Dr. David Barrett
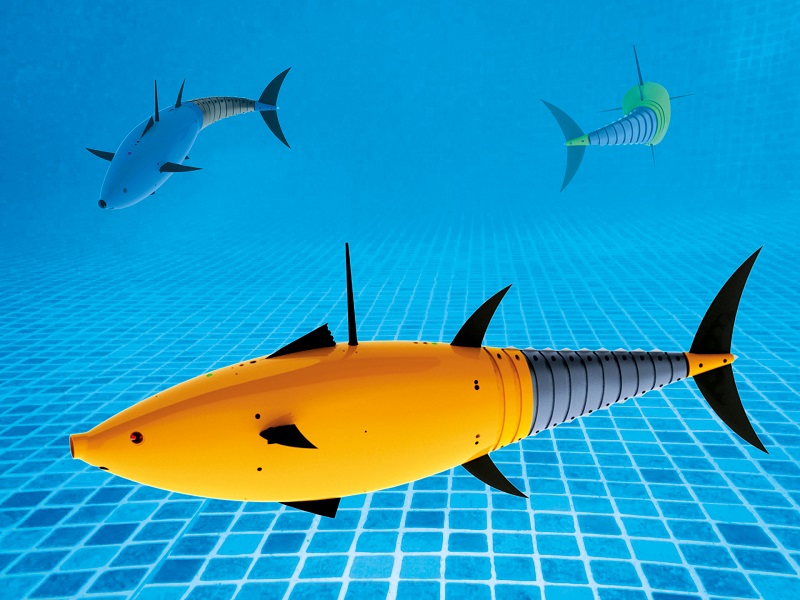
Peter Donaldson talks to this marine robotics expert about what we can learn from nature about efficient underwater propulsion
Swimming lessons
Propulsive efficiency under water is one of many areas in which nature has had the advantage of hundreds of millions of years of evolution to hone the design of its creatures. Large pelagic fish such as tuna and sharks, and cetaceans such as whales and dolphins, outperform all human made underwater vehicles that aren’t nuclear powered in terms of speed, range and endurance despite having far less power available to them.
Dr David Barrett of Olin College of Engineering, in Massachusetts, has dedicated much of his working life to figuring out how the animals do this and creating robotic vehicles that can replicate their feats. He is perhaps best known for his robotic tuna.
“I am a biomimetic roboticist, so I copy nature,” he says. One of his more ambitious aims is to create technology that will allow humanity to understand the ocean well enough to stave off climate breakdown.
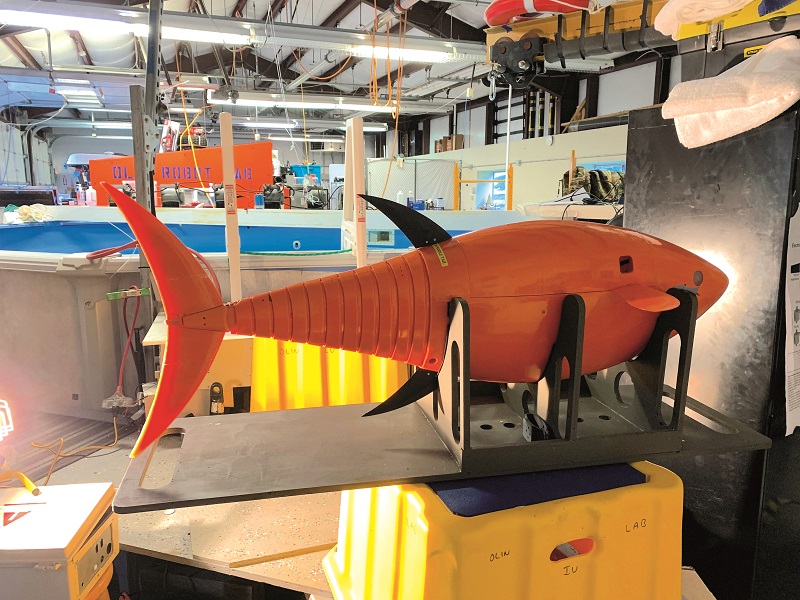
Seeking warp drive
It was as a graduate student at MIT’s Department of Ocean Engineering in the first half of the 1990s that his involvement with robots that move like fish began. Here he met Professor Michael S Triantafyllou, who was interested in the fluid mechanics of Gray’s paradox. “Gray’s paradox is basically that fish and dolphins shouldn’t be able to swim as fast as they do,” he explains.
