USVs
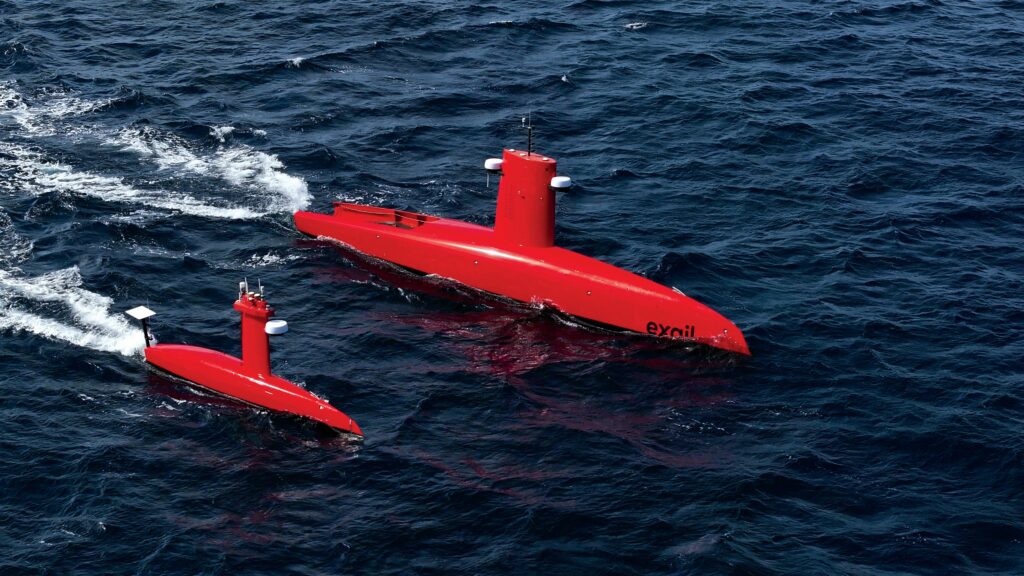
(Image courtesy of Exail)
The unsinkables
Rory Jackson investigates how USVs today are being engineered and supplied for the redundancy, reliability and endurance needed to make them serious industrial assets
Although AI is booming both as an industry and as a buzzword worldwide, those among our readership understand that the true autonomy of an uncrewed vehicle depends on far more than just its intelligence.
It is especially hard to consider a maritime vessel as truly ‘autonomous’ if it cannot survive the ravages of the aquatic environment, ranging from the harsh weather and sparse connectivity of the oceans, to the many collision and beaching hazards of inland waters.
Even if a USV is programmed to undertake rapid and well-informed operational decisions, it will not successfully shoulder a customer’s dull, dirty or dangerous burden effectively if that customer must constantly rescue it because of failures, accidents or untimely power depletion.
On top of that, time is money, as the saying goes, and the longer and further USVs can successfully carry their payloads, whether for hydrography, border monitoring, freight logistics or other purposes, the better the case for industry to switch from crewed to uncrewed operations in pursuit of a greener, safer and more efficient world.
Fortunately, one can see numerous USVs setting new standards in endurance, reliability and resilience, and hence making a good case for the deployment of uncrewed assets on the ocean, in coastal waters and in rivers – a selection of which follows here.
Archipelagic mapping
After several years of continuously working and surveying for a wide range of organisations, the Exail DriX H-8 USV is now joined by a larger, longer-endurance sibling vessel, the DriX O-16 (also called the DriX Ocean).
While the 7.7 m long H-8 is set to continue its coastal monitoring, mapping and inspection operations, the new 15.75 m long O-16 has been engineered to engage in seabed mapping at full ocean depths, with the endurance, reliability and connectivity needed for consistently safe operations in such conditions.
As Exail technical director Stéphane Vannuffelen explains, “A bigger platform inherently enables more fuel capacity, and we knew that the DriX H-8’s hull shape was already very hydrodynamic, so a straightforward and simple process of scaling it up meant keeping a similar level of efficiency and hence limiting the environmental footprint of the O-16’s energy usage.”
To facilitate the reliability needed for 30 day operating endurance, the O-16 features an overhauled internal architecture that encompasses redundancies for every key function, including energy storage, power generation, thrust, steering, communications, firefighting systems and bilge pumps. It is also designed to standards set by Bureau Veritas, Lloyds or national authorities.
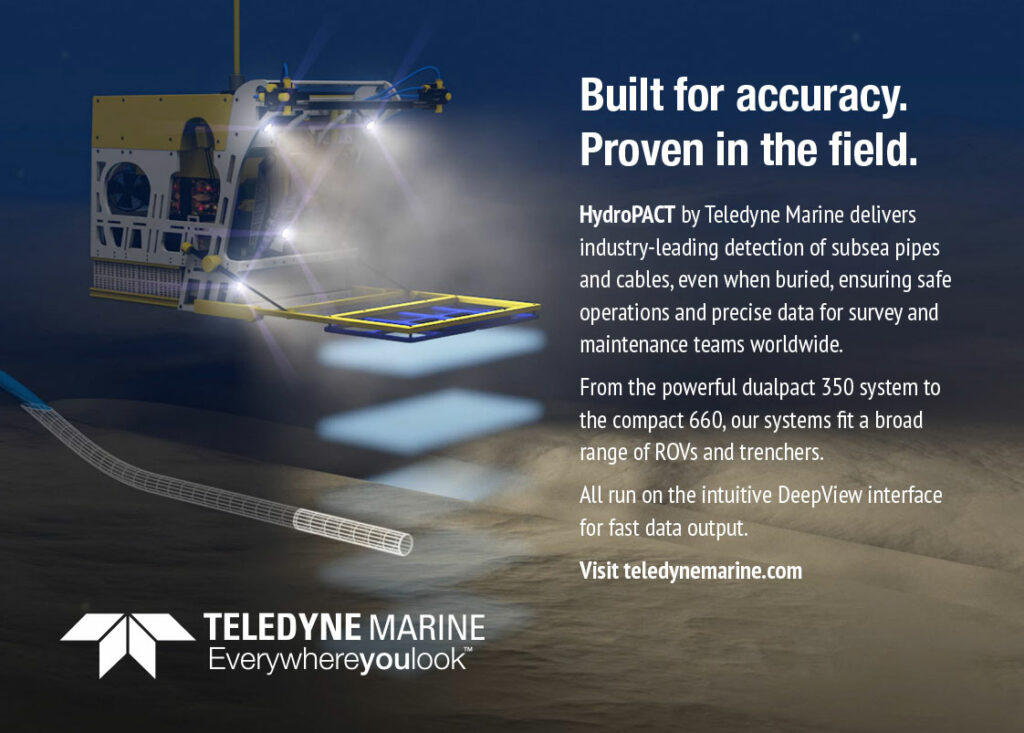
“For propulsion redundancy, we have one diesel engine that drives one propeller, and we also have a diesel generator. The dual hybrid redundant architecture for power generation allows the recharge of high-capacity batteries as well as a second propeller, which is entirely electric and battery-powered,” Vannuffelen says.
