Transponders
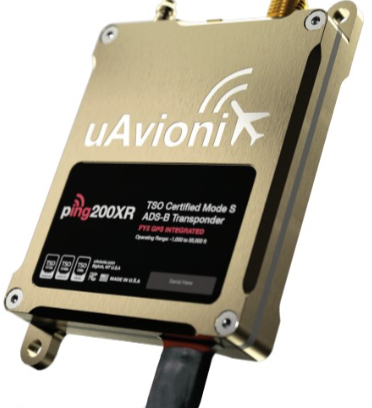
Rory Jackson finds out the latest in innovation, regulation and production of transponders for keeping UAVs flying safely in the skies
The past few years have seen a marked rise in demand for transponders, transceivers, and related solutions for the identification and air traffic management (ATM) of UAVs. Accompanying this is a general consensus across crewed and uncrewed aviation spaces that Automatic Dependent Surveillance-Broadcast (ADS-B) will surpass secondary surveillance radar (SSR) as the common standard by which all next-generation aircraft can be tracked, and collisions or excess traffic in the air can be safely avoided.
As a reminder, an ADS-B transponder works by periodically broadcasting its host aircraft’s GNSS position, altitude, velocity and identification codes; sometimes (but not necessarily) as a response to receiving an interrogation signal from ground- or air-based devices – a function typically referred to as ‘ADS-B Out’.
Through such information, which is often more accurate and useful than SSR data, ATM authorities can securely separate aircraft over radio instructions, and general or uncrewed aviation pilots can take safety-critical evasive action. Receiving such data is a functional capability termed ‘ADS-B In’.
Around 80% of crewed aviation already uses ADS-B, often through the use of a Mode 5, Mode S or Mode S Extended Squitter (S-ES) transponder (which integrate ADS-B Out functionality as standard). Arguably, the only problem with ADS-B Out is its frequency bands: it must be broadcast at either 978 MHz or 1090 MHz. These frequencies are also used by Mode A and C transponders, as well as radar and other systems, making for painfully crowded bands.
Hence, many anticipate that the older, less detail-heavy transponder modes will be disabled in time to free up their transmission frequency bands for ADS-B (such as military Modes 1, 2, 3 and 4, and civilian Modes A and C, with Mode S possibly included too).
For all these reasons, manufacturers seeking to build certifiable UAVs are seeking transponders configured for ADS-B (as well as remote ID, but only where US and European law requires it). Also critical are the efforts of transponder manufacturers in developing transponders with thoroughly minimised weight, size, power consumption and failure modes to fit within the greater need for efficiency and autonomy in uncrewed system airworthiness.
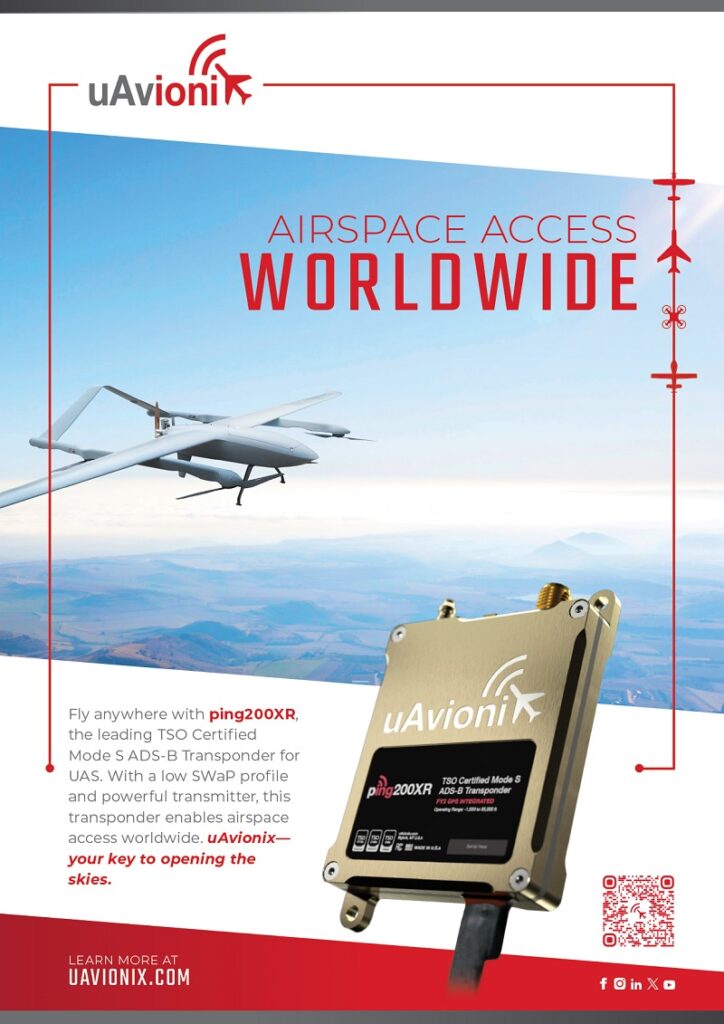
Innovations and investments in the UAV space are enabling the bulk production of transponders (including Mode S and S-ES compliant systems) smaller than smartphones that can broadcast scores of kilometres away with ten or fewer watts of power, as well as larger but no less power-efficient systems for broadcasting farther away in applications requiring hundreds of kilometres of traceability.
As well as devising architectures and leveraging new components for advancing SWaP optimisation, new transponder standards are emerging that will soon be key for certifying which units and companies meet the highest grades for safety-rated avionics. These certifications are regulated and granted by the FAA, EASA and other aviation authorities, including defence departments defining military certification standards for Mode IFF (interrogation, friend or foe) devices.
As of writing, DO-181F and the Technical Standard Order (TSO) C112e are the latest to define required performance standards on transponders, while DO-260C and TSO C166b govern ADS-B minimum performance and certification requirements.
On top of these, future airborne collision avoidance system (ACAS) regulations for mixed crewed/uncrewed airspaces now have FAA-defined groups of algorithms, created through work with MIT and Johns Hopkins University, and categorised based on the size, weight and configuration of UAV (particularly whether they are above or below 25 kg, crewed or uncrewed, and fixed-wing or rotorcraft design).