Working in the 1930s, British zoologist Lord Gray calculated that a typical dolphin has the muscle to generate about half a horsepower. He found that according to the basic principles of fluid mechanics, that power should enable it to reach just 4 knots, but dolphins can swim at up to 30 knots. “The paradox is that dolphins and tuna have what looks like warp drive for underwater vehicles,” Dr Barrett says.
A traditional AUV is a cylinder with a propeller on the back, and is severely limited by drag, which increases with the square of the speed. So most AUVs have speed, range and endurance limitations that restrict them to the continental shelves around the world, if launched from the coast.
“Mike’s work at MIT was about how to break the range barrier, so we can explore the ocean, work on fisheries, solve global warming and do all the other things that undersea vehicles could be good at,” Dr Barrett says.
“There are three ways to solve this. One is to build much better batteries, another is to make everything nuclear powered – but no nation would risk thousands of nuclear-powered mini-subs drifting around the ocean and washing up on beaches – and the third is to find a way to dramatically increase propulsive efficiency. And so we got into this by trying to solve Gray’s paradox.
“In water, Gray’s paradox is like the sound barrier in air. Fish and cetaceans, particularly the large pelagic predators – sharks, tuna, dolphins and killer whales – are doing something that a conventional rigid-hulled vehicle is not doing that lets them have these enormous propulsive efficiencies. We are nowhere near fully solving the problem, but we have been able to drop the drag on a wiggly body down almost to zero,” he says.
Wiggly drag reduction
Wiggling, it turns out, is central to the natural secret that Prof Triantafyllou’s team figured out, because it plays a role in vortex-shedding in a manner that turns drag into thrust. Dr Barrett explains that the vortices, or ‘vorticity’, forms in the boundary layer between a moving body and the mass of stationary water surrounding it.
“At the boundary is a viscid layer that is rolling out vorticity, and the vorticity will pop off the back end of the moving body,” Dr Barrett says. The direction in which the vorticity spins is crucial.
In a rigid-hull vehicle moving from left to right in our imagined frame of reference, the vorticity on its port side will spin anti-clockwise while that from its starboard side will spin clockwise. They continue to spin when they pop off the back of the vehicle, producing a net flow of water in the direction in which the vehicle is travelling, so that the vessel is effectively pulling the water along behind it.
“Flow in this direction is drag, which increases with the square of your speed,” Dr Barrett says. “If you have a wiggly tail you can take the drag vortices from one side of the body and drop them on the other side. You are turning your drag into thrust.”
When a tuna or a shark beats its tail from side to side, each vortex it sheds is flicked to the opposite side of the fish’s line of symmetry, so those that form on the port side are shed to starboard and vice versa, although their direction of spin does not change. This causes them to produce a net water flow in the opposite direction to the fish’s movement, he says, so the fish is effectively pushing the water away behind it. In accordance with Newtonian mechanics, that action has an equal and opposite reaction, which is the thrust.
In this context, Dr Barrett characterises thrust as negative drag. “I have built bodies that have massive amounts of negative drag,” he says. “Gray’s numbers are something like a 10 or 20-to-1 multiplier, and I can get 2 or 3-to-1 here, but even so that means a 100 mile mission range could become 200 or 300 miles with the same battery.”
The difference between Gray’s numbers, representing nature’s achievements in drag reduction, and Dr Barrett’s current best means there is a lot more to come.
