Xer Technologies X12 and X8
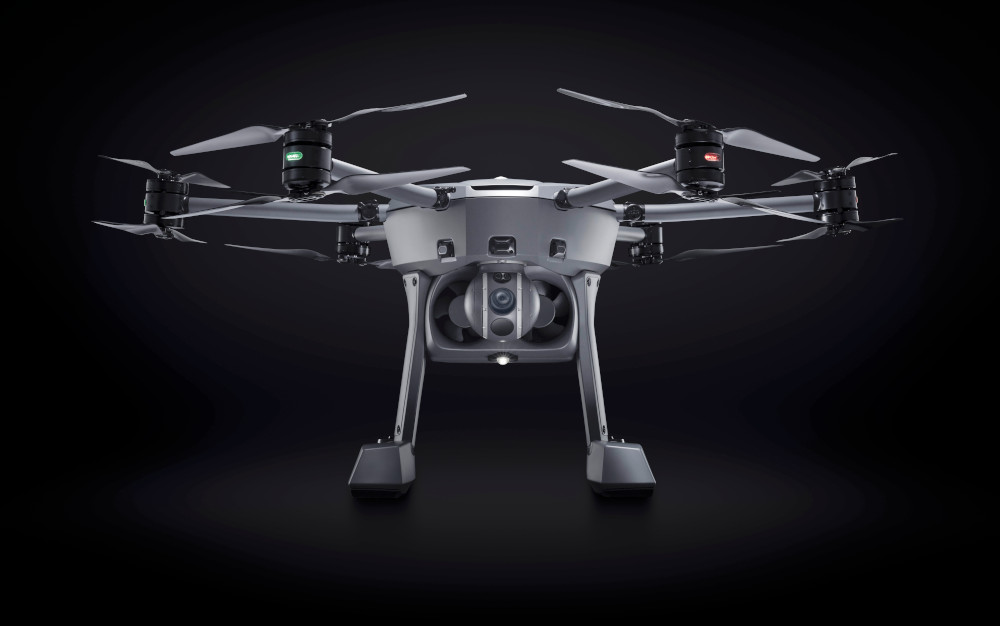
(Images courtesy of Xer Technologies)
The X factor
Rory Jackson traces the development of these electric multirotor UAVs that feature gasoline two-strokes for range extension…
While Xer Technologies might be regarded as something of a newcomer to the world of UAV manufacturing, it is not a novice in the sector. The seeds of this Swedish OEM were planted about 10 years ago, and come from a company tasked with monitoring railway stations in the south of Sweden for vandalism on trains and to buildings. After several years, it determined that aerial surveillance would be far more efficient and less labour intensive, and began researching tools to enable that transition.
For the past 10 years the team, led by security expert and current COO Joakim Palsson, elected to fly inexpensive consumer UAVs to look for graffiti artists and other acts of vandalism around rail stations. Eventually the group was acquired by a larger security company, Bevakningsgruppen, renaming it UAV Development Sweden and assisting in the arrest of nearly 550 offenders as a result.
After some years of flying, the team gradually became concerned that the tools being used were not sustainable. Having to land every 20 minutes to recharge or swap batteries amid the blustery Swedish weather was impractical and deeply cost-ineffective. They also discovered that the performance and longevity of their consumer-grade batteries was far from what their vendors claimed.
In the summer of 2021, Bevakningsgruppen sold UAV Development Sweden to a Singaporean company, Xer Technologies, in which a gas company named Rex International Holding bought a stake and committed $4 million towards UAV development. The company’s first products, the X12 and X8, were unveiled in October 2021.
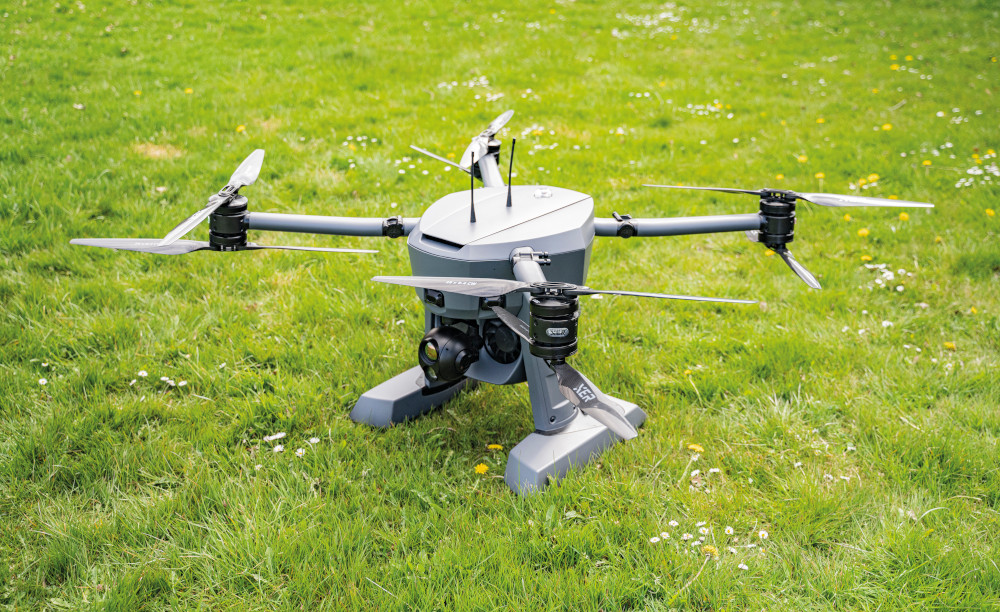
“It was about 3 or 4 years ago that the team started prototyping their ideal work tool,” says Kristofer Skantze, who moved from Rex in June 2021 to his present role as CEO of Xer Technologies. “This was to be an electric multi-rotor UAV equipped with a two-stroke gasoline range extender to carry out long-endurance monitoring, surveillance, inspection and public safety missions.”
The X12 is the larger of the two aircraft, at 75 cm tall and 248 cm across. Its MTOW is about 67 kg, and it has a payload capacity of 20 kg, as well as an airframe notable for its X-12 configuration. This features 12 electric motors and propellers mounted across six carbon tube rotor arms that extend from a carbon composite hub, powering the craft for a 4 hour maximum flight time. The hub also holds a frontal payload bay, sensor mounting racks underneath and two large cooling fans.
The X8 closely follows the design of the X12. It is an octocopter, and has been designed to meet the 25 kg weight limit set by regulations in Europe, North America, Australia and many other places. It therefore has a 2 kg payload capacity and a smaller power unit than the X12, but it delivers about 2.5 hours of flight time. It measures 63 cm tall and 203 cm across, and while smaller than the X12, both can achieve a top speed of 50 kph and position-hold amid rain, snow
and even winds of up to 18 m/s.
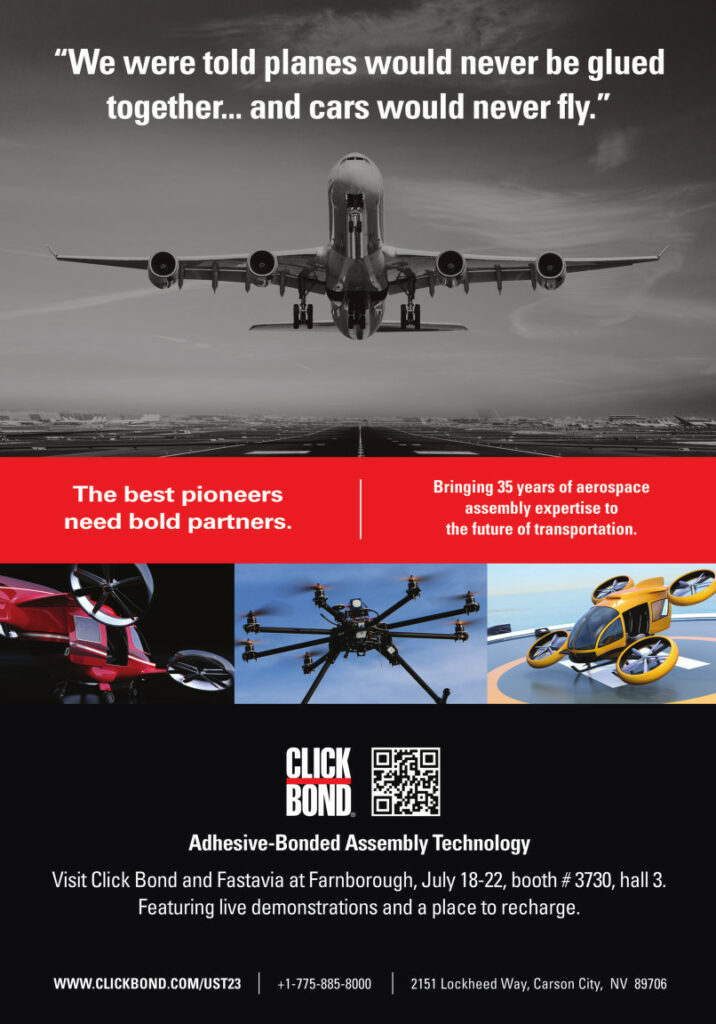
Much of Xer’s early components were made in-house, owing to what the company describes as the professional uncrewed industry’s lack of manufacturing maturity at the time and its lack of variety, affordability and supply chain security for its plans. These days, Xer’s engineers source many parts from a range of high-end suppliers before modifying some of them, and also draw on the local high-tech scene in Sweden wherever suitable, with the goal of achieving a UAS as capable as any of those from leading manufacturers.
In particular, the X12’s and X8’s capabilities in heavy lifting, seamlessly switching in and out of stationary hovering, and environmental ruggedness, open up numerous mission capabilities that were previously challenging for some users to access or afford.
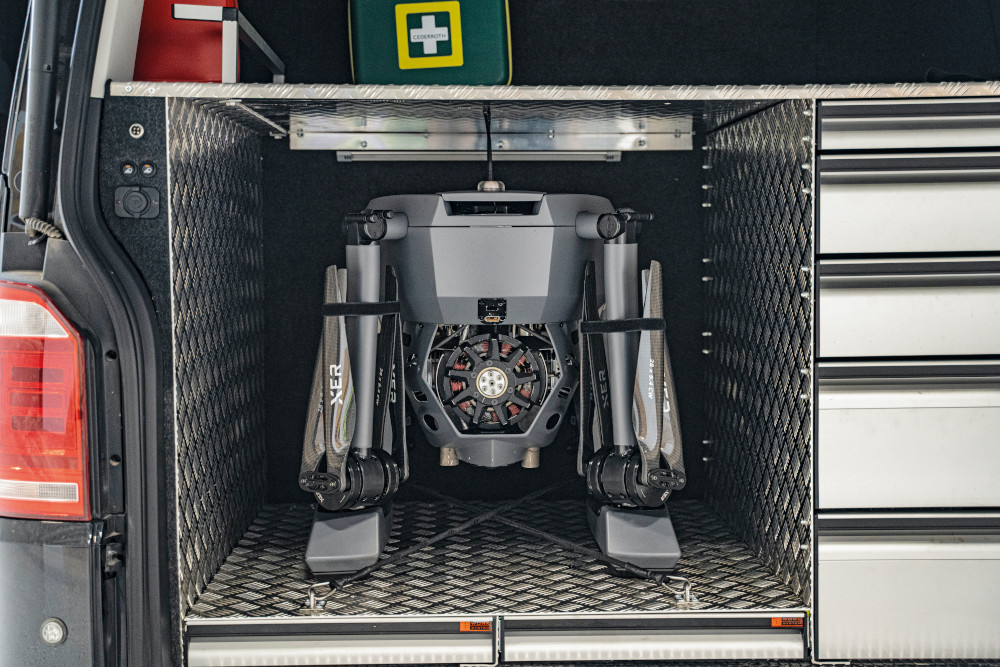
Given its roots in monitoring transport hubs, long-distance inspections of large industrial infrastructure are a focal point for Xer’s UAV development. However, Skantze and his team are also starting to supply their UAVs to many other applications across Europe and beyond.
