Xponential Part 2
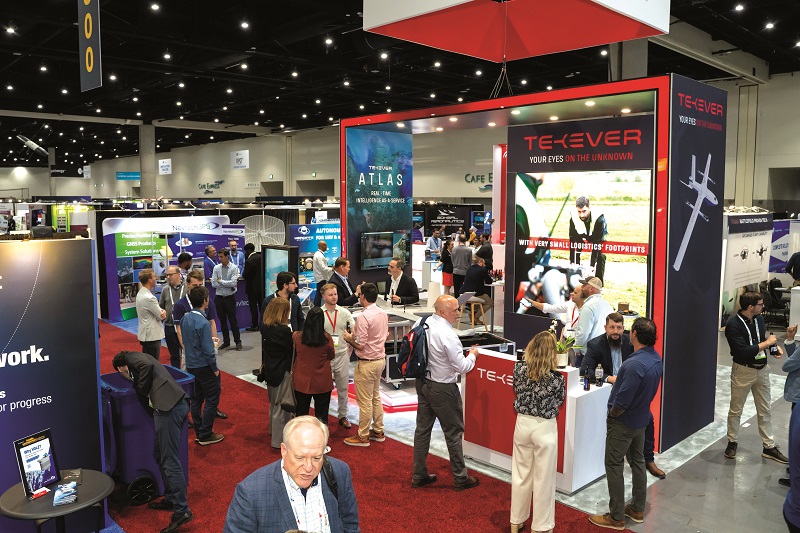
Rory Jackson checks out the latest and the greatest in uncrewed system technology
The biggest show in the world for autonomous systems, AUVSI Xponential, landed at San Diego, California in April, gathering hundreds of companies from around the world to showcase their newest uncrewed system and componentry offerings for land, air and sea.
The following is the second half of our report, covering the vast commercial tech news coming out of this industry defining show, to complete our account of what technologies are setting the stage for the uncrewed systems of tomorrow.
Tekever unveiled its ARX UAS, which is being developed to function as a carrier-aircraft for future swarming drone operations, with commercial availability expected in 2025.
“Swarming is something we do every day, with multiple units of our UAVs co-operating to execute missions,” said Ricardo Mendes of Tekever.
“We will have AR5s connected with AR3s, with distributed mission execution. For instance, the AR5 UAS is SATCOM-capable, and AR3s aren’t currently, so we will often have missions where AR5s act as network nodes for AR3s.”
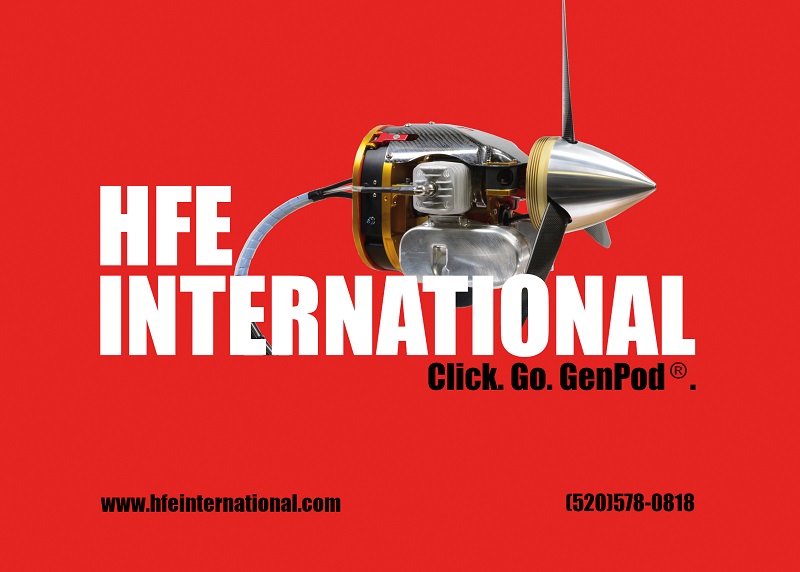
However, projecting the reach of one’s intelligence, surveillance and reconnaissance (ISR), including beyond radio range and into congested environments, requires larger UAVs for longer endurance and the capacity to carry SATCOM terminals and equipment for GNSS-denied localisation or other, smaller UAVs.
The ARX is intended as that larger, more capable platform. It integrates roughly the same autonomy stack as the AR3, but with a 600 kg MTOW instead of the AR5’s 180 kg MTOW.
Through that greater carrying capacity for fuel and payloads, ARX can fly hundreds of kilometres farther than the AR5, and at critical locations it will deploy smaller UAVs that can survey closer to vital points of interest.
“If you limit yourself to a single UAV, you have to choose between close-proximity observation, which multirotors are great at but they can’t fly very far, or far-off observation, which fixed-wing UAVs are suited for but then you’re not inspecting with good fidelity,” Mendes noted.
“The ARX will launch from bases, fly its payload of smaller UAVs to a faraway place, including over oceans, launch its other drones or ‘mobile sensors’, and loiter or perform long-range observation while acting as a node for the smaller systems.”
In addition to distributed mission planning, replanning and execution for swarm operations, the CONOPS includes one day engineering the ability to recover the smaller UAVs onboard the ARX, so the airborne carrier UAV will be able to return with its fleet to the launch point.
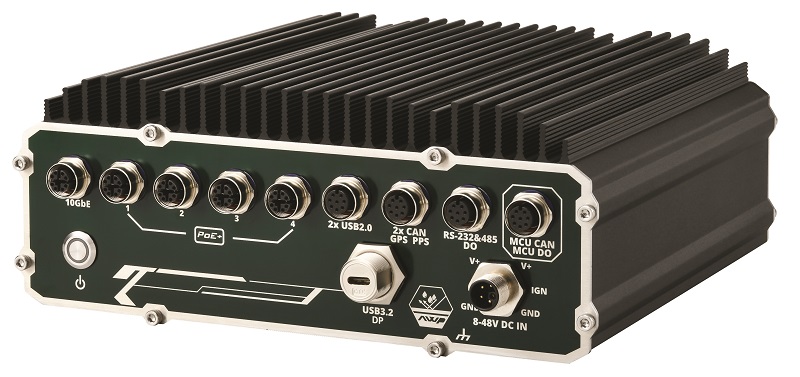
Neousys Technology unveiled two new, ruggedised AI computers, the NRU-230V-AWP and NRU-240S-AWP, which integrate nVidia Jetson AGX Orin systems, and are aimed at autonomous vehicles in offroad and roadside deployments.
“The systems’ housings were developed using experiences from earlier housings we designed for our SEMIL-1000 and POC-465AWP products, the former being a high-end, waterproof enclosure; the latter intended as a cost-effective, waterproof one,” said Neil Liu at Neousys. “Those on the NRU-230V-AWP and NRU-240S-AWP are designed as both affordable and waterproof housings.”
During the design phase of the two new products, key tests included sinking the whole machines into water tanks to validate each part of the waterproof design, from its O-ring to its panel cut-out, its waterproof cap and waterproof cables.
For verification, the systems were sent to a third-party laboratory, and subjected to high-pressure water-cannon testing; then IP66-certification was granted.
Several protocols are available for sensor integration with the two AI computers, including GMSL2 for automotive cameras or depth sensors to interface with high bandwidth over a single coaxial cable. The NRU-230V-AWP has eight GMSL2 ports for connecting solutions such as Sonyøs IMX490, ISX031 or IMX390 automotive cameras, or StereoLabs 3D cameras.
“A system-monitoring port is added on the NRU-230V-AWP, which can constantly report the computer’s thermal, voltage and OS operational health via an independent automotive MCU. It is our first step to help the customer build a reliable, functional safety ADAS or autonomous system,” Liu noted.
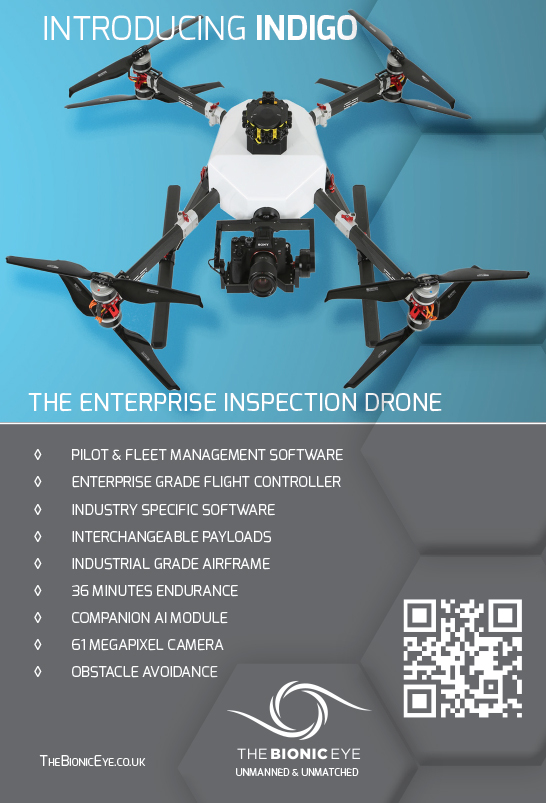
The firm also displayed its FLYC-300 computer, originally designed for low-SWaP UAV integrations, which, since its release last year, has been adopted into various applications, including 3D mapping, agriculture, infrastructure inspections, environmental monitoring, and search and rescue.
Interest has been expressed in its use in UGVs, such as industrial AMRs and robot dog-type systems, which can benefit from its light, 297 g weight and small, 124 mm x 123 mm x 30 mm form factor.
Taisync spoke with us about its ViuRC7 GCS, which is now available in the US and Europe as a compact, handheld control solution. An NDAA version will be in mass production by the end of this year.
“It is designed with a 7 in [17.8 cm] display, with dual control function systems. As well as having its own in-built radio-transmission system, it can integrate external radio modules to enable the customer to reach longer ranges,” said Eric Zhang at Taisync.
