Accession Class USV
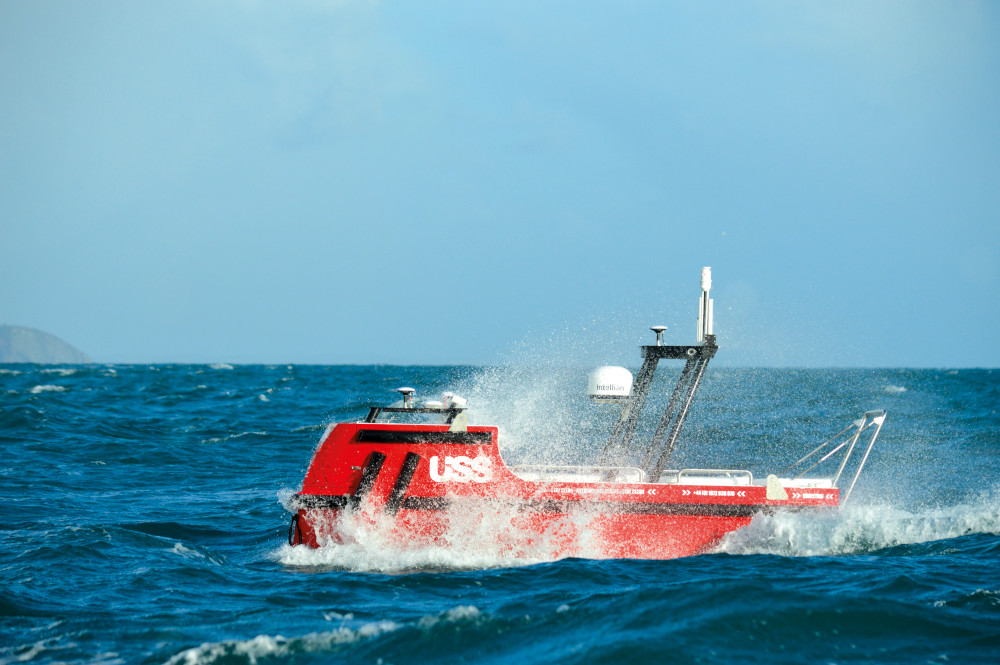
(Courtesy of USS)
Multiple choice
Whether it’s Port Authority operations or offshore surveys, this modular USV can handle it. Peter Donaldson looks at its development
Adaptability through modularity was central to Unmanned Survey Solutions’ concept for its Accession Class USV. The craft can be operated in its 3.5 m-long base version, or extended to 4.25 or 5 m by inserting a modular hull section either 0.75 or 1.5 m long.
Equipped with combinations of extra payload and diesel fuel, these modules increase the USV’s endurance from 12 hours with a DC-only version at typical hydrographic survey speeds, to up to 20 days for a hybrid version.
All the hull sections are independently watertight, buoyant and fitted with bilge pumps. They are built from glass reinforced plastic, the structure consisting of resin-infused laminates forming two skins separated by a core.
We caught up with company director James Williams and his team at the Ocean Business 2022 show in mid- March, where they were demonstrating the pre-production vessel in its Accession 425 configuration with the 0.75 m central hull module.
The USV’s hull is designed to USS’ specifications by Jack Gifford Marine Design. “I’m not a naval architect, I’m a hydrographic surveyor, and I use that expertise to create a design brief for the architect,” Williams says. “The final design then goes to a professional boat builder, who builds the bare hulls. These then come to us, where we fit them out with everything from command & control systems to sensor payloads.”
The propulsion system is a series hybrid configuration, with a diesel generator to charge the lithium-ion battery pack and powering electric thrusters directly. There is also an onboard charger so that the boat can plug into shore power to top up the batteries when required.
Functional sections
The vessel is arranged in functional sections from bow to stern. The forward section has a detachable beak, behind which is a watertight hatch over the compartment housing the command & control systems, the power management system, the dual 4G modem and all the wifi equipment, with the batteries underneath.
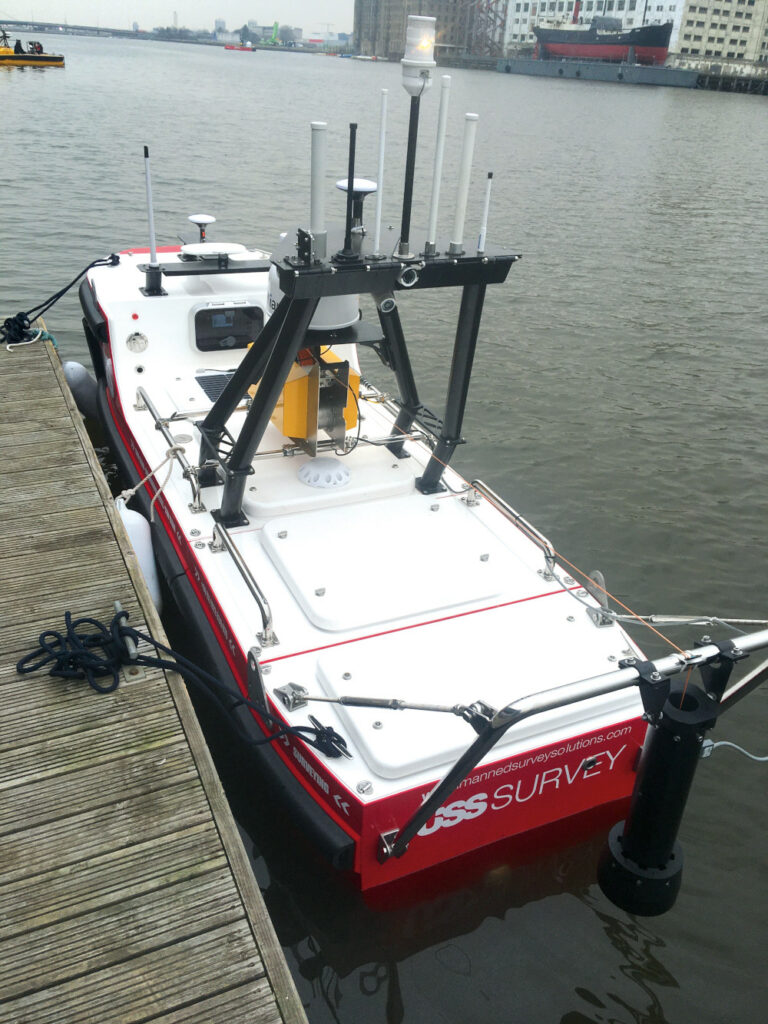
(Author’s photo)
A set of back-up batteries is kept charged by a solar panel for redundancy. Williams says, “In the event of losing primary power to the boat, we can establish contact through a separate Iridium installation and tell the boat to restart and boot up.”