These will fuse ADS-B transponder data (labelling this ‘cooperative’ data) and radar or camera data (‘noncooperative’) into response formats that are stable and predictable as regulators like them, because simply installing cameras into every vehicle and trusting them to duck below or dodge other vehicles would be a haphazard and unsafe way of organising the world’s airspaces.
All of this is driving the design evolution across transponders, being formed through discussions between regulators and leading manufacturers, so that integrating such products can help reduce the barriers to routine flying for high-end UAVs.
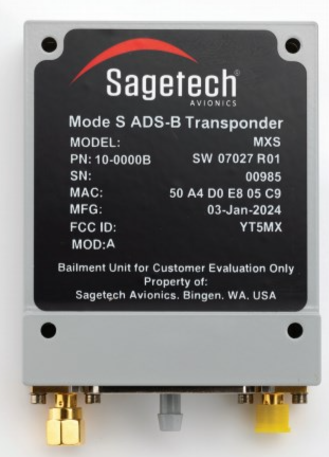
Anatomies and ecosystems
The components of a transponder-type device can be few or many, depending on the kind being considered. If one thinks principally of an ADS-B Out solution, whether of higher or lower power, then one will find, at a minimum, a highly sensitive receiver for detecting low-power ADS-B signals from tens or hundreds of kilometres away, and a high-power transmitter for delivering such signals over such distances on defined frequencies.
Just as important is an integrated circuit for deciphering received signals, and requesting the necessary onboard data for generating and communicating a signal of its own. As transponders are required by standards to respond to signals or interrogations within extremely short timespans, to opt for CPUs that run software would be too slow or risk losing the signal in an iterative loop, so microprocessors and field-programmable gate arrays (FPGAs) typically form the high-speed, low-complexity ‘brain’ of a transponder.
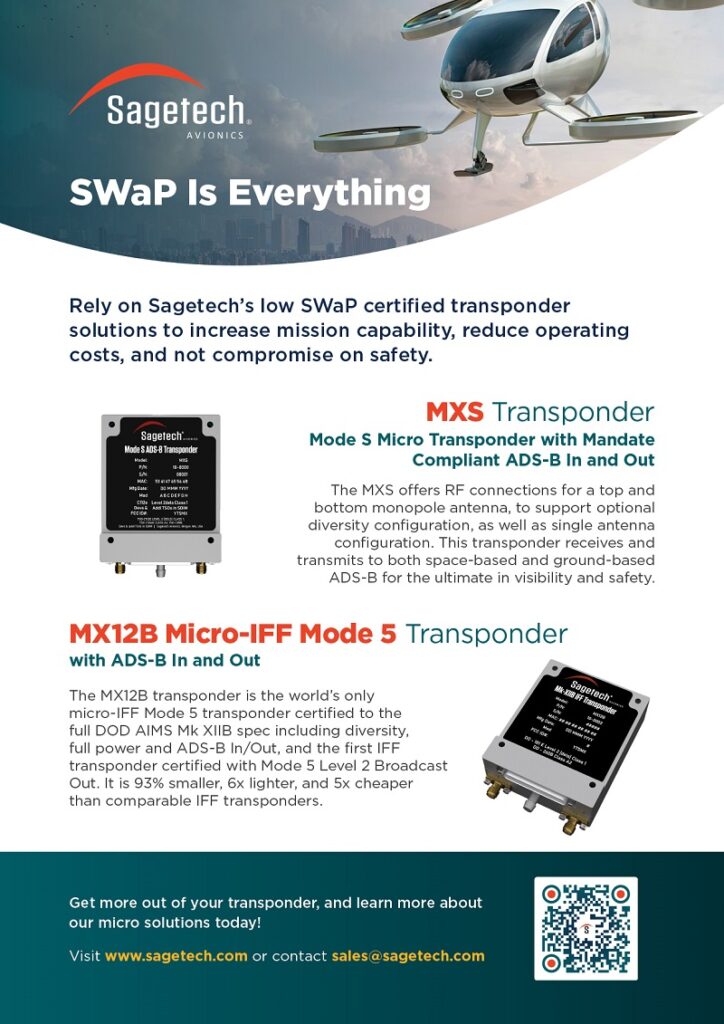
Additionally, some power-conditioning systems must be installed around these components to minimise variations from the input voltage reaching the transmitter, receiver or microprocessor and damaging them. For instance, some high-end transponders integrate capacitors to store power over time that exceeds the troughs of the transmit cycle, so when such cycles peak – meaning an ADS-B signal must be amplified to full; perhaps 500 W for a fraction of a second – the stored power can be released to satisfy the transmitter’s load.
A growing number of transponder-type solutions made for the UAV space now integrate GNSS receivers to create a more complete solution, which can be particularly crucial in ensuring both a UAV’s transponder and its GNSS source fit TSO-specified minimum standards on precision, accuracy and integrity.
Simpler than these are interrogators (which ping out requests for ADS-B information from in-range aircraft) and ADS-B In receivers. While not technically transponders, transponder manufacturers are increasingly producing both. The former are key for military users in distinguishing friendly from non-friendly aircraft, and will likely constitute part of future ACAS infrastructure. Meanwhile, the latter are anticipated by some to be used even more prolifically than transponders among UAVs over the next few years, because ADS-B Out still lacks the breathing room of a dedicated frequency band.
As certified transponders will increasingly need to transmit 200-300 km away, it would greatly alleviate band congestion to require that some UAVs – particularly smaller, Part 107-sized aircraft such as delivery drones working at lower altitudes, where crewed aircraft will be rarer – simply receive ADS-B data from other aircraft (specifically bigger, more expensive and more imposing aircraft that genuinely need to be tracked) and thus give way to them as and when they come near, rather than have every single UAV fill up the airwaves.
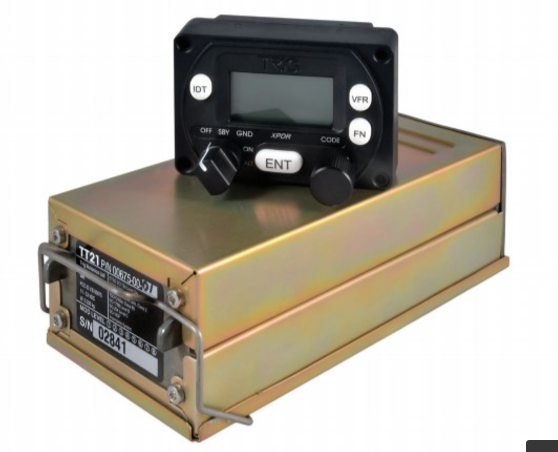
Specific advancements
For those certified UAVs in need of robust, SWaP-efficient transponders, a number of improvements across these components are being targeted and leveraged by system makers today.
