Additive manufacturing
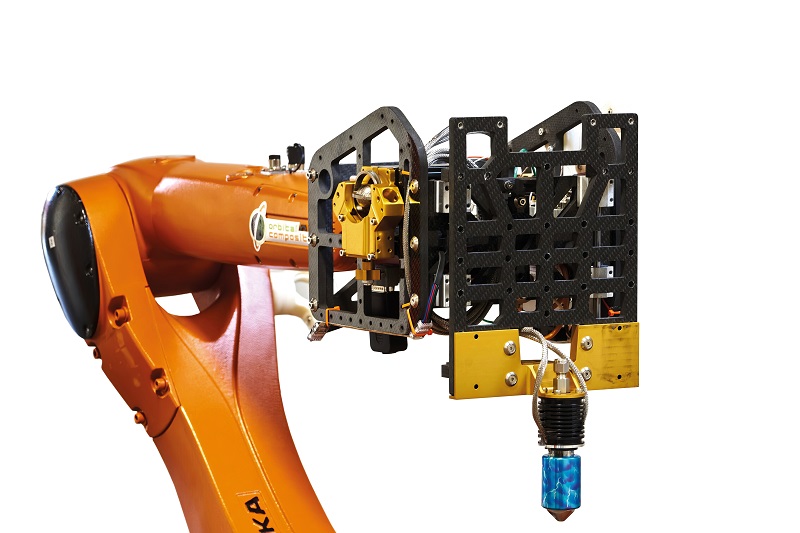
Nick Flaherty takes stock of the latest research into new methods of 3D printing and the applications they look set to open up
Print preview
Additive manufacturing (AM) and 3D printing are pushing the limits of materials, processes and designs, for prototyping as well as manufacturing uncrewed systems.
The technology is regularly used for prototyping, allowing faster iterations of designs without having to change tooling. But increasingly it is also a key part of the design process, for example by adding self-healing elements for repairs, de-icing surfaces and allowing large curved surfaces to be printed.
Machine learning (ML) is also increasingly being applied to improve the quality of the AM process to identify and minimise any defects and ensure parts are suitable for long-term use. All of this is driving more use of the technology in a range of uncrewed system designs. Multi-axis carbon fibre production
One 3D-printing system has a customisable 12-axis frame to allow as much flexibility as possible in the printing process. It allows an uncrewed vehicle to be designed around the parts it creates using a range of modular end-effectors with numerous customisation options.
The system is flexible enough to print curved surfaces, and can be installed in a shipping container with the feedstock to provide local manufacturing in a controlled environment.
One type of end-effector uses a lightweight carbon fibre chassis that holds a filament driver and motors, with multiple nozzle sizes available from 0.5 to 3 mm and handling temperatures of up to 600 oC. These can process a wide range of thermoplastics, including high-performance materials such as PEEK, in the industry-standard 1.75 and 2.85 mm filament sizes. For continuous fibre printing, the system supports fibre lengths from 3k to 100k.
The end-effector can also process carbon fibre in a more cost-effective way. Rather than using a resin pre-loaded with long or short carbon fibres, one particular end-effector can apply the carbon fibre precisely where specified by the design software. By reinforcing only where necessary, this creates lightweight, strong thermoplastic parts at a much lower price compared to current carbon fibre manufacturing technologies.
Another end-effector can use a newer technique called AM Compression Moulding (AMCM). This uses a short fibre-filled polymer and a continuous fibre polymer to print directly onto a mould with precise orientation to make parts such as propeller blades or battery boxes.
Compression moulding then turns the print into an accurate finished piece. This significantly reduces the time and cost by producing 100 parts in 5 hours compared to layer assembly, with each piece taking less than 3 minutes to print.
Combining the fibre control of an additive process with the low porosity of compression moulding enables high-volume production of lightweight composite materials for more energy-efficient designs.
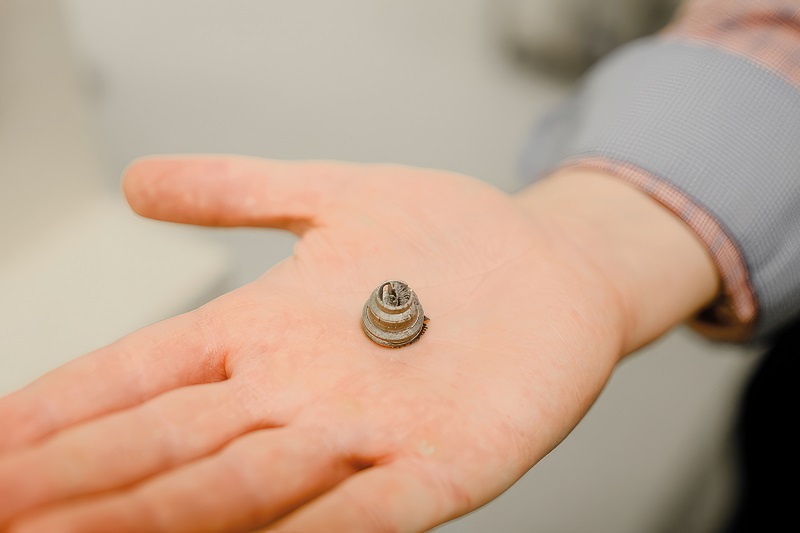
Magnets
One area of development is to reduce the size and weight of magnets that can be produced using AM.
Finding the optimal conditions for 3D-printing permanent magnets from hard magnetic compounds based on rare earth metals will allow small-scale production of magnets of any shape, and create complex configurations of them. Using 3D printing to produce them reduces waste and has a shorter production cycle; such magnets are suitable for miniature electric motors and generators.
Creating complex and small magnets for sensors for example is not an easy scientific and technical task, but they are in demand for various specialised applications. One of the most promising ways to create complex-shaped parts from magnetically hard materials is to use selective laser sintering.
This is an AM method where the magnetic material in the form of powder is sintered layer by layer into a 3D product of a given shape based on a previously created 3D model.
The technology makes it possible to change the internal properties of the magnet at almost any stage of production, such as changing the chemical composition of the compound, the degree of spatial orientation of the crystallites and crystallographic texture, and to influence the resistance to demagnetisation (the coercivity).
Small magnets are currently created by cutting a large magnet into pieces, but because of the mechanical processing about half of the material used is waste. Cutting also introduces defects in the near-surface layer, which causes the properties of the magnet to deteriorate.
Additive technologies avoid this and allow more complex magnets to be made, such as with one north pole and two spatially separated south poles, or a magnet with five south poles and five north ones.
The latest permanent magnets are about 1 mm thick and are made from a powder containing samarium, zirconium, iron and titanium. The compound has suitable characteristics for permanent magnets, but traditional manufacturing methods eliminate most of its properties.
When sintering a sample, adding a fusible powder from an alloy of samarium, copper and cobalt allows the magnetic characteristics of the main magnetic powder to be retained. The alloy melts at lower temperatures than those at which the properties of the main alloy change, which is why the final material retains its coercive force and density.
