Subsea Tech SeaCAT
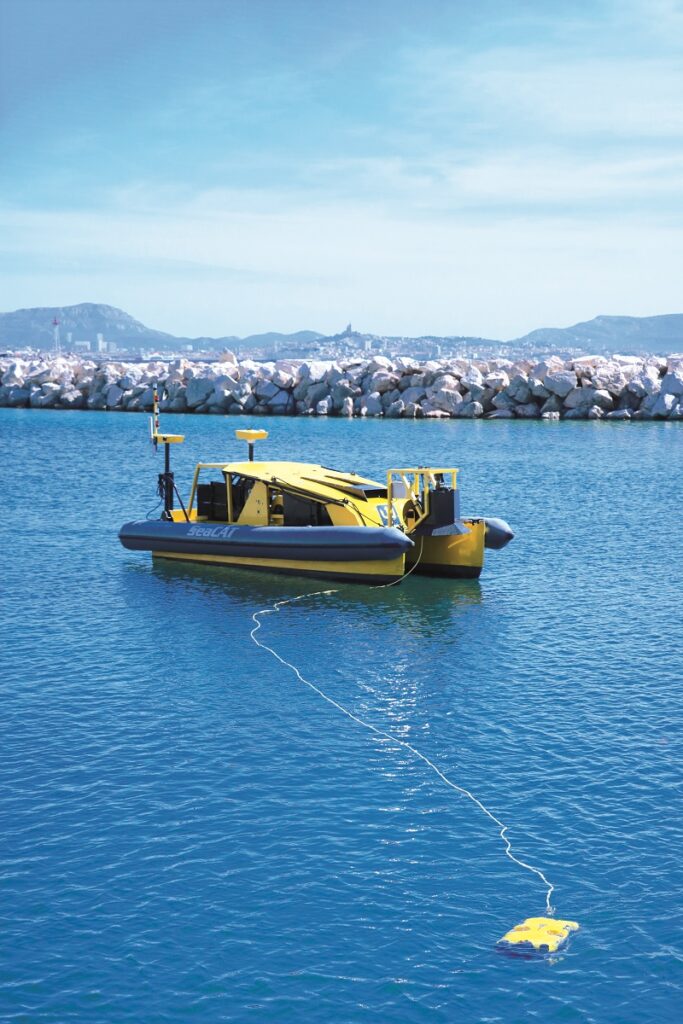
Rory Jackson reports on this new USV that cut its teeth on a project to clear inshore waters of our garbage
In the north Pacific sits a patch of debris covering about 1.6 millionsqkm and containing up to 130,000 t of marine and plastic debris. Known as the Great Pacific Garbage patch, it is estimated to have grown tenfold each decade since 1945. It is ecological damage on this scale that is spurring new approaches to cleaning up our oceans, ones that use AI and autonomy.
The patch is a prime example of the damage we have done to the environment, but research indicates that more than 75% of ocean litter is actually in shallower waters, within about 1000 m of the shoreline and particularly in more populated areas.
Collecting this waste is hard enough, although we have detailed a few successful autonomous solutions from OEMs for tackling this challenge, such as NXInnovation (issue 48, February/March 2023) and RanMarine (issue 11, December 2016/January 2017). However, collecting litter that sinks to the seabed, where it can stick in the sand and be difficult to see and therefore collect, is a task on another level of difficulty.
Present clean-up efforts are few and far between, and are largely carried out by volunteer divers, who are limited in how many hours they can give and how much they can remove from the seafloor. Professional divers can be contracted for heavier lifting work and longer hours, but they are strictly regulated and command high prices.
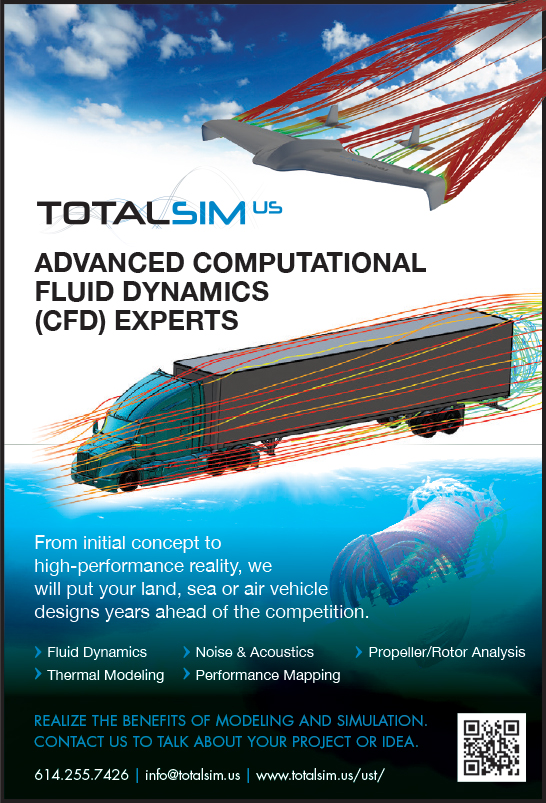
Autonomy though offers a path towards cost-effective, high-throughput cleaning of the shallows and presents no risk to divers, but to date there has been little development of practical systems.
Recently however, the EU-funded SeaClear project has been making the case for using autonomous systems in clean-up efforts. At its heart is the SeaCAT USV from Subsea Tech, and the project’s key aim is to show how AI and uncrewed vehicles can automate and simplify these efforts.
