DSEI 2023
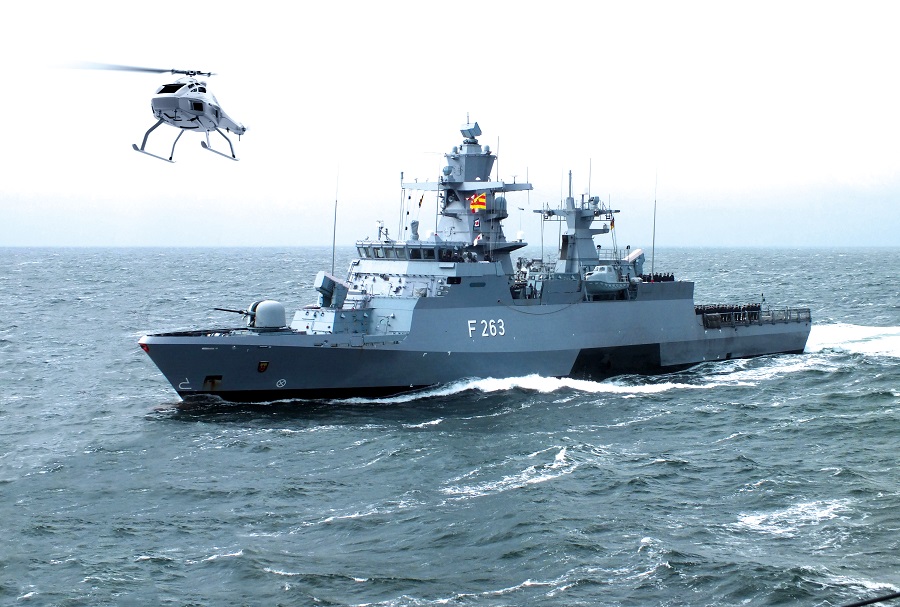
Suppliers of a wide range of systems and subsystems were gathered in London to show their wares to the defence industry, a selection of which Rory Jackson presents here
The Defence and Security Equipment International remains the biggest defence technology show in the world. As an illustration, more than 1500 defence and security suppliers exhibited at the 2023 iteration of this four-day event in September.
As well as increasingly intelligent and capable uncrewed vehicles on display, cutting-edge subsystems for computation, navigation, connectivity, power, maintenance and more were unveiled.
We met with ESG, a company that provides system integration services for aircraft, land vehicles and maritime systems to organisations across military and government services.
“We’ve worked increasingly with uncrewed systems, particularly UAVs, although other uncrewed vehicles are being demanded at a faster rate,” explained Daniela Hildenbrand.
“We consult with defence and government agencies to find the ideal vehicles for each of their use cases, including autonomous platforms of different sizes and capabilities, and we bring those systems into operation with their crews, mostly for ISR missions and especially reconnaissance.
“As well as understanding the ins and outs of the uncrewed system and how its missions are carried out, we also have to work with the primes to make sure the demands – such as actionable intelligence – that the customer wants to derive from the uncrewed vehicle are being met by their operations.”
ESG therefore researches and selects uncrewed vehicles, chooses and integrates payloads into them, and provides software for mission planning, monitoring and control, as well as post-processing and analyses. Examples include the VorMUAS and AImEG projects in which ESG integrated a custom version of UMS Skeldar’s V-200 helicopter UAV to operate from the German Navy’s K130 corvettes, as well as providing documentation and initial runs of spare parts for the aircraft and integrating its GCS into the K130’s operations centre.
It has also designed and established counter-UAS infrastructures, including combinations of ground-based EO/IR surveillance with hunter UAVs to fire nets for capturing non-compliant or trespassing UAVs.
“We fuse static and mobile surveillance systems and uncrewed vehicles via our Elysion C4I software, which provides the core intelligence and a GUI, and hence an operational overview for air defence of sensitive ground assets,” Hildenbrand added.
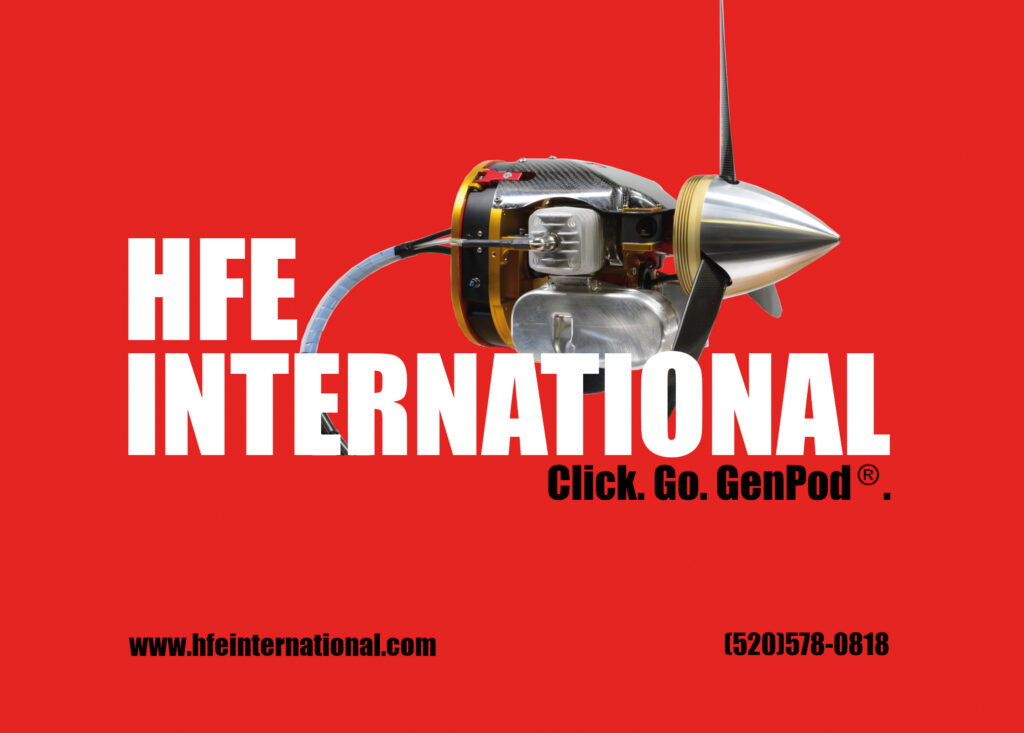
Click Bond showed us two new solutions aimed at making maintenance with its fasteners and other bonding products easier.
The first was a sleeve liner component that’s used to protect hole liners or to enable the use of smaller bolts in larger holes by inserting a sleeve to narrow the hole (rather than using a larger bolt, which can be more expensive and have a longer lead time than smaller bolts). The units are manufactured by die-punching sheet metal to long-draw the sleeve shapes.
“You just take one of these sleeves, press-fit it over a bolt, and you’ve created your oversized fastener on the fly, or if you have an oversized hole then you drop the sleeve into it to bring it back to nominal size,” said Sean Costella.
The company is also developing an AR and VR-based version of its product portfolio, to be used by technicians or systems integrators to choose the right fastener for an airframe, or for design engineers to select the optimal solution during the concept stage of a new vehicle.
“By viewing their vehicle or a CAD model of it with an AR or VR headset, the systems integrator can see, based on dimensions and shapes the software recognises, the ideal gasket, fastener or cabling running or mounting solution to put in each place,” Costella added.
“The software enables a technician to perform real-time quality checks, helping to ensure they are grabbing the correct component, that they have the right size, that they’re putting it in the right place and at an accurate angle, and similar properties. It can thereby help correct errors by a maintenance technician or help train new ones who haven’t worked on a given UAV before.”
