UUVs
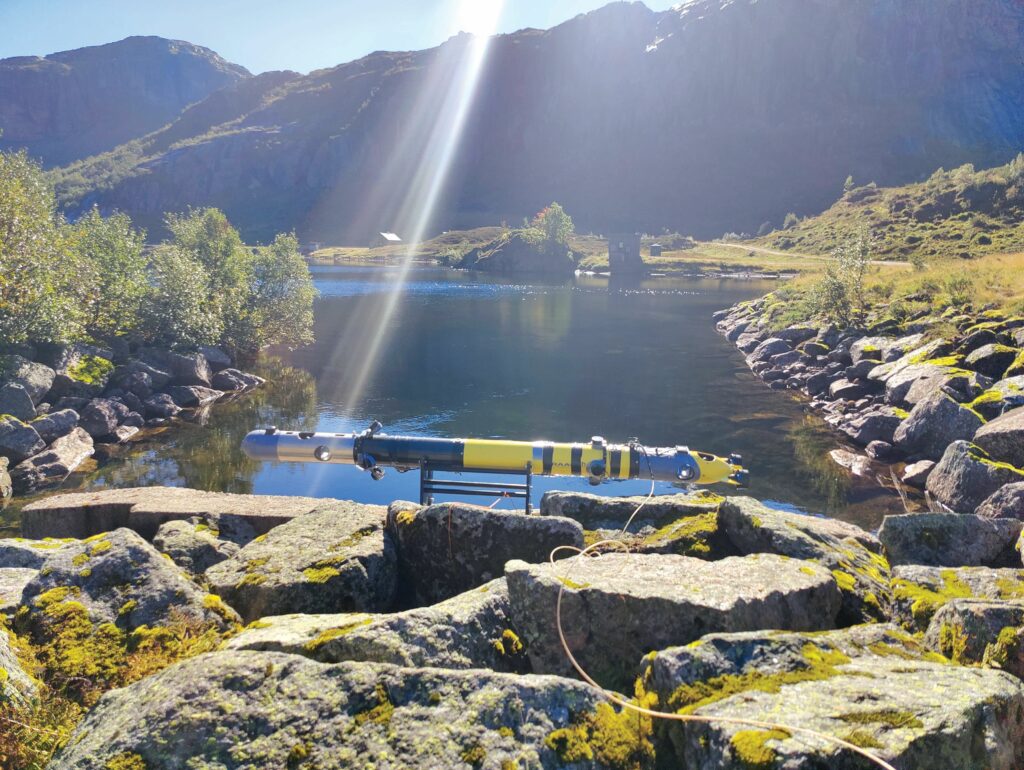
(Image courtesy of Graal Tech)
New frontiers
Rory Jackson looks at how different submersible vehicles and robots are handling data-gathering operations at the farthest limits
Since the first AUVs were developed in US universities between the 1950s and 1970s, new UUV systems have been engineered and deployed in every ocean around the world, gathering priceless data for defence, offshore industry, scientific research and other applications.
Today, the final edges of the maps are being filled in, with uncrewed systems now operating in places that were once deemed too remote, too shallow, too narrow or unserviceable. A fresh generation of nimble, intelligent, robust and cost-effective solutions is bridging these new frontiers, and a selection of these vehicles are explored below.
Hydroelectric plants
Graal Tech in Italy is configuring its X-300 Explorer AUV for inspection work in the tunnels of a hydroelectric plant in cooperation with the Norway-based company operating it.
“There are regulations requiring companies such as our Norwegian customer to do periodic inspections of those tunnels, not just for the plant’s safety but also its efficiency. If rocks and debris are accumulating inside the tunnels, the flow of water driving the turbines in those tunnels will be impacted, so the power output will drop,” says Alessio Turetta, director of business development at Graal Tech.
The company’s X-300 Explorer is a battery-electric AUV, typically measuring 2.1 m long and weighing 25 kg in air. Its Lithium-ion energy storage of 1.2 kWh enables up to 12 hours of operating endurance and a top speed of 5 knots, with 4 knots the standard cruising speed.
Engineered to be neutrally-buoyant in water, it navigates using a combination of sensors, including an INS, sonars, five cameras (one nose-mounted, the others oriented around the vehicle’s circumference for 360° visibility) and a 3D inclinometer. It is also connected to the surface during operations via a fibre-optic tether for real-time telemetry and survey data streaming.
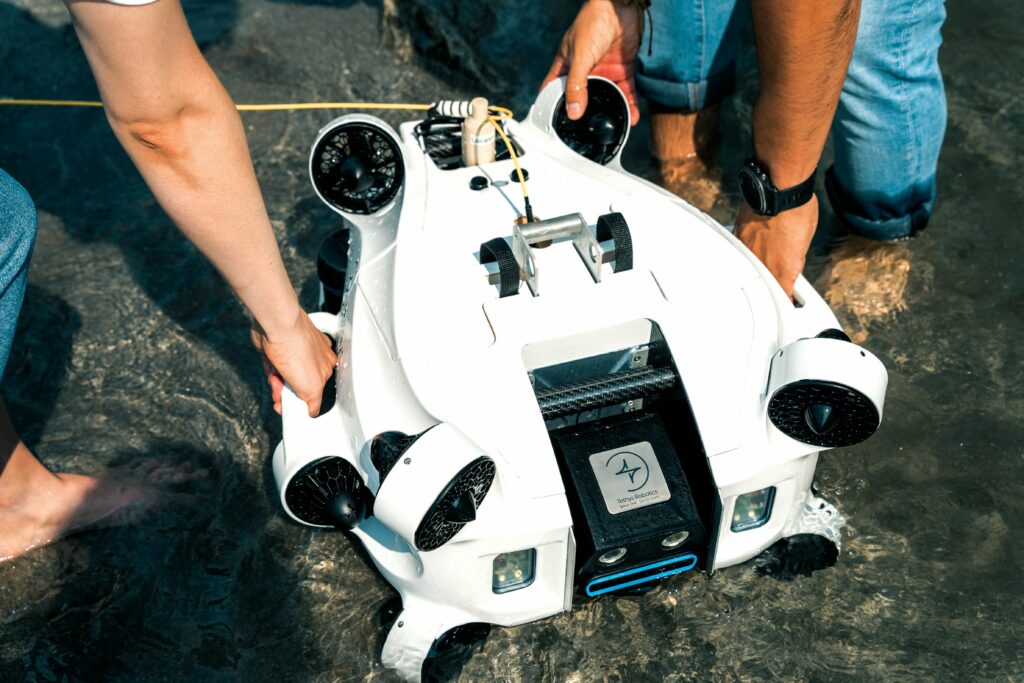
(Image courtesy of Tethys Robotics)
“When the vehicle operates in the customer’s plant it will have two operating modes,” Turetta says. “One is an autonomous mode without the tether; it will perform the first inspection. To do that we’re upgrading it with additional AI software layers, so it can understand the topography of the tunnels, robustly avoid obstacles and perform other intelligent tasks by itself with high reliability.”
