Paris Air Show 2023
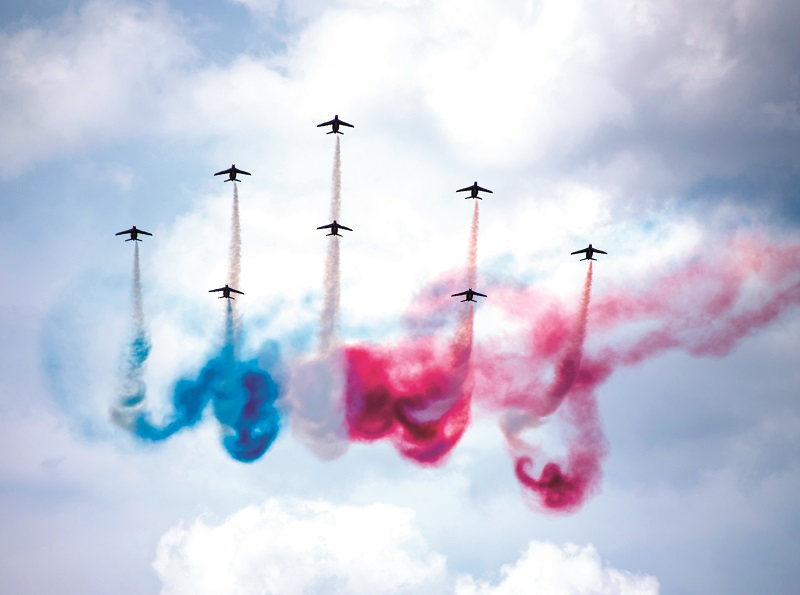
Rory Jackson reports from the world’s largest aerospace exhibition with his highlights of the uncrewed systems it had on display
The 2023 edition of the Paris Air Show was held from 19 to 25 June at Le Bourget exhibition centre, which over the week played host to 292,000 visitors and nearly 2500 exhibitors; close to $15 billion worth of contracts were signed as well, according to the show’s organisers.
There were a number of themes at the event, including decarbonisation of air transport and developments in urban air mobility. Naturally, the show also played host to a range of tech start-ups bringing new innovations and perspectives for aviation.
And with autonomy maturing and taking its place among traditional certified aerospace engineering disciplines, those innovations – from start-ups and primes alike – included new platforms and technologies for the uncrewed and autonomous sector. Here’s our selection of them.
Saft attended the show to exhibit its aerospace battery technology, with particular emphasis on its ULM (ultra-low maintenance) cells. These have plastic-bonded electrodes (PBEs) to reduce water consumption and hence improve sustainability compared with sintered electrodes. PBE technology also reduces overcharging during operations, enhancing the lifespan and safety of Saft’s batteries even if cycled repeatedly at high temperatures.
The company uses mostly Ni-Cd cells, with the ULM solutions containing 12 to 53 Ah, although others optimised for power or energy are available. Nickel-plated copper cell links and terminals are used for durability, with thermo-welding preventing leaks from cells into aircraft structures.
For thermal runaway conditions, the Saft modules integrate temperature sensors for cell monitoring, proprietary membrane and separator components for isolation, as well as a nylon vent valve for evacuating any harmful gases. A stainless steel enclosure provides environmental ruggedness, although the cells are accessible and designed for easy individual replacement.
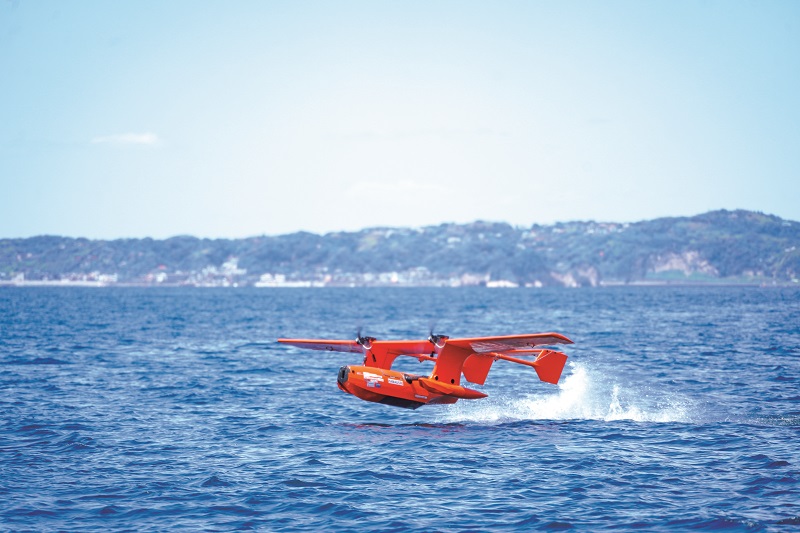
Laboratory’s Hamadori 3000 Space Entertainment Laboratory, in Japan, unveiled a new design concept for the next-generation aircraft in its series of Hamadori seaplane UAVs.
