UAVs
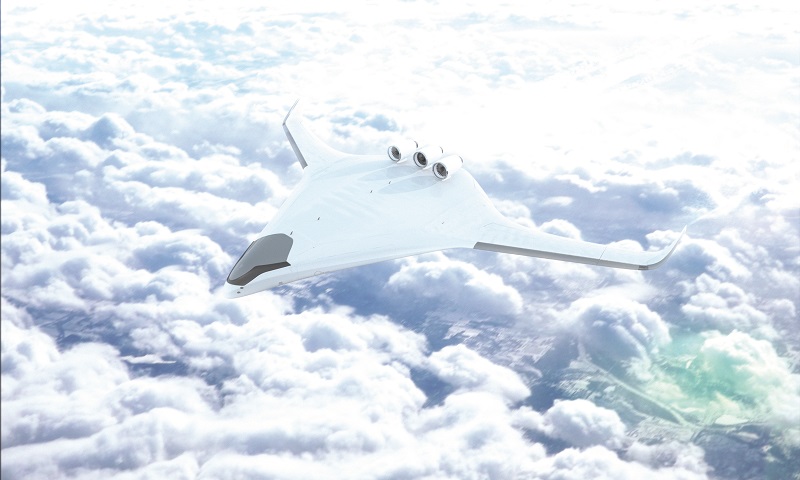
Rory Jackson investigates the new breeds of UAV, from the tiny to the gigantic
While the words ‘drone’ and ‘UAV’ still conjure up images of toy multirotors in the mind of the average person on the street, those within our industry know that uncrewed aircraft have evolved and diversified into vehicle configurations far beyond that.
Some of the new breeds of UAV are still as small as photography drones; others are as big or bigger than business jets and heavy road vehicles. But, all of them share a similar advantage over crewed aircraft in that there is no need for a pilot’s cockpit or passenger cabin, so UAV developers can experiment with different internal space allocations, weight distributions and outer aerodynamic profiles to maximise efficiency and value.
Thus, autonomy has unleashed the full creativity of aircraft designers and engineers, and produced a vast range of UAV configurations that may seem quite shocking to those who know nothing beyond the simple quadcopter. In this feature, we will investigate some of these configurations, and uncover the benefits that their novel structures and layouts may yield to interested customers.
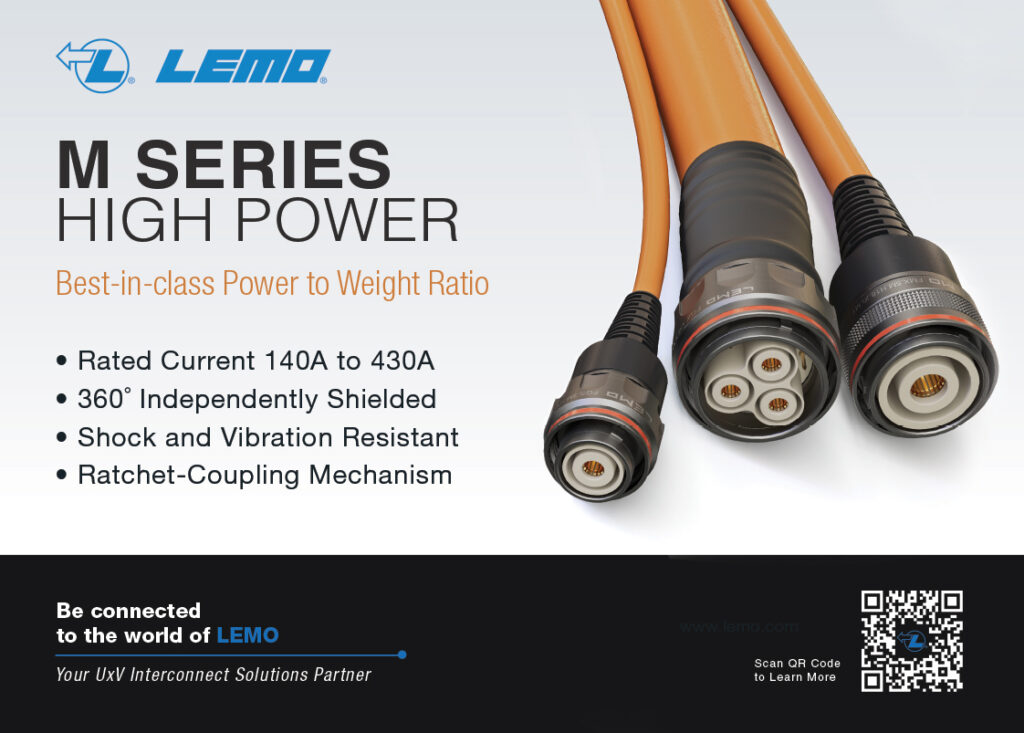
Air freight
We last featured US-based Natilus just over five years ago (Issue 23), showcasing its concept for a blended-wing UAV with a 1 t payload capacity.
Since then, the Californian company has spoken with prospective aerial freight customers who asked whether the aircraft could be redesigned to carry standard aircraft pallets and containers within its cargo bay.
“To fit those containers we had to grow the configuration, so the aircraft has quadrupled in size and now has a 4 t payload capacity for carrying 12 standard LD3 [4.5 m3] pallets, and to lift all of that we moved from a single turboprop to a dual-turboprop configuration,” says Aleksey Matyushev, CEO of Natilus.
“Since those high-level changes, we’ve done at least 10,000 hours of CFD analysis, including wind-tunnel tests, here in San Diego, where we have access to a world-class one. Through amassing good data, we adopted new ideas in the wings, tails, everything to make something that will work aerodynamically, not just from a controllability standpoint but from performance too.”
While one pictures a C-130 or similar as the ideal freight aircraft, they are designed for prioritising volume rather than weight, and keeping onboard crews comfortable during banking and disembarking. Matyushev estimates that the blended-wing body enables twice as much payload relative to the size of the UAV than in a conventional, comparable-sized tube and wings design.
FAA certification of the UAV, now named Kona, after the Pacific winds that interact with the trade winds, depends on its design being stable in air without needing an overly complex autopilot, hence Natilus’ exhaustive CFD.
Aero simulations have validated the aircraft’s stability, so Matyushev says the design is mature and the Kona is at TRL 6, with expected flight endurance of up to six hours at a long-range cruising speed of 200-210 knots, a top airspeed of 240 knots and a flight ceiling of 22,000 ft (with an operating altitude of 12,000 ft).
“We are now building its hardware in a 12,000 ft2 facility, and we’ve fed high-quality wind-tunnel data into the autopilot’s control loops to start software- and hardware-in-the-loop simulations,” he adds. “We’ve also done scale-model flight tests to validate the aerodynamics and the fixes we made following the first iterations.”
Key contributors to the hardware at present include Collins Aerospace for the cargo-loading system, Janicki Industries for the airframe carbon composite, and Pratt & Whitney Canada for the engines.
Two PT6A-67D turboprops will power Kona’s flight. These weigh 234 kg, measure 48 cm in diameter and produce 1,271 hp (or 948 kW), with a specific fuel consumption of 0.546 lb/hp (or 332 g/kWh). Their construction features a four-stage axial compressor, a one-stage centrifugal-flow compressor, a one-stage gas-generator power turbine and a one-stage free-power turbine.
“Within the power-plant categories we were interested in, it came down to either the Catalyst engine from GE Avio Aero [Issue 41], which is a cutting-edge turboprop, or Pratt & Whitney, which has been producing these engines for 80-odd years,” Matyushev explains.
