Skyline Robotics Ozmo
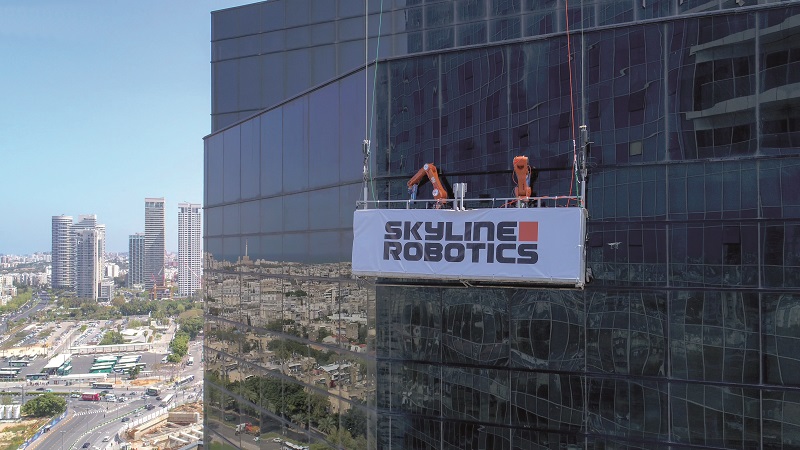
Peter Donaldson reports on how this uncrewed system brings the windows of tall buildings back to their best
Cleaning the windows of high-rise buildings is one of those dull/dirty/dangerous jobs that cries out for an automated and uncrewed solution. Skyline Robotics now offers one in the form of the Ozmo, which consists of a robotic arm that rides in a building’s existing window cleaning cradle, and an intelligent control system that runs the arm, the cleaning tools and the cradle.
Unlike earlier robotic window cleaning systems that used pre-programmed cleaning routines unique to each building, the Ozmo maps the building and works out how to clean the windows as it goes, giving it much more general applicability.
Skyline Robotics was founded in 2017 by Israeli inventors and entrepreneurs Avi Abadi and Yaron Schwarcz, who hold the patent on the “device and method for use in cleaning a facade” that became the Ozmo. The idea stemmed from a desire to get into robotics and from conversations with professionals in property management and maintenance who identified high-rise window cleaning as a task currently performed in an antiquated and risky manner that was ripe for automation.
In 2020, Skyline’s board decided that the founders had taken the company almost as far as they could, and that it was therefore time to bring in others who could take it further, so president and chief operating officer Ross Blum and chief executive officer Michael Brown joined the company in December that year. These days, Skyline has partnerships with Kuka for robotics, Platinum and Principle Cleaning Services for operations, Karcher for r&d and Gefen for venture capital.
As well as an operations partner, Platinum is also the first major customer for the Ozmo. The company provides services including window cleaning and maintenance for what it says are more than half of the Class A commercial buildings in Manhattan and the New York Metropolitan area. On 31 October 2023, Skyline announced its second major customer and new partner Principle Cleaning Services, which provides corporate commercial cleaning in London.
“Our business model is to partner with leading window cleaning companies in their regions,” Blum explains. “We want to partner with people that have existing customers and that already have great relationships with their local regulator, that have the necessary insurance policies, and, candidly, have the workforce, because we don’t want to have sales and marketing staff who need to go to every single building on the planet. We want to focus on being a technology company.”
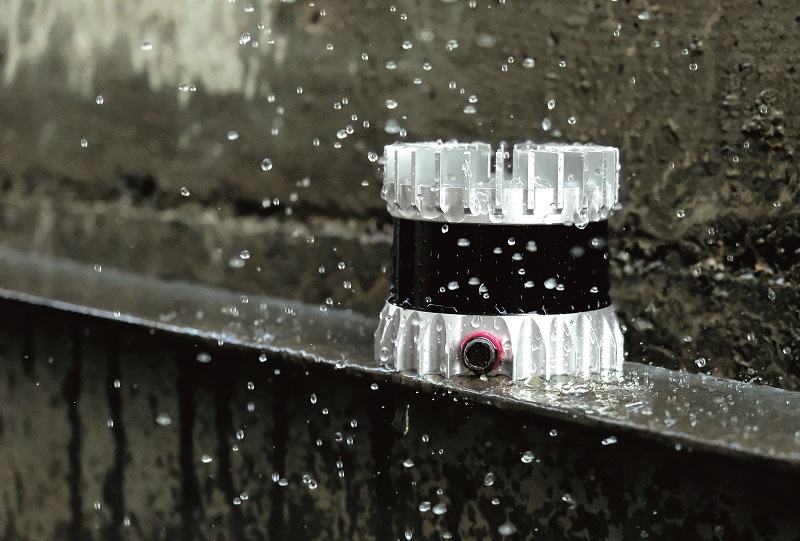
The arm and machine vision
At the heart of the system is the waterproof version of Kuka Robotics’ Agilus-2 six-axis robotic arm. Designed originally for use in a range of manufacturing environments, the Agilus-2 can be mounted on floors, walls or ceilings and at any angle. The arm weighs about 51 kg and has a footprint measuring 320 x 320 mm. It has a maximum reach of just over 706 mm and a payload of 6 kg.
