Amanda Smith
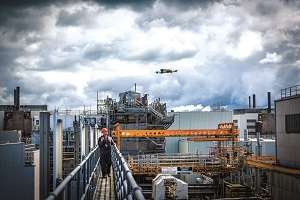
The RTG engineer leading Sellafield’s UAV equipment programme explains its innovative work to Peter Donaldson
Uncrewed aerial vehicles (UAVs) have become essential inspection tools at Sellafield, the large nuclear facility on the coast of Cumbria, northwest England. It treats and stores nuclear waste, and it also carries out decommissioning work on its fleet of reactors, which were previously used for grid power generation and research.
Amanda Smith, 43, the engineer who leads the UAV equipment programme at Sellafield, gained her engineering education at the site and brought its capabilities up to a level that was recognised by a Nuclear Manufacturing Award for innovation, which she shared with her team in November 2023.
Smith’s UAV team is part of the Remote Technologies Group (RTG). She reports to the group’s leader, and four equipment engineers/UAV pilots report to her.
“They live and breathe drones, as they need to know everything from how to fly and maintain them to how to assess new systems coming through. And then, at any one time, I can have one or two graduates from the Sellafield scheme on secondment,” she says. “They learn a lot from us, and we get a lot of work from them to support my team.”
The Sellafield site has many old buildings, complex pipework, tanks, hard-to-access roof spaces, waste cooling ponds and areas that pose various levels of radiation hazard, all of which must be inspected somehow.
The RTG’s remit is to keep people out of harm’s way through the application of advanced inspection technologies. In addition to the UAVs, the group operates robotic arms and a variety of uncrewed ground vehicles (UGVs), remotely operated vehicles (ROVs) for underwater work, and many simpler inspection devices such as cameras on long poles.
“It’s the overall inspection capability that we look at. With a new technology, we will try as many things as possible to see what works, and then bring it back to which tools are best for which job.”
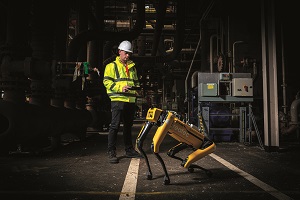
Risk management
The team works on the ‘ALARP’ principle, which seeks to keep risks “as low as reasonably practicable”, Smith explains. “If there is no need to fly a drone over a building or into an area, we don’t. However, if it keeps people away from harm then we do. Usually, that means avoiding having people working at height or in high-dose areas.”
The first UAVs that came to Sellafield were DJI models, used in the security and resilience role, before Smith became team leader. The inspection role arose from the need to check a large number of external ventilation ducts more frequently and thoroughly, she explains. Previously, this involved erecting scaffolding, but it was impossible to inspect the tops of many ducts.
Sellafield’s solution was to bring in an outside contractor to help set up a central UAV team that was able to operate within UK Civil Aviation Authority regulations. Smith’s first task as team leader was to help the contractor understand how things must be done on a nuclear site.
