Skygauge
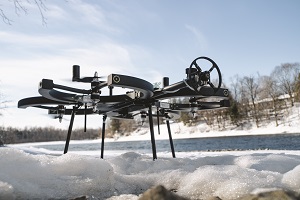
(Images courtesy of Skygauge Robotics)
Rory Jackson looks at a UAV designed for taking on the risk to humans working at height
This publication has featured many ways in which infra-red (IR) cameras, Lidars and other contactless sensors can be used to great effect by UAVs and UGVs to inspect industrial buildings. But many countries have regulations requiring ultrasonic inspections of high-rise metal structures at routine intervals, and ultrasonic sensors or gauges must make physical contact with an object to reveal its thickness and integrity.
The normal approach to such ultrasonic inspections is much like that for other contact work on industrial structures at height, such as painting or welding: either scaffolding is erected for workers to climb up, or a rope access system or cranes can be used by them to tether their way to the high-up job site.
All three of these methods for getting a human onto an industrial structure at height are expensive, time-consuming and dangerous. Naturally, substituting uncrewed systems for people in dull, dirty or dangerous work is a familiar and successful idea to us, but getting a UAV to precisely hold an ultrasonic tool against a vertical wall is extremely challenging, whether it’s autonomous or remotely piloted – given that a multirotor must pitch down to move forwards, level out to hold position, and avoid its rotors making any physical contact with any solid object to prevent its self-destruction.
Skygauge Robotics’ answer to this challenge is a UAV (eponymously named) designed with four coaxial rotors, which can articulate independently from one another, and a combination of sensors and autonomous behaviours to control them. Together, these keep the airframe steady during hover, and compensate for the sudden inertia changes caused by initiating physical contact with standing structures, as well as for wind or gusts that could break that contact while the UAV carries out its work.
Skygauge Robotics CEO Maksym Korol says: “Aerial ultrasonic testing has been our first commercial application with our UAV, because it’s a huge and established market, and one of the biggest reasons why you find as much scaffolding and rope access as you do when looking up at plants, factories, chimneys, tanks and other industrial assets.
“It isn’t a replacement for IR surveys; the two are quite apples and oranges from each other, especially given that there are regulations mandating certain types of inspections for different types of industrial structure.
“Standard API653 for storage tanks, for instance, dictates that you have to check the thickness of their metal walls every five years – maybe more often, depending on what you find in terms of corrosion rates – so you simply must do it. There is just no substitute for ultrasonic thickness testing. It has been done for decades across all sorts of industrial sites and our customers are now doing it by drone.”
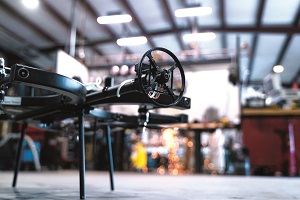
The Skygauge UAV
The Skygauge UAV is a coaxial quadrotor (or ‘X-8’, as some have referred to the configuration) with four shrouded rotor pairs and a horizontal boom extending from the front of the airframe, on which an ultrasonic gauge is installed for inspection work. It weighs approximately 7 kg and measures around 90 x 90 cm x 40 cm when deployed (or 70 x 70 cm when collapsed and packaged into its standard carry case).
Battery-electric, the system flies for 10 minutes between recharges or battery swaps, which Korol admits is short for multirotors nowadays.
“But, given that it rarely flies more than 100 m away from where its technicians and spare batteries are, extending flight time really isn’t an urgent focus of our development,” he says. “It just lands, we replace batteries, and we keep on going. Other industrial inspection UAVs might fly kilometres and kilometres away, but that’s not our use case at all.”
The original founder of Skygauge Robotics was Linar Ismagilov, who invented and designed the UAV, and is now chief design officer. The concept first came to him at high school, while mulling how UAVs might perform more tasks than the photography sessions they were limited to at the time.
“He didn’t have a clear picture then of the mechanics required or of a niche use case; more a feeling that one could create a UAV capable of interacting with a physical environment, and be more stable and manoeuvrable than multirotors generally are today,” Korol says.
“A multirotor that has to pitch or dip around to move around is never going to do anything needing a stable or steady hand, he figured.”
After forming a concept for an alternative UAV design in 2015, Ismagilov met with Korol and Nikita Iliushkin (now chief commercial officer), who co-founded the company with him. Together, they engaged in R&D for the UAV, until receiving their first funding round in 2018, whereupon they were able to build and fly a working prototype.
In 2019, the Ontario-based Skygauge was invited to join HAX Accelerator, whose main offices are in San Francisco, Shenzhen and Tokyo. This gave the three men access to wider expertise, investment and suppliers.
In the following year (during Covid), the trio spent six months in the UK with a prospective client, developing a ConOps for using their UAV in ultrasonic testing, and they demonstrated it to other interested parties, leading to considerable further funding.
“Since 2020, we operated in a more professional manner, growing the team to 15-25 people, and redesigning the prototype into a sellable, shippable product, with deliveries beginning in 2023 to customers around the world who had been waiting for it,” Korol recounts.
“We built and sold an initial production run of 10 units in the first half of last year. We’ve since delivered 25 further units and signed contracts for some more. Some of those users are here in Canada, some are in India and close by in the Middle East, and multiple companies we sell to are in The Netherlands, where there are very positive attitudes towards drones and robotics for industry.
“We are also starting to sell in South America, where we’re seeing considerable and fast-growing interest in commercial uncrewed systems, and we’re about to close a contract back in the UK too.”
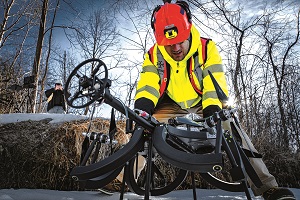
Pre-flight preparations
Most operations are carried out by the customer’s facility staff, such as maintenance technicians and inspectors, with Skygauge only operating for clients in the event of a demonstration or a particularly challenging use case.
