Battery technology
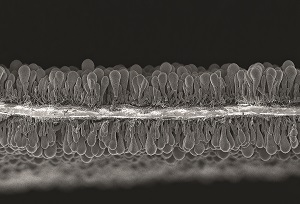
Nick Flaherty explores the new wave of battery tech, boosted by AI, 3D printing and enhanced materials
A new generation of materials is boosting the performance of lithium battery cells in commercial production, reducing weight while increasing power. The use of silicon anodes, nickel manganese cobalt aluminium oxide (NMCA) cathodes, lithium sulfur and solid-state electrolytes are all improving the energy density of cells.
Increasing the safety of lithium cells through additives or solid-state electrolytes reduces the need for additional sensing and protection, further reducing the weight of the battery pack. 3D printing with solid-state materials opens up new ways to use batteries in different shapes, while AI is identifying thousands of new substances that could lead to improvements in gravimetric specific energy, as measured in Wh/kg, and volumetric energy density, as measured in Wh/L for smaller cells.
All of this is helping designers of uncrewed aerial vehicles (UAVs) and autonomous electric vehicle take-off and landing (eVTOL) aircraft to boost mission times, often doubling performance, and providing faster charging rates for quicker turnarounds and more time in the air.
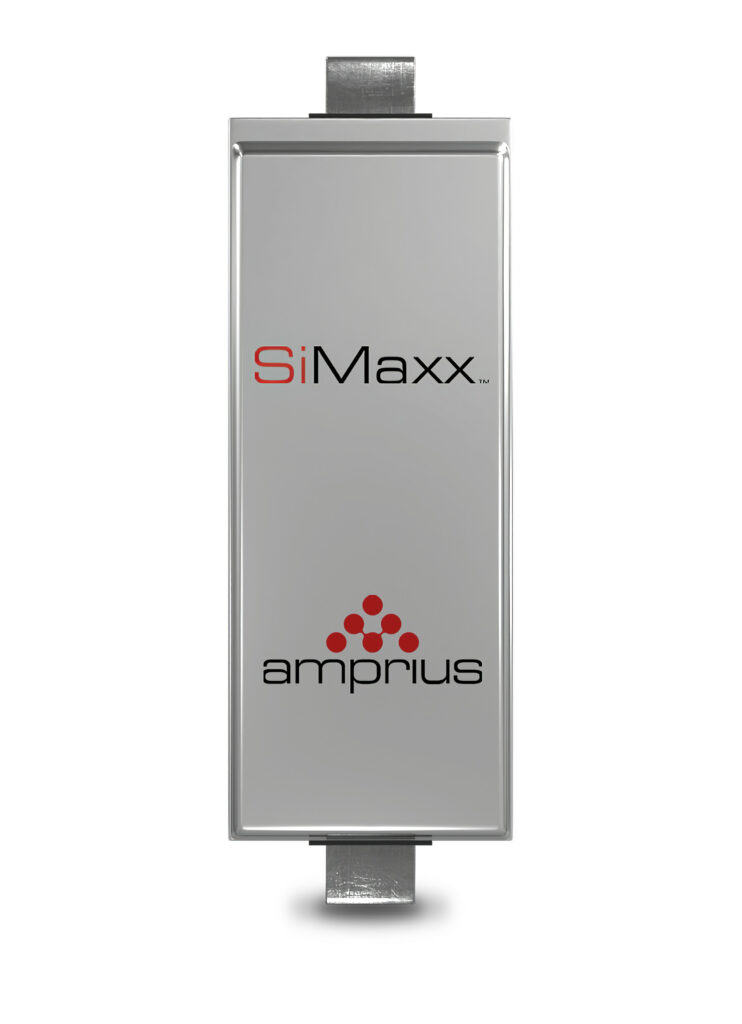
Silicon anodes
A key technology for batteries in uncrewed systems is using silicon as the anode. While silicon has twice the energy capacity of carbon, it suffers from significant expansion of many times its original size when charging. This leads to safety issues as a cell will swell when charging and discharging, risking the lithium-based liquid electrolyte leaking out and catching fire.
The current approach is to use silicon alongside various types of carbon, from 3D structures to encasing the silicon in carbon nano-structures, which provide an incremental increase in energy capacity.
However, for airborne applications, particularly High-Altitude Pseudo Satellites (HAPS) that operate at altitudes above 60,000 ft and need to store power from solar cells for operation overnight, this requires significantly higher energy-density battery cells and a new approach.
One method is to produce a full-silicon anode without graphite and binders, and this is being used by all three main HAPS developers. This started in 2009, to develop the structure that supports and adapts to the expansion of the silicon using nanowires without using other materials, thereby improving energy density.
This uses a 3D structure, where expansion happens at nano level, so the nanowires move around and can expand without pushing out the cell. The nanowires, typically 10 μm long, are grown from the foil on the current collector directly, like a carpet, with the fine wires on both sides, using a high-temperature process. This produces an electrode that resembles a coated electrode, only thinner and more flexible.
Another advantage of the silicon nanowire is that it is grown vertically on the foil, so wires of varying lengths can be produced for different loadings, avoiding the limits on power loading that comes from graphite and carbon/silicon anodes.
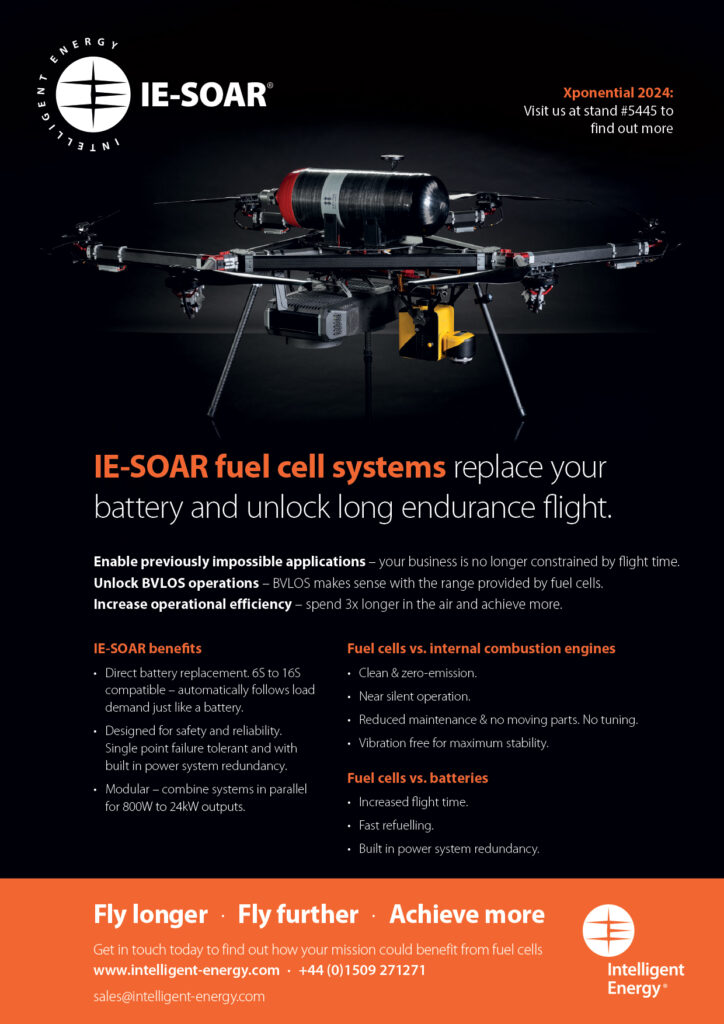
Most of the HAPS projects are using the anodes in pouch cells of varying sizes to fit into different parts of the airframe, but the anodes can also be used with cylindrical cells.