As well as providing backups, this arrangement also means the O-16 can work in a hybrid-only mode to maximise fuel economy, or for up to 45 minutes in battery-only mode (with no active recharging) for very silent operations – ideal in reconnaissance work, fish stock monitoring and certain other tasks.
For redundant steering, a rudder is mounted sternward of the engine- and shaft-driven propeller, while the electric propeller azimuth can be controlled; the two can also work together for sharper turns if needed. Comms onboard the O-16 include Iridium Certus and Starlink (relying on two separate constellations ensures continuity of service), as well as a low-bandwidth, C-band Iridium link for emergency situations.
The O-16’s gondola features a dual keel design (by which the front and rear of the gondola connect to the USV hull above) and an optimised T-shape (slightly resembling a hydrofoil) to convey a full-ocean-depth multibeam echosounder.
“It actually took a lot of design work to minimise the lift generated by the gondola, so that it doesn’t affect the trim or dynamics of the vessel in motion,” Vannuffelen explains.
“It looks like that because the sonar must have both transmitting and receiving arrays, and they must sit at 90° to each other. This type of engineering challenge may sound unfamiliar because echosounders of this size almost always require crewed vessels to carry them; as far as we know, this is the first time a sonar this large is being integrated on a USV.”
In addition to ocean-depth mapping, another key motivation for designing a larger DriX USV was the growing number of customers asking Exail for a vessel that could autonomously carry, deploy and retrieve small inspection-class ROVs (particularly to enable both below- and above-water inspection of offshore wind farms). To that end, the O-16 features a sizable ‘half deck’ at its stern, where an automated launch-and-recovery system is integrated.
Although several organisations are expected among the end users of the DriX O-16, the first announced O-16 purchase is by the Oceanic Observatory of Madeira (OOM).
“It’s very interesting, because OOM is at the forefront of oceanographic research. So, it’s fair to view their usage of the DriX Ocean – combined with their past use of the H-8 and our R7 ROV, and their suggestion for future multi-vehicle operations – as a sign of how other national oceanographic institutes may evolve their CONOPS in the future,” Vannuffelen says.
“The ability to switch from a crewed vessel to a USV is game-changing for scientific research in how dramatically it cuts the fuel and labour costs of ocean operations; the O-16 uses one-hundredth the fuel of a crewed research vessel, while carrying sonars just as big as they do. It really scales up their capabilities to unlock levels of deep-water seabed mapping, biomass monitoring and other studies in a way that wasn’t possible before.”
Offshore survey
Although typically a manufacturer of small UAVs for photogrammetry and aerial inspection applications, Poland-based GeoPixel has developed its first USV, the 2 m long D210, following requests for an industrial-type offshore survey solution.
As Michał Szczodrowski, CEO of GeoPixel explains, “We started building our first USV model, called Sharky, around five years ago, which was a small yellow catamaran. I have a number of acquaintances who are surveyors, and knowing that I had designed, manufactured and sold several UAV products, they asked for something similar that could work on lakes and rivers.
“That led to further requests for something that could provide similar performance in open-ocean conditions, meriting a bigger construction, which could hold heavier equipment, especially something like a high-quality echosounder, which can weigh 20-40 kg.”
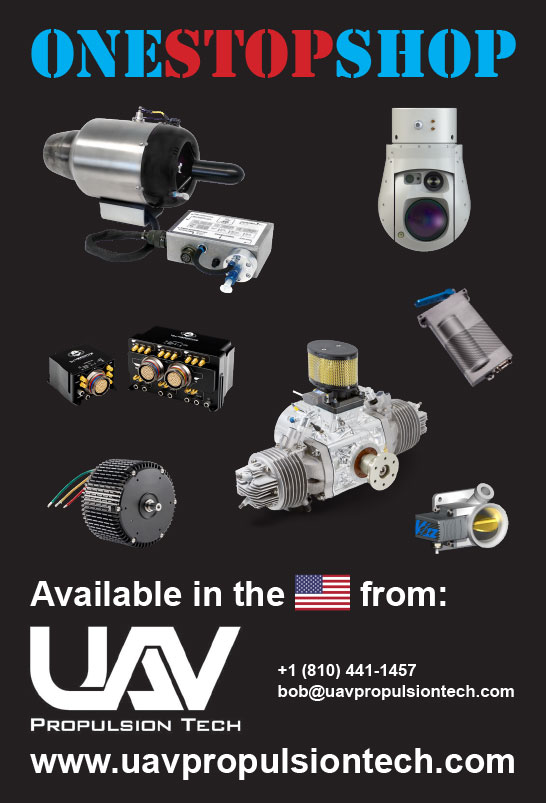
Given this need to not only survive the severe waves of the open ocean, but to consistently produce sonar imagery free from vibrations and shaking without breaking down, the D210 has been designed (in close consultation with a yacht designer within GeoPixel) to weather harsh sea conditions with a minimum of movement, together with optimised survivability and energy efficiency.
The vessel is designed as a monohull, with a flat-bottomed shape (rather than a traditional round-bottomed or v-shaped profile) and a smooth, sloping bow, somewhat resemblant of barges and freighters. Overall, this configuration trades speed for a stable, hydrodynamically efficient surveying platform capable of roughly 11.66 knots (6 m/s), optimising it for long endurance operations (compared to its size) of 6-8 hours depending on payloads and environmental conditions.
Additionally, the rear of the USV’s top deck features a roll bar with an empty upper section that is filled with air. So, even if the D210 should capsize because of a strong wave or a severe weather event, it passively self-rights itself, thereby preventing one of the major reasons for USV operators to either lose their autonomous boats, or have to sail out with a crewed vessel to attempt a rescue.
Onboard energy comes entirely from battery packs, with propulsion provided via two shrouded thrusters installed beneath the stern of the USV’s hull, which represents a simple differential thrust capability enabling the vessel to steer without relying on servos (be it for turning rudders or for an azimuthing function from the thrusters). Maximum speed is to be determined through testing, although Szczodrowski estimates it should be somewhere around 19.44 knots (10 m/s) based on simulations.
“We hope to have started in-water testing of the D210 prototype in the Baltic Sea by June this year. Although we’re planning to acquire funding before we go to the lengths of commercialising it as a fully available product alongside our UAVs,” Szczodrowski says.
Similarly, long-established uncrewed systems OEM Kongsberg Maritime has delivered the REACH REMOTE 1 USV to its end user, ROV and engineering services company Reach Subsea ASA in Norway.
