Xponential Europe 2025 part 2
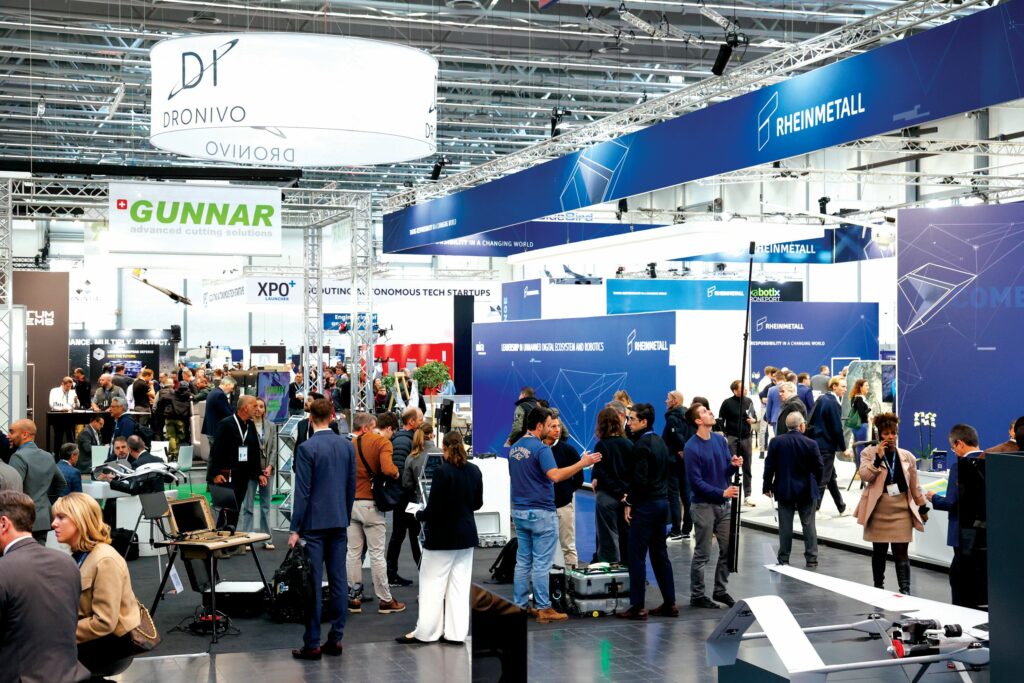
(Image courtesy of Messe Düsseldorf)
Euro vision
The 2025 Xponential Europe brought many new solutions into the spotlight. Rory Jackson presents the second instalment of our two-part post-show report on the event
Although the Association for Uncrewed Vehicle Systems International’s first European Xponential show was a long time in the making – and represented a risky venture – all parties are now in full agreement that producing a European show was well worth the effort.
The two hundred companies spread throughout the Messe Düsseldorf’s Hall 1 found themselves courting thousands of attendees from industry, government and beyond, all of whom had specific applications, products and specifications in mind and were on the hunt for partnership deals to sign.
In turn, those companies made use of the great European platform that the exhibition and conference provided, unveiling scores of new products across aircraft, avionics, propulsion, sensing, connectivity and more.
With so much happening at the show, this issue features the second instalment of our two-part report on Xponential Europe 2025 to finish detailing the most eye-catching innovations on show around the hall.
C-Astral Aerospace unveiled its SQA2, the next generation update of its SQA UAV series, which brings a raft of upgrades aimed at improving its end-user value.
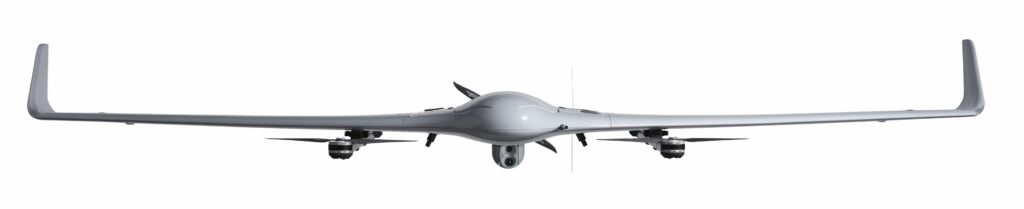
“For one, we’ve integrated a new battery with higher gravimetric energy density; that makes it more energy efficient and lighter, saving weight for the new aircraft and improving its endurance to a figure of up to three hours,” said Rok Tomazic of C-Astral.
“We’ve also changed the pusher propeller at the back; it used to be a two-bladed prop, but now we have three blades, which gives us better propulsive efficiency and also makes the UAV fly more silently.”
Forward along the underside, the SQA2 now features a belly mounted 360° rotation gimbal camera because the company found that this approach makes continuous target tracking (with unbroken LOS contact) easier than with the former nose-mounted gimbal configuration.
The gimbal on display was a REX 100 Mini MkII from C-Astral’s fellow Slovenian tech company AtmoLab. It features a high-resolution electro-optical and infrared camera system and offers 360° continuous rotation. The gimbal in question, and other gimbals from AtmoLab, will be added to the existing family of C-Astral gimbals to ensure increased resilience of C-Astral’s supply chains.
“We’re also integrating new payloads that are generating a lot of interest, like for instance the YellowScan Surveyor Ultra Lidar, which we’ve successfully mounted on the SQA and flown for LIFT Forest, an EU forest management project,” Tomazic said.
“With Lidar, we successfully measured wood mass changes by comparing point clouds in post-processing software, meaning they didn’t have to be measured manually, as would be the conventional, more time-consuming and laborious way.”
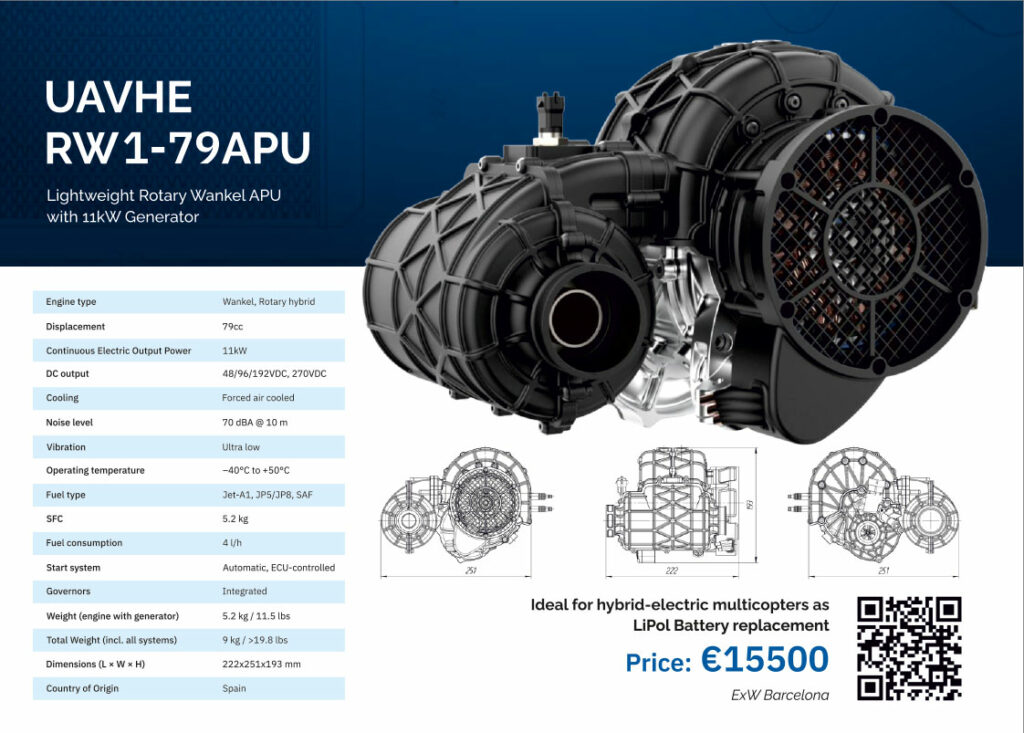
Vodafone showcased a wide range of technologies across uncrewed and robotics systems, including an augmented reality (AR) solution for training new UAV operators in both remote control of drones and in-the-loop monitoring of autonomous operations.
As Vodafone’s Maja Michaelis told us, “Our Virtual Gesture Drone solution creates a virtual drone, and a virtual course to fly it through, visible through an AR headset. We’re using a PICO 4 Ultra from ByteDance, which has a ‘pass-through’ mode enabling people to see the virtual objects as well as actual reality around them, such as people and the local environment.”
The headset and Vodafone’s software enable users to interact with AR menus and planning wizards using their own hands (rather than gloves or a controller). The software also allows users to remotely control the virtual UAV in flight with hand gestures, including movements along all three axes, and rotations.
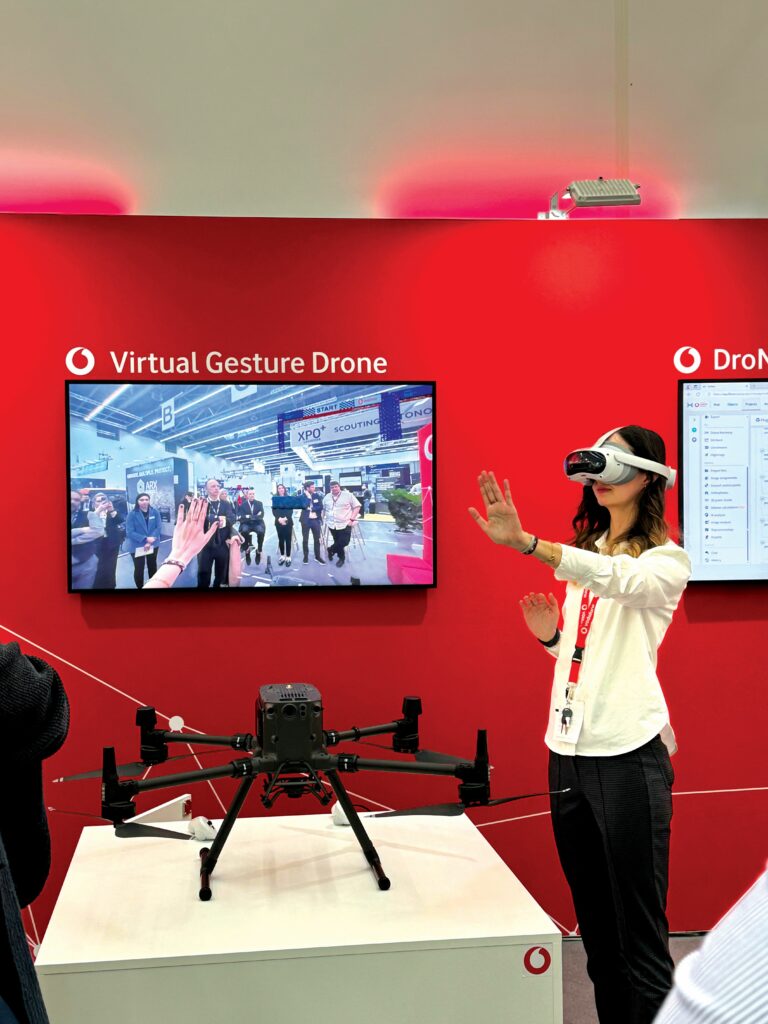
Development of the system took three months and was based on a previously completed master’s thesis by Vodafone and Mohamed Azzahhafi, titled ‘Development of a Mobile Network-Enabled Control Platform for a Quadcopter via a Mixed Reality Headset for Immersive Flight Training’, in which control software was designed to enable a physical UAV to be controlled remotely via a HoloLens that optically registers hand gestures.