These have a slow charge and discharge requirement that is suitable for high-energy designs at 500 Wh/kg with a 0.5 C charging rate, moving to 1 C. For higher charging rates of 2 C, the power density is lower, at 450 Wh/kg.
With full-silicon anodes at 450 Wh/kg and 1300 Wh/L, this is almost double the current technology using standard NMC commercial materials. The smaller cells measure 5 cm2 with a capacity of up to 5 Ah, while the mid-sized cells that are starting to be used in UAVs have a capacity of 10-20 Ah. Larger projects for self-driving cars and eVTOLs for urban mobility are looking for cells with a capacity of over 50 Ah.
The NCMA cathodes use nickel, cobalt, manganese and aluminium oxide, with increasing proportions of nickel to reduce the need for cobalt. However, these NCMA cathodes are not yet fully integrated into commercial cells and would give a 5-10% boost to 500 Wh/kg.
This can go to 550 Wh/kg with the current materials as a ceiling. New cathode materials in development will raise the energy density to 700-800 Wh/kg with lithium-ion electrolytes by 2030. Higher than that, the 1000 Wh/kg goal requires a lithium metal anode.
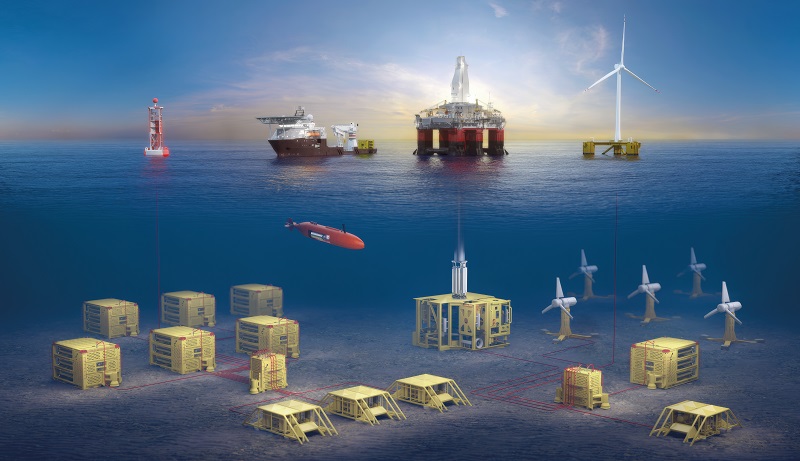
Stress-testing
Researchers have stress-tested a set of custom lithium-ion cells at very high charging rates up to 60 C to see how performance changes.
There is demand for more high power-driven studies to assess the extremely fast charge and discharge needs for advanced air mobility applications. United States Advanced Battery Consortium (USABC) guidelines for testing batteries for EV applications indicate peak power testing at 5 C discharge current for a pulse duration of 30 s.
Depending on the type of eVTOL system, loading can range from 200 N/m2 up to 1000 N/m2, which needs a discharge rate ranging from 10 C to 60 C, with peak power required at both the beginning of the discharge cycle (low depth of discharge) and at the end of discharge (high depth).
In specific power terms, these values can potentially exceed 1000 kW/kg, depending on the mass of the payload, mission profile and aircraft design.
To test this higher level of power requirement, specially designed cells containing a fast charging and discharging electrolyte were discharged at 15 times the battery’s optimal capacity – the total amount of energy it could store – for 45 seconds. This process simulated the rapid, high-power discharge required during vertical take-off. After the initial discharge pulse, the cells were further drained at a more normal discharge rate and then recharged.
The cells are charged at a nominal 1 C-Rate until a full state-of-charge (SoC) is achieved with a 4.2 V cut-off. At the beginning of discharge, a current pulse equivalent to 15 C is applied for 45 s. Subsequent discharge is carried out at a nominal C/3 current. For the batteries investigated here, 1 C corresponds to ~0.08 A, while 15 C corresponds to roughly 1.2 A.
The team found that none of the tested cells lasted more than 100 cycles under these high-stress conditions, with most starting to show decreased performance at around 85 cycles.
After being stressed, the cells were subjected to a more normal, lower-rate power draw. This showed the cells partially retained their capacity under low-rate conditions, but failed quickly when placed under rapid current drain conditions again. This shows that existing fast-charging cells might not have the characteristics necessary for long-term, high-stress usages, but they could be retired and meet more typical power demands in other applications, such as battery back-ups for power supplies and energy-grid storage.
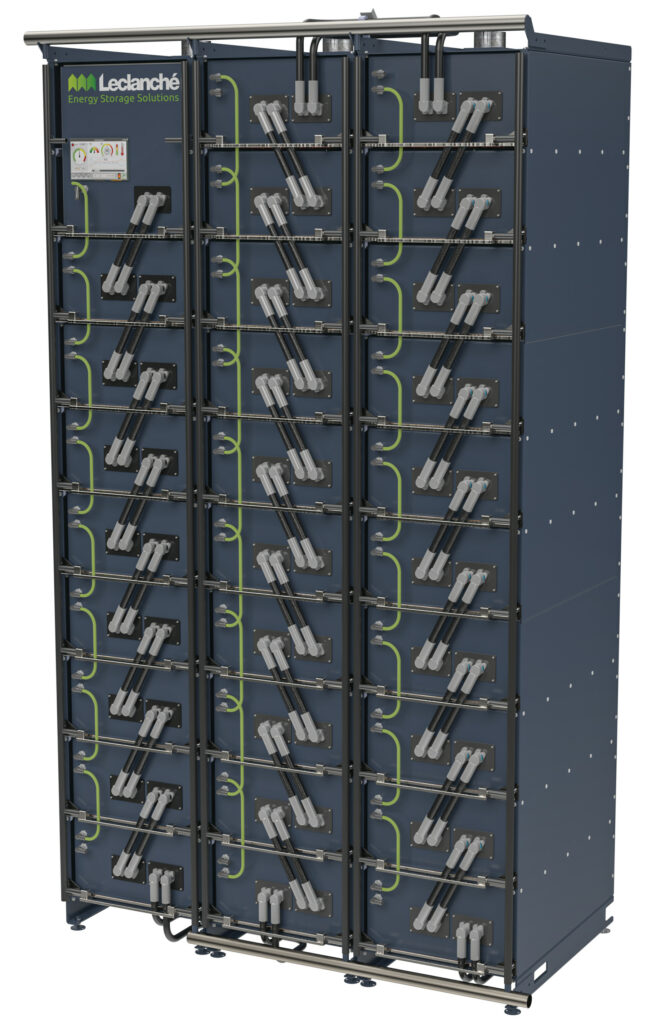
Maritime power
Increasing the power density with cathodes using NMCA and silicon anodes brings more safety considerations.
