UUVs
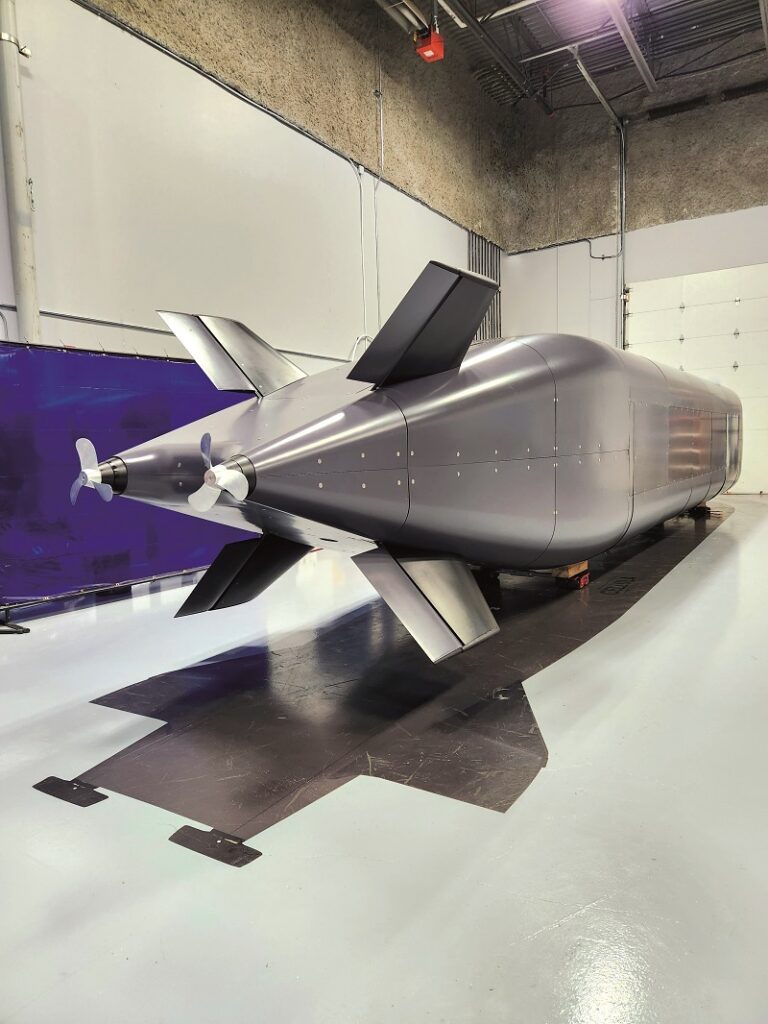
Station to station
UUV customers appear to be prizing station-keeping and hovering over other capabilities, leading to specific innovations as Rory Jackson explains
Many UUV platforms that are now well-known have been developed and supplied to civil, commercial and military markets since the 1990s. For most of that time though, the majority of UUV operations have consisted of a few hours of submerged sonar data gathering, with a small range of applications including seafloor mapping and mine countermeasures.
However, these days there is a plethora of new UUV concepts of operation (CONOPs) appearing, as a result of uncrewed systems engineers recognising new market niches to fulfil, and because growing awareness of autonomous vehicle capabilities are showing customers new ways that UUVs could help them.
Defence

For instance, naval forces around the world have long made use of uncrewed aircraft such as the Predator and ScanEagle to conduct coastal and maritime surveillance missions. But only in recent years have they begun to realise the efficiency and effectiveness that UUVs can enable in a host of very long endurance applications other than general ISR.
These can include persistent survey missions such as border monitoring, or inspecting and protecting vital underwater assets such as subsea cables for power and comms, as well as more dynamic operations such as anti-submarine warfare.
Engineering a UUV to perform such operations for months on end is challenging, but it has become a major focal point for several navies. One such vehicle is the Solus-LR from Cellula Robotics (see UST 30, February/March 2020). Its design comes with a suction anchor that can be deployed to station-keep at zones of high interest, such as contested maritime border areas or near naval docks or labs at risk of espionage, to enable it to continue surveying without using its thrusters.
The Solus-LR was built for Defence Research and Development Canada (DRDC), which wanted a long-range and endurance autonomous subsea solution. While the trialling and use of that system is ongoing, DRDC’s feedback has motivated Cellula to develop two more platforms, principally for naval use in some key contexts.
One is the upcoming Solus-XR. As its name suggests, it takes a lot of lessons and inspiration from the Solus-LR.
“The LR’s long endurance and 2000 km range came primarily from its hydrogen fuel cell powertrain and considerable onboard storage of hydrogen and oxygen reactants,” says Alex Johnson, director of AUV products at Cellula Robotics. “From its development, we have received a lot of interest in going even further than that, maybe 5000 km between refuelling, and carrying bigger, more powerful payloads.
“That’s where the Solus-XR came from. There are a number of defence and even commercial users now interested in having much more onboard energy than even the 8.5 m-long Solus-LR, while retaining the modularity and swappability of its payloads, with a standard set of interfaces capable of accepting COTS or custom sonars, special equipment and so on for different mission profiles.”
The Solus-XR is 12 m long, 1.7 m wide and 1.7 m tall (its cross-section being square-like with rounded corners), with an estimated range of 5000 km and an expected maximum endurance somewhere of more than45 days, pending further trials to ascertain an exact figure, if it never uses its suction anchorto station-keep. It also has an 8 knot sprint speed and displaces about 10,000 kg, depending on configuration differences between units.
“This is the largest UUV we’ve built so far, and it means we’re not very space-constrained. There’s a minimum volume for reactant storage, then we have to fair that in with the nose and tail, but at each of those two ends we get so much space. We can fill it with 5000 litres of payloads in total, around 10 kW of redundant Honeywell fuel cells, and all the navigation equipment, actuators and so on that we’d need,” Johnson says.
He adds that the power and volume available in the XR enables it to deploy other uncrewed systems, such as ROVs that could use manipulators for hands-on infrastructure work. For now, the Solus-XR’s first prototype has completed construction, bench tests and pool tests, and its initial sea trials are set to begin in the first half of next year.
The other new UUV solution from Cellula is the Imotus-S, a vehicle notably smaller than either the XR and LR to suit its targeted mission niche.
“The intention behind the Imotus-S is to have three or four small UUVs that users can carry on their ship, to deploy them when needed to measure their ship’s magnetic and acoustic signatures, say before entering potentially contested waters,” says Jacqueline Nichols, from business development at Cellula.