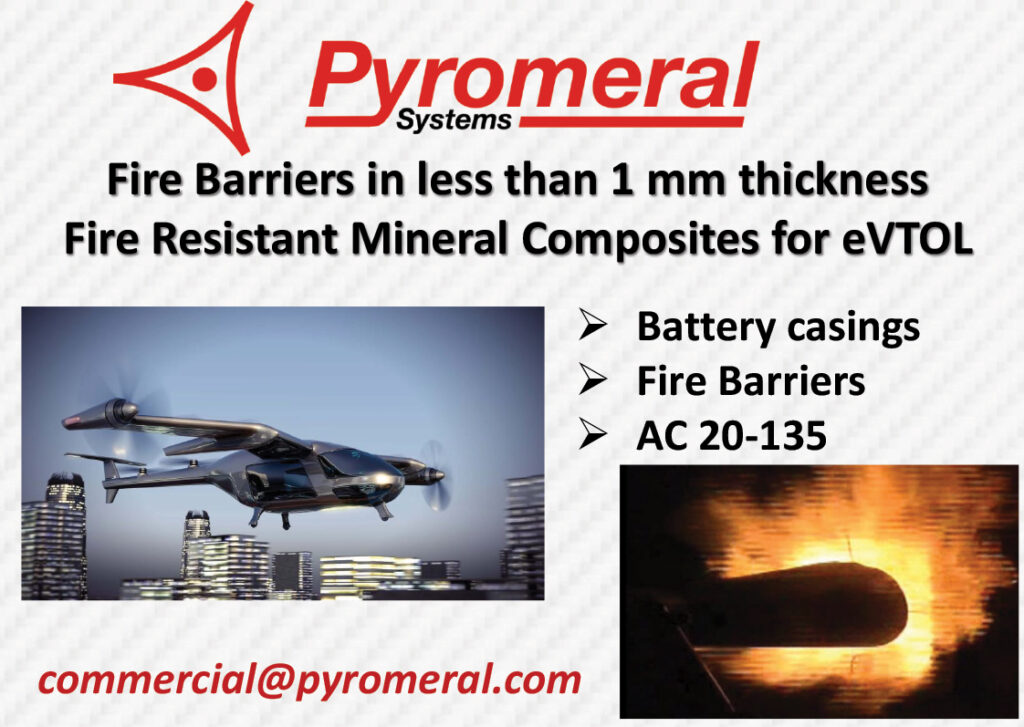
Peristaltic pump
Researchers have also 3D-printed a miniature vacuum pump that uses a peristaltic mechanism.
The pump can create and maintain a vacuum as low as 9 Torr (about 1200 Pa), an order of magnitude lower than other types of commonly used pump, with a 10 standard cc/minute flow rate.
The design, which can be printed in one pass on a multi-material 3D printer, prevents fluid or gas from leaking while minimising heat from friction during the pumping process. This increases the device’s lifetime.
The pump uses a novel actuator design with a notched cross-section that requires less than half the force of other types of pumps to fully seal, making it possible to create and maintain low vacuum at low actuation speed.
The device is made using multi-material extrusion. The rigid parts of the pump are made from polylactic acid, while its compliant parts are made from FiberFlex 40D – a relatively new flexible material that is easier to print than mainstream Ninjaflex, even though the two materials have similar hardness. FiberFlex 40D also has good chemical compatibility with substances such as oil, butane and ethyl alcohol.
Characterisation of the 3D-printed FiberFlex 40D demonstrates that over 105 cycles for the pump, and experimental characterisation of the prototype pump, there is an order of magnitude lower base pressure than a state-of-the-art, single-stage, miniaturised diaphragm vacuum pump. The technology can also be used for pumps in space systems.
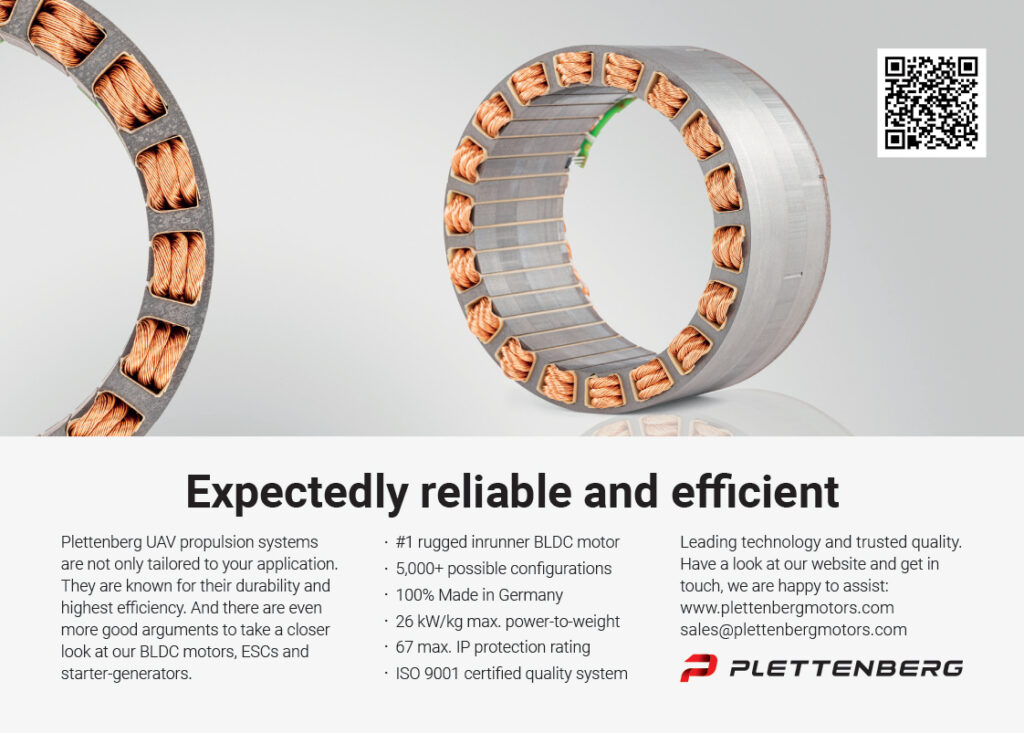
Printing completely airtight layers in the flexible tube is necessary to get the working vacuum pumps. Trial and error found that an extrusion multiplier of 1.2 and an extrusion width of 0.4 mm were suitable for printing the airtight tubes with a radius of only several millimetres.
The cross-section of the tube has been designed to overcome the limitation faced by traditional peristaltic pumps when used to create and maintain vacuum. The starting tube design had an outer diameter of 9 mm with 1 mm wall thickness. The design has two symmetrical notches to prevent dead volumes from forming when the tube is compressed and to reduce stress concentration in the material.
The tubes are printed vertically, for two key reasons. First, printing them without any overhangs makes it possible to achieve much cleaner prints without any supports inside the tube. Second, printing individual layers perpendicular to the tube’s length axis results in a more durable structure during compression, because the weakest bond in structures printed using material extrusion is between separate layers.
FiberFlex 40D is also used to print the support structure for the vertical tubes, close enough to the tube to prevent it from bending but also far enough to prevent the support from bonding to the tube. After the print, the flexible support structure is simply peeled off by hand.