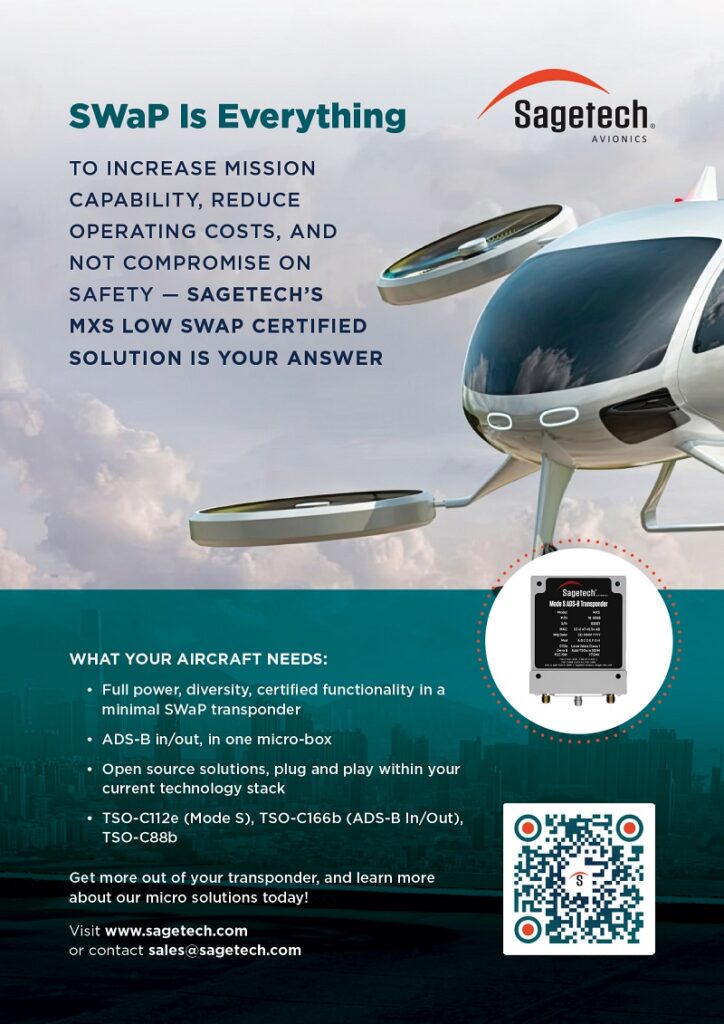
Evolving UAV fleet
The UAV chosen was the Intel Falcon 8, which proved successful. It remains on the fleet but is now getting old and coming up for replacement. “It’s quite hard to find a like-for-like system, but we still use the ones we’ve got, and have multiple spares so we can keep them going for a little longer yet.”
The current fleet includes DJI Enterprise 2 models, which are used for training emergency response teams.
For internal inspections that present collision hazards, the Elios 1, 2 and 3 UAVs are used, which have integral protective cages.
“That’s not to say we can rule other types out, as Elios is relatively expensive, and if we are going to put them into areas with radioactive contamination, potentially we won’t be able to get them back. However, we have proved their value on many tasks to date.”
All of the UAVs except the Elios 2 and 3 are ageing. The DJIs are being slowly phased out and the team is looking for replacements for the Falcon 8 fleet.
Sellafield’s UAV team has two Skydio quadcopters for use in beyond-visual-line-of-sight (BVLOS) operations, for which they are currently going through the process of obtaining Civil Aviation Authority permissions, Smith says.
Each UAV has its own suite of sensors. The most used are Lidar, along with a variety of camera systems for video, thermography and photogrammetry.
Smith says the team is also considering trialling a UAV-based, non-destructive testing (NDT) capability, and they have received demonstrations from potential suppliers, including Voliro.
The company’s multicopters are designed to fly at a wide range of attitudes and feature rotor guards that enable them to apply an ultrasonic non-destructive testing (NDT) contact probe to the surface under testing.
When it comes to developing such new capabilities, the team seeks to anticipate future needs. Historically, at Sellafield, Smith says the approach was to wait for someone to ask, but “now we are doing it differently. We know there’s a need out there, and we know what the technologies can do, and will soon be able to do.”
This, she adds, enables the UAV team to suggest new ways of doing things to their customer at Sellafield, while also nudging the UAV industry in directions the team would like it to take.
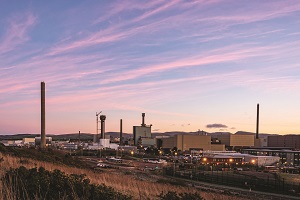
Contaminated area ops
Any of these vehicles may have to fly into contaminated areas to carry out inspections, which raises issues around their decontamination and retrieval.
“We work closely with the plant areas that we’re going to be flying in, so we understand what their contamination levels are, and what the risk is of contamination entering any parts of the systems,” Smith says. “If they can monitor their equipment and prove there’s no contamination anywhere, then we can get our systems back out, and that’s fine.”
