Xponential Europe 2025
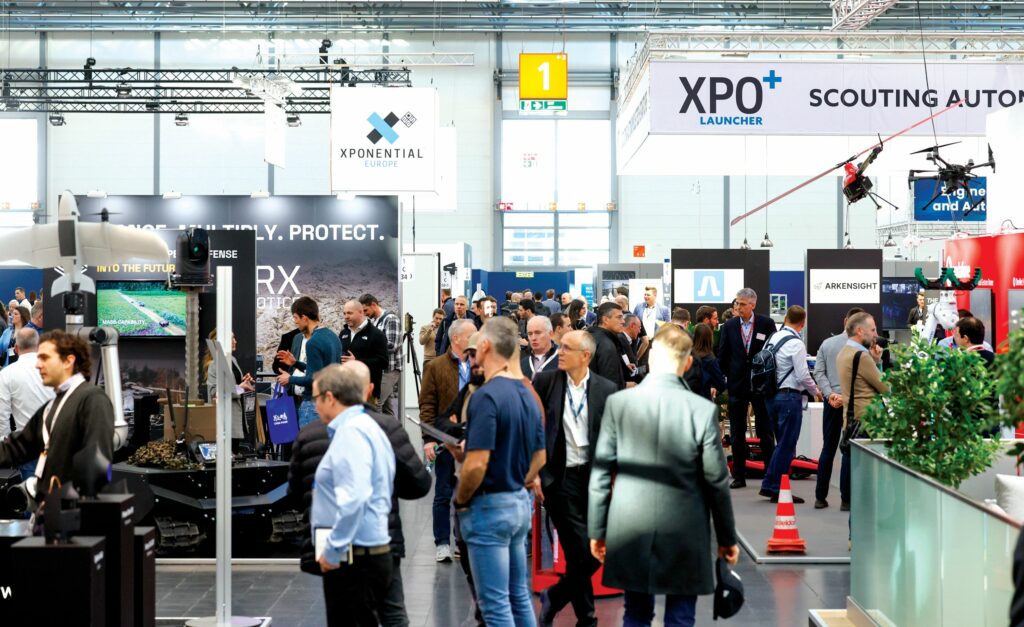
(Image courtesy of Messe Düsseldorf)
Standing ovation
The first-ever Xponential Europe surpassed all expectations with thousands of professional attendees seeking uncrewed solutions throughout the expo hall. Rory Jackson reports
Founding a new trade exhibition and conference is among the riskiest business ventures out there, but after the doors opened to the AUVSI’s first official Xponential Europe event (co-located with the European Drone Forum), it quickly became clear across both conference halls and the expo floor that the risk had been well worth it.
There, at the Messe Düsseldorf, from February 18-20, roughly 200 exhibitors were greeted by an influx of thousands of attendees. They hailed from various professions all over Europe and beyond, seeking sophisticated uncrewed solutions to a veritable smorgasbord of industry challenges.
With the clear message that Europe is awake and welcoming to the latest developments in uncrewed systems and technologies, the exhibitors showcased a plethora of new innovations in control, navigation, propulsion and more for vehicles operating on land, in the air and at sea.
A selection are presented here in the first of a two-part post-show report. Robot Aviation showcased its range of UAVs for defence and critical industrial applications. Among them was its SkyRobot FX-Y, which the Norwegian company is now manufacturing at a series-level of production.
“It’s a multicopter built with six motors, integrated as three coaxial pairs [a Y-6; hence the ‘Y’ portion of its product name], which gives a level of redundancy if one motor or prop should be damaged in flight, and it achieves just under 60 minutes of flight time,” says Niklas Nyroth of Robot Aviation.
“That’s typical while carrying an EO/IR camera such as those from NextVision, as well as either a standard commercial cellular radio or a 100 g high-end Radionor data link, which gives some extra resilience for defence users plus 20 km of effective comms range, or more with a bigger ground antenna.
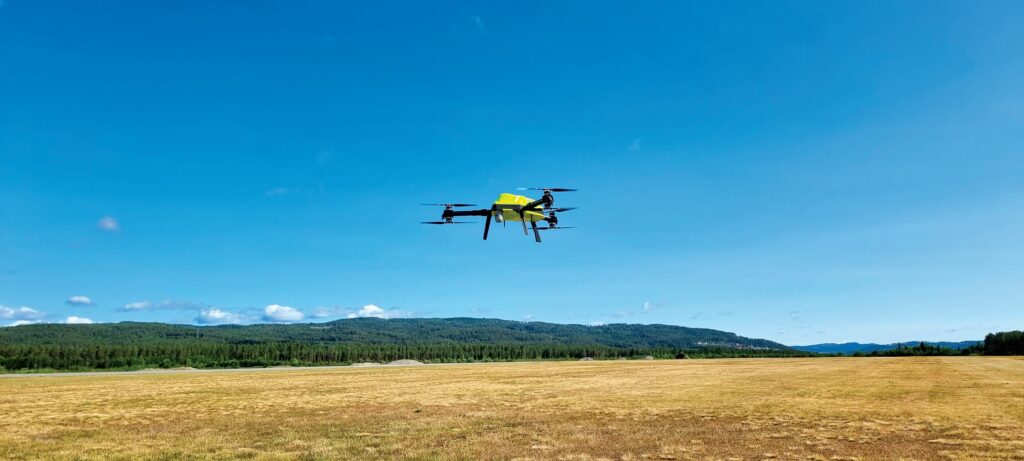
“There are many further payload possibilities. We’ve successfully integrated and combined a radiation sniffer and camera on another of our UAVs for highly georeferenced and detailed radioactivity surveys, which we could also do with the FX-Y now.”
The UAV can carry up to 5 kg of payload, which reduces its flight time, but keeping to a 2 kg payload typically enables an hour of flight, and integrating a tether enables continuous power and endurance.
Mission management can be performed via open-source GCSs, such as Mission Planner or QGroundControl or via Robot Aviation’s own SkyView GCS, depending on customer preference.
Among the FX-Y’s present customers are Lithuanian border control, which owns and flies 24 units as of writing (Robot Aviation having trained 320 operators for that customer), after starting to use the hexacopter two years ago. Romania’s Ministry of Internal Affairs is also now using the FX-Y in an emergency response capacity.
“We’re trying to source all components from within Europe, wherever possible. This is now very achievable for things like motors, propellers and flight controllers, for instance, although, historically, it has been hard to get European batteries. But, with this trade show, we’ve now found some really promising prospects for high-end batteries that are European,” Nyroth says.
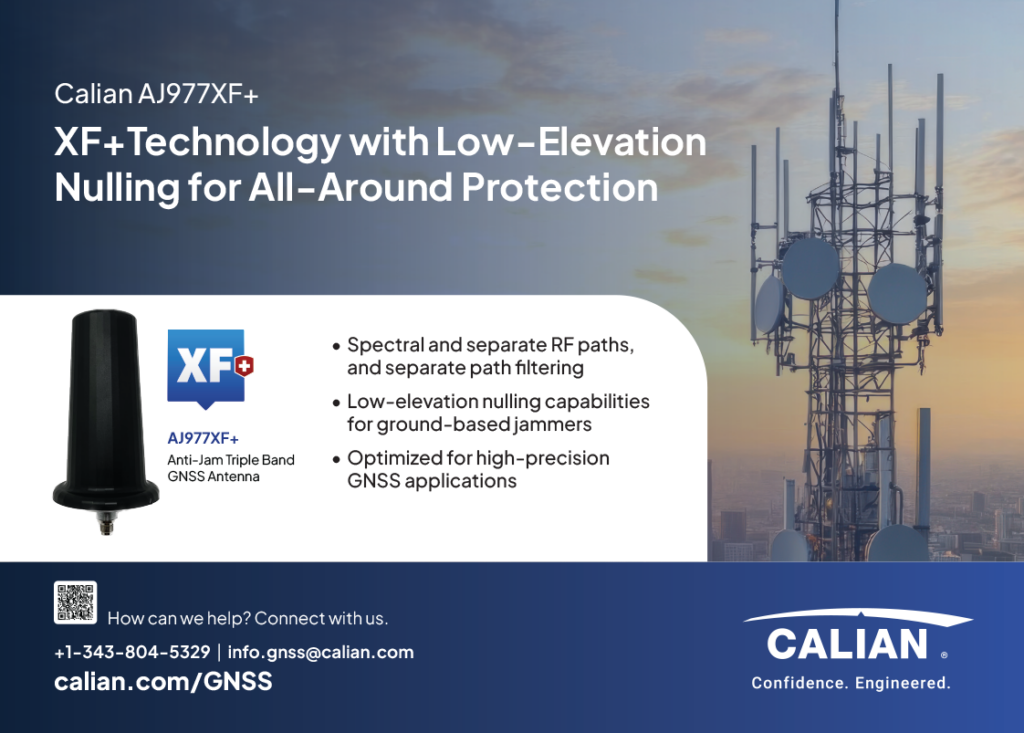
To further its supply chain resilience, Robot Aviation has set up its own composite production facility. This fact, along with its parent company owning one of Norway’s largest CNC machining suppliers, enables veritable independence and extensive customisation of all mechanically engineered components.
Mejzlik Propellers continues to expand its high-end product portfolio, reporting considerable advances in its r&d in engineering and producing helicopter-type blades, particularly for smaller, UAV-type helicopters. These often use unoptimised RC-type blades and do not benefit from the elasticity of traditional, fibreglass-based helicopter blades (and hence can benefit more from Mejzlik’s lighter and stronger carbon-composite blades).
We spoke to the Czech manufacturer’s Jan Hruska. “We’re now able to accurately simulate the behaviour of the helicopter blades in both static and dynamic conditions, which gives us the same platform for designing and optimising those as we have for the fixed-wing and multirotor UAV propellers that we’re best known for,” he says.