“But the Virtual Gesture Drone can also be used with a hand controller, such as a gaming controller, a computer, or a tablet with buttons and joysticks, depending on what their use-case requires familiarity with,” Michaelis added.
EU Motors is a Poland-based company that is working to produce ranges of electric motors, not only with competitive or superior quality to those available elsewhere on the market, but also made entirely with components and raw materials sourced within Europe.
As Michael Berger of EU Motors told us, “One hundred per cent of our processes are based in Europe; there are motor manufacturers elsewhere in Europe, but it’s very common that they buy their stator cores already wound from Asia, with just the final assembly happening in their European factories.
“Our entire design and production chain is in Europe. We went this route precisely because we were surprised at how low the resulting costs were to do everything in Poland. We actually saved considerable costs versus shipping from, say, China, and outsourcing manpower or land costs to there, and we adhere closely to European standards on things like hazardous materials and labour conditions which aren’t always standardised globally.”
Among the products on display were EU Motors’ 35-series motors, designed as 35 mm diameter devices that produce approximately 7–8 kg of thrust in standard operations, or up to 10 kg peak. Berger notes that a quadrotor with four such motors and a decent battery could be capable of carrying 20 kg payloads over significant distances.
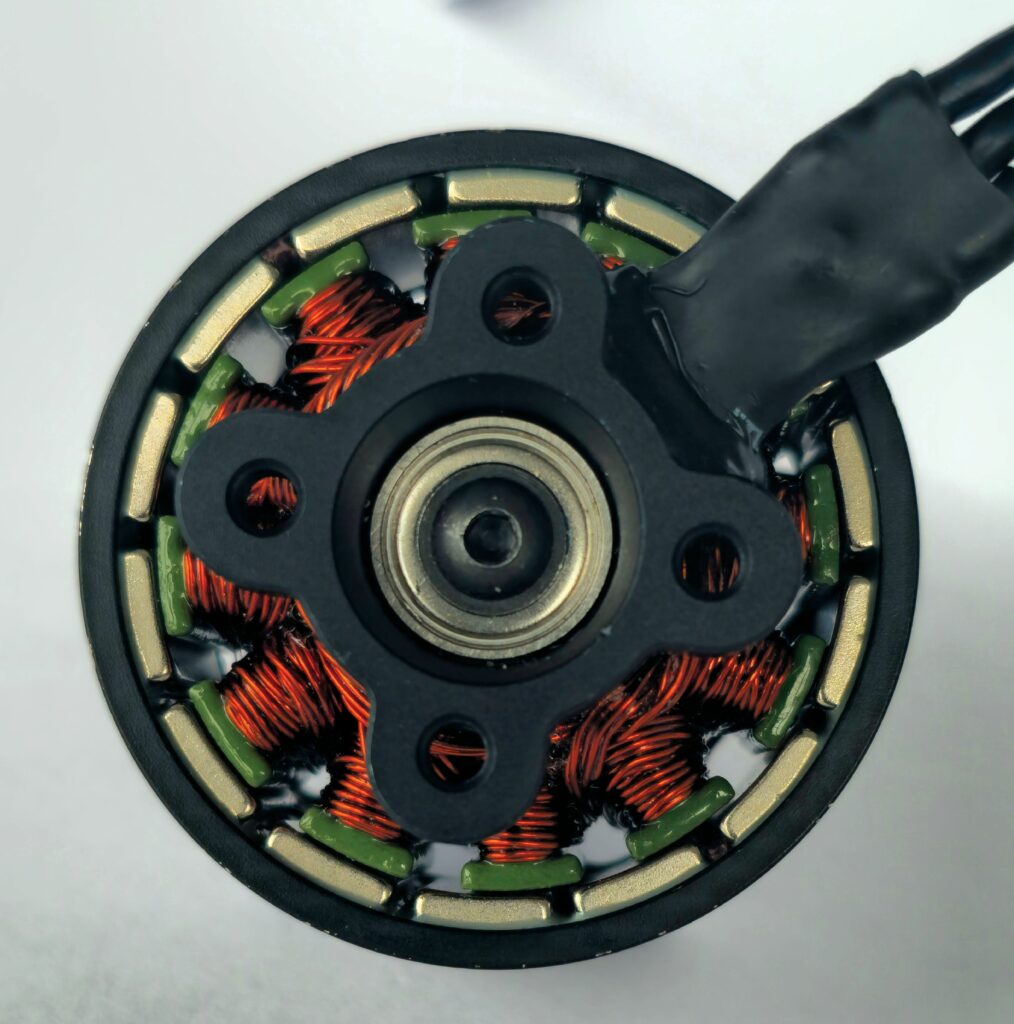
“And one of our most popular products is our 3115, which generates 4–5 kg of thrust, and we also manufacture a range of 28 mm diameter, 3 kg thrust motors, and 15 mm diameter motors for very small, civilian-type photography drones,” Berger says. “We can achieve very high thrust in small packages, making them very efficient versus both weight and price.”
The company has initially sought to match the quality and ranges of existing UAV electric motor companies, orienting its distributed and concentrated windings based on established methods and standards, and using N52 neodymium magnets (the strongest commercially available type of permanent magnet).
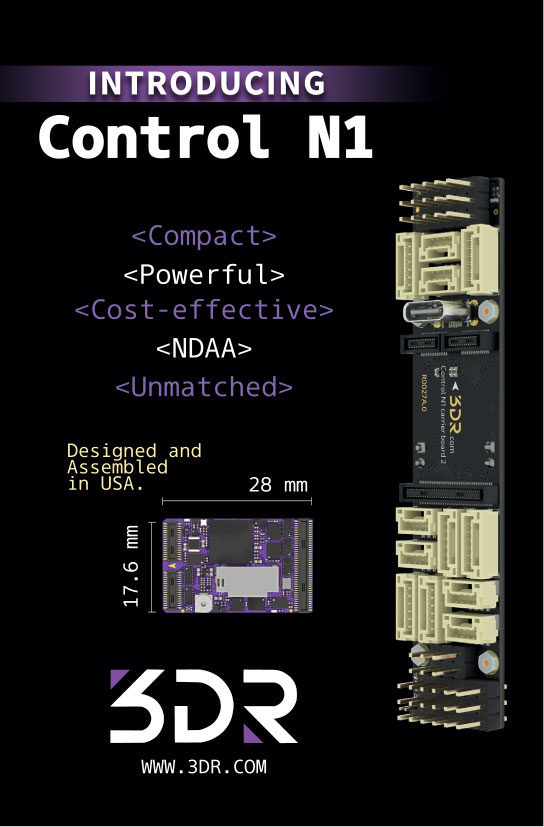
“But we’re also investing a lot in new motor designs and technologies, researching into manufacturable Halbach array designs, dual-flux motor designs for smaller UAVs, and more which could bring much, much more power into small packages,” Berger added.
“Going forwards, we’re also naturally going to strive more and more to use certified, trusted European suppliers, and not cut corners like a lot of e-motor manufacturers sadly do.”
Vixos came to the show from Denmark to exhibit its ‘Beyond’ flight termination system, originally developed as part of UAV r&d at Aalborg University’s robotics department, but now commercialised and manufactured as a certification-critical avionics solution.
“European regulations strictly require containment functionalities for every UAV weighing more than 25 kg, and the best way to achieve that containment is by using a dedicated solution for safely ending or terminating the flight,” said Anders la Cour-Harbo at Vixos.
“Much like autopilots and cameras, making your own flight termination system tends to cause problems due to insufficient specialisation in the necessary hardware and software. For instance, it’s very easy to accidentally trigger termination due to a false positive in your control software, or a data link failure can mean it fails to trigger at a critical moment upon a remote request or confirmation, with the UAV then potentially causing major accidents either way.”
All Beyond units are designed as standard with an Iridium satcom radio to enable unlimited range and persistent connectivity, with significant years of r&d going into integration of the Iridium system, both mechanically into a small, durable enclosure, and electronically as part of the Beyond avionics package.
Each unit consists of two modules: a Beyond 12 that integrates with the customer’s UAV – working with their choice of satellite antenna – and a handheld Beyond base device. The latter features an array of buttons corresponding to different signals sent via Iridium to terminate the flight.
That flight termination can take whichever form(s) the customer prefers to select in their system. For example, they might choose to cut the engine in a fuel-powered system, or to set aileron servos to a gliding position for controlled descent of a fixed-wing aircraft, or to switch to autorotation in a helicopter UAV.