“The reliability that Pratt & Whitney engines are known for was a key selling factor to a lot of our customers. And if we’re going to sell this aircraft globally, having the global maintenance and support network of a P&W was a major factor in our final decision, especially if the engines will bring Konas and their freight to remote areas like the icy Canadian north or hot desert climates one day.”
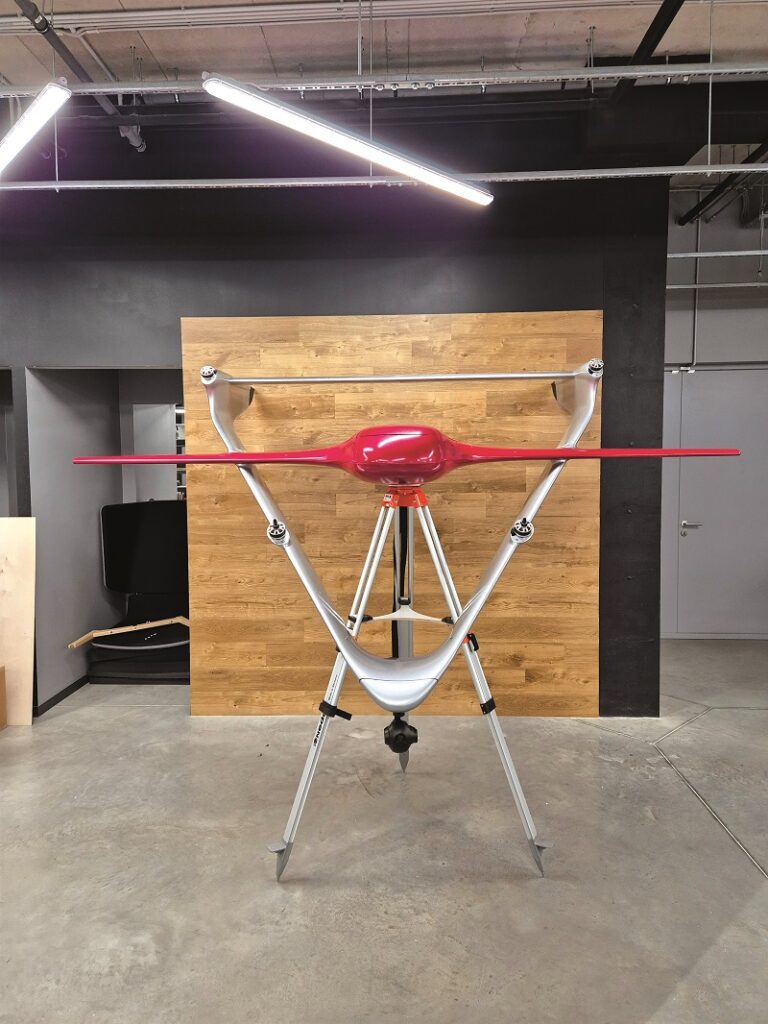
Long-distance inspection
In the course of designing its VTOL-capable UAVs, FIXAR (FIXed Angle Rotor) applies its namesake technology stringently, its CEO Vasily Fainveits having found that VTOL-transitioning between vertical and horizontal flight is possible without needing tiltrotors if the lift rotors can be fixed at a tilted angle somewhere between the horizontal and the vertical.
The Latvian company (which recently moved headquarters to the US) is best known for its first product, the fixed-wing quadrotor FIXAR 007 UAV, but it is now developing a remarkably different airframe configuration in its larger FIXAR 025 UAV.
“Both UAVs use the exact same tilted-angle rotor technology, and the exact same lower-level autopilot control laws, with only some high-level changes in software between them,” Fainveits says.
In developing a proprietary autopilot with the right logic for taking off and landing vertically using angled rotors, FIXAR also created proprietary data links, GCS solutions and airframe designs in the 007, with an eye towards optimising the payload-to-weight ratio (with the 007’s 7 kg MTOW, including 2 kg of payload capacity).
“There were a lot of aerodynamic tweaks to get the 007 to perform as well as it does in such an unusual, specific shape, but as we looked into offering a bigger solution with a higher payload capacity, we had a choice: either try to scale up this existing design and get it to work in larger form, or work on something completely new to hit the higher carrying targets,” Fainveits recounts.
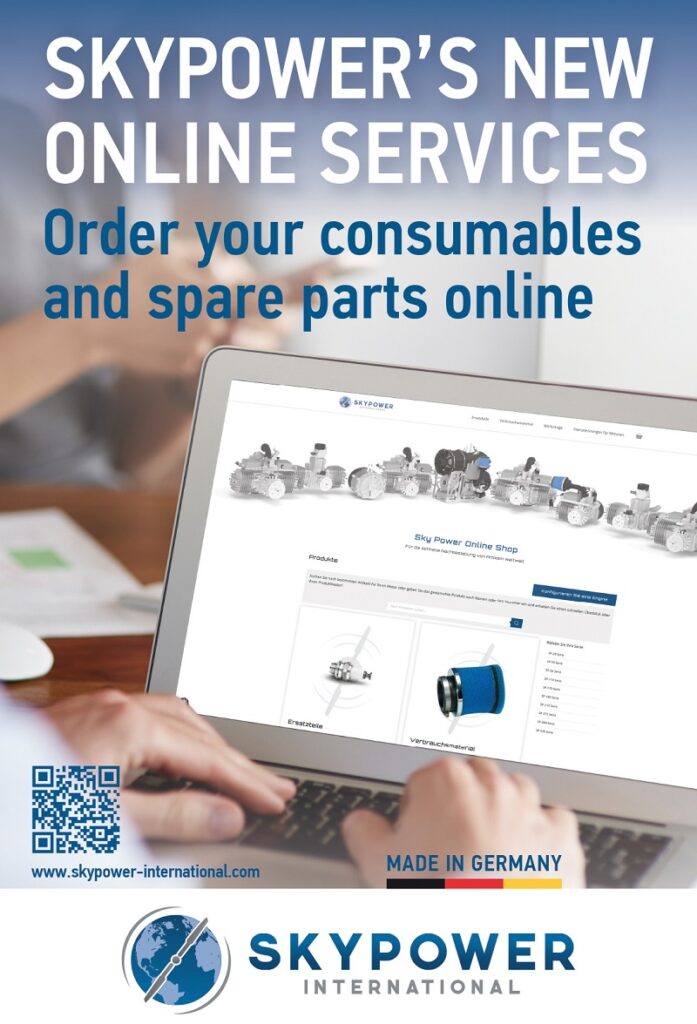
“In truth, we prefer being creative over the boring work of scaling up existing designs, but also while thinking about the 007’s legs, especially how UAV legs can be a dead weight in not contributing anything in mission, I started thinking about my chair’s legs and how it didn’t need four of them. In fact, a three-legged chair is more stable on uneven ground than a four-legged chair is.”
Those thoughts drove two engineering questions for Fainveits and his team: how could the UAV be optimised to VTOL on three legs rather than four? And how could the frame, legs included, be designed to contribute lift instead of being dead weight?
Around its blended-wing main body, where the fixed-angle rotors mount, the FIXAR 025 features a triangular aerofoil, the corners of which serve as landing struts. This achieves the more pragmatic, functional and efficient frame that Fainveits wanted, with just over a year of CFD and CAD modelling to optimise it.
