Tampa Deep Sea Barracuda
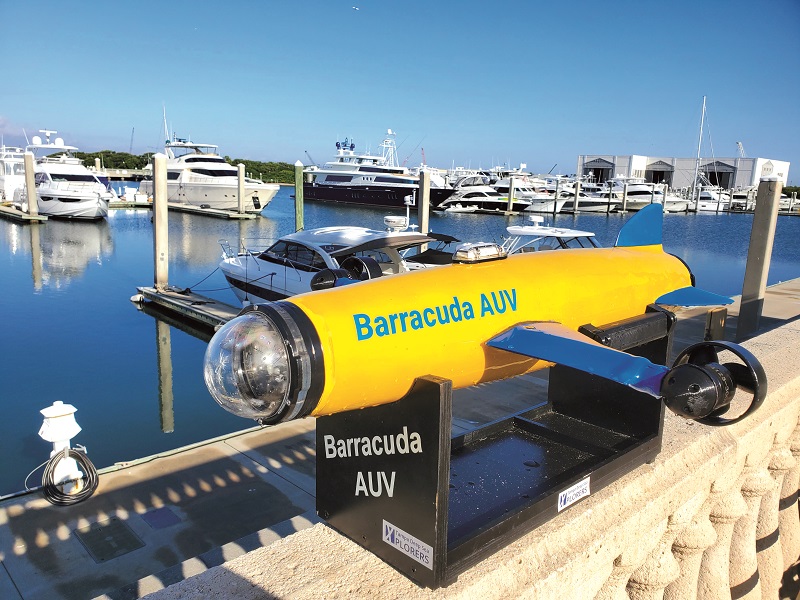
Peter Donaldson reports on the unusual design aspects of this light and affordable AUV
Thrust of the matter
Tampa Deep Sea Xplorers’ Barracuda AUV stands out from the growing range of small AUV designs by virtue of the thrusters on the ends of its dive planes, a distinctive feature that on its own almost justifies its existence.
It brings some more practical advantages to the party, however. Among them are great manoeuvrability at low speeds and confined spaces, which is notoriously poor in more conventional torpedo-shaped AUVs with a thruster or propeller at the rear, and extra space in the tail cone for sensors or other equipment.
The intention is to produce a fleet of Barracudas with swarming capabilities that are affordable for organisations whose budgets won’t run to ownership or even rental of a single large AUV. The base model is available for $15,000.
CFO Joe Daum credits CEO Ed Larson and mechanical engineer Dennis Lorence with the design of the vehicle, which they undertook for the Shell Ocean Discovery XPRIZE competition looking for innovative solutions for ocean floor mapping.
The Barracuda measures 1.2 m long and 10 cm in diameter. Its body is covered with a streamlined layer of syntactic foam, and weighs 12 kg in air, making it small and light enough to be launched by hand.
Within that all-up weight, about 1.4 kg can be devoted to payload in the standard configuration, accommodated in an internal bay with a maximum length of about 30 cm as standard. However, the body can be lengthened by adding a separate housing that adds about 23 cm of length to the bay and around 3.2 kg of extra payload capacity.
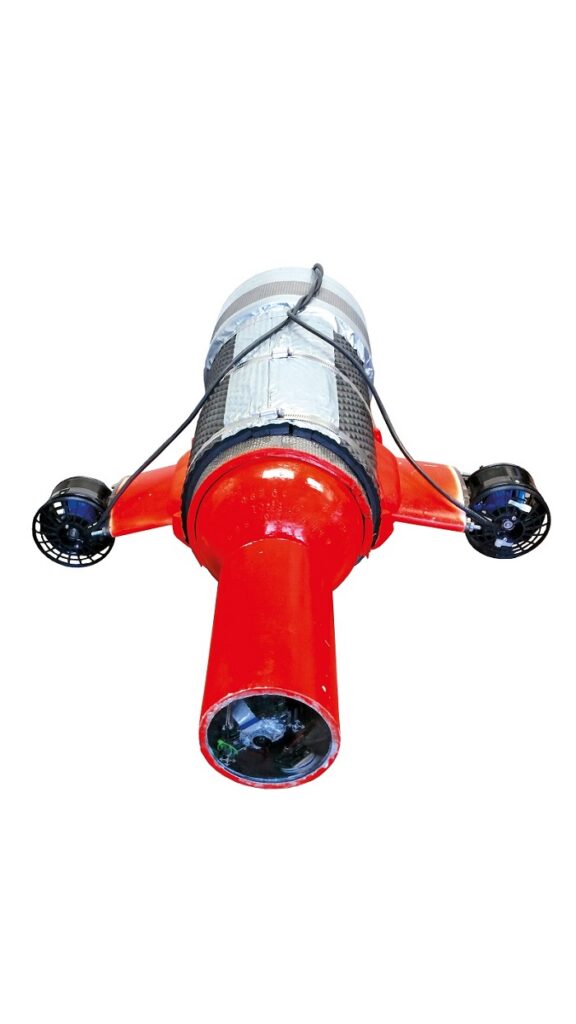
Under pressure
With time and money at a premium for its XPRIZE effort, the team based the pressure hull of the proof-of-concept vehicle on a scuba tank.
“We needed a pressure hull that could withstand at least 3000 psi for round one of the competition,” Daum says. “We decided to use aluminium scuba tanks and modify them by cutting out the bottom and having a pressure flange machined for them. That worked well, and our pressure vessel successfully passed a tank test to 3200 psi.”
