Xponential Defence
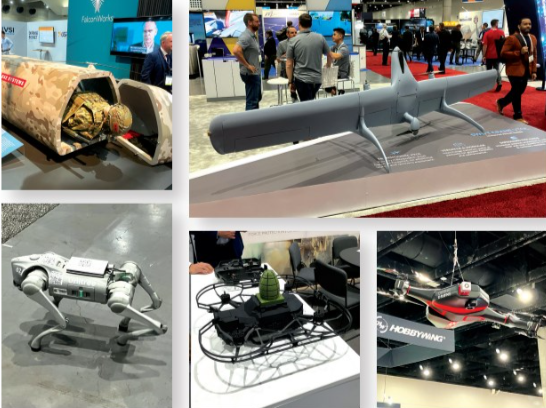
Peter Donaldson eyes the best uncrewed systems that the world’s military can dream of in his report from Xponential 2024
Burgeoning use of uncrewed systems in the wars in Ukraine and the Middle East, and during US preparations for future conflicts its armed forces may face, made the dedicated military section of the exhibit floor and conference programme at Xponential particularly apt. Staged on April 22-25 in San Diego, USA, the event brought industry and established defence giants together with military procurement officials in a showcase of new technologies, ideas and emerging needs.
Don Sheehan from the US Navy’s Program Executive Office, Unmanned Aviation and Strike Weapons (PEO U&W) team, discussed the urgent requirements of the organisation charged with procuring and managing all of the uncrewed aerial systems (UAS) and related equipment for the US Navy and Marine Corps.
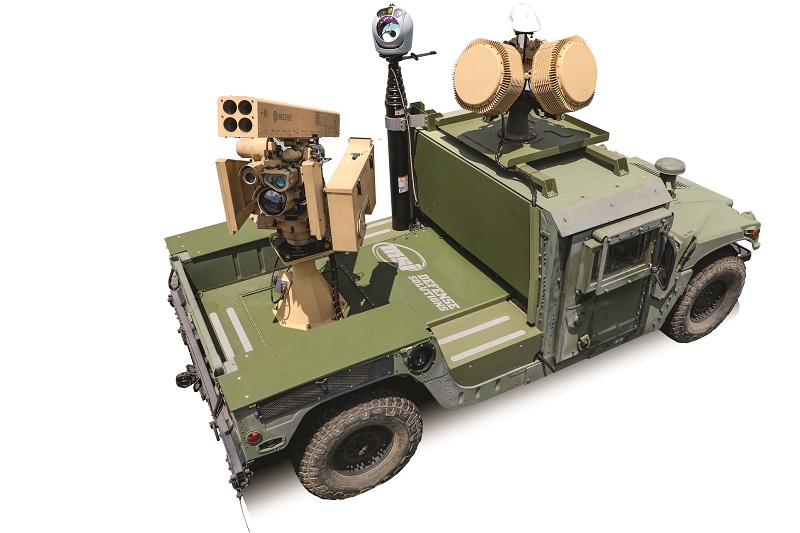
As the deputy PEO responsible for contingency operations and disruptive technologies, Sheehan handles procurements that are not normal programmes of record and need to progress quickly. As recent examples, he chose two lethal Counter-UAS (C-UAS) systems, the EAGLS from MSI Defense Solutions and the VAMPIRE from L3 Harris. VAMPIRE has been deployed to Ukraine, while EAGLS is set to go to the Middle East.
“The EAGLS system I got on contract within 15 days, and with VAMPIRE, we delivered 14 systems into theatre within 60 days from concept to go,” he says.
A key point of focus is accelerated fielding of artificial intelligence (AI) and autonomy. Sheehan explains: “The adversary is forcing us to change the way we fight, and we’re on a trajectory to take uncrewed platforms and arm them.” He asked for the industry’s help in building trust in AI-driven autonomous systems among the personnel who will have to use them, and the other US armed forces and ‘partner’ nations who fight alongside them.
Ideas are also needed on how best to get AI technology into the hands of operators. “How do we train folks who can have that technology and that capability at the lowest possible level?” he asks.
A further challenge is that there is no common definition of AI and autonomy agreed among the US Armed Forces, which makes it hard to get funds from Congress and to operate in combined arms teams, so the US Air Force (USAF) is currently writing the definitions which the other services plan to adopt, he says.
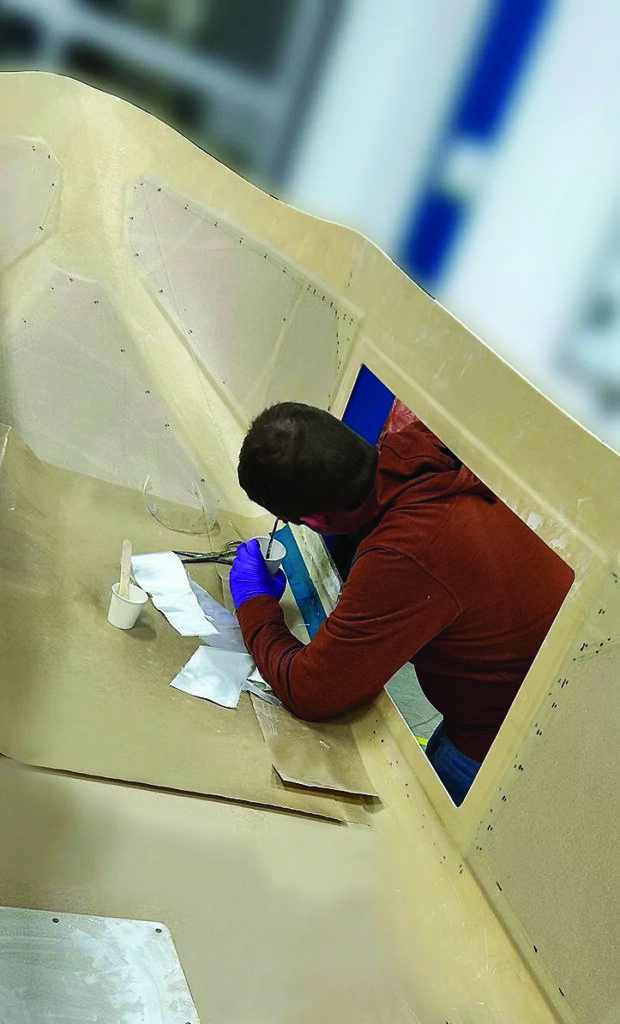
Ed Sujecki provided insights into areas where the Program Executive Office USC/LCS wants help from industry. He is assistant programme manager for specialised mission modules in the US Navy organisation, responsible for uncrewed, small combatants and the Littoral Combat Ship. The key mission areas are mine countermeasures (MCM) and surface warfare.
