USVs
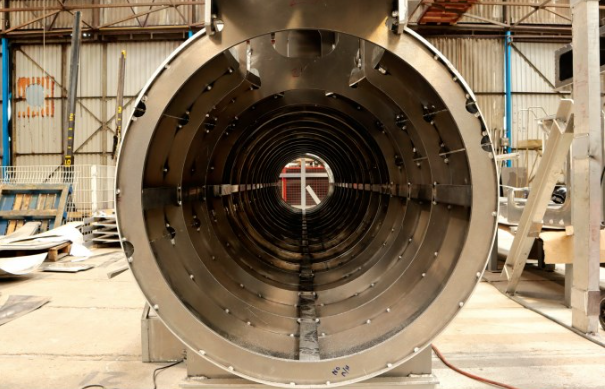
Electrification is picking up for USVs as the powertrains are more reliable and battery weight is not an issue on water, as Rory Jackson discovers
Stability at sea
The ‘blue economy’ comprises ocean data markets, offshore industries, maritime logistics and more, all of which are growing relentlessly.
Some have suggested to us that the growth rate in ocean industries has outpaced the rate at which USVs are being adopted throughout them, and they attribute this disparity to a few technical challenges facing manufacturers.
One concerns how these vehicles handle rough operating conditions and sea states. Stability is critical when out at sea, as USVs risk gathering poor-quality survey data, capsizing, or being damaged to the point that they must be retrieved by a crewed ship or go missing entirely and constitute a lost investment.
It is also increasingly requested that USVs come with sufficient onboard power and space to integrate, launch and recover powerful payloads, or potentially even other uncrewed vehicles, and to perform onboard processing of collected data (potentially with AI-powered edge computers for transmitting actionable analytics to end-users and their customers).
Lastly, and closely relating to the first point, reliability across the architectures of USVs is vital for assuring potential customers that they can be trusted to run remotely and beyond their line-of-sight. As we have said in past issues, a vehicle is not truly autonomous if it constantly needs to be collected and maintained or repaired before its onboard energy store even has a chance to run dry.
For example, many USV designers try to provide high power for payloads by integrating a large, multi-cylinder diesel engine and generator. That brings a cluster of oil changes, filter changes, potential points of mechanical failure, and so on, which cannot be addressed at sea mid-mission because there are no crew or parts inventory on the vessel for fixing the engine.
Fortunately, a new generation of USVs is being engineered that overcomes these problems through astute design and component choices, which are bringing a variety of additional benefits across sustainability, efficiency and more to push the state of USV tech forwards.
SWATH vessels
UK-based ACUA Ocean is eschewing engines for the use of hydrogen fuel cells to power its H-USV. The first prototype of this vessel is under construction (and near completion) at the AMC yard on the Isle of Wight. It is set to be 13.5 m long and 9 m wide, giving it a notably more rectangular profile than most USVs when viewed from above.
“Distributing its weight and buoyancy like that delivers a significantly more stable platform than most. As a SWATH [small, waterplane area, twin-hull] vessel, the H-USV’s size and 25 t weight helps it to significantly outperform the stability of a conventional, 39 m monohull,” says Mike Tinmouth, COO at ACUA Ocean. “Meanwhile, smaller, below 6 m-length, autonomous vessels just aren’t capable of long-endurance, open-ocean operations that industry requires.”
A SWATH vessel is a form of catamaran in which the hull cross-section area at the surface of the water (where wave energy exists) has been minimised, with most of the boat or ship’s displacement sitting below the waves instead. This approach greatly reduces the impact of sea state on the vessel’s stability, including at high sea states and vessel speeds.
“We wanted a platform that could operate in open ocean conditions, and function as a stable survey ‘hub’ for launching and recovering whatever payloads or smaller, uncrewed vehicles an end-user might like. Too many USVs nowadays pitch and roll about in any sea state of significance, which is a nightmare for consistent comms, data quality, payload deployment – so for that we targeted high stability, as well as designing for much space, weight capacity and available power onboard the H-USV as possible,” Tinmouth explains.
“Its configuration was developed by Ad Hoc Marine Designs, a global leader in SWATH vessels, in partnership with the University of Southampton, and the Southampton Marine and Maritime Institute for wave-tank testing and other key analyses.”
SWATH vessels have been in active deployment since the late 1960s, with their inherent stability putting them in high regard among naval architects and particular usage as crew transfer vessels (CTVs). However, their cost and engineering complexity has hindered widespread adoption, so much of ACUA and Ad Hoc’s focus over the last two years has gone into design refinement to lower such costs and make for a practical, profitable production and business proposition.
On certification, Tinmouth says: “While there is talk of a future mini-MASS code for smaller USVs, currently these are hard to get past muster from a regulatory perspective. Compliance and approvals are an important objective for ACUA, and we are working in line with the UK MCA’s Workboat Code Edition 3, as well as the Lloyd’s Register UMS Code. Very few vessels have been able to achieve certification to those standards; Sea-KIT and XOcean being the industry leaders in that regard. Meanwhile, the vast majority of USVs continue to struggle to win approval for full, open ocean operations, because they just haven’t got the stability or redundancy built in.”