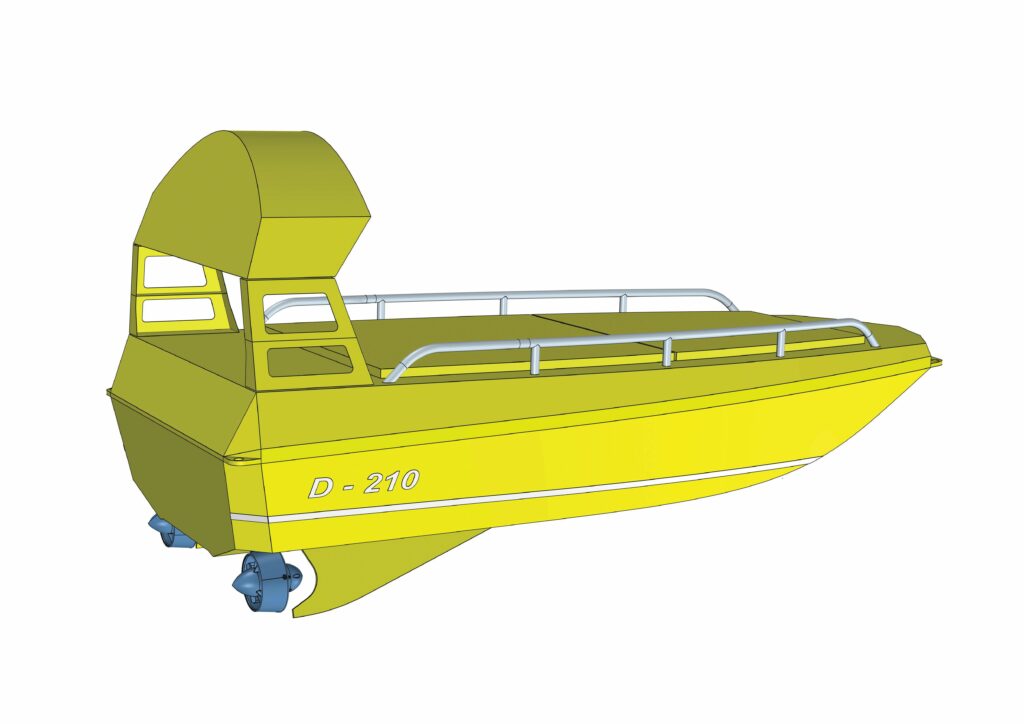
(Image courtesy of GeoPixel)
The REACH REMOTE 1 is a 24 m long USV, integrating numerous Kongsberg Maritime electronics as well as an ROV, and it is expected to initially conduct underwater surveys off the coast of Haugesund in Norway, although a broader remit of applications is expected in the future.
Delivery of the product has come after a programme of intensive sea trials by classification society DNV as well as the Norwegian Maritime Authority to validate its safety and reliability. The involved partners also aim for the USV to reduce emissions by 90% compared with its typical crewed alternatives.
During its sea trials, the USV was monitored and controlled from a temporary, mobile remote operations centre (ROC) onboard the nearby support vessel, Avant. For its pilot operations, Massterly (a joint venture between Kongsberg Maritime and Wilhelmsen), will control the USV from a land-based ROC in Horten, Norway. Increased autonomy will be introduced in a gradual approach pending technology readiness.
Inland shipping
Part of the reason behind the push for autonomy in logistics is that many industries stand to gain efficiencies (in energy usage and environmental impacts, not to mention improved employee satisfaction) from moving certain freight operations away from manually driven trucks to self-driving vehicles and low-altitude cargo UAVs.
With autonomous water taxis, ferries and seagoing freighters having provided measurable evidence over the last few years that going autonomous cuts fuel usage significantly, those familiar with USV technologies are now breaking ground in terms of inland shipping via rivers and canals. One of the largest efforts in this regard comes from the ReNEW (Resilience-centric, smart, green, Networked EU inland Waterways) project, funded by the EU’s Horizon Europe initiative, with one of its four key segments focusing on the development of an autonomous, zero-emission barge of 1500 t (90 TEU).
As of writing, the vessel design of the barge is finalised – and compliant with the Conférence Européenne des Ministres des Transports (CEMT) standards, enabling it to transport freight between any CEMT-member countries – with prototype construction to commence very soon.
Antoon van Coillie, director of autonomous freighter developer ZULU Associates and project leader for the ReNEW project’s autonomous X-Barge tells us, “Situational awareness, even in a busy shipping lane, is totally different from automotive. In the latter, your vehicle needs to make split-second decisions, or else there’s a traffic collision or maybe even a pedestrian gets impacted and killed. In shipping, timely decisions are still important, but it’s far easier to predict what’s going to happen around you.”
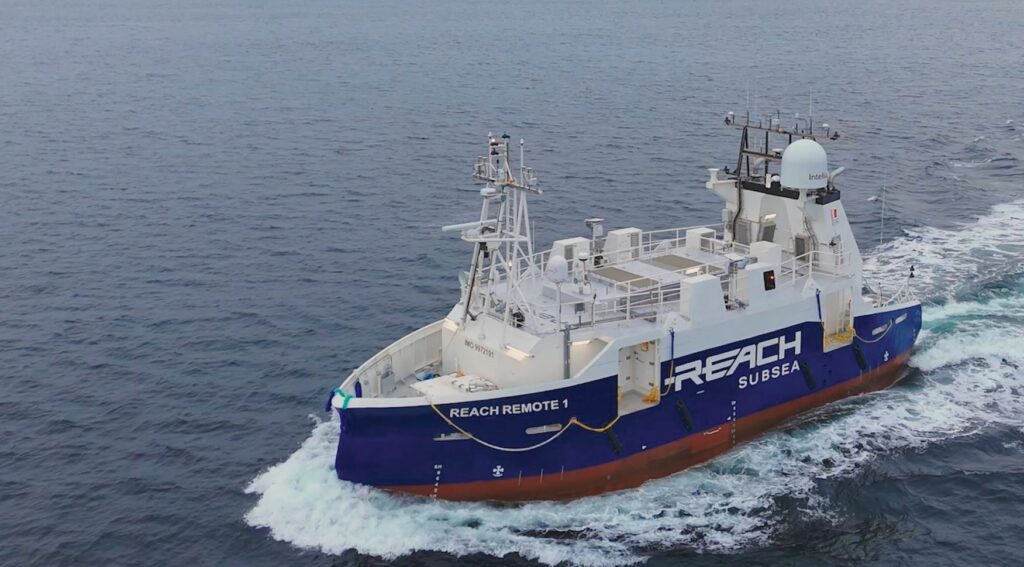
(Image courtesy of Reach Subsea)
This has implications on the X-Barge’s planned sensor architecture. The vessel is to integrate sonar to negotiate underwater obstructions, radar for tracking the distance and bearing of above-surface objects (and hence avoiding them), cameras mainly for remote supervisors to keep an eye on their assets, and potentially Lidar for mooring (although van Coillie notes that Lidar is otherwise too short-range for most inland shipping applications). Positioning data will also be achieved likely through GNSS or cellular links, with Starlink being solely used in an auxiliary fashion owing to “the supplier’s present unreliability.”
