Space vehicles
Critical missions
Uncrewed systems are playing a vital role in understanding off-world environments and keeping space crews safe in them, as Rory Jackson explains
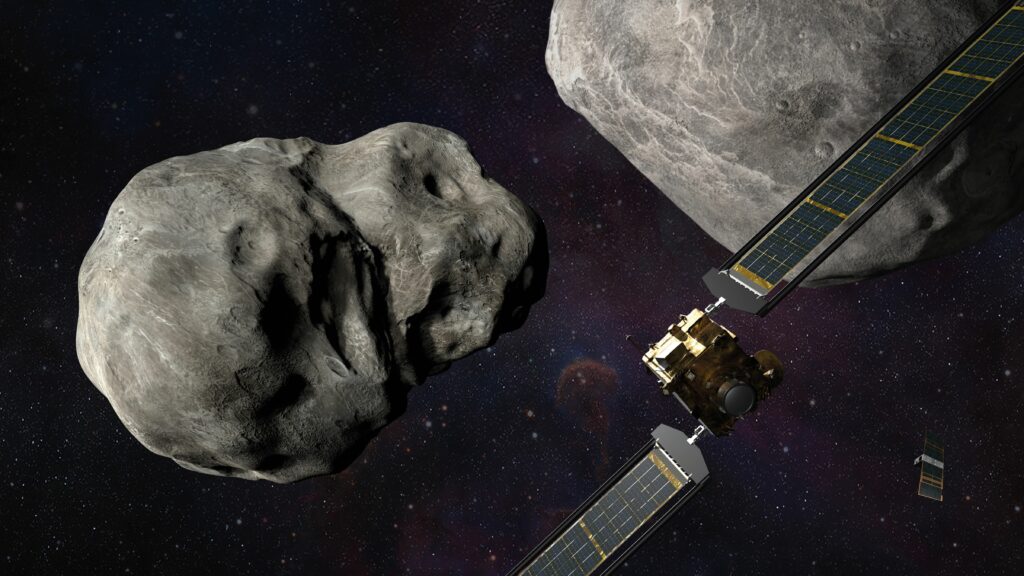
(Courtesy of NASA)
Missions
While many of the world’s newsrooms and social media platforms discuss plans for human colonies on the Moon and Mars, it must be remembered that an immense amount of groundwork must first be laid by uncrewed missions before they can be established. That does not simply mean laying the literal foundations for habitable environments and the energy and resource inputs needed for human survival. Space and alien worlds are still hugely unknown environments, even before we consider astronaut safety.
Fortunately though, the spacecraft industry continues to pursue a wide range of uncrewed missions and systems, to uncover more of the mysteries of our Solar System, and in turn reveal ways that we might mitigate against or defend space crews and uncrewed assets from the most dangerous threats.
Asteroids
In a major leap forward in humanity’s ability to ensure its survival against existential threats, NASA’s Planetary Defense Coordination Office has successfully crashed an uncrewed spacecraft into an asteroid with the intention of deflecting it from its original path.
The spacecraft in question was the DART (Double Asteroid Redirection Test, a name it shared with the mission programme around it), a vehicle equipped with numerous new subsystems NASA aimed to mature as part of the mission. It measured about 2.6 x 1.9 x 1.8 m and weighed 610 kg at launch.
Of those subsystems, the Didymos Reconnaissance and Asteroid Camera for Optical navigation (DRACO) was key to its terminal approach, with SMART Nav (Small-body Manoeuvring Autonomous Real Time Navigation) algorithms powering the autonomy key to DRACO’s intelligent path-planning towards the asteroid. The algorithms ran on a Coresat (Core Small Avionics suiTe) computer built by John Hopkins Applied Physics Laboratory (APL), and streamed photographs back to Earth at 1 Hz via a radial line slot array high-gain antenna.
The target asteroid in question was Dimorphos, one of two bodies in the Didymos binary asteroid system. It is 160 m in diameter and orbits the larger, 780 m Didymos. Part of SMART Nav’s functions included distinguishing between the two objects using DRACO’s imagery, to ensure that the correct asteroid was being approached.
Dimorphous and its sibling are not threats to Earth, but researchers anticipate that the impact will shorten Dimorphos’ orbit by about 1%, or roughly 10 minutes. Precise measurements of the degree of deflection achieved was one of the primary purposes of the full-scale test, with closer understanding of how to redirect the trajectories of asteroids through kinetic uncrewed spacecraft impacts, planetary defence being the end goal.
To reach Dimorphous, the DART also integrated the NEXT–C (NASA’s Evolutionary Xenon Thruster – Commercial) ion engine, an electric propulsion solution developed by the Glenn Research Center in Ohio, in collaboration with California-based Aerojet Rocketdyne.
The electric demonstrator engine ran using xenon (with 50 kg of hydrazine propellant for manoeuvring and attitude control) and was powered by two solar array concentrators produced by APL, each 8.5 m long when fully deployed.
Ground-based telescopic observations are now being performed to measure the change in Dimorphous’ orbit as a consequence of the impact, as well as observing the effects of the impact (including any ejection and distribution of regolith) on the asteroid. Also, a CubeSat named LICIACube built by the Italian Space Agency separated from the DART before impact to help observe the collision, photography from which continues to be studied.
Earth’s orbit
As the commercial space sector develops, small satellites for low Earth orbit (LEO) and adjacent altitudes are being produced and launched at an increasing rate.
Numerous technologies are critical enablers of this new generation of uncrewed spacecraft. Some, such as solar cells and radio transceivers, are well-known, but the important role of additive manufacturing (AM) in building small satellite craft is comparatively less well-established.
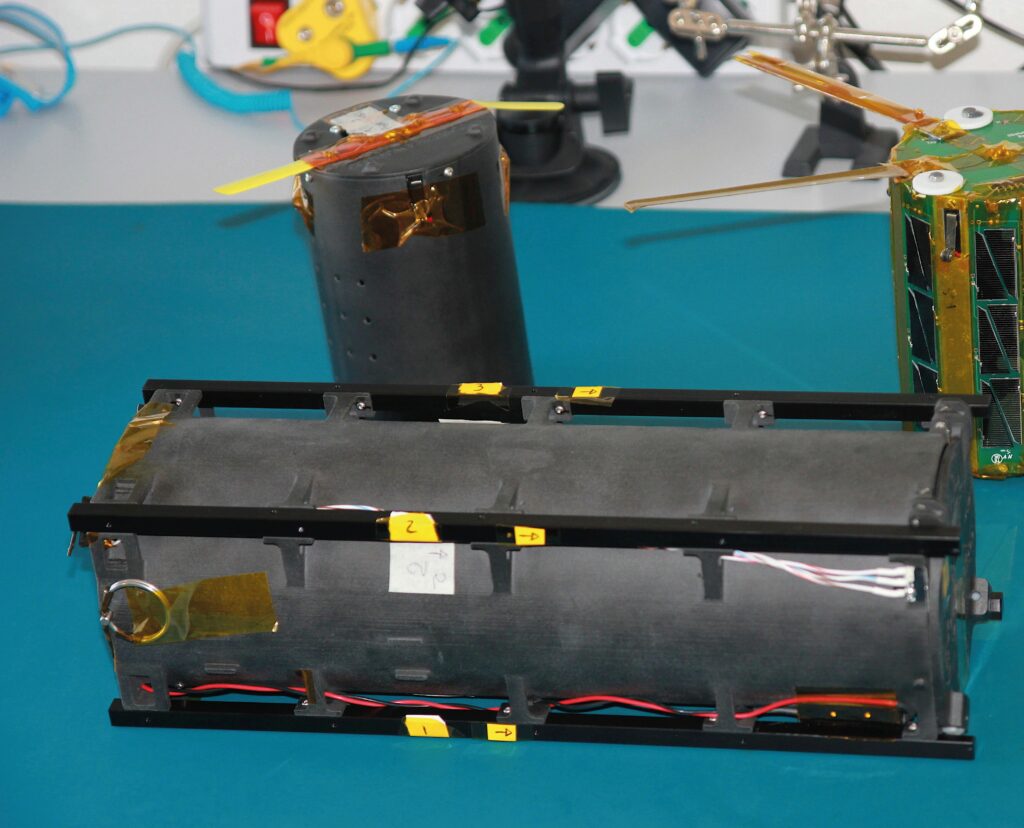
manufactured TuPOD during their
integration phase, made using
CRP’s Laser-Powder Bed Fusion
technology
(Courtesy of GAUSS)
The KYSAT-2 1U CubeSat for instance was launched into orbit as part of the NASA ElaNa IV mission in 2013, with a hybrid single-part additively manufactured propulsion system being used as a high-impulse thruster for small to micro cube-shaped satellites. Also, a completely additively printed satellite, the TuPOD, was the first of its kind to be launched from the ISS, being used as a CubeSat model and as a dispensing system for tube satellites called TubeSats. Notably, both of these systems were produced using CRP USA’s Windform composite AM technology, specifically a form of laser sintering called laser powder bed fusion (L-PBF).