“That triangular wing actually enables the UAV to glide, so long as the CoG is placed correctly, as we’ve found in flight experiments,” he adds. “Following aerodynamic and structural validations of the wing shape, we then had to figure out where to put avionics, batteries and payloads.
“That motivated us to design the blended-wing body in the centre of the triangle – which created an internal volume space for those enclosures to go, without disturbing the aerodynamic profile of the triangle wing – and add some extra wings in the left and right to compensate for the less aerodynamic central body.”
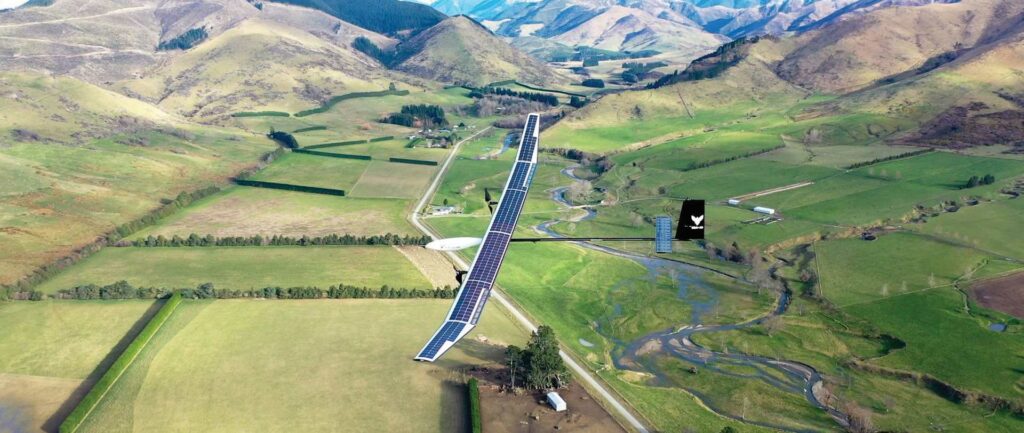
New Zealand-based Kea Aerospace’s Atmos Mk1 is a 12.5 m-wingspan stratospheric solar UAV; design of the 30 m-wingspan Atmos Mk2 will be completed in 2025 (Image courtesy of Kea Aerospace)
Through this design, every part of the 025 UAV generates lift. The 25 kg UAV will carry a payload of up to 10 kg, with gimbals installable in the nose, and Lidars and downward-pointing mapping (or oblique) cameras in the centre of the fuselage. From the batteries, FIXAR expects up to 3.5 hours of flight endurance, 300 km of flight distance and cruising speeds of 85 kph between charges.
“We’ve completed scale-model flight tests of the 025, and estimate 20-22% energy efficiency improvement over the 007 UAV. Making the 1 m-wingspan scale prototype was key to affirming that the triangular wing could be manufactured conventionally, from composites off of an aluminium mould,” Fainveits adds.
In June, the company went on to successfully display its full-scale, 3 m-wingspan prototype of the 025 UAV at Eurosatory 2024 in Paris, and it began its first flight tests in Montenegro.
Earth observation
Not many are aware that New Zealand is among the five most prolific countries on Earth when it comes to routine rocket launches (the others being China, Russia, the US and India). Much of that success comes from the activities of Rocket Lab, whose space-launch activities from its private orbital launch range in Mahia, New Zealand, have motivated great interest from New Zealanders in other critical future applications towards which its fast-growing aerospace resources could be leveraged.
Among the main interested parties is Mark Rocket, CEO of Kea Aerospace, formerly the seed investor and co-director of Rocket Lab. Rocket partnered its now-CTO Philipp Sueltrop to develop the latter’s idea for a New Zealand-based, high-altitude pseudosatellite (HAPS) aircraft, which could perform stratosphere-based services such as Earth observation, high-resolution aerial imaging, telecommunications, synthetic aperture radar surveys and upper atmospheric research testing.
“As we looked at the commercial opportunities of HAPS, and engineering and test-flying infrastructure we have here in New Zealand, we became convinced it was an ideal opportunity to develop a lightweight, composite-material, solar-powered aircraft,” Rocket recounts.
“So, three years ago, we gained the funding to found Kea Aerospace’s Kea Atmos Mk1 project, which is designed as a single-day, solar-powered stratospheric system, and next year we will start the design of the Kea Atmos Mk2, which will be a multi-month endurance platform.”
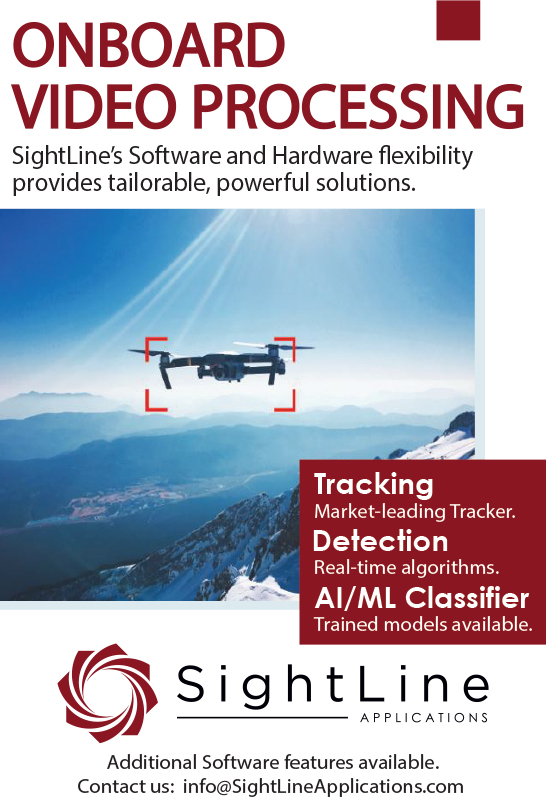
The Kea Atmos Mk1 is a 12.5 m- wingspan UAV with a single boom and tail, which takes small, 2-3 kg payloads into the stratosphere. Two are built as of writing, and in flight tests the stratosphere itself is targeted to be reached at the end of this year, when summer conditions in the southern hemisphere allow.
By contrast, the Kea Atmos Mk2’s wingspan is expected to be about 30 m long, with a 5-6 kg payload capacity (on top of its far greater flight endurance). Its engineering will be heavily informed by test data and lessons learned from the Kea Atmos Mk1 on how to optimise aerodynamic and structural performance in stratospheric environments.
“There’s a raft of different systems we’re looking to characterise and optimise via the Kea Atmos Mk1 test flights – communications, autopilot, composites – so it is prudent to split our development into two steps, where the Mk1 flies specific, small payloads while being a test platform for a lot of our proprietary technologies, and the Mk2 design builds on the Mk1’s data and successes,” Rocket says.
“We are taking an iterative approach that enables us to move quickly, test systems very swiftly, evaluate data concisely and keep moving. We learned at Rocket Lab how to prototype and optimise various safety-rated aerospace technologies rapidly, how to work well with solar and composite materials, and other important approaches to innovation that now serve Kea Aerospace well.
“And, working in New Zealand, which has all the infrastructure we need, but typically doesn’t have deep pockets for technology development, it really teaches you how to innovate on a budget.”
The Kea Atmos Mk2 design phase will be completed in 2025. Simultaneously, Kea will work on the Mk1’s ongoing flight tests and commercial projects for early adopters. An increasing majority of Kea Aerospace’s testing and development takes place at Tāwhaki National Aerospace Centre, a one-hour drive from the company’s facility in Christchurch.