That 3000 psi requirement would mean a depth of more than 2000 m; however, the production Barracuda is designed to operate down to 600 m, where the pressure is typically about 880 psi, depending on temperature and salinity.
An aluminium pressure hull is therefore unnecessary, so the production vehicle’s structure is formed from a high-impact plastic sealed by 4 in end caps from Blue Robotics. The team has completed preliminary pressure testing to 800 psi, and Daum is confident that the vehicle will be good for at least 1000 psi.
One of the major engineering challenges facing the team centred on packaging, particularly in fitting all the components required into the volume available in the slim hull. Another challenge was sourcing affordable through-hull connectors that could take the water pressure.
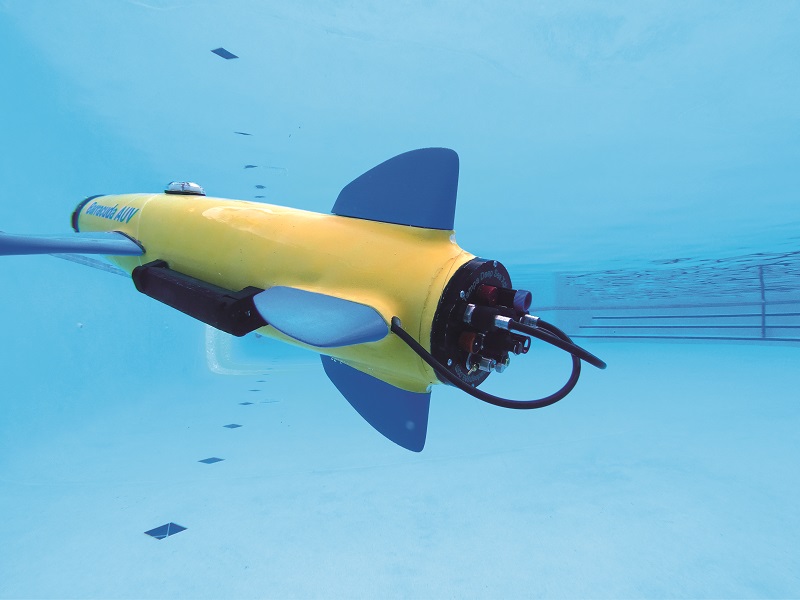
Home-grown propulsion
Affordable thrusters that were suitable for mounting on the dive planes and that could provide the performance the company needed were not available at the time, so the team developed its own, and still makes them.
The motor is a commercially available waterproof high-torque brushless unit, but Tampa replaces the standard bearings with hybrid ceramic ones, dips the electrical windings in insulating resin, and 3D-prints its own propellers. The motor mounts are also the company’s own design.
As well as propelling the vehicle forwards and backwards, the thrusters can also run at different speeds and in opposite directions to provide steering and to enable the vehicle to turn through 360o within its own length, eliminating the need for a rudder.
“If we have an obstacle in front when we are in a tight corner, for example, we can back out of the situation, turn and then avoid it,” Larson says. “That is one of the things that makes the vehicle unique among the mini and micro AUVs.”
The thrusters are the only external moving parts, as even the dive planes are fixed. Pitch control is provided by using the battery as a moveable weight to shift the vehicle’s centre of gravity fore and aft.
The thrusters and all the externally mounted sensors and antennas, for GPS and wi-fi for example, are served by power and data cables that meet waterproof connectors in the rear pressure plate, minimising the number of penetrations that would otherwise require extra strengthening.
The team designed its own lithium polymer battery, a 6S, 26 V unit rated at 23 Ah. This delivers current to a 26 V bus and a 5 V bus to power loads including the thrusters, navigation and comms systems and the sensors.
The propulsion system enables the Barracuda to cruise at between 1 and 6 knots, with a maximum run time of between 4 and 5 hours depending on the mission, the payload and the chosen speed.
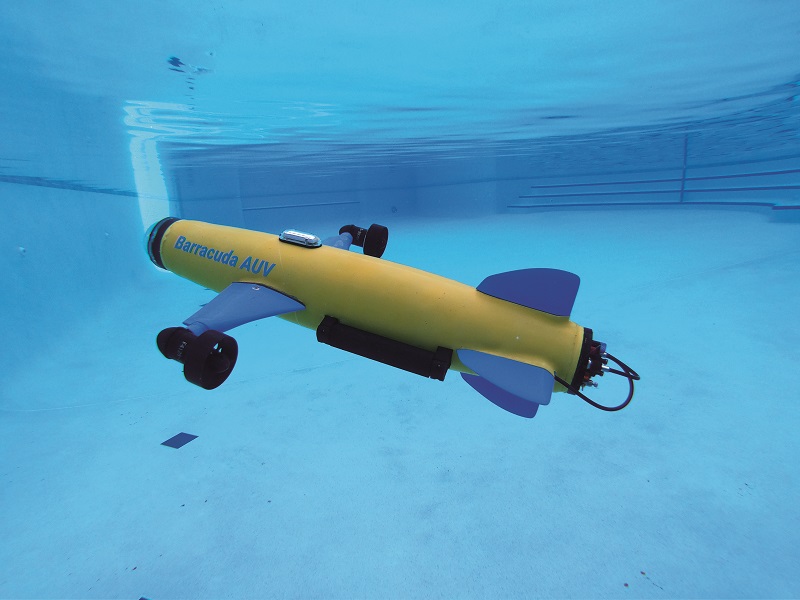
Computing power and obstacle avoidance
The onboard computing power to manage the vessel comes from an Nvidia Jetson Nano CPU/GPU AI platform running the Robot Operating System on a Ubuntu Linux distribution. The module also provides the Barracuda’s systems and sensors with I2C, USB, SCI and SPI interfaces.
