Cleo Robotics Dronut X1
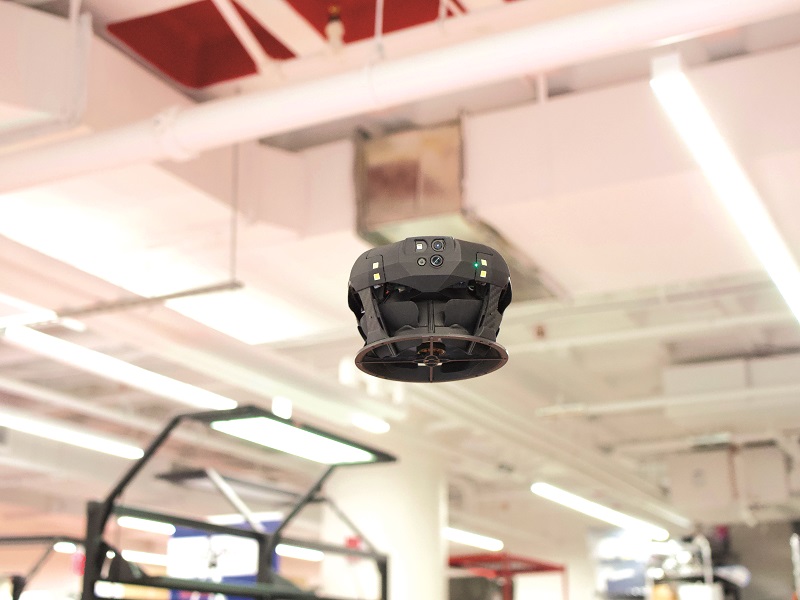
Tight fit
This duct-shaped UAV has been designed to inspect confined GNSS-denied spaces. Rory Jackson explains how it works
In the past 2 years there has been a growth in uncrewed systems designed for autonomous operations in enclosed, indoor spaces, where GNSS cannot be relied on for navigation. Although SLAM (often the key to indoor autonomous navigation) might once have been confined to high-end military systems, it is now in use on such a range of commercial uncrewed systems that vehicles are now able to delve safely into tighter and more confined quarters than ever.
The Dronut X1 UAV represents an optimal design for inspecting indoor or otherwise GNSS-denied locations. It is shaped as a duct, about 16 cm in diameter and 10 cm tall, and has two rotors shrouded by the duct with meshes at both ends, to prevent impacts of the blades against any surfaces or people.
It has been developed by Boston-based Cleo Robotics, which was founded by CEO Omar Eleryan and CTO Simon Czarnota in 2017 to create a vehicle that could inspect confined spaces and potentially hazardous environments. Like many in the professional, high-end UAV space these days, Eleryan previously worked in the oil & gas industry, although he says aerospace is his passion.
“During my time in oil & gas, however, I had to inspect underground tanks, which is a pretty awful job – you have to get into really dirty, dangerous types of environments – and I quickly noticed that most of that work was visual in nature, with engineers going in largely just to take a bunch of pictures and then inspect them afterwards,” he says.
“So Simon and I thought, ‘Instead of sending people in to do this work, why not use robots: wouldn’t that make more sense from the safety and healthcare perspectives?’ We quickly realised though that existing robots don’t operate well in those kinds of environments. UGVs for instance can’t climb ladders or scaffolding, and most UAVs are too large or have exposed propellers, making them unsuitable.”
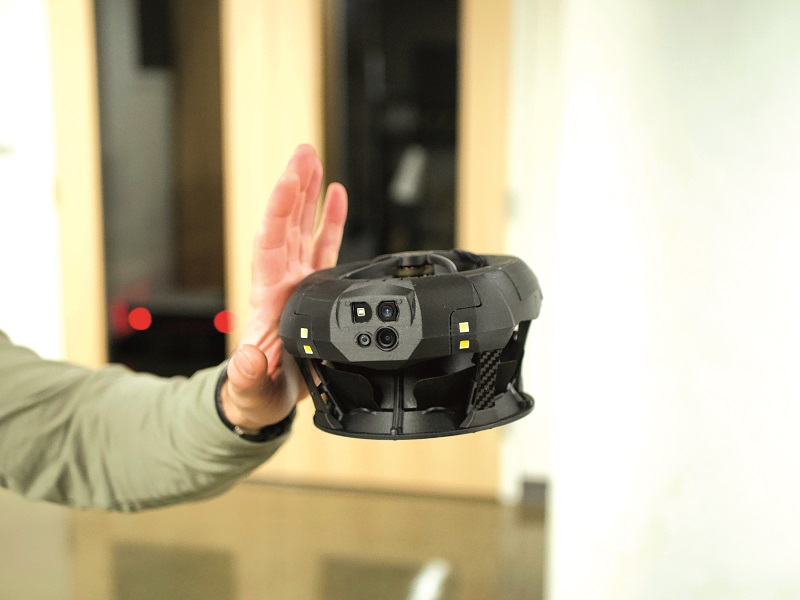
Ducted aerial vehicles
As it happened, part of Eleryan’s passion for aerospace was an interest in ducted aerial vehicles – not the quadrotor type, with four ducted fans, but a proposed design consisting purely of a duct with a fan rotor enclosed inside and the necessary electronics and control surfaces in the duct’s housing.
