Uncrewed space vehicles
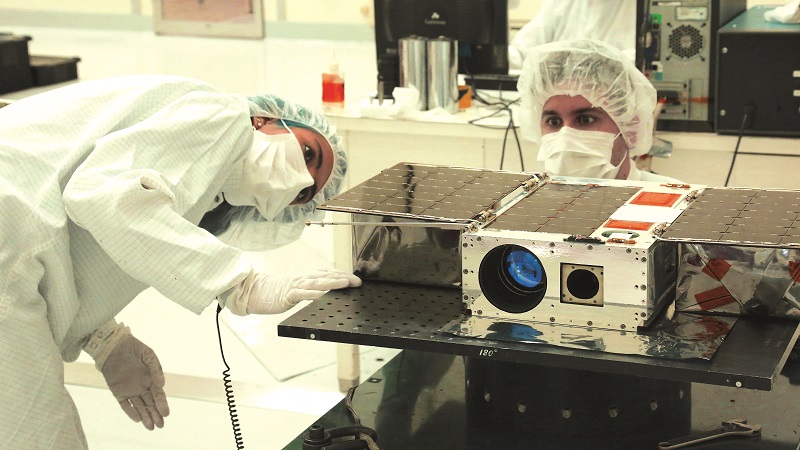
Small satellites are proving so versatile that they have become an industry in their own right. Rory Jackson reports
For many years, space companies have been developing novel uncrewed vehicle concepts for exploring and researching the Solar System. They include new types of rovers for trekking across the Moon and Mars, drilling machines for boring through the icy crusts of the Europa and Enceladus moons of Jupiter and Saturn, and UUVs for diving through those boreholes to see if an alien ocean truly lies beneath.
As these operating concepts evolve into working vehicles, a new industry of small satellites and the subsystems and launcher rockets supporting them has sprung up, paving the way for new missions aimed at furthering humanity’s understanding of space and our planetary neighbours.
Many of these are ‘CubeSats’, a concept developed and standardised by California Polytechnic State University and Stanford University as a ‘1U’ size, measuring 10 x 10 x 10 cm. However, 1U can also extend to larger sizes, including 1.5, 2, 3, 6 and 12U, and given the cost-effective platform they provide for new technology demonstrations, scientific experiments and so on, they have become an industry unto themselves.
And although they might cross into the territory of CubeSats, also being developed are a variety of ‘SmallSats’, which are defined as spacecraft with a mass of less than 180 kg. Within this are minisatellites that range from 100 to 180 kg, microsatellites weighing 10-100 kg, nanosatellites weighing 1-10 kg, picosatellites at 0.01-1 kg and femtosatellites from 0.001-0.01 kg.
With such a variety of spacecraft sizes, masses and therefore planned missions, some imminent and ongoing projects in uncrewed space exploration serve to illustrate the opportunities this new space industry offers.
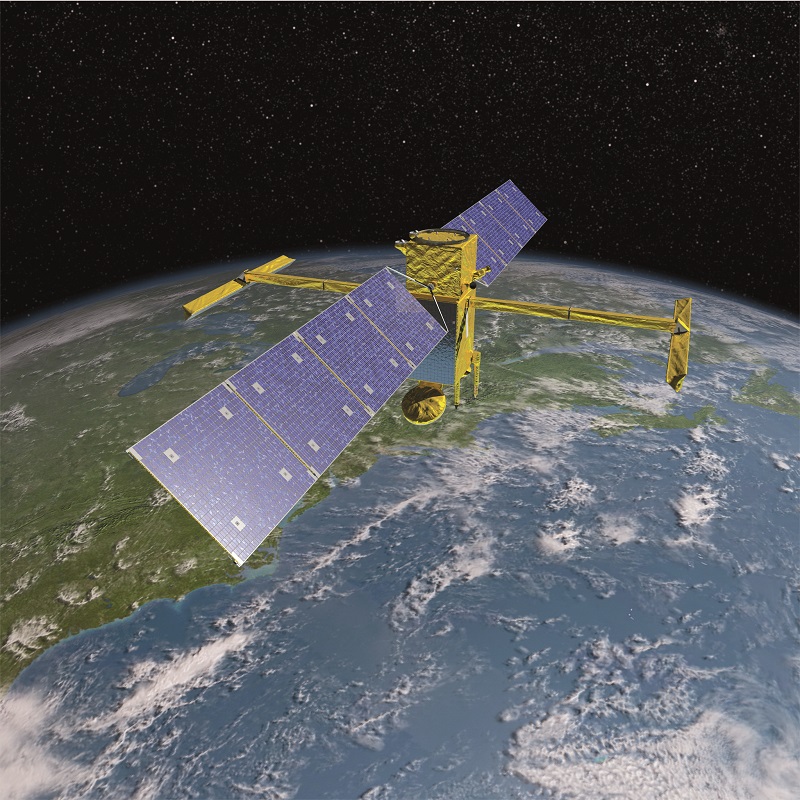
Environmental observation
Arguably, the most important use for new satellites is to perform cost-effective surveys of the Earth, given the planet-wide data they can deliver.
As a result, NASA’s Jet Propulsion Laboratory (JPL) has several CubeSat missions now in orbit, gathering data on a range of environmental parameters. The Geo-Cape ROIC In-Flight Performance Experiment (Grifex) for instance is a 3U CubeSat launched in 2015 to perform engineering assessments of a JPL-developed all-digital in-pixel, high frame rate, read-out integrated circuit (ROIC) with a frame rate of 16 kHz.
The core aims of the mission are to verify with real-world testing the performance, functionality and data integrity of the ROIC in space for use in instruments and missions revolving around imaging interferometry. The missions include geostationary coastal and air pollution event (Geo-Cape) surveys, and high spectra resolution studies and measurements of atmospheric compositions, from geostationary Earth orbit (GEO) or other altitudes.
Grifex has also integrated the Geo-Cape PanFTS (Panchromatic Fourier Transform Spectrometer), an imaging instrument designed to operate from GEO, with the CubeSat serving to demonstrate the PanFTS’ digital focal plane assembly and signal chain technology.
