Addverb Dynamo 1T
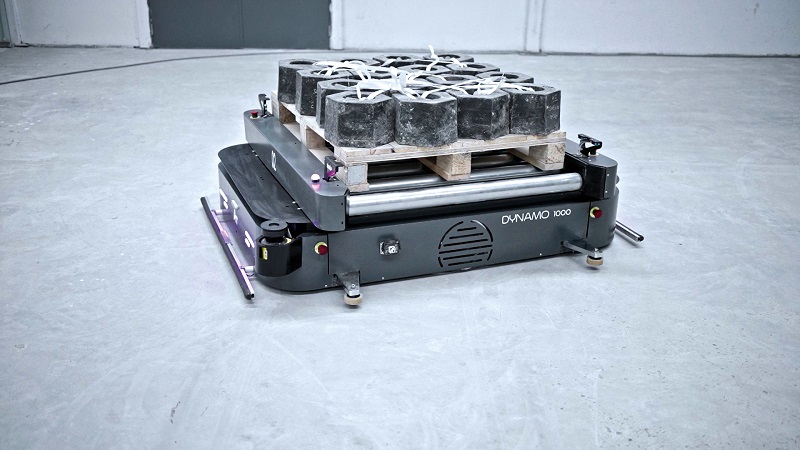
Rory Jackson reports on what it took to create this particularly heavy-duty autonomous logistics vehicle
Warehouse weightlifter
While it is tempting to attribute the rising use of UGVs in warehouse operations (or AMRs – autonomous mobile robots, as they are often called in that context) entirely to labour shortages, it is important to remember that autonomy stands to greatly enhance the safety, efficiency and throughput of warehouses, and so enable all-around better deployment and care of human assets across logistics chains.
Robotics company Addverb understands this, having developed and produced a range of automated robotic systems for warehouses and other intralogistics operations. In addition to its in-house hardware manufacturing and software programming capabilities, it regularly consults with logistics firms about the contexts and use cases for tailoring its AMRs and stationary robots, much as in the UAV world these days.
This has led to Addverb designing and manufacturing numerous automated rail-based vehicles, autonomous ground marker-guided vehicles and other technologies, such as speech recognition for streamlining logistics operations.
More recently, it has launched its Dynamo family of fully autonomous materials transportation robots. Previously, there were only three vehicles in this series – the Dynamo 100, 200 and 500, so-called for their respective payload capacities in kilos.
Addverb has now expanded the series by unveiling one of its largest robots yet, the Dynamo 1000 (also called the Dynamo 1T), which with its 250 kg empty weight and 1000 kg carrying capacity gives it the biggest payload-to-empty weight ratio of any vehicle we have yet covered. Also, it measures 1550 x 950 x 281 mm, operates for 4 hours between battery recharges, and moves at up to 2 m/s.
Addverb and Dynamo background
Headquartered in Uttar Pradesh, India (with offices across Asia, Europe and the US), Addverb was founded by a team that for the most part had previously hailed from Asian Paints, a paint and coating products manufacturer (also in India) that was among the country’s early adopters of warehouse automation solutions.
There, Addverb’s would-be founders carried out research across the automation industry to learn about the kinds of solutions that were available, and found that most of them were manufactured in either the US or Europe, and were rather expensive.
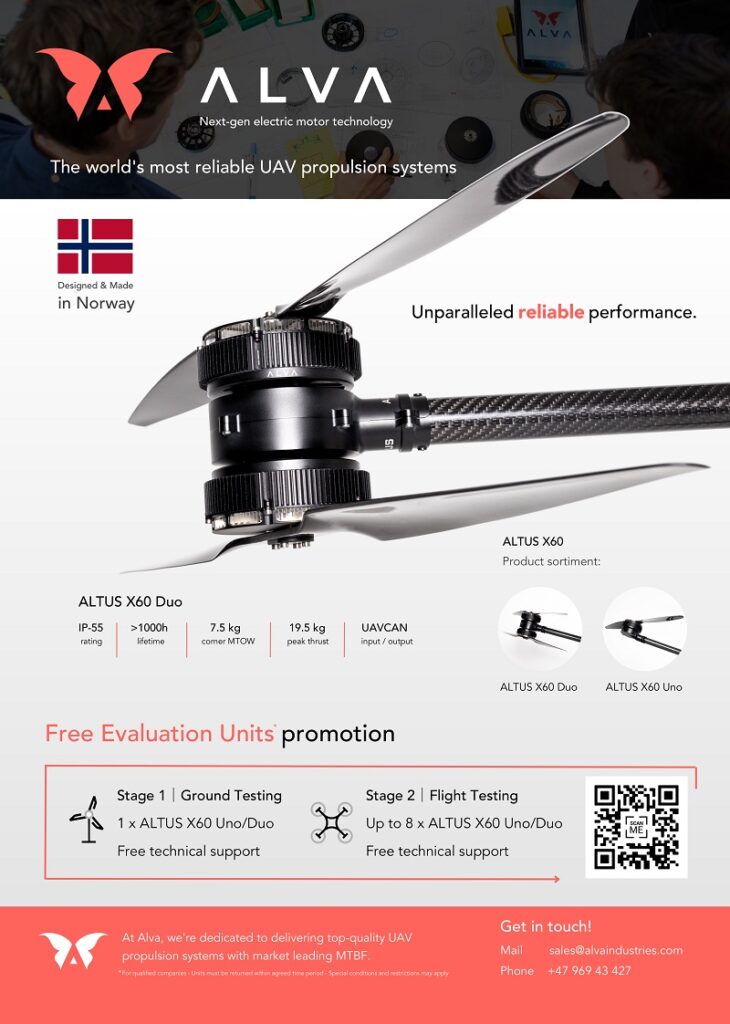
That motivated them to try to develop the technology in-house, not only to manufacture a cost-effective solution they could tailor and optimise but also sell to their immediate neighbours at more competitive prices.
