Xponential 2024 Part 1
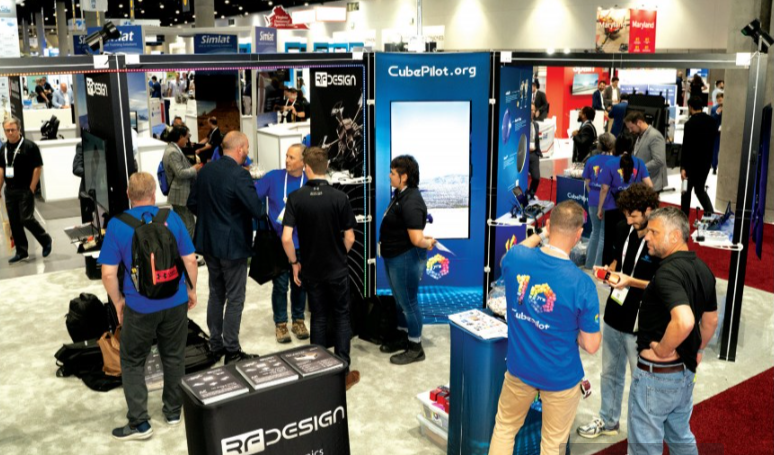
Rory Jackson considers innovations he saw in San Diego in this first of a two part report from Xponential 2024
Xponential in motion
Though California is already known as a major tech hub the world over, 2024 saw the ‘City in Motion’ of San Diego play host to hundreds of new tech companies from around the world, as AUVSI Xponential ran at the San Diego Convention Center from April 22 to April 25. With the uncrewed industry rapidly growing to meet demand from dozens of markets awakening to the capabilities and efficiencies that autonomous vehicles can bring them, a vast host of new products and innovations were unveiled – a selection of which we present here, in our first part of our report on Xponential 2024.
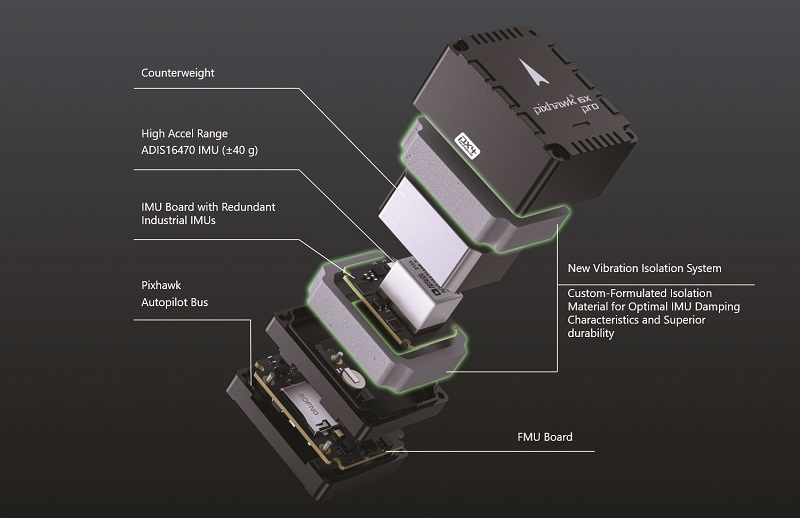
Holybro exhibited a range of new avionics products, including its new Pixhawk 6X Pro flight controller, as well as its Pixhawk Jetson Baseboard. The Pixhawk 6X Pro has an STM32 H753 processor, a triple redundant IMU, and dual redundant barometer. The main IMU onboard is the Analog Devices ADIS16470 Industrial IMU, which integrates an accelerometer with an acceleration range of ± 40 g.
The 6X Pro has also been engineered with a proprietary vibration isolation system, which forgoes traditional foams for a material formulated by Holybro specifically for flight control applications. Holybro claims that this new, stiffer vibration isolation is more durable, has a resonance frequency further away from a UAV’s vibration frequency, and is ideal for industrial and commercial UAV applications.
Holybro has also released a new version of its Pixhawk 6X, which has triple ICM-45686 IMUs. The ICM-45686 is a new IMU from TDK Invensense with a ±32 g acceleration range and that company’s BalancedGyro technology.
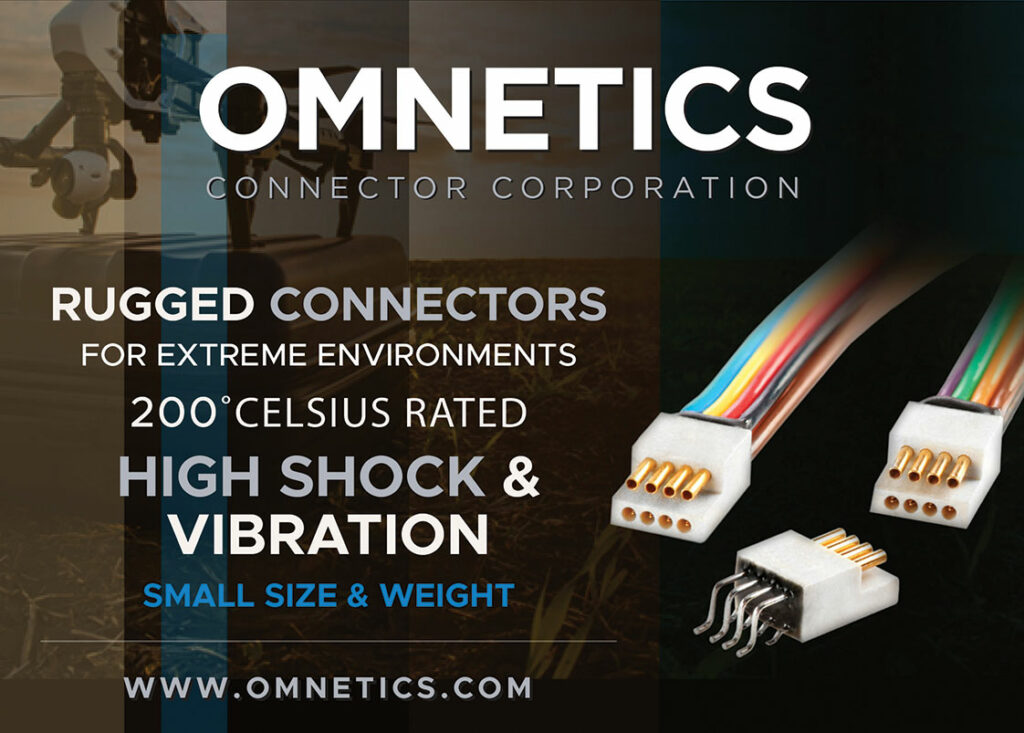
Both the Pixhawk 6X and 6X Pro follow the Pixhawk Autopilot Bus (PAB) open standards. “By following the PAB Standard, its connector allows it to plug into various carrier boards or baseboards, whether manufactured by us or by others,” said Vince Poon. “Then, our Pixhawk Jetson Baseboard integrates the Pixhawk and Nvidia Jetson Orin NX, all on one board; on the bottom are two M.2 Keys for Bluetooth, wi-fi, and SSD interfacing,” Poon continued.
“This baseboard is also built around the PAB standard, so theoretically, any flight controller unit that follows PAB can be swapped into it in place of the 6X Pro. The two systems are connected via CAN, UART, and Ethernet switch, and we’ve optimised it for developers who want to program an autopilot with AI functions like image recognition in a small form factor.”
Holybro also displayed its range of GNSS solutions, including its Mosaic-H dual-antenna RTK-GNSS. “When you rely on a magnetometer for heading, there’s a high chance of interference from, say, power lines or metallic structures; dual antenna GNSS heading doesn’t have that type of weakness,” Poon added. “It also has embedded anti-jamming and anti-spoofing capabilities programmed into the chip it’s built around.”
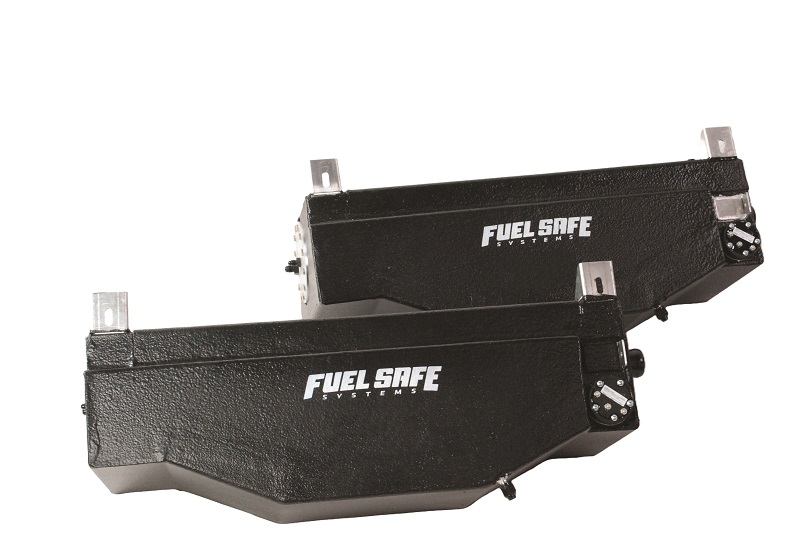
Fuel Safe Systems has developed a new material for making fuel tanks that are bulletproof (in a sense): this coating technology creates tank walls that self-seal following piercing ballistic strikes. “When the self-sealing coating takes a wound, it has a two-stage reaction,” Trevor Hart explained to us. “The first is an elastic reaction, in which molecularly the material wants to rebound back to where it was before the strike, and the second is a chemical reaction triggered by exposure to the fuel.
“The material is extremely incompatible with fuel, so it reacts by swelling up, and that closes the wound very rapidly after fuel passes through, after which the exposure is minimised and the swelling stops.”
As well as optimising the reaction time and rate of swelling, Fuel Safe Systems has also worked closely on reducing the weight of the coating, to ensure the fuel-saving gained for users in environments with firing risks is not significantly offset by reduced flight time. That involved roughly one-and-half years of testing and changing materials, including formulating a proprietary chemical structure.
“The coating is available today, and we’ll customise tanks for the different calibre rounds that UAV operators might need to protect against – obviously, the smaller the calibre, the lighter the system can be because the coating doesn’t have to be as thick ,” Hart noted.