The concept aircraft will have a twin hull design that will enable payload pods to be integrated into the centre of the main wing, such as AUVs winches, cargo pallets and various sensors.
It is set to be the company’s largest UAV yet, with a MTOW of 1000 kg, a wingspan of 14 m and a length of 8 m. Also, its 300 kg payload capacity will enable a wide range of aerial and maritime logistics, research and survey missions in Japan’s exclusive economic zone and elsewhere.
The aircraft is likely to be powered by twin turboprop engines, and have an expected range of 920 km. It will come with satcom as well as LOS data links, and the ability to navigate waves of up to 3 m while on the water.
Of the two other aircraft in the series, the Hamadori 3000 is the smaller, and is powered by a lithium-ion battery for an endurance of 120 minutes and a range of 150 km, as well as a cruising speed of 35 knots. It has a 3.1 m wingspan, a 19 kg MTOW, and comes with an EO/IR camera gimbal as standard.
The Hamadori 6000 UAV is still in development, but it will be powered by twin engines for an 8 hour endurance, a 740 km range and a 60 knot cruising speed. The airframe will be 4 m long and have a 6 m wingspan, along with the ability to carry 10 kg of payload within its 100 kg MTOW.
All three will incorporate autopilot functionality for automatic take-off and landing on water as well as accurate navigation while on water surfaces (as currently available in the Hamadori 3000), along with acoustic comms for low-bandwidth subsea data links with underwater infrastructure or UUVs.
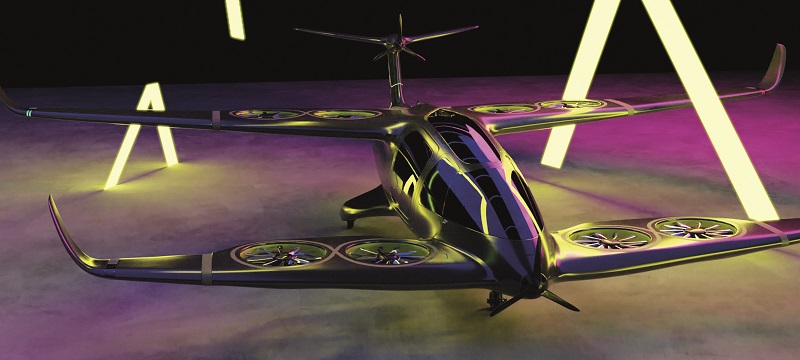
Ascendance Flight Technologies (AFT) attended the show to discuss its ATEA eVTOL, being designed for urban air taxis, medical emergencies, logistics and aerial monitoring.
The air taxi version will have a hybrid-electric powertrain called Sterna, which AFT is optimising for running on an array of fuel engines, including those for kerosene, biofuels and synthetic fuels. There are plans to integrate hydrogen fuel cells as well.
A distributed lift system of eight rotors mounted inside the forward and aft wings (four in each) help give turnaround times of 10 minutes, and once in the air the aircraft is anticipated to achieve ranges of over 400 km between refuelling and top speeds in excess of 200 kph.
The ATEA prototype’s first test flight is expected next year, with the company aiming to deliver its first commercial unit in 2027. So far, Solvay and Airborne have been announced as suppliers for its composite aerostructure, with Evolito providing the battery.
Demgy Group showcased its newest developments and materials solutions in plastics and composites.
Among its offerings is the ability to provide functional carbon composite parts using PEKK (polyether-ketone-ketone). These are produced on an EOS P 810 laser sintering machine, which uses EOS HT 23 material along with carbon fibres for reinforcement. EOS HT 23 is based on the Kepstan PEKK resin engineered by Arkema.
Through that material and manufacturing approach, Demgy is able to produce complex and high-performance carbon-PEKK parts in series, up to dimensions of 700 x 380 x 380 mm. In addition to having high strength-to-weight ratios, the parts can withstand temperatures in excess of 200 oC, and can also be metallised for EM shielding or paths for current flow.