“As one example, with our endurances, carrying capacities and high electrical supply capacities, we see a clear value proposition to coast guards, border control and other government agencies for constant monitoring of national borders,” Skantze says.
“Furthermore, we can perform environmental monitoring at a fraction of the cost of some of the alternative high-end UAVs on the market. That entails several very different mission sets, such as tracking endangered species and poachers, or surveying the exhaust plumes from large container ships for regulatory compliance.
“We’ve also connected with several search & rescue organisations for future sales, as well as the UN. For them, we are looking to start investigating how we might use the X12 and X8 to find landmines, using Lidar, IR or other sensing payloads. It would be fantastic to find that our aircraft can indeed help clear land of dangerous munitions.”
Engineering challenges
The two most critical targets for Xer’s r&d have been specific energy (energy-toweight ratio) and energy density (energy to volume). While the company considers itself agnostic regarding propulsion technologies, it knew early on that it could not possibly hit the flight times it wanted on battery energy alone.
“Even though there have been great advances in the specific energy of battery technologies since we started development, they have plateaued significantly in recent years, and we couldn’t take a wait-and-see approach for better batteries,” Skantze comments.
“As far as zero-emissions options go, we initially had a serious look at hydrogen fuel cells, and there are now some excellent systems out there.”

He adds however that while the specific energy of hydrogen gas is almost unbeatable, its energy density is lacklustre. Unless the hydrogen is liquefied or compressed to 700 bar (which makes certification of componentry difficult), large tanks must be used, which are difficult to fit inside a multi-rotor airframe. Also, the slow ramp-up rates of fuel cells compared with reciprocating and rotary IC engines, would hamper quick transitions between hover, cruise and top speed.
“Gasoline has around 100 times the specific energy and energy density of lithium-ion batteries, which makes it viable for our UAVs,” Skantze notes. “Furthermore, gasoline supplies and engine parts are far, far easier to secure than those for hydrogen at the moment, although if the hydrogen economy continues its pace of advance over the next few years, that could potentially be enough for us to consider switching.”
Arriving at this conclusion for the choice of power system – and for the various other onboard components – was by no means a linear path. Skantze describes the bulk of early r&d having been “garage engineering”, which eventually
progressed into the professional laboratories and development processes used internally now.
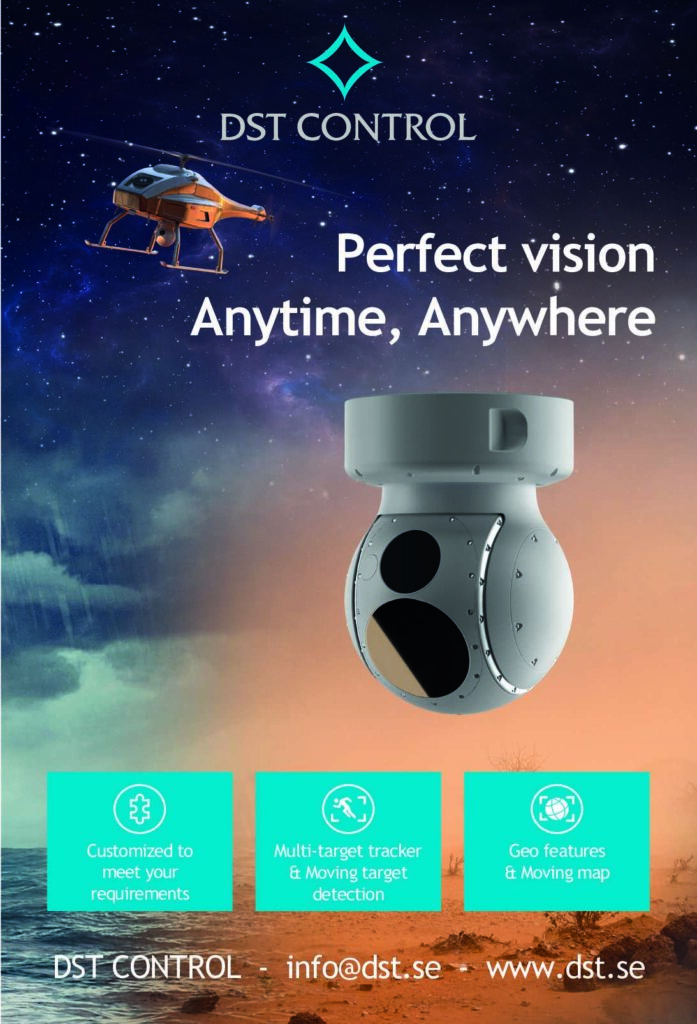
By ‘garage engineering’ he means that non-stop testing, iteration and analysis of different assemblies of UAVs were the order of the day between 2018 and 2021, with one 3D printer and some helpful suppliers of carbon fibre and CNC machined aluminium providing new airframe pieces as needed. The team pursued how they might maximise flight times, resolve other key engineering or operational issues, find the best suppliers for their most helpful components, and learn from mistakes along the way.
“For instance, one day we’d find our airframe was too weak, leading to vibrations and resonances that interrupted flight stabilities,” he recounts. “Other days we’d trial engines from certain suppliers and find they performed nowhere near what their data sheets claimed, or find that they couldn’t be supplied with the regularity that was promised.
“Gradually we solved one issue after another, with cooling, vibration and power management in particular having been the real sticking points and hence focal points of our development. Those are endemic to hybrid multi-rotor platforms, and interfere with our ability to calculate how power-toweight affects endurance. As such, they’ll probably guide all future component and redesign choices too, except perhaps in subsystems such as autopilots, which as far as we see are well-solved with millions of units supplied worldwide.”
The cooling problem stems from the IC engine generating copious heat, which the X12 cannot dissipate through forward flight alone, as fixed-wing aircraft can, so a complex thermal management strategy is critical to preventing hazardous buildup of heat spreading outwards from the engine bay.
Vibration is of course perennial throughout the industry. Resonances threaten to shake airframes apart, for Xer as much as any UAV company wanting to pack power units with moving parts into tight spaces.
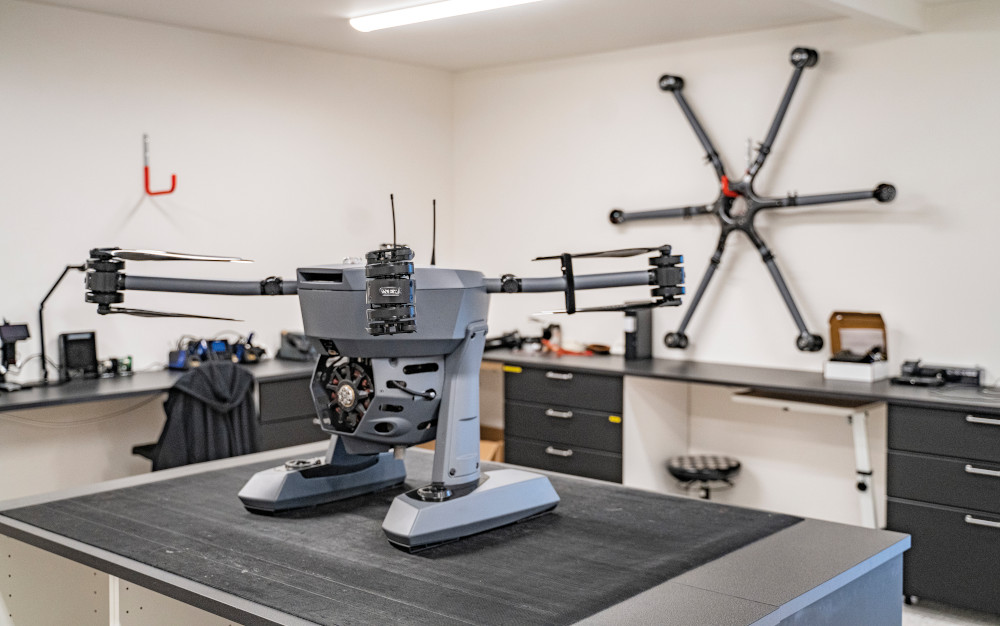
“As for power management, there is between 70 and 160 A flowing throughout the X12 at any given time, which means we need good knowledge about soldering, switches and the many related components and dynamics,” Skantze says.
“And every connection point must be secure against vibration and not produce excess heat. Handling all these interrelated problems has been a major headache, but we’re now flying and have a comprehensive understanding of what works and what doesn’t.
“We know for instance that we can’t just buy off the shelf; we use many fantastic suppliers but almost every component is taken apart, modified and put back together to optimise for our use-case. Barring producing all our parts in-house, we need that kind of re-engineering of supplied parts to make and sell a UAV of such quality that we’d want to use it ourselves.”
The company’s coastal location, in Helsingborg, southwest Sweden, has enabled thorough validation of its aircraft in windy, wet and salty conditions ranging from -15 to +35 C. With the final version of the X8 having logged hundreds of hours of bench and flight testing, the first units will start trials with clients later this year, and series production and supply are planned to start by early next year.
“We’ll have constructed a modest number of X8s by the end of this year, with a minimum fivefold increase in manufacturing capacity a year after that, and a projected tenfold increase in production and sales by the close of
2024,” Skantze says.
Multi-rotor overview
As mentioned, the X12 has six rotor arms mounted evenly about a hexagonal hub, with ESCs installed in the arms and a pair of electric motors at the end of each arm arranged coaxially.
Opening the hub’s lid reveals Xer’s ‘starfish’, an arrangement of structural walls that interconnect and lock the mounting brackets for the arms, which extends from the top of the hub downwards and doubles as a frame of mounting surfaces for most of the internal electronics. As well as providing enough space and threads for mounting, it has also been designed to distribute the internal weight of the X12 such that the CoG is stabilised and kept low in the airframe.