Compared with other versions of the arm, it has additional interior seals, more robust surface treatments and stainless steel covers instead of plastic.
Incorporated to enable the arm to operate in wet and dirty production environments, these protective features allow it to meet IP67 ingress protection standards and make it suitable for applying water to windows in all weathers.
The Ozmo’s machine vision system processes information from onboard cameras and an Ouster OS1-6 Lidar to work out its precise location and direction of movement relative to the building’s facade and the window it is cleaning. Together they provide data to algorithms written in-house that produce a 3D map of the facade and generate instructions to control the arm and the cradle.
While Skyline refers to the process that enables the Ozmo to find its way around the building facade as SLAM, it is using the term in a general sense to characterise a method that includes a localisation component and a mapping component, rather than any specific simultaneous localisation and mapping technique.
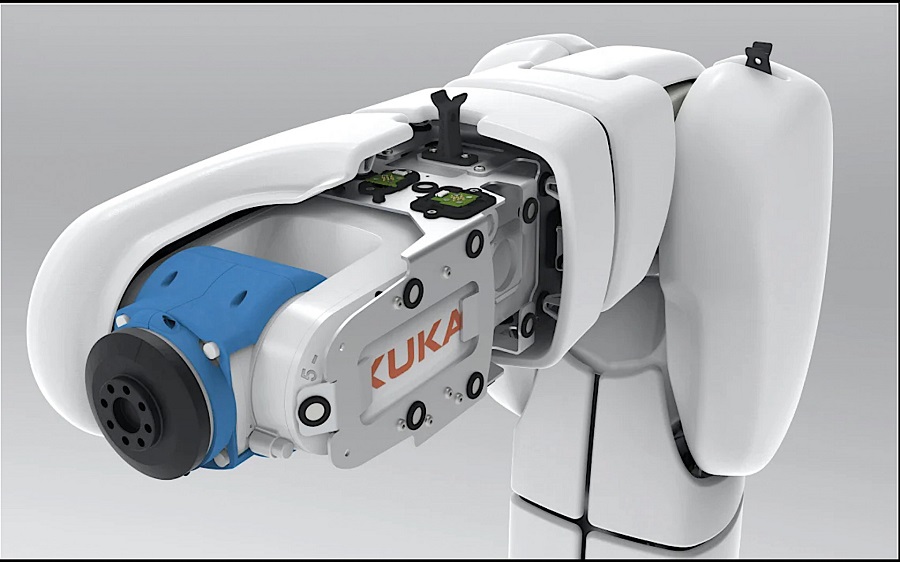
Tactile feedback
The robot also has what is in effect a sense of touch that allows it to apply enough pressure to the glass to clean it properly without the risk of cracking it. This feedback is provided by a set of OnRobot Hex 6-axis force/torque sensors. Further, algorithms use data from inertial and other sensors to respond to gusts of wind and keep the robot stable in highly variable conditions, and the operator can always stop the system remotely at any time.
The cleaning water supply passes through an Ionic Systems QuattRO reverse osmosis filtration and de-ionisation system, which contains a number of complementary filters. These include a carbon filter that removes chlorine from the water to protect the reverse osmosis (RO) membrane, a 5 micron filter that removes all particles above that size, the RO membrane itself that removes 98% of remaining impurities and a de-ionisation filter.
An inline water softener is recommended for hard water areas to remove calcium, which can degrade the performance of the RO filter and cause it to fail prematurely. The QuattRO feeds the water to a cleaning brush specially designed for the Ozmo.
Although the Ozmo is not intended to be a cobot (a robot designed for direct human interaction), operators have to set it up for every job, so it is fitted with the Airskin safety system that stops it when it detects any contact. A modular add-on, custom-fitted to each robot model, the Airskin is a system of soft, pressure-sensitive pads that form an airtight skin over a flexible support structure.
This structure also houses dual-channel sensors that detect pressure changes when a pad is deformed by a contact anywhere on its surface. Each pad has an integral piezo-electric micro-pump that maintains an overpressure of 400 Pascals which serves as a reference for correct operation, while all the pads are connected in series and monitor each other for integrity every 4 ms. The force threshold that triggers a safety-rated protected stop is 5 Newtons.
The Ozmo, however, is more than a collection of components from vendors, and creating an effective integrated whole presented some engineering challenges. As Blum explains, “Robotic systems in general are relatively complex, and you need to bring a few competencies together across mechanical, electrical and software disciplines.
High-rise challenges
“With the Ozmo, we have a few challenges in our working environment. We’re in an outdoor multi-variable environment, and we need to be able to adjust and react to things in true real time. Wind gusts can come along at any moment, so we have to stabilise the platform to ensure the basket doesn’t crash into the facade or create any sort of safety incident,” Blum says.
“From a machine vision standpoint, we’re localising and mapping on highly transparent and reflective surfaces, so sunshine, shade and cloud movements present different challenges.”