Industry can help with managing the burgeoning amounts of data generated by the uncrewed systems. “How can we leverage machine learning and AI to cut down the workload of our operators to make sure they’re only focused on the areas they need to?” Sujecki asks.
Both mine countermeasures and surface warfare missions are conducted by multiple cooperating platforms, and they rely on many communication links, and Sujecki emphasised the need to make them much more robust and secure.
“How do we make sure we have those comm links there?” he asks. “How do we operate if we’re in a degraded comms situation/non-comms situation, and everywhere there is an open comms interface that is an avenue for our adversary? So how do we make sure all our systems are cyber-survivable and have the appropriate level of cyber security?”
The Navy regards the medium USV (MUSV) as a modular ‘truck’, able to do many jobs, and it is looking for vendors who can help integrate a range of different autonomy engines into it. The organisation is also looking to work with companies who are “pushing the limits” of situational awareness, particularly with small form-factor systems that can fit a 38 ft craft.
As well as acquiring more MUSVs to meet an eventual target fleet size of 48, the PEO wants more MCM-related payloads.
“We are looking at the Barracuda system for mine neutralisation, but if anybody is producing other payloads with an application for a smaller USV, we would love to talk to you and hear your ideas,” Sujecki adds.
Apex Space & Defense Systems discussed how to scale up production of UAVs to meet growing military demand in the shadow of demonstrably massive Chinese and Russian industrial capacity. The company is looking for new and improved composite materials that will support fast, high-volume manufacturing while meeting quality and performance standards.
A major supplier of composite structures for a wide range of military platforms, Apex focuses on the manufacture of fuselage, wing and control surface parts for aircraft from pre-preg composite materials with another division that makes filament-wound parts.
“Our customers come to us when they’re in the infancy of a design programme, and we help them to find materials and design their products for manufacturability,” says Apex CEO Tracy Glende.
The drive for larger numbers of UAVs has created an urgent need to reduce manufacturing times and this has consequently brought advanced materials such as snap-cure resins to the fore.
“We’re paired with material suppliers, and are testing and validating their snap-cure resin systems, along with some other new lightweight foam materials,” says Tom Millspaugh, director of new product development.
“Where normally you’d have a two- to three-hour cure, these cure in 10-20 minutes and offer basically the same properties as a long-cure system. And the suppliers are doing a pretty good job of toughening the resin systems,” he adds. “We’re looking at them to increase production from, say, 10 UAV component sets a day to 100.”
Apex is also seeking better lightweight foams used to stiffen structures by keeping wing skins apart.
“A lot of the manufacturers have gone to commercial insulation foams because they are cheap and readily available. The issue with them is that they are uncontrolled; they are not mil-spec foams that they have to qualify every time they change blowing agents,” he explains.
Today, he says, the gap in performance, consistency and price between the qualified aerospace-grade foams and the commercial ones is getting smaller. “Now, they are specifically engineering and formulating these foams to have the right properties.”
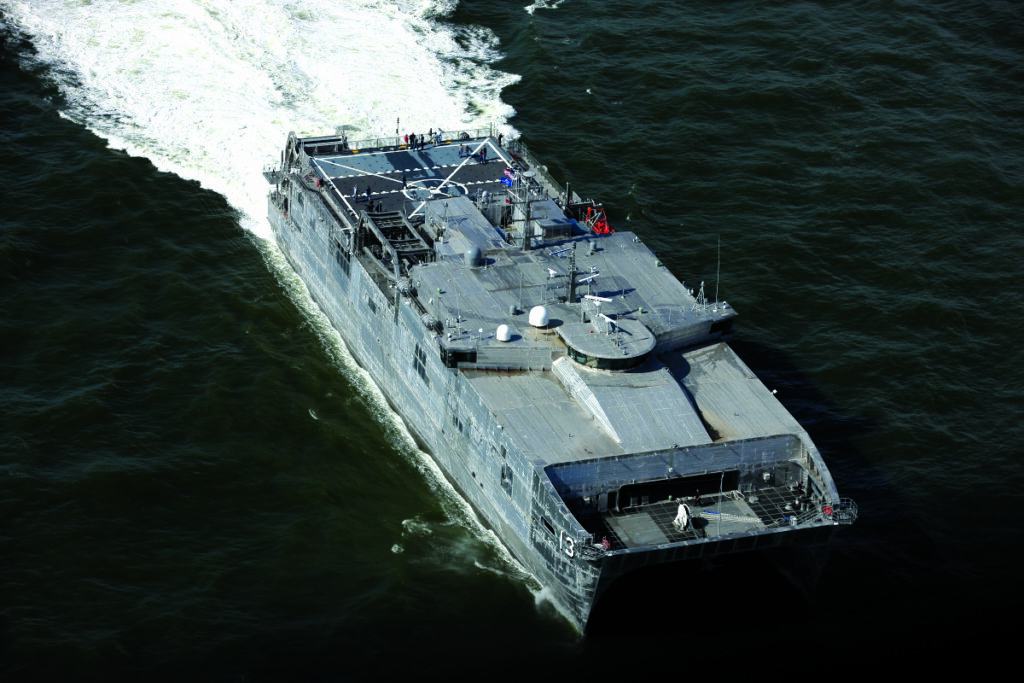
Austal USA showcased its capabilities in integrating autonomous control systems into large naval vessels. The company has several different autonomous vessels, either recently delivered or under construction, including the commercial crew supply boats of the US Navy’s ‘ghost fleet’ that were converted to uncrewed operations under Project Overlord, along with units of the Spearhead-class expeditionary fast transport (T-EPF) fleet.
