UGVs
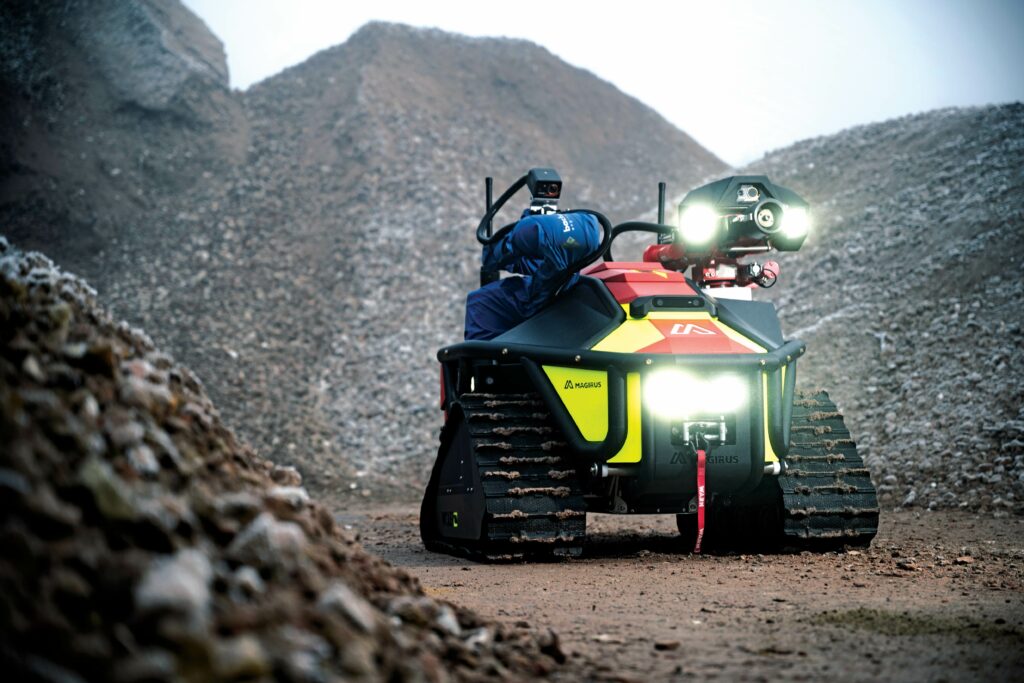
(Image courtesy of Alpha Robotics)
To the task at hand
Doing a job well means having the right build and equipment for it. Rory Jackson investigates how UGVs are being right-sized and optimised for a range of applications
As we have often heard over the years, it makes little sense for car makers to boast of a new model having the most powerful engine ever, or any other singular parameter or achievement, if they have forgotten to make the components work together at the system level.
Without that holistic system engineering, it cannot be expected that the car will be optimised to tackle its purpose well, whether that be ferrying children or shopping bags, or performing at test tracks and on autobahns.
With UGVs, holistically suiting the vehicle – and its ancillaries – to purpose is even more critical, given that, unlike cars, UGVs must drive themselves and potentially execute a number of more complicated tasks still. They must increasingly also handle very different environments to public roads, with unique hazards that push mechanics, powertrains and autonomy to their limits.
Fortunately, when one looks across the field of UGV solutions today, one can mark a number of ways that these autonomous terrestrial systems and their components (internal and remote alike) are being optimised to better suit the risk case, range requirements, cost profiles and more that end-users truly need, for widespread adoption of UGVs to become a reality. A selection of such cases is presented here.
Firefighting
There is a strong argument to be made that firefighting is the hardest application to engineer UGVs for, owing to strictness of regulations on safety and liability (for obvious reasons) that must be complied to. Such is the severity of these standards on autonomy, that most UGVs aimed at firefighting services are, in fact, entirely remotely-operated systems, forbidden from operating with any notable degree of autonomous behaviours.
Nonetheless, the capacity of uncrewed systems to save firefighters’ lives – by, for instance, entering burning buildings or areas before they do, to ascertain how safe or unsafe it is first, or initiate fire control tactics before human firefighters step in – cannot be ignored.
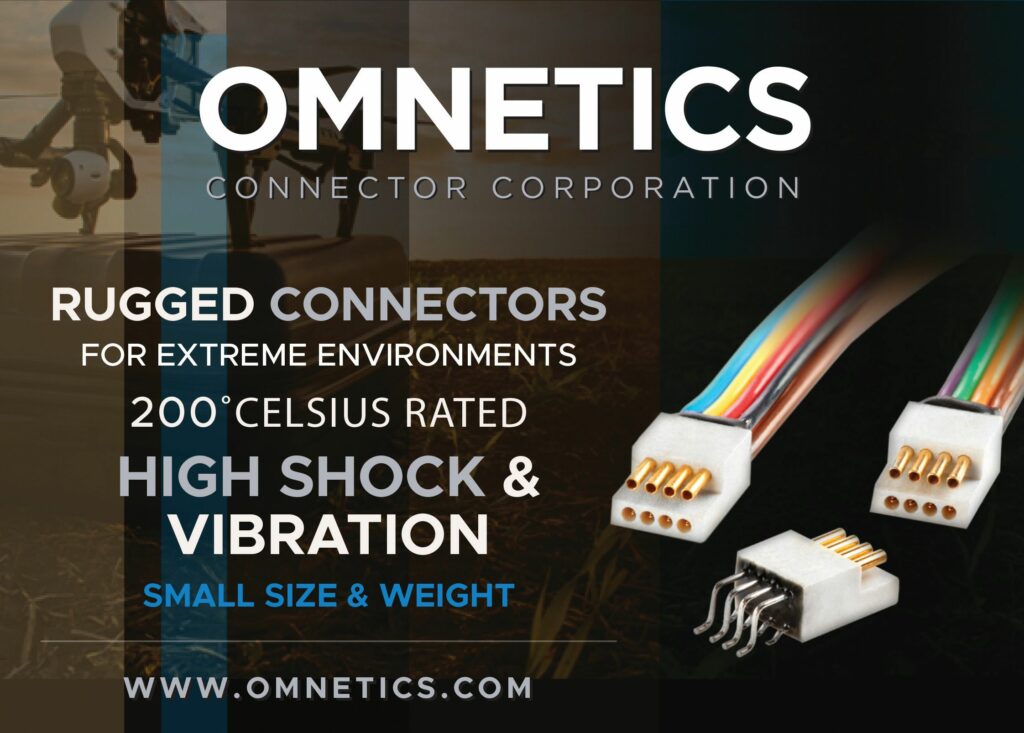
For such reasons, Alpha Robotics is developing an autonomous version of its Wolf R1 UGV. The Wolf is a 900 kg max weight vehicle measuring 1500 x 1200 x 1300 mm and running on dual tracked treads, with two 7.5 kW axial-flux electric motors providing up to 1050 Nm of torque each, its energy coming from a 9.4 kWh battery pack enabling eight hours of endurance as standard.
As Philipp Hartke, authorised officer at Alpha Robotics tells us, “If it carries too much equipment that might fall to six hours, though we’ve seen it operate up to 12 hours when it’s not carrying so much – but for its intelligent perception, we’re integrating a Lidar system and stereo cameras for real-time 3D mapping about the robot, so that it will be able to drive autonomously into buildings and different areas.
“It already has sufficient drive-by-wire systems installed; with sensors and autonomy software added, it will be able to efficiently operate by itself, or assist the firefighters with recommendations based on its own AI analytics of its sensed surroundings. The firefighters would then just press a button to select the Wolf’s next course of action, and it can then carry that out autonomously.”