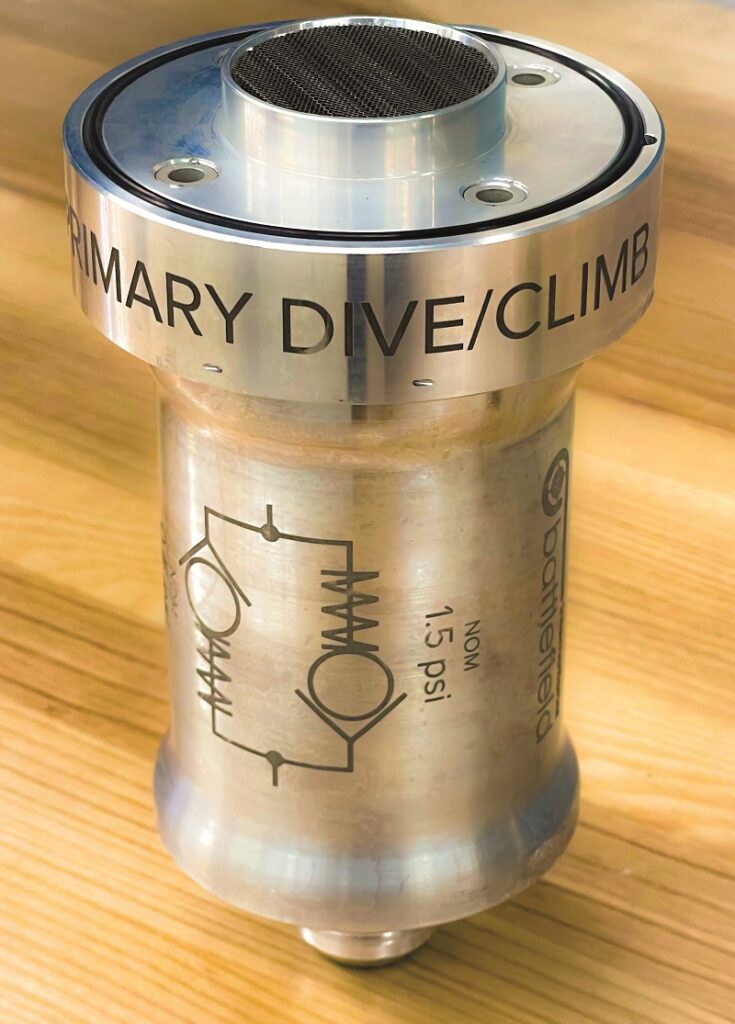
Battlefield International debuted a new fuel valve designed for small-to-medium-sized UAVs, called the Climb/Dive. It has been designed to help equalise the outer and inner pressures of UAVs’ fuel tanks, particularly during climbing and diving manoeuvres.
“The reason it can do this is because it’s designed with two independent internal flow passages, and each path can be set to a specified, independent cracking pressure. We can therefore set the outflow of the tank to one cracking pressure, and the inlet flow to another, with the internal flow passage design optimised using software code in Ansys,” said Fadi Mishriky.
“When a UAV climbs, the ambient pressure outside the tank becomes lower than the pressure inside, and when you’re consuming fuel, the tank is subjected to lower pressure than ambient.
“During descent or diving, the tank’s pressure stays constant but the outside pressure goes up. This valve essentially permits air to flow back and forth between the tank and the outlet, allowing the pressure to equalise and prevent the tank from damage through implosion or explosion.”
The Climb/Dive is also plated with a special conductive coating that discharges any static charges on the assembly.
The company also displayed its Siphon QD, which has been designed as a dripless quick-disconnect solution for completely draining a fuel tank within a few seconds, and for preventing ingress of air during connecting and disconnecting.
“As the Siphon QD will probably be bonded to carbon fibre, we apply a special phosphoric coating that ensures a safe, rigid and reliable connection,” Mishriky said. “It’s also designed to be fully flush, with a cap, so that it won’t alter the aerodynamic profile of a UAV after being integrated, and we can scale it from a Dash 2 size up to a Dash 40 [sizings for fuel lines according to the JIC/AN measurement system].”
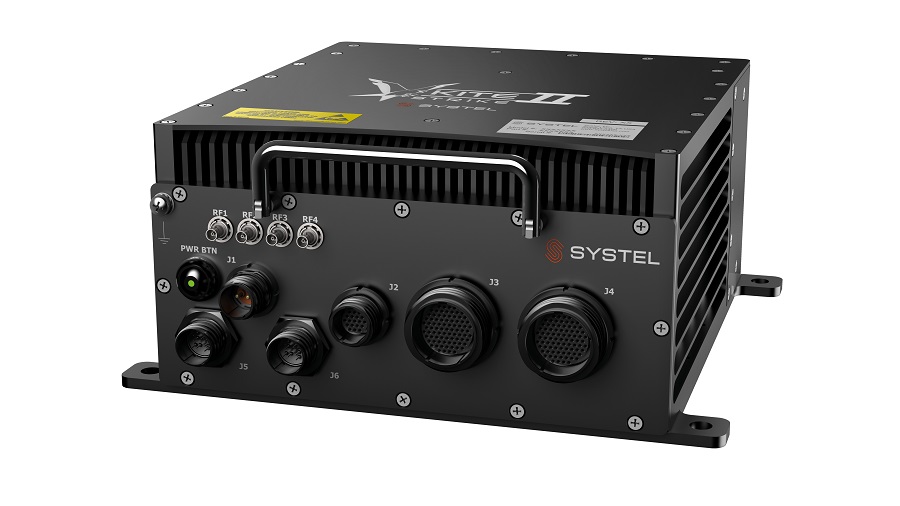
Systel showcased its Kite-Strike II embedded computer system, its latest solution built around the Nvidia Jetson AGX Orin (both the 32 and 64 Gbyte versions) and ruggedised to military standards including Mil-Std-810H, 461G for EMI protection, and 1275E/704F for uninterrupted power.
“It’s designed as a modular platform, to tailor it for customer needs such as software-defined radios or capture cards, and to future-proof it in terms of replacing future generations of computer hardware while keeping the same architecture,” said Brian Russell.
“There are severe trade-offs and challenges with building rugged systems like this, such as removing and dissipating heat from powerful boards like the Orin while still making the housing rugged enough to keep shocks and vibrations away from the board. It’s hard sometimes for uncrewed vehicle OEMs to have the time and tools to manage those in-house, especially when designing a UAV presents so many other challenges, so ruggedised computer enclosures often end up as an afterthought.”
The Kite-Strike II measures 21.5 x 20 x 10.7 cm and is IP66-rated, with integrated cooling fans that blow over an internal heat sink. With the Orin, it integrates a GPU with up to 2048 CUDA cores and 64 Tensor cores, a CPU with up to 12 Carmel ARM v8 cores and a maximum frequency of 2.2 GHz, and up to 64 Gbytes of onboard memory, as well as a 64 Gbyte eMMC 5.1 storage system.
Also, in October, Systel introduced its Sparrow-Strike, which integrates an Nvidia Orin NX and is entirely passively cooled. “It’s designed to be our ultra-small form-factor rugged computer offering, weighing about 3 lb [1.36 kg], but with its Orin NX it’s still powerful enough to provide edge AI processing,” Russell said.
“We’ve also designed the Sparrow-Strike to integrate smaller, single-board computers such as the Intel Atom or SMARC boards, for users who want the Sparrow-Strike’s form factor and ruggedisation but want to integrate it as something like a flight controller instead of an edge AI solution.”
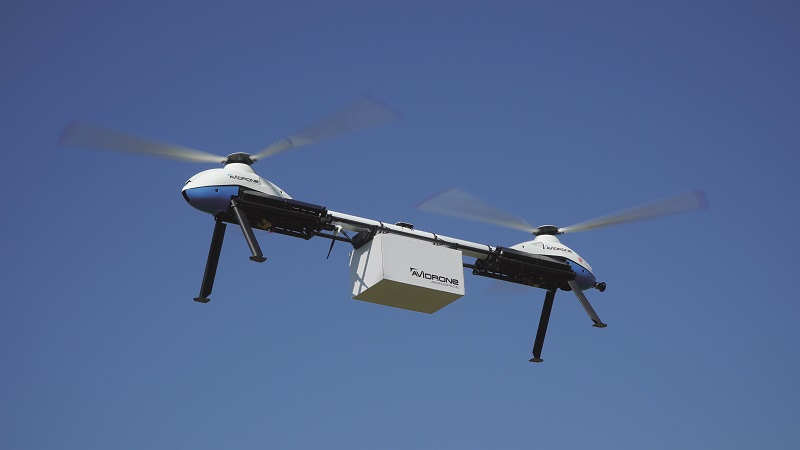
Avidrone displayed its flagship 210TL UAV, which it manufactures and supplies to users across defence and industry. The system is designed as a tandem rotor helicopter, a configuration often associated with the US Army’s Chinook helicopter.
“It’s a fully electric dual rotorcraft, and a lot of our projects are all about carrying cargo, particularly fully autonomous deliveries of cargo with no pilot in the loop or FPV camera requirement,” said Scott Gray.
“We write all the software, assemble the hardware, and construct the aircraft in-house as a turnkey system. We designed the airframe from a blank sheet, because there was no-one on the market that could feasibly supply us with a tandem rotor airframe, and we wanted to optimise and exploit the high-speed and heavy-lift capabilities that we know the Chinook is capable of, but in a smaller package.”
The company’s proprietary Avidrone G4 autopilot has similarly been produced from a blank sheet, owing to the rarity with which flight software and controllers suited to the particular control regimes and dynamics of tandem rotor helicopters are supplied. These circumstances also apply to GCSs; as such, no third-party software or hardware products are installed in the 210TL.
“Having a closed system like this is useful for defence users to ensure security, and on top of that all the UAV’s protocols are encrypted,” Gray said.
The 210TL has a MTOW of 38 kg, with around 16 kg of payload capacity that can be configured with various battery sets. In this typical weight allocation, and assuming a cruising airspeed of 80 kph, the aircraft has an endurance of slightly longer than 30 minutes. Its top speed is 100 kph, and its maximum range if the battery weight is maximised is 100 km.