In this mode, the X-300 Explorer will be equipped with a multibeam echosounder for measuring the structural health of the tunnel and checking for the presence of any obstacles within them that might hinder fluid dynamics.
“Once the customer has checked the data from the autonomous inspections, they’ll look into whether there are any points that need closer inspection and evaluation,” Turetta says.
“In the second mode, the tether will be reinstalled and the AUV will autonomously navigate between points of interest to reduce operator workload, although it can be steered by the operator using
real-time visual data from the nose camera to view their points of interest up close and in various controlled angles.”
To create the Explorer (as a derivative of the Genoa-headquartered company’s X-300 AUV model), a variable-buoyancy system was removed from the standard X-300 design. So the vessel is tuned to be neutrally buoyant for each mission, based on the salinity of the water, as reported by the user.
“This allowed us to reduce the length of the Explorer AUV by roughly 40 cm from either end, compared with the standard X-300. We also installed a transceiver for the fibre-optic tether, but that’s a very small component, about the size of a credit card, so comparatively easy to integrate,” Turetta adds.
In addition to the fibre-optic tether reassuring owners and inspectors that the value of the uncrewed data collection is just as good as them being there themselves in real time, Turetta says the tether used is a thin, nimble component that allows the AUV to move as freely as if it were untethered – up to a maximum length of 5 km. This is in contrast to the heavy, movement-constraining, power-and-comms umbilicals typical of ROVs, which would have been unsuitable for navigating the bends and turbine blades in the tunnel.
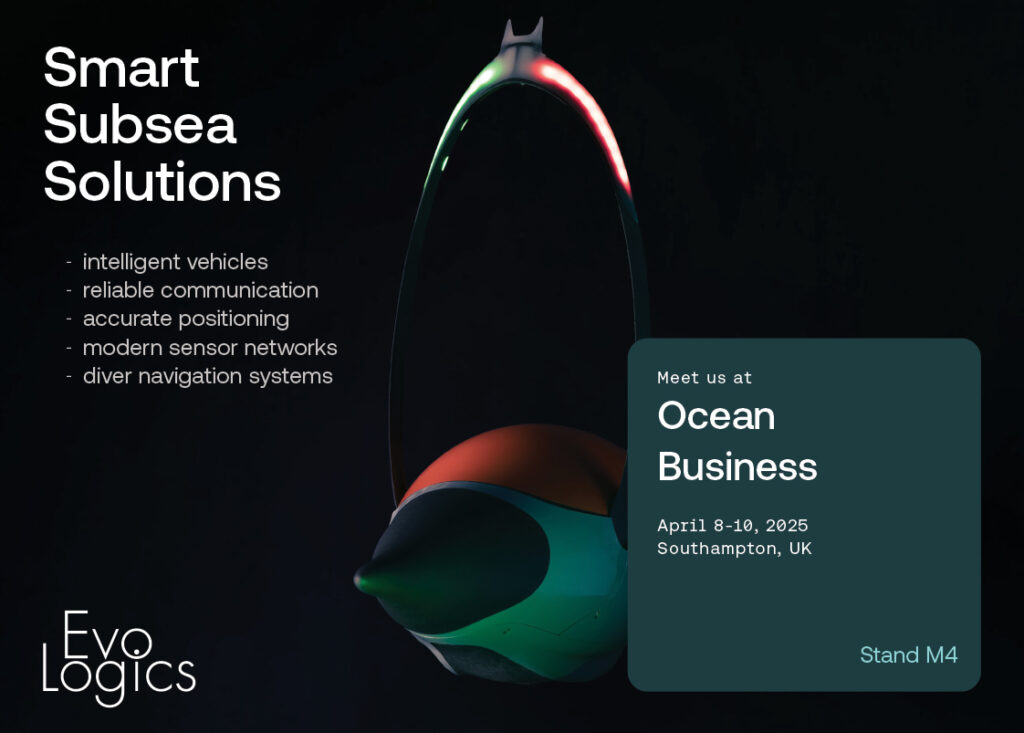
“Our first customer, at a hydroelectric company in Italy, requested something suitable for exploring a submerged tunnel with turbines inside that joined two lakes at differing altitudes,” Turetta recounts.
“Normally, to explore such tunnels, the owner first empties them using valves at either end and then people can enter for inspection. But these specific tunnels had never been explored since their construction around 50 years ago, so using an AUV was critical to protect human inspectors in case the tunnels’ structural integrity was unsafe.”
Lake surveys
Like Italy, Switzerland is home to a number of lakes and water bodies that form part of the country’s wealth of natural beauty spots. However, there is a growing awareness of problems with their condition, as Gallus Kaufmann, co-founder and business developer at Tethys Robotics, tells us.
“The lakes and rivers outwardly look beautiful, blue and perfect, but if you look inside them with underwater robots there will sometimes be visibility of 20 cm distance; maybe even 10 cm only, which is very, very low,” he remarks.
The challenge, however, for Kaufmann and his fellow engineers (at the time, researchers at ETH Zurich) in inspecting lake shores or riverbeds was that currents in such shallows are very strong, and AUVs capable of withstanding such environments and capturing quality data are rare.
“We had originally considered just engineering software for an existing robot that might have been otherwise mechanically suited to working in shallow, space-constrained, high-current waters to meet customer needs. Our work at university ETH Zurich had been focused on key software enabling precise, autonomous, underwater 3D mapping, but we didn’t feel there was one on the market that was designed and open to work with third-party code, such as our own code for autonomous control and navigation,” Kaufmann says.
“On top of that it’s important that software and hardware work together harmoniously. Having precise localisation, integrating and analysing with machine learning the output of all the collected data, the number and orientation of thrusters on a robot, how they’re integrated or oriented, and how much energy is stored on the robot may seem like small details, but they really build up to have significant interactions on how well the software can execute tasks in the long term.”
Unveiled in August 2024, the Tethys ONE weighs 35 kg in air and runs for up to four hours on battery power, integrating a wide range of payloads, including a 4D manipulator and grabber arm, an underwater metal detector, a magnetometer, and CTD and pH sensors, as well as various sonars (along with a DVL and IMU for navigation). It is capable of operating in waters as deep as 300 m and maintaining its position amid currents of up to 3.5 knots.