The compartment containing this equipment is divided from the rest of the forward section by a vertical bulkhead, aft of which is the diesel generator and two hullskin fuel tanks that hold about 170 litres.
Aft of the 0.75 m hull module, which houses payload equipment, is the stern section that supports a pair of steerable DC electric thrusters, although there is no rudder. “We wanted both azimuth steering and variable thrust, so that if we lose one thruster we can still manoeuvre the boat,” Williams says. “We can turn one to the left and run it in reverse and the other to the right and run it forwards, so that the boat can do a 360º turn on the spot. She is highly manoeuvrable in close conditions.”
Good sea-keeping qualities are vital for survey vessels, a requirement that drove a couple of distinctive aspects of the hull design. “She has a reverse bow, so she is designed to cut through the tops of the waves instead of bouncing over them, which reduces the pitching motion, and she has four fixed stabilisation fins, which reduce roll motion by up to 40%,” Williams says.
The Accession, then, has the internal volume of a monohull available for payload or energy, but with stability closer to that of a catamaran.
The payload module in the centre of the Accession 425 shown at Ocean Business featured a multi-beam sonar from R2Sonic linked to an SBG Systems Navsight Ekinox INS and an onboard PC. The sonar’s ‘wet end’ acoustic head is in a flooded compartment at the bottom of the module, while all the electronics sit above it on a dry top with a watertight gland fitting for the cables.
The different centre module sizes provide more flexibility to tailor the boat to a given mission. “For the really long endurance missions we would put in a 1.5 m section with a 10 kVA generator and 300 litres of fuel, giving us a range of more than 1500 nautical miles at a speed of 4-5 knots,” Williams explains.
Swapping modules
USS has developed a means of swapping modules with the boat out of the water and supported by three trolleys, one for each section. Swapping them out involves going in through a deck hatch in the stern section, disconnecting it mechanically and electrically, and pulling it out of the way on its trolley. The process is repeated for the centre section so it can be exchanged for another.
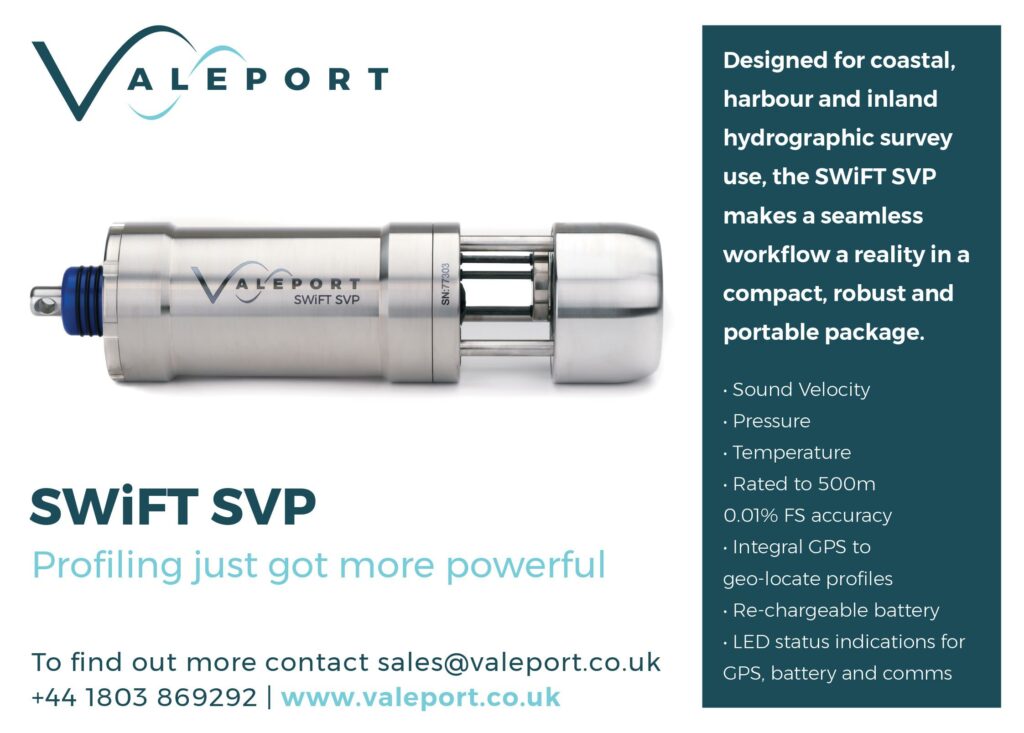
The power and signal harness includes jumper cables between the sections, providing quick connections for 48 V power through the boat and an Ethernet connection in every section that links to the comms router and the PLC that runs the power management system. “The whole power management and control system is set up so that you can plug in all the different components; the PLC recognises them and everything works,” Williams says.
Technical project manager Kevin Wittamore notes that USS can provide customers who want to install their own survey equipment with an empty hull section. “You don’t have to worry about comms or power, you just put your kit in and plug it into our systems,” he says.
The PLC monitors all the electrical loads, so it will report when a bilge pump is running, for example, and each compartment also contains a camera and LED strip lighting to provide the operator with visuals of what is happening. As with all the other loads, these can also be turned on and off remotely to minimise energy consumption.