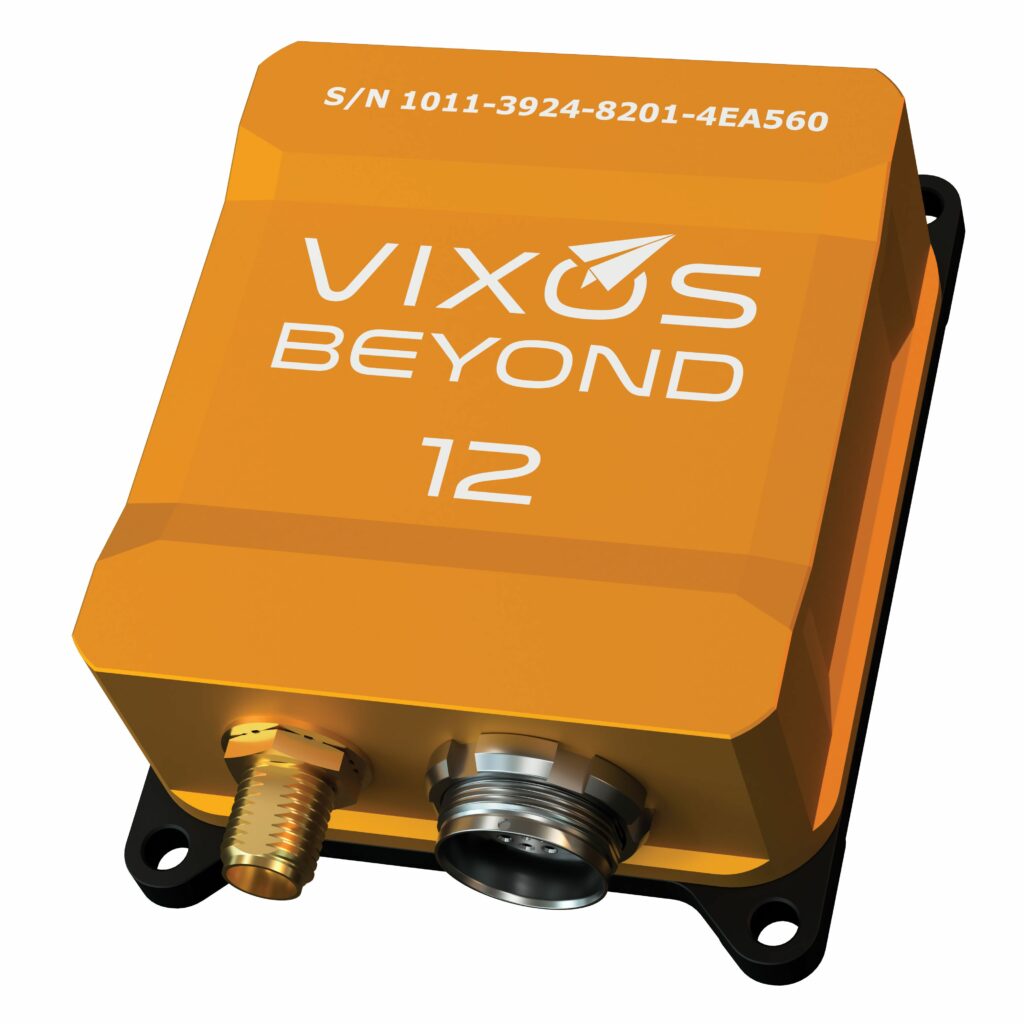
“Our system is programmable for many different kinds of termination; naturally this also means options like launching a safety parachute or flashing warning lights are also currently available, and can be timed to activate as secondary events at specified time intervals after a primary termination event like cutting engine or rotor power,” la Cour-Harbo added.
Aerial Precision BV has developed a time-efficient Lidar solution for cost-effective, on-site 3D Lidar mapping. It combines a proprietary Lidar sensor with a specialised iPad-based software stack.
As the company’s Vicente Payo Ollero explained, “We founded Aerial Precision five years ago to bring down the cost of industrial Lidar mapping to levels comparable with photogrammetry. Lidar has always been associated with high costs and complexity. Today, we offer Lidar sensors that can be mounted on any UAV, with data processed on an iPad immediately after landing.”
As a result of Aerial Precision’s software optimisations, 20 minutes’ worth of Lidar mapping data can be processed in under 10 minutes directly in the field. This enables users to land, process and redeploy their UAVs quickly throughout the day, significantly increasing area coverage and efficiency during fieldwork.
“Lidar is often seen as difficult and time-consuming. We’ve simplified the process so much that it only takes three taps on your iPad to process the data after landing. That includes Lidar and PPK-GNSS post-processing, all computed at the edge, entirely on site, with no need for wi-fi, cellular service, or cloud connectivity,” Payo Ollero said.
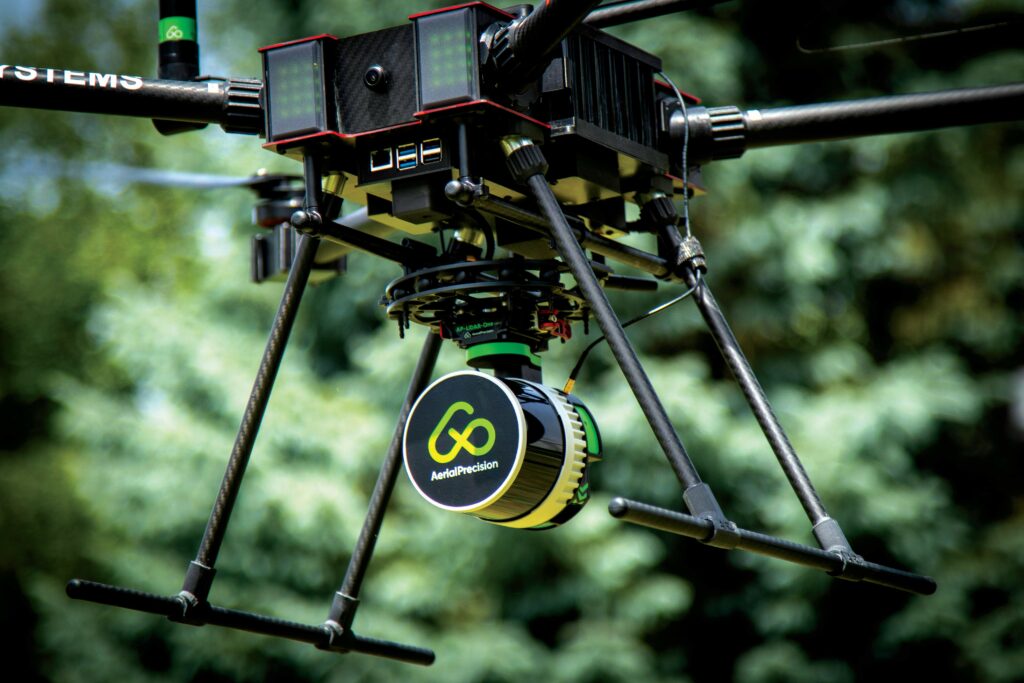
In addition to its software, Aerial Precision has also developed two Lidar products, after finding that no existing products met its hardware requirements for achieving fast, accessible 3D mapping in the field.
One is the AP-LiDAR-One GEN II, a 32-channel sensor weighing 650 g, offering 3 cm accuracy and a range of up to 300 m. The other is the AP-LiDAR-M GEN II, designed as a more affordable, entry-level model with six channels, 5 cm accuracy, and a range of up to 450 m and weighing 690 g.
Both systems connect via USB-C, support triple returns per laser pulse, and are compatible with multi-frequency GNSS receivers. They also integrate seamlessly with RGB, thermal and multispectral cameras for advanced precision and colourisation.
We previously featured UAVHE’s Wankel rotary hybrid engines in Issue 55 (Apr/May 2024), and the Spain-based powertrain manufacturer was walking the aisles of the event to discuss some extensive updates it has made to its engine products since then, based on feedback from customers.
“Our most-produced engine, the RW1-79, is in its second generation, with updated materials, coatings, software and controllers, and we’ve also made a lot of improvements to our internal processes to speed up engine production considerably, which have enabled us to supply more than 200 engines since the start of 2025,” said Andre Bogdanov of UAVHE.
Among the physical changes to the 79 cc RW1-79 are the use of a higher-quality diamond-like coating at the apex slots of its rotor, which was made possible by UAVHE updating its coating machinery, processes and rooms. Those updates have also made the coating processes less time-consuming.
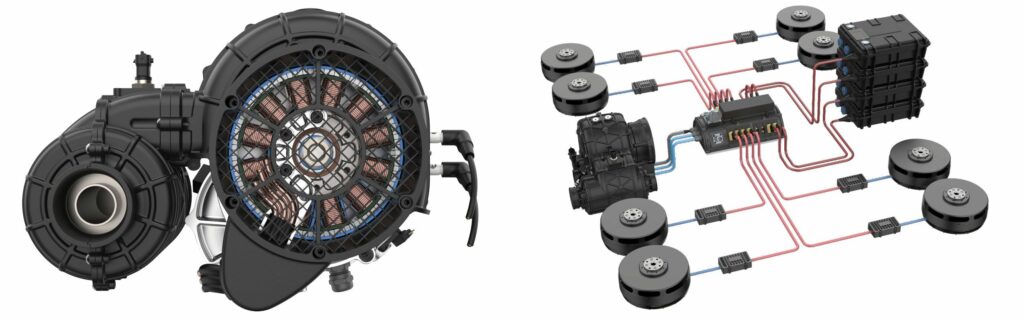
Software changes include improvements to the engine control and power management loops, including wider tracking of performance and health statistics across the powertrains. The UI has also been updated to make the engine software accessible via a web browser, making it easier for users to remotely monitor and update their software from various devices.
“Additionally, engines that our customers send back to us for servicing and overhauls are being upgraded with new plastic covers, injectors, connectors and other seals, which are especially useful for expanding the range of temperatures and harsh environments that our engines can perform consistently and safely in,” Bogdanov noted.
The team from Hobbywing UAV attended the event with a vast array of products on display, including its P50M, which is among the largest of its solutions.
The P50M is a combo propulsion solution, integrating the company’s 15635 motor, its 80 A FOC ESC and either a 54 in or 64 in propeller, which has been designed as a propulsion system for high-voltage demands of up to 400 V.
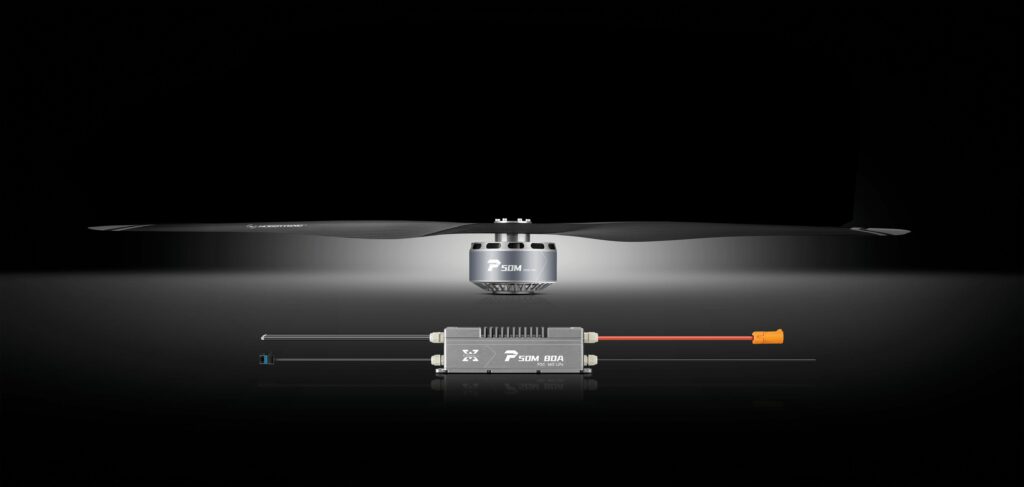
It has been constructed with fully isolated high-voltage power circuits, low-voltage signal circuits and protective earthing. Such design qualities are aimed at ensuring the safety of both personnel and UAV systems, as well as securing the reliability of data transmissions during operations.