“As well as needing highly-capable control software to withstand currents as strong as that, the body was heavily optimised in CFD to prevent it being pushed or pulled too much,” Kaufmann says.
“We’ve also designed it with 10 thrusters angled about the body, as well as software for data fusion of a lot of sensors – for dense navigation-and-control input data, as well as 3D mapping. Together, these feed into effective station-keeping and manoeuvring, including omnidirectional movement and attitude adjustment.”
Tethys Robotics has also used the Tethys ONE to inspect hydroelectric plant facilities; its autonomous station-keeping enables it to view turbines and tunnels closely without the turbines needing to be shut off, which is a significant boon to plant operators. It is also able to autonomously inspect dam walls with its acoustic sensors to scan for cracks and generate geo-referenced 3D acoustic and photogrammetric models.
Having validated its technology in the lakes and rivers of otherwise-landlocked Switzerland, and in the Baltic Sea, Tethys Robotics is looking into offshore energy markets such as wind-power fields, where currents are extremely strong and autonomy can be of great benefit to inspection work. Demonstrations and pilots are planned in early 2025.
Seafloor surveys
While UUVs have long been developed and deployed in deep-sea surveying applications such as hydrocarbon exploration, ROVs and conventional AUVs suffer from certain inefficiencies when it comes to the type of long-term data-gathering missions typically entrusted to automated (but wholly immobile) ocean-bottom nodes, such as those applied in ocean-floor geophysics.
Kyrre Tjøm, CEO and founder of Norway-based iDROP, identified these inefficiencies in 2008, while serving as a consultant on engineering a new generation of geophysical data-gathering nodes.
“We brought two ROVs to place our survey nodes on the seafloor, piloting them from the vessel to retrieve nodes from a node-handling frame we’d lowered onto the seabed, and carry them to predefined installation points. It was time-consuming, labour-intensive, and the systems were placed at great risk due to the harsh conditions of the water. In fact, we ‘lost’ an ROV on the first job after an umbilical snatched on something,” Tjøm recounts.
“Eventually, we wondered why can’t we just drop the nodes off the side of the vessel? We envisioned making a node that could steer itself to control its own heading and pitch throughout descent, and then ascend once it finished gathering data. We did some calculations, realised it was possible, and filed a successful application for EU funding support.”
Through that funding, iDROP has engineered its Oceanid autonomous ocean-bottom node, a 25-30 kg, torpedo-shaped system (not including a ballast attachment weighing a few kilograms, installed just before deployment and descent) integrating a battery that powers up to 180 days of data recording, assuming a 2 ms recording frequency.
Initial near-shore trials of Oceanid units have been carried out, thanks to iDROP’s proximity to the Oslo fjord, and the test sites, test vessels and 500 m sea depths there. In addition to EU funding, the system’s ongoing development and trials are supported by a consortium composed of ExxonMobil, HESS and Woodside Energy.
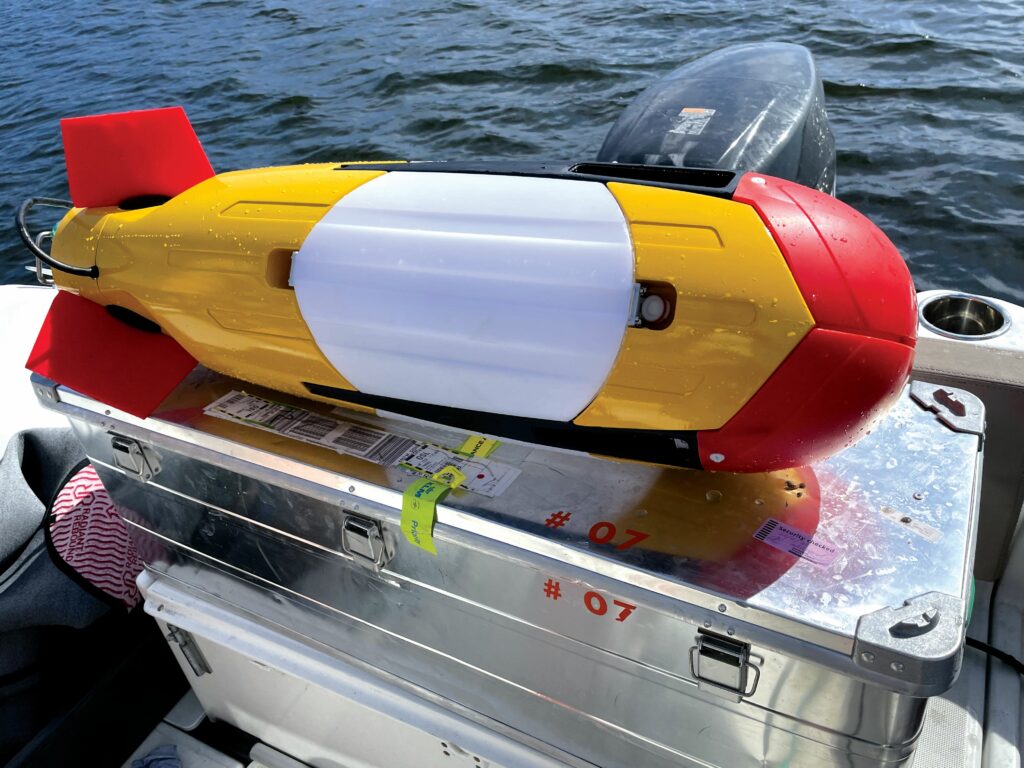
(Image courtesy of iDROP)
Oceanid is designed to be positively-buoyant and without thrusters. Following deployment, it descends under the mass of the aforementioned external ballast attachment, while steering itself autonomously to a specified survey point on the seafloor (thanks to its hydrodynamic cylindrical shape and three symmetrical, electromechanical, servo-actuated fins about its body).
Upon arriving at the seafloor, the Oceanid deploys its seismic sensor package, as well as a proprietary soil-skirt mechanism that couples it securely to the seafloor. Once it has gathered the requisite data, based on its programmed mission plan, the autonomous node retracts its coupling system and releases its ballast to float up to the surface (potentially steering itself again to a recovery location predefined at the ocean surface).
“This approach means we reserve 95% of battery energy for data gathering and recording, with maybe 5% used in descent, ascent, and acoustic modem communications between nodes and to the survey vessel. It keeps the solution very efficient,” Tjøm says.
“We plan to deploy swarms of nine Oceanids at a time, positioning them in a 3×3 matrix on the seafloor to survey large areas, and through their acoustic modems the nodes can transmit and receive time-of-flight data among themselves for precise navigation and guidance, without needing to rely on USBL or traditional LBL positioning systems.”