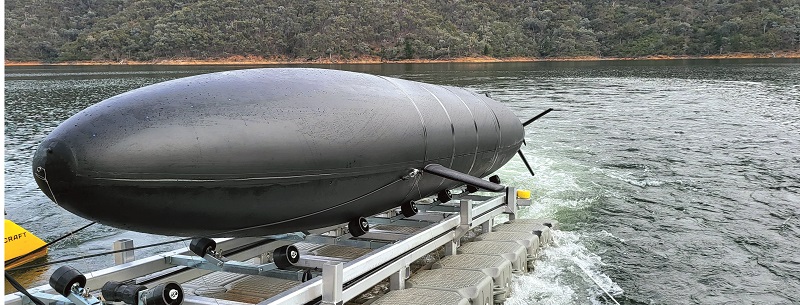
“Some people in the industry wanted to know what their ships ‘sound like’, both magnetically and acoustically, while travelling. They usually have to navigate a new ship to one of two static ranges in Canada to measure that, but after only a couple of months of travel, the ships build up a new magnetic signature, and their measurements become obsolete.”
Like the Solus-XR and LR, the Imotus-S is programmed with Cellula’s centralised, ROS-based computer and network architecture, which Johnson explains is equally capable of controlling a UUV with a slow cruise (like the XLUUVs) or one like the Imotus-S that can use its eight ducted thrusters to remain stationary, so long as it is equipped with an IMU, DVL and other standard navigation systems.
“The Imotus-S craft hold their positions in water, working as a swarm, and their host ship moves around either near or above it depending on their relative positions, so that the UUVs can take measurements from different distances and angles,” Nichols explains.
As of December 2022, sea trials off the coast of British Columbia of the first prototype of the Imotus-S had concluded successfully, with future iterations being aimed at containerised launch and recovery solutions (as opposed to the current approaches based on ship cranes), as well as further miniaturisation of the UUV to make it portable by one person.
Just as the Canadian defence forces are requesting UUV innovations from Cellula to match its growing maritime ambitions across the Pacific and Arctic, so the Royal Australian Navy (RAN) is working with companies such as C2 Robotics to achieve greater capabilities and more ambitious mission goals with the latter’s Speartooth LUUV.
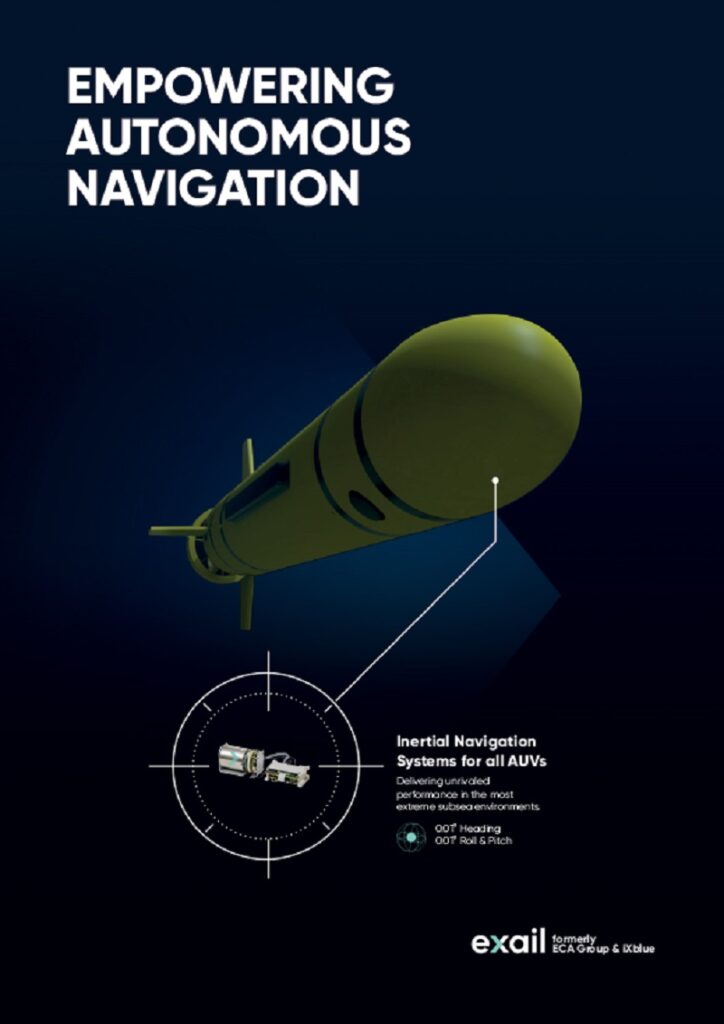
This is an 8 m-long, 1 m-beam hybrid-electric vehicle, developed for a range of 2000 km between refuelling and operations down to 2 km below sea level. Its design targets also include modularity and scalability – specifically the ability to manufacture it rapidly in high volumes and at lower costs than has been typical of the UUV industry.
These are key factors in the growing success of micro-AUVs such as the ecoSub (see UST 28, October/November 2019) and the Seaber YUCO (UST 46, October/November 2022).
“The overall outer frame, control surfaces and propulsion system generally don’t change greatly per customer, but power systems, payload space, buoyancy compensation systems and a range of other factors can all be customised by inserting or removing key modular segments to achieve different mission objectives,” explains Tom Loveard, CTO at C2 Robotics.
“Even the size of the vessel’s hull can change to a degree by using extended centre payload segments. My experience of building autonomous systems tells me that the minute we lock in a specification to a fixed value, the next customer will want to change it in some critical area, which can be very-time consuming and costly to work around.”
So although there is an initial 2 km depth capability requirement that Loveard and his engineering team have worked towards, that figure will not be a requirement in all cases. Some heavier and bulkier components can therefore be replaced if less depth capability is needed for a new user’s mission set.
“The Speartooth is thus a vision for designing systems that are far more adaptable to changes in mission sets or improvements in technology,” he continues. “If some great new subsystem element is developed tomorrow, the integration effort is more rapid, and older systems can be easily updated through modular replacement. I think this will be a critical factor for successful asymmetric warfare systems in the future.”
The scalability is also intended to bring down the Speartooth’s price point, as traditional defence UUVs owe much of their exorbitant cost to the fact that they are not designed for scale production, so there is not much impetus to push unit costs down.