Built-in redundancy
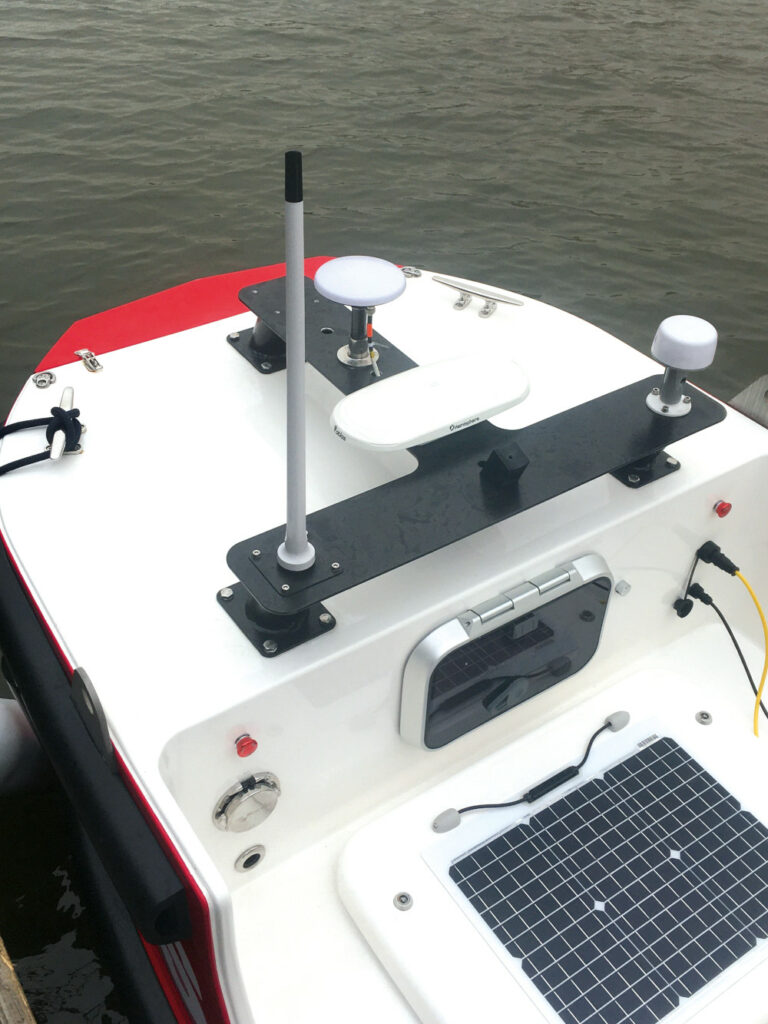
Much of the design effort that went into the boat’s power system was directed towards flexibility, redundancy and graceful degradation by minimising single points of failure.
“Everything has redundancy,” Wittamore says. “There are two power supplies, so if one goes offline the other can take up the load. If any single point fails you still have a fighting chance of keeping the boat fully operational. You can turn a lot of things off and it will still work.”
Inevitably that brings a degree of complexity to the overall power management system, which incorporates a control panel located behind a transparent hatch cover in the aft bulkhead on the forward superstructure. “You open that up and start it with a key, then the PLC powers up the boat’s systems in the correct order, interrogating the individual batteries to find their states of charge,” Williams explains.
In the original proof-of-concept boat, the power management system was built from discrete parts including off-the-shelf cables and switches, but the production ready system is a ground-up industrial design. “As well as the PLC it has resettable, controllable electronic circuit breakers, so if anything trips we know what tripped and why, and we have a chance to restart it,” Wittamore says.
This can also be done remotely, via satcom from the main operational control system or from an app on a smartphone if the USV is within wi-fi or cellular comms range. “I can log into the boat and, say, close the breakers associated with the generator, or shut down the entire stern section for safety reasons, if there’s somebody in the water nearby for example,” Wittamore says.
Comms and navigation
Visually prominent on the vessel are two ‘trees’, one forward and one aft, which are masts that support antennas for the comms and navigation suites. The rear tree folds down to reduce the overall height for transport and storage in a 20 ft container, while the top antennas pivot back to provide full access to all the connectors.
The largest antenna is the dome of the Intellian system that connects with the Iridium satellite network, whose services are provided through USS’ partner AST Global. Other bearers include dual wi-fi systems and 3/4/5G cellular comms.
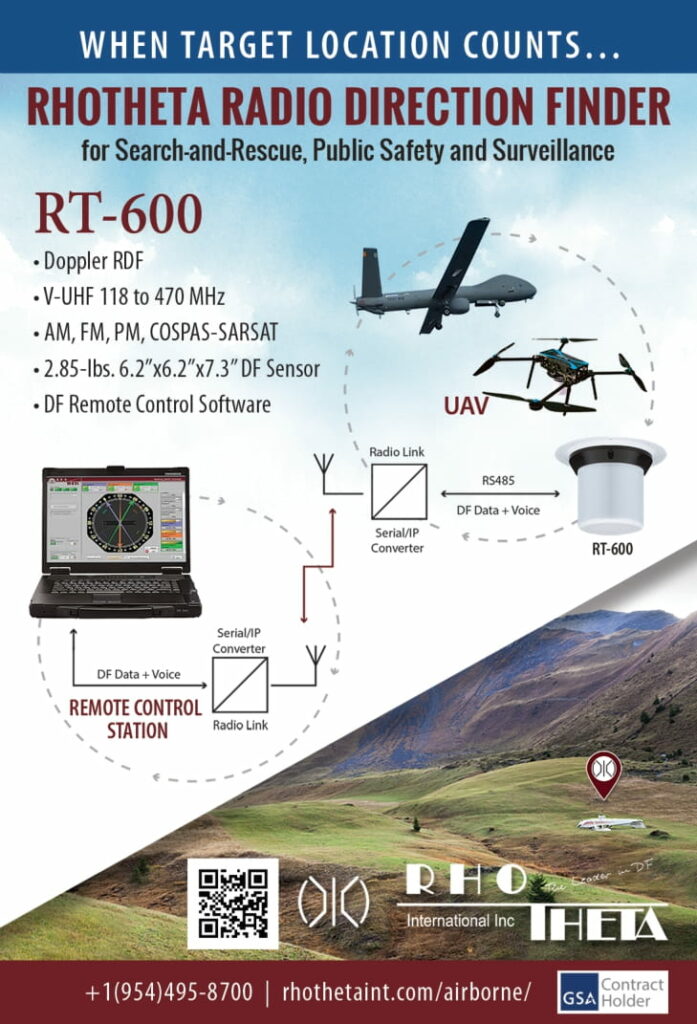
The comms management system is programmed to choose the bearer offering the best combination of signal strength, bandwidth and cost at any given moment, Wittamore says.