The company is also working on a much larger version of the 210TL, to be named the 740T, which will weigh 600 kg and have a 225 kg cargo payload capacity. It will be powered by a gas turbine engine, and its official unveiling is set for 2025.
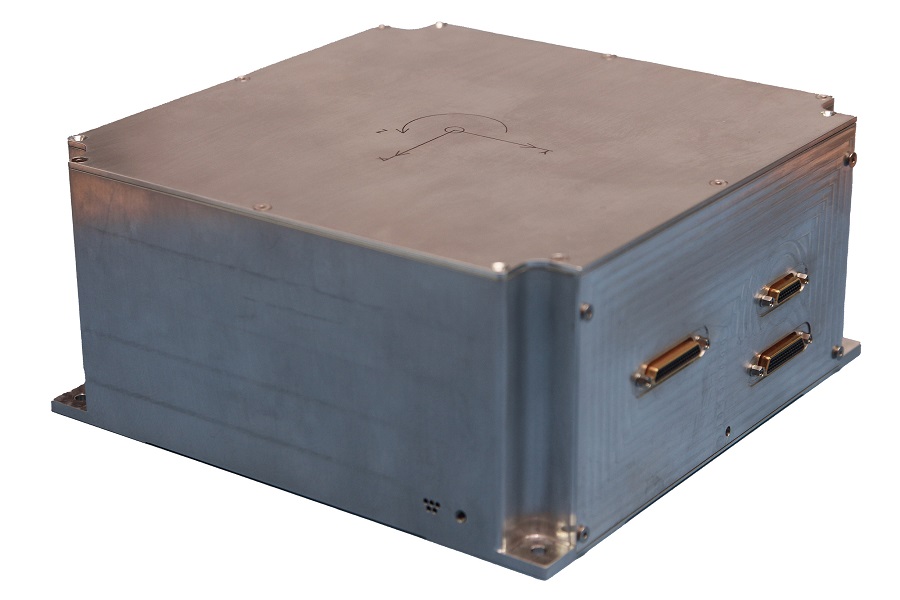
Innalabs attended the exhibition to show and discuss its inertial sensing devices, which have been used in various space and defence vehicles.
“Our Arietis is a radiation-hardened gyroscope that was developed under an ESA-funded programme, but we’ve matured it further for the new space market, including creating a radiation-tolerant version that costs much less,” said Ian Robinson.
“Our gyros are currently installed in at least 40 satellites, including one from the European Space Agency, and they have racked up over 3 million flight hours.”
The gyroscopes are based on coriolis vibratory elements, cylindrical metal resonator devices that piezoelectrically detect vibrations derived from angular motion. They can also detect True North, owing to their low drift (in degrees per hour) over their lifetimes.
“We can supply individual gyros or integrate them as triple-axis solutions with an FPGA to process the raw data into actionable inertial measurements,” Robinson said.
The company also produces quartz-based accelerometers with measurement ranges of 60 g and one-year repeatability within 600 ppm for UAVs, as well as land and marine navigation and optical systems.
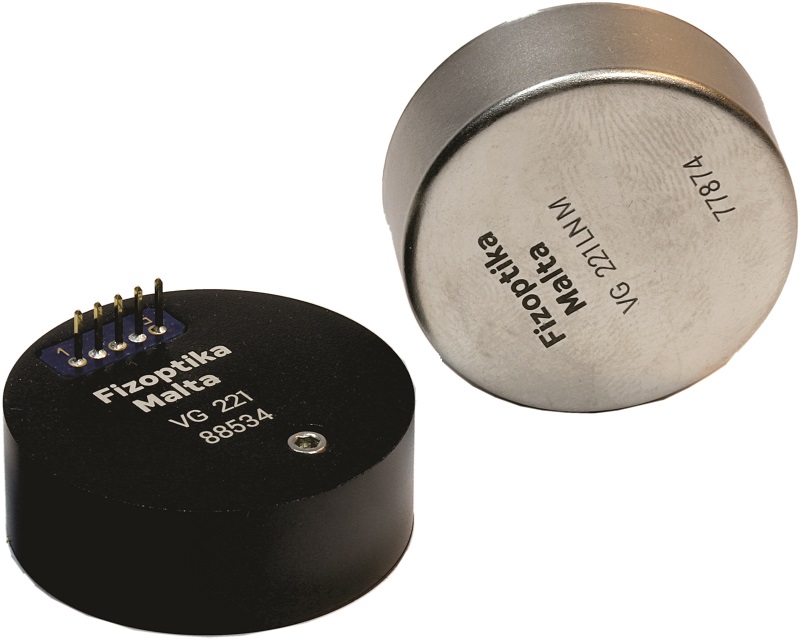
Fizoptika Malta showcased its new VG220 series of fibre optic gyroscopes (FOGs), which come in two versions – the VG221, offered as a lower-power device; and a lower-noise version, the VG221LN.
The VG221 consumes 0.3 W in typical operations and has 0.05o/√hour of angular random walk as well as an MTBF of 150,000 hours. The VG221LN requires 0.5 W to operate, although its angular random walk is lower, at 0.025o/√hour, albeit with a lower MTBF.
“Both can come in either aluminium or µ-metal housings, the latter providing lower magnetic sensitivity,” said Arthur Tua.
The VG220s weigh 15 g in their aluminium enclosures and 25 g in μ-metal. The latter housing however reduces bias from 3o/hour to 1o/hour and has a magnetic response from 4o/hour/Gauss to 0.1o/hour/Gauss.
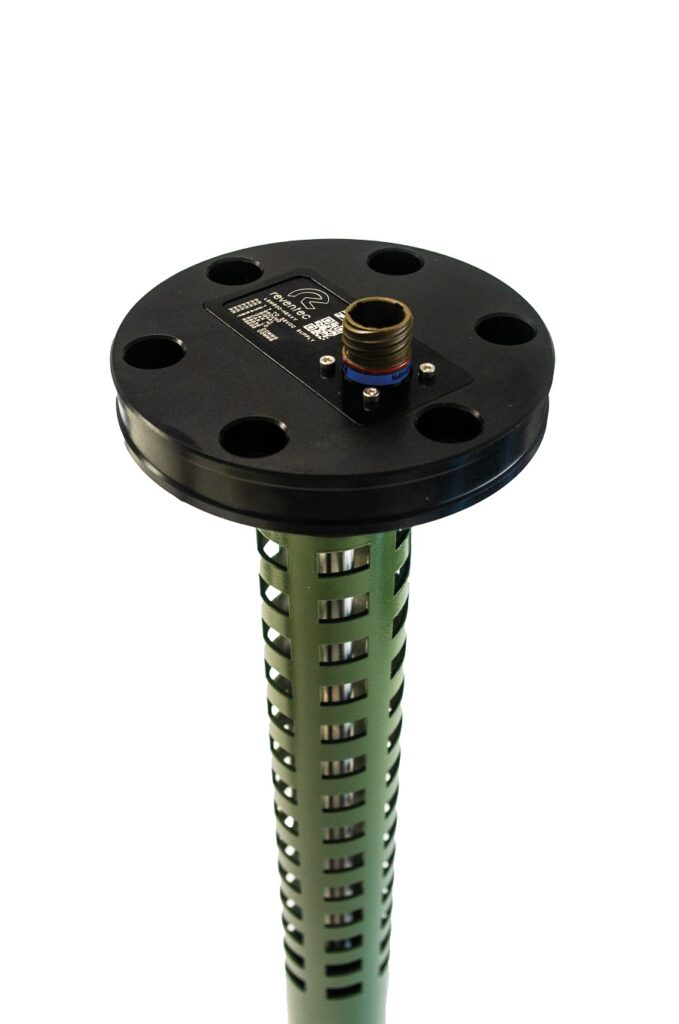
Reventec spoke with us about its newest fuel and oil-level sensors, which it showcased at DSEI with defence and security integrators in mind.
The first was the LSM600-Heavy, which is ruggedised and comes in a contoured version to integrate into tanks with angled top plates – a way of increasing volume in the tank while maintaining access to the plate and insulation.