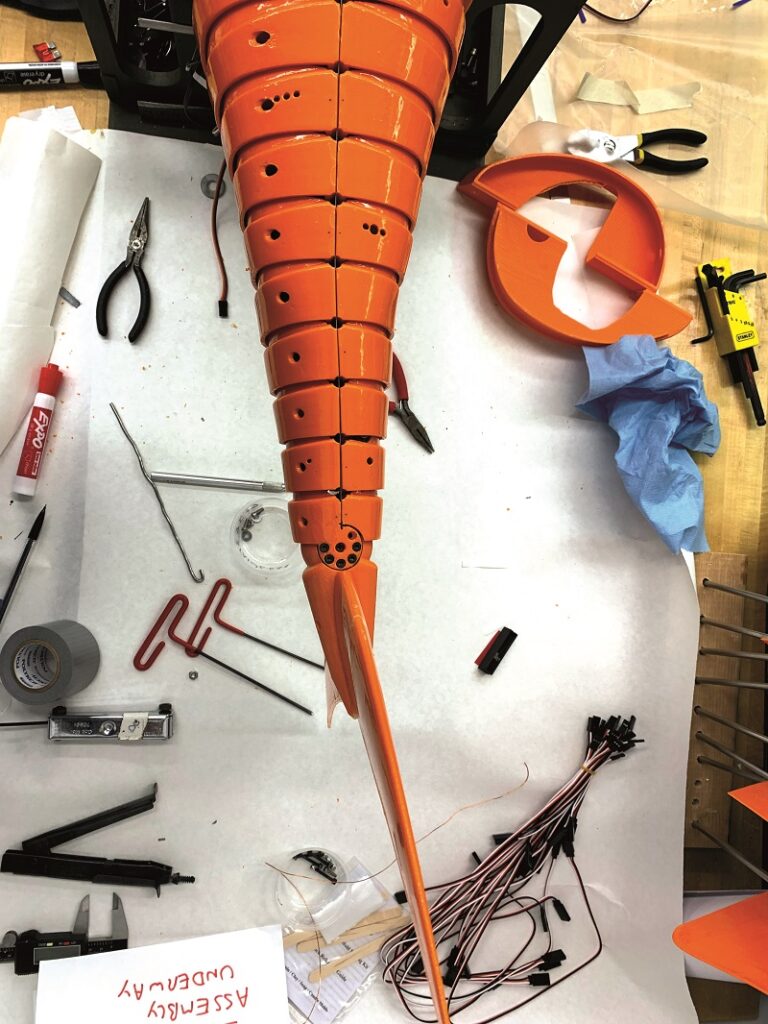
Sensing and harmonics
One important source of future improvements is sensing. In common with most fish, sharks and tuna have a pair of lateral lines that run along the sides of the body that form an array of pressure sensors. “They run from the nose to the tail, and they can sense the pressure changes created by the vortices on both sides of the body so that they know when to release them,” he says.
The sensors provide feedback to what is effectively a closed-loop tuned harmonic oscillator in fish, which he contrasts with the traditional brute-force approach to propulsion, explaining that small forces applied in phase are much more energy-efficient. The body of a tuna, for example, has a mechanism that takes advantage of such harmonics.
“The back end is a big cantilevered spring that oscillates at the same natural frequency that we need to shed the vortices to get the warp drive,” he says. “If you take a dead shark and tow it behind a boat, the back end will wiggle. Its mechanical design is set up to oscillate at the frequency it needs to propel itself, so it takes it very little energy.”
Dr Barrett and his team have built 3D computer models of tuna musculature, starting by cutting several of the fish into half-inch thick sections and photographing them. “The muscles are attached to cartilage and bone in the front, and to a springy elastic tendon at the back. The tendon is very complex and has sub-tendons and muscles in it, and it is basically a variable stiffness spring.”
The fish’s control system is decentralised, using a set of ganglia along the spine to run the oscillating motion, he explains. “It is a central pattern generator and, basically, the brain says ‘Start wiggling’ and the wiggle is generated by computation down among the ganglia and not by the main brain.”
Having analysed tuna locomotion, Dr Barrett’s team also had to reproduce it. “With modern materials like titanium and glass-reinforced plastic and carbon fibre, we can replicate a tuna skeleton pretty accurately, and using urethanes and silicones we can recreate the skin and tissue,” he says. “We are using linear Lorentz force actuators to replicate the muscles.
Speakers for muscles
“With a linear drive Lorenz force actuator you can oscillate it back and forth at very high speeds and extremely high efficiency,” he adds. “The system we are using is very similar to the voice coils in microphones and speakers.
“The actuators are paired, twitch back and forth to create the oscillation, and are connected by springs to the next pair. We do that for the 12 or 14 ribs in the back end of the fish, and if we oscillate them all at their natural frequencies, we get very efficient drive.”