Decontaminating the UAVs can be difficult as air is drawn through the motors to cool them, and it is not usually possible to take them apart to physically check for contamination. “We’ve got multiple areas across the site where a drone has been flown in and now has to stay. They can be used for future tasks within those buildings or plants, so they are not sacrificed completely,” Smith says.
Those vehicles must be maintained while they remain operational, and this mostly involves changing batteries, which generally prove to be clean when checked, so they can be taken back to the UAV team’s maintenance facility. However, with more involved tasks, such as changing propellers or motors, or carrying out a thorough check, it has to be done in situ, wearing personal protective equipment (PPE).
“We always make sure, where possible, that we can either get the system to a location where we can maintain it, or if we can’t physically get in ourselves, we work with the plant to determine whether they have operators that we can train up to carry out basic tasks,” Smith says.
When selecting new vehicles, any elements of their design that make it easier to work on them in PPE are important, she says, “because for some of these areas we’re talking about, they’re going into [them] in full PVC air-fed suits, and possibly three pairs of gloves. You’ve lost a lot of your dexterity when you’ve got that many pairs of gloves on.” Anything sharp on the vehicle is a potential hazard.
The team must consider what to do if a vehicle suffers a failure and becomes stuck in a contaminated area. Any such case will receive its own risk assessment.
“Each individual plant will look at the risks to understand what is the worst that can happen,” Smith says. “We will tell them the worst thing that will happen is that they will have a UAV with a lithium-ion battery stuck in the area. They will look at their safety cases and decide whether the risk is acceptable under the ALARP principle.”
Retrieval and confined spaces
The risks involved in any retrieval effort will be judged on the same basis. While the team hasn’t sent another uncrewed vehicle to retrieve a downed UAV yet, they did use a tether on a Tiny Whoop UAV that was used in a trial where it was sent down through a 150 mm-diameter access port to take a sample from an interior wall with a swab.
“We tied fishing line to it so that, in the worst case, we could pull it back up to retrieve it. It was an interesting task and it satisfied the team we were working for.”
This experiment also led to Sellafield’s Game Changers challenge to develop UAVs for use in confined spaces, which went out to industry through innovation facilitator FIS 360. “Now we’ve got two companies at the proof-of-concept stage with systems that can access these sub-150 mm port entries.”
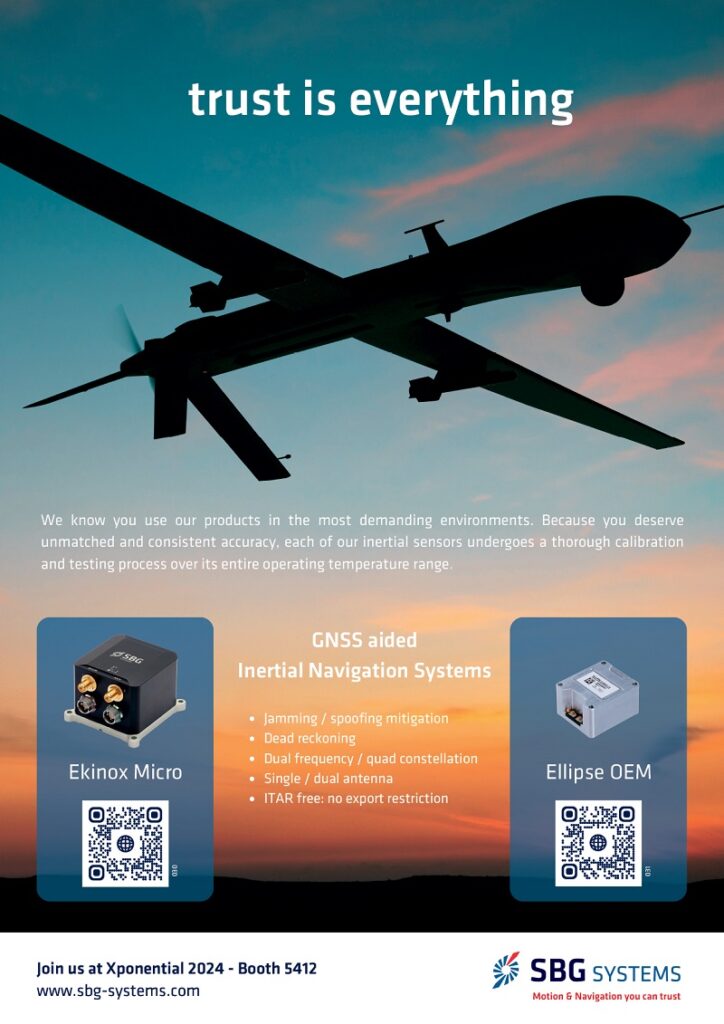
BVLOS plans
Until the team is granted BVLOS permissions, all the vehicles must have a remote pilot. Even though some missions are flown automatically to a pre-loaded flight plan, the regulations say the pilot must maintain visual contact with the UAV.