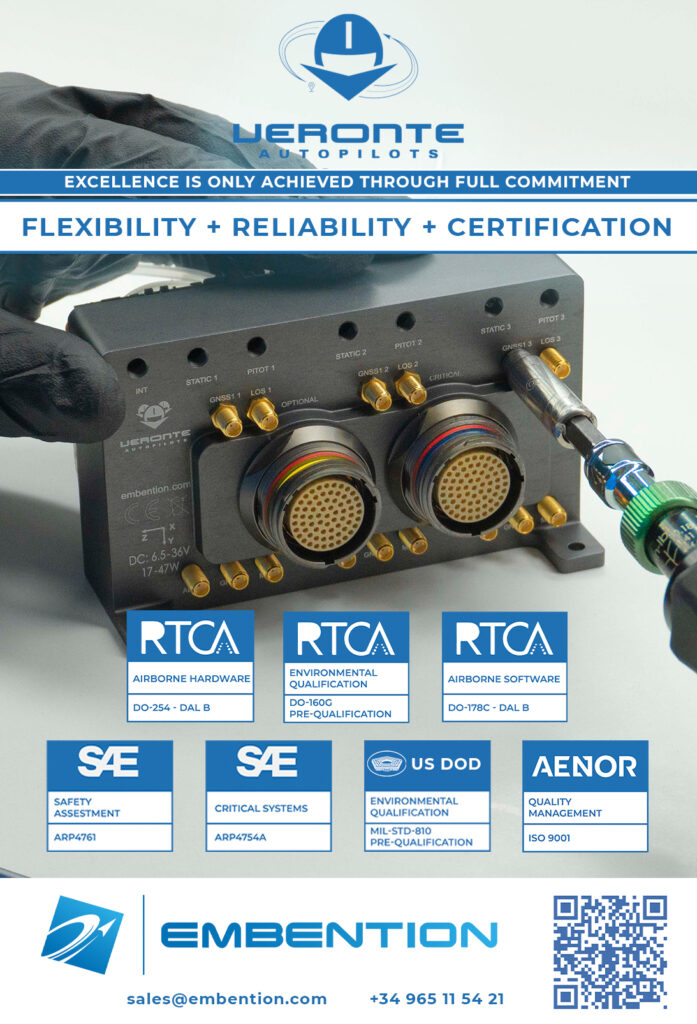
“The cover can also be exploded off by a built-in parachute we include as part of the standard configuration, which is installed inside the top of the hub, at the level of the arms, and deploys autonomously using a pyrotechnic charge,” Skantze says.
Beneath the starfish in the top enclosure are most of the electric and avionics systems. These include the batteries, which serve as balancers for electrical loads and for the CoG (and it also provides back-up energy in the event of an engine malfunction), the autopilot, navigation systems, power management unit (PMU), and an engine management board developed in-house to handle the running and cooling of the engine.
Below these is the engine compartment, which is completely isolated from the avionics chamber. Inside it is the engine, an alternator, a fuel pump, an EFI system and the cooling system.
“It’s important to note that we’ve developed two cooling systems: an air-cooling system that’s the base configuration, and a water-cooling system for end-users who maybe expect to be flying in temperatures of upwards of 40-50 C. Both configurations have been successfully tested,” Skantze adds.
Forward of the engine compartment are the payload gimbals and other mission installations, and beneath are the X12’s legs. Fuel hoses run inside the legs, with the ‘feet’ or pontoons containing the fuel tanks (also helping to keep the CoG low) as well as comms antennas, while the GNSS antennas sit atop the hub.
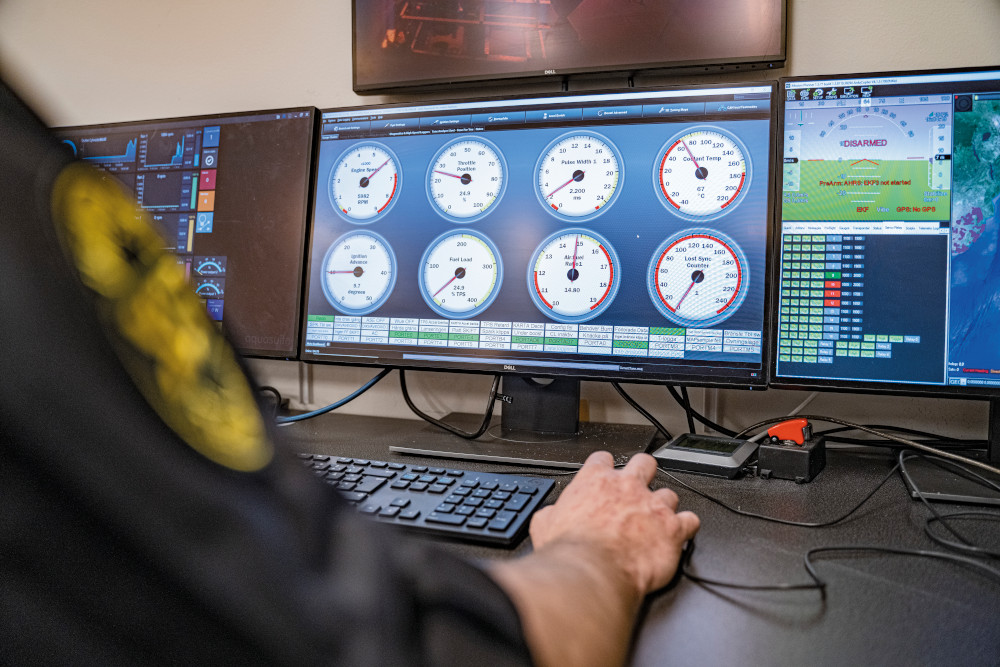
“One thing we’ve tried to optimise is the useability of our UAVs,” Skantze says. “That’s why for instance we’ve gone from rotor arms that had to be screwed in to ones that snap into place in seconds simply by folding outward, and clicking into the lock position at the correct angle, all without the need for tools. Then a manual unlocking of the arms is quickly performed after the UAV is recovered.”
While the 25 kg X8 is portable by a single person, Xer recommends two personnel carrying it and the X12 from a road vehicle – especially the X12, given that it weighs more than 60 kg when fully loaded and fuelled. With two trained personnel, either UAV can be set up in 30 seconds, with a short period after for electronic start-up and engine warmup
before take-off (notwithstanding any waypoint programming, geo-fencing or other mission planning details not addressed beforehand).
“The more you need tools, or to handle cables or screws or the like, the more things can get damaged, lost or otherwise go wrong in the field,” Skantze comments. “All the parts of the starfish – the hull, arms and folding and locking brackets for the arms, as well as all the structural fittings and mounts – have been developed in-house. They seem like minor things but for the feel and useability of the product, not to mention its stability and vibration damping, they are major technological IP.”
Airframe structure and materials
As mentioned, rapid prototyping and the supply of composite and metal parts have been critical to the r&d of both UAVs to date. To that end, Xer Technologies uses local suppliers for its CNC-machined metal parts and carbon composite. Both suppliers serve effectively as extended development arms for Xer, which cites geographical proximity, close communication and specialist knowhow as having been key to rapid turnarounds of new parts and hence the speedy evolution of the X1 and X8 designs.
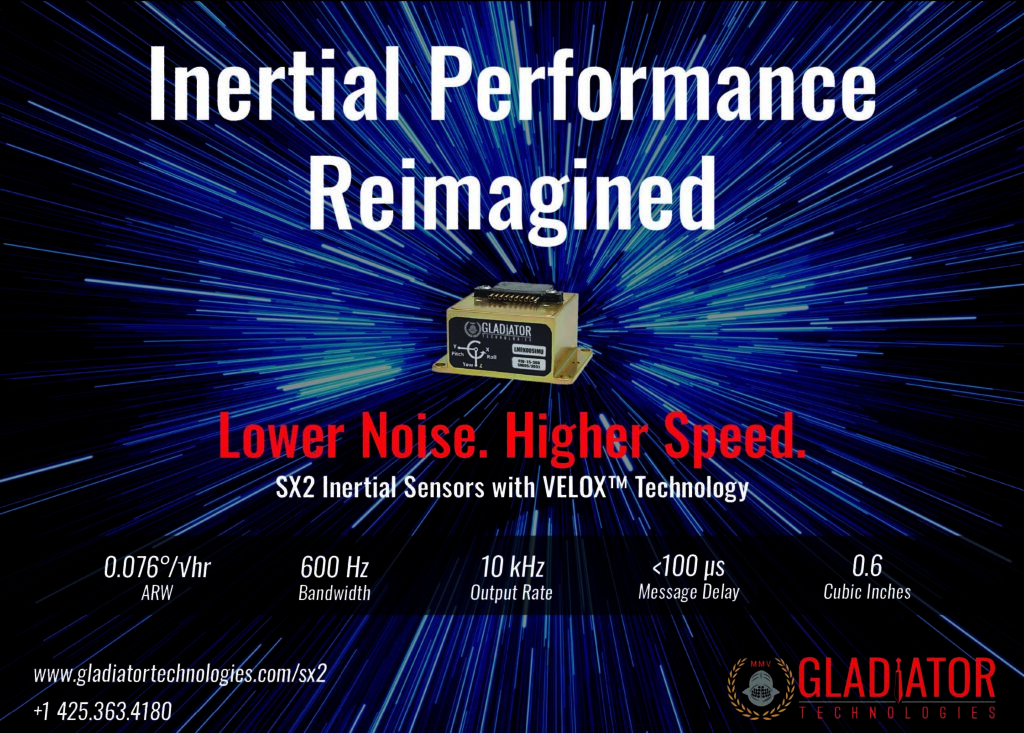
“Their considerable competencies and experience serve as a vital first step for any new design direction we’re considering,” Skantze says. “Outsourcing to high-quality materials suppliers isn’t cheap by any means, but we’ve made a conscious decision not to become a prototyping or materials company. Instead our structural parts suppliers provide our engineers with industrial grade components at almost a moment’s notice along with extremely valuable input as part of a collaborative approach to the engineering of our systems.
“Take for example our CNC partner, who supplies precision-cut aluminium parts for the UAVs. In the past, they’ve delivered lots of parts for high-end sportscars, so they’re used to making very high quality components, and we’ve found them to be an extraordinarily good partner.”
The carbon composite for the hull’s covers, fairings, tube arms and internal starfish structure from another local partner have been similarly supportive, both with rapid manufacturing turnarounds and extensive consultation regarding new designs of carbon polymer parts.