To save more energy, regenerative drive electronics for the ‘speakers’ can reverse the motion with efficiencies of 98-99%, comparable to regenerative braking in an electric car.
“Although we are nowhere near as sophisticated as Mother Nature, we are potentially far better than a traditional AUV in terms of efficiency, duration and speed,” he says. “I hope someday to be 20 times better, but it would be arrogant of me to say that we can achieve that in a short time frame.”
Environment and aquaculture
While gliders achieve great range and endurance, they are limited in speed and manoeuvrability, and fish robots are potentially far more flexible, he argues. “You could drop 100 of them along a transit route across the Atlantic and tell them all to swim due south at the same time,” he says. “That way we could do a transect of the entire ocean at once, and to capture that amount of data would revolutionise our understanding of ocean mechanics.”
The same acoustic sensors that allow the robot fish to ‘see’ vortices could also serve as passive sonars, complemented by other acoustic and optical sensors on the head to home in on and identify targets, or to assess the effects of mitigations for environmental issues such as coral reef bleaching.
By adding a chemical sensing ‘tongue’ a robot tuna could follow chemical gradients to trace pollutants to their sources, he says. They could also download data from arrays of sensors deployed on the seabed using a megabit-class optical datalink and raise a satcom antenna to beam it back to shore.
He also sees a future for fish robots in aquaculture, monitoring the condition of salmon farmed in pens or preparing seagrass beds and, further in the future, potentially herding tuna as they grow in the open ocean and bringing the mature fish in for harvesting. Aquaculture needs a low-cost general-purpose vehicle, an equivalent of a $20,000 tractor, he says.
A better world
Barrett regards engineering as a powerful disruptive force with tremendous potential for good and evil. “In robotics we struggle with this on a daily basis,” he says. “So my overall philosophy is we should create things that make the world a better place, and I should be training my students to do that,” he says.
“Engineering isn’t about making money or about making yourself famous; it’s about legacy and about passing on a better world.”
As to his own future, he’s happy where he is. “My job is my hobby and my hobby is my job,” he says. In a few years I’ll probably become a professor emeritus and just keep doing it as long as I can. If I train a lot of young engineers to do it well, maybe they’ll keep me around!”
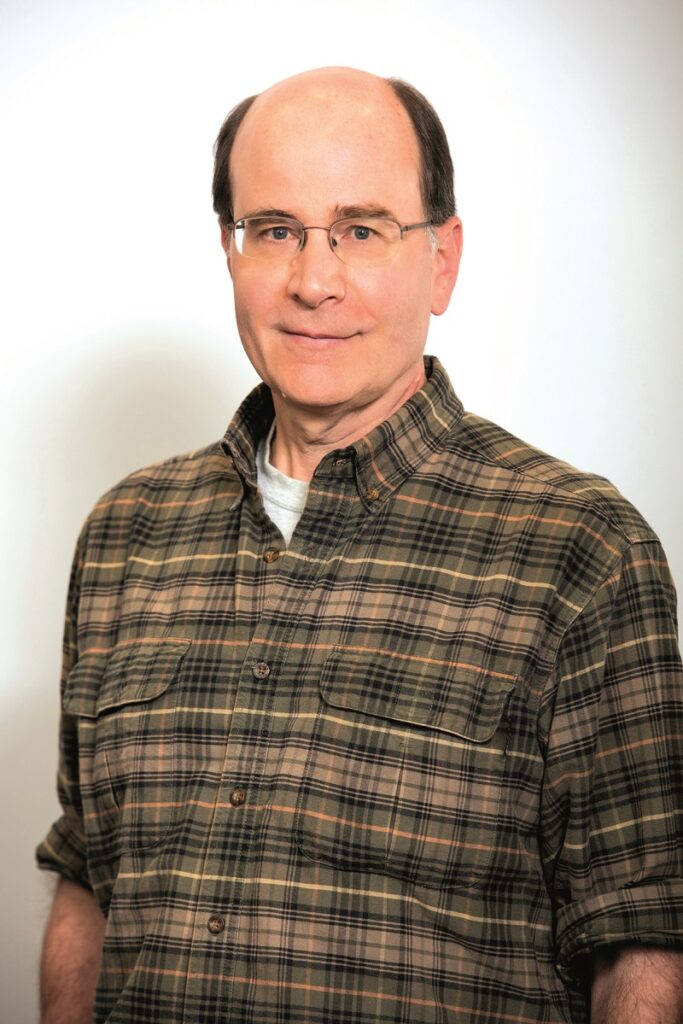
Dr David Barrett
Born out on the end of Cape Cod on the east coast of the US in 1956, Dr Barrett grew up close to the water and developed passions for the ocean and building machines, inspired in part by the televised underwater adventures of pioneering French diver, naturalist, naval engineer and film maker Jacques Cousteau.
