TideWise USV Tupan
The checking crew
Rory Jackson reports on the development of this USV-UAV/ROV combination designed for inspecting offshore energy facilities
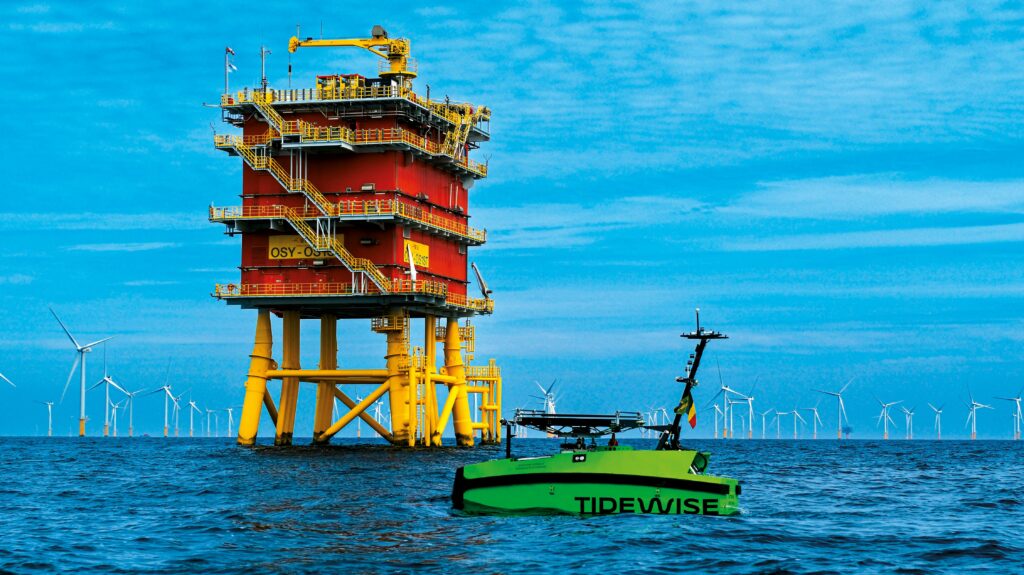
Brazil’s surging market for inspecting maritime oil, gas and wind power facilities motivated the founding of TideWise and the creation of the USV Tupan
(Images courtesy of TideWise)
In Brazil, offshore energy is big business. The country is the world’s eighth-largest oil producer, most of which comes from basins off the south east coast, and its output is expected to rise, with some new oil and gas fields now coming on stream.
Brazil is no stranger to clean energy though: nearly half of its total energy supply and 83% of its electricity comes from renewable sources. Of the latter, 80% of it comes from hydroelectric dams. However, because Brazil’s low-rain season coincides with its high-wind season, wind farms are also in huge demand to complement its hydroelectric sources.
Wind turbine construction is therefore accelerating across Brazil’s maritime regions, with a mathematically exponential rise in installed plants, from just 27 MW in 2005 to more than21,000 MW in 2021.
The country’s energy security and much of its economy therefore relies increasingly on an immense number of wind farms, hydroelectric dams, oil rigs and other infrastructure continuing to operate without failures.
Inspections and other maintenance duties across such infrastructure are typically performed using highly dangerous and costly approaches, such as suspending workers from helicopters to take thermal images of sections of concern or manually perform repairs.
This, and the consequent expansion of harbours and other coastal and riverine structures, has generated an enormous demand for uncrewed and potentially autonomous inspection solutions to remove the risk of human casualties and the costs of crewed vehicles.
Enter TideWise, based in Rio de Janeiro and formed by marine autonomy experts Rafael Coelho (its CEO) and Sylvain Joyeux (CTO) after the two met in2018 while working on a project together. At the time, Coelho was head of design at ASV Global (now part of L3Harris)where he had worked for 7 years on USVs such as the C-Cat 3 (featured in issue 18, February/March 2018), while Joyeux was technical director at13 Robotics, now Kraken Robotics Brazil.
“We both foresaw the huge market for ‘floating inspection robots’ to service Brazil’s energy industry, and our technical skills were highly complementary,” Joyeux recounts. “The planned offshore energy facilities, waterways, new ports and other infrastructure work due to unfold across Brazil through to2030 informed a clear business plan that supported our first investment, allowing us to build our first product, the USV Tupan.”
The USV Tupan is a 4.95 m-long,1.78 m-wide autonomous vessel, with a0.6 m draft, a fully laden displacement of 1400 kg, and weighing 1100 kg when unladen. It has been designed to fit in a20 ft container, as well as in cargo planes and to achieve dimensional compliance with regulations on the transport of items on Brazilian roads.
It carries a hybrid-electric power train that enables a top speed of 6 knots, a turning radius of 10 m at 4 knots or 0m with differential thrust, and a maximum practical endurance of 12 days. It can also carry payloads of up to 200 kg of sensors and, unusually, a secondary uncrewed system such as a UAV or ROV.
The main benefits of seating, launching and recovering a multi-rotor UAV from a platform on the Tupan are twofold. The first is that the UAV’s high vantagepoint allows it to rapidly detect distant oil spills on the water’s surface, which the USV can then sample and test for more precise details after recovering the aircraft and navigating to the reported position of the slick.
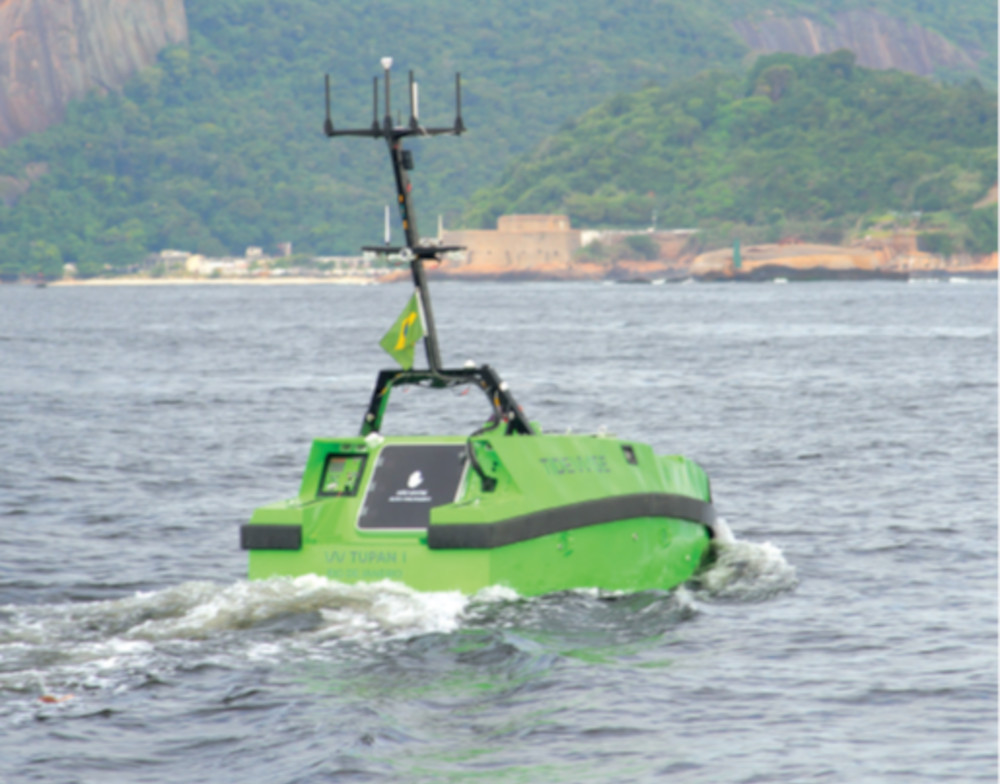
Second, the UAV’s ability to fly high –well above the maximum height of windfarms and oil rigs – allows for close and precise inspection of such infrastructure from top to bottom for cracks, fouling or anything else that could be harmful to continued operations. The USV can simultaneously conduct surface- and subsurface-level surveys for structural problems, be it with EO/IR, sonar, Lidar or other sensors too heavy for the UAV.