“If we do get our BVLOS permissions through that’s the first step down the fully autonomous route,” Smith says.
“We would love to get into a position where we can do that at Sellafield, particularly for emergency response. We don’t want to send pilots onto the site if there’s an incident. We would much rather they were sitting in a control room offsite and be able to fly as if they were really on site.”
Meanwhile, the plan is to use BVLOS capability to open up areas that UAVs currently cannot inspect (even though they can access them) because there is nowhere the pilot can stand to maintain a line of sight with it. That might be as simple as being able to get behind a ventilation stack, for example.
Looking forward, Smith would like to see Sellafield’s UAV capability begin to grow, with a balance of internal personnel and outside suppliers.
“My core team is really small, and we can’t do everything all the time, so if I can use SMEs to boost what we can do internally, I can see growth taking off exponentially,” she says.
“We do a lot of work across the Nuclear Decommissioning Authority (NDA), and there are multiple sites with their own drone teams, so we are working together to learn from each other and gain value for money. I would like to keep that ball rolling and create a unified NDA UAV team.”
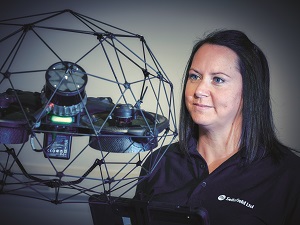
Amanda Smith
Born in West Cumbria in 1980, Smith attended the Wyndham School in Egremont from the age of 11, where she developed a talent for mathematics. “I like to know a definite answer,” she says. “That’s probably why I like being an engineer, because there’s a right and a wrong answer, and you know how you got it.”
Maths helped her into engineering, but via a route that narrowly avoided accountancy. “I’d applied for universities and wanted to be an accountant, but when it came to actually going to university, it just didn’t feel right, so I took a step back before I could get into a lot of student debt and run up bills for my dad to pay.”
Instead, in 1999, Smith got a job at Sellafield as a technical assistant in a team tasked with testing handheld radiation detectors, subsequently joining a team of electricians and mechanical fitters, again as an assistant.
The desire to do more led her to an electrical and instrumentation (E&I) apprenticeship. After excelling at this, Smith went on to gain a Higher National Certificate (HNC) in E&I engineering and associated National Vocational Qualifications (NVQs) at Lakes College in West Cumbria in 2006.
Five years ago, her line manager, Craig Branney, whom she regards as a mentor, suggested she take the newly open leadership position in the UAV programme. His main piece of advice about developing new capabilities was to seek forgiveness instead of permission.
“We err on the side of caution and there are often barriers, but we’ve seen the benefits of UAVs and he’s a full advocate of pushing the walls down,” she says.
Outside work, Smith has rediscovered the power of the gym to improve her fitness and clear her mind.