“L-PBF is similar to laser sintering, but the term ‘sintering’ implies that particles aren’t fully fused, which is an inaccurate way of describing how thoroughly our powders are melted together,” says Stewart Davis, president of CRP USA.
It might seem odd that a company best known for supplying racing parts is now providing critical components and services to spacecraft, but as Davis notes, “Race and space vehicles both suffer from extremely tight packaging constraints and weight limits, and need to be designed to withstand potentially massive forces.
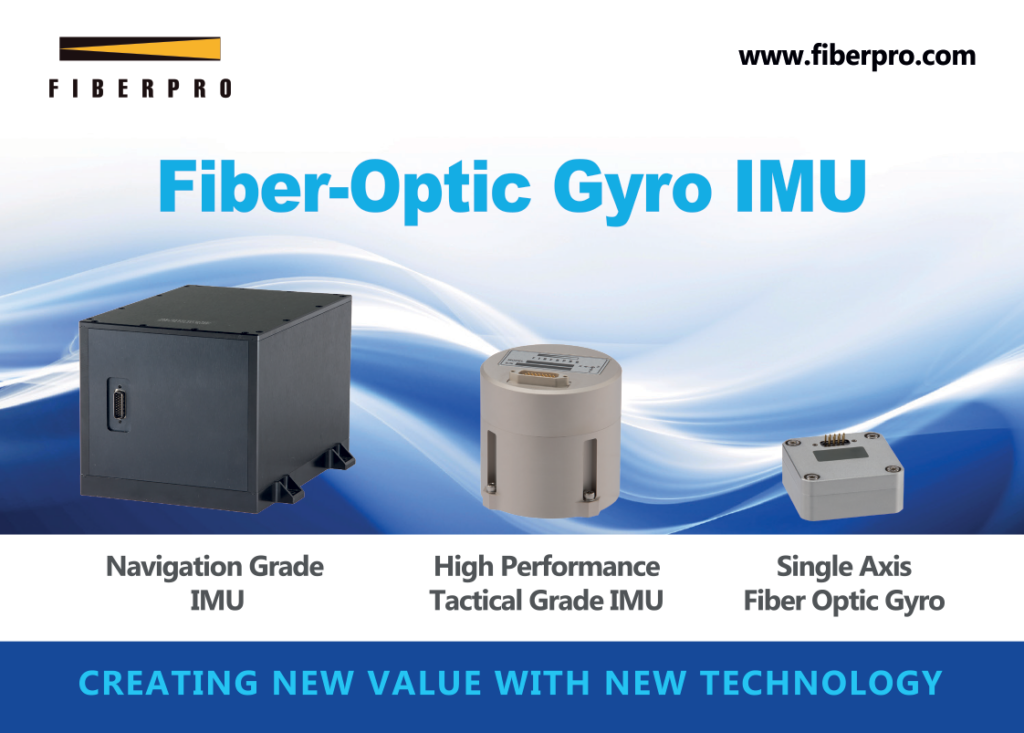
“When we look at a 1U CubeSat, which is about 10 x 10 x 10 cm, and understand that it needs to carry up a bunch of equipment for scientific experiments, that can mean a really complex structure for mounting instruments, PCBs, battery trays and other electronics that absolutely have to fit inside that shape. Compared with, say, a five-axis aluminium milling machine, making the structure through AM gives the end-user freedom to mount their subsystems in ways that might not otherwise have been possible.”
CRP materials currently in use in Earth orbit include its Windform XT 2.0, SP and LX 3.0. This last one is a non-conductive composite of mineral glass fibres and polyamide, whereas the first two are carbon microfibre-based (also with polyamide matrices) with conductive properties.
“The first step in qualifying our materials and properties for spacecraft was out-gas testing, to ensure the polyamides weren’t going to be off-gassing polymer molecules into space, as they would then be attracted to flat, shiny surfaces like lenses, solar panels or other critical devices that need to stay clean in space to avoid endangering the satellite,” Davis says.
“We have also exhaustively tested our materials against UV radiation and in vacuum conditions, and proven that they have no issues with enduring those environmental factors.”
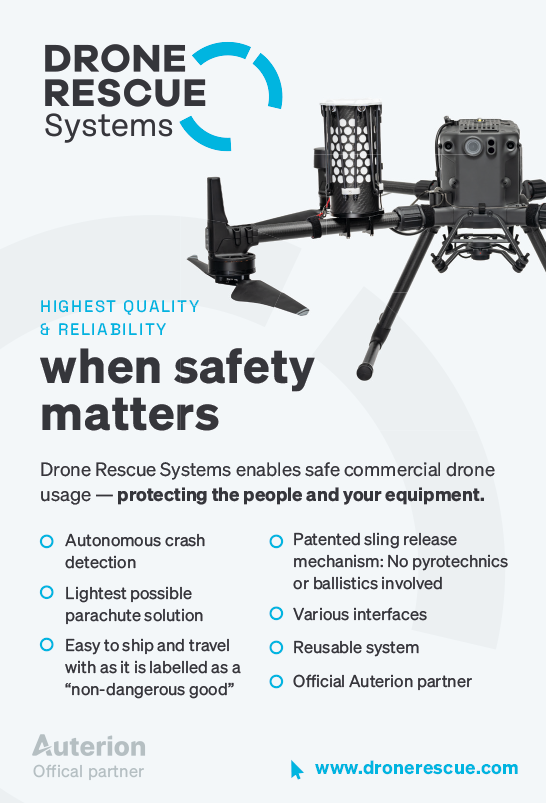
Although details about actual customers cannot be disclosed, Davis adds that CRP’s materials and processes are contributing to a wide range of small satellites and uncrewed rockets, and that the company is likely to explore alternative AM approaches such as fused deposition modelling or techniques for metal AM to supply parts with the properties needed for future orbital spacecraft.
“We expect to have parts in use on the Moon relatively soon, based on what our customers are doing,” he says.
While the use of satellites of all sizes for comms, mapping, surveys and more is well-established, there remains a gap in capabilities for inspecting the satellites themselves, which could be critical regarding proper maintenance and safely de-orbiting ageing space structures.
HEO Robotics, based in Australia, is one company aiming to resolve this, given the benefits of well-maintained orbital spacecraft as well as the risks to orbital industries posed by the growing amount of space junk. Its proprietary HEO Inspect software is programmed to use existing Earth observation satellites as in-orbit inspection cameras to visually examine other satellites, generating critical data in real time for satellite owners and operators.