To help tackle this problem, the cameras are spaced vertically and laterally from one another so that they can image the facade from different angles, which is helpful in 3D mapping of reflective/transparent surfaces because algorithms can use it to reduce optical noise from such surfaces.
This photogrammetry is combined with the direct range measurements to the surfaces provided by the Lidar. The mapping itself is performed by 3D point cloud stitching and processing, with localisation through visual odometry.
He also notes that Skyline had to solve some knotty comms problems over a long tether. “When you’re in the centre of these metropolitan areas, there are some really interesting radio frequency patterns, and we need to be able to pass comms from the rooftop down to the robot and vice versa, in absolute real time,” Blum says.
“These days, when you’re constructing a building, you’re advised not to run an Ethernet cord for more than 100 m, because at that length you’re going to start to lose throughput. We’ve had to come up with an innovative solution and, at this point, we’re able to transmit about 127 Mbit/s at 400 m through a cable that’s insulated and protected.”
Like most of the comms equipment in the Ozmo system, this shielded cable and its connectors come from Rockwell International’s Allen Bradley division.
The cable also carries electrical power to the Ozmo. “I wish it were battery-powered, but, that doesn’t seem like a viable solution at the moment because of weight. All these cradles have weight limitations for safety,” Blum says. “So the power and comms lines come from the rooftop, pass power down to the robot on the platform, and then the robot gives its sensors the power they need.”
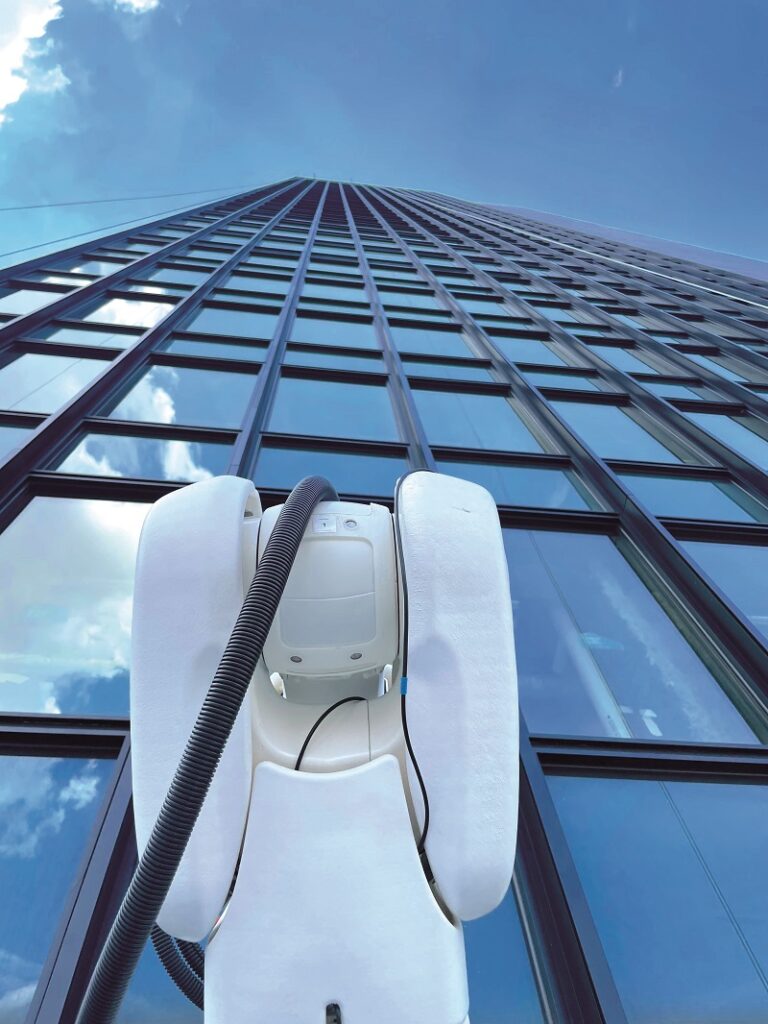
Under pressure
Water pressure is also an issue, but it is one of avoiding excessive pressure rather than dealing with insufficient pressure. This is because the Ozmo takes the water supply from the building’s main tank on the roof, which is much easier than pumping it up from ground level.
“We don’t want a water line to burst down the side of the building. If you’re 100, 200, 300 m down a building, you have to imagine yourself diving that deep into the ocean where the pressure would increase around you,” Blum says. “So we had to come up with a system that would allow a mixture of air and water flow into the water line.”
While water is incompressible, air will compress and absorb energy that might otherwise rupture the hose. “So, depending on the elevation of the platform, there would be different mixtures of air and water,” he says.
Yet another challenge centred on dealing with the high temperatures caused by the combination of direct sunlight and reflections from the windows. “It could effectively feel 20 oF warmer than it actually is. And if it’s already 100-plus degrees, that can be extreme,” he says.