Following geometric design and optimisation, Mejzlik aims to perform additional structural design optimisations, followed by manufacturing. For low-volume batches, the company can use its traditional composite manufacturing procedures, but higher volume production runs are increasingly anticipated to be carried out using its new hot-press plant.
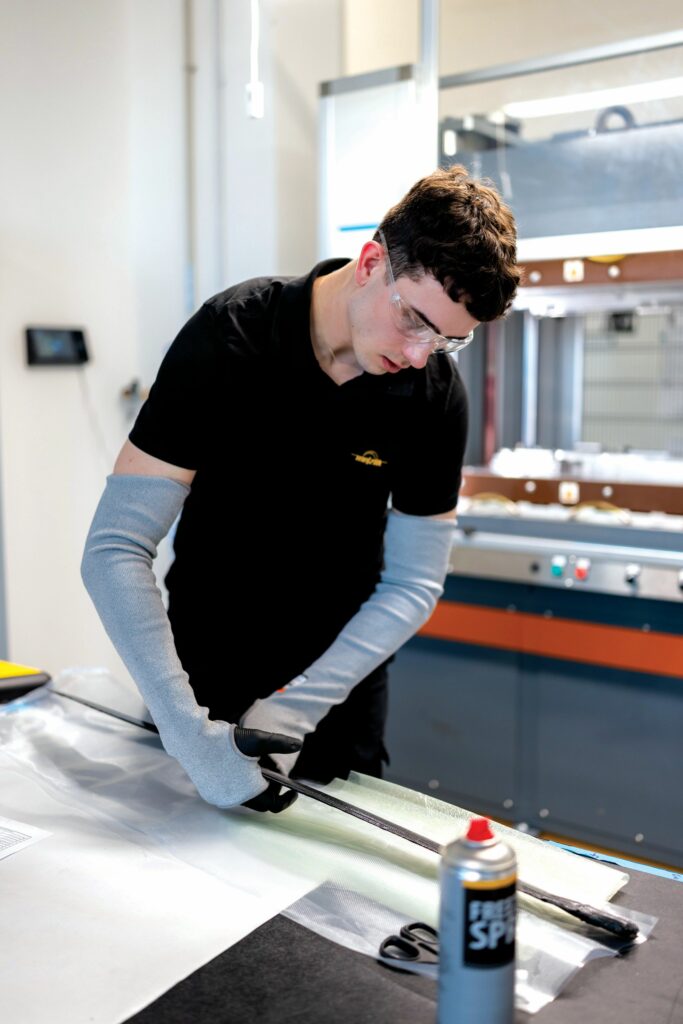
“The hot press is now running very proficiently and consistently, and we have six or seven project customers whose propellers are in production via the hot-press machinery, and we’re now preparing to get that new plant certified to ISO:9100,” Hruska adds.
“Through the hot press, we anticipate becoming the highest-volume supplier of carbon-composite propellers outside of China, particularly for the bigger sizes of multicopter UAVs we supply for. With supply chain resilience being more important than ever, we anticipate a need to increase our output by maybe three or four times for sudden surge orders coming in at short notice. That’s what the hot press will be really good for.”
TM-IT Systemhaus has launched Version 1.3 of its BeastFC flight controller, which is engineered to be a very small, lightweight system-on-module (SOM) device for UAVs with the highest SWaP requirements.
“We’ve been producing flight controllers for 15 years, but most recently it was asked of us to create one for mass production and huge scalability, sized as a miniature module that can be directly placed onto PCBs as part of an industry-standard, automated, pick-and-place production line,” says Martin von Kameke from TM-IT.
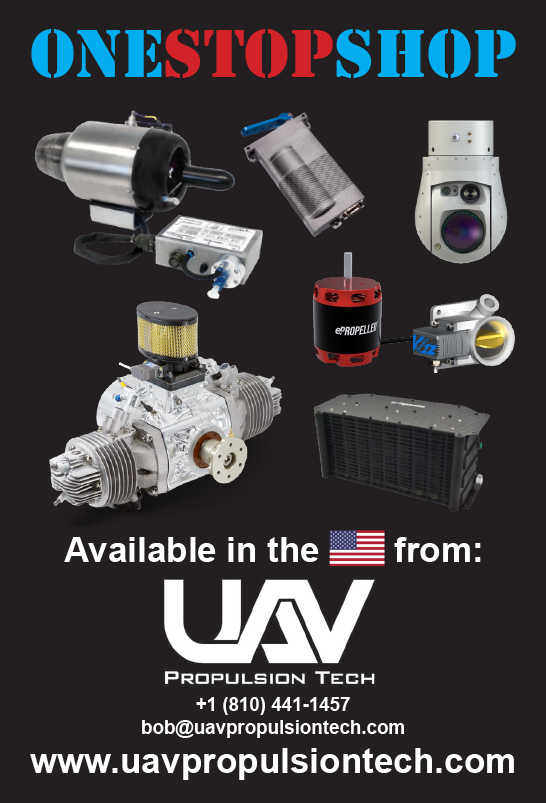
“The new BeastFC consists of a chip measuring 33 mm wide, 33 mm long and 0.5 cm tall, as well as 8 g in weight, with a shield on top and the complete electronics underneath, including Ethernet magnetics. That means one only needs to connect it to the circuit board. There’s no need for additional resistors, protection or anything.”
It runs on an STM32H753 Cortex-M7 MCU and an Invensense IMU, integrating a compass, barometer and IMU heater (the latter ensuring an optimal performance environment for the inertial sensor). As well as featuring two CAN bus interfaces, 20 PWM ports, five serial ports, USB, Ethernet and more, the flight controller can also be supplied on a carrier board for users who do not produce or assemble their own.
In addition to ensuring the supply of extremely small, lightweight components to fit the product’s tight form factor, TM-IT has worked to ensure the new BeastFC is NDAA-compliant using components from trusted and verifiable sources.
“After manufacturing, we perform end-of-line inspections in which we test every pin, we flash the system and we perform calibration over the full temperature range,” von Kameke adds.
“For software, we provide Ardupilot and PX4 support, and we also have an internal software development department that provides key technical support to our end-users.”
The new BeastFC is commercially available with a one-week expected maximum waiting time for orders.
Volz Servos is now mass producing its DA 14-N, which has been designed as a lower-priced, entry-friendly BLDC actuator for UAV manufacturers looking to move away from hobby-grade servos to ones with a higher-quality performance and lifespan, but still wanting something physically resembling them (particularly for ease of installation).
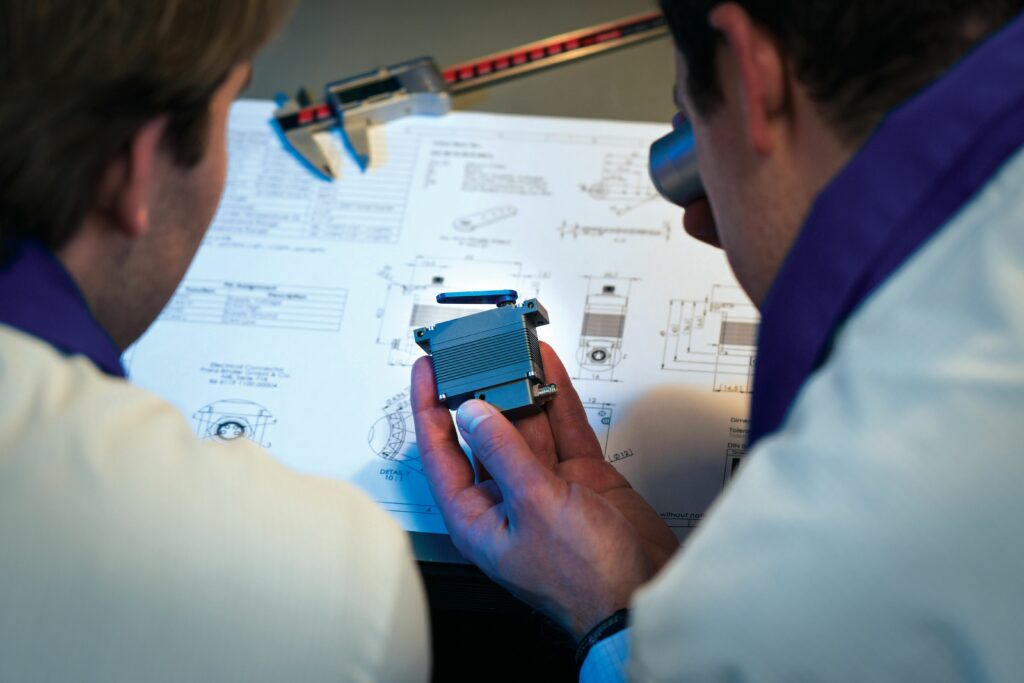
“Unlike our other servos, which come in many variants and can really only be built to order, the DA 14-N comes in one version, which we’re manufacturing to have hundreds in storage so batches can be delivered at very short notice,” says Volz’s Paul Felber. “The DA 14-N weighs 28 g and costs about €300 (£250) per unit. However, as customisation is a key part of Volz’s business, we still offer a certain degree of modification for the DA 14-N, but only for high-volume orders.”
Additionally, after the show, the company plans to unveil its DA 20-N actuator, which has been developed to suit customers for whom the company’s DA 15-N and DA 22-BLDC servos are, respectively, too small and too large.
To develop the DA 20-N, Volz engineered a new gear-train design to suit its size and reliability standard, as well as a new CAN-based PCBA (with RS 485 connectivity). The new servo is rated to a continuous torque of 1 Nm and peak torque of 2 Nm, with further specifications to be released soon.