The Wolf R1 as standard integrates four (non-stereo) cameras, statically positioned to capture 360° of video around it, principally for the remote driver’s awareness, but to enable machine vision-based autonomy in the near future, with a thermal camera for heat analysis. It additionally equips a water cannon for active firefighting, capable of pumping 3000 L/min at a range of up to 70 m.
“The heart of this UGV is our VCU [vehicle control unit], by which digital signals can be processed and distributed throughout the robot’s systems, including a tethered or wireless data link to a UAV connected for capturing and transmitting a high-level view of the surroundings, with either visual or thermal imagery, for firefighters to use in their area assessments,” Hartke adds.
The company also assembles and supplies mobile control centres, consisting of vans renovated to fit multiple GCS consoles (including five computer monitors and a number of gaming-type, industrial standard controllers, typically), as well as a loading bay to fit both a Wolf R1 UGV and a multirotor UAV. Hartke adds here that a critical part of the Wolf’s design was keeping it small enough to be carried by such a road vehicle, as otherwise the UGV would need to be engineered for sufficient speed (instead of torque) and autonomy to drive on public roads.
For its own survival in the field, the UGV also integrates an automated camera cleaning system utilising compressed air spray cans, and also carries jets for spraying a water cloud about itself, which protects the vehicle against both fire and overheating at critical moments. Also installed is a winch capable of roughly 2.4 t of tractive force, with the UGV able to tow up to 4 t, and an extendable claw can be integrated to improve the UGV’s stance while hauling particularly heavy loads.
“A robotic arm can also be integrated, and that’s something we’re especially focusing our AI R&D on; for instance, in grabbing objects or opening doors to clear its path through a dangerous area, without the operator needing to handle a cumbersome task like that via hand controller,” Hartke says.
A Wolf C1 is also manufactured as an alternative to the R1 built around firefighting-related logistics functions, such as carrying up to 200 kg of water pumps or casualties.
Passenger transport
While the case for autonomous ‘robotaxi’ vehicles remains challenging, given the greater ease of use and security that human chauffeurs provide in covering bespoke, potentially ad hoc routes and waypoints, autonomous shuttles, buses and coaches continue to be developed with valuable niches in mind.
With autonomous logistics and passenger transport trials both on sea and through the air proving definitively that autonomy can significantly cut back fuel and power usage (largely thanks to precisely- and AI-optimised control and navigation), fleet operators are now looking to invest – or at least gain experience – in self-driving solutions to make good of some of their (traditionally) less profitable operations.
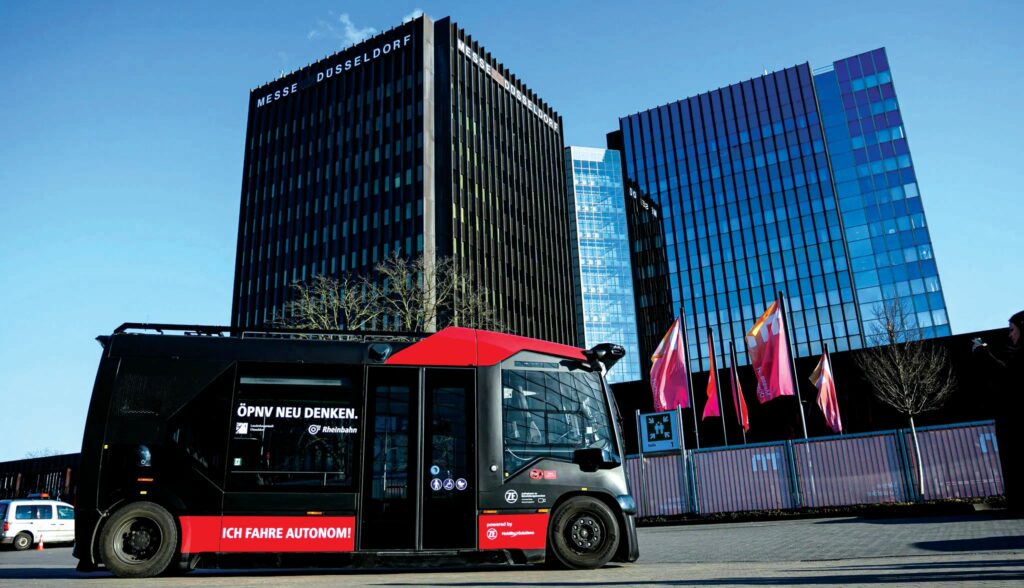
(Image courtesy of Rheinbahn)
One of these is Rheinbahn AG, a public transport operator in western Germany, which has commissioned ZF Mobility Solutions to test the short-term use of an autonomous mobility solution with a safety driver on public roads in Düsseldorf.
As Jonathan Scheu, technical project lead autonomous shuttle program at ZF Mobility Solutions, tells us, “We have already tested this type of vehicle with AD technology from ZF as part of the RABus project in the southwestern German cities of Mannheim and Friedrichshafen. That connected villages with cities, through gradually optimising a cost-effective, autonomous means of driving the rural and remote roads that fleet operators traditionally don’t always cover.”
The vehicle is a 9.2 t shuttle measuring 7 m long, with nine seats and one wheelchair space. As of writing, the trials are only performed with seated passengers, though pending optimisations and safety assurances, additional standing passengers will be permitted.
To fully assure safe operations on public roads, where mixed traffic remains a risk despite the remote nature of the routes to be covered, the shuttle integrates a plethora of Lidars, cameras and radars such that all three technologies fully overlap in covering 360° around the vehicle.
“We have both long- and short-range Lidars, and our configuration and development road map are set-up so that we can gradually connect more sensors to our [AD] stack,” Scheu explains.
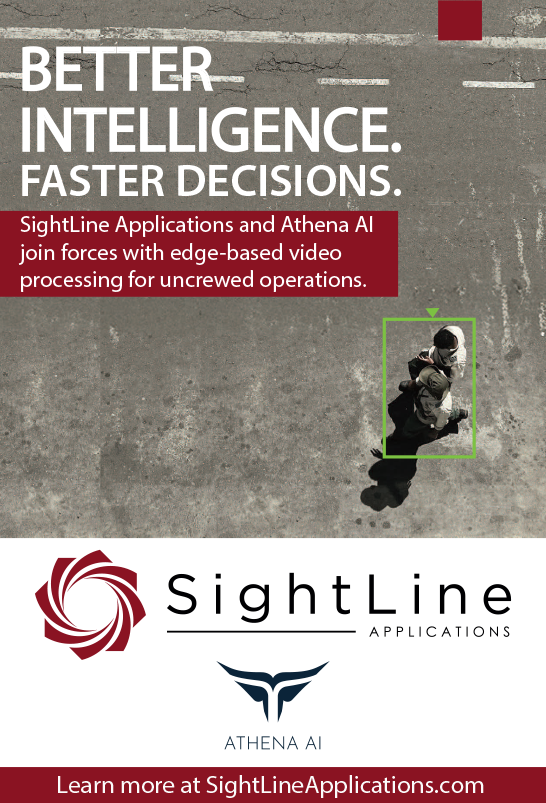
“That means we actually carry more sensors than we currently need, but as we expand our trial routes, and take on more complex traffic and manoeuvring in the future, we’ll need those sensors which currently sit inactive around the body. And the good thing about that is that we won’t have to do architectural changes every three-to-five months as we advance up our development roadmap: everything we physically need is already on the shuttle, making our development engineering very efficient.”