As Subsea Tech’s CEO Yves Chardard recounts, “In 2019, the University of Delft in the Netherlands contacted us and explained that they wanted to set up a proposal for funding from the European Commission via its Horizon 2020 research and innovation funding programme [since 2020, this has been succeeded by the Horizon Europe programme]. They explained the nature of the SeaClear project, and the kind of autonomous aquatic clean-up operations they were aiming for, and we quickly agreed to take part.”
It so happened that development of the SeaCAT was nearly complete at the time, so Subsea Tech saw Delft’s proposed mission as the ideal opportunity to test its 6.8 m-long, 1 t diesel-electric autonomous catamaran in this use case.
The SeaCAT had its first tests in Dubrovnik in November 2021, working as the mothership for a handful of other uncrewed vehicles (not all from Subsea Tech) with their own roles in the operation, and supported by the appropriate AI, planning and infrastructure; further tests followed in Marseille and Hamburg. Most recently, in June this year, the first public demonstration of autonomous seabed litter cleaning took place in Hamburg, and further tests are to follow.
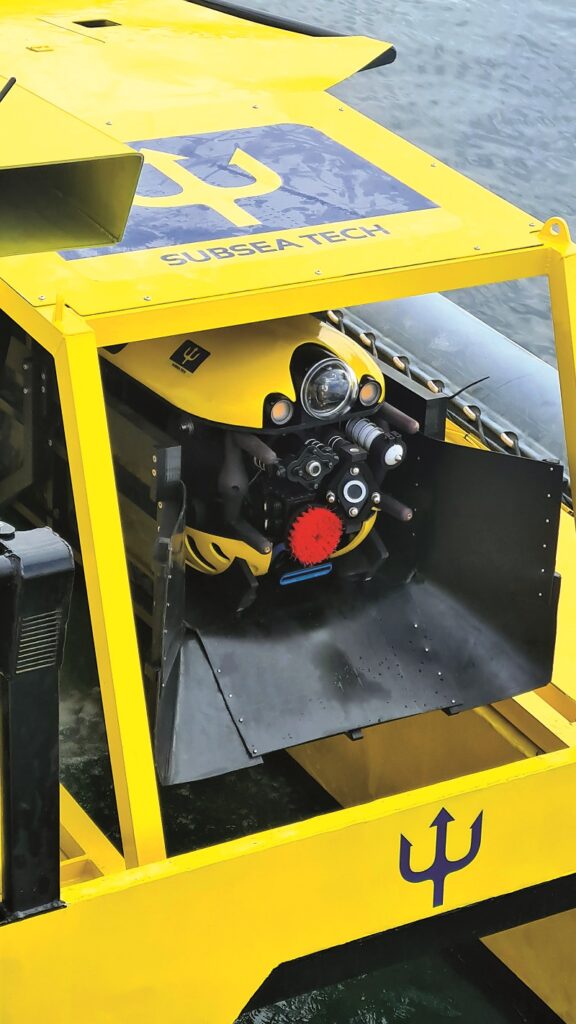
SeaCAT and SeaClear
The SeaCAT has two rigid hulls, with inflatable pontoons to increase stability in heavy seas, although it can sail with them deflated in low sea states. This gives it dimensions of 6.83 x 3.1 x 2.15 m when inflated and 5.78 x 2.15 x 2.15 m when deflated. The solid, 5.78 x 2.15 m frame on top of the inflatables provides enough room for the USV’s key subsystems and three additional uncrewed systems.
“As standard, the USV has one ROV on board, Subsea’s Tortuga, which was designed for users who needed the kind of autonomous deployment of an inspection-class ROV from the stern of the vessel. It is responsible for picking up the litter,” Chardard explains.
“For SeaClear though, we needed to modify the vessel to also have an ROV deployable from the bow, and that does the underwater mapping; the SeaCAT is large enough to allow that. Then, on top of the launching system for the ROV at the bow, we have built a platform for the launching and landing of a UAV.”
At the stern is an electromechanical winch for launching, powering, controlling and recovering the Tortuga, a 37.5 kg system with four horizontal thrusters capable of 17 kg of force each and two vertical ones each rated to 10 kg of force.
At the bow is the Mini Tortuga, a 19kg ROV that travels at up to 4 knots. As with the Tortuga at the stern, it is tethered to the SeaClear, its umbilical providing power and control signals from the USV as well as key telemetry from the ROV. The UAV chosen for the project is a DJI Matrice 210, its low cost and weight (6.14 kg MTOW) being felt to be enough for the purposes of the SeaClear trials.
The SeaCAT weighs 1075 kg, and 500 kg of payload can be carried on top of this. A diesel generator supplies electrical power to the onboard thrusters, ROVs and subsystems such as its embedded control PC, DGNSS, radar, AIS, inertial systems and wi-fi antennas.
“The diesel-hybrid powertrain gives us an endurance of almost 7 days, which also happens to be largely in line with what we want for this kind of operation,” Chardard says.
