Swiss-Mile UGV
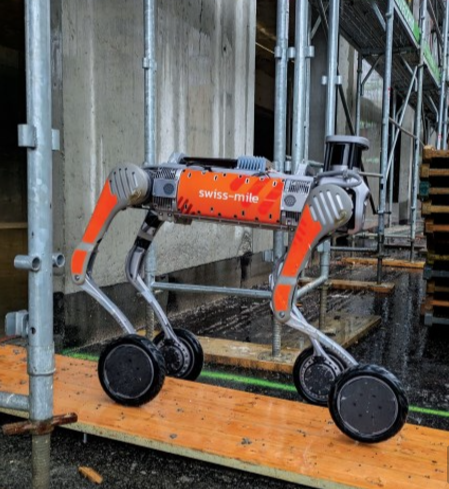
Rory Jackson investigates a robot that can walk, roll, stand and grab as needed for highly proficient work on site, fulfilling observation, monitoring and security roles
Of all types of bio-inspired uncrewed systems around the world, legged UGVs, and particularly quadrupeds, have made the greatest strides. Their ability to traverse stairs and challenging terrain, and push doors or gates open, makes them highly effective in many indoor and outdoor environments where UAVs and wheeled UGVs struggle.
However, present limitations of battery energy density and electric-motor efficiency cause legged robots a few specific weaknesses in comparison with wheeled robots. Namely, the latter outperforms the former in movement speed, turning speed and energy efficiency, particularly on flat terrain.
As of writing, most industries and businesses using legged robots are deploying them in predominantly flat areas, such as power stations, hydrocarbon facilities, factories and foundries. Hence, wheeled robots could work in such places if doors, stairs and small ground obstacles could be circumvented.
Understanding how legs and wheels overcome each others’ minor weaknesses inspired Swiss-Mile’s founders to consider combining the best of both worlds: putting wheels on a legged robot. Such a UGV could walk up and down stairs, and cross uneven or cluttered ground, while also energy efficiently driving through the flat corridors and floorspaces that compose 90% of the areas they operate in.
“During our PhD research at ETH Zürich, we experimented by modifying an ANYbotics ANYmal UGV [see Issue 40], adding wheels to its four legs and, of course, that made it much faster, but the far more important benefit was that energy consumption went down significantly by being able to move on wheels instead of legged locomotion in many places,” says Swiss-Mile’s co-founder and CTO for software, Lorenz Wellhausen.
“Instead of being limited to one hour on a single battery charge, our modified robot went for two hours. The wheels significantly extend the operational domain of any legged robot.”
With such potential for greater uptime for indoor and outdoor operations, including on hazardous sites such as construction, Swiss-Mile was spun out from ETH Zurich and incorporated as a company in mid-2023 – now with 13 staff and five prototype UGVs.
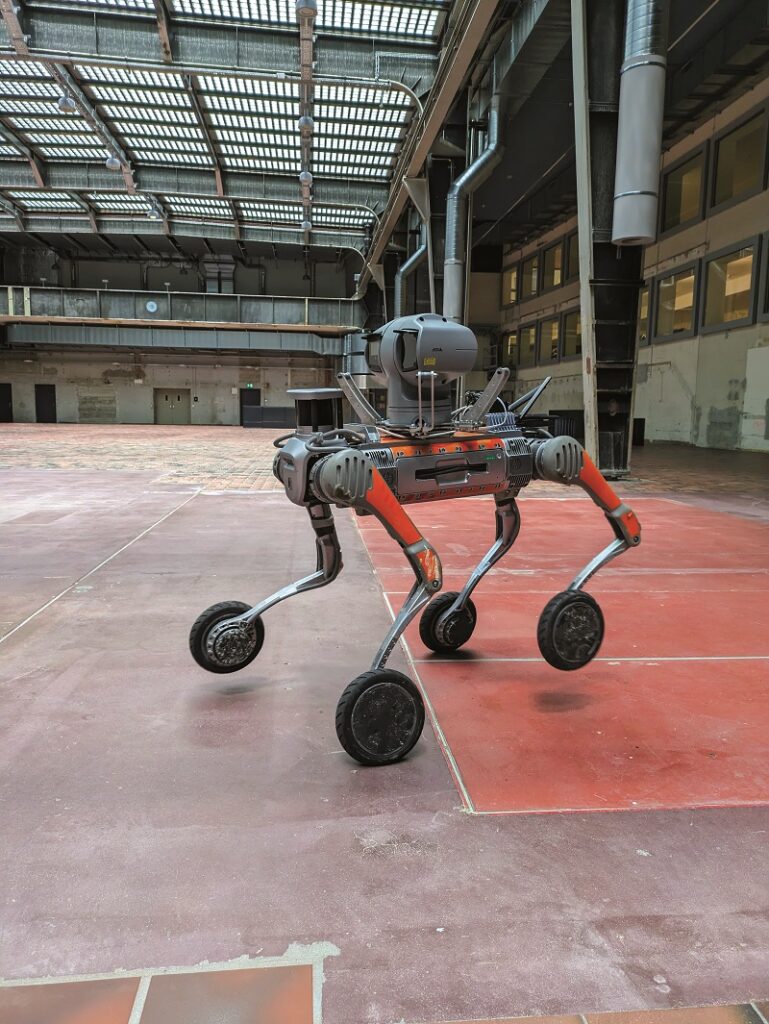
Swiss inspired, Chinese built
The Swiss-Mile founders’ early research used the aforementioned ANYmal from its fellow ETH Zurich spinout, ANYbotics, but since its founding, the former has switched to using the B2-W quadruped UGV from Unitree Robotics, based in Zhejiang, China, as a platform for its UGV development and commercial services.