Gaining approvals for trial operations also took exhaustive hardware and software engineering across a plethora of safety systems, the latter integrating multiple subroutines for constant internal self-supervision and inroads for safety driver intervention. The former encompasses a wide range of ZF’s safety-critical automotive parts, among them one of its FRGen imaging radars at the front, to sensor fusion using a ProAI automotive supercomputer, and a ProConnect modem enabling real-time interfacing with fleet management systems, remote supervision UIs, and telemetry analysis servers.
Uniquely (among those solutions we have covered), the shuttle also integrates eight microphones throughout, to audio-detect police, ambulance or firefighters’ sirens approaching. As well as enabling the shuttle to autonomously make way much earlier than cameras, due to the greater distances over which audio detection will work than visual detection, camera views can easily be blocked by surrounding traffic or structures. Through this approach, the project stands to make one autonomous road vehicle significantly less of a nuisance than some others picked up in mainstream news.
Defence
Use of UGVs for defence applications has become increasingly widespread, as inherently crucial tactical and strategic assets, and for saving the need to send humans to front line areas.
Specific use-cases for military UGVs vary from frontline logistics, casualty evacuations (CASEVAC), and intelligence, surveillance and reconnaissance (ISR) missions. To serve in all of these types of operations and more, Munich-based ARX Robotics has engineered its flagship Gereon RCS UGV with modularity as a forefront design goal, such that different payloads can be swapped on and off the vehicle. Such payloads include Saab surveillance radars, Thales ground radars, Hensoldt optronics, UAV launchers from Rheinmetall and UAV launch-and-recovery solutions from Quantum Systems.
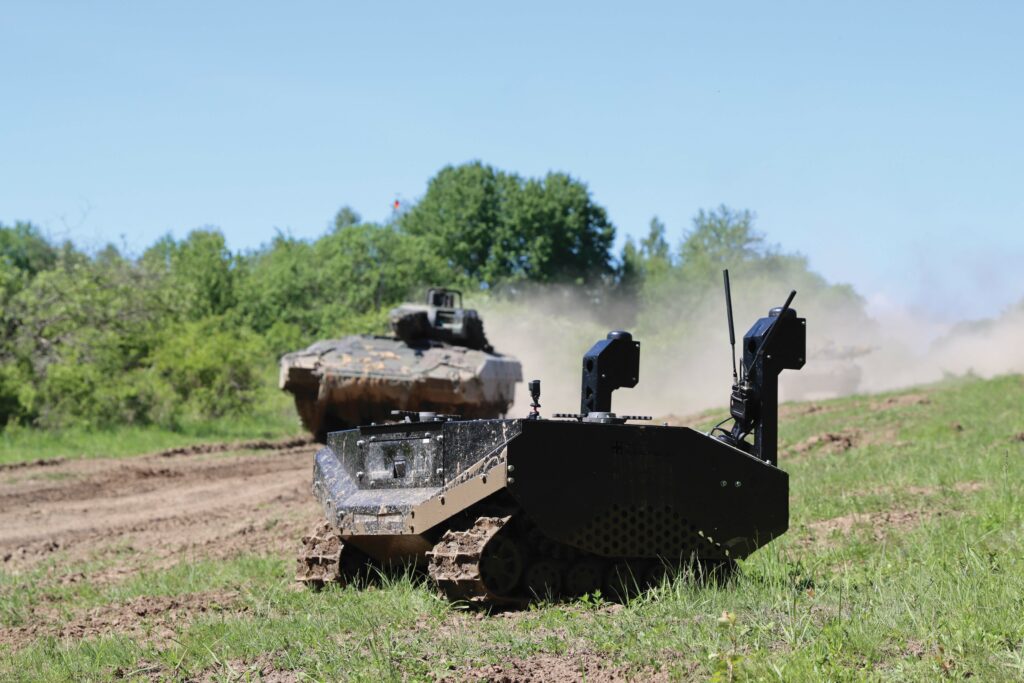
(Image courtesy of ARX Robotics)
“As standard, we have 360° of cameras around the robot for environmental perception, with a thermal camera for night vision and a stereo camera for depth sensing at the front, as well as a front-mounted and -oriented Lidar also,” says Carsten Ramke, senior robotics software engineer at ARX Robotics.
“Wherever possible, we’ve aimed for a lower-cost approach in subsystem selection compared with other UGV manufacturers. We’ve made it a highly-capable system but the fact is, in warfare scenarios, UGVs can’t be expected to survive very long, so what matters more is that you engineer a UGV that’s affordable to build and supply en mass.”
To that end, ARX has picked and integrated automotive sensors and other components wherever possible, such systems being sufficiently rugged for harsh environments while also being manufactured in bulk.
Information on the UGV’s own health telemetry and on its surroundings is delivered and processed via ARX’s Mithra OS, which has been developed as an open interface, AI-powered software core that can enable interconnectivity between crewed and uncrewed vehicles, as well as over-the-air software updates and swarming operations between meshed uncrewed assets.
As an off-road vehicle, the Gereon RCS has been successfully tested in snowy and muddy terrains, including negative temperatures in winter and above 40 C heat in summer.
The standard UGV configuration is fully-electric, silent operations being more important than the extra range a fuel powertrain would bring; the Lithium-ion battery pack gives up to 40 km of range between charges, and is based on a design intended for heavy-duty machine vehicles.
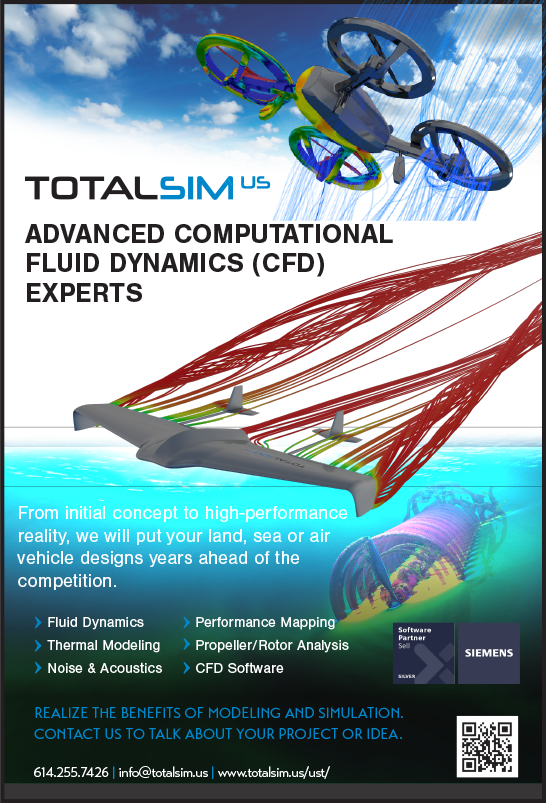
Up to 72 hours of operation can be achieved, given the CONOPS for such UGVs involving potentially many hours spent in a stationary ‘watcher’ role. The system is also capable of carrying up to 500 kg of payload at a time.
“To thermally manage the batteries in extreme environments, we’ve equipped them with a heating system for winters, and a wide heat sink for cooling – but as a high voltage pack, we tend not to have severe heat losses,” Ramke says.