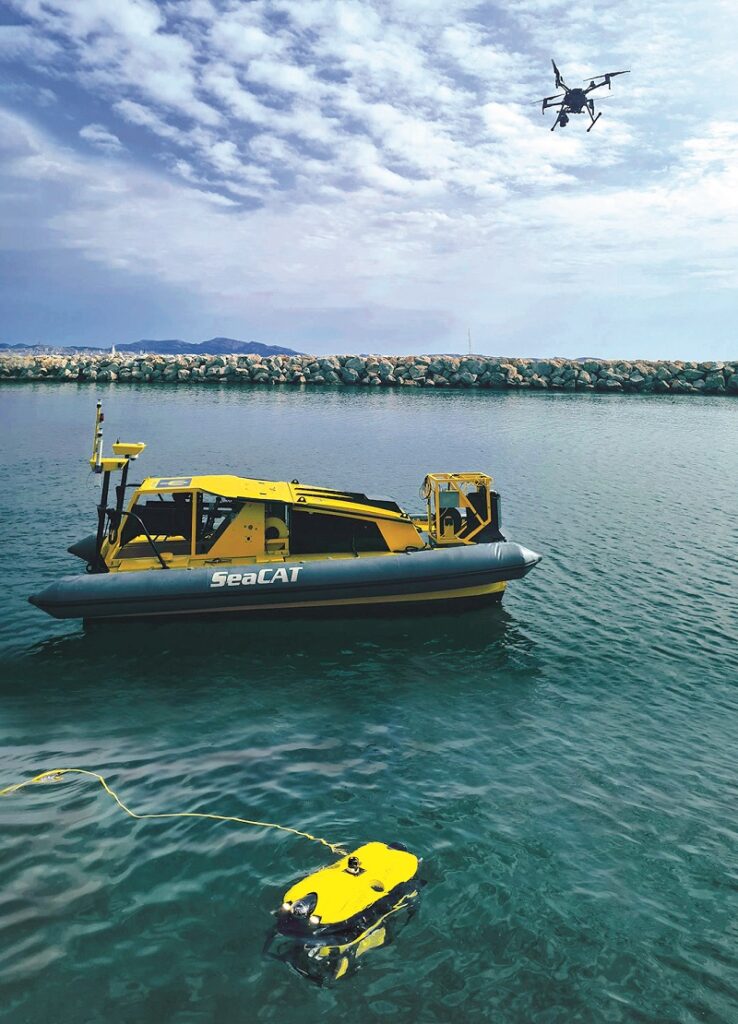
Containerised transport
Despite being large enough to host two ROVs and a UAV, the SeaCAT fits into a standard 20 ft shipping container (once deflated), which as Chardard explains was not something that could be done with other USVs large enough to fit three other vehicles onboard.
“Transporting things in a 20 ft container isn’t exactly cheap but it’s simple, because you can fit everything needed for the mission on any standard container ship,” he says.
“Making the SeaCAT container-transportable was a key target during the design phases, and we emphasised that to our naval architects early on, as well as making clear that the USV had to withstand sea states 4 to 5. That all culminated in an architecture that’s quite long, and uses the inflatable hulls to enhance the navigability and stability of the vessel in rough seas.”
The two ROVs and the UAV are transported with the USV in a 20 ft container to the launch point. There, the doors are opened and a system of rails with a motorised winch inside the container enables the USV to be pulled out safely (after the container has been connected to a power source of course).
While the Tortuga is always stowed at the USV’s stern, the Mini Tortuga sits between the deflated hulls in the container and is therefore installed at the stern, along with its lifting frame and the UAV platform after the SeaCAT is out of the container. Also, the USV has two masts for mounting its navigation sensors and antennas, which are also unfolded to their operating height after removal and before a launch, at about the same time as the pontoons are inflated.
“Once we’re on site, preparations for launch take just under an hour,” Chardard notes. “That includes pre-planning the waypoints – generally standard lawnmower patterns like a survey UAV – for the SeaCAT to follow on a simple tablet, to scour a given area for litter. We also fuel the USV and carry out a naval-standard checklist of visual and digital subsystems to make sure everything is working as intended.”

Clearing the sea
As the USV follows its mission path, its Norbit multi-beam echosounder generates a 3D bathymetric map of the seafloor, looking for large refuse items such as tyres or pipes, but in principle the map serves as a reference point on which to overlay other data.
This other data comes from the Matrice 210 and the Mini Tortuga. The former has a power and data tether to the USV for persistent flight as well as to receive navigation commands for sweeping overhead the USV. Its altitude enables wide visual scanning of the water, which (when clear enough) allows the UAV to spot groups of litter and assign them RTK-GNSS coordinates. Regardless of water condition, it can also look for surface obstacles to aid the USV’s collision avoidance.
The litter’s RTK-GNSS coordinates are transmitted to the Mini Tortuga via the SeaCAT, so that the ROV can travel to them (the SeaCAT tracks its own GNSS position, while the Mini Tortuga localises itself relative to the USV using its BluePrint SeaTrac USBL). The ROV uses its 2D sonar – either a BluePrint Oculus or a Teledyne BlueView M900 – to pinpoint the location, orientation, size and shape of litter.
That data is added to the reference map and transmitted to the Tortuga, which navigates to the litter’s location via USBL (BluePrint’s SeaTrac or Applied Acoustics’ Easytrak) and its DVL (a WaterLinked A50 or Teledyne WayFinder). It grabs the litter using a customised suction-based gripper, avoiding issues with litter that standard manipulators might struggle with.
The Tortuga lifts up to 10 kg of litter at a time, which is deposited into a custom-designed basket that the USV lowers by winch to the seafloor. The system has the capacity and speed to remove up to 300 kg a day.
The basket’s opening has a gate made from organic fibres to prevent litter floating or falling out, and also features acoustic beacons to help the Tortuga localise and approach it.
“Most of the machine vision for spotting, classifying and grabbing litter, spotting obstacles and so on have been developed by university partners,” Chardard explains.