“We got into autonomy not through shipbuilding but through our machinery control systems,” says Anton Schmieman, the shipbuilder’s director of advanced concepts. “When the Navy came out with their requirements for Project Overlord, we recognised that the systems we developed originally for commercial, high-speed vessels met around 92-94% of the requirements that the Navy had.”
Austal USA teamed up with L3Harris to convert the first and fourth units of the Overlord USV (OUSV) fleet, integrating L3Harris’ navigational autonomy with its own machinery control technology.
Austal USA’s highly automated hull, mechanical and electrical systems controls were already integrated into the Spearhead class T-EPF ships as standard when the company won the contract to convert USNS Apalachicola (T-EPF 13) to autonomous operation.
The 103 m, 2,500 t, 35 kt (or more with a light load) catamarans of the Spearhead class can carry a 600 short ton payload 1,200 nm. Apalachicola is the Navy’s largest ship with autonomous capabilities and it completed more than 2,500 nm of autonomous operation in the Gulf of Mexico in 2023.
“We did a series of tests that gradually increased in complexity from simply turning the autonomy system on to giving the ship full missions under autonomous control,” he says. “The culmination of that was a seven-day run around the Gulf of Mexico up into the Straits of Florida because we had to go to a place like that to find enough traffic to stress the system.”
While a supervisory team was on board, the ship operated with no one at the controls for more than 90% of the time. “There were just two interventions over a week-long trial, which is minimal,” Schmieman says.
Austal USA is one of six primes under contract to design the US Navy’s future, large uncrewed surface vessel (LUSV), for which the company is putting an engine/genset through a 720-hour test in a cell in Utah, during which no maintenance is allowed.
To meet the Navy’s desire for open architecture computing, machinery control systems are likely to move away from programmable logic controllers (PLCs) towards the kind of edge computing that characterises the Internet of Things (IoT) and mobile devices, Schmieman says.
“We will go as far as we can in that direction. It might not be completely like the iPhone example that the Navy likes to use, but it can certainly move to a more modular, flexible, open system that you can put on a greater range of ships,” he explains.
Schmieman also identified damage response/damage control as a capability gap in autonomy for large ships, partly driven by regulations mandating a human presence.
“A perfect example is firefighting systems. It would be pretty easy to automate them, but there is a little nuance to how you would take the person out of the loop,” he says. “That’s one of those gaps that we want to address in the near future.”
Hidden Level presented its UAV detection, and airspace management and protection services, based on complementary passive radio frequency (RF) direction finding and passive radar technologies. Direction finding relies on antennas and receivers that detect and locate RF emissions from UAVs, while passive radar exploits signals of opportunity available in the operating environment. Hidden Level’s system can operate in both modes. Naturally, these technologies have both civil and military applications.
The company provides an airspace-monitoring service (AMS), a data-as-a-service solution for broad area critical infrastructure protection and public safety.
Hidden Level makes wide-band passive direction-finding systems that are used in this specific application for detecting drones in a given airspace, says a company representative. A commercial solution would involve the installation of our sensors around an area of interest, which could be a city or a football stadium, for example. Then the company would provide a data feed that the customer can use to determine what type of drone activity is happening, he adds.
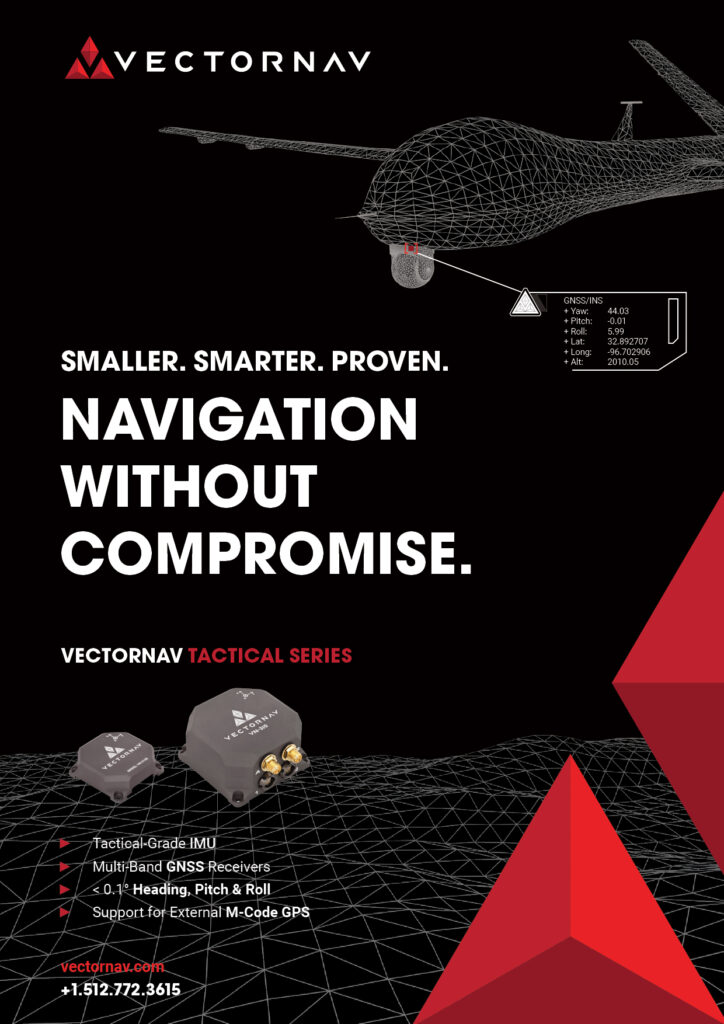
Hidden Level has discussed military use with representatives of NATO countries. There is a strong application for base defence and also for mobile systems. For example, it can provide a manoeuvre force with a mobile ‘bubble’ over the vehicles, the representative explains.
In military use, passive direction-finding and radar are essential in most mission-critical use cases, says the company. For broad airspace awareness, passive direction-finding is the best option when range and stealth are required.
Hidden Level’s technology has been assessed by the US Government and the Department of Defense as mature.