Adding a fire-retardant additive to the water-soluble electrolyte formula composition lowers the risk of a thermal event by close to 80%. This has been demonstrated in industry standard nail-penetration tests on a 60 Ah cell.
Despite the test cells being punctured with the resulting internal short circuit, they exhibited a far lower risk of fire than the same cells without the flame-retardant additives. This is particularly important for electric uncrewed maritime systems.
With the higher energy density, liquid cooling technology is needed in the marine battery systems to manage the increased heat generated. This method efficiently dissipates heat, maintaining optimal operating temperatures and prolonging the life of the battery. Additionally, liquid cooling enhances safety by reducing the risk of overheating and thermal runaway events, which is crucial for marine safety. These systems are integrated into the vessel’s infrastructure to minimise the need for space.
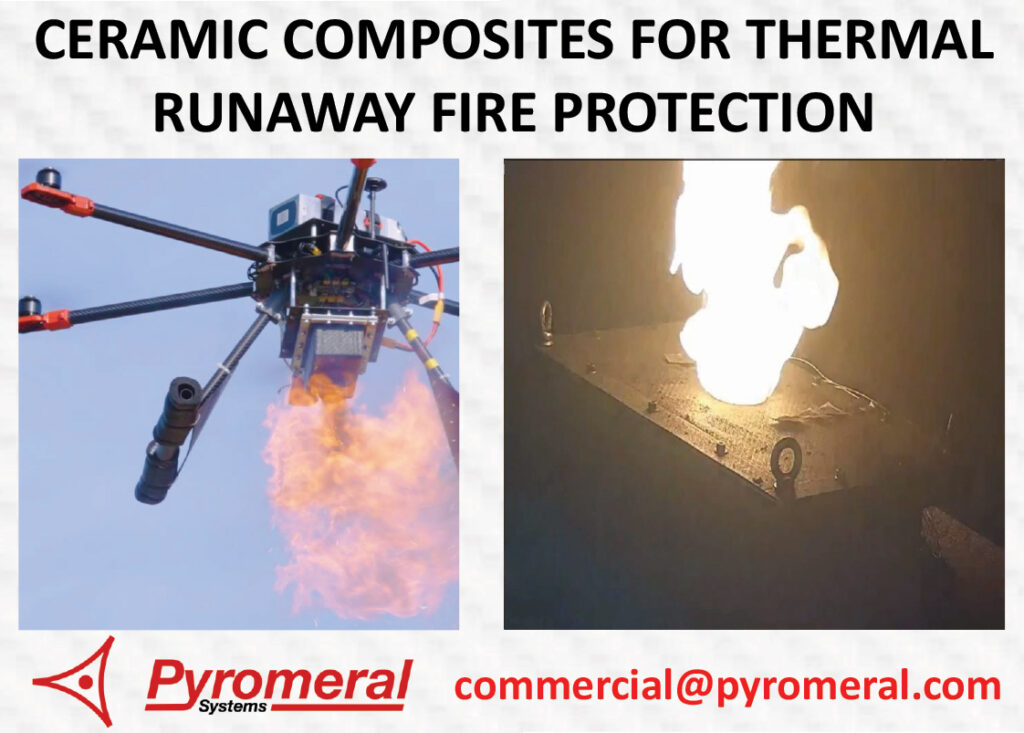
Underwater power
A cylindrical battery pack is providing power for uncrewed underwater vehicles (UUVs) and underwater charging stations. The design started out with a 180 mm-diameter cylinder in a titanium housing using lithium ion cells. This operates to a depth of 6000 m for ocean monitoring and seawater quality control. The 6 m long, 361 Ah cylinder weighs 17 kg in the air and 9 kg in water.
However, demand for higher voltages up to 600 V are driving the need for a modular system with larger diameters for various UUV platforms – beginning with a 310 mm diameter to target the majority of underwater applications, and then a smaller, 260 mm version and a larger one of 416 mm.
These are all built with smart power modules using the same standard, 18650 cylindrical lithium-ion NMC cells that are used in electric vehicles. Arranged in concentric circles, the cells are always one cell deep and come from the same manufacturing batch to maintain consistency as much as possible.
A standard stencil is used to arrange the batteries in the modules, and the length of the pack depends on the capacity required. There are about 300 cells for a 6.6 kW module.
All the data from the sensors in the module runs through a 12-pin connector to a monitoring module at the end of the cylinder. Current monitoring is on the top of the module. The modules are placed on a rail and connected in parallel with connectors that have four power lines, one charge control line and seven data lines.
There is cooling for each module as these are in air. There are two fans that move the air around to minimise hotspots with a typical 3.5 C to 35 C operation, and 7 C to 45 C for charging.
The housing is aluminium, stainless steel or titanium, depending on the depth of operation, with aluminium down to 100 m and stainless steel for high-reliability projects to 1500 m.
The cylinders are also used for underwater power storage, with both wired and wireless inductive charging of UUVs being developed.
The highest demand was 1 MWh in a unit measuring 3 m high and 4 m wide with 12 86 kWh battery packs. Metal-cage barriers are used to prevent thermal runaway between the modules.
For a UUV, the packs can be fully cylindrical or half-round if there is a space limitation. Unlike for aircraft, the weight is not that important for UUVs because of the buoyancy. It is typically 400-600 kg, 1 m to 1.3 m in length, and 416 mm in diameter – consisting of 10 modules with the BMS for power demand for 4-6 kWh.
It is possible to move to the larger 21700-format cells, but this would require a change in design as the standard stencils mean there is actually less capacity because of the additional space between cells.