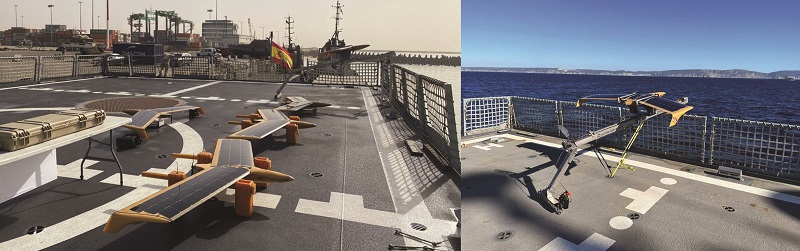
Tāwhaki’s facilities include a 1 km sealed runway, a large test corridor that extends out 100 km over the ocean and to 60,000 ft, and hangar facilities targeted to be completed in the next few months.
“That extensive airspace enables us to do a lot of flight testing, and being at the bottom of the Pacific Ocean just generally means we get really low air traffic, which, along with the coastal terrain and low population density, means we can carry out near-constant, exhaustive and lengthy flight tests of new technologies without incurring anything close to the risks or clearance paperwork needed in most other places around the world,” Rocket notes.
Maritime survey
While solar cells are critical for high-altitude UAV operations, they are also a useful addition for UAVs in lower-altitude, long-endurance applications as an alternative to batteries in maximising range.
The M5D Airfox UAV from Spanish manufacturer Marine Instruments serves as a key example of such engineering. This 4 kg, blended wing body electric aircraft achieves a 10-hour flight endurance through its combination of photovoltaics, battery energy and aerodynamics.
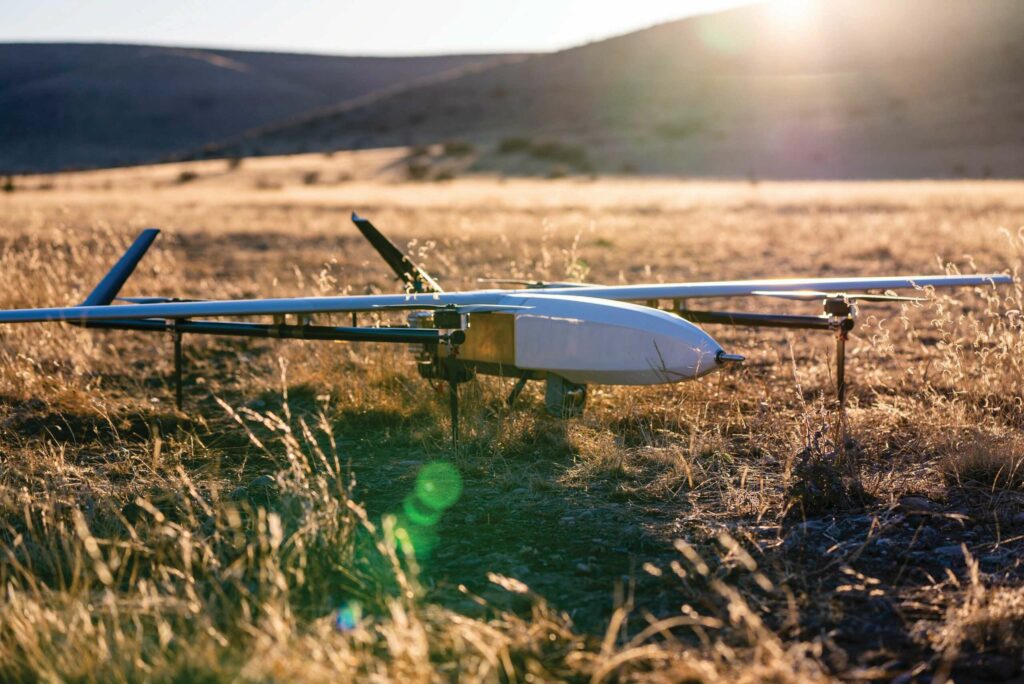
The VTOL-transitioning EchoMav Mk1 UAS flies using EchoMav’s EchoPilot AI autopilot, which integrates an nVidia Jetson computer to power AI requirements (Image courtesy of EchoMav)
As Javier Gravalos Belloc, business development manager public sector, tells us: “We first started developing this aircraft for the tuna fishery industry, because our core business lay in tuna fishing satellite buoys, and a UAV could provide coverage where the buoy could not. After COVID-19 made it difficult to interact with the fisheries, we moved over to the maritime defence market.”
Having transitioned from fishing industries to naval users, much like the Insitu ScanEagle (Issue 56), the end goal of the M5D’s engineering has remained the creation of something easy to operate, such that neither fisheries nor navy surveyors would need to become UAV engineers to use it. Hence, Marine Instruments has developed and manufactured its autopilot, avionics, communications systems, payloads and software in-house.
“The Spanish Navy has three OPVs [offshore patrol vessels], one of which is fighting piracy off the Gulf of Guinea, and there the Airfox’s 10-hour maximum endurance – 1.5 hour minimum – and its 18 nautical mile range are critical assets,” Gravalos Belloc adds.
“The airframe is built from a carbon-Kevlar airframe, which keeps it lightweight and easy to handle; that means it can be launched either by catapult or by hand. The M5D-Airfox also oversees fisheries monitoring along more than 7,000 km of the Spanish coast under a contract with the Ministry of Agriculture and Fisheries, and has successfully completed various naval exercises with the Spanish Navy, NATO and the US Navy.”
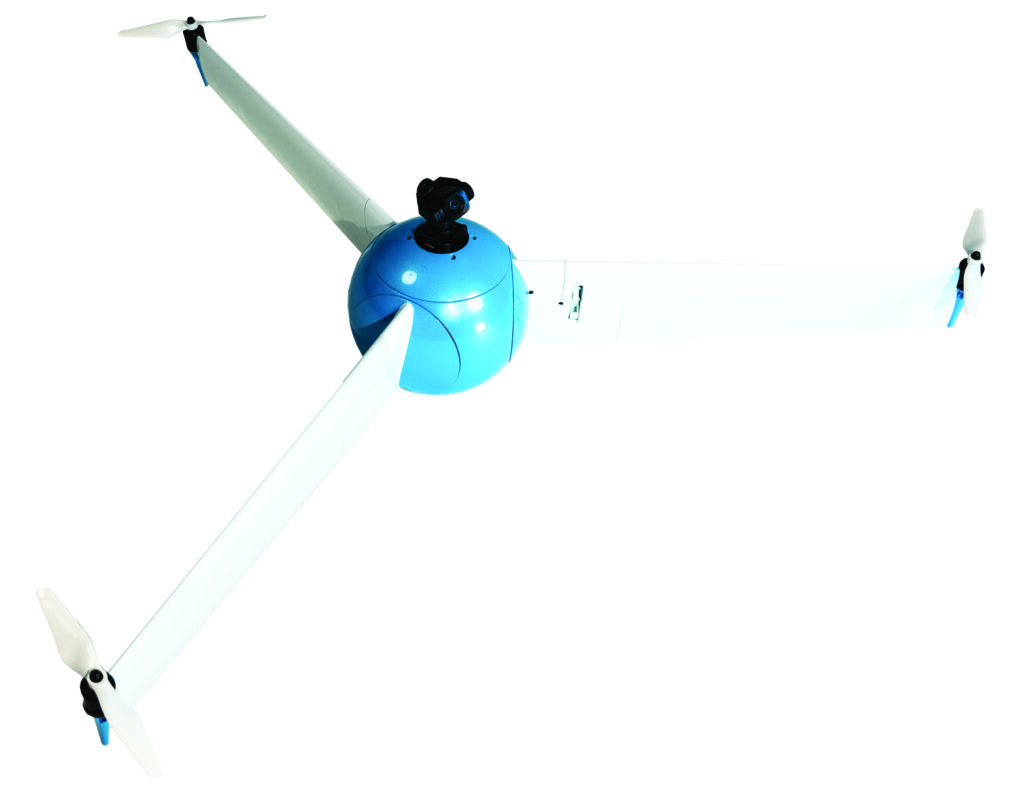
Public safety
For UAVs to excel in public safety applications, and other use-cases centred around stable surveying over potentially populated areas, they must be heavily optimised to hover in a safe, stable and energy-efficient manner, with conventional multi-rotors sometimes struggling to manage all three of these (not least the energy-efficiency part).