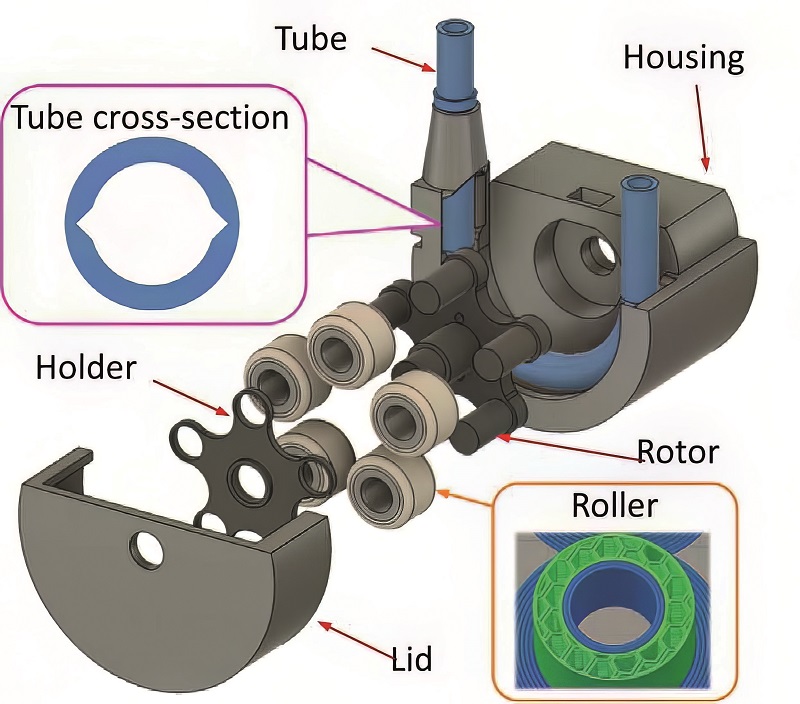
Materials
Other materials are being tested for uncrewed systems that operate at high speeds. Current 3D metal printing has been described as using papyrus in a modern printer – it works, but not as well as it could. Researchers are therefore developing alloys that are optimised to undergo both 3D printing and are suitable for use in hypersonic flight.
Not every material, or every shape, can withstand travelling at five times the speed of sound and faster. AM offers far more design flexibility than traditional manufacturing here though, as it allows designers to create precise geometries that aren’t otherwise possible, particularly for features such as cooling pipes incorporated directly into the structure of a vehicle.
This requires new metal alloys. Inconel 718 for example, which was developed in the 1950s specifically for forging, has a mixture of elements such as nickel, chrome and iron to give it maximum strength. But it also has some elements that cause the material, when processed using AM, to become brittle.
The new materials will have to operate with temperatures of up to 2760 oC, so heat resistance is one of the most critical features of the new alloys. The materials will also need to be resistant to oxidation. Needless to say, testing these materials is a major challenge.
Ceramics are more heat-resistant than metal, so hypersonic vehicles are often coated with specialised ceramics that can withstand ultra-high temperatures. But the vehicles are made largely of metal, which is less brittle and better able to bear the mechanical loads at hypersonic speeds.
That means there has to be metal underneath the ceramic. Improving the temperature capabilities of the metallic structures offers significant design and performance benefits with the ceramics.
This high-temperature expertise and cooling design can also be applied to the engines to boost their performance.
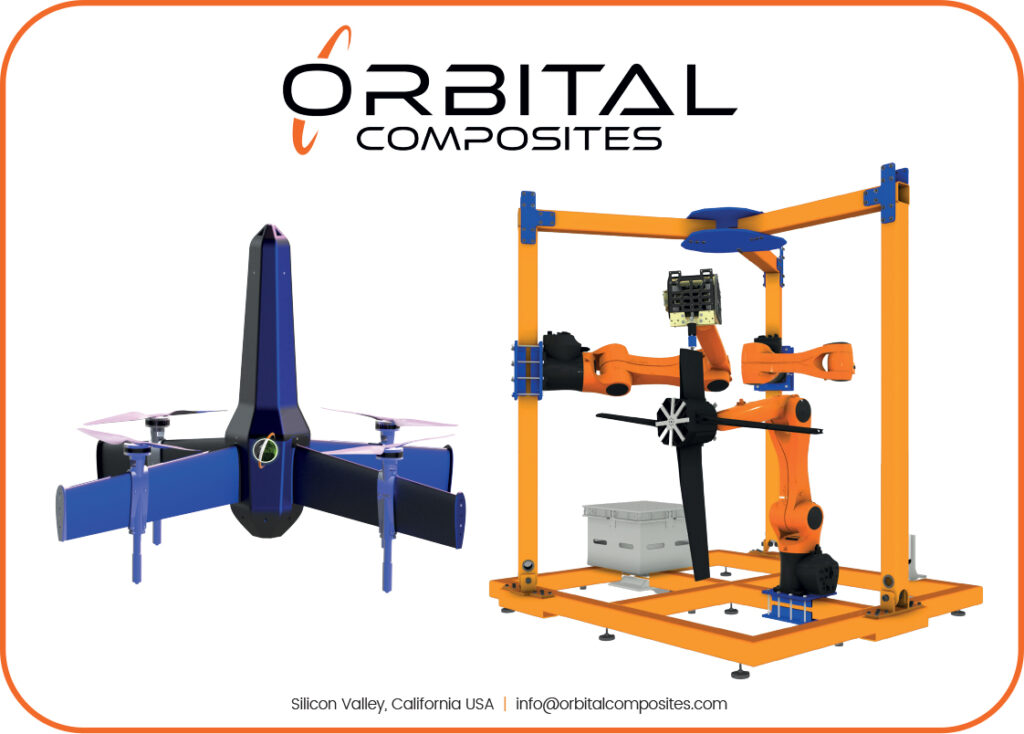
Welding pen
Joining these 3D-printed metal components together is also a challenge. One new technique is a metal 3D-printing pen that can continuously print metal in a 3D space.
It can freely and continuously print metal with freedom in the direction of the welding torch’s movement in the 3D space. Compared to conventional metal 3D printing using lasers, the equipment construction cost is low, and AM can be performed quickly using commercially available welding materials, making it more economical.
Metal AM using welding techniques has limitations in realising complex structures, because it is a limited process of building one layer at a time. That in turn is because subsequent layers are laminated after complete solidification, preventing the molten metal from flowing down. This slows down the process, as a cooling time is required and the conditions that can be laminated are limited to specific examples.
To solve this problem, computer analysis precisely controls the surface tension of the molten metal and the solidified volume according to convection/conduction. This can be used in all conditions, including horizontal, vertical, inclined and overhead positions.
By continuously laminating the metal in the liquid phase before it fully solidifies, the manufacturing time is shortened. There are no boundaries between layers, and it forms a dense microstructure with excellent mechanical properties.
In the case of ductility, the technology gives a 24.5% improvement compared to the existing Wire Arc AM process, based on Inconel 625.