Similarly, Italian multinational oilfield services company Saipem first conceived of a resident ROV solution in 2009, as a means of improving underwater inspection and maintenance operations. By having a ROV working in residence, rather than having to be deployed, controlled and retrieved by a crewed vessel, underwater operations could be performed with greatly reduced costs, carbon emissions and risk to personnel.
“The technology available at the time was not sufficiently mature,” recounts Mauro Piasere, COO of robotics and industrialised solutions at Saipem.
In 2016, however, Saipem revived the concept and started the Hydrone investment programme, finalising the first prototype of its Hydrone-R resident UUV solution by the end of 2019. Around that time, Piasere adds, Equinor awarded Saipem the first resident uncrewed vehicle service contract in the energy sector.
“Between 2020 and 2022, the vehicle was customised to meet the specific needs of this first application and final tests were performed. Hydrone-R was accepted by Equinor in late 2022 and launched into the water in June 2023,” he says. “After a familiarisation period, the drone was recovered for maintenance in November 2023, and relaunched into the water at the end of May 2024.”
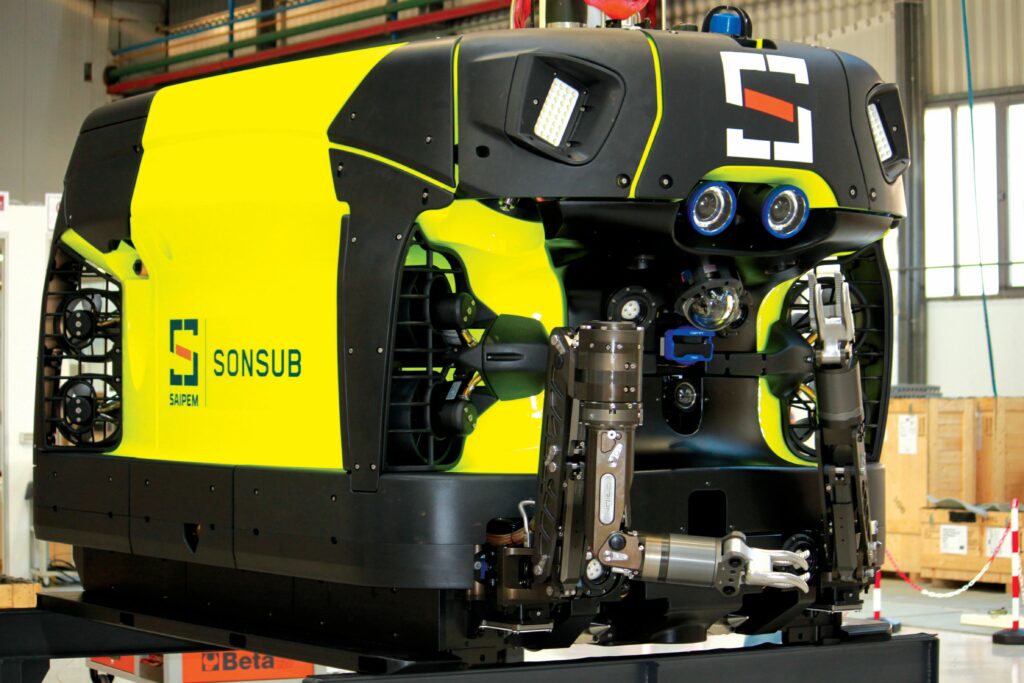
(Image courtesy of Saipem)
Today, the Hydrone-R ROV/AUV hybrid vehicle is a system typically weighing 3800 kg in air, and measuring 3000 mm long, 2100 mm tall and 1800 m wide, while capable of operating down to depths of 3000 m.
In addition to integrating cameras and sonars for its AI-based navigation-control system, the UUV has served in operations over the past 12 months in which it remained connected to a docking station, which provided a data link for real-time data streaming and a power line for battery charging.
Through this capability, the system achieved an uninterrupted dive of 167 days in 2024, with Saipem estimating that up to 12 months of uninterrupted operation should be possible, based on the data gathered so far.
Environmental sampling
While offshore wind energy has been cited numerous times as a key growth market that is spurring investment in oceangoing uncrewed systems, the seabed mineral market is also a critical emerging space. It depends on UUVs capable of supporting explorations and potentially infrastructure establishment at depths greater than 5000 m.
“Both of these industries require environmental monitoring and surveying beyond conventional bathymetry, and it can’t be done scalably or flexibly with ROVs,” explains Jake Russell, CEO of Orpheus Ocean.
“Before becoming aware of the need for both environmental data and sample collection in these industries, the team conceived of an AUV design for routine and scalable scientific research of hadal zones: areas of the ocean 6000-11,000 m deep. Only a few assets in the world – often crewed submersibles or very heavy ROVs – are effectively capable of reaching and returning from those depths.”
To that end, Orpheus Ocean has engineered its vehicle (called the Orpheus AUV, as of writing, subject to change) as a 70 x 60 x 52 in (177.8 x 152.4 x 132.08 cm) AUV, weighing 550 lb (250 kg) in air, including 50-70 lb of payload capacity. The system features an elongated, cuboid body with four LEDs mounted near the nose for forward illumination, a glass sphere for integrating cameras, batteries and other electronics inside the nose, a payload bay at the underbelly, thrusters at the rear, and landing skids extending from the undercarriage.
Using its standard-issue battery, the vehicle can operate for up to 12 hours when using its thrusters in ‘active’ mode or up to 120 hours in ‘passive’ mode, such as surveying on the seafloor while landed on its skids. For such surveys it will be able to integrate sensors for methane, dissolved oxygen, pH and turbidity, as well as a UHD colour camera, an eDNA sampler, and a sediment push-core sampler capable of scooping and storing up to 12 samples of seabed material per deployment.
Headquartered in Massachusetts, Orpheus Ocean was incorporated as a start-up in mid-2024. The Orpheus AUV technology had been conceived and developed at Woods Hole Oceanographic Institute (WHOI) since 2019, in collaboration with NASA JPL. Orpheus now has the exclusive licence to design and commercialise it.
“Over the course of r&d, getting the sample collection right has been what’s really stretched the capabilities of the autonomy software. We are not just navigating a 3D open ocean space; we’re actually interacting directly with the seafloor,” Russell says.