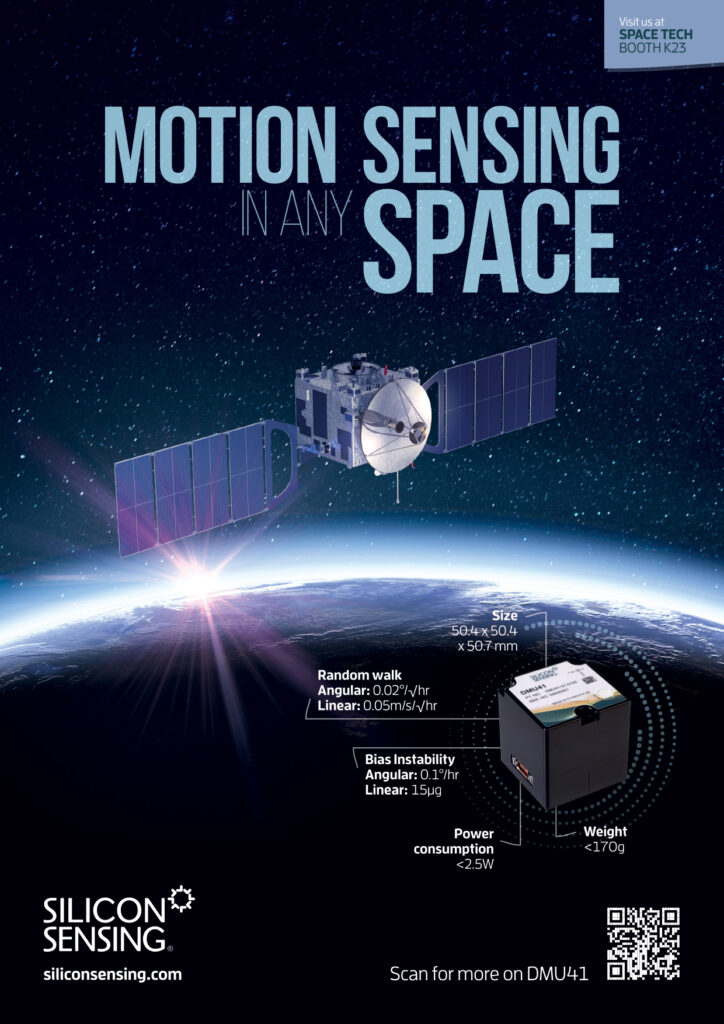
The PanFTS can measure a range of trace gases at high resolution, being sensitive in the UV, visible and IR wavelengths. It covers a spectral range of 260 to 3500 nm with a ground resolution of 4 x 4 km, and has a repeat cycle of 1 to 2 hours. As a result, its technology could support chemical transportation modelling, pollutant monitoring and assessing the amounts of ozone and aerosols among others in the Earth’s atmosphere.
With the study of such environmental parameters becoming imperative for most of the world’s governments, NASA’s international SWOT (Surface Water and Ocean Topography) satellite has in recent months been increasingly deployed for its orbital oceanographic data, NASA reported in September this year.
SWOT was developed for measuring the heights of every body of water on Earth. Following the 2023 summer however, its survey data has been used to better understand El Nino, the periodic climate phenomenon that disrupts the Earth’s weather. Given that water expands when warmed, El Nino tends to be characterised by higher than average sea levels as well as warmer than typical ocean temperatures, particularly along the US West Coast.
The spacecraft’s capability is achieved through the KaRIn (Ka-band Radar Interferometer) instrument, which uses two antennas spread 33 ft (10 m) apart on a boom to produce a pair of data swathes as it orbits the Earth to collect water-height measurements by bouncing radar pulses off the water’s surface.
Ben Hamlington, a sea level researcher at JPL, comments, “SWOT’s ability to measure sea surface close to the coast will be invaluable for researchers but also forecasters looking at things like the development and progress of worldwide phenomena like El Nino.”
Through this orbital data, and in combination with other sources, the US government’s National Oceanic and Atmospheric Administration has forecast a higher than 70% chance of a strong El Nino in winter this year, leading to a range of impacts on the weather and environment.
SWOT was launched in December 2022 as a collaboration between NASA and the French space agency, CNES (Centre National d’Etudes Spatiales), with contributions from the Canadian and UK space agencies.
A few months ago, NASA reported that a device called the Tropospheric Monitoring Instrument (Tropomi) has been used to explore how red solar-induced fluorescence (SIF) measurements could be used to detect Karenia brevis, a harmful red algae we discussed in issue 42 (February/March 2022) for researchers using UUVs in lakes to study factors influencing its growth and spread.
Tropomi has the capacity to measure fine wavelengths of light: it is designed for a typical pixel size (near nadir) of 7 x 3.5 km2 for all spectral bands, except in the ultraviolet 1 band, where it is 7 x 28 km2, and SWIR bands where it is 7 x 7 km2. That ability could help agencies and communities better forecast and manage harmful outbreaks of the algae.
The system is a payload co-funded by the ESA (European Space Agency) and the Dutch government’s Ministry of Economic Affairs and Climate Policy, Ministry of Education, Culture and Science, and the Ministry of Infrastructure and Water Management. It is deployed on the ESA’s Sentinel-5P satellite, and is designed principally as a spectrometer for sensing UV, visible, NIR and SWIR; these enable it to monitor ozone, methane, formaldehyde, aerosol, carbon monoxide, NO2 and SO2 in the atmosphere.
The Sentinel-5P was launched in 2017 as part of the ESA’s Copernicus programme of uncrewed environmental monitoring spacecraft. It measures 1.40 x 0.65 x 0.75 m, carries 156 Ah worth of batteries and consumes 1.5 kW in standard operation.
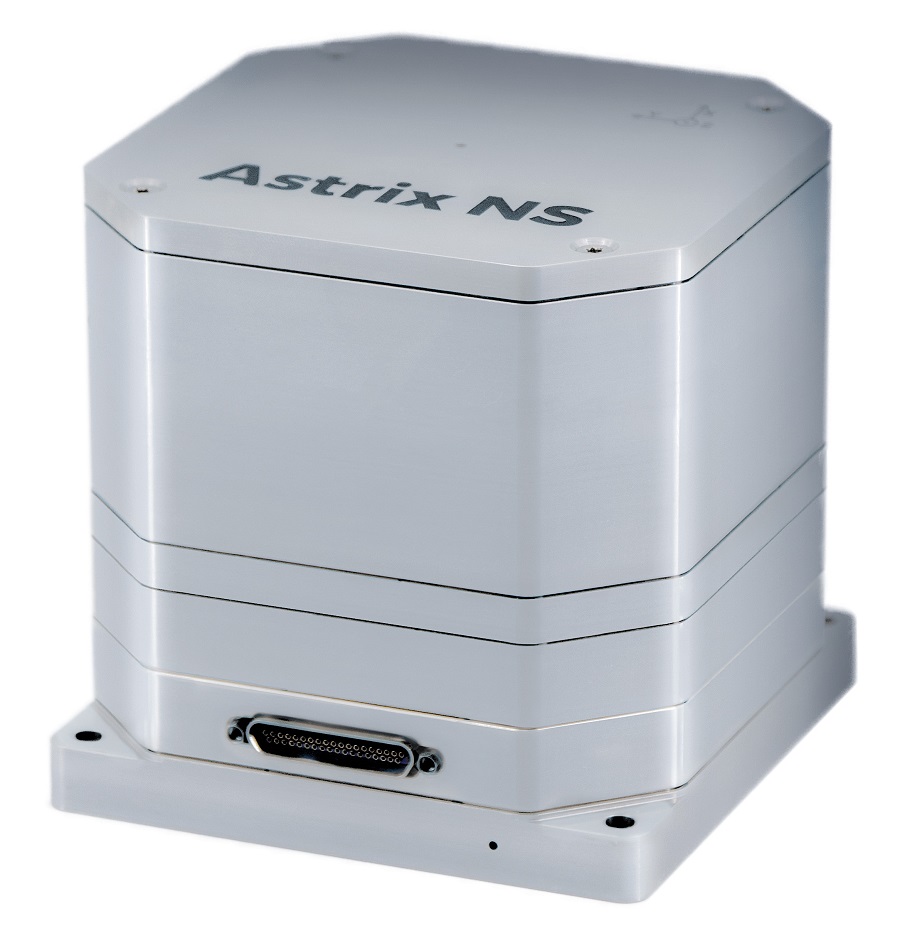
Orbital navigation
Asked to name the various technologies on spacecraft, people often think first of the rocket engines, solar panels and radio equipment, but the navigation systems aboard satellites and launchers are also mission-critical and highly complex devices that require meticulous engineering and qualification for use in space – failures in them can almost never be addressed hands-on by repair technicians.