Wi-fi is normally the preferred bearer for operations near the shore, but at the exhibition centre dockside there were many systems competing for bandwidth and causing interference, Wittamore notes, so the Accession’s comms management software had automatically switched to Iridium satcom.
“It has lower bandwidth than wi-fi or 4G, but it is still enough for remote desktop control and over-the-horizon operations,” Williams adds.
The forward and aft trees each support a GNSS antenna. These are far enough apart to allow the navigation system to work out the boat’s vector heading from the difference in their measured positions, Wittamore says. Providing survey-grade accuracy, these systems are part of the survey payload.
Back-up position and heading are provided by a permanently installed Hemisphere GNSS system, with the Atlas system that receives error-correction signals from ground stations relayed via satellites.
The rear tree is home to several more antennas serving, for example, 2.4 and 5 GHz wi-fi signals, Bluetooth comms with a winch-deployed sound velocity profiler (SVP), and comms with the remote control unit that provides local direct control capability.
The antenna trees also support an Automatic Identification System (AIS) from Weather Dock and a set of day/night-capable cameras on the rear tree to support all-round situational awareness.
Floating cradle
Although USS has mostly been launching and recovering the Accession 425 from a trailer, the vessel is fitted with four lifting eyes for a crane, and the company is also developing a floating cradle system designed to enable launch & recovery at sea.
“It is almost like an RHIB with inflatable fenders around it. You drive the boat into it and then just lift the whole assembly in one go,” Wittamore explains. “The cradle can be towed at 4 knots through the water while the USV drives into it, so it is a boat in its own right.”
Remote operations
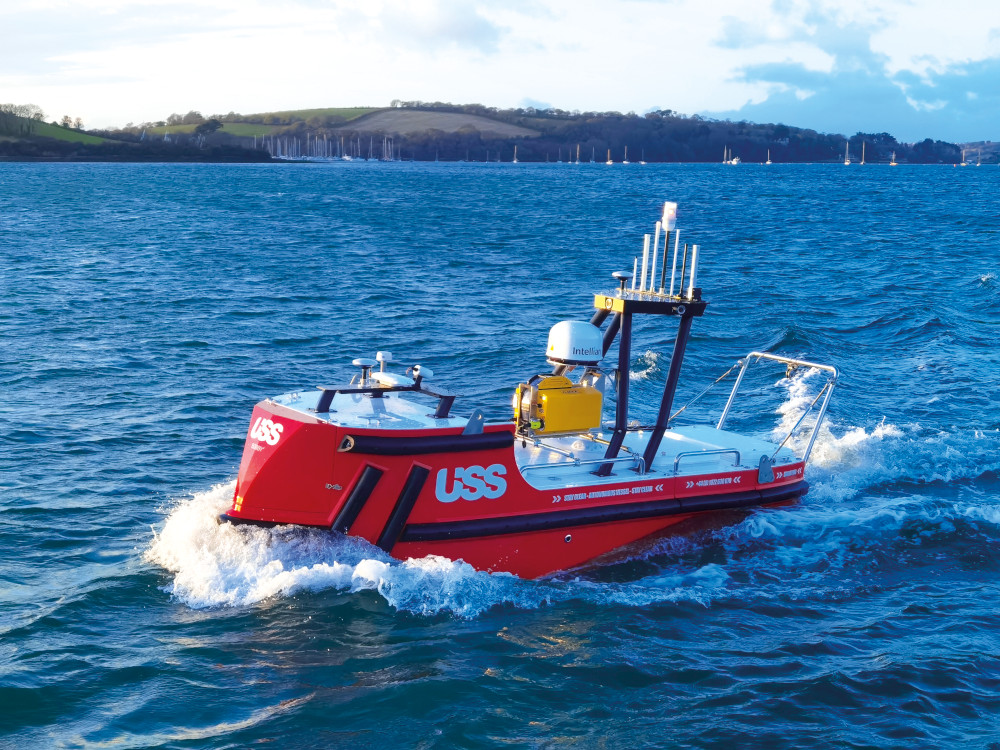
(Courtesy of USS)
Operations can be managed from a mother ship or from a shoreside remote operations centre, with the boat under human supervision at all times. “We have a USV operator with a minimum of an RYA Powerboat Level 2 qualification, and then we have a master mariner who overseas them,” Williams says.
This crew can be enlarged to suit the operational circumstances. “For 24-hour operations, depending on where and how we are working, there will be two or three operators plus a master mariner overseeing operations, and we will have surveyors looking after the payload,” Williams adds. While the AIS works all the time,
Williams says the system does not stream camera images constantly during over-the-horizon operations, because of the cost of satcom bandwidth. Instead, the camera imagery is processed locally by Guardian Vision software from Marine AI that recognises nearby objects and alerts the operator, who then streams the camera imagery and determines whether any avoiding action needs to be taken.
Autopilot development
Developed by Reygar, the autopilot can execute all the usual waypoint defined survey route plans that would be expected, and accommodates direct manual control via satcom and from the short-range RC handset. However, it also incorporates a number of advanced behaviours specified by USS to cope with contingencies such as comms outages and/or the loss of a thruster.