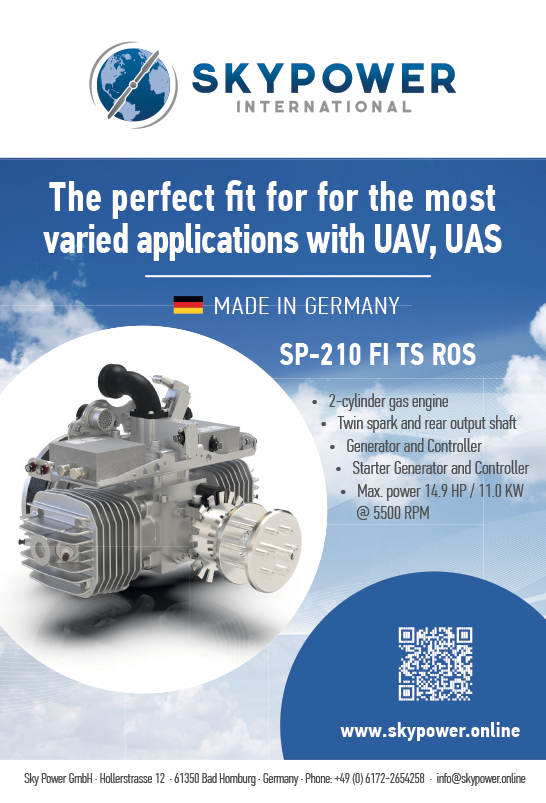
“We are primarily a software company, working with satellite operators with existing assets in space, currently 33 satellites in LEO,” says David Balson, managing director of HEO Robotics in the UK. “And in summer 2023, we’ll be partnering with operators launching satellites into geostationary orbit, which opens up opportunities to inspect and protect an enormous range of comms and military satellites that provide critical infrastructure for life on the ground.”
Partnering with satellite operators gives HEO Robotics the ability to access and programme the necessary patterns of thruster movement and camera operations for such spacecraft to zoom in on and provide close scrutiny of others.
The partnerships also give critical realtime locations of where different satellites are so that HEO can calculate the angles and directions to enable each camera to track their targets precisely.
Also, as of this September, the company has unveiled the Holmes Imager, a telescopic space camera designed to be hosted as a secondary payload on spacecraft. It is a 2.3 kg system that consumes 6 W in normal operation, with a 94 mm aperture and a 0.4º field of view.
So far, HEO has partnered with three space companies to have four Holmes cameras launched into orbit by the end of next year, with a target of 2500 cameras in orbit by 2027.
“We have development plans beyond that too,” Balson adds. “EO data is very useful, but IR and NIR sensing can identify material qualities and deeper signs of damage to other spacecraft, so we’ll almost certainly develop solutions based around those, as well as adopting more edge computing for real-time or postprocessing of in-orbit image data.”
While the ability to perform persistent, autonomous, high-resolution inspections of spacecraft stands to help satellite operators keep track of the conditions of their growing numbers of orbital assets, HEO notes that the number of satellites in space is already extremely high, and that the hope is that HEO Inspect and Holmes will encourage operators to use individual assets for longer, rather than continuously launch more and more.
“The European Space Agency [ESA] has a vision for 2050 to achieve a circular economy in space, within which all ESA members will be responsible for anything they put up in space.” Balson explains.
“They would be charged with bringing it back down or otherwise remanufacturing or repurposing it in space. “Only through accountability and transparency can that policy come into effect, which is where our platform is really coming to the fore. It’s allowing organisations to see satellites in a precise, detailed and fine-grained sense for the first time, so that they can be tracked really closely as to how they’re being used or misused, cared for or neglected, and recycled or discarded.”
The Moon
NASA is pushing forward with its Artemis programme to return astronauts to the Moon, despite problems with its efforts to launch the initial Artemis I uncrewed Moon-orbiting mission.
Artemis I comprises NASA’s Space Launch System (SLS) expendable rocket and the partially reusable Orion spacecraft. A faulty reading from a redundant sensor prompted the cancellation of the first launch attempt, on August 29 this year, while a hydrogen leak scuppered the second attempt on September 3. The third launch opportunity was on September 27, but trajectory forecasts for (then) Tropical Storm Ian now mean the mission is expected to begin in November this year.
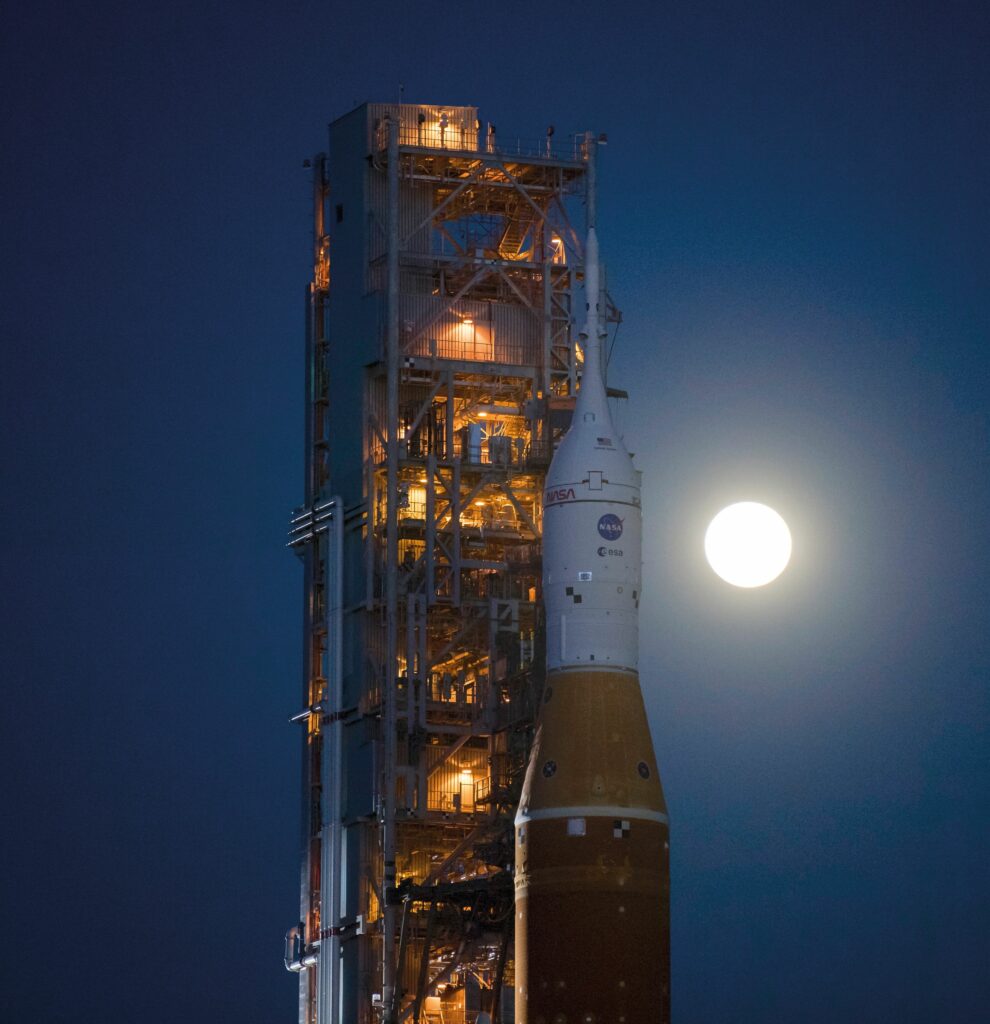
(Courtesy of NASA)
The mission will test the Orion’s subsystems and performance in deep space by sending it on an uncrewed flight test around the Moon and back, with a crewed mission to follow on a future Artemis II mission.