“It provides a maximum thrust of 104 kg per rotor; we recommend using multiple P50M units in multi-rotor configurations, where the UAV manufacturer or operator runs each motor at 50 kg of rated thrust,” said Dunkan Bossion of Hobbywing’s European division.
“It is especially suited to industrial drones performing operations such as firefighting, emergency response, and both onshore and offshore logistics, even in missions such as lifting materials to oil rigs, where they need to fly very long while carrying large payloads as heavy as 100 kg.”
T-Global Technology displayed a range of its newest passive thermal management solutions, including its main product lines of silicone thermal pads, as well as more advanced solutions such as vapour chambers.
“Some of our high-end thermal pads have top-end thermal conductivities of 16–17 W/m.k,” explained Edward Benson from T-Global.
“The ‘holy grail’ target when developing great thermal pads is a soft material with high thermal conductivity, but unfortunately the two properties are somewhat mutually exclusive. Thermal conductivity typically comes from thermally-conductive ceramic particles – boron nitride, aluminium oxides, and similar sorts of things – but the more of these fillers we load into a pad, the harder it becomes.
“So, a lot of our success comes from r&d into silicone chemistries, maintaining a soft matrix even with lots of ceramic filler particles, and understanding how those particles interact with each other in the mixture, depending on their sizes, shapes, thermal properties and so on. Getting it right means hitting those high thermal conductivity measurements while staying soft enough to adhere to and work with different objects’ surfaces.”
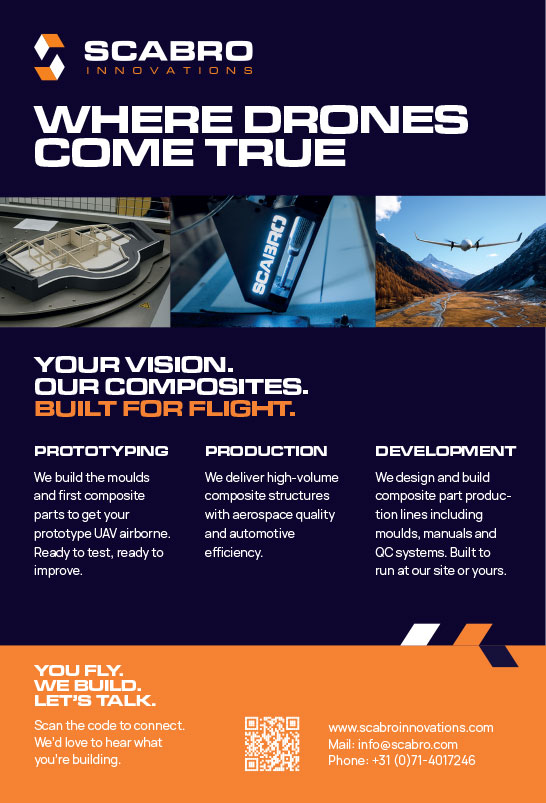
Those objects can include high-power batteries, motor controllers, electronics modules and engine firewalls. The company makes a range of thermal pads, from lower-end lower-priced units to a higher-end solution such as that described above, with the lower-end materials typically getting applied via continuous extrusion machines, and the higher-end ones made in silicone hot presses to balkanise the silicone particles under high pressure and temperature (to manage the high filler loading properties).
The vapour chambers, meanwhile, are a new and upcoming product intended for chips and electronics with increasingly high power densities. They consist of sealed, packet-like units filled with distilled water as a fluid coolant, which can achieve rapid heat transfer from narrow, concentrated spots across wide areas.
“Vapour chambers work a lot like heat pipes; a heat source on one side of the vapour chamber evaporates the distilled water inside, which then migrates to the opposite, cold surface of the chamber where it condenses back into water,” Benson said.
This phase change process – from liquid to gas and then back to liquid – transports considerable heat, with the thermal energy being distributed and dissipated across the chamber via a form of capillary routing actions. That routing is achieved via a sintered copper and wick structure inside each vapour chamber that holds and ferries the water throughout.
“All-in-all, it’s a simple and reliable technological concept, but very difficult to manufacture. Sealing, for instance, is very tricky with vapour chambers, and the sintering happens under something like 1000 C temperatures, so we exhaustively test every single unit we make before shipping,” Benson concluded.
“And for the most weight-sensitive UAV components, we’re exploring versions of our vapour chamber made from aluminium, and using acetone coolant to save weight versus copper and water.”
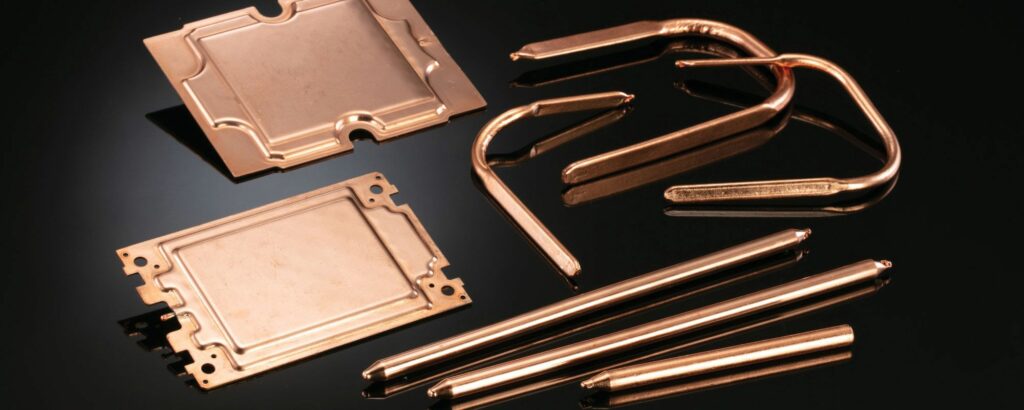
LightWare showed it’s GRF-500, a laser rangefinder capable of measurements up to 500 m away, and SWaP-optimised such that it consumes 0.6 W of power in typical operations and weighs 10.7 g.
“Designing a rangefinder for very accurate measurements at longer and longer ranges enables UAVs flying the GRF-500 to operate at higher altitudes than they previously could, which is especially important for applications where end users want to fly undetected,” said Andre Schoeman at LightWare.
The GRF-500 is particularly aimed at applications such as ISR missions on behalf of defence groups, or environmental protection missions such as tracking (recording and hence, successfully prosecuting) poachers or those involved in illegal fishing activities.
“Its small size, weight and power make it ideal for integration into space-constrained gimbals, for tracking targets and geo-pointing to report the GNSS locations and headings of those targets,” Schoeman added.
“To achieve such exceptional high range and accuracy out of such a small package, we focused a lot of r&d effort into how we do signal processing inside the unit, coupled with the advanced precision manufacturing that LightWare is known for.
“Testing and calibrating every unit in bright African sunshine atop white surfaces makes LightWare’s devices reliable across a huge range of conditions that would hamper other laser rangefinder sensors.”
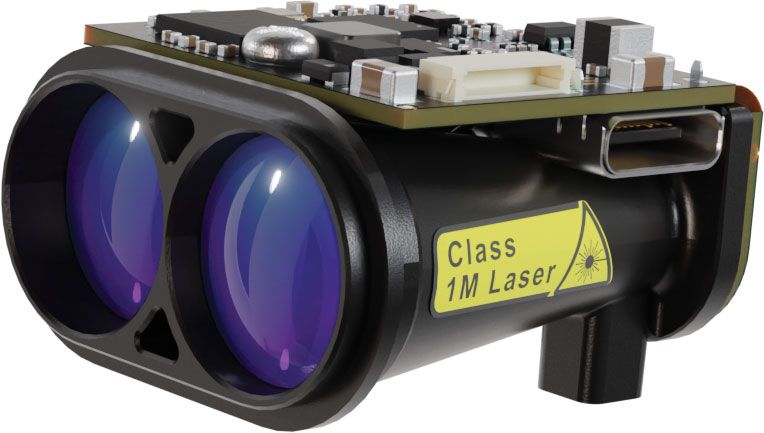
We met Avio Race walking the aisles of the show, having travelled from Italy to showcase its latest motor sport connectivity products, among which were the new Size 1 data connectors from Souriau. This product line has been developed to create the smallest connectors possible, so that they can fit into extremely tight spaces around the bodies and chassis of racing cars.
As Lidio Patrizio from Avio Race told us, “They were made to fit in places like amidst the brakes of Formula One cars, where it’s very narrow, there’s many other connectors, a lot of heat and severe vibration to endure, and there’s a very strict need to save weight too.
“Being designed to handle all these qualities makes the Size 1 connector family ideal for UAVs. Its lightness leaves more weight for payload capacity, and the units can work in tight spaces with very harsh environments like gimbal housings or engine shrouds. So, we’re transferring the tech from high-end motorsport to high-end uncrewed aviation.”
In addition to being able to supply the new Souriau connectors in Mil-Spec compliant configurations, the company also discussed its new, highly SWaP-optimised miniature pressure sensors, which are developed internally and available in a wide and flexible range of calibrations that enable them to gauge fuel pressure, oil pressure and other fluid pressure parameters.