UPCOMING EVENTS
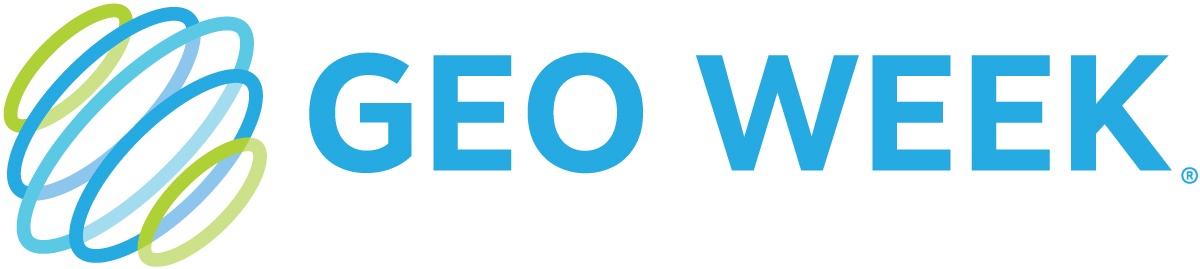
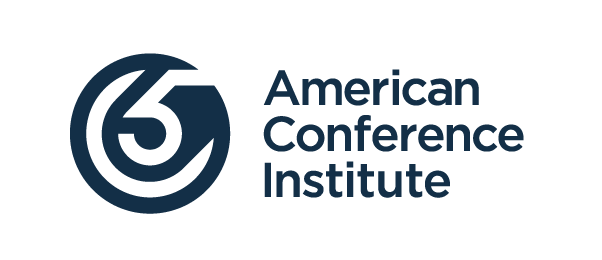