Tapan Pattnayak, director of system architecture at Addverb, recounts, “Before working at Asian Paints, our co-founder and CEO Sangeet Kumar had been my friend at undergraduate degree level for 4 years. After university I worked in semiconductor design, including at Google, Nvidia and Intel.
“During his tenure at Asian Paints he worked on a project in Chennai to create Asia’s largest automation plant, so he talked a lot with me about the shortcomings of automation solutions available for that. So, as he identified cost-inefficiencies with the systems available, he realised there was a huge market for something more cost-effective.”
As Kumar saw it, this was not just a matter of UGV pricings but of throughput – how much freight and material could be moved in and out of storage per hour, safely and correctly, with every movement and asset detected, tracked and recorded through the fleet management and warehouse management systems (WMSs).
Addverb’s r&d therefore began with the initial layers a warehouse depends upon: technologies for storing, sorting, picking and moving goods. After that it started developing automation solutions (particularly rail-travelling robots and AGVs with grid-based navigation) before moving onto the autonomous Dynamo series.
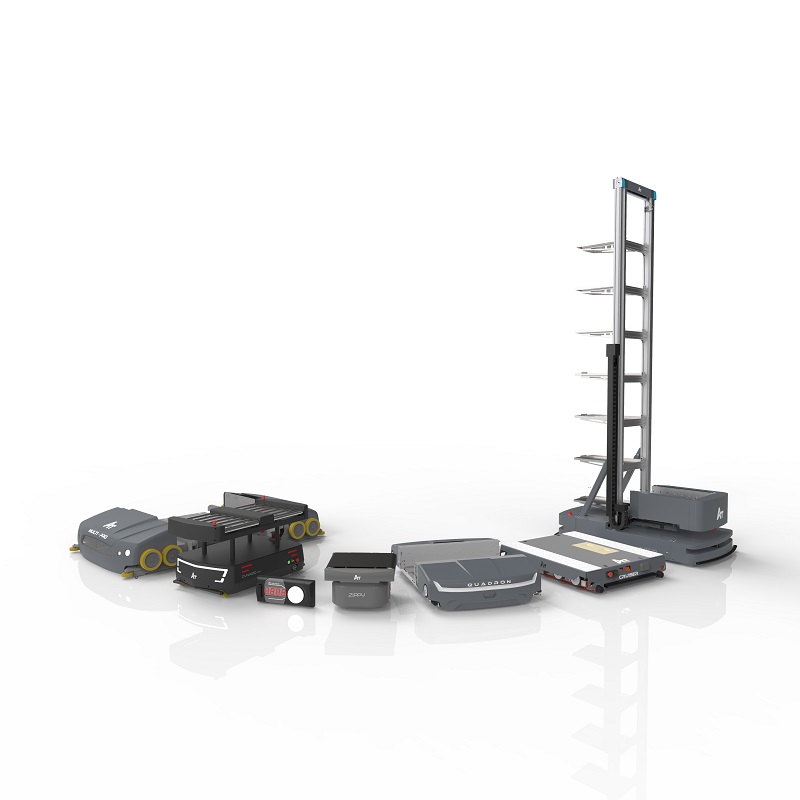
Development history
“The Dynamo 200 was the first in the series to be created, although at the time we were also working on ASRS [automated storage and retrieval system] robots for handling pallets – essentially an automated pallet shuttle that ran on rails,” explains Abhishek Jain, head of products at Addverb.
“The Dynamo 1T was actually conceived during the pallet shuttle’s development. The thought process was that if we were going to start moving up to 1000 kg via these pallet shuttles, which were fixed conveyor solutions, it made sense to build on that with an autonomous robot that could perform more dynamic movements of those quantities, either between different shuttles or key workstations.”
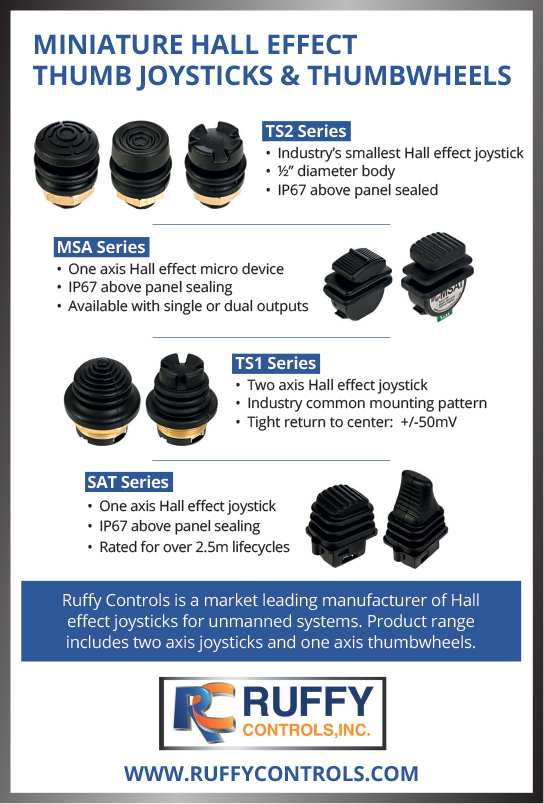
Of the 1T’s development, Pattnayak recalls that the increase in weight-handling requirements was so great between it and the other Dynamo UGVs that much of the 1T’s development had to be from a blank sheet. ‘Copying and pasting’ the same engineering principles from the smaller robots onto the bigger one was unfeasible.