Although autonomous shipping symposia have discussed much over how to ensure that autonomous vessels abide by the International Regulations for Preventing Collisions at Sea and behave in exactly the same manner as crewed vessels, the project leader notes that neither safety nor efficiency would be aided by rigid adherence to crewed norms.
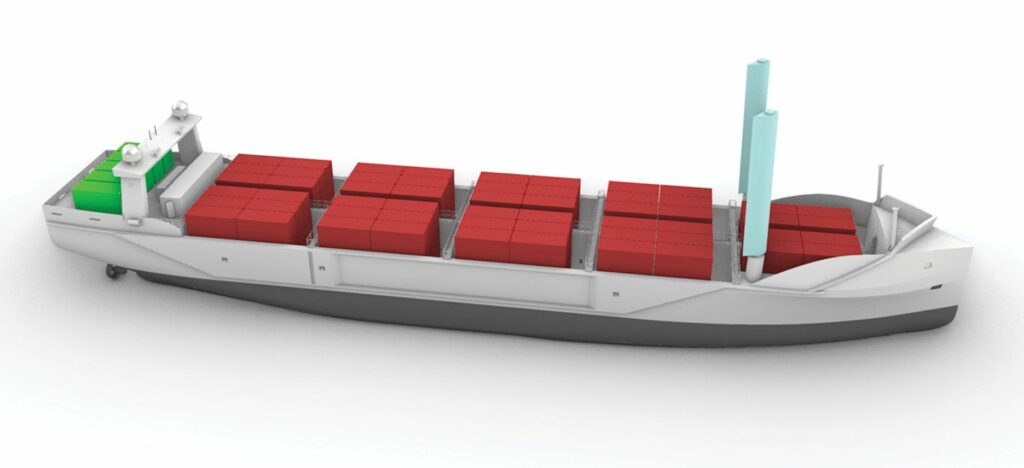
(Image courtesy of ZULU Associates)
“People may think you need crew onboard the vessel in case something goes wrong, but small faults are already either ignored by the crew, or should be covered by onboard system redundancies, and if there’s a really big fault, safety regulations require that you evacuate the crew right away,” van Coillie muses. “It’s very rare that the crew actually repairs the vessel mid-sail. So, why keep them onboard?”
Additionally, by removing the crew, accommodation, kitchens and other life support facilities, space is freed for three 20 ft containers filled with batteries at the stern, enabling the outer hull to present a more slender and energy-efficient shape than that typical of inland barges.
“Because of this hull, and thanks to the fine, digitalised, by-wire autonomous control, the X-Barge will only use around 250 kWh/h at its operating speed; the Flanders Hydraulics Institute verified this through extremely detailed CFD and tow tank analysis,” van Coillie explains.
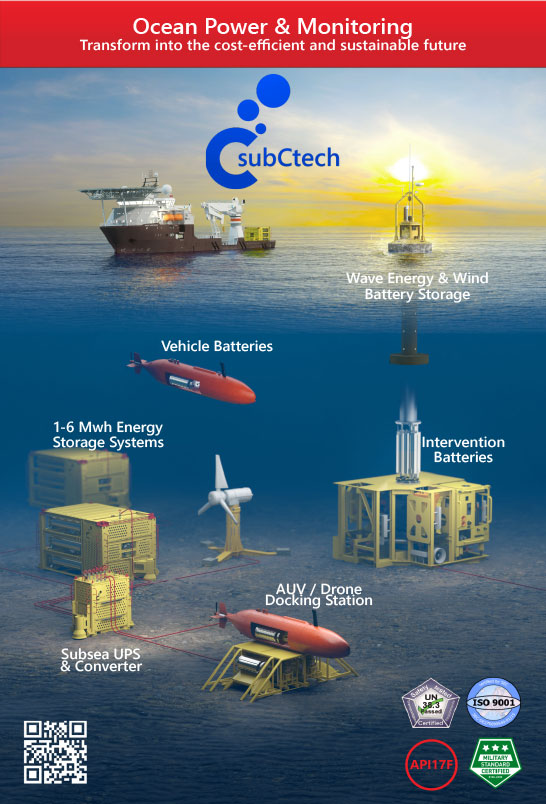
“And designing the ship such that energy is placed onboard, as a separable, containerised subsystem means we’re energy-agnostic. If we need more range, we can put a diesel generator and tanks onboard, or even a hydrogen fuel cell system. Each 20 ft battery container gives us 2.5 MWh and hence 10 hours of operation, meaning a 30 hour maximum endurance, and maybe a 24 hour conservative estimate for operating endurance if we account for unexpected disruptions here and there.”
To maximise safety over those 24 hours, every subsystem is at least dual-redundant, even down to the navigation lights. Additionally, the vessel’s drivetrain features two rudder-propellers at the stern, and one bow-mounted azimuthing jet stream thruster; the latter enabling much simpler algorithms for fully automated steering than would be possible through rudder-propellers alone. Van Coillie adds that the propulsion systems have been supplied by Schottel in Germany, with electrical systems by EMS and solutions for both vessel autonomy and remote control provided by MAHI in Belgium.
Underwater inspection
In a new leap forward for USVs empowering underwater operations, EvoLogics has unveiled a new capability for its Sonobot 5 (featured in Issue 37), in which the 1.3 m length USV can integrate a USBL device that underwater vehicles can use as a real-time source of subsea positioning data – as demonstrated by the Quadroin AUV produced by the German company.
As Llewellyn Fernandes, electronics team lead at EvoLogics explains to us, “A consistent problem in underwater positioning is that USBL buoys are typically static, which limits the range of their effectiveness and hence the range of operations of UUVs reliant on them for real-time navigation.
“But by successfully integrating USBL into the Sonobot, with a deployable and retractable arm, the USV can track and follow underwater assets at a certain distance from the surface, including AUVs like Quadroin as well as human divers, and hence we can track them both through the Sonobot’s GNSS. We can also get live health and mission telemetry from the Quadroin to understand what it’s doing and what condition it’s in, and update or reconfigure the mission through the acoustic connection from the USV to the AUV.”
