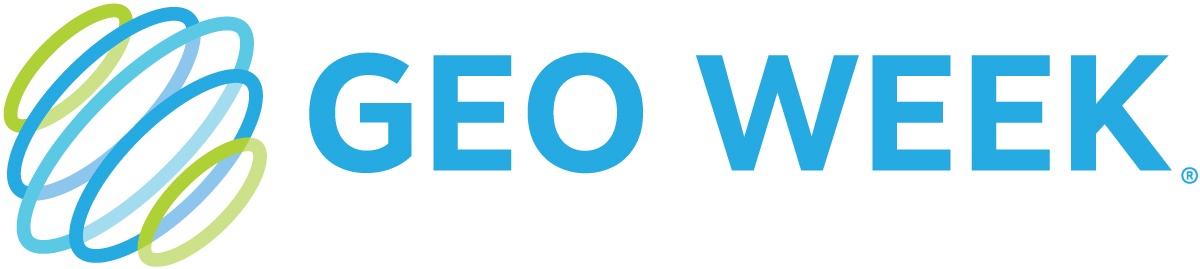
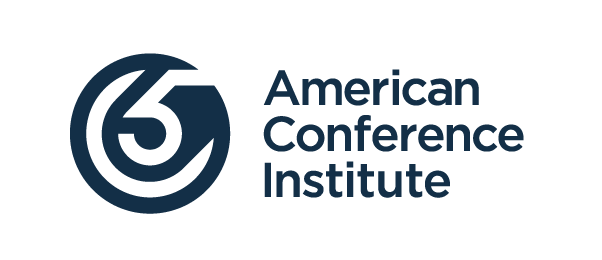