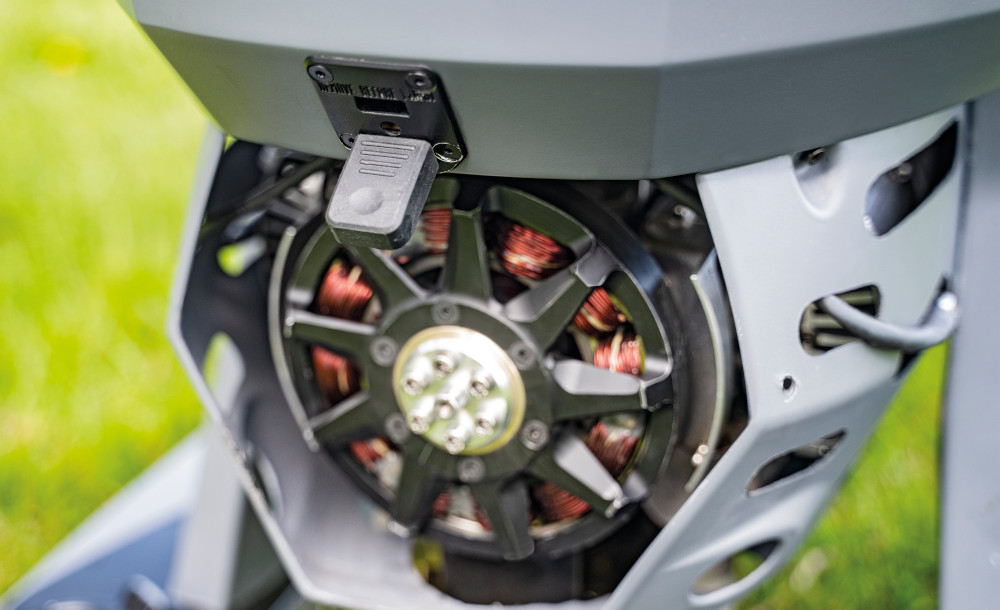
Critical trade-offs between the weight and rigidity of the metals and composites have been made, with Xer finding that lightness in some areas led to softness and hence dangerous vulnerability to resonances. This trade-off, as well as cost considerations, has informed vital choices such as the number of layers of carbon fabric used in various sections of the hull.
“The layers are measured against 3D-printed tooling before being laser cut to exact measurements,” Skantze says. “More layers means more strength, heaviness and material costs, assuming you’re using the same material all over. There’s also the possibility of using fewer layers if you swap to a more expensive and high-end fabric.
“Then there’s the direction of the fibres that you should consider in terms of how stress is transmitted through them. For instance, we could have just made our arms with uniform fibres, but by using non-uniform ones we can better sustain the structure’s rigidity and longevity against the upward lifting force generated by the rotors. Then we compensate for that extra weight in areas such as the hub cover, which suffers no particular stresses and can therefore be made really thin and light.”
What greatly determined the material types, layer counts and directions was the distribution of loading points identified throughout the airframe structure from the testing and CAD simulations the team carried out. Wherever there was more strain – be it from compression, tensile stress, vibration or other issues – higher amounts and quality of fibre were laid up, and the directions of the fibres selected to counteract any directionalities in the strain, without overcompensating and causing torsional stress and additional vibrations.
“Advanced modelling is great but will only get you so far, which is why most of our structural r&d consisted of receiving a new hull part design, bench-testing it, identifying where it would break first and how, then iterating something that improved on it, either with more rigidity or less weight and cost,” Skantze says.
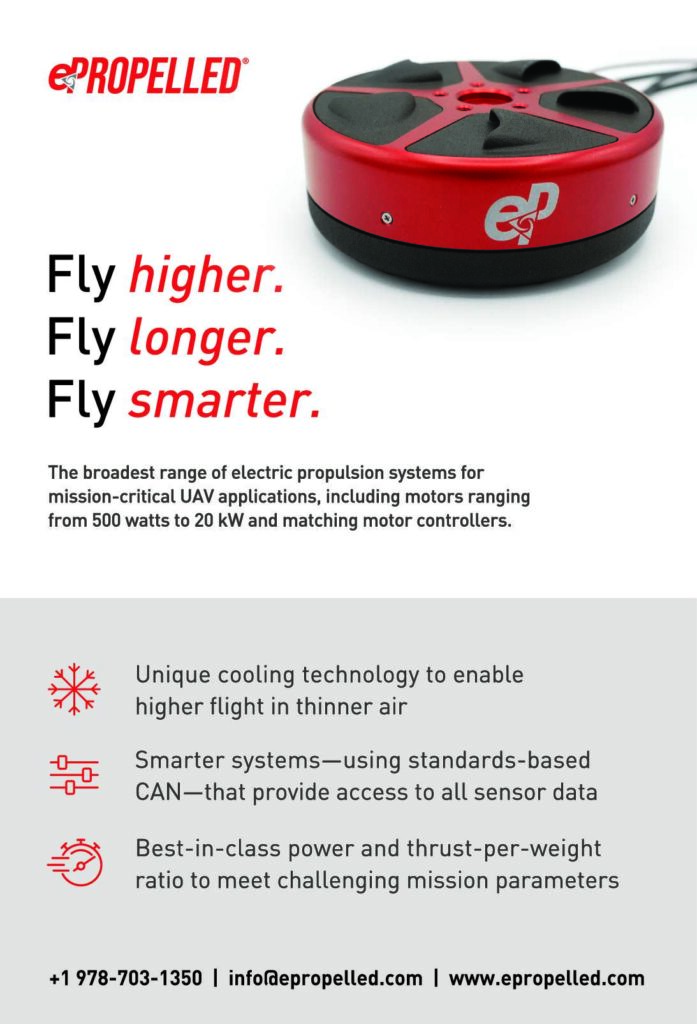
“We’ve carried out a lot of test flights, and several of the test aircraft have sustained crashes with only minor damage; they are sturdy vehicles. So we’re now happy with the design and functionality of the structure, inside and out, and any further changes we make will be purely to target weight reduction, even sacrificing strength where it’s not needed. It might be OK for some structural things to snap in a crash; better to avoid crashing in the first place using either the parachute or autopilot.”
Autopilots
The X12 has used various autopilots, both PX4-based and other independents. The clincher for Xer in selecting autopilots has been the ability to communicate engine data to the GCS.
“That isn’t as trivial as you would expect, as we discovered in-house,” Skantze says. “We have sensors left and right throughout the power unit for rpm, heat, current, battery charge rate and more, and that data has to be sent to the engine controller and the autopilot, then via the antennas to our computer on the ground running GCS software so we – or the end-user – have full knowledge about the health and response rate of the engine.
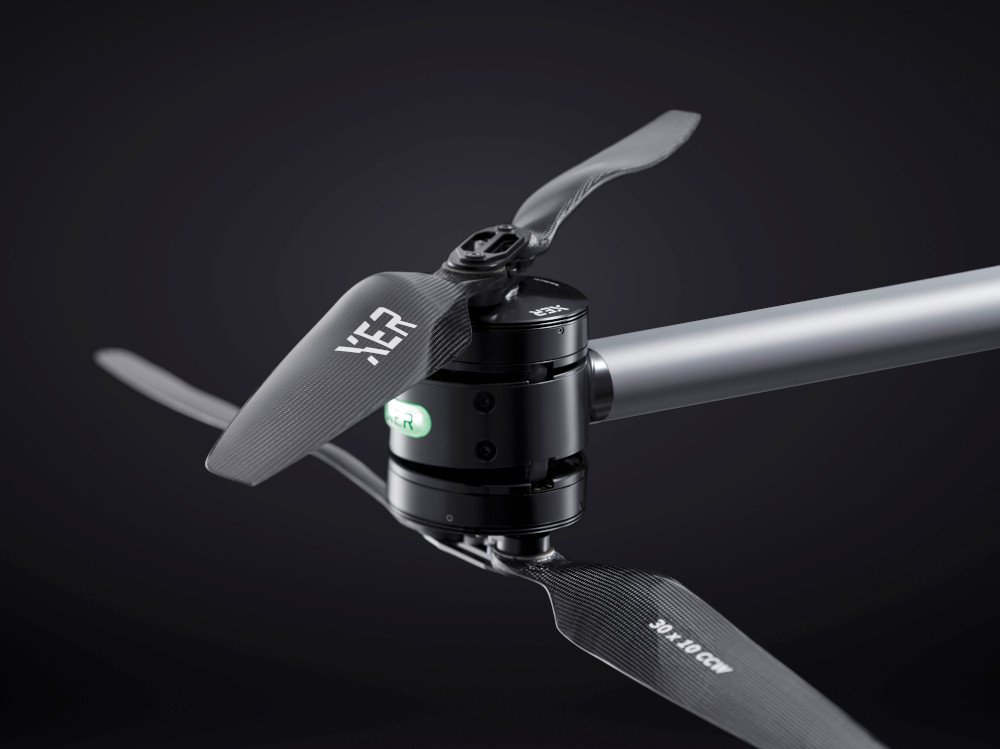
“As an alternative to PX4-based GCSs we’ve also modified the ground control software by working closely with UgCS to be able to interpret and visualise what’s going on throughout the UAV. That also helped to determine the level of information presented on screen, alerts and availability of remote control step-in options for mission safety and the customer’s sense of security regarding their asset.
“We try to build as much autonomy into the UAV as possible. For instance, if the engine runs too hot or suffers certain failures, the X12 will start an emergency controlled landing sequence, but the user must always feel able to intervene as much as is necessary.”
In addition, Xer cites the flexibility, transparency and price of PX4 autopilots as attractive qualities, particularly in terms of changing components ad hoc to meet customer requirements using plug-ins from across the open-source networks.
Data signals run between the autopilot, ECU, payload and comms systems using standard CAN and MAVLink protocols, largely carried over COTS 5-12 V connectors and wires, with most ofthe connection r&d going into the power management system to achieve resistances that are as low as were feasible to minimise their heat dissipation requirement.
“Corrosion can be an issue with low voltage connections, but we’ve protected them in various ways to reduce potential issues. We’ve also gone through a lot of cables and learning for the higher voltage battery and three-phase cables across the powertrain,” Skantze notes.
Gasoline engine
“By far the biggest of our three main challenges was cooling. It’s really difficult to do that well when you have such a lot of energy and power surging through a compact multi-rotor platform,” Skantze says. “In a two-stroke engine, you have maybe 20% of the energy in the fuel being transmitted through the pistons into the crankshaft’s power output; the rest is released largely as heat that needs to be dissipated.”
The engines in both UAVs were therefore modified to respond better to the air cooling from the fans, or to integrate water-cooling circuits instead (Xer declines to say how it solved that issue).
The X12 uses a 170 cc engine, while the X8 has a 120 cc unit. Both are boxer two strokes built mostly from 7075 aluminium.
“We’ve cut up the engines and opened up their cylinders, which is not something you’re really supposed to do,” Skantze says, “But it’s worked out well for us, and solved our problems, and in the long run we will of course look for safer approaches.
“There are good engines on the market, however many of them were designed for running big propellers on their fronts. Not only do we not have those or the air wash they bring but our engines are contained in a protective housing where there would be really bad heat concentration without our proprietary solutions. We devised those with a lot of r&d into getting the volume and flow rate of cooling air or water done correctly, as well as venting air and exhausting it out afterwards.”