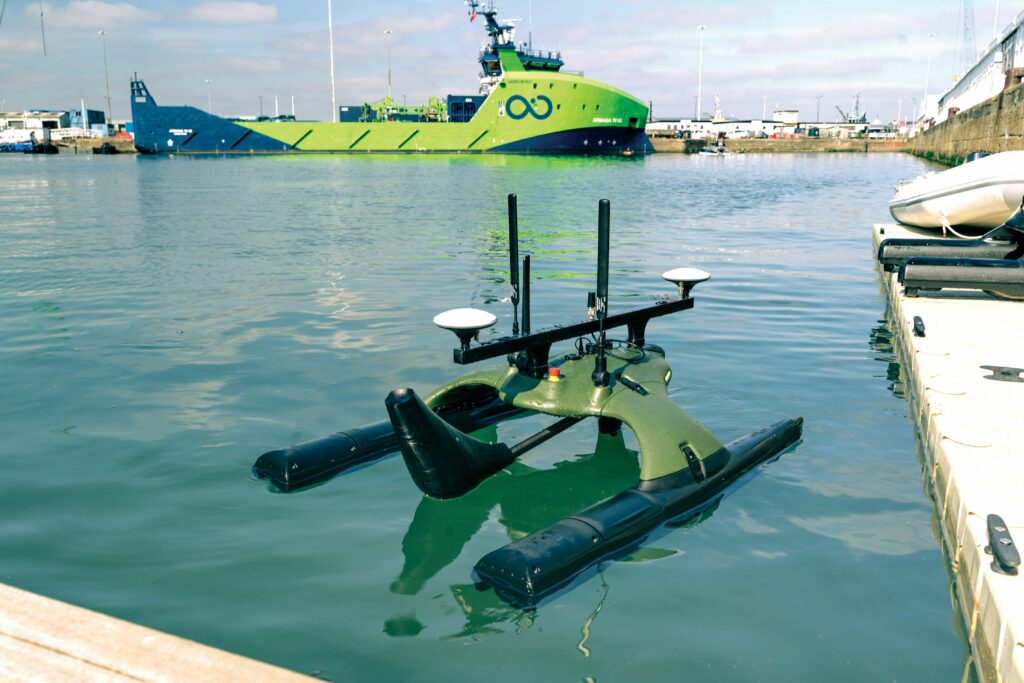
(Image courtesy of EvoLogics)
The core of the system is the retractable mechanical arm, partially because it enables the USBL transceiver to be retracted above the USV’s floats when stowed on land, and then lowered beneath the floats into the water when the vessel is operating (hence why a static pipe or shaft would not work).
“That also gives the USBL depth and keeps it away from the surface; but the mechanical arm also needs to be very accurate, returning to the exact same point every time you deploy it. If it moves by even a few degrees, that means USBL positioning errors start accumulating,” Fernandes says.
The arm integrates a brushless DC servo motor, a gear and a position sensor (separate to the servo) to enable closed-loop control of its movements.
“And to work reliably in water, its enclosure needs to be IP-rated and watertight; good stiffness is also needed, so overall that led us to choose a carbon composite tube, with cables routed through the centre of the tube, and the USBL head at the bottom,” Fernandes says.
“Rather than use our standard USBL product there, we modified the outer profile of the USBL to make for a streamlined shape that wouldn’t interfere with the hydrodynamics or drag profile of the Sonobot.”
Underwater maintenance and repairs
With so many major organisations across both public and private sectors now looking to substitute industrial USVs for large crewed vessels, a rising number of shipyards and designers distinguished for their crewed vessels are being engaged to produce their first uncrewed systems.
One of the latest notable examples of this trend comes from USV AS, a Norwegian joint company formed between DeepOcean Group, Solstad and Østensjø Rederi. The company commissioned the design of the recently launched USV Challenger – a 24 m long, 7.5 m wide, diesel-electric vessel – from Norway’s Salt Ship Designs, with its construction undertaken by Spain’s Gondan Shipyard.
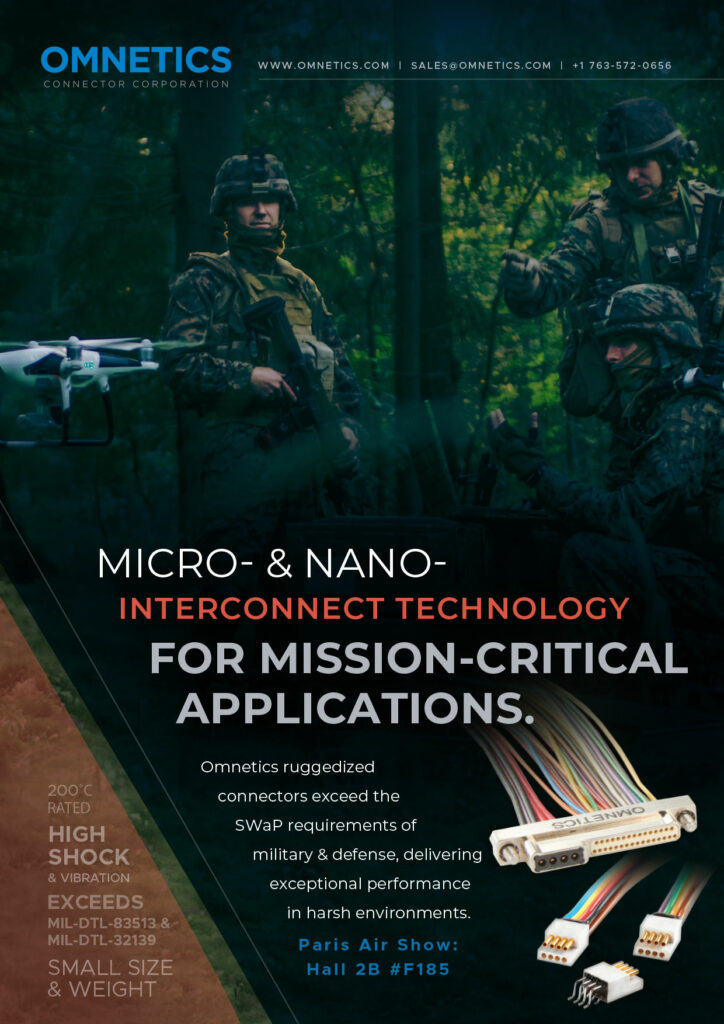
Like the REACH REMOTE 1, Challenger is intended to save around 90% of CO2 emissions compared with its crewed equivalents, serving particularly in the field of inspection, maintenance and repair of offshore and underwater infrastructure.
Its most anticipated application will involve functioning as an autonomous platform for the launch and recovery of ROVs, the latter of which will be controlled from an ROC owned by Remota (a company specialised in remote-, semi-autonomous- and fully autonomous-control of maritime industrial vehicles) in Killingøy, Norway.
As Inge Skaar, design manager at Salt Ship Designs tells us, “While designing a ship should theoretically be the same whether crewed or uncrewed, creating USV Challenger did pose something of a challenge, primarily because of its size. It has a very small structure, both compared to our existing portfolio of vessel projects, and relative to the amount of equipment to be fitted onboard; it fell to us to determine where the subsystems – largely selected by the owner – would go.”
While the vessel’s 400 kWh battery pack is small relative to the overall ship volume, keeping space for the gensets, switchboards area, ROV bay, and launch and recovery system was more difficult; hence, designing Challenger was largely an exercise in packaging around those subsystems. Up to 10 t of diesel can also be stored onboard.