As a possible point of reference, Reference Technologies’ Hummingbird XRP UAV (UST 27, August/September 2019) uses a ducted and centrally mounted Wankel rotary engine for power and thrust, although its design differs from the ducted aerial vehicle principle by including eight outboard BLDC rotors around the duct for VTOL-transitioning and attitude control.
“I realised that a ducted air vehicle would be ideal for flying into chemical tanks and other tight, hazardous spaces for various reasons,” Eleryan explains. “One, they’re very thrust-efficient relative to their size, meaning they can be made a lot smaller than quadcopters of a similar power output, and second they can carry more weight, meaning more sensors and more computational power.
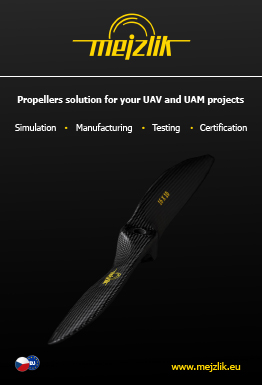
“And of course, the fact that the propellers are shrouded is essential, because no matter how much intelligence you have on board in your obstacle recognition and collision avoidance system, it’s still really easy to bump into a wall or pipe, or snag a blade on a cable. Any kind of catastrophic failure in those kinds of environments is going to be costly for the asset’s owner.”
However, ducted air vehicles are inherently difficult to control, which is why very few have been made and none successfully commercialised, despite having been first proposed back in the 1950s. Thanks to modern technologies such as advanced processors, MEMS IMUs and ESCs though, Eleryan and Czarnota saw they could resolve the control issues and make the first commercially viable ducted (and uncrewed) aircraft.
Design and materials
The result of that, the X1, was unveiled in 2022. It weighs about 440 g and is built largely from polycarbonate. Very little carbon composite is used, as prioritising impact resistance over weight is more important to the Dronut’s design than strength alone, given the impacts it might suffer when in use.
“Also, carbon composite can act as a Faraday cage for radio signals, which isn’t good for maintaining clear data links for video and commands between the X1 and its operator,” Eleryan says.
While putting antennas on the outside might have been a feasible workaround, such an approach would have left them unprotected against impacts, and so gone against Cleo’s electronics integration philosophy.
The X1’s body consists largely of the duct itself, which is thicker towards the top for housing more electronics, and thinner towards the bottom. All the perception sensors are currently integrated at the front (turning as necessary towards whichever direction it needs to travel horizontally), and include a Lidar, a 4K camera and a global shutter camera. Its computer systems are also integrated at the front for easy connections of key data inputs for autonomous navigation and processing.
A battery pack with about 3000 mAh of capacity snap-fits into the upper rear of the body. The pack is made up of three lithium-ion cells in a horseshoe-like shape, to achieve a half-doughnut geometry that conforms with that of the rest of the Dronut’s body. That though is to optimise the pull and flow of air into the duct, not necessarily for aerodynamic efficiency in forward flight.
The two triple-bladed thrust fans sit in the middle, while four flaps sit around the bottom of the duct, being electromechanically actuated during flight for attitude control. Eleryan adds that the fans are also polycarbonate, and their shape as well as the duct’s geometry have been optimised in-house to the point that no Dronut has ever needed a prop replacement.
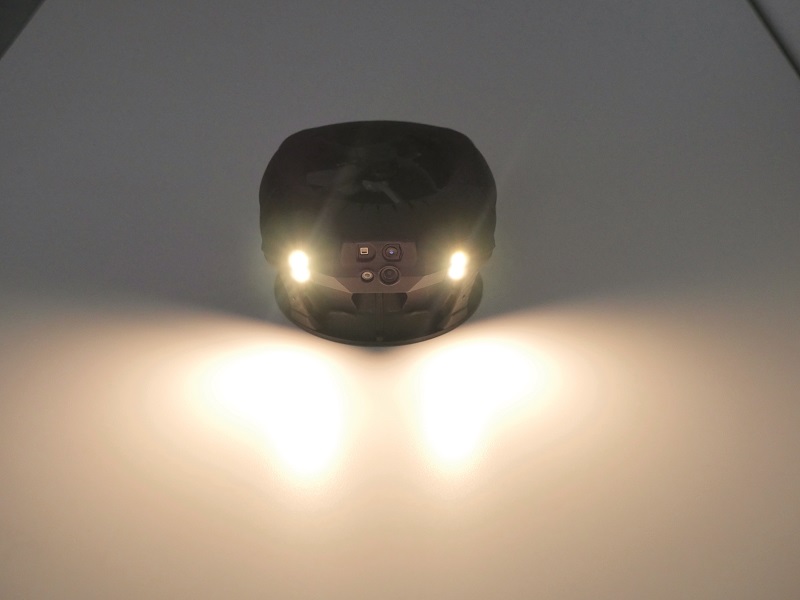
Launch procedure
To date, the Dronut has been successfully used by numerous organisations around the world, including some governments and Fortune 500 companies, Eleryan says. “Some of our customers use it for inspecting inside tanks, pressure vessels, vents and mine shafts, although some also use it for factory floors where theoretically another, more matured or cheaper UAV could have been used,” he says.