To hit all three targets, Angel Aerial Systems has engineered its flagship Trio UAV with three wings attached to a central fuselage (hub). Each wing has a rotor at the end and can be independently modulated to allow the aircraft to fly in three flight modes: VTOL, forward flight and “windmill mode.”
“In VTOL, it functions like a traditional, multi-rotor aircraft with the propellers pointing upwards to lift the Trio into the air. Once airborne, the aircraft ultimately transitions to a windmill mode, where the three wings spin around the hub, their rotors tilting sideways. The Trio takes the shape of a large propeller, with the rotors providing the necessary torque to spin it around its yaw axis,” says Dennis Krause, co-founder at Angel Aerial Systems.
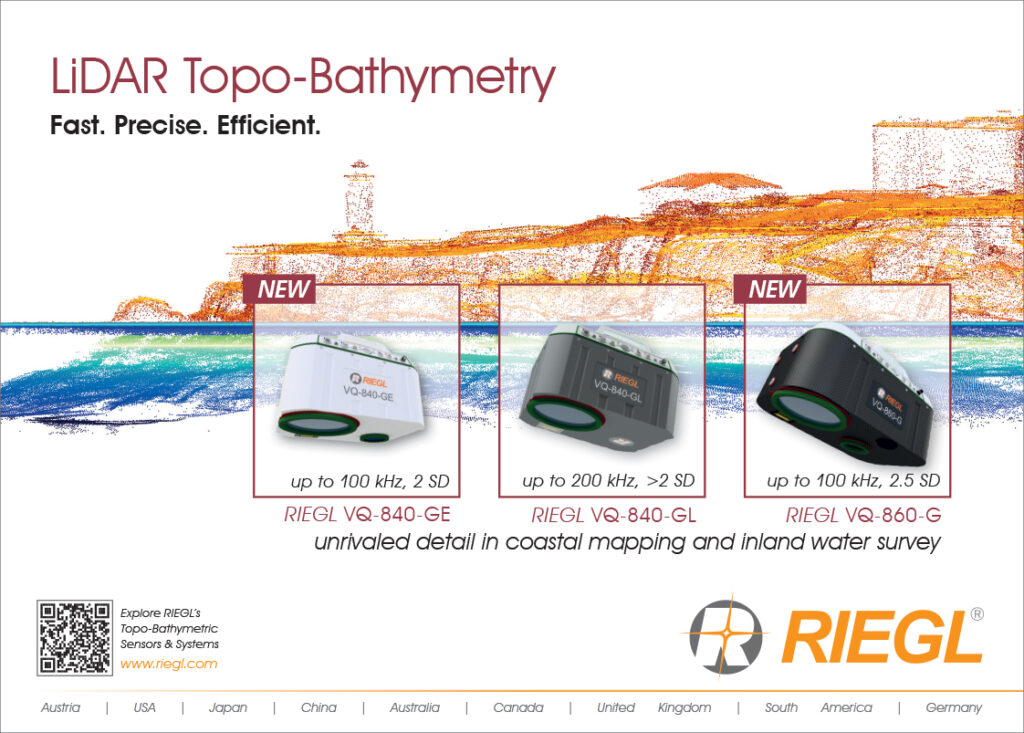
“In forward flight mode, the Trio pitches sideways from vertical take-off until it is flying horizontally. We’ve not finished optimising it for that flight mode, but when activated it uses two of its three aerofoils to generate lift, which gets it where it needs to be quickly and efficiently.
“Once spinning in windmill mode, all three aerofoils are generating lift, so the UAV’s rotor speed can drop significantly from the full thrust needed for VTOL, which, in turn, drops the power consumption by 80% compared with normal hovering.”
Through its energy-efficient windmill mode, the Trio achieves up to two hours of hover time, compared with 20-35 minutes of hover in a traditional multirotor of equivalent size. While this mode is active, a slip ring, along with a counter-rotating motor inside the hub, enables a bottom turret with a camera payload attached to remain static and stable amid the spinning wings above. This allows for the same quality of stabilised video output as a conventional multi-rotor, but over a longer period.
Defence & security
US-based EchoMAV’s MK-1 has been designed as a durable, long-range, VTOL fixed-wing aircraft that meets today’s requirements of Group 2, 55 lb (25 kg) UAS. It is engineered for simplified deployment using a hybrid power plant with on-board charging, quick refuelling, cost-effective maintenance and diverse payload integration, with a maximum operating altitude of 15,000 ft (4500 m). The MK-1 is constructed modularly, using aluminium and carbon-fibre, grey matte finish components throughout.
“Its design centres around being able to take off and land with very little space and no ground equipment, being able to disassemble into a single box, and being able to assemble and launch in under 10 minutes with no support equipment,” says Chip Coffin, aviation specialist at EchoMav.
“The wingspan is roughly 9 ft [2.7 m] wide, the fuselage is about 48 in [122 cm] long, and we have separate fins at the tailplane rather than a single, joined, inverted vee because this approach helps with disassembly and the ability to keep all parts compacted together in a case.
“We get about six to eight flight hours from the system’s 5.6 L fuel tank at cruise, and maybe 20 minutes after take-off the battery is refilled to 100% state-of-charge.”
Power comes from a rear-mounted, gasoline-electric power plant, combining a two-stroke engine running on 40:1 gas and pre-mix. The engine’s motor-generator (which mounts on the output shaft between the engine block and propeller) recharges a 9000 mAh, 12S battery pack, which gives a stable voltage bus for the four lift motors in take-off, with the UAV transitioning into horizontal flight at roughly 200 ft altitude, at which point the engine drives its pusher propeller for cruise.
The autopilot governing flight and VTOL-transitioning is EchoMav’s own EchoPilot AI. This consists of an 89 x 53 mm board, its design based on Pixhawk open-hardware standards, and integrating an nVidia Jetson compute module (either the Nano, TX2 NX, Xavier NX, Xavier NX TAA or Orin NX) to power machine learning, computer vision, and other AI or edge computing requirements.
Up to 100 TOPS of compute power can be installed for computer vision, machine learning, and more. Comms options include highly-encrypted telemetry and payload links up to 100 miles, via radios such as Persistent Systems’ MPU5, Silvus’ Streamcaster, and Doodle Labs’ modules.