The Tupan’s ability to act as a mothership for UAVs as well as ROVs lends it to many other uses for commercial, civil and defence customers for tasks such as hydrographic surveys, environmental monitoring and surveillance. “It’s a multi-purpose USV capable of interacting with different sensors and uncrewed systems, and the hardware has been designed so that we can change from one job to another within hours,” says Coelho.
“The vessel has a moon pool [a payload integration space extending from the vessel’s bottom to its deck] with a footprint of 580 x 560 mm and a height of 1355 mm through the hull, while the USV’s electrical system can provide up to 3 kW of 220 V AC to the payloads,” he adds. “Also, functionalities and characteristics of the USV’s powertrain, such as low roll, low energy consumption, low noise and of course high reliability and redundancy, make it particularly desirable for multiple tasks.”
Development timeline
The Tupan was developed over the course of 15 months, beginning soon after the company’s formation and first investment round. Initial concept sketches were produced in May 2019, and the first sea trials came in mid-2020.
“The Tupan was really meant to be the first workhorse for the company’s r&d ,proof of concept, customer and investor attention, and so on, even from those early days,” Coelho says.
“We are not new to ocean robots and USV design. Sylvain has been doing robot software for 15 years now, and I have been designing and building USVs for 10 years. We also have other team members who have been developing USVs for several years in different countries, so we have a very robust design methodology.”
This methodology began with listing key project requirements, both commercial and operational, which was performed in 2 weeks. After that, the concept was generated in 4 weeks, after which TideWise executed a preliminary design review, then a round of basic designs, followed by a more detailed design round. To meet its project deadlines, the detailed design phase overlapped with the structural welding of the first prototype.
“Also, software development ran in parallel with physical design,” Joyeux says. “And like the vessel’s mechanics and hardware, the software was also developed iteratively, starting with the very basic controls, user interface [UI]architecture and functions, and was built-up from there.
“Naturally we had an overall plan for the software architecture, but we updated that as different projects and potential user needs arose.”
The Tupan’s first sea trial was in early August 2020, in Rio’s Guanabara Bay; extensive mechanical, electrical and software tests had already been run on each of its subsystems. The bay and unsheltered waters around it offered plenty of wind, strong currents, traffic and salt spray to prove the USV’s robustness in autonomous navigation and data-gathering, and the team determined it was ready for service in December that year, with the UAV’s landing capability also being demonstrated in that month.
“Six months later, we demonstrated the system to [state-owned petroleum company] Petrobras, an expected customer, along with the ability to safely hand control of the Tupan from one console to another,” Coelho adds.
A qualification process for the Tupan was also carried out in partnership with Petrobras, and involved inspecting the offshore infrastructure operated by the company, as well as carrying outa launch & recovery procedure from a platform supply vessel, to demonstrate the USV’s operational capabilities.
This vessel is the sole Tupan built so far, as TideWise’s immediate plans are centred not on production and sale of USVs but on ‘robotics as a service’, with the team carrying out missions on behalf of clients, and actionable information being the actual product sold.
“Its comparatively small size has a tendency to make people underestimate its capabilities, but it complies with the MASS [Maritime Autonomous Surface Ships] Code of Practice, and is more than capable of handling a wide range of missions both near-shore and far offshore,” Coelho comments.
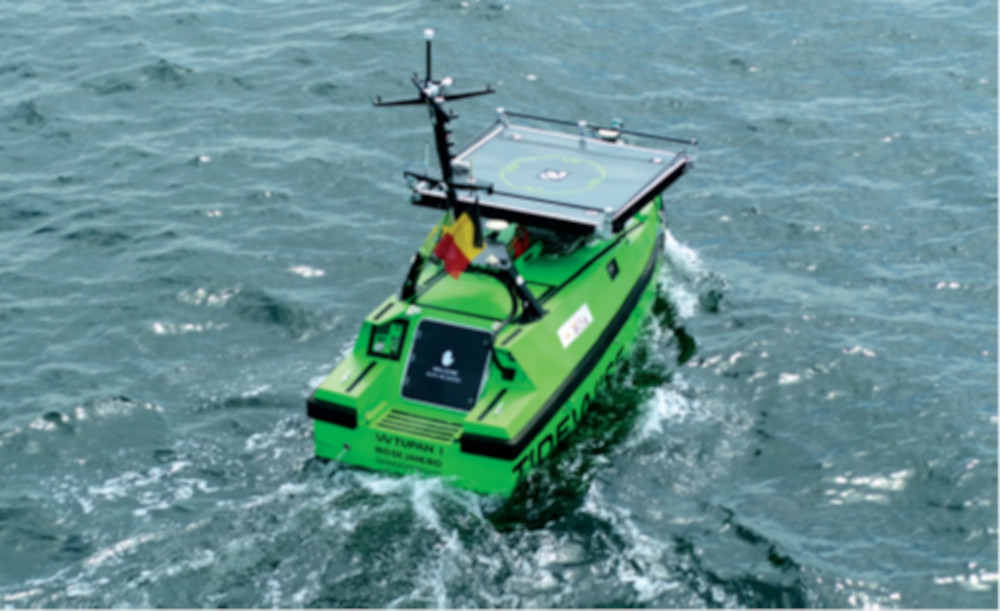
System architecture
The Tupan is divided into two compartments. The ‘engine room’ runs from the transom to a watertight bulkhead in the middle of the USV, and at the front is the ‘payload compartment’, although this section also holds the batteries.
The engine room holds a 9 kW diesel generator, AC-DC power converters, battery chargers, some comms equipment, and the propulsion and steering system.
The payload compartment meanwhile has a 19 in rack that fits 10U-heightelectronics enclosures – more than enough volume to fit multi-beam echo sounders, Lidars, acoustic Doppler current profilers (ADCPs) and other USV geophysics sensors. Companion computers, data storage drives and other devices can also be fitted as TideWise or customers wish.
Naturally, the moon pool is accessible from the top deck, as is a single-point lifting structure for the vessel, mooring cleats, an antenna mast, and payloads such as a gimballed platform from which UAVs can be launched and landed. While the payload capacity is nominally 200 kg, the real payload limit depends on the arrangement of sensors or other systems to be carried.
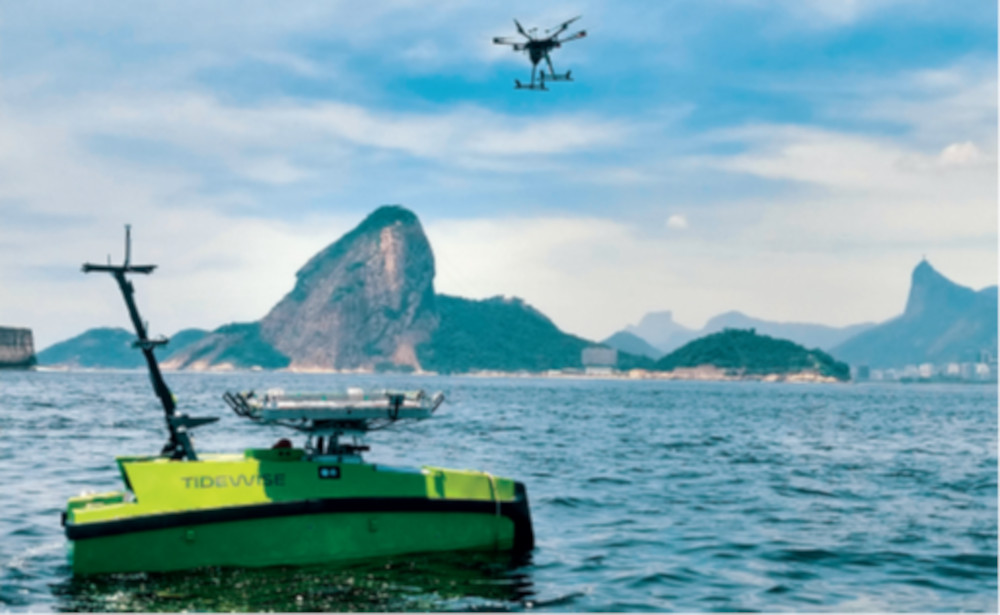
“For example, the UAV and its gimballed platform sit rather high above the deck, which somewhat limits the vessel’s overall stability,” Coelho says. “In this situation, the Tupan can carry 200kg spread out across the electronics rack, the moon pool and the deck.