Compared with terrestrial applications, inertial sensors made for space vehicles must be engineered with three unique considerations in mind. The first are the effects of operating in a vacuum, while the second is that the solutions must provide 8 to 15 years of uninterrupted use without servicing. Lastly, any cosmic radiation – varying as it does between different levels of orbit – must have no impact on the precision, accuracy or integrity of the sensors.
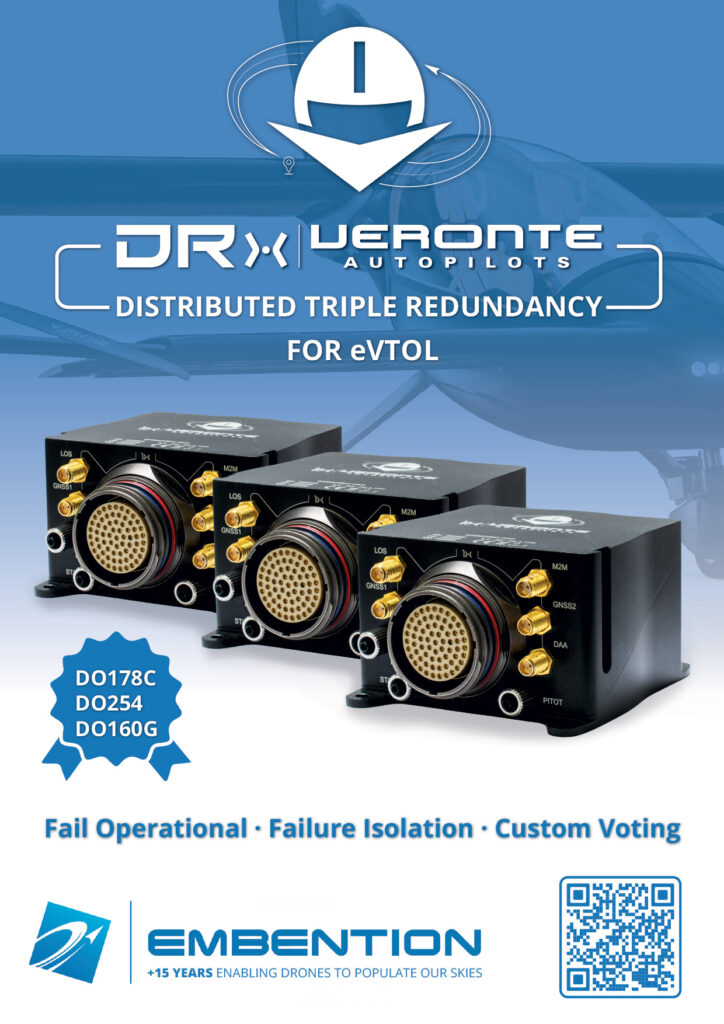
“If you fail to account for those three problems, you could lose the gyro,” says Elliott de Toldi, product manager for inertial systems in space applications at Exail. “Lose the gyro and you will lose the mission, because without stability, satellites can’t observe, transmit or receive effectively, and launchers can’t maintain course.”
Exail, through one of its two former companies iXblue, has been designing and producing space-qualified navigation solutions in partnership with Airbus Defence & Space for the past 20 years. This has come primarily through supplying its fibre optic gyroscopes (FOGs) for GEO and LEO (low Earth orbit) applications, although many of its quartz (silicon dioxide) accelerometers are used in orbital satellites as well, and both sets of products also deliver inertial data in launchers and interplanetary space missions.
Exail’s clients in the space industry include Arianespace’s Ariane 5 and 6 launcher rockets, the ESA’s Aeolus, Sentinel 2, Solo and MTG programmes, and the ExoMars mission planned for launch in 2028. Exail says that through these various projects, its FOGs and accelerometers have amassed more than 6 million hours of orbital flight without incident.
Over the past 20 years, the Astrix 90 and 200 FOGs have been supplied for space applications by Airbus through its partnership with Exail (with both solutions embedding Exail’s technologies). More recently however, Exail has developed its own space gyroscope, the Astrix NS, to address the new challenges faced by the space industry.
The Astrix NS is aimed at newer spacecraft like SmallSats being produced at volume. It weighs 1.4 kg, consumes up to 7 W until end of life (EOL) with an angular random walk (ARW) of 0.005o/√hour, as well as an EOL bias stability of 0.2o/hour (less than 0.02o/hour at start of life).
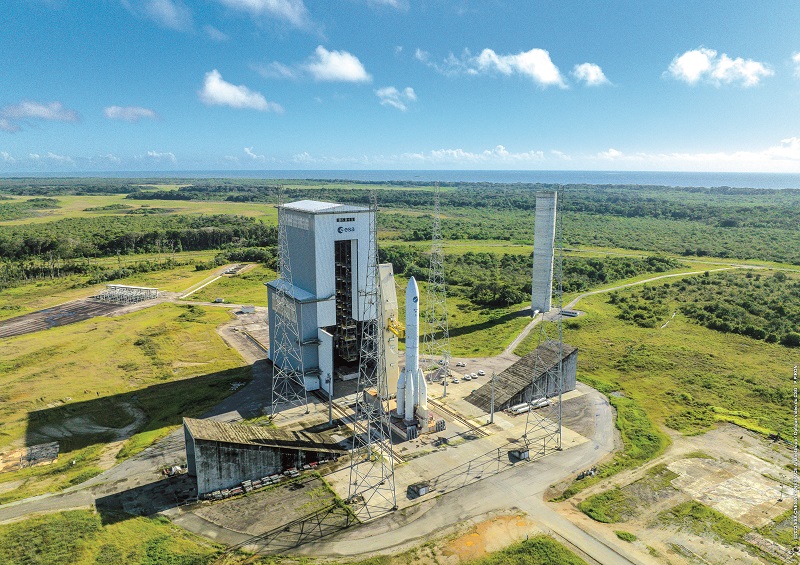
All of Exail’s FOGs are interferometric systems, and their operating principles are the same as its terrestrial FOGs, albeit each part being qualified for use in space according to ECSS (European Cooperation for Space Standardisation) rules. The qualification requirements are applied to the company’s optical fibres, diodes, pottings and integrated optical chips, along with its PCBs and all other electrical, electronic and electromechanical components as defined by the ECSS.
“To prevent problems arising from the vacuum of space, we have a team dedicated to the thermal design of the system,” de Toldi says. “One big problem in vacuum conditions is that we can’t dissipate heat from our components, as there’s no air, so we need to transfer it through the base mounting plate.
“The other main problem is outgassing, which is really bad for Earth observation satellites as gases emitted from components can have an impact on their optical elements, but the gyros need to be near the optical payloads to minimise interference in attitude readings. Our circuit boards and everything used in potting and adhesives are most at risk of outgassing, so a lot of work goes into selecting the right components for that application.”