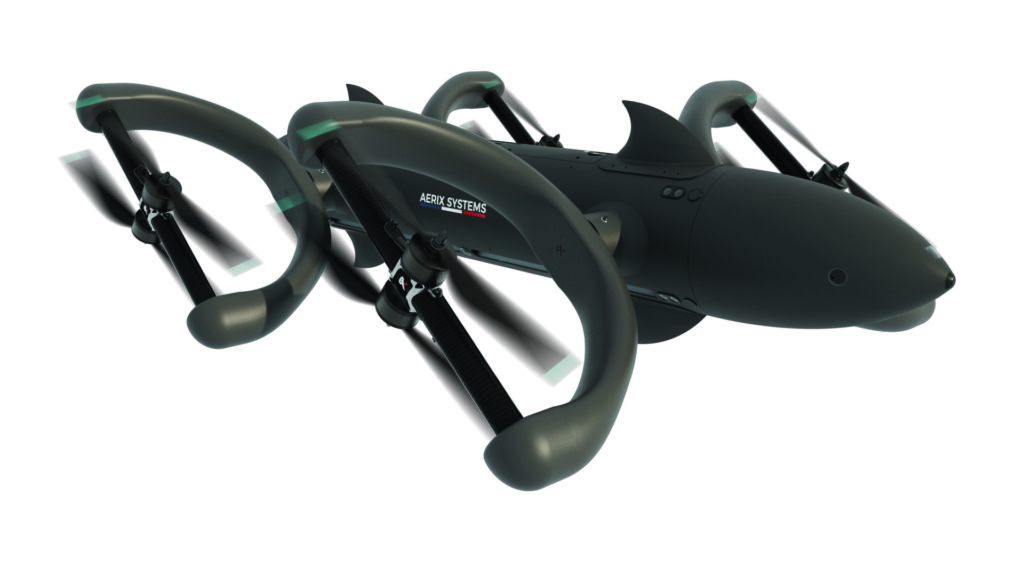
Counter-UAS
While Aerix Systems’ AXS-M1 UAV might look like a conventional multirotor at first glance, it actually integrates four omnidirectional rotors designed for driving 16 in (40.64 cm) propellers and enabling payloads of 3 kg to be carried for 35 minutes on the 1 x 1 m aircraft, with a maximum payload capacity of 10 kg.
Each arm rotates on an electric motor in the UAV’s horizontal (pitch) axis, and holds a shaft mounting a pair of coaxially oriented motor-propeller drives, with that shaft also electromechanically rotating in the UAV’s forward (roll) axis. The design is productionised as the AERIX T-16 propulsion solution, each producing up to 16 kg of thrust force and running on the supply voltage of 6S to 12S battery packs.
Through this arrangement of motors, the aircraft can transition quickly between VTOL, forward flight, stationary hover, reverse flight, and various different angles of flying or hovering as needed. It can also pitch, roll or yaw at a maximum rate of one rotation per second, moving into angles as requested by the autopilot (or remote pilot) accurate to 1o.
“We’ve developed the design and all the control software in-house to achieve and optimise this propulsion system, so none of it is open-source, but it is fully autonomous with very precise control,” says Hugo Mayounove, president and co-founder of Aerix Systems.
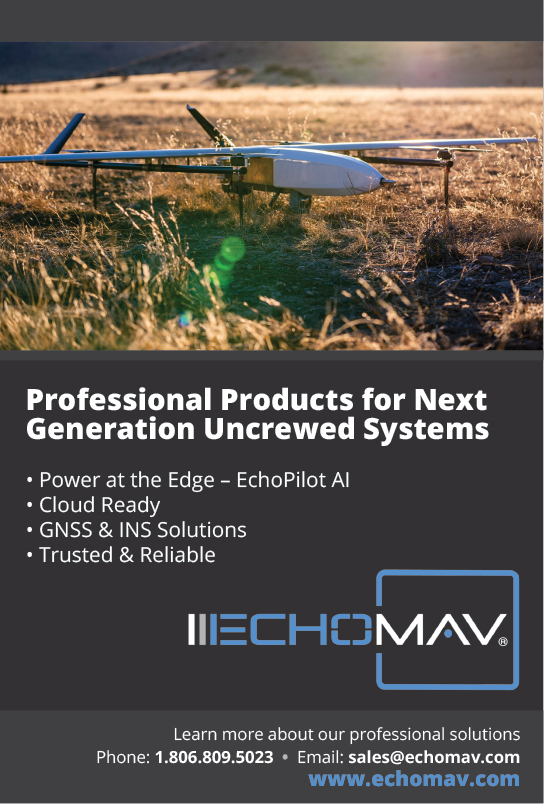
“We are principally mechanical engineers, so the five years of development we’ve put into our propulsion and UAV technologies were heavily focused on mastering the control laws necessary for correct autonomous operations of the omnidirectional rotors.”
Through its unique propulsion configuration, the AXS-M1 can achieve top airspeeds of 220 kph (also accelerating from 0 kph to 100 kph in 2.5 seconds) and turn with a radius of 1 m, thanks to a novel control architecture-managing for high acceleration and deceleration. It also resists winds of up to 100 kph during station keeping.
“Our business position is quite different from most other UAV manufacturers; we’re developing the airframe, propulsion arrangement and flight controller to give new aerial capacities to other drone builders or integrators,” Mayounove says.
“Our work is technically over by the time any mission begins. We let other manufacturers take care of integrating payloads, data links and other mission-specific systems. They just need to communicate with our system via software with CAN or I2C, or other interface types available, through to the propulsion system.”
The front and rear of the fuselage feature detachable cones, which can be customised and fitted rapidly for payload or antenna integrations, and the central part of the fuselage features 32 attachment points for the mounting of subsystems.
The AXS-M1 has been designed with specific operations in mind, such as 360o industrial inspections, or defence and security tasks such as counter-UAV or other counter-vehicle applications where the UAV’s agility over other mobile systems will be critical.
Summary
If configuring a UAV to specialise it for a particular application secures interest from long-term customers and operations, the next question on end-users’ minds will be what their long-term maintenance and infrastructure will look like. In many cases, their ordinary way of doing things may be unaffected, save for stocking parts inventories with spare servo actuators, propellers and the like.

However, non-VTOL fixed-wing UAVs will invariably require some kind of infrastructure for launch and recovery, be it a runway, a catapult, a net or similar. And, for any multirotors and VTOL-transitioning UAVs working in resident applications, such as logistics functions, or in industrial or transport infrastructure needing routine monitoring, some manner of specialised equipment for recovering, storing and recharging the aircraft between flights will be needed.
All this means that, rather than forgoing external infrastructure, the UAVs of the future will need a novel ecosystem of launch and recovery systems, designed to minimise overheads and labour burdens for users and planning authorities.
Those readers interested in such launch and recovery systems are encouraged to stay tuned, as we intend to publish an investigation into their state and evolution early next year.