By contrast, Xer uses a by-the-book approach to its fuel management, given that such components are well understood and widely available. Aside from the pumps, hoses and many other components, some novel features are installed. For instance, tank foam, such as that used in Formula One cars, is fitted around the fuel tanks to prevent spatters of gasoline in the event of a crash.
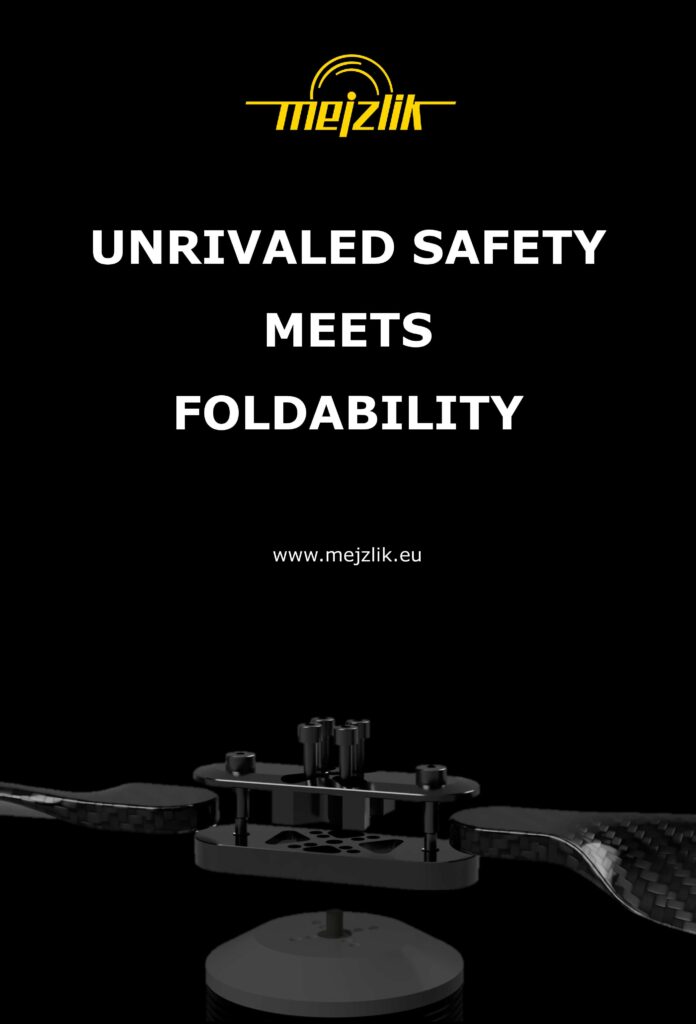
Engine control and cooling are managed by Xer’s proprietary engine controller, which processes data inputs from across the power system to do so and transmits much of them to the GCS. Development of the controller began soon after Xer’s initial purchase of an ECU that was not designed for use on multi-rotor platforms yielded improper throttle control for running the engine in precise power bands.
“We mentioned speed and heat sensors, but we don’t want to overload or distract the user with unnecessary information,” Skantze notes. “It is safety-critical during r&d to keep an eye on things such as crank rpm, cylinder head temperature [CHT], exhaust gas temperature and, if applicable, coolant temperature.
“In general though, not all of those are urgent for the end-user. If we had to keep just one it would be CHT, because if that’s normal it pretty much always follows that the rest of the power unit is fine as well.”
The ECU is worth mentioning alongside the core challenges of cooling, vibration and power management, as it took a lot of design and programming work to tune it for safety and efficiency. Whenever the autopilot sends rotor commands to the ESCs, power management commands must also be sent to the PMU to ensure that power is distributed correctly and that not too much strain is placed upstream on the engine, battery or generator. Logic has therefore been programmed into the ECU to stabilise the engine and generator, and thus stabilise control over the UAVs.
Electric power
The generators are modified threephase brushless AC units from Sullivan UV (now Acutronic Power Systems) that are designed for direct drive on engine crankshafts and use neodymium permanent magnets. The X12 uses a 7.2 kW alternator, although peak electric power delivery is capped at 6.5 kW, while the X8 has a 5 kW system.
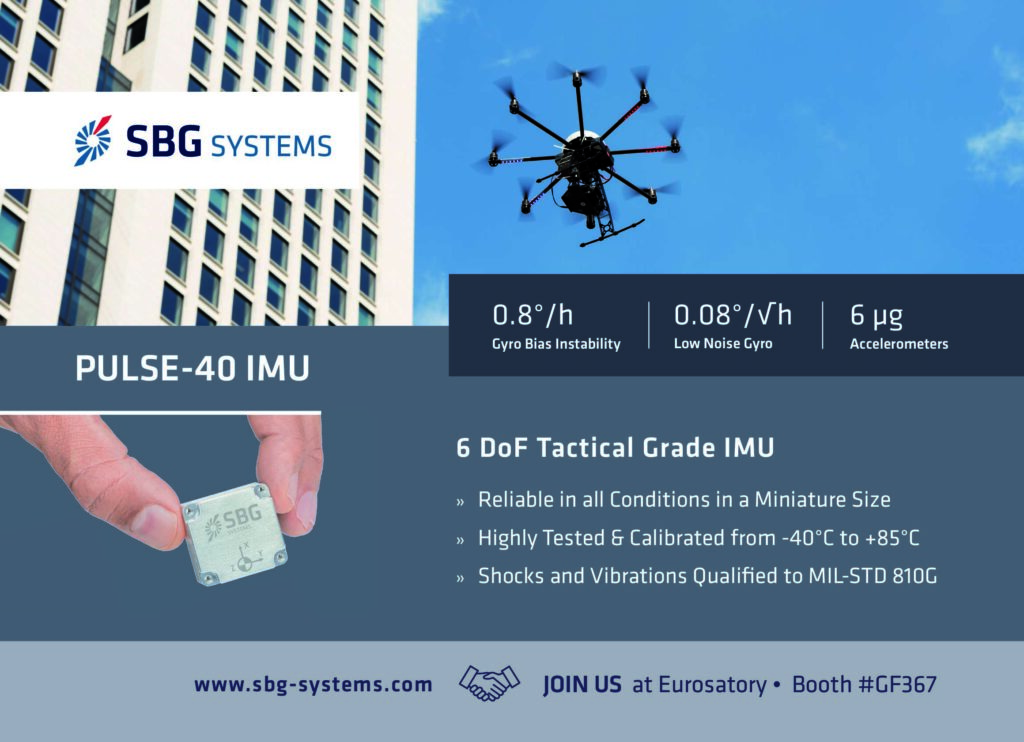
“Originally we used a hybridisation ‘kit’ that another supplier put together for us, but we didn’t like the results because of various quality issues,” Skantze says. “We had to break down and analyse each component in detail to ensure we’d have no issues with generating electric power.
“It has been a rather long and unexpectedly complicated process, indicating that it has not been done before for our type of product. Many components, such as Sullivan’s, are high end products for sure, but even here we’ve had to make modifications to cater for our needs.”
To ensure optimal efficiency and minimal thermal losses in the PMU, much of the connection soldering was redone in-house after receiving parts from manufacturers, but it acts largely as a slave to the autopilot and carries no intelligence of its own.
“It has however been a major mechanical and thermal challenge,” Skantze recounts. “Time and again, the expensive and much-vaunted parts we bought for it kept failing, without any clue most of the time as to why, so it took time to climb that learning curve and find the right PMU component supplier.
“Our supplier is a world leader in such technologies, and has helped make the PMU much lighter and less expensive over time. Naturally though we can’t reveal who it is.”
As fuses and mechanically actuated switches would be too heavy or unreliable for professional UAVs, Xer’s PMU boards mount solid-state IGBTs, high-end units being selected to minimise thermal output, power inefficiencies and the amount of space they take up. By contrast, COTS batteries are integrated and are unmodified, given their relatively simple duties and the maturity of battery technology. While high C-rate modules are used to enable fast recharges from the alternator, they are otherwise standard.
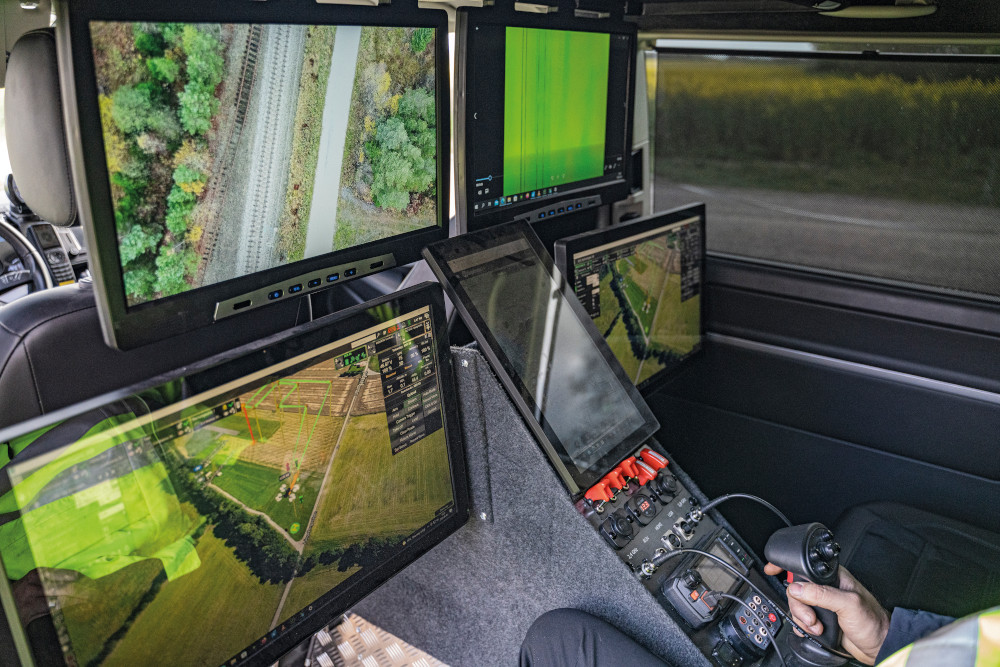
All this ensures stable power delivery to, and output from, the electric motors (which will be T-Motor systems for at least the first batches of both UAVs). The X12’s motors have a combined weight of 5 kg, and are capable of delivering a total of up to 15 kW continuous power output. The X8’s motors meanwhile have a combined weight of 2 kg and deliver 7 kW.
“We’ve had good experience with T-Motor’s machines and ESCs. The supply chain works well, their power-to-weight ratio is solid, and they’ve paired well with propellers from Mejzlik,” Skantze comments.
In addition to receiving commands on torque outputs for steering and propulsion, the autopilot will also generate commands for wind compensation based on movements sensed by its IMUs that deviate from the expected readings in pitch, roll and yaw.