“One major car manufacturer here in the US used the Dronut above their factory floor, and we asked them why they didn’t use another UAV. They said that using pretty much any other kind of drone would have triggered their health and safety people to get involved. They’d then have to start barricading inspection areas, making sure no-one was around, and similar things that disrupt factory operations and make it harder to maintain productivity.
“But they said that with the Dronut, it is safe enough and small enough that the health and safety people don’t have a problem with it – they let it fly overhead while the factory workers continue with their day. People can bump into our drone, or push it away with their hand, and neither party is harmed.”
In addition to the safety of having a solid wall of ducting around the propellers, the Dronut is inherently easy to use, with its requirements for launch being very minimal.
Before launching, some visual inspections are recommended, such as checking that camera lenses are free from dust or any other debris that could hamper perception or photography. Similar checks of the propulsion and servo motors are also recommended.
“We haven’t received our IP ratings yet, but we know the Dronut has worked well in beta tests with customers, in-house trials in some pretty harsh environments, and similar trials conducted by independent third parties on our behalf,” Eleryan says.
The X1 automatically activates and establishes a 2.4 GHz wi-fi link with the operator’s tablet GCS. The process takes around 40-60 seconds, after which the user can begin flying.
The standard-issue tablet is a Navigator Tab 3 system from UXV Technologies, although Cleo is flexible regarding the Dronut’s control software, to the point that smartphones can also be used as GCSs, or combined with PlayStation-type controllers for when an in-the-loop operator wants to take manual control for ad hoc point inspections or other purposes.
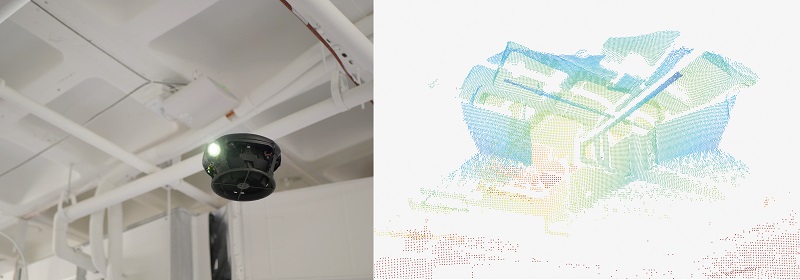
Flying inside storage tanks
The Dronut’s flaps operate on the basis of thrust vectoring principles, much like a rocket or Harrier jump jet. As air is drawn down into the duct by the fans, the flaps – which typically are pointed downwards at rest – are individually actuated to hug inwards. That redirects the airflow as it streams out of the bottom of the duct.