“Unitree seems to have already seen what we were doing in a research context, and gotten inspired to build a wheeled version of its B2 UGV [B2-W meaning B2 with Wheels], so we were able to start buying those at a very good price and they came ready-made with motorised wheels,” Wellhausen says.
“That means we don’t have to do any significant hardware modifications and we can focus on our software work, as well as on finding ways to suit the UGV to market applications.”
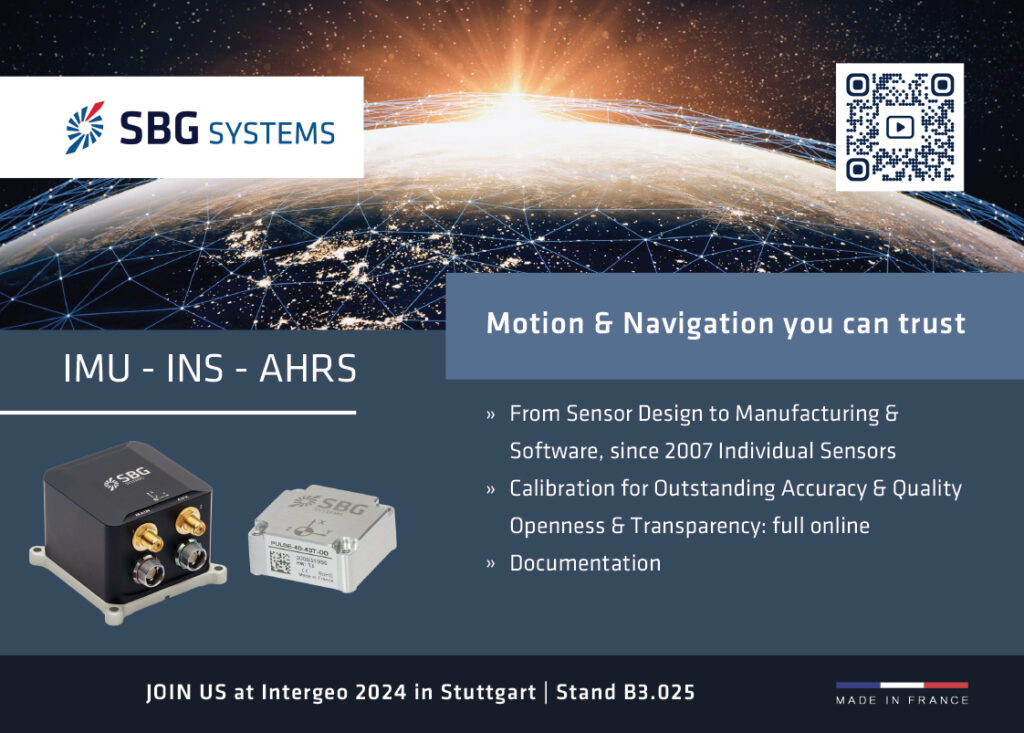
With its 22 cm-diameter wheels, the B2-W has a top speed of 6 m/s (21 kph). It weighs 75 kg and can take payloads of 60 kg. Able to climb stairs or inclines of 45°, it runs on an Intel i7 CPU and is IP67-rated for ingress protection.
Importantly, Swiss-Mile only uses the B2-W’s hardware and none of its software; every piece of code on Swiss-Mile’s UGVs is unique to the Swiss company.
“We had worked heavily on creating our own algorithms at a time when wheeled-legged robots were a totally new robot morphology, and we’d made our IP while also coming to grips with hardware challenges, like getting the wheel hardware right for both driving and stepping over obstacles,” he recounts.
“With bio-inspired robots, you can always take engineering inspiration from nature: how a dog walks, how a bird flaps its wings, how a fish swims, for example. But there is no wheeled-legged animals in nature, and we, as humans, don’t necessarily have the intuition for it. So it has been really hard from the beginning, when we tried to use model-based control approaches to design our motion, to ensure the robot only steps when it needs to, or only drives when efficient.
“That’s where reinforcement learning [RL] had a huge impact, enabling the robot to figure out good locomotion by itself, once we’d defined the parameters and constraints on what it couldn’t do, as well as the optimisation objectives. It marked a breakthrough in our autonomous locomotion and performance.”
With Swiss-Mile’s own autonomy stack and intelligence installed, the UGV becomes a unique autonomous system in its own right. To mark the intelligence and capabilities of its robotic dog apart from the B2-W, Swiss-Mile has named the new system Milo.
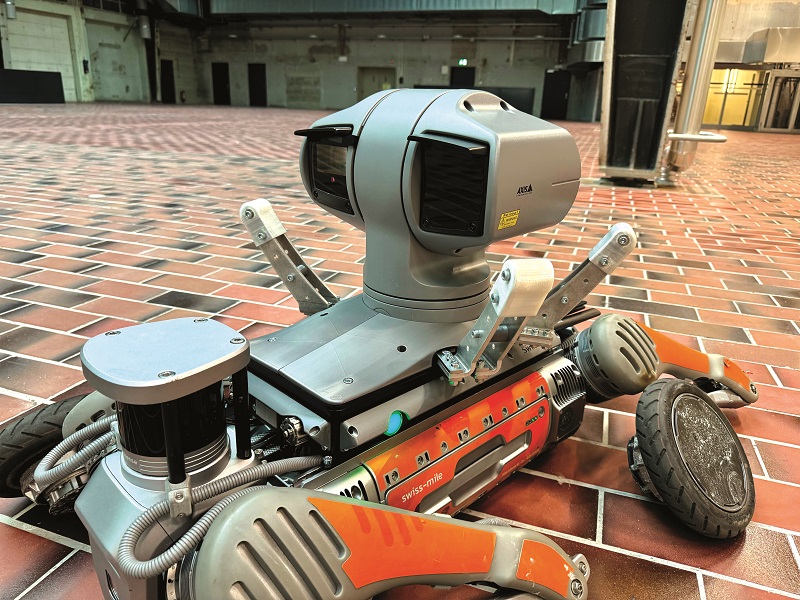
Training Milo
We previously saw RL being used to great effect by Spanish firm Keybotic in training its Keyper quadruped UGV (Issue 52), and Wellhausen puts forward two reasons why it is proving revolutionary in engineering legged robots.