“Electronics don’t love extreme heat, so we had to invest in creating a cooling system that can mitigate those temperatures. As we think ahead, we might need further iterations of the cooling system for environments with higher humidity.”
All this technology ultimately supports the deployment of a simple brush and squeegee combination on the end of the Agilus 2 robotic arm. “The brush design we use is really akin to window cleaning brushes from 50 or 60 years ago,” Blum says. “We have adopted a geometrical shape that’s very close to traditional brushes, although we don’t use horsehair.”
Distributed symmetrically among the synthetic bristles are water nozzles that keep them moist so they can clean the windows effectively, with the help of the Lidar.
“Essentially, the Lidar is localising and creating a border for each window, so we’re localising on the window frames and giving the arm a ‘paint between the lines’ scenario,” Blum says. “We recalculate the cleaning path more than 200 times a second to make sure the arm follows the most efficient path and that the robot can react in real time to any disturbances.”
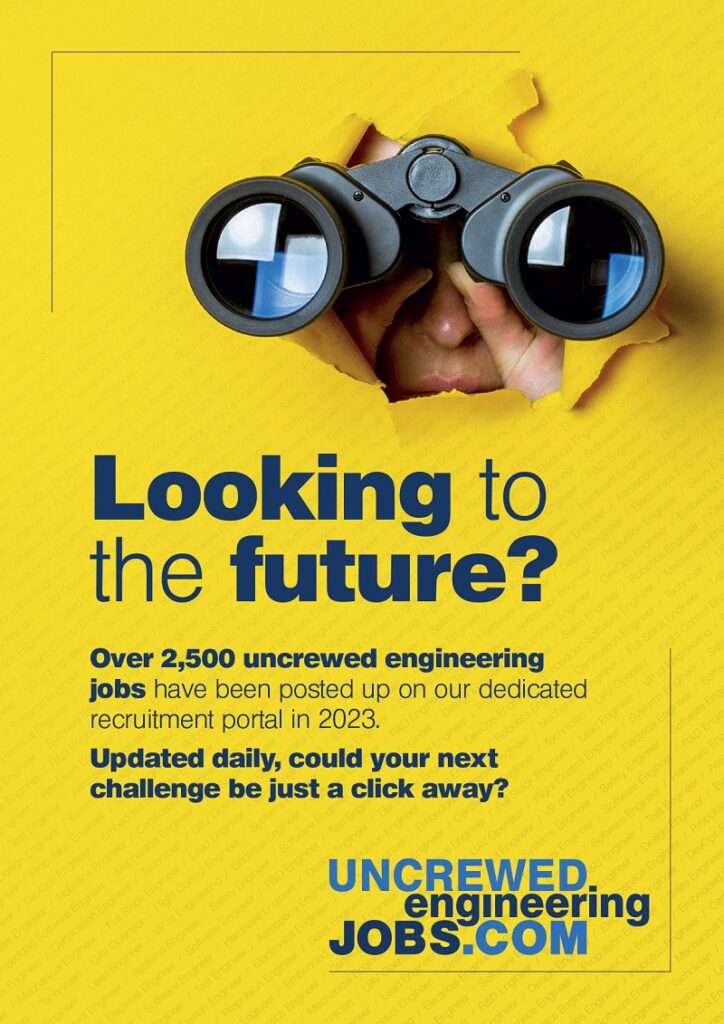
AI decision-making
This is where AI comes in, although Blum is careful about its definition. “This isn’t generalised or even generative AI – we are talking about making correct decisions based on variable parameters,” he explains.
As the basket is moving, the system needs to decide how much counter-pressure the robot is going to apply. “Essentially, the arm is both creating and damping down forces against the window at the same time, so we need to create as stable a working environment as possible,” he says.
The software environment is Linux-based, with code written largely in C++. “This gives us the best ability to react in real time,” Blum says. “For example, we need to limit how many Python libraries our software needs to look through in order to make decisions, because that takes time. When a wind gust comes along, you don’t have that time.”
The hardware this software runs on is an Allen Bradley programmable logic controller.
Infrastructure integration
One key decision about the development of the Ozmo system was to use as much of the building’s existing infrastructure as possible, including the crane or davit system that supports the cradle, for example.
“That’s a strategic decision, not just from a speed-of-implementation standpoint but because the equipment on the rooftop is regulated and has been approved by the local governing body,” Blum says. “By making no adjustments to it, we avoid bringing any unnecessary regulatory bodies into an implementation.”
This approach meant the Ozmo’s control of the cradle had to be as simple and non-intrusive as possible. “We control only the y axis, and what we have is just a very basic electrical relay that opens and closes the circuit at the appropriate time, just as a human operator would press a button for the basket to go down,” Blum explains.
That leaves the x axis of motion across the building’s facade under separate control from the rooftop. In advanced countries, there are typically three people in a high-rise window cleaning crew: two in the cradle and one on the rooftop near the crane for extra safety and support. The Ozmo needs only one operator, and it is from the roof that they would start and manage the robot once it has been installed and set up in the cradle, and control its horizontal movement.