The company also discussed other techniques for advanced materials manufacturing and treatment, including laser direct structuring for selective metallisation of parts, and laser ablation of specific metallised areas of components.
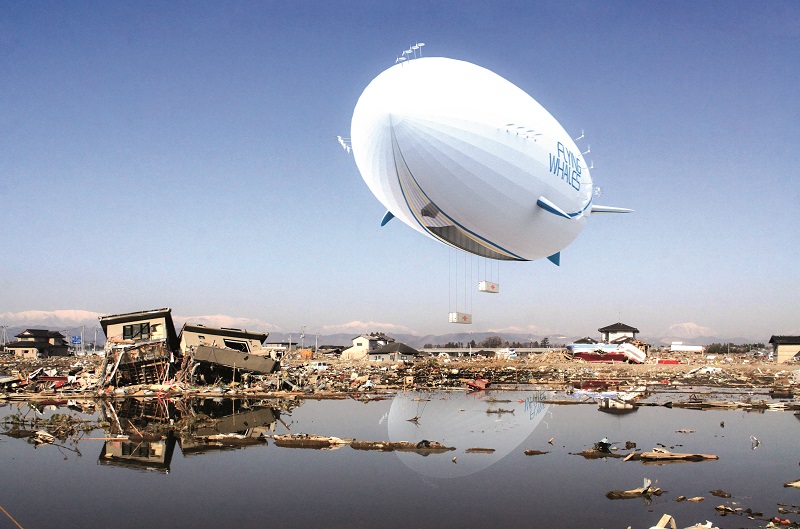
Flying Whales exhibited its rigid airship-based solution for high-volume uncrewed aerial logistics.
The CONOPS was conceived when the French National Forestry Office started looking into less costly ways to transport renewable wood resources from forests than the traditional approach of building ground tracks.
The result of that r&d is the LCA60T uncrewed airship, built by Flying Whales Industry and operated by Flying Whales Services (the two halves of the company). It will be 200 m long, and its cargo hold will be 96 m long, 8 m tall and 7 m wide. It generates lift through 180,000 m3 of helium inside its envelope. Up to 4000 kW of electricity for propulsion, avionics and its cargo mechanisms will come from a hydrogen fuel cell powertrain.
The LCA60T’s first flight is planned for 2025, and the plan is to incorporate enough electric motors for a 100 kph maximum airspeed, transporting up to 60 t of payload (with transfer of cargo achievable during hover) and a flight ceiling of 3000 m (with payload).
As well as moving pallets of lumber, the craft is being promoted for use in a range of other applications. These include transporting wind farm blades of up to 80 m long, ship-to-shore ferrying of containers from freight vessels to ports, construction material logistics, and moving rocket and satellite parts for the space industry.
ADDEV Materials exhibited its latest range of chemical products for the aerospace market. Although these included sealants, adhesives, coatings and composites, the company placed a focus on new liquid solutions for aircraft maintenance.
Its Cor-Ban series for instance is a line of corrosion-inhibiting products formulated for use on large structural components, as well as avionics, cables and other smaller components. Some formulations are also being produced for heavy-duty applications and long-term storage if needed.
The company also promoted its Aero-Lube line of aircraft lubricants, which includes multi-purpose greases, silicones, Teflon, molybdenum disulphide and graphite lubricants. The product line includes systems for lubricating high-temperature areas, penetrating lubricants, and for preventing ice build-up on rubber seals.
Aerix Systems showcased its X-8 octocopter, which is capable of highly dynamic manoeuvres thanks to its four coaxial motor-propeller pairs being mounted on rotationally actuated beams inside their shroud housings. The beams also sit in electromechanical rim drives that change their yaw.
This integration and actuation approach allows the UAV to take off and land in different orientations, to pitch, roll and yaw stably in 360o during every phase of flight, and instantly correct trajectory or any erratic movements.
The UAV features a gimbal on its nose, and the company adds that thanks to its propulsion configuration, the craft can circle around structures such as boat hulls, aeroplane wings or complex building shapes to take continuous video or imagery.
The UAV measures 1 x 1 m, and is designed for top speeds of 200 kph (to which it accelerates within 2.5 seconds) as well as a 1 m turning radius at speed. It also has an endurance of 35 minutes, can carry a 2.5 kg payload and will withstand winds of up to 100 kph.