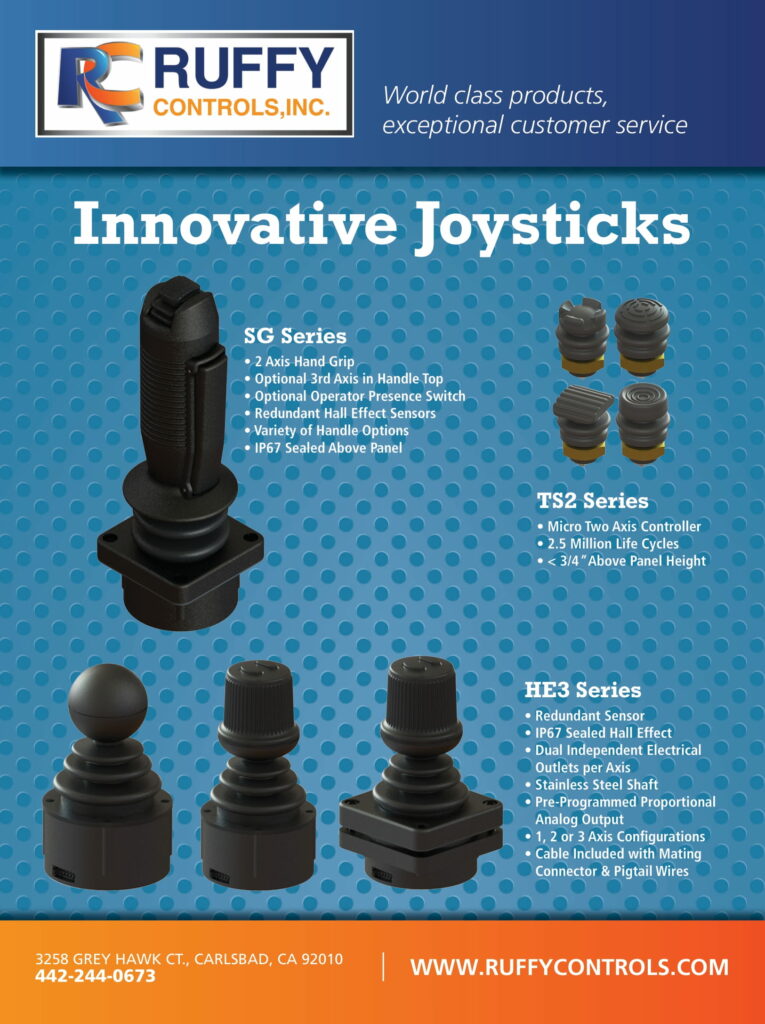
While simple solutions such as carrying on with the planned mission, turning back to port and drifting in ‘dead ship’ mode are also options. The autopilot can be programmed to go into passive or active loiter mode as well.
A passive loiter will see the USV motor back to a selected position if it drifts more than a set distance from that position – 5 or 10 m for example – before switching its thrusters off again. In an active loiter mode it will continually run its thrusters to stay as close to the selected position as possible.
“Eventually it finds where the current and wind are and points its nose into that and quite happily sits there,” Wittamore says. “Obviously, one takes a bit more energy than the other.”
Reygar was able to build on earlier work on an autopilot for uncrewed survey vessels and draw on experience with dynamic positioning systems to create an autopilot for USS incorporating these behaviours, says Richard Crowder, Reygar’s IoT development manager.
The software had to be tuned to take the Accession’s dynamics and manoeuvring capabilities into account. “We have our own dedicated control systems engineer who came out of the defence industry,” Crowder explains. “He knows all the values to tweak to tune all the PID controllers and so on.”
The hardware is based on a custom PCB that connects to the navigation system and the PWM motor controllers and azimuth steering system for the thrusters, he adds. “We also have a PLC version in anticipation of changes to work boat regulations.”
Underway SVP
With any sonar work demanding high precision and accuracy, up-to-date information on the speed of sound through the water and its relationship to depth are vital. That often means stopping at regular intervals to lower an SVP through the water column to take measurements.
Stopping is inconvenient and time consuming, requiring towed sensors to be recovered and then redeployed, for example. Instead, Accession carries a newly developed Vigo underway profiling winch from C-MAX.
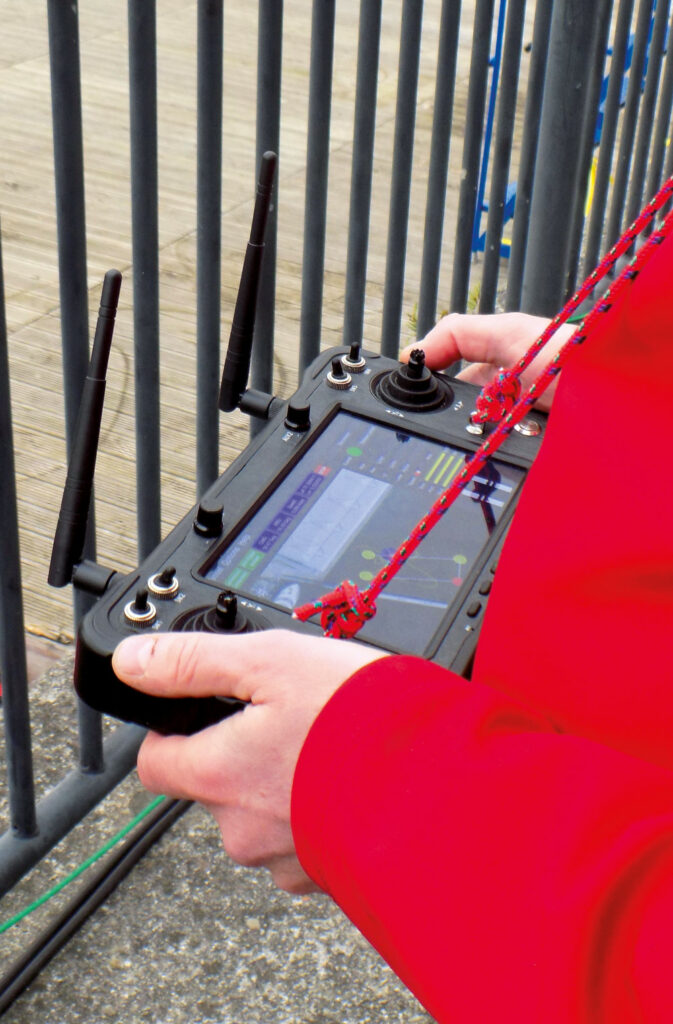
(Author’s photo)
It is important that the SVP falls through the water column as near vertically as possible to take accurate measurements, and the Vigo winch takes advantage of the natural behaviour of the Dyneema line in water to achieve this while the boat is moving, explains Hugh Frater, C-MAX’s lead software engineer on the project.