UPCOMING EVENTS
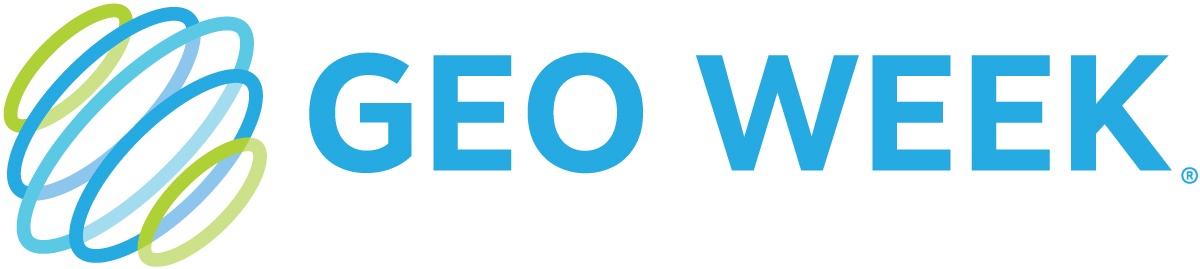
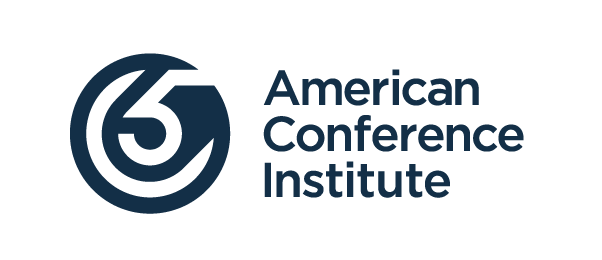
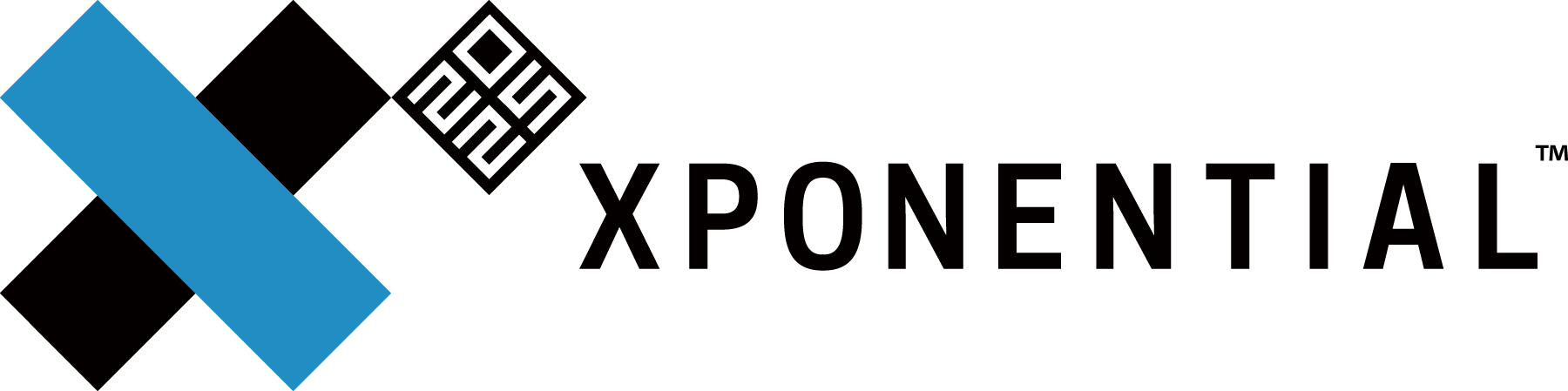
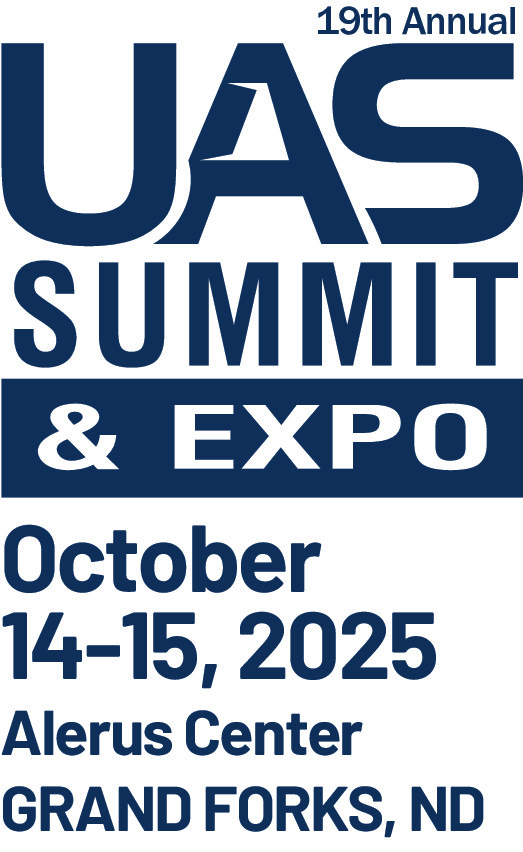
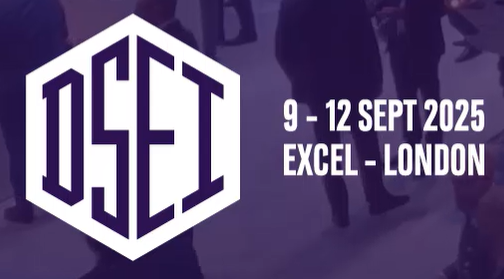