Embention has released a vision-based navigation system for GNSS-denied environments, integrating a camera to generate a visual map of unjammable reference points, allowing UAVs to localise and guide themselves in flight.
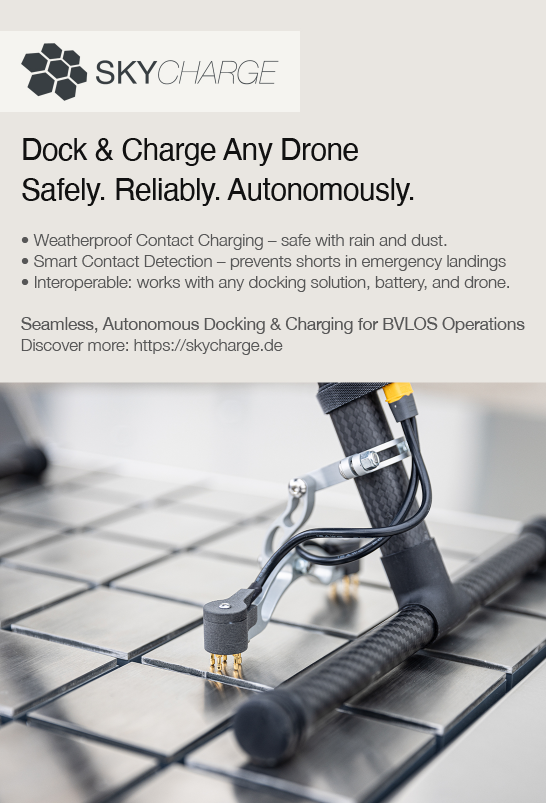
“We have seen many solutions on the market for visual navigation, but the problem is that most rely on Nvidia-based hardware. We know Nvidia does not support UAV certification at any stage. Instead, we’re using other processor technologies, which we aim to engineer for certifiability as part of our roadmap,” says Javier Espuch at Embention.
The company has released a new update for its Veronte autopilot system, ensuring compliance with two new European regulations introduced in 2024 regarding UAV geofencing and geocaging. The former defines restricted no-go areas for UAVs, while the latter establishes designated only-go zones.
“These regulations now require, depending on the type and size of the uncrewed aircraft, generally three layers of actions in the event of a geocage breach. First, the UAV must autonomously exit the restricted area. Secondly, if it can’t leave, it may deploy a parachute or take a similar safety action. Finally, as a last resort, the flight must be terminated,” Espuch explained.
Additionally, recent updates to the Veronte autopilot enable CAN- and serial-based integration of IMUs and other sensors, allowing messages from these sensors to be prioritised within end-users’ vehicle networks.
SF Motorsporttechnik presented a large selection of its components for fuel-supply systems, including various pumps with DC and BLDC motors.
“The pumps with BLDC motors have an integrated motor controller, which helps keep the entire system as small and compact as possible. We will now build these versions in a smaller version that meets the new requirements of UAV customers,” explains Martin Spickermann from SF Motorsporttechnik.
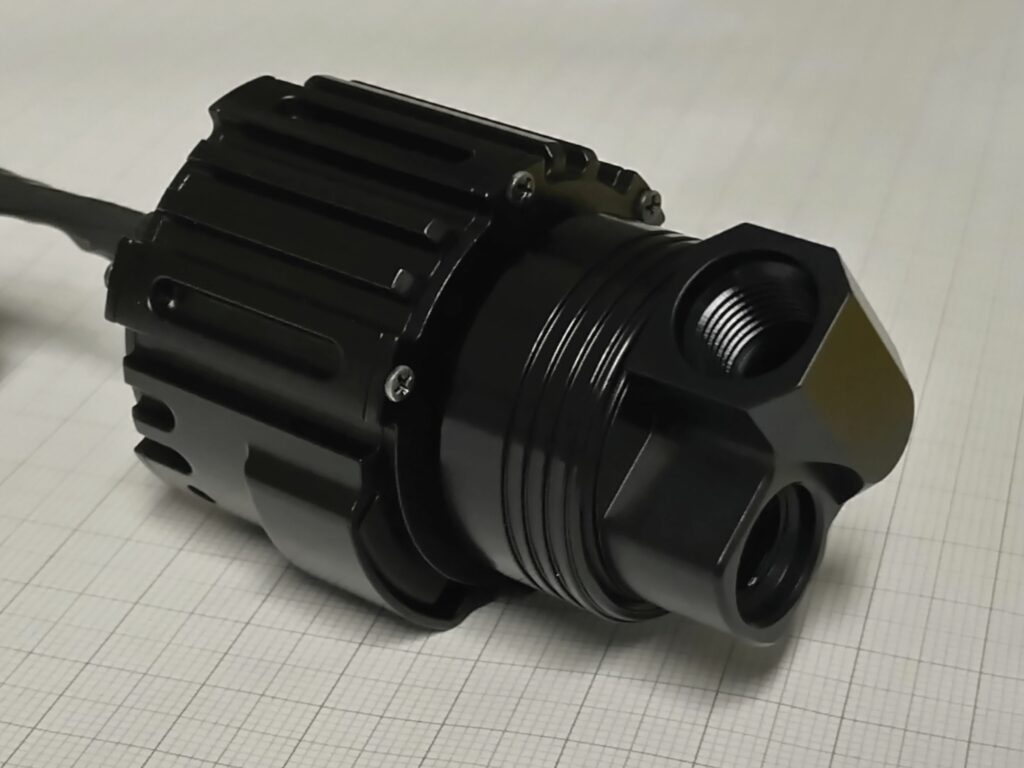
“Since we come from motorsport, we are used to fulfilling customer-specific designs precisely and at short notice, even for small production series. And that doesn’t just refer to the supply of the hydraulic output power, but also to the customer-specific design of the electrical connection, the hydraulic connections and the fastening of the complete units.”
Nicomatic displayed a wide range of its latest connector solutions, among them a new product conforming to the VITA 66 standard for optical interconnects in embedded computing systems.
“It integrates 12 optical fibres into a single connector housing. Engineering it took close optimisation for all the tolerances, so the fibres will always be connected without any misalignments,” says Nicomatic’s Simon Soppart.
“We’ve also integrated our own innovations in expanded beam technology for optical connections. That effectively functions like a lense, but oriented in the opposite direction to the beam, so it extends the light and you don’t have to exactly match two paired fibres together. You have a gap in between, so the manufacturing, handling and cleaning of the connections are all made easier. It also makes the connections more durable and resistant to contaminations.”
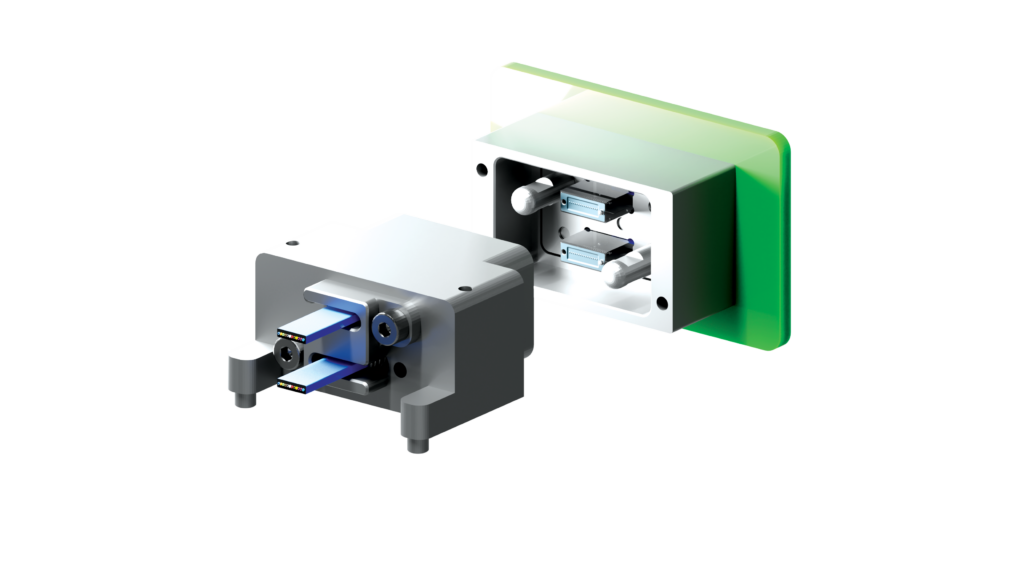
Nicomatic offers the VITA 66 standard connector with wiring provided by aerospace-certified cable harness manufacturers, and it can supply customised versions of the connector on request, including different form factors, materials and locking mechanisms.
The connector design is tested to 500 mating and unmating cycles, as well as 500 temperature cycles between -55 C and 105 C, and 10 cycles of humidity testing from 89% to 94% humidity, among other validations.
“The VITA 66 standard is also compatible with the VPX [VITA 65] standard, providing seamless integration with other VPX components, and is especially well-suited to backplane racking applications,” Soppart adds.
“Our Vita connectors come in variations with either one or two cavities. These versions of the product are called the VITA 66.4 and VITA 66.1, respectively, and each cavity can house either 12 or 24 fibres.
“On top of engineering and supplying this product, we’ve also worked to make our lead times as short as possible to supply fibre-optic cable harnesses when needed, and provide customer support and extra services such as fibre-optic training on call.”
Skycharge, a Berlin-based technology company, is enabling UAV automation with its patented contact-based charging, docking technology, and hangar systems. The company enables UAVs to autonomously land, recharge, and relaunch, eliminating the need for human intervention between operations.
“Conductive charging functions reliably, with virtually zero current losses and in a very predictable way that ensures we can estimate how long a given charging process will take” explains Andrea Puiatti of Skycharge.