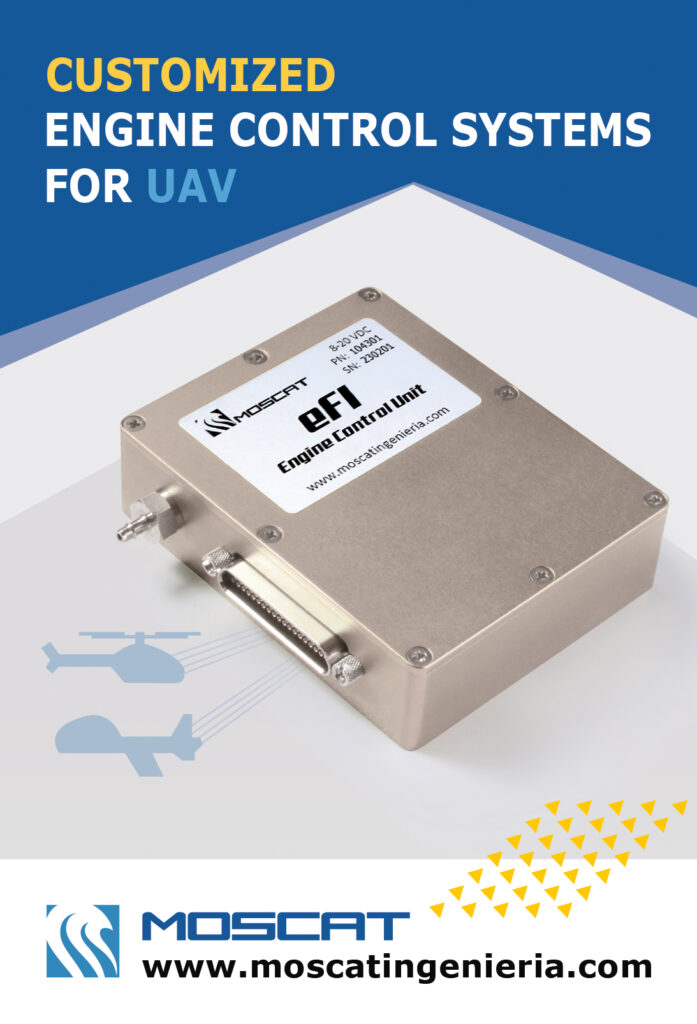
“You would do that with a rocket’s exhaust gases, or tilt the nozzle, which causes the rocket to manoeuvre in the general direction of where the air’s being sent; our UAV changes its attitude the same way,” Eleryan says. He adds that finding servo actuators small enough – and indeed, finding everything small enough – was a challenge during development.
To ensure safe manoeuvring through narrow spaces, Cleo’s software is designed to control and take inputs using multiple components, not only its forward cameras and Lidar, but LED lights for illuminating areas ahead of the UAV.
“The LEDs and Lidars are key, because in these sorts of missions it’s inevitable that you’re going to end up in very dark spaces where vision doesn’t work very well,” Eleryan explains. “In the event that those aren’t enough – say the X1 flies into a 100 ft-radius tank, where the LED and Lidar ranges aren’t long enough – then we can fall back to remote control [potentially by a pilot standing by the tank] until the sensors can pick up points of reference for time-of-flight measurements within their ranges again.
“Even if you have a high degree of autonomy and collision avoidance, there is still a risk of failure due to lighting conditions or lack of features, and we’ve seen instances where commercially available UAVs would respond by just veering off to one side and crashing into a wall.
“And even if that were to happen to us, the severity of the impact is limited thanks to our 4 m/s maximum speed, and the propellers and electronics are guarded well enough to prevent a catastrophic failure in most instances.”
In addition to flying for 12 minutes between charges, the Dronut can land and continue surveilling a target or corridor, if flight is unnecessary for a given objective. The battery contains enough energy for up to 60 minutes of operation without flying, such is the sensor and onboard computing power.
Primary perception comes from the 4K vision camera, with the Lidars acting as a secondary perception tool to verify or substitute the camera data as necessary, as well as an inspection tool. The Lidar’s point clouds are outputted for the end-user to download and analyse after the mission.
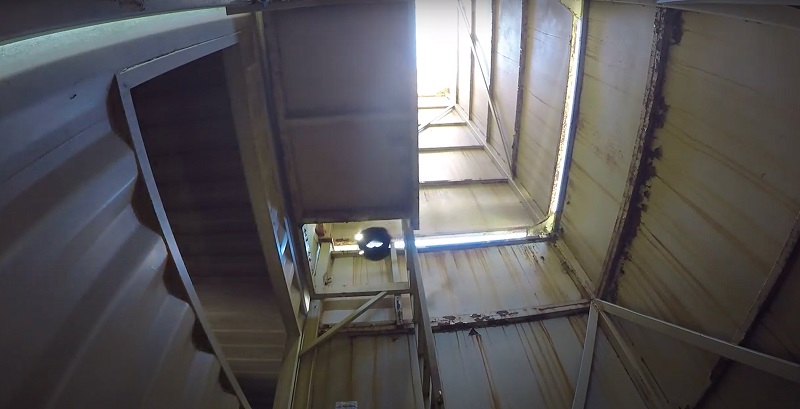
The Lidar itself is a photonic mixer device sensor from PMD Technologies. Its system integrates a sensor element as well as its electronics for signal processing on a single silicon chip, enabling highly accurate measurements in an industrial-grade housing. Also, its small laser light spot makes it suited for detecting small parts and details, not only for high-resolution mapping but 3D modelling and inspections as well.
“We get a 100 x 100o FoV with each Lidar, and an effective range of up to 6-7 m,” Eleryan says. “That’s ideal for the kinds of confined spaces we want to work in.”

And while Lidars tend to be the most power-hungry system on a UAV, he adds, “They’re actually very low SWaP, which again is something that’s inherent in the PMD design, and helps us get the most out of our batteries.”