“For missions in still waters though, where the USV’s anti-roll gimbal or maybe even the UAV’s stabilised platform are not needed, we could remove those and devote the freed-up weight to more payload or fuel, as dictated by the mission and how the selection of payloads are distributed to maintain the centre of balance.”
Endurance can also change depending on the mission profile. For data harvesting that requires just a low-speed transit and station-keeping, the Tupan can go for 12 days without refuelling. For higher speed survey missions of say 5 knots, the endurance will drop to 72 hours, with TideWise able to simulate the expected endurance via its navigation software.
Around the hull
The Tupan was built using three processes running in parallel. First, the hull was made by welding aluminium bulkheads and struts, painting the outer hull, and routing cables through the hull’s sections.
Second, electrical and electronics boxes along with other hardware were put together and installed as soon as chambers were built or when mounting points became accessible. The third process was the mechanical and electrical assembly of the comms mast.
“The goal was to have the hull ready by the time the electrical boxes were completed and the main equipment – the motors, generators, batteries and so on –arrived at the workshop,” Coelho says
“That might seem imperfect, but assembling a relatively small vessel means that sometimes it is faster to pre-install and remove equipment than it is to install it permanently and then workaround it.”
The hull is made of various aluminium alloys: 5083 in some parts and 5086and 6061-T6 in others. Building a weight-efficient 5 m-long hull from aluminium proved a considerable challenge, one that the team tackled by selecting 2.5 mm-thick, low-loaded panels, with skilled welders proving vital for handling and joining such thin plates.
The structure is painted in an epoxy coating, as standard among work-class vessels to ensure low-maintenance surfaces, and the vessel is fully encased in a custom-made, lightweight high-damping rugged fender in order to make operations easier and safer. The hull bottom is then painted in anti-fouling paint.
Landing Pad
The UAV’s landing pad is also made of aluminium, as a compromise between weight and robustness. The team concedes that composite materials could have lower weight-to-strength on paper, but the hardness of composites could be insufficient for avoiding damage during hard landings.
“Another reason for choosing aluminium for the landing pad is its excellent energy absorption properties,” Coelho adds. “During harder landings, we don’t want the UAV to bounce back upwards or along the pad’s length, sot he easiest way to avoid that is to have a structure that’s very good for bending or ‘shivering’ a little to absorb such impacts.”
Joyeux says, “The key to a successful landing is to minimise the relative motions between the two bodies – that is, the UAV and the pad. To achieve that, we contracted Stable, in Norway, a specialist in stabilised platforms and other items such as furniture for marine vessels, to develop an actuated, gyro-stabilised gimbal to sit under the landing pad. We are now on the second generation of that system, and it runs smoothly.”
A mechanism for catching the UAV and holding it securely atop the landing pad has been designed by TideWise, and is in the process of being patented. It draws the UAV inward from wherever it is in the1.7 sq m area of the pad to within the 0.45sq m centre – matching the UAV’s landing footprint – in less than3 seconds, without damaging the UAV.
This proprietary mechanism is the result of several prototypes. Referred to in-house as the ‘hashtag’, four bars are electromechanically actuated from the perimeter of the pad into its centre, with just enough force to slide the UAV’s legs into the middle (if offset) while trapping them to avoid knocking it over.
“We’re on the second generation of the hashtag too,” Coelho says. “On the first version, the bars moved parallel to each other, but now they rotate in the four corners of the landing pad, in a way that creates a special shape and reduces in size at the ideal rate for capturing the UAV.”
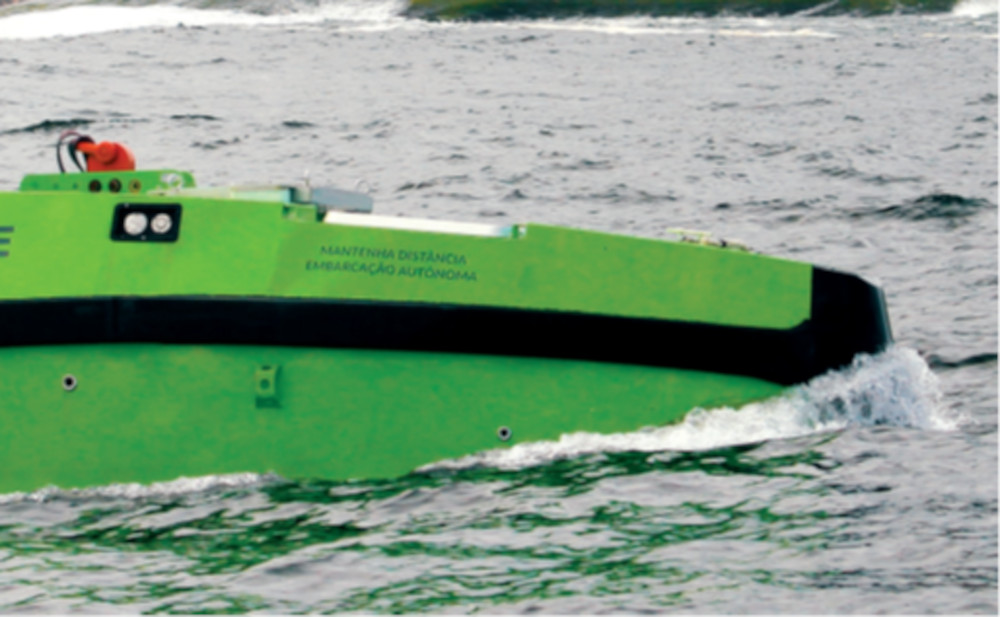
Survey systems and integration
The selection and combinations of sensor payloads on the Tupan are dictated by customer demand, and the biggest demand is for ocean data, including stabilised 360ºelectro-optical cameras, multi-beam sonars, motion sensors, water quality measurements such as salinity pH levels, and water current data from ADCPs.
Coelho adds, “We use Eiva’s software to collect and process the data; they’ve been doing marine data acquisition and related solutions for many years now.”
On the integration of mission sensors, Joyeux comments, “The beauty of having a moon pool is that you can mount the gear needed to operate each specific sensor in it, and the vessel’s autonomy main computer will see the whole assembly as a single payload, in mechanical as well as electrical terms.”
“At the moment, we have one payload frame in there to vertically lower multi-beam echo sounders and ADCPs, to keep them away from interference during operation and protected inside the pool from wave impacts or floating debris during higher speed transits.
“As we’ve said, the total payload weight depends on the centre of balance and the height of the centre of gravity, although in the moon pool alone we can safely have 150kg without having to move other weights on the vessel to adjust the trim,” he says.
Removing one payload frame and installing a new one is a 20-minute job; cable routing takes longer though. As Joyeux explains, “If we’ve installed a system before, familiarity means we can be done in 2-6 hours. If not, it can be longer, maybe up to 12 hours depending on the new system’s complexity.”
Also, any UAV sitting atop the Tupan’s landing bay, or an ROV stowed in the moon pool, can be considered a mission payload in terms of the weight it add sand the critical data it gathers throughout its deployments from the USV. The UAVs available for TideWise’s customers to choose from are currently limited to systems powered by the DJI A3 flight controller, as the proprietary software responsible for intelligent and safe landing on the pad has been written for compatibility with the A3’s architecture.
“As a result, we’re currently using a DJIM600, which is about as big and heavy as the Tupan can safely carry, but we don’t intend to be limited to this model,” Coelho says.
Joyeux adds, “We are already capable of interfacing our flight algorithms with MAVLink-based autopilots, because we regularly communicate over the MAVLink protocol for simulations and testing. We’re also open to working with other partners in the world of UAV autopilots, it’s just a question of how good their velocity controller is, because honestly, DJI’s velocity controller is really good, which is extremely helpful when it comes to landing a drone safely on a USV.