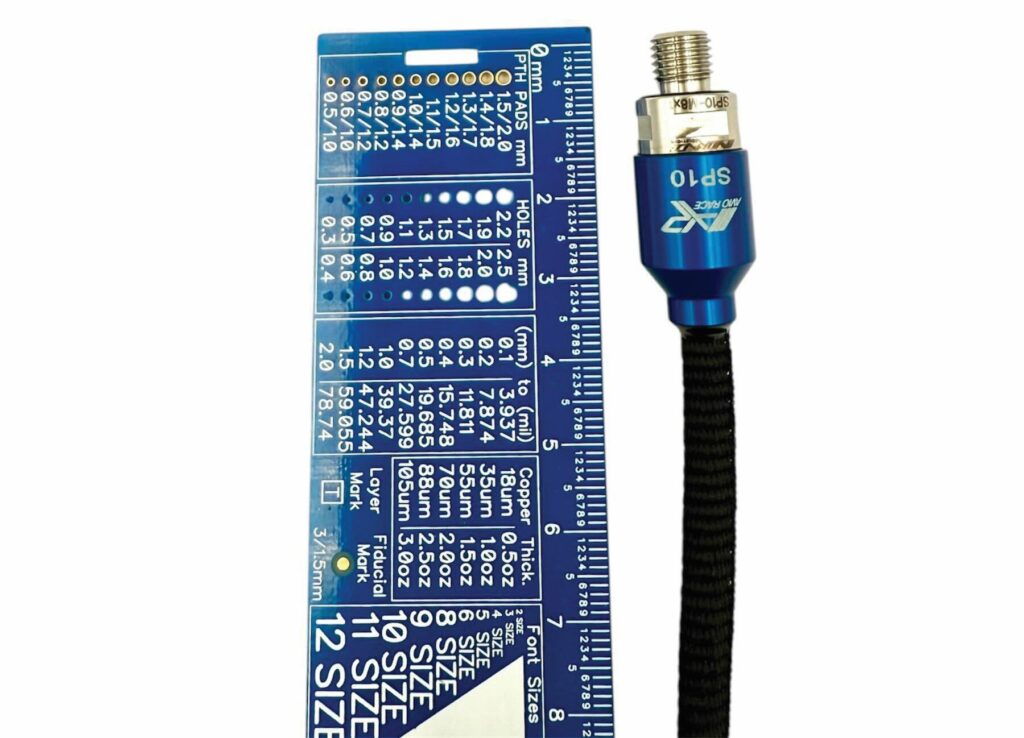
“These pressure sensors are very compact, and have to be reliable, because we’ve developed and integrated them first in MotoGP, as well as LMH, LMDh WEC and IMSA Hypercar competitions. On top of that, most of the NASCAR and IndyCar teams are using our pressure sensors on their engines and chassis, and a reliability issue in any of those means disaster, so we believe it would fit for serious UAV applications also,” Patrizio added.
Linden Photonics, a manufacturer of fibre optic tethers, attended the event to exhibit its latest solutions for buoyant, strong cable-based data links for real-time monitoring and control of UUVs.
“Our fibre optic tethers can be made according to various shapes and sizes, to achieve specific strengths and buoyancies, and typically we supply to smaller, inspection-focused vehicles, which often merits a neutrally buoyant tether so that it doesn’t drag the UUV up or down,” said Stephen O’Riorden of Linden Photonics.
“We also typically supply our tethers with brightly-coloured orange or yellow jackets to ensure they can be seen by other vehicles, especially boats at the surface, so they don’t run over them or get tangled in them.”
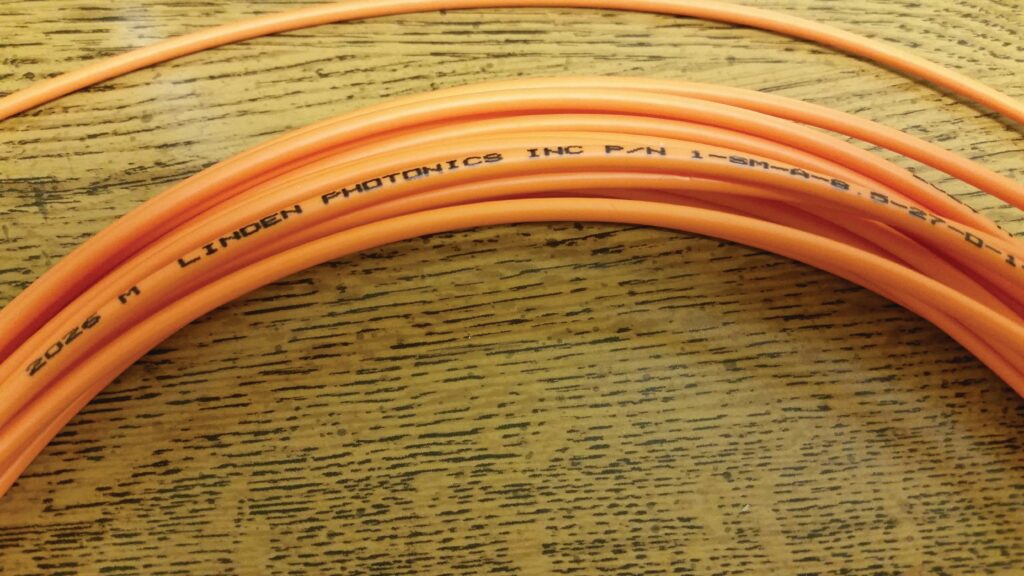
The company also showcased its fibre optic cable packs, which are designed to spool out lengths of tether over distances behind a vessel, preventing the need to install a winch with a rotary joint, or similarly expensive machinery for cable deployment.The packs can be supplied with up to 50 km of continuous tether lengths, and are typically manufactured with single-mode fibre optic cables to enable lossless data feeds of sonar and HD video over such distances (rather than copper wire links, which degrade dramatically at fractions of those distances).
“More and more customers want their autonomous underwater robots to integrate a tether, just in case they need to provide real-time data feeds or intervene during an inspection operation in real time,” O’Riorden added.
“Getting the tethers right for such applications comes down to manufacturing the tethers thin and lightweight, as well as knowing how to adjust the buoyancy. Often we use a polyurethane jacket, and introduce a foaming agent to trap very precise air quantities in the cable to achieve closely calculated buoyancy parameters, accounting for all the other elements in the product.”
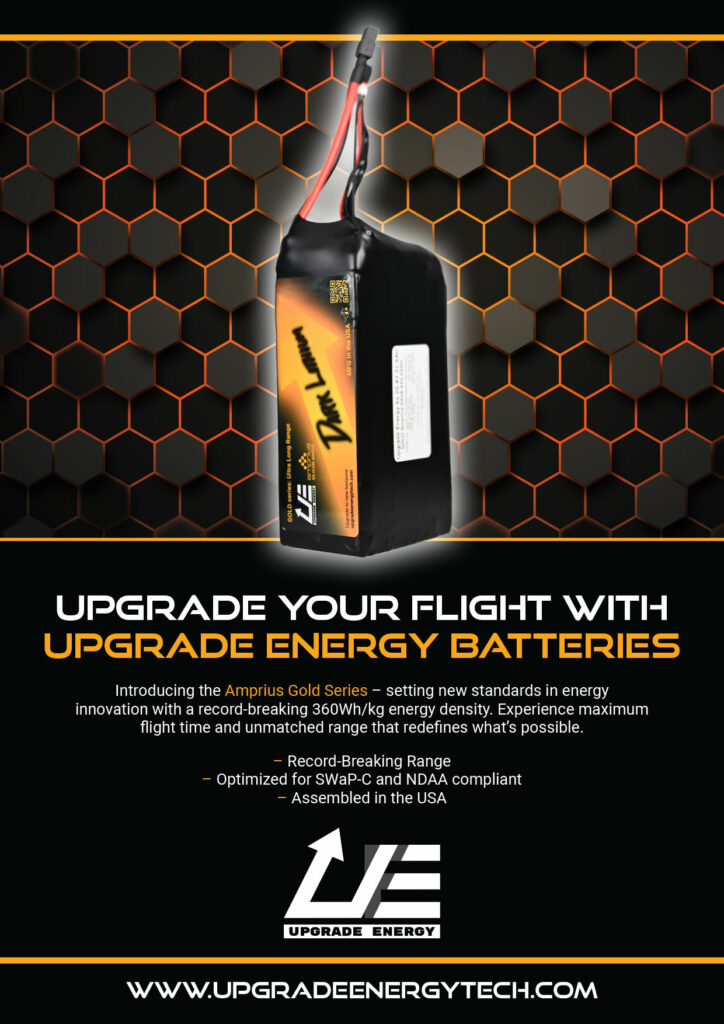
Holybro presented three new UAV navigation solutions at the show. The first was its recently-released H-RTK NEO-F9P Rover, which is an IP66-rated (waterproof) GNSS module built around the u-blox NEO-F9P receiver.
“It comes in multiple versions, enabling UART or DroneCAN compatibility, and it also comes with a high-precision RM3100 magnetometer,” said Vince Poon at Holybro.

“We’re also exhibiting our ZED-F9P Rover, which uses GNSS L1 and L2 bands, while the NEO-F9P is built for L1 and L5 bands. The former also has a slightly bigger antenna, greater weight and higher price than the NEO, partially because L2 signals are longer-proven and very robust navigation sources, but L5 is going to be improved a lot as time goes on. Both have similar enclosures and waterproofing certifications.”
Holybro also provides module versions of both products, in which the antenna comes separate from the housing, unlike the integrated rover versions. Three different antenna options are available: a vertical array patch antenna, a helical antenna and a base station antenna.
“We manufacture the vertical array patch with a dual stack design: a ceramic antenna in the middle, with a PCB array antenna covering all four sides, making it one of the best performing antennas in its small-size class,” Poon added.
The company also showed us its new H-Flow sensor, which takes optical flow and distance measurements for navigation in GNSS-insecure or -denied environments. The device combines an optical flow sensor with a time-of-flight sensor into a single module together with an IMU, enabling continued stable flight and safe navigation without GNSS at altitudes of up to 30 m from the ground.
“H-Flow’s GNSS-denied navigation performance does also depend on the qualities of light surfaces, but in testing we’ve found it performs very well at altitudes up to 20–25 m,” Poon added.
Scabro Innovations attended the exhibition to showcase its expertise in producing high-end and large-volume composite material components for uncrewed vehicle manufacturers. A key capability on display was the company’s ability to deliver cost-effective prototype parts at high speed.
“For us, rapid prototyping doesn’t necessarily mean 3D printing prototypes, although that can be a part of it,” explained Jaap Ruwaard of Scabro Innovations.
“Producing precise composite parts requires tooling, such as moulds. But prototype parts often need to be revised after their first test flight. That means the original mould might be discarded after just one use – and that’s expensive; in many cases, the cost of the mould far exceeds the cost of the part itself.