“If you consider what an AMR is, and take away the mechanical differences between the various types, what remains is the perception and sensor fusion stack at the core of their intelligence,” Pattnayak says. “That’s what stays roughly the same between the Dynamo models, and even theoretically between the Dynamo and a Roomba, albeit maybe with differences in sensing and localisation architecture – and of course a lot more added industrial-grade safety.
“The process of accounting for the differences that we would need between versions of the Dynamo was carried out by our ‘solutioning’ researchers, who would go out to the warehouse floors of clients and understand how the autonomous systems would interface between the human workers and the automated systems.
“We couldn’t be successful by behaving like so many start-ups do in California, where they develop an AMR and only afterwards unveil it and look into how the market likes it. I knew a few such companies back in my Google, Nvidia and Intel days, so we knew we had to inform our design and engineering by working through customer requirements.”
Having investigated and defined the roles, carrying capacities, speeds, throughput rates and sense & avoid capabilities its UGVs would need across logistics operations, Addverb’s CAD, perception, embedded computers, mechanical engineering, electrical engineering and manufacturing departments were tasked with producing a UGV capable of handling pallets of 1000 kg.
Modular body
The 1T is a battery-electric system with differential steering across its two drive wheels and four caster wheels. Around the exterior of its body can be seen Lidars as well as 3D cameras for navigation and safety, along with emergency stop buttons for added precaution.
“There are also adjustable attachment points on top and around the exterior, so that the robot can have transfer mechanisms like an actuator-lifter or platform lifter installed on top of it,” Jain says. That means it can move or lift pallets as well as other objects like trolleys from itself to shelves or to our automated shuttle robots.
“You can also put a winch on it to tug a trolley or a chain of trolleys behind it, and its cameras can help with recognising the correct trolley to be tugged, which helps with inventory management beyond moving and sorting goods.”
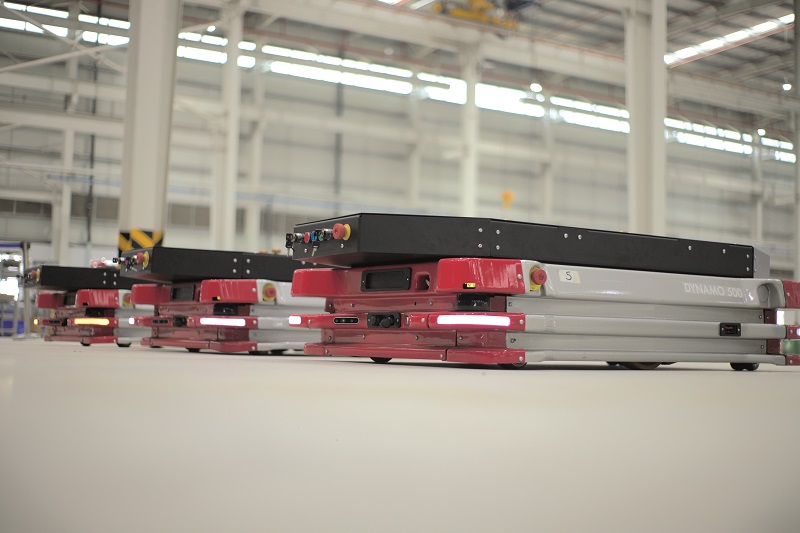
Load distribution
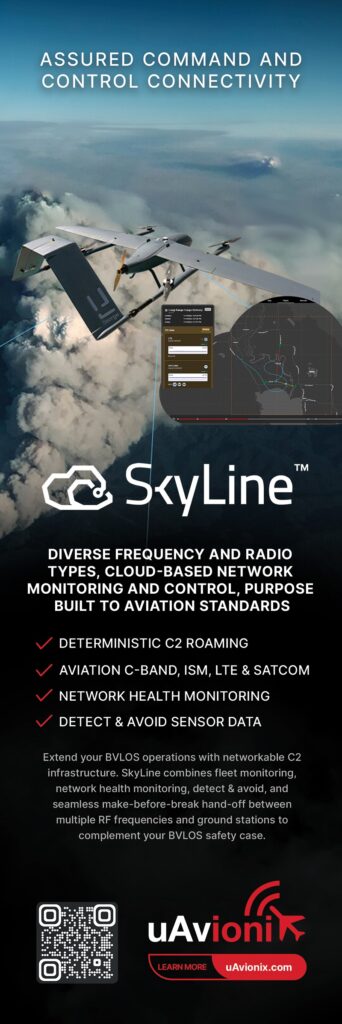
Inside the robot is a chassis with a cabinet-like design. Within that are the control computers, suspension components for load distribution and to make sure the drive wheels always maintain ground contact, as well as a frame that has been formed for broader distribution of a 1000 kg load.