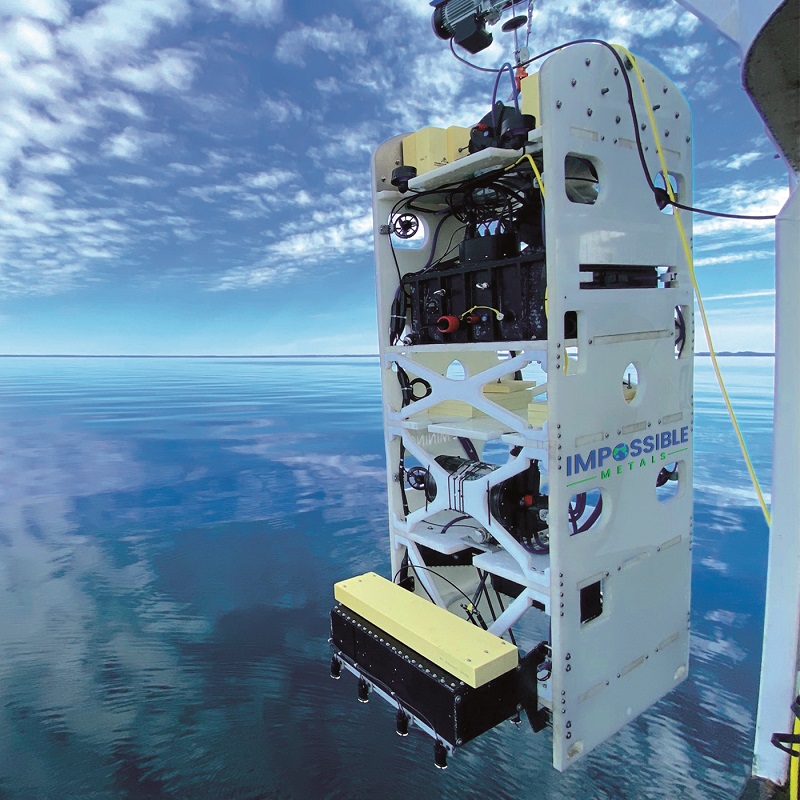
Although exact details about initial missions and some specifications remain confidential, Loveard comments, “Our current development effort with the RAN is progressing well, with a number of milestones having been reached within a rapid time frame of development.
“That has validated our approach, but there is some way to go before we can publicly say exactly where we are heading with mission or payload specifics. I think any robotics company that doesn’t have the flexibility to adapt to the technology changes ahead and have a way to incorporate them effectively into their systems will be left behind very quickly.”
Sustainable mining
North American subsea mining company Impossible Metals is continuing to develop its Robotic Collection System, which has been conceived as a UUV swarm-based solution aimed at ecologically sustainable mineral extraction by autonomously harvesting nodule-type mineral deposits on the ocean floor.
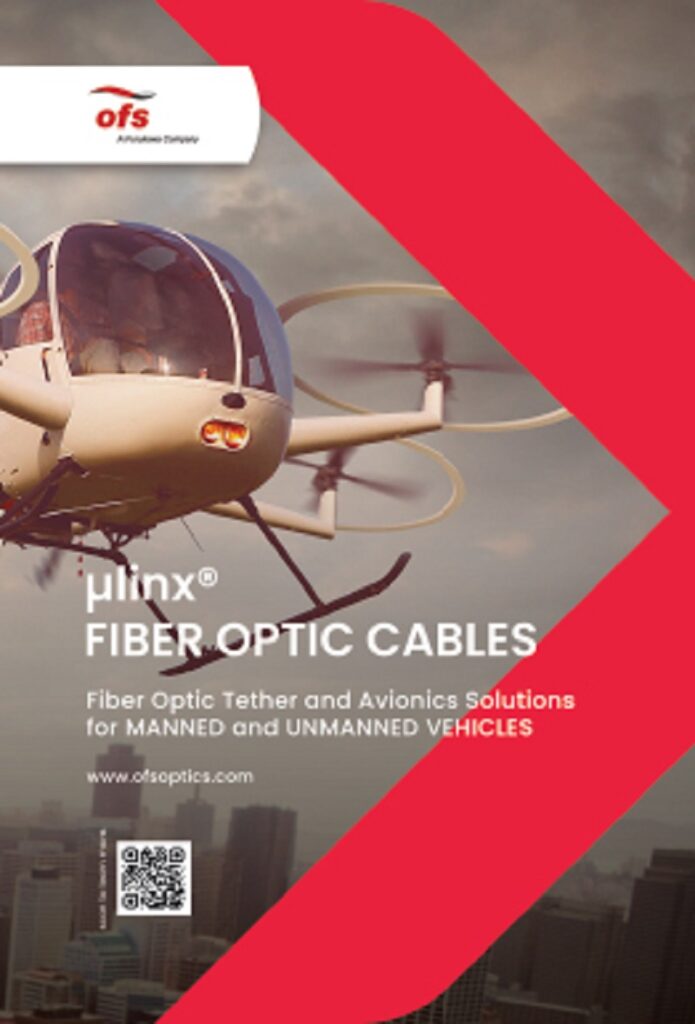
As Jason Gillham, CTO and co-founder of Impossible Metals, explains, “The world is facing a projected deficit in the amount of critical battery metals to support the transition to green energy and mobility. That is particularly so with cobalt and nickel, which are key to the highest energy-density lithium batteries, and terrestrial sources of these are either in short supply or problematic to extract from an environmental and social governance point of view.”
The deep ocean, by contrast, contains several million tons of cathode minerals (along with other useful metals) in the nodules. They were formed over millions of years and sit quite accessibly on the seabed, particularly across the Pacific and Indian oceans and in the Gulf of Mexico. They could in fact be the world’s largest and greenest source of such minerals.
“Conventional solutions for subsea mining using dredging-based technology will generate sediment plumes that could be damaging to aquatic flora and fauna that aren’t dredged from the seafloor,” Gillham observes.
“Our AUVs by contrast are designed to hover over the seabed, and once in operation they won’t generate large sediment plumes. We’re programming them to autonomously use manipulator arms to selectively pick nodules from the ground, while leaving the life behind. We can also leave habitat and habitat corridors untouched, leaving some nodules to maintain ocean biodiversity.”
Initial trials of its first, proof-of-concept prototype at 25 m depths have concluded successfully, with a second, larger prototype in development.
Gillham points to some technologies that are key to Impossible Metals’ AUV. The first is the computer vision and depth sensing necessary for identifying nodules and their location relative to the UUV.