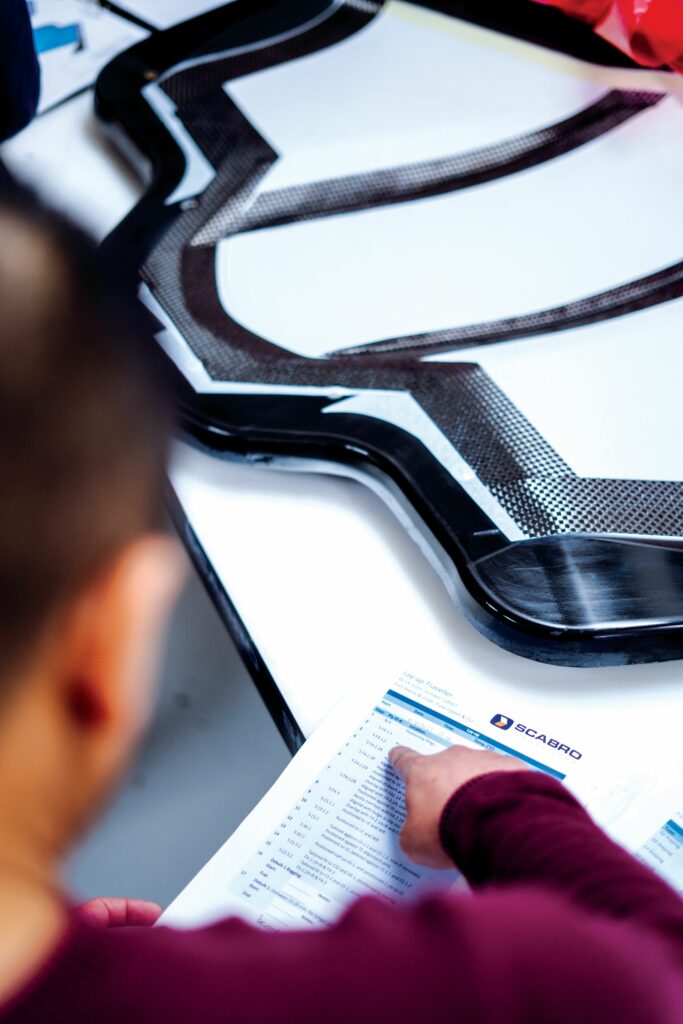
“Our background is in tooling and composites, including the resale of high-tech raw materials used to make both parts and moulds. Some materials allow a mould to be used hundreds of thousands of times; others are much cheaper and suitable for just one or two uses.
We combine materials and methods to create tooling that’s precisely matched to the expected production volume. That’s how we ensure cost-efficiency and speed where needed.”
As an example, Scabro recently produced the skin panels and nacelle for a 7 m experimental jet-powered UAV, with the understanding that only a single production run would be needed before a possible redesign following initial flight tests – which Scabro was prepared for. Similarly, another client ordered five sets of 3 m plug-and-play foldable wings for VTOL UAV prototypes, intending to revise the wing shape based on flight performance before scaling up to full production.
“It is our task to select a mould option for such customers that allows them full freedom while keeping the costs as low as possible. That’s where our tooling knowledge directly supports agile prototyping,” said Ruwaard.
Beyond UAVs, Scabro has also supported hundreds of projects since 2008 by advising on manufacturing materials and methods, learning from markets such as aerospace, foundry and thermoplastics, and from the chemistry or techniques used in processes such as rotation moulding, thermoforming and close contour casting.
Upgrade Energy, a California-based producer of battery packs, offers solutions that use high-energy-density silicon anode cells from Amprius to supply similarly high-energy-density modules and packs to companies such as HAPS developer Skydweller Aero, which uses a 153 kWh unit in its 70 m wingspan solar-powered HALE UAV.
Upgrade’s Matt Barnard was on hand to explain how his company does this. “Upon taking delivery of Amprius cells, we first sort them by quality via an ACIR test, which measures the impedance of each cell, showing its resistance and hence the potential voltage drop of each cell when under use.”
Cells that pass this early testing are then stacked into groups, shaped in rows and columns to meet the form factor requested by customers, and then laser-welded together to maintain that physical configuration. After this, they may then (depending on requirements from the end integrator) be subjected to a compression procedure to enable smooth operations at stratospheric altitudes, or integrated into a custom housing with specified sealing, active cooling and electronics.
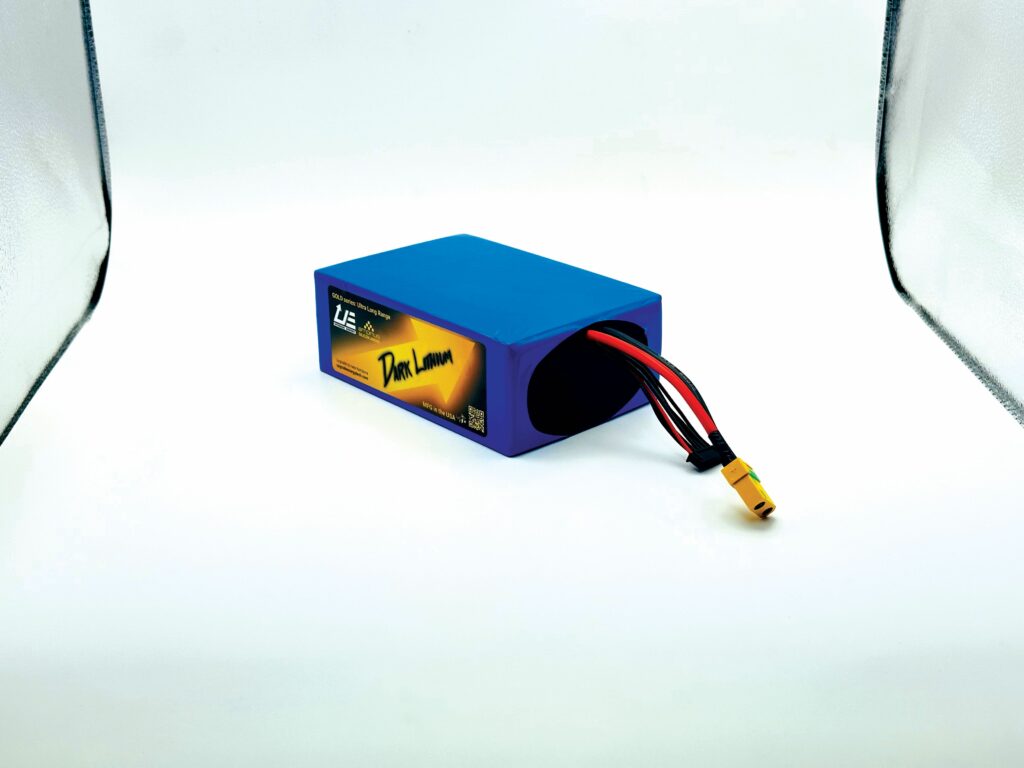
“Those enclosures will need custom software for battery management, thermal management and so on. So, we also have a team of in-house software and electrical engineers who develop control systems for our BMSs, our UIs and similar subsystems; we use TI components for consistent quality and NDAA-compliance,” Barnard added.
“Once all mechanical and hardware components are installed, the software is uploaded, and the batteries go through validation tests to ensure all operations and functionalities are in order. Then, they get encased and labelled, and go through another validation testing process under load conditions to verify operations again, with one more ACIR test also before getting packed up for delivery.
“We’re Class 9 certified, giving us relatively low costs for international shipping; for instance, we’re shipping over 5000 batteries to Ukraine for some contracts over the next five months, and we also work with a lot of drone delivery companies including Amazon Prime Air, DroneUp and Drone Express.”
CUAV Tech discussed a range of its newest avionics products with us. First was its 7-Nano flight controller, which integrates a STM32H7 processor, dual redundant IMUs and expansion interfaces, and supports Ethernet.
“We’ve also made a new airspeed sensor, our SKYE 2, which is able to communicate its telemetry over a DroneCAN bus, and also integrates an auto-heating system to maintain consistent operations in very cold temperatures,” said Lindy Liang from CUAV Tech.
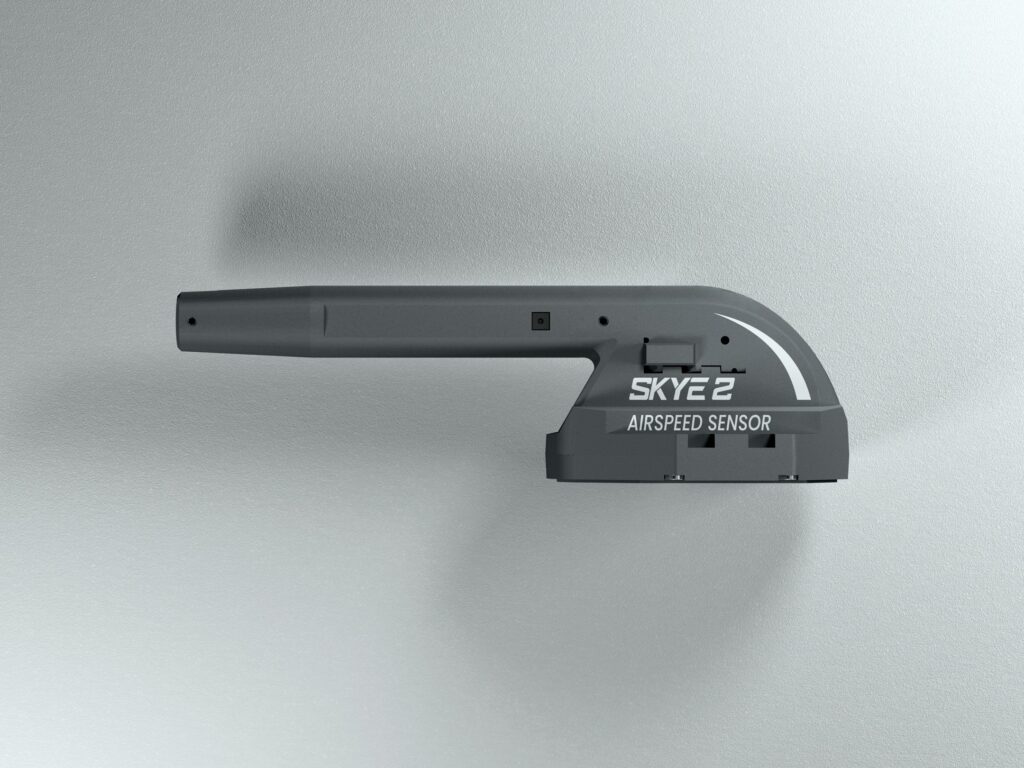
To self-heat, the SKYE 2’s pitot tube integrates a 35 W heating device, which automatically activates and configures itself according to data on the ambient air temperature and humidity conditions; hence, avoiding data errors that can occur if the pitot tube were to freeze or become blocked by rain and greatly improving the reliability of the system – and of UAV with which it is integrated.
“Also new at this show is our SKYE 2 Nano, which is built similarly to the SKYE 2, but comes without the auto-heating for users who don’t need it and prefer a smaller product,” Liang added.