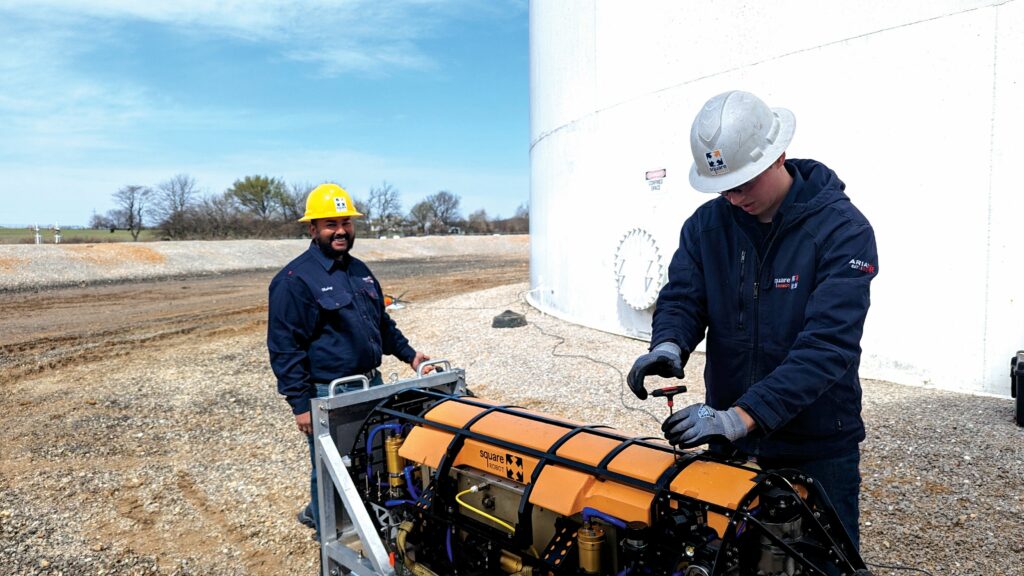
(Image courtesy of Square Robot)
“There is the aspect of terrain following, by which we navigate very closely to the seafloor for high-resolution surveys, but we also then have to choose a place to land that is best for collecting samples. That depends on inputs from the onboard sensors to gather what is the most opportune area, and after the sample collection you actually have to evaluate whether you’ve collected good samples or whether you should abandon some samples and attempt collection again.”
The aforementioned core-sampler payload will fire six pairs of sampling tools in sequence, each one retrieving a sediment core roughly 5 cm wide and
25-30 cm long. The first prototype sampler payload is near completion, as of writing. Two Orpheus AUV prototypes have been built, with one more in the works at Orpheus’ HQ, and four test deployments have concluded successfully (most recently on a NOAA-sponsored expedition, which included explorations of methane seeps in Alaskan waters at depths of 4900 m).
“But you don’t know what seafloor material at such depths is like until you actually touch it, so we’re programming a lot of adaptive decision-making into the autonomy software that is unlike anything that’s come before, because no other AUV has had to interact with the seafloor this way,” Russell says.
“There are also hardware challenges when it comes to operating at extreme depths, but the engineers here, and at WHOI, including my co-founder and CTO, Casey, are all well-versed in building things that can mechanically handle those kinds of pressures and conditions.
“Keeping costs and weight down are the less practised items, and we’ve focused on resolving those, particularly on our road towards scalability. So we’re planning to scale up our manufacturing, starting in summer 2025, around a commercial, productionised version of the AUV.”
Tank inspections
As well as exploring strange new waters, some uncrewed systems are now operating in entirely different fluid mediums. Since 2019, Massachusetts and Texas-based Square Robot has completed over 250 commercial tank inspections worldwide using the SR-1 and SR-3 autonomous submersible robots. These inspections have involved tanks containing a variety of fluid products, including fuels, lube oils and alcohols.
Square Robot’s three founders previously worked for a defence contractor, developing UUVs for military applications such as MCM, with one underwater robotic system in particular being used in scanning the exterior of ship hulls.
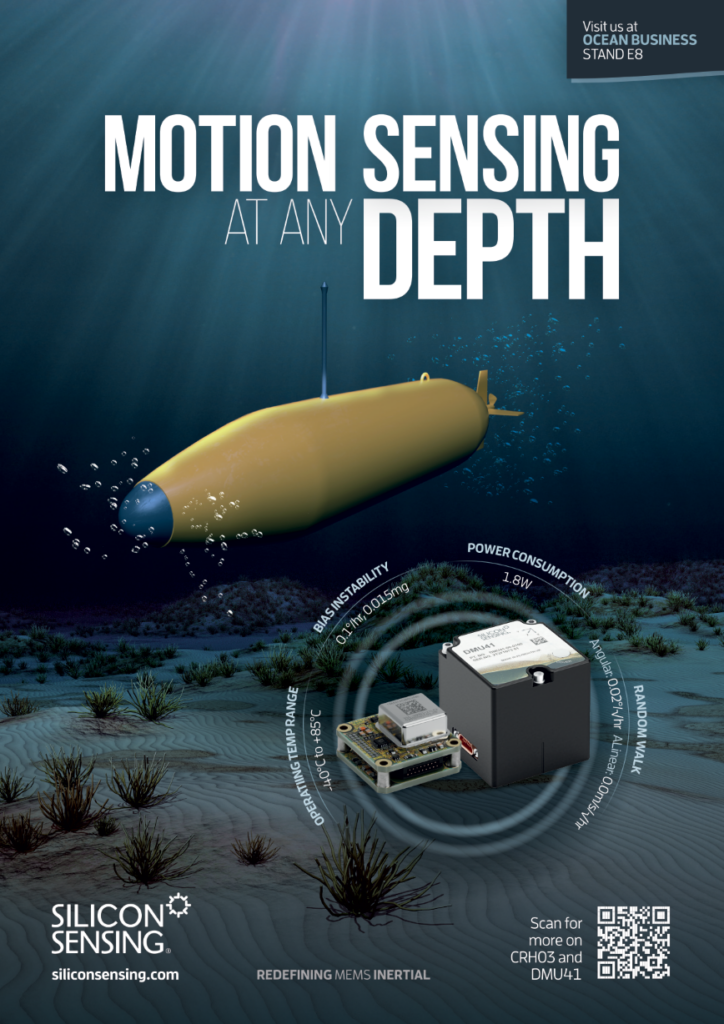
“Somewhere along the line, an oil and gas industry veteran saw the ship-hull inspection robot, and queried that if it was possible to inspect the outside of a ship hull while it was still in the water, we ought to be able to inspect the inside of a fuel storage tank while it is still in service,” says Ross Jarvis, technical director of sales and marketing at Square Robot.
The SR-1 was therefore engineered from day one as a solution specialising entirely on inspecting the interior of above-ground atmospheric storage tanks, and enduring and navigating through chemicals of varying temperatures, densities and viscosities.
After four years of real-world operations with the SR-1, Square Robot analysed extensive feedback, field experience and the hard lessons learned (as well as vast amounts of data) to develop the SR-3, its flagship inspection system.