Currently, the autopilot is a system made by CubePilot, linked to a compatible GPS sensor for navigation updates at the surface and an inertial system once submerged. The baseline Barracuda is also fitted with a depth sensor from Blue Robotics, and a sonar altimeter from the same company is optional.
At the moment, when running in autonomous mode, there is no communication with the surface, and all data is downloaded for processing after the vehicle has been recovered. However, it can be run with a tether that provides an Ethernet connection, and Tampa is working with the University of South Florida (USF) to develop two-way comms with the surface and with other Barracudas working in a swarm.
On the base vehicle, mission sensors include a forward-facing stereo camera system of the company’s own design, which combines two low-light cameras with 1080p resolution and a Sony chipset. This serves as the sensor for the Barracuda’s object identification and obstacle avoidance system.
Daum explains, “The stereo camera identifies objects and their relative position and distance. This is done using the Nvidia GPU and a trained model; we trained our model using PyTorch software. Distance and direction are then passed to the autopilot, which is programmed with an obstacle avoidance algorithm.”
Larson says the processor can be trained using PyTorch (or similar) to recognise objects of interest, adding that the company plans to offer the vehicle with Nvidia’s Orin processor, which he says is about 30 times more capable than the Jetson Nano.
Daum adds that Tampa has tested several iterations of the obstacle avoidance capability on a dedicated test vehicle. “It performs well at moderate speeds, around 3 mph. We have yet to test it at higher speeds.”
The base vehicle also comes with an echo sounder that serves as an acoustic altimeter to measure the water depth below the vehicle, as well as a set of fins that can be swapped for ones equipped with sensors without changing the AUV’s balance or hydrodynamic characteristics.
“That’s what you get for the $15,000 – the basic model plus the software needed to program and operate it,” Daum says.
Daum notes that other sensors are left to customers to choose, and can come from a variety of vendors, including AML Oceanographic for example. “Of course, that adds more to the price, but for about $50,000 you can outfit the whole thing, and you are still well below the price of a medium-size AUV,” he says.
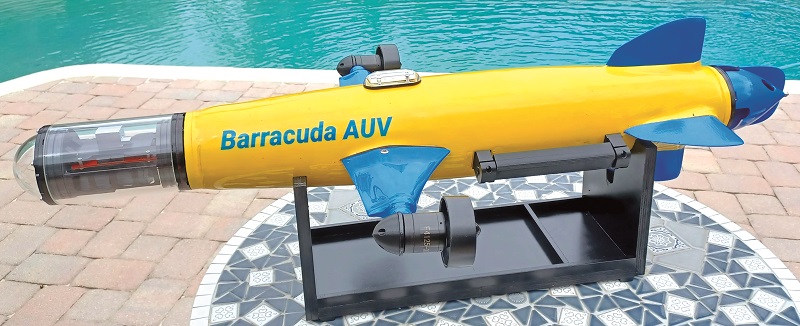
Sidescan sonar
One of the optional sensors is an 1800 kHz, 600 m-capable ARC Scout Mk II sidescan sonar from Marine Sonic. It comes with a pair of transducers for mounting on the sides of the vehicle and a single small box of processing electronics for installation inside the pressure hull.
A Barracuda on display at the Ocean Business event in April in Southampton, UK, was fitted with a pair of mock-up transducers, which are a little over 9 in long, and which the company fitted in order to test their effects on the vehicle’s stability and drag characteristics. Customer Ocean Builders is due to take delivery of the first Barracuda to be equipped with this sonar.
Daum admits that the sonar transducers, which sit a little way from the hull, look rather like grab handles, even though they are not intended to be used to pick the AUV up. However, they are quite sturdy and are screwed into inserts in the hull.
“Although I wouldn’t recommend you do this every time, if you were to pick it up that way I don’t think you would break them off,” Daum says. “Also, if you did happen to break one off you could put the inserts back in with regular marine-grade epoxy, and you could do that repair on the boat so you wouldn’t have much downtime.”
The ARC Scout Mk II comes in single and dual-frequency forms covering six centre frequencies between 150 kHz and 1800 kHz. In 1800 kHz form, it has a maximum range of 25 m from either side and an along-track resolution of 5 cm, enabling it to create highly detailed images of objects on the seabed.