Plastic-metal interfaces
Linking plastic and metal components is also a challenge. However, a new multi-material digital light processing 3D printing (MM-DLP3DP) process can fabricate metal-plastic composite structures with arbitrarily complex shapes.
This MM-DLP3D process starts with the preparation of the active precursor chemicals that are converted into the desired chemical after 3D printing. Palladium ions are added to light-cured resins to prepare the active precursors to enable electroless plating (ELP), a process where the catalytic reduction of metal ions in an aqueous solution forms a metal coating.
Next, the MM-DL3DP system is used to fabricate microstructures containing nested regions of the resin or the active precursor. These materials are then directly plated, and 3D metal patterns are added to them using ELP.
Various parts with complex topologies have been built to demonstrate the manufacturing capabilities of the technique. They had complex structures with multi-material nesting layers, including microporous and tiny hollow structures, the smallest of which was 40 µm in size.
The metal patterns on these parts were very specific, and could be precisely controlled to produce 3D circuit boards and sensors with complex metal topologies. This approach also needed a new type of 3D printer. It uses a 5.5 in, 405 nm 70 W ultraviolet parallel light source with a light intensity of 85 MW/cm2 and a light uniformity of 98%. During the printing process, different slice thicknesses and single-layer exposure times are used.
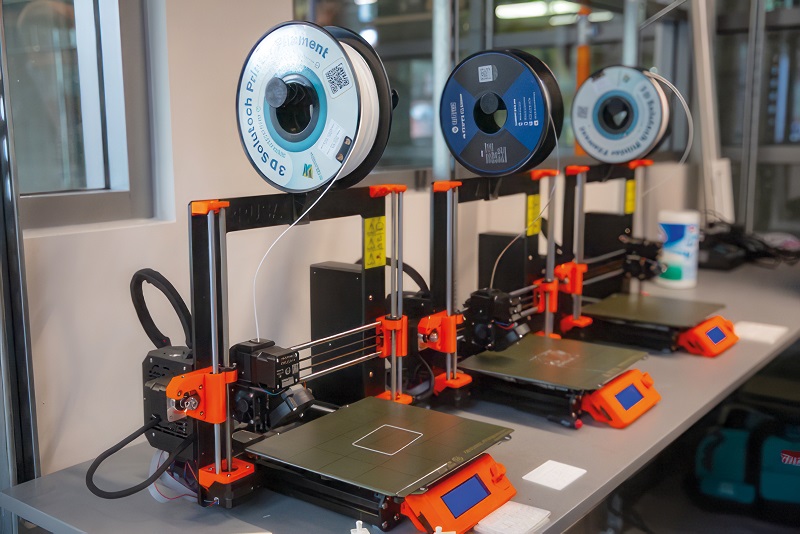
Photopolymer AM
Another additive technique is photopolymer AM (PAM). This uses digital light processing (DLP) with two lasers at different frequencies to cure photosensitive materials and curb the associated over-curing. That enables components to be fabricated with higher resolution and greater precision than existing PAM technologies.
Rather than using a single laser, this DLP2Curb process uses the first laser to cure the photopolymer, while the second prevents the material from over-expanding into the surrounding area. This can increase both the accuracy and the resolution in three dimensions, and allows faster printing.
The technique is still being developed, with testing of how the process works and how different materials behave under different conditions. This will involve creating a digital twin that will simulate how tweaks made to the process or material will change the outcome.
In the second part of the development, interferometric and ultrasonic monitoring systems will analyse the materials in real time to characterise PAM, providing data for AI to optimise and enhance the printing process.
Using a single wavelength to cure polymers while printing is already complex. Adding a second escalates that complexity, but the ML can enhance the accuracy. Conventional ML calculations take time and aren’t fast enough for real-time control yet, but the digital twin will provide more data to speed up the AI algorithms.
ML is also being used for real-time detection of keyhole pores that occur in a common AM technique called laser powder bed fusion (LPBF). LPBF uses metal powder and lasers to 3D-print metal parts, but porous defects remain a challenge, and they can come from deep and narrow depressions which are the keyholes.
The formation and size of a keyhole is a function of laser power and scanning speed, as well as the materials’ capacity to absorb the laser energy. If the keyhole’s walls are stable, it enhances the surrounding material’s laser absorption and improves manufacturing efficiency.
If, however, the walls are wobbly or collapse, the material solidifies around the keyhole, trapping the air pocket inside the new layer. That makes the material more brittle and more likely to crack under environmental stress.
A combination of synchrotron X-ray imaging, near-infrared imaging and ML has been used to capture the unique thermal signature associated with keyhole pore generation.
Porosity in metal parts remains a major hurdle for wider adoption of LPBF in some industries. Keyhole porosity is the most challenging defect type when it comes to real-time detection using lab-scale sensors, given that it occurs beneath the surface, but this high-resolution detection of keyhole pore generation can be readily applied in many AM production processes.
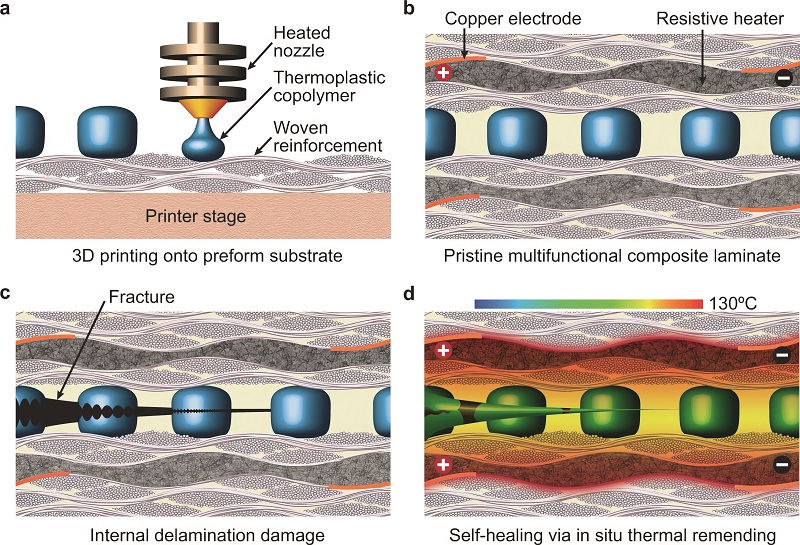
Self-healing materials
AM also allows for self-healing laminated composites to create structures that can repair themselves without having to be removed from service.
Previous self-healing materials had to be removed in order to heal, for example by heating in an oven, which can’t be done for large components or while a given part is in use. This repair process might also only be possible a few times.
Laminated composites on the other hand are made from layers of glass or carbon fibre that are bonded together. Damage most often occurs when the ‘glue’ that binds the layers together begins to peel away from the reinforcement, a process known as delamination.
The laminate is created by 3D printing a pattern of thermoplastic healing agent onto the reinforcement material and embedding thin ‘heater’ layers in the composite. When an electrical current is applied, the heater layers warm up, which in turn melts the healing agent that flows into any cracks or microfractures and repairs them.