“Beyond that, it’s a matter of how open the autopilot is, and hence how deep we can go into its control layers. Anything Pixhawk-based ought to work well, as DJI’s system is quite opaque, technically speaking.”
GNSS navigation
Navigation and autonomy are processed through TideWise’s proprietary embedded control software, Wise Control. It relies on GNSS for localisation, although Joyeux and his team are working to add real-time, close-range situational awareness and path planning to help close-quarter navigation in congested areas such as ports. Such upgrades are expected within the next 2 years.
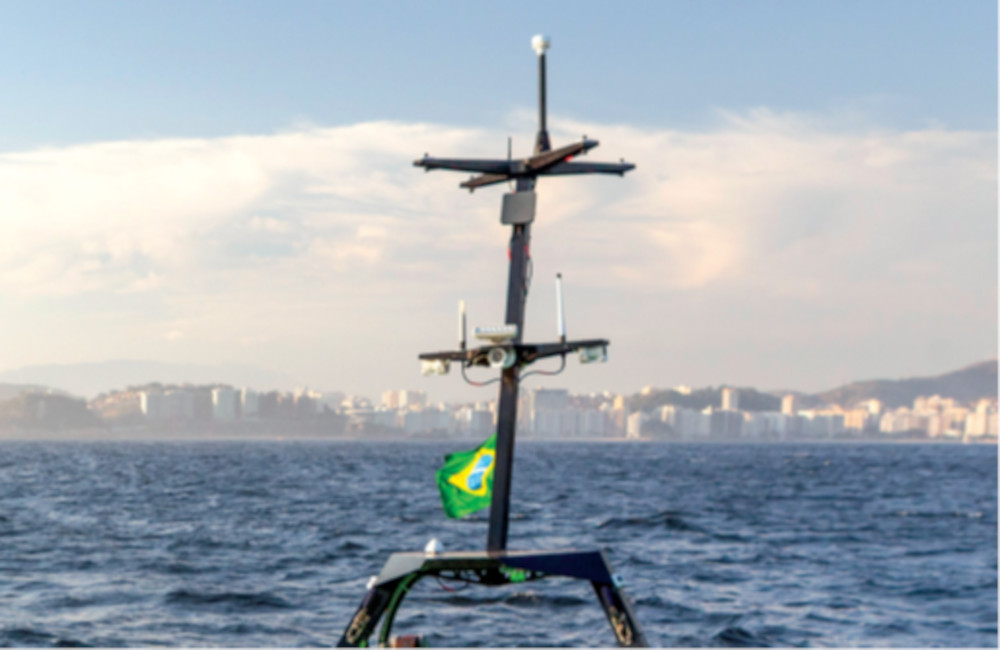
obstacle detection, and will probably be
used for object classification next year
“We use a relatively inexpensive GNSS-INS solution that combines the Open IMU product from AceINNA and theF9 GNSS from u-blox, both of which are very high quality,” Joyeux says. “We fuse the data signals from two F9s to calculate heading readings from the GNSS, with one integrated directly into the INS.”GNSS signals are received via two Tallysman antennas, which TideWise describes as “not survey-grade but very high quality”. The main constraints on
GNSS antenna selection were size, to fit on the antenna mast without creating interference, and the ability to support all the major constellations. The payload survey gear meanwhile uses its own dedicated GNSS antennas else whereon the mast for survey-grade accuracy of position data, which are installed as needed for a given mission.
As a final navigation assistant, CV7 anemometers from LCJ Capteurs enable the user to account for wind speeds when operating the USV and UAV.
WiseControl autonomy
The main computer on the Tupan is a ruggedised COTS PC running Linux, while the WiseControl software is based on the Robot Construction Kit (aka Rock, from Rock Robotics) and an open-source robot framework Joyeux helped develop when he worked in Germany on the FlatFish project in Brazil. This was a joint venture between the German Research Center for Artificial Intelligence and the Brazilian Institute of Robotics and Shell, and was aimed at designing a long-endurance AUV for oil & gas inspections.
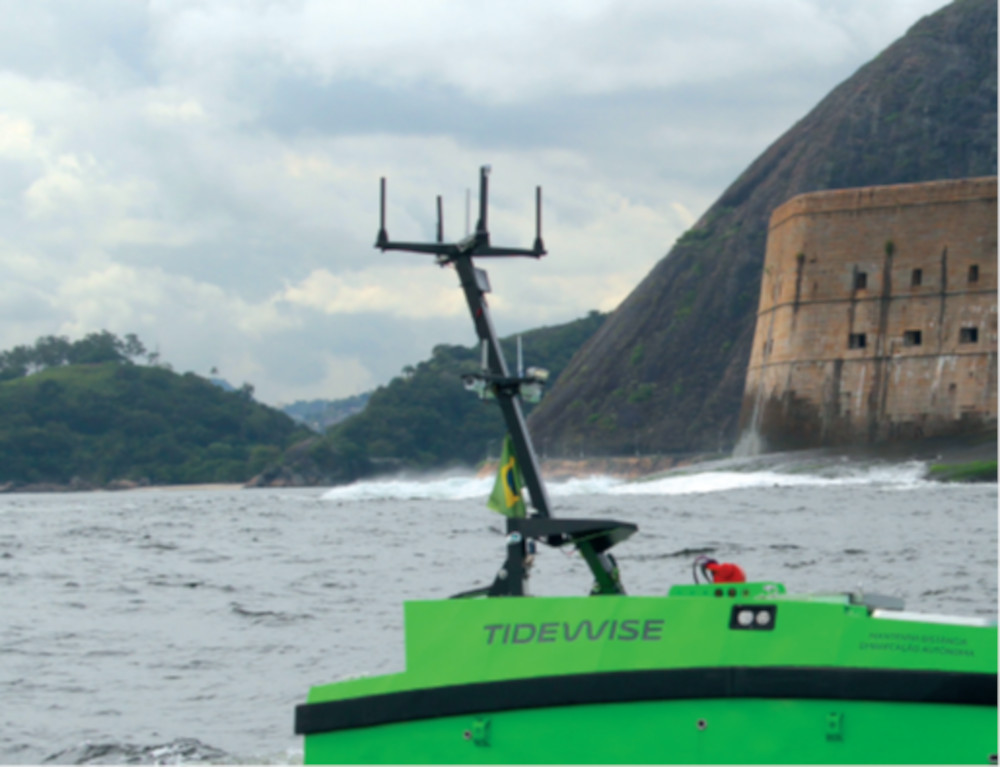
two cellular antennas and four COFDM antennas
“The main driver in creating our own software architecture was to have a very flexible layer for both system building and mission management, something we found lacking in the leading robotics software frameworks,” Joyeux says.
“And while the current version of WiseControl uses AIS and cameras for obstacle detection, we are currently working on a robust data fusional algorithm that will integrate Lidar, EO/IR cameras, radar and AIS. The system architecture has been designed to allow fusion of data from onboard sensors as well as data to be transmitted remotely from external sensors.”
For example, the UAV could provide enhanced situation awareness for the USV in heavy water traffic or poor visibility, by taking off and streaming live geo-stamped video to the Tupan’s computer.
Such streaming systems could also work from stationary sensors installed on harboursides and offshore infrastructure. Joyeux notes here that the reverse could also work: some port authorities have expressed an interest in receiving any live vessel data that the Tupan happens to pick up to help inform traffic management decisions when visibility is poor.
“We’ve just started working on the obstacle detection and avoidance, and we’ll probably have the first trials next year,” he adds. “It needs to meet high technical targets for its performance before we can trust using it in customer missions, because the marine environment is prone to very dynamic changes in light levels and operational conditions. Rain, fog, sunlight, traffic, reflections and clouds or landscapes in the background can have dramatic effects on perception systems.”
A combination of convolutional neural network-based image training and (less complex) heuristics-based classification is used for TideWise’s object recognition. The team notes that such algorithms are less intensive at sea than on roads owing to the visually simpler scenes to be processed. And apart from obeying COLREGs, the low speeds that vessels adhere to when operating around critical infrastructure mean obstacle avoidance is less safety-critical than in highly congested and dynamic road environments.