However, traditional contact-based charging has long faced a critical safety challenge — exposure to water and debris can cause short circuits, leading to potential failures, fires, or even explosions.
Skycharge’s patented technology introduces two innovations that make conductive charging safe and viable for BVLOS (Beyond Visual Line of Sight) and fully autonomous drone operations. The first of these is weatherproof docking, through which the system prevents short circuits, ensuring safe operation even in rain or dust, unless fully submerged.
The second is smart contact detection: to achieve this, current in Skycharge’s docking and hangar systems only flows after a secure physical electrical connection is detected, preventing shorts from emergency landings, wet surfaces, or debris.
“We started engineering this system in 2014 under a contract from NASA JPL, in collaboration with a robotics accelerator and the Qualcomm Research Center,” Puiatti recounts.
“At the time, our charging platform was flat and assembled from multiple isolated tiles. However, if water splashed onto it, the tiles would short, preventing the system from working.
“My father, an engineer, was walking on the streets of Trento when he suddenly realized how the gaps between the cobblestones allowed water to drain, keeping the surface safe to walk on even in the rain. He suggested applying the same principle to our charging platform—by slightly separating and insulating the tiles, water could slide off into channels, eliminating the risk of short circuits and ensuring safe operation in all conditions.”
Skycharge’s system hence features air-insulated stainless-steel tiles, dynamically activated based on sensor inputs and power management algorithms to ensure reliable and safe charging in all conditions.
The docking system is designed to work with any UAV model, accommodating landing displacements without mechanical components. The charging system supports any battery type (currently 11-52V DC) and dynamically adapts to different power requirements.
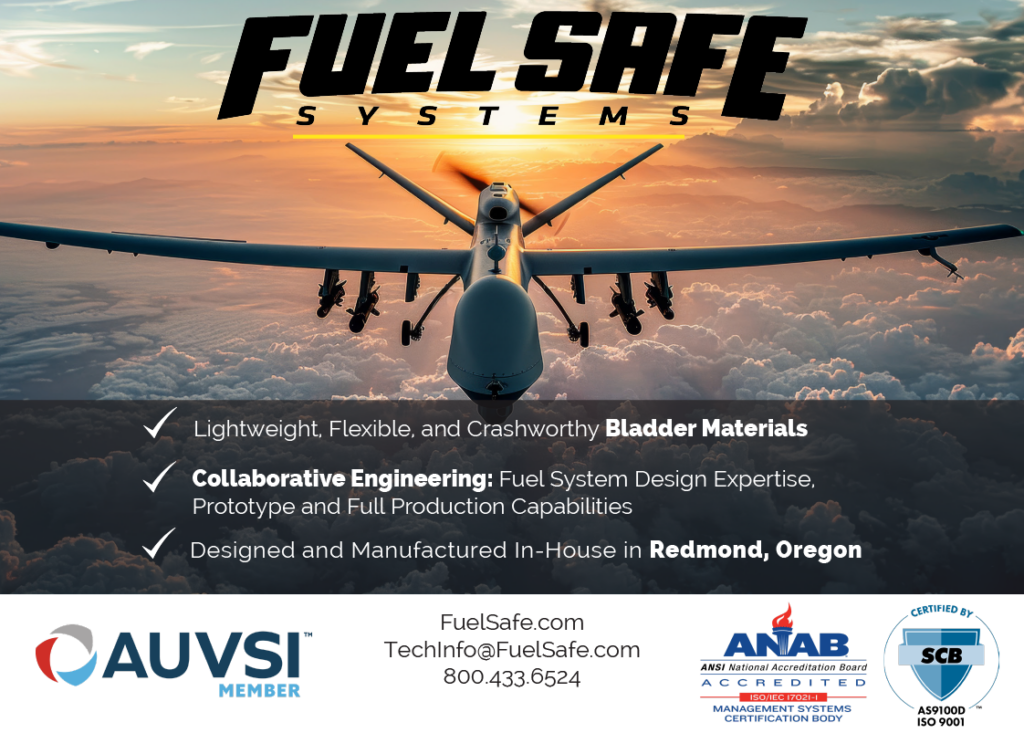
“Many of our clients operate fleets with different UAV types. Rather than requiring multiple incompatible drone boxes, they will have the option to rely on a unified charging solution that supports them all,” Puiatti added.
MostaTech has introduced a number of improvements to a range of its FOG-based inertial sensing offerings. The first is a new version of its VG2103S gyro, capable of withstanding 3000 g shocks, whereas previously the highest possible limit was 1200 g.
“A customer with a very specific application requested this version of the VG2103S, so we’ve made the new VG2103S-3000 by redesigning the case for increased strength, as well as lightening the components within, which reduced their inertia and hence the force they impart during impact,” says Arthur Tua.
“In particular, we decreased the size of the modulator, which was very important as that is the part that tends to fail first, being a piezoceramic ring – it cracks.”
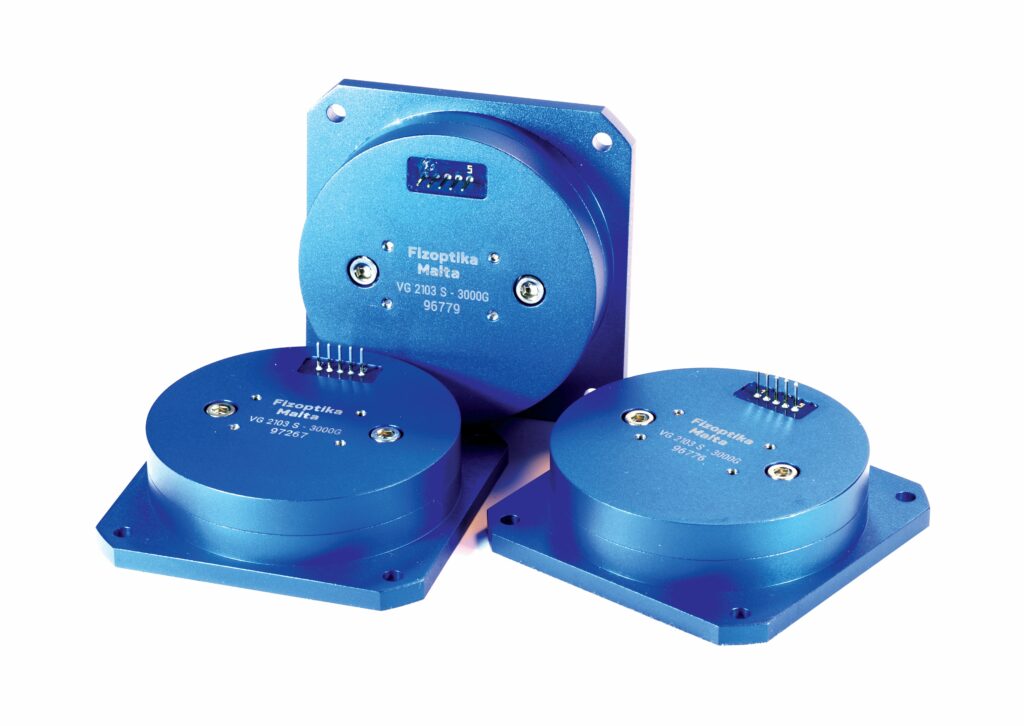
MostaTech has also reduced the height of its U123 FOG IMU by about 1 cm by redesigning it such that the shielding is now internal on each gyro and the component configuration is tighter.
“The U123 contains three versions of our VG221 FOGs, which we can now manufacture wrapped in shielding for a smaller overall IMU,” Tua adds.
“Our newest G321M three-axis FOG has been made smaller than its predecessors, again by introducing new components, optimising internal space within and using some smaller electronics. There’s a lot to be learned by looking at one’s past r&d and looking for opportunities where components can be moved or reduced inside.
“The G321 is also equipped with a more advanced, three-channel ADC board, featuring an 8 kHz data rate [compared with previously available 4.8 kHz].”
Hirth exhibited its range of engines, including the two most recently updated versions of its 42-Series and 35-Series two-stroke engines.
“You can see the spherical fin design we have on the cylinders of the 42 engine, which gives a thorough and even heat dissipation from the kerosene combustions, and the kerosene itself is delivered using our ‘i-power’
pre-chamber approach, where we preheat it in the transfer ports using exhaust gases for good vapourisation and burn,” says Marko Forkert from Hirth.
“It then uses a double ignition system for a robust, even spread of combustion. We have been running the 42-Series prototype on test benches for the last year, and we’re now at the phase where we are preparing to send prototype units to pilot customers.”
The 42-Series is a 183 cc engine, outputting up to 15 bhp (11 kW) and weighing 6.3 kg, with all ancillaries integrated. A reduction drive weighing 1.2 kg may also be integrated for propeller driving, as can a few generator options, up to 1 kW, weighing 800 g.
The 35-Series engine (featured in Issue 36 as the 3507) weighs 36 kg, produces 44 kW (60 bhp), and displaces 625 cc. Unlike the 42-Series engine, it is direct-injected using an air-assisted rail.
The latest version of the engine is the 3508, which integrates a 5 kW starter-generator as part of the company’s increased hybridisation work. Prototypes of the 3508 are running on test benches, and pilot customers are to receive their first test units in the near future.
Alpha Unmanned Systems displayed its A900 fuel-powered tactical helicopter UAV, which continues to accrue use-cases and mission time since its unveiling in 2023 as the successor to the A800 (covered in Issue 21).
“The A900 is currently operating in 12 countries. Its users currently include the Greek Navy, which is using and deploying it for ISR off of the Libyan coast,” says Eric Freeman, CEO at Alpha Unmanned Systems.