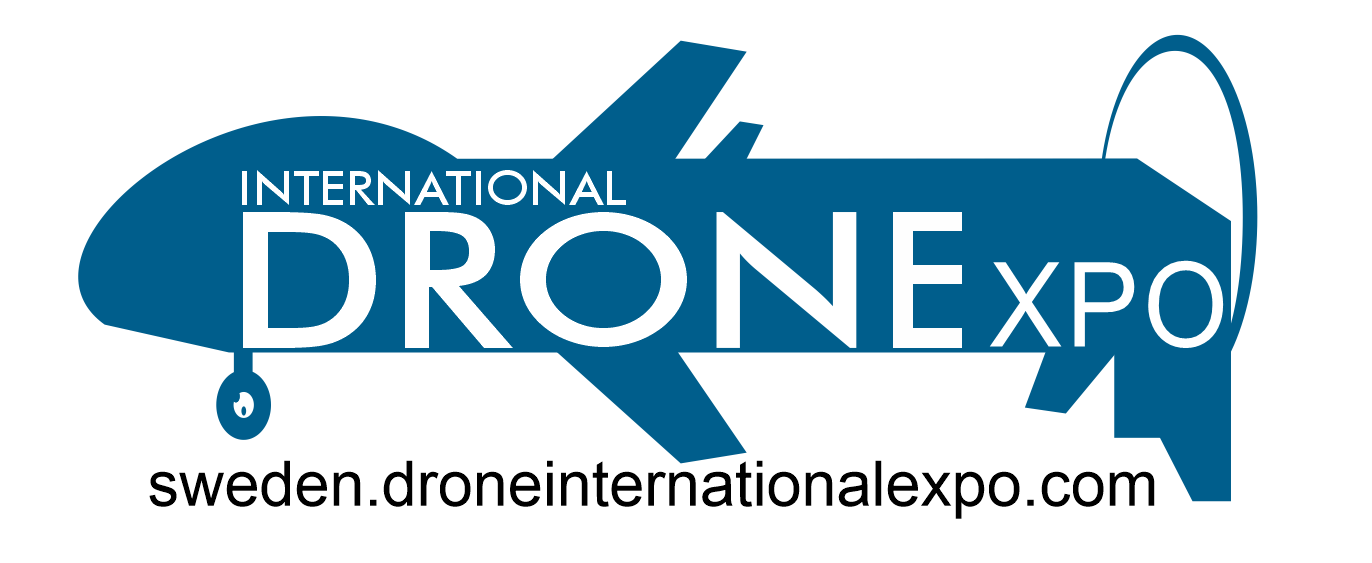
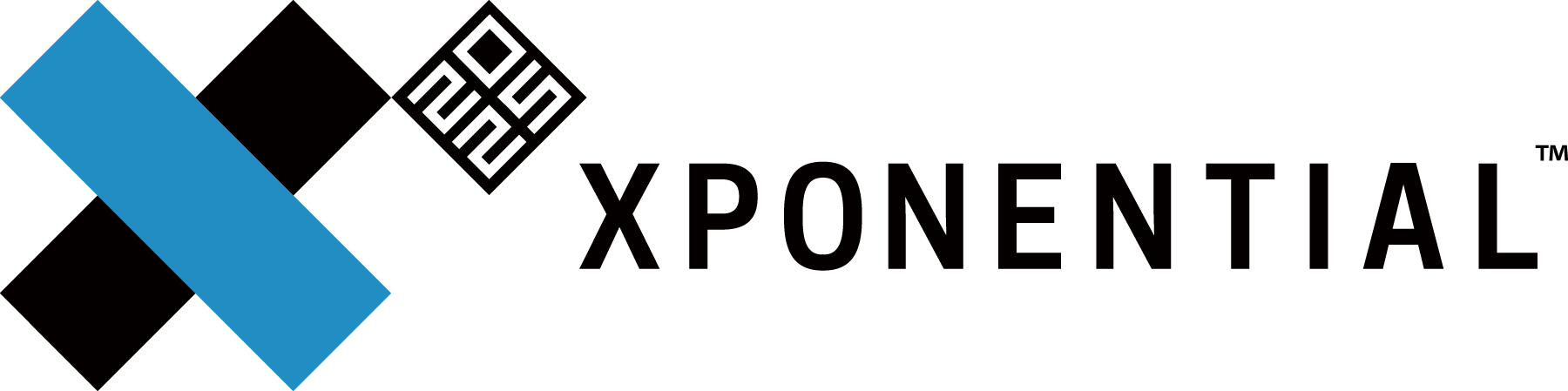
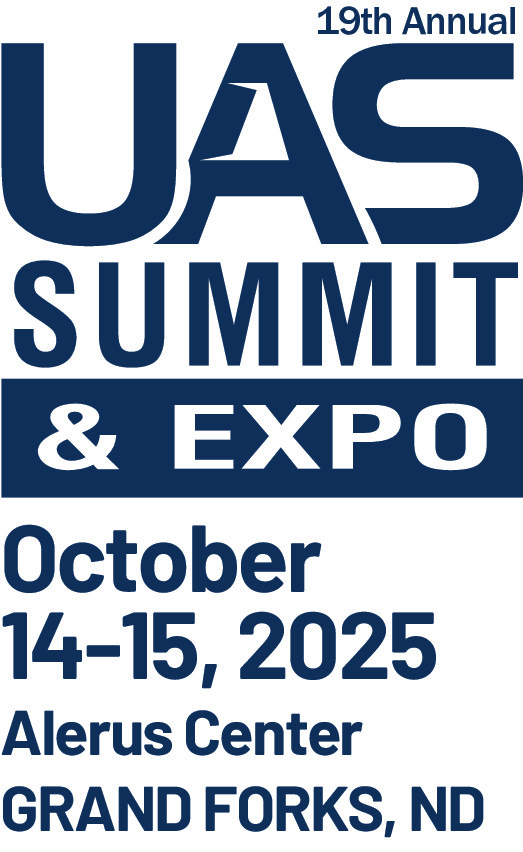