“The SeaCAT’s own autonomous navigation and comms software was developed by us, with litter identification and categorisation mostly by the University of Delft. Meanwhile, the automatic flagging of litter on the reference maps came from the Technical University of Cluj-Napoca in Romania, intelligent coordination between the USV and the ROVs was written by Fraunhofer, and algorithms such as automatic landing for the UAV were provided by the University of Dubrovnik.”
As well as housing all this intelligent software for commands and control, the SeaCAT supplies up to 10 kVA of power for the Tortuga and up to 3 kW for the Mini Tortuga, along with 1 kW for the UAV, although each robot can be stowed when not needed, to avoid overburdening the generator.
The SeaCAT also moves very slowly (if at all) when its robot subordinates are sighting and collecting refuse, which helps to balance out conflicting power needs. On top of that, Chardard explains that the onboard CPU and GPU are quite low-duty systems, and the SeaCAT itself requires no power-hungry electronics, as GNSS, AIS and the UAV’s mapping provide for all its navigation and collision avoidance needs.
The operators meanwhile monitor the mission via the tablet and a 5 GHz wi-fi link to the SeaCAT, which has dual-redundant wi-fi antennas with a range of up to 5 km (although Chardard notes that these missions rarely need to go more than 1 km from the shoreline to find the vast majority of ocean litter). The tablet has joysticks if operators feel the need to take remote control of the USV or any of its subordinate robots.
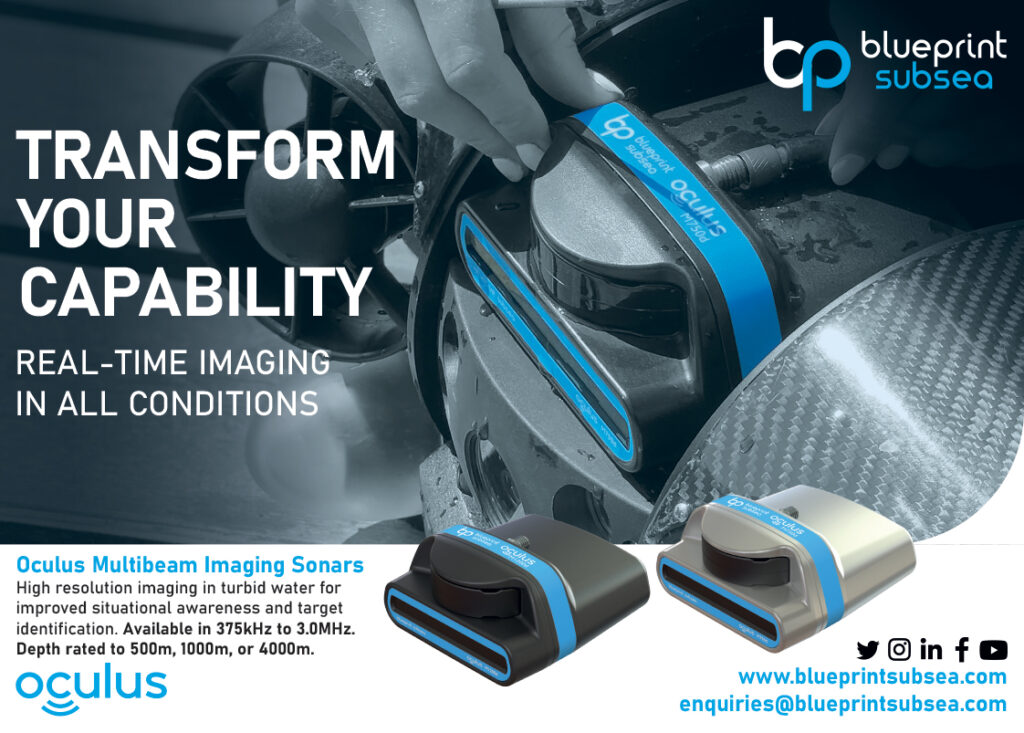
Diesel-electric power
As mentioned, the SeaCAT runs on a diesel generator, which produces up to 12 kW. That is enough for two unidirectional Fischer Panda Aziprop thrusters and speeds of up to 6 knots, as well as for all control, navigation, comms and other electronics. Two tanks containing a total of 200 litres of fuel provide the USV’s endurance.
“It’s quite a simple powertrain, and the electric propulsion is a good choice for us in control terms, as it’s much easier to control an electric thruster than a gas outboard or similar marine engine,” Chardard says.
“With this being an environmental mission, we would of course have loved to use a totally zero-carbon power system, but for the project to demonstrate autonomy as a viable long-term solution for clearing up coastline litter, we needed a much longer endurance than batteries alone could give.”
Alternative zero or low-carbon options were found wanting. For instance, designs and simulations of a hydrogen fuel cell powertrain were more complicated and expensive than the current power configuration.
“If the SeaClear project is to offer a solution that any coastal authority can afford, we can’t drive up the price and then cut the endurance by, say, two-thirds,” Chardard says.
The company has also considered biofuels, but finds them insufficiently carbon-neutral in their planting and processing stages, and their lower energy density compared with diesel poses another drawback.
Back ashore
Once a coastal sweep is done, the SeaCAT is designed to be lifted by standard harbour cranes and stowed on a ship or quay with a four-point mooring system. Ideally however it should be hoisted directly onto the rails of its container and cleaned with a powerful freshwater hose to prevent fouling or corrosion from seawater.
The infrastructure for the Mini Tortuga and DJI 210 can then be dismantled, the navigation masts can be folded down, and all systems can be stowed in their containers. Overall, the recovery, cleaning and disassembly takes about 2 hours.