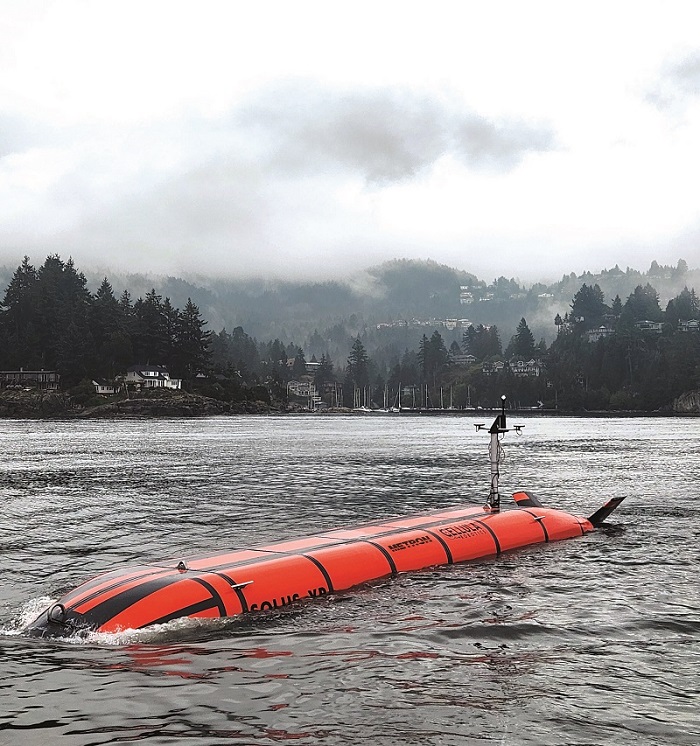
Metron and Cellula Robotics discussed their recent partnership to deliver long-range, long-endurance, AUVs capable of carrying out complex operations requiring flexible payload configurations for covert missions in areas with restricted or denied communications.
Metron brings decades of experience as a prime integrator and developer of advanced UUV technology for US defence and commercial applications to the partnership, while Cellula has its family of Solus LR and XR hydrogen fuel cell-powered, long-endurance AUVs. The result is a class of fully autonomous UUVs that can be produced cost-effectively at scale, with flexible energy/power options and payload capacity for high-priority missions.
Christine Judd, vice-president of Metron’s uncrewed systems division, believes their Resilient Mission Autonomy technology is distinguished from competitors’ offerings in two key areas.
“First, our approach to autonomy has always focused on communications-denied, navigationally challenged environments. Most competitors developed their autonomy with a human in the loop, where the platform calls for help if something goes wrong. We developed our software from the get-go without a human in the loop, building in onboard decision-making from the start.”
The second area of distinction is Metron’s 40-year history of delivering advanced software and sensor solutions that successfully manage uncertainty.
“Our ability to process and utilise real-time or near real-time sensor data in our active mission plan is different. Most people make a plan, start to execute it, and try to adjust it when the platform has to cope with unexpected events,” she says.
“Today, most autonomous software will abort, come to the surface and call for help when something unexpected occurs. Metron’s Resilient Mission Autonomy will make small adjustments throughout the mission – and there is a threshold to what that means – but if we encounter something above that threshold, we replan on the fly, at depth and in-situ from scratch without any human input, making the process more robust.”
Founded in 2001, Canadian company Cellula Robotics recently opened a US arm based in Houston. It has a portfolio of proven UUVs for mission-critical defence, civil and commercial operations, including in the offshore energy sector.
“Recently, Cellula expanded into hydrogen fuel cell-powered vehicles to extend the range and endurance of UUV operations,” says CEO Neil Manning. “For this partnership, Cellula’s Solus LR and XR vehicles will be integrated with Metron’s autonomy for specific customers in offshore energy and US defence.”
Solus XR is an extra-large uncrewed underwater vehicle (XLUUV) that measures 12 m long and 1.7 x 1.7 m in cross-section, displacing 25.5 t when submerged. It has a range of 5,000 km or an endurance of up to 45 days, depending on the mission.
The vehicle weighs less than 10 t in air, allowing standard dock cranes and small ships to handle it, and it fits into a standard, 40 ft shipping container, says Manning.
“Solus XR’s modular features are an important differentiator, especially as mission parameters change. Currently, the XR has flexible, standard noses and tails that can attach to mission-specific centre sections, while other modules housing extra hydrogen tanks can be attached underneath to increase the range to about 8,000 km,” he explains.
Both companies will conduct a series of in-water demonstrations for energy and defence customers this summer.
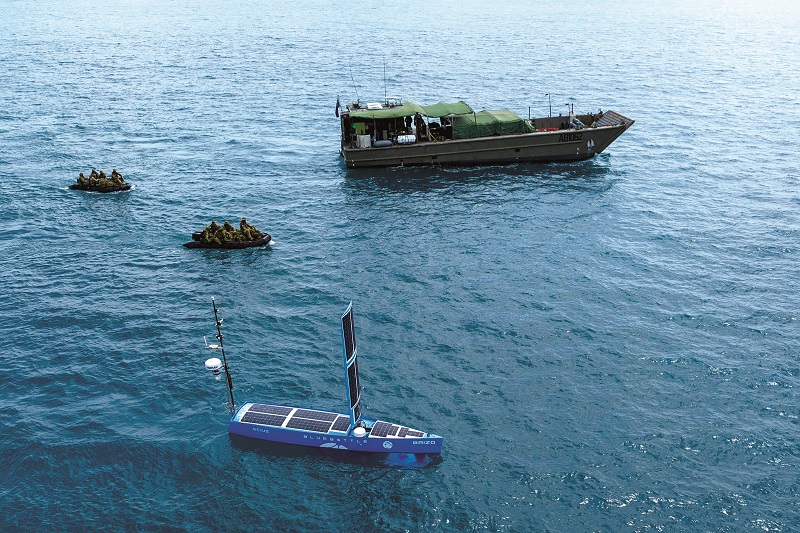
Ocius Technology discussed one of its Bluebottle solar-, sail- and wave-propelled USVs (previously detailed in issue 51) with a small, towed array sonar from autonomous maritime surveillance and offshore solutions provider ThayerMahan, a combination jointly developed by the two companies.