The in-built radio functions over either 2.4GHz or 5GHz, with a transmission power of 26 dBm (at 2.4 GHz) or 24dBm (at 5 GHz), with an effective range of just over 20 km. With an external radio module, this can be increased to more than 50 km.
The ViuRC7 weighs 1.35 kg, measures 292 x 160 x 80 mm, and typically runs for six hours on its battery, with recharging taking 3.5 hours on a 30 W USB-C charger. It consumes 12 W as standard, takes GPS, GLONASS and BeiDou GNSS signals, and it can operate in temperatures from -20C to 55C.
“As a company, we’re still primarily focused on communication solutions, but we’re also taking opportunities to expand our expertise into connected areas, such as GCSs to start with, and we’ll also launch our first cameras next year as integrated, connected, remote survey solutions,” Zhang added.
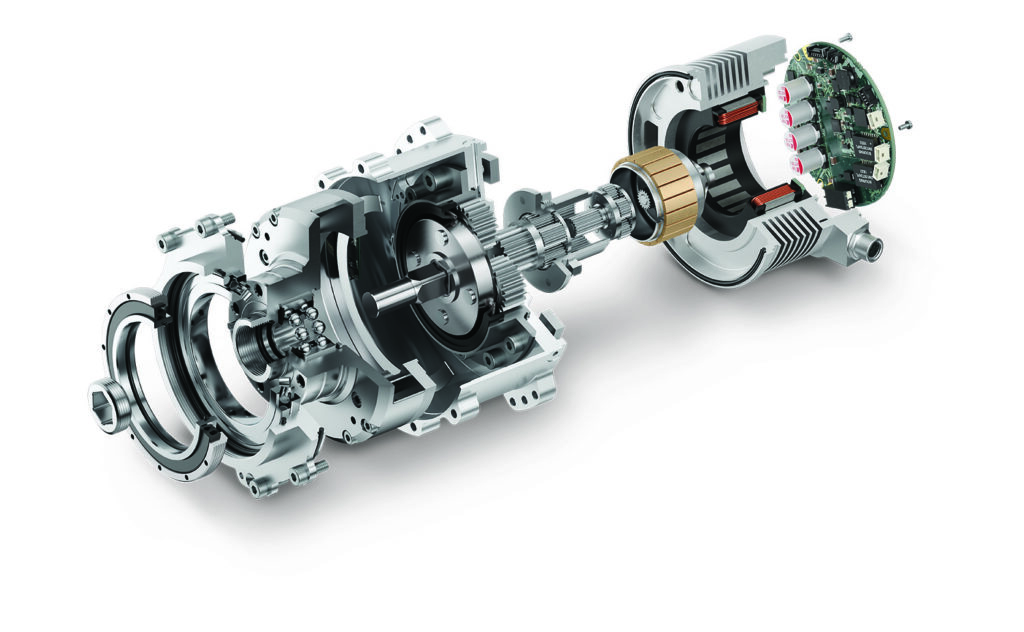
We also met with Maxon Group to discuss some of its electric motors for specialised uncrewed applications.
“We have a predetermined subset of our motors, gears, encoders and resolvers that can be used in space, which are rated for vacuum conditions, high levels of shock and vibration,” said Jeff Randall at Maxon.
“One recent space application involved using a frameless, brushless DC motor from our DT [Dynamic Torque] motor family, and configuring it with a dual-redundant winding in the stator, essentially packaging two independent motors into this one solution. That system was used in solar array deployment, so that if one winding failed, the motor could still extend the solar array so the spacecraft could replenish its energy.”
Included within its range of space-rated solutions is the EC4-pole 22 SPACE, a brushless DC motor rated for 90 W and measuring 22 mm in diameter. The product weighs 175 g, functions on a 48 V DC input and can operate in ambient temperatures from -20C to over 100C.
The company also exhibited several of its new UAV propulsion motors in diameters of 22-90 mm. With their ESCs, they are configured to achieve minimal weight while retaining lifespan and reliability.
Among the larger solutions in Maxon’s propulsion range is the EC 87 flat UAV, which is a 87 mm-diameter, 309.5 g brushless motor, designed to produce up to 9 kg of thrust with a maximum speed of 6500 rpm, consuming up to 22.3 maximum continuous current.
Additionally, the UAV ESC 52/30 CAN is one of the larger ESCs, which communicates using the DroneCAN v1 protocol and commutates motors via sensorless FOC. It weighs 102 g, including cable and housing, and it is designed to deliver up to 30 A continuously (90 A peak) to e-motors at just over 99% efficiency.

Hirth Engines is working on a series of updates to enhance its two-stroke, two-cylinder, 41-Series engine with technologies not yet used elsewhere across its engine portfolio.
“The engine is undergoing a facelift to have a smaller exhaust and possibly a new coating in the cylinder,” said Torsten Windorfer at Hirth.
The new (undisclosed) coating is expected to make the spark-ignited, air-cooled engine more reliable over long endurances, and extend the TBO slightly by reducing the rate of scratches and ensuring against failures internally. It may also increase the engine’s 8 hp output by about 5% due to reduced friction of the piston against the cylinder wall and less blow-by.
“We are now simulating the new, smaller exhaust for optimised resonances along the length of the port, which will also increase horsepower by around 5%,” Windorfer added.
The German company is updating its 23-Series engine, targeting 10% more power output for the 50 bhp system, as well as increased torque, partially through a similarly redesigned exhaust system, but also via a new injection system.
“We’re well-versed in different kinds of direct injection that we could implement, and now we’re also looking into transfer port injection,” Windorfer explained.
“The latter may turn out to be better for inline engines, like our 35-Series [Issue 36], because of packaging advantages, but we’re also looking into it for the opposed-twin engines. Meanwhile, we have a new FEM simulation tool for examining how weight could be removed from any and every part, so we have big weight-reduction targets we want to reach too.”
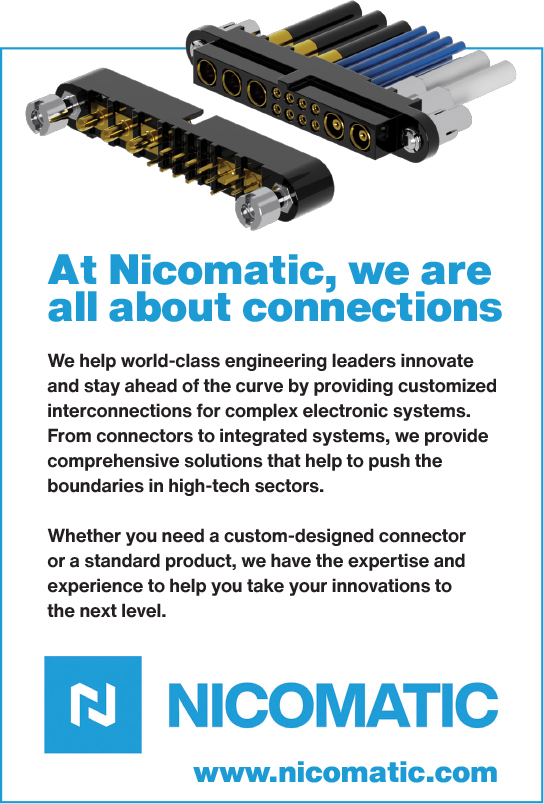
Domo Tactical Communications (DTC) has developed an RF ranging capability, leveraging its existing BluSDR IP Mesh radio technology and MeshUltra waveforms.
“While DTC BluSDR radios are typically used for C2 or ISR downlink comms, they can now also measure the time taken for a signal to get from one radio to another and then back to the first radio again,” said Rob Garth at DTC.
“This round-trip Time of Flight allows us to understand how long the signal took to travel through the ether, and as we know the speed of light we can then calculate the distance between the two radios. Add further nodes with known positions into the system and we can start to triangulate an absolute position for a UxV in a GNSS-denied environment.”
DTC is also working with its partner, Inertial Labs (INL), which is integrating its IMU and GNSS data with DTC’s RF ranging data to deliver a single, ‘fused’ best estimate for position with a single NMEA output, which removes the need to add additional software to an existing flight controller.
“The partnership with Inertial Labs enables us to combine DTC’s many years’ expertise in delivering robust, long-range, wideband, wireless communication links with INL’s innovative Alt Nav technologies to deliver a really exciting, multi-source, fused-positioning capability, which can enable effective drone operation in GNSS-denied environments,” Garth added.
“We’ve done a lot of trials in different ground and air environments to gather data for optimising the system, and we are pleased to see RF ranging accuracies as good as 20-30 m, irrespective of operating range.”
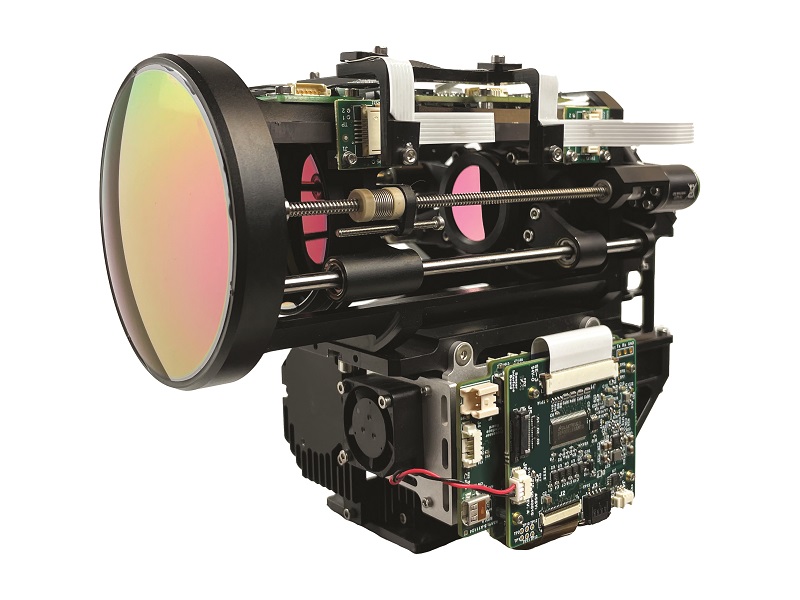
Sierra-Olympia Technologies exhibited a range of new capabilities for its Ventus HD6 series of cooled MWIR cameras, including different lenses.