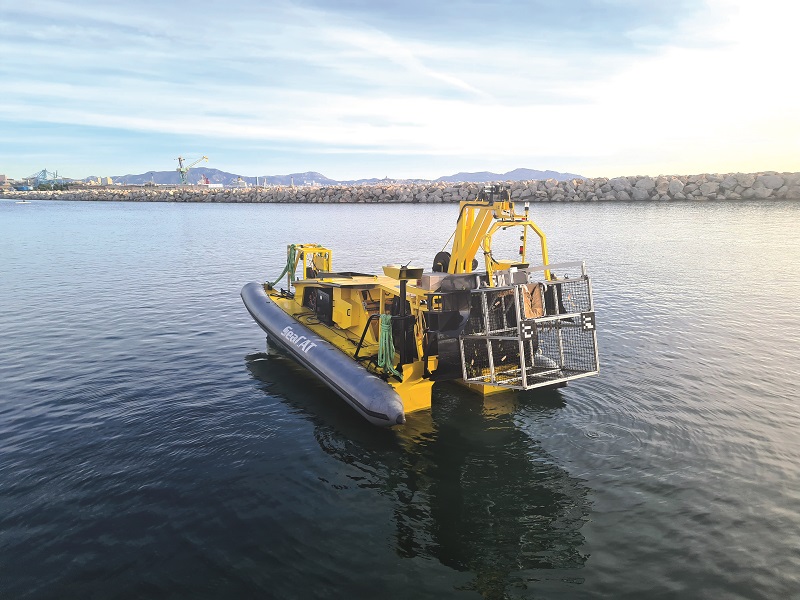
SeaClear Phase Two
The second phase of SeaClear began in January, with the first phase set to conclude at the end of this year, after further public demonstrations this October when the consortium returns to Dubrovnik, so technically there is a one-year overlap between the two phases.
The second phase is aimed at improving various performance aspects across the autonomous ecosystem. To that end, a USV like the SeaCAT but larger and with integrated solar power is in the works.
On that USV, the stern ROV will be replaced with a smart grappling arm to be designed by the Technical University of Munich and equipped with sensors and thrusters, which will increase the weight capacity per lift to 250 kg.
That means objects too large and heavy for the Tortuga or professional divers can now be removed from the sea, such as discarded household appliances, industrial vehicle tyres and motorbikes. An A-frame and winch will lift and lower the smart grappler to grab waste from up to 300 m below the surface.
“Also, the larger USV will be paired with a much smaller USV we’re working on, which we’ve called the Tender Shuttle,” Chardard explains. “It will be hydrogen-electric, and its job will be to go back and forth between shore and mothership, taking the litter loads from the large USV and transporting them to coastal sanitation workers.”
For the company’s purposes, having a hydrogen fuel cell and bottles of hydrogen gas on the Tender Shuttle makes sense, as it is to be a small USV with a small powertrain, one that is relatively inexpensive compared to the size of fuel cell and hydrogen storage that the SeaCAT or its larger successor would need. The Shuttle’s frequent trips back to shore also dictate an energy storage system that can be quickly replenished, so the hydrogen bottles can be replaced and refilled within a few minutes.
With all these changes to the operation, Subsea Tech expects that about 2000-2500 kg of litter will be collected each day.
“One thing I want to add is that we didn’t want to collect surface litter during phase 1 of SeaClear, as there are small USVs and static systems that already do that, but in phase 2 we’ll add that capability,” Chardard comments. “We’ll hang a frame and net with room for 500-1000 kg of litter between the inflatable hulls, and the catamaran will sail over floating litter, making for a more complete cleaning solution.”
At the time of writing, Subsea Tech had the capacity to produce up to five SeaCATs a year, although it was confident it would find and partner with as many subcontractors as needed should more of the USVs be required for SeaClear, similar research projects or organisations who want to take on the project’s concept on a more industrial scale.