“And for safety and approvals, crewed vessel regs specify a huge number of areas where humans manually intervene, so redundancies were absolutely crucial for covering Challenger in situations where a crewmember would interfere to resolve an issue,” Skaar says.
“A crewmember can do a lot of things to identify faults: they can look around, they can smell for chemicals, they can listen for leaks or metallic noises, and they can touch surfaces to feel how hot they are. Replacing those human senses with CCTV cameras, thermal cameras and microphones was critical for Challenger’s long-term survival at sea. It also means the human in the ROC can ‘feel’ and take note of everything that’s going on onboard.”
Further approval-critical redundancies required doubling-up the onboard generator and switchboard rooms, to cover situations where a fire might break out in one engine room, requiring that room to be shut down and the other engine room relied upon while onboard fire extinguishing systems contained and diminished the flames.
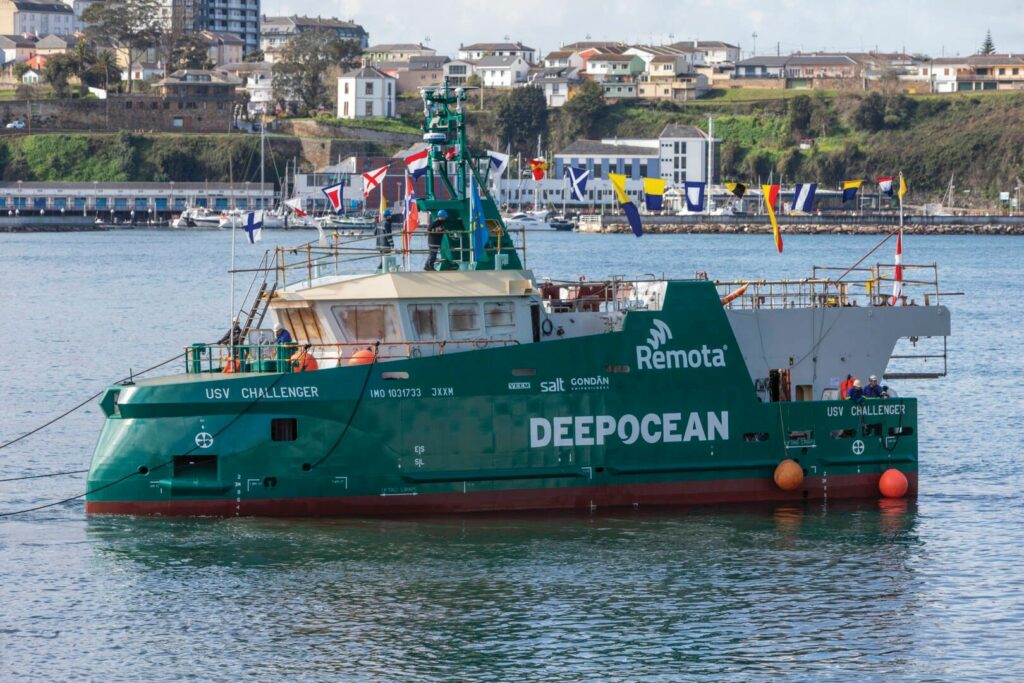
(Image courtesy of Gondan Shipyard)
“That took huge discussion: how to optimise the layout, subsystems, and CONOPS of the vessel so that at the very least, it would always be able to limp home amid the loss of one diesel generator or switchboard,” Skaar notes.
The vessel’s batteries provide a critical course of backup energy in the event of generator failure, including short-term faults such that a mission can continue while one or more generators are remotely troubleshot and restarted. The batteries are also covered by fire safety systems (as is every room in the USV, in fact), so that any feasible fire can be extinguished during operations.
Once USV Challenger has tallied a modicum of successful real-world operating hours, the parties involved anticipate that USV AS will want a larger fleet; hence, further collaborations and USVs will follow.
Summary
As one observes these industrial-grade vessels, it is hard not to notice how many are serving as platforms for UUVs of one sort or another, following the trails blazed by the likes of TideWise (Issue 45), the WAM-V (Issue 49) and ACUA-Ocean (Issue 60), all of whom focused efforts on large, stable USVs for carrying uncrewed aircraft and underwater robots.
Just as UAVs are sometimes referred to as tools for getting cameras where people need them, more USVs are now functioning as mobile hangars for other vehicles, particularly as autonomous vessels get better at surviving the dire conditions of open water. Even inland freighters like the X-Barge could serve as dual-use platforms, carrying containerised goods and drone-in-a-box solutions for UAVs to periodically pop-out and survey riverside infrastructure (many have suggested that trains should integrate UAVs to such ends).
Such opportunities for uncrewed–uncrewed teaming also represent potential for growth in their key enabling technologies. Improvements in fibre optic tethers and acoustic or optical modems for underwater connectivity, for instance, will be increasingly vital for such CONOPSs, as will mesh radios and lightweight SATCOM or transponders for above-surface comms.
And as UUV owner-operators also start operating USVs, UAVs and potentially UGVs too, a race might soon commence for major offshore asset holders to start employing technical experts in aviation, robotics and more, to keep their fleets ahead of the competition, and ensure that all of their vehicles – on sea, air and land – can come home safe and sound.