He excelled in arts and sciences at school, and loved making things in his railway engineer grandfather’s basement workshop from an early age, along with his brothers. “I built my first robot arm in the 1970s,” he recalls. “I welded a bunch of soup cans together and put electric motors in the joints controlled by a set of switches and potentiometers, and it worked pretty well.”
As a student he qualified in mechanical engineering and ocean engineering at universities including the Massachusetts Institute of Technology (MIT). That led to a career that has included senior posts with companies including iRobot and Walt Disney Imagineering, as well as posts with research institutions including the Charles Stark Draper Laboratory, MIT and Olin College, where he is now Professor of Mechanical Engineering and Robotics, and Principal Investigator for the Olin Intelligent Vehicle Laboratory.
UPCOMING EVENTS
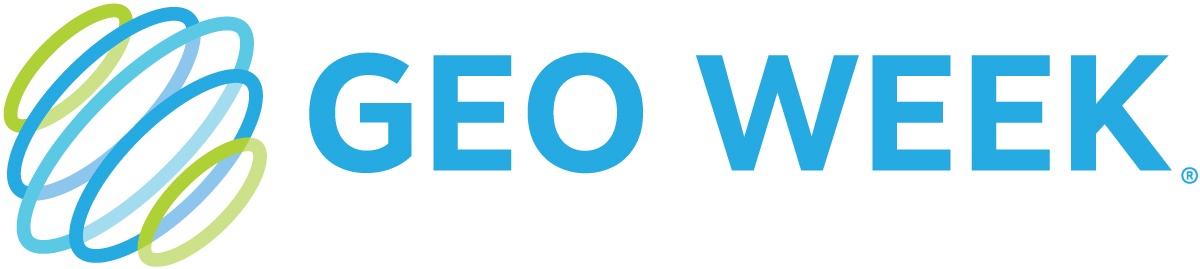
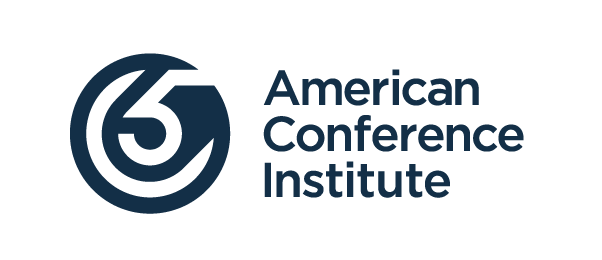