As mentioned, a 4K camera, a global shutter camera, and the PMD Lidar are installed at the front, although in the near future Cleo plans to upgrade the X1 with several additional 4K cameras and four more Lidars (along with an improved radio), distributed about the airframe for full awareness of its surroundings in all axes.
“We already have a fair amount of overlap with our sensors’ FoVs in the front, and with the new design there’ll be some overlap at the rear and sides, though not as much, because naturally the idea is that users will still primarily fly the UAV forwards,” Eleryan says.
Real-time decision-making regarding flight trajectories and position holding are performed using a Qualcomm Snapdragon SoC, which processes sensor data to determine the optimal flight control logic, with some additional ARM processors for handling ancillary tasks in a dedicated manner. The vision and Lidar in particular are key to correcting the drift that MEMS IMUs inevitably suffer from.
As the Dronut flies, a 2.4 GHz MIMO radio from Microhard (which is likely to remain Cleo’s comms supplier) enables a generally persistent link between the UAV and GCS for control as well as live video telemetry. The often metallic operating environments in which it flies enable transmitted signals to be bounced along to their receiver in most cases rather than suppressed.
“It’s an industry-standard and very lightweight radio design; we know other UAVs that are contemporaries of the Dronut in application terms use the same or similar models,” Eleryan adds. “We’ve also sought to integrate our antennas as far away from our propellers as possible, to minimise interference.”
At mission’s end
At the moment, an autonomous return capability to allow the Dronut to make its way back to its launch point is being developed and will be released with the upgraded version soon. Until then, the Qualcomm Snapdragon integrates automated warning messages to let the operator know when the battery’s energy or comms signal strength is running low. The Dronut will automatically land if either is close to a total loss, for the operator to retrieve it.