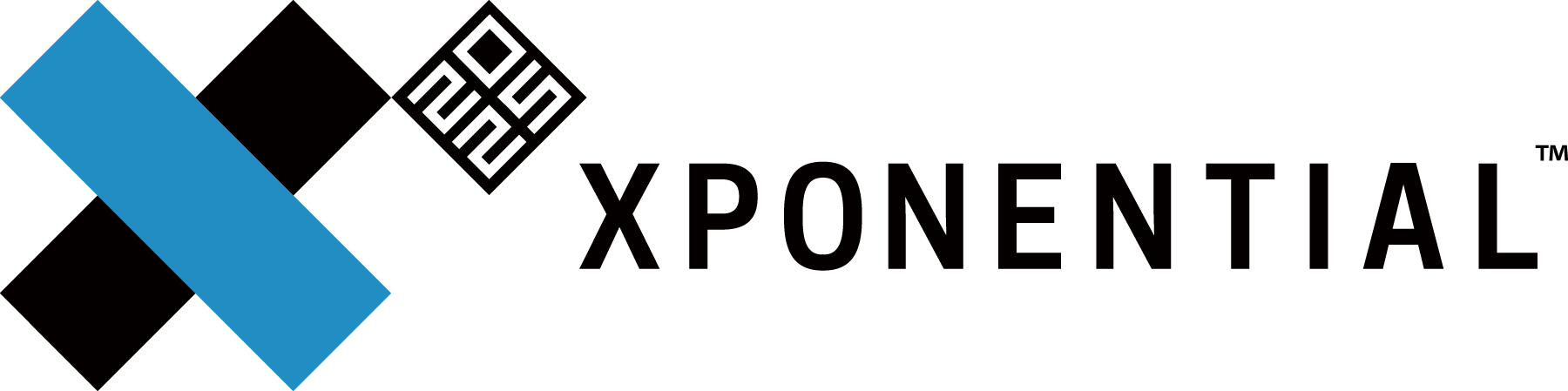
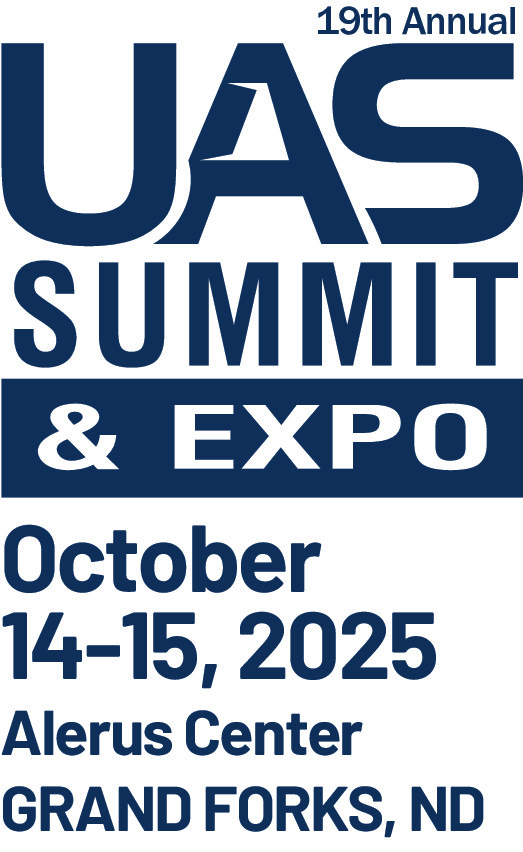
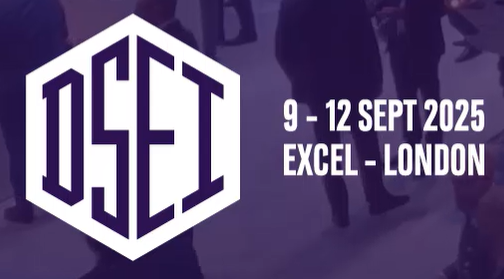