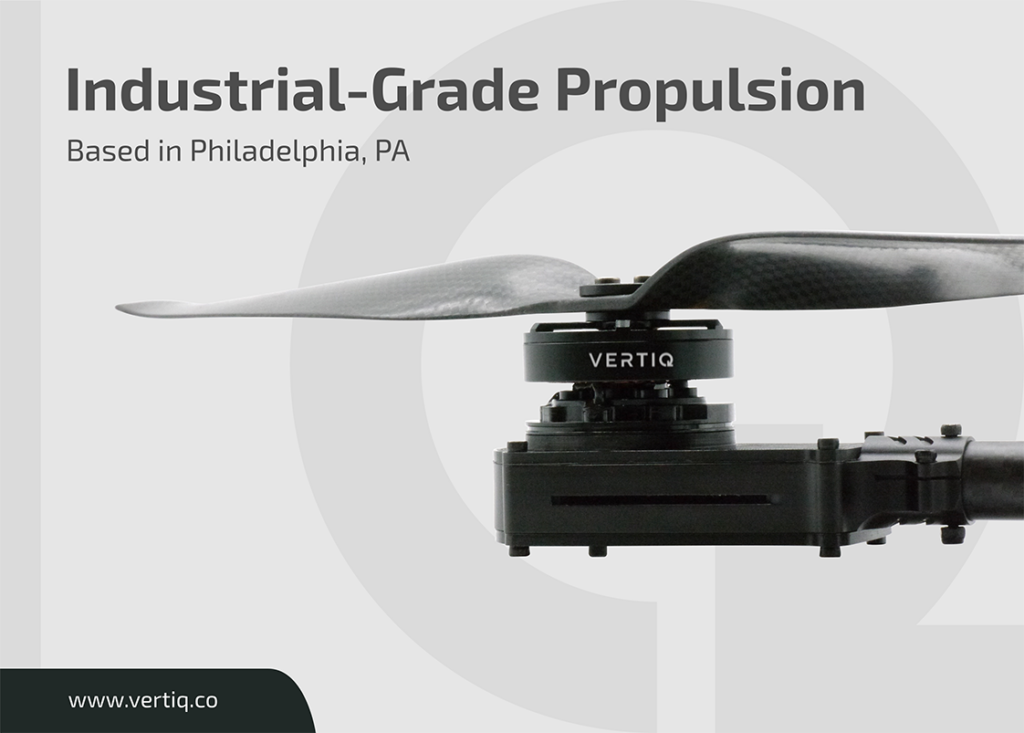
Cobra AERO has unveiled a new form of ignition that it anticipates will make its two-stroke engines considerably more efficient. “The technology is a turbulent jet ignition process, which is trademarked in our configuration as JetFire, though it’s something used across Formula One at the moment,” explained Sean Hilbert. “Every Formula One car is powered by a pre-chamber ignition system of some sort, but JetFire specifically is optimised for mitigating the poor fuel efficiency of small, lightweight two-strokes.”
Though pre-chambers have been associated with poor efficiency due to the added surface area they bring into combustion chambers (among other factors), JetFire’s performance is controlled, via modern hardware and software means, in a way that brings about 50% indicated thermal efficiency in Cobra’s tests thus far.
“That’s hydrogen fuel cell-levels of efficiency, but without the degradation of a fuel cell, or the inefficiency of passing a fuel cell’s electricity through DC/DCs and a battery before getting it into a motor shaft,” Hilbert said.
The original concept for Cobra Aero’s JetFire arose roughly two years ago, from discussions between Hilbert and Dr. Harold Schock at Michigan State University. Dr Schock had had an idea he was researching that potentially held interest for Hilbert at the time (Hilbert having queried Dr. Schock about efficient means of running engines on hydrogen, as a means of discovering new roles or places for ICEs in a sustainability-focused world).
“It’s still in the research phases, running on a single-cylinder test engine at the moment and in a lot of simulation software, but we think it’s going to bring a lot of efficiency in a few years when it’s ready for production, and it’ll be able to run with a wide variety of fuels, including hydrogen,” Hilbert concluded.
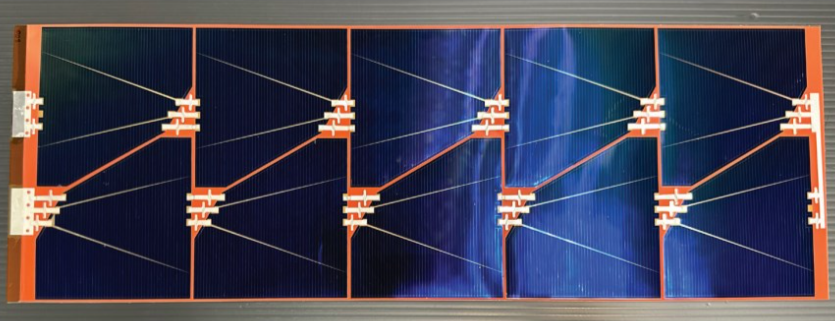
MicroLink Devices is embarking on space qualification of its multi-junction solar cells. With expected completion in 2025, the US government is funding the company to fulfil a need for solar arrays in space applications such as LEO satellites. “We have locked in our solar cell structure, and we have performed radiation testing to verify robustness,” said Ray Chan.
“We will begin testing out the cell interconnects through extended thermal cycling tests, to simulate the conditions that LEO satellites experience as they orbit the planet every 90 minutes. The satellite and solar arrays go through extreme hot and cold temperatures many times each day, such that a seven or eight year mission can mean up to 50,000 thermal cycles for the solar array.”
Each of the tests above and more will be broken down into multiple batches to validate that the cells perform consistently. They will continue to be the AlInGaP-GaAs-InGaAs triple-junction cell MicroLink is known for, but with an encapsulation scheme suited for the vacuum, thermal, and radiation conditions of space. A unique coverglass-free approach is used in assembling the space solar power modules.
LEO satellite applications include new generation GNSS, communications, and observation constellations, and other satellite formats such as cubesats are possible.
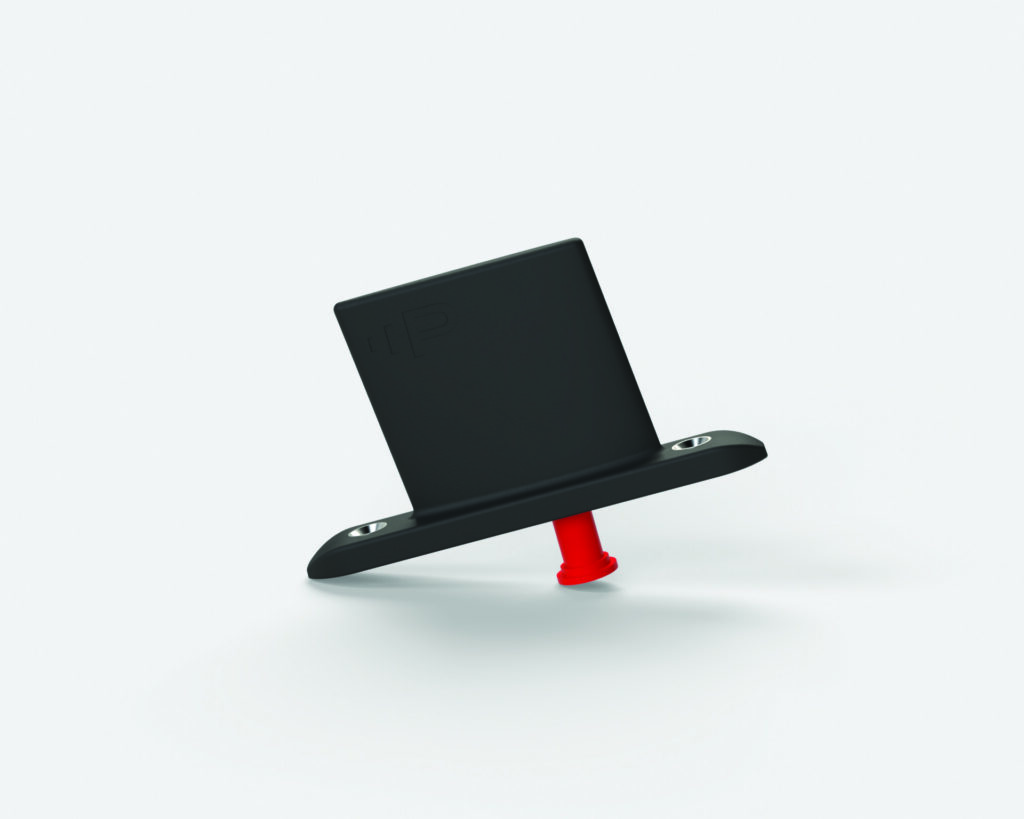
PIDSO was walking the aisles of the show to discuss the SDI.015-00A, a new dual-band blade antenna it has launched, which is capable of transmitting and receiving in the S- and C-bands. “As well as designing it for high gain, we’ve also focused on its weight and power efficiency to suit it to UAV and RPA requirements, bringing it down to a weight of approximately 26 g,” said Manuel Marbach.
“It’s ideal for broadband applications, functioning in the S-band at 2.2-2.5 GHz and in the C-band at 4.4-4.94 GHz; we’ve picked those frequency bands to especially optimise it for working with Silvus’ Streamcaster radios, which we’ve been told by customers – and validated in our own tests – work really well.”
Also launched recently by PIDSO is a new L-band antenna, SDI.013-00A, configured for 1-1.5 GHz, which the company optimised to be as small as possible (a key challenge as lower frequencies typically entail a bigger antenna). It is also working on LTE antennas, starting at 700 MHz as well as a dual-band blade antenna for L-Band and S-Band.