“The key thing is that we can detect and classify objects with our cameras, then transmit that data to the main computer, faster than a Lidar would,” Coelho says.
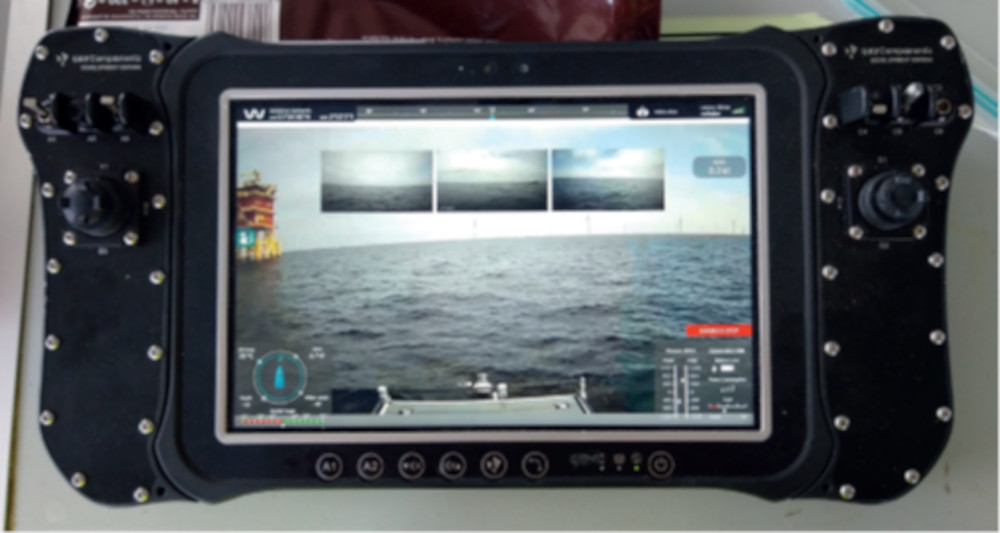
The data comms and control outputs throughout the Tupan are handled largely over an Ethernet network. When devices aren’t Ethernet-based, the USV has the capacity to interface with RS-485 or CAN on the main computer.
Alternatively, the team can add a small single-board computer to interface with sensors or actuators, and hence provide a software route to it. TideWise opts for the industrial version of the BeagleBoneBlack from TI’s BeagleBoard family.
“This is sometimes also done to reduce or facilitate cabling requirements,” Joyeux says, “For instance, the main propulsion motors communicate over RS-485, but the rudder’s motor controller is CANOpen. Other sensors might be analogue,NMEA2000, NMEA0183 or similar.”
Diesel hybrid power
“The Tupan, being a diesel-electric vehicle with differential thrust, can keep fuel consumption extremely low, especially in station-keeping operations,” Coelho comments.
The thrust is provided by two customised electric motor and propeller drives from Brazil-based WEG. Each one provides up to 3 kW of power at a speed of 1800 rpm.
Steering meanwhile is performed by Jefa-brand rudders controlled by a Roboteq DC motor controller.
“In addition to robustness, we saw configurability and feedback as being the most critical considerations for our motor controllers,” Coelho says. “They were key throughout the powertrain – all our gears are ruggedised for industrial use, for instance – and the motor controllers had to be able to withstand significant levels of temperature and current for long periods without it affecting their MTBFs too much.
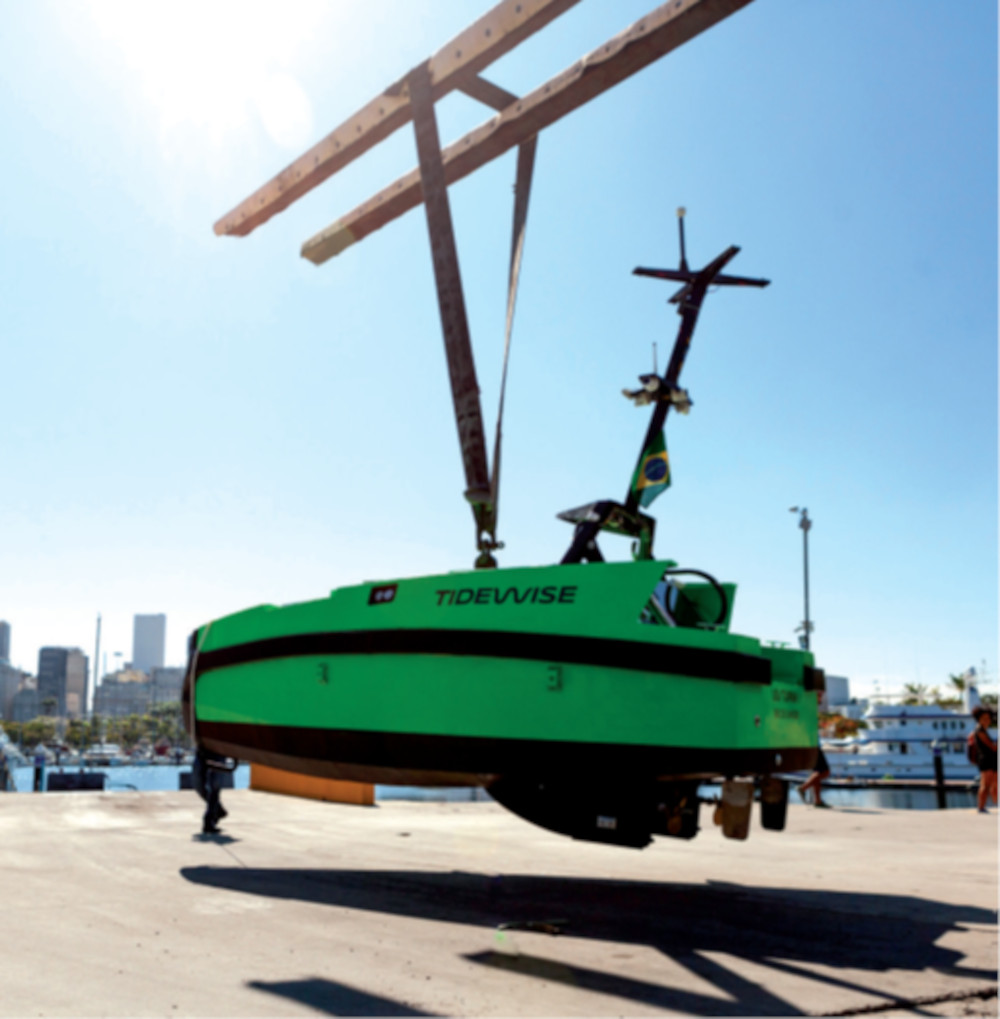
working zones, as is a 20 m-long USV
for deploying larger and more advanced UAVs
“I think Jefa’s steering components are the best in the world, really reliable. The main commercial marine autopilot suppliers – Garmin, Raymarine, the list goes on – all buy from Jefa, sometimes just with a different label.”
Joyeux adds, “Right now, we can go from 0 to 3 kW in 4 seconds. That’s quite a bit of current to push, even fora company as experienced in electric motor engineering as WEG.
“As well as robustness, we wanted our motor controllers to be smart – that is, to give detailed health and performance data for trialling and diagnostics, anything that could help us verify that the USV is working as it should be, and to carry out predictive maintenance in the future.”
A 48 V pack of four 185 Ah lead-acid batteries is installed for distribution of stable electric power to the thrusters and elsewhere. Coelho adds that current marine regulations in Brazil were the main blocker to not using LiFePo cells, but with more recent changes in regulations, TideWise is now designing a fully electric version of the Tupan for a couple of clients.
The diesel generator recharging the battery is the Piccolo 8 from Netherlands-based Whisper Power. The generator produces up to 6 kW of continuous power, and runs on a Kubota Z482,a 479 cc two-cylinder four-stroke with inductive discharge ignition, a permanent magnet alternator and water cooling. WhisperPower’s DC Cube system meanwhile steps the voltage down from120 to 230 V AC to 48 V DC for the battery.