“One is an 18-180 mm folded zoom lens; that folded aspect making it ideal for use in airborne applications like 8 in gimbals. When that’s integrated, we call it the Ventus HD2.4, for its 2.4° horizontal FoV at full zoom, going up to 25° at wide angle,” said Jacob Begis at Sierra-Olympia. “The other lens is a 50-720 mm zoom lens.
“Both lenses are f/2.6, so they collect a lot of light compared to the other big-zoom lenses used in the mid-wave market. A lot of them are f/4 or f/5.5, so we collect about two to four times as much light, which improves sensitivity.”
The HD6’s core includes a focal plane array with a 6-micron pixel pitch on a HD (1280 x 960) format detector. The larger format, paired with the small pixels, results in excellent spatial resolution while maintaining its FoV. Conventional, mid-wave cameras are VGA resolution (640 x 480) and typically have 10-15 micron pixel pitch.
“The HexaBlu sensor, made by Leonardo DRS, has a demonstrated 27,000 hour-plus Dewar lifespan, keeping it working in the field for longer,” Begis added.
“We also sell the Ventus HD6 with our image processor from Sightline Applications, which performs video encoding, allows non-uniformity corrections over zoom, and provides software features such as focus metric and KLV metadata injection.”
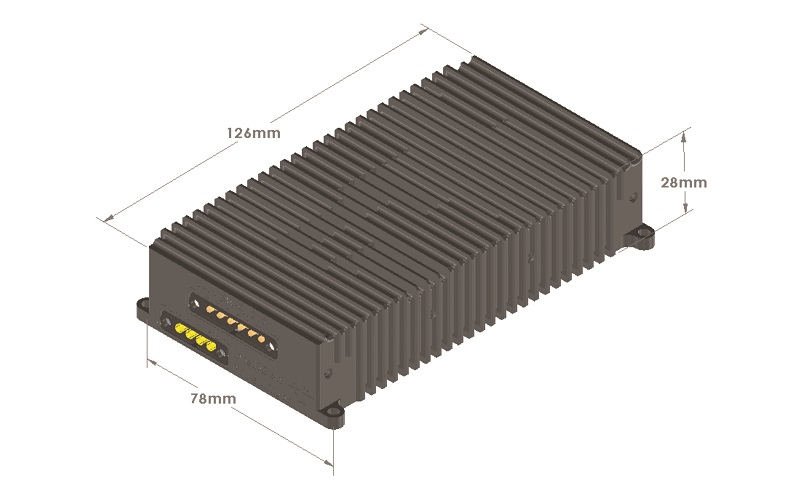
Power4Flight unveiled its IntelliGen, which has been developed over the past several years as an intelligent controller (or PMU) for starter-generators in today’s high-end UAV powertrains. It has been programmed and matured as a solution for efficient charging of eVTOL battery packs, thrust augmentation, adaptive load sharing and management, and, of course, electronic starting.
“The electronics used to start and drive today’s engines are often massive, because starting an electric motor with full torque at 0 rpm is hard, especially in a sensorless motor, but IntelliGen is designed with Hall sensor inputs, which allows it to pull correctly commutated currents for quickly cranking an engine to 1000 rpm from zero, while using significantly less power and space than conventional starter-controllers,” said Bill Vaglienti at Power4Flight.
As the system runs, it uses synchronous rectification to turn a generator’s alternating current (up to 70 V AC and 40 A) into direct current for charging a battery. But, rather than using passive rectification with a six-diode bridge (which can incur significant losses), IntelliGen runs using active rectification and can set the voltage coming off the DC rail to match the battery requirements independent of engine speed.
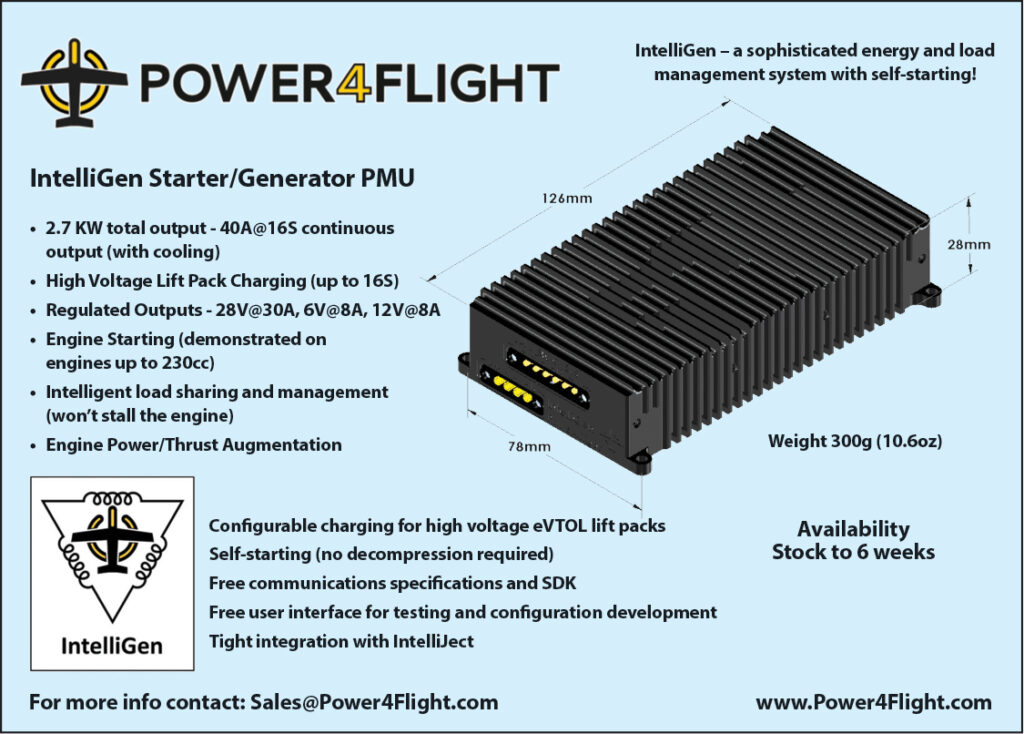
Downstream of the rectifier, a regulator is installed in IntelliGen for outputting regulated 28 V DC power to the rest of the UAV (this output can be configured for an 8S LiFePO4 pack or a 6S LiPo pack). Installed with that are additional 6 V and 12 V regulators, ensuring diversity of power supplies for differently sized DC buses across voltage architectures.
“Perhaps most uniquely, we’ve designed a variable, real-time, current-limit control function into it, which means the amount of power the regulator can supply can be chosen through the software at any given time, or set to limits based on certain engine speeds or temperatures,” Vaglienti added.
“That also means we can configure the system to avoid overloading the engine if the electrical load becomes too big – not something that is possible in a passive rectification system. If your payload suddenly pulls 1000 W, but your engine is overheating, we can trigger a backup battery to take the load while the engine slows down and then pay the battery back later once the engine is in a safe thermal state to recharge it.”
From its 28 V output, IntelliGen nominally provides up to 15 A, though with adequate cooling this can increase to 30 A. The system weighs 300 g, measures 126 mm x 78 mm x 28 mm, and communicates over either CAN or a serial interface.
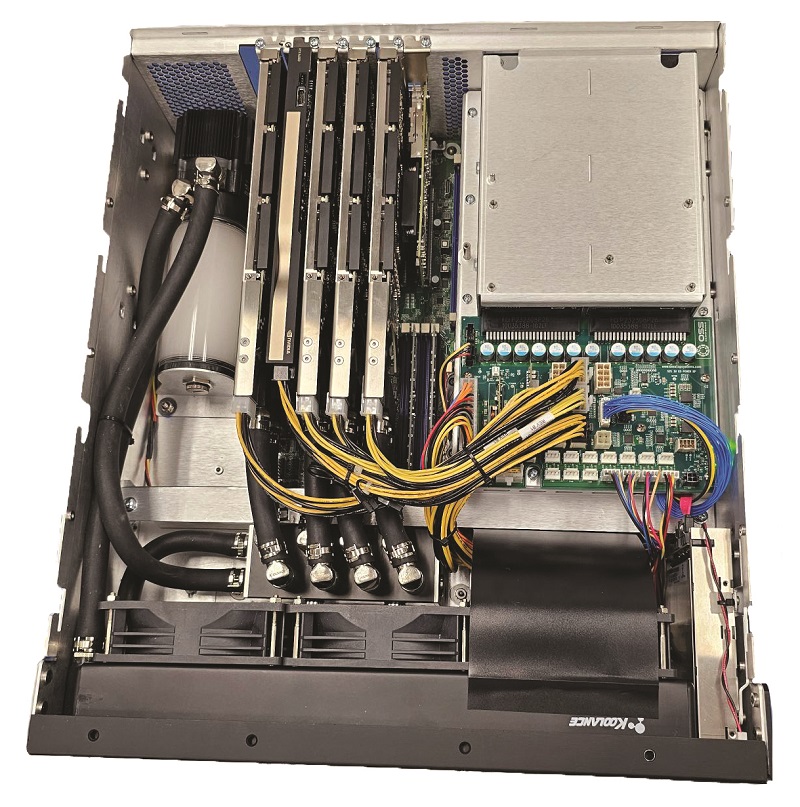
One Stop Systems (OSS) exhibited the PCIe Gen4 version of its 3U short-depth server, a rack- or flange-mountable chassis compatible with flexible power inputs ranging from 48 V DC up to 240 V AC, the past versions of which are currently deployed in several autonomous systems operating in rugged environments.
“This version is our liquid-cooled 3U SDS, supporting four NVIDIA A100 GPUs,” said Jaan Mannik from OSS. “It still has the forced-air system of the previous generation to cool PCBAs and other devices, but today’s CPUs generate too much heat. Some new CPUs have a 250 W TDP [thermal design power] and GPUs are around 350 W of power.”