Much of this revolves around making the microprocessor’s job easier, and ensuring the transponder works in harmony with other systems. For instance, selecting or designing a transmitter with very robust masking, such that it transmits with extreme precision on the 1090 MHz frequency, and with minimal (if not zero) out-of-band transmissions, is critical.
One reason is that spilling out of band could cause transmissions to not be recognised by receivers. Another is that as the transmissions slip closer to, or even past, 1100 MHz (1.1 GHz), the secondary harmonics encroach on the 2.4 GHz ISM band. As crowded as 1090 MHz is, such harmonics could then interfere with and smother uncrewed system C2 links, among countless other systems.
Conversely, high-end transponder manufacturers are discretely managing all of the filters across their receivers, such that out-of-band signals can be rejected and relevant signals can be recognised for the precise timing of their pulses, even when multiple transmissions are coming in.
Not doing so risks copious interference for transponders from unwanted signals, or the device failing to recognise when and how it is being interrogated for its ID and position data (and failing to respond in good order), along with other issues that make it harder for the microprocessor to do its job.
Fortunately, chips are coming in smaller packages with higher processing power, enabling more internal space for lengthier and more complex transmit/receive arrays. These include highly power-efficient system-on-a-chip (SoC) devices that integrate microprocessors and FPGAs directly (rather than having the two sit as separate components inside a transponder), eliminating the need for a comms bus between them that could form a bottleneck in the transponder’s functioning, enabling far more rapid movement and storage of data.
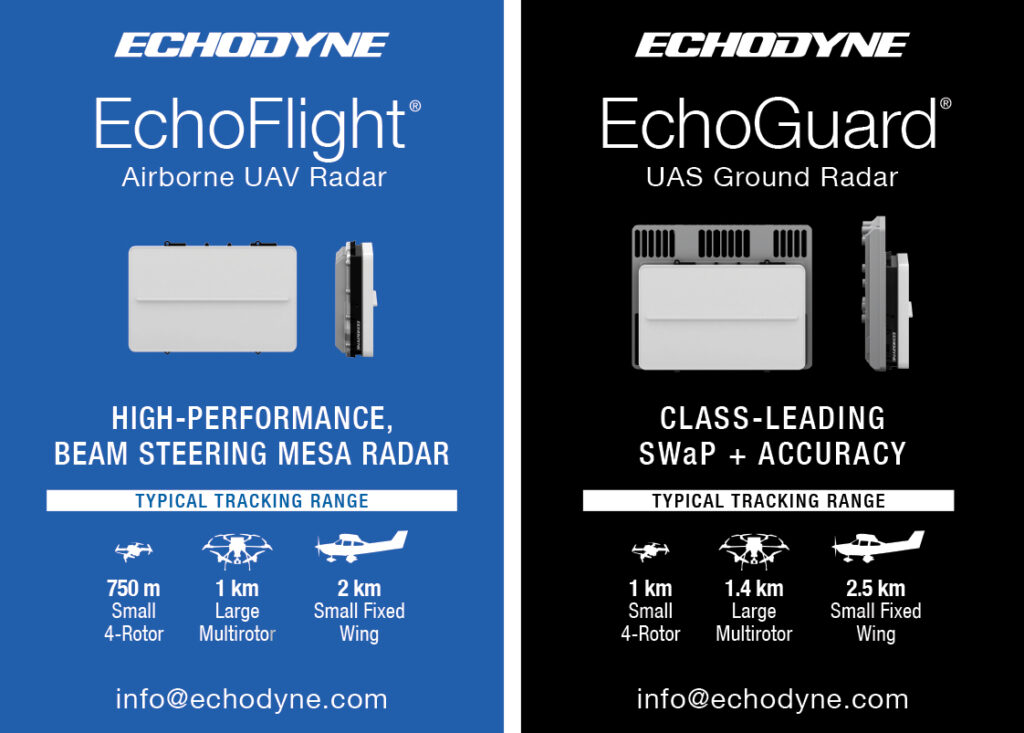
With device manufacturers increasingly leveraging SoCs, next-generation transponder designs may run on multi-core processors, probably still in SoC formats but allowing the separation of cores to allocate functions between them. For instance, one core could run an ACAS algorithm, another could run ADS-B functions, one more could perform inter-protocol translations and another could run encryption if needed; such separation could be key for proving design and operational assurance levels to aviation authorities one day (by preventing crosstalk, lag or other issues caused by relying on a single core).
Also increasingly critical are integrations of high-quality GNSS receivers and pressure altitude sensors into transponders, both of which continue to miniaturise to the benefit of manufacturers. Choosing these and all other components must be done with absolute certainty, as once a design is certified, it cannot be significantly changed, lest the developer risk losing their certification.
This means not changing a component or any aspect of the hardware configuration, so ensuring secure supply chains of certifiable components is a vital part of modern transponder development. From a software perspective, it can merit a bare-metal engineering approach, by which the lowest levels of algorithms – down to programming languages and toolsets are controlled in-house – so the transponder software engineers are not beholden to third-party tools (and, more seriously, layering-in third-party programming libraries or similar inputs can interfere with certification if they themselves are not certified).
Additionally worth noting is the growing integration of cryptography modules into Mode 5 IFF transponders. In the US, this means using KIV encryption modules certified exclusively by the National Security Agency (NSA) (and no UAV transponder companies are authorised to produce KIVs at present), so that encrypted transmissions can be received by the transponder, and then processed, validated and decrypted by the KIV, and the KIV can send data back to the transponder for it to transmit.
This entails a very narrow timing window, meriting extremely tight integration between the two parts, and the standards for doing so come with a very high level of requirements, covering not only timing but validity, bandwidth and other parameters that the transponder manufacturer must mind.