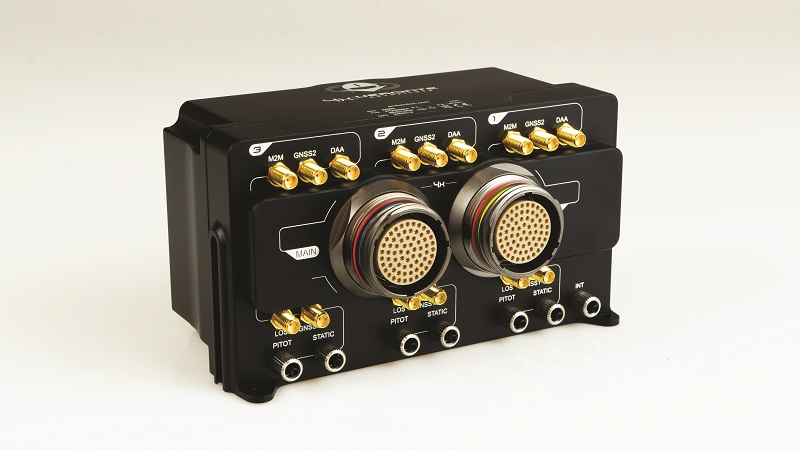
Embention is continuing to update its Veronte Autopilot line, recently adding the Veronte DRX alongside the 1x and 4x autopilots in this series. The DRX brings a distributed redundancy architecture to the mix, intended for robust and safe eVTOL control, and maximising its certifiability across future eVTOL and BVLOS UAV operations.
“The Veronte autopilot architecture has redundancy in almost all of the internal sensors, with three IMUs, two GNSS receivers, two static pressure sensors and three magnetometers – along with one pitot tube input,” said Ángel Monllor Hurtado. “Additionally, we provide for the optional integration of an internal ADS-B transponder, or for a remote ID device, into the autopilot enclosure. All this, together with an internal 4G module for BLOS communications through a secure network powered by Veronte Cloud.”
The Veronte 4x is built with three complete Veronte 1x systems plus an arbitration computer that monitors the three, so that if a failure condition is detected in one of their cores or sensors, the arbiter removes the connection to the failed part.
“We avoid commonality of failure modes by using dissimilar sensors, and a fourth full dissimilar autopilot core can also be integrated. This versatility permits Veronte to communicate with any third-party autopilot, with Veronte itself serving as a failsafe core for certifiability and keeping the fourth core as the main control unit,” Monllor Hurtado added.
“We’ve also split the old Veronte management software into different software tools, including one for PID configuration, one for sensor calibration, and one for uncrewed vehicle operations. This helps provide operators and different engineers with specialised tools best suited to what they need to focus on.”
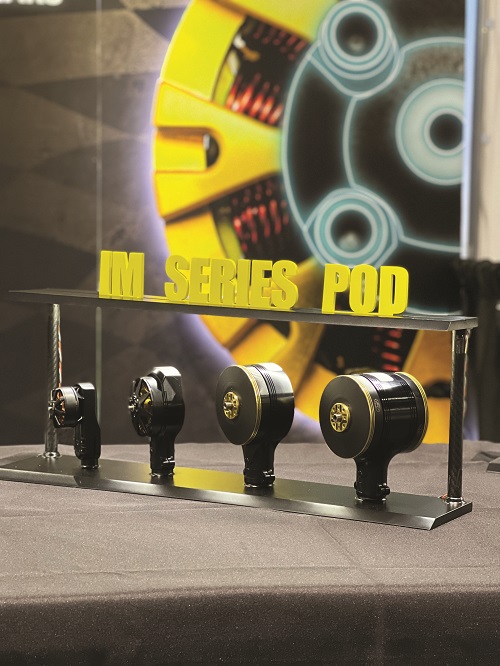
Scorpion Power System Ltd exhibited its ranges of motors and ESCs, with different families of products for varying UAV applications, and debuted its IM (Industrial Multicopter) series of electric motors and IM-series Pods (incorporating a motor, ESC and tube mount). These are currently available in power outputs from 1.5 to 3.5 kW.
“The IM Motors Pods have full telemetry capabilities, and can be operated via DroneCAN, UAVCAN or our own SProto CAN protocol, as well as traditional PWM, One Short, Multishot, D-shot, and they run in different sizes for different UAVs, for pairing with propellers from 15 to 30 inch diameters,” said Kyle Dahl.
“They pair with our Legatus ESCs which use all western components and are manufactured in Taiwan, and utilise our proprietary FOC motor control algorithm. We spent four years developing our own algorithm, rather than use a stock chipset algorithm, to have complete control over the motor driving algorithm and ensure we could retain high flexibility and adjustability to tune it for different application requirements.
“Normal FOC algorithms require specific tuning to work with a fixed motor, whereas ours is motor agnostic, meaning it can work with any motor with little to no adjustment. They also often come with an rpm-limit; ours is about twice as high as the average, and can also achieve about 15% more top-end torque, with up to 12% more energy efficiency. Combining the Legatus ESC with our IM-series motor can realistically achieve up to 20% increase in overall flight efficiency.”
The company also showcased its new Tribunus III ESCs, which it has engineered closely for heat transfer and hence thermal management of its PCBs. Also its A Series of motors which are optimised for fixed wing UAVs, and its HK5 motors which are for helicopter or high speed UAVs, and have recently been optimised with a new internal structure for improved cooling.
“As well as having all these systems ranging from 500 W to 10,000 W, COTS and in-stock, we can customise for different performance requirements, Kv ratings, connectors, engravings, and more,” Dahl added.
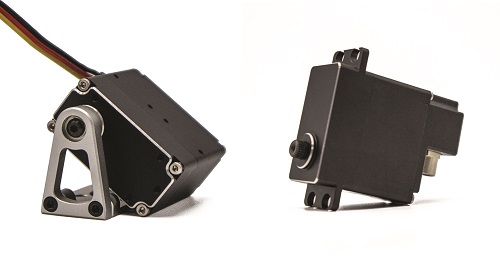
Hitec has customised some new servos with improved, application-specific functions, based on actuator designs from its MDB961 series. “Like the 961 servos, these are engineered with high torque, waterproof and hardened cases, and hardened steel gears, but one of the new units has a robotic servo-type bracket – an axial bracket, for applications where the servo needs to take higher axial loads,” said Shawn Spiker
“A lot of requests for that come from tiltrotor engineers, who are mounting the motor-propeller drive straight onto the servo. The axial bracket supports the servo arm on both sides, takes a lot of pressure off of it, and handles gyroscopic forces well. It’s also in-demand from animatronics engineers for use in arms, knees and other robotic limb joints that need to handle higher loads.”
Another of the new servos comes with a US-made circular MA connector, per request from several US-based companies eyeing Blue- and Green-UAS ratings. Such servos are designed with 32 V architectures to enable handling of the bigger, shielded cabling of such connectors.
Gladiator Technologies was walking the aisles to discuss its GA50, a new chip-based accelerometer introduced in early 2024. “It’s an open-loop accelerometer, and comes in multiple g-range variants, from 5 g all the way up to 70 g,” said Eric Yates. “We’re looking for opportunities to integrate it with other inertial products, particularly groups looking to build new tactical systems.”
At 70 g, the GA50 has a bandwidth of 300 Hz, a one year bias repeatability of 7 mg, and a bias stability of 180 µg. At 5 g, its bandwidth is 250 Hz, its bias repeatability is 0.8 mg, and its bias stability is 60 µg. Across all g-ranges, it weighs just under 0.7 g, measures 8.9 X 8.9 x 3.2 mm, consumes just under 13 mA (on a 3.3 V DC power supply) and can function in temperatures from -50˚C to +85˚C.
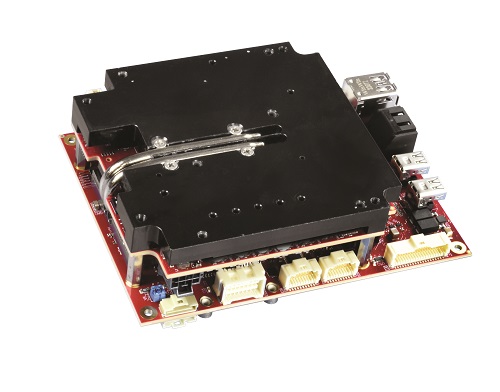
Aircraft Electronic Engineering GmbH (AEE – a subsidiary of Volz Servos) presented its Next-generation Flight Control Computer (NFCC), which it has co-developed with the Technical University of Munich. “AEE is an EASA-certified production, maintenance, and alternative design organisation, focused especially on commercial avionics,” Nils Schlautmann told us. “To that end we’ve created the NFCC using similar approaches and technologies to some of our other products, which have been flown on vehicles of 700 kg+ MTOW already,”
“We’ve designed it to be extremely flexible in terms of interfaces – both the types and total number available – for customers that want to get started using it, but maybe don’t yet know 100% what kinds of protocols or channels they want.”
The NFCC hence can come with either two D38999 or EN4165 connectors, providing up to eight CAN interfaces, up to 16 ARINC 429 Rx ports, up to 8 ARINC 429 Tx ports, 8 serial ports (including RS-232, -422 and -485), and up to 32 discrete inputs as well as 16 discrete outputs – per lane, depending on the chosen configuration.
“It’s available with COM-MON [Command and Monitor] or Dual Lane architectures; though you can also configure it to only monitor,” Schlautmann added. “It has twin T1024 or optionally T1042 CPU modules , with direct Ethernet for connecting with them.”
UXV Technologies has developed a soldier-borne compute module (SBCM) designed for both dismounted soldier applications and vehicle mounting.