Logistics
The use of autonomous tow tractors in warehouses, factories, airports and other industrial logistics zones has been established for several years now, but with greater experience and cognizance comes optimisations, which bring vehicles and software alike ever closer to something ideally cost-efficient, scalable and applicable for real-world business applications.
As UK-based Fusion Processing has found, while developing such vehicles through customer projects, there is great demand for applying full autonomy to tow tractors, to relieve drivers and fleet managers of some of their most repetitive burdens, and improving overall workplace efficiency. Achieving that requires optimisation, but not absolute maximisation of UGV intelligence nor capabilities.
“While we’re still working in a number of road vehicle projects, we’ve had a collaboration with Bradshaw Electric Vehicles for around three years now, which involved working with a customer to get tow trucks working to their exact needs onsite – we can’t name them, but they’re a manufacturer with several sites in the UK and on every continent,” explains Jim Hutchinson, CEO of Fusion Processing.
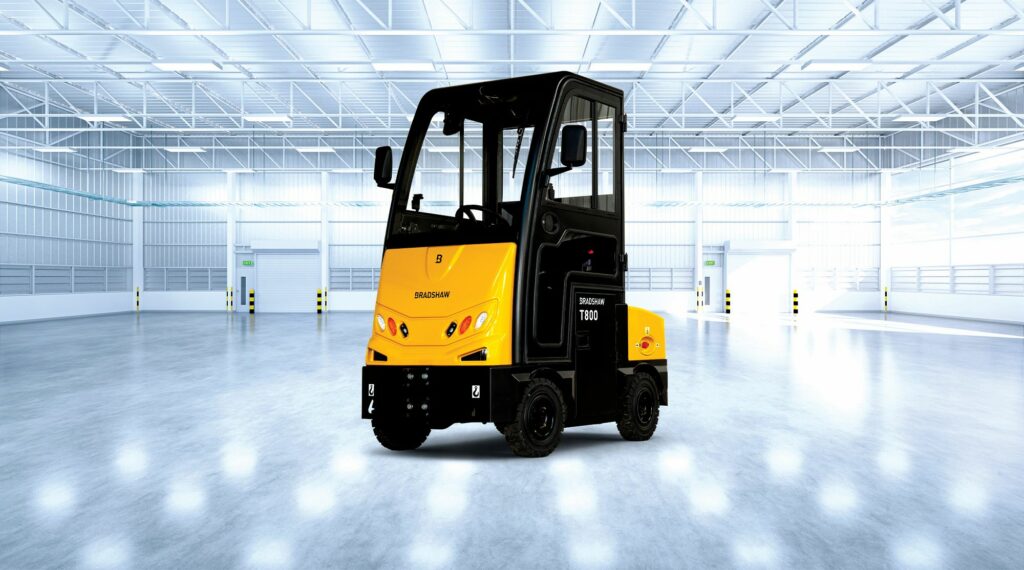
(Image courtesy of Bradshaw Electric Vehicles)
“Like many successful companies, they already use significant automation, but are reaching a point where their tow trucks need a sudden jump in movement intelligence, and flexibility in autonomous decision-making, to cope with different factors to their usual problems – for instance, when switching between outdoor and indoor navigation, or moving amidst HGVs in an off-loading area.”
The level of autonomy being engineered into the Bradshaw tow tractors is analogous to SAE Level 4 autonomy, as close supervision is unneeded, though the operating domain is limited to finite work sites, closed-off to the public and their vehicles, and tow tractors consistently drive at low speeds. As a result, the technologies and configuration processes (and by extension, the dev roadmap) have been far less complicated than those needed to make self-driving vehicles functionally safe for public roads.
An embedded map is installed on each autonomous tractor, enabling them to localise and geocage themselves within the limits of the operating zone. To sense where it is and identify objects around itself, each vehicle integrates a set of cameras and one Lidar as standard (as well as radar when appropriate for the specific route or use-case), as part of Fusion Processing’s CAVstar suite and ecosystem of autonomy-enabling technologies.
“For very complex or higher-speed scenarios, such as the autonomous bus projects on public roads we also do, then you need a very capable sensor set, with overlaps between sensor types and FoVs, to triplicate redundancy and cover a wider array of risks, which massively ups the costs and edge-case hurdles that autonomous road projects have to overcome,” Hutchinson notes.
“But because of the slow and predictable nature of these tow tractor operations, we don’t need very long-ranged or high-speed sensing to be safe – theoretically, this use-case might even work with only cameras – the system is now ready for active commercial deployment, and we’ve reached this point using all low-cost solutions, with a couple of launch customers ready to try it themselves.”
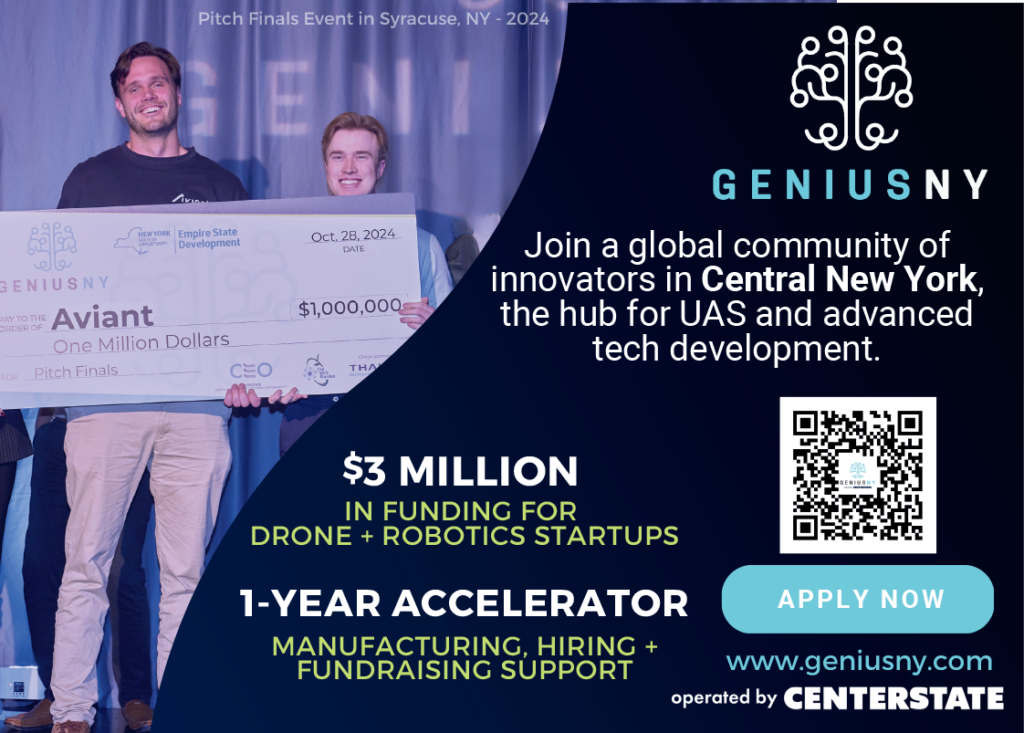
Where possible, the data from the tow tractors’ sensors are cross-referenced with GNSS for added safety and redundancy. Fusion Processing has also trialled some indoor positioning and localisation systems, such as RF-based beacons fixed throughout structures, which can come pre-installed in some places, or are otherwise easily placed.
“Like GNSS, those stand to provide crucial cross-referencing for what the sensors are picking up, and a useful security add-on,” Hutchinson says.