Cambridge Sensoriis travelled from the UK to unveil its RadarAware product, which is a SWaP-optimised air-to-air radar system designed for obstacle detection applications onboard small UAVs.
“Our latest radar solution weighs a few hundred grams, and can detect, locate and track small UAVs in the air hundreds of metres away, and light crewed aircraft over kilometres, also compensating for the motion of its own platform while flying to maintain accurate object tracking,” said Dr. Steve Clark of Cambridge Sensoriis.
“Radar is a great long-range, all-weather sensor; Lidar, cameras and other optical sensors can be hampered by nighttime conditions, or by fog and battlefield smoke. For applications where reliably seeing a small object far away – in both night and day – is important, and where you need to be able to consistently measure its range for effective avoidance; radar has the advantage.”
The company’s r&d has focused particularly on reducing the size and price of its radar to suit small UAS budgets. It has also pared down the new product’s power consumption to 15 W (on a 12 V DC input) in typical operations.
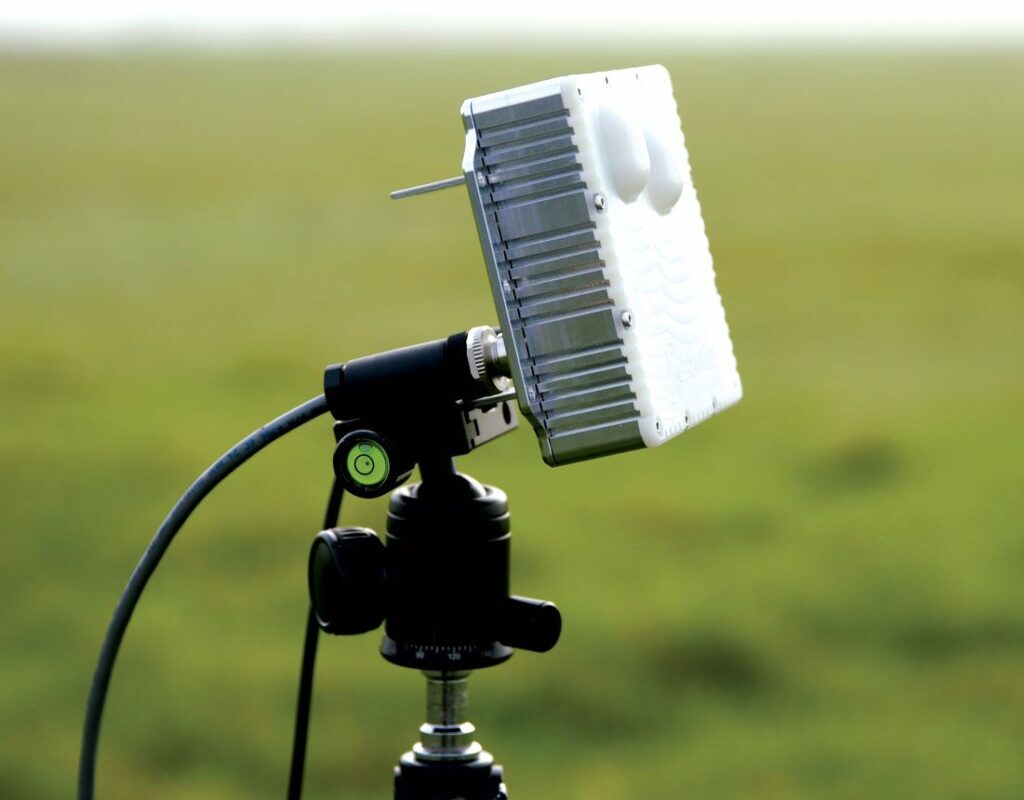
UPCOMING EVENTS
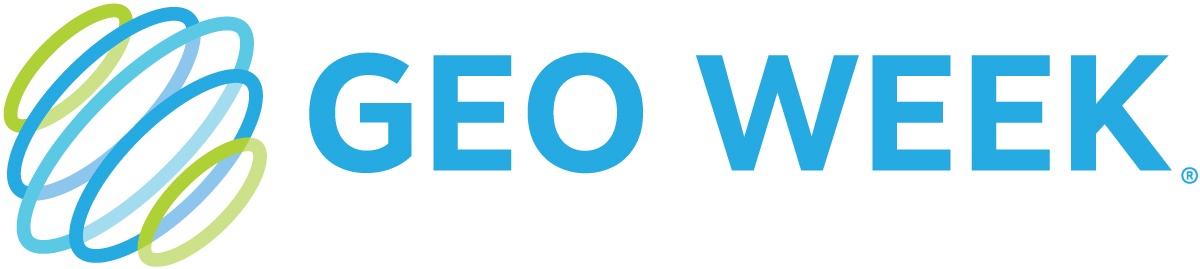
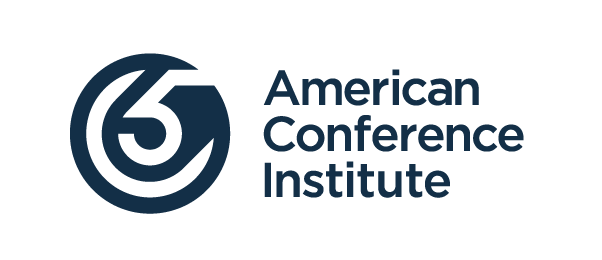
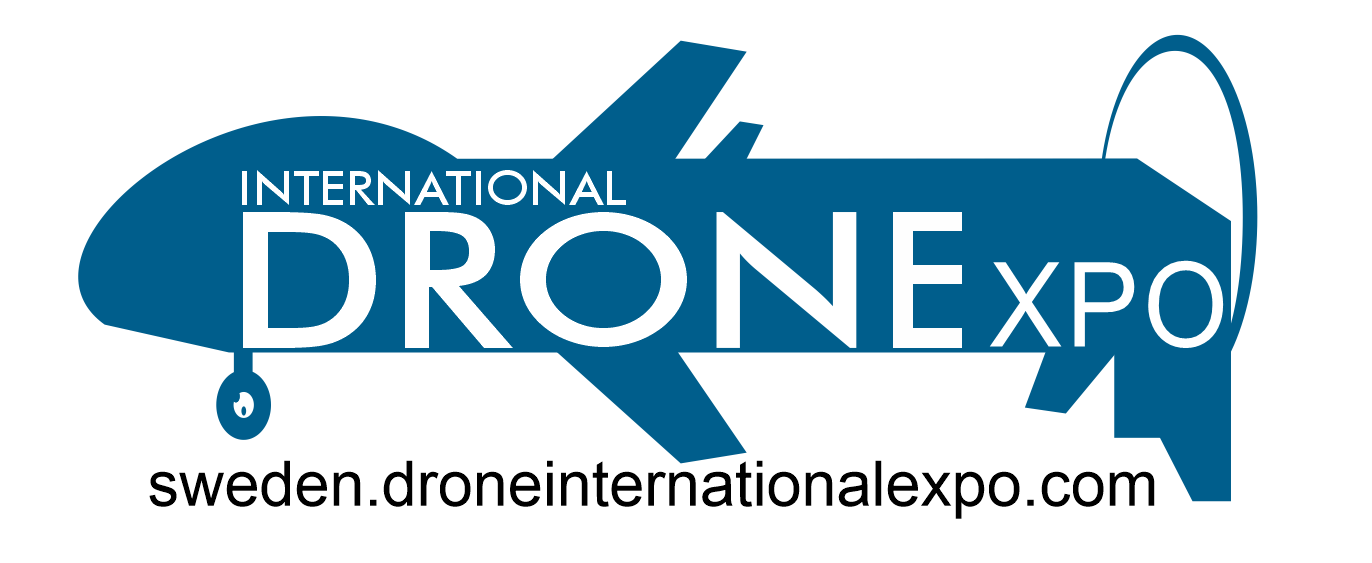
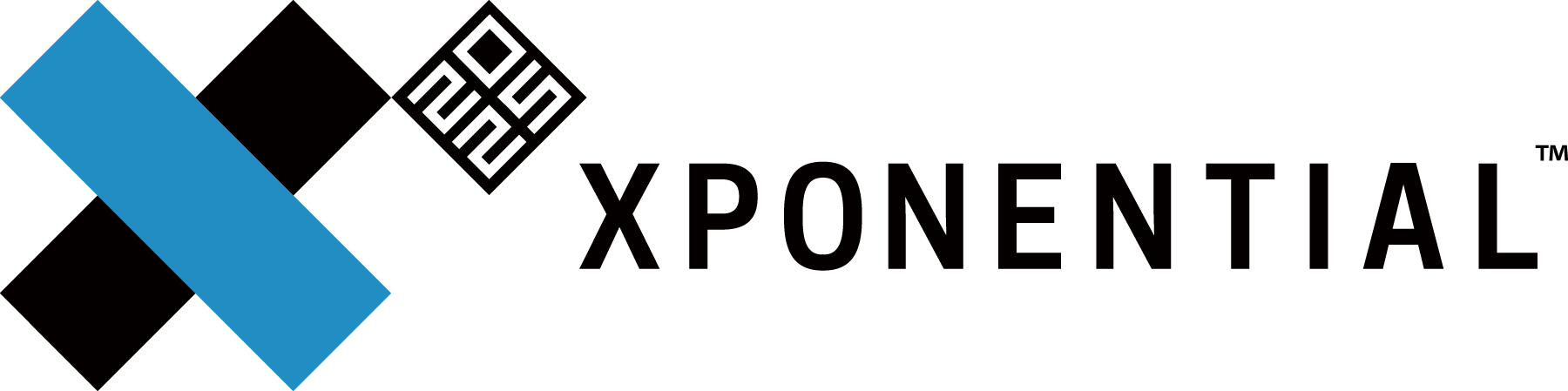
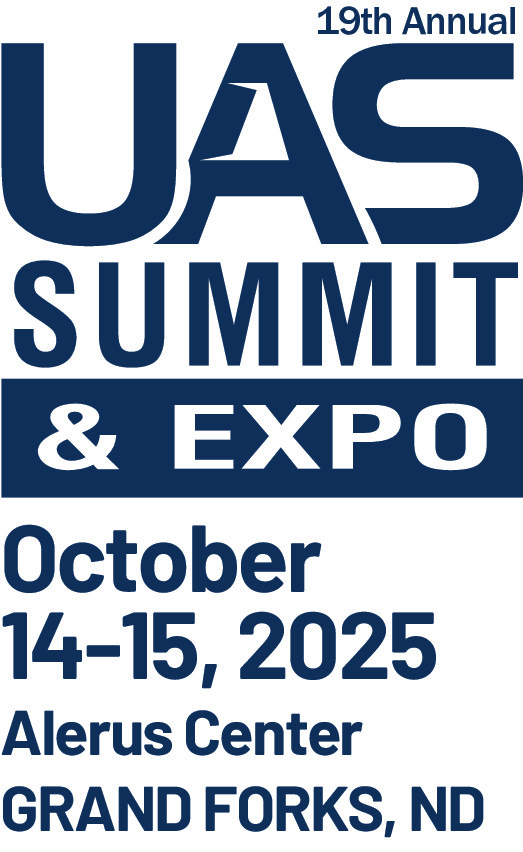

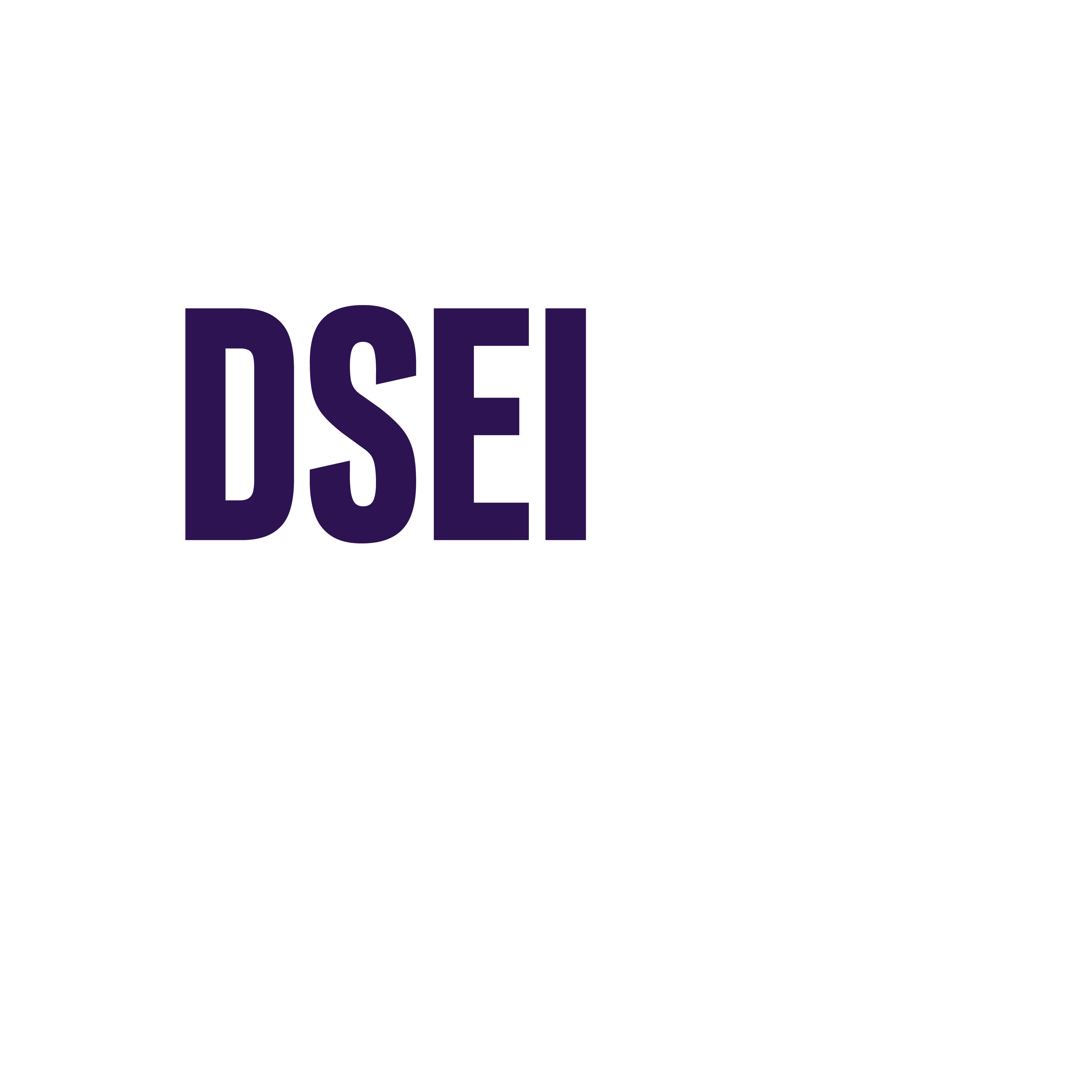
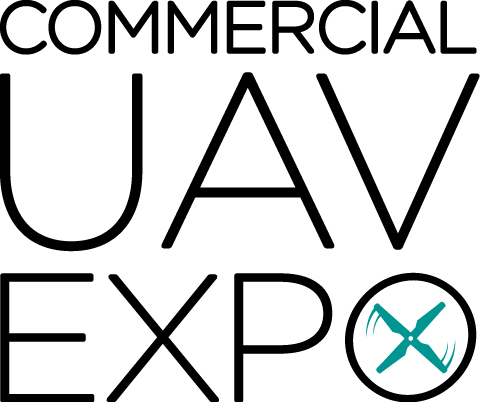
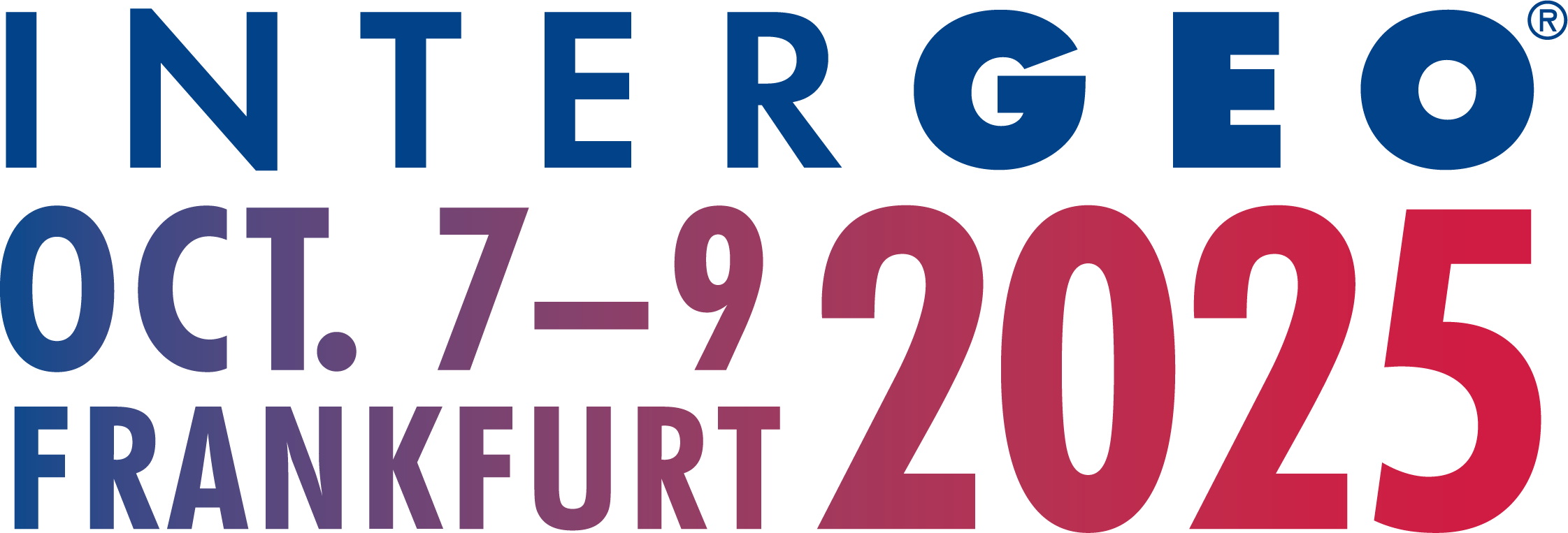
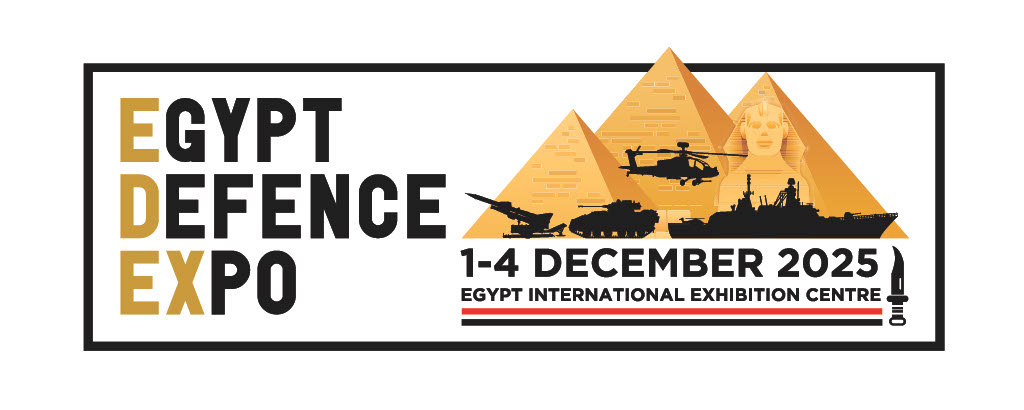
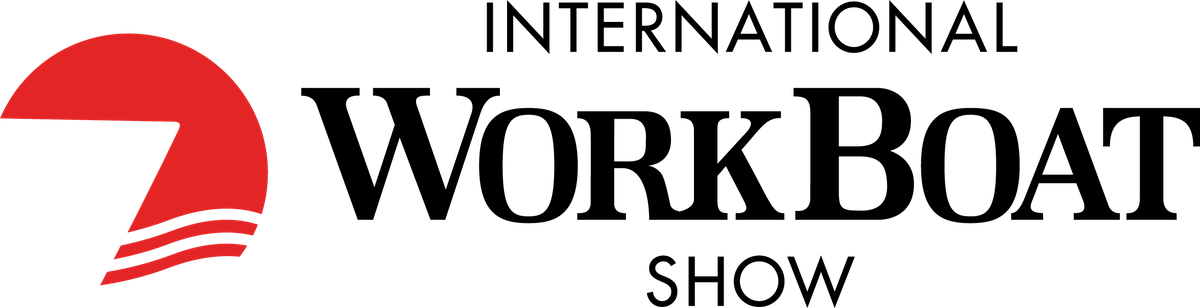