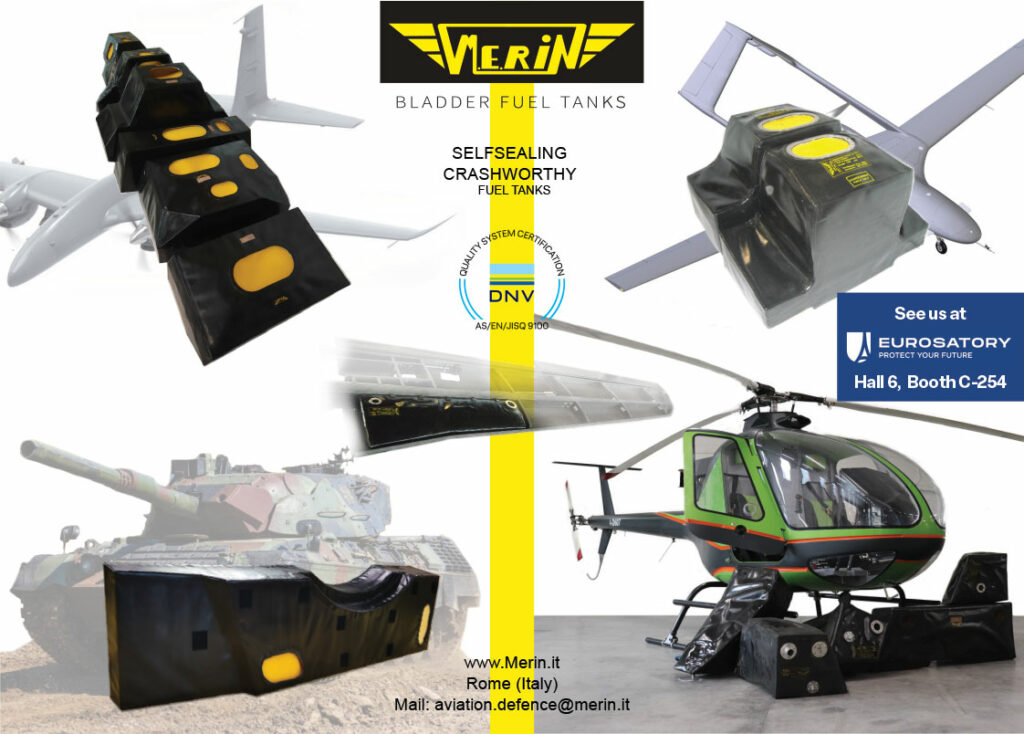
“The SBCM is built around an Nvidia Jetson Xavier NX computer to process raw data being downlinked, such as data from a gimbal or other mission payload. This allows soldiers to utilize the information as quickly as possible mid-mission,” explained Frederik Bergenfelt Friis of UXV Technologies.
“Combined with the Soldier Robotics Controller [SRoC], the SBCM can connect multiple radios to control several vehicles simultaneously. It can also switch between different sensors to process and display intelligence data from various locations as needed.”
He added that the module is also a Nett Warrior hub compatible system thanks to UXV Technologies’ Swappable Radio Modules ecosystem, which enables it to integrate directly with sensors, process data immediately, and make it remotely accessible to soldiers equipped with the SRoC or other personnel and vehicles via a mesh network.
Additional versions of the soldier-borne compute module are in development that will run on the Jetson Orin NX.
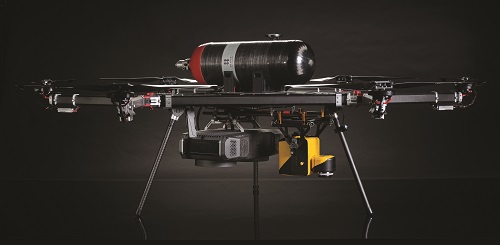
Intelligent Energy is continuing to optimise and manufacture its larger fuel cells for UAV applications, showcasing its work in a demonstrator UAV integrating its 2.4 kW hydrogen fuel cell. “We’ve taken an airframe from Gryphon Dynamics in South Korea, a 3.7 kg YellowScan Navigator Lidar, along with COTS parts for couplings and joints,” noted Andy Kelly. “With our 2.4 kW fuel cell the system can fly 2.5 hours, compared with 30 minutes on battery alone. It flies with a 10.8 litre fuel tank, storing hydrogen pressurised to 350 bar.”
As of writing, the 2.4 kW fuel cell is in rolling production and available as a COTS system, with a stock of several hundred maintained continuously. The company has capacity to ramp up production, which it anticipates will become necessary once BVLOS certification standards for UAV operations make 2.5 hour flights over the horizon legally permissible.
“There are a few operators flying with Part 107 BVLOS waivers, to trial pipeline inspection, power line monitoring, and offshore flights. However, regulations will decide when things really take off, and a hydrogen fuel cell is needed for regular, routine BVLOS flights with a low-maintenance electric powertrain,” Kelly commented.
MP Antenna showcased its multipolarised antenna technology. This is manually-constructed and -tuned to passively transmit or receive in more than one geometric orientation, giving in dynamic environments an advantage over standard, singularly-polarised antennas.
“We manufacture and design our antennas from the ground-up in Elyria, Ohio, tuning our unique 3D elements to capture wider frequency ranges along with different polarisations than what’s possible with conventional PCB or dipole antennas,” explained Brent Miller.
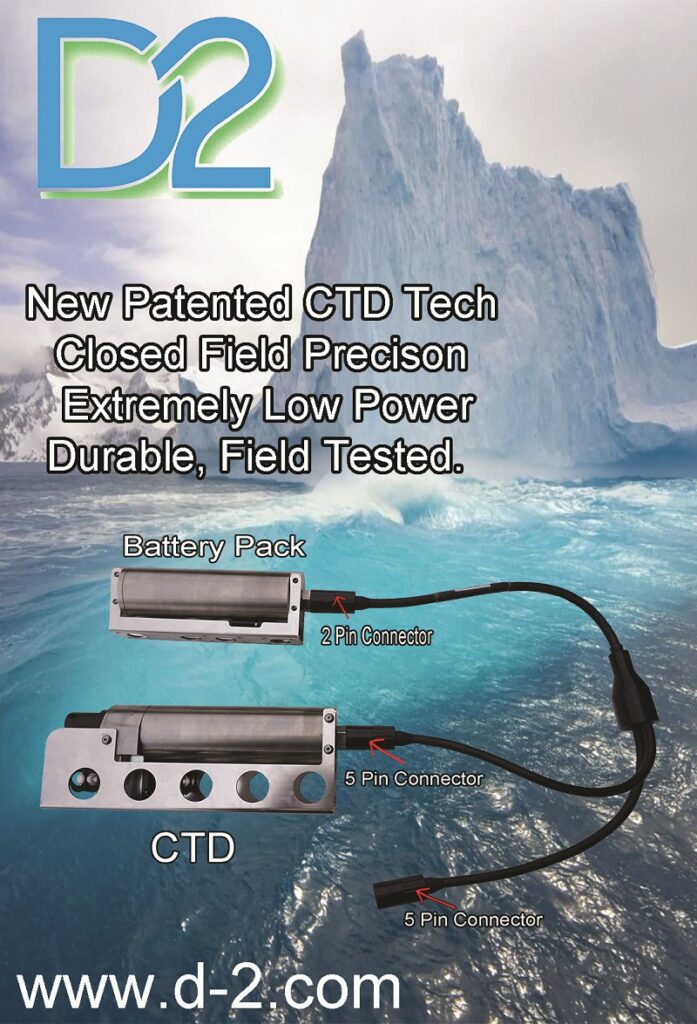
“Our proprietary approach to designing and manufacturing our antenna configurations in house allows for complete customisation to meet customer’s requirements while keeping lead time at a minimum. We provide our standard model lines but also provide custom solutions whether it be for frequency range, gain, mounting location, or any specific customer requirement.”
VersaLogic announced its new Swift embedded computer. The system comes with a six-core Xeon processor from Intel, up to 32 GB of memory, 128 GB of NVME storage, two Gigabit Ethernet ports, and numerous USB ports. “The especially new thing about Swift compared with some of our other releases is that we’ve designed for more expansion sockets than usual; rather than have just one or two at most, Swift has three: one Mini PCIe socket and two different M.2s,” explained Chris Miller.
“The extra sockets allow end-users to take our general-purpose computer and apply it at the edge to add extra functionalities they need for their uncrewed vehicles, without having to stack boards to do it. For example, we’ve got users that are working on installing 5G systems onto this board, and we have others using APUs such as those using Intel’s Movidius chips, to try and expand their AI inferencing capabilities.”
The Swift weighs 476 g, measures 95 x 125 x 41 mm, and consumes 26 W in standard operations, operating over a 10-15 V DC supply. It functions in temperatures from -40° to +85°C and is rated to MIL-STD-202H for shock and vibration.
On Swift’s development origins, Miller explains, “When we released our Sabertooth product, we’d developed it as a two-board set, and the upper board – which we called the ‘Saber’ module – had the CPU, high-speed signalling, and the memory. The lower board carried the NVME storage and slower speed I/O, using a custom connector.
“Swift is very similar to our Sabertooth and Eagle products but with a completely redone base board, to bring in the additional storage and expansion options. The biggest challenge in the work to make Swift was space; it’s always a huge effort to realise the layout you want, to get the routing correct, to bring the PCI signalling off the connectors and down to the base board and make it all fit. It’s physically difficult to get all the sockets where you need them on a board this small.”
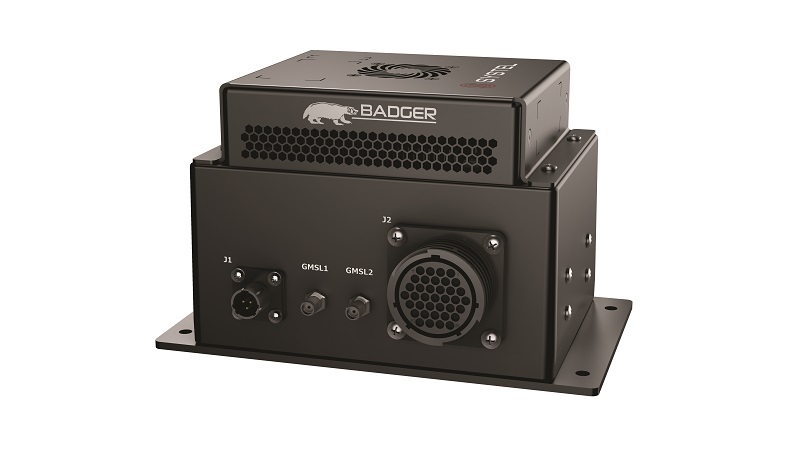
Systel attended the show to unveil its new Badger rugged computer, developed as an industrial-grade edge AI processing solution. “We wanted to bring something with the edge computing power of a Jetson Orin NX, as per our Sparrow product, but price it affordably for commercial and industrial markets, and still have it be a ruggedised, IP67-rated system,” explained Brian Russell.
In addition to integrating the Orin NX, the Badger is also designed with native Gigabit Multimedia Serial Link, a protocol popular among cameras and other sensors in commercial autonomy, and a wi-fi modem for integrations requiring wireless downlink from or uplink to the system.
“Badger’s first big engineering challenge was finding the right form factor of COTS chassis to design it around: using a COTS chassis rather than a custom designed and milled metal chassis was critical for keeping unit costs down,” Russell said.