Specifically, Artemis I will test the Orion’s navigation and comms systems without help from the Earth’s comms satellites, and examine how its radiation sensors and shielding perform outside the protection of the Earth’s magnetic field. It also carries the world’s largest heat shield, which will be tested during a high-speed return from the Moon.
The uncrewed Orion will have a gross lift-off weight of 32,650 kg, including 7250 kg of propellant. During its journey, most of its propulsion (as well as thermal management and electric power) will come from the service module provided by the ESA. That therefore carries 14,000 kg of propulsion equipment, composed of 24 reaction control system thrusters, each producing 23 kg of thrusting force, and eight auxiliary engines each producing 50 kg of thrust, with an orbital manoeuvring system that creates a further 2700 kg of thrust.
Also, four solar arrays comprising 15,000 photovoltaic cells will extend out from the Orion’s service module to a full length of 19 m, collectively to generate up to 11 kW of electrical power.
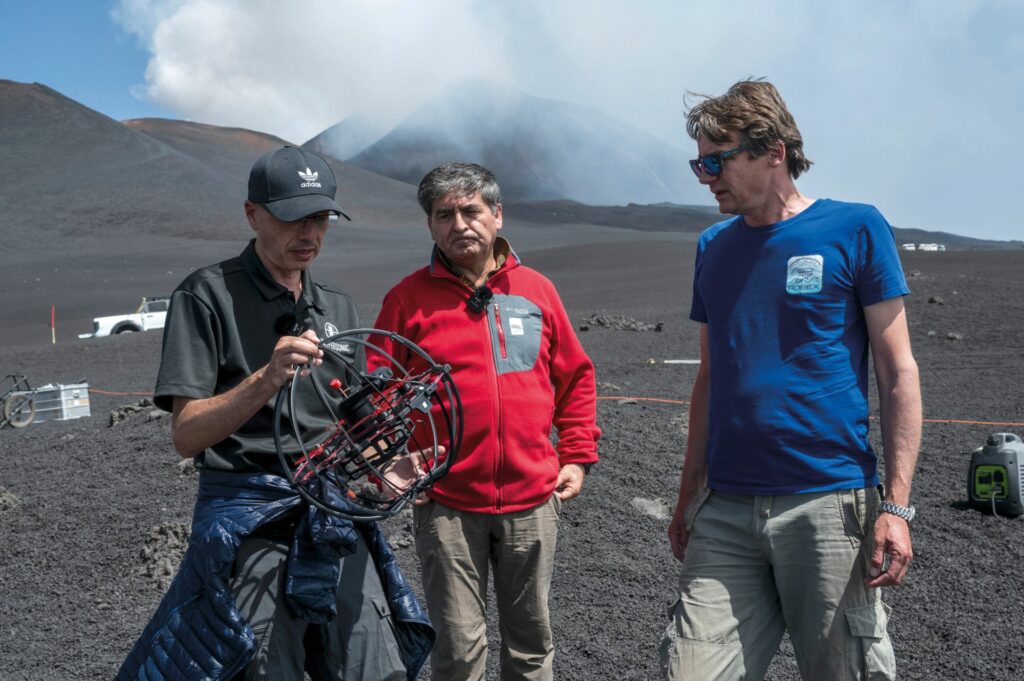
(Courtesy of Skypersonic)
The heat shield is 5.03 m in diameter, and will shed severe heat away from the crew module (the reusable portion of Orion) as the spacecraft returns to Earth at roughly 40,200 kph and enduring temperatures of around 2760 ºC.
The heat shield’s outer surface is built from 186 billets of an ablative material called Avcoat, which is an epoxy novolac resin with special additives in a fibreglass honeycomb matrix; it is a variant of the material used on the Apollo mission capsules. It is bonded to a titanium skeleton and a composite skin to enable its shape and structural support for the crew module during descent, during which the Avcoat burns off in a controlled fashion to transmit heat from the module.
Furthermore, after the Orion separates from the SLS’ stages, 10 uncrewed CubeSats will be deployed for carrying out experiments and technology demonstrations as part of studies of the Moon, asteroids and the deep space radiation environment.
Each CubeSat weighs a maximum of 13.6 kg and carries its own propulsion and navigation systems alongside its research instrumentation. The Orion’s stage adapter contains a secondary payload deployment system to separate and launch the CubeSats, with mounting brackets for COTS dispensers, cable harnesses, a vibration isolation system and an avionics unit.
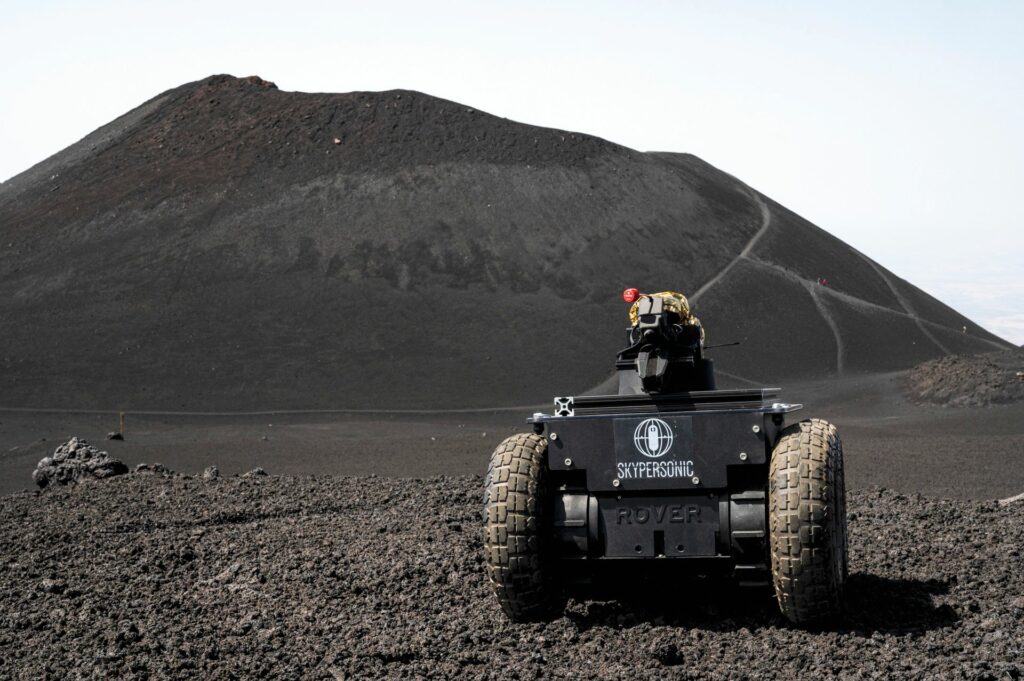
(Courtesy of Skypersonic)
After separation from the Orion, and after the spacecraft is a safe distance away, the deployment system’s avionics unit will send signals to release the payloads at pre-scheduled times to allow their orbital research to begin.
Mars
Further out in the Solar System, NASA’s uncrewed systems are continuing to reach research milestones.
In September this year for instance, a paper was published detailing how the InSight lander measured seismic and acoustic waves from four space rock impacts on the Martian surface a year earlier. It also detailed how the Mars Reconnaissance Orbiter flew over the estimated impact sites to confirm their location and capture colour close-ups of the craters.
Meanwhile, the Perseverance rover (with mapping support from the Discovery UAV) has recently collected four rock-core samples from within an ancient former river delta in the Jezero Crater, an area long identified by scientists as potentially holding signs of ancient microbial life, and which means the UGV has now collected 12 scientifically compelling rock samples from the planet’s surface.