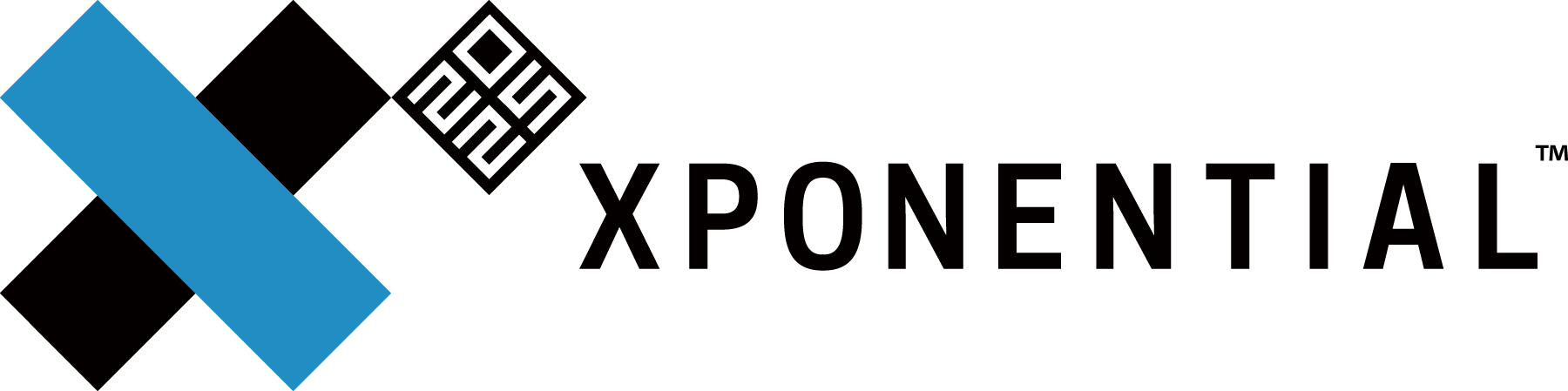
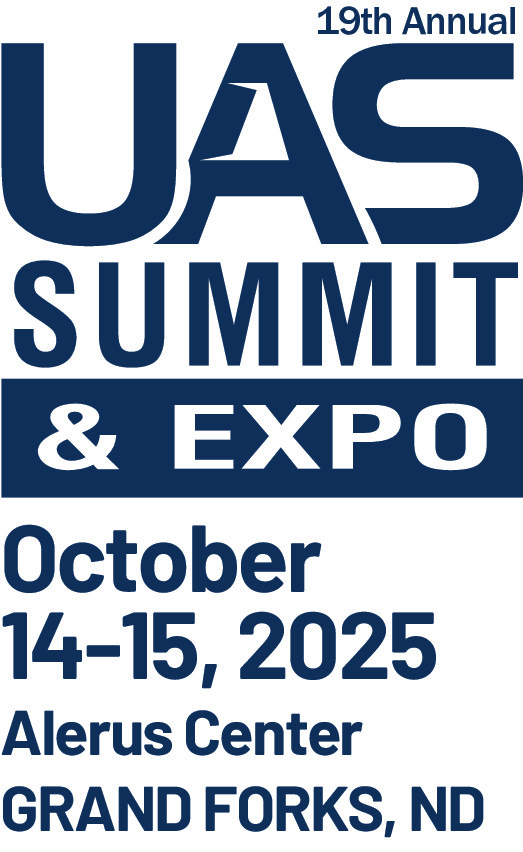
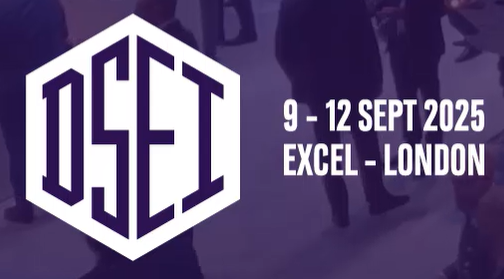
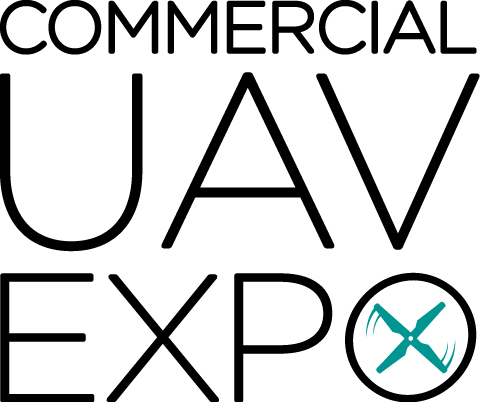
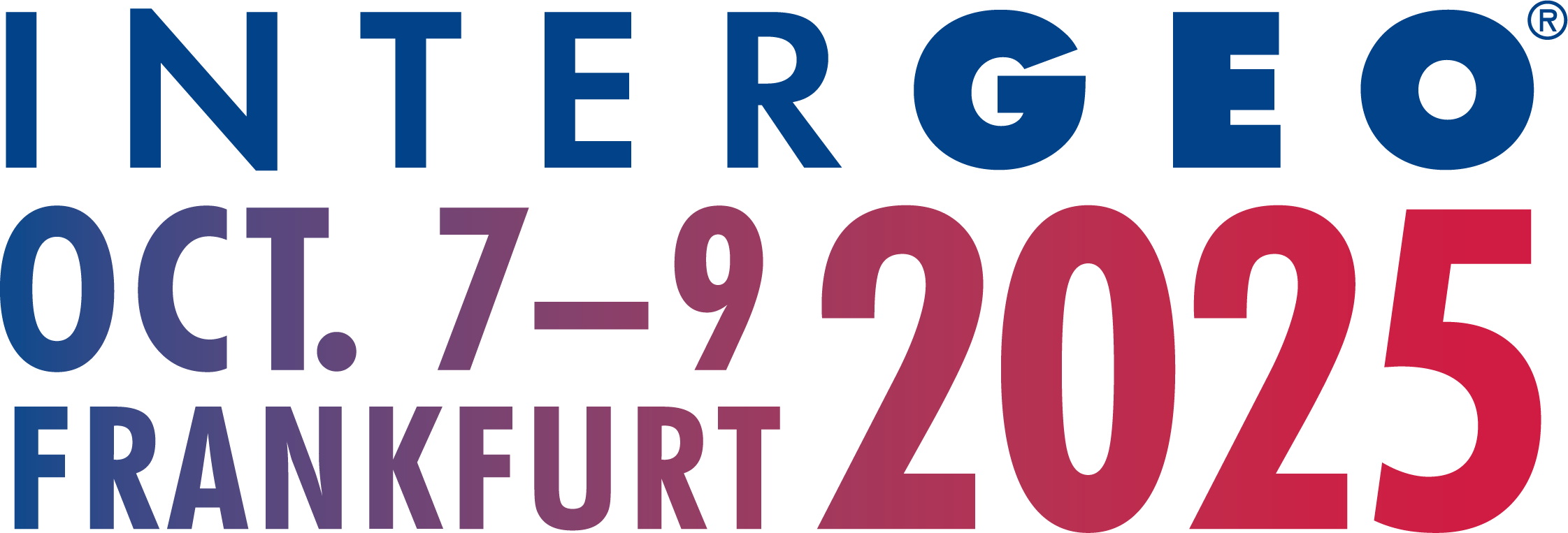
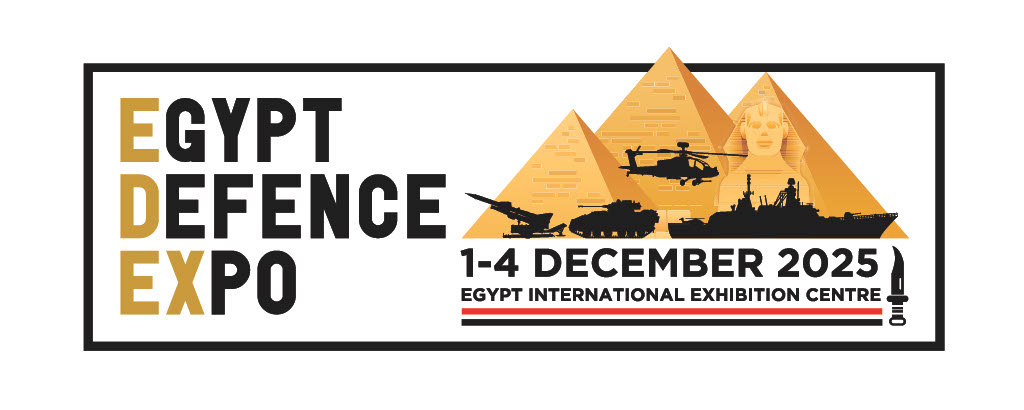
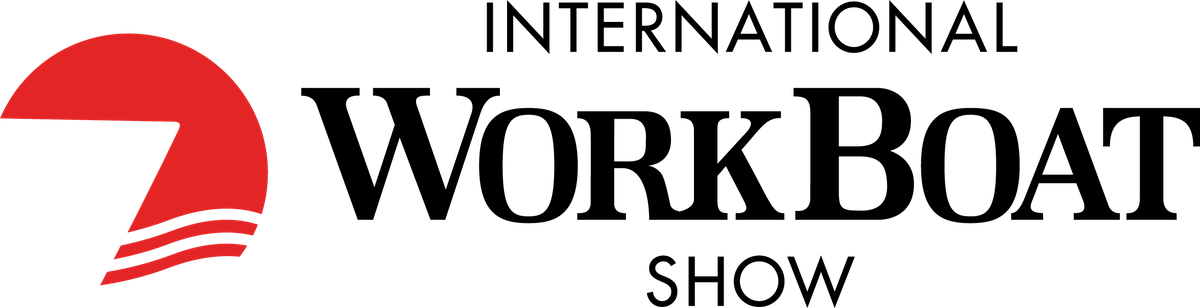
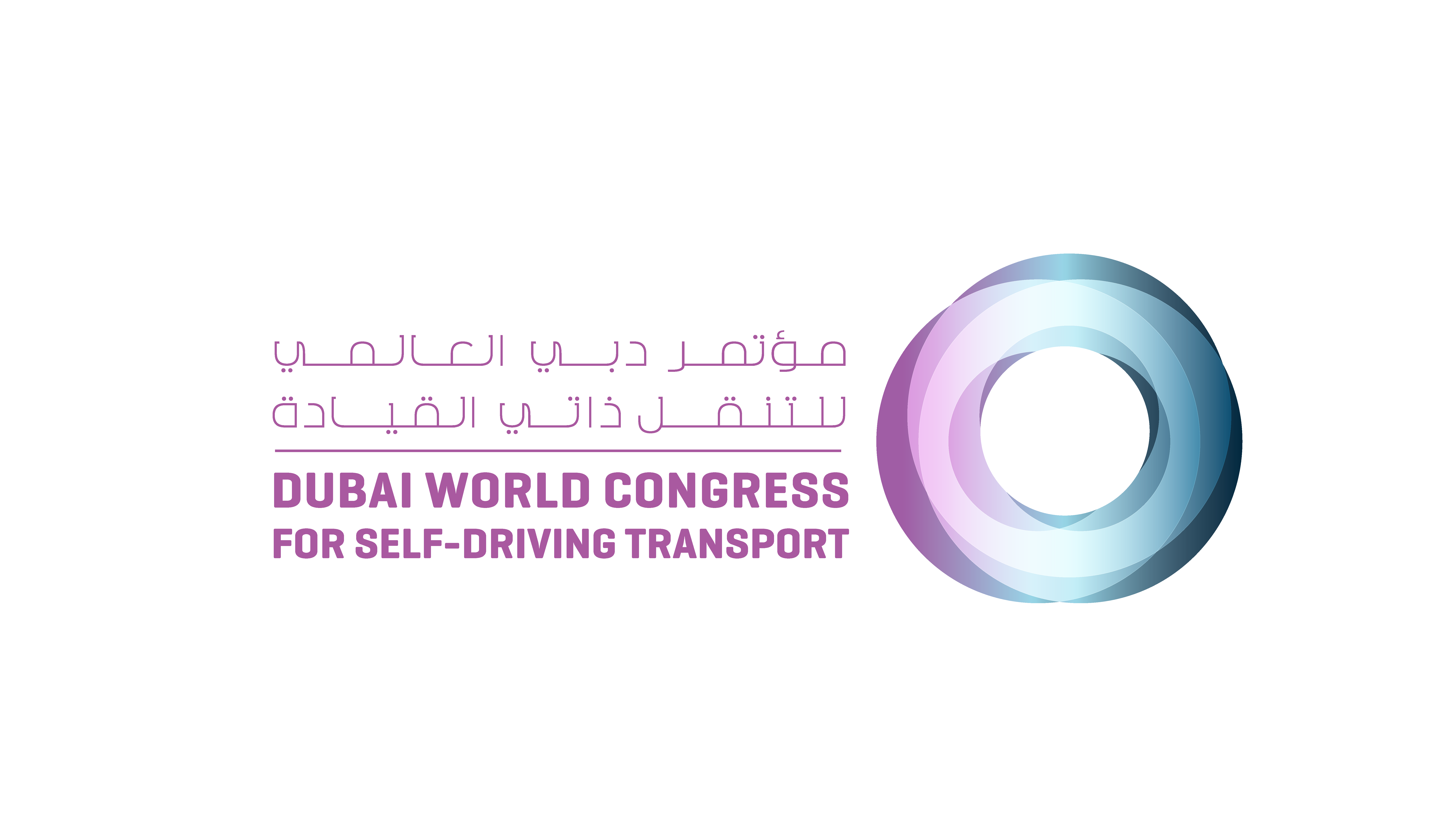