Ocius CEO Robert Dane says the 22 ft Bluebottle can be launched from a boat ramp in a remote area by local people and carry out a mission lasting 60-90 days at a “disruptively low” cost.
In operations based in northern Australia, Bluebottle has made 450-mile transits to Ashmore Reef near Indonesia, an area often transited by people smugglers. “We’ve been able to transit from Darwin, stay a month out there, and keep a continuous coverage of that island for about $3,000 a day, compared to the cost of a manned ship, which would be about $90,000 a day.”
Integration of the sonar array, called Outpost, increases the range at which the system can detect boats with noisy propellers, says Dane. “We can see something on radar at 5-10 nautical miles, but we can hear it at 20 nautical miles, which gives us an extra detection capability.”
The towed array consists of 100 m of 10 mm-diameter cable, which is normally installed with the winch on a boat’s transom in a package weighing about 150 kg. On the Bluebottle, however, the winch is fitted into the keel with the cable wrapped around a “bicycle wheel”, which deploys and retrieves it.
One of the two Bluebottles demonstrated at the show was deployed off Point Loma, about 16 nautical miles from the coast of San Diego, with its array at a depth of 250 ft monitoring marine traffic. A live feed from the USV brought the sonar waterfall display to a screen in the show’s demo area, revealing a number of strong contacts as distinct vertical lines on different bearings relative to the array.
“We’ve spent four days here now, and I can pretty confidently tell you that nothing has come in and out of San Diego Harbour without us at least knowing about it,” says Mike Varney, director of international programs at ThayerMahan.
Real-Time Innovations (RTI) discussed its new Observability tool for communication networks that enables developers to monitor network performance down to the health and behaviour of individual nodes on uncrewed vehicles, says Brian Senese, senior field applications engineer at RTI.
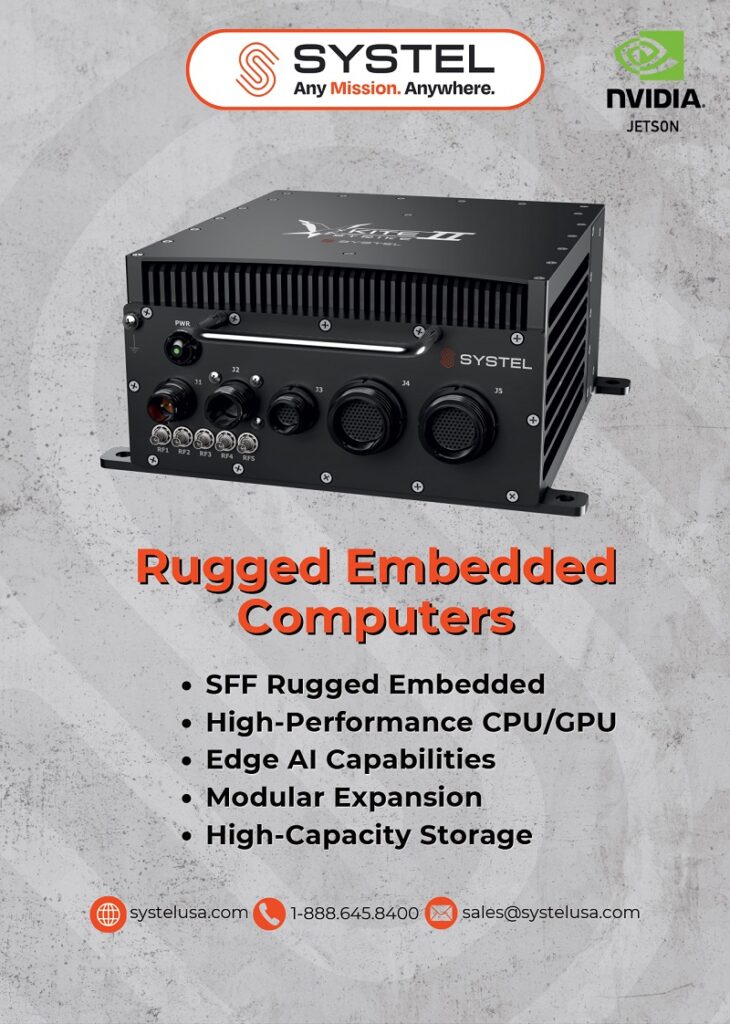
RTI describes its Observability Framework as a tool for understanding the current and past state of applications, empowering developers to identify and resolve potential system issues. Based on the Data Distribution Service (DDS) standard, it enables secure, reliable, real-time information exchange over large and diverse networks, including Lockheed Martin’s Aegis naval combat system.
DDS is the predominant standard for implementing mission-critical open architecture systems, enabling interoperability, portability, loose coupling and real-time quality of service assurance. RTI’s DDS solution offers broad support for programming languages, operating systems, processor architecture and network types, enabling it to integrate everything from sensors at the edge to track management in the cloud.
“When you have a complete DDS system up and running, observability is essential,” Senese says. “You’ve got to understand if a node has gone down, or if there’s a bottleneck or data obstruction, or another issue in your network. You can detect issues before they become critical.
“Additionally, RTI was key in developing the DDS specification for the DoD because they needed a resilient, transport-based technology to replace server-based naval systems. Observability was developed to collect telemetry and system health data available from DDS nodes by using a graphical dashboard, so information can be delivered intuitively.”
As customers prioritise different information, the dashboard is customisable. One key parameter is ‘liveliness’, which Senese likens to a heartbeat. “Each node on the network generates a heartbeat once a second or every five seconds – it’s a configurable parameter – to let all the other nodes know it is there,” he says.
The Observability tool detects this liveliness heartbeat and indicates whether a node is healthy.
“If it’s unhealthy, you will get a red indicator on a timeline saying there has been a problem for this period of time, for example,” Senese adds.
At the moment, the information is displayed graphically on a screen. “Somebody has to be paying attention,” Senese adds.