Evolito exhibited its 800 V axial flux motors, which are based on a proprietary segmented topology and cooling system the company says requires 75% less iron, as well as less copper and fewer permanent magnets than radial flux motors.
The motors are designed as propulsion solutions for eVTOLs, urban air taxis, and single or multiple-propeller fixed-wing aircraft. Its D1500 motor is 440 mm in diameter and 110 mm in length, weighs 35 kg and produces a peak torque of 1200 Nm and peak power output of 150 kW at 1000 rpm. The system also has a maximum speed of 2500 rpm, and a top continuous power output of 100 kW.
Its D500 is a lighter and more powerful motor. It weighs 30 kg, produces 320 kW at 6200 rpm continuously, up to a peak of 350 kW at 6000 rpm, with 560 Nm of peak torque. The system measures 375 mm in diameter and 128 mm long.
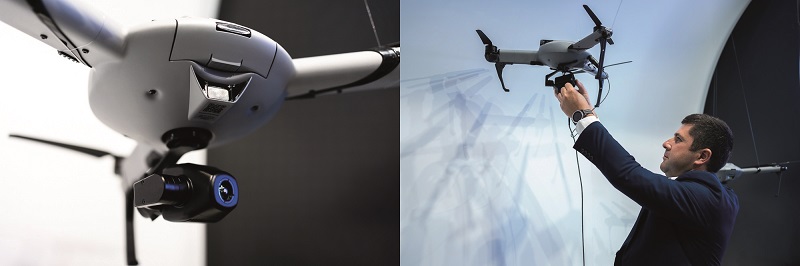
Atlas UAS debuted two new UAV systems. The first is the AtlasTether, which consists of the company’s AtlasPro UAV combined with a Ligh-T 4 tethering kit from fellow French company Elistair.
The AtlasPro is a battery-electric tricopter measuring 558 x 417 x 116 mm, weighing 1585 g and with a payload capacity of 315 g and hence a MTOW of 1900 g. It is capable of operating in temperatures from -20 to +55 oC, and communicates over a 2.4 GHz data link with navigation based on GPS, GLONASS and Galileo.
It also comes with options for standard propellers that give it a top speed of 56 kph, or quieter propellers that give it up to 46 kph. The UAV and its GCS are typically equipped with mesh radios, enabling BVLOS in-the-loop monitoring, as well as group formations (with UAVs within LOS of the GCS acting as comms relays for those beyond).
Typically, the AtlasPro can fly for up to 32 minutes with payload (depending on environmental conditions), but with the tether, it can operate for as yet unspecified durations, but theoretically as long as the 200 V AC or 400 V DC power supply lasts. The Elistair kit allows a flight distance of up to 70 m from the ground station.
Atlas also unveiled its AtlasPerkons UAV, which has been designed with light weight and affordability, although the company has yet to disclose its physical or performance specifics.
The company also promoted its AtlasNest, a docking station designed for the AtlasPro which can perform autonomous battery swapping by way of a robotic hand system, enabling the UAV to take off and continue performing missions without waiting for its old battery to charge. It uses a 220 V power socket and weighs just under 75 kg.