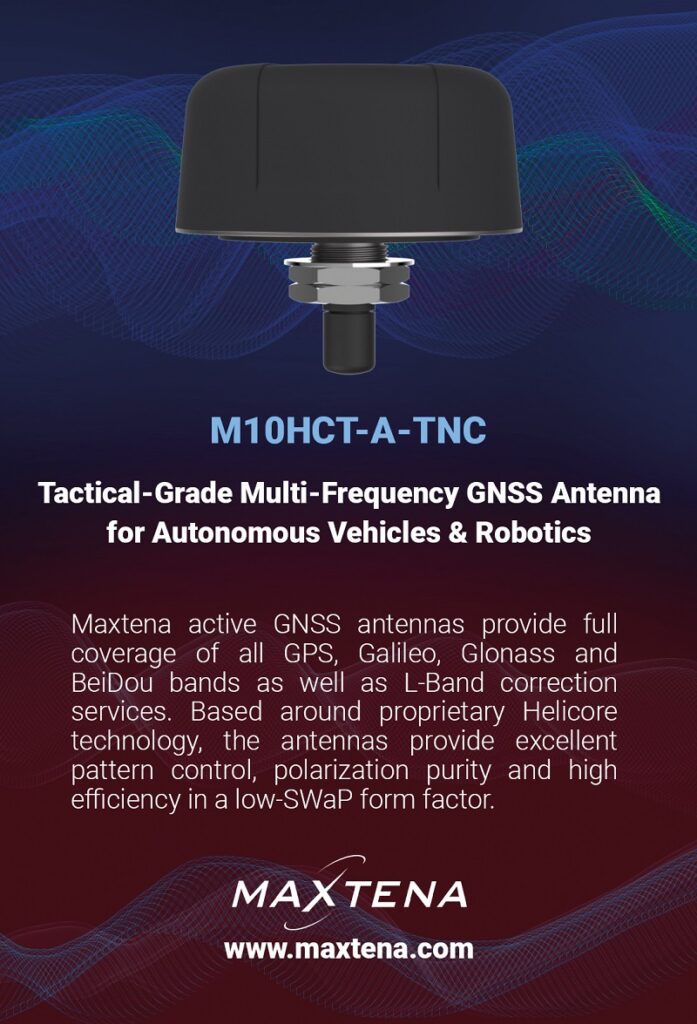
“These are variations on the standardised capacitive level sensors we’ve supplied to motorsport for years, but they’ve been ruggedised for military environments, to make them more heavy-duty for UGVs in particular,” said Jack Birmingham.
The LSM600-Heavy measures fluid levels accurate to ±0.5% and can be manufactured from stainless steel with IP69K-rated protection, to enable for instance jet-washing or steam-cleaning, or salt water protection with 316 stainless steel. Hard-anodised aluminium is also available.
Reventec also showed us its LSM100-Micro, which is designed to be the company’s lightest level sensor yet, to meet the UAV market’s (and similar) requirements on weight reduction. To achieve this, lighter construction materials and components have been implemented. The exact weight will depend on the fuel tank and UAV integration case, but the company estimates it is 30% lighter than its next-lightest product.
“All our electronics have been rated to EMC standards under Mil-Std 461F; we’re also getting a lot of interest in retrofitting discontinued fuel level sensors thanks to our ability to customise new units to fit into existing platforms and footprints,” Birmingham added.
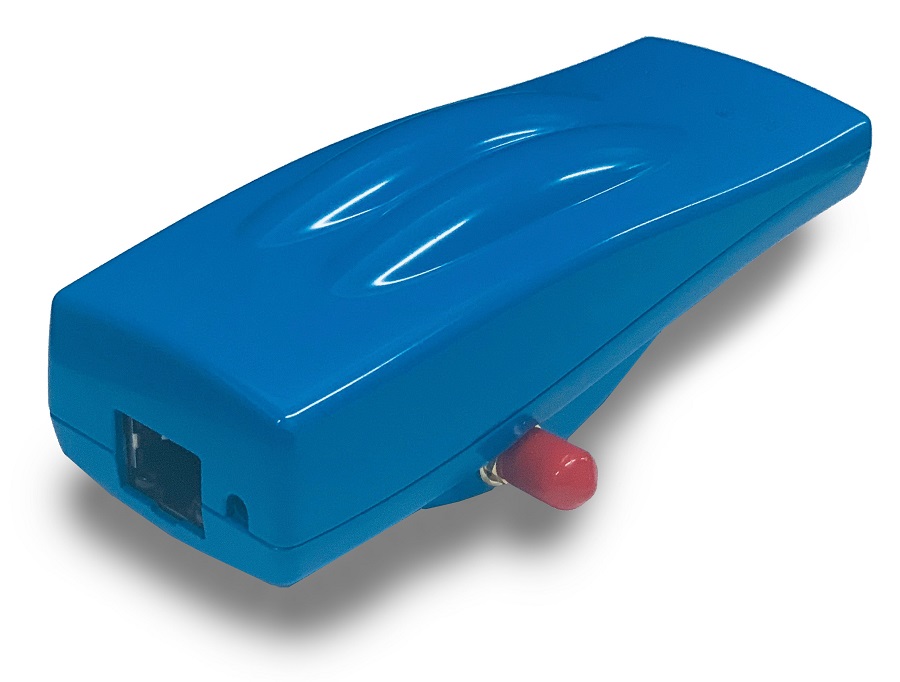
Rajant showcased its Peregrine series of BreadCrumbs, which it offers as quad transceiver, industrial-grade mesh platforms with a 2 x 2 MIMO interface and compatibility with 2.4 or 5 GHz among other frequencies, across military, licenced, public service and proprietary bands.
“Peregrine units have been used in oil facilities, ports, military fixed sites, mines and other locations where persistent actionable information is needed in real time but where point-to-point communication is challenging, so they can create effective LOS connectivity from uncrewed vehicle to soldier, to command post,” Robert Castillo said.
The Peregrine can achieve data rates of up to 2.3 Gbit/s over its four transceivers, each of which is capable individually of up to 866.7 Mbit/s and consumes 10 W in standard operations, up to a maximum of 34 W over a 48 V input. The system weighs 2946 g, measures 265 x 254 x 46 mm and is designed with an enclosure rated to IP67 protection, as well as USB and Ethernet connectivity.
Rajant also discussed its DX2, a 123g radio that consumes 2.8 W in normal operations and has a maximum data rate of 300 Mbit/s. It is designed as a smaller, single-channel system for UAVs with tighter SWaP budgets, which nonetheless might see use in mesh networks.
Maxtena disclosed its development of the M10HCT-TNC helical antenna, which is designed as a tactical-grade GNSS antenna for L1, L2 and L5 navigation satellite constellations. It is aimed at high-precision and multi-frequency autonomous operations, and is powered by the company’s patented HeliCore technology.
The solution is ground-plane independent and has been optimised for low power consumption and minimal phase-centre variation over azimuth, as well as a minimised axial ratio for mitigating multi-path errors. Several filtering groups power the M10HCT-TNC’s filtering capabilities and RF anti-jamming mitigation capabilities.
The system receives navigation signals over the 1164-1300 MHz and 1539- 1610 MHz bands, and is rated to Mil-Std-810G for shock and vibration tolerance.
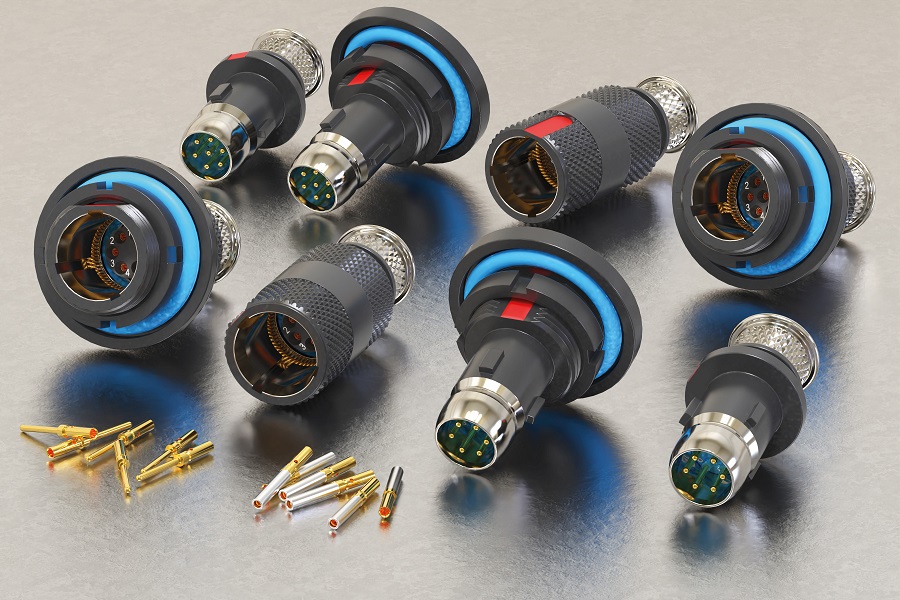
Omnetics exhibited its new Kilo 360 Warrior series of connectors designed to meet the new Nett Warrior connectivity standard. Although the Nett Warrior programme has stalled for the time being, Omnetics’ r&d is complete and the company is now supplying the new connectors for any users with authorisation (at the time of writing, the US Army’s authorisation was pending).
“The connectors have the EMI rating and specific plating conforming to the Nett Warrior standard. It will withstand 500 hours of salt spray, and we’ve tested its survivability by mating and de-mating it 2000 times without issue,” said Scott Unzen.
As well as being fully inter-mateable with any other connectors from approved vendors designing systems to the Nett Warrior standard, it is also compatible with NATO Stanag 4695 systems.