“The interface between the water and the air acts as a pulley, if you can get the line off the drum without any real tension,” he says. “You either push the line out under power while monitoring the tension, or you allow the profiler itself to just pull the line off as it falls, which is how we work.”
He adds that the profiler will still fall vertically whether the vessel is stationary or moving, because the pulley effect will put a 90º bend in the line. The portion on the surface will lie flat and the profiler itself will maintain its position in the horizontal plane while it descends down the water column and the boat continues forward.
“With this, we can do everything underway so we don’t have to stop the boat, and we can keep the efficiency of the survey going,” Williams notes. “We can take profiles constantly or whenever we want them.”
Immediately after the Ocean Business show, USS trailered the Accession 425 to Germany for an offshore wind farm route survey job, after which there is the chance of some passive acoustic monitoring work listening for cetaceans.
Further ahead, Williams is looking forward to upcoming consultation on a new Remotely Operated Uncrewed Vessel annex to UK maritime regulations that should remove the need to apply for mission-specific exemptions to rules designed for manned workboats. “It is an exciting and challenging time at the moment for anyone who wants to work with USVs in UK waters,” he says.
Specifications
Length: 3.5, 4.25 or 5.0 m
Beam: 1.3 m
Height: 1.65 m
Draught: 0.6 m, depending on configuration and payload
Weight: 750-1200 kg (fully laden and depending on vessel length)
Hull type: monohull with reverse bow, glass-reinforced plastic construction
Power and propulsion: Series-hybrid diesel electric, steerable thrusters
Speed: 5-6 knots for surveys, 8 knots maximum
Endurance: 12 hours to 20 days depending on configuration
Range: 10-15 km with long-range wi-fi, unlimited with cellular or satcom coverage
Launch & recovery: trailer or bespoke floating system
Some key suppliers
Autopilot: Reygar
Underway profiling winch: C-MAX
Bathymetric sonar: R2SONIC
Bathymetric sonar: GeoAcoustics