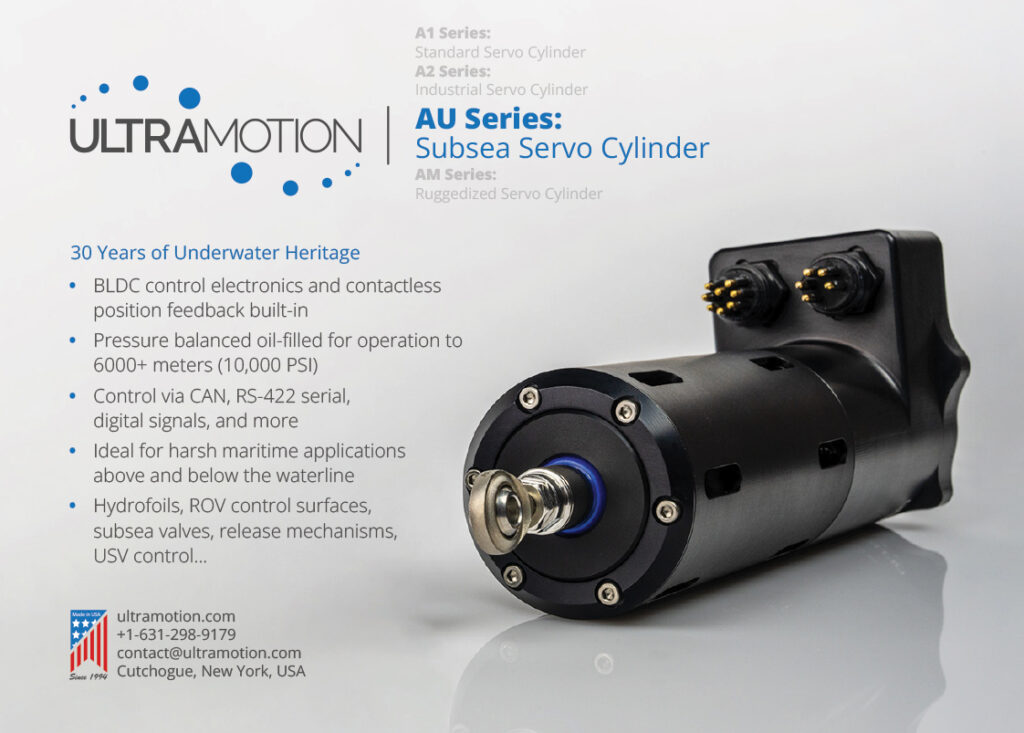
This process can be repeated at least 100 times while maintaining the effectiveness of the self-healing.
The printed thermoplastic is also inherently more resistant to fracture compared to moulded structures by as much as 500%, meaning more energy is needed to cause delamination in the first place. In addition, the healing agent and heater layers are all made from readily available materials, and are relatively inexpensive.
If incorporated into aircraft wings or propeller blades, the internal heating elements would avoid the need for chemical agents to remove ice and also provide de-icing in flight.
Counterfeit protection
Metal 3D printing is also being used to embed a hidden cache of information within products to help combat counterfeiting. The technique uses a hidden magnetic tag, encoded with authentication information, during the part’s fabrication.
This avoids the vulnerabilities of physical tags such as barcodes or QR codes, as they serve as permanent and unique identifiers, helping to keep the supply chain secure.
Once embedded into a non-magnetic item, the tag can be read by a magnetic sensor device such as a smartphone, allowing the information to be accessed by the user.
Various approaches have been used to try to change the local properties of the metals during manufacturing to be able to codify the information in the part.
For example, one component built from non-magnetic 316L stainless steel uses embedded ferromagnetic 430 or 17-4PH stainless steel regions for local control of the magnetic response. The magnetic flux normal to the surface is recorded using a magnetic sensor, to create a map, and the distribution of the magnetic regions can be retrieved from the map, creating a tag for storage in a secure database.
Conclusion
The technology for 3D printing and AM is advancing quickly. The days of a filament printer chugging away to produce a low-quality part are long gone.
Systems with large degrees of freedom and high-quality end-effectors offer faster production of sophisticated shapes with less weight, while ML algorithms are boosting the quality of the resulting parts.
These structures can now integrate anti-counterfeiting materials and self-healing mechanisms to keep components secure and in operation for longer, and can be combined with smaller, lighter components such as magnets and pumps.
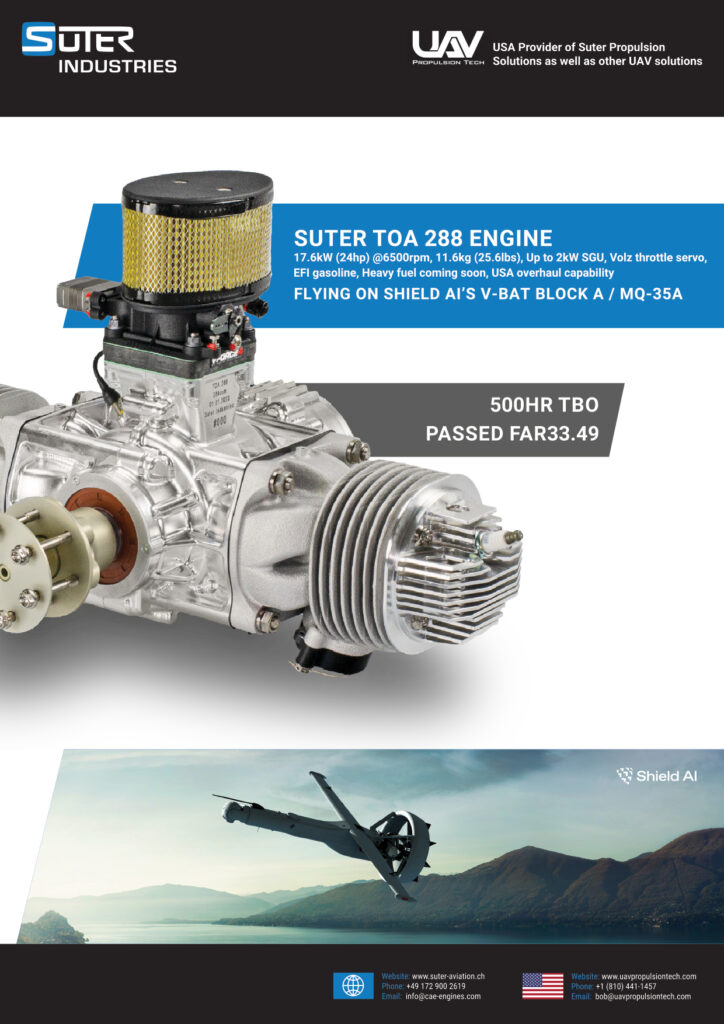
Acknowledgements
The author would like to thank Amolak Badesha at Orbital Composites, Michael Sheath at Greenjets, and Robert Bagheri at Sakuu for their help with researching this article.
3D-printing batteries
Solid-state batteries lend themselves to AM processes to form custom shapes. The technology is being used with lithium metal cathodes and 3D-printing solid electrolytes for batteries with high energy density. The technology is now coming to market, allowing batteries to be printed close to where vehicles and systems are assembled rather than requiring gigafactories.