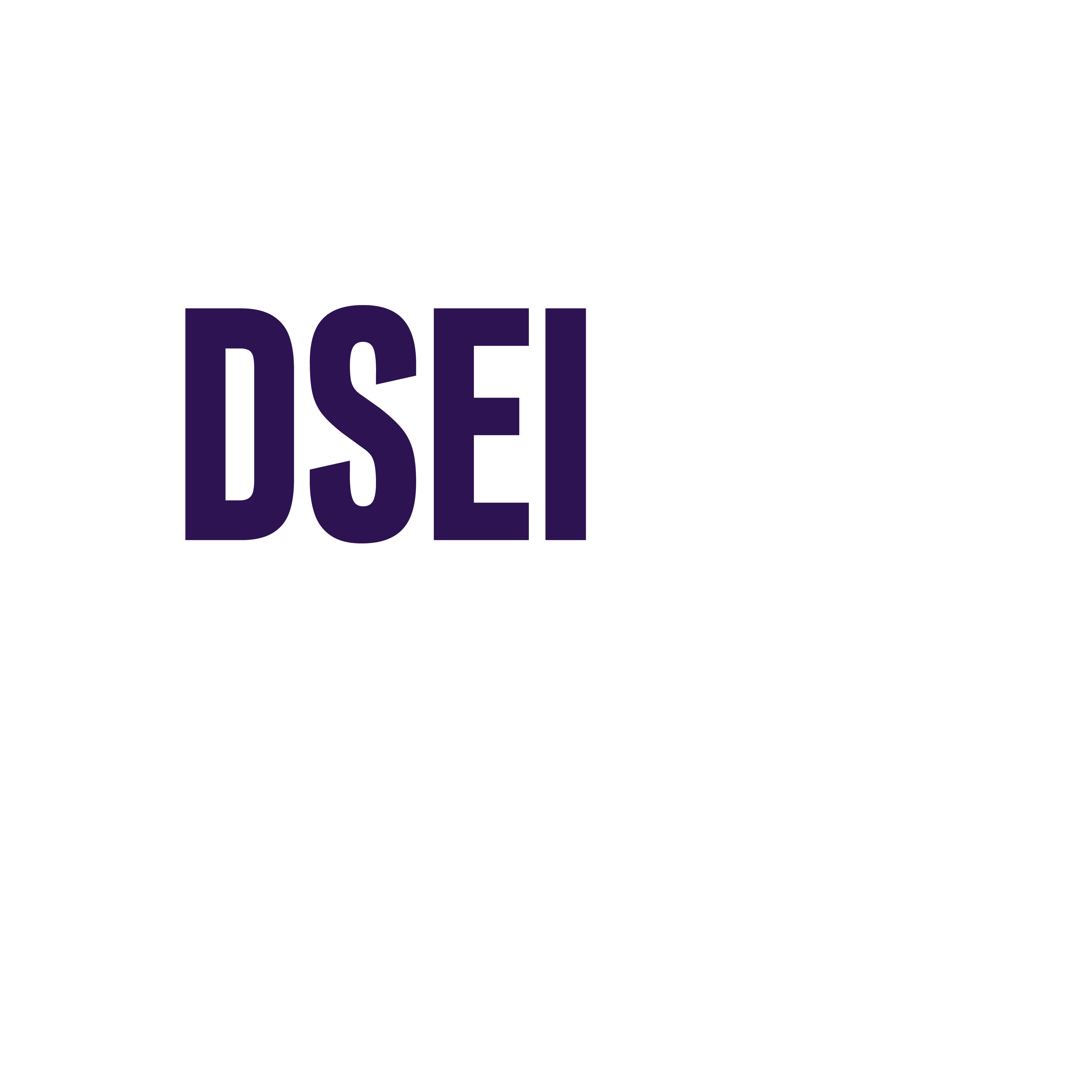
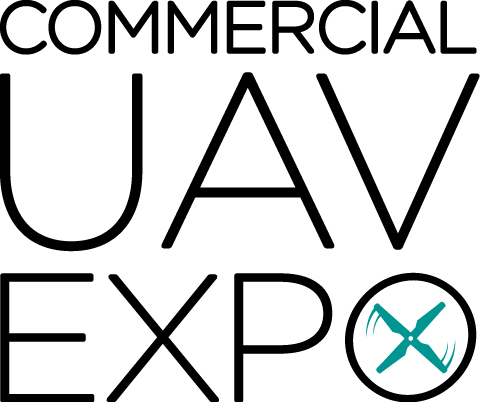