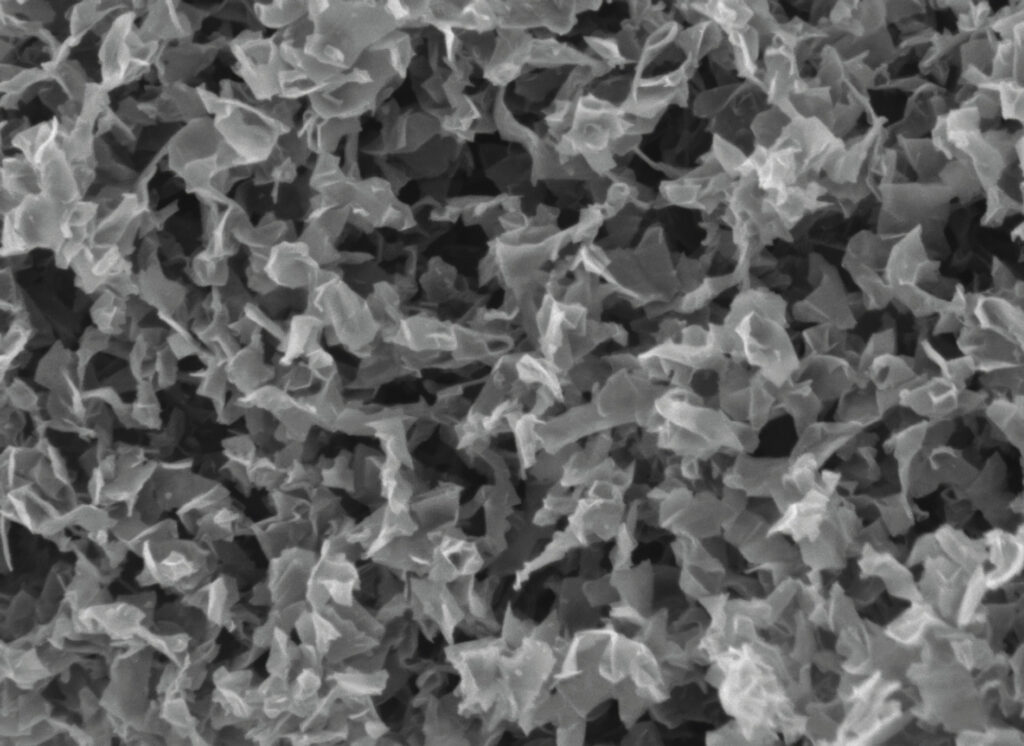
Sulfur
A 3D version of graphene is key for a new generation of lightweight lithium-sulfur cells. The 3D graphene is tuneable in the production process and can be engineered at the atomic level to bond with other elements. This can optimise thermal and electrical properties, or customise porosity to improve strength and stiffness or decrease weight.
The battery chemistry requires no nickel, cobalt or manganese in the cathode, and no graphite in the anode, allowing the lithium-sulfur battery to be fully sourced and manufactured locally in North America or Europe. Lithium-sulfur cells in both cylindrical and pouch formats are being produced using the same equipment and manufacturing processes as traditional lithium ion batteries. These have an energy density of up to 900 Wh/kg, making them suitable for UAV designs.
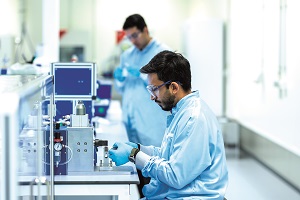
Solid-state batteries
There are several competing technologies for solid-state batteries (SSBs) that combine lithium-metal anodes with a solid electrolyte to boost the energy density of cells.
This drive to SSBs aims to address the safety issues of cells with liquid electrolytes that can leak and catch fire. Mitigating the safety risks in a battery pack with separators and monitoring adds weight and cost to the system, which is a key consideration for UAVs.
Using a higher-capacity cell that is inherently safe with a higher gravimetric energy density, as measured in Wh/kg, and an energy density above 800 Wh/L will drive adoption in airborne systems. However, these cells need to have a high C-Rate for faster charging, so that a UAV can get back in the air, and a longer cycle life than current solid-state batteries so the packs can operate reliably and safely for several years.
The main contenders for SSBs are sulfite materials, oxides and polymers. A solid-state polymer electrolyte that works with the silicon anode starts as a liquid, but converts into a solid in the cell, so it doesn’t change the manufacturing method. This was developed for military products that need to be bullet-proof but can be integrated into other products.
Maintaining the manufacturing process is key. Changing one step needs to match the throughput of the rest of the factory, and if the equipment is not mature it can take two to three years to catch up. That’s why it will take time for silicon anodes to be integrated into cell production at GWh scales of manufacturing.
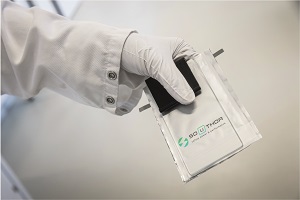
Nano-composite electrolyte
One potential technology for solid-state batteries for aircraft such as UAVs and maritime uncrewed surface craft is a silica-based, nano-composite matrix.
The key for the energy density, as measured in Wh/L, is to finesse the thickness of the electrolyte material, and the first versions use a layer that varies from 500-900 μm, or almost 1 mm thick. This is reducing to 30-50 μm and, along with very thin lithium-metal anodes, allows multiple layers to be stacked in a high-capacity cell.
One version of the electrolyte is thermally stable above 200 C, up to 300 C in a 3 Ah cell. This high-temperature operation is key for airborne applications, where the battery can be closer to the high-temperature inverter, and operate at atmospheric pressure and below.
Other important aspects include the ability to use commercial cathode materials such as NMC lithium and to fit the application of the electrolyte into existing commercial cell-manufacturing processes, rather than requiring high pressure to compress the anode during manufacturing or high pressure in sealed cells during operation.
Using lithium metal as an anode is only becoming possible with a solid electrolyte due to previous safety issues, but the ability of the solid electrolyte to transfer the lithium ions from the cathode to the anode is crucial.
In a liquid electrolyte, this is much easier as the ions move in the liquid. The solid electrolytes need to have a structure that allows ions to move through it to give higher conductivity and support higher current rates, but this leads to more heating effects.
The nano-composite matrix, which is similar to a polymer, has a conductivity of 1-10 mS/cm (milliSiemens per cm) at room temperature, which is close to a liquid electrolyte. The matrix includes lithium ions and allows them to move on the walls of the nanopores in the matrix, acting as highways for the lithium ions to move along.
Before it becomes solid, the material is a liquid precursor, so it can be added to the existing battery cell manufacturing process before it solidifies.
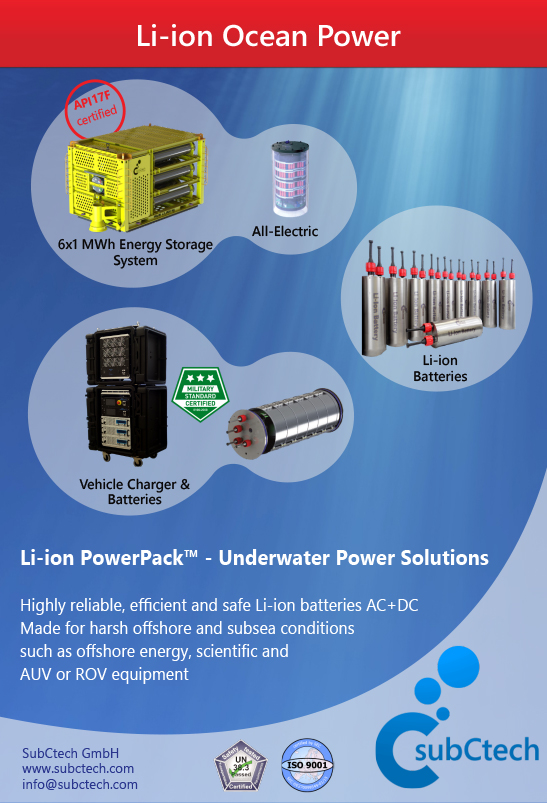
The nano-composite matrix is a family of materials with additives to tune the performance for conductivity for faster charge/discharge, thermal behaviour, and how soft or hard it is for the interface to the lithium metal anode and the cathode.