AM is also being used for sodium batteries, building on the experience of using it on lithium-ion batteries. While they are lower in energy density than lithium-ion cells, sodium is more readily available and has fewer safety issues than lithium metal batteries. These are set to be demonstrated by 2025 at a pilot plant in Germany.
Constructing a sodium solid-state battery cell using AM increases its energy density and improves many of its safety aspects. The prototype method of producing sodium batteries is designed in such a way that a variety of active materials can be used, and changes for different products can be made quickly. The printing process is a key factor, and allows volumetric optimisation in addition to geometric adaptation.
3D printing also simplifies production. The process can print entire battery cells, from anode through electrolyte to cathode, including the casing. It is also flexible enough to print the materials for a typical lithium-ion battery cell chemistry, as well as future battery technologies, with capabilities to print a range of cathode and anode materials as well as solid-state electrolytes.
This replaces the four-step wet process of coating, drying, calendaring and notching with a simple deposition and cure process in 3D printing. It can reduce the production cost for a 24 kWh automotive battery by more than £480/€550, remove environmentally damaging N-methyl pyrrolidone solvents from the cell production process, and generate up to 85% less waste.
One fully industrialised process for printing batteries uses a proprietary multi-material, multi-layer approach in a parallel, dry process, instead of slow layer-on-layer wet printing or screen printing. These wet processes require a lot of energy to remove unwanted solvents, and are susceptible to poor printing quality and unreliable production.