“The autopilot’s built-in IMUs are of such high quality nowadays, there’s no point in reinventing the wheel in that respect,” Skantze says.
Mission systems
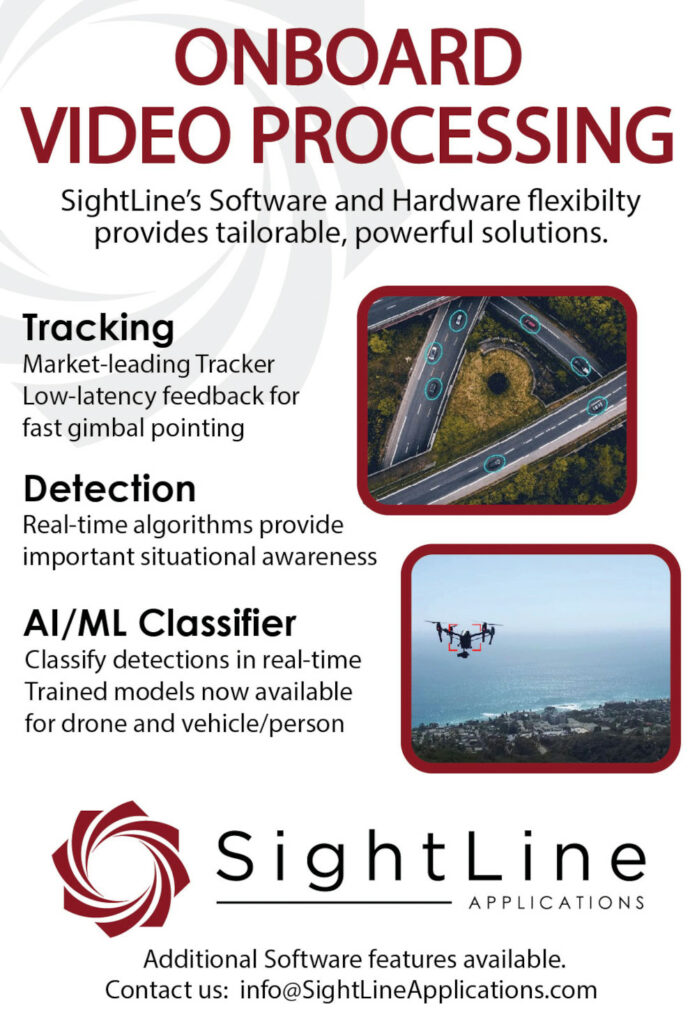
Different comms systems have been tested and can be used to enable secure control and monitoring links between the UAVs and an end-user’s GCSs, communicating on 2.4 GHz bands with a minimum range of 15 km. Some 4G equipment has also been integrated to enable cellular data comms wherever there is access to 4G networks. Satcom has been prepared for and can be integrated upon customer request.
“We’ve carefully modelled for stable waveform propagation from our antennas, and heavily modified camera and sensor feeds to be able to establish solid streaming functionalities down to the ground,” Skantze says.
“In terms of what we can stream, the engine and generator together offer an excess electric power supply of 500 W or more to allow any sensors our clients may want to add. We have a modular rack for integrating any sort of payload, but as keeping the CoG stable is very important to us we’ll probably take care of integrations in-house on behalf of our clients – at least initially – and we are in the process of developing a quick hotswapping system.”
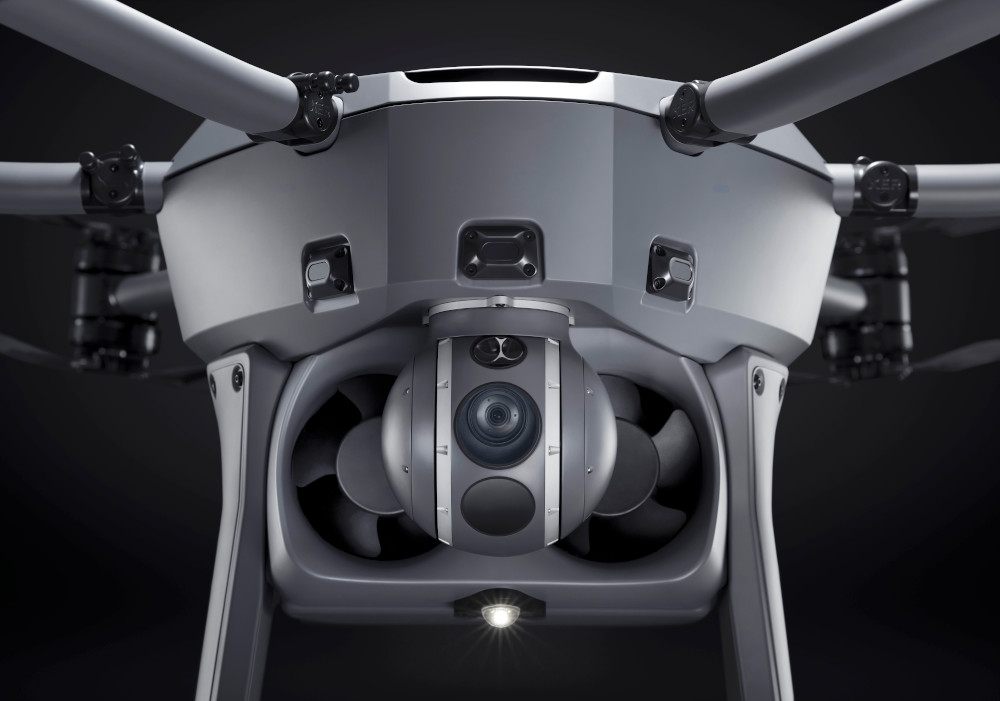
As standard issue for surveillance missions, gimbals from fellow Swedish manufacturer DST Control can be installed in front of the cooling fans, which Xer regards as especially highend multi-sensor payloads. However, as the platforms are sensor-agnostic, the team suggest that Phase One cameras or other types of Lidar as well as comms relays and gas detectors (among other systems) could also be installed quite easily.
Computing and data storage systems could also be seamlessly fitted to conduct onboard post-processing of survey data for later extraction, if wireless bandwidthsare insufficient for real-time streaming.
“We can also put on a release hook for extending or lifting things below the UAV, which is especially tough to get right due to load-drone resonances that can easily develop while flying,” Skantze adds.
“We’re going to demo that with Swedish maritime search & rescue services soon. We also already have a lot of interest from the UK and other European countries in that kind of solution.”
To enable safe flights in airspace potentially congested with other aircraft (crewed or otherwise), transponders will be installed. The impetus for that comes from a client’s request as well as Xer’s own internal initiative that dedicated transponders are a must-have for professional UASs that have been selected for their particularly low weight and prices.
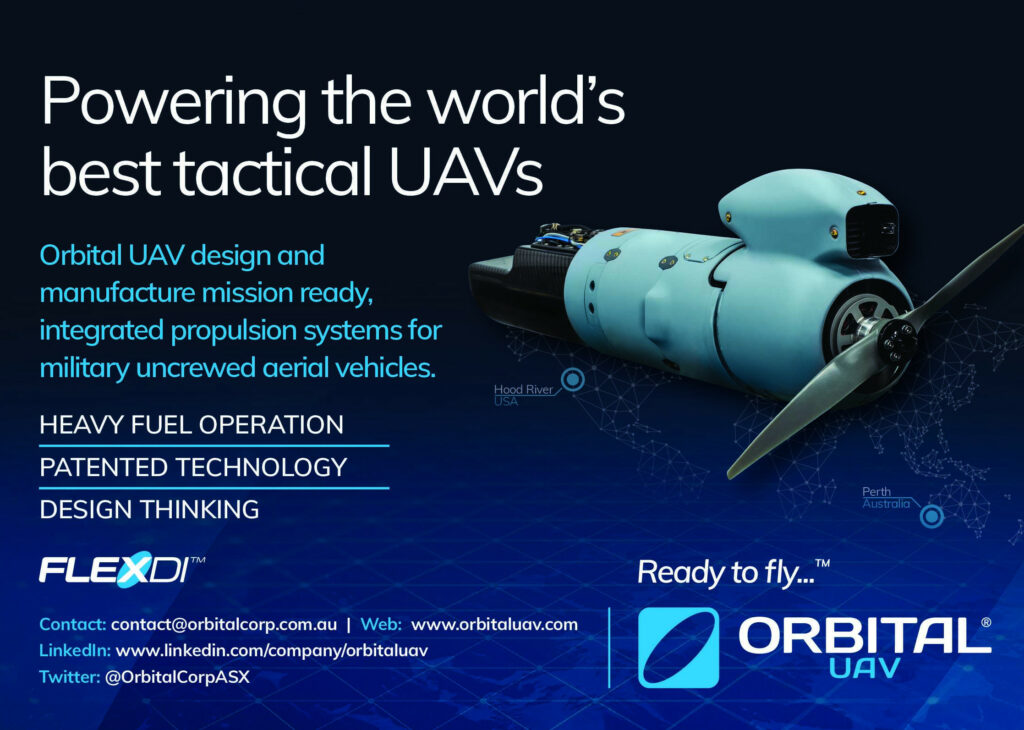
For further safety amid trees, power lines and other obstacles, a system of small Lidar sensors is installed for autonomous collision avoidance; it was designed in collaboration with an unnamed partner who had previously consulted Xer regarding autopilots.
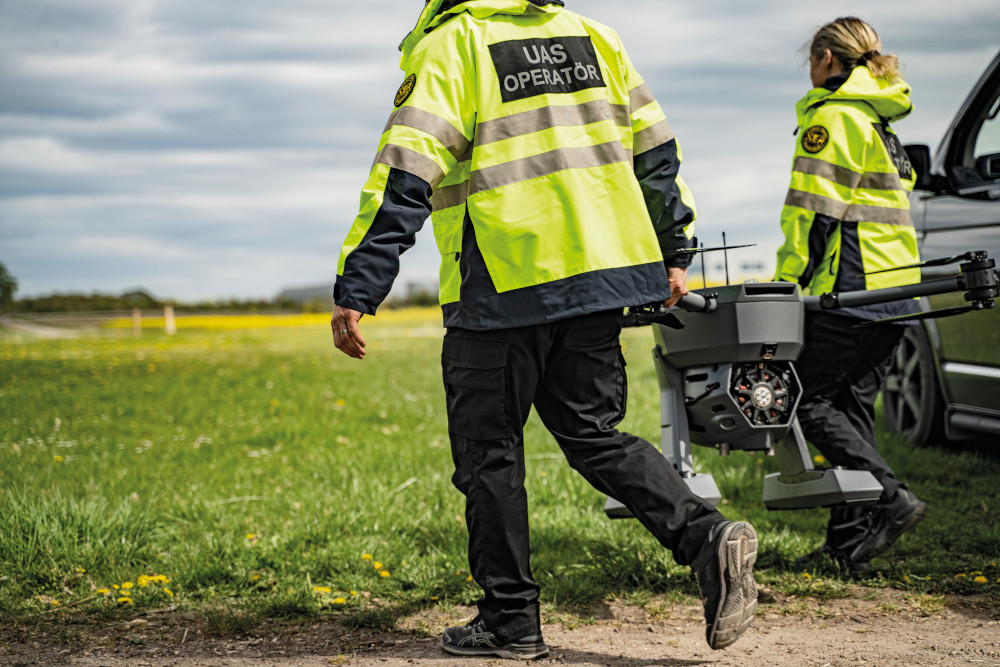
Depending on the configuration, three Lidars are installed on the front of either UAV to give a 200 m detection range ahead of its path, with a fourth Lidar pointing downwards to aid with safe landings. A plug-in from the opensource network has been used for quick integration with the PX4 autopilots.