“On our first prototype, the Eureka 1, we installed three stereo cameras for two main purposes – as a navigation aid through visual odometry and visual-inertial data fusion, for identifying nodules,” he explains. “That information is then processed so that the arm on the AUV can calculate and execute its nodule-picking.”
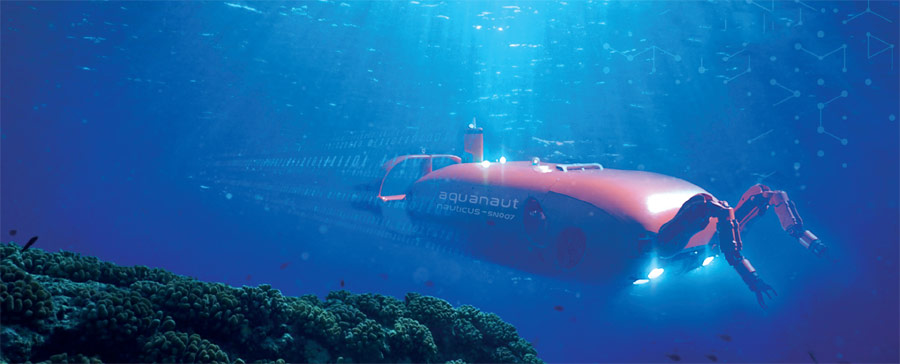
As for the arm itself, existing underwater robots use arms with serial joints, where each joint is moved by those that are closer to the base of the arm, but this style of arm is relatively slow for what Impossible Metals needs. It has therefore developed what it believes to be the first underwater ‘delta’ robot arm, a parallel robotic system in which all the actuators sit at the base to allow the end effector (and by extension, any nodule it has picked) to move quickly from location to location.
“For now, the end effector on the Eureka 1 is a simple claw mechanism, but we’ve started a programme to investigate other designs in a test tank, as well as evaluating different picking processes, for their efficacy in nodule collection and their impact on sediments,” Gillham says.
In the present design, the end effector puts nodules into a suction conveyor, which then pulls them into a hopper, to be unloaded after the AUV is recovered.
A buoyancy engine enables the AUV to return to the surface while potentially carrying many kilos of nodules. Although not a new invention, Gillham and his team have developed a displacement buoyancy system geared towards manufacturing and operational costs per kilo lifted, as well as reliability and survivability at depths of several thousand metres.
“A lot of smaller-displacement buoyancy engines are what I’d call ‘fixed-mass, variable volume’,” he says. “They always have the same mass, and change size using a piston or pump actuator, so they expand or contract to change the amount of water displaced.
“We have a fixed volume though, using a pressure vessel designed to resist external pressures at extreme depths. By pumping lots of water in and out of that vessel, we can adjust our buoyancy dynamically, so as we harvest and add mass to the AUV, we also offset that mass by pumping water out of the vessel.
“The potential energy of work needed to take those nodules from the seabed to the surface is actually equivalent to the work of pumping the water out from the buoyancy engines. So once we’re at capacity at the end of a run, we just pump a bit more water out and float up to the surface.”
He adds that for horizontal propulsion and high-frequency vertical adjustments, the Eureka 1 has 12 electric thrusters, while the Eureka 2 will have eight, as well as several control surfaces. Impossible Metals plans to test this new iteration at far greater depths than its first prototype, potentially at 4000-6000 m below sea level. This will include investigating ocean currents and how best to compensate for them during transit relative to the seafloor, with live position monitoring enabled through integrated USBL systems.
The company anticipates the first commercial uses of its system in 2026 at the earliest, as regulatory frameworks are put in place for responsible access to this mineral resource.
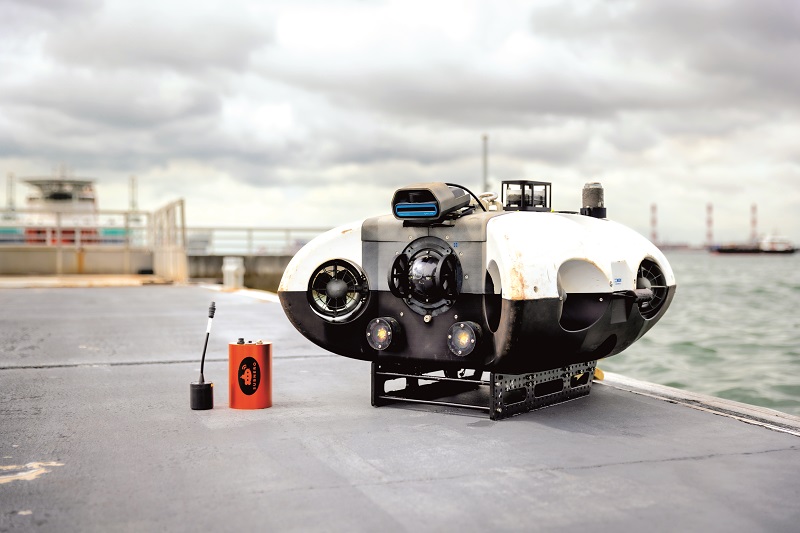
Networked inspections
As UUV missions and capabilities progress, our coastlines and oceans could see increasingly high levels of underwater traffic as uncrewed systems monitor, inspect and interact with subsea assets.
Although autonomy and sensing solutions enable UUVs to coordinate themselves in their navigation and actions, as swarms or some other group definition, the ability to wirelessly monitor uncrewed underwater systems, communicate with them and potentially take remote control of them without needing a tether – as is now commonly done with UAVs, USVs and UGVs – remains a sought-after goal for many UUV companies. Such technology would go a long way to giving assurances of vehicle safety, as well as the ability to analyse subsea data in real time and respond with optimal efficiency.
However, traditional wireless comms fail underwater because electromagnetic waves are rapidly attenuated. Acoustic comms pose an enticing alternative, but in reality they are around 200,000 times slower than EM waves. Optical modems meanwhile are a faster alternative but they lack range.
“UUV operators using acoustic comms aren’t blind to how their UUVs are performing though, but the poor bandwidth and latency makes dynamic analysis and operations impossible,” explains Manu Ignatius, CEO at Subnero.
“And in shallow waters they struggle to get even periodic telemetry updates from or commands to their craft owing to multi-path, Doppler and other noise-related effects.”
With an eye towards longer ranges, higher data rates and reliability in underwater comms, Subnero has optimised its acoustic modems first to be more robust and reliable than existing systems, and then to be tailored for wherever different end-users’ priorities lie in the trade-offs that are unavoidable when trying to communicate acoustically underwater.