While autonomous capabilities are improving all the time, operators still need to be capable of tracking uncrewed vehicles and intervening, if necessary, all in real time.
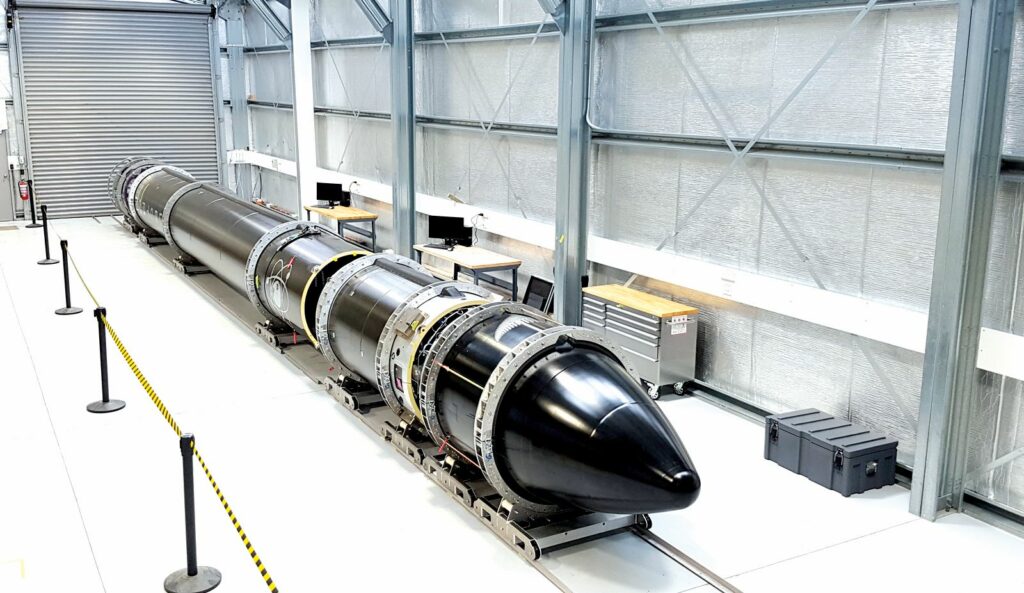
(Courtesy of Rocket Lab)
At present, the comms between Earth and Mars take 5 to 20 minutes, and even if that became much shorter as a result of Martian colonisation, the absence of numerous comms satellites or any GNSS on Mars could render UAV- and UGV-based exploration a slow and arduous affair.
Skypersonic, however, which is based in Michigan and has a European office in Italy, has been running simulated trials of uncrewed Mars exploration missions using a combination of its autonomous vehicles and its very low latency data link technology. It signed a 5-year contract with NASA in 2021 to provide UAV and rover software, hardware and support to NASA’s simulated Mars mission, with the simulation being performed on Mt Etna owing to its rocky and chaotic geography bearing close similarities with Martian terrain (see Video Systems focus in this issue, page 38).
The mission will consist of crew members living and working in a 1700 sq ft 3D-printed module called Mars Dune Alpha. It will simulate many of the challenges of a mission on Mars, including monitoring and operating UAVs and UGVs thousands of kilometres away without access to GNSS or magnetic compasses (given the absence of a magnetic field on Mars).
“Our Long Range Real-Time Remote Piloting System enables the UAV or rover and its operator to be located separately, anywhere on a world, but the comms and control are performed with extremely low latency using a simple 5G connection, and we don’t use GPS or any other satnav, which is what drew NASA’s interest,” says Skypersonic’s CEO Giuseppe Santangelo.
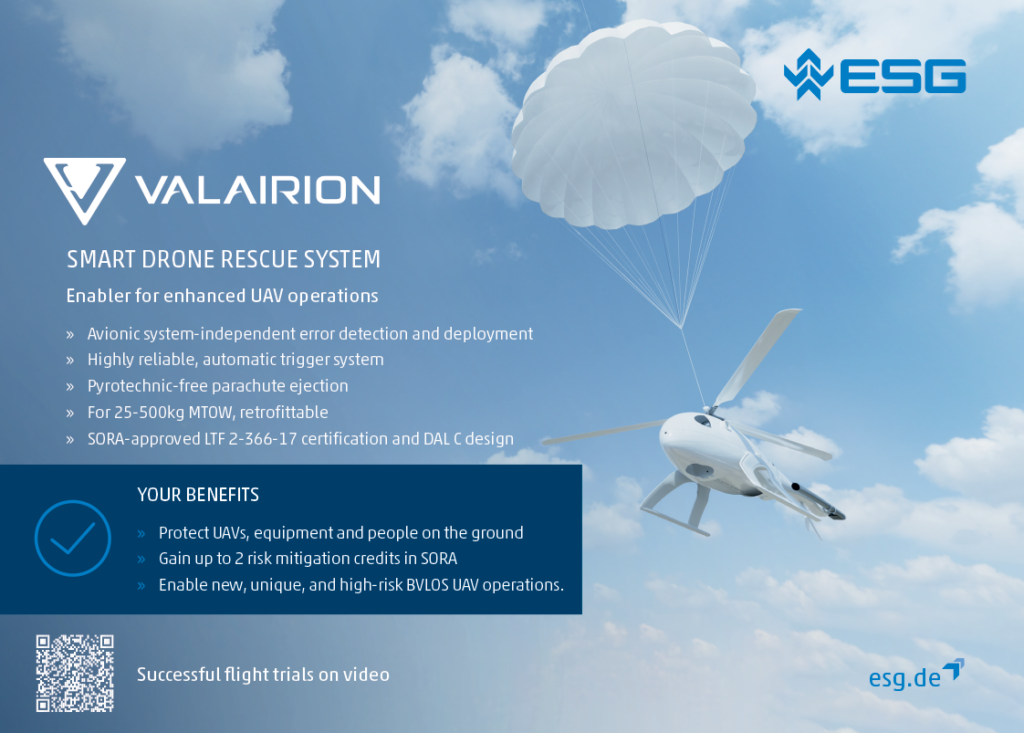
“The core of our programming, with very streamlined algorithms and high-quality compression, is what enables latencies as low as 70 ms over distances of 7000 km. That is the kind of speed with which Mars colonists would be able to see visual, audio and health data feeds from their UAV or UGV, as well as navigating using fusions of inertial and optical flow telemetry, assuming an orbiter is available to create a BVLOS link.”
The tests are using Skypersonic’s Skycopter caged UAV as well as a four-wheeled rover UGV it has built for the simulation. Skypersonic has also developed a Stratocopter UAV capable of flying at extremely high, low-pressure altitudes, which could theoretically be used to simulate flights in the thin Martian atmosphere, sometime between now and the end of the contract in 2026.
Venus
Although crewed and uncrewed mission planners alike have their eyes fixed on Mars and have made a myriad of preparations, it is not the only body beyond Earth’s orbit that beckons astronomers and space engineers.
For example, US-based Rocket Lab is funding an uncrewed flyby of a small spacecraft through the clouds of Venus for about 5 minutes at an altitude of 48 to 60 km (with design assistance from MIT), to study the make-up and properties of the Venusian clouds as well as search for signs of organic life among them.