The Kilo 360s are designed with 5 A receptacles (with at least six per connector housing), making them suitable for high-current soldier-worn battery chargers, radios and equipment such as GCSs.
They are typically manufactured with a shell made from aluminium alloy with ZNU (black zinc over electroless nickel), while its contacts are produced in gold-plated copper alloy. They also come with a rigid dielectric insulator and fluorosilicone O-rings for sealing.
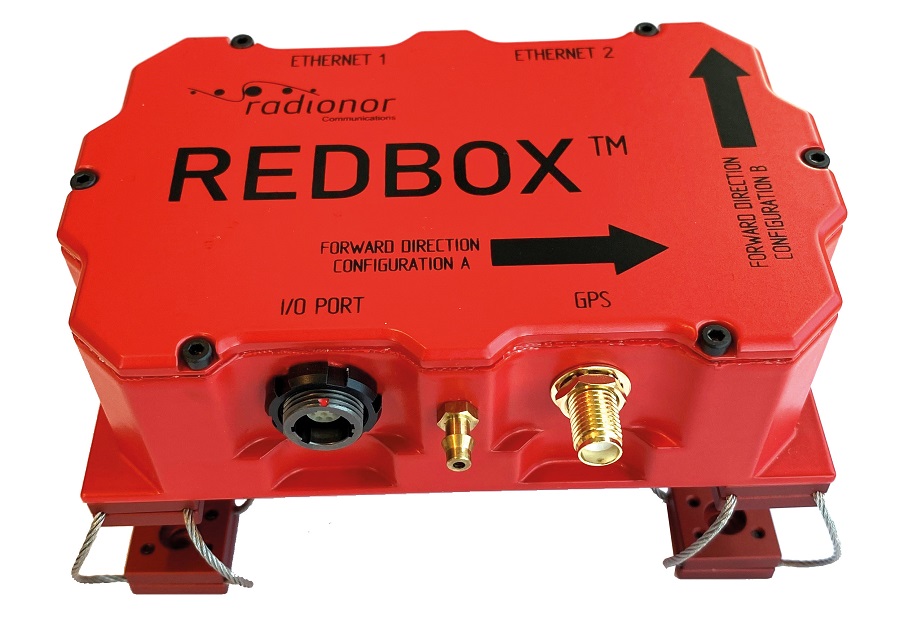
Radionor Communications launched its RedBox solution at the show, which has been created to enable GNSS-denied navigation and to integrate as an accessory to its Radionor product family.
“The RedBox enables relative positioning through our phased array antenna technology, enabling a means of navigation independent of GNSS signals, and one resistant to jamming given that our data links are difficult to jam,” explained Raymond Soderholm.
Positioning through the RedBox works in a similar principle to GNSS, in that the device extracts angular and distance information using the signals coming from the phased array antennas within comms range but using the relatively higher power and narrower beams (compared with satellite signals) of Radionor’s data links. This means that with the Radionor equipment it is possible to operate without GNSS.
The RedBox is scalable, with location update rates exceeding 1000 per second. The largest version weighs 300 g, and is aimed at bigger UAVs typically integrating Radionor’s CRE2-179-UAV radio antenna, while the smallest one is for very small UAVs, and weighs around 130 g.
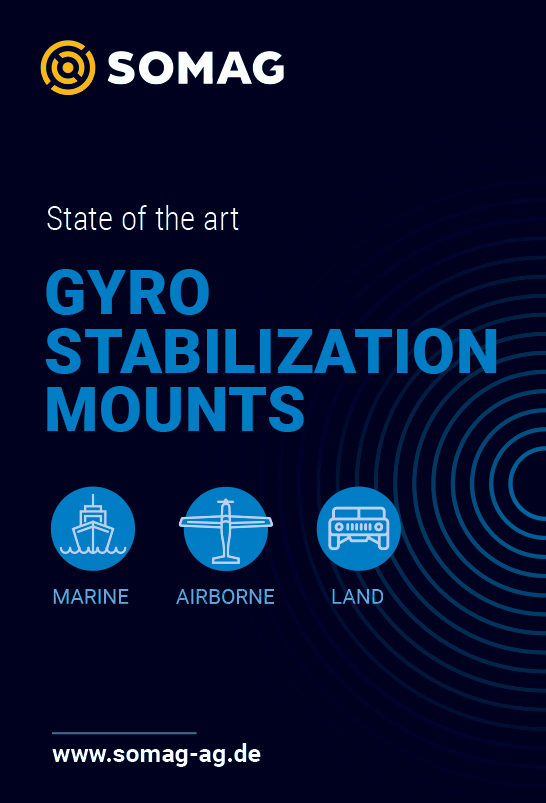
In its 300 g configuration, the RedBox consumes 8 W over a 9-36 V connection, and measures 122 x 83 x 58 mm (104 x 65 x 30 mm if its dampers are not counted). It features two 10/100Base-T Ethernet interfaces as well as a single RS-232 connection, and can function in temperatures from -60 to +50 oC. Its estimated effective range is at least 300 km, and its links are encrypted to AES-256 at the hardware level.
UXV Technologies told us about a series of quality improvements it has made to its G2Nav GCS, a containerised system with four detachable legs weighing 55 kg all-up, and measuring 121 x 42 x 32 cm.
“The physically largest of these changes is that the G2Nav’s power-on switch used to be covered with a red toggle, but through real-world use we’ve learned that the toggle can be accidentally flipped to the ‘off’ position, so we’ve changed it to a key-based rotary switch to stop that happening,” explained Filip Karandysovsky.
“We’re also now integrating our SRM [swappable radio module] interface into custom versions of the G2Nav, in order to offer customers the ability to select whichever radios and suppliers they want through a more radio-agnostic GCS, and to swap them in the field seamlessly and without using tools.”
The G2Nav features two 1920 x 1080, 21.5 in-diameter screens and resistive touch interfaces, as well as physical interfacing controls including a keyboard, a numpad for entering numbers, a mouse trackpad or trackball, and numerous switches, toggles, push-buttons and a joystick.
UXV Technologies is also continuing to optimise its Optroxa GMB 600. This EO/IR camera gimbal is currently in its fifth version, with a sixth on the way.
“The sixth version will integrate a laser rangefinder and active cooling, and will maintain continuous rotation in both pan and tilt axes,” Karandysovsky said. “We’re also offering an open API for configuring different software features for the gimbal, such as active stabilisation, moving target detection and tracking, and electronic boresight alignment.”
At the time of writing, the Optroxa was a 600 g gimbal, measuring 125 x 98 x 83 mm integrating a 1.6 MP Sony IMX 296C camera, as well as a Teledyne FLIR Boson. Karandysovsky added however that version 6 will be far smaller than version 5.
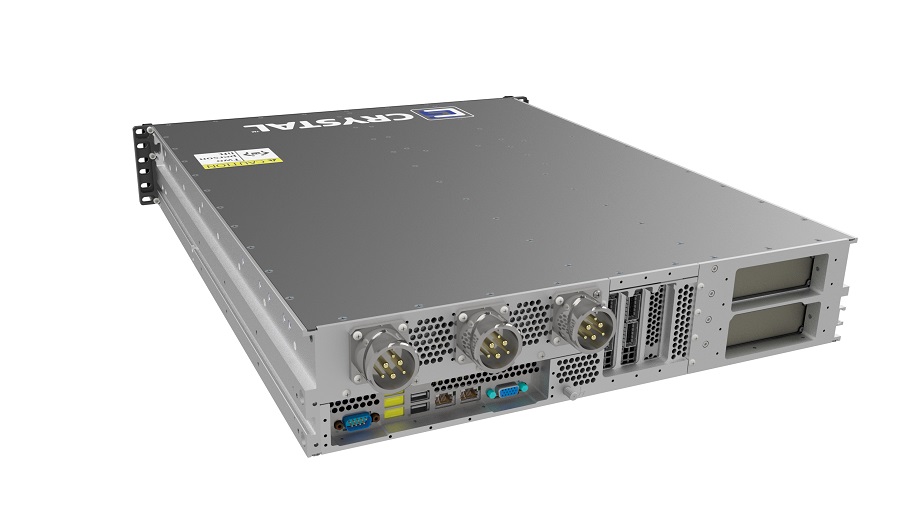
Crystal Group showcased its RS2704L22, a 2U, ruggedised, Mil-Spec computer server designed for edge AI applications such as battlespace management or intelligence gathering.
“The server has a DC power supply and an X13 motherboard with dual Sapphire Rapids CPUs, as well as up to 30 Tbytes of removable hard drives,” said Greg Johnson.
The company added that reliable edge computing hardware requires higher power as well as a smaller chassis relative to present standard 2U computers, key factors that fed into how the RS2704L22 was designed.
“The RS2704L22 also has two A100s in the standard design, which are some of the most powerful GPUs on the market; they are ideal for efficient, real-time data-crunching,” Johnson noted.
“This system is designed around optimised data processing speed, and to either read and write to self-encrypting NVME drives, or move the data to other elements on the platform using two 100 Gigabit Ethernet ports in real time.”