“The next extensive challenge was designing a carrier board that would have all the capabilities we wanted. For that, we actually worked with Connect Tech, who were very helpful with bringing out the signals and other things we wanted from the carrier board. For DoD products, we generally design our own carrier boards but to optimise the system for cost and speed, and other specs we wanted, Connect Tech were incredibly helpful.”
The lion’s share of ruggedisation work revolved around trialling different cooling fans, at varying speeds, to maximise the system’s thermal tolerances and cooling efficiency when running at max performance in hot environments. Validation tests of the system have passed muster, and production is expected to commence in summer 2024.
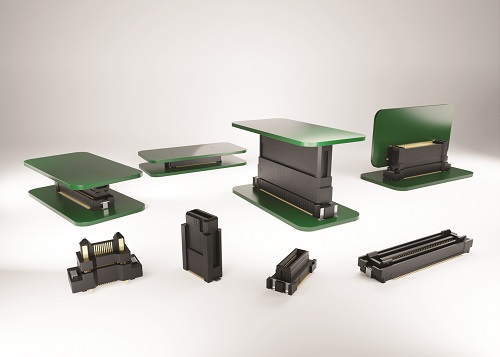
Harwin displayed many solutions including its new Flecto Floating Connectors series, which are designed for enabling multiple board-to-board connectors on a single PCB. “With traditional board-to-board rigid connectors, you run into issues with tolerance stack-ups, because even sub-millimetre misalignment risks damaging connectors, putting stress on the board, and similar problems,” explained Ben Neumann.
“In Flecto, the male connector can float slightly in place, up to 0.5 mm in most of the series – though some offer greater floating range – allowing the board-to-board connection to function as intended, even with minor misalignments, without putting stress on the connector or board.”
The floating capability stems from the connectors being designed around spring-type contacts, which gives a measure of elasticity and provides structural load distribution away from the pins and joints of each connector.
The Flecto connectors are available in a variety of forms, including three different pitches (0.5 mm, 0.635 mm and 0.8 mm), pin counts of up to 160 contacts, various stacking heights, and with signal or power connections (including 3 A pins for a 0.5 mm pitch design).
Sky Power has developed a reduction gearbox for integration with its SP-210 and SP-275 two-stroke engines. “The gearbox is engineered with a 3:1 reduction ratio, and the first tests have been completed with a 33×40 variable-pitch propeller,” said Karsten Schudt. “Running the engines at 9000 rpm, we got 3000 rpm at the propeller output as well as immense torque, to the point that we found the propeller is still too small to fully utilise the engine’s torque gain.”
The gearbox adds 1.5 kg to the engine, which itself weighs 6-10 kg depending on configuration, in return for tripling the torque output. Though designed for a customer-specific request, Sky Power is considering adapting the gearbox design to work on its other two-strokes as well as its rotary engines.
“We’ve also developed a heavy fuel version of our SP-180 SRE rotary hybrid engine, for running on JP-8 or Jet-A1, and optimised it to now produce up to 22 kW shaft power and 15 kW electrical power, exactly like our gasoline engine,” Schudt added.
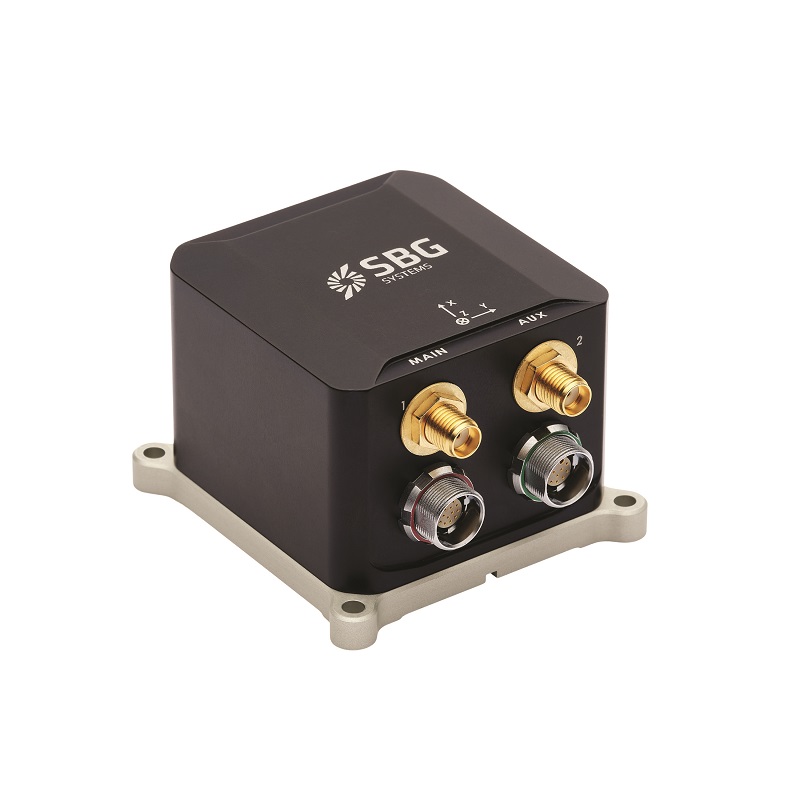
SBG Systems has commenced production of its new Ekinox Micro compact INS, which consists broadly of its Quanta OEM board product, encased in an IP68-rated case. “It has dual antenna GNSS, giving heading and differential GNSS readings, with equal accuracy to our bigger Ekinox products, but in a smaller package to suit smaller vehicle platforms requiring tighter SWaP parameters,” said Jack Mawson.
“Compared with the OEM product, it can be mounted much more easily thanks to its enclosure making it tolerant of wider environments and vibration profiles. It also has larger connectors and wires, so it’s easier to work with; you can solder the connectors, or use DB-9 connectors, rather than being stuck with board-mount connectors.”
The 165 g Ekinox Micro can operate in temperatures from -40˚C to +71˚C, and is rated to Mil-STD-810H for vibration and shock tolerance, with a calculated MTBF of 246,000 hours. “It’s also designed with more I/Os than some of our other smaller units, so you can put more auxiliary inputs into it, and you can do more data syncing,” Mawson added.
Vertiq attended AUVSI to showcase its line of high performance electric motors and ESCs for UAS applications, and discussed with us much of the engineering that has gone into optimising the efficiency, responsiveness, and reliability of their propulsion systems.
“We integrate the motor and motor controller together and embed a position sensor inside that package. The sensor reads the orientation of the magnetic field generated by a magnet in the shaft of the motor and feeds that information into our control loop,” Jon Broome explained.
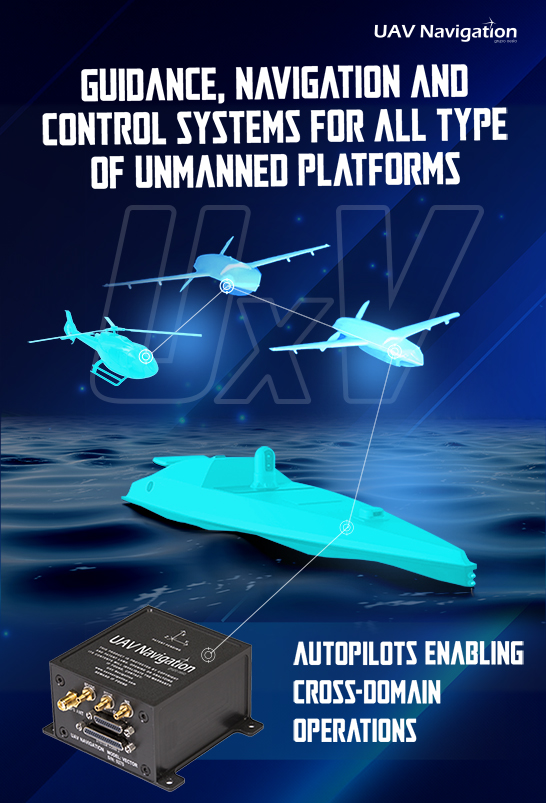
“By knowing the rotor’s exact position, we can do some really interesting calibration and control techniques to optimise performance. We can make propulsion systems 5-10% more efficient, as well as smoother, quieter, and twice as fast in response time. We’ve also built in many more safety and reliability protocols compared to conventional BLDC motors and ESCs.”
Currently, the company’s largest available solution is its 81-08 Module, a motor-ESC package designed for driving propellers of 20-34 in (50.8-86.36 cm) diameters on UAS weighing up to 25 kg. Its smallest solution is the 23-06 Module, which is designed to spin 5-7 in (12.7-17.78 cm) propellers and UAS weighing 1-2 kg.
Seven electric motor modules have been unveiled by the company (five available now, the rest to become available within the next six months). These modules cover the size range in between the 23-06 and 81-08 Modules, as well as including a 81-17 Module, which will become its most powerful commercially available product when it is released.
All of Vertiq’s new products are second generation ‘G2’ modules, which will allow UAS manufacturers to attach add-ons (including custom connectors, covers to increase IP rating, LEDs for FAA certification, and more) to the core motor and ESC. By tailoring the propulsion solution to the exact needs of the vehicle, UAV companies can both take advantage of Vertiq’s high end technology while customising it to optimise integration and capabilities.
One of the biggest issues with UAV motors and ESCs is thermal management. “We approach this challenge on two fronts, in the design stage and in operation. We design the motors to shed as much heat as possible, and the tight pairing of the motor and ESC allows us to create a highly accurate thermal model of the entire propulsion system during flight using a temperature sensor on the ESC,” Broome adds.
By measuring the ESC temperature and modelling the coil temperature, Vertiq’s modules can prevent the motors from overheating and inform the operator that the vehicle should be landed to prevent a crash.