UPCOMING EVENTS
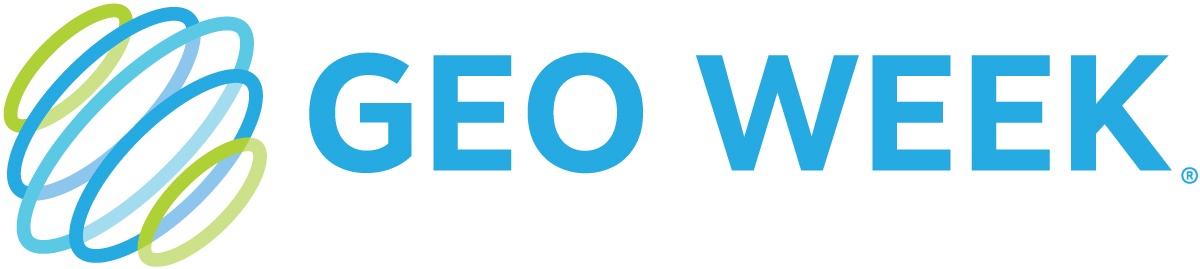
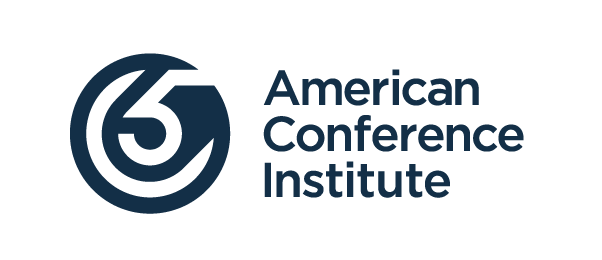
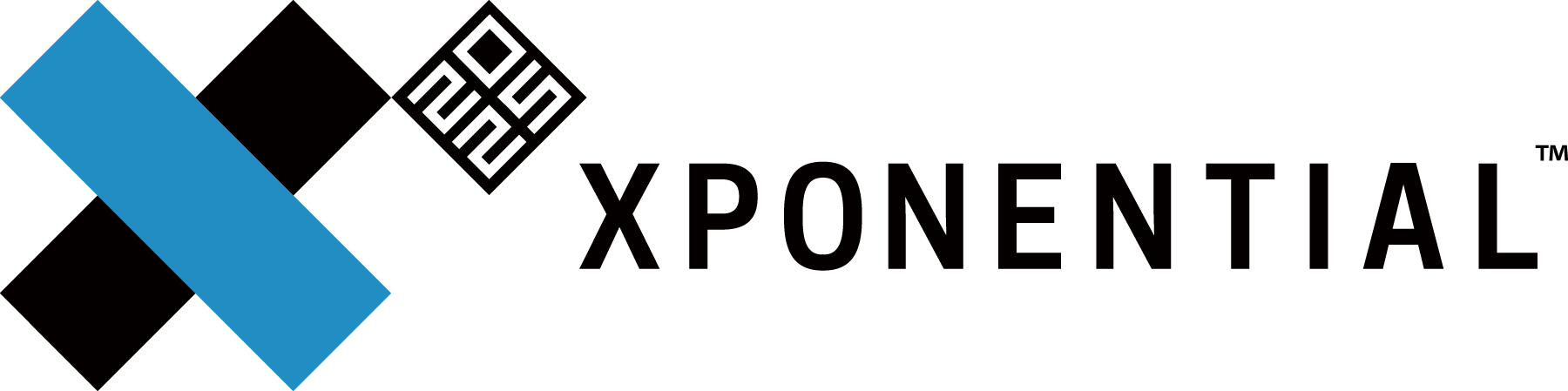
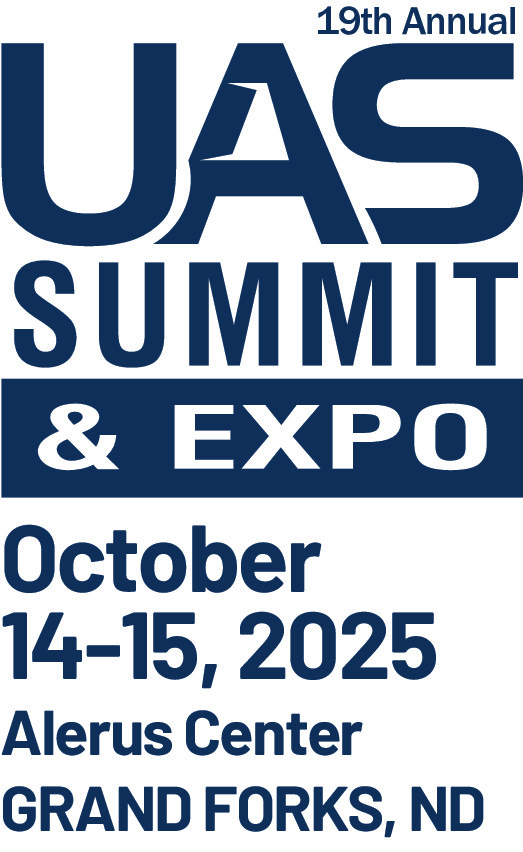
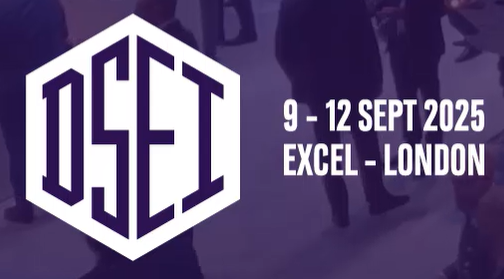