While one might presume, as a newer technology than ICEs, that adopting hydrogen as a power source would risk certifiability, Tinmouth says fuel cells have been through multiple cycles of development and improvement over the last decade. Several manufacturers are working towards or have achieved approval in principle for marine fuel cells, and the number of supply chain uncertainties hindering longer-term benefits of hydrogen-electric powertrains is shrinking.
“Those benefits include the reliability of fuel cells, the high electrical power they generate for payloads, the low vibratory output from being a solid-state, electrical system, and chemical benefits in that they only vent water and a small amount of H2, compared to diesel engines, which give off CO2, NOx and other things,” he adds. “They also have a lower acoustic and thermal signature, compared with diesel engines, which you can imagine is very appealing to end-users who don’t want to be detected.”
The hydrogen-electric powertrain was developed under Innovate UK’s Clean Maritime Demonstration Competition, while the H-USV’s thrust comes from RAD Propulsion’s drive-by-wire, 40 kW electric twin drives.
“This is a prototype vessel, so there will certainly be learnings and iterations as we go forwards, but with our large, modular and payload-agnostic design, we are looking at multiple uses across the offshore sector, including industrial surveys, marine conservation, biodiversity data collection, and defence and security applications,” Tinmouth concludes.
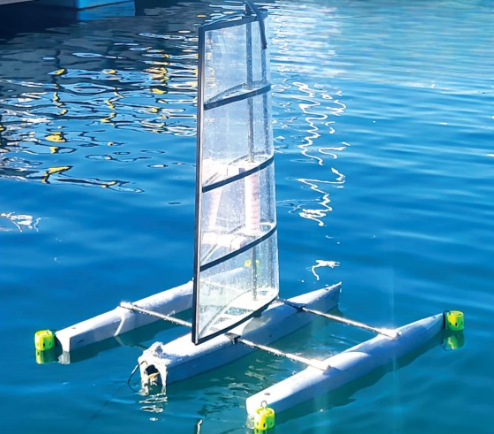
Trimarans
Monohull vessels are a common sight among oceangoing USVs for the stability that such designs possess inherently, based on their weight distribution. Multi-hulled vessels, by contrast, leverage their width for stability, but experience a critical, angle weakness tipping point and they can roll over, requiring at-sea rescue.
San Diego-based SubSeaSail designed its first autonomous undersea and surface vehicle (AUSV), HORUS, which was featured as the ‘Gen6 USSV’ in issue 33, with a monohull configuration. It is a semi-submersible that sits mostly submerged – a configuration that is stable and saves energy over traditional monohulls by not producing wave-making drag while sailing.
SubSeaSail received funding from the US National Science Foundation (NSF) to conceive a second line of vehicles – multi-hull vessels that can self-right themselves when tipped over. This has motivated it to design and produce a new trimaran AUSV called HERMES, featuring new capabilities over its monohull sibling, while still including much of SubSeaSail’s established technological IP.
“We’ve initially created a functioning, 4 ft-long [1.2 m] scale prototype. For ocean operations, HERMES will likely be scaled to a minimum of 6 ft [1.8 m] – a size needed to right itself at sea, but we suspect it will also be popular because AUSVs that small can be transported and launched by car or trailer. We believe the design can be scaled up to 100 ft [30.5 m] or more,” states Ryan Lorence, mechanical engineer at SubSeaSail.
“At bigger lengths, HERMES will be able to generate significant electricity from its solar panels and be able to power a whole host of onboard systems. You could power payloads, recharge batteries for other vehicles, or generate hydrogen or fresh water from saltwater.”
Lorence notes in particular that the trimaran might be used for transporting cargo with significant energy- and operational-efficiency. If a large trimaran AUSV should arrive at its harbour too early, or at a time with high loading traffic, insufficient free warehouse space or damage to the port, it can loiter out of the way, above or below surface, or sail up to the sand at the nearest beach.
“The design doesn’t even need a full-sized port to deliver goods. Multi-hull vessels are very low draft – they don’t need a deep keel for stability, so this boat could sail right up onto the shore and be dragged up by workers.”
While performance specifications are still being established, the trimaran is expected to achieve higher speeds than its monohull counterpart due to its shallower draft, resulting in less water resistance, and not needing a heavy keel for stability.
Propulsion is achieved primarily by wind power via the wingsail and electric thrust as a backup. Solar panels will be located in the wingsail or on deck, depending on the vehicle and size. Wingsails are moulded from fibreglass with RF transparency, which results in a very low radar signature, to the appeal of SubSeaSail’s defence customer base.
“New shapes and internal structures provide advantages to the support of the wingsail solar panels to keep them in a nice, curved shape,” Lorence notes.
“Wingsail skins, including internal solar panels, are being designed to simplify manufacturing. The whole configuration will be much easier to replace and service than our past versions.
“Maximising the surface area for solar collection utilising new solar-panel manufacturing techniques affords the greatest potential energy collection, as well as electrical system redundancy. This is a big improvement for all AUSV and USV operations.”