UPCOMING EVENTS
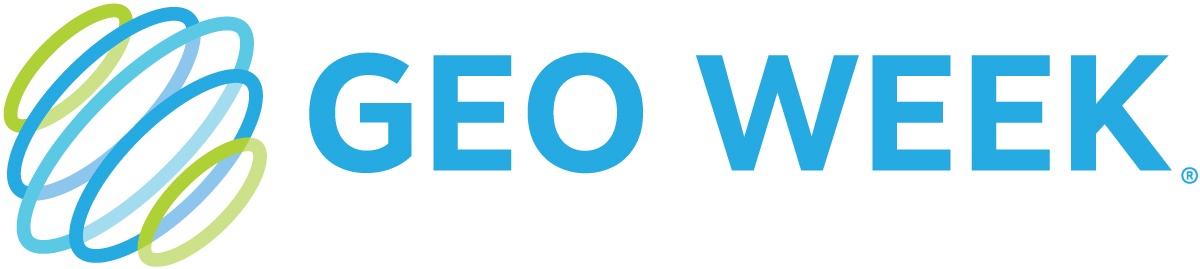
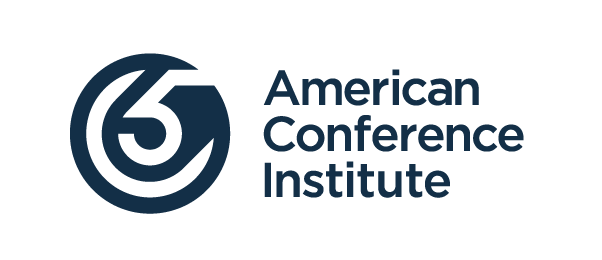
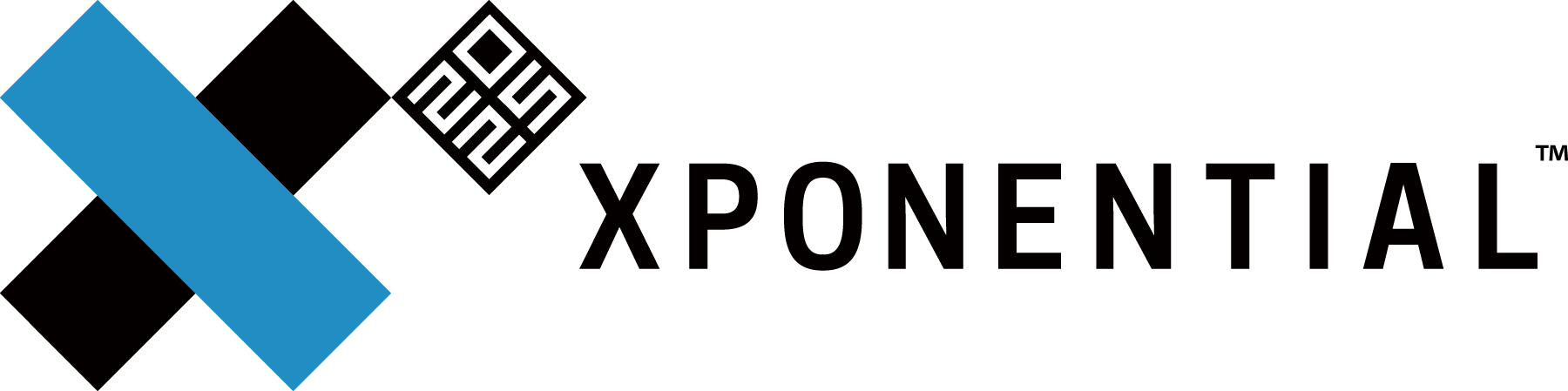