The generator also features sound guards to reduce audible noise and its impact on sonar and antenna reception, advanced diesel engine suspension to reduce vibration, and an integral liquid-cooling system. It also comes with its own ECU and a BMS.
Primary energy storage comes from two isolated fuel tanks of 90 litres each, situated parallel to the moon pool, with certified fuel lines running to the generator.
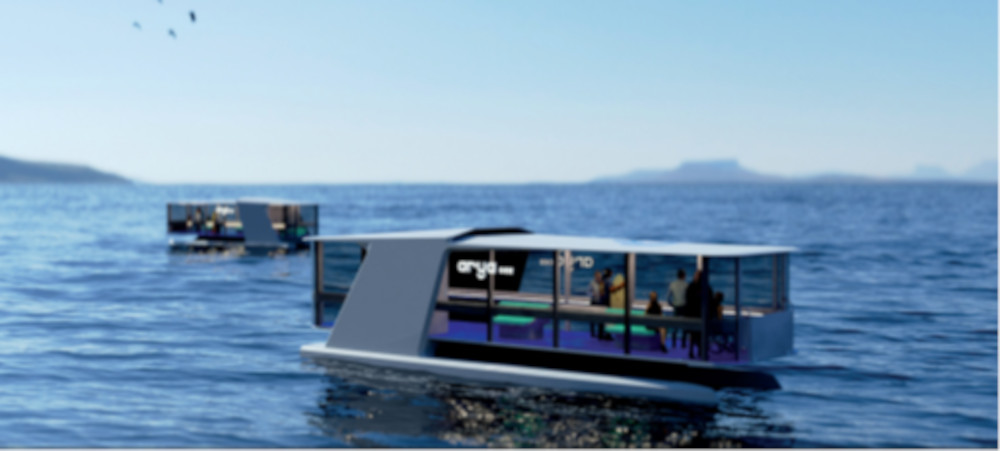
ferry for commuters around Rio De Janeiro, as an alternative
to using the congested roads in the Brazilian metropolis
Data links
For communication to the operator’s station, the comms mast has a 2.4 GHz wi-fi antenna, two cellular antennas from Poynting, and four COFDM antennas from Domo Tactical Communications that transmit at 1.6 GHz.
The USV’s aft meanwhile integrates a single 5 GHz antenna for the UAV-to-USV comms, so that the user can track the telemetry of the UAV through the USV’s main computer and data stream. TideWise also plans to install a KVH satcom antenna on the mast soon.
For maritime traffic management and awareness, the Tupan also carries an Em-Trak B300 AIS transponder, and for added safety TideWise is running an r&d project on integrating a VHF DSC capability.
“DSC is an SMS-like system that can automatically message authorities in emergency situations, such as if a boat is going down or it’s lost propulsion or navigation abilities,” Coelho explains.
Joyeux adds, “From a regulatory perspective, we can get away with not having one because we’re uncrewed, but really in principle every USV should have a VHF DSC system, not just for the safety of USVs but because it’s meant to act as a relay for other boats in distress. It could be crucial for making sure crews in danger are able to call shoreside authorities for help.”
WiseBridge UI
TideWise’s WiseBridge GCS and UI software shows information solely about the USV, with DJI’s A3 architecture having prevented interfacing with both the USV and UAV through the sole portal of WiseBridge. The UAV is therefore controlled from a separate GCS, although TideWise plans to find a solution to that in the future.
“The core objective in developing WiseBridge has always been the same: to have the capacity to adapt the GCS software to our operational needs,” Coelho says. “A USV like the Tupan is very versatile, so we can’t be begging our vendors to implement what we need to support our operations.
“In our opinion, this is one of TideWise’s main edges: that we can iterate our technology to all subsystem needs that might arise. The UAV-to-USV or ROV-to-USV systems for instance couldn’t even be planned if we didn’t have the capacity to integrate the control and UI software.” Joyeux adds, “On the UI side, WiseBridge is meant to be an intuitive control system – don’t overload the operator with data, show what they need when they need it. We iterate quite a lot on the design side because of that.”
WiseBridge’s core functionality has therefore been kept simple, with interfaces for waypoint planning, execution of onboard functions, and manual control where necessary. TideWise uses a Gazebo simulator with added plug-ins to simulate the behaviour of the Tupan in a digital environment, and has a running project for certifying the control system soon.
“One other interesting capability of our system is the ability to have multiple control stations for the same vehicle,” Coelho says.
“For example, we can run the Tupan via satellite from the control room, and a local operator200 miles offshore can take control of the vessel when it’s within line of sight. That was a big milestone for us, to develop and demonstrate this capability while maintaining full cybersecurity.”
Key to successful control hand-off were high-fidelity connectivity and robust programming of control laws. “You must have only one console in control of the USV at any given time, as well as clear definitions in the software pointing towards who has the authority to give control, and who has the authority to request it,” Joyeux explains.
“All those actions have to be executed in concert with the software. It must track and record what is happening between the two consoles in such a way that the moment and act of control transfer don’t disrupt the core activities of the USV’s controller.
“That part was particularly tricky to perfect. And for defending against hostile remote agents, we kept close tabs on the latest and best practices across the global cybersecurity community, not just the marine cybersecurity community.
“We also added an extra layer of authentication on top of our pre-existing comms encryptions, just to be sure of the who’s and where’s of the transfer function. We’re not going to stop there either – that’s the thing about cybersecurity, it never really ends.”
The TideWise fleet
In addition to building two more Tupans the company is, as mentioned, developing an all-electric version. Its design will be similar but useable of course in zero- or ultra-low emissions zones, and the core engineering goal is to be able to operate for up to 48 hours without recharging. The anticipated concept will be to keep the system a short distance (40 nautical miles) from an operating area or recharging station.
“We have a Brazilian supplier of batteries, and we’re working with them to find an optimal size of battery pack with the best trade-off between energy, cost and weight,” Coelho says.
The company is also designing a roughly 20 m-long USV as a multi-purpose platform for offshore work with a greater payload and vehicular capacity than the current Tupan.
It will be capable of carrying small ROVs with the ability to operate in deep water, performing seismic missions, and launching and recovering AUVs and UAVs including VTOL-transitioning craft for long-range logistics, inspections and search & rescue missions.
“We’re aiming for 18 months to finish the design of that USV, and then another 2 years after that to get it launched,” Coelho says. “We’re running that project in parallel with all our other new vessels, as well as our projects in object recognition and avoidance, VHFDSC and so on.”
TideWise also plans to diversify into transportation, by using its expertise in autonomy and high-voltage powertrain engineering to develop an autonomous electric ferry.
“There’s a vast area along the Rio lagoon where the subway lines end, leading to massive traffic jams – it takes thousands of commuters several hours to do just 5 km,” Coelho says.
“A local company has given us a contract to provide a zero-emissions ferry that will cut commuting times to 15 or20 minutes. We’re in the detailed design phase of that right now, and we plan to have built the prototype and put it in the water early next year.”
The ferry is expected to be about 12 m long and powered by motors of 30 kW or so, in order to transport 16 passengers and a few bikes at a time, with floating solar pontoons at the docking stations to enable zero-emissions fast charging. Coelho notes though that these are subject to change as the project requirements dictate.
In the medium term, the company also plans to expand into Europe. At the time of writing, it had conducted successful trials in Belgium, and taken note of the huge offshore wind farm market in the northern Atlantic and the potential for more applications for the USV Tupan.