“That’s important, because underwater you have many different and dynamic environments, and each UUV vendor must be prepared for multiple CONOPs,” Ignatius adds.
While every UUV manufacturer and operator would derive some use from live telemetry and command updates these acoustic modems could offer, Ignatius notes that there is a new and growing generation of ‘hovering UUVs’ (HUAVs)that are similar in dynamics and thrust layout to ROVs, but without tethers.
These navigate autonomously, in much the same way as conventional torpedo-shaped AUVs, but they also tend to perform point inspections while hovering about critical infrastructure. These inspections can then warrant either immediate feedback or even teleoperation of sensors or manipulator arms by a human in the loop to fix an imminent area of concern.
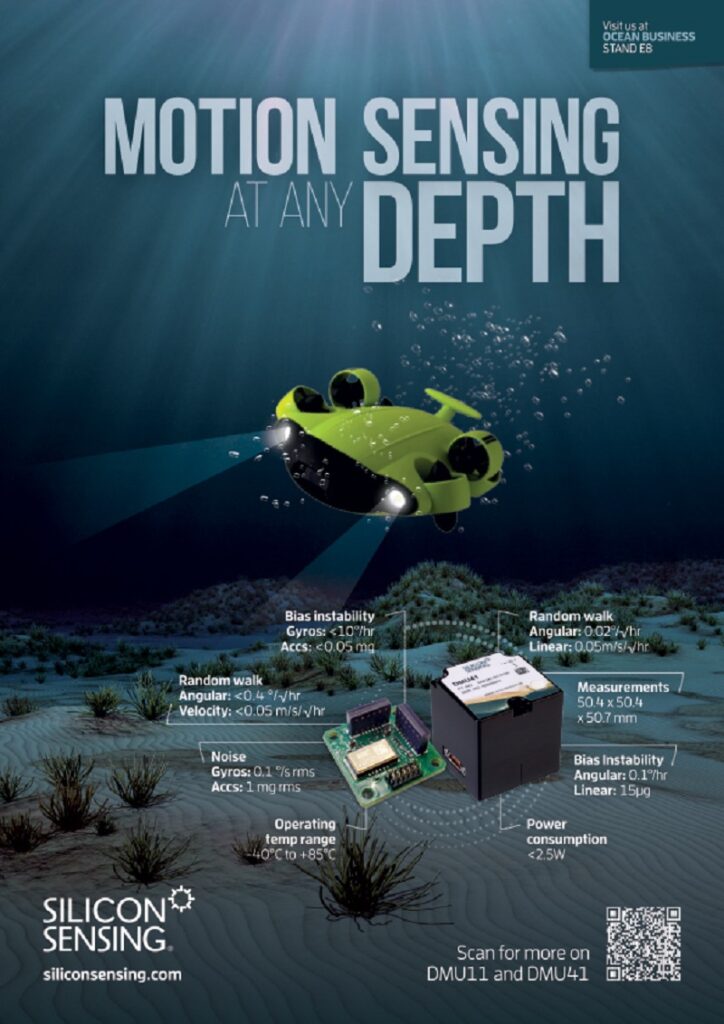
Subnero’s modems are accordingly garnering attention from parties interested in installing them as permanent comms relay networks on infrastructure such as wind farms, oil rigs and subsea cables.
“There are a few we can name who we’re now working with to that end,” Ignatius says. “One is Nauticus Robotics [formerly known as Houston Mechatronics], who selected us as the comms provider for their Aquanaut.”
The Aquanaut is a 4.4 m-long UUV that cruises in a torpedo shape for transit and survey patterns, but also transforms into an intervention mode in which it deploys two electric manipulator arms, which are stowed inside a hatch at the front when not in use.
The arms can use grippers, cleaners or other tools for manipulating underwater assets such as energy or telecoms installations.
Ignatius adds that Subnero is also working with a fellow Singaporean company BeeX Autonomous Systems, whose A.IKANBILIS HAUV we featured in our previous issue (UST 47, December 2022/January 2023) regarding its wind farm inspections.
“Our software is flexible and configurable, and marine robotics OEMs can easily integrate with our stack using different computer languages and at different levels, whether they want just bare bones transmit-receive capability or custom protocols to support content-aware end-to-end connectivity,” he concludes.
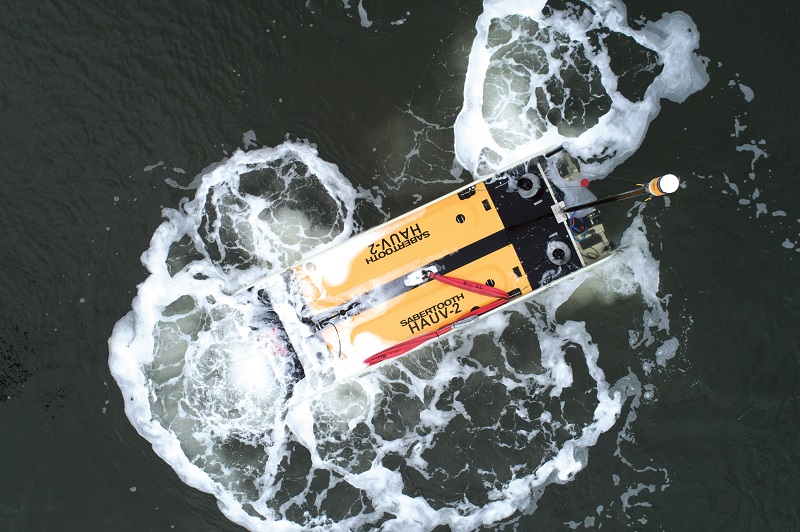
Oil & gas
HAUVs are also gaining in popularity elsewhere in the energy industry. While UUVs have long been launched for (and recovered from) pipeline inspections, there has been growing discussion about the concept of resident UUV operations.
That means having one or more UUVs stowed in an undersea hangar at some critical infrastructure where it sits, charging or refuelling, until it needs to carry out its periodic inspection duties, or is remotely activated to check for damage if a sudden fault in the asset is suspected.
As a result, the typically high costs of launching and recovering UUVs (which are normally driven up by needing a large vessel with a suitable crane) could be significantly reduced, as could the emissions associated with such vessels.
UK-based Modus has received what it claims to be the world’s first contract for resident UUV operations. One of its HAUVs will be deployed from this year to mid-2024 for “underwater intervention drone operations” at Equinor’s Johan Sverdrup field, following successful trials with the Norwegian energy company in November 2021.