Although the system originated from a request to replace an end-user’s 4U rugged server, Crystal Group decided during the development process to engineer an existing solution’s features into a 2U system weighing 14.5 kg.
Johnson added, “The primary challenge for designing this server was sufficient cooling, particularly given the low air densities at higher altitudes. The engineering process required lots of CFD modelling and testing to make sure we had not just met the thermal management requirements, but also that the MTBF for all our components met the customer’s needs.”
Domo Tactical Communications (DTC) displayed its newest software-defined IP mesh radio modules and associated applications, including an integration into a gantry-mounted EO/IR camera head on a pan/tilt/zoom base.
Such systems are typically cabled solutions, and are aimed at extending their range and usefulness as LOS remote surveillance devices for protecting UAV operators and forward operating bases. DTC’s configuration includes an IP camera encoder for streaming EO/IR data over a mesh link to whichever operator wants it.
“Underpinning our radio technology is our MeshUltra waveform, which is our own so it’s not based on wi-fi or similar, and has its own built-in error correction systems as well as a media access algorithm for controlling who can transmit and when,” said Sam Medler.
“The algorithm is token-based: the ‘token’ is a kind of software identifier that’s passed around so that each radio can transmit in a defined sequence based on their node IDs.
“It allows each radio to track the others’ transmission quality and packet sizes, and the sequence in which it’s passed around can change dynamically as the network evolves, overcoming the cross-talk problems that can result with, say, CSMA-based networks, and improving latencies,” he added.
One solution integrated one of the company’s BlueSDR-30 radios, which weighs 461 g in plain boxed form (110 g in OEM configuration) and consumes up to 7 W in typical mesh operations, transmitting at up to 1 W maximum power per output (for 2 W in total).
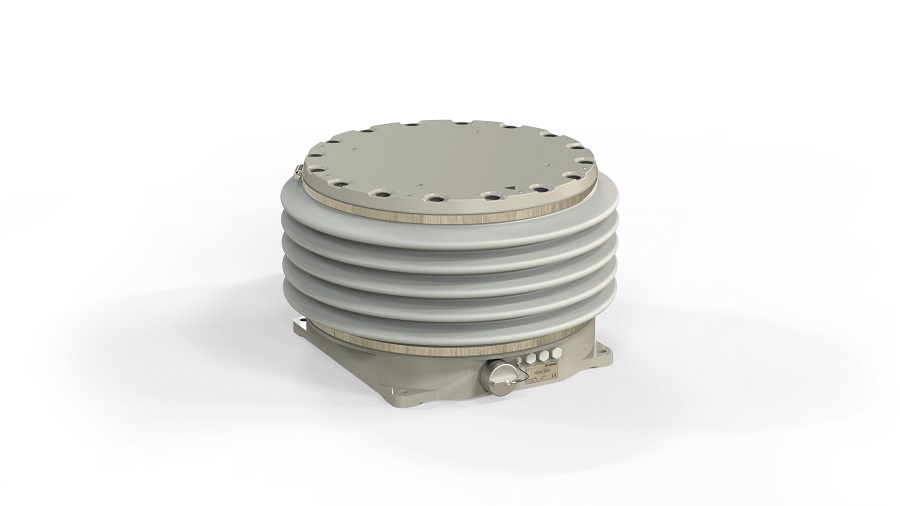
SOMAG had active displays of two of its gyro-stabilised mount systems, which can be integrated into USVs and UGVs to help balance payload sensors.
“You can install any kind of sensor – a camera, radar or Lidar, say – and the mount systems, which are made for harsh environments such as sea states up to 7, can mechanically compensate for lateral motions; they are also IP67-rated for use offshore,” said Soren Lieske.
“Our mechanical compensation for high payload weights is based on hydraulic circuits, which lends them to much more powerful motion and lifting than electromechanical systems used on our small stabilisation platforms.”
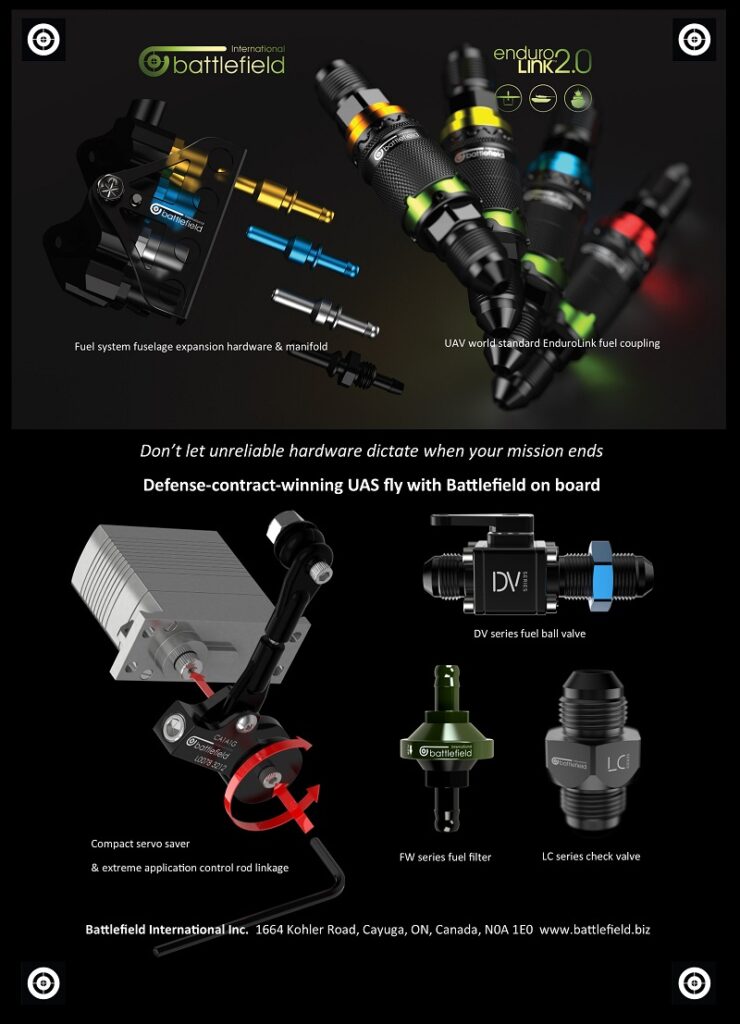
The company’s biggest mount, the OSM 5000, can lift up to 300 kg; its smallest, the RSM 50, is configured for up to 40 kg, although the geometry and CoG of the payload will influence its exact capabilities. At the time of writing, SOMAG’s platforms were being designed to compensate for motion in the pan and tilt axes, but the company is also working on a version with additional yaw compensation.
“We also have models for helicopters and UAVs acquiring survey data,” Lieske added. “Our airborne mounts stabilise in all three axes, and a passive vibration isolation ring is integrated on top, which we design to mitigate specific vibrational frequencies that the end-user is concerned about, and which are adapted to a specific weight of the sensor application.”
Subdron spoke with us about its V Dron UUV, a 52 kg vessel measuring 1.6 m in length and 0.23 m in diameter. It is electrically powered to achieve speeds of up to 3 knots and endurances of up to 10 hours.
“We built the vessel for performing underwater inspections of ships’ hulls, port structures and offshore structures,” said Marie Weiss.
“In addition, we’ve also developed our proprietary Relative Object Navigation [RON] software, for autonomous underwater navigation as well as close following of objects of interest.”
The RON software is hence designed to ensure that the V Dron not only closely measures the surfaces of structures, it also maintains a consistent distance and orientation from them. As a result, the 3D point clouds generated from the sonar surveys achieve a consistent resolution across every square metre of the resulting model.
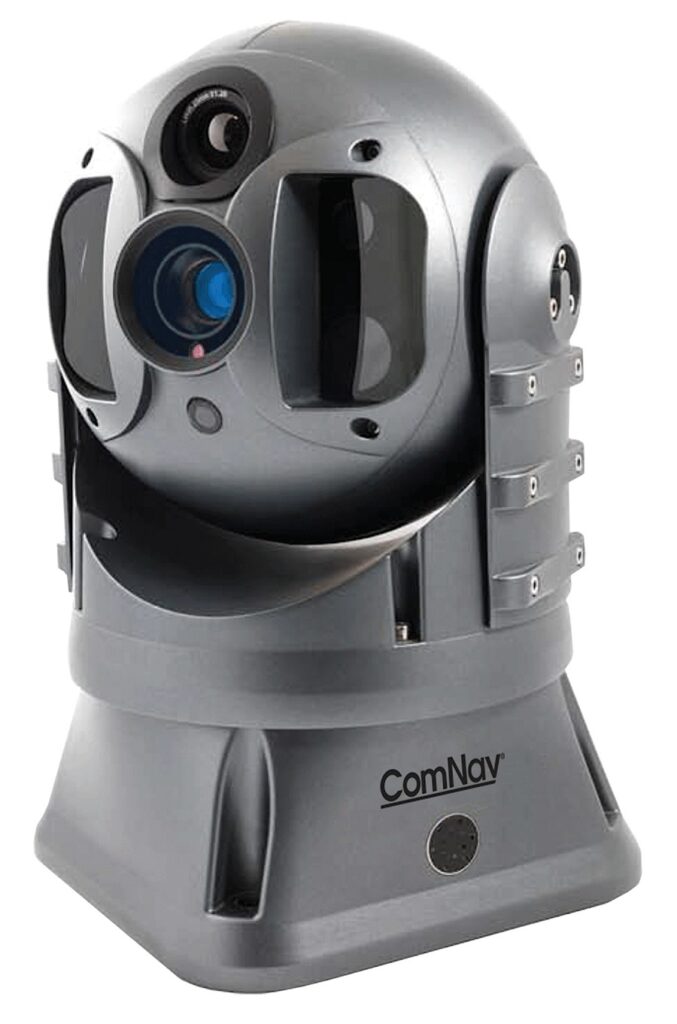
ComNav Marine attended the event to display a range of precision marine electronics systems for integration into USVs.