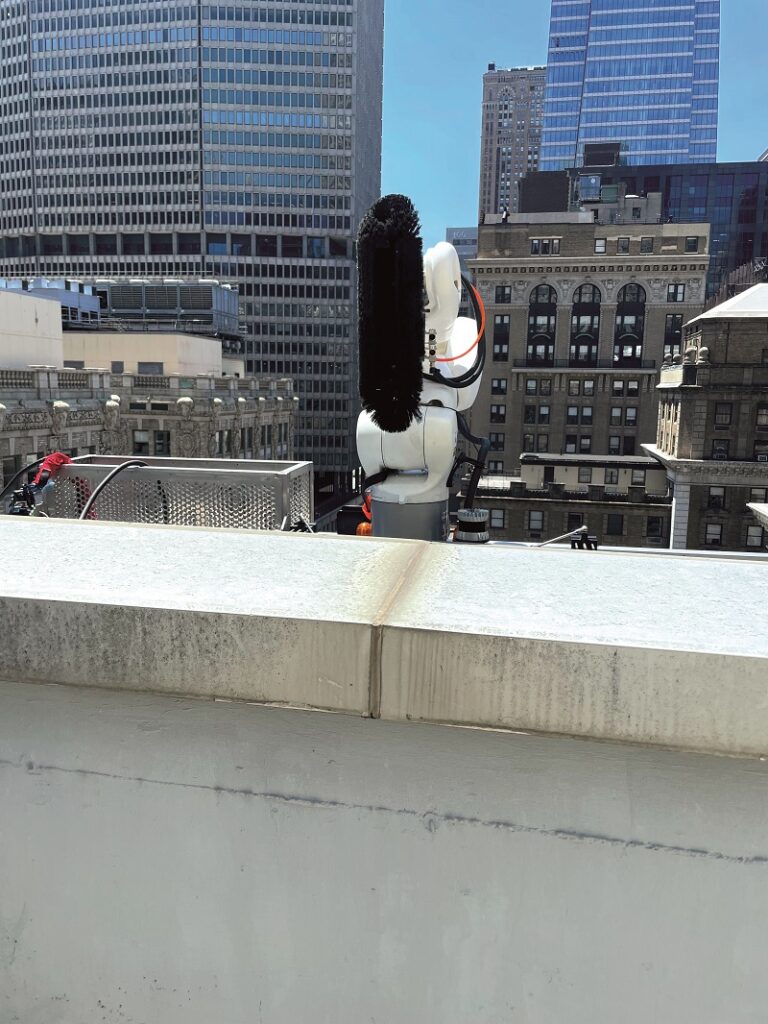
Set-up and operation
Before anyone can operate the Ozmo they have to be trained and certified by Skyline. Blum says, “The first step is always getting the robot and the equipment to the roof. There might be an elevator to the rooftop, or you might have to load the robot into the cradle through a balcony, so you’ve always got to figure out the logistical plan.”
Once all the equipment is on the rooftop, set-up takes about 90 minutes to two-and-a-half hours, he says, adding that the procedure is fairly well standardised from building to building, although there can be subtle differences.
Next, he says, the operator follows their training to clamp the robot, the Lidar and cameras in their correct positions. They then log into the Ozmo system and initiate its self-checking process, which confirms, for example, that the connection to the y axis of the crane is made correctly, that all the cameras and sensors are operational, and validates sensor readings as the Ozmo descends the facade, particularly on the first day.
The checking process typically takes 10 to 15 minutes. There is a similar shutdown procedure at the end of the day.
Skyline continues to invest in the technology, and by the end of this year Blum is confident that it will have completed development of a multi-arm version of the system. “That’s been a big development effort this year, but we are now fully industrialised and fully waterproof, and we are commercialising the product.”
‘Owning’ the facade
“The goal with the Ozmo is to ‘own’ the facade,” Blum says. “There’s more than just window cleaning that happens on a building; there are inspection services, polishing, light masonry work, surveying and water pressure testing. We look at the Ozmo as a platform, and the more services we can provide simultaneously, the better we feel we will be in the long run.”