“When RL policies are trained correctly they can handle uncertainty a lot better than other forms of motion control can achieve,” he says. “RL neural networks internalise uncertainty about their environments while learning, making them very robust. Basically, by training Milo in environments where it was subjected to external disturbances, it learned how to bypass, work around or ignore those disturbances.”
Conversely, model-based approaches require that the engineer model such disturbances, and then install some means for the UGV to detect and classify those disturbances, overall entailing far more engineering labour than RL does.
“Second, with RL, you don’t have to design the motion manually. Trying to manually specify when the robot should step, and when it shouldn’t, brings forth a huge combinatorial problem, because this robot has four legs, and each leg requires a decision to be made based on both directional commands and terrain properties,” Wellhausen explains.
This requires immense heuristics, including matters such as step detection (for intelligent reaction in case a leg gets stuck, for instance), so being able to learn the right reactions itself via RL makes developing the UGV far easier.
Having developed its algorithms in this way on a modified research quadruped, the company was swift to install and adapt them into the new B2-W platform to create Milo, with the first prototype entering in-the-loop simulations after roughly five days of work, and hardware locomotion tests after three weeks.
“Of course, we had a six-year r&d background at ETH Zurich, which helped us know going in what was necessary to make this work in hardware, including defining constraints and rewards for the machine-learning network to achieve good motion,” Wellhausen says.
“With the B2-W’s morphology being fairly similar to the modified research quadruped, it was fairly easy to switch it to a new platform. If we had to move to another new one, we’d probably be pretty fast still.”
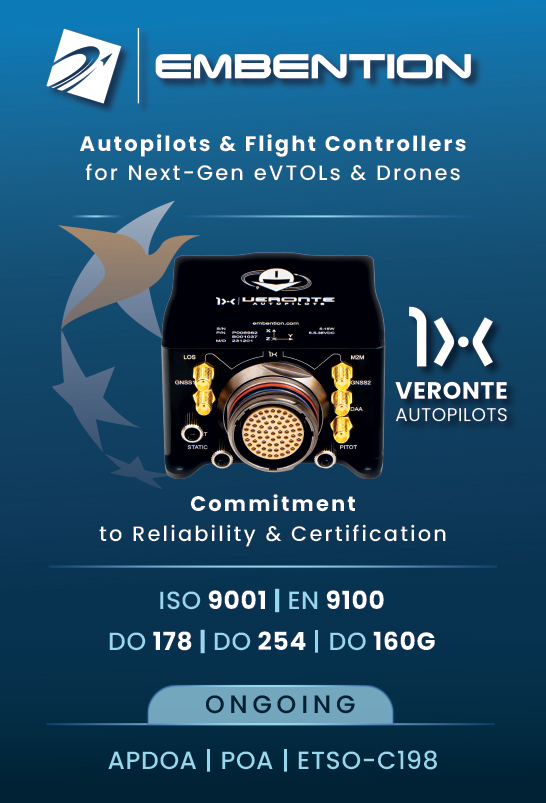
Hard hats on
Among Swiss-Mile’s target use-cases, construction stands out as an industry that uncrewed systems have had trouble breaking into, owing to a variety of regulatory and technological hurdles. Despite these, construction companies are inviting Swiss-Mile to demonstrate Milo’s capabilities at project locations.
One key application on site is safety monitoring, where a high-resolution camera is installed on Milo to take videos and photography to verify that everything is up to code, such as the accessibility of emergency exits, the correct placement of heavy equipment and the installation of guardrails.
Another is progress monitoring, which would see Milo running controlled routes with cameras (or Lidar for high-fidelity digital twins) to identify work progress since the last survey, and also to compare the new 3D model with the customer’s digital model to see if construction is proceeding correctly.
“Rework is one of the construction industry’s biggest sources of cost. One estimate puts up to 30% of construction costs being just rework costs, because incorrectly built sections get disassembled, materials go to waste and significant work has to be done all over again. So, if Milo can be used to catch errors earlier, when they’re still small, it works out much cheaper for the end-user’s medium- to long-term expenses,” Wellhausen explains.
Future work may include logistics, such as Milo moving heavy tools and materials for construction workers, but this would require engineering added subsystems for loading and unloading, such as robotic arms or gantries. Hence, Swiss-Mile is focusing on the first two use-cases to secure market share and revenue, such that its future growth will come from proven commercial successes.
“Whichever use-case we’re doing, the core autonomy stack is the same, needing no software adaptations per the environment for the locomotion, obstacle avoidance and so on to work,” Wellhausen says. “There might be rules you need to follow on construction sites, pathways you use or don’t use, restricted areas, that sort of thing, but those are just minor, surface-level tweaks.”
A Swiss-Mile engineer is always present at its proof-of-concept deployments to ensure the system is safe and to perform a pre-operational checklist. That involves looking for signs of damage on Milo’s hardware, listening for wear or jamming in its joints, and ensuring there are no obstructions or obscurants on the payloads before it sets off for the day.