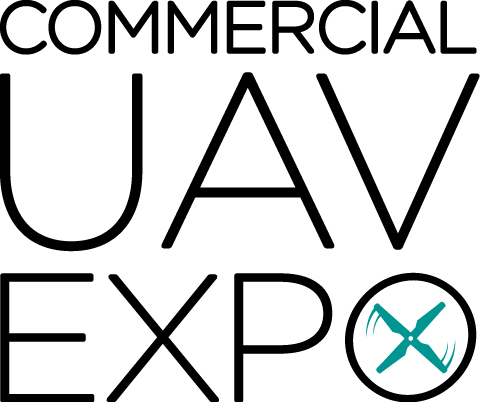
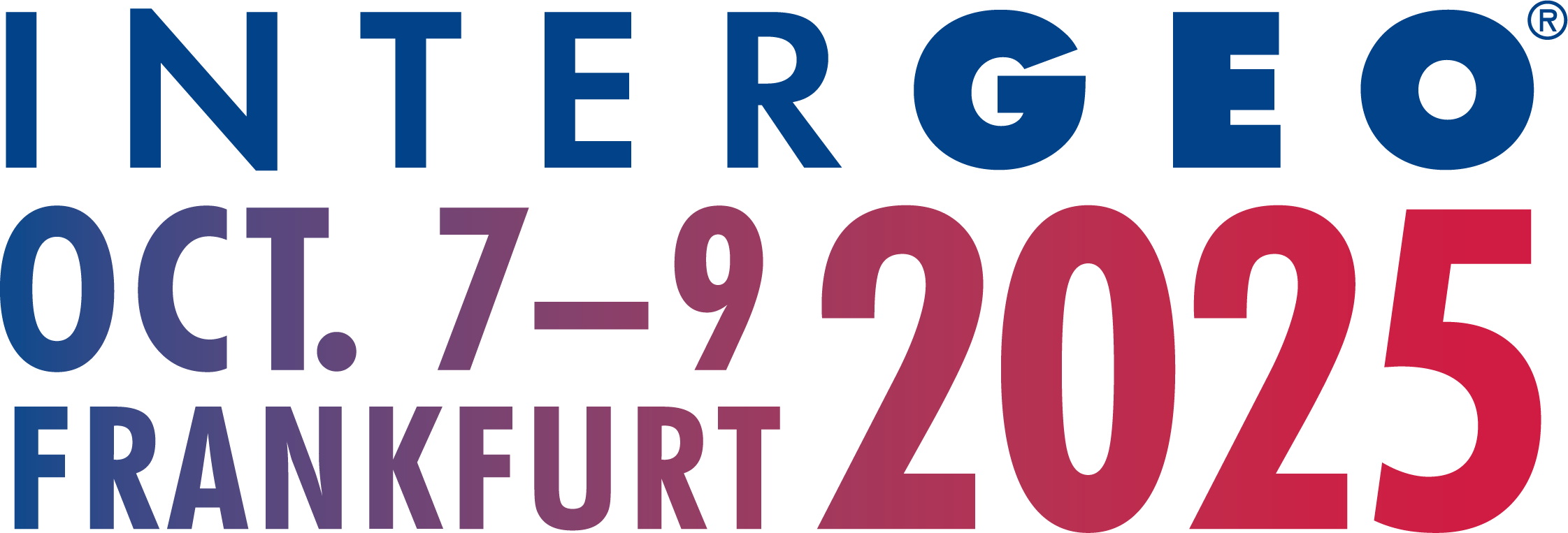
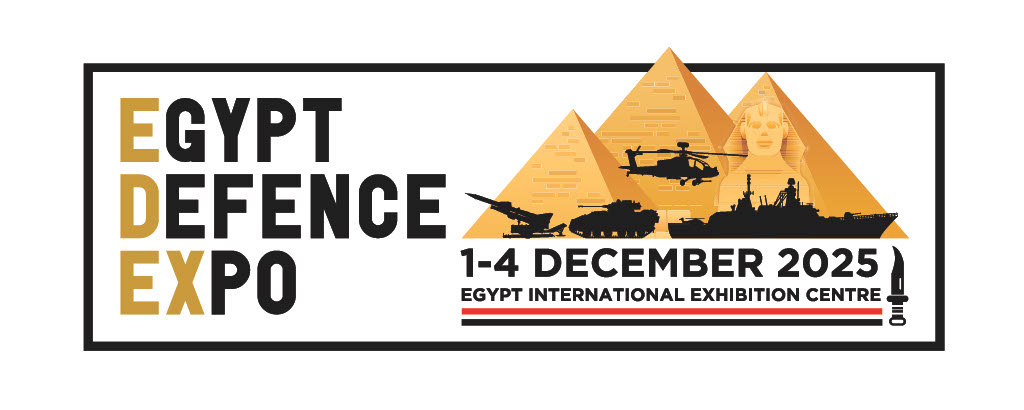
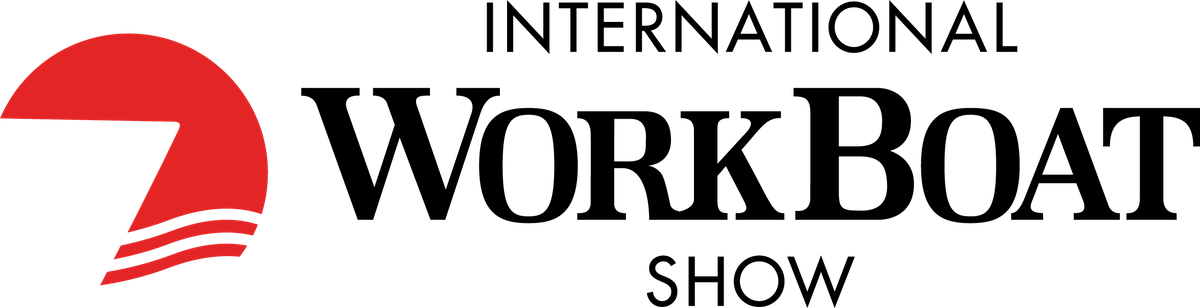
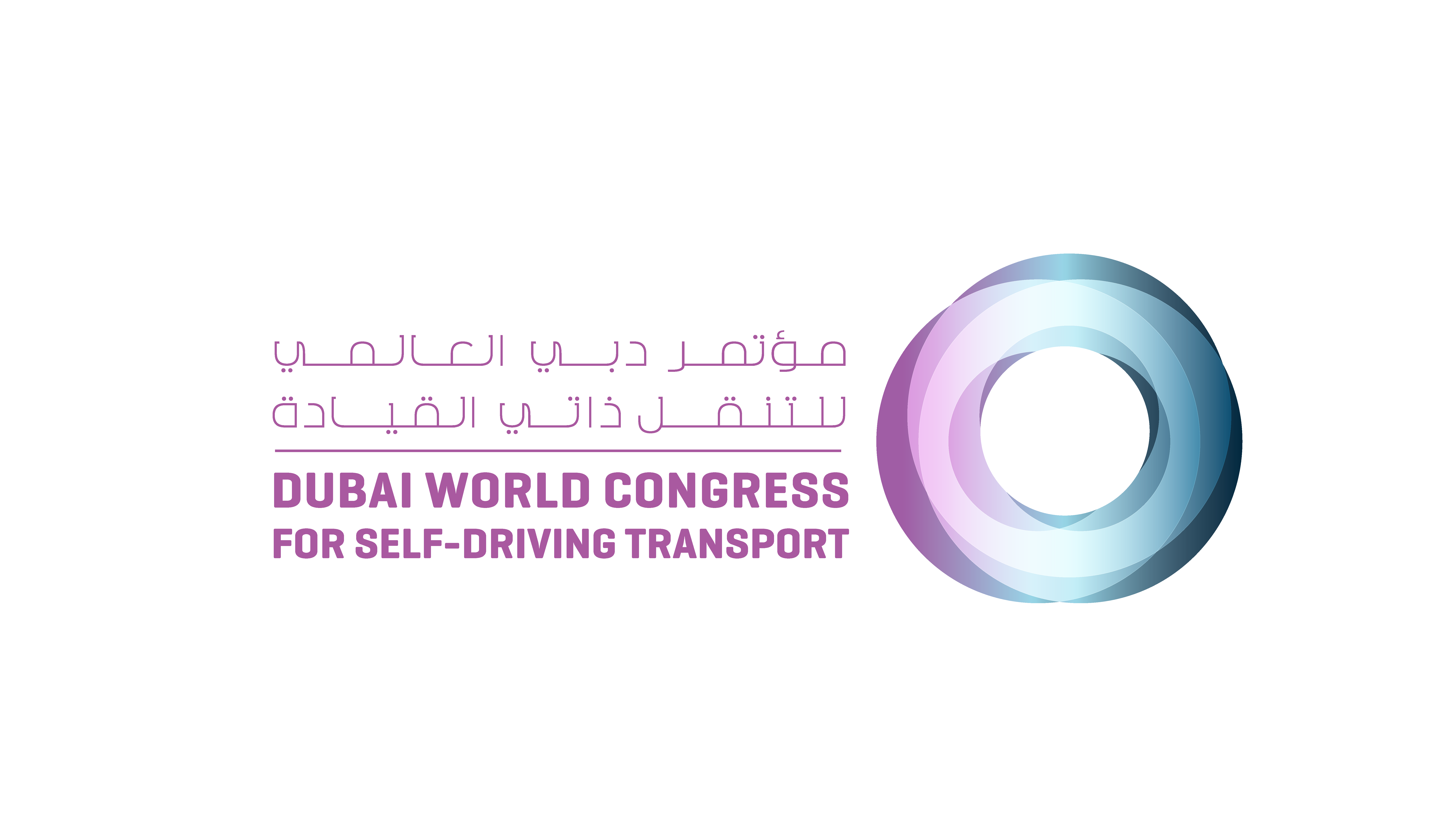