Some key suppliers
- Robotic arm, AI, computer vision and machine learning: Kuka
- Safety sensor system: Airskin
- Programmable logic controller: Allen-Bradley
- Networked comms: Allen-Bradley
- Water filtration and de-ionisation: Ionic Systems
- Force/torque feedback sensors: OnRobot
- Lidar: Ouster
- Control station: Panasonic
UPCOMING EVENTS
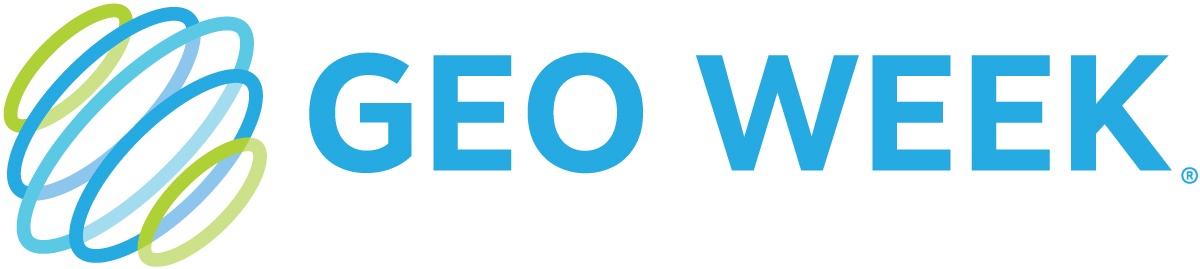
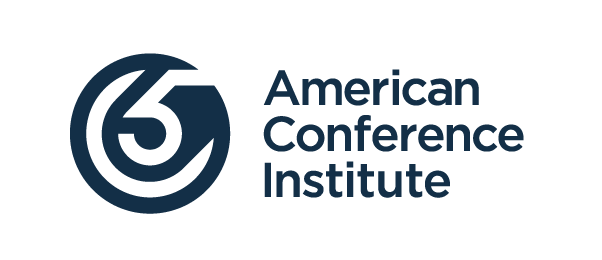
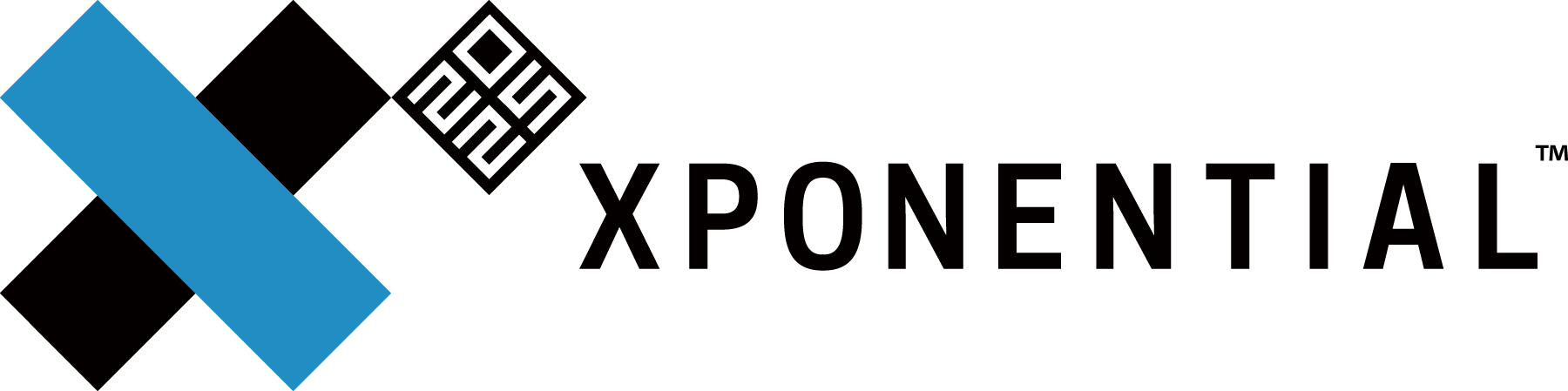
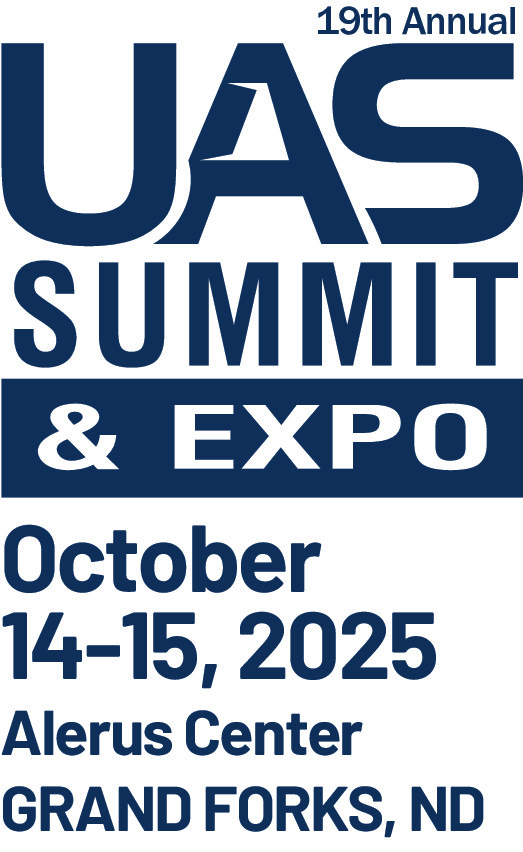