To that end, large and sensitive interior components such as the battery are also placed and housed in a way that guarantees loads are distributed evenly across the pack.
“With this approach we also make sure the centre of gravity remains at a constant height and position for keeping material transfer operations as safe and smooth as possible,” Jain adds. “The cabinet-type chassis also makes maintenance quite easy, as components can be swapped in and out for inspection and servicing without difficulty.”
The frame is steel, and features numerous heat sinks about its interior for thermal management of the densely packed electronics. Meanwhile, the body covers are fibre-reinforced plastic formed using injection moulding techniques; Addverb declines to disclose further details about the mechanics.
“Load-bearing in a warehouse environment isn’t just about mechanics,” Pattnayak notes. “Any AMR must also move with fine-tuned dynamics, even when stopping or navigating to avoid obstacles.
“The differential drive and motor control for instance had to be extensively tuned and corrected for very balanced movement and very smooth torque and acceleration, to avoid any danger to a pallet or to the robot from the inertia of a pallet being carried. That meant control systems from the motor to the main computer had to be continually adjusted for such smoothness in normal, uninterrupted operations, and also for when they were reacting to something picked up by the perception systems.”
Navigation and autonomy
Localisation is executed using different arrangements of components in different warehouses, as each user will have their own preferred trackers and beacons, as well as Lidar-based tracking, SLAM or other ways of localising assets inside warehouses where GNSS cannot be relied on.
“On the use of SLAM for localisation, my engineers and I spent several weeks training the Dynamo robots in all types of warehouse simulations, within which were all types of floor traffic, lighting, everything you can imagine, and then we deployed it for testing in a real warehouse,” Pattnayak says.
“All those hours of simulation did not translate to any success in that first real-world test though. We can’t emphasise enough how challenging warehouses are for getting an autonomous system up to scratch; the gulf between training an AMR and an autonomous road vehicle is enormous.
“Warehouses are so dynamic and unpredictable, and the visibility you get from onboard sensors is so limited, that you can use the best visual 3D SLAM algorithms in the world but put them 4- 5 cm from the ground in a busy warehouse and you lose so much of their capabilities.”
Perception for the 1T is primarily powered by two Lidars, at opposite ends of the body to cover the full 360o around the robot. Addverb also has an alternative, less costly design concept for the 1T that uses a single Lidar placed at the centre of the body, with openings around it for a clear view ahead and to the sides of the UGV.
However, the team and customers generally prefer to have complete coverage via the two-sensor configuration, given the safety and confidence of detecting and avoiding surrounding objects this gives.
“The resolution of the Lidar data points was the most important thing for us when choosing a Lidar, but also key was the FoV we could get with each sensor, because seeing as much as possible around the vehicle at all times ensures that we’re not compromising on safety,” Jain says.
Pattnayak and Jain add that measurement distance was also critical for path planning, noting that the warehouse floors in which they work can be highly dynamic and even chaotic environments, and that navigating around one object is insufficient if an AMR cannot make additional plans for navigating around several other objects afterwards.
“Furthermore, as well as potentially having many people and vehicles moving around, warehouses aren’t always consistent in how well-lit they are,” Jain notes. “Some might have very dark spots, others will have really bright spots, so testing and trialling Lidars for how well they continued delivering accurate data points across a wide range of light intensities was really important. And the robot is safety-certified, so the Lidars and other components had to be similarly certified.”
The 3D camera system on the 1T provides a second layer of data points, and the colour and shape information they supply also help provide key contextual information on the nature of objects detected. Most critically, the camera has a wider vertical FoV than the Lidar, so it can detect objects at heights that could interfere with the pallets on top of the robot.
“In warehouse environments, barcode reading is also very important,” Jain adds. “The camera can therefore identify pallets and trolleys as insurance that whatever cargo the WMS has asked the AMR to find, the correct cargo is in the right place, the WMS hasn’t recorded a mistake, and that the robot doesn’t pick up the next pallet to it by accident.”
The camera set-up can be customised according to the end-user’s preferences on safety and cost. As a result, the 1T can integrate one camera or multiple cameras, and have them installed at different mounting points and angles.
Addverb notes that one popular configuration is to have two cameras at the front and two at the back, as this provides for redundancy and to prevent robots from backing up into each other. The perception software stack is written with sufficient logic for integrating and fusing visual data streams from any number of sensors.