The Modus HAUV-1 is a double-hulled Sabertooth model from Saab Seaeye (see UST 36, February/March 2021). It achieves propulsion and hovering through seven electric thrusters distributed about its hull, specifically Saab’s SM9 model which draws 9 A during nominal operation to produce 60 kg of thrust at 250 V DC, or 100 kg of force if 500 V DC is supplied.
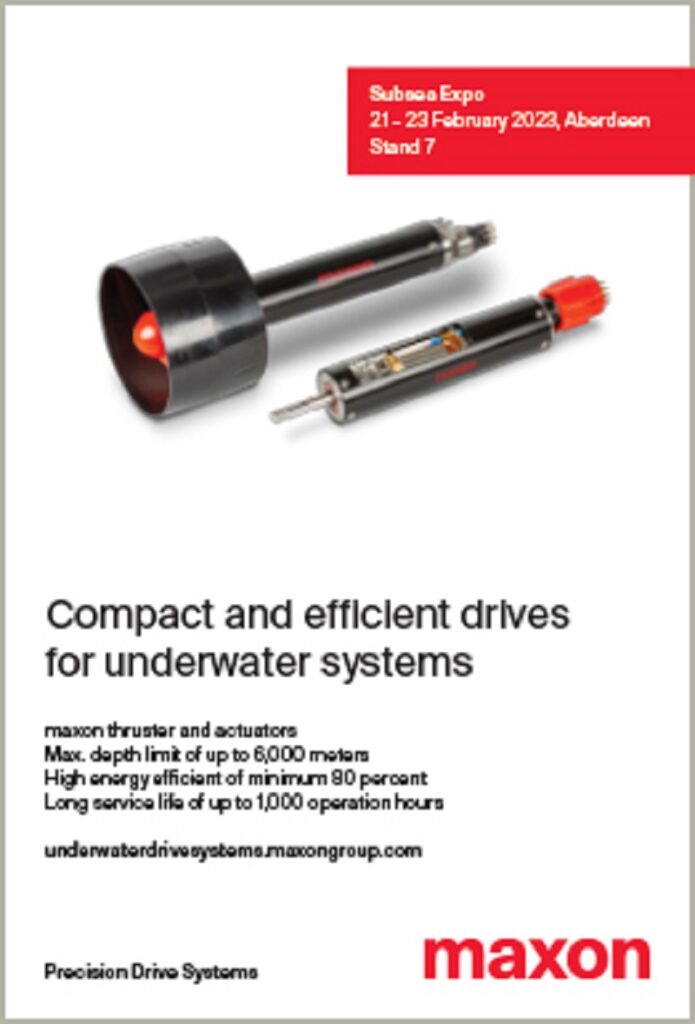
Its battery holds up to 30 kWh, enabling more than 14 hours of endurance and powering four 3200 lumen floodlights as well as a variety of payload sensors. These include cameras from Axis and Bowtech, and sonars from iXblue/Exail, Edgetech, Norbit and Teledyne.
As well as charging underwater, the Sabertooth will probably perform underwater data transfers, enabling near real-time analyses of its survey and inspection findings without having to waste time or battery energy surfacing to establish an RF data link.