The SR-3 measures 1.70 x 0.51 x 0.45 m and weighs 120 kg in air. As well as integrating a plethora of sensors (including cameras complemented by illuminators), the robot’s hull holds eight thrusters, a 256-element phased array ultrasonic (PAUT) sensor, rollers for navigating along the inside of tank walls, and an auger brush for moving sediment on the tank bottom out of the path of the PAUT sensor.
“A large part of the design choices and improvements that went into SR-3 focused on material compatibility. Our engineering team’s work required not just choosing structural materials that would be strong enough and light enough, but also materials that wouldn’t degrade in harsh products, like naphtha and methanol,” Jarvis notes.
The SR-3 typically operates at a maximum speed of 15 cm/s while inspecting; that being the operating limit for the PAUT sensor integrated principally for measuring plate thicknesses to a high degree of accuracy, which allows for the identification of defects, corrosion and pitting.
The PAUT sensor is able to collect 96,000 individual UT data points for every square metre of tank bottom inspected. Significant work was done to ensure appropriate sealing of the system to protect electrical and electronic systems against the pressures and corrosive properties of the surrounding fluids. The SR-3 can work in pressure up to 275 kPa (40 psig) as atmospheric storage tanks can reach 15 m in height.
“Meanwhile, the fact we’re working in GNSS-denied spaces means we needed a high-quality inertial navigation, supported by our onboard acoustic sensors suite for localisation. Our system has a navigational accuracy to within 0.153 m anywhere within the tank,” Jarvis says.
While the SR-3 inspects autonomously 90% of the time, Square Robot always has a trained field engineer as the operator at its GCS, to constantly monitor but also assist the autonomy system in the most complex scenarios, when invariably it is faced with a new and unexpected obstacle – one that even a well-trained AI system would struggle to determine the optimal response to (for now).
Summary
While the use-cases documented here cover a broad mix of operating locations, from lakes and tunnels to 10,000 m-deep seafloors, they all share the property of targeting cost-effectiveness, either in their use, construction or both.