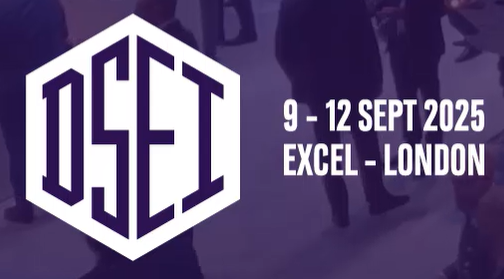
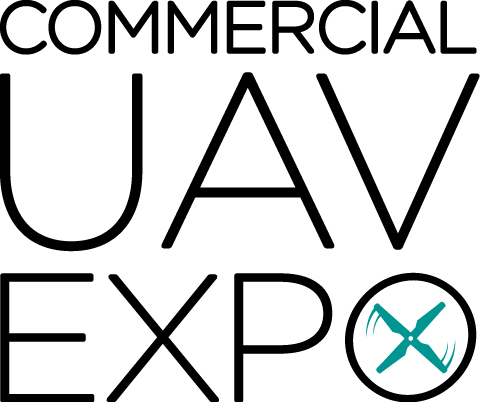
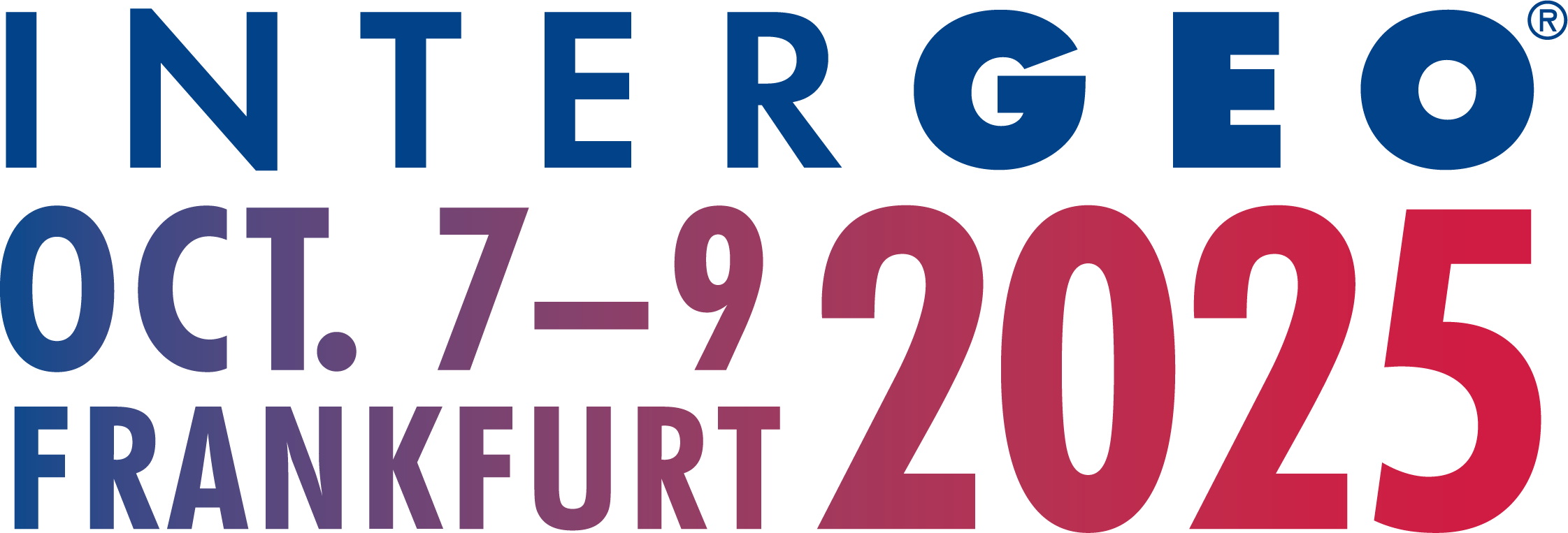
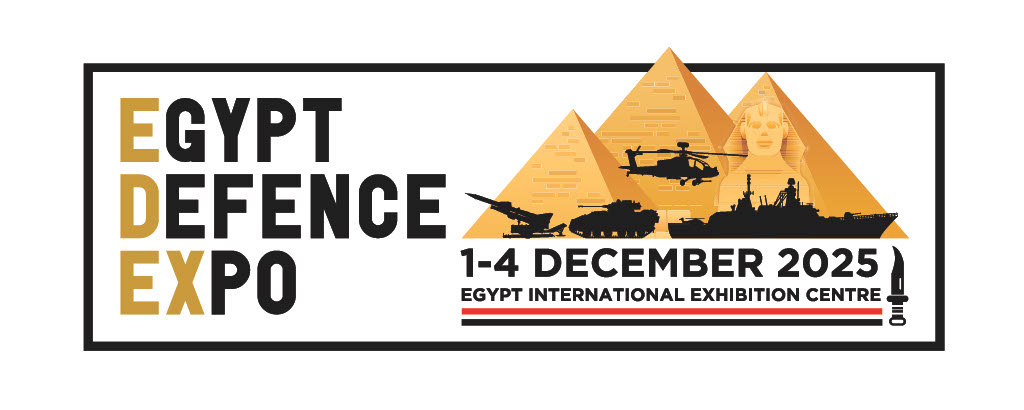
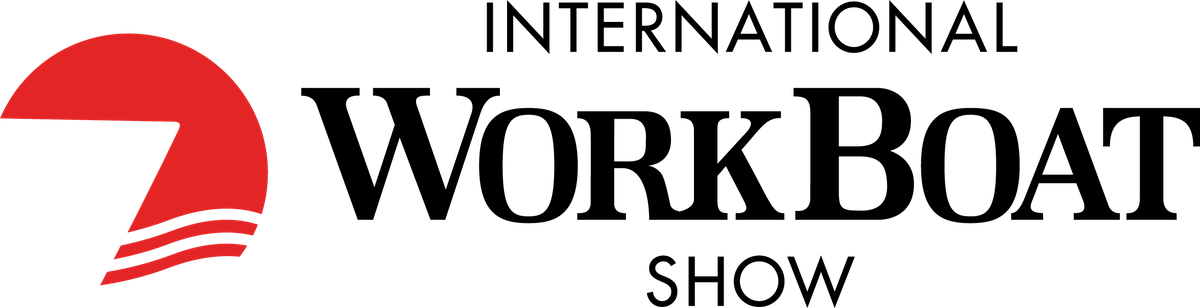
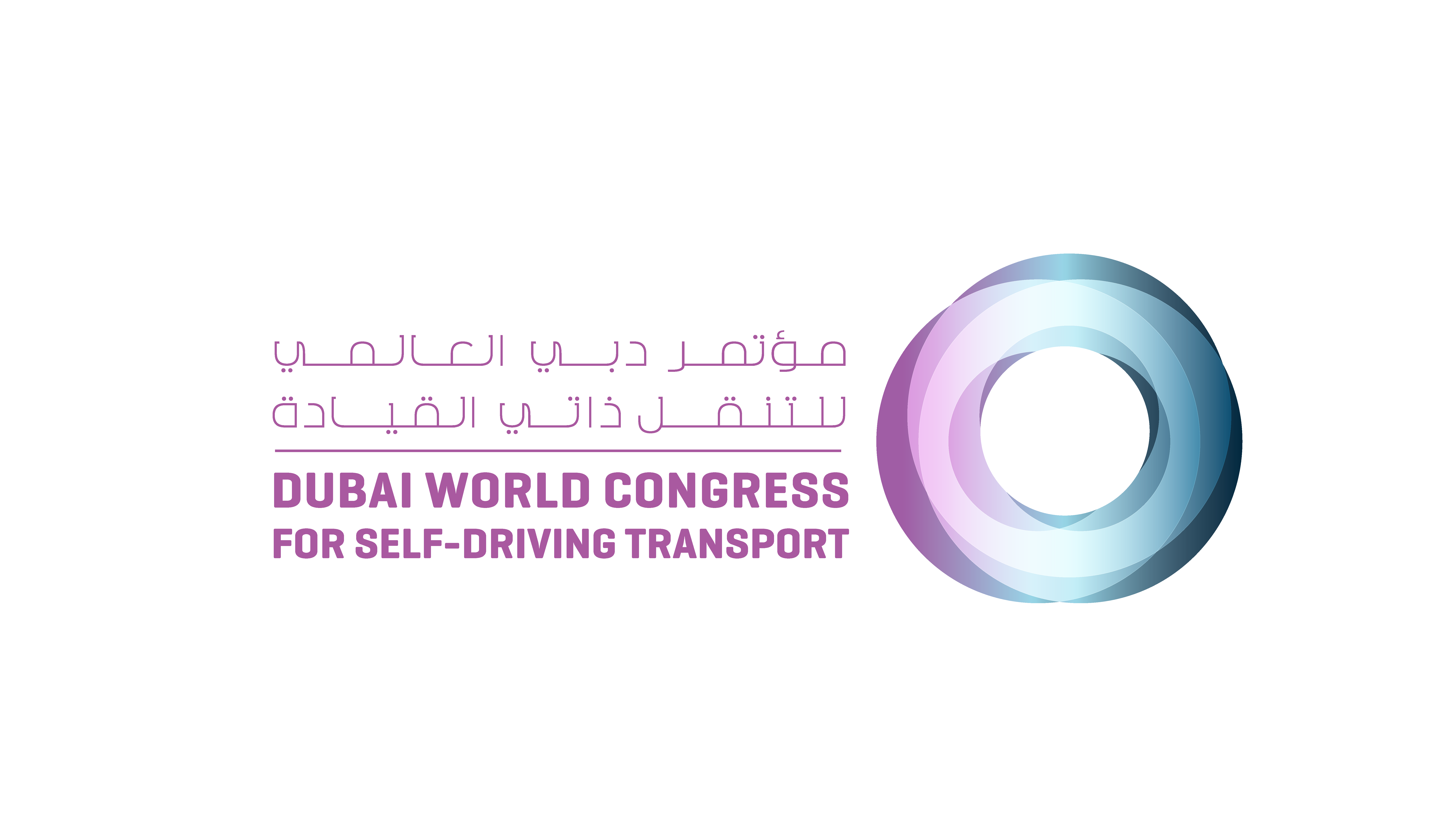