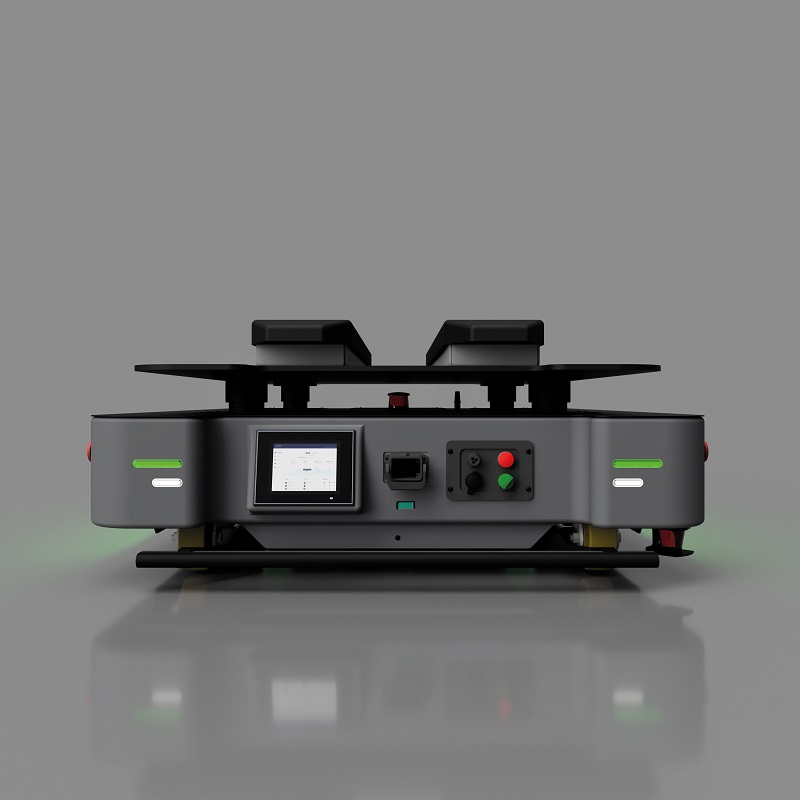
Power and energy
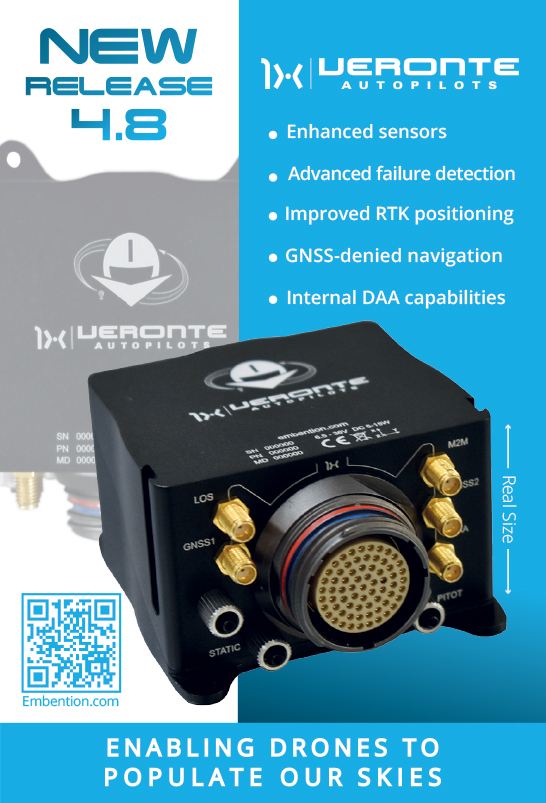
The difficulty of training the 1T’s behaviour for safety in warehouse environments is why the drivetrain speed is capped at 2 m/s. In reality though it will rarely maintain that speed for long, given the need to account for the potential for moving objects to emerge from around corners, pallets or machinery.
Exact details about the 1T’s drivetrain and components are proprietary, but Pattnayak comments that its design has been based largely on the application of classical mechanical theory, without any particular breakthrough or experimental component in the motors or suspension.
When it came to choosing battery technologies, Addverb opted for safety. As many readers will know, lithium nickel manganese cobalt oxide (NMC) remains the most widely available cell chemistry, and is generally still a winner in terms of gravimetric energy density. However, it is not the safest, particularly with regard to its risk of off-gassing and thermal runaway in the event of an impact, puncture or being run at excessively high currents during periods of high torque demand.
The Dynamo series’ packs therefore integrate cells of two chemistries, both newer and safer than NMC. One is lithium iron phosphate (LFP) cells, which in addition to being much safer than NMC cells also deliver power at a more stable voltage level over their charge cycles, meaning greater energy efficiency throughout the Dynamo’s operations. And although NMC cells are more stable in cold temperatures than LFPs, the reasonably controlled environment in warehouses ensures that the UGVs will effectively never be dealing with extremes of temperature in the first place.
The other cell type is lithium titanate oxide (LTO) cells, such as those made by Toshiba. They can be charged very rapidly with no impact on lifespan, but cost a bit more than LFP-based packs.
They are also safer even than LFP. In our article on the Clevon delivery UGV (UST 47 December 2022/January 2023), we reported that the company used LTO packs on the road and asserted that they could be pierced with a nail without any risk of leaks or fires.
Regardless of cell type though, the 1T is programmed with opportunity charging, autonomously seeking out charge points between orders to replenish its energy without disrupting workflows.
Future plans
Addverb plans to continue development of its uncrewed solutions. In addition to optimising and potentially expanding its existing solutions across ASRS and pallet-moving autonomous robots, it views quadrupedal and bipedal UGVs as the ideal next avenue to go down.
As we have seen in previous articles, such as that on the ANYbotics ANYmal (UST 40, October/November 2021), legged robots can walk up and down stairs as well as over objects, and can potentially even open doors. Such capabilities could greatly benefit goods transportation and warehouse logistics, and Addverb intends to play its part here.