To achieve product lifetimes for the required number of years, reliability analyses are performed in-house to identify ways to prolong their MTBFs, including installing triple redundancies in components and using more than one inertial unit on each craft.
“More recently though, we’ve been running analyses using the FIDES method,” de Toldi adds. “This is a guide for calculating reliability estimates for electronic systems, and based on what those results say about our reliability, many of our clients could use just one Astrix NS instead of the two you would require for cold redundancy.
“In general, GEO satellites will use our more robust gyros and in higher numbers than LEO and launcher craft. That comes from radiation being most severe at GEO levels, and LEO satellites only need to last 7-8 years, as well as launchers being used just once unless they can be landed, compared with 8-15 years for GEO systems.”
Exail adds that the new Astrix NS has been qualified for use in 15-year GEO missions and 8-year LEO missions.
“We’re also developing our accelerometers and gyros together as IMUs for interplanetary missions through the Eurisa project, such as collecting mineral samples from the Moon or Mars and then bringing them back to Earth,” de Toldi notes.
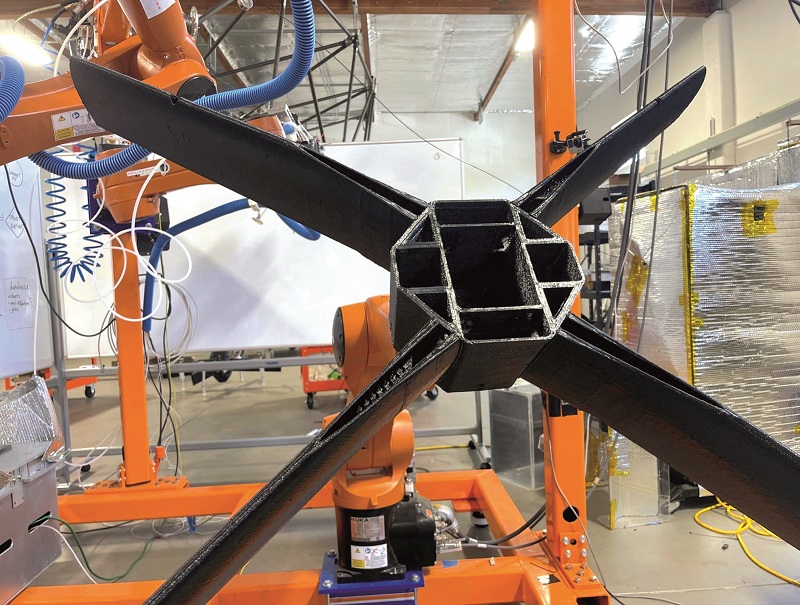
Orbital industry
As well as providing a high vantage point for observing and surveying different facets of the Earth’s atmosphere and topography, the zero-gravity conditions in orbit also lend themselves to highly efficient production facilities. The absence of dust and other contaminants in space effectively makes for a natural ‘clean room’, and various processes involved with the production of different goods can be accelerated without the burden of gravity and weight.
To that end, some organisations are pursuing a path towards full-scale orbital construction facilities. One of these is Space Cargo Unlimited, which has signed a contract with Thales Alenia Space to develop the REV1, a reusable uncrewed spacecraft intended for production applications in orbit.
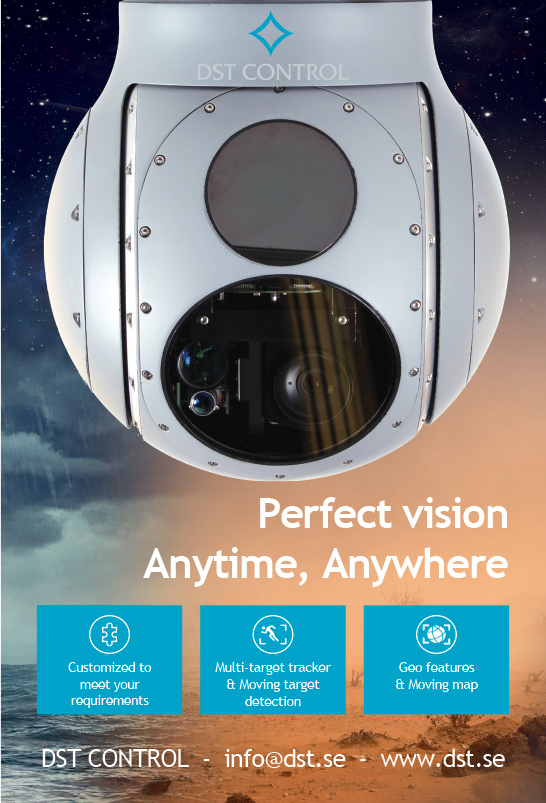
The company has a few key areas of interest. One is pharmaceuticals, as the company anticipates space microgravity will aid in protein crystallisation, a process vital to discovering new medicines but difficult to achieve on Earth.
Similarly, it expects additive printing of organ tissue and even complete organs to be optimised in microgravity, as will micro-encapsulation. This is a process in which compounds including biological material can be sealed inside another material, potentially of 1 µm to several 100 µm thickness, to protect them against environmental conditions, both of which could make huge differences to medical supplies to the Earth.
Lastly, it proposes that developing new forms of plant life adapted to microgravity could lead to hardier species of crops, and hence higher yields on Earth. The company therefore aims to study how this could be achieved and how such orbital agricultural research could be industrialised.
Although the REV1 is intended to be around 4.5 m long, it is also being designed to carry up to 1000 kg of payloads, including additive printers, bioreactors and passive containers. This capability is enabled through the absence of any life support or habitation systems needed on crewed spacecraft. Some pressurisation will still be maintained inside the REV1 though, particularly for biological experiments.
Manufacturing processes and scientific experiments would take place after the REV1 docks with an autonomous orbiter station in LEO; the station is being designed by Thales Alenia Space. Solar panels and electric rocket engines will enable the orbiter to stay aloft for about 10 years, or about 20 REV1 missions.
Construction is another industry that stands to gain from moving operations into orbit. Given the lack of gravity, workers or robots could use a propellant pack or climbing frame to travel in any direction around an orbital shipyard for example, assembling chassis and then climbing around them as needed to install subsystems or hull parts in whatever orientation desired by the designers.
With that in mind, Orbital Composites continues to work on its technologies for in-space servicing, assembly and manufacturing, and has been granted a contract for exploring ways towards these by SpaceWERX, the innovation arm of the US Space Force and a subgroup of AFWERX, part of the Air Force Research Laboratory (AFRL).