To compensate, OSS has engineered a fully self-contained liquid-cooling system into the server (bypassing the need for any external hoses or fittings for coolant), the first unit of which is deployed in a submarine as of writing.
The coolant itself is a proprietary mix of ethylene glycol and some other components from OSS’s partner. It sits in a reservoir in the chassis, runs into a radiator, and out into a switch that proliferates the mil-spec hoses outwards to the heatsinks on the GPU and CPU.
“The design is ideal for any integrator or operator who has to deal with extended ambient operating temperatures, or who just doesn’t like generating a lot of noise,” Mannik added.
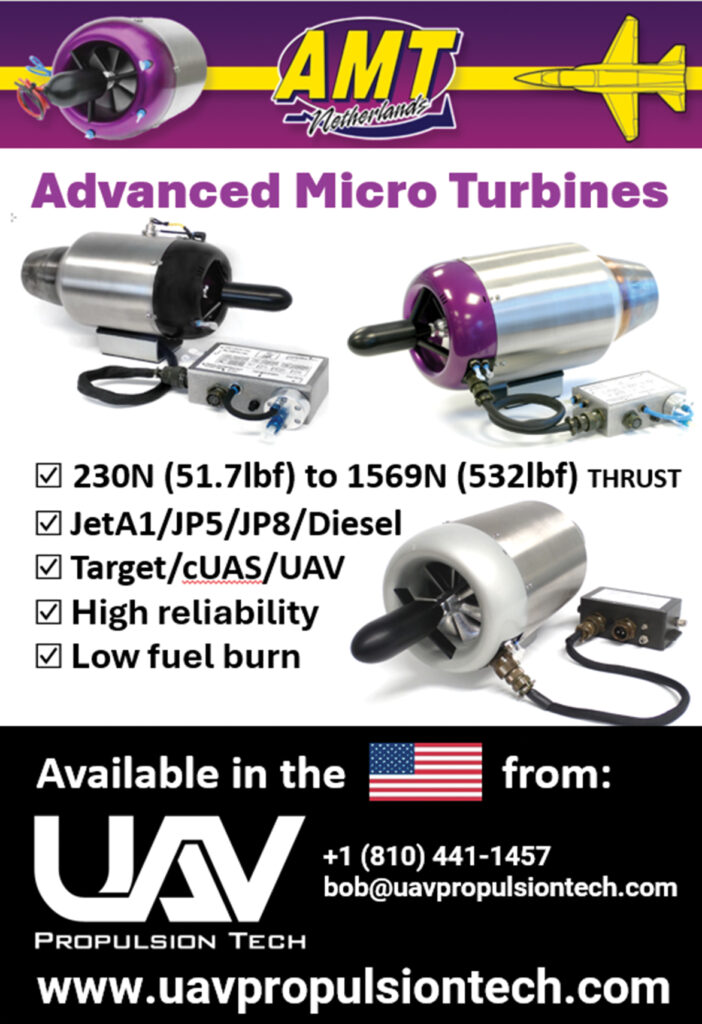
“It is also fully configurable for customers to implement PCIe 4.0 or 5.0. They can also use Intel CPUs or AMD CPUs, and select their end-point devices.”
The company also showcased its Donati and Cernis solutions, its first embedded compute platforms. The former is a 4.8 kg system with 64 Tensor cores and 275 TOPS of AI processing performance, while the latter is an 8.66 kg system with 32 Tensor cores and 40 TOPS processing.
“These were highly purpose-built for a specific army application for 360o situational awareness in an armoured military vehicle and had to survive submergence in 1 m of water – a tough requirement we were able to meet and exceed. To that end, both Donati and Cernis have waterproof, mil-spec 38999 connectors,” Mannik said.
“Second, many users leveraging an NVIDIA Orin ECU will connect multiple Orins together via Ethernet to create greater performance, but we networked ours via PCIe, leveraging our core competency in high-speed PCIe design.
“Hence, Cernis functions as a big PCIe switch, like a top-rack Ethernet switch, but 256 times faster. That high speed and low latency removed a serious glitching problem the end-user suffered every time one of their cameras moved.”
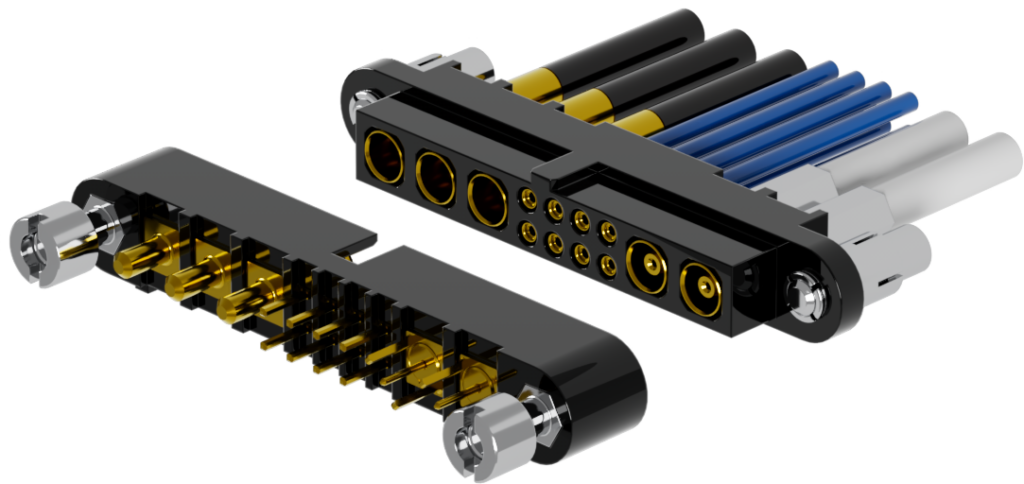
Nicomatic spoke with us about its CMM modular connectors, which have been developed as a highly customisable solution for overlapping connector requirements.
“The CMM connector can integrate power, signal and coaxial contacts in a small form factor, reducing the total number of connectors per PCB, and hence the weight and cost across such boards,” said Nicholas Wojtusik at Nicomatic.
“Up to 12 high-power contacts can fit per row, with up to two rows of those special contacts, or if it’s all signal pins then up to 120 contacts in three rows can fit in a connector, derated to 3 A. So any combination of those two extremes is possible. There is maybe up to 60 million different forms the CMM can come in to fit different users’ needs, covering not just pin permutations but features like blind-mating and others, and they can be available anywhere from two to five weeks, depending on volumes.”
Most recently, the CMM series has begun integrating high-speed SMPM data contacts from France-based Radiall. The resulting CMM SMPM-Series connectors enable high-speed signal transmissions of up to 40 GHz and 50 GB/s, with up to 10 such pins being able to fit on a single row in each connector.
“Those pins are also compatible with the other hardware designs in the CMM series, so they can be through-hole, surface-mount, right-angled, straight, cable-to-cable and so on, housed in a high-temperature thermoplastic that can function in environments up to 260 C, down to -50 C,” Wojtusik added.
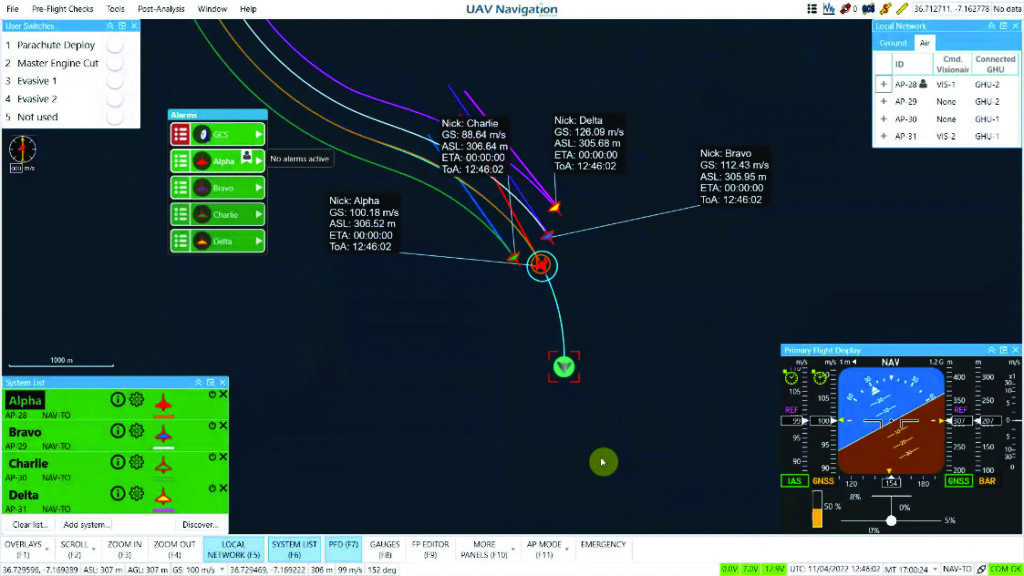
UAV Navigation-Grupo Oesía talked to us about the nineth version of its VECTOR autopilot software. It has been developed to expand customers’ portfolios of mission applications with improved complex swarm, synchronised and coordinated flight operations via intercommunications and telemetry exchanging among multiple UAVs in flight.
“We have also enhanced its GNSS-denied navigation capabilities for precision in real contested environments, and enabled control of uncrewed vehicles from onboard crewed platforms and from multiple GCSs, facilitating seamless GCS handovers,” said Miguel Angel de Frutos Carro at UAV Navigation-Grupo Oesía.
“The flight-control system now includes key functionalities such as mission replanning with autonomous recalculation of flight paths to avoid unauthorised or geofences air zones.”
The new version of VECTOR supports 4D trajectory executions for automatic and precise arrivals at specific waypoints within predefined timeframes; a key capability in applications including target drones and package-delivery UAVs.
Meanwhile, the company has refined the internal algorithms of the POLAR-300 AHRS-INS (embedded in the VECTOR autopilot) for navigation estimation and it is developing new components for it, with a target of reducing the rate of drift accumulation during flight.