Specifications
Dynamo 1T
- Dimensions: 1550 x 950 x 281 mm
- Empty weight: 250 kg
- Payload capacity: 1000 kg
- Maximum speed: 2 m/s
- Maximum endurance: 4 hours
UPCOMING EVENTS
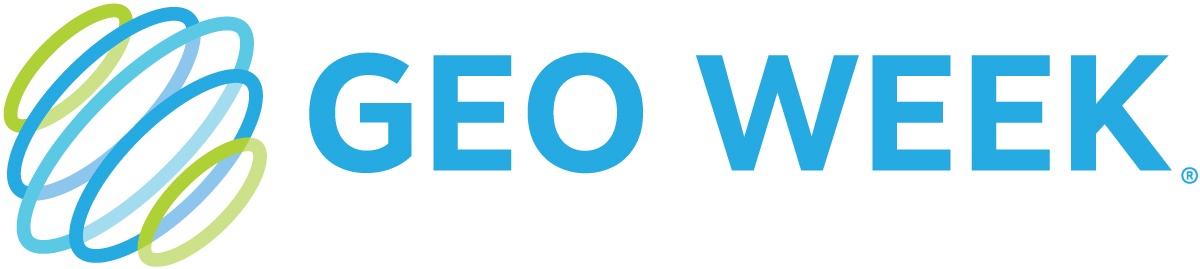
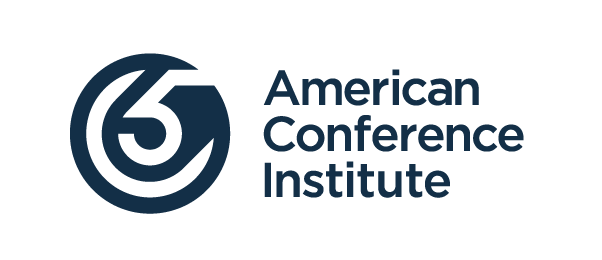
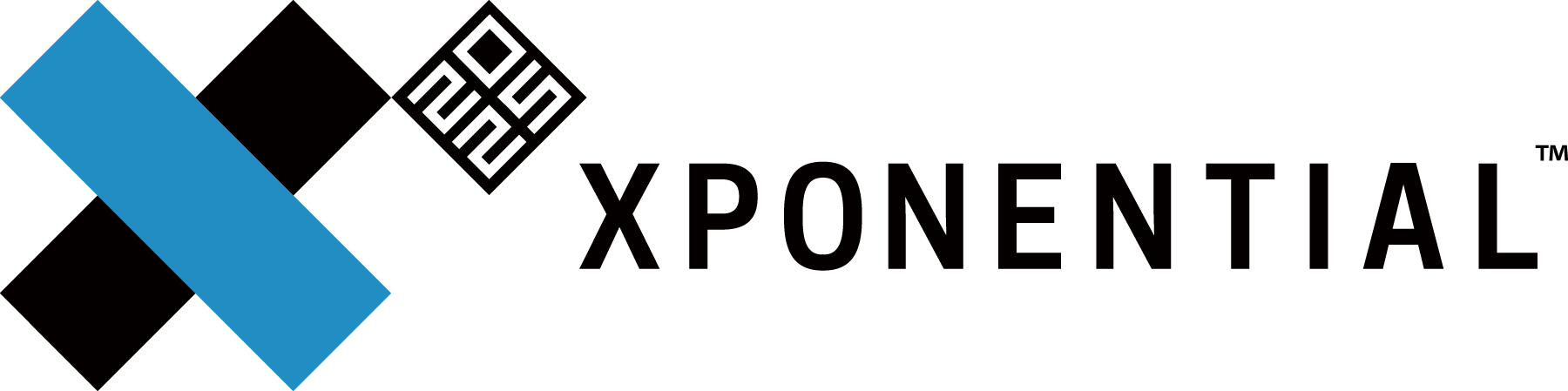
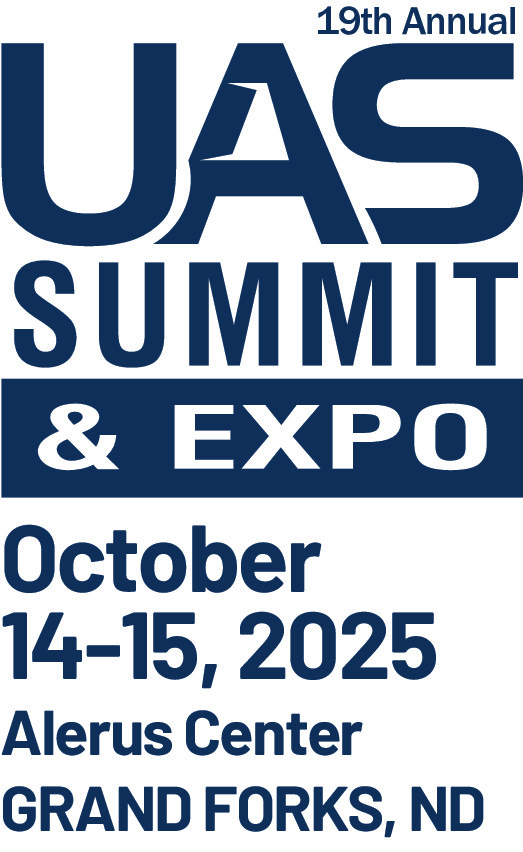
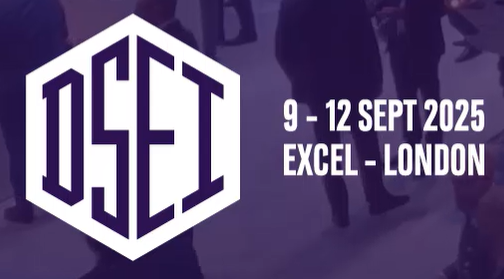