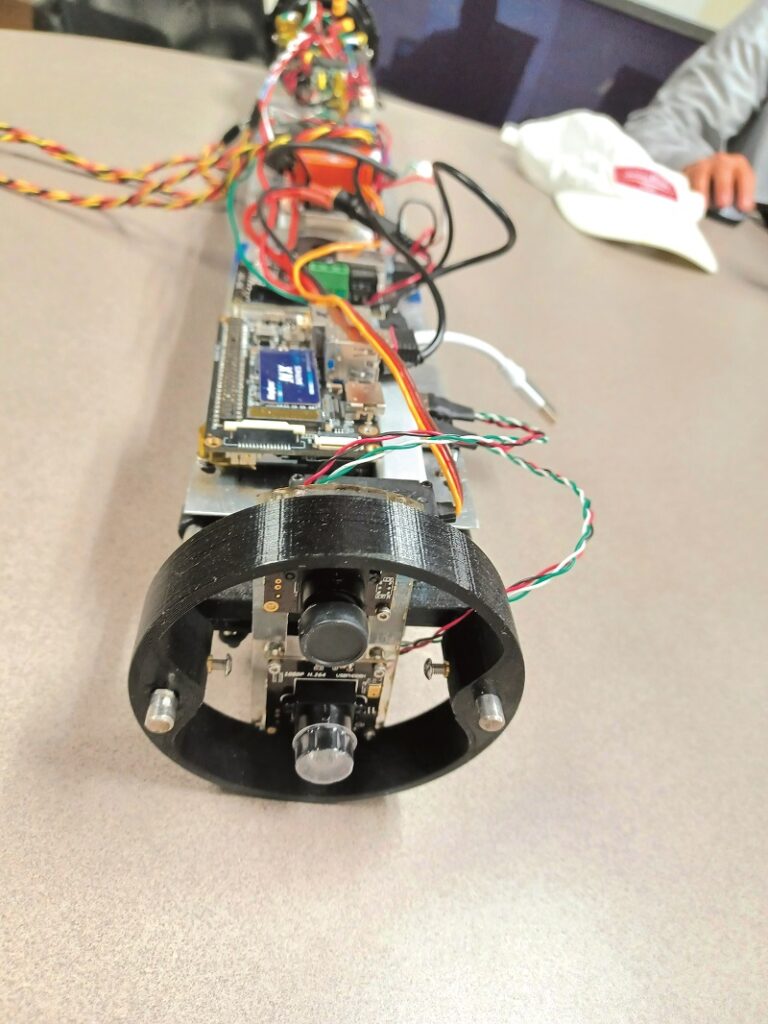
Lidar and RGB camera
Another sensor system under development for the Barracuda is an underwater Lidar system combined with an RGB camera. Together, these sensors are designed to create 3D images in colour of underwater objects.
The RGB camera is a high dynamic range 24 MP scientific sensor, which provides a colour overlay on the 3D point cloud generated by the Lidar.
“The Lidar we are developing has a blue-green laser, generates about 300,000 points per second and has RGB capabilities of its own,” according to Larson. “The separate RGB camera is downward-facing, and we will be taking about four images per second with it. Once we have collected the point cloud and processed it into a topology, we can overlay the RGB images and get, more or less, a photo of the bottom in 3D.”
“The system is a true colour Lidar that will capture about four images per second,” he explains. “The sensor package is being provided by Beam Sea Associates and SEE Monster Vision Solutions.
“The system provides colour-corrected 3D point cloud datasets at a sub-centimetre spatial resolution. Once the data has been collected and processed, we will have a photorealistic 3D image of the bottom. The end product will be useful for applications such as subsea mapping, coral reef surveys and obstacle detection.”
Together with these two companies, Tampa is working to miniaturise an existing system to fit inside the Barracuda. All the companies are small businesses located in Florida, and this project is the subject of a US Government Small Business Innovation Research programme from the US National Oceanographic and the Atmospheric Administration.
Daum reports that the team is now assembling the prototype, which should be ready for testing by this autumn, with the full Lidar capability expected to be available in 2025 or 2026.
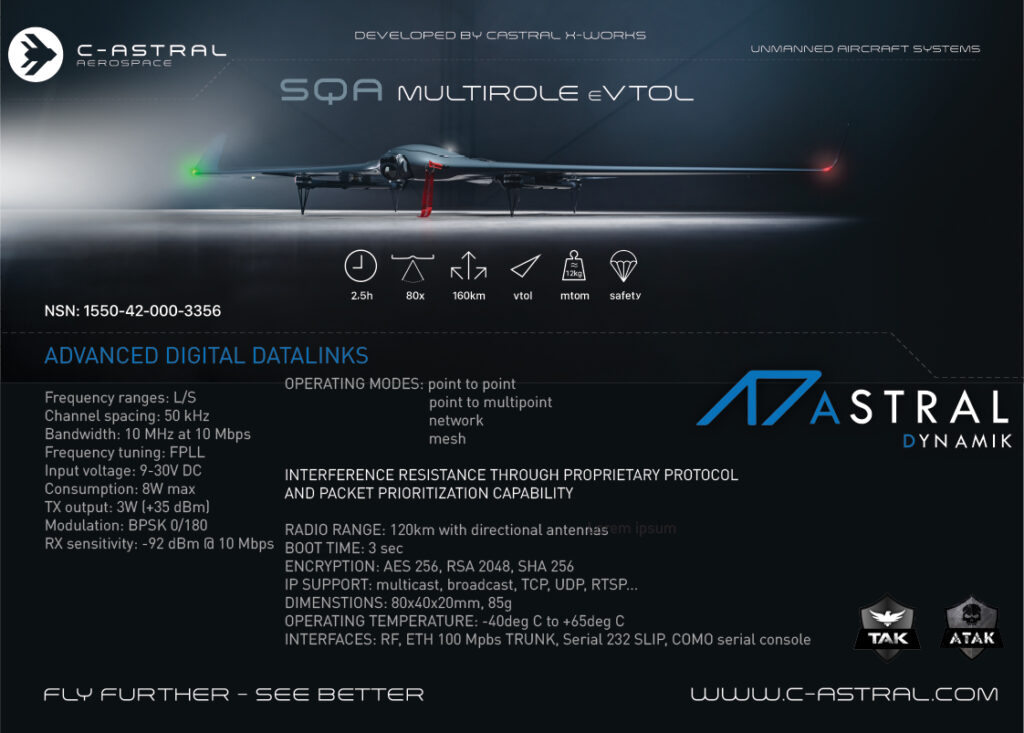
Operational practicalities
Operable by one person, the Barracuda is provided with an open source user interface based on Mission Planner for loading missions into the autopilot. Comms with the Nvidia GPU are through a network connection and command line interface.