Among these were its G2, G2B, G3 and G7 GNSS systems, which are designed for integrating two antennas to support heading data outputs from 1 to 50 Hz. “They also come with software algorithms to minimise drop-outs and enable fast re-acquisitions after loss of satellite signal, tracking multi-frequency multi-constellations simultaneously across GPS, GLONASS, Galileo and BeiDou,” said Satish Narayan.
The G2, G2B and G3 are IMO-compliant and type-approved for precise heading, positioning, heave, pitch, roll and rate of turn. The GNSS is aided through an inertial sensor to provide enhanced roll, tilt and heading stability, as well as aiding during any momentary losses of satellite signal. The G7 provides precision GNSS of up to 1 cm position, and 0.01o heading.
The company also showcased its V7 gyro-stabilised EO/IR gimbal. Its night vision thermal camera is an LWIR system powered by a 640 x 512 silicon CMOS detector; the camera produces full-frame rate video output to 50 Hz with a 26 x 20o FoV.
Its colour camera has a 30 x 30° FoV, 1080p resolution and comes with a 40x optical zoom lens, as well as a 120x digital zoom. The system integrates a light intensifier with a spectral range of 200-900 mm and a wireless remote control IP capability.
UPCOMING EVENTS
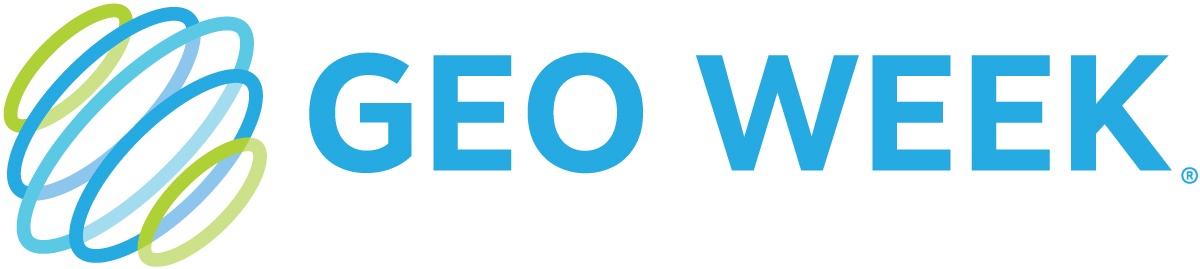
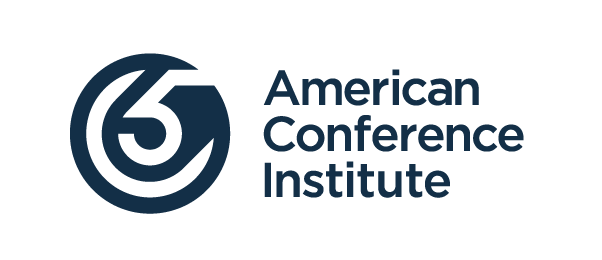
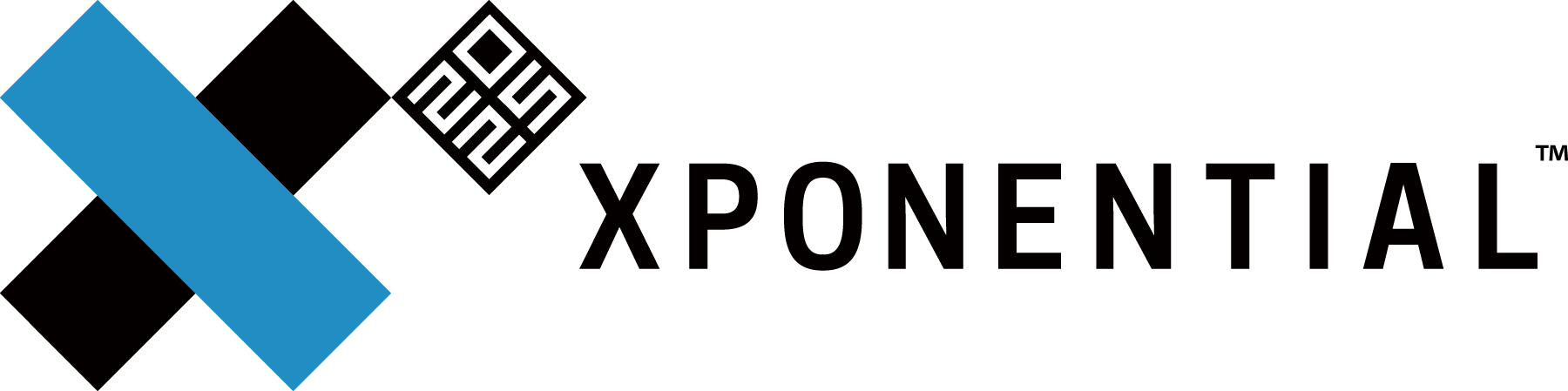
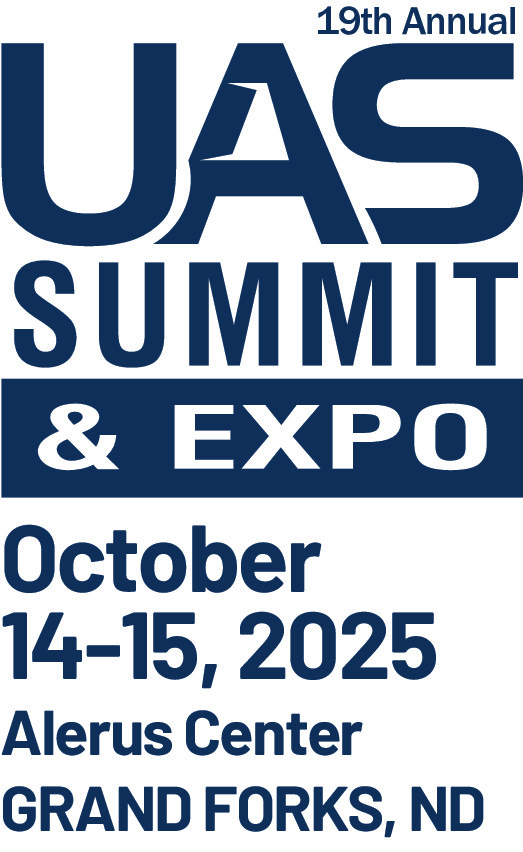
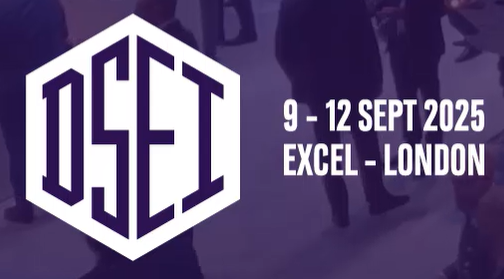
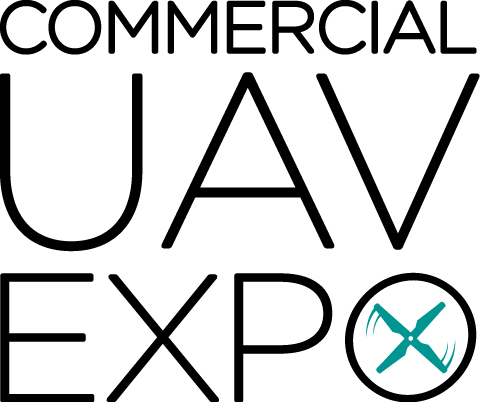
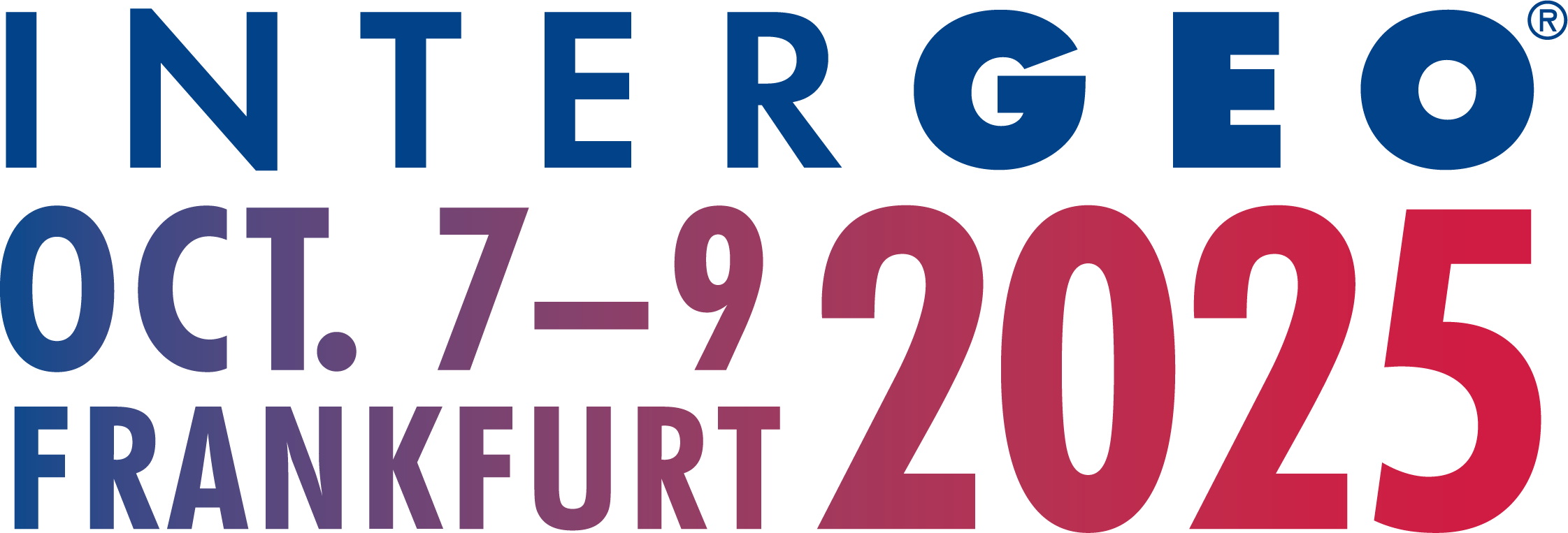
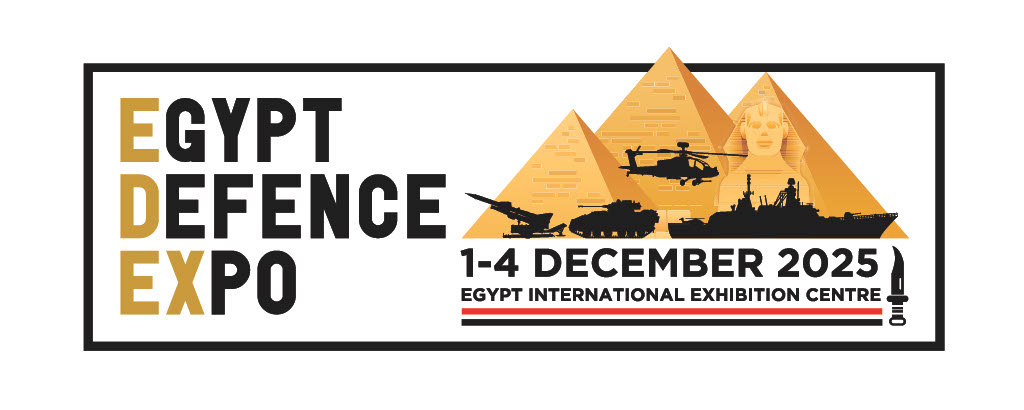
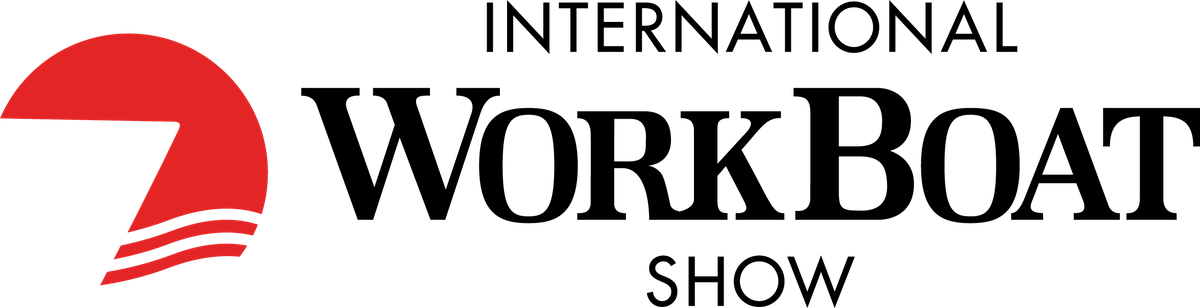
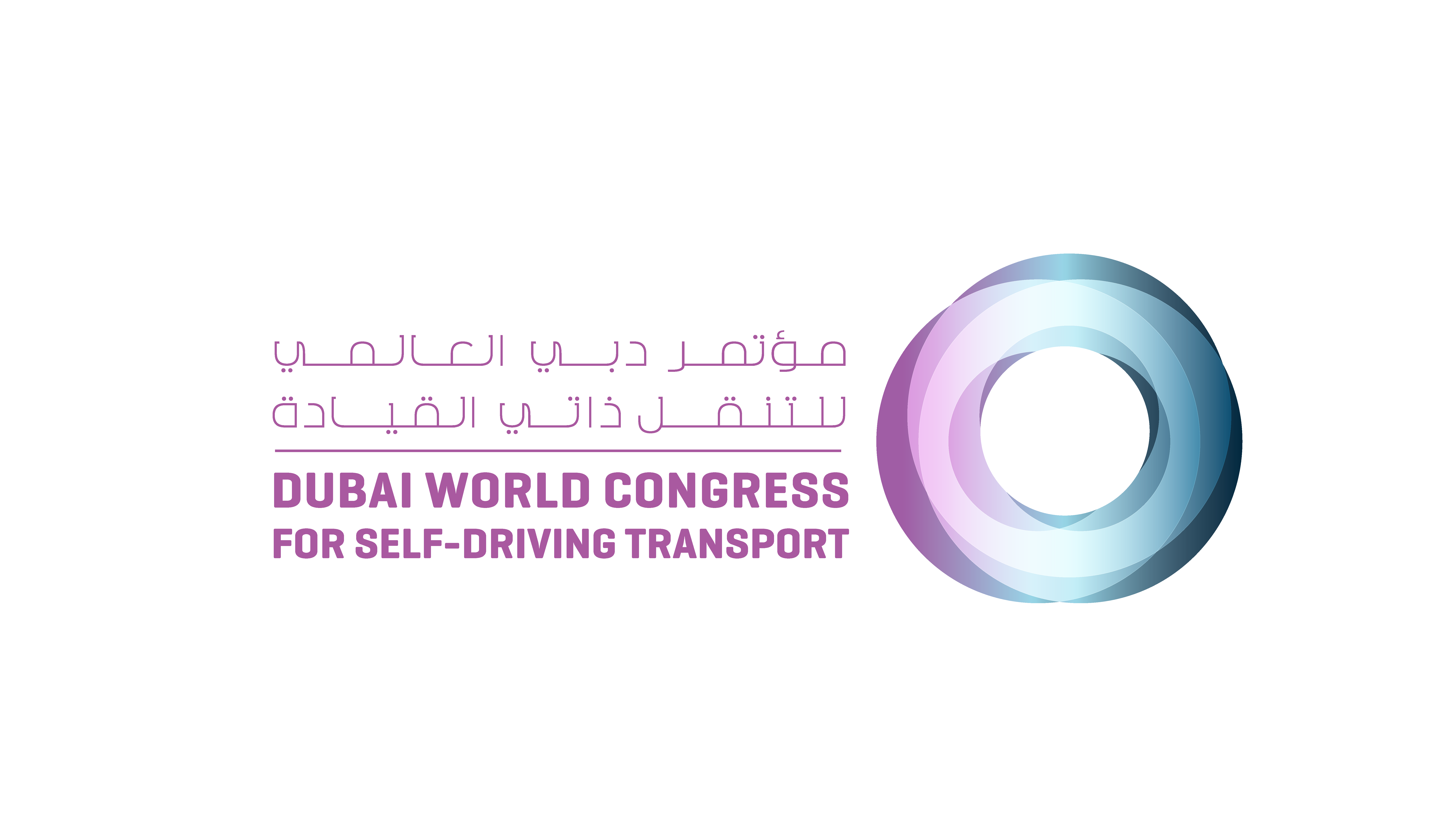