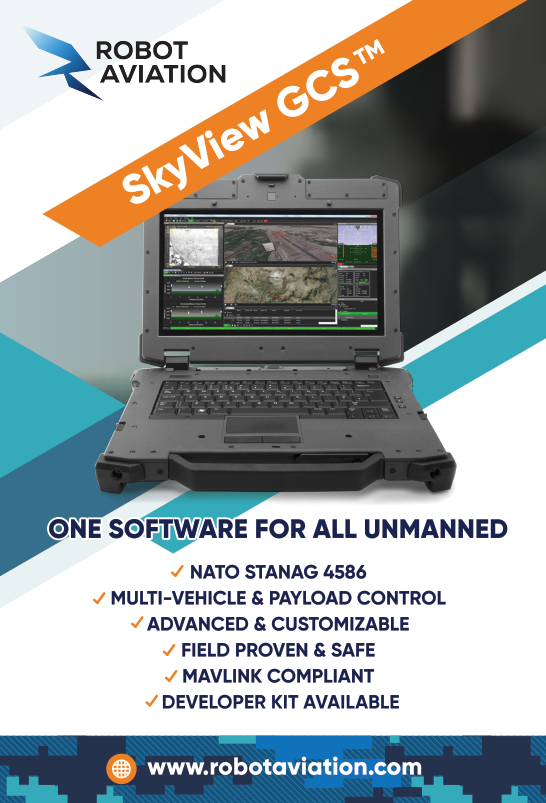
Rocket Lab’s Electron launch vehicle will deliver the 20 kg probe into a 165 km orbit above Earth, at which point the Photon upper-stage vehicle will carry out several burns to reach escape velocity, and eventually deploy the probe into Venus’ atmosphere. The journey is expected to take roughly 5 months, with the mission launch being aimed for May next year, meaning the Photon would reach Venus in the October.
The probe will contain a 1 kg scientific payload with an auto-fluorescing nephelometer to detect suspended particles in the clouds, to search for organic chemicals and investigate the clouds’ habitability. It is hoped that the probe will transmit this data during and after the 5 minutes and 30 seconds it spends falling through the upper section of the atmosphere.
While exact configurations of the Photon vary depending on parameters of each mission, it uses hull-mounted solar arrays and lithium-polymer batteries to power an attitude control system consisting of star trackers, sun sensors, an IMU, reaction wheels and a cold-gas reaction control system.
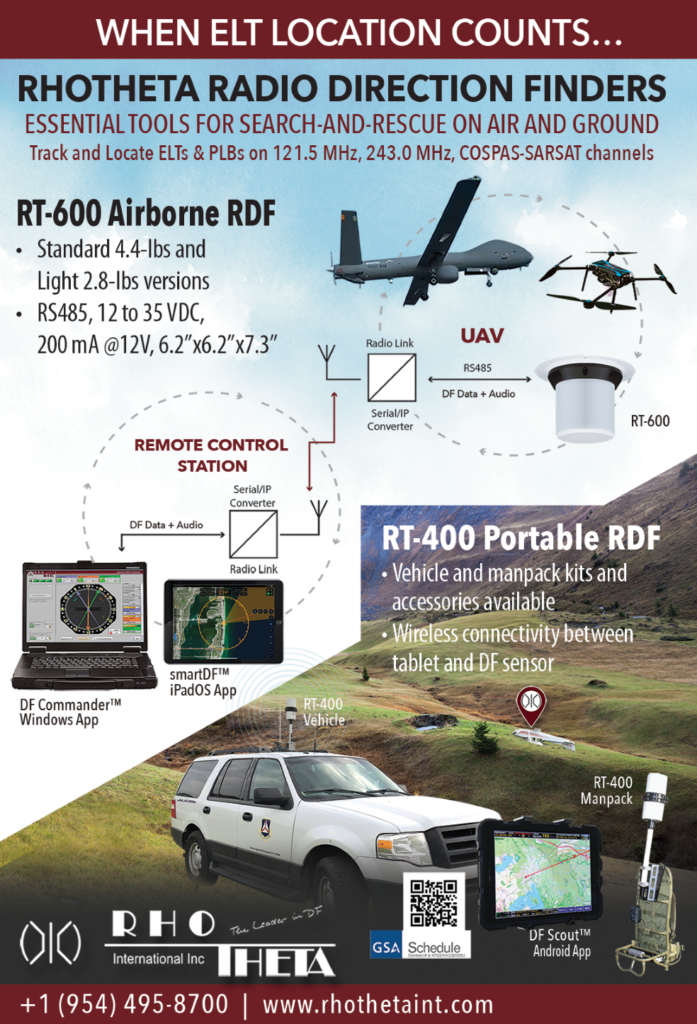
Also, onboard S-band and X-band RF ranging transponders enable comms with NASA’s Deep Space Network and commercial networks, as well as deep space radiometric navigation, while a GNSS receiver is used for navigation near Earth. A bi-propellant propulsion system called Hyper Curie uses electric pumps to supply pressurised propellant to a thrust vector-controlled engine.
Summary
We have seen a glimpse here of humanity beginning to prevent some key issues that space exploration poses to our future in the Solar System.
By deflecting asteroids and taking better care of uncrewed systems in orbit, we might prevent the kinds of harm posed by the Kessler Syndrome or surface impacts.
By gaining a better understanding of the different environments on the other planets, and in the space between them, insights are being gained into how human life could be better protected or adapted for long-term space travel or living.
Every lengthy space voyage yields critical data on making spacecraft more robust, increasing the chances that autonomous systems and humans alike can one day be ferried to the furthest regions of the Solar System.
Anyone designing uncrewed systems to work in our terrestrial atmosphere would do well to watch the progress and technical developments of these missions. Autonomously handling the least understood and most dangerous environments currently reachable by human means is an impressive achievement, to put it mildly.
Just as the NASA missions of decades ago gave us countless innovations that are now critical to our day-to-day lives – including water purification systems, home insulation and CAT scanners – the many unique computers, payloads, power systems and more being used in uncrewed spacecraft could be gamechangers for terrestrial uncrewed vehicles as commercial, civil and defence markets all request ever-longer endurances and tolerances of more extreme environments and mission parameters.