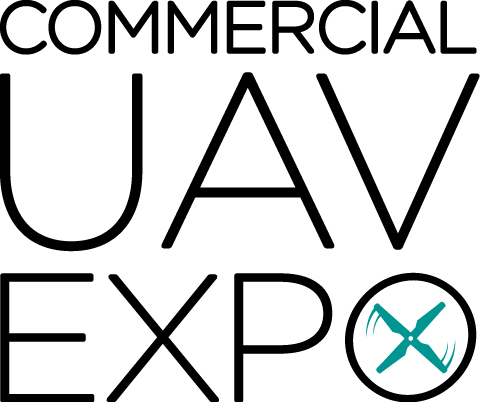
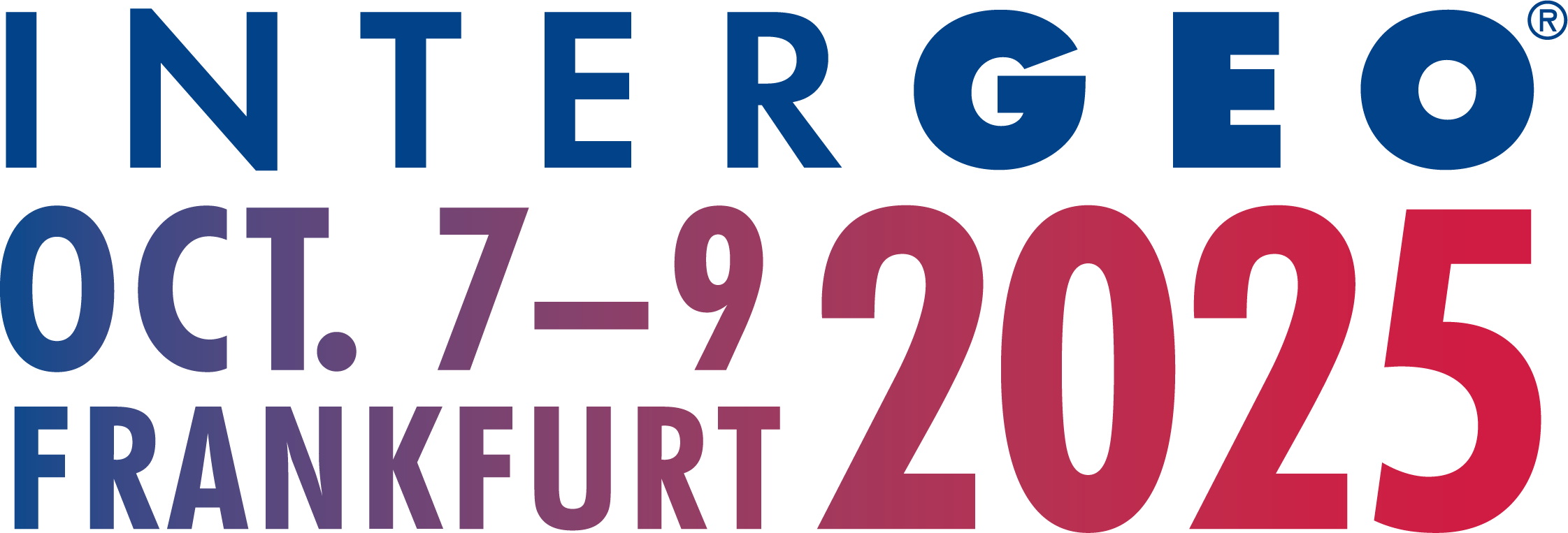