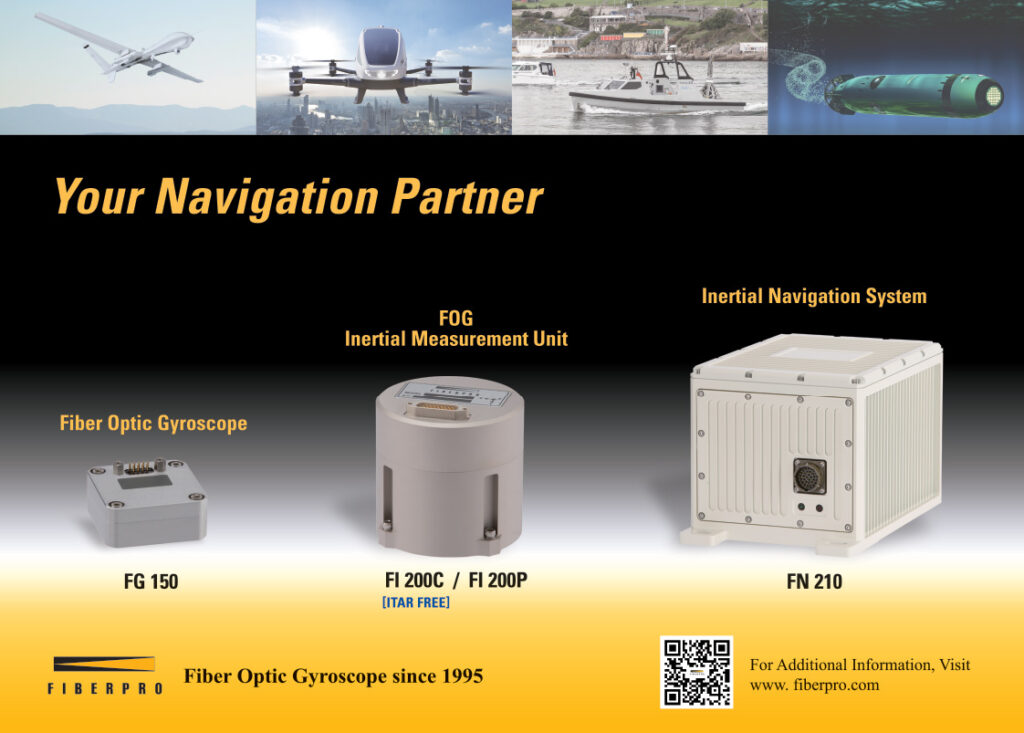
Part of the project is to examine how uncrewed orbital vehicles could remediate space debris by locating and approaching them, then assessing how best to deal with them. If the debris in question is a defunct satellite for example, ideally the vehicle would repair, refuel and reposition it as needed for it to continue in service. Safe de-orbiting or recycling would follow if the satellite could not be repaired.
Orbital was also recently granted a Direct-to-Phase-II SBIR contract from the US Air Force to develop carbon-carbon (C/C) composite manufacturing technology, with which C/C parts could be printed for American hypersonic craft.
C/C consists of carbon fibre reinforcement in a matrix of graphite, and is best known as the material used in the nose cone and leading edges of the wings on the NASA Space Shuttle. Orbital notes however that it can also be used in rockets’ nozzle linings and various structural components, satellites’ chassis and antennas, aircraft brake discs and landing gear, other vehicles’ brakes and structural components, and hydrogen fuel cell powertrains.
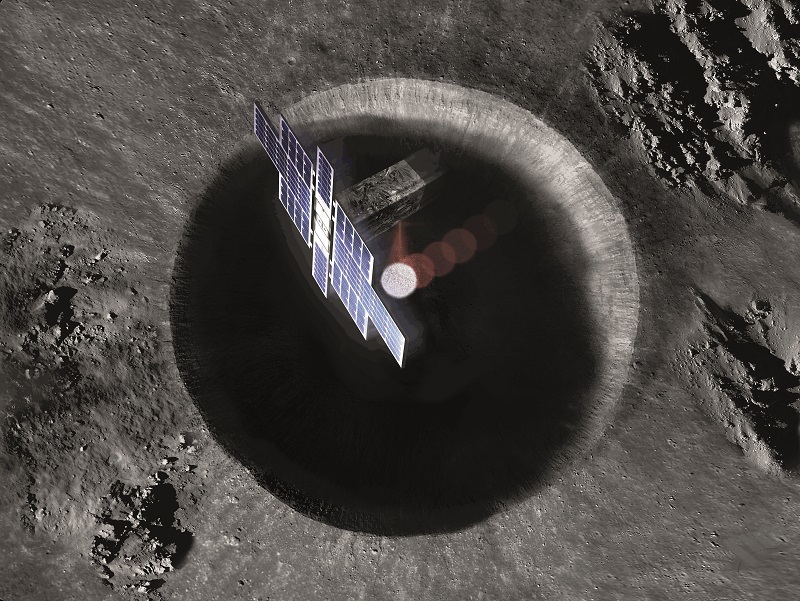
The Moon
Further out from Earth, CubeSats and SmallSats are being used to gather information for the following generation of spacecraft. NASA’s recent Lunar Flashlight for instance was sent to the Moon to survey for surface water ice in craters on the lunar South Pole.
The Flashlight is a 6U CubeSat, being just under 14 kg in launch mass. Although the mission was aborted earlier this year, the project still fulfilled aims that will contribute to future missions.
For one, its propulsion system ran on a green monopropellant (a fuel that does not need a second tank of additional reactant). The propellant is known as Ascent (Advanced Spacecraft Energetic Non-Toxic) and was developed by AFRL’s Rocket Propulsion Division.
It has been formulated to deliver a 50% increase in density-specific impulse over hydrazine monopropellants, which are considered to be among the state of the art. In addition to its performance advantages, Ascent decreases the handling hazards compared to hydrazine, and so requires fewer personnel and less equipment during its ground operations on Earth or wherever else it might be used.
The custom-designed, Ascent-fuelled propulsion system was developed by NASA’s Marshall Spaceflight Center and Georgia Tech’s Space Systems Design Laboratory to deliver over 3000 Ns (Newton-seconds) of total impulse for the orbit insertion and attitude manoeuvres.
Its design uses metal additive manufacturing, custom electronics and unique micro-fluidic components, fitting overall a 2.5U volume in a bay inside the 6U vehicle, with a total wet mass of just under 6 kg. The mission was aborted en route to the Moon owing to underperformance of three of the craft’s four thrusters.
This has been attributed to debris build-ups in some of the fuel lines. Despite that, NASA found that many components throughout the propulsion system exceeded performance expectations, and that its non-toxic alternative to hydrazine performed well in space.
Also, its survey technology, consisting of a reflectometer equipped with four lasers (which emit NIR light in wavelengths absorbed by surface water ice), performed well in all tests during the mission, satisfying NASA that the payload design will detect Lunar surface ice if applied as such.
Also demonstrated were NASA’s new Sphinx flight computer, developed by JPL as a low-power computing system capable of withstanding deep space radiation. Also, an upgraded Iris radio will enable future small spacecraft to rendezvous and land on Solar System bodies.
Jupiter
Larger satellite vehicles start coming into play when venturing to the largest bodies in the Solar System. The ESA’s Jupiter Icy Moons Explorer (Juice) for instance was launched earlier this year, and its mission is to perform observations of the gas giant and its three ocean-bearing moons (Europa, Callisto and Ganymede) using a range of remote sensing and geophysical instruments.
Through this payload it will study the three moons, in particular the bodies of liquid water that are believed to exist beneath their icy surfaces. The results of those studies are expected to help gauge their potential for harbouring lifeforms.
Juice measures 16.8 x 27.1 x 13.7m and has a dry mass of 2420 kg. Within that mass are 10 scientific instruments, including a laser altimeter, a magnetometer, a spectrometer for visible and IR imaging, a sub-millimetre wave instrument, and a radio and plasma wave instrument.
As of September this year, Juice had travelled 370 million km, and is expected to complete its research in 2031.