This allows the solid electrolyte to be used with conventional cathodes, such as NMC 622 and 811, and high-nickel cathodes that have more power and less cobalt, while still being as close as possible to the existing manufacturing lines as a drop in replacement material.
The first-generation cell with an NMC cathode shows an energy density of 340 Wh/kg and >800 Wh/L to be on a par with current liquid cells, with a charging and discharging rate of 1 C and 500 cycles.
The second-generation cells are targeting 385 Wh/kg and 1100 Wh/L, with a 3 C-Rate and a lifetime of 750-1000 cycles.
Meanwhile, the third-generation cells are aiming to be above 450 Wh/kg and 1100 Wh/L, with the same or higher C-Rate. This is a bigger challenge, as the current density is much higher, and that higher current has an impact on cycle life.
This is particularly important with a 3 C discharge rate, according to the mission profile for the aircraft, with higher power requirements at take-off and landing, rather than during horizontal flight.
Performance in a module is also important to assess, as cells can start to behave differently when placed together, so there is a need to optimise the module.
Another solid-state battery system that is currently sampling for evaluation uses a lithium-metal anode with a solid electrolyte. This has an energy density of 950 Wh/L for the active cell area, which translates into a specific energy of 260 Wh/kg for a cell. The specific power is 792 W/kg at a 3 C discharge rate.
The cell has a 3 C sustained discharge for high-power applications, with a peak of 10 C with full recovery. Testing has shown a lifetime of more than 400 cycles to 80% capacity, which is key for UAV performance.
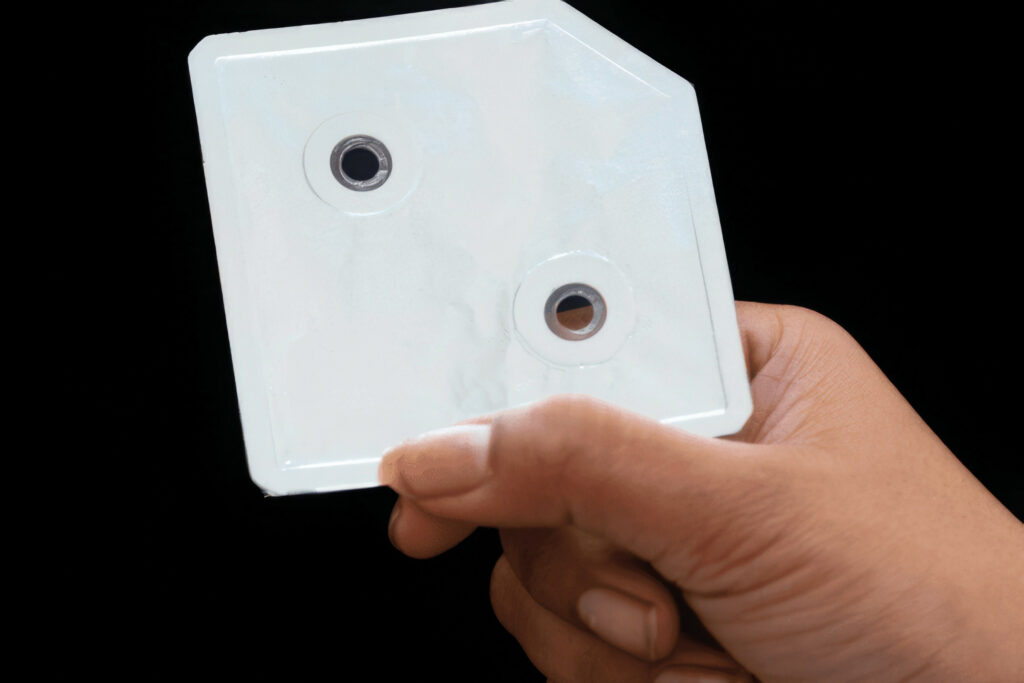
(Image courtesy of Sakuu)
3D printing
The move to solid electrolytes creates the opportunity to use additive manufacturing to print battery cells. It has the ability to quickly modify performance and create cells in non-standard formats. This is particularly important as the improved safety of the materials allows for conformal batteries that make up part of the structure of a vehicle.
This can reduce the weight of the vehicle or allow more power in the same-sized design, and also allows a sensor to be added inside the battery cells for more effective monitoring.
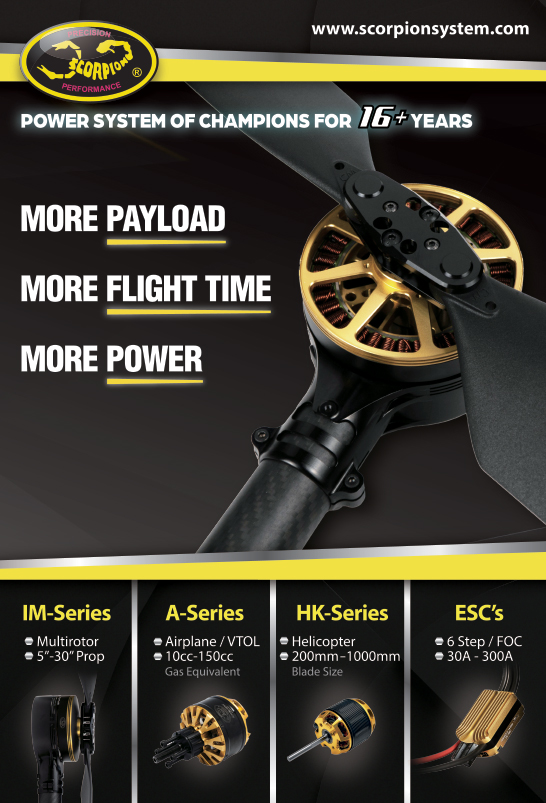
The first versions have been printed as cells containing patterned openings for thermal management. This uses a proprietary, multi-material, multi-layer approach in a parallel and dry process, instead of layer-on-layer printing or screen-printing, which is used to build solid-state battery cells. Those inherently wet processes require significant energy to remove unwanted solvents, and they are susceptible to poor printing quality and unreliable production.
The first printed batteries with a lithium-metal anode have demonstrated successful cycling performance at a slower C/5 charging rate and are expected to achieve an energy density of 800-1000 Wh/L.
Future directions
Generative AI is being used to discover and produce new electrolytes for solid-state batteries, and to speed up the testing process.
A tool called the Graph Networks for Materials Exploration (GNoME) was trained on data about the efficiency of 48,000 stable materials. This identified 2.2 million possible structures, many of them new. The AI then sifted through the list to find 321,000 potential materials that were then simulated at a molecular level to determine the functions to an accuracy of 11 megaelectron volts per atom (meV/atom).
Of the stable structures, 736 materials have already been independently experimentally produced to verify the AI output.
A hybrid approach couples experimental and simulation methods, enabling insights into the formation process and characteristics of battery interfaces at the molecular level, while using experimental data to improve the accuracy of the models. This uses AI to extract patterns from gigantic data sets for electrolyte design and battery life prediction.