Specifications
USV Tupan
Diesel-electric
Differential thrust
Dimensions: 4.95 x 1.78 x 0.6 m
Full displacement: 1400 kg
Unladen displacement: 1100 kg
Maximum speed: 6 knots
Maximum endurance: 12 days
Payload capacity: 200 kg nominal
Some key suppliers
Simulations: Open Robotics (Gazebo)
Data collation and processing: Eiva
Stabilised platform gimbal: Stable
Diesel engine generator: WhisperPower
Onboard battery charger: WhisperPower
Propulsion electric motors and controllers: WEG
Rudder mechanics and motor: Jefa
Rudder motor controller: Roboteq
GNSS: u-blox
IMU: AceINNA
Wind sensors: LCJ Capteurs
Survey motion unit: Applanix
Multi-beam sonars and data acquisition: Norbit
Lidar: Velodyne
Main computer: COTS
SBC: Seeed
StudioCoaxial cables: AF Datalink
Antennas for wi-fi and cellular: Poynting
Networking equipment: Mikrotik
COFDM radio: Domo Tactical Communications
Satcom antennas: KVH
GNSS antennas: Tallysman
AIS transponders: Em-Trak Specifications
UPCOMING EVENTS
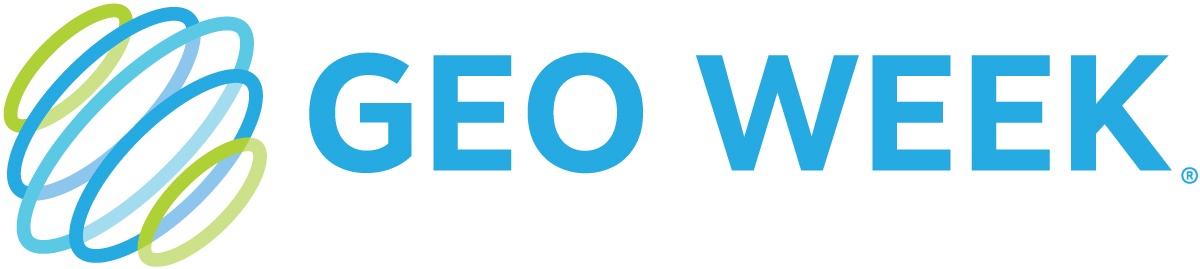
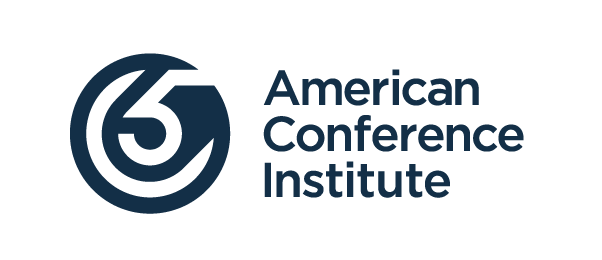
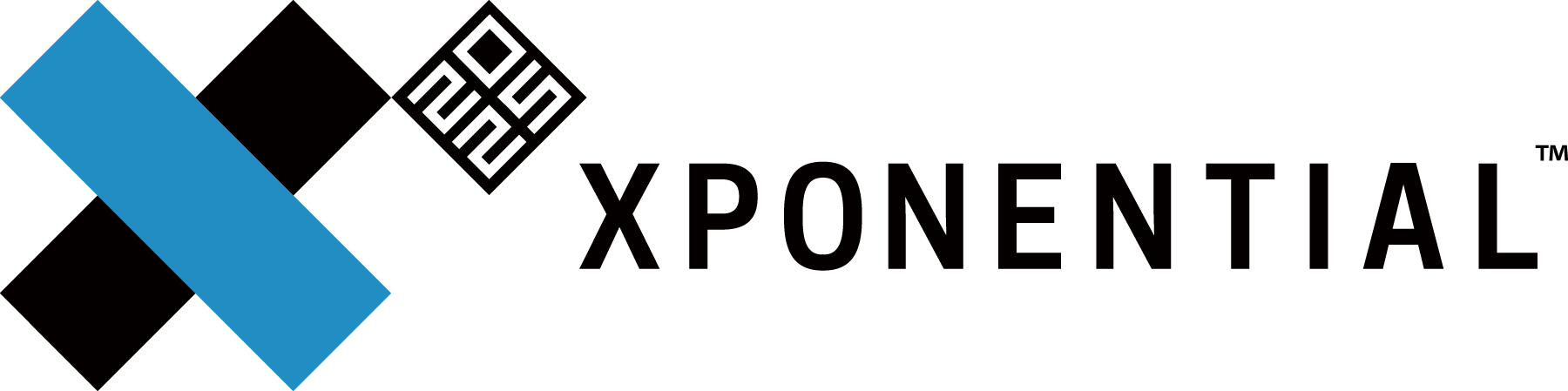
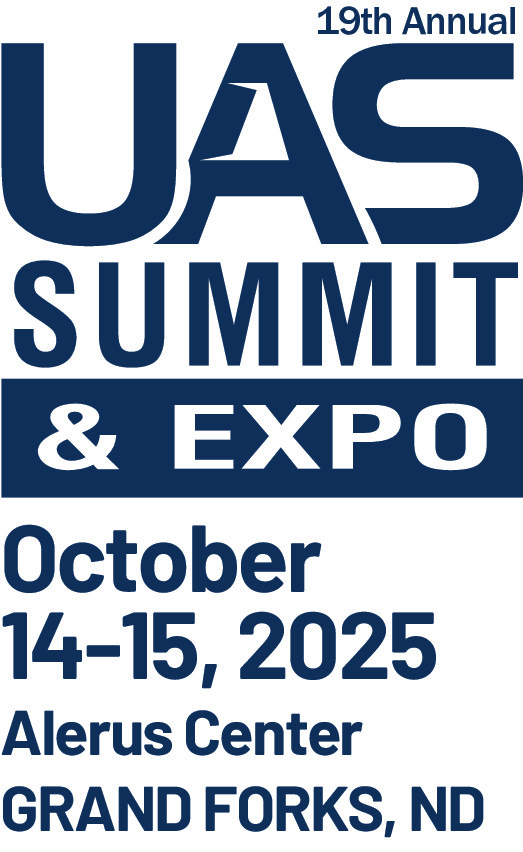
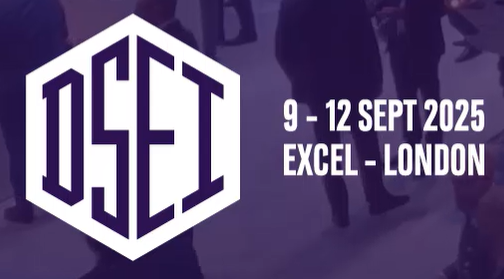
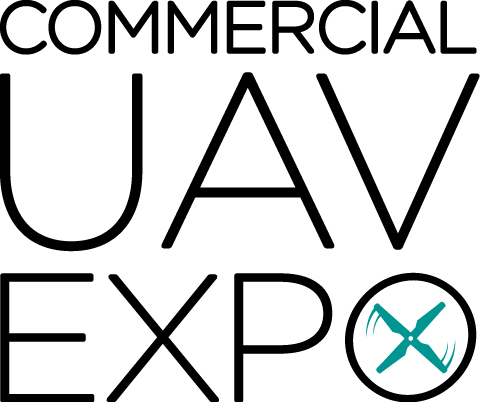
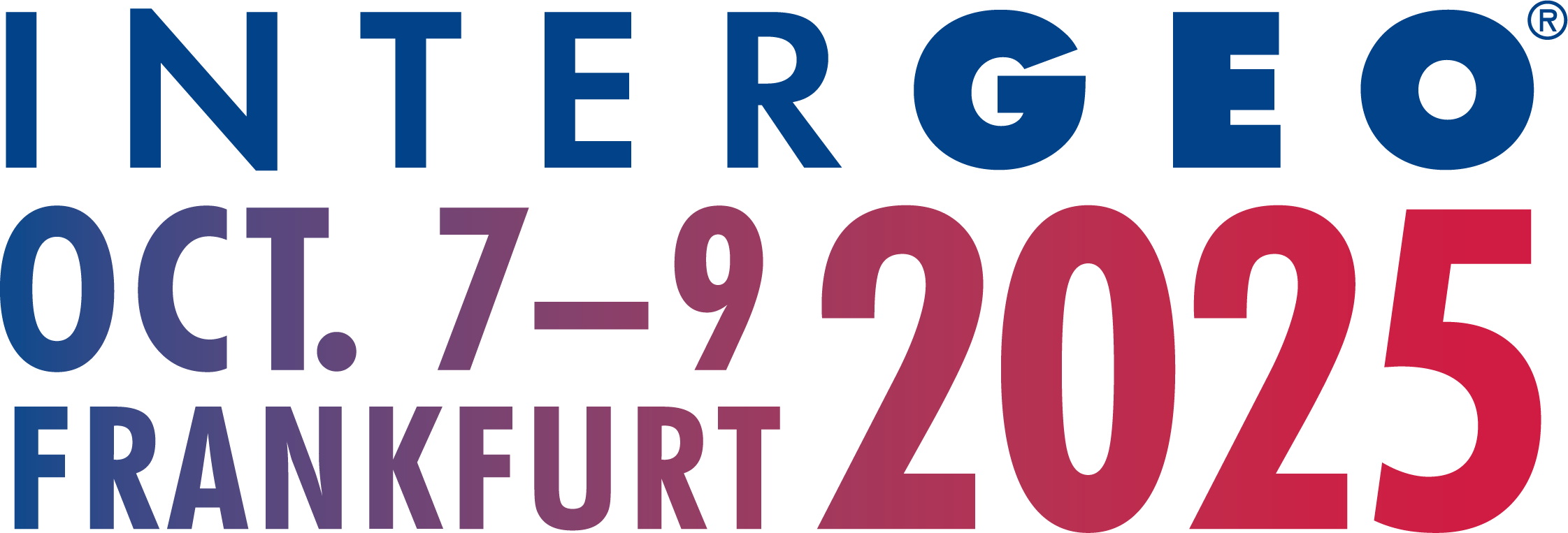
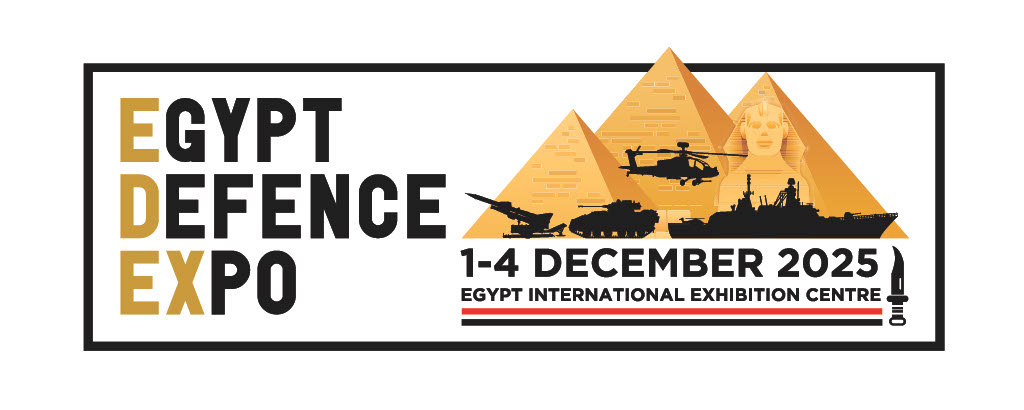
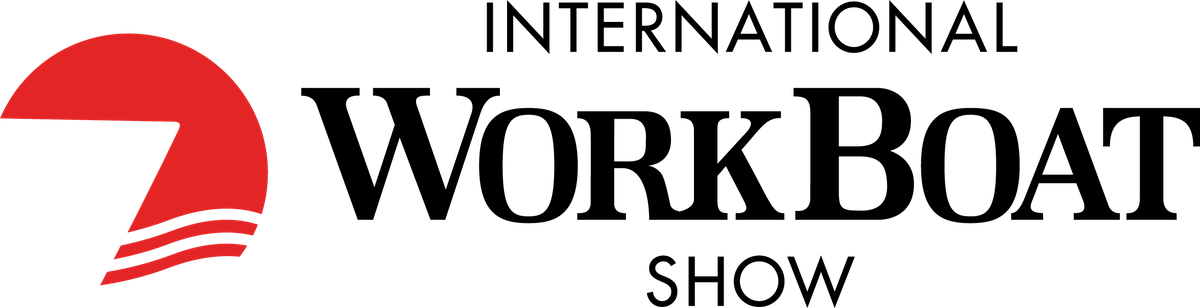
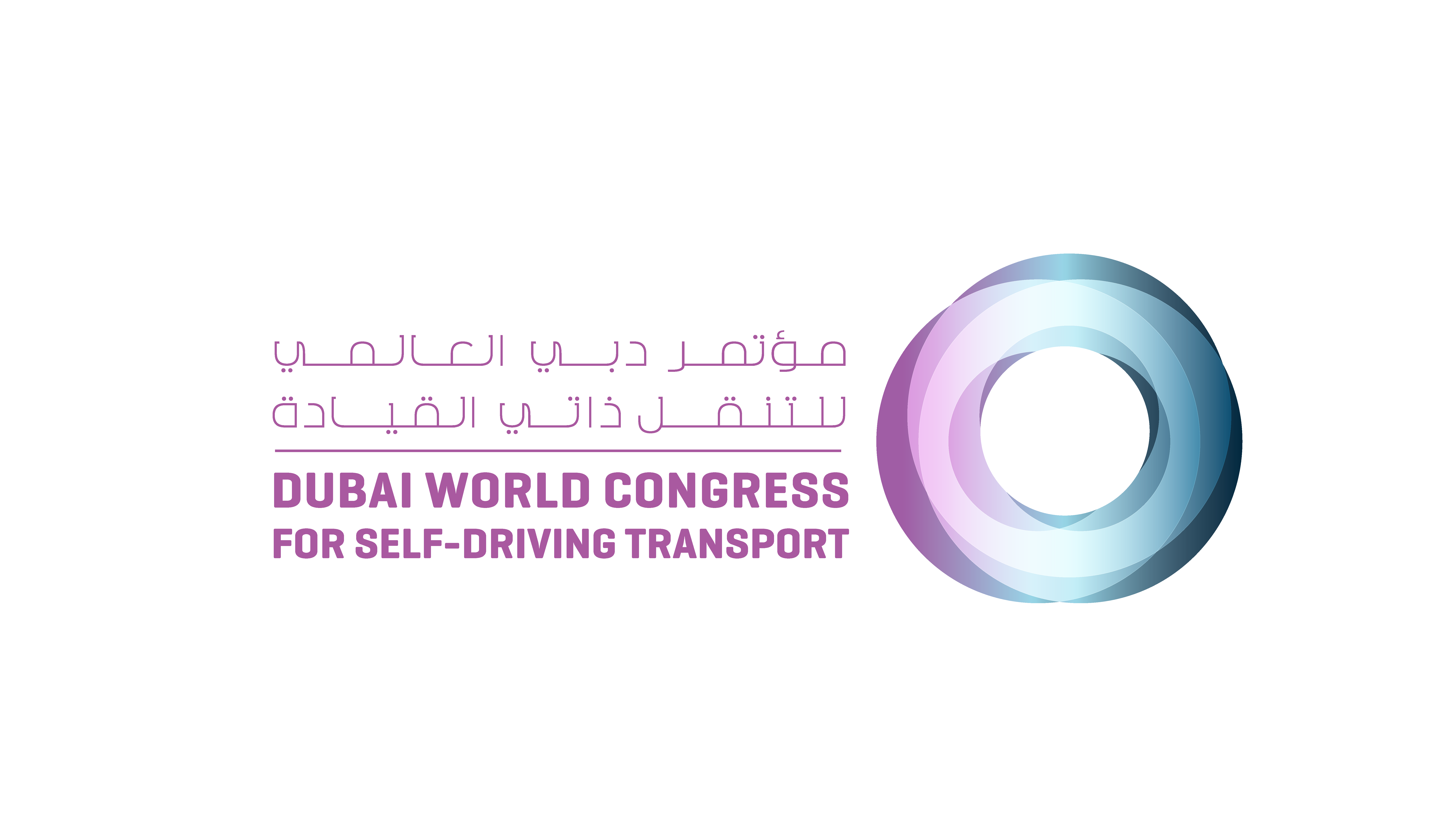