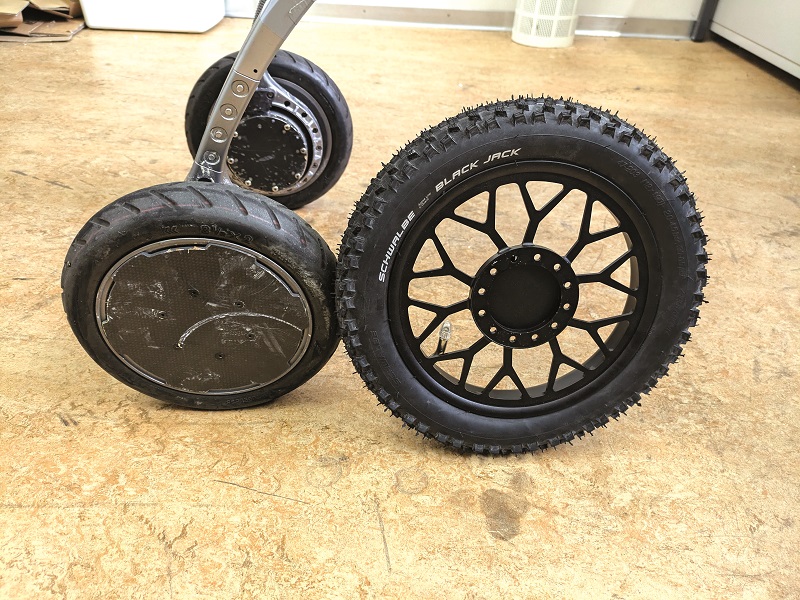
Do the locomotion
Milo will roll around the construction site at 2 m/s (a safety imperative speed limit) until it identifies some stairs, at which point it will switch to walking mode. Otherwise, it will roll so long as the terrain is reasonably flat, including in slightly curved paths, as it can slightly angle its body posture to drive forwards with a turning radius rather than needing to stop in place and then step to rotate itself, as legged UGVs do at present.
“It still steps if it must turn in place, and it sidesteps if needed, and if it slips or loses balance it steps to stabilise itself. Those are places where nature has designed the leg for good work,” Wellhausen notes.
“We make sure to choose the right tyre for optimising traction across different terrains. In construction sites, we would pick a high-grip tyre, something akin to a mountain bike tread, to minimise slipping. The size of the wheel must also be chosen carefully, because a bigger wheel will drive better over rugged ground, but be worse at climbing stairs with secure footing.”
Slip is detected from the joint motors’ and wheel motors’ data on speed and torque, and from the onboard IMU, with the neural network compensating accordingly with whichever steps, posture or mode switching it has determined is sensible. One thing it does not need to avoid is humans as trials currently only run after the sites have been cleared of personnel for safety reasons, but it has been trained to do so, given the work that Swiss-Mile anticipates carrying out commercially one day.
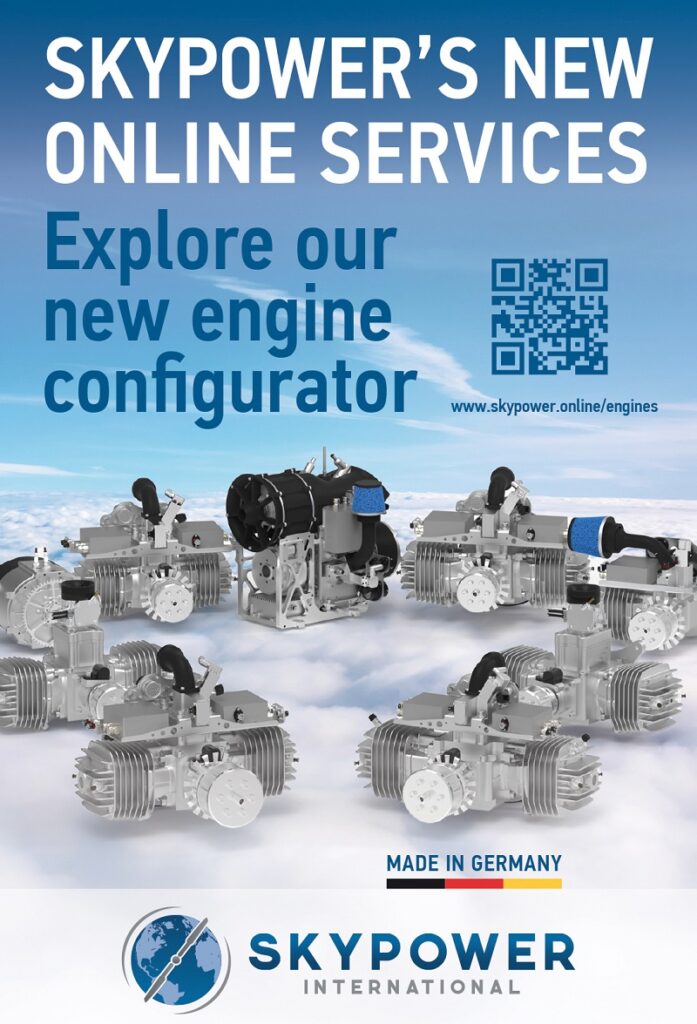
Stand proud
While walking UGVs can push doors open or use automatic sliding doors, if they encounter a pull door they must either return from whence they came or ask a nearby human for help. Milo, by contrast, can stand on its hind legs, reaching with its front legs, and gripping handles with its front wheels to pull doors open.
Programming the robot to stand was originally done by Wellhausen and his colleagues at ETH Zurich on a whim, simply to see if it was possible. Only after they managed it did they come up with other ideas on how the standing function could be made useful.
“First, we trained it to grip packages and move them around a little. Then we focused on door manipulation, and in construction sites it could be used to move non-heavy objects blocking emergency exits and similar sorts of tasks,” Wellhausen says.
“There is still a bit of optimisation work to do with door-related intelligence. Milo needs to consistently recognise whether a door is left-hinge or right-hinge, or if it can only be pulled versus being push or pull, for instance. And we’re dead-set on the robot figuring that out autonomously without needing a human.”