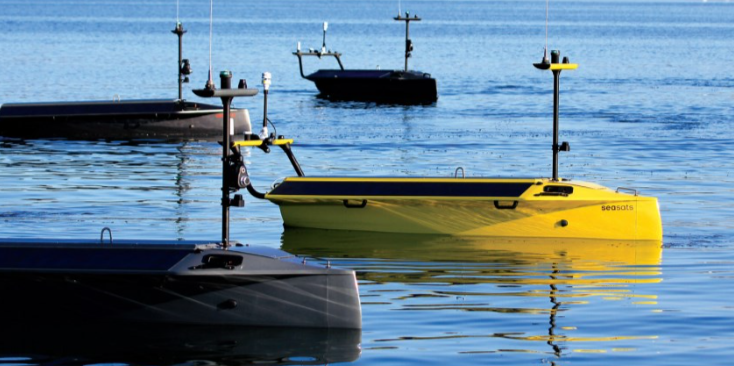
Monohulls
Arguably, the most aggressive litmus test of a USV’s reliability at sea is trialling whether it can perform a Transatlantic crossing autonomously, as explored in detail with the Mayflower USV in issue 42. The ambition to perform such a crossing was what inspired Dylan Rodriguez, CTO and co-founder of SeaSatellites Inc (Seasats), to create the Scout USV with his fellow students in 2013.
Developed over two years, the Scout was built largely from carbon fibre to save weight and powered by solar panels for reliable endurance, and it set an autonomous surface voyage record a few months after its launch.
Rodriguez and his fellow students broke up afterwards to build individual careers and experience, later reuniting in 2020 to found Seasats in San Diego, with the aim of redesigning and updating their past IP into a USV that was less complex, less expensive and more reliable than what they perceived much of the USV world’s offerings to be capable of.
Today, its technology is enshrined in the Lightfish, which, much like the Scout, features a composite monohull (though now fibreglass, rather than carbon fibre, as on Scout), designed with a low-profile and retractable keel to aid stability, along with solar cells on its top deck and gunwales for energy efficiency and self-sufficiency at sea. Masts at the front and rear provide for payload and antenna integration.
“They are COTS solar panels, just with an effective weatherproof coating to keep them safe and clean against saltwater,” says Declan Kerwin, VP of operations at Seasats. “Another benefit of designing this USV as small, low and close to the water is that the waves periodically wash the panels off, giving it an effective, self-cleaning effect for salt, biofouling and so on.”
The Lightfish measures 10 ft by 3.3 ft (3 m by 1 m), weighs up to 354 lb (160.5 kg) in air, and has shown endurances of up to six months in testing of its prototypes (with a focus on the lifespan of its solar cells and electric thrusters). Its PV panels nominally supply up to 400 W over a bus voltage of 5-28 V, while its battery stores sufficient energy for about 575 nautical miles without solar. Its motor provides a top speed of 5 knots.
Up to 110 lb (50 kg) of payload can be installed onboard, as can an optional generator for those seeking the extra redundancy, power or energy of a hybrid powertrain.
“In addition to our defence users, we have some customers who are very interested in mapping applications for Lightfish, as well as marine scientific uses like water-condition monitoring, as well as monitoring and prediction of harmful algal blooms,” Kerwin adds.
Solar power is rapidly becoming a universal sight among monohull USVs as an apt use of the real estate atop their decks for efficient and clean energy; PV cells serving as either a primary or redundant energy source. The larger the USV, the more real estate available for powering onboard payloads and computers sustainably, and for autonomously recharging batteries without returning to port.
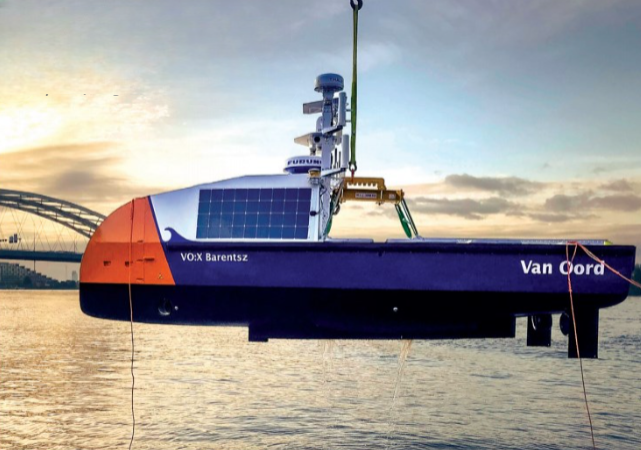
One notable new unveiling is Demcon Unmanned System’s new DUS V5750, the Dutch company’s newest USV class, at a length of 7 m.
In addition, in integrating photovoltaics into its redundant powertrain, the vessel is engineered with a dynamic positioning system, featuring a new weathervane control mode, which enables the USV to serve in real-time inspection of subsea cables as they are laid down for offshore wind farms.
Typically, a crewed survey vessel will follow the cable-laying ship for such inspection, but will become highly unstable and potentially hazardous in challenging weather conditions.
In addition to an electric USV being far less expensive and polluting than a large, diesel-powered boat, the 5750’s environment-dependent control mode points its nose in the optimal direction of wind, current and waves to minimise resistance. It can then follow the cable-laying ship while angled laterally, thereby optimising its power resistance and stability while sailing behind the cable-laying crew.