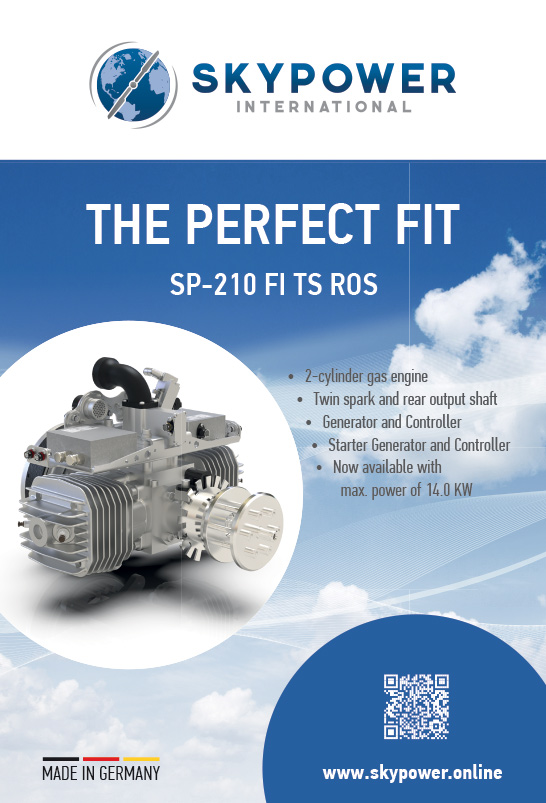
Specifications
- SeaCAT USV
- Catamaran with rigid inflatable hulls
- Diesel-electric hybrid
- Dimensions (inflated): 6.83 x 3.1 x 2.15 m
- Dimensions (inflated): 5.78 x 2.15 x 2.15 m
- Weight: 1075 kg without payload
- Maximum payload: 500 kg
- Maximum speed: 6 knots
- Maximum sea state: 4 during operations, 6 during transit