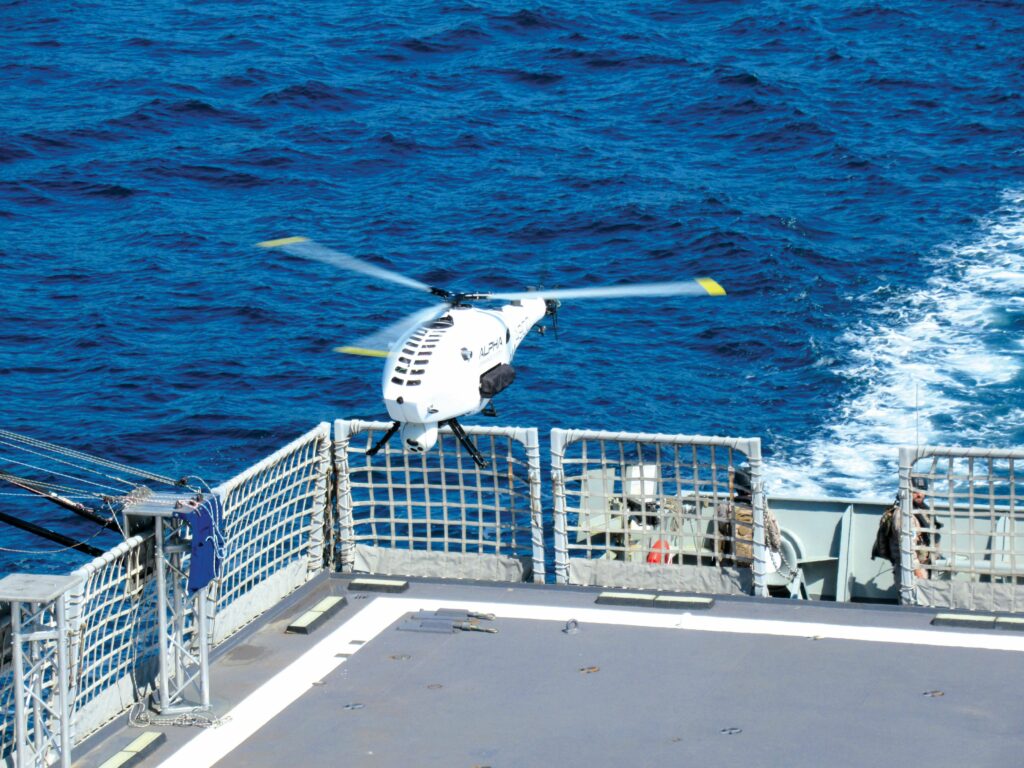
“It is also flying with Bulgarian border police in a Frontex [European Union Border & Coast Guard Agency]-backed project. There, the A900 is operated both from land and a small patrol vessel, where it is taking off, flying and landing, all fully autonomously.
“It is also being used for persistent surveillance by the US DoD, flying at approximately 1000 m above ground level, tracking 1 km2 at a time; each 1 km2 image being broken into nine equal parts, which are each refreshed roughly every three seconds. Any pixel that moves is detected, identified and classified according to the risk it represents.”
The A900 can fly for up to four hours with up to 4 kg of payload. Its most commonly installed payloads are high-end EO/IR sensor gimbals. Its flight endurance and payload capacity come from a two-stroke, two-cylinder boxer engine using a customised EFI system. The A900 operates for roughly 200 hours between overhauls.
The company has also developed the A900-T, which is a target drone version of the UAV, to be used by European defence manufacturers looking to optimise counter-UAS technologies and simulate manned helicopter targets.
The craft’s 4 kg payload capacity enables it to carry relevant devices such as Luneburg lenses, which amplify its radar signature such that it can emulate crewed helicopters or other objects. The A900-T can also deploy flares to increase its thermal signature, which may, for instance, be used to trial and calibrate early warning and detection sensor arrays.
SBG Systems is releasing a sizeable new firmware update to improve the capabilities and value of its Ellipse series of INSs, which has been engineered for full backwards compatibility, and
over-the-air downloading and installation, with all existing Ellipse products currently in use throughout the world, provided they have a hardware revision greater than 3.0.
“Once updated, the Ellipse INSs will finally run on the more modern algorithms usually only seen in our newer high-performance inertial products, making for more reliable position, heading and heave measurements,” says Kaoutar Benmakhlouf from SBG Systems.
“While the specifications of the Ellipse series may not show significant changes at 1 σ level [σ being noise standard deviation], the update focuses on enhancing robustness and reliability. The major performance improvements become clearer at the 2 σ and 3 σ levels, where a higher percentage of measurements exhibit improved accuracy.”
After writing the firmware update, SBG undertook meticulous testing and validation of its performance and consistency, starting with testing individual components of the INS before moving to whole-system tests. Those consisted of mounting the updated Ellipse INSs on vehicles and running them for several hours in aerospace environments, harsh ground-level environments and in tunnels.
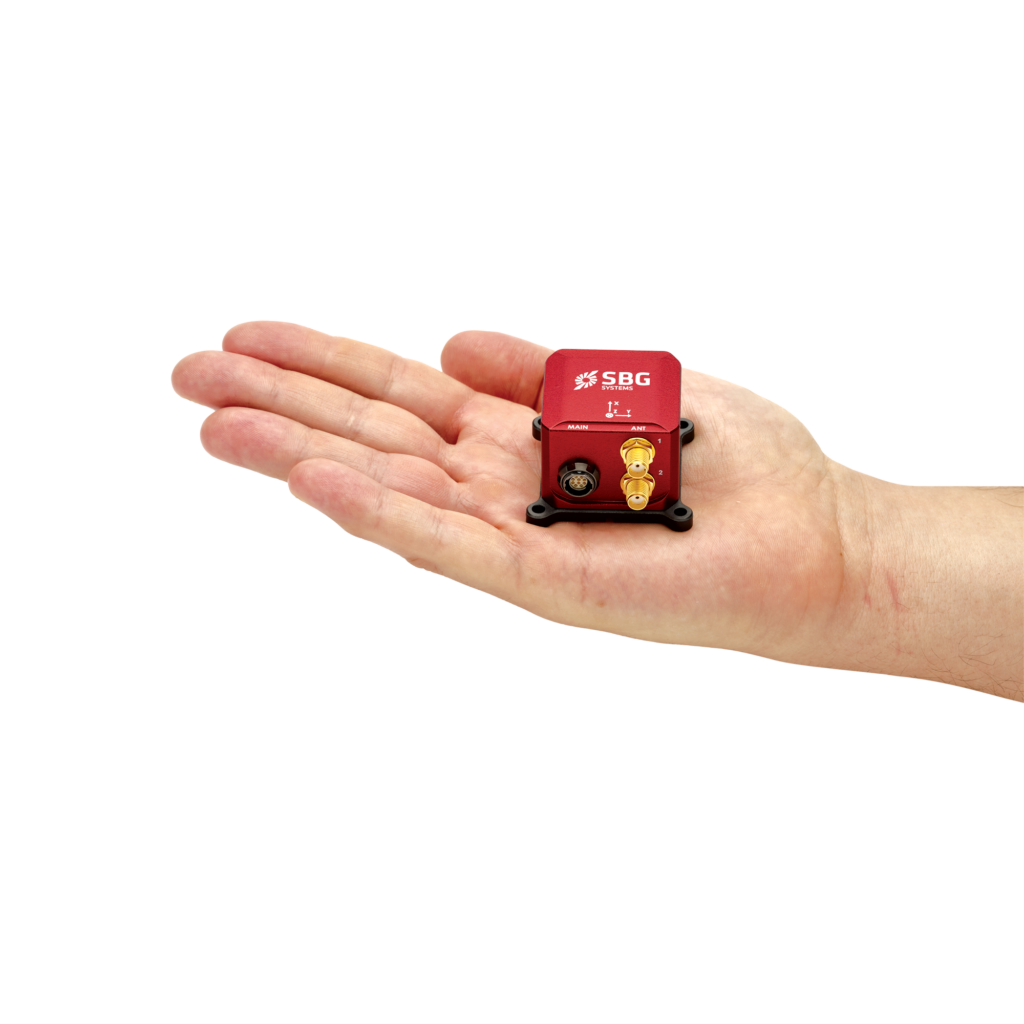
“We’ve also tested the firmware in marine environments by mounting the Ellipse on a boat, and also run specific flight tests on UAVs while analysing feedback from customer-led beta tests,” Benmakhlouf adds.
CubePilot also attended the show and spoke with us about its Cube Red, which the company has designed specifically to be the dual-redundant offering among the company’s Cube family of flight-management units (FMUs).
As Siddharth Purohit at CubePilot tells us: “The Cube Red FMU helps users easily manage uncrewed exploration vehicle operations as the module has two dual-core, double-precision FPU microprocessors for faster data processing than other systems.”
The system design includes an Ethernet port for enabling expansion of networking capabilities. The module additionally features an external flash memory drive to accommodate larger and more complex programs than can be fitted into the FMU’s main memory.
Naturally, the dual-redundant nature of Cube Red also lends the system to easier certifiability than non-redundant flight controllers; a key benefit for UAV designers and integrators engineering their aircraft for safety assurance and integrity levels.
“And all the key components feature a redundancy system to ensure uninterrupted vehicle operation, regardless of a fault occurring in one of them,” Purohit adds.
Hargrave Technologies launched its new nanoDRIVE 4LPi on the first morning of the event. It is an ESC that has been designed principally for the speed and agility requirements of FPV quadrotor UAVs with around 5-10 in (12.7-25.4 cm) diameter propellers.
“It supports all the standard protocols, like PWM and DShot, but we’ve designed it to work using DroneCAN first and foremost, especially for scalability,” says Hargrave’s Saami Bashar. “Users could install nanoDRIVE 4LPi on thousands of UAVs and still configure them, update them, and plug and play with them smoothly. That’s what DroneCAN allows.”