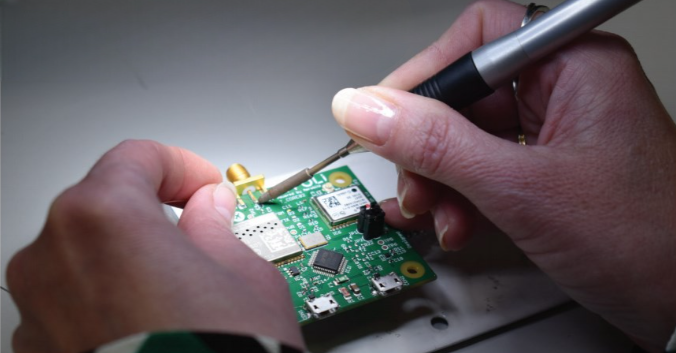
Engineering process
Developing a new transponder, be it to meet a new standard or fit a customer’s spec, starts with defining system requirements, such that concept transponder architectures can be tuned with the right components, firmware, measurements and so on.
Transponder engineers therefore pay close attention to the letter of the law from regulatory standards, as software and parts tailored to do anything outside of certification requirements may wind up interfering with other communication links or causing faults with their own timing requirements.
Once this onerous planning process is completed, design simulations can be run to define the schematics and engineering tolerances of the first prototype’s hardware, taking account in such modelling for how the transponder will perform electrically, electromagnetically, and thermally within the possibly cramped and harsh environment internal to a UAV. As with any avionics, care can also be taken in CAD and FEA simulations to check that the board and enclosure layouts tolerate shock, vibration and outside sources of EMI, as well as certification requirements.
Software development can be run in tandem and this typically moves faster than for hardware. Transponder software engineers increasingly use development boards based on past product iterations, as components reasonably similar to that on the expected prototype provide an adequate environment for programming ADS-B or related software to new standards. Such software will routinely be run in simulations to affirm the future transponder’s ability to understand received signals and respond appropriately with the correct ADS-B information.
Then, parts can be surface-mounted on board assemblies to build prototypes, with several iterations often taking place with significant hardware and software testing to define redesigns of system architectures and the contents of firmware patches. As discussed, a certified product cannot be significantly changed once released, so any mistakes cannot be patched out post-release, as they are in many other products.
The route taken to get to that point can vary between companies. Some will start with a ‘breadboard’ design, which is a PCB several times larger than the deck of cards-sized transponder commonly made for the UAV space. With so much room on a large board, the functional pathways and lines of code needed to meet performance and safety requirements are defined and then shrunk down to fit the desired form factor.
However, breadboard development yields a high chance of hitting a wall in how far the prototype can be miniaturised, as the software and architecture have been constructed using a certain measure of processing power, hard-drive space and bandwidth, and other parameters across the board.
So, transponder developers increasingly impose a hard and tight limit on the form factor of their first prototype, possibly allowing a few millimetres of expansion when unavoidable. Going forwards, developing and certifying a GNSS device small enough to fit within such limits will become an expected duty of manufacturers to guarantee that UAV operators can document in their aircraft when seeking certification to fly routinely and beyond visual line of sight (BVLOS).
Also being engineered into some transponder architectures are mutual suppression buses. These are a common system in crewed commercial and military aircraft, by which multiple onboard L-band transmitters can arbitrate and take turns to transmit (during which the other systems’ receivers can stop listening for a measure of milliseconds).
Naturally, as UAVs integrate mounting numbers of L-band radios for ADS-B, GNSS, mobile networks, multimedia broadcasting and even C2 data links, all of these could interfere with each other while operating near-simultaneously onboard. So, including mutual suppression buses in transponder designs (guided by published standards on such systems) could become as important to UAV certification and safety as correct placements of antennas and ground planes.
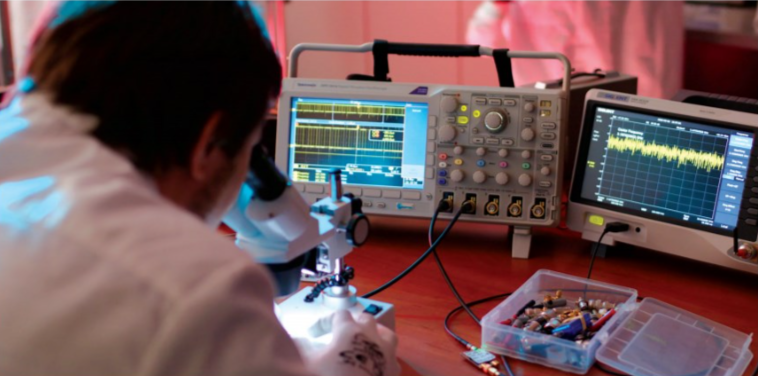
Rigorous testing
Once a prototype has been iterated enough times that the transponder manufacturer is confident in its compliance and performance, it can enter rigorous functional tests to unearth bugs through hardware-in-the-loop testing, and ensure the basic data processing and that transmit/receive tasks can be performed correctly.
On top of this, environmental testing (compliant with DO-160 standards) is critical for revealing that further bugs remain hidden during operations in Goldilocks conditions and lets engineers program or calibrate them out. While the development of software often outpaces that of hardware early in the engineering process, the last hundred or so tweaks tend to be software changes.
This includes extensive shock and vibration testing to ensure the physical exertions of UAVs at high speeds, catapult launches, dynamic manoeuvring and so on will not cause capacitors to crack or housing lids to come loose. Environmental chambers will simulate extremes of pressure altitude, humidity and temperature, with the standard laying out many further tests, including waterproofing, salt and fog resistance, dust ingress and lightning susceptibility (the latter can involve linking a transponder to a copper plate and running 600 V into it to simulate lightning).
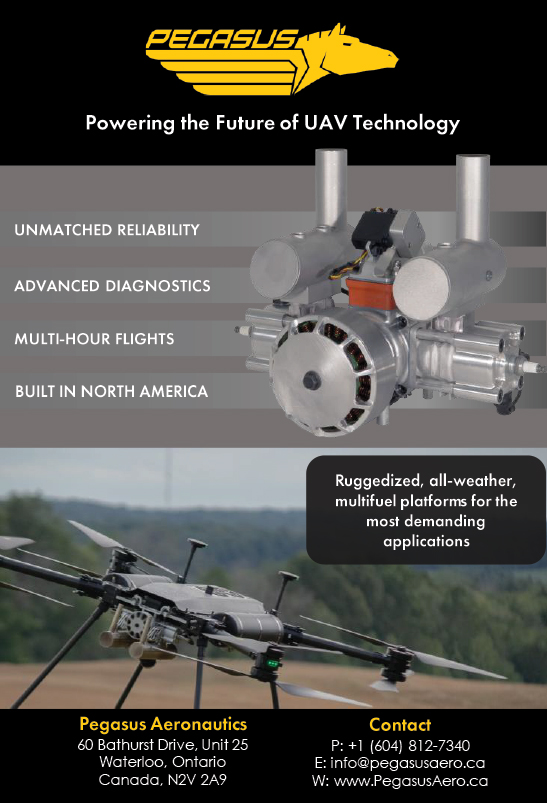
More transponder-specific testing equipment may naturally include anechoic chambers to precisely gauge transmission and reception accuracy and integrity when combined with an antenna. On top of this, GNSS simulators can pose a great expense to manufacturers (hence not all transponder makers have one), but effectively emulate satellites from the GPS, Galileo and other constellations (with signals either conducted to the transponder via a cable or radiated throughout a test facility).