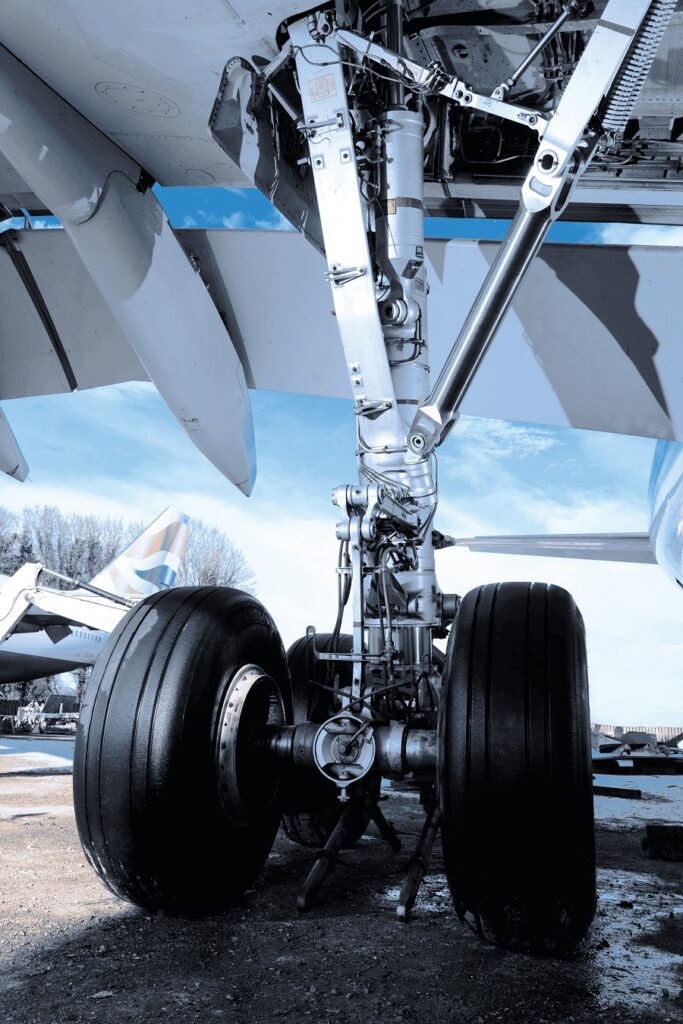
TISICS is a producer of metal matrix composites, and attended the show to discuss the weight-saving and hence fuel cost-saving qualities of its products (bringing a set of its Light Land airline landing gear made from one of its materials to the show as a demonstrator).
Its metal matrices can be made from titanium or aluminium