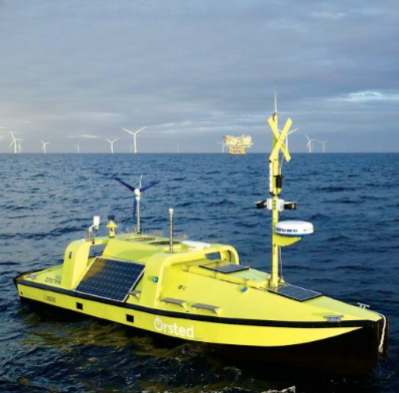
Further north in Europe, Danish offshore wind-farm producer Ørsted’s Hugin USV is, much like the ACUA H-USV, intended as a stable, multi-sensor survey platform, though especially for deep investigation of data that is critical to early-phase development activities prior to new wind farms being built. These include wind conditions, seabed hydrography, biological and ecological parameters, and further specifics of the local area.
The Hugin USV integrates five solar panels as standard across its fibreglass-constructed hull (two on its front deck, one at port and starboard, and one at the rear). It can also equip two small wind turbines to further supply clean onboard power, as well as added redundancy for the hybrid-electric powertrain.
Propulsion comes from twin, 130 hp outboards, and when fully fuelled, the 900 x 400 x 227 mm USV weighs 6.8 t.
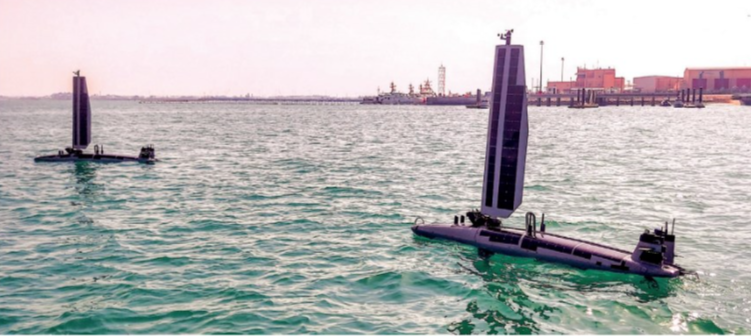
USV-UUV hybrids
The Triton is the latest version of Ocean Aero’s AUSV technology, with its design featuring a deployable wing, enabling the vehicle to use prevailing wind conditions to assist in surface transit as a long-endurance USV. When required to dive, the Triton’s wing is stowed in a lowered, hydrodynamic position for submergence, and battery power is used for subsurface station-keeping or transiting (to maximum depths of 100 m).
Intended as a multi-use, modular, sensor platform, the Triton features a payload bay within its underbelly, as well as optional payload integration locations in its keel and wing. All power generation comes from the solar cells along its sail and hull; its batteries can recharge at up to 740 W when the PV panels are at peak solar exposure.
We last featured Ocean Aero eight years ago, in issue 9, investigating the Submaran S10, a predecessor of the Triton. The Triton measures 26 cm longer, at 4.4 m from bow to stern, and it notably has a 200 kg greater maximum weight at 350 kg, with its 37.6 kg payload capacity enabling 14 kg of additional sensors over its ancestor.
On engineering objectives since 2016, Pasquale Derosa, director of product development at Ocean Aero, tells us: “We’ve made a lot of internal changes to power distribution, internal comms networks and edge processing computers, leveraging proprietary technology advancements, as well as utilising new innovations that have come out commercially since 2016.
“Obstacle avoidance and threat evasion technology are especially important among those. We use a vision-based computer approach that ties above-surface cameras together with underwater sonar sensing for full situational awareness.”
Ocean Aero’s main customers today are defence departments across the US and its allies, including recent exercises and deployments in the UK and South Korea, as well as with US Navy Task Force 59 and 52 in Bahrain (especially tasked with integrating, trialling, and maturing autonomous vehicles and AI capabilities in a naval context).
A 360° camera system on Triton observes, detects and helps to identify potential threats, such that it can determine autonomously whether diving to evade them is prudent. It can then idle below the surface or power its thrusters to keep moving underwater at up to 2 knots.
“The threat evasion logic is programmed with multiple tiers. Based on object classification, it can also report back to its operator to query if something is or isn’t a threat. Of course, if it already knows that what it is looking at is a threat, it will automatically go underwater to avoid capture or destruction,” DeRosa says.