The motor controller has been designed with a very small form factor, weighing just 20 g, which posed significant thermal management challenges during development, given the minimal surface area for heat dissipation relative to the ESC’s four 20 A channels and up to 34 V system operating voltage.
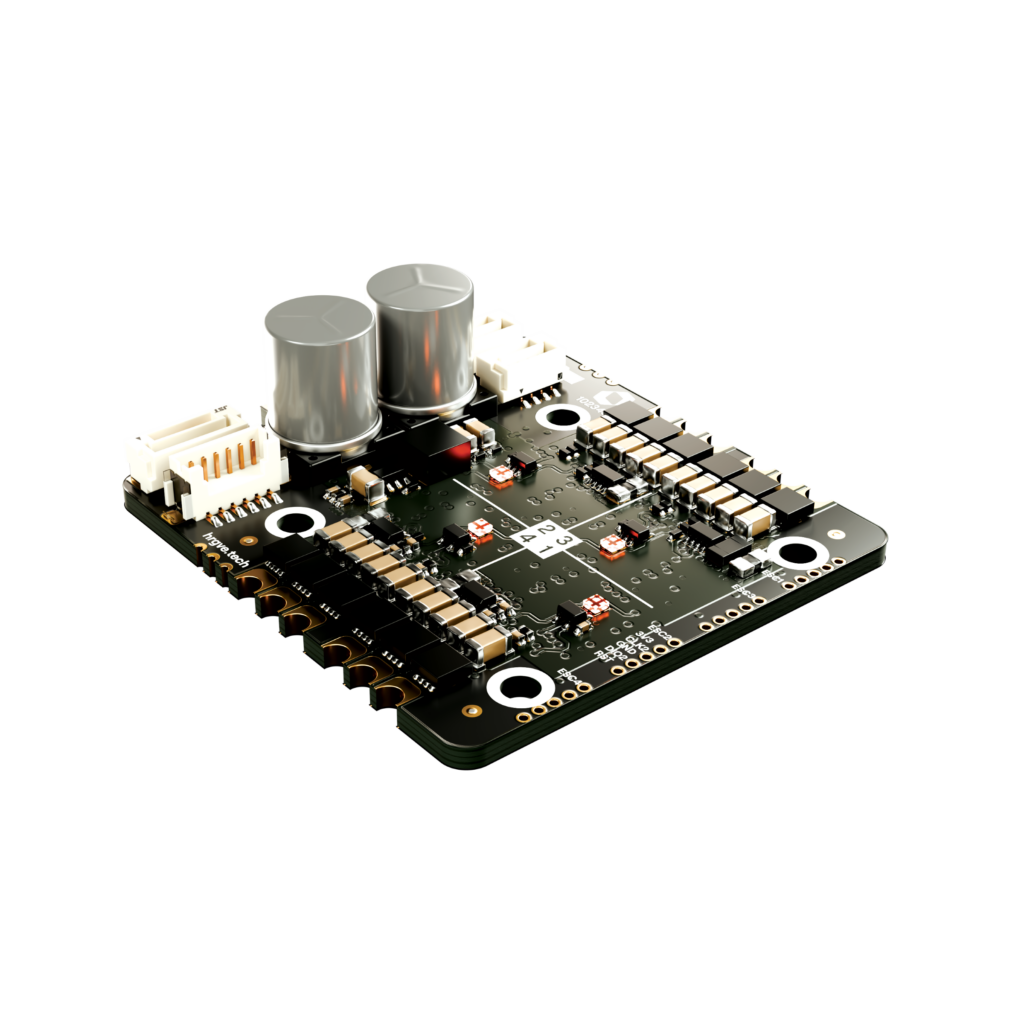
As Bashar explains: “One novel part of solving that has been putting the capacitors atop the board, which most manufacturers don’t do because of the extra processing steps it entails. Adding capacitors this way reduces ripple current and therefore heat generation, and also gives us a fairly open design, such that we can use the board itself as a spreader and dissipater of heat. It also hugely helps the system cool down when it is inside an aircraft hull without direct exposure to any air rush.”
The nanoDRIVE 4LPi runs using Hargrave’s new, proprietary FOCAL motor-control algorithm, which the Australian company engineered to be more efficient than the conventional FOC in real-world applications, after discovering that FOC was often more effective in lab conditions than in actual operations.
“FOCAL behaves adaptively, because when you change environments with a UAV, you deviate somewhat from the optimal conditions that the motor and motor controller are tuned together for working in. After about three years of r&d, we have an algorithm that adapts on the fly instead,” Bashar explains.
Notably, Hargrave did not use or train AI to write the adaptive FOCAL algorithm. While AI is highly valuable in applications such as perception-based object classification with 90-98% confidence, anything less than 100% reliability is dangerous for flight-critical components such as motor controllers.
“We estimate FOCAL gives 3-5% power-efficiency gains over FOC in the average mission profile, which could be huge for a company using UAVs regularly every month,” Bashar adds.
SightLine Applications has launched its new 1710 dual-channel processor module, which comes with two MIPI channels for integrating a pair of MIPI cameras into a single unit, generating two processed video streams at once.
“It is similar to our 1750, which we released a couple of years ago, and runs on the same NXP multi-core processor, but we’ve redesigned it for a smaller form factor to fit into smaller gimbals,” says Hanni Wehrman from SightLine.
“The biggest contributor to that redesign and rightsizing has been the dual MIPI approach. Instead of having a bunch of different connectors and interfaces as a catch-all approach, the 1710 just has MIPI connectors.
“This redesign will particularly appeal to customers who previously used the 1500 module, which reached end-of-life after its processor manufacturer discontinued production. The 1500 was the smallest processor in SightLine’s lineup, and with its discontinuation, the company developed the 1710 as a more powerful replacement, capable of supporting the full suite of SightLine functionality.”
The company has finalised a number of new software capabilities, including an AI detection feature that tracks objects and determines (with a given confidence index) what each object is, including people, UAVs and vehicles.
Additionally, a new precision acquisition feature will allow operators to pause a video for up to 20 seconds, use their cursor to drag a box around a specified object, and then return the video to real-time. This feature only pauses the video for the operator, while the video continues streaming onboard, ensuring no loss of video integrity.
“We are also continuing our developments on the counter-UAS side of things. For instance, based on requests, we can track up to 10 drones in a given video frame, and the next request is for up to 20 drones, so that’ll be what we release in that vein next, along with a new module update for enabling three video streams at once,” said Wehrman.
MAD Components displayed a range of its newest products for UAV propulsion, paramount among them being its XP Series of drone arm solutions, each consisting of a connected electric motor and ESC pairing, pre-integrated on a carbon tube for turnkey installation into a multirotor hub.
“We have designed our drone arms with agricultural spray UAVs in mind, and as well as being plug-and-play solutions, they integrate LED warning lights for working in night time or poor weather conditions,” says Jay Chen from MAD Components.
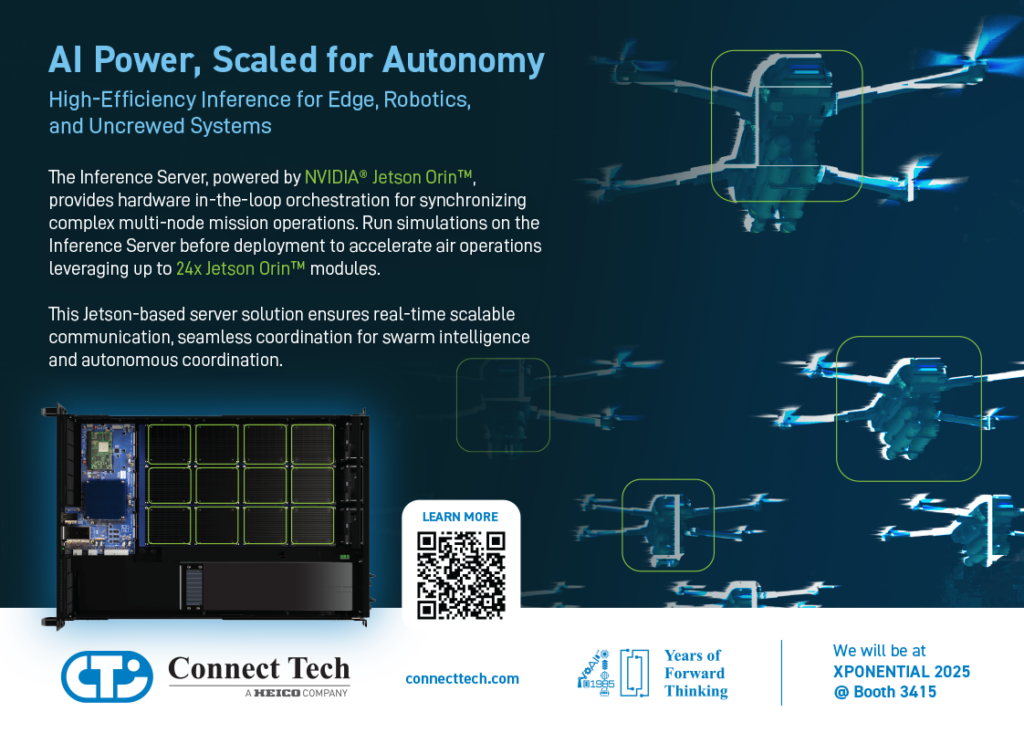
The company’s XP6S Drone Arm Set is designed with an IPX6 protection rating, weighs roughly 766 g, and produces up to 12 kg of peak thrust (plus 3.5-5.5 kg continuous thrust). The system is suitable for integration on quadrotor UAVs weighing 14-20 kg with 5 litre fluid-tank payloads, or hexacopter UAVs weighing 21-33 kg and carrying 10 litres of payload.