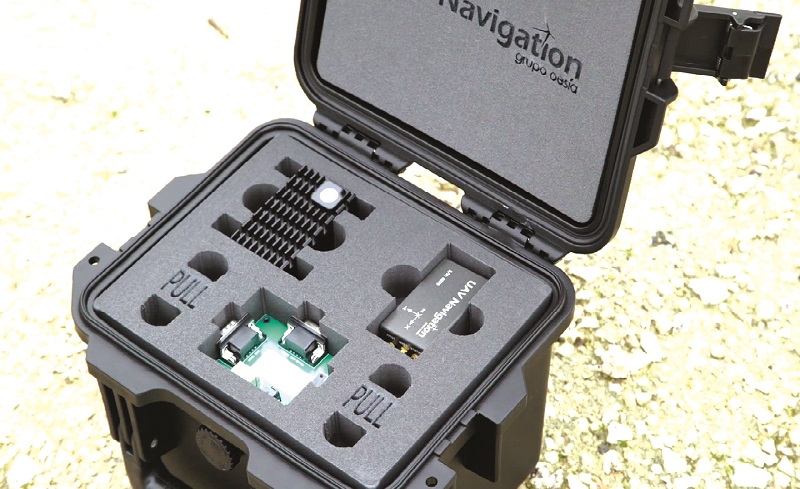
“We are also continually making improvements in our AI-based visual-navigation system, VNS01, especially to enhance and optimise its GNSS-free positioning precision in low-visibility conditions and complex environments where the camera might not always work properly,” de Frutos added.
The firm has released a GNSS-Denied Navigation Kit, consisting of the VNS01 with the POLAR-300, for clients looking to operate accurately in areas with limited satellite signal coverage, or where the signal is subject to jamming or spoofing.
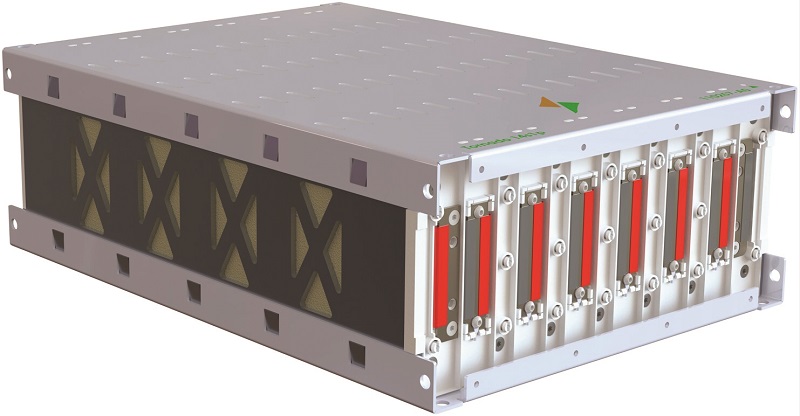
Stafl, a manufacturer of optimised battery packs and BMSs (as well as other automotive electronics), has partnered Amprius, a leading manufacturer of silicon-anode lithium-ion battery cells.
Amprius is Stafl’s preferred supplier for advanced battery packs in uncrewed, urban air mobility and other aviation-type applications. In turn, Stafl has been named as Amprius’ preferred pack manufacturer for more complex systems, including those in need of sophisticated battery management systems.
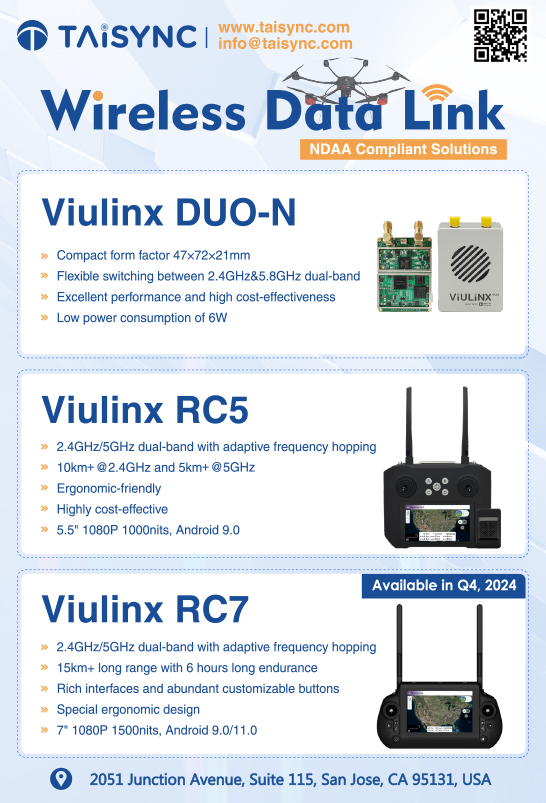
“Stafl battery packs are great when you need a system that can be certified; something rugged and secure enough to take off and land on a naval vessel or operate in an austere environment, including underwater,” said Trevor Steele at Stafl. “Our battery packs are high-performance and are often used in larger applications that need something more than a shrink-wrapped battery pack.”
Stafl constructs battery packs of up to 1 MWh in size down to tiny packs for smaller UAV manufacturers eyeing certification. The company’s Amprius cell-stocked packs achieve up to 280 Wh/kg (at pack level), the reduced gravimetric energy density coming with greatly increased longevity, reliability and safety in severe environments over unprotected cells.
Regarding Stafl’s pack architectures, Steele explained: “We use a layered approach to pouch cells. We start with a pressure foam to give good pressure on the pouch cells, [and] then we put on a fireproof layer designed for passive propagation resistance to prevent at all costs a situation where one cell could ignite another, sending the rest of the pack into thermal runaway.”
The company can also integrate various other pack subsystems, such as active thermal management via cooling plates, passive cooling via conductive heatsinks, and heating systems.
All Stafl packs are manufactured using laser welding to bond cells together, with in-house testing capabilities (including shock, vibration, environmental and altitude tests, along with in-house validation of cell data) certified to UN 38.3 standards, such that the company can legally transport its own packs, and recover them back to its facilities.
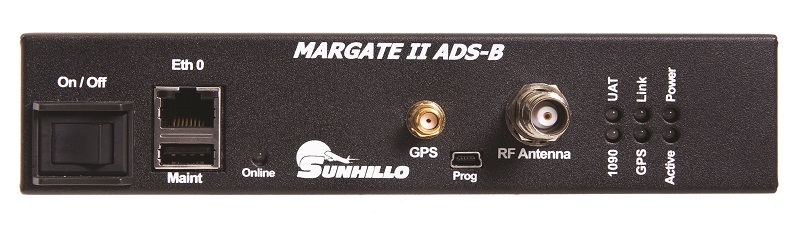
Sunhillo displayed a range of new systems for uncrewed traffic management (UTM) and operational integration, developed with standards for government and defence users in mind.
“We’ve focused on technologies for acquisition, conversion and display of surveillance data on UAV traffic for end-users’ situational awareness, and porting it via different outputs into actionable user interfaces,” said Doug Walczak at Sunhillo.
“Our display is an off-internet design, often mandatory for military uses, and is configurable with different overlays and several areas of customisability, including filters and visual/audio alerts for targets entering predefined ranges or geofences for flight-safety restrictions.”
Sunhillo’s surveillance technology ecosystem includes software for the fusion of surveillance data; a key solution for users who possess multiple radars and/or ADS-B sensors, and are at risk of target overlap and cluttering on a visualisation display. This data fusion is used at multiple US Military ranges, and it will be deployed to NASA and AFWERX for a digital Advanced Air Mobility (AAM) operations centre for uncrewed systems.
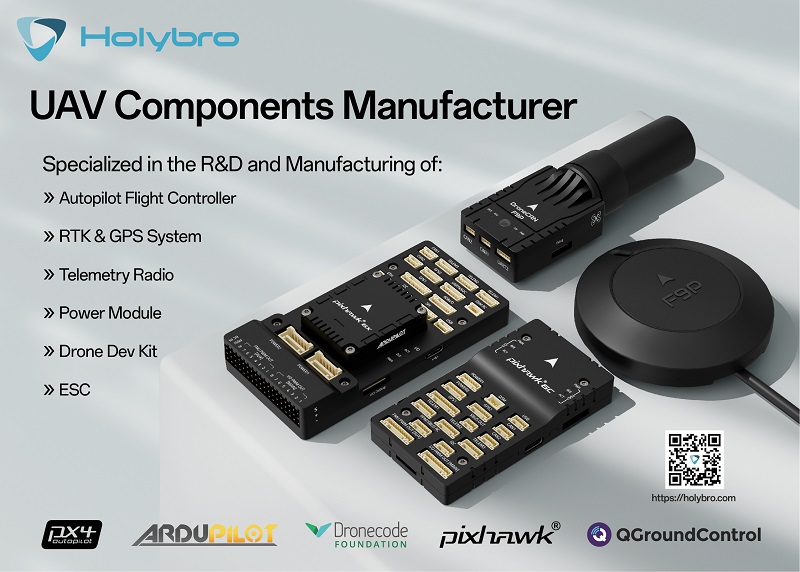
“Sunhillo also has ADS-B receiver technology, which is currently deployed in all branches of the US military, usable via a simple plug-and-play installation with an antenna, and it can receive targets up to 200 miles [321 km] away,” Walczak added.
Vector Technics attended the expo to showcase its capabilities in manufacturing bespoke BLDC electric-motor and motor-controller designs.
“As well as providing electric propulsion and power-distribution solutions for high-end UAV manufacturers, we provide our manufacturing capabilities to overseas electric-motor companies. CR Flight, for instance, have chosen Vector Technics to manufacture their counter-rotating electric-motor product, which involves their patented eVector technology,” said Prudhvi Raj of Vector Technics.
“Traditional manufacturing facilities are filled with mechanical engineers and technicians of that sort, but we’re all aeronautical engineers and pilots who have built UAVs. So when a customer comes to us, we don’t offer them an off-the-shelf motor; we ask them about their aircraft: its design, its aerodynamics, its weight and so on. We’ve brought in expertise in electronics, aerodynamics, materials science, coatings and more to cover all possible ways to optimise an electric UAV powertrain.”