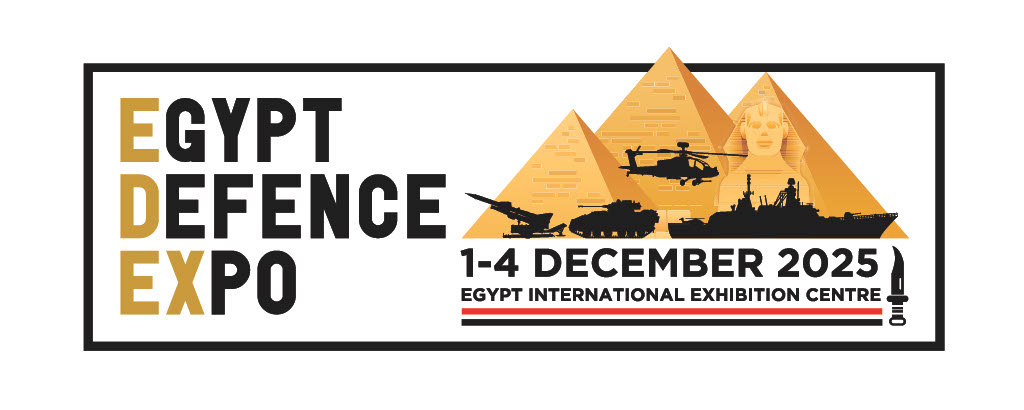
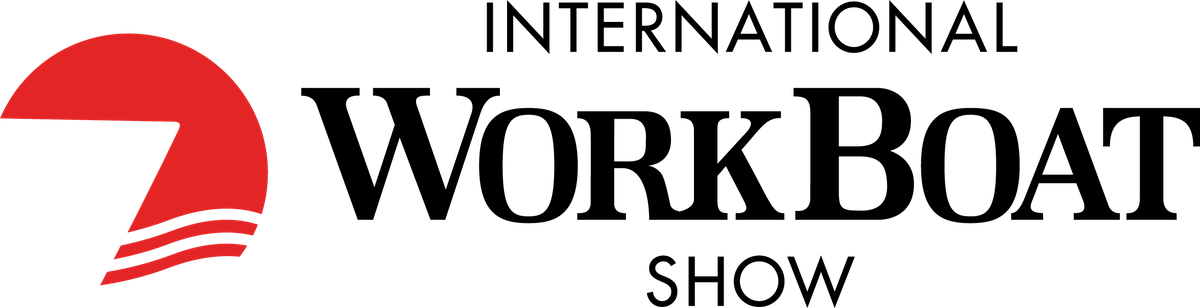
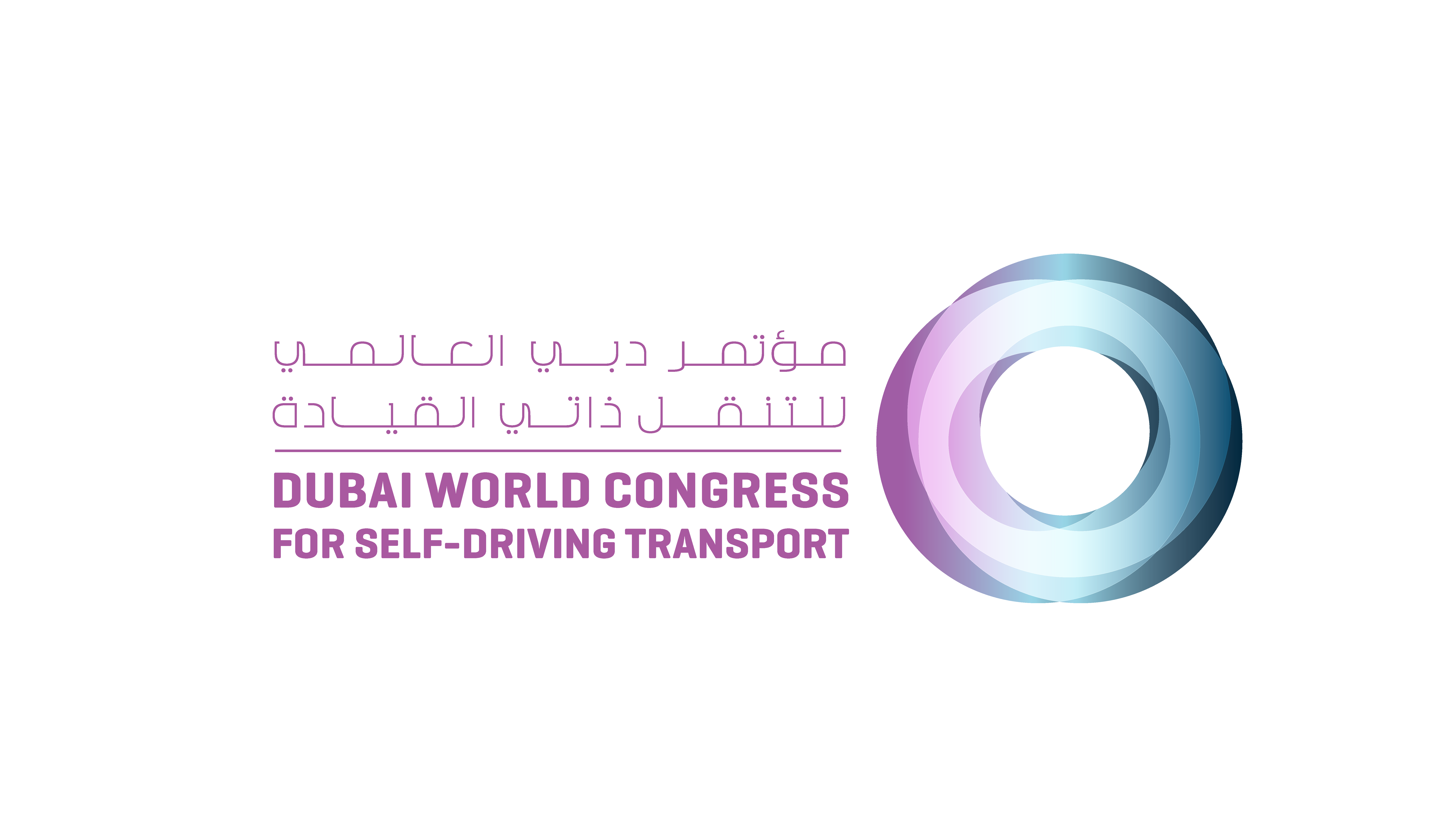