UPCOMING EVENTS
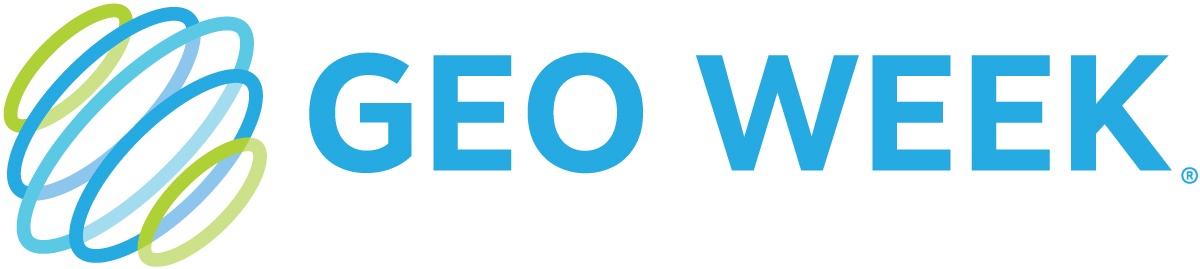
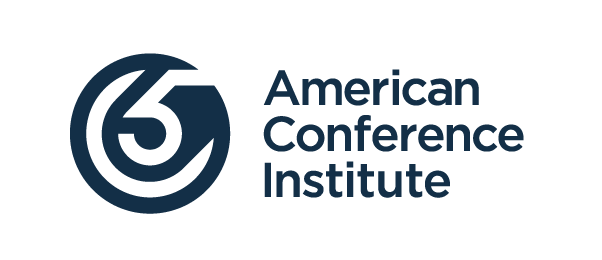
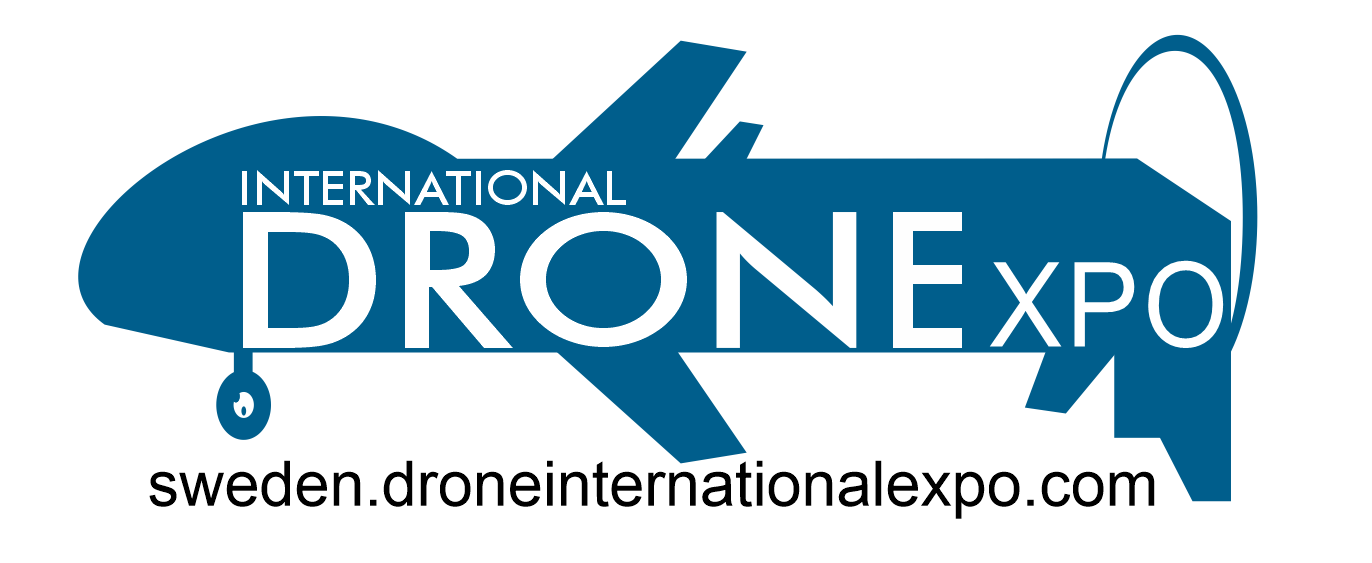
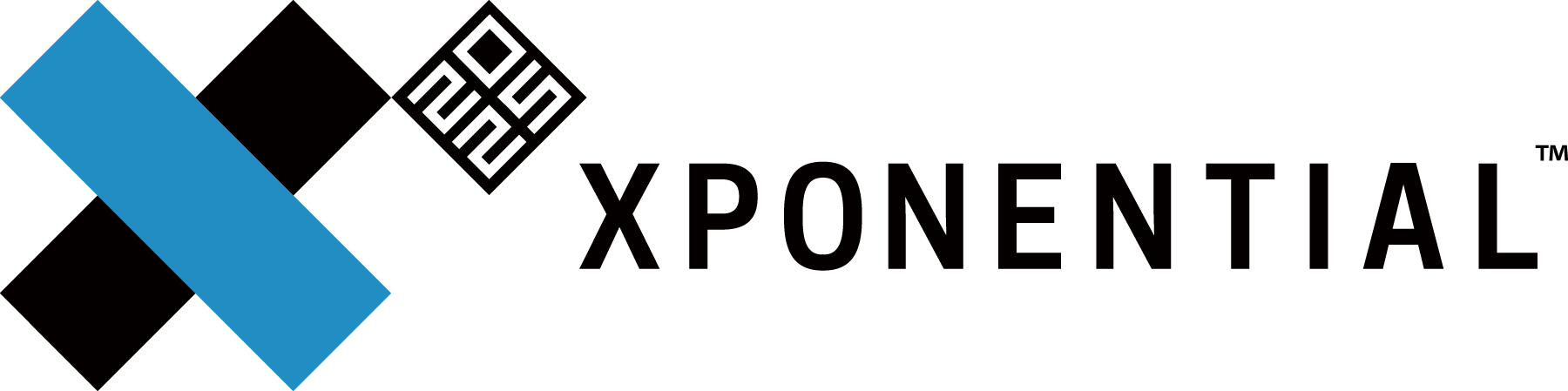
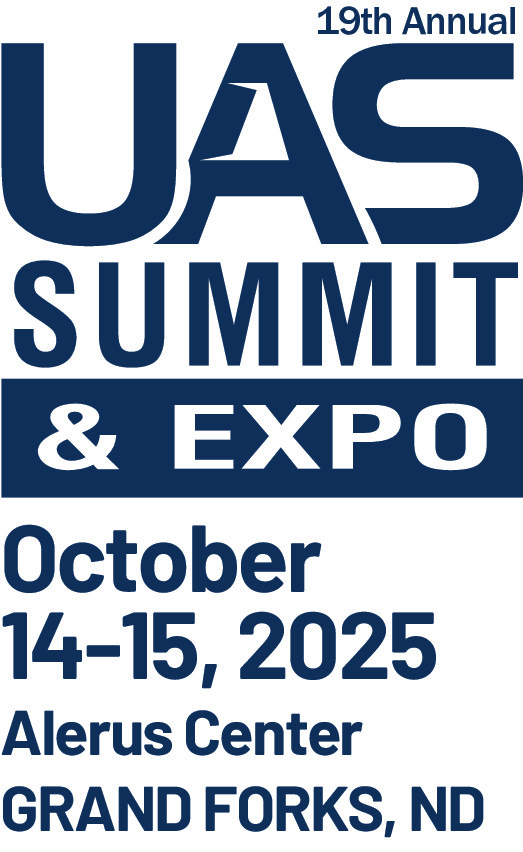