Further key assets in Vector Technics’ manufacturing are the use of Litz wire in its stators, and a policy of completing comprehensive design and development cycles within two weeks of a consultation with a customer.
“That includes finishing a first prototype for them to trial,” Raj says. “We will design both outrunner and inrunner motors, and linear motor actuators, as well as rotary ones, with integrated sensors upon request; and as well as accommodating most any constraint the customer specifies in the custom design, everything we produce is mil-certified, so they can be flown in NATO aircraft.”
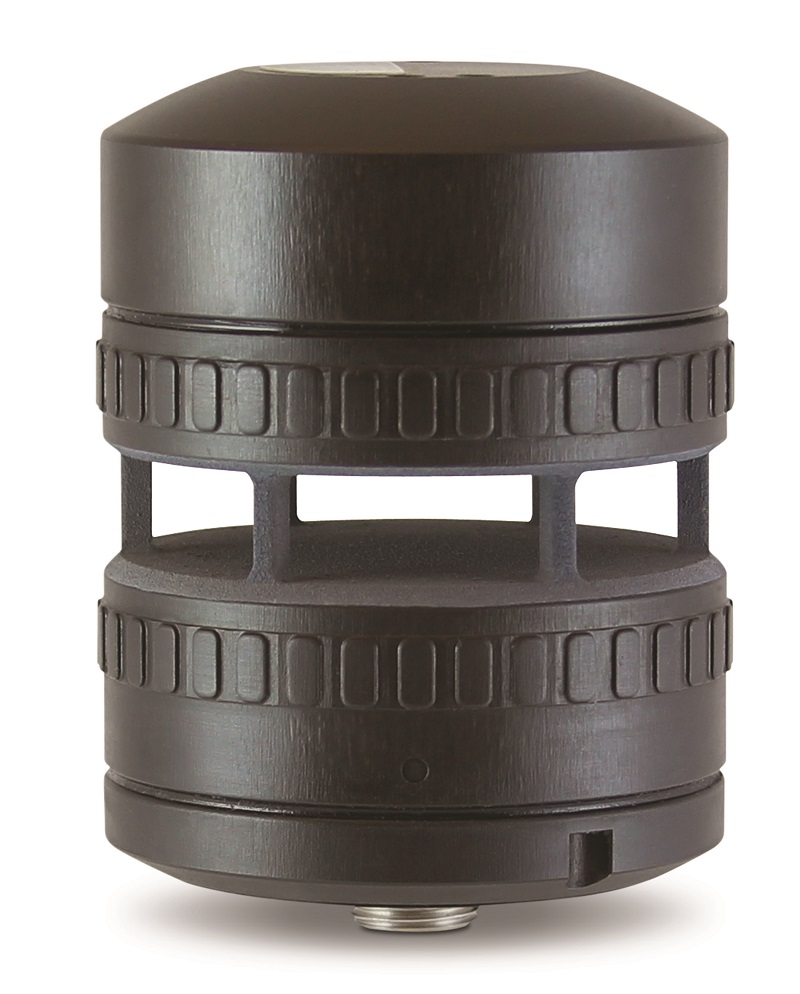
FT Technologies discussed with us one of its wind sensors, which has recently been updated with integrated barometric pressure following customer requests.
“It was previously known as the FT742, but with the added capability we’ve renamed it the FT743, and putting it on a UAV means you can now also measure altitude using barometric pressure data,” said Gordon Bease at FT Technologies.
“Our Acoustic Resonance core-measurement technology is unique and exclusive to FT Technologies. It is the only ultrasonic wind measurement technology that is immune to vibration and external noise. Our customers are using our sensors on multi-rotor craft and fixed-wing drones to provide critical meteorological information to assist in applications such as methane-leak quantification, windfarm energy production analysis, wildfire monitoring, atmospheric profiling, scout drones [and] Pitot tube replacement, etc.”
The FT743 weighs 252 g, measures 71.2 mm tall, can detect wind speeds from 0-75 m/s, and operates in temperatures from –40 C to 85 C.
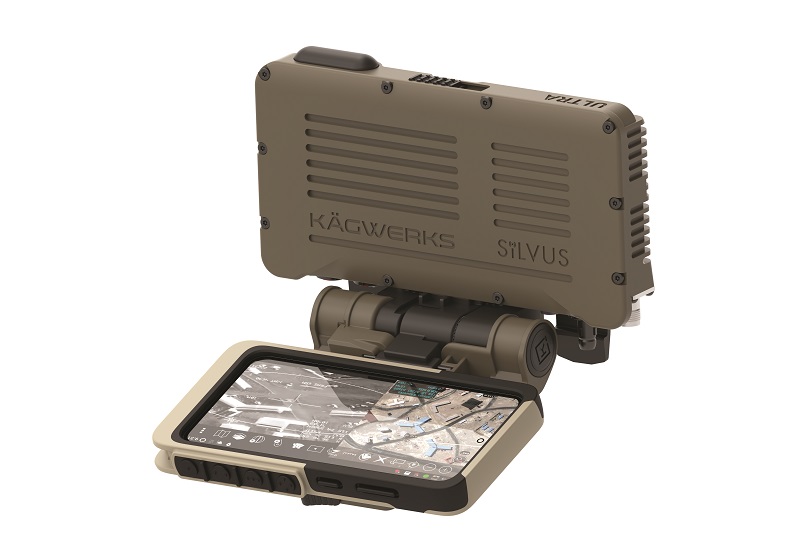
Silvus Technologies showcased its DOCK StreamCaster, DOCK ULTRA SL4210P, a body-mounted, tactical networking system with integrated EUD, MANET radio mesh networking, edge computing and AI processing capabilities.
“We integrated our StreamCaster 4200 radio with a Samsung S23TE EUD [end-user device] in one compact, chest-mounted unit, providing the warfighter with video, voice and IP data communications, and instantly access Android Tactical Assault Kit [ATAK], and Intra-Soldier Wireless and Nett Warrior connected devices,” said Brad Carraway at Silvus.
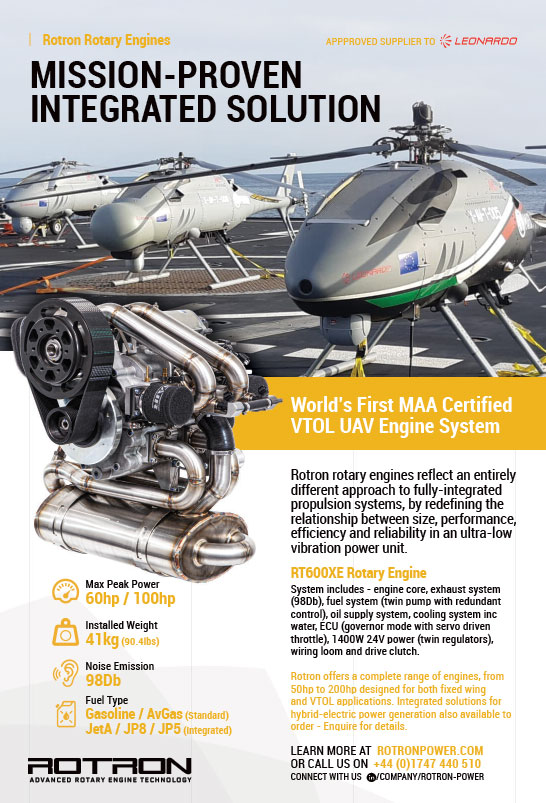
“It takes them from a personal area network to a wide-area mesh network instantaneously, and utilises unified power for both the MANET radio and the EUD, removing 36% of the cabling and weight than if you just ran those two systems separately about your person.”
As well as using ATAK to tap into any connected UAV’s sensor feed, the DOCK ULTRA SL4210P integrates an nVidia Jetson Nano AI for AI-powered object recognition and dynamic typography in mapping data.
Silvus showcased its StreamCaster PRISM sectorised MIMO antenna array, which has been designed as a modular and mobile solution for air and ground data links, with quick installation at semi-mobile positions in mind.
“To the end-user, set-up is completely toolless – everything from antennas to integrated StreamCaster MANET radios just snap-fits into place, while still being secure, and able to accommodate all different kinds of mast poles,” Carraway said. “A modular solution, each sector provides up to 90° to 120° of coverage, making it easy to connect three in an array to get up to 360° coverage, with L-band, S-band and C-band systems available.”
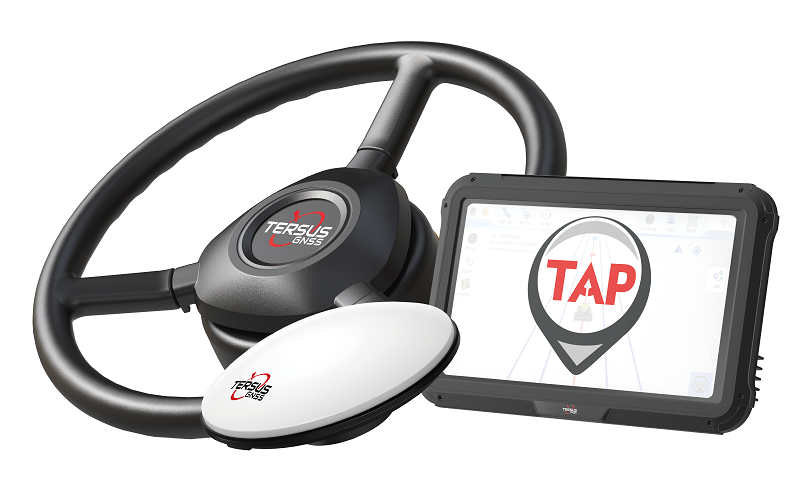
Tersus GNSS exhibited its new BX50 GNSS Boards for integration and its AG992 auto-steering system, which has been developed with automating precision agriculture, particularly tractors, in mind.
“We released them just this year, not long after releasing our TAP service at the end of last year,” said Nick Zhu at Tersus.