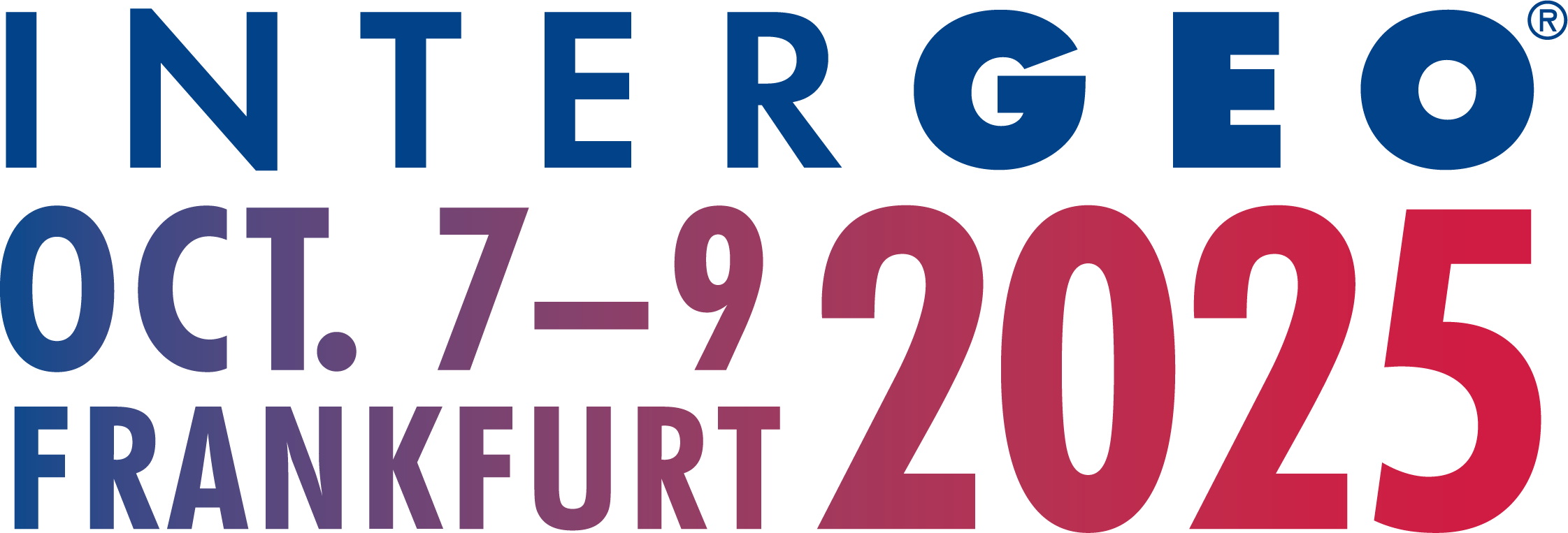
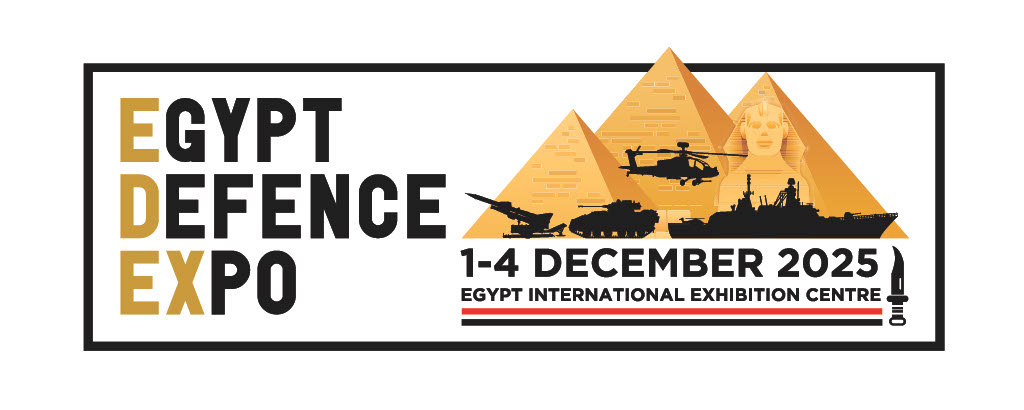
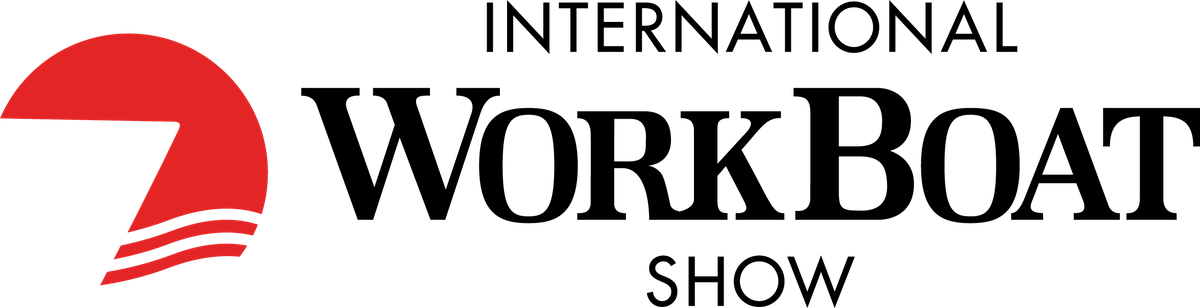