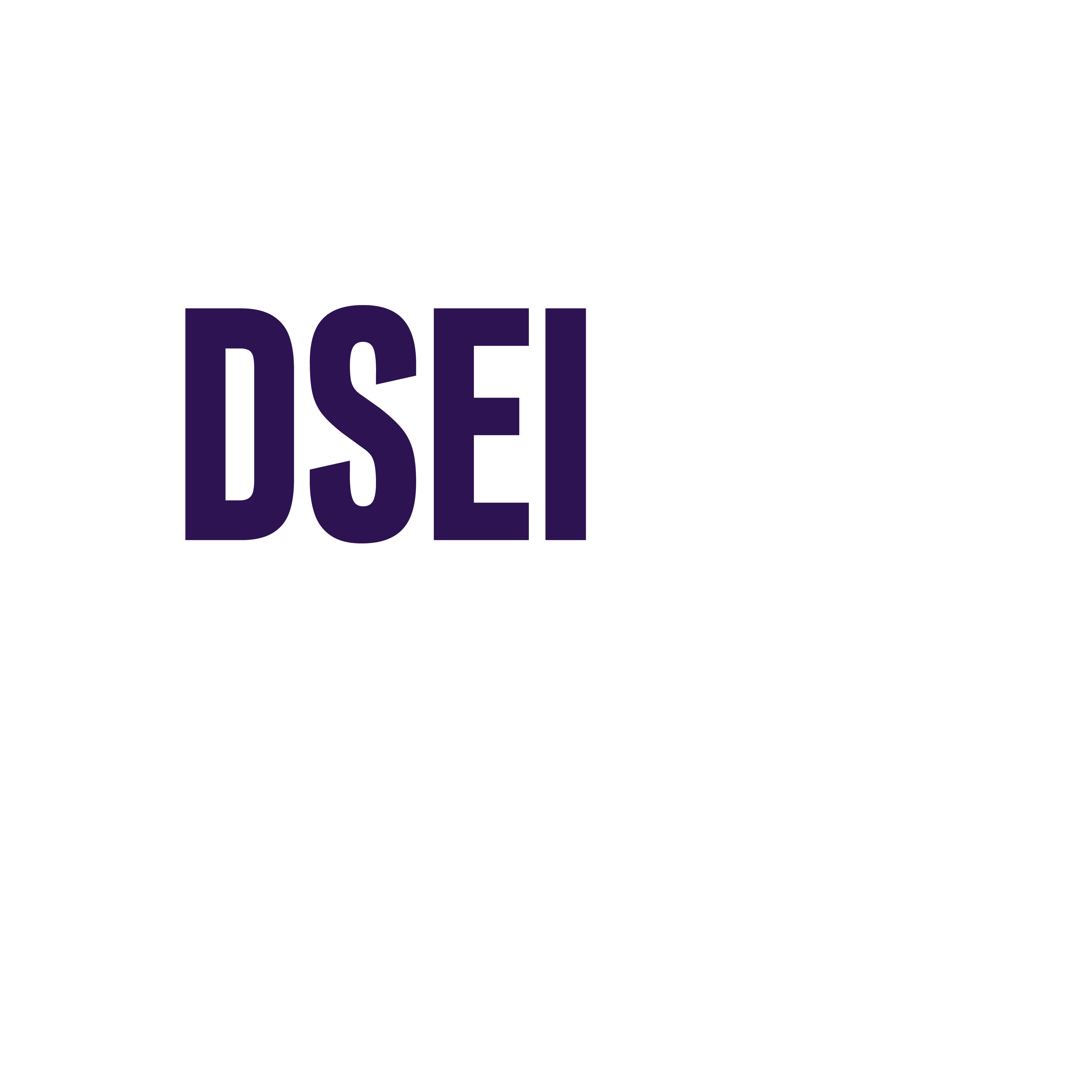
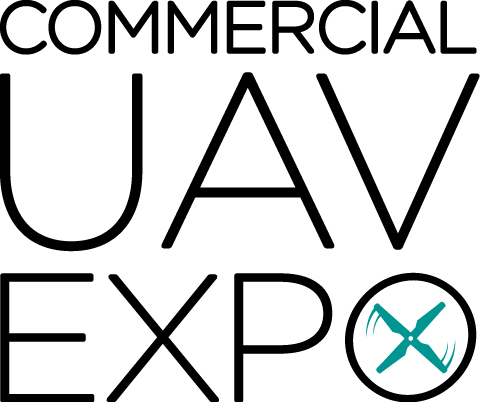
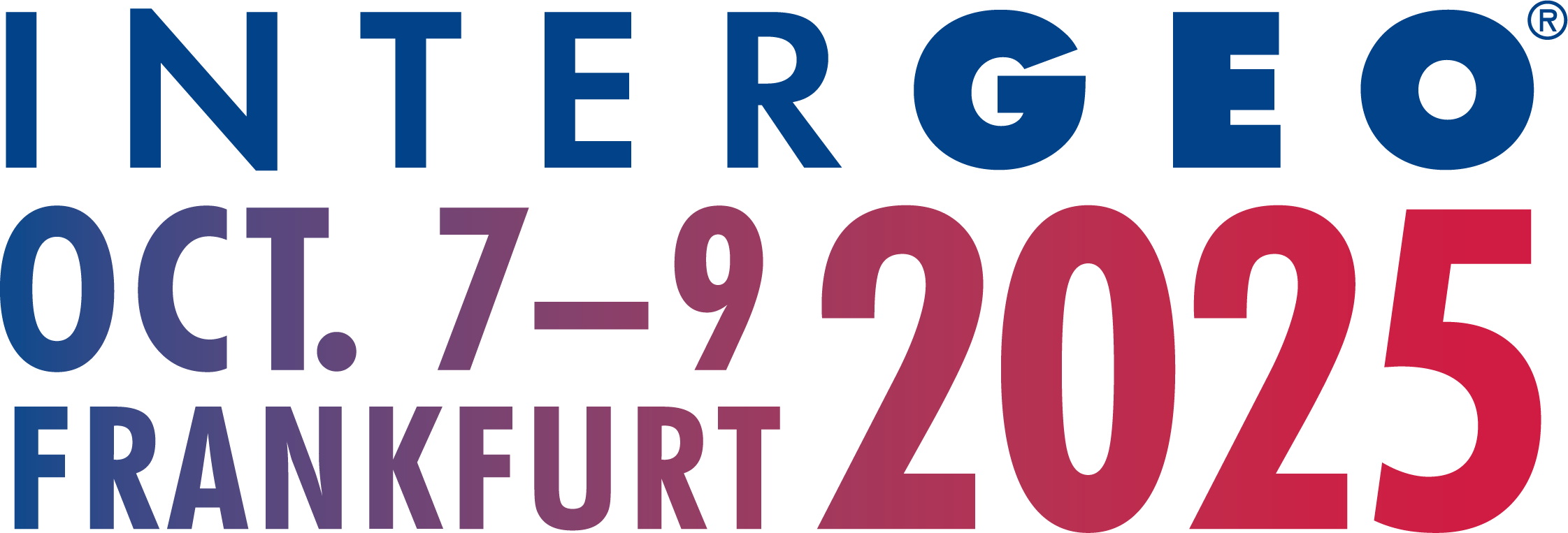
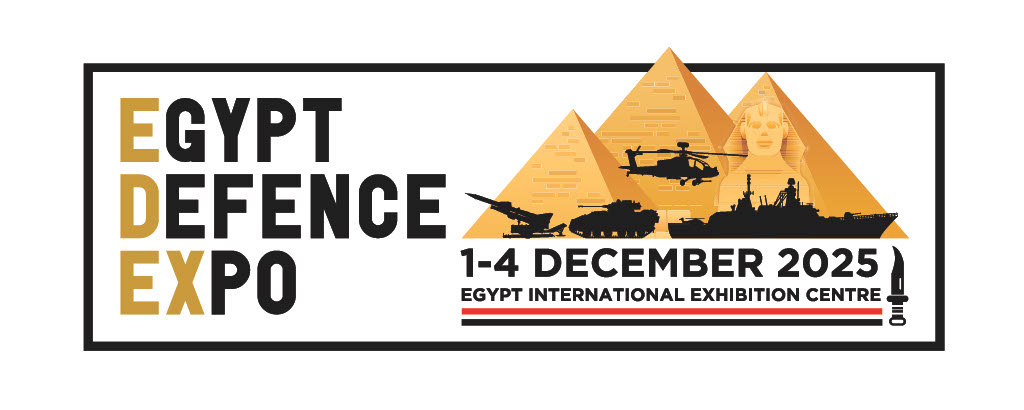
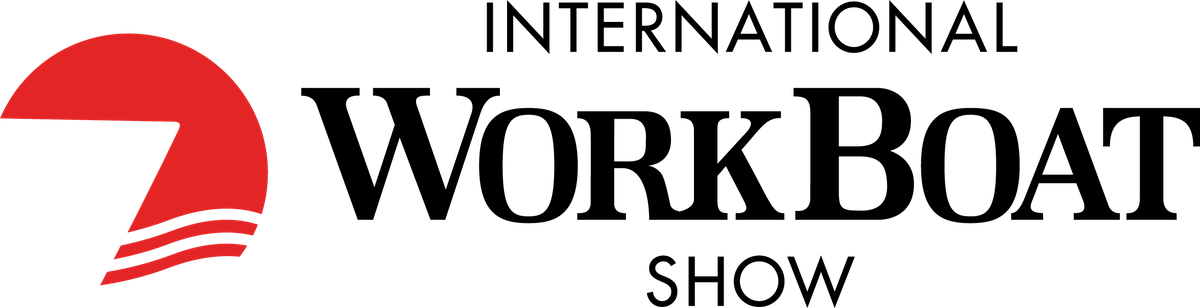