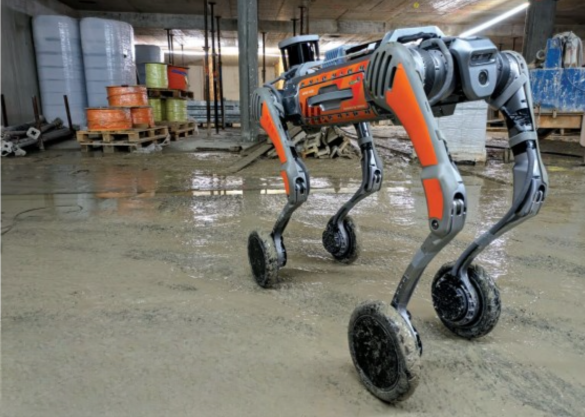
Building success
Data collected from change-monitoring surveys will be analysed post-recovery of Milo, using the customer’s post-processing systems (including COTS software designed for progress evaluations on construction projects), and no prospective end-user has yet required real-time video or photo streams from the UGV.
“Even in safety inspections it isn’t so urgent that the data be actionable immediately. It is unlikely, for example, that a speaker will be installed on Milo so it can go and tell a worker to put on their hard hat,” Wellhausen says.
“The far more important thing to construction companies is that the UGV can autonomously circumvent obstacles, stairs, and so on, to do its surveys and provide data without needing human help.”
Naturally, it helps that Milo can run far longer than non-wheeled robots, and Swiss-Mile reports that it has operated for up to six hours on singular charges.
Once near depletion of battery energy, the robot walks to a predefined location where a compatible charging plate is known to be, so it can sit on the plate, dock its charging