Lastly, as mentioned, a parachute is installed in the top of the hub. It is supplied by Galaxy Parachutes, in the Czech Republic, as a last-resort safety system, and has an explosive deployment mechanism to quickly launch and inflate the ’chute when the IMUs sense that the UAV is falling.
“Making a high-end UAV isn’t just about pleasing end-users, the X12 and X8 also have to please the authorities, so having multiple tiers of robust safety contingencies is absolutely critical,” Skantze says.
Future plans
As a final point of Xer’s future r&d plans, Skantze says that in the years ahead the company is likely to develop an aircraft with an even heavier lifting capability than the X12 – around an are insufficient for real-time streaming.
“We can also put on a release hook for extending or lifting things below the UAV, which is especially tough to get right due order of magnitude larger – not for urban air transport but purely for large-scale aerial logistics. His team believe that the competencies accumulated thus far would make prototyping a UAV with a payload capacity of about 200 kg to be straightforward, compared with the blank-sheet garage engineering of the company’s early days.
While the X8 is reaching the market later this year, the X12 is expected to
be available from early next year, with a limited supply run for trials to a handful of clients that the company has lined up. Xer expects these and the subsequent beta tests of the X8 and X12 to be extremely tough use-cases that will also yield useful data for future design and engineering iterations, particularly in treacherous maritime conditions where itis unsafe to operate helicopters.
“My vision there would be to have drone pods along a troublesome coastline with automated refuelling, so that maritime rescue organisations could remotely launch one of our UAVs to fly out and survey for lost sailors or refugees with some kind of wide-area maritime surveillance payload. We can go far and quickly, while communicating real-time data back to onshore rescue coordinators,” Skantze says.