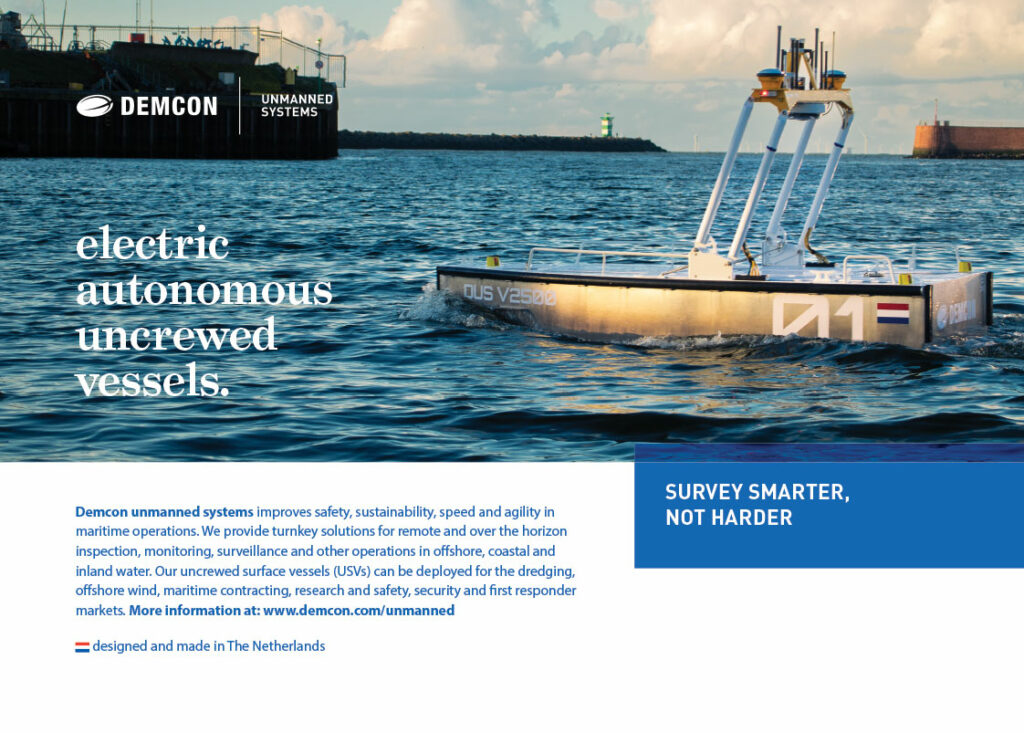
Summary
Looking across the new vessels and their use cases discussed, it is notable that electrification seems to be picking up across USVs at a comparable pace to that seen in road vehicles.
This makes sense when one considers that fleet managers across industry must optimise for cost and reliability, and electrified powertrains come with greatly reduced failure points compared with combustion powertrains. Additionally, with weight posing less of a problem in vessels