connector and replenish its energy stores. By this autonomous behaviour, human workers are also freed from the maintenance burden of recharging it manually, although they can replace the battery if someone is on location and they want Milo to immediately return to work.
As shown in trial demonstrations, a Swiss-Mile engineer is onsite, and once Milo has returned from a survey they will perform a set of maintenance checks much like that carried out before the operation commenced, visually inspecting for signs of damage and listening for suspicious clicking or grinding sounds from electric motors.
“Then, of course, the data that the robot collected will be transferred so the customer can perform the valuable analyses they actually want. That is typically done wirelessly. As mentioned, there is no frantic urgency to perform the analysis immediately, and for security reasons most customers don’t want a physical plug-in between the robot and their network,” Wellhausen adds.
“Lastly, on our side, we run some automated telemetry analyses to check the robot’s subsystems have been operating smoothly.”
Future
Going forwards, Swiss-Mile plans to continue carrying out use-case demonstrations across not only construction sites but also other industries where security and monitoring are useful, as well as looking into ways of applying Milo in logistics while minimising the engineering overheads that such work would entail.
“Nailing the first use-cases will enable us to go into series production and have a sustainable business,” Wellhausen says. “And, in terms of our technological focus, we’re going to keep working to improve the robot’s core capabilities however we can think of doing so, because different use-cases and sectors will have little nuances for how the autonomous behaviours need to change slightly, and accounting for those just makes our product and its services better.”
Much of that will involve honing the wheeled quadruped’s abilities in manual manipulation: being able to pull open doors is rapidly becoming a hot-button issue in autonomy discussions, because if a UGV can pull doors open it becomes notably more useful than one that cannot, and a UGV’s real autonomy – its ability to work without human intervention – becomes considerably more far-reaching.