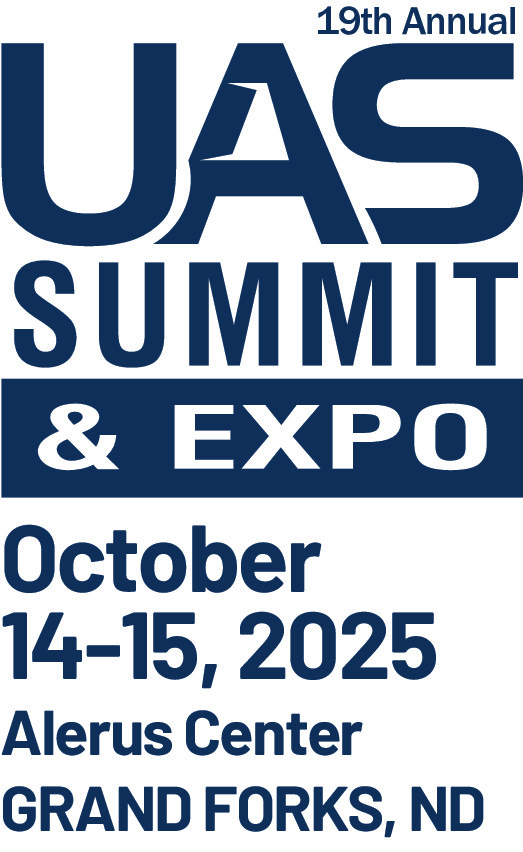
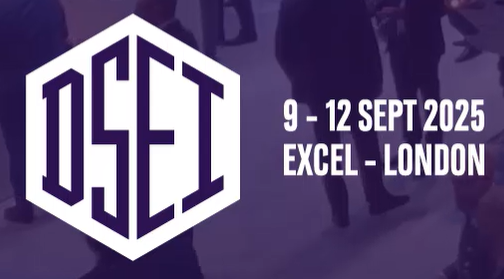
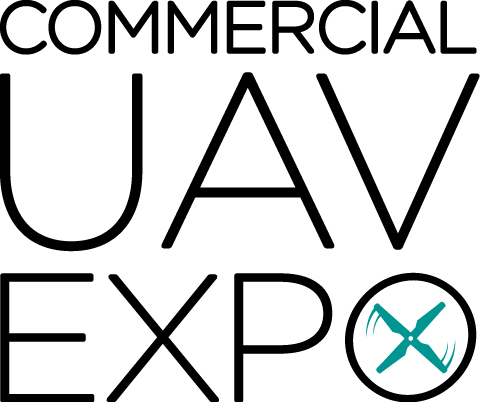
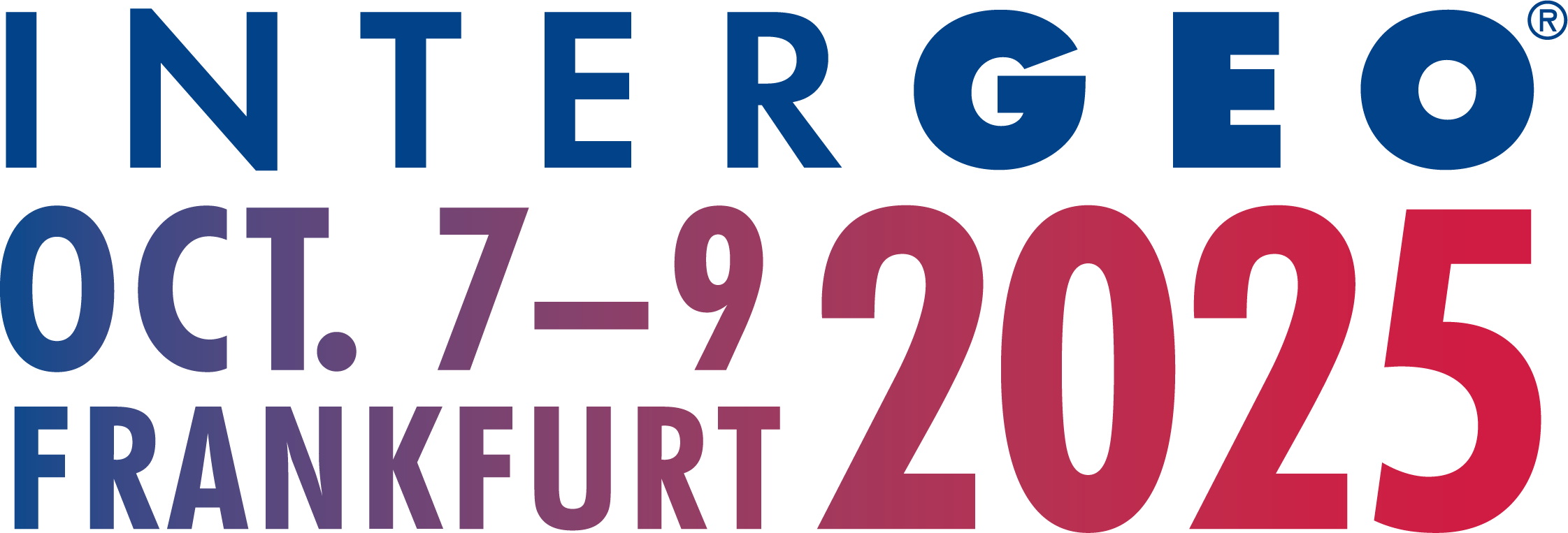