alloys, and are reinforced using continuous SiC mono-filaments manufactured in-house. The filaments are produced in 100 and 140 µm diameters using chemical vapour deposition.
The composite parts can then be produced through a net-shape additive manufacturing process in order to achieve complex shapes with fully bonded joints, and with reduced waste and processing times compared with more conventional forgings and castings.
Among the aerospace uses of these materials are for composite actuators, truss struts and wing ribs. As well as enabling mass savings of up to 50% in these parts, newer types of components such as liquid hydrogen tanks using TISICS’ metal composites are in development.
UPCOMING EVENTS
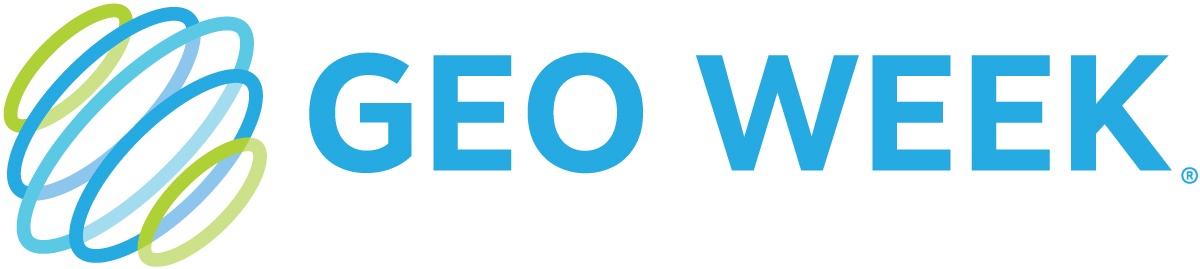