“Beyond that, we will want to improve Milo’s high-level decision-making across all operating environments,” Wellhausen says. “That will mean delving into cutting-edge AI topics and leveraging foundation models to increase the robot’s autonomy and its intelligent understanding of its surroundings more than any uncrewed system has before.”
Key specifications
- Milo
- Wheeled quadruped
- Battery-electric
- Weight (no payload): 75 kg
- Maximum payload: 60 kg
- Dimensions (standing four-legged): 1098 x 550 x 450 mm
- Maximum wheeled speed: 6 m/s (21 kph)
- Operating speed: 2 m/s (7 kph)
- Maximum incline: 45o
- Endurance: 6 hours
UPCOMING EVENTS
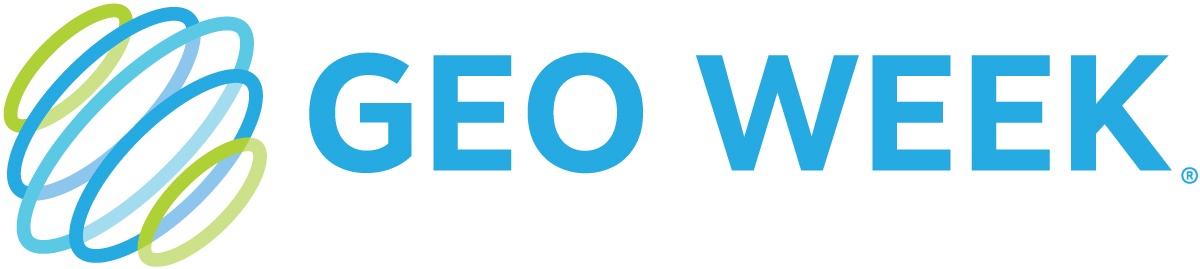
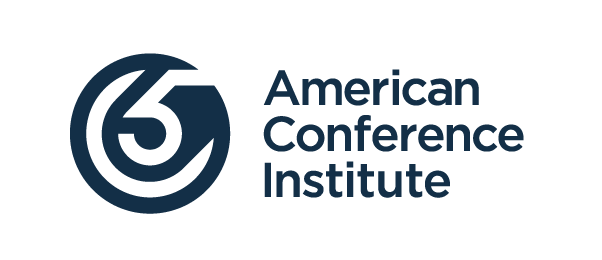
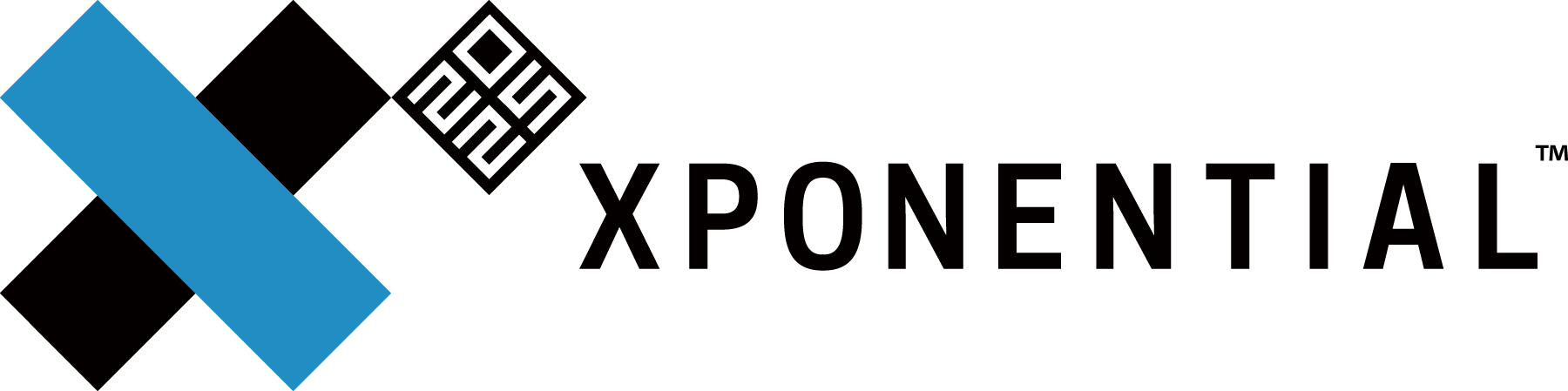
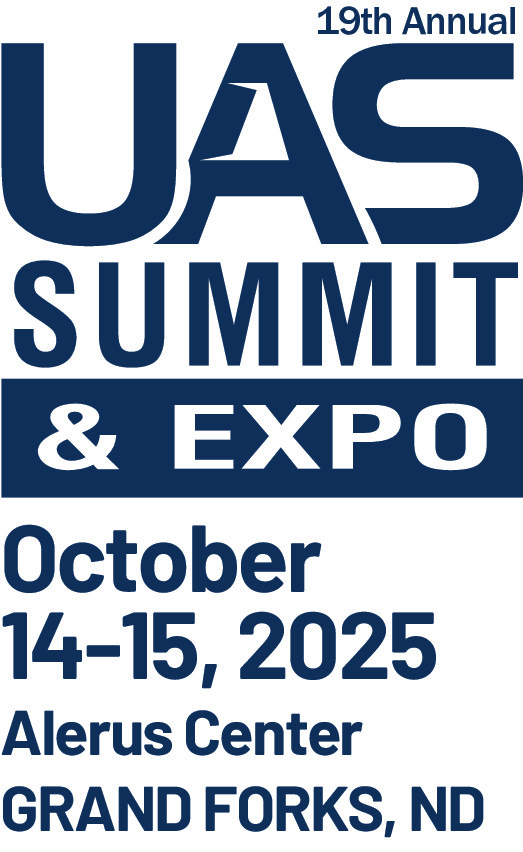
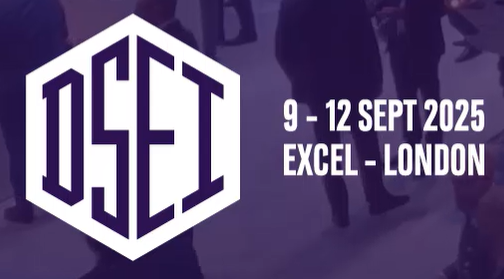
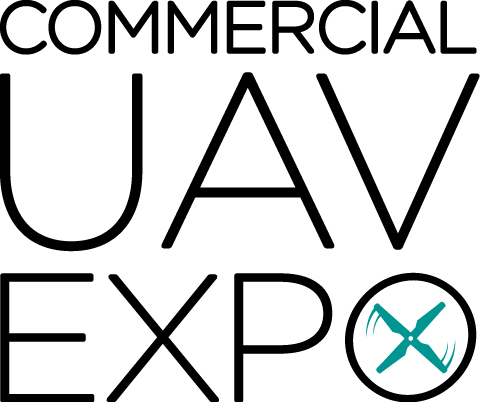
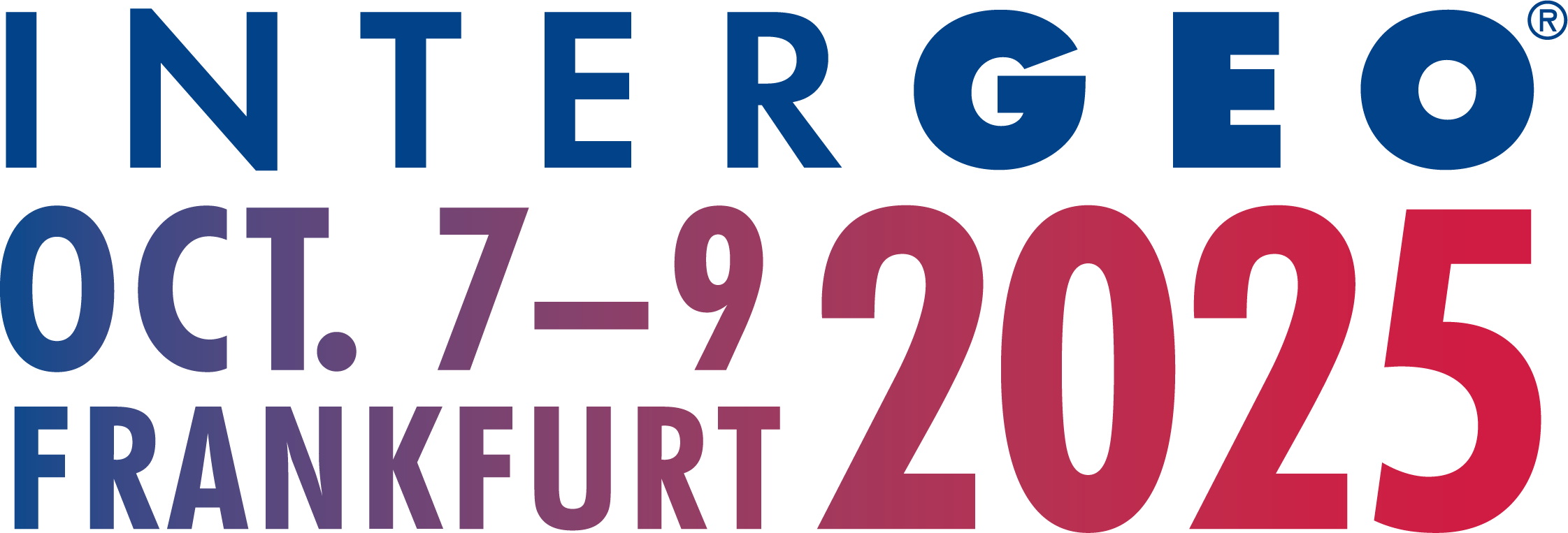
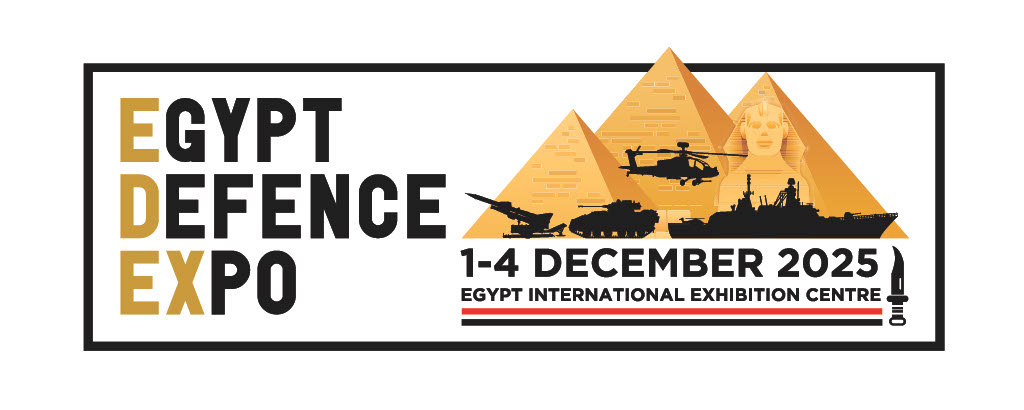
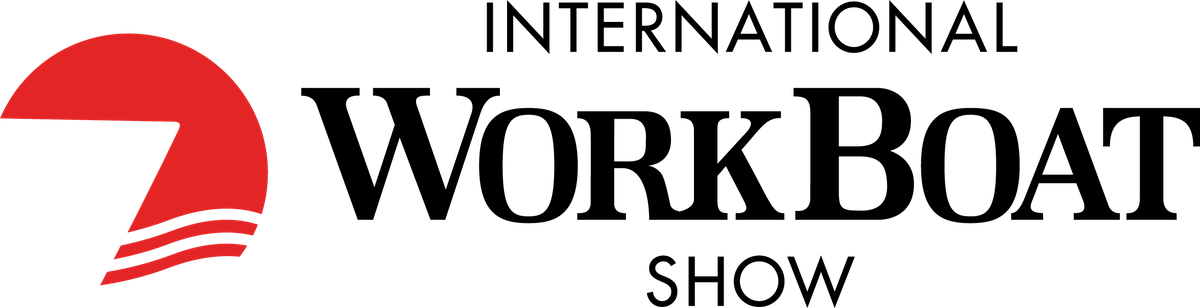
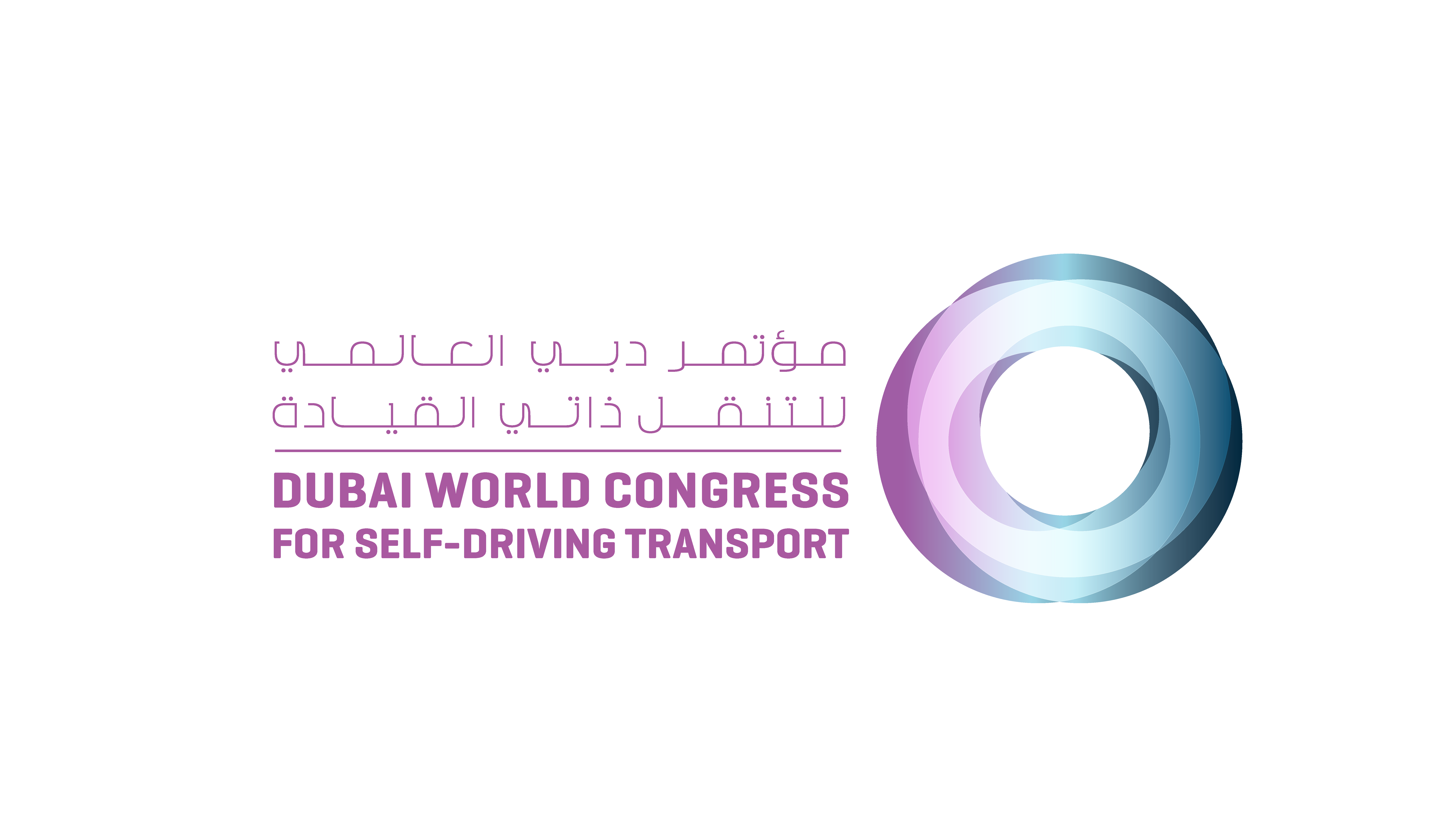

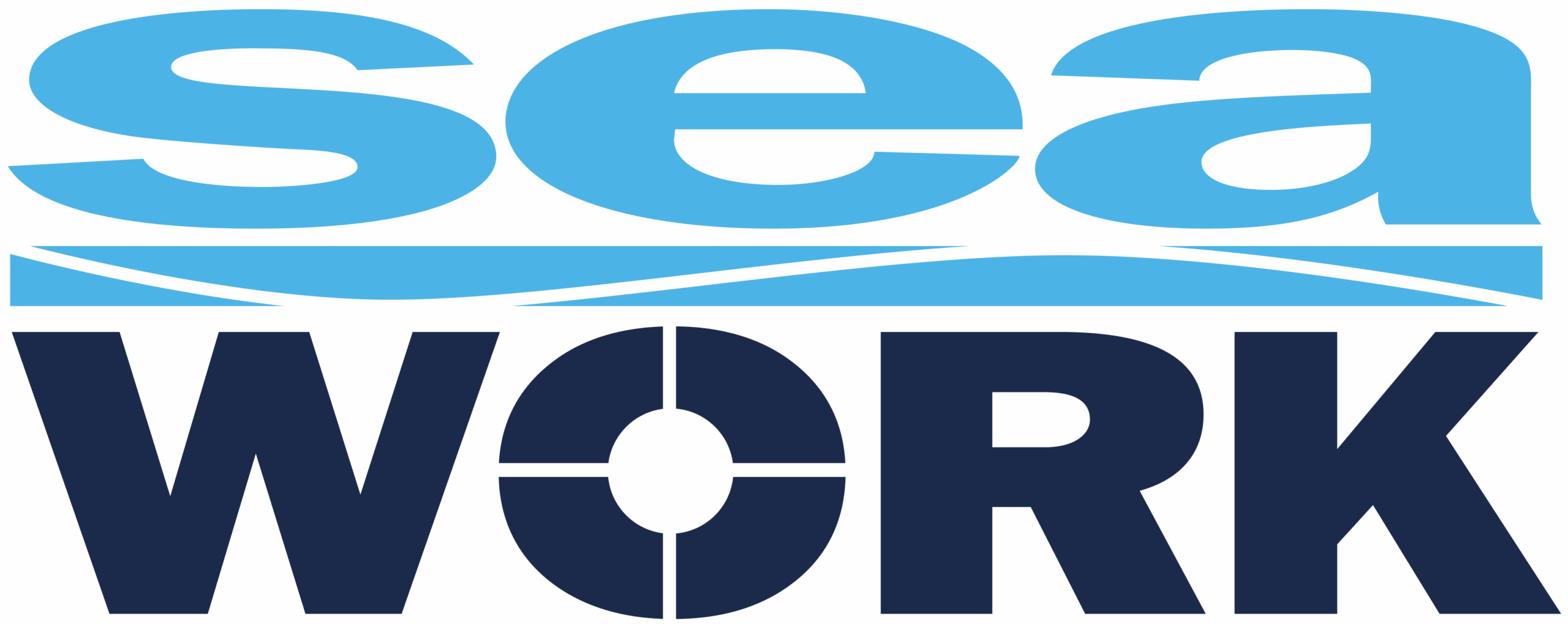