than in cars, more battery packs can be installed in USVs without the effect of compounding mass, as seen in EVs in recent years.
With the proliferation of hydrogen, hybrid and battery technologies across USVs, combined with autonomous vessels gradually becoming leveraged across ocean industries, infrastructure is likely to be adapted over time with new approaches for keeping eUSVs working and maintained at sea.
Just as a few UUVs are now operating as resident systems via subsea docking and charging equipment, tomorrow’s wind farms may integrate electrolysers to generate hydrogen for on-site refuelling, as well as automated, battery swap stations.
Such technologies are rapidly being commercialised for vehicles of varying sizes and configurations, and automated slipways for placing USVs into serviceable positions for battery swapping and other maintenance activities are well established. CONOPS and specialised equipment for many different vessel types have existed across international maritime standards for decades, and those for industrial ocean USVs can be expected to join them soon.
UPCOMING EVENTS
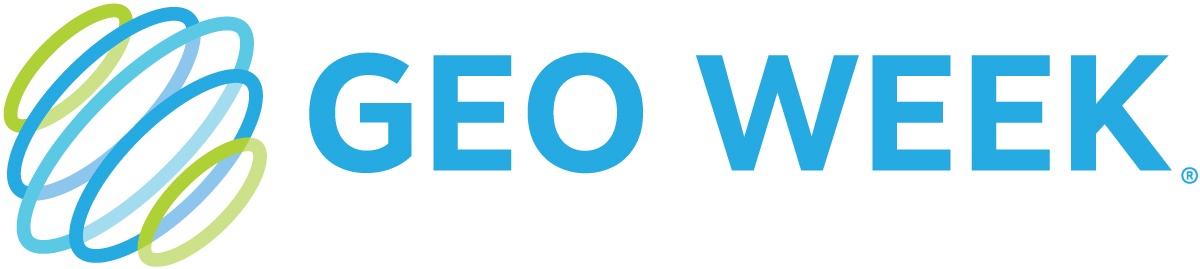
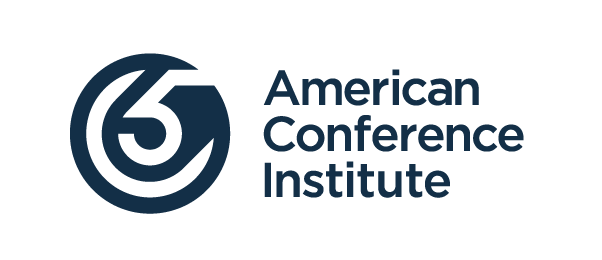
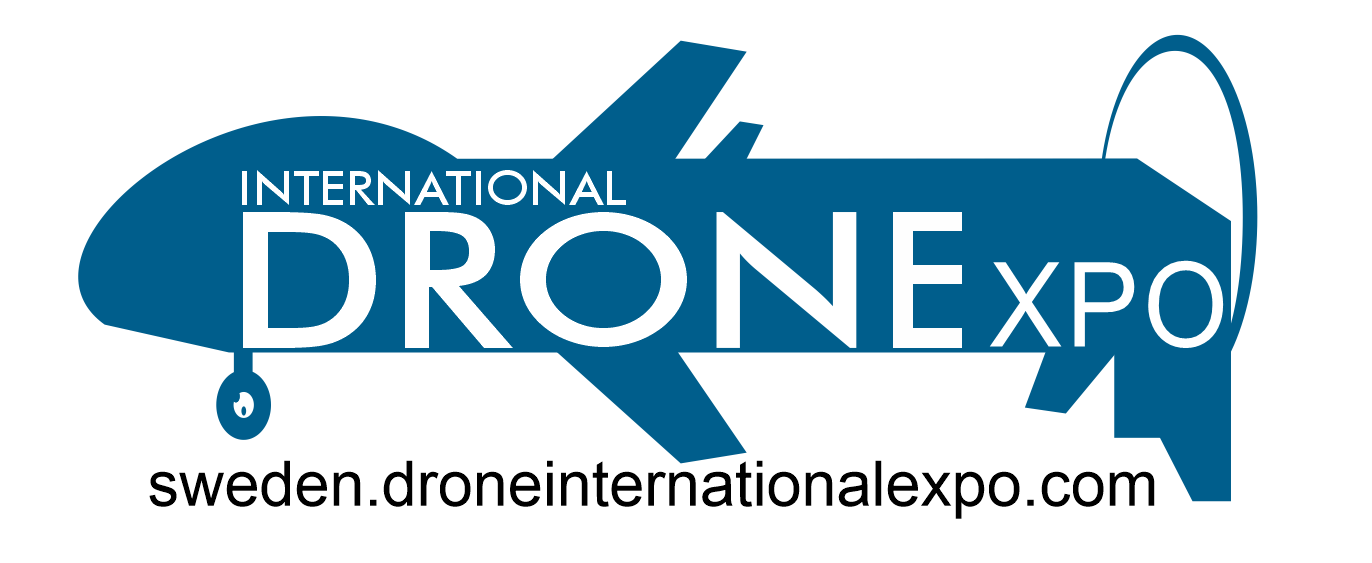
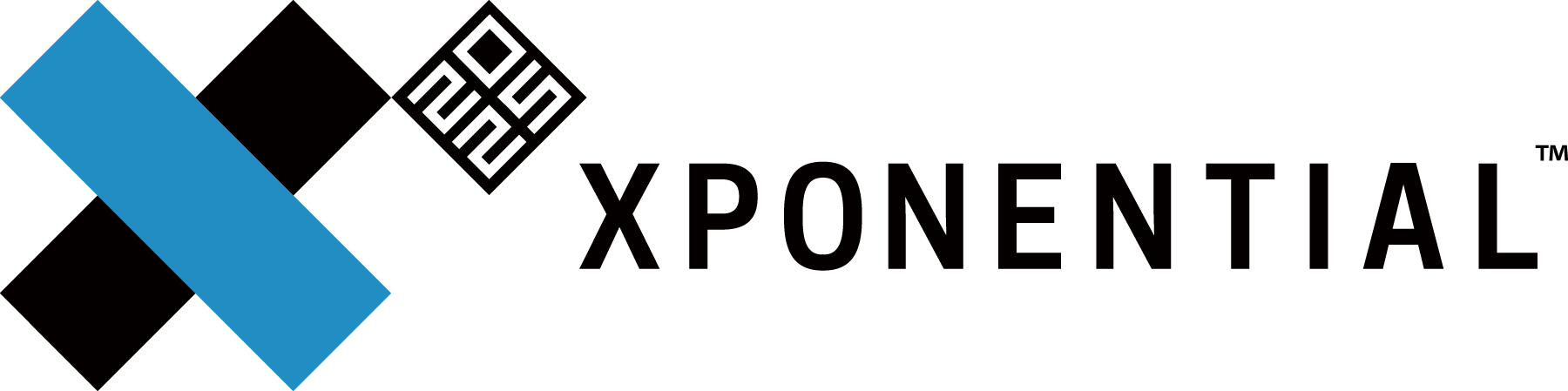
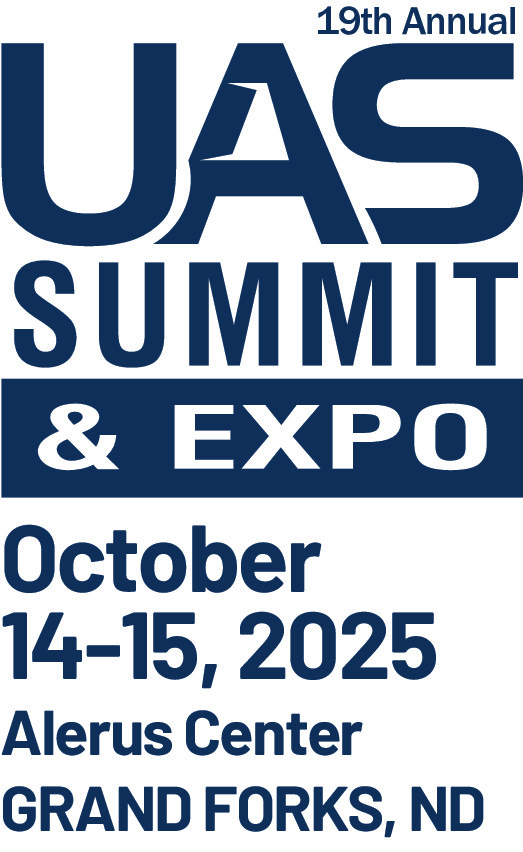

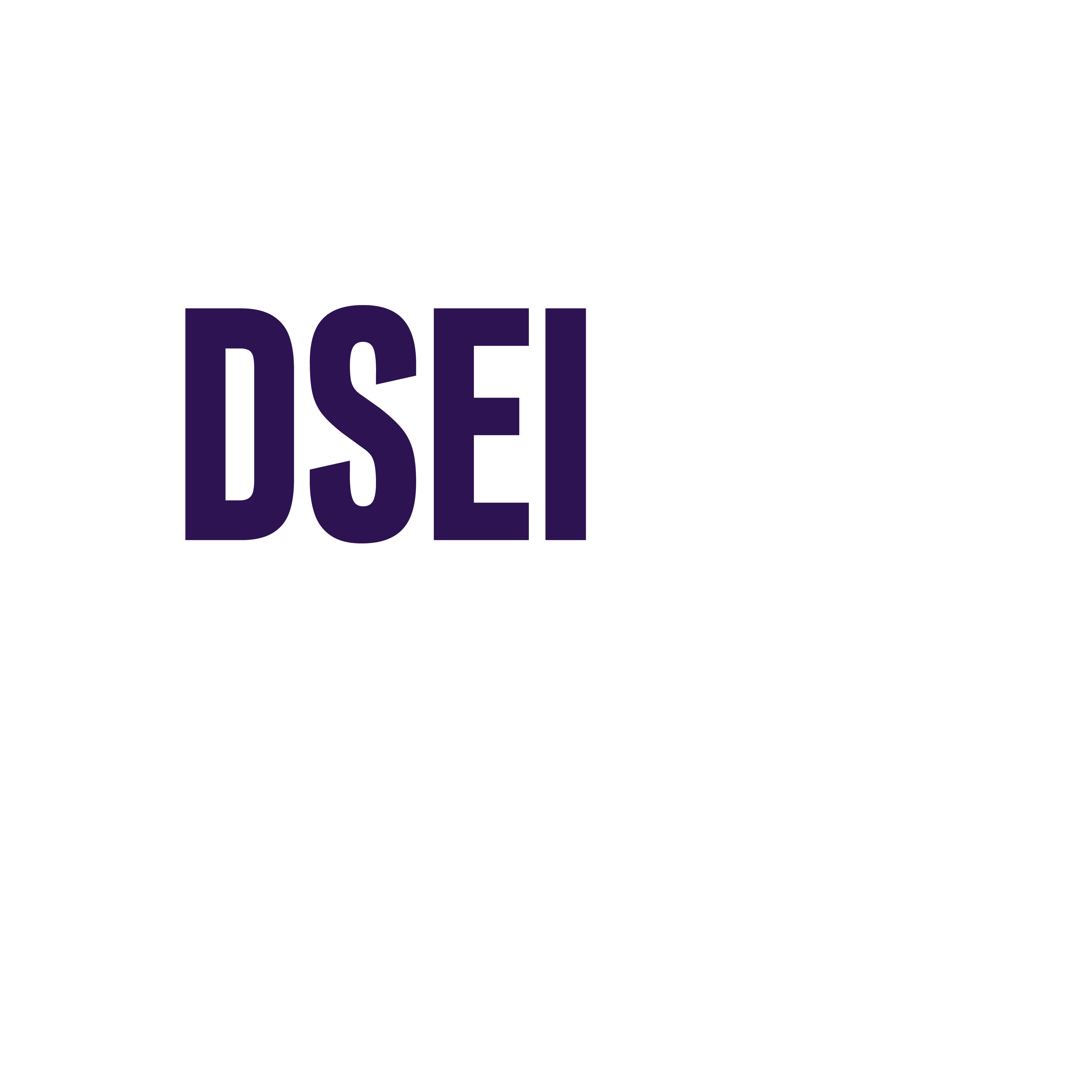
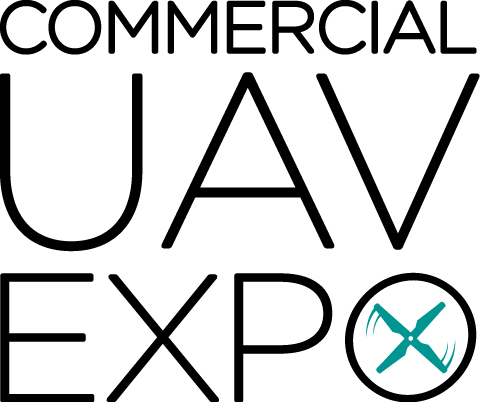
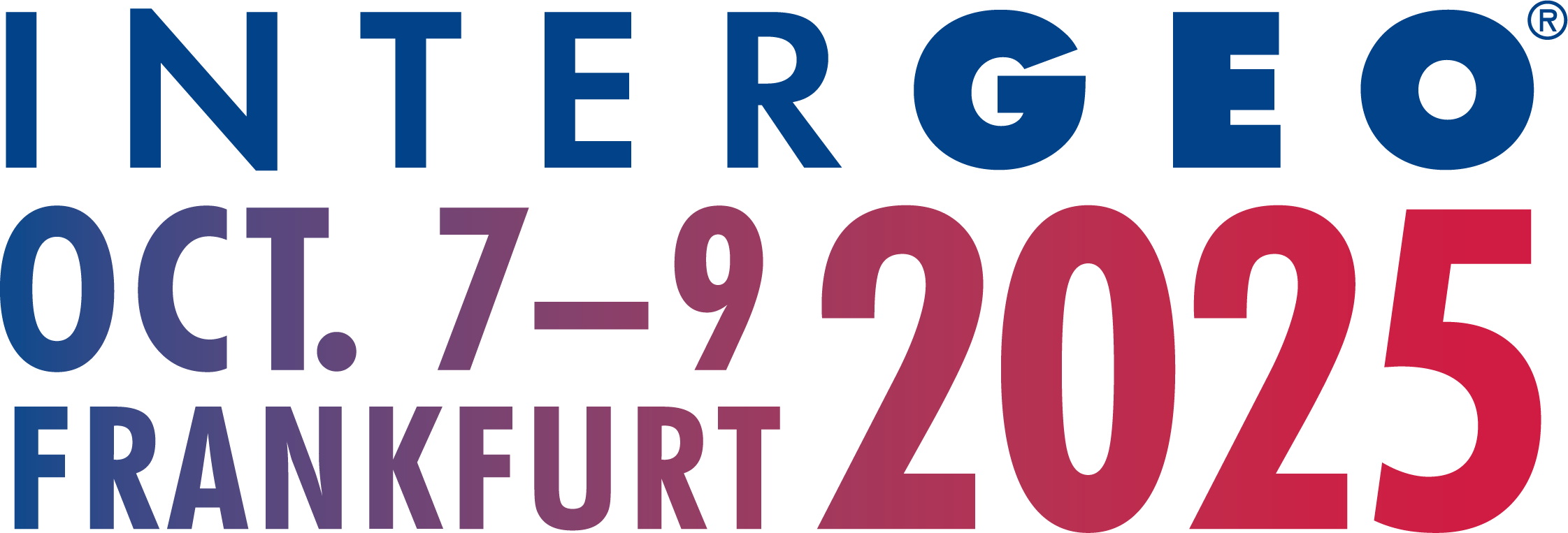
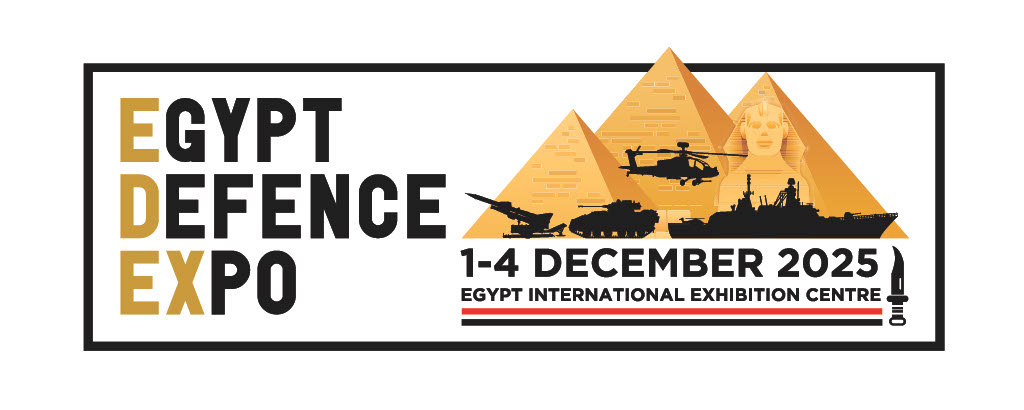
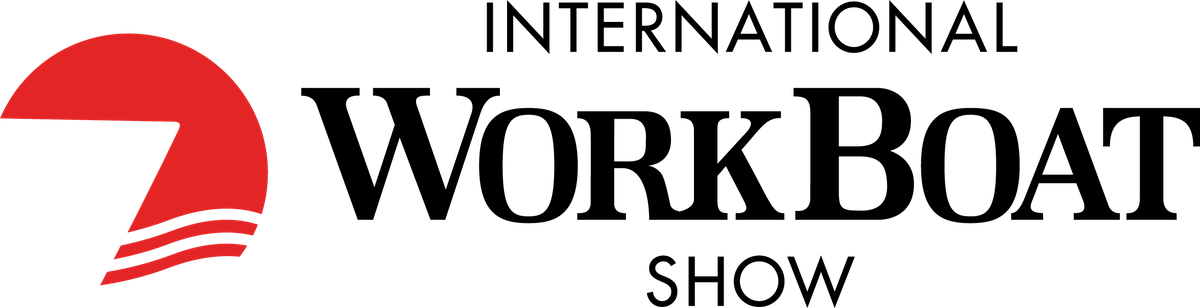