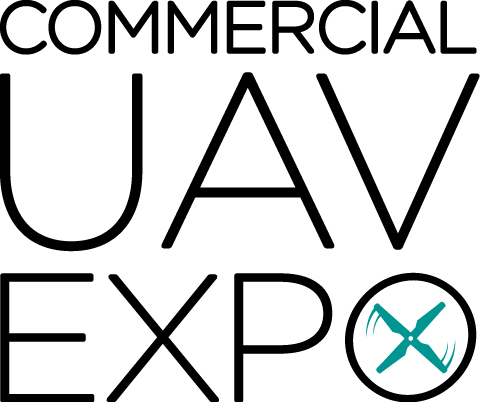
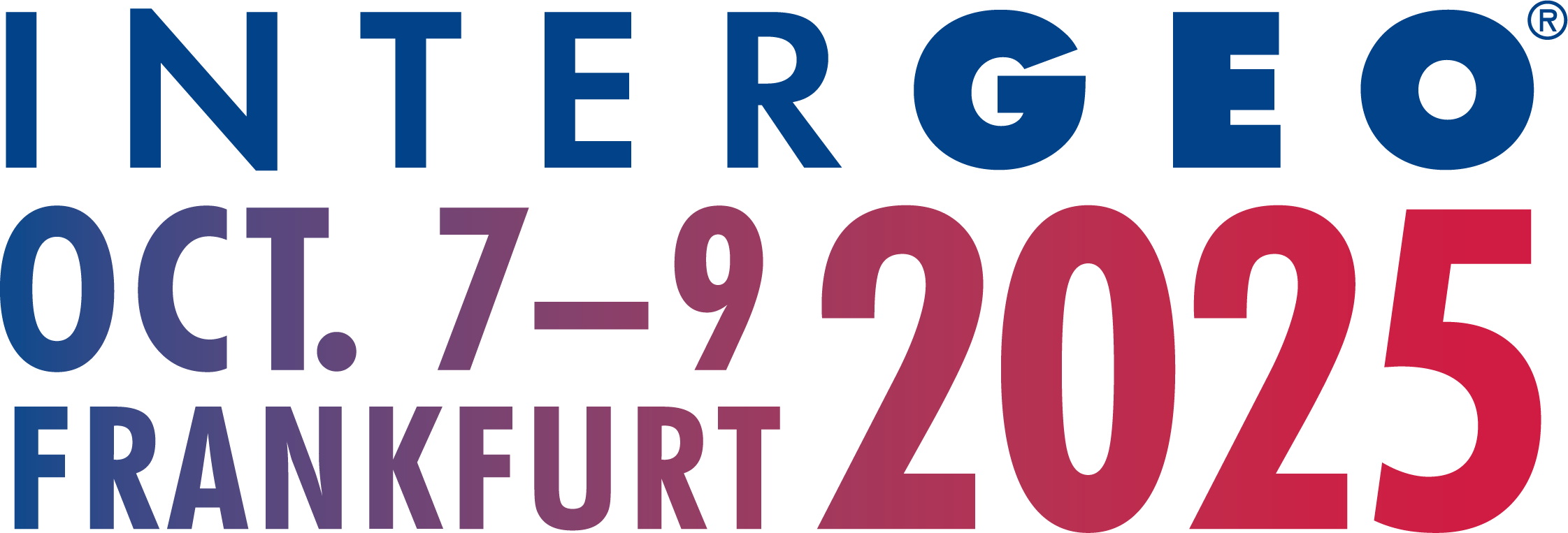
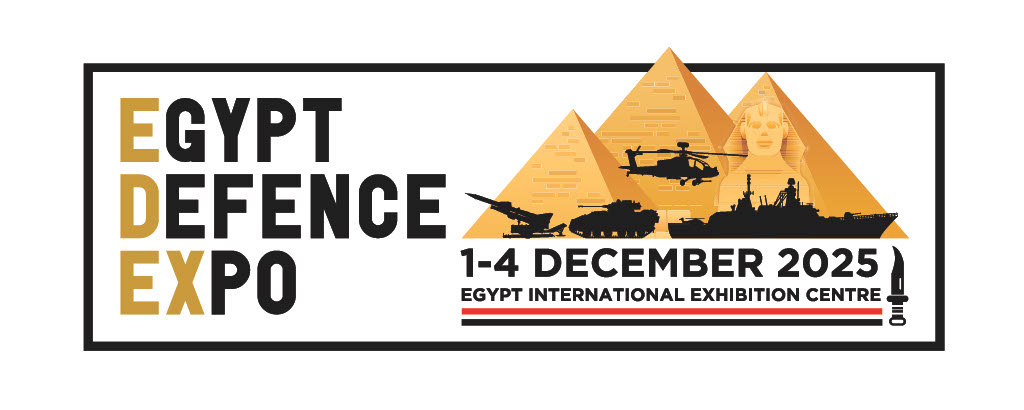
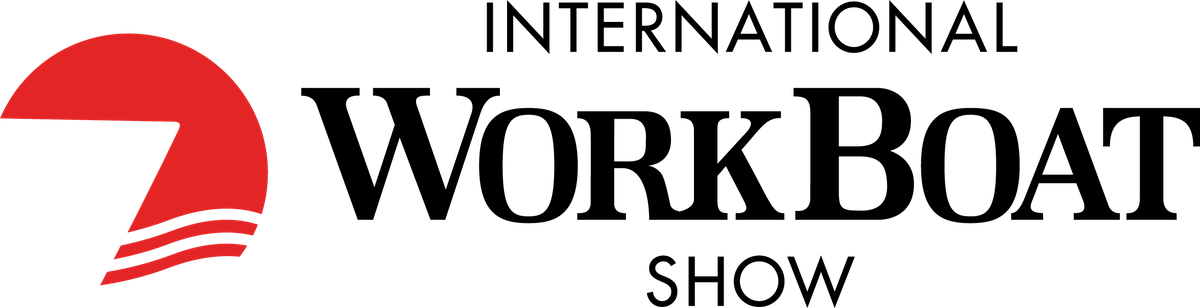
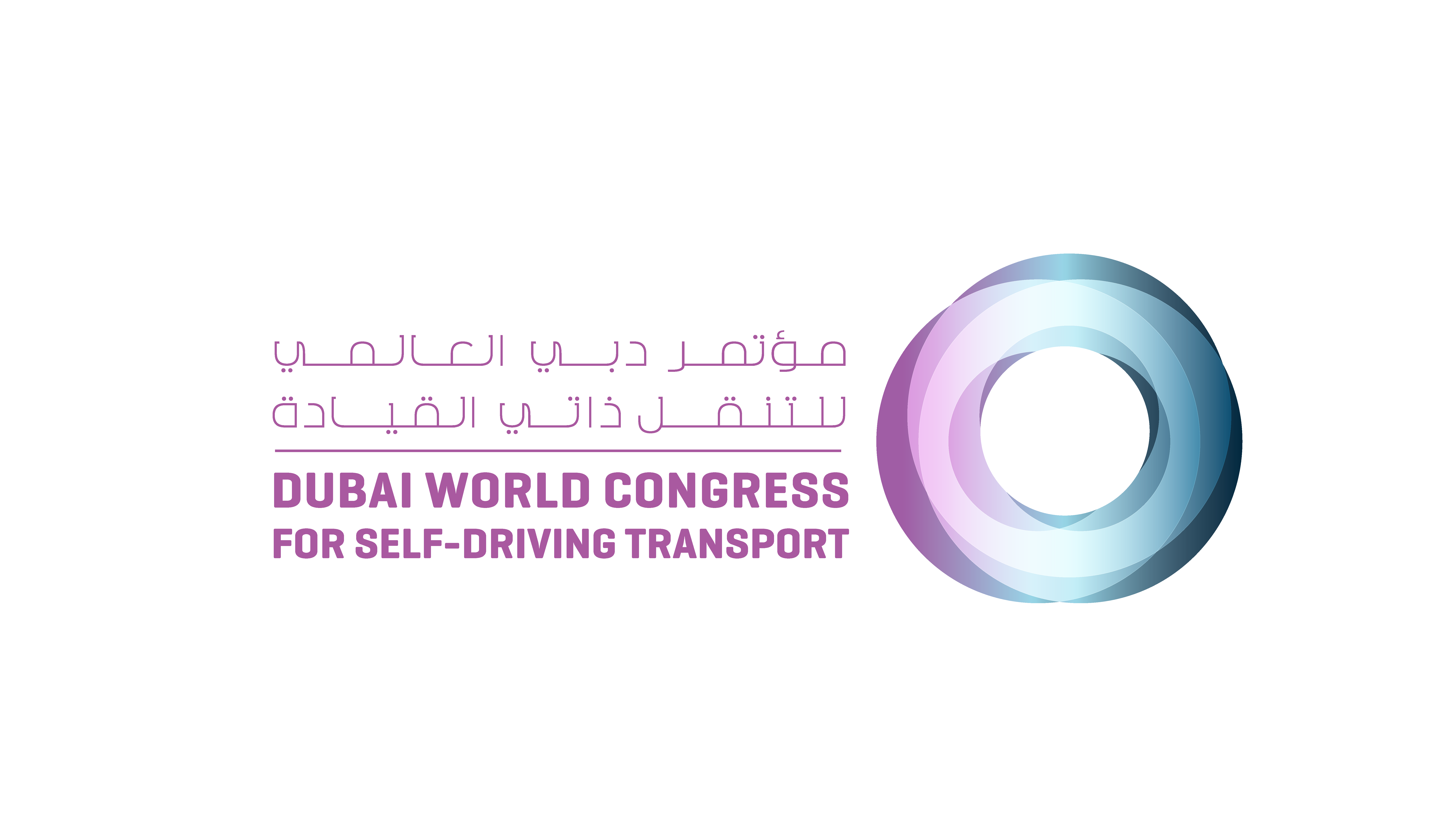