“TAP is Tersus’ own PPP [Precise Point Positioning] service that provides real-time, centimetre-level correction via satellite link. As farmers can’t install base stations for every time they need RTK-grade precision, and there can be rules or range difficulties preventing them from using such radio frequencies, PPP is a must for agricultural applications.”
The BX50 GNSS board can do RTK and PPP simultaneously and independently, which can be integrated for various applications like precision agriculture, uncrewed systems and robotics, construction and surveying. It can achieve 8 mm accuracy in RTK mode and 15 mm accuracy in PPP mode.
The AG992 system typically consists of a 152 x 62.2 mm GNSS antenna, a 281 x 181 x 42 mm control terminal and a 410 mm-diameter electric steering wheel. Overall, the system conventionally achieves auto-steering accurate to within 2.5 cm, with a three-minute convergence time.
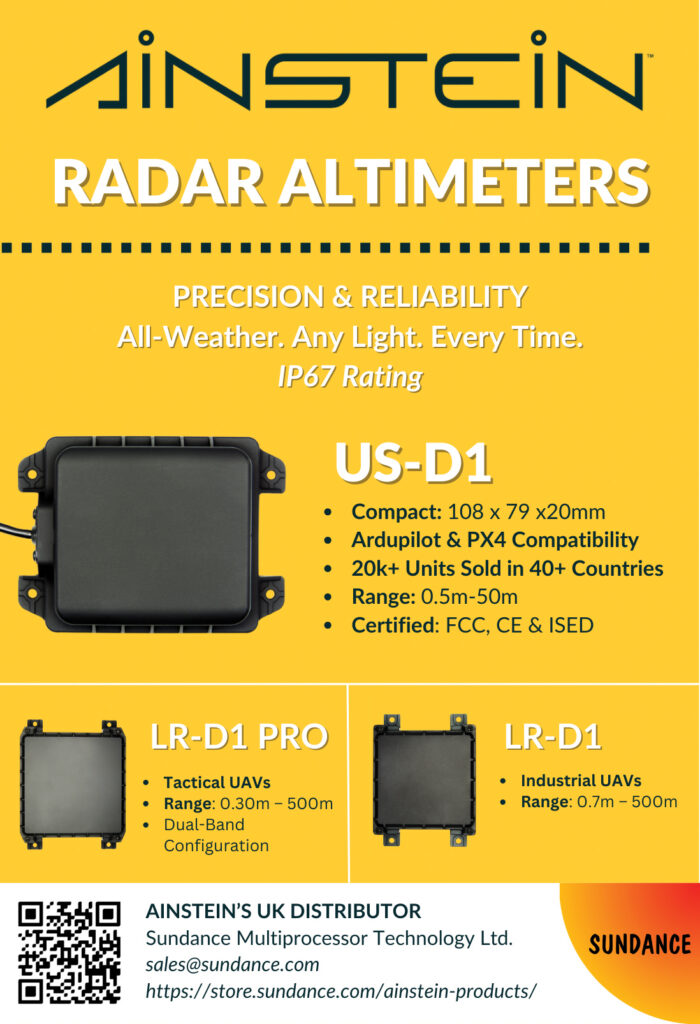
Plettenberg spoke with us about its new Nova X-Series electric motor, which was developed following discussions with its customer, Dufour Aerospace (covered in Issue 52), on some specific qualities needed in its Aero2 UAV’s tail motor.
“Dufour are very serious about making their Aero2 certifiable, and the tail motor is safety critical, so they needed redundancy in it to validate its safety for aviation authorities one day,” said Bastian Greiner of Plettenberg.
“To provide what they needed, we took inspiration from past e-motor designs with multiple winding segments, and so added three different winding segments into one of our Nova 15-Series designs.”