ElevonX unveiled the latest version of its Tango UAV with a wingspan of 4.4 m, enlarged from 3 m.
“A key customer doing medical deliveries in Africa requested a UAV that could manage cargo transport missions over 100 km flight distances. That meant we needed to increase the size and weight of the fully electric version of the Tango aircraft to handle a bigger, doubled-up battery pack,” says Matej Meglic of ElevonX.
Using the hybridised version of the Tango, incorporating a fuel engine as a range extender, would have increased the noise and maintenance requirements of the UAV beyond that customer’s tolerances, so staying all-electric was a strict requirement. Instead, the new Tango flies using a 12S battery pack with 60,000 mAh of energy.
With the new updates, the battery-electric Tango UAV can carry a payload of 5 kg over 100 km, drop it for the recipient and fly back over the 100 km distance with a safety margin of 27%. That is, the battery is expected to return to its original take-off point after 2.5 to three hours of flight with a 27% state of charge. Endurance can be increased further if some of the payload weight is dedicated to extra battery mass.
“We do our own composite manufacturing in-house, so we thought that making the new wings would be simple – that turned out to be untrue,” Meglic says.
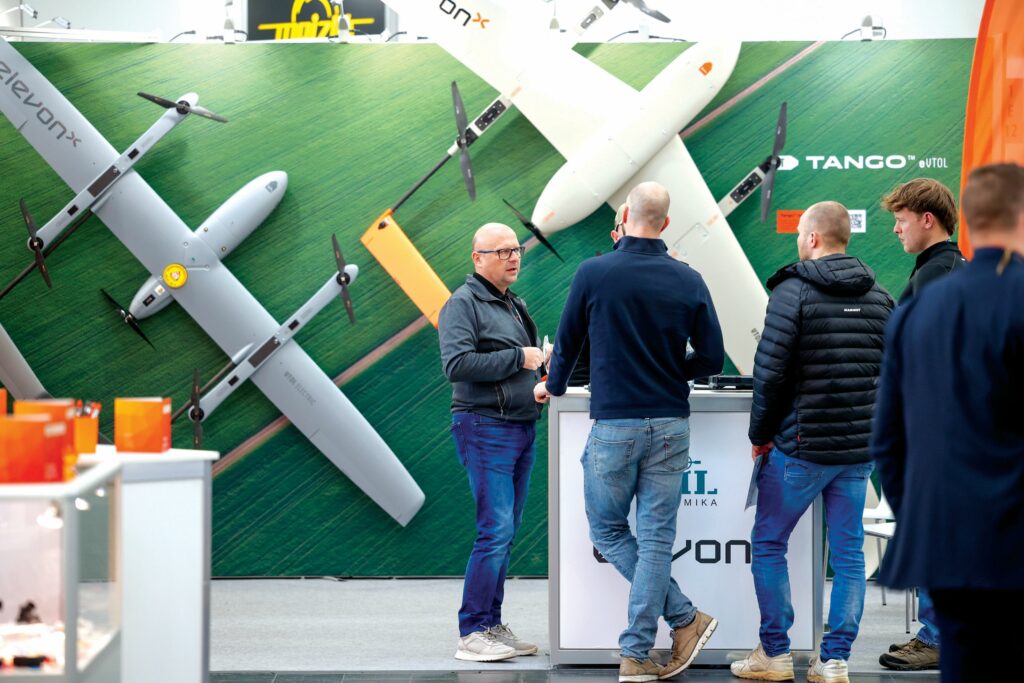
(Image courtesy of Messe Düsseldorf)
“Creating and perfecting the wing took a lot of optimisation between weight, airfoil geometry, and its stability and efficiency in different airspeeds. We needed to make sure the aircraft could slow down in flight while dropping its payload and still switch back to high speeds, especially to get away from things like sudden weather hazards.
“We started with CAD simulations, and then made sure to thoroughly test the iterations of the wing in many hours of real-life flight tests to ensure it worked for all air speeds.”
UPCOMING EVENTS
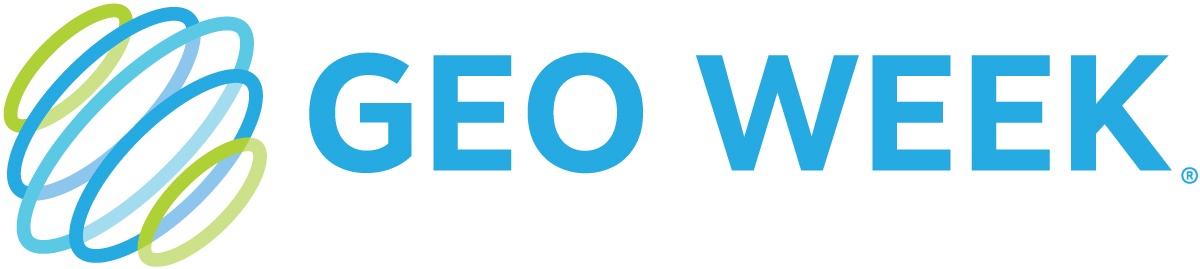
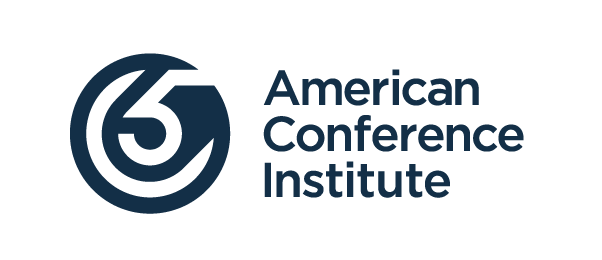
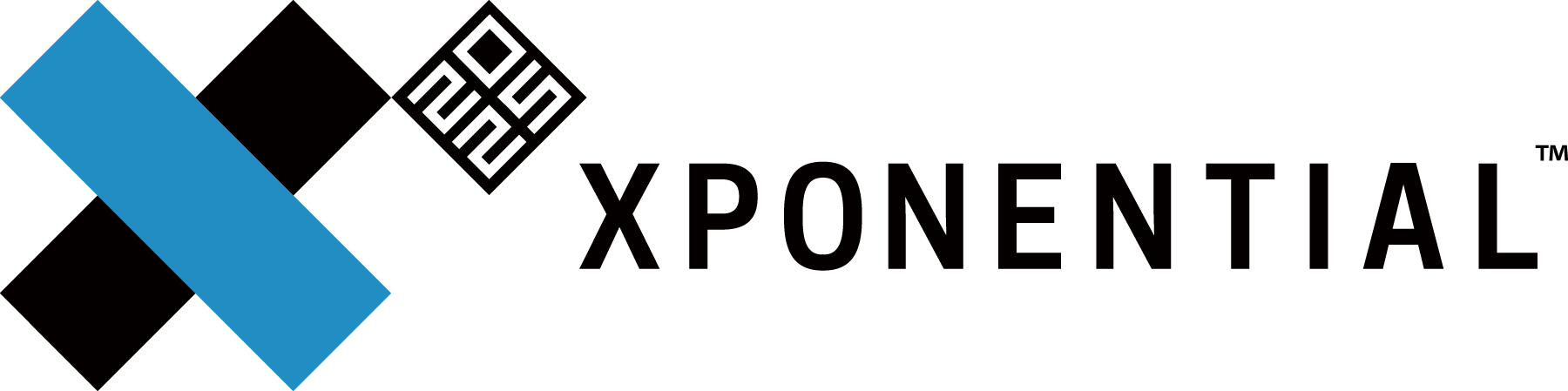
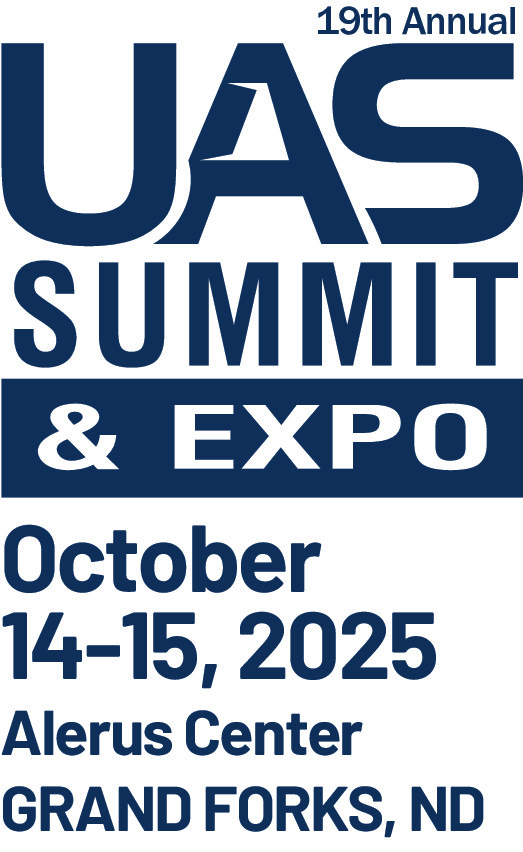
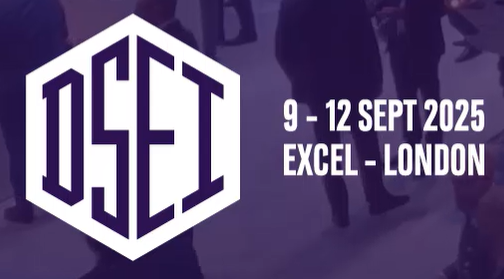
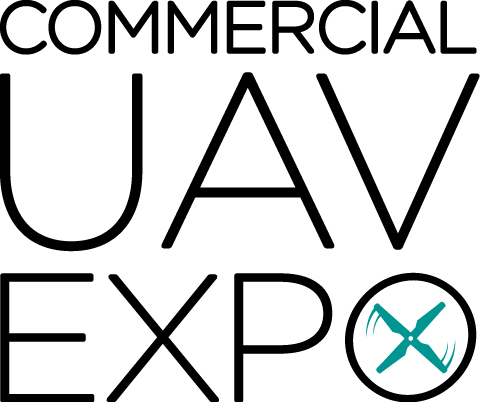
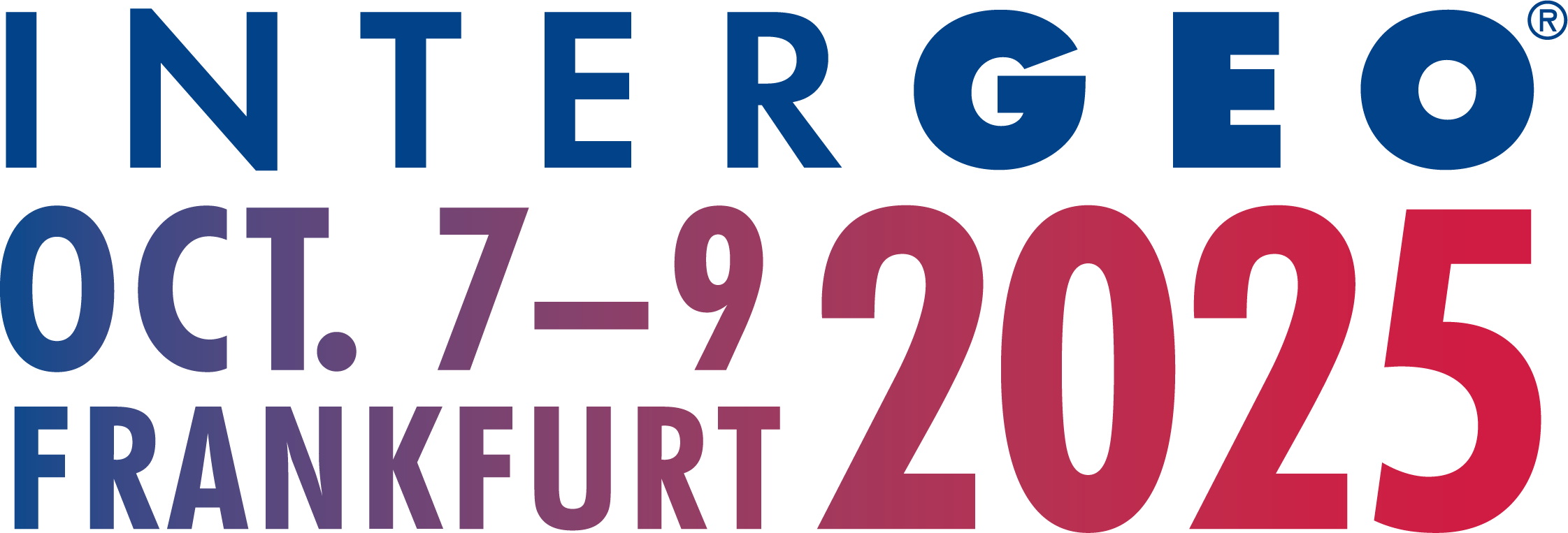
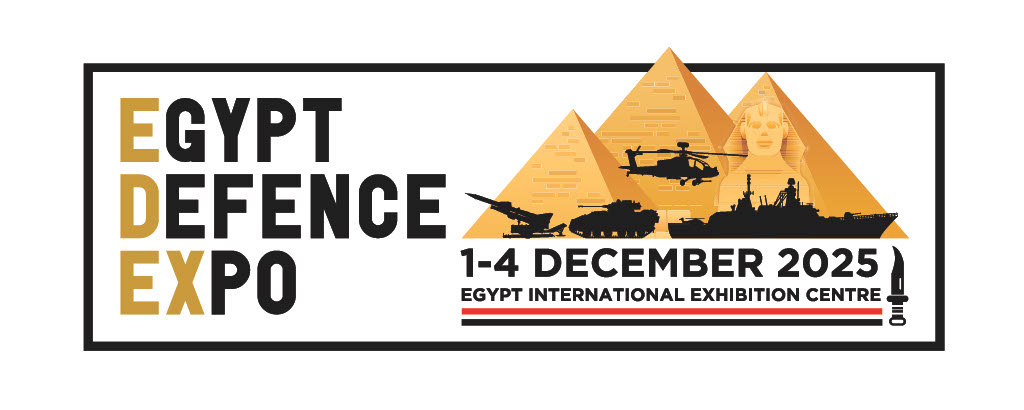
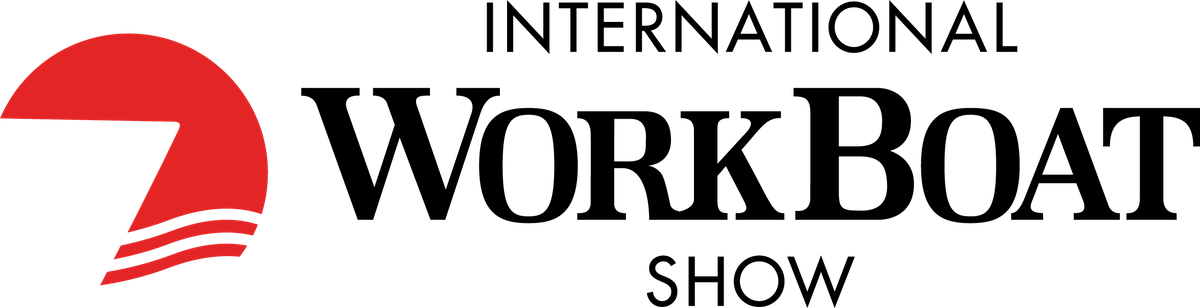
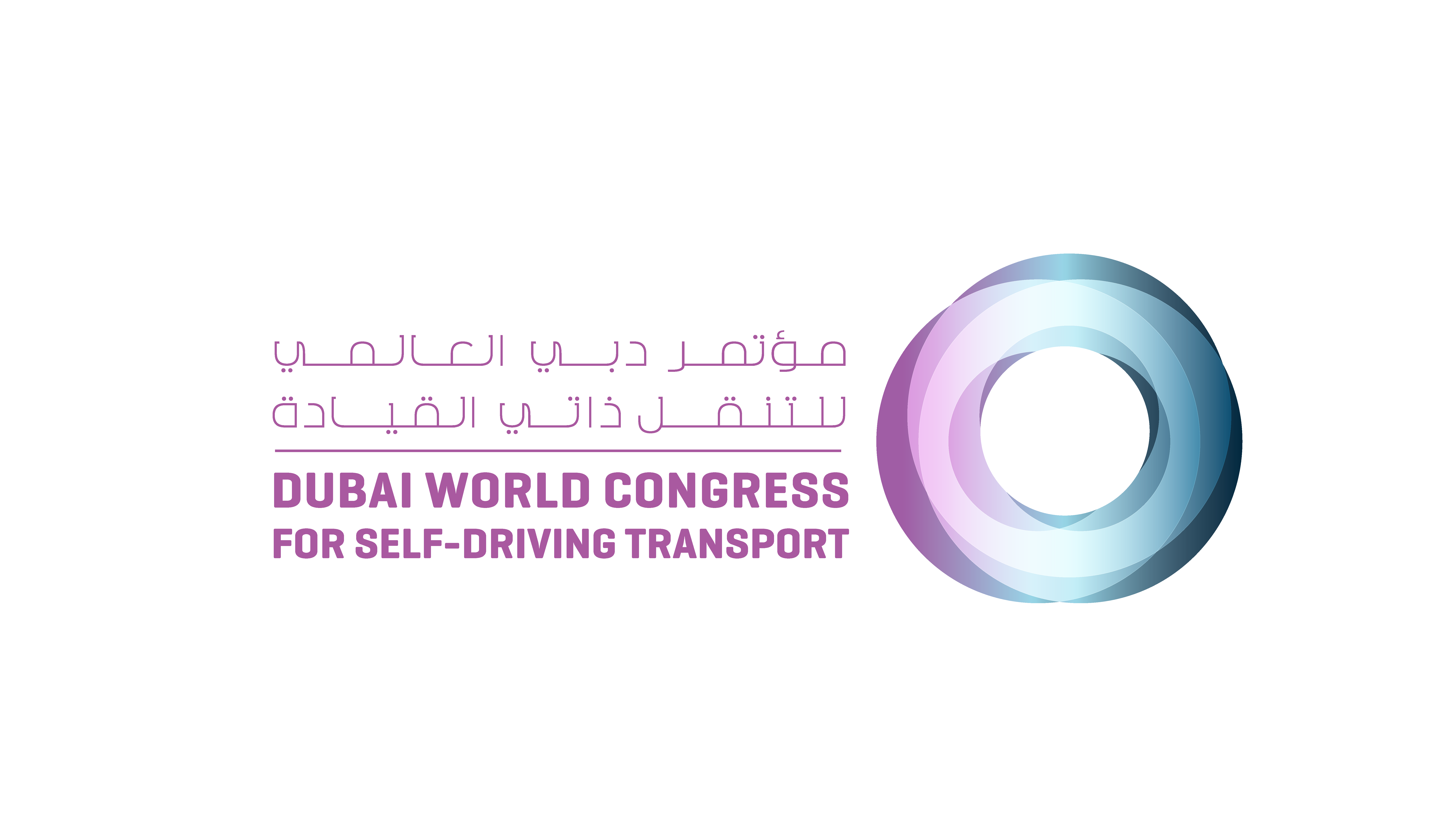