The first printed batteries have demonstrated successful cycling performance at C/5 and 1C current rates, and they are expected to achieve densities of 800-1000 Wh/litres using a lithium metal battery chemistry.
Using patterned battery printing enables a more effective use of battery cell volume with new pathways for thermal regulation. It also allows fixtures and sensors to be added to the cells during assembly, as well as new patterned designs, especially when thin sub-cell battery structures are stacked with identical patterned openings for improved thermal management.
Some examples of additive manufacturing suppliers
AUSTRIA
Voestalpine High Perf Metals | +49 211 522 0 | www.bohler.de/en |
AUSTRALIA
Evok3D | +61 1800 386 533 | www.evok3d.com.au |
BELGIUM
Materialise | – | www.materialise.be |
CANADA
Burloak Technologies | +1 905 592 0244 | www.burloaktech.com |
FRANCE
AddUp SAS | +33 4 73 15 25 00 | www.addupsolutions.com |
Pollen | +33 1 58 46 20 52 | www.pollen.am |
GERMANY
EOS | +49 89 893 36 0 | www.eos.info |
ExOne | – | www.exone.com |
GKN Additive | – | www.gknpm.com |
Oerlikon | +49 39203 510 60 | www.oerlikon.com/am |
OWL | +49 15901 313 89 7 | www.owl-additive-manufacturing.com |
ITALY
3NTR | – | www.3ntr.eu |
CRP Technology | +39 059 821 135 | www.crptechnology.com |
Sinthesi Engineering | +39 331 556 557 | www.sinthesieng.it |
JAPAN
ARRK | – | www.arrk.com |
Mimaki | – | www.mimaki.com |
Ricoh | – | www.ricoh.com |
NETHERLANDS
Additive Industries | +31 40 218 0660 | www.additiveindustries.com |
NEW ZEALAND
Zenith Tecnica | – | www.zenithtecnica.com |
SWEDEN
Sandvik | +46 8 456 11 00 | www.sandvik.com |
UK
3DDC | +44 1234 391894 | www.3ddc.eu |
3T Additive Manufacturing | +44 1635 580284 | www.3t-am.com |
Alloyed | +44 1865 954250 | www.alloyed.com |
CA Models | +44 1786 464434 | www.camodels.co.uk |
Croft Additive Manufacturing | +44 1925 767070 | www.croftam.co.uk |