“We could even mount our UAVs with loudspeakers, comms base stations and inflatable life rafts for people in need, buying critical time for the rescue services to prepare their larger scale medevac or sheltering resources.”
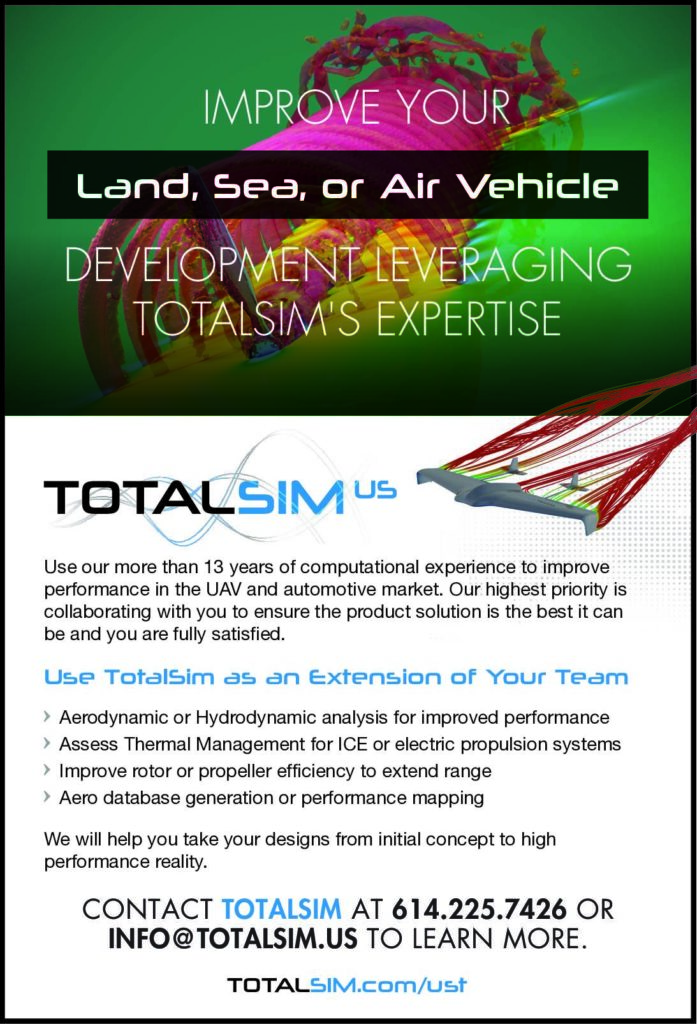
At the time of writing, Xer had been in contact with specialised sensor manufacturers in order to research how their payloads could be optimised for a multi-rotor airframe. Other partnerships and integrations for vital mission sets are expected to follow.
And while the company is sufficiently funded to take its first two UAV platforms to the market, it is also considering raising additional funds in order to expand its activities further, including integrations and development of both hardware and software.
Specifications:
X12 Dodecacopter Battery-powered with gasoline-electric range extender
Dimensions: 248 cm (maximum width) x 75 cm (height)
MTOW: 60-plus kg
Maximum payload capacity: 20 kg
Maximum endurance: 4 hours
Top airspeed: 50 kph (27 knots, 14 m/s)
Maximum wind resistance: 35 knots (18 m/s)
X8 Octocopter Battery-powered with gasoline electric range extender
Dimensions: 203 cm (maximum width) x 62 cm (height)
MTOW: less than 25 kg
Maximum payload capacity: 2 kg
Maximum endurance: 2.5 hours
Top airspeed: 50 kph (27 knots, 14 m/s)
Maximum wind resistance: 35 knots (18 m/s)
Some key suppliers
CNC machining: undisclosed
Carbon fibre: undisclosed
Electric motors: T-Motor
ESCs: T-Motor
Propellers: Mejzlik
Autopilots: Various PX4-based suppliers
GCS: customer-defined
Transponders: undisclosed
Generators: Sullivan/Acutronic
Safety parachutes: Galaxy
UPCOMING EVENTS
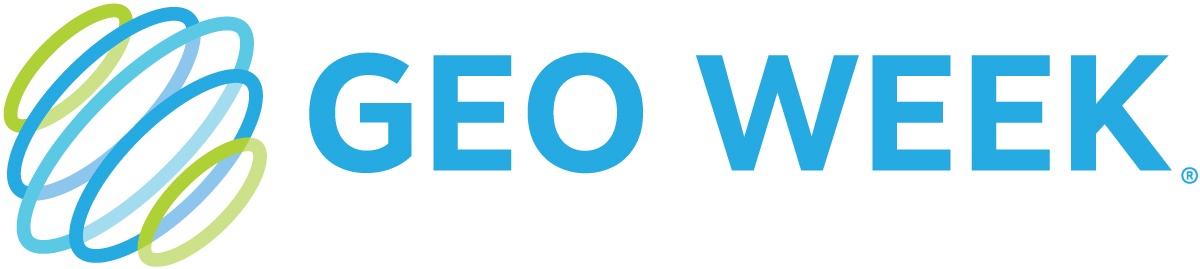
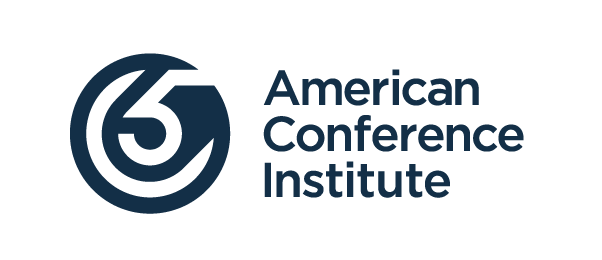
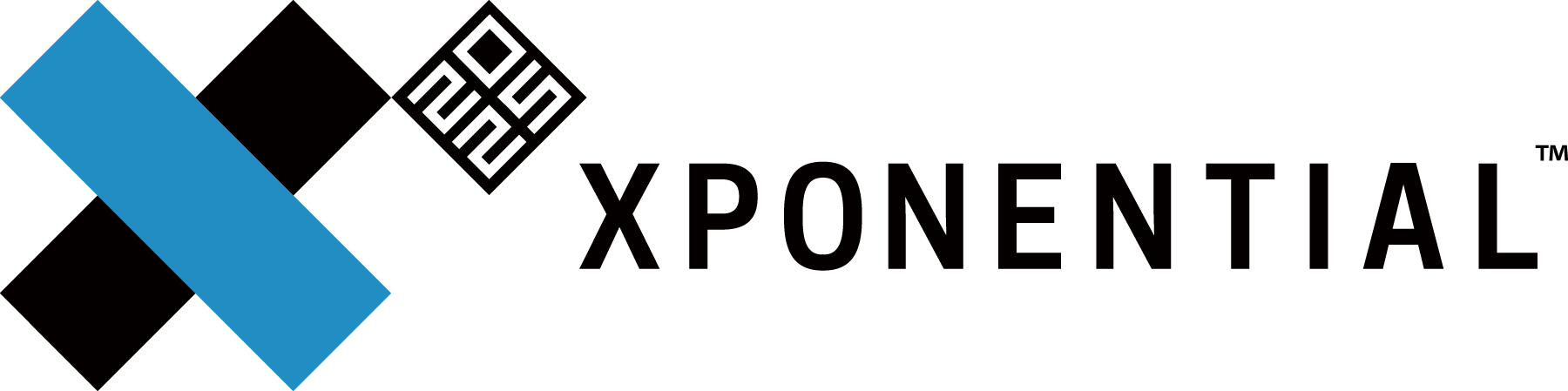
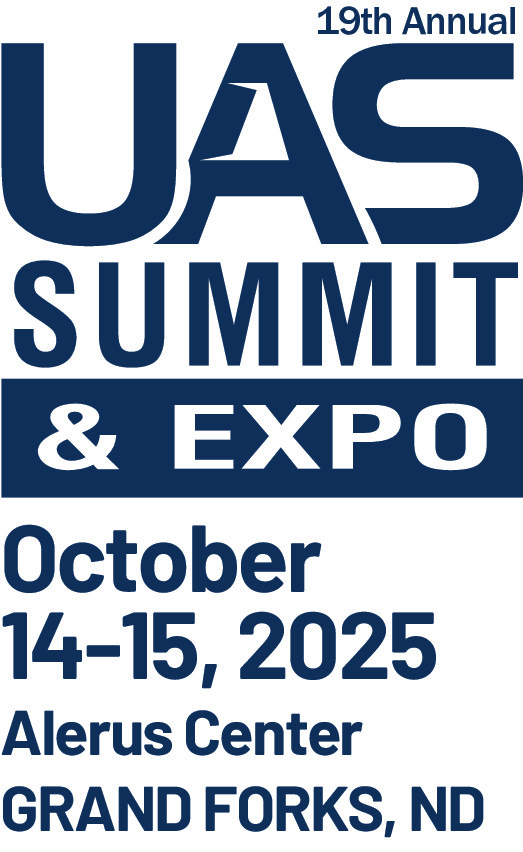
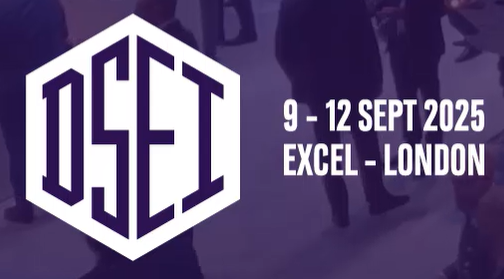
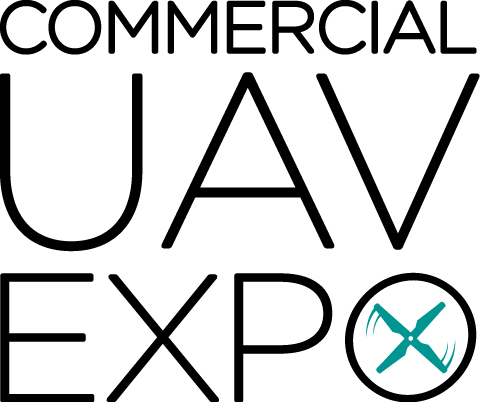
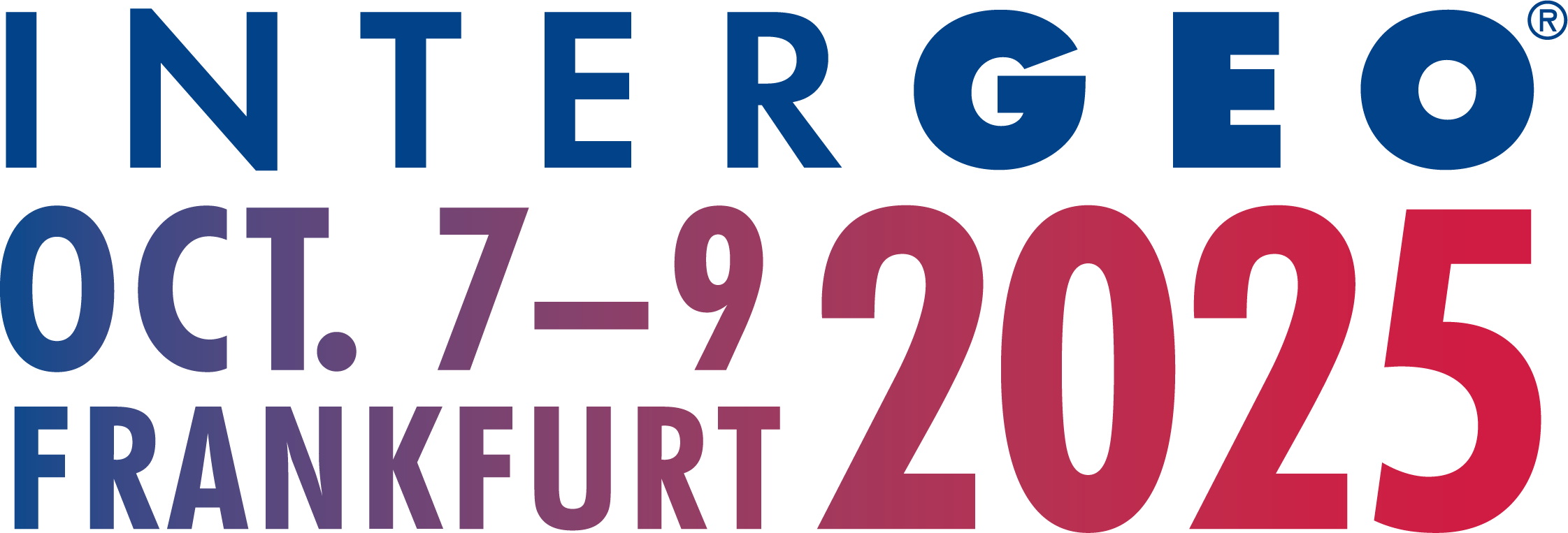
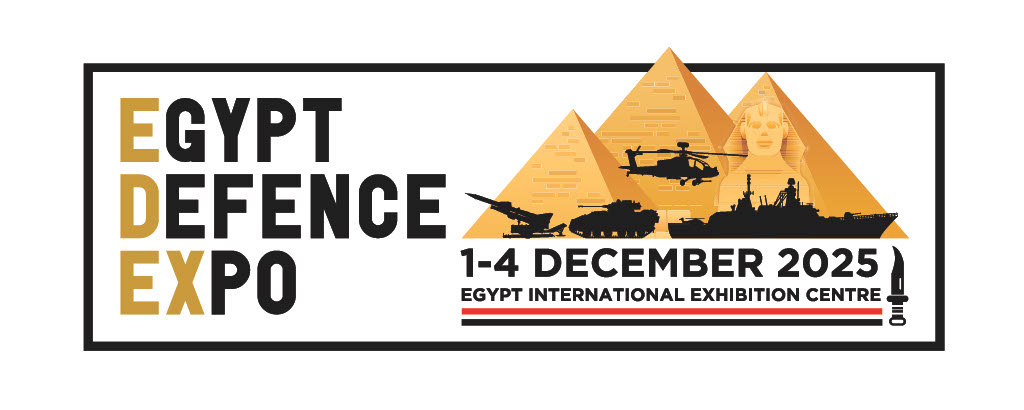
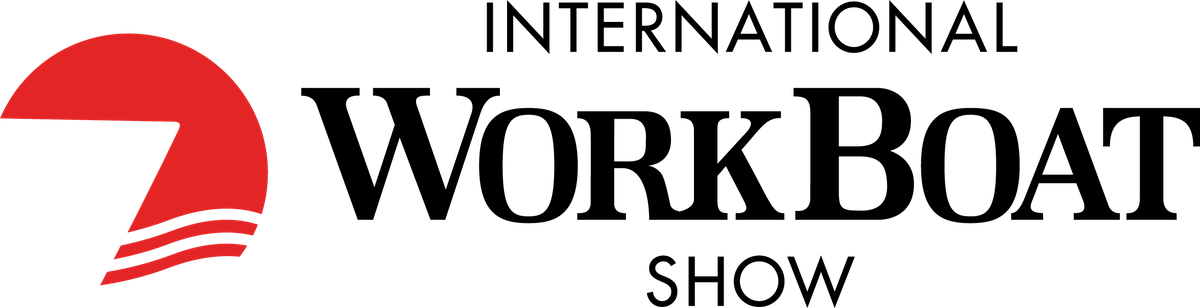
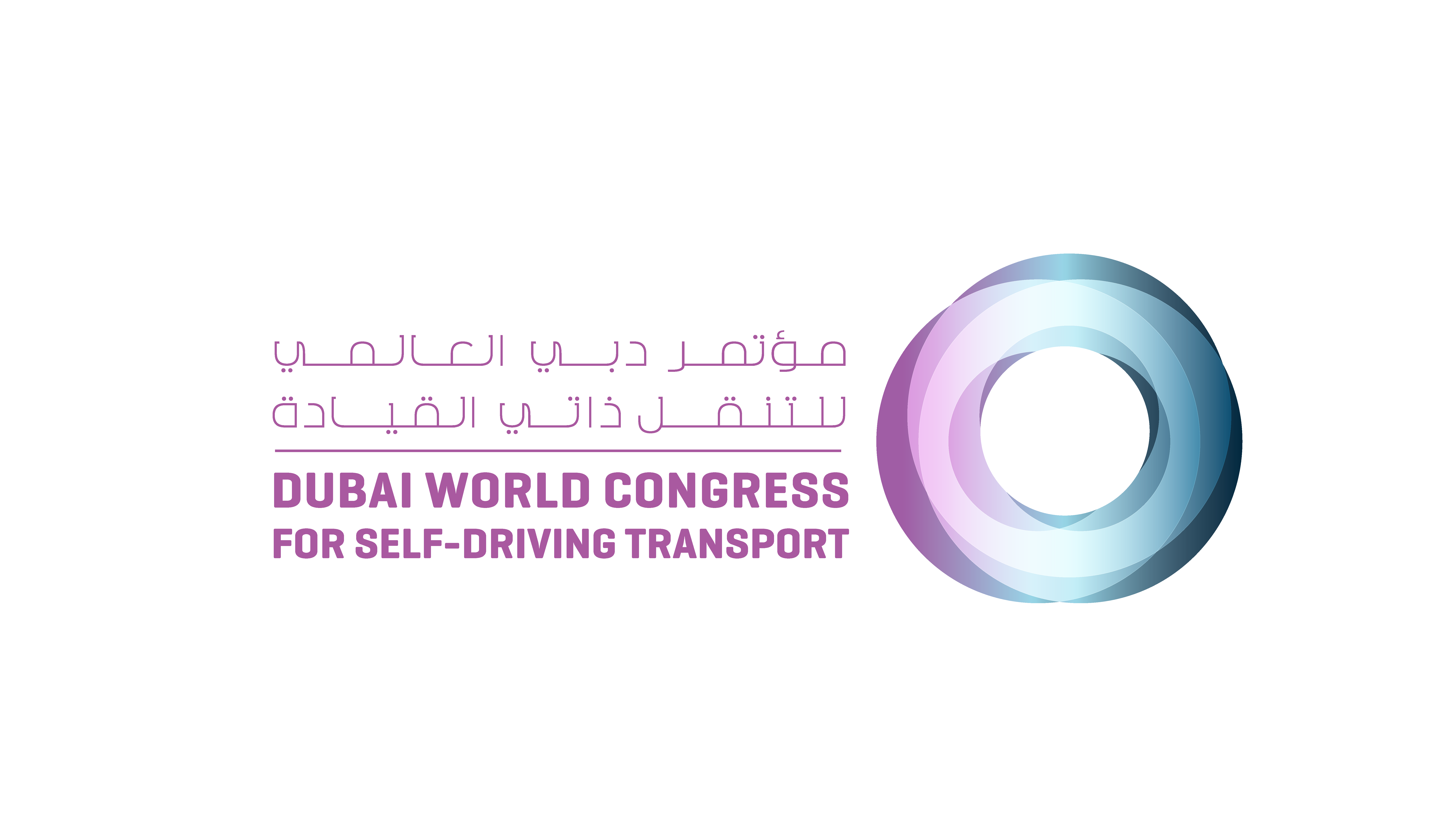