To run a mission, the operator needs only a laptop with Mission Planner installed, an umbilical and a control yoke for operation in ROV mode and a wi-fi hotspot, although wi-fi is not needed if the tether is in use. Launching at sea can be done from a small boat such as a RHIB, although the AUV can be launched from the beach as well.
To prepare the Barracuda for a mission, the operator puts the dive planes and rear stabilising fins on to the hull; both are attached mechanically using a metal tube coupling and secured with a Chicago bolt. The electrical power and data connections are made with waterproof connectors from Blue Line Engineering.
The next task is to charge the battery and install it. If the mission is to run in autonomous mode, the operator connects the laptop to the electronics and uploads the mission plan, then installs the sled on which the battery and electronics are mounted into the vehicle. Next, the operator switches on the AUV’s power, connects to it either with the wi-fi or the tether, launches the vehicle and sets the mode to manual, guided or autonomous, Daum explains.
The sled can be withdrawn from the hull after the tail cone is detached. Larson explains, “It all comes out the back in one piece when you want to swap out the battery, the SSD card or you need to repair or replace something. Using regular hand tools you can replace anything on the electronics sled and put it back together, replace the battery, and in 10 or 15 minutes you’re back in business.”
This is an example of the design philosophy applied to the Barracuda to make it relatively simple and forgiving to operate. “One problem operators typically have with big AUVs is that it takes a person with engineering qualifications to run and maintain them,” Daum says. “The Barracuda is aimed at the technician level, so a person with reasonable mechanical skills can operate and maintain it.”
The Barracuda is also designed to be easy to transport, weighing about 40 lb in total or 50 lb when carried in a hard case, so one person can carry it, and it can be carried aboard an airliner rather than having to be shipped ahead. However, transport regulations covering lithium-ion batteries still have to be followed.
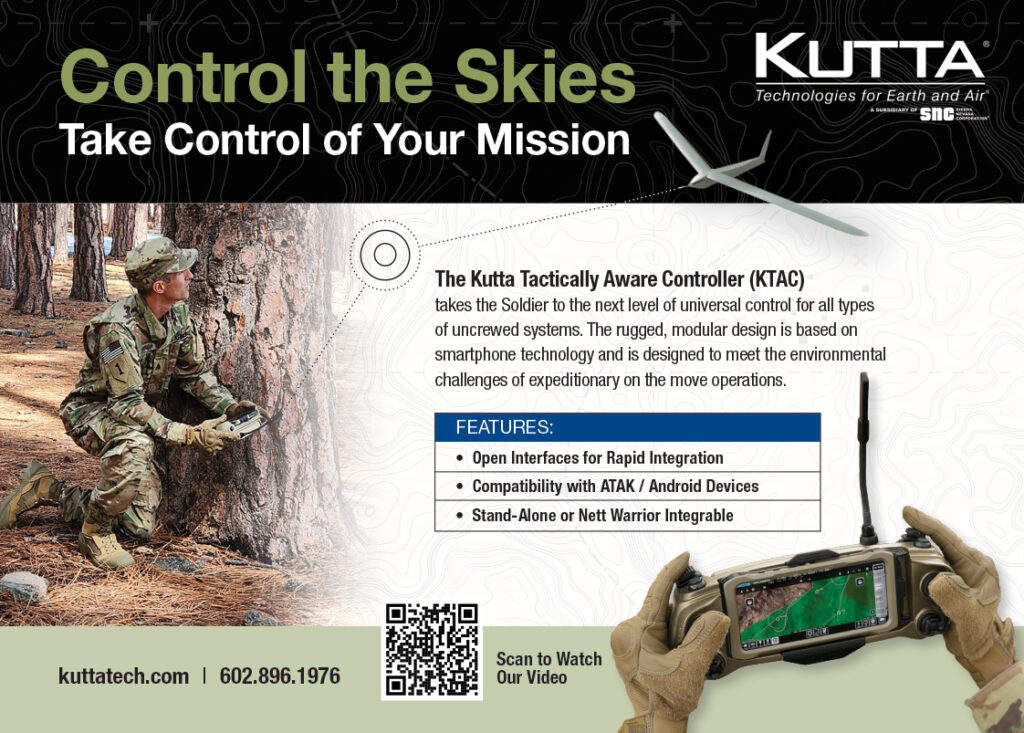
Advanced comms and swarming
USF has demonstrated an optical underwater comms system and performed some bench testing, Daum says. The system will enable comms between vehicles and with systems on and above the water surface, although the exact arrangements are still to be worked out.
Larson says, “I think the way it is going to work is that there will be a comms node that serves as a central hub, and multiple devices will communicate through that, so you will get vehicle-to-vehicle comms primarily through the hub.” The hub would be aboard a stationary buoy or, potentially, a larger mobile vehicle, he adds.
Daum says the swarming software is being developed in collaboration with the USF and Certus Group under a phase two small business technology transfer grant. A working prototype has been built and preliminary testing carried out, he says, and integration into the vehicle is next.
An underwater navigation system that is not prone to the inevitable drift with inertial systems is also under consideration. One possibility here is an ultra-short baseline network.