Meanwhile, NASA’s Juno spacecraft is already orbiting around Jupiter, having been launched in 2011 to research the planet’s composition, magnetic field, gravitational field and polar magnetosphere.
The satellite is also looking for signs of how Jupiter was first formed, including measuring its mass distribution, looking for indicators of a rocky core, studying the amount of water in the deep atmosphere, and researching its winds, which can reach speeds up to 620 kph.
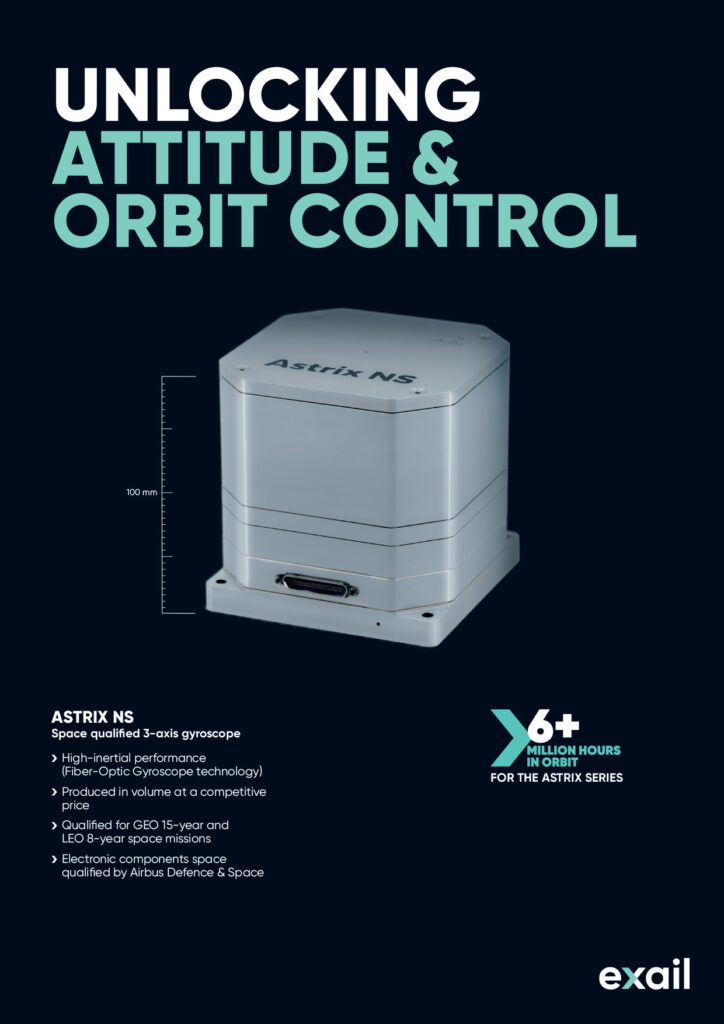
Juno has a cylindrical body of 4.6 m diameter and 20.1 m length. Included in its payload is a microwave radiometer with six antennas that can penetrate Jupiter’s clouds to a depth of around
550 km to measure its atmosphere for the presence of ammonia, water (and hence oxygen and hydrogen) and temperature, at various altitudes.
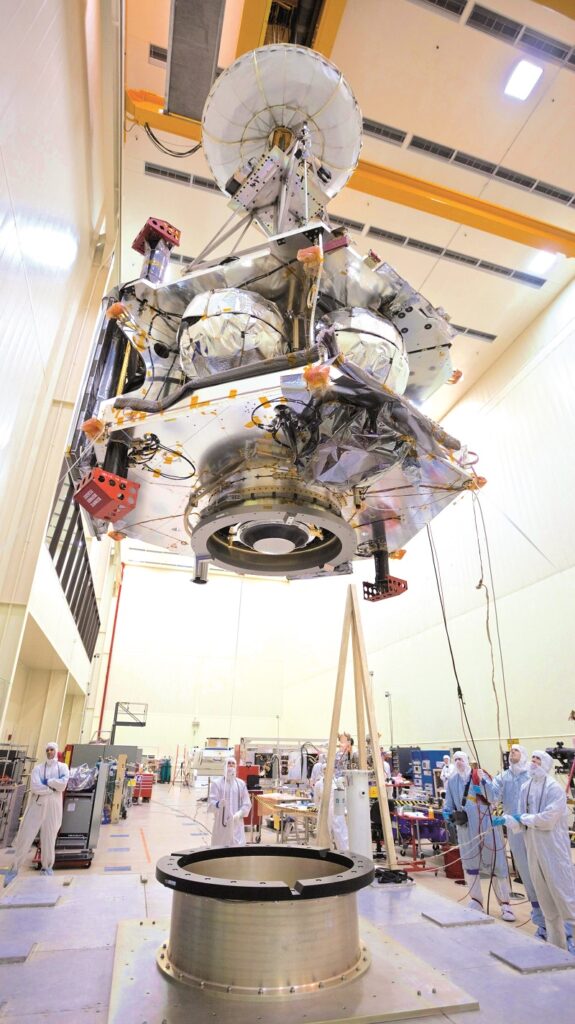
Summary
Juice and Juno are notable among exploration satellites as they are among the first to visit the outer planets without using radioisotope thermoelectric generators – essentially nuclear batteries.
Their powertrains instead make use of newer solar technologies. Juno in particular features the three largest solar panel wings ever deployed on a planetary uncrewed spacecraft, setting a precedent for future innovations in interplanetary power.
Amid all these advances in small satellite technologies, crewed spacecraft such as autonomous Lunar transport rovers and SpaceX’s Starship continue to be developed, with the latter making a widely televised (and uncrewed) test launch in April this year.
That launch did not make its tentatively planned splashdown in the Pacific Ocean after its intended journey through the atmosphere and into orbit, instead ending prematurely in a remotely forced termination about 4 minutes after launching. However, it was still the most powerful rocket stage ever launched, and gathered invaluable data needed for launching larger spacecraft in the future.
A primary cause of the failure stemmed from three of the rocket’s engines being disabled during the launch sequence, with several more failing in mid-flight. However, given the range of successful powertrain technologies available for autonomous space vehicles, missions can continue to be launched as often as possible. That can only add to our understanding of the conditions in outer space for when we follow them.