“If there’s discrepancies between the two sources, the vehicle can opt into minimum-risk manoeuvring to temper whatever’s wrong, and flag the end-user’s control room for a potential issue. We’d expect that to be an extraordinary event, not a routine occurrence, but it’s still important to have in busy logistics zones.”
Fusion Processing also helps end-users set up their remote control and monitoring rooms, providing vehicle and fleet management software as well as plug-ins, depending on customers’ pre-existing hardware, software, and operational routines.
Meanwhile, autonomous logistics on roads continues to develop, with DHL Supply Chain having recently begun autonomous freight transportation on Texas roads, using the Volvo VNL Autonomous truck co-developed by Volvo Autonomous Solutions (VAS) and Aurora Innovation. As with the Bradshaw-Fusion Processing collaboration, the former’s truck integrates an autonomy suite from the latter to go from being a driven vehicle to a self-driving one.

(Image courtesy of Volvo)
Much like Kodiak Robotics’ Kodiak Driver (featured in issue 48), the Aurora Driver is an autonomous driving system engineered for SAE L4 autonomy, which encompasses sensors including high-resolution cameras, imaging radar, and proprietary long-range Lidar able to detect targets 400 m away, for enabling functional safety at highway speeds.
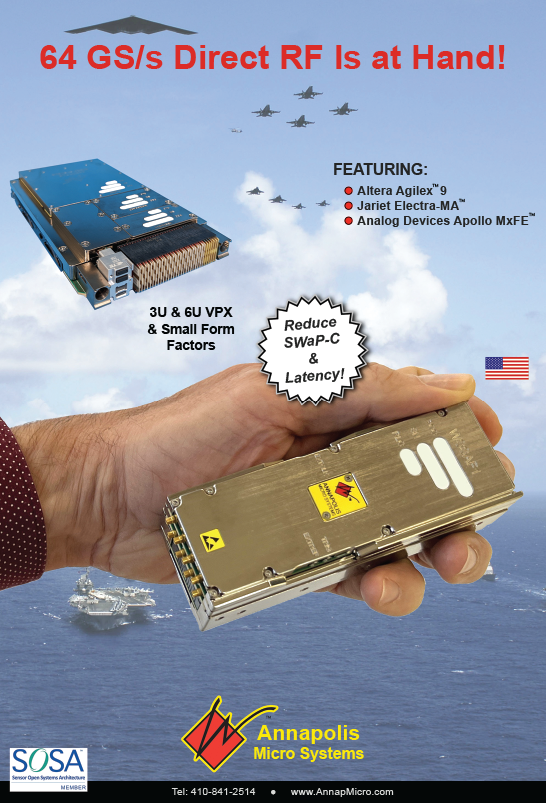
To further the safety case for this operation and others, the Volvo VNL Autonomous integrates redundant computers, steering, braking, comms, power management, energy storage and vehicle motion management systems.
DHL Supply Chain North America has commented that greater reliability in long-haul freight and 24/7 operational capabilities are among the benefits it especially anticipates yielding through the Volvo ANL Autonomous. The truck is assembled at Volvo’s New River Valley plant in Dublin, Virginia, and though modularly configurable, runs as standard on Volvo’s D13 engine, a direct injection I6 diesel producing up to 500 bhp and 1950 lb-ft (2643.84 Nm) of torque, with a variety of transmission options to suit the routes and payloads to be hauled.
Mining
As global mobility electrifies and digitalises, sustainable access to key elements such as silicon, lithium, neodymium and more becomes paramount.
And as fleet operators across countless industries are discovering, switching from crewed to uncrewed vehicles consistently reduces the use of fuel and battery energy, thanks to high-resolution sensing, fine digital control, and automated traffic management to cut out all unnecessary manoeuvres. It also reduces the need for humans in hazardous mining environments or such repetitive operations, cutting medical, training and PPE costs.
Hence mine operators are rapidly trialling and evaluating how small autonomous trucks (as an easier integration project and a more scalable introductory solution than large self-driving trucks) might save them fuel and parts replacement costs, not to mention yield compliance or credit benefits via emissions reductions.
Such trials were seen many years back on the part of the Rio Tinto mining corporation, where Scania – among other companies – has been providing small trucks equipped with autonomous sensing and compute systems for trials in its Australian operations.
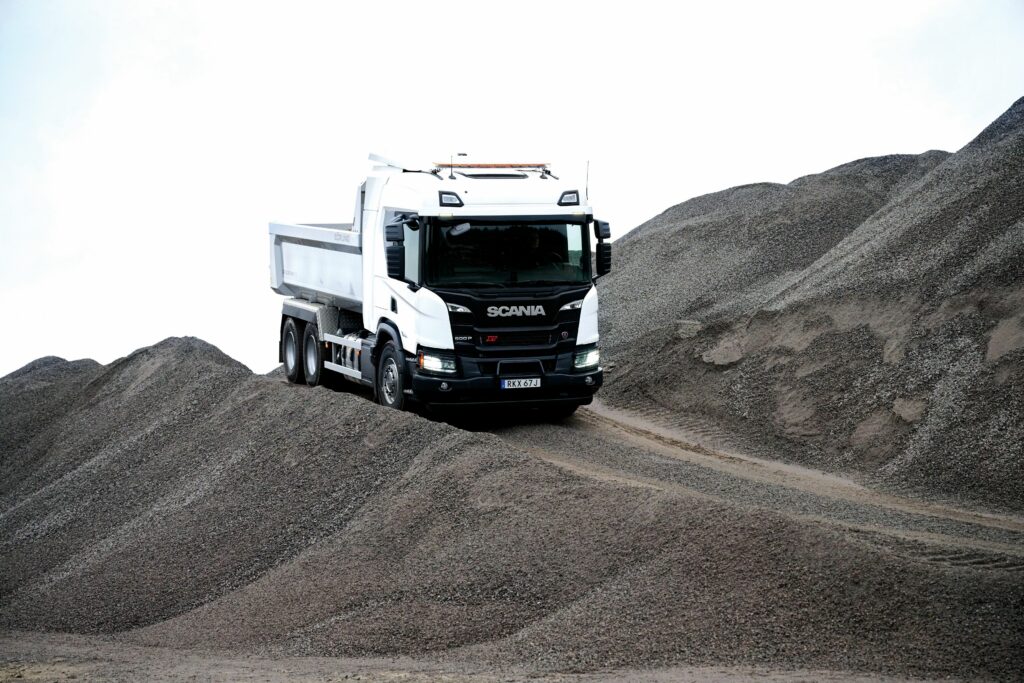
(Image courtesy of Scania)
More recently, the Swedish OEM has agreed with Fortescue, another Australian mining corporation, to jointly-develop and validate a fully-integrated autonomous mining road train solution – that is, when a single autonomous truck hauls multiple trailers – with the resulting vehicle likely to be one of the heaviest-haulage AVs ever made.
Scania focuses its autonomous truck development in both mining and hub-to-hub logistics. For the former, Scania’s solutions are engineered to move materials from mining sites to storage or processing facilities by following predetermined routes of waypoints. Data from GNSS as well as Lidars, radars, and cameras encircling the trucks’ bodies are gathered to inform not only obstacle evasion and safety behaviours, but also a central control system. Scania’s V2X (vehicle-to-everything) antennas maintain a data link to that system, which can then make decisions for optimising routes, maintenance, and productivity.
The company’s self-driving mine trucks are trialled and optimised at the Scania Demo Centre’s Gläntan circuit, located in Södertälje, Sweden. There, the systems are cycled through different routes as well as autonomous material loading and unloading operations (including automated waiting as a crewed excavator dumps material into the truck trailer).