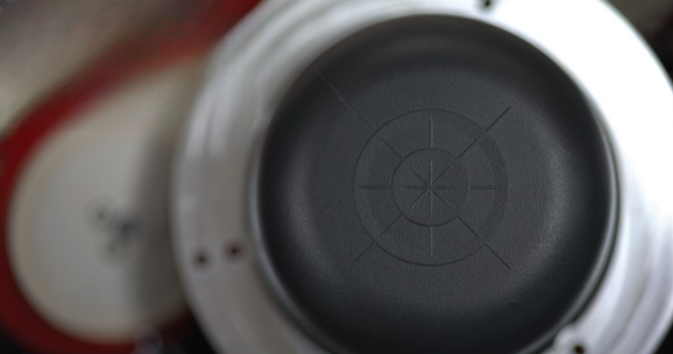
Calian launched several new GNSS antenna products, one of which was a miniaturised version of the VeroStar technology, the full band SSL990XF. With the introduction of Galileo’s new High Accuracy Service (HAS) providing GNSS corrections, full-band GNSS coverage has become highly desired.
“The SSL990XF antenna element inside the enclosure is a lightweight, miniaturised version of our VeroStar mini antenna,” said Joseph Botros at Calian. “It features a four-petal element rather than the distinctive eight of the VeroStar, has a gain of about 3 dB at zenith over the entire GNSS spectrum, and a low roll off of about 6-8 dB from zenith to horizon, while also maintaining good axial ratio near horizon. This enables good multipath mitigation and good tracking of low elevation satellites.
“These features make it very useful for receiving L-band corrections, especially for those operating uncrewed systems in the far northern or southern hemisphere. In this case geostationary satellites are seen very low on the horizon and as a result the received signal is very weak. We’ve also pared the weight down to 88 g, or about 75 g without the ground plane.”
The antenna’s enclosure is IP67-rated, though Calian is currently working on IP69K certification, which most of its antennas have. The mechanical team has also optimised its curved shape for handling and distributing stresses efficiently, making it a robust antenna.
Calian also recently released its low profile helical, the HC990XF; like the SSL990XF it is a full-band GNSS antenna including coverage of Galileo HAS. The low profile helical HC990XF antenna does not need a ground plane, and weighs in at 45 g. It too is IP67-rated with IP69K rating expected in the future.
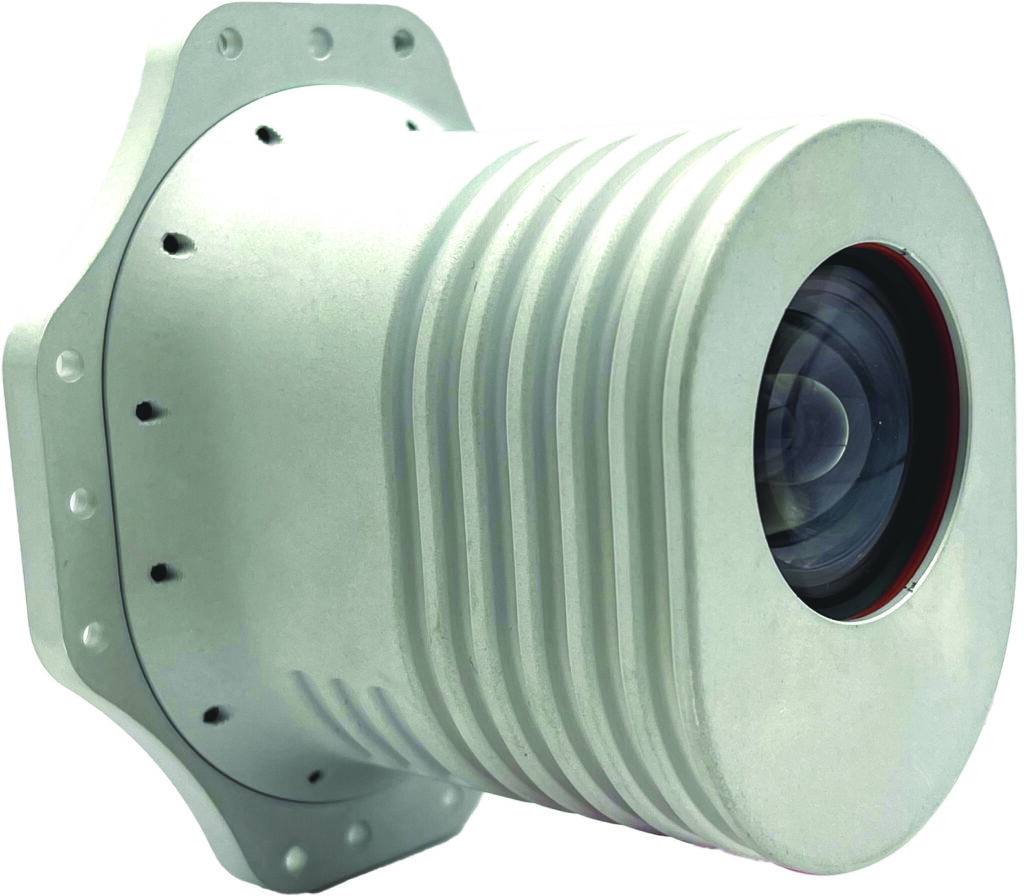
Inertial Labs attended the show to exhibit its growing ecosystem of modular navigation solutions and sensor fusion capabilities. “Good navigation starts with a good IMU; Inertial Labs develops IMUs and recently added the Kernel-201 with 0.5 degrees per hour gyro bias in-run stability and tactical grade accelerometer as the core of our small size INS,” explained Jamie Marraccini.
“We’ve been heavily focused for the last year or two on building-out an ecosystem of aiding-data sources for feeding critical external information into users’ INSs. This comes in addition to core data from things like its IMU, barometer, magnetometer, and GNSS receiver, to create a more complete and robust system for navigating in GNSS-denied environments.
“Some of those external sources are computer vision modules, airspeed sensors, air data computers, alternative navigation receivers – from sources like LEO satellites – radio TOF systems, and one of the latest we’ve integrated is a controlled reception pattern antenna (CRPA) product, which helps mitigate jamming for much larger mission portions than what was previously possible.”
When customers approach Inertial Labs to add a new external aiding sensor to one of their INSs, the company first investigates the quality and type of data that would be yielded, for instance how accurate they might be when used for position or velocity updates. Subsequently, they examine the feasibility and extent of cooperation with the aiding sensor manufacturer (such as sharing of interface control documents or anything else needed for extracting the necessary data from the system).
“Something like a TOF radio would be more challenging just to get the TOF data out of it, but something like a CRPA is relatively simple and plug-and-play, despite being complex systems themselves,” Marraccini said. “To develop our computer vision, we first had to tightly integrate and calibrate our camera sensor so that dewarping and lever arms were accounted for in outputs, then we had to write the software – though we’ve also made allowances for third parties to write their own software, activate it and licence it within our module if they prefer. We also offer our system with NVidia processors all the way down to much lighter Linux processors.”
Mejzlik is continuing to develop its new hot-press production line, anticipated to greatly increase the rate and consistency of carbon propeller manufacturing. “The first versions of the hot press machine produced props with a 100% scrap rate, but we’ve advanced to just an 8% scrap rate, and further decreasing it; doing so involves optimising how we lay-up the propeller materials, discovering which ones don’t bond correctly, examining why some batches come with voids in the material, and other factors,” said Tomas Mejzlik Jr.
“As one example of the parameters involved: our foam core technology has to be pressed with very precise temperatures, pressures and timing. If you press too much a little early on, for instance, the epoxy resin won’t have liquidised enough, and the core gets crushed.”
Extensive scanning of props taken from the hot press (including ultrasound to observe internal voids and cracks and 3D to measure the dimensional tolerances and bending) is yielding critical data for Mejzlik to understand the tunings required to stabilise and optimise the process. The company’s engineers are also investigating ways to cut away excess, overflowed resin using the press itself, saving time over having to post-trim overflows.
The company has also recently finished a custom project for an undisclosed number of carbon propellers measuring 3 m in diameter, now delivered to its customer (an eVTOL manufacturer), to be certified by them. The project took approximately a year, and the manufacturing was performed in compliance with EASA CS-P standards on propeller integrity.
“That involved CNC-machining a 3.5 m block for a mould, accounting closely for how the material would expand or shrink in different conditions throughout the production stages, controlling for those conditions across our workshops, and accounting in the design for bird strikes,” Mejzlik Jr continues.
“There’s a spar in the front so that if a bird impacts, it only disrupts a small area, and we’re investigating how to apply this design feature into our normal-sized propellers too – all this stuff that’s normal in general and commercial aviation is quickly becoming normal for UAVs.”
In serving different aircraft industries, Mejzlik is also working with new materials, one of which is a spread tow fabric; this is a thinner, more durable carbon fibre than others available, and the company anticipates making thinner and either stronger or lighter blades with them.
“We’re making a new propeller using the spread tow which weighs under a gram; it’s less drape-able than other fabrics, so for complex shapes it’s challenging to use, and it’s expensive, but the properties of the material make it potentially very valuable in some specialist applications,” Mejzlik Jr added.
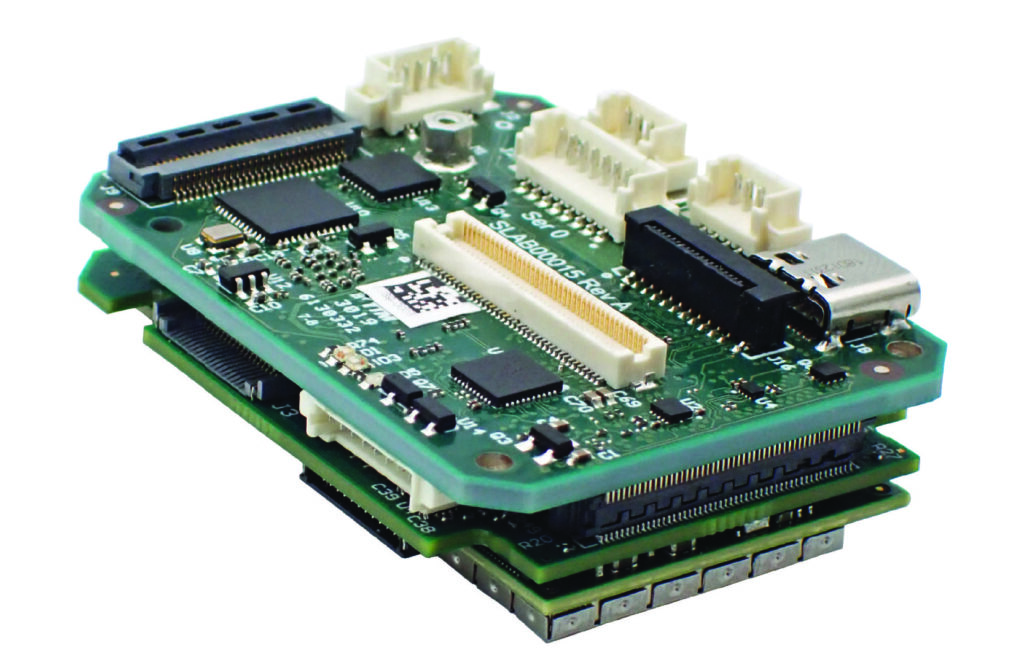
SightLine Applications has launched its new 4100-OEM video processor, its most powerful solution to date, and one capable of processing and streaming video to 4Kp30 quality. “It has the same interface control document and mostly the same form factor as our previous 4000-OEM product, making it easy for customers to drop-in replace the 4000-OEM without reconfiguring their power or software – the 4100-OEM is just 2 mm taller than its predecessor,” explained Hanni Wehrman.