With the leading but highly expensive UUVs of the world now sharing space with lower-priced systems, democratised access to ocean data can gradually be expected to boost demand for UUV units.
Within the next 10-15 years, one should not be surprised to see factories dedicated to series production of these new UUVs springing up. Production of complementary systems, such as subsea autopilots, marine batteries and marine actuators, can be expected to increase around them as part of a real, dedicated UUV manufacturing boom – much like what is happening around UAVs today.
UPCOMING EVENTS
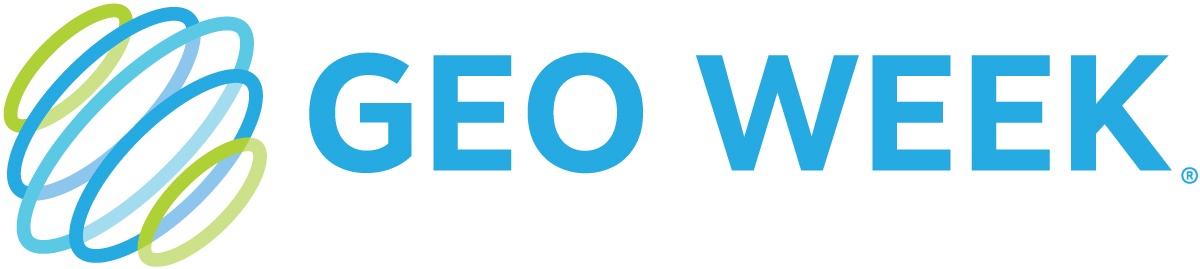
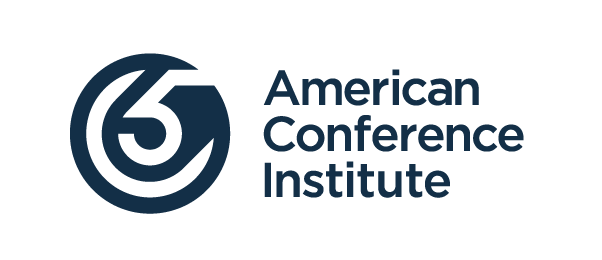
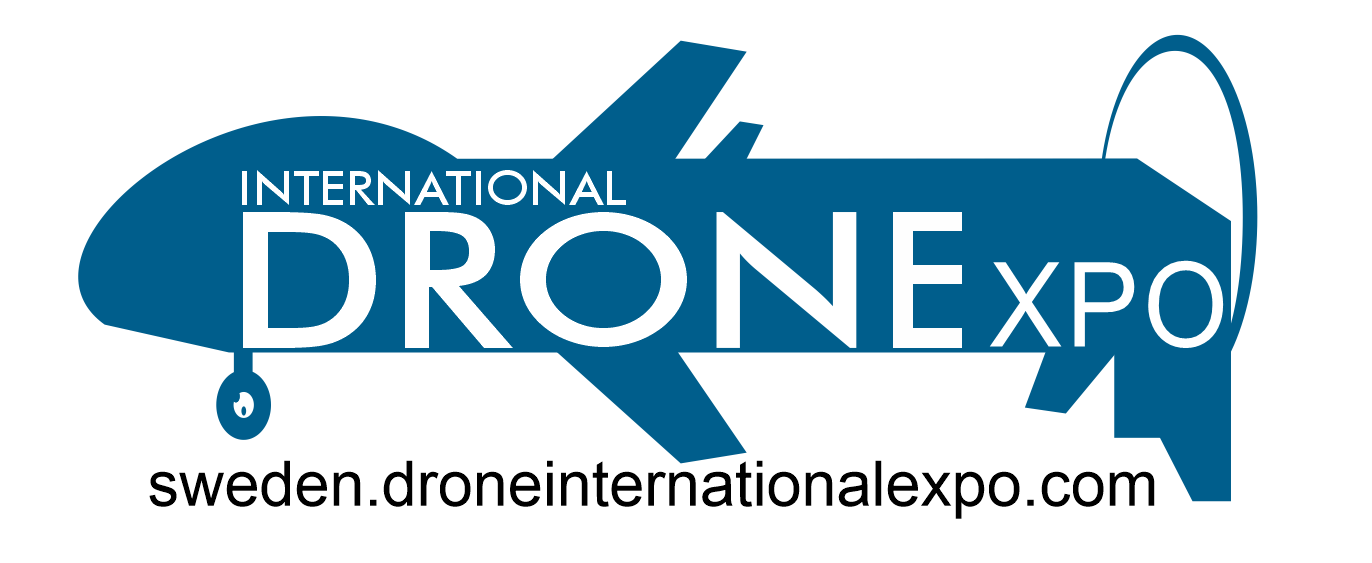
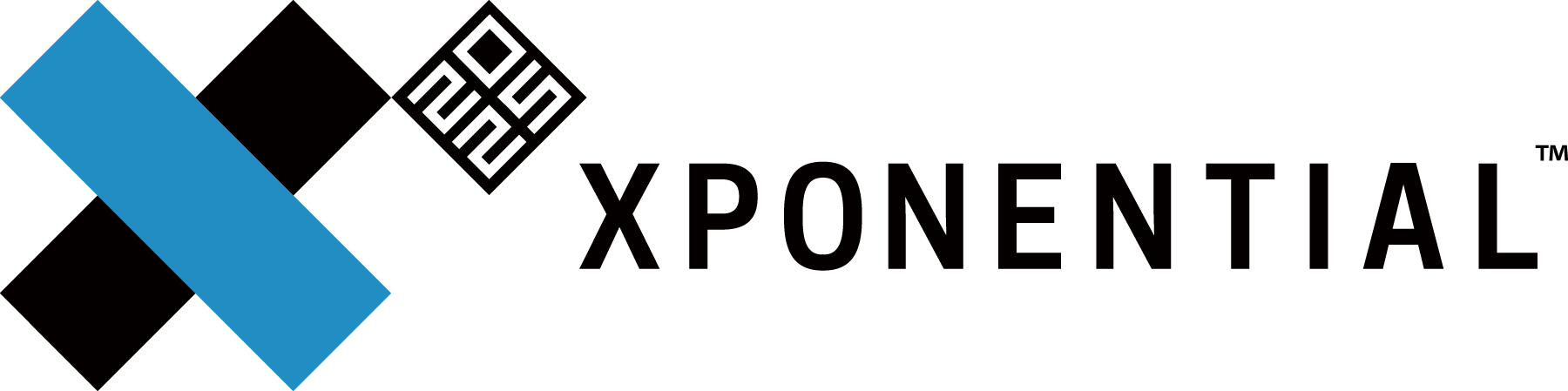
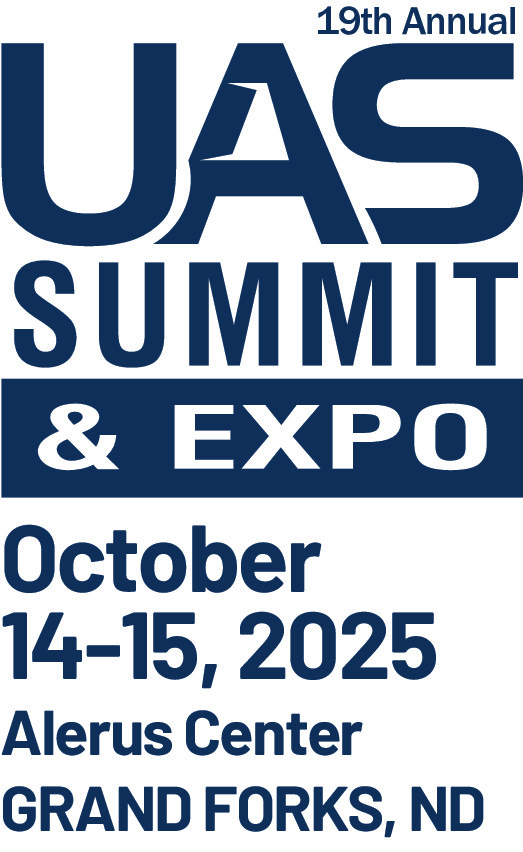

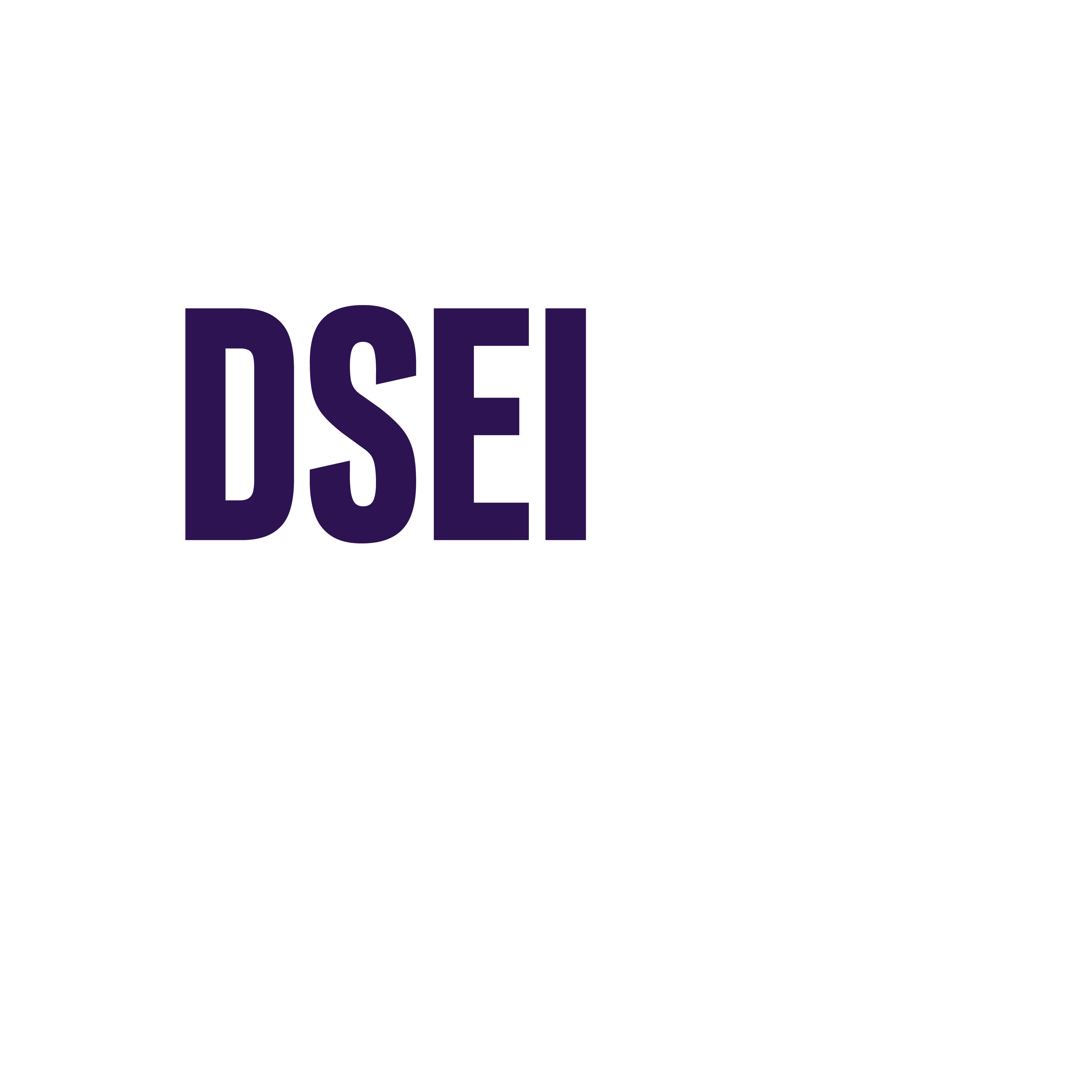
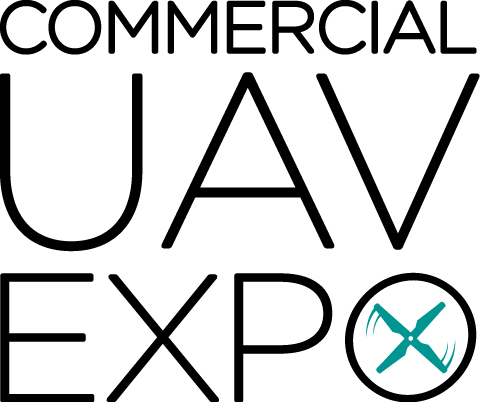
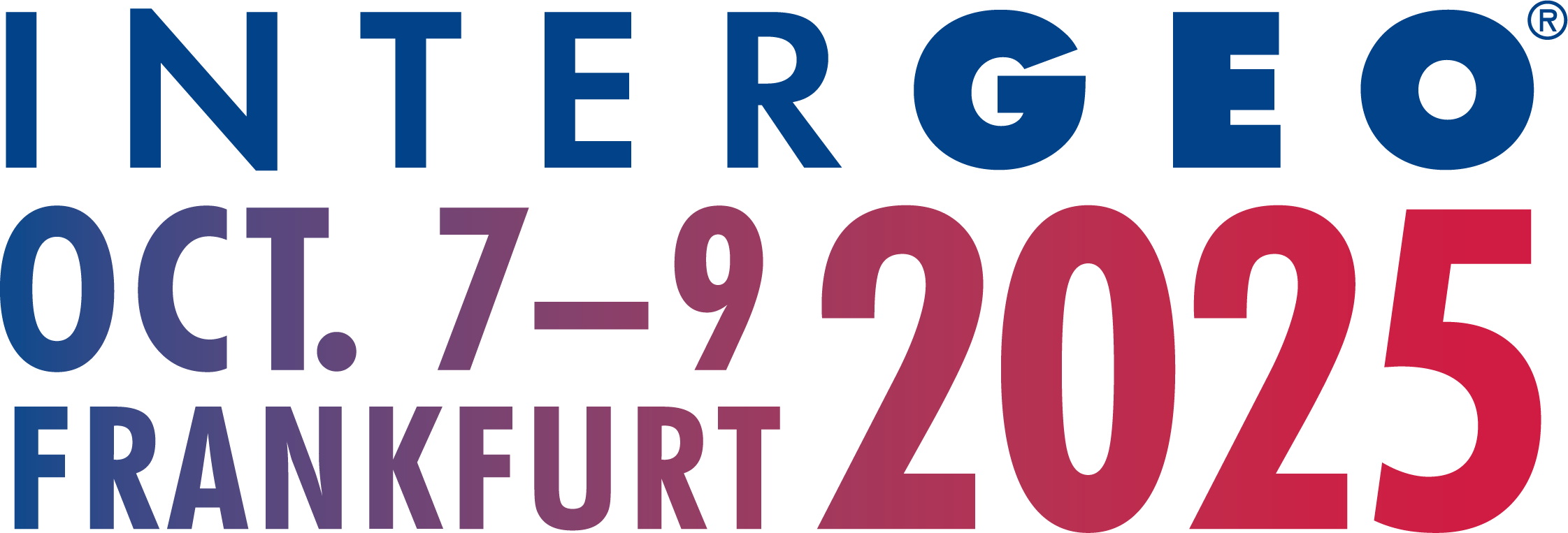
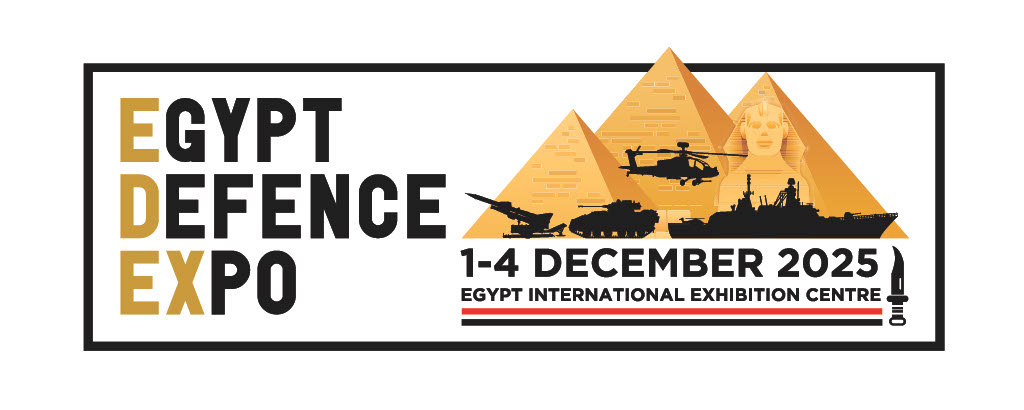
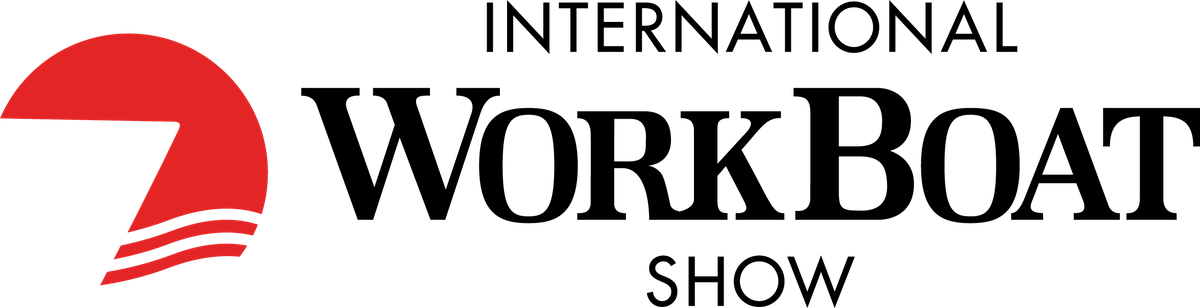