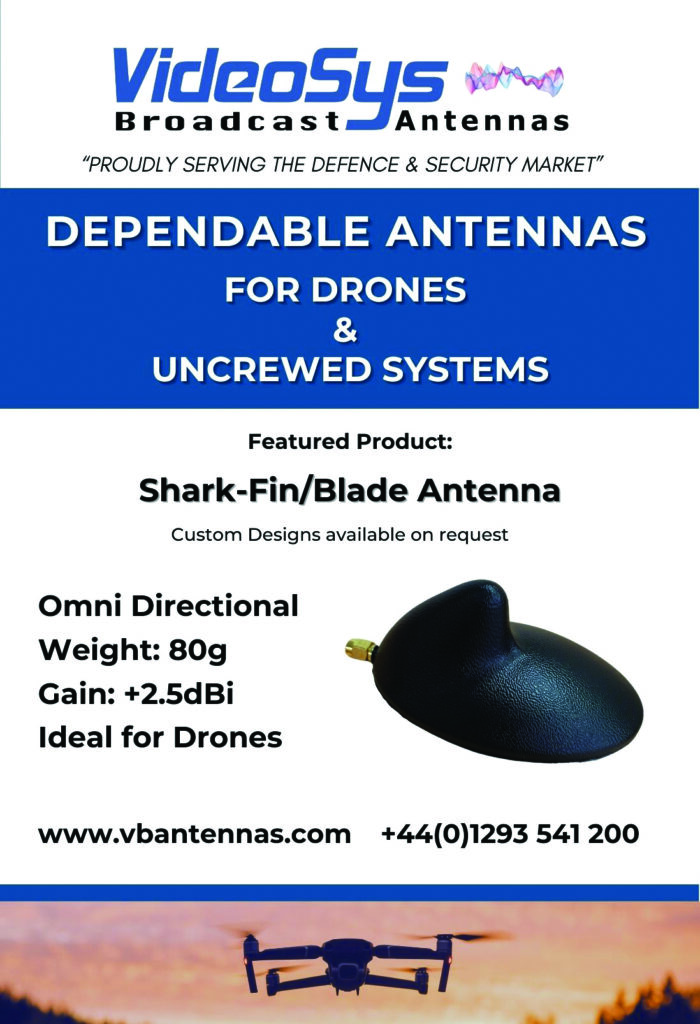
Up to 10 trucks are typically managed from the Gläntan operations centre at a time (a self-imposed safety limit, with management of more being technologically possible), with a safety driver either present or not depending on the nature of the incipient test.
Summary
Across these applications, one can see that the push for efficiency is growing to encompass not just individual components, but entire vehicles, their surrounding infrastructure, and the way they are manufactured.
As well as more cost-effective numbers and selections of parts (especially sensors and batteries, among the most expensive single components on ground