“It integrates a newer more powerful Qualcomm processor with dedicated hardware for AI processing, so we’re planning on doing more AI-powered functions with it, and potentially three simultaneous channels through it, as a lot of customers have been asking about doing that, and it certainly has the processing power for it.”
The 4100-OEM can process and stream two video channels simultaneously at 1080p30. It is also designed with four serial ports (though a MIPI-Input adapter can now be connected, which would add three more as well as GPIOs), an I2C interface, and Ethernet. It weighs 29.7 g, measures 50.5 x 38.1 x 16.5 mm, and consumes less than 5 W in normal operations.
SightLine has also updated its 1750-OEM video processor with a second channel, following customer requests for a version capable of outputting two simultaneous streams. When running both streams at once, they can output video quality to 720p30 (if just one channel is streamed, it can provide 1080p30 video).
Both the 4100-OEM and 1750-OEM are engineered for H.264 and H.265 encoding, with three digital video inputs (one MIPI, one USB 3.0 and one parallel digital and camera adapter).
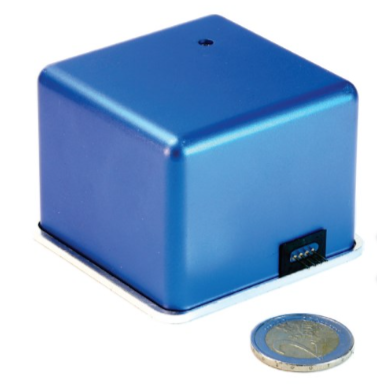
Fizoptika Malta has updated its U173D FOG-based IMU with more powerful accelerometers, to give it a higher g-range capability.
“It now has a range of 50 g, as opposed to our other products which have a range of 10 g; this improves its capacity in gimbal stabilisation as well as some short-term navigation applications,” said Arthur Tua. The system continues to use the same SWaP-optimised FOGs as before for angular rate, which have a bandwidth of 1 kHz, an input range of 300˚/s and a bias of 1˚/hr. The new accelerometers have a bias stability of 50 µg and a bandwidth of 800 Hz.
UPCOMING EVENTS
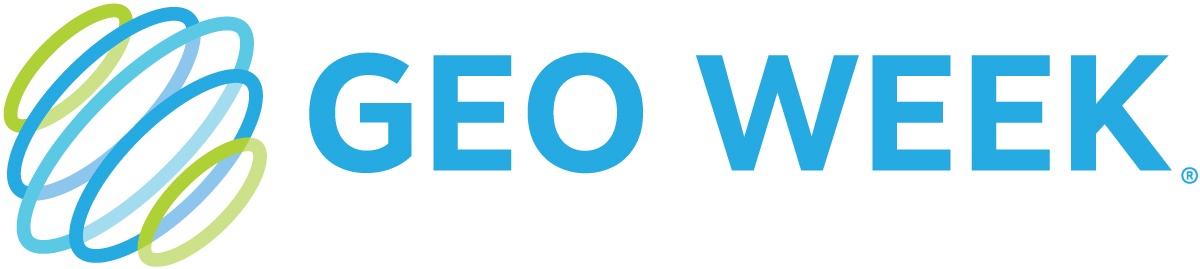
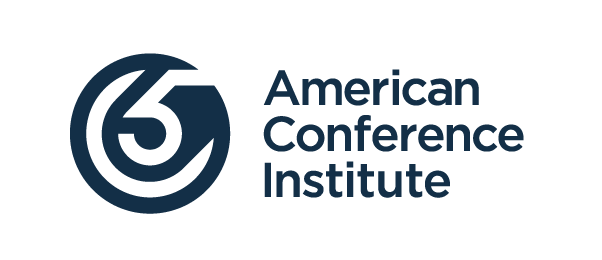
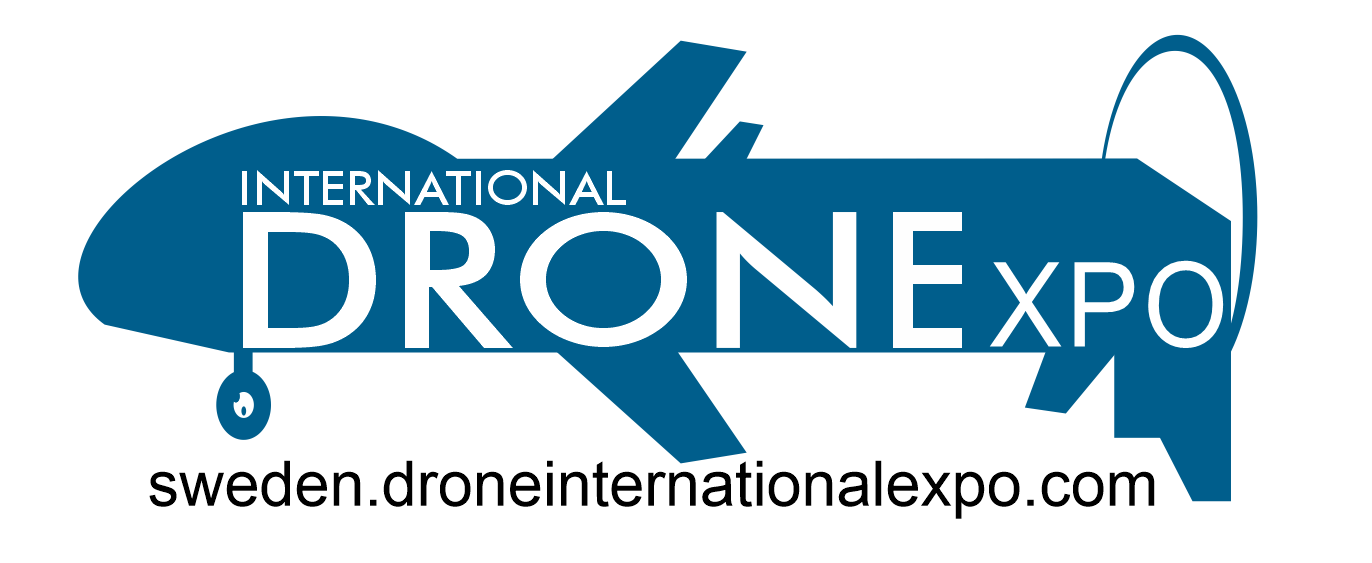
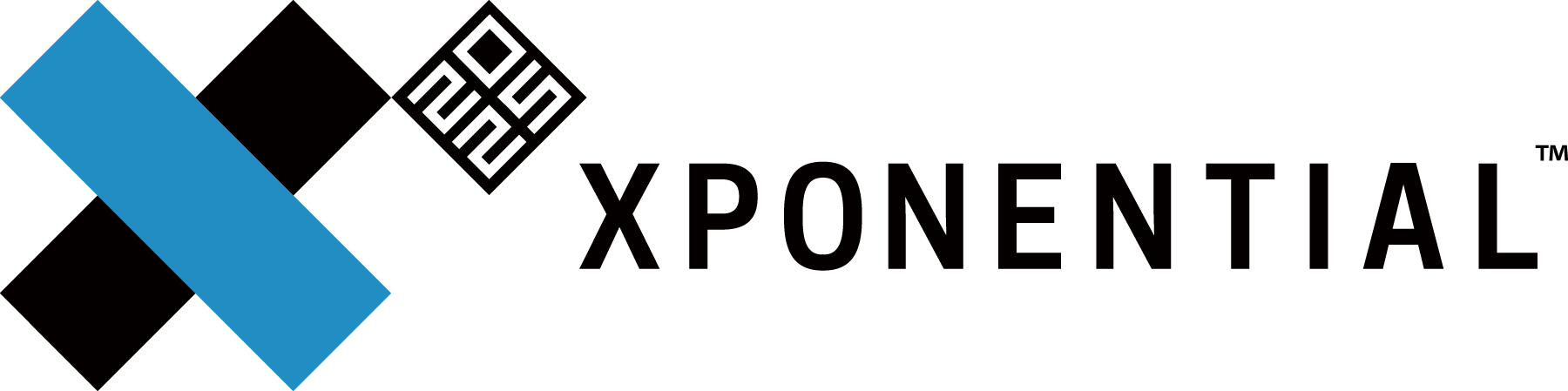
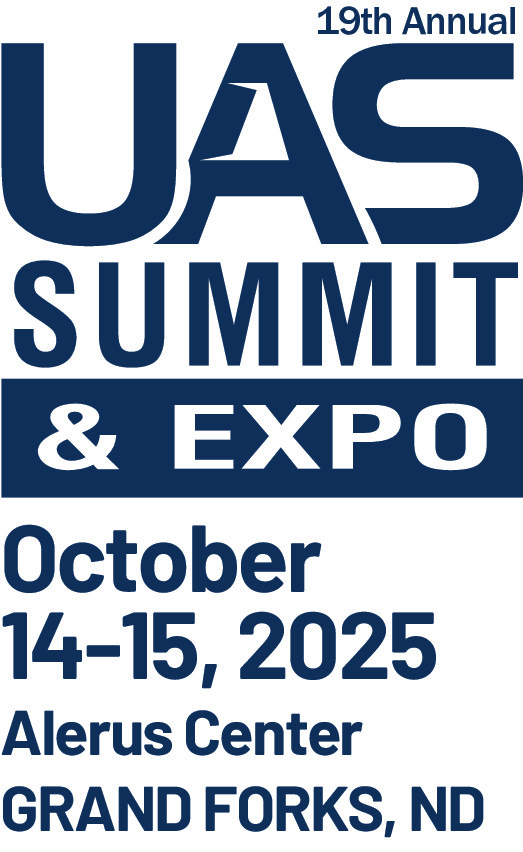

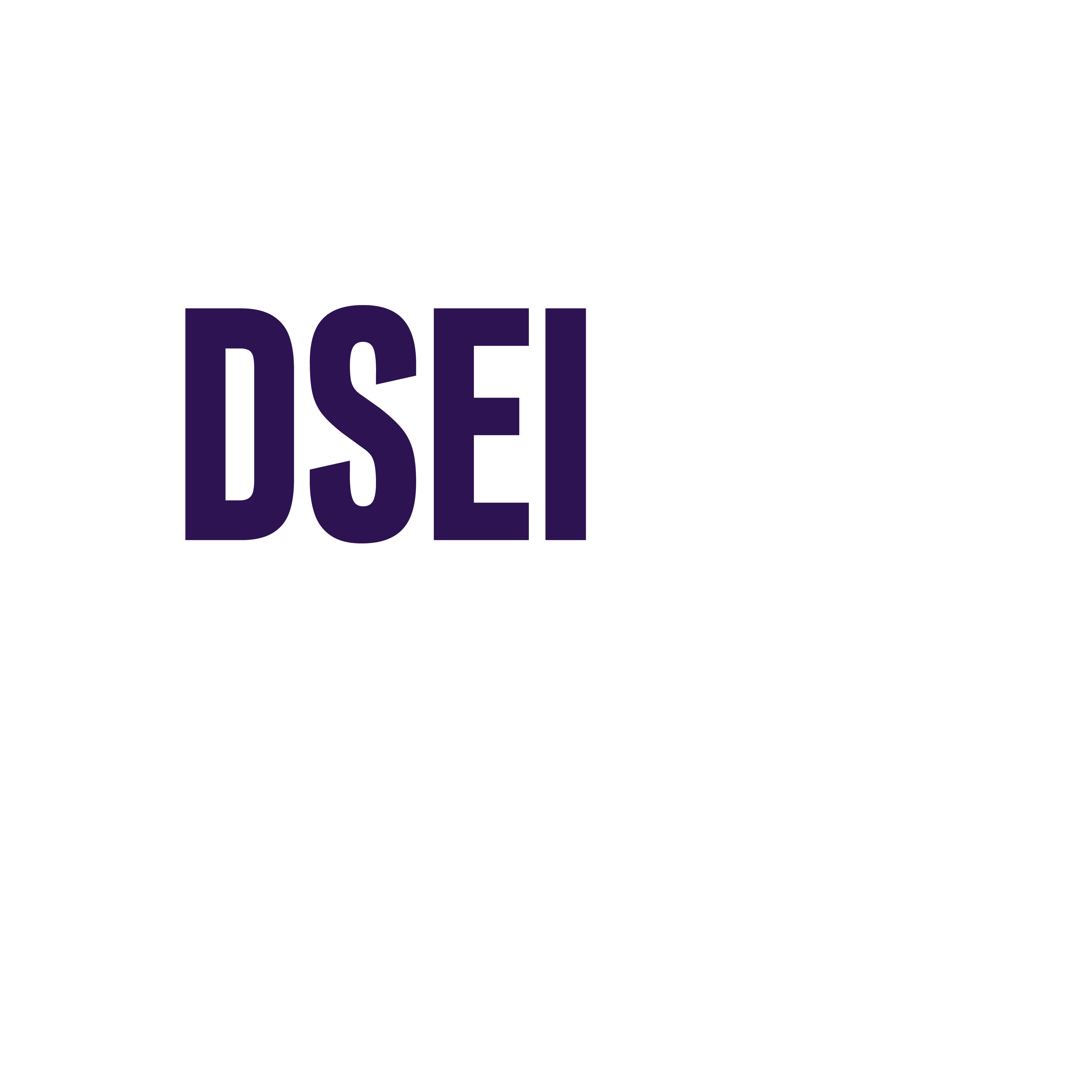
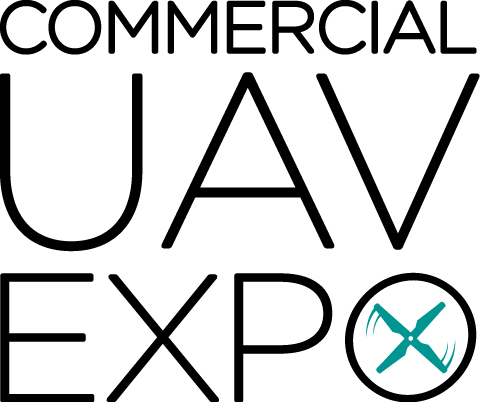
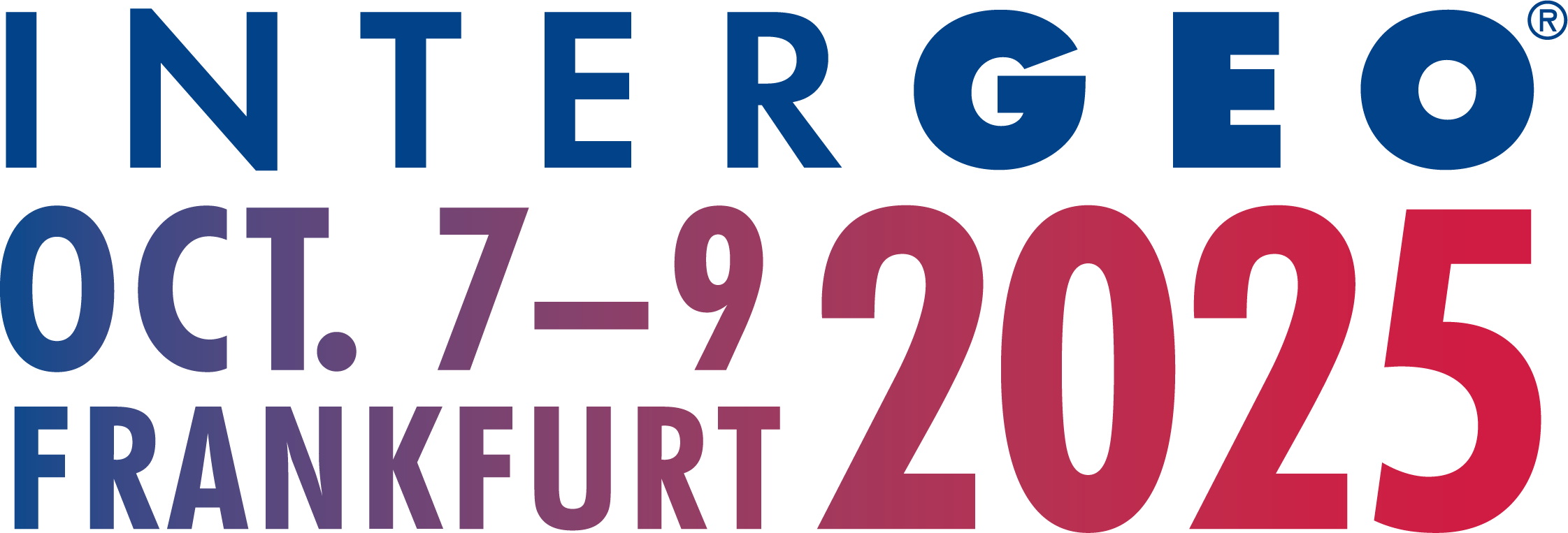
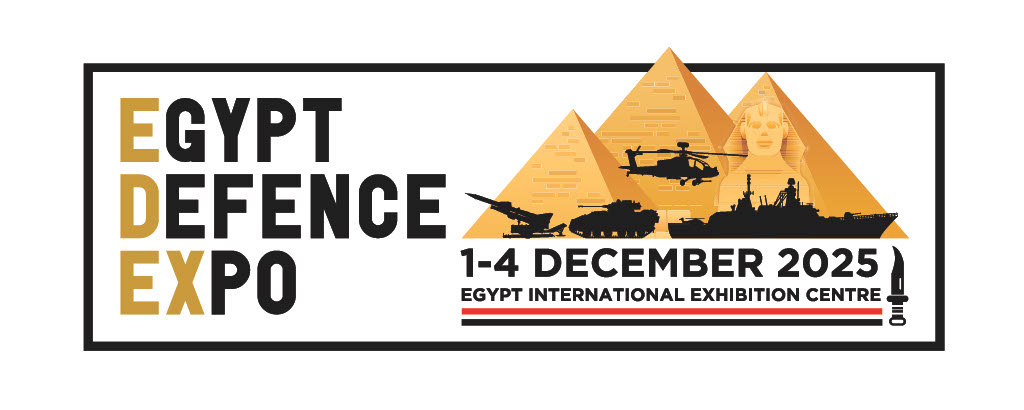
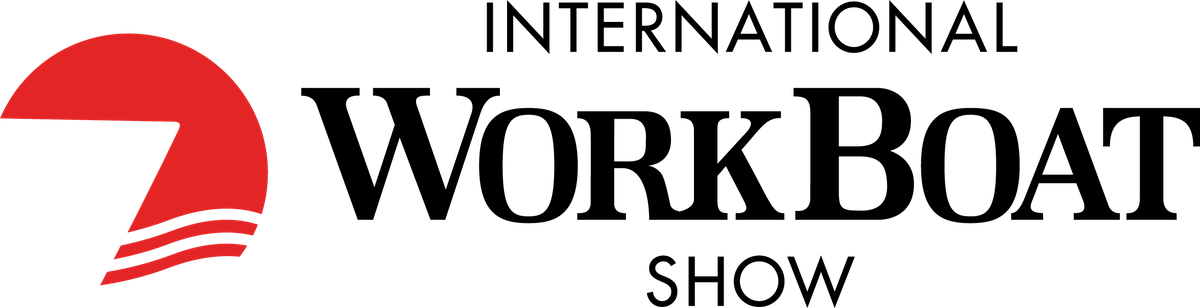