For testing, a tool called Coscientist, which is driven by GPT-4 generative AI, can autonomously design, plan and perform complex experiments with code execution and experimental automation. This is used to accelerate research across various tasks with autonomous experimental design and execution.
While this might find new electrolytes and cathode materials, and also speed up confirmation of the suitability for building battery cells with higher energy density and lower weight, there are many steps to producing the cells in volume.
Ease of integrating materials into existing industrial manufacturing processes is increasingly the dominating factor for the adoption of battery cells to create reliable power packs for UAVs and autonomous eVTOL designs in the air, and for driverless cars on the ground.
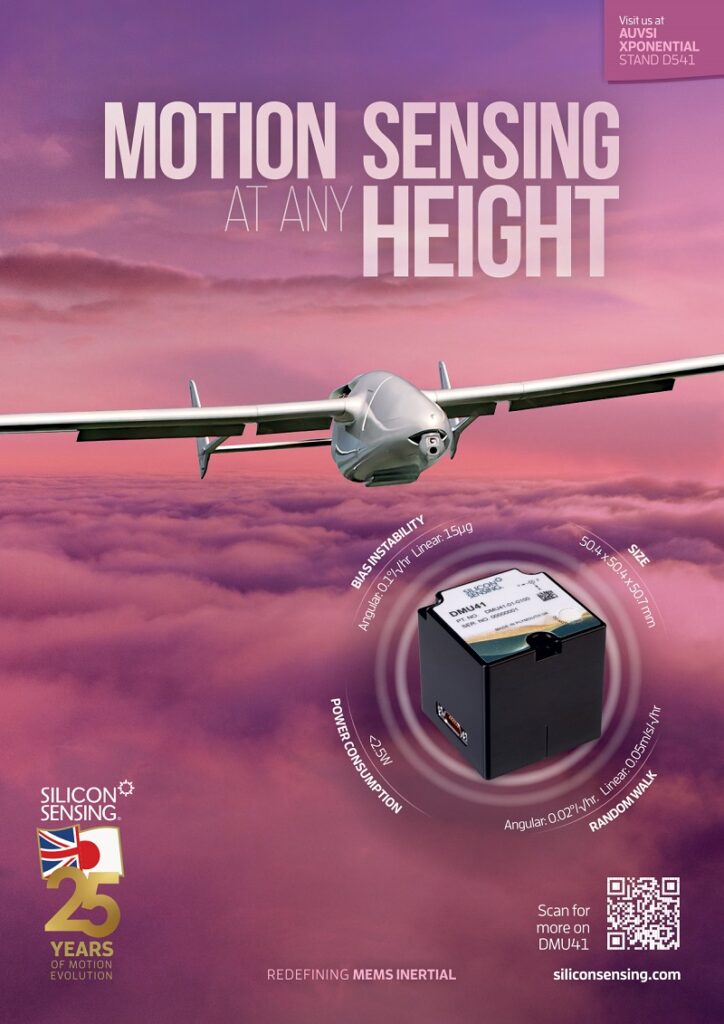
Acknowledgements
With thanks in the preparation of this article to Fanny Barde of Solithor, Stefan Ionel of Amprius, Sören Johannsen of SubCtech, and Ilias Belharouak and Marm Dixit at Oak Ridge National Laboratory.