Each winding segment is powered by a completely different, independent ESC, so that if one should fail, the other two continue running and powering the motor to enable an emergency landing. The design was developed into the Nova X-Series (X signifying multiple winding segments), although it can be adapted and applied to other Plettenberg motor designs for customers hoping to certify their UAVs.
“It’s not a cheap solution, but compared to a coaxial motor set-up, as the route most taken towards motor redundancy, it saves quite a bit of weight, as well as saving on an additional propeller,” Greiner added.
The company has also developed its Nova Maritime Series electric motor for USVs, UUVs and maritime UAVs (the latter still subject to corrosion when flying missions at sea with sub-optimal motors).
“Again, this is a new design, based on the Nova 15 as a template, but with all the materials replaced with seawater-proof, down to every screw, every seal, the housing, the shaft, everything, with an IP67-rating,” Greiner said.
“We’re also applying some of those technologies and lessons learned to other motors and applications, with different combinations of the waterproof parts as needed. USVs in particular are growing fast as a target segment for us for the next few years.”
UPCOMING EVENTS
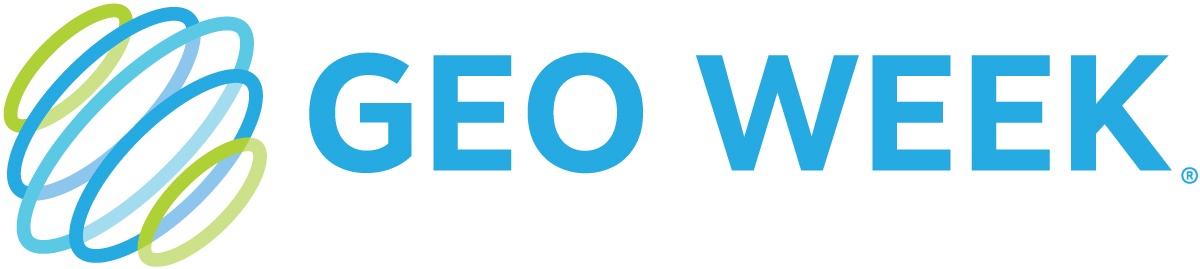
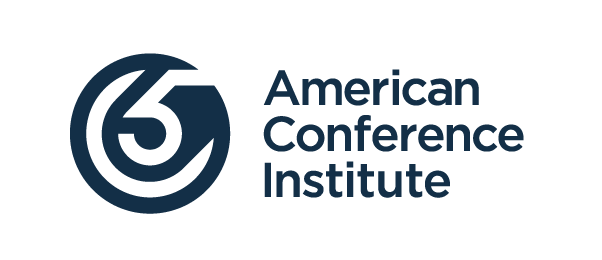
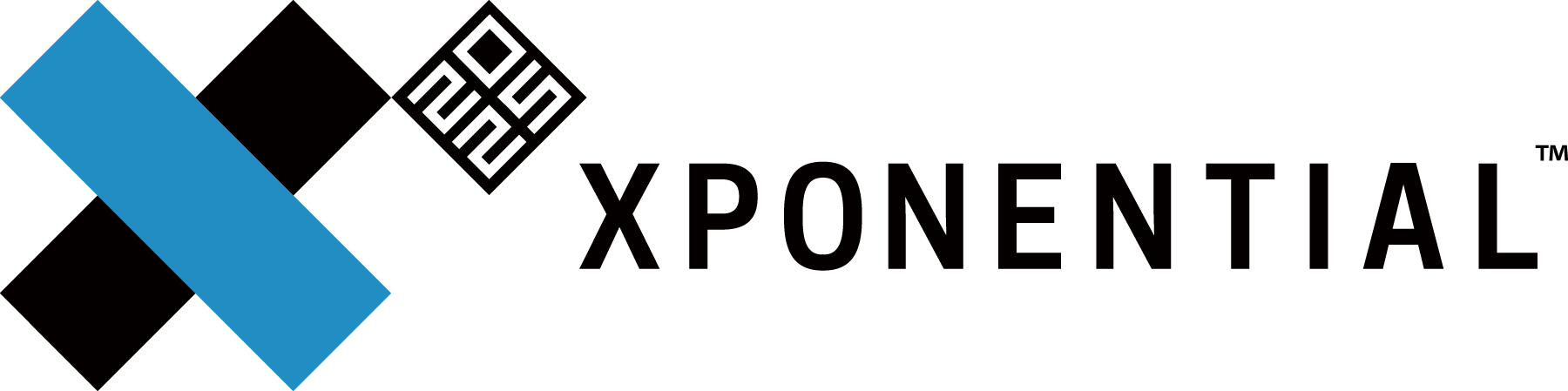
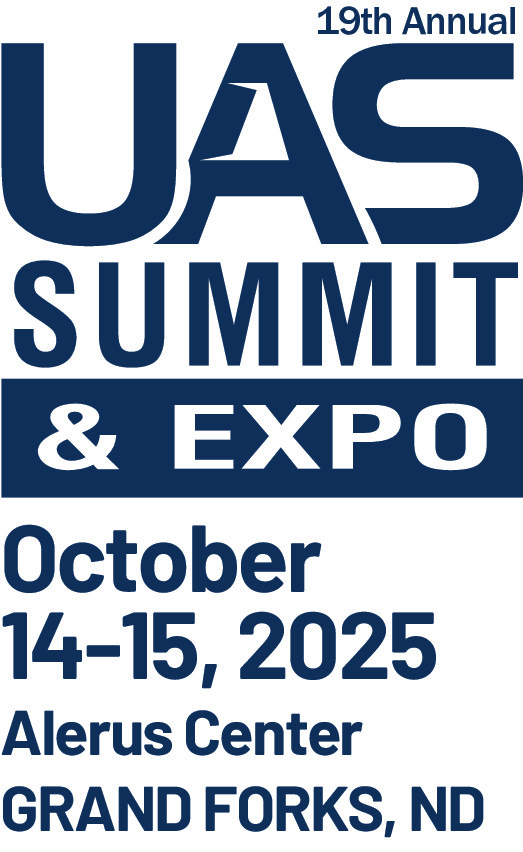
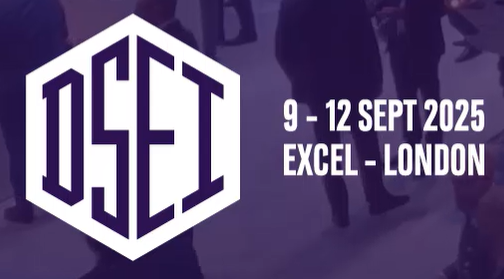
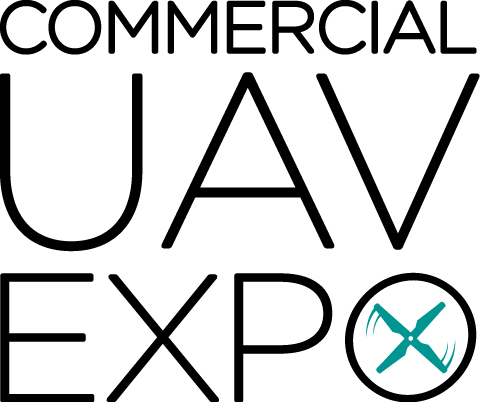
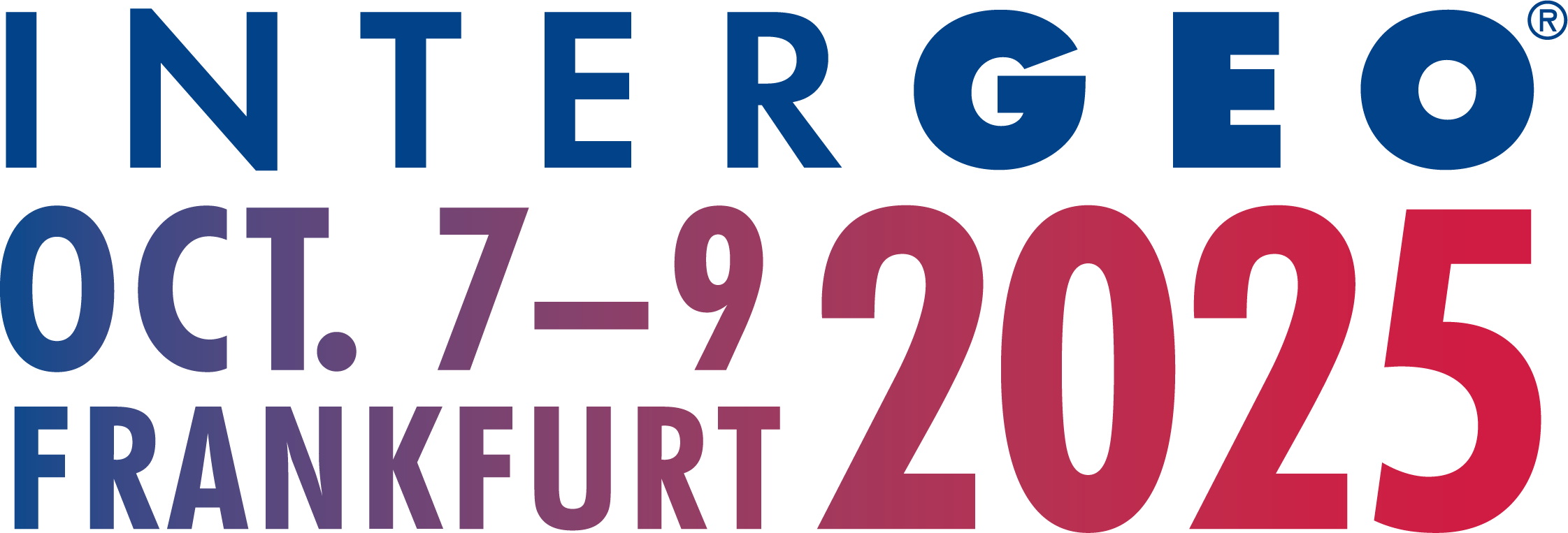
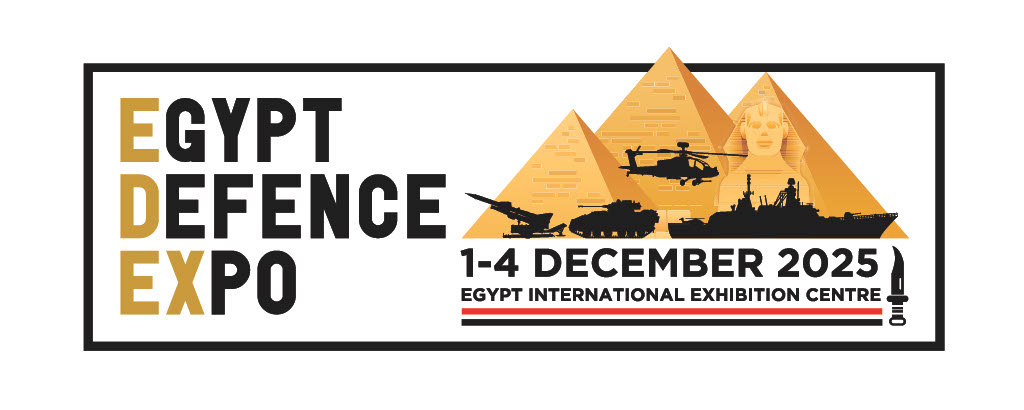
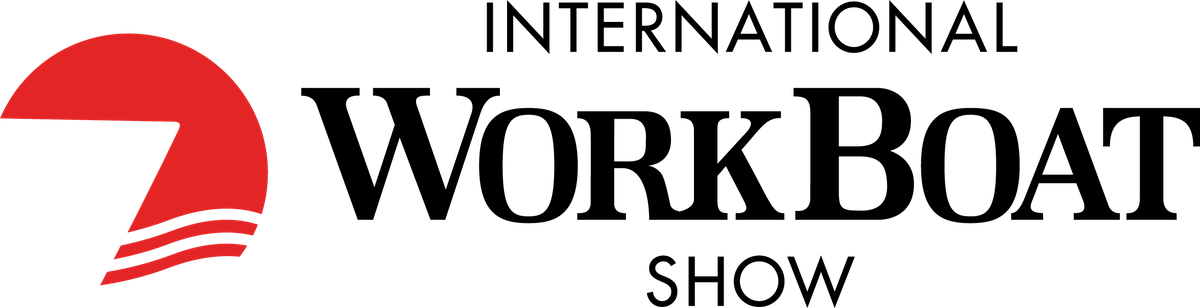
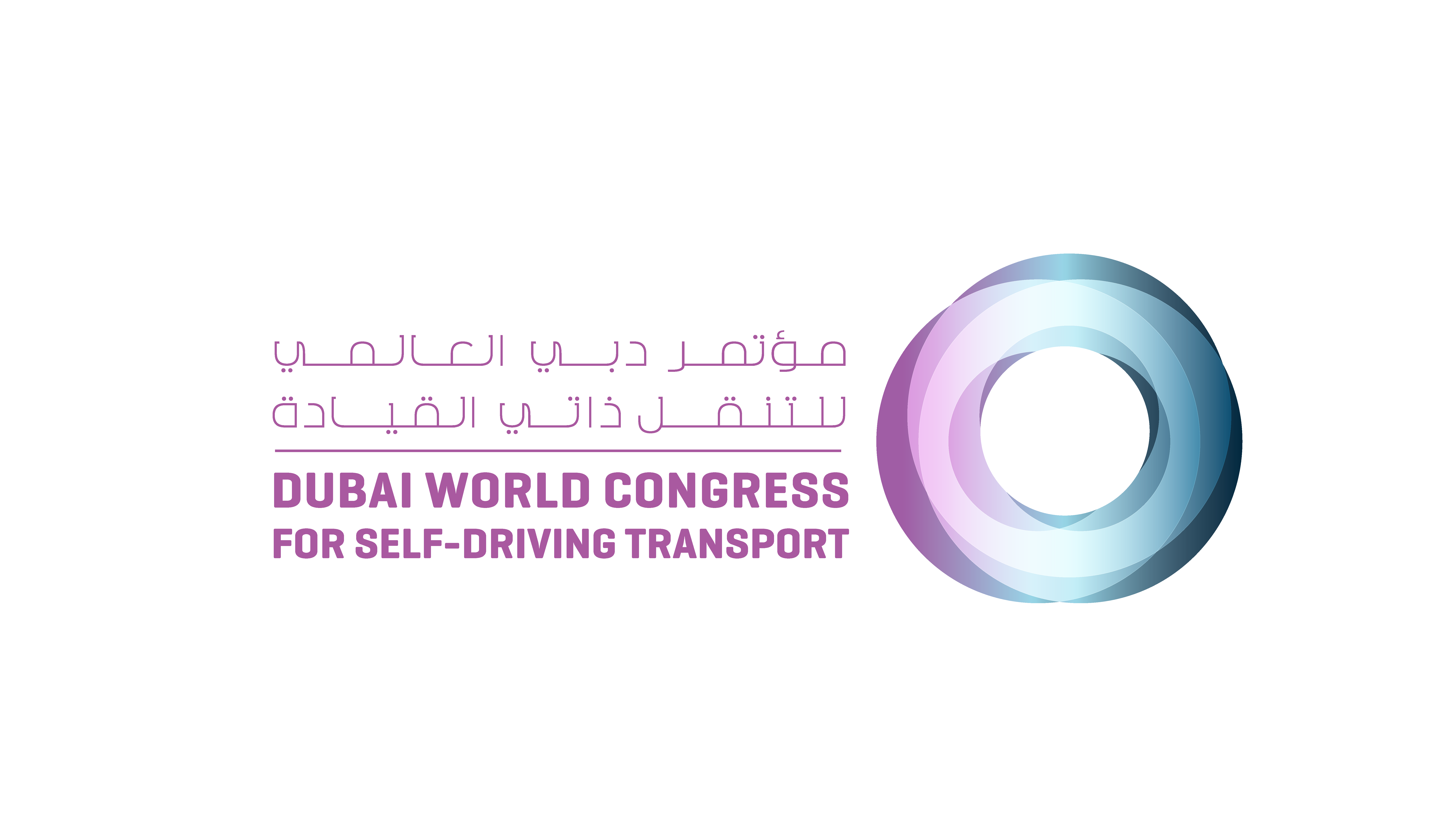