Bathymetric sonar: Reason
Bathymetric sonar: EdgeTech
Bathymetric sonar: Norbit
Bathymetric sonar: Kongsberg
Sub-bottom profiler: GeoAcoustics
Sub-bottom profiler: Innomar
Sub-bottom profiler: EdgeTech
GNSS: SBG Systems
GNSS: Trimble
GNSS: Hemisphere
Satcom antenna: Intellian
Satcom services: Iridium
Collision avoidance: Marine AI
Inertial navigation: SBG Systems
Inertial navigation: Applanix
Automatic Identification System: Weather Dock
Sound velocity profiler: Valeport
Sonar data compression: Hypack
Sonar data compression: Qinsy
Sonar data compression: BeamworX
Sonar data compression: Eiva
Thrusters: Torqeedo
Batteries: Torqeedo
UPCOMING EVENTS
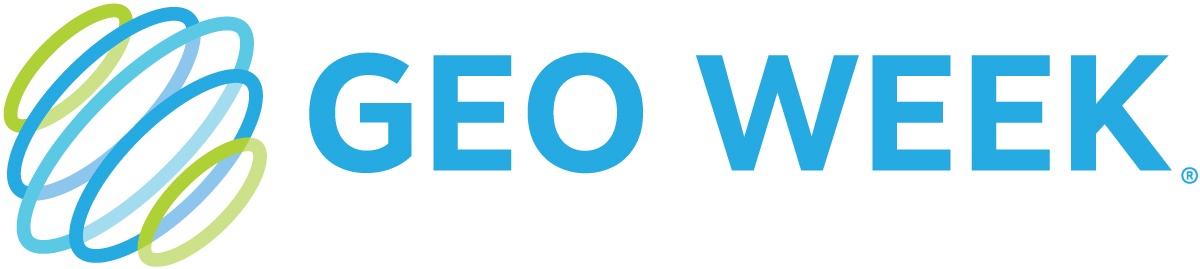
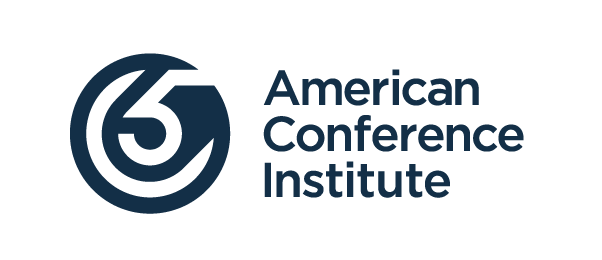
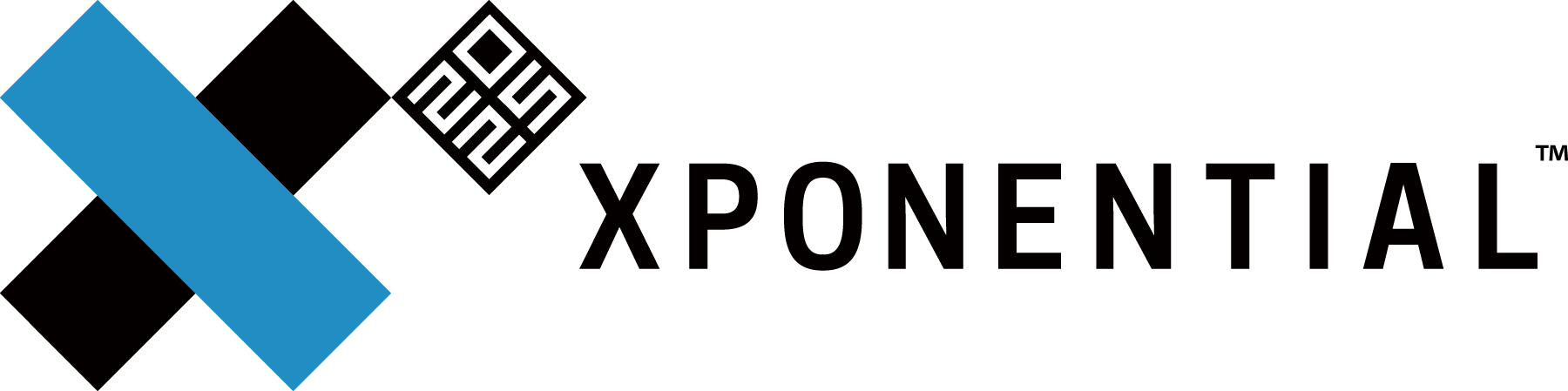
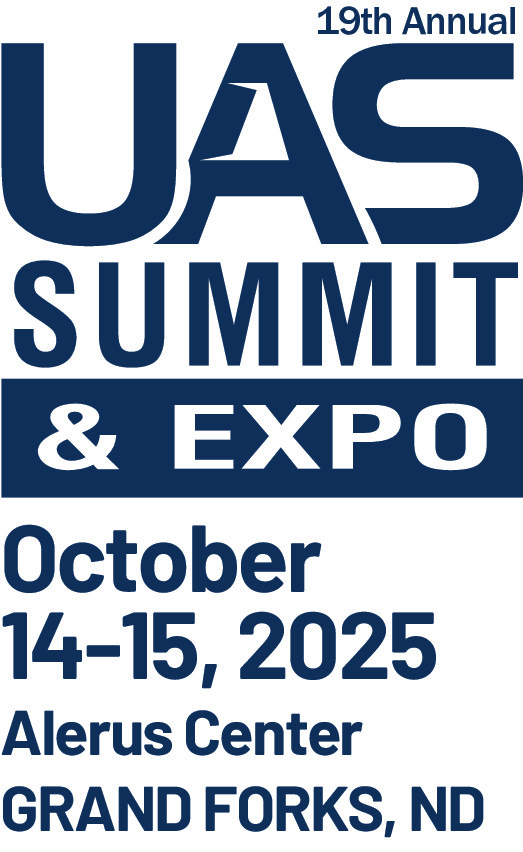
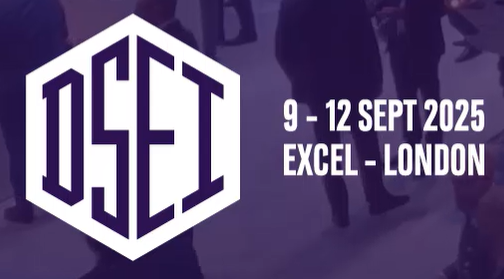
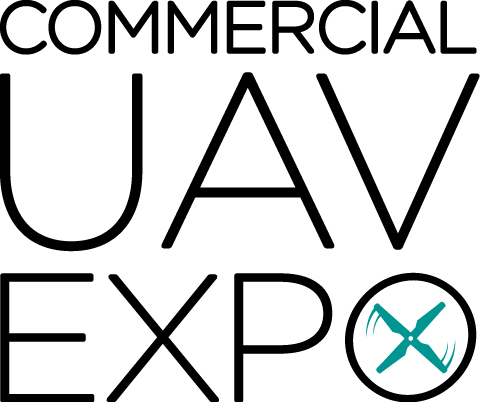
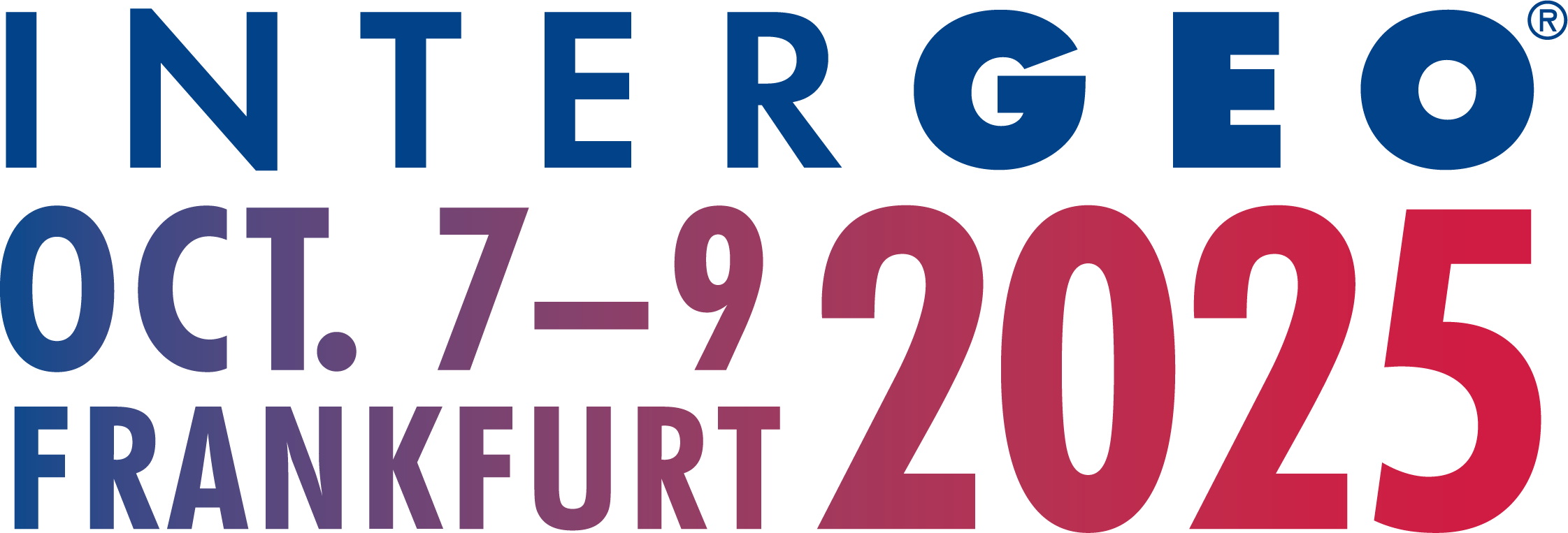
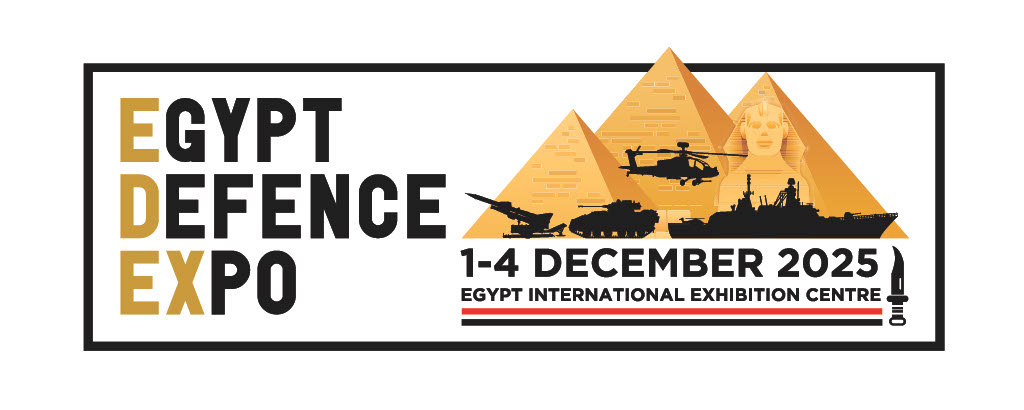
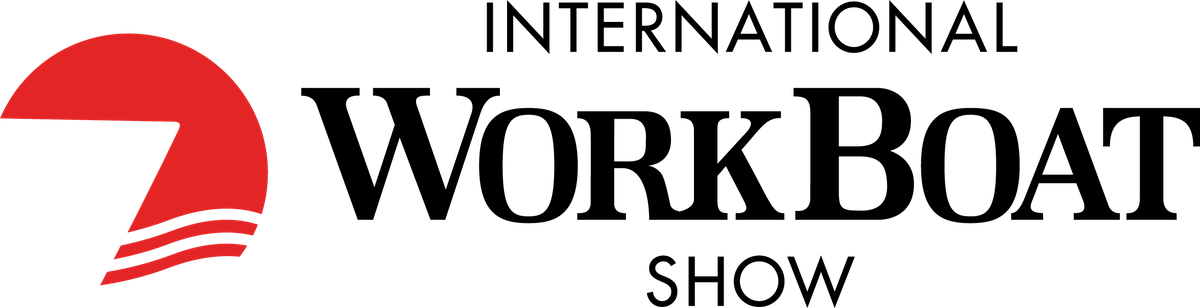
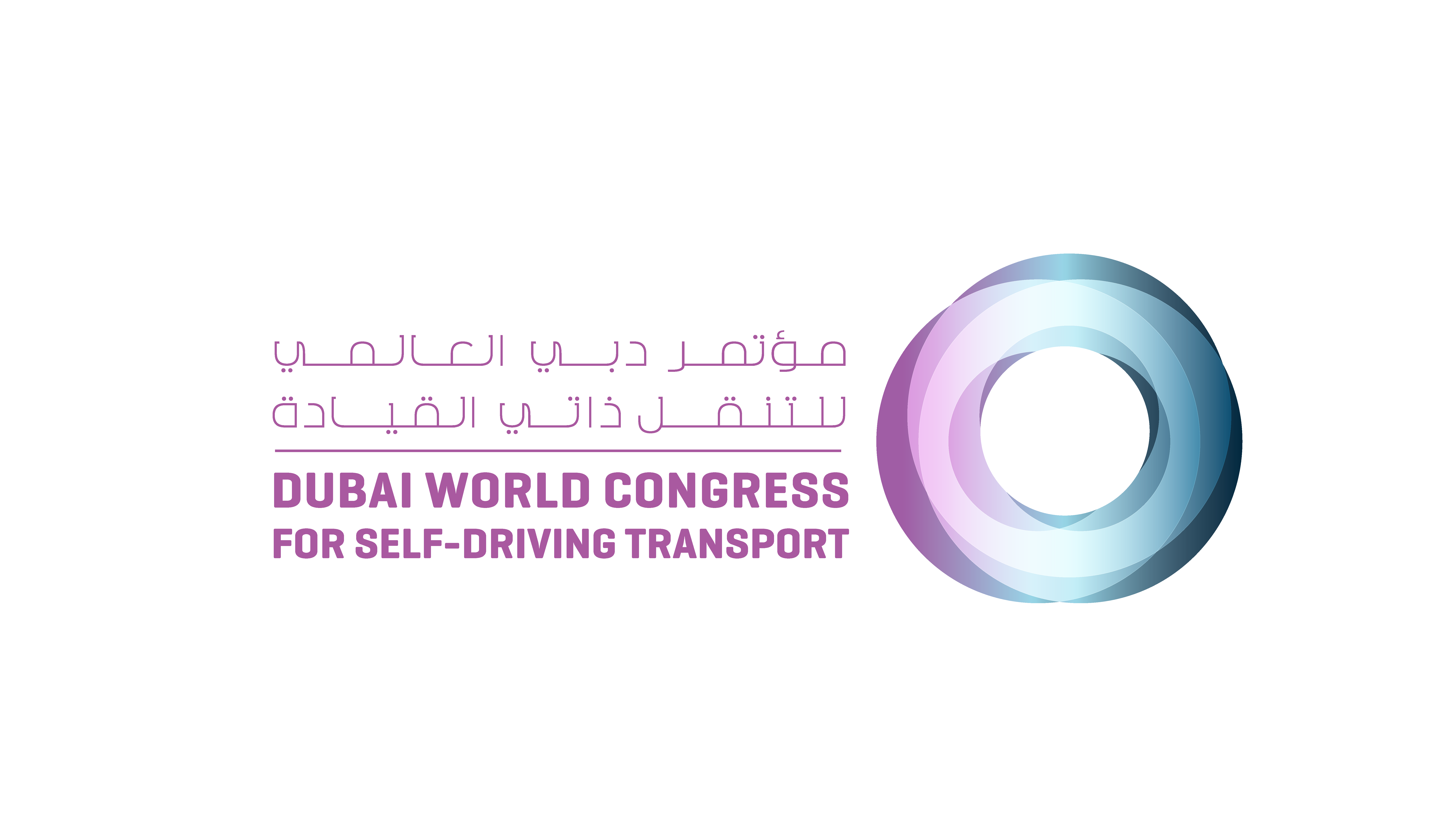