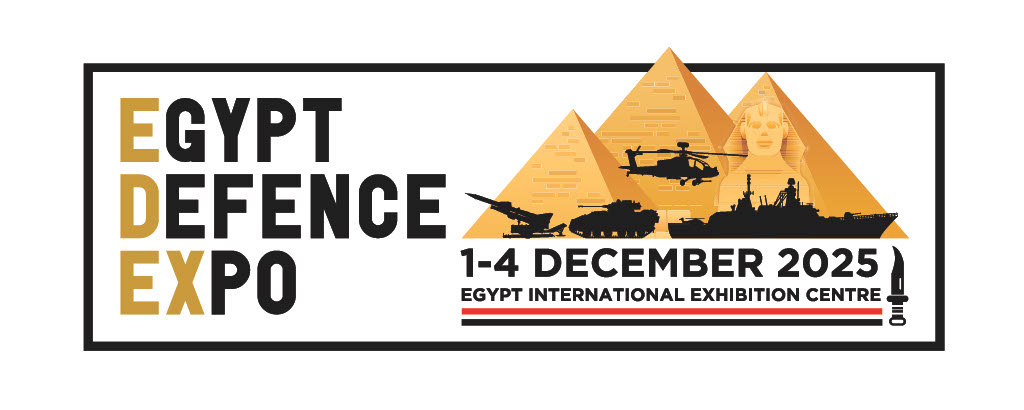
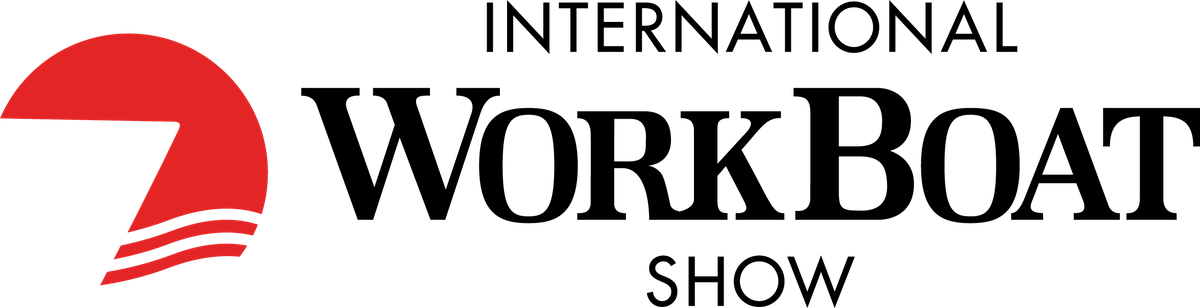
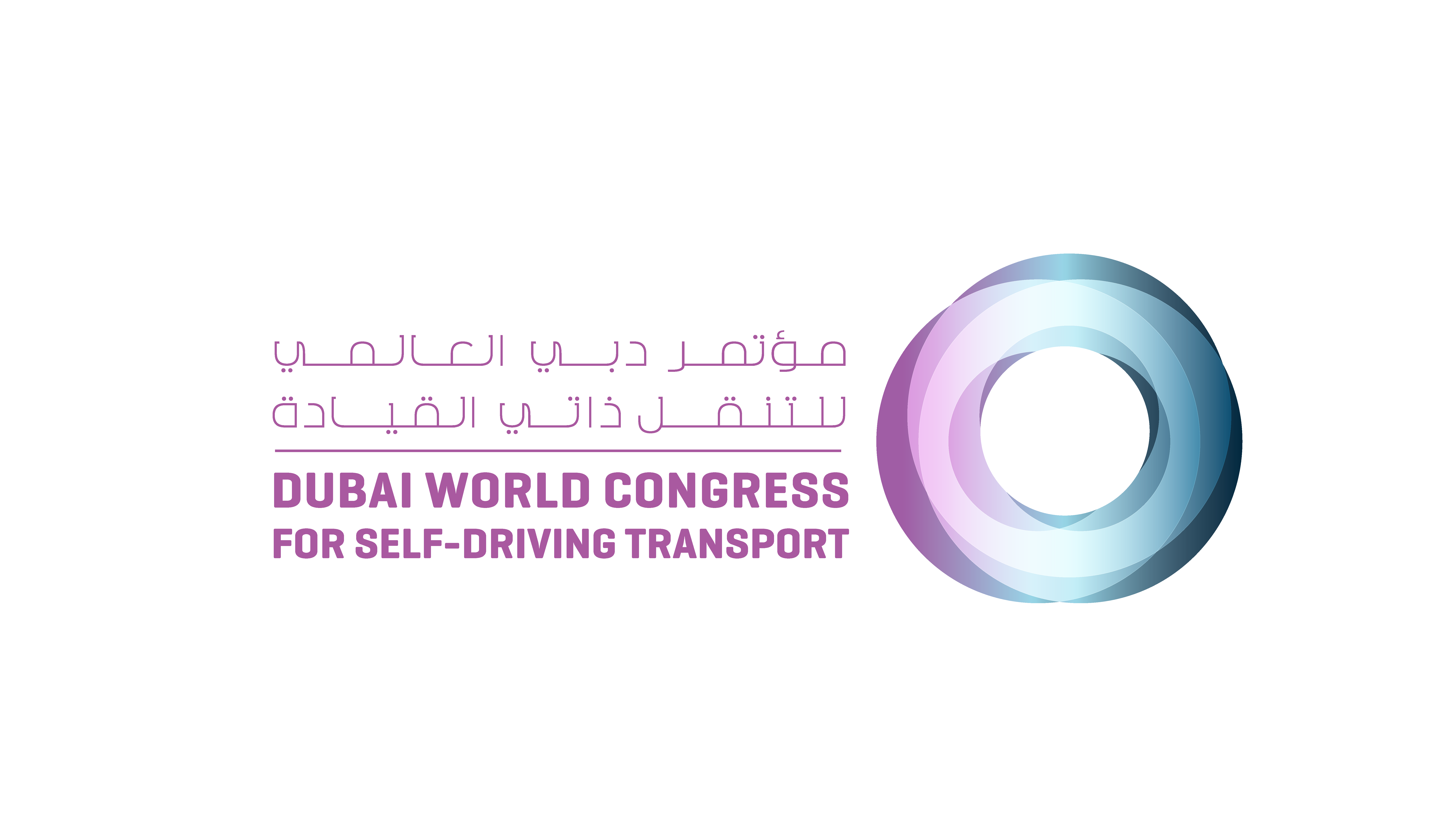

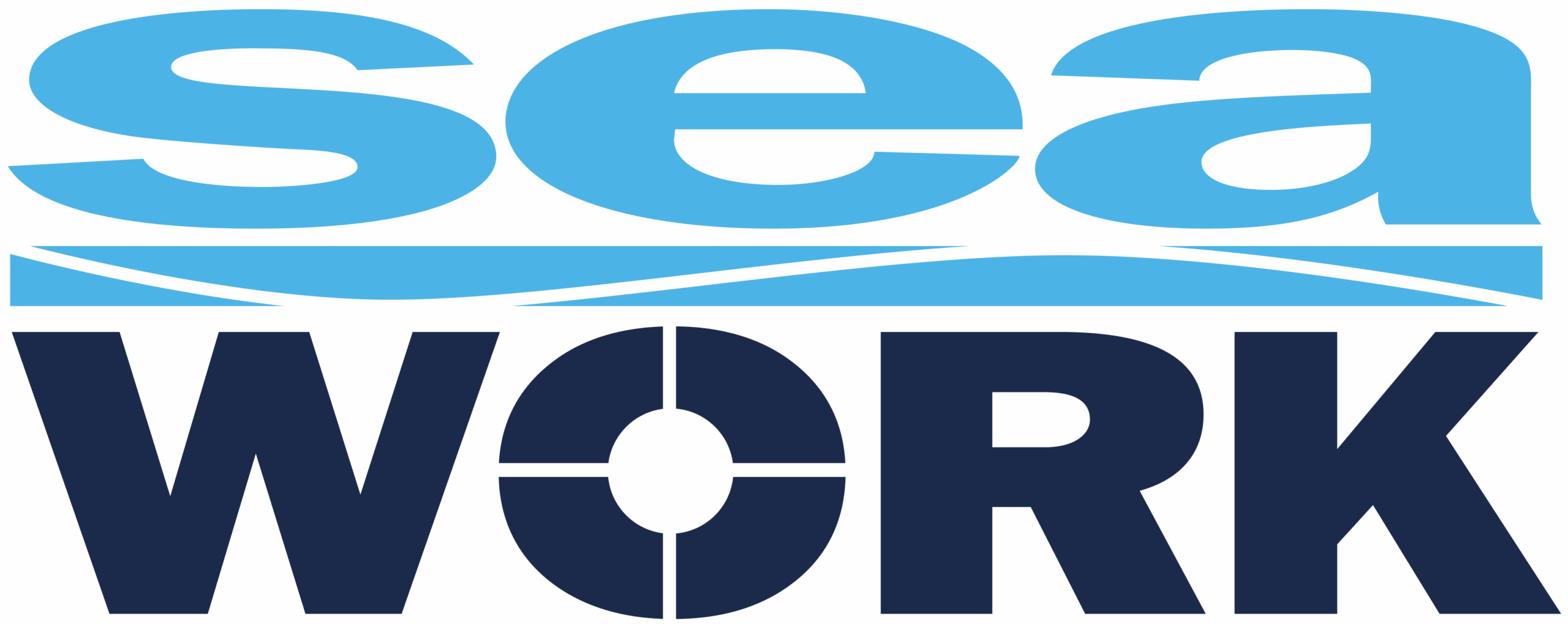