Summary
The systems described here suggest that the growing specialisation of UUVs in their mission sets seems to be bringing with it a greater emphasis on station-keeping rather than speed or efficiency of movement. Be it through buoyancy engines, thrusters or suction anchors, it appears that the more tasks end-users demand of UUVs, the more they want them to stay still.
It might sound peculiar, but station-keeping and hovering are key to how UUVs can zero in on points of interest that are vital to underwater asset owners, and carry out tasks beyond just close observation.
If autonomous subsea robots can perform mining or mechanical intervention tasks, it might only be a matter of time before they are entrusted with underwater construction, repair or scientific sampling tasks that have traditionally been entrusted to human operators. While innovations in deep machine learning and other software-defined AI are enabling more and more edge cases on land to be tackled, many other use cases below water are waiting to be addressed.
UPCOMING EVENTS
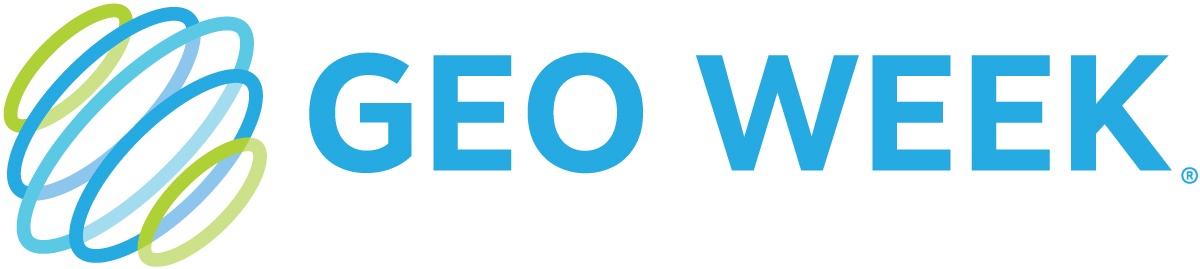
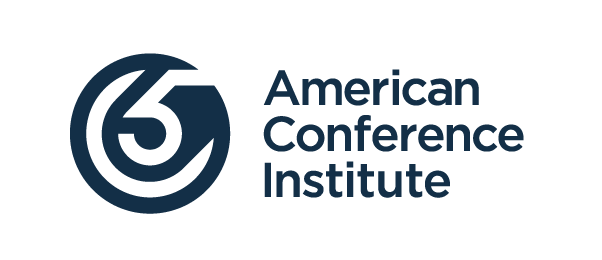
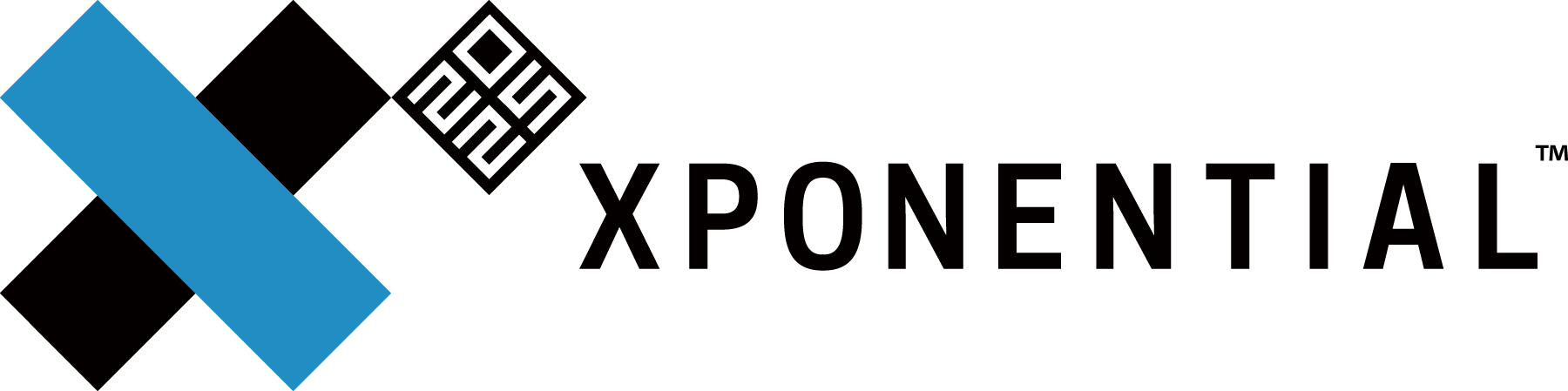
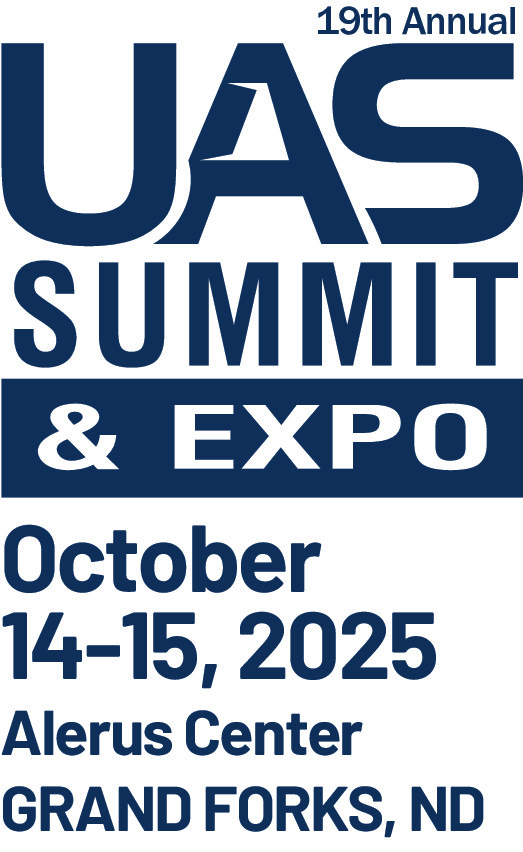
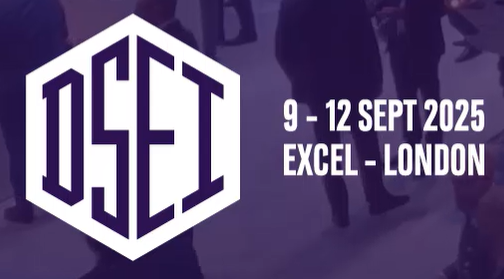
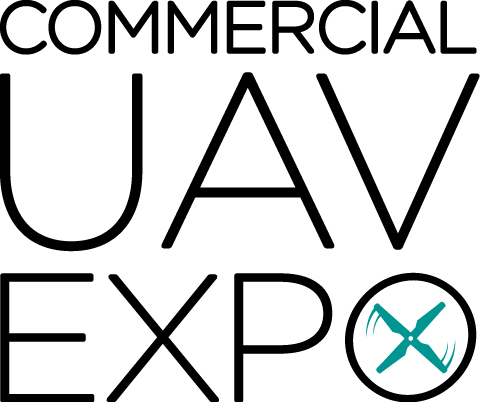
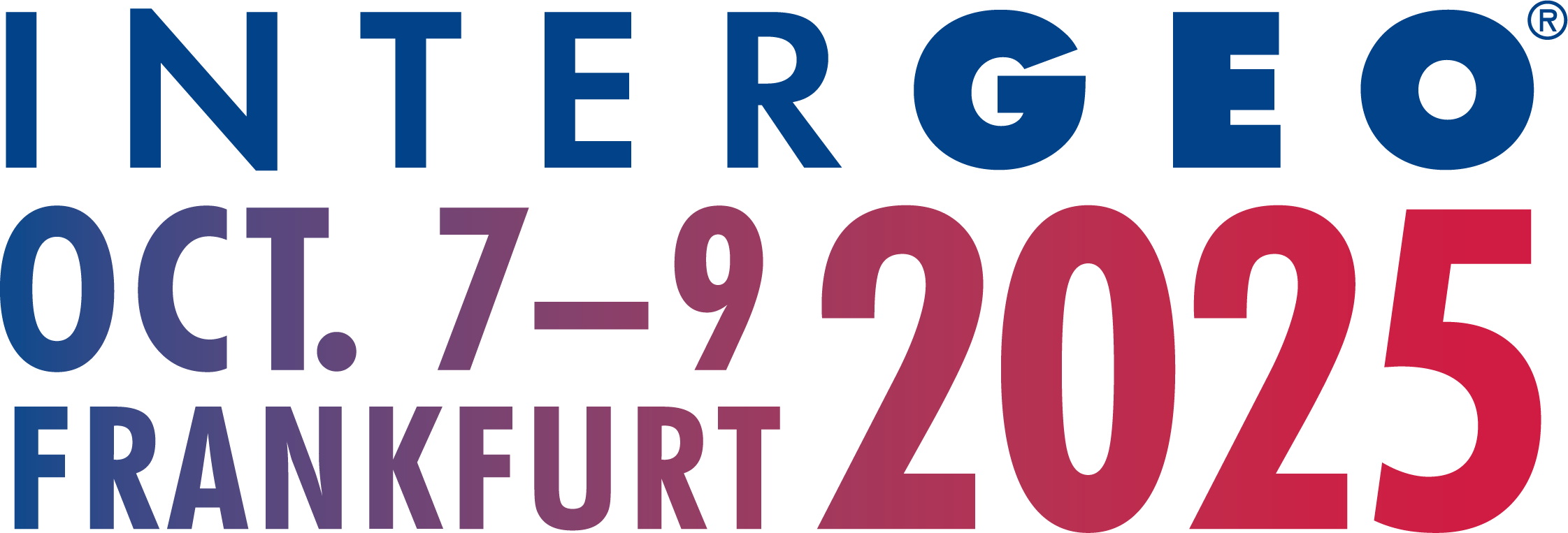
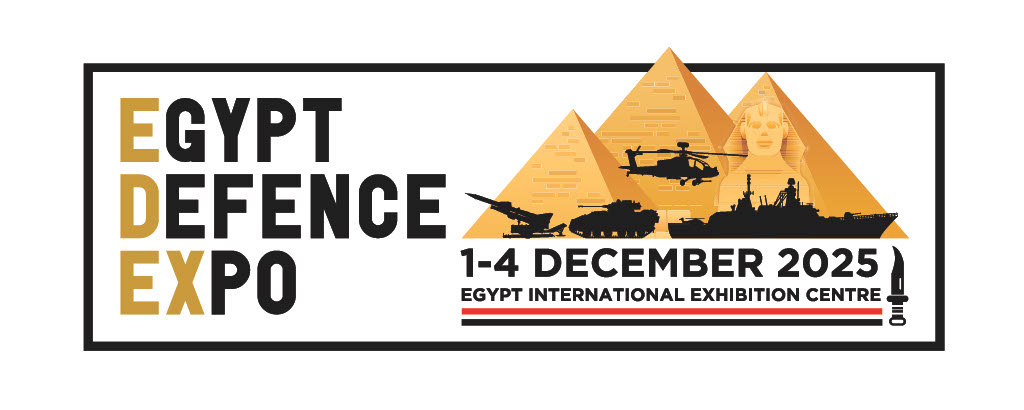
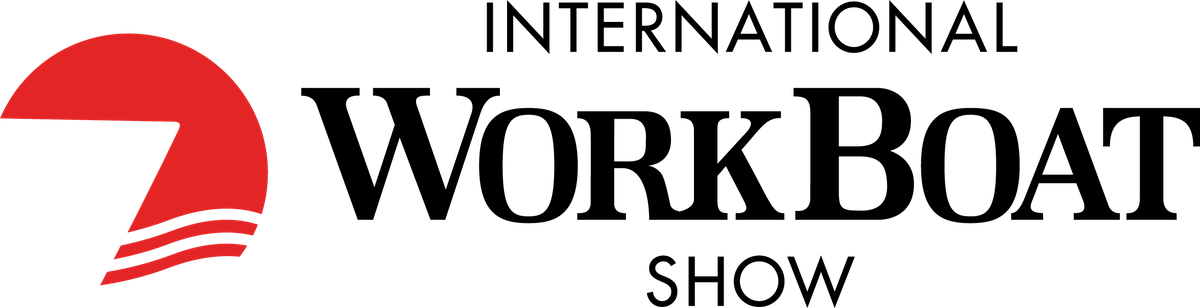
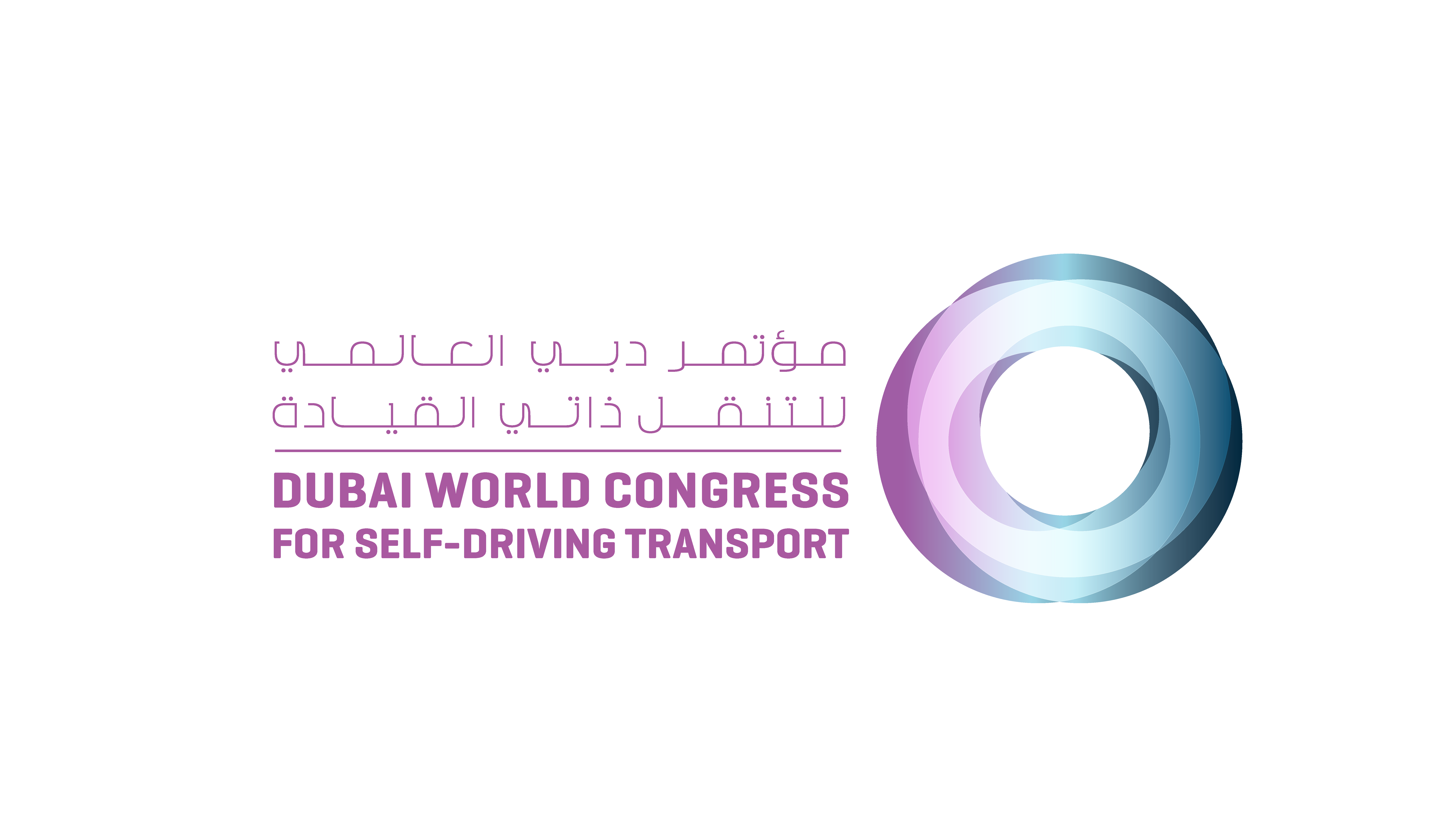