Some key suppliers
- Diesel engine-generator: Kubota
- Thrusters: Fischer Panda
- Coordination intelligence software: Fraunhofer
- USBL: Blueprint Subsea
- USBL: Applied Acoustics
- Imaging sonar: Blueprint Subsea
- Single-beam bathymetry sonar: Airmar
- Multi-beam bathymetry sonar: Norbit
- 3D Lidar: Norbit or Velodyne
UPCOMING EVENTS
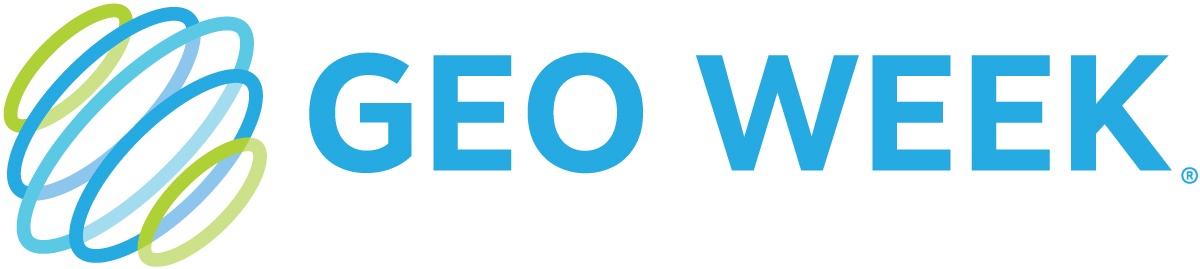