Some examples of battery technology suppliers
BELGIUM
Solithor | +32 11 490 777 | www.solithor.com |
Solvay | +32 2 264 21 11 | www.solvay.com |
CANADA
Targray | +1 514 695 8095 | www.targray.com |
CHINA
BYD | +86 755 8988 8888 | www.byd.com.cn |
FRANCE
Saft | +33 1 58 63 16 00 | www.saftbatteries.com |
GERMANY
SubCtech | +49 431 22 039 880 | www.subCtech.com |
ISRAEL
Amicell | +972 88 56 16 12 | www.amicell.co.il |
Epsilor | +972 8 655 6280 | www.epsilor.com |
StoreDot | +972 3 509 7710 | www.store-dot.com |
JAPAN
Connexx Systems | +81 774 66 6886 | www.Connexxsys.com |
Fuji Pigment | +81 72 759 8501 | www.fuji-pigment.co.jp |
SPAIN
Grabat Energy | +34 968 07 20 49 | www.grabat.es |
SWITZERLAND
Vanguard Power | +41 55 415 1200 | www.vanguardpower.com |
UK
Faradion | +44 1865 309678 | www.faradion.co.uk |
Nexeon | +44 1235 436320 | www.nexeon.co.uk |
Steatite | +44 1527 512 400 | www.steatite.co.uk |
USA
Amprius | +1 866 685 7420 | www.amprius.com |