UPCOMING EVENTS
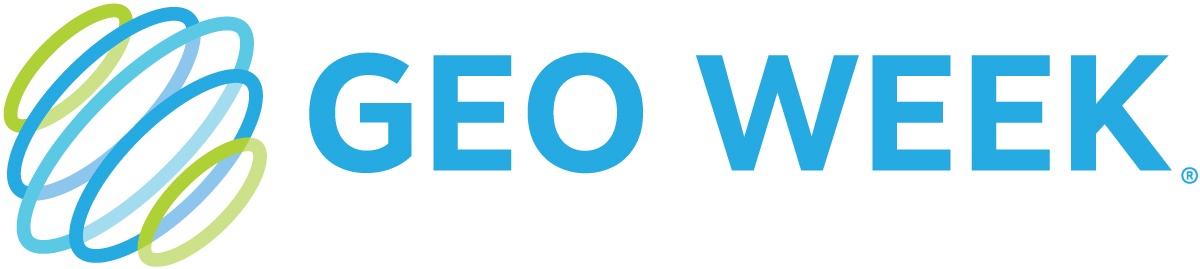
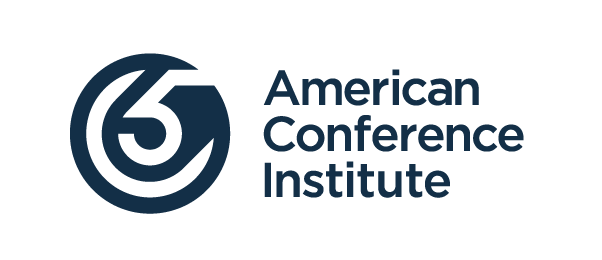
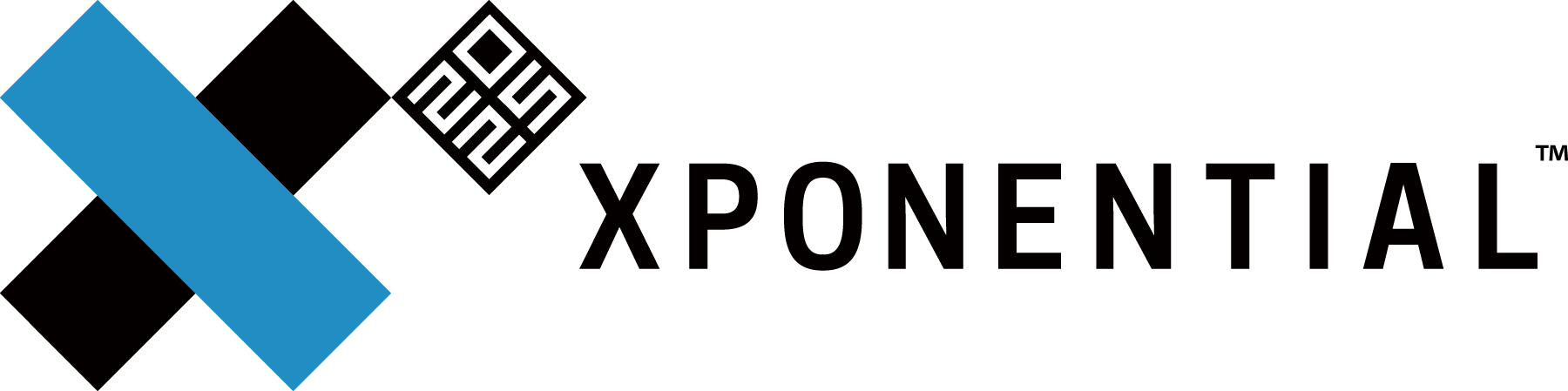
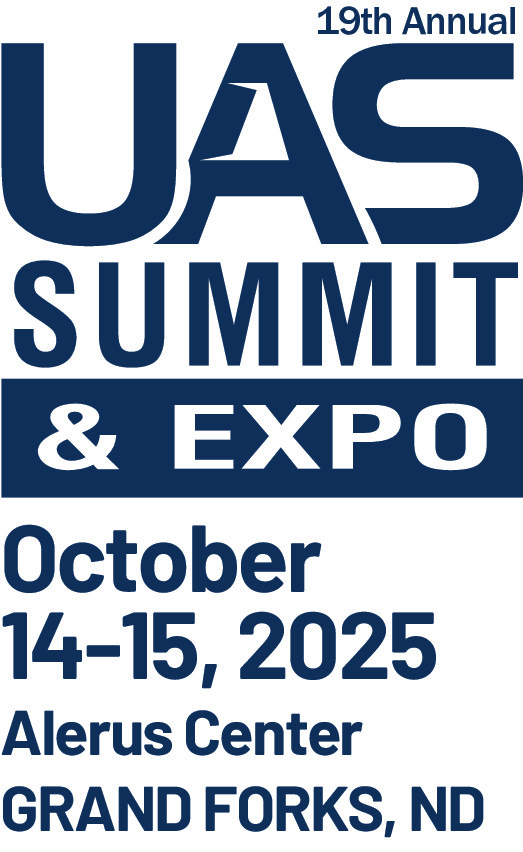
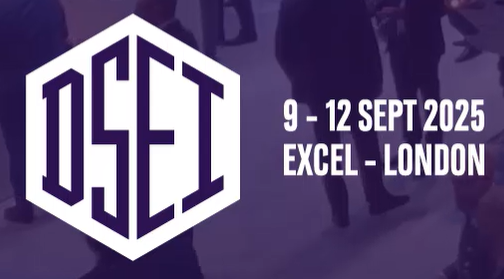