Once it has been recovered, the lenses, control surfaces and propellers can be cleaned. The battery can also be removed and charged, which takes around 40 minutes, although naturally a pre-charged pack can be plugged in if the X1 is needed quickly for another task.
Future r&d
On top of adding more perception sensors to the Dronut and upgrading its radio, Cleo plans to research and improve a few areas of its performance. One is the reduction and mitigation of noise. As discussed, some end-users actively seek to have the Dronut flying around people, and while Eleryan notes that the X1 is “not painfully loud”, he concedes that it is not quiet either.
“In most of the use cases I’ve mentioned, noise isn’t a concern, because factory floors for instance are pretty loud already, but it will become critical in our next phases as we look to inspecting quieter industrial assets,” he says.
Improving propeller designs will form a key part of Cleo’s r&d in this respect. Here, Eleryan nods towards the toroidal propellers recently unveiled by MIT Lincoln Labs, not far from Cleo Robotics’ base, as an example of how such noise reduction can be achieved. Lastly he adds that increasing flight times to around 20 minutes and enhancing the X1’s autonomous capabilities are also on the cards for this year.
Specifications
Dronut X1
Ducted aerial vehicle
- Weight: 440 g
- Dimensions: 16.5 x 10.1 cm
- Maximum flight endurance: 12 minutes
- Maximum endurance during stationary observation: 60 minutes
- Charging time: 40 minutes
- Maximum airspeed: 4 m/s (software-limited)
- Maximum wind speed tolerance: 15 kph
Some key suppliers
- SoC: Qualcomm
- Lidar: PMD Technologies
- Radios: Microhard
- GCS: UXV Technologies
UPCOMING EVENTS
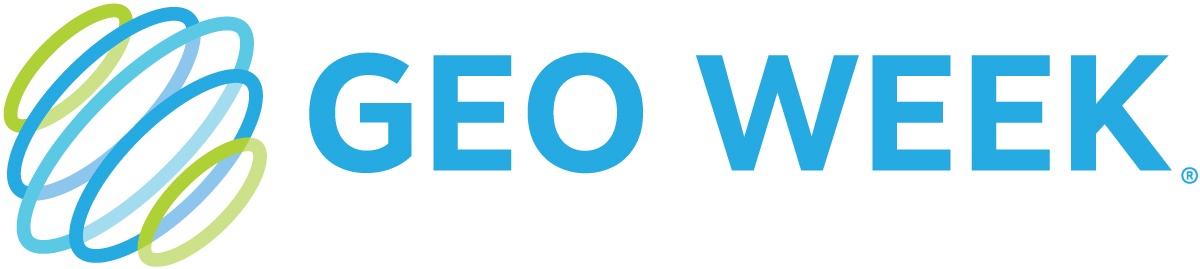
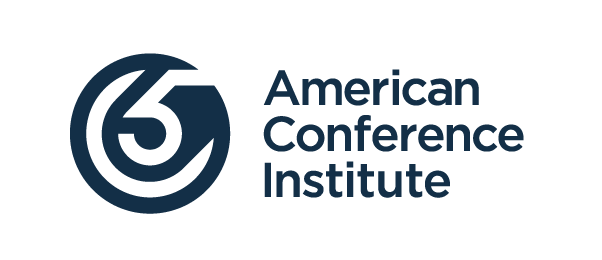
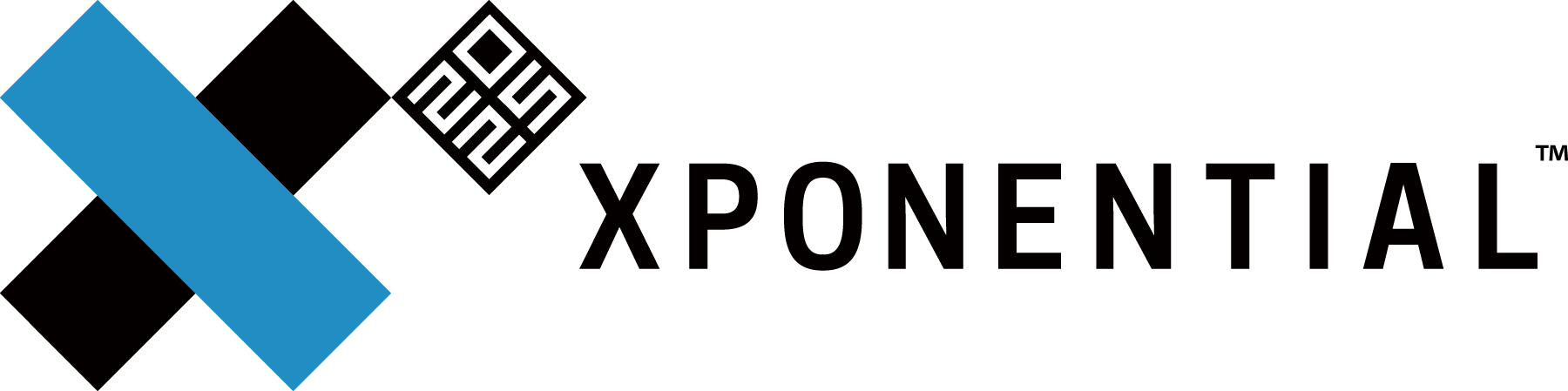
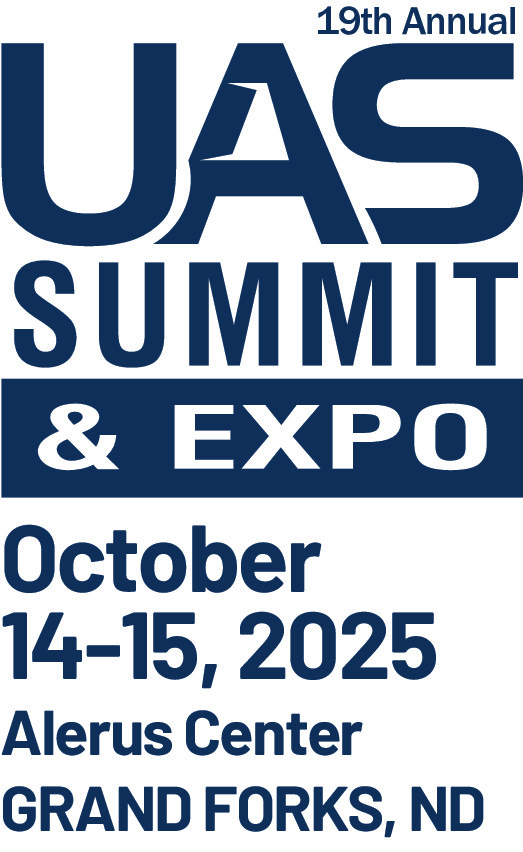
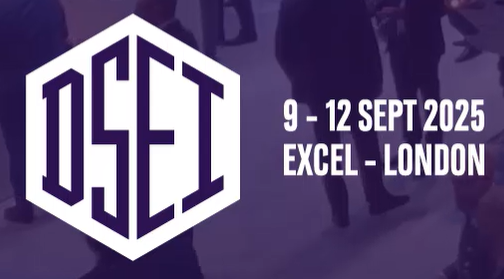
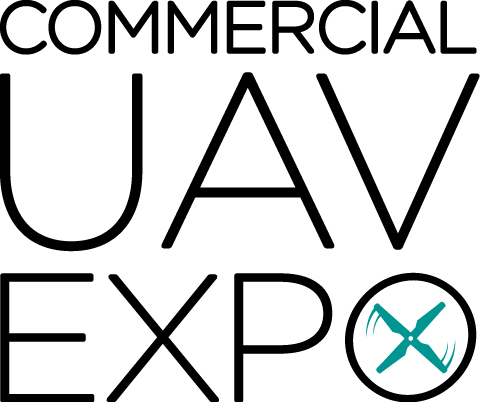
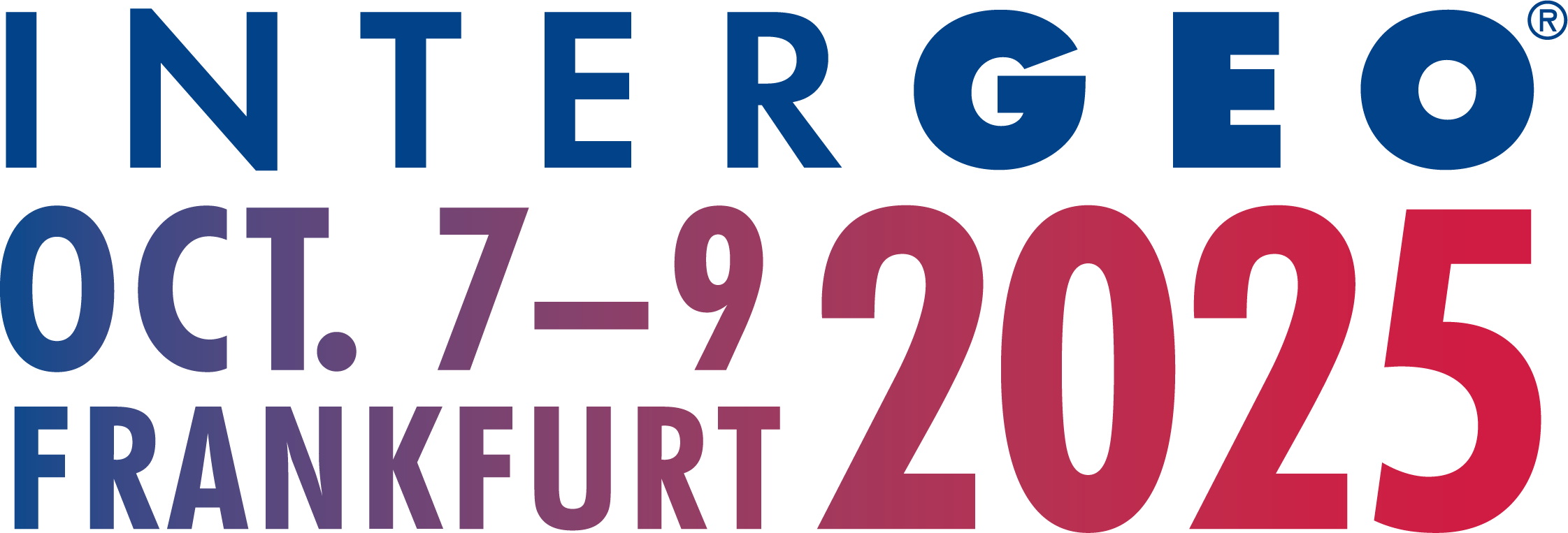
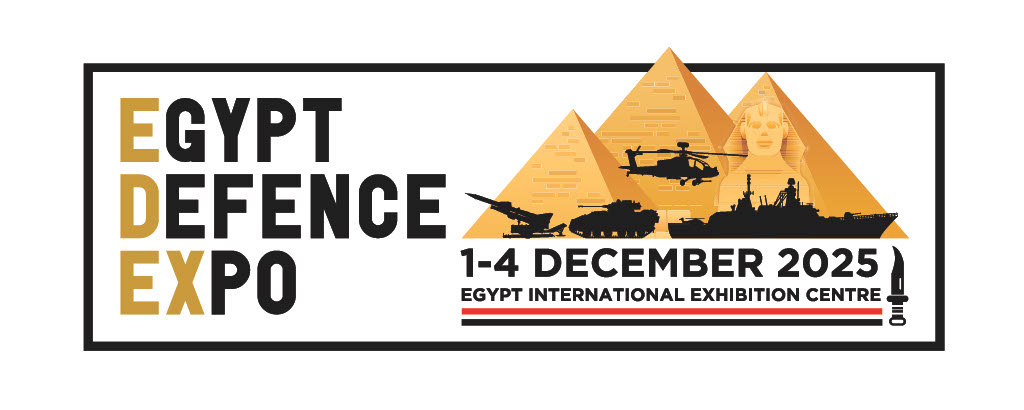
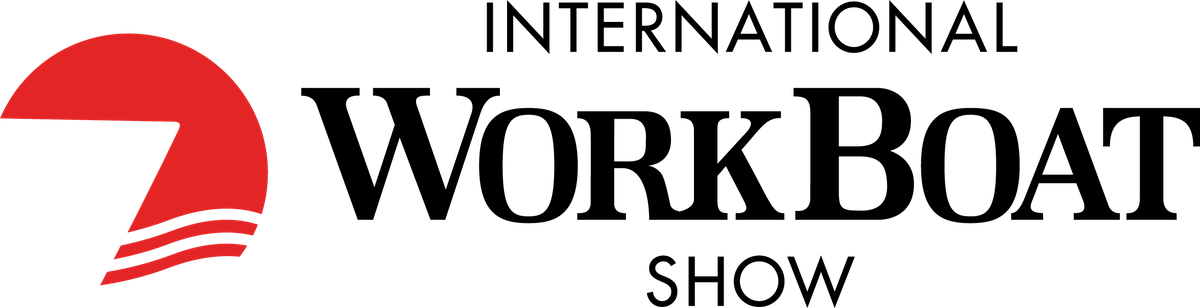
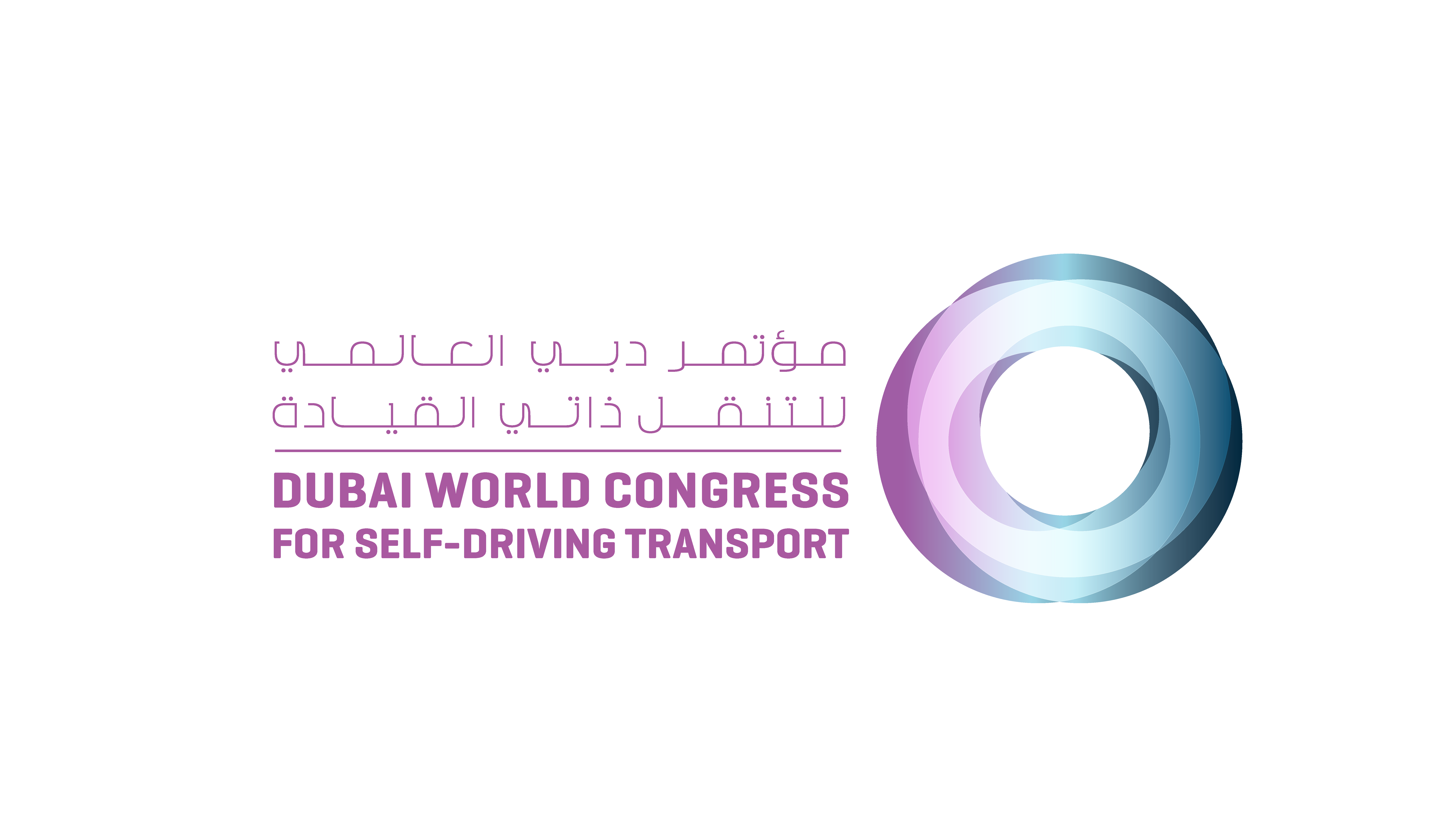