BASF Catalysts | +1 732 205 5000 | www.catalysts.basf.com |
EaglePicher | +1 417 623 8000 | www.eaglepicher.com |
Enevate | +1 949 243 0399 | www.enevate.com |
Maxamps | +1 888 654 4450 | www.maxamps.com |
NEI | +1 732 868 3141 | www.neicorporation.com |
Nuvera | +1 617 245 7500 | www.nuvera.com |
One D Material | +1 650 331 2192 | www.onedmaterial.com |
Prieto Battery | +1 970 492 4195 | www.prietobattery.com |
Seeo | +1 510 782 7336 | www.seeo.com |
Solid Power | +1 720 300 8167 | www.solidpowerbattery.com |
XG Sciences | +1 517 203 1110 | www.xgsciences.us |
UPCOMING EVENTS
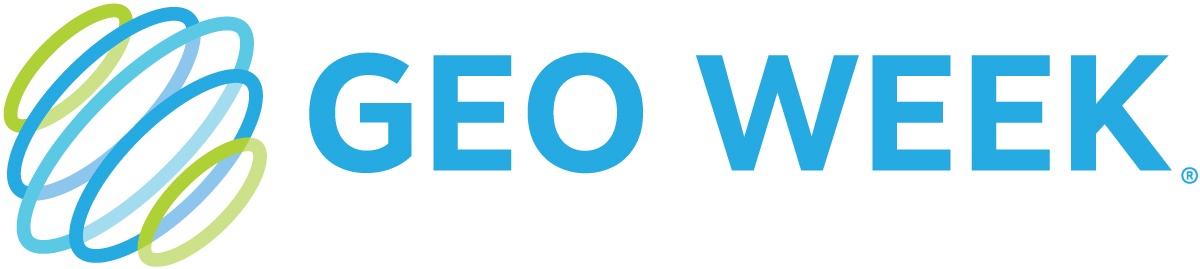
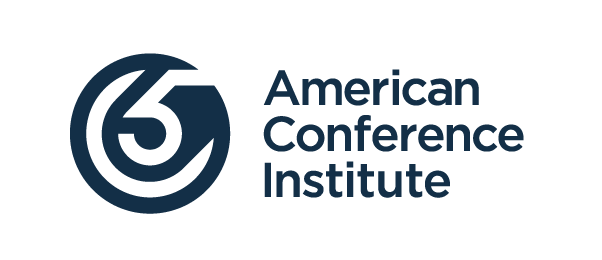
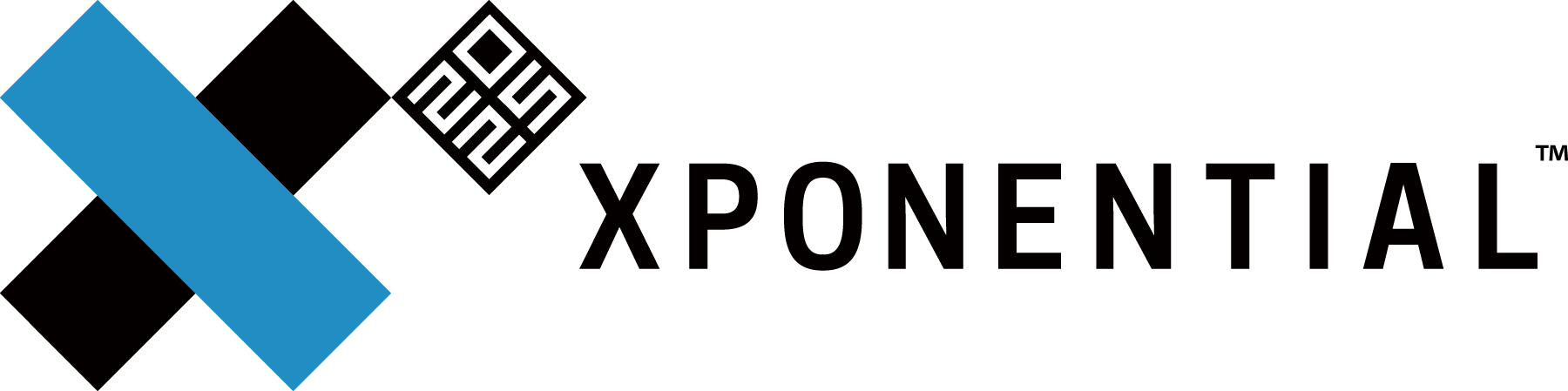
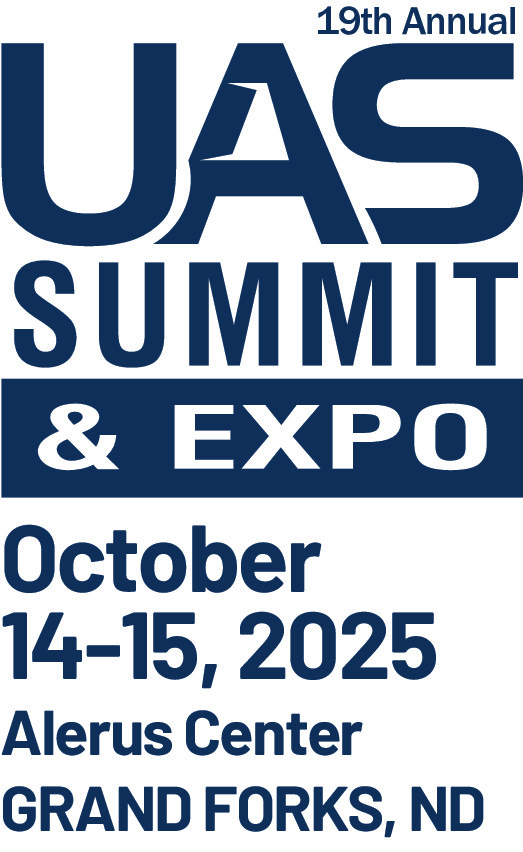
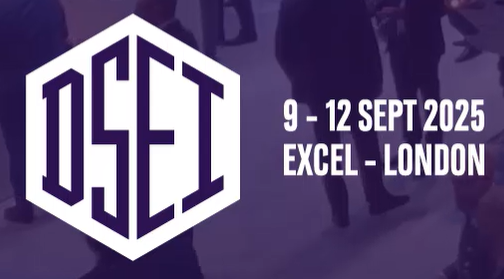
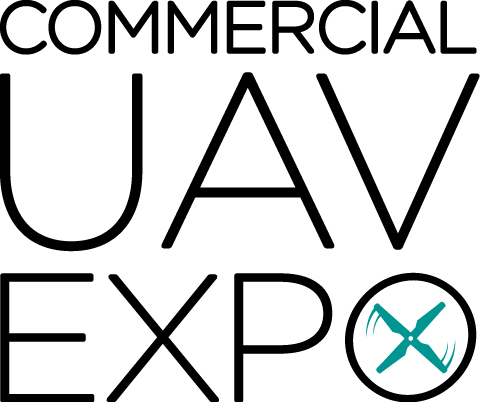
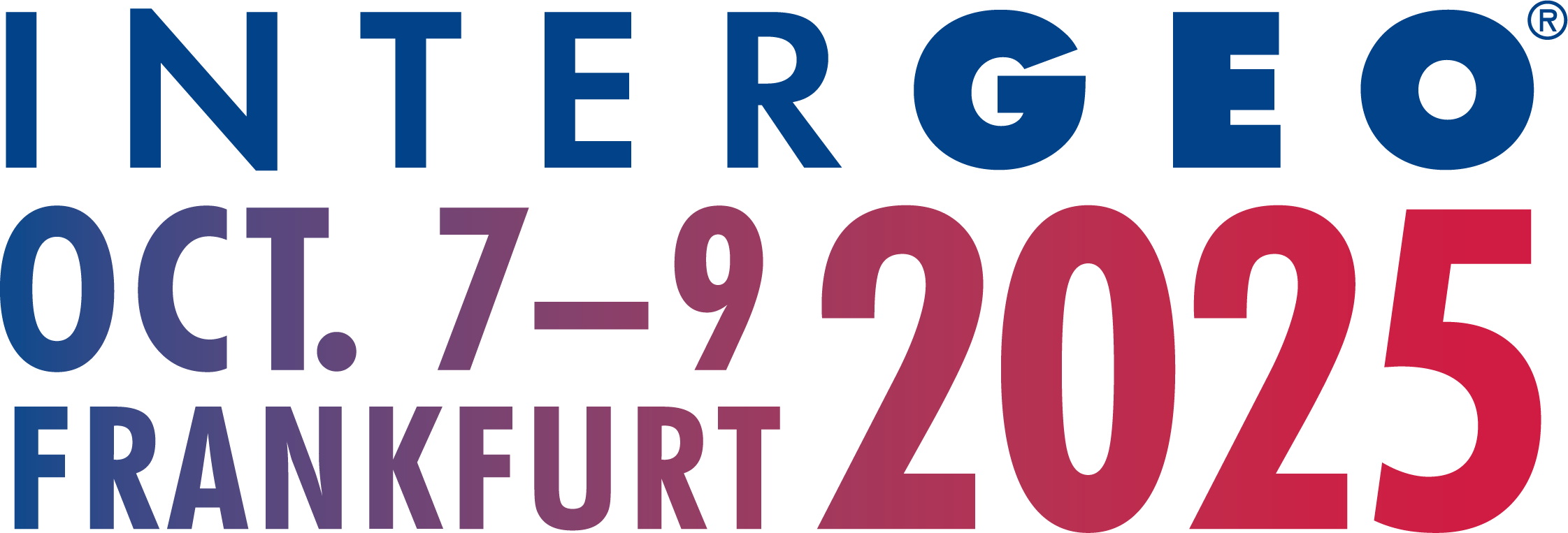
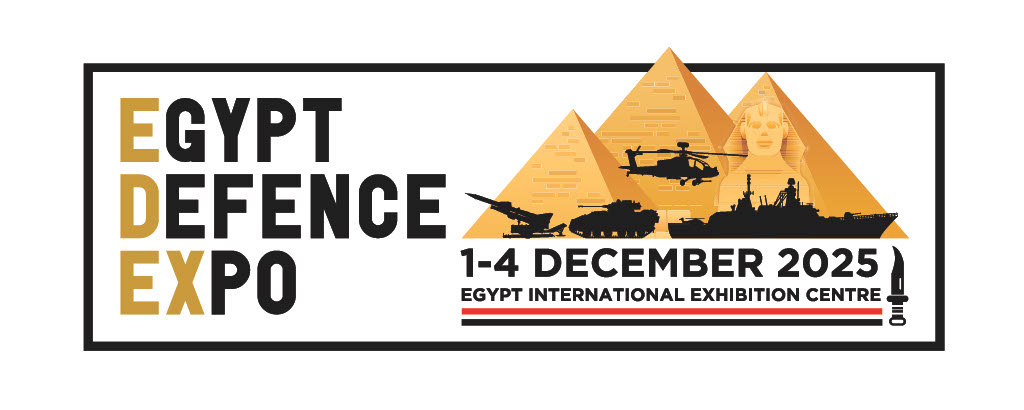
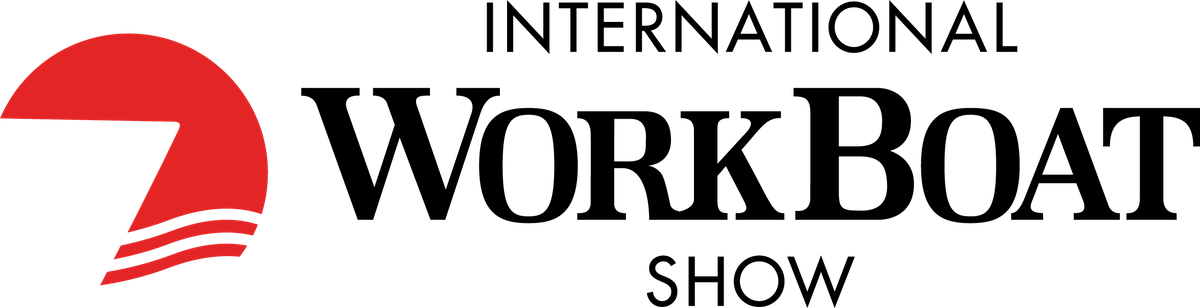
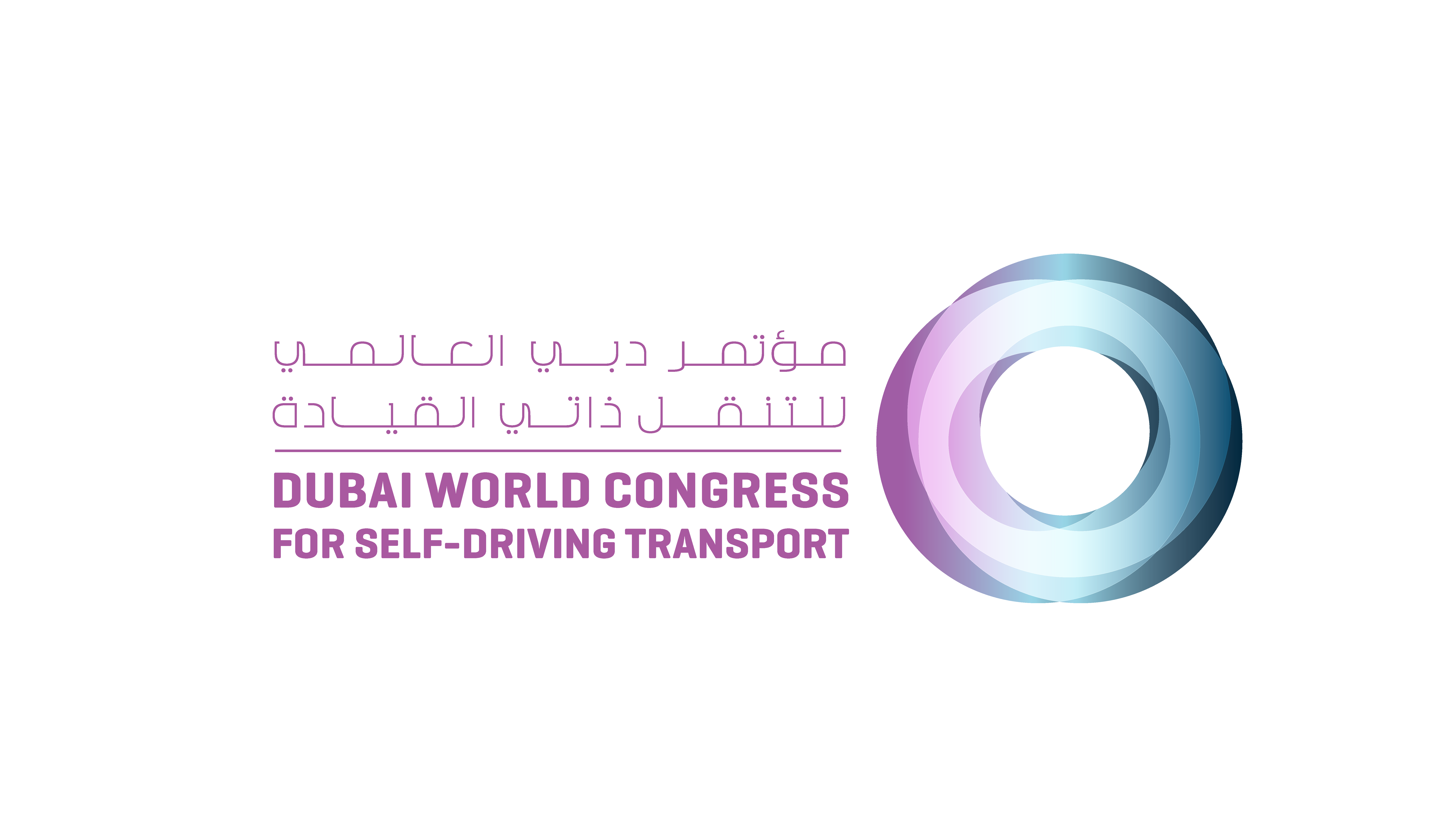