Laser Lines | +44 1295 672588 | www.laserlines.co.uk |
Laser Prototypes | +44 2890 706940 | www.laserproto.com |
Material Solutions | +44 1905 732160 | www.materialssolutions.co.uk |
Performance Engineered Solutions | +44 1143 216375 | www.pes-performance.com |
Progressive Technology | +44 1635 500480 | www.progressive-technology.co.uk |
Renishaw | +44 1453 524524 | www.renishaw.com |
Ricoh 3D | +44 0800 3047196 | www.rapidfab.ricoh-europe.com |
SHD Composites | +44 1529 307629 | www.shdcomposites.com |
Smith’s High Performance | +44 1767 604708 | www.smithshp.com |
USA
3D Systems | +1 803 326 3930 | www.3dsystems.com |
Airwolf 3D | +1 949 478 2933 | www.airwolf3d.com |
Arris Composites | – | www.arriscomposites.com |
Desktop Metal | – | www.desktopmetal.com |
Form Labs | +1 617 702 8476 | www.formlabs.com |
GE Additive | – | www.ge.com |
HP Enterprises | +1 888 342 2156 | www.hpe.com |
Incodema | +1 607 227 7070 | www.fathommfg.com/incodema |
Markforged | +1 866 496 1805 | www.markforged.com |
Orbital Composites | +1 510 825 9555 | www.orbitalcomposites.com |
Protolabs | +1 877 479 3680 | www.protolabs.com |
Questek | +1 847 328 5800 | www.questek.com |
Solvay | +1 770 772 8451 | www.solvay.com |
Stratasys | +1 800 801 6491 | www.stratasys.com |
Velo3D | +1 408 610 3915 | www.velo3D.com |
Vetted Tech | +1 315 802 6505 | www.vetted3d.com |
Xact Metal | +1 814 205 1505 | www.xactmetal.com |
Xerox | +1 866 460 2248 | www.xerox.com |
UPCOMING EVENTS
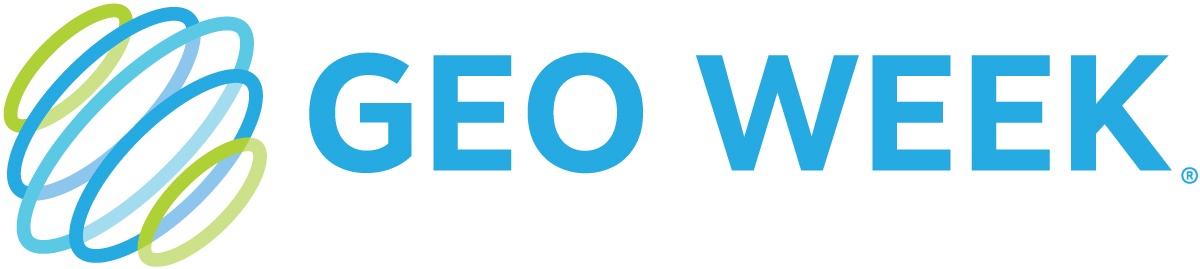
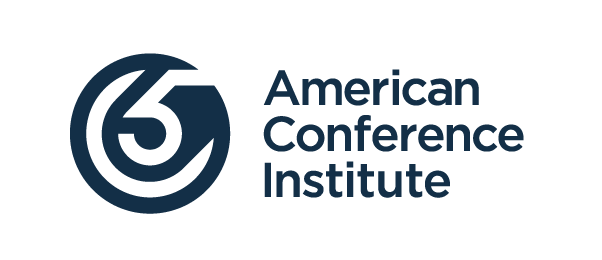
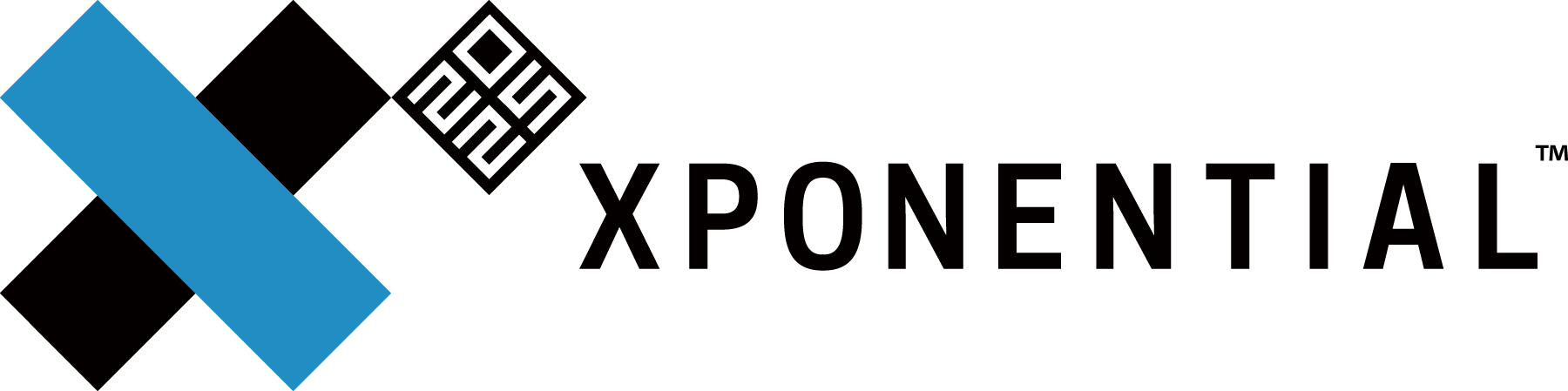
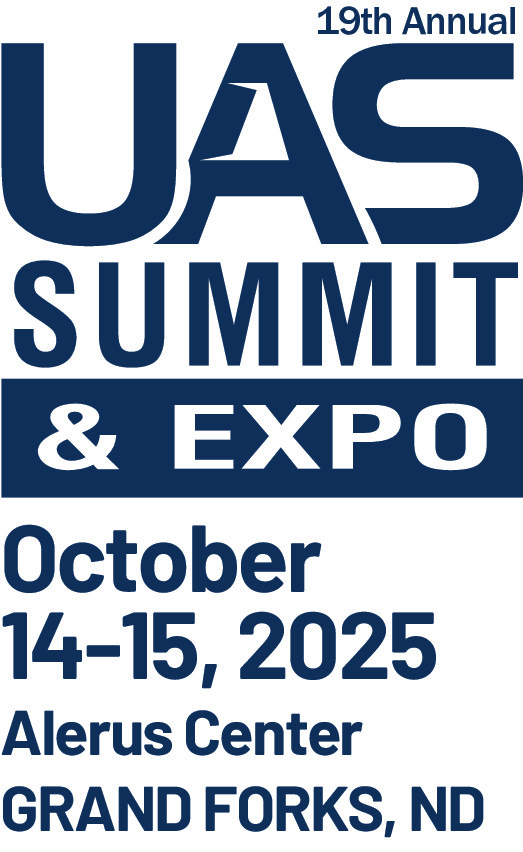
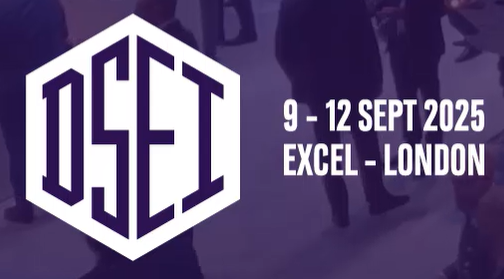
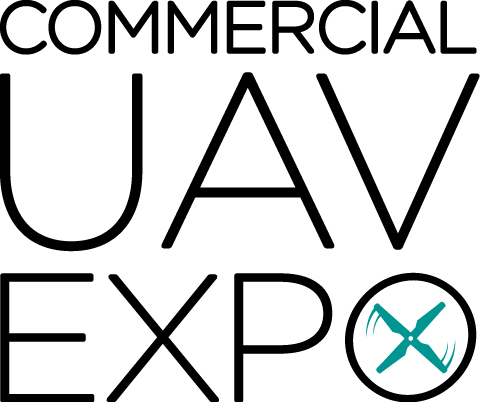
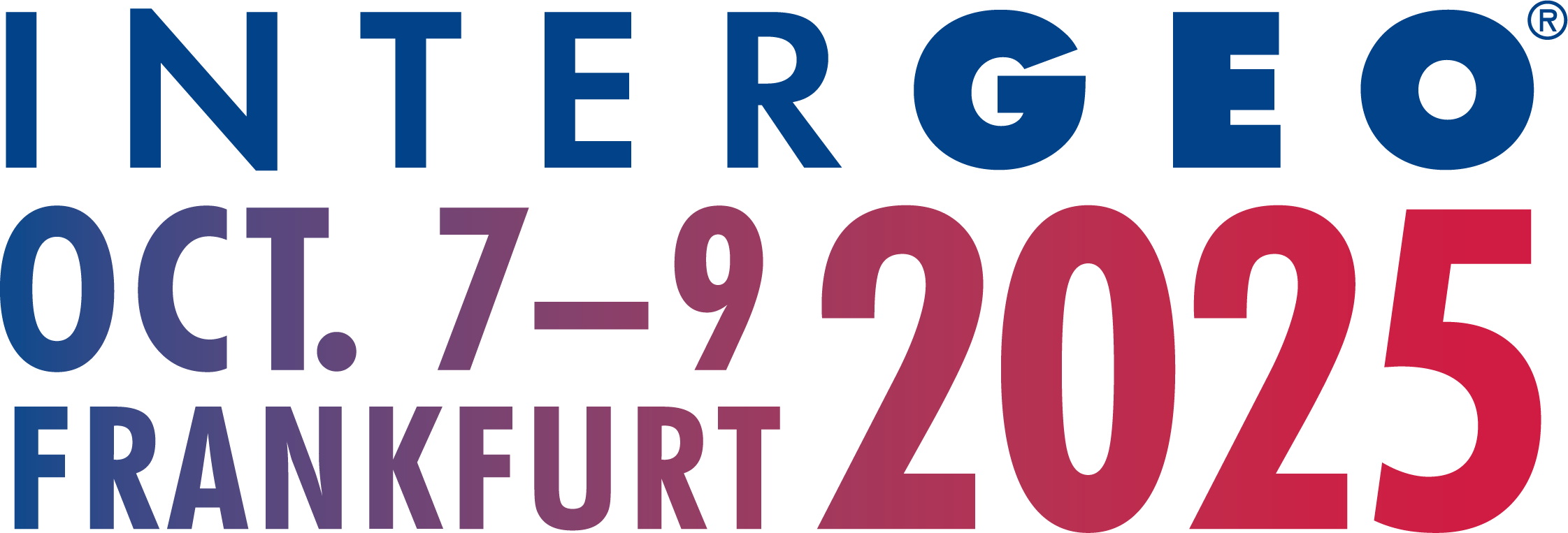
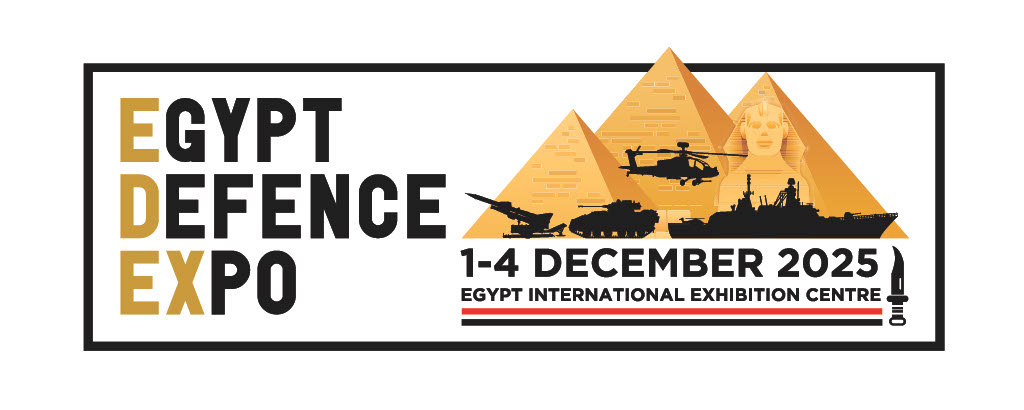
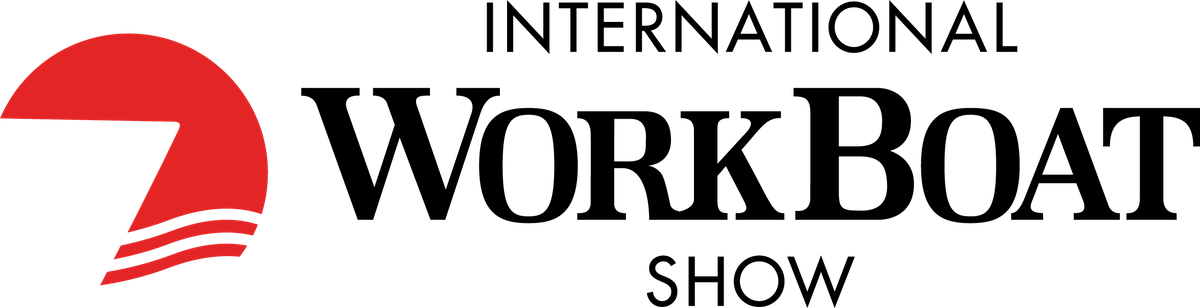
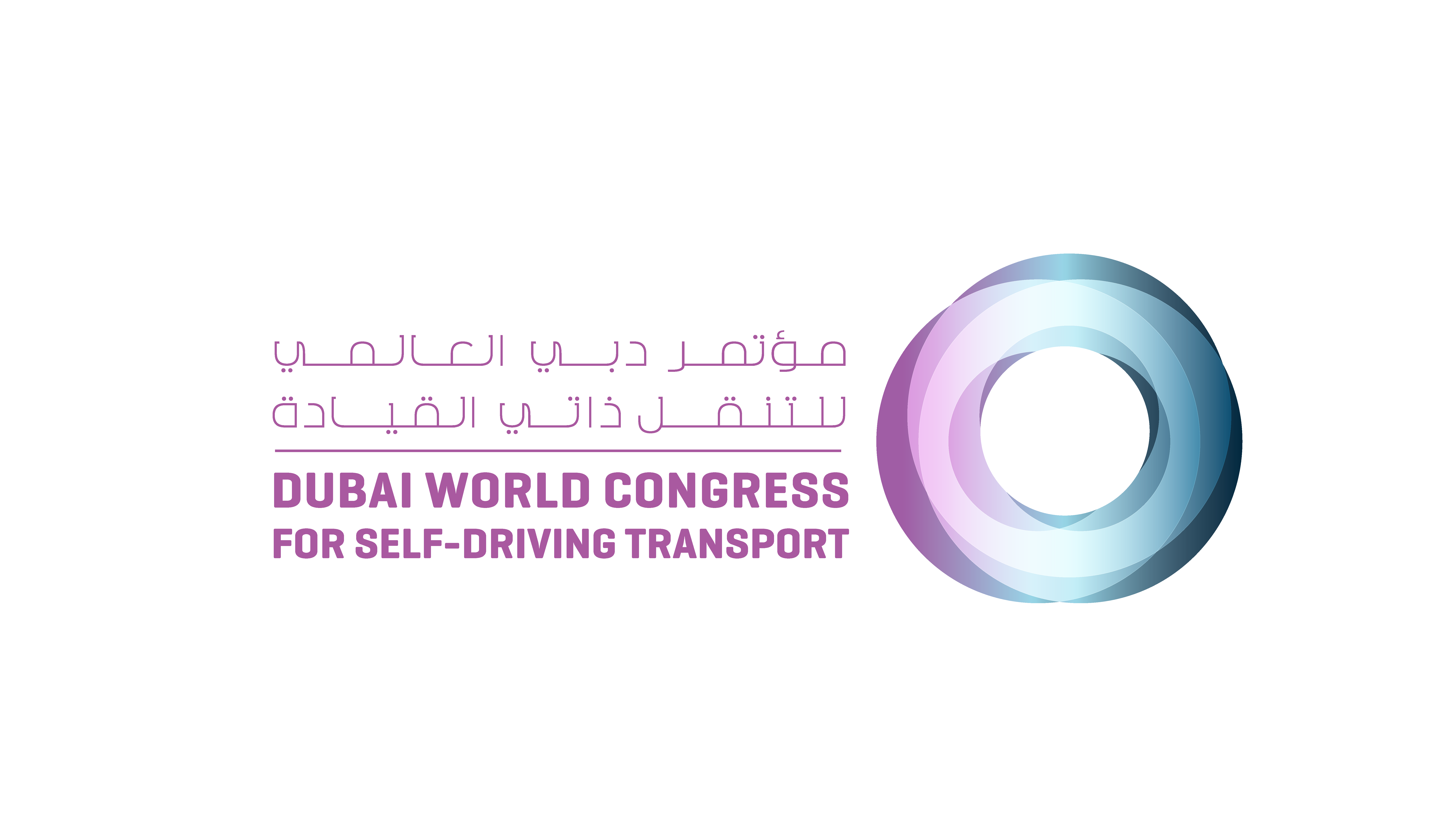