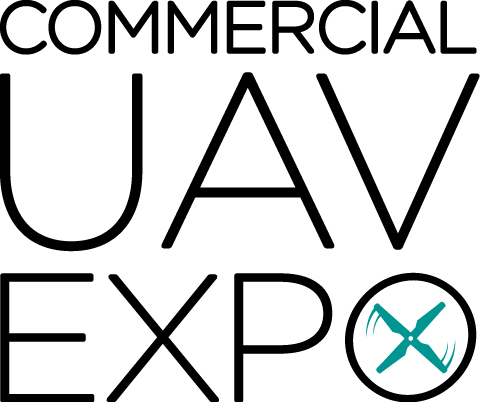
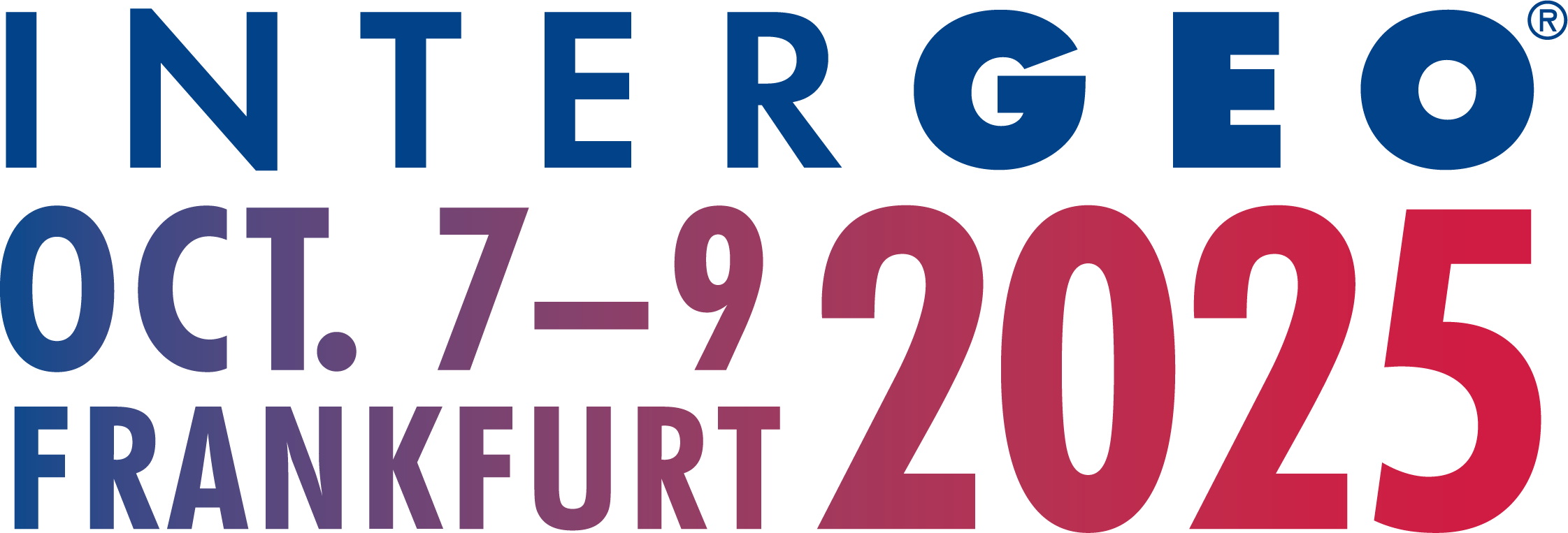
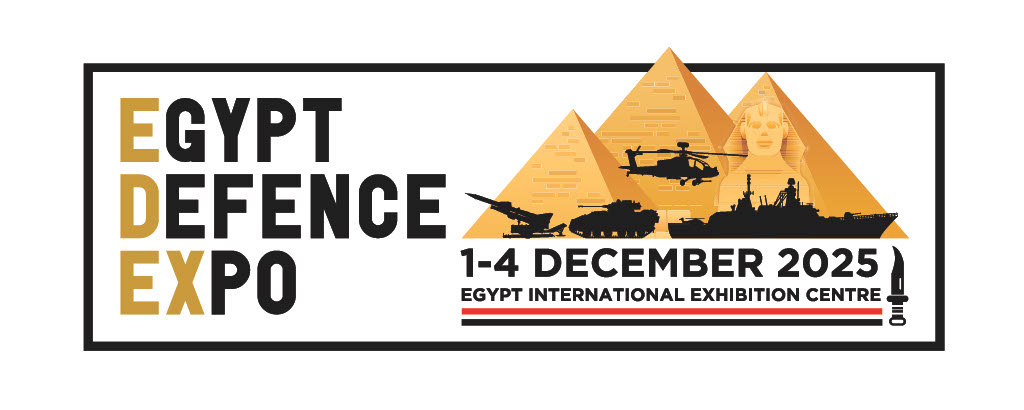
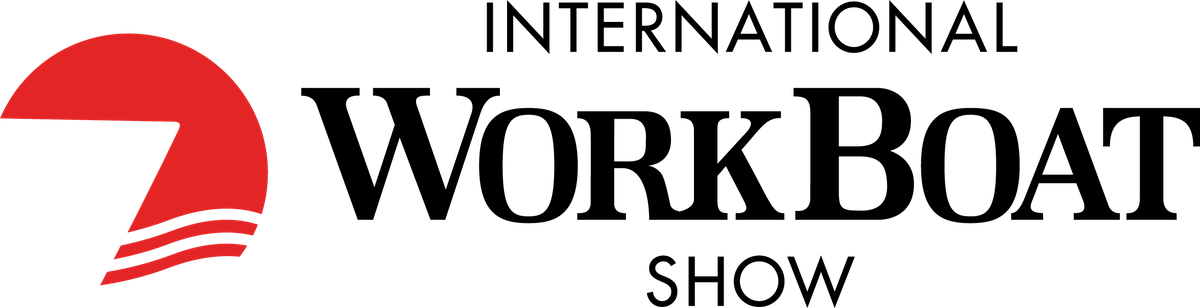
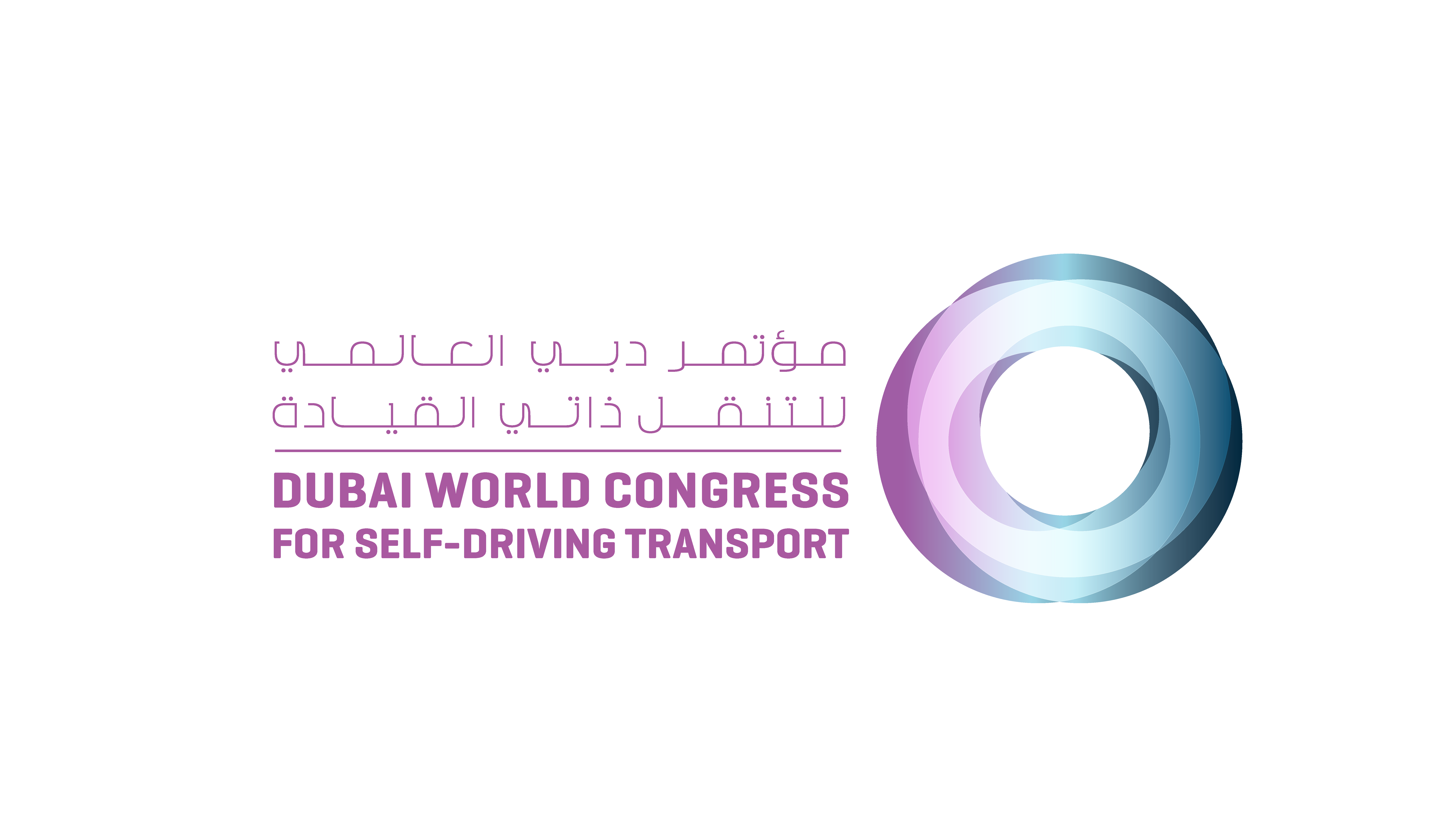