Tampa is now taking pre-orders for a limited number of Barracudas, with Daum reporting that the company has commitments for 10 and plans to sell a maximum of 30 this year before moving into full-scale production in 2024 once it has reached a deal with a suitable manufacturer.
Specifications
- Barracuda AUV
- Length: 1.2 m
- Diameter: 10 cm
- Weight: 12 kg (in air)
- Payload: 1.4 kg (standard), 4.6 kg (extended)
- Cruising speed: 1-6 knots
- Endurance: 4-5 hours
- Maximum depth: 600 m
Some key suppliers
- Autopilot: CubePilot
- Bathymetric sensors: AML Oceanographic
- Computing/AI platform: Nvidia
- Depth sensor: Blue Robotics
- Lidar: Beam Sea Associates
- RGB camera: Allied Vision
- Sidescan sonar: Marine Sonic Technology
- Swarming software: University of South Florida, Certus Group
UPCOMING EVENTS
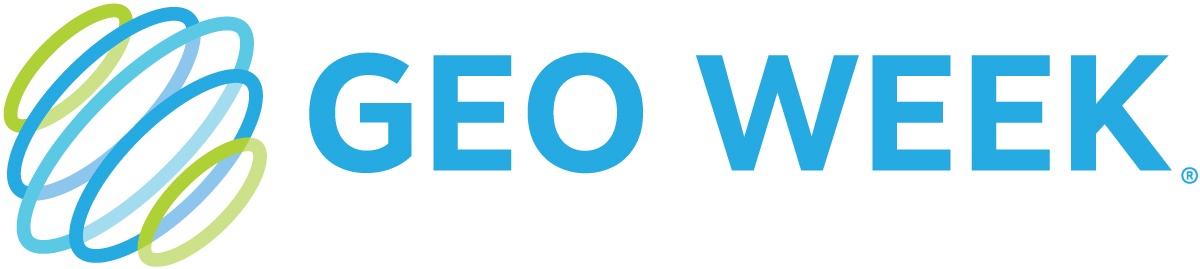
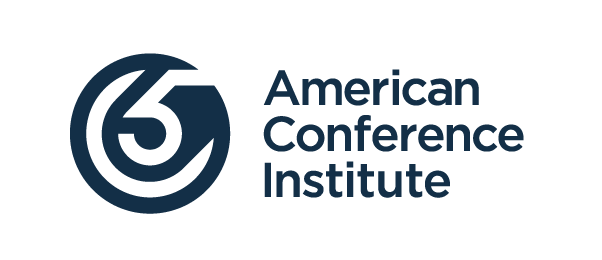
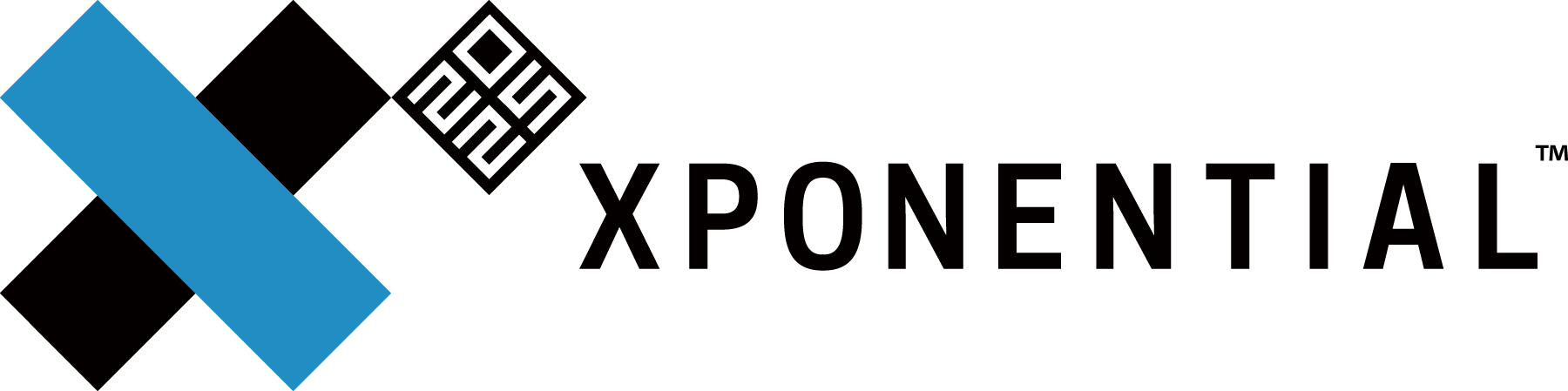
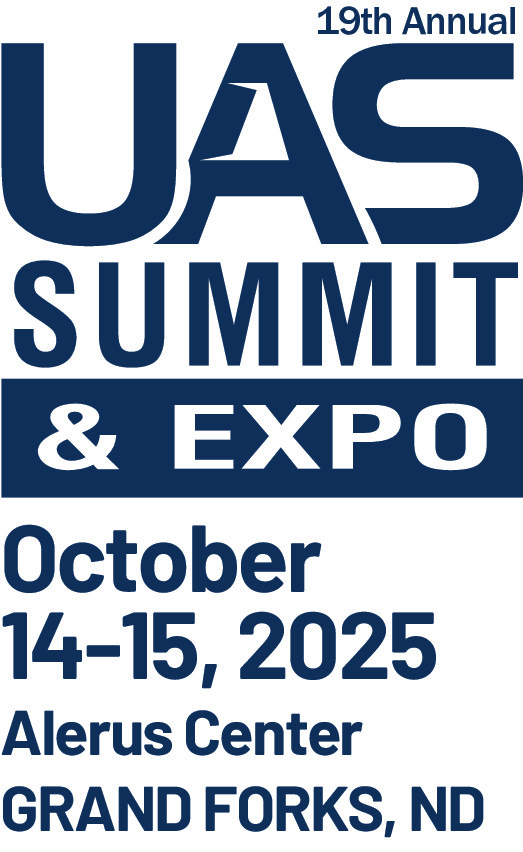
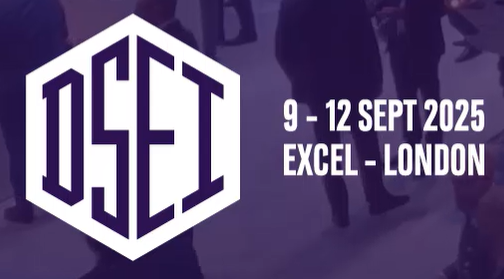
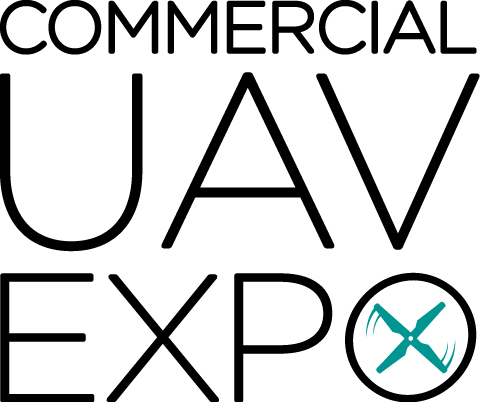
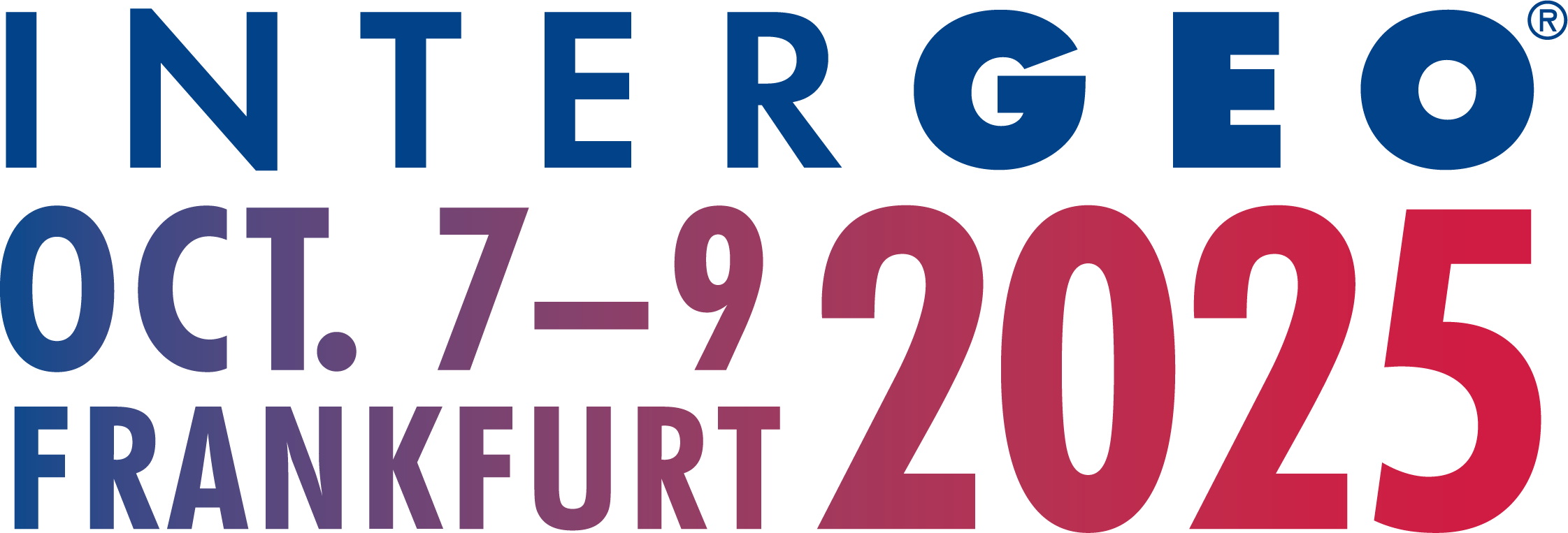
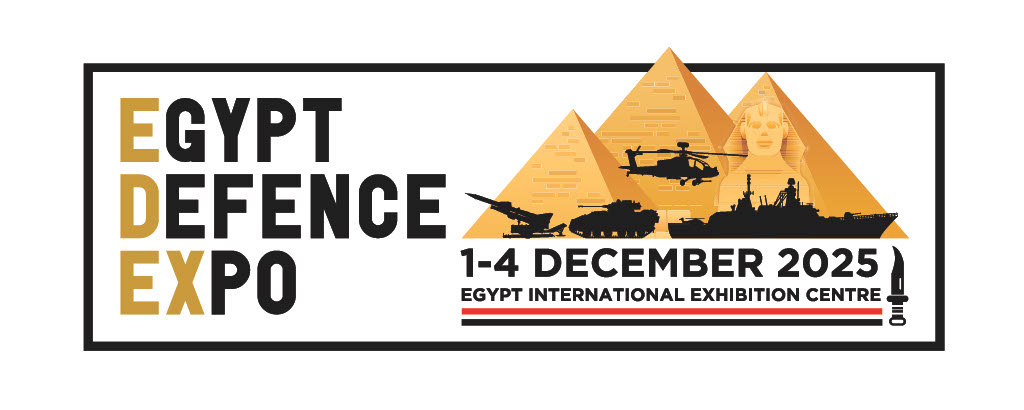
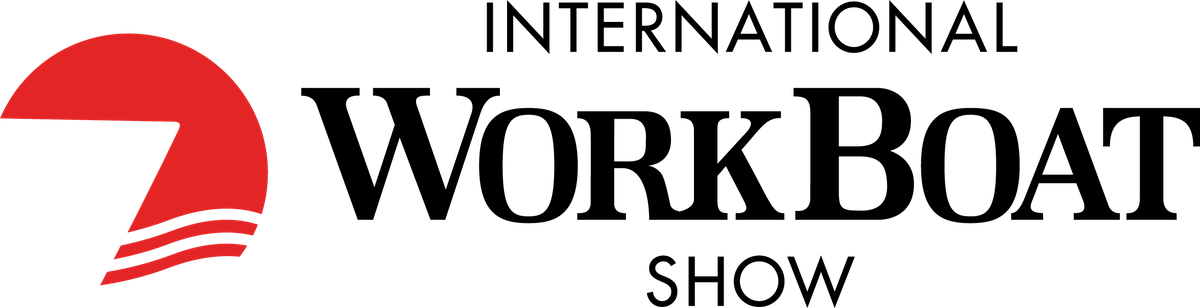
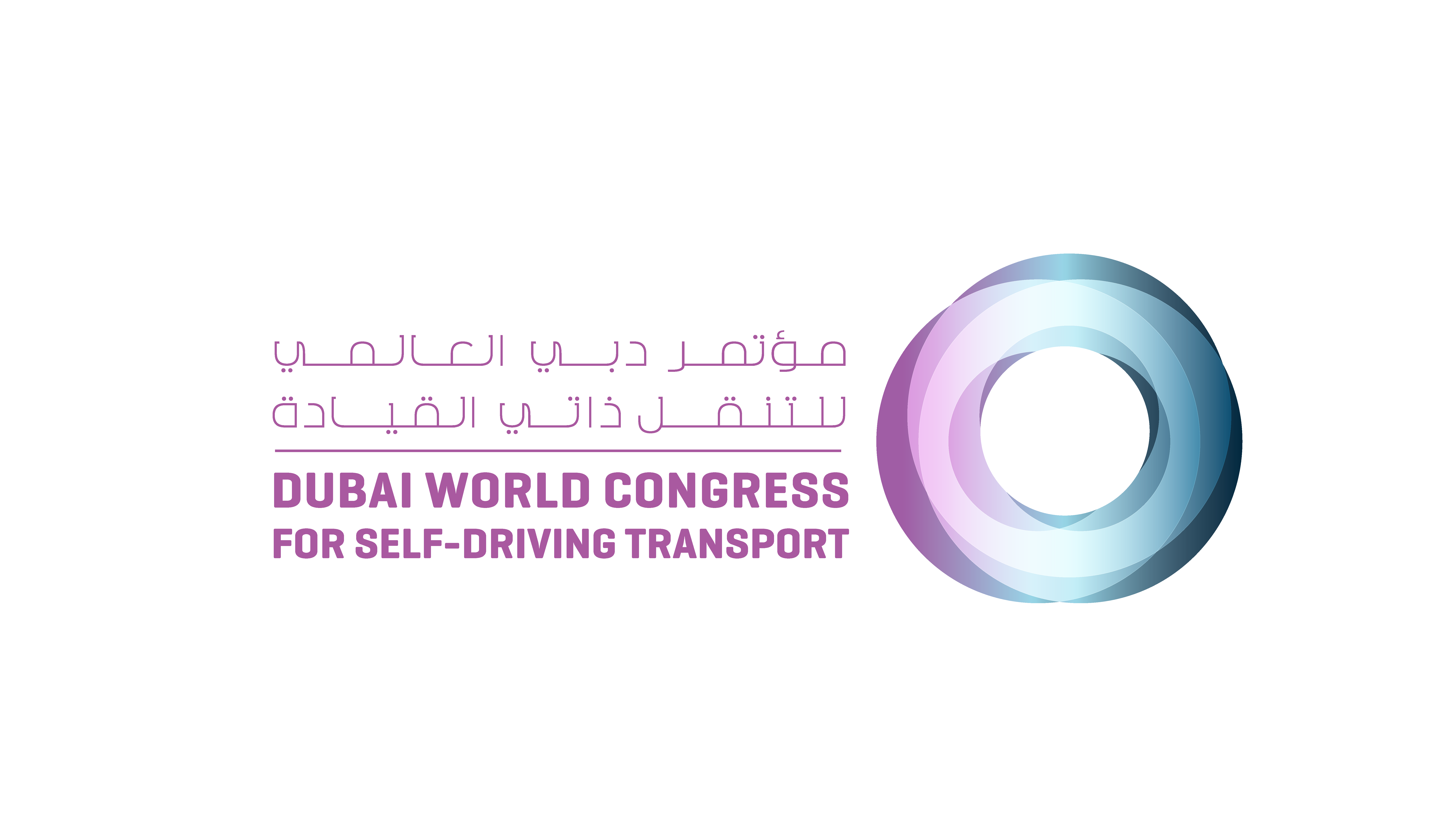