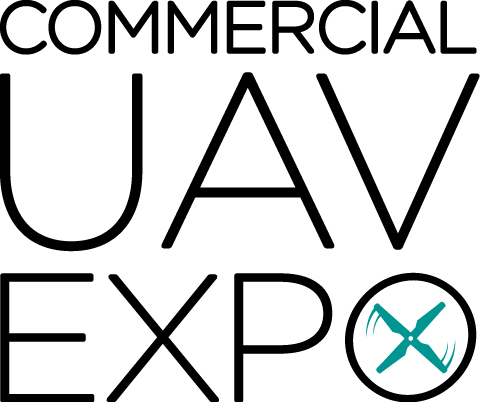
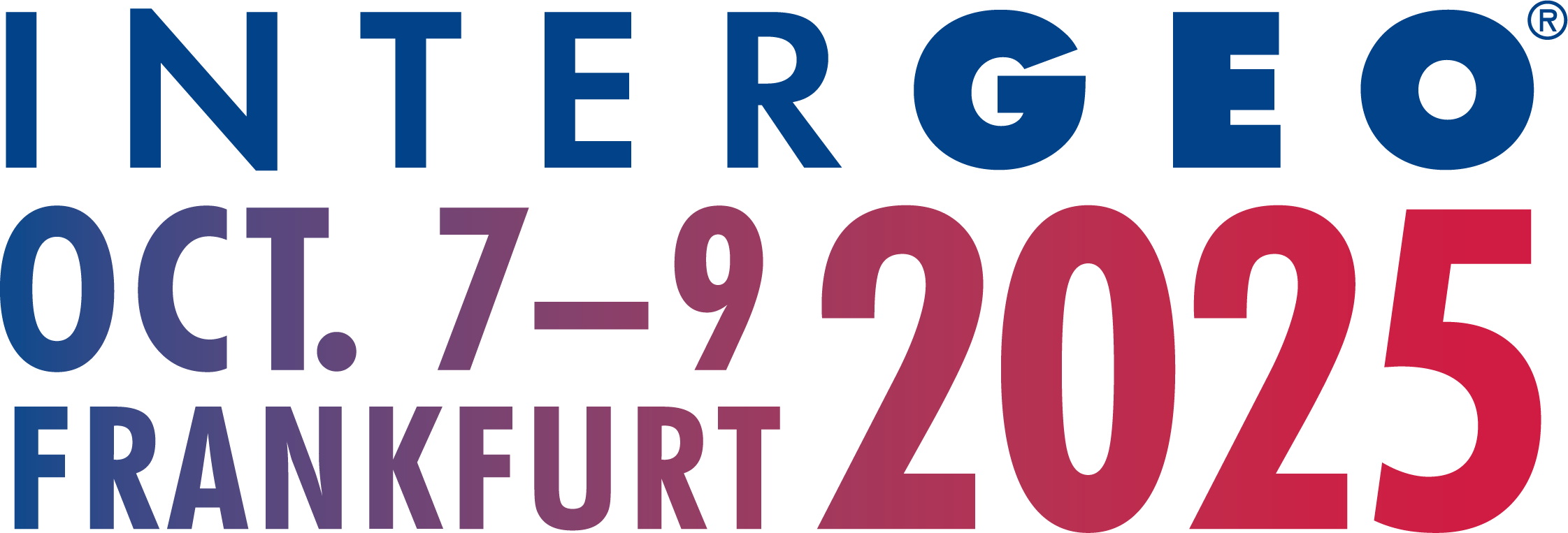
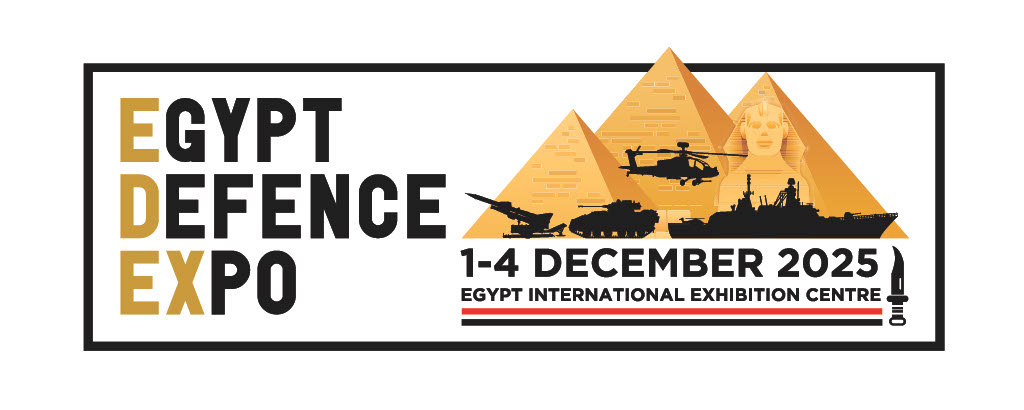
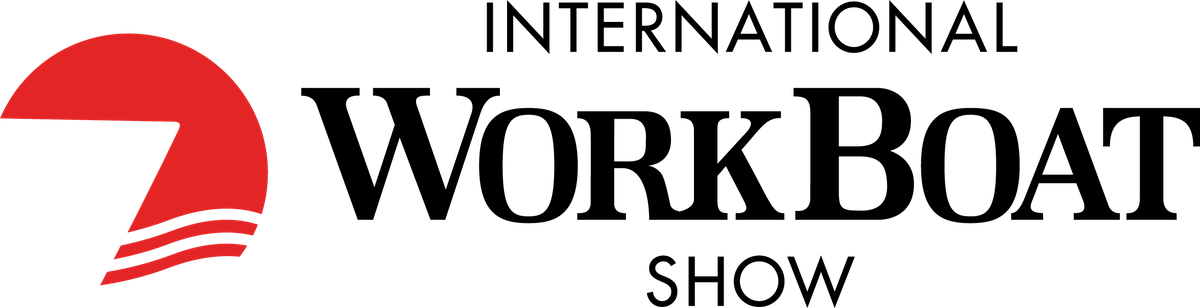
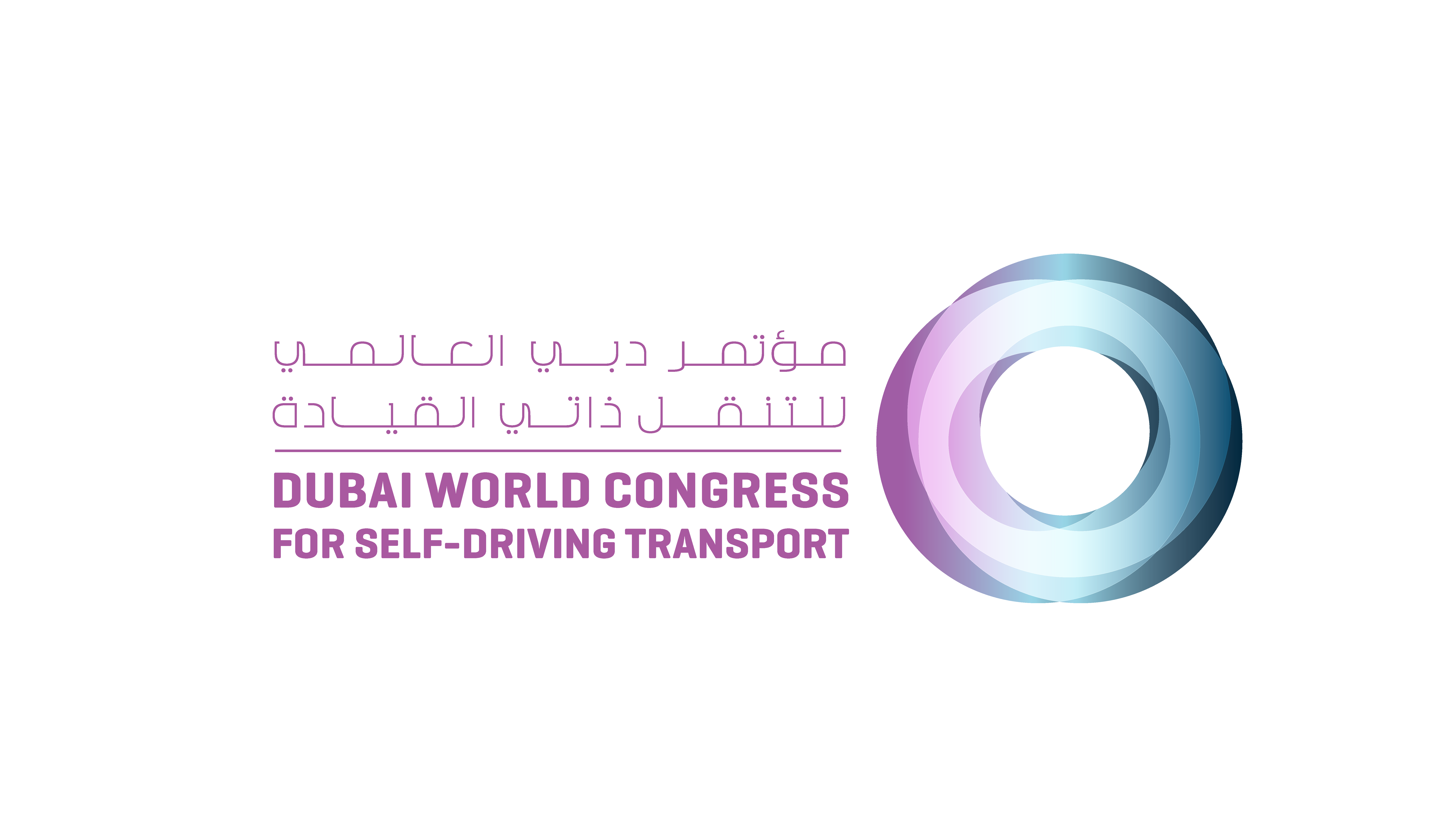