vehicles), designing for manufacture and engineering for plug-and-play are becoming common practice to ensure a viable level of pricing and useability for customers. This is reflective of an industry maturing beyond one-off experimental robotics projects, towards series manufacturing.
With self-driving component manufacturers now producing safety-compliant autonomy computers and by-wire systems in bulk, UGVs can increasingly be engineered – and manufactured – at lower and lower costs, to suit customers’ budgets and drive home the efficiency advantage of going autonomous.
But it is also imperative that UGV manufacturers continue to make face-to-face contact with both regulators and customers on a regular basis, to ensure uncrewed vehicles on- and off-road will not only be permitted, but wanted by those across all industries who have come to understand the potential of uncrewed systems.
UPCOMING EVENTS
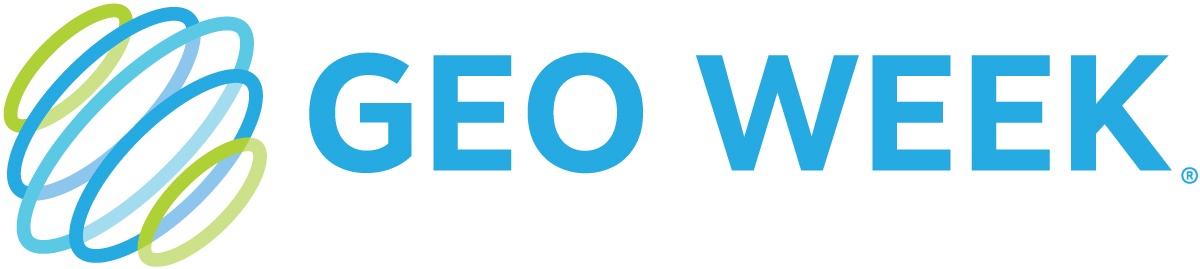
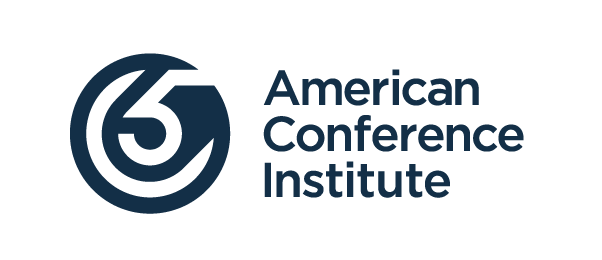
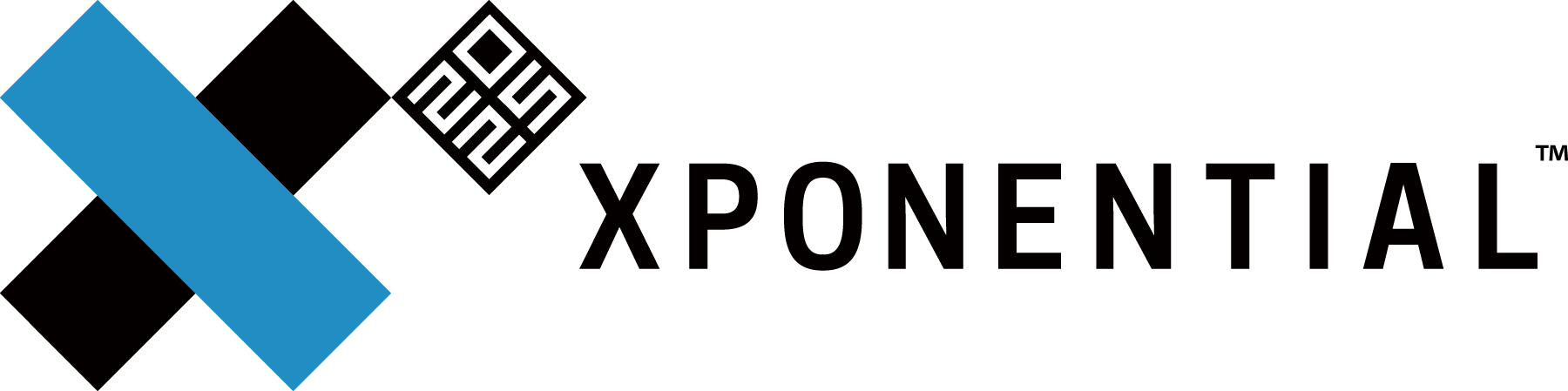
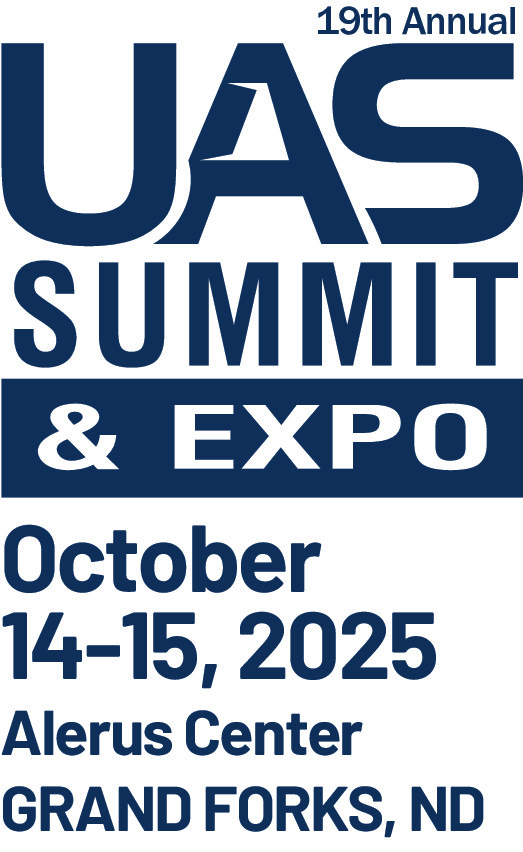
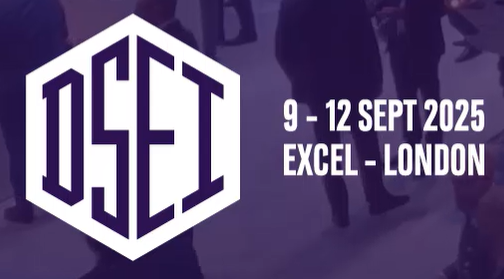
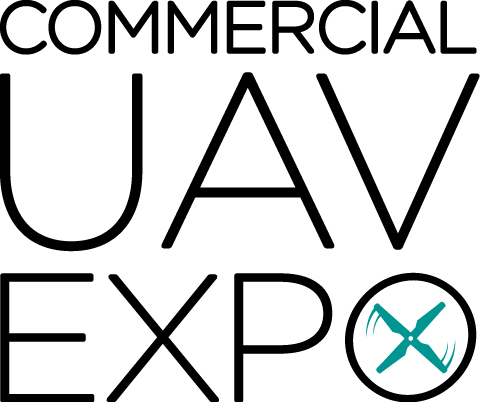
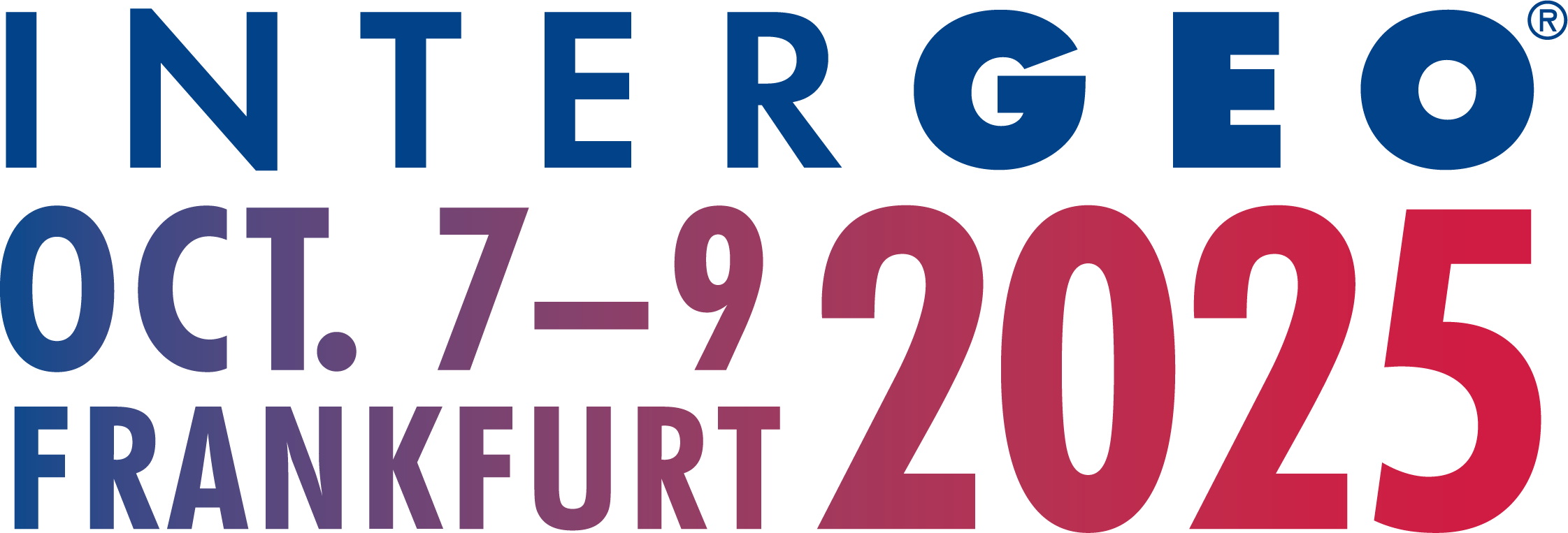
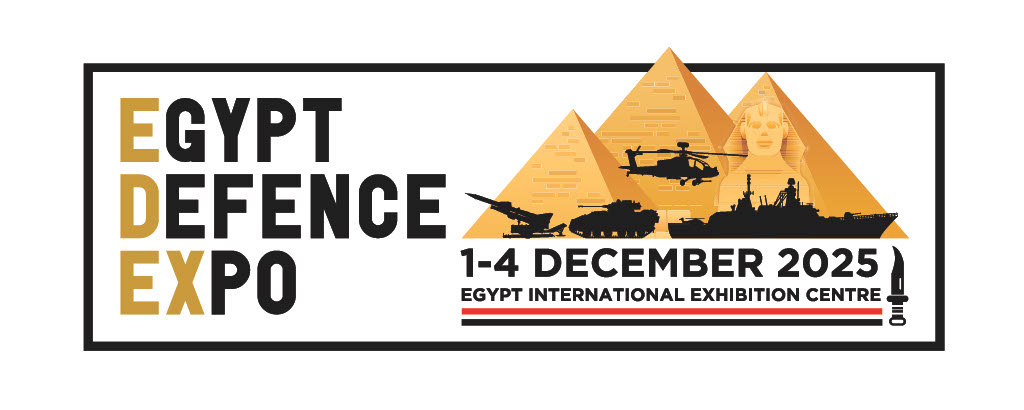
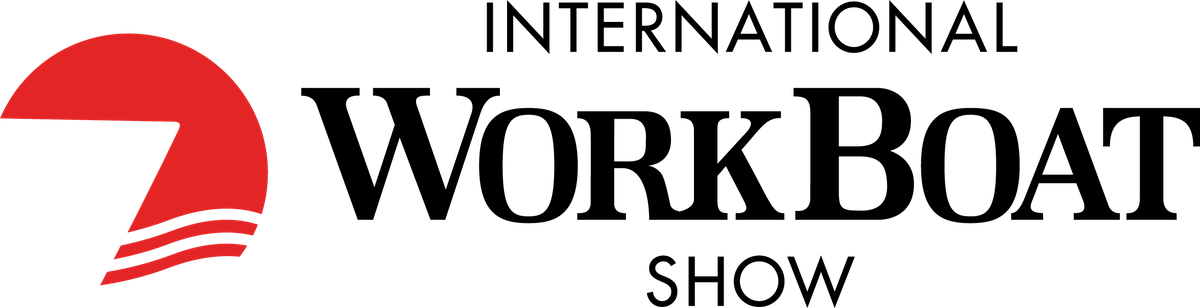
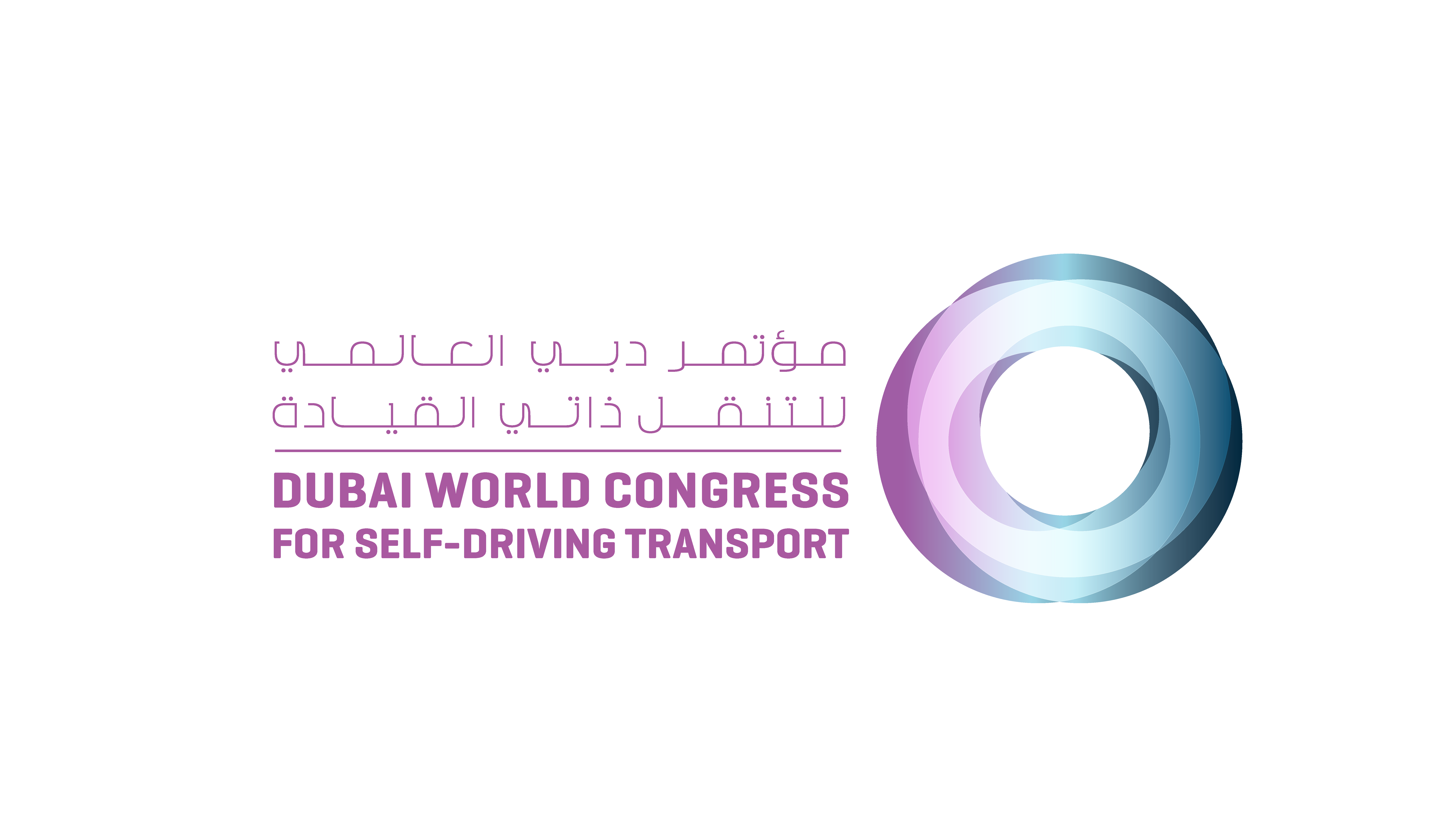

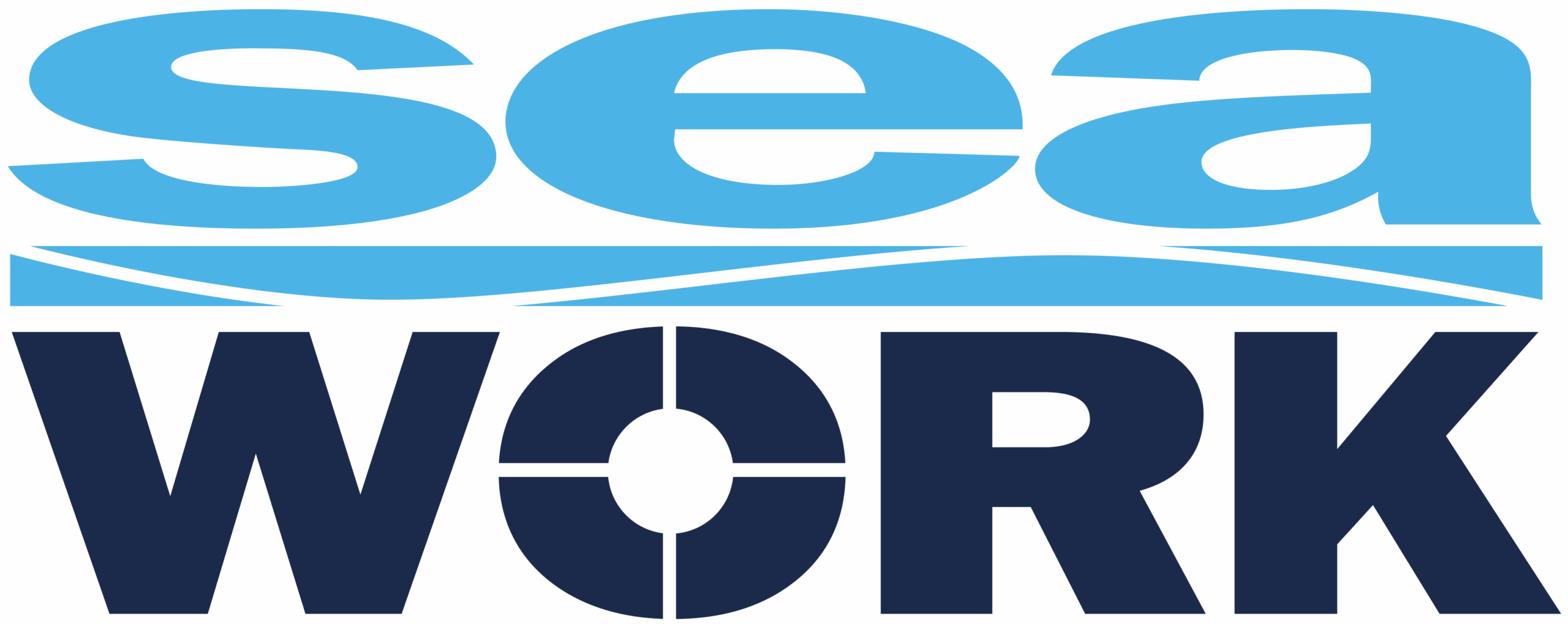