These simulators enable scenarios for satellite movement and visibility (relative to the transponder) to be programmed and played out, thereby showing how well a transponder continues performing in the face of GNSS variations, and allowing for calibrations to compensate for such changes.
Rarer still are KIV emulators for IFF transponder testing. These cannot be purchased and can only effectively be made by reverse-engineering the interfaces for a KIV, although non-NSA encryption would still have to be used to measure how a transponder performs amid cryptography duties.
As unusual as these testing and simulation systems may sound (among avionics testing), tests for transponders must become even more wide-reaching to ensure their consistent functioning in all environments that UAVs may fly in.
One firm has discovered a bug in its ADS-B receiver that occurs only when flying over the Null Island coordinate at 0°N latitude, 0°E longitude (not a real island). While that might never have actually resulted in a functional safety issue, it is indicative of the breadth of measures that high-end transponder companies must try to undertake to prove the robustness of their engineering to aviation authorities.
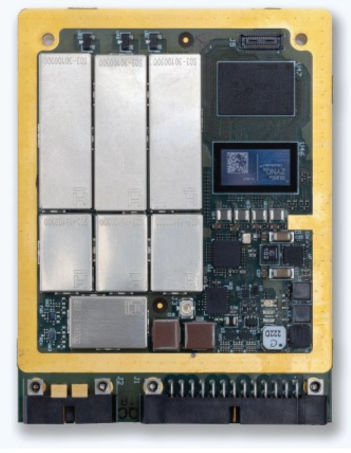
Manufacturing
With certification and batch manufacturing of UAVs taking off, safely critical avionics such as transponders are now being produced in facilities geared up for TSO-certified volume production (company owned factories and third-party contractors, depending on the organisation).
To make a certified transponder requires undergoing frequent audits by regulators to ensure production processes, quality control, equipment, employee training, and traceability of tools and raw materials are all compliant with standards. Typically, this means every input part – chip, capacitor, PCB, radio, connector, fastener and so on – entering the production facility must be inspected.
At the higher end, some manufacturers will use optical profilometers for contactless metrology, by which they can gauge uniformity between components in a batch, down to sub-millimetre details such as improper surface treatment on a housing or board component, and either clear or reject them for use in production.
It is increasingly common that each part across inventories (no matter how small or how many of them there are) will be marked with some kind of barcode, QR code or serial code to ensure traceability. In certified aerospace, if a defect should ever be discovered in a specific batch of connectors, chips, resistors and so on, the manufacturer must be able to authoritatively state which transponders contained units from said batch.
Following this will be different combinations of manual and automated processes (with automation increasingly the norm): robotic picking and placing of chips and capacitors, soldering of board-mount components, matings of boards together, mechanical assemblies of enclosures with mated boards, and possibly some burn-in testing to verify that a board has been assembled and flashed into good working order.
The enclosures themselves will often be CNC-milled from aluminium or a similar metal (and coated) to extremely strict tolerances. While a transponder’s housing might seem its most unsophisticated component, it is in fact critical to creating a Faraday cage about the inner components and separating electronic circuits from each other. It also serves to contain or route the considerable heat output of the amplifier to a prudent location (so customers can then mount that to the skin of the aircraft for air cooling).
Each step of the way, processes are tightly controlled with production data logged to show aviation authorities that manufacturing, assembly, programming and testing are executed in compliance with approved guidelines for making airworthy transponders.
At the end of a production line, further metrology validates the quality to which the transponders have been assembled, including 3D vision and laser scans of surface-mount component arrangements and solder quality, and robotic probe tests of voltages and resistances across boards to check for connectivity or power-safety issues. Calibrations can be critical here for ensuring correct power levels throughout transponder-board assemblies.
Where quality is found to be lacking, a production house with skilled technicians will resolder or otherwise remanufacture the offending transponder under microscopes to the desired standard until it passes validation, rather than dispose of the system and generate waste.
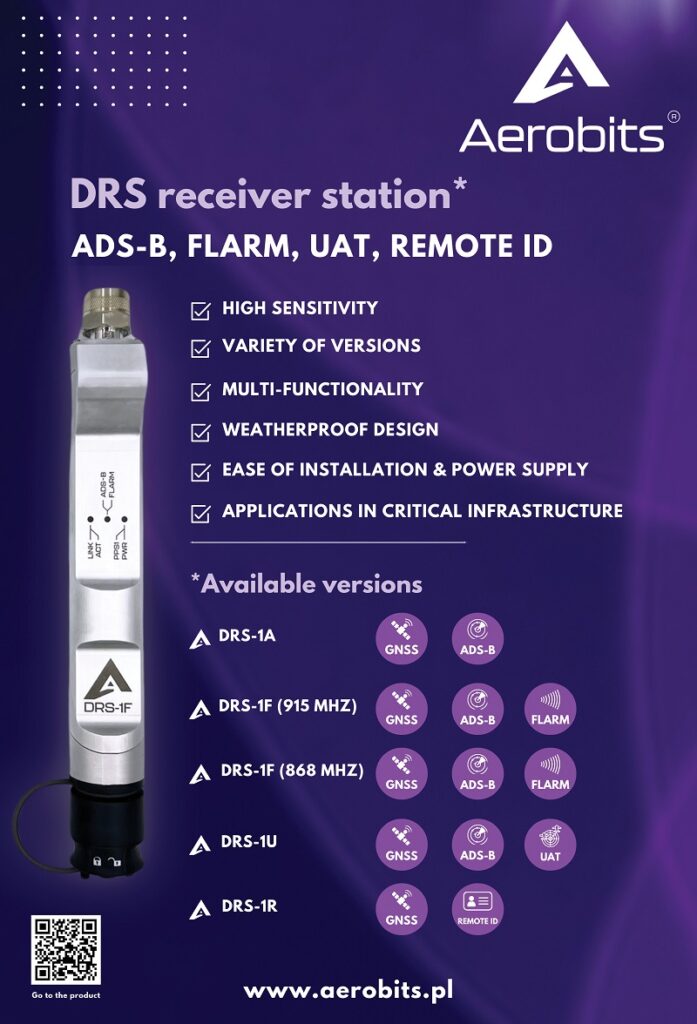
Future moves
As future requirements for ACAS in uncrewed aviation develop, the minimum components and functions of a transponder will expand to encompass certified GNSS, pressure sensing or encryption (for military integrators) components. However, interrogators will form a critical part of the mix within the next few years, so that transponders can identify when another UAV’s GNSS is being spoofed (when time-of-flight data does or does not correspond with the ADS-B data on the position and heading being received).