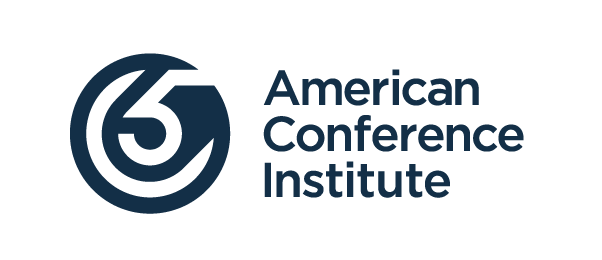
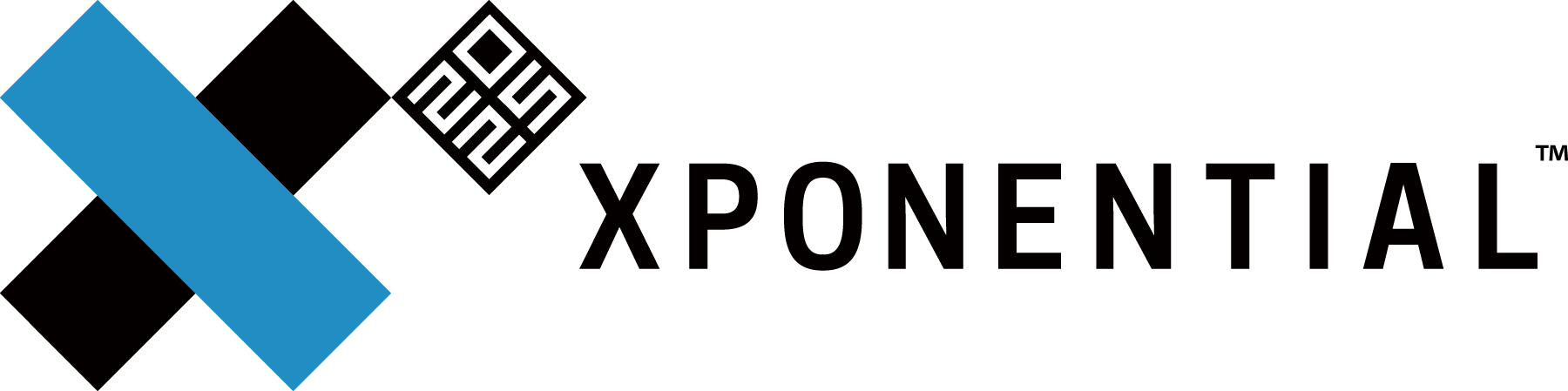
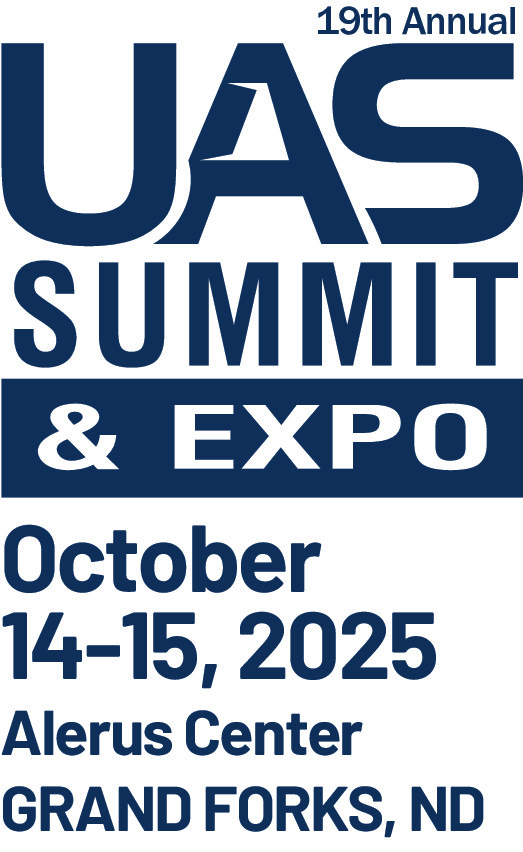
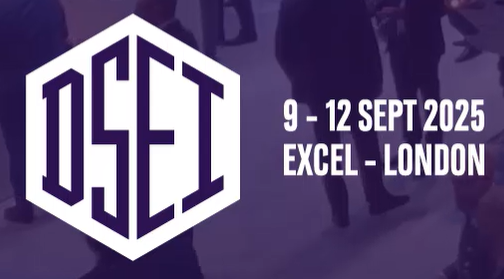
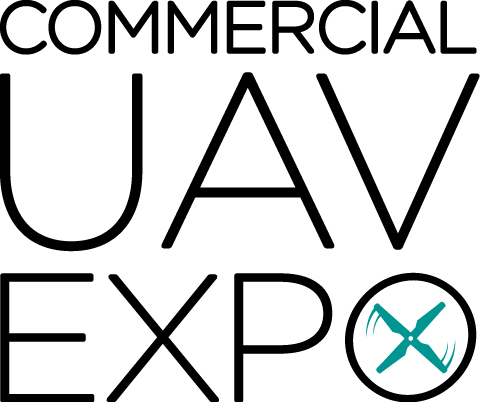
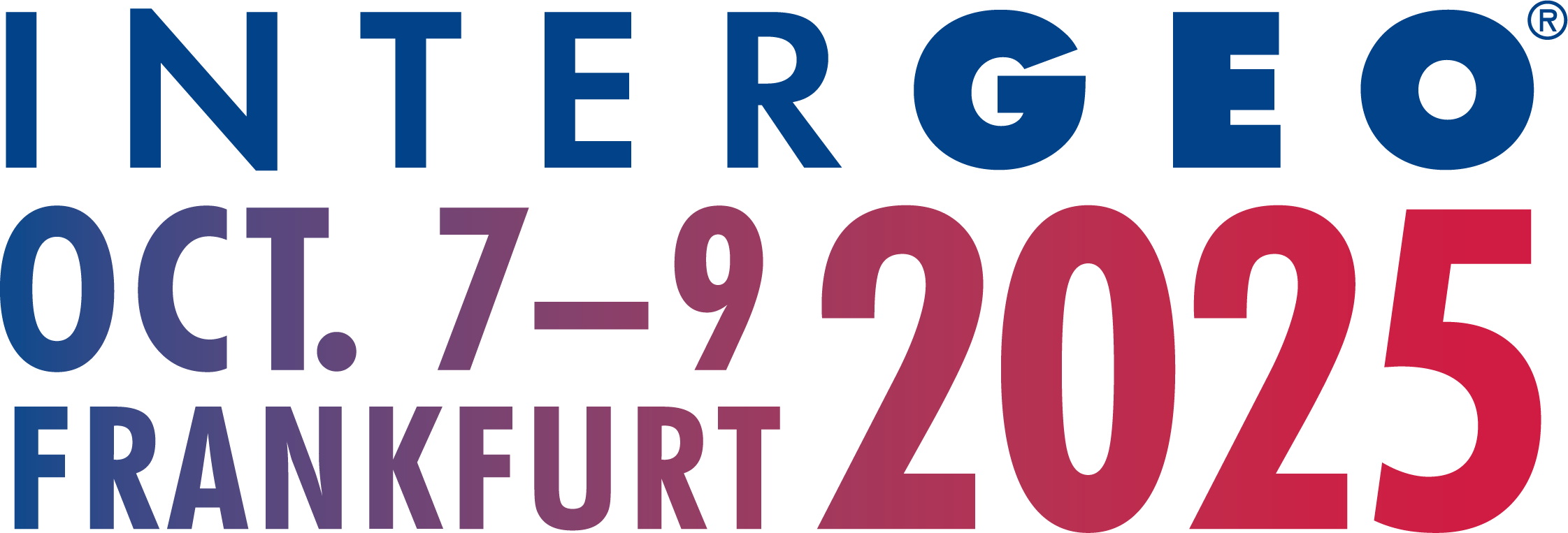
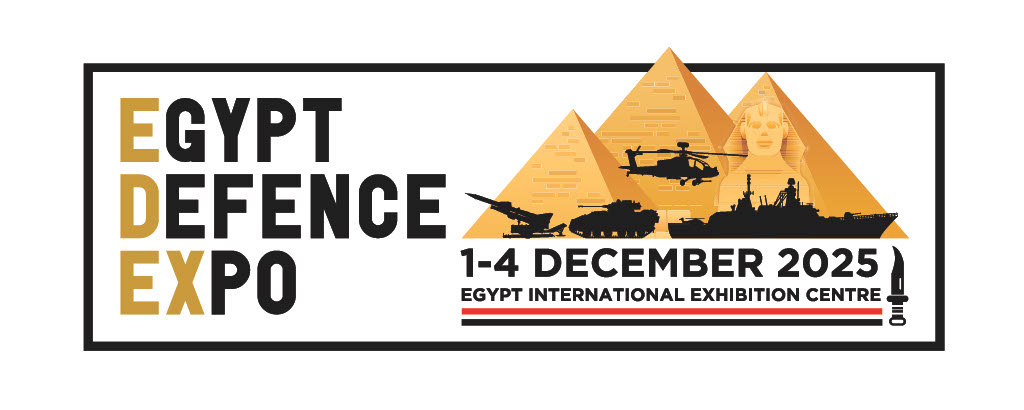
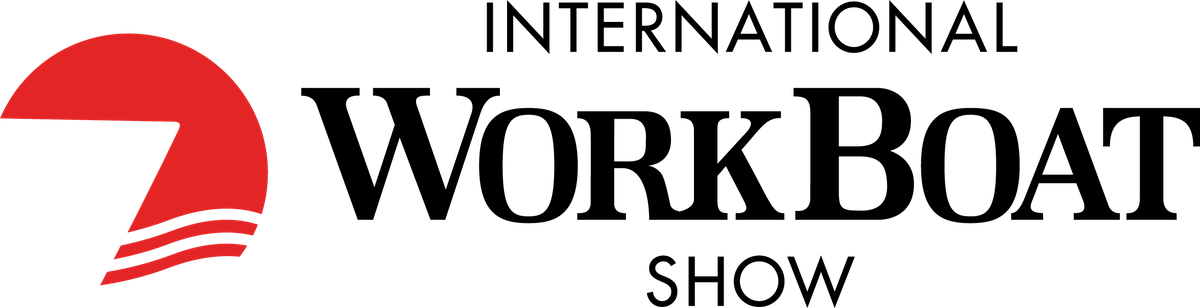
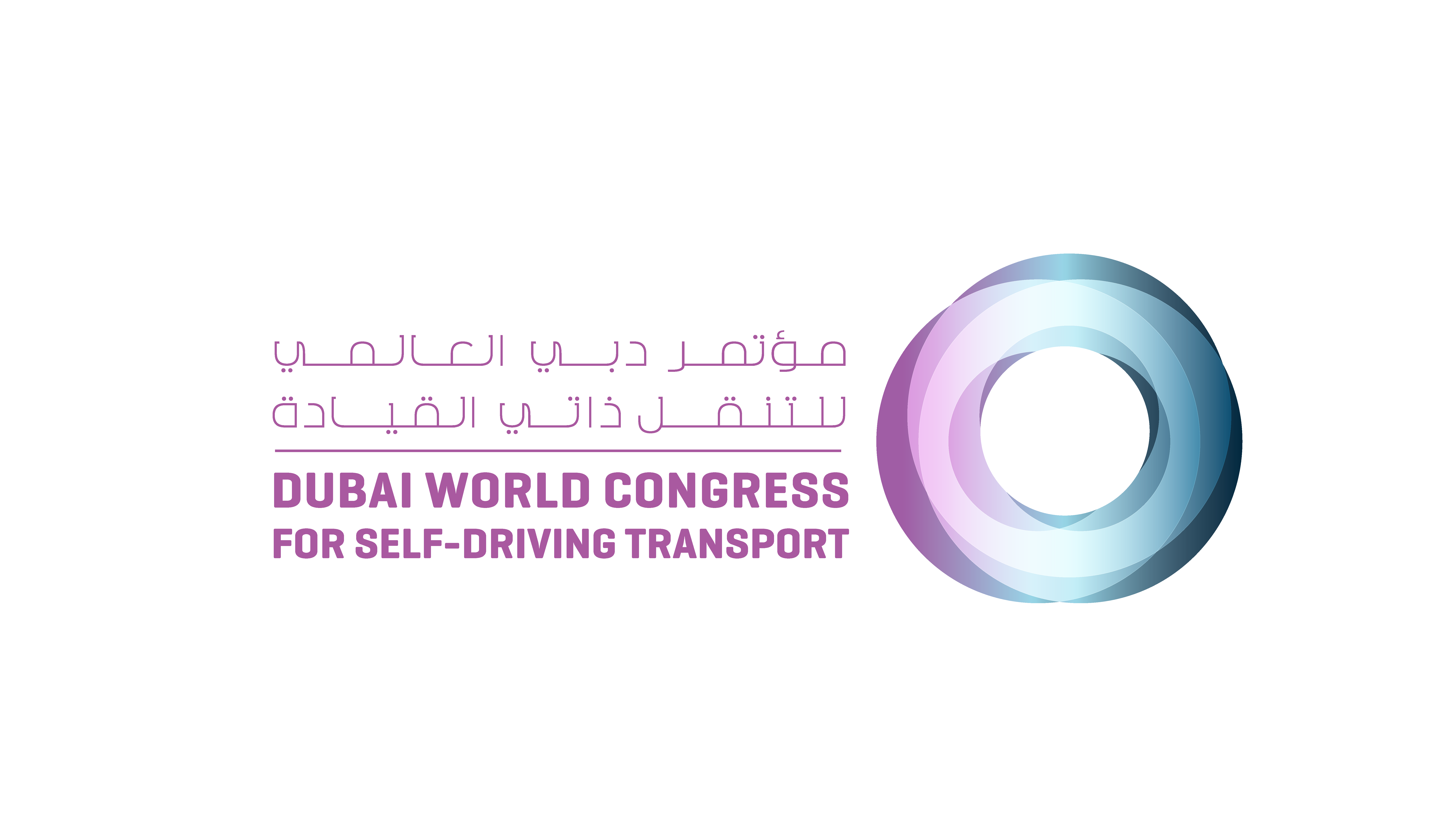