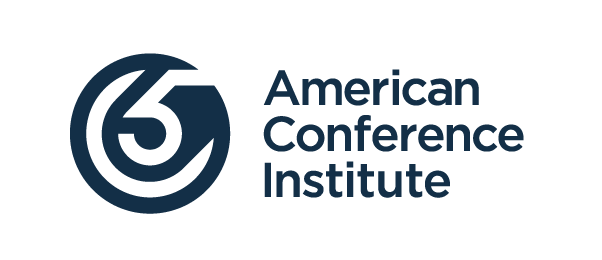
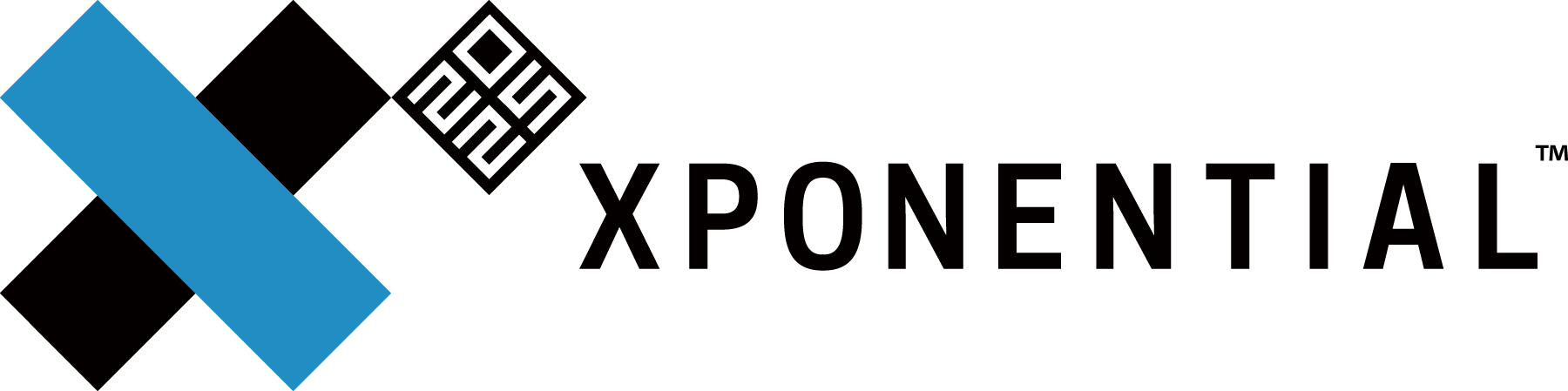
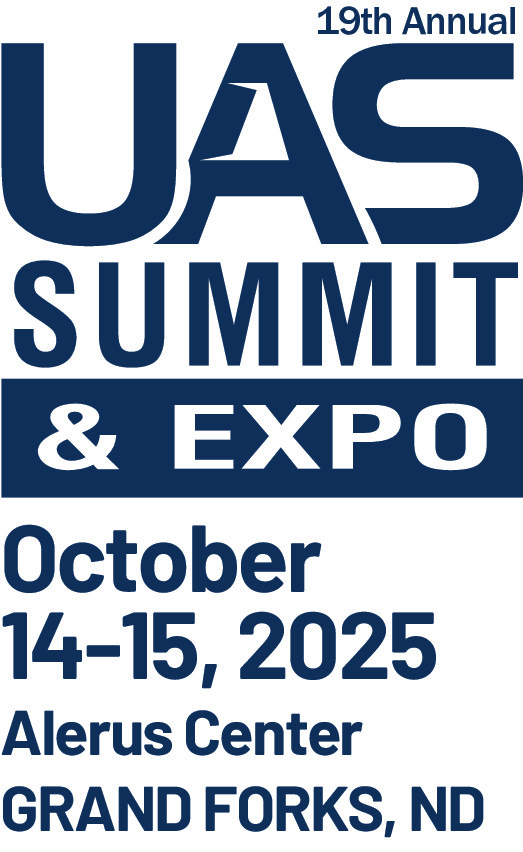
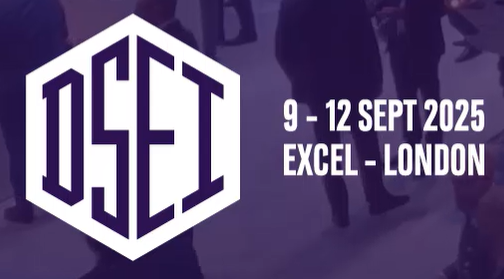
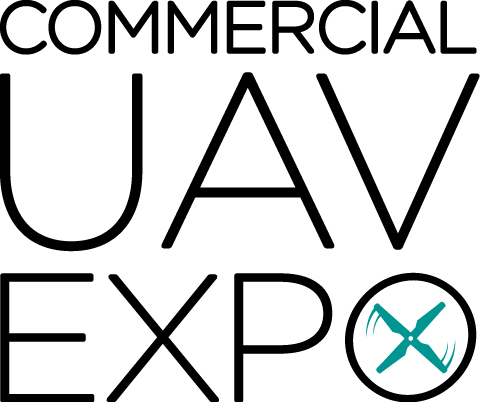
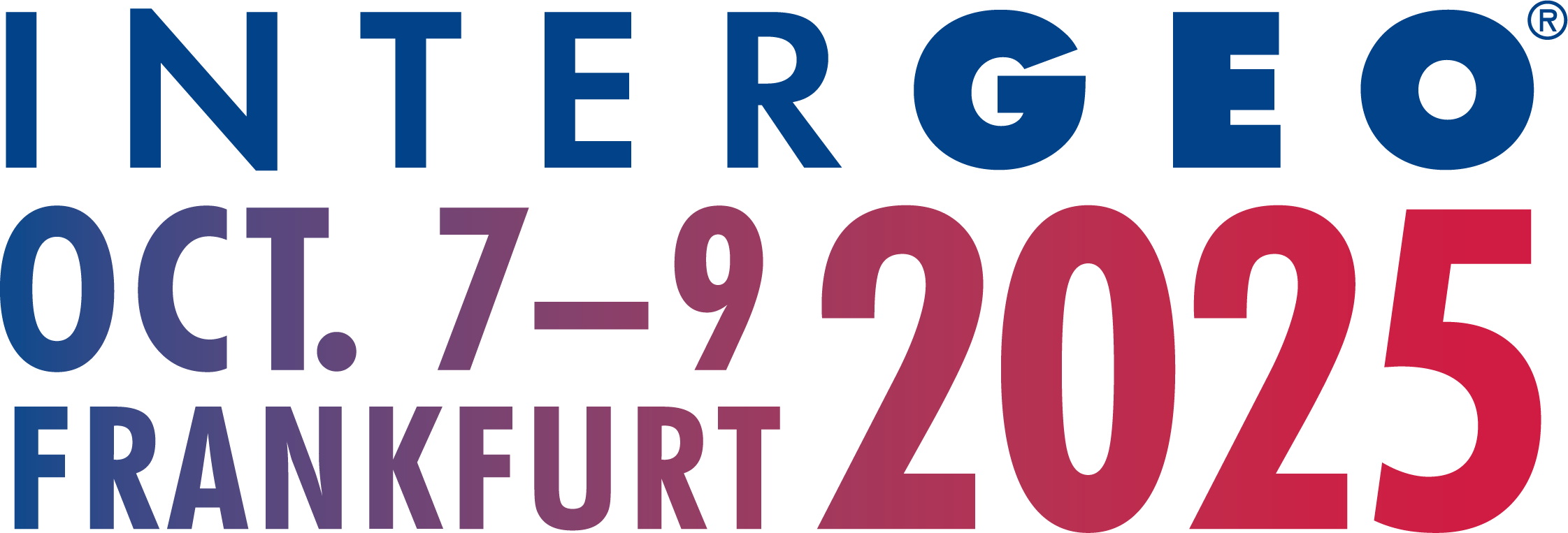
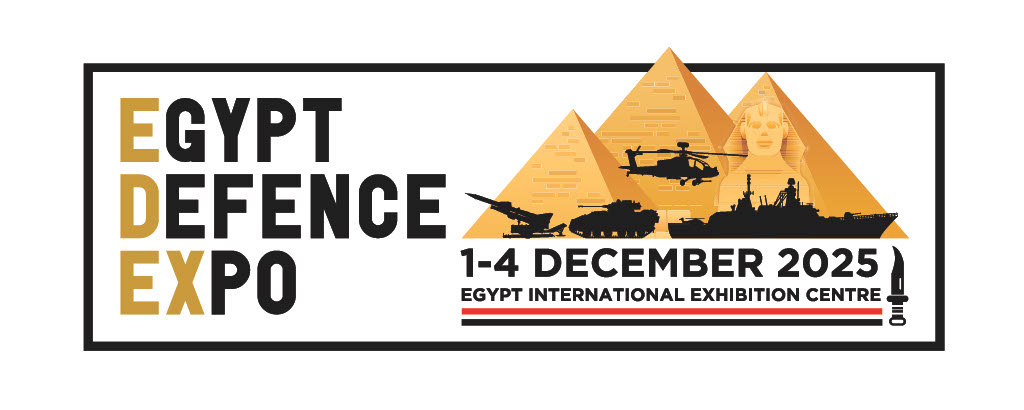
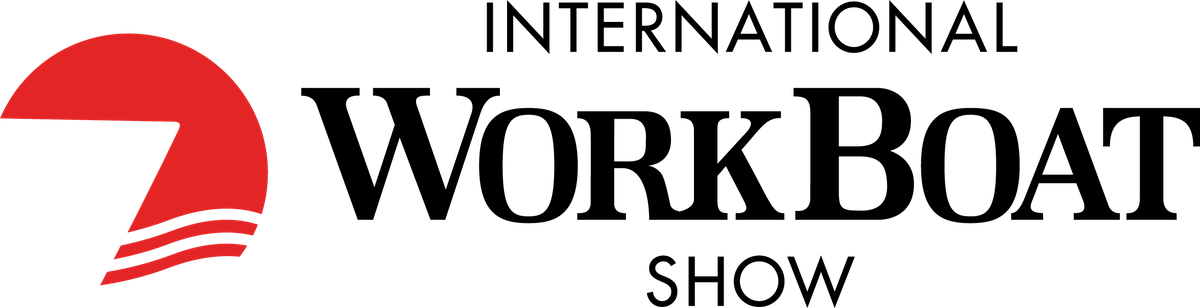
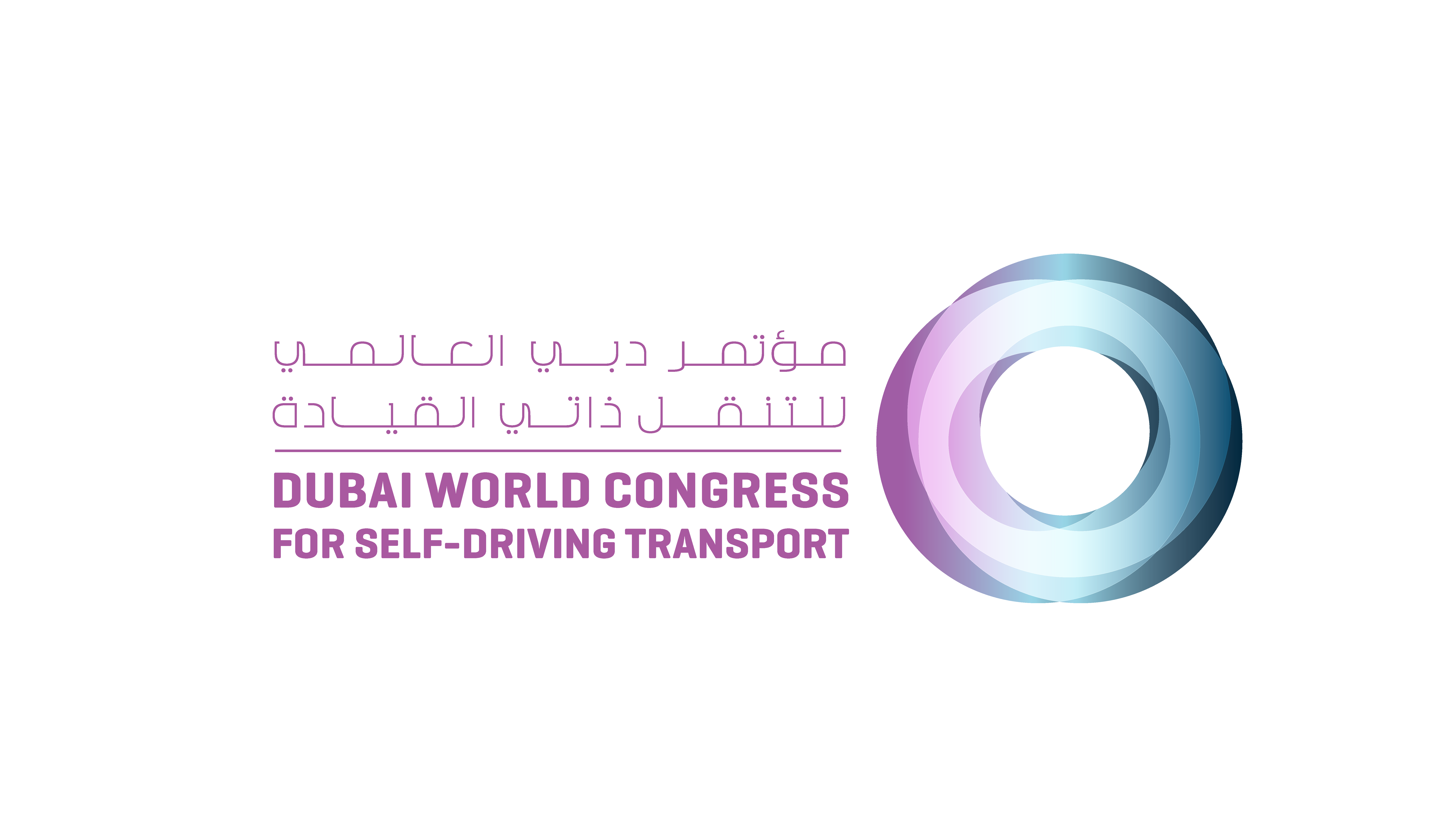