Future conversations will merit deep-dives into how higher-end interrogators are made, how transponders may integrate them while remaining SWaP-optimised, and how interrogations may be performed without congesting airspace.
While it may feel to the casual observer that regulators’ standards and TSOs come out so often that transponders will need to change and update all the time, the reality is that standards on transponders themselves – ACAS standards (and how those might build upon transponders) notwithstanding – are expected to stay as they are for many years to come.
Future technical updates on transponders will therefore likely focus more on advancements in the wider ecosystem of uncrewed air traffic safety, covering devices for GNSS, receivers, transceivers, and conspicuity, and how these may be tailored for the differing requirements of small versus large UAVs, as well as fixed-wing versus rotary uncrewed aircraft.
Some examples of transponder manufacturers and suppliers
AUSTRALIA
Microair Avionics | +61 7 41553048 | www.microair.com.au |
GERMANY
Air Avionics | +49 6224 98 96 999 | www.air-avionics.com |
ITALY
Leonardo | +39 063 24731 | www.leonardocompany.com |
POLAND
Aerobits | +48 500 501 305 | www.aerobits.pl |
SPAIN
Indra | +34 914 805 000 | www.indracompany.com |
UK
Trig Avionics | +44 (0)131 449 8810 | www.trig-avionics.com |
USA
Avidyne | +1 781 402 7400 | www.avidyne.com |
BAE Systems | – | www.baesystems.com |
Collins Aerospace | +1 704 423 7000 | www.collinsaerospace.com |
Harris Corporation | +1 321 727 9100 | www.harris.com |
Honeywell | +1 602 365 3099 | aerospace.honeywell.com |
Kratos Defence | +1 858 812 7300 | www.kratosdefense.com |
L3Harris | +1 623 445 7040 | www.l3harris.com |
Micro Systems | +1 850 244 2332 | www.kratos-msi.com |
NextGen UAS Transponders | – | www.nextgenuastransponders.com |
Northrop Grumman | +1 847 259 9600 | www.northropgrumman.com |
Raytheon | 1 781 522 3000 | www.raytheon.com |
Sagetech | +1 509 493 2185 | www.sagetechcorp.com |
Sierra Nevada Corporation | +1 775 331 0222 | www.sncorp.com |
Thales | +1 240 864 7000 | www.thalesdsi.com |
uAvionix | +1 844 827 2372 | www.uavionix.com |
UPCOMING EVENTS
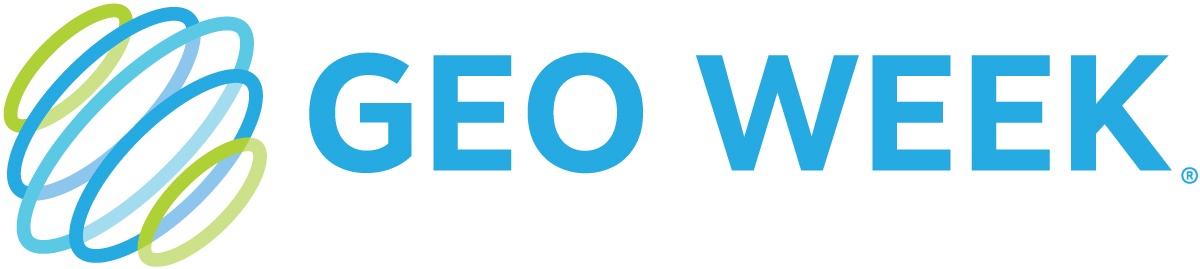
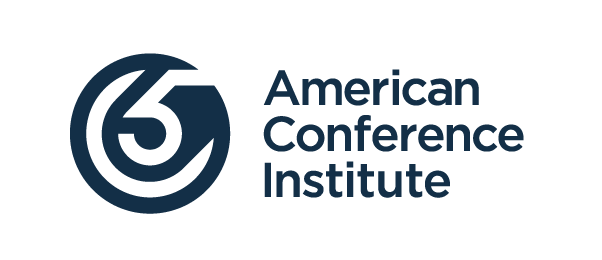
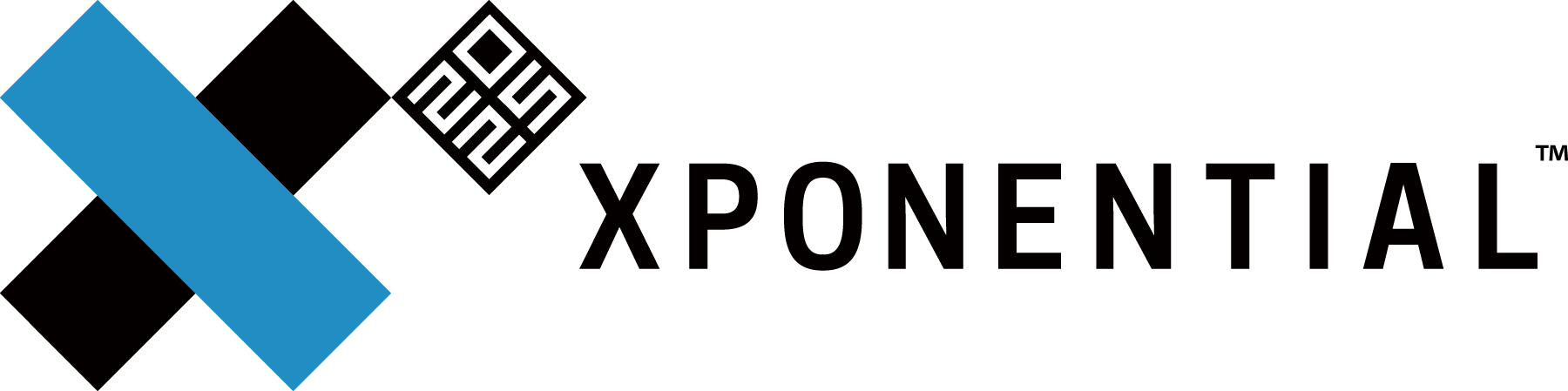
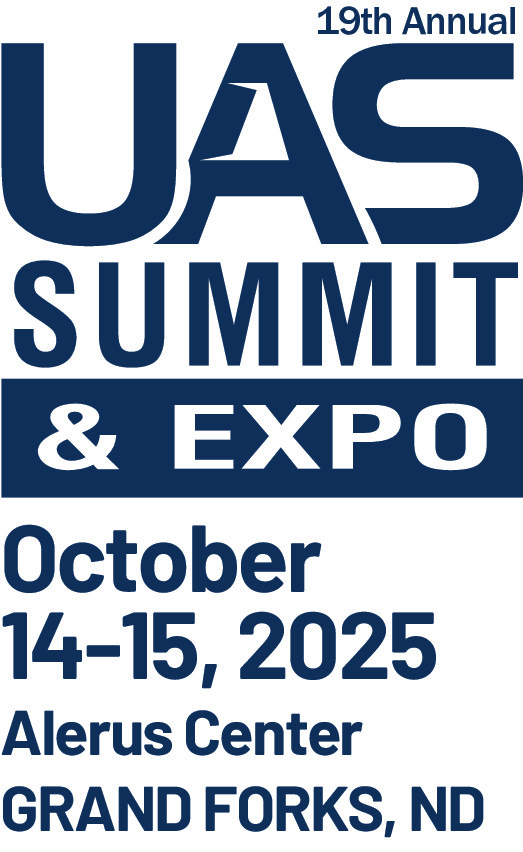
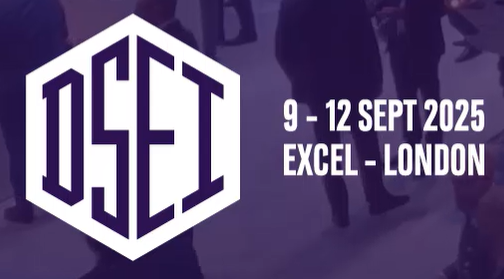
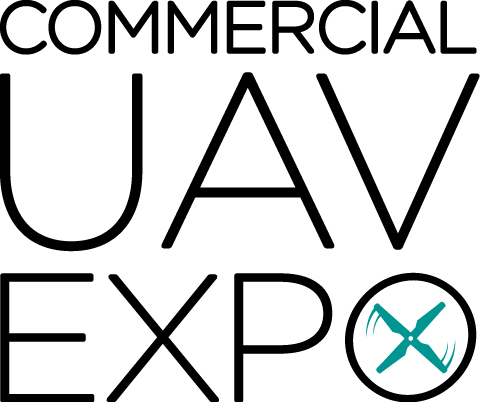
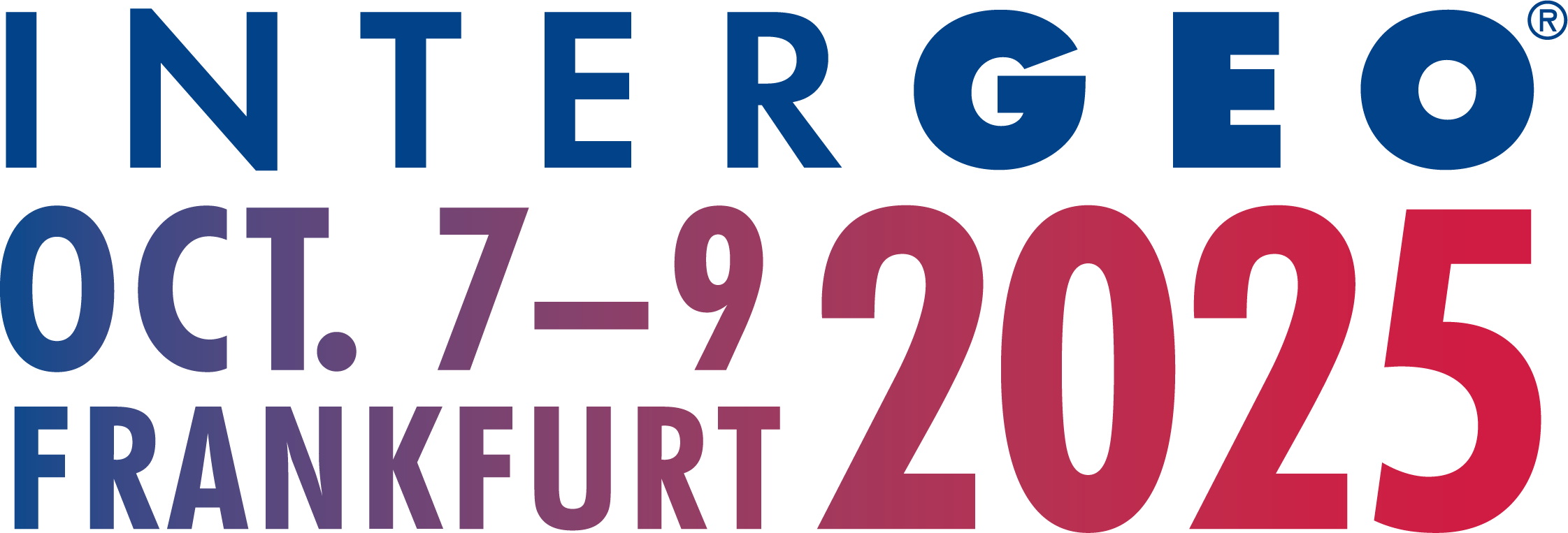
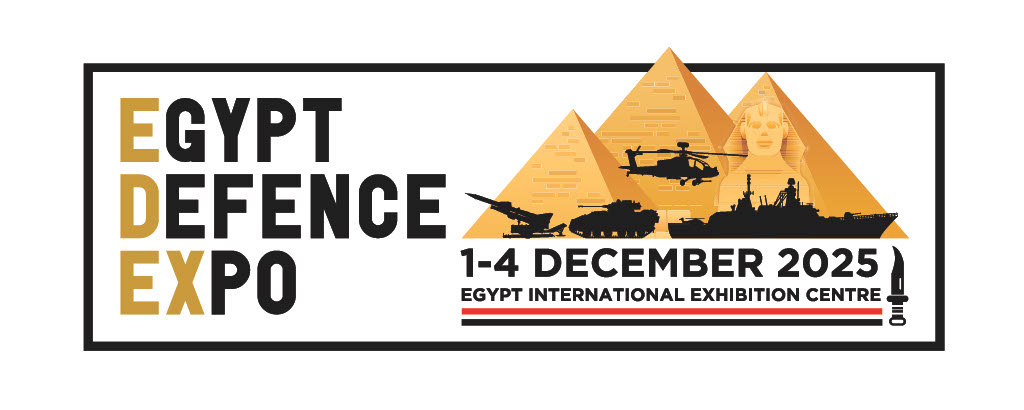
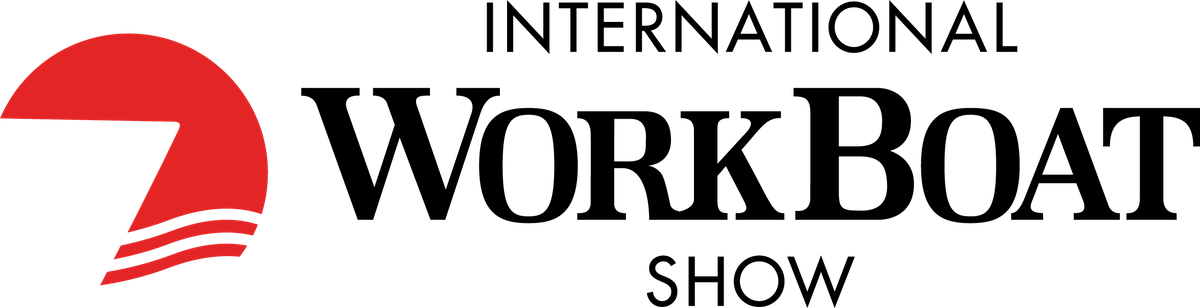
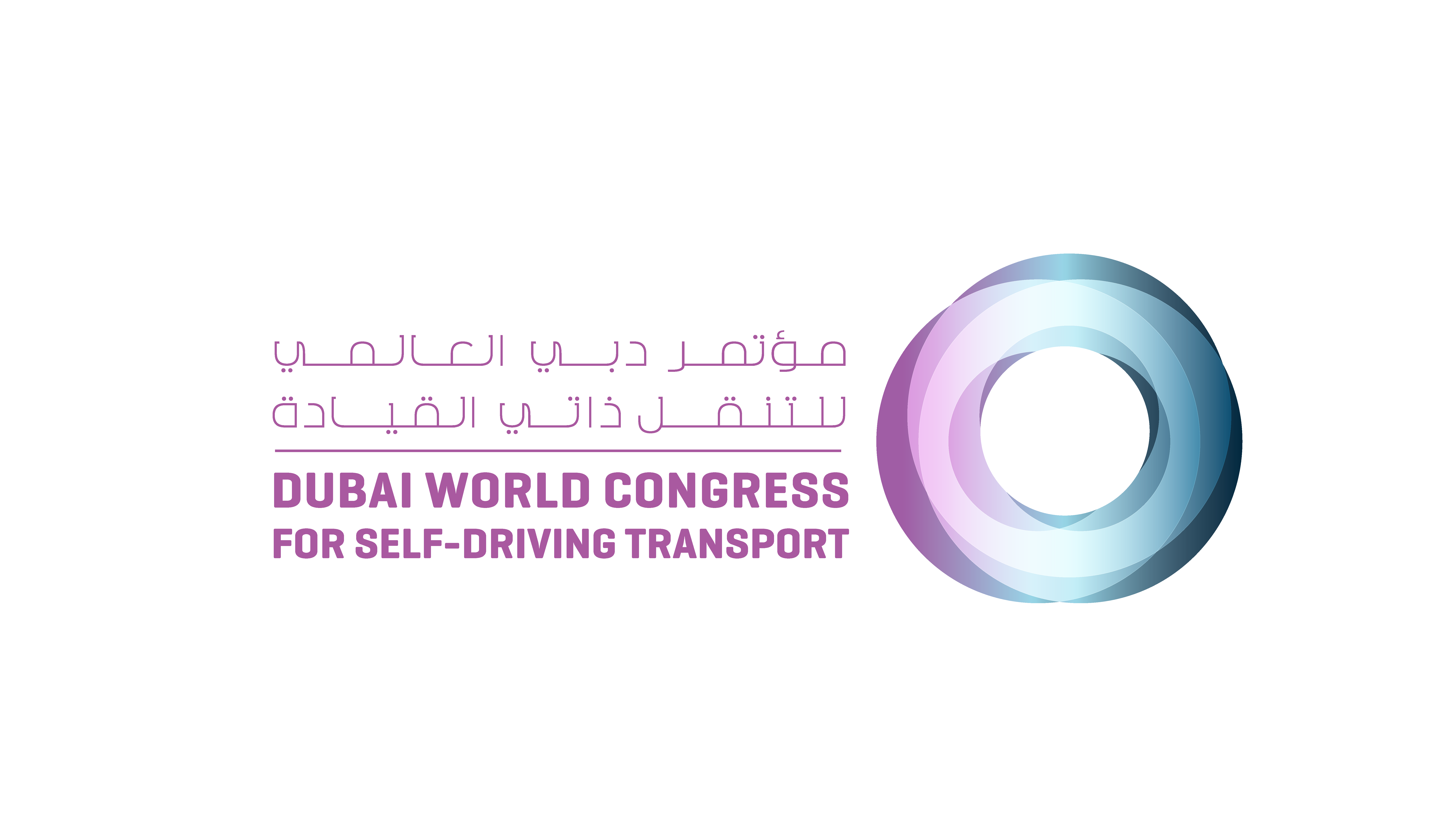