Skygauge does, however, develop a ConOps, and hence a set of instructions for how customers should use and operate the UAV. To do this, it first takes delivery of a client’s past inspection reports to determine an inspection pattern for the pertinent infrastructure.
“So, if they have a 40 m flare stack that they need inspected, we can discern from those reports and their own comments to us if they want, as an example, a set of inspections across the north, east, south and west scan lines, which are vertical lines of points along which these types of ultrasonic inspections normally get performed,” Korol says.
“Picture a grid being laid or wrapped around the surface of this cylindrical structure, and then needing to take a measurement at every grid intersection; that’s the basic idea. Maybe an inspection at every metre, with four points around the tower – that would mean 160 measurements for that 40 m tower.”
Once a flight plan has been created to achieve these measurements, the UAV is brought out of storage, unpacked and set down near the structure – ideally in a location free from collision hazards such as pipes, wires or other occlusions, and where a sky view is available for GNSS.
“Although you’re unlikely to get gusts of 20 knots in an industrial area with a lot of structures, it’s still important to make sure there aren’t really strong winds blowing, given how close to buildings the UAV flies,” Korol adds.
The UAV internalises all self-tests and self-checks within the realm of possibility. Upon activation and throughout its flight it engages in autonomous condition-monitoring of the state of its GNSS feed, servos (for articulating the thrusters), thrust motors, batteries, internal network, computers and onboard collision avoidance sensors (a camera and Lidar).
“If any subsystem is detected as not running in a nominal state, the user is alerted. And in some products we install a subroutine, which prevents take-off if that alert happens pre-flight,” Korol notes.
“The IMU auto-calibrates, so if the end-user keeps moving it around, lifting or adjusting it, then it will refuse to take off until they’ve let it sit still and calibrate for a short while.”
As a final precaution before take-off, once the motors are powered on, the UAV sits in a semi-powered mode, during which the rotors start spinning up and the servos begin operating, to evidence if anything might suffer a mechanical failure in-flight before actual flight happens. Once the mechanical flight systems have been proven for a few seconds, the autopilot allows take-off to commence.
In-flight autonomy
In the future, Skygauge aims to develop more automatic means of generating flight plans to ease workflows for themselves and customers, pending regulatory approval.
Regulations sometimes require that at least the initial runs of ultrasonic inspections with the Skygauge UAV are performed by remote control, to ensure sufficient oversight, as well as similarity to past operational methods. But even these use a plethora of autonomous functions, including: autonomous approaches and contact handling by the UAV in every measurement, autonomous articulation of the thrusters to maintain contact against turbulence and contact-induced oscillations, and autonomous emergency return and landing subroutines.
The future operating model is for users to tie all these functions together with autonomous take-offs and autonomous movements between inspection points.
Usually, the mission is a two-person job: one person to operate and monitor the UAV (for instance, taking direct control if emergency situations demand) via the ground control station (GCS), while the other monitors the inspection via a laptop that receives data from the ultrasonic gauge in real time. The latter may also instruct the operator in real time, particularly on the quality of results being obtained and whether the flight plan must be interrupted to redo one or more inspection points.
“When the UAV gets to the GNSS and altitude of a given inspection point, its flight-control system essentially locks it in to hover and station-keep there, at about a 50 cm distance between the arm with the gauge on it and the wall,” Korol says.
“Then it starts its approach, slow and smooth, into the wall. It bumps the gauge into it, detects contact, and then the flight system locks in again and the gauge starts the inspection process; the reading usually being captured within two seconds or less before the UAV can move on to the next point. And the results are beamed down into a little map of the inspection plan, so the inspector can view it.”
The ultrasonic gauge system for measuring wall thickness has been developed and supplied by Evident Corporation, formerly part of Olympus Corporation until the latter split off its Scientific Solutions Division into the former, now an independent company.
“They’re the existing world leader in this kind of technology, and we’ve been working closely with them to integrate their conventional sensor into our UAV and tailor it to be more of a robotics solution than a manual, handheld one,” Korol explains. “They’ve helped us a lot with integrating the unit, providing a lot of open detail on its workings, as well as just supplying us with units for R&D and then product purposes.”
Windspeeds are computed based on GNSS position, with a dual-antenna and receiver GNSS and inertial navigation system (INS) onboard and embedded with Skygauge’s algorithms for wind prediction. The angles taken by the servo motors to maintain contact are also useful data inputs for understanding wind directions and speeds in those algorithms.
A single-point, laser rangefinder system is installed on the UAV, which serves as the primary sensor for distance between the UAV and the wall. Based on that data feed, the autopilot slows down the flight speed as the wall gets closer and closer, from 20 cm/s at the initial approach to 3 cm/s at the point of impact. A 1080p camera with 60 fps is also used to enable situational awareness; significant algorithmic work for the camera has enabled it to detect obstacles in the dark and provide useful, high-resolution imagery of the structures being inspected.
“All of that data is critical for how we’re trying to digitise these inspections. This kind of work is traditionally very pen-and-paper. Literally, they would write the results and commentary from inspections on to pieces of paper, which would frequently then go missing, but we generate video and photo data, ultrasonic waveform models showing the full thickness, GNSS and altitude data, and so on,” Korol adds.
Contact is detected via a force torque sensor on the end of the arm, which measures the quality, force and torque being exerted between the wall and the UAV. As well as preventing excess force being imparted on the UAV, this data feed also helps the UAV to stay level via the flight-control system maintaining a target pressure level for the aircraft to keep to.
“We like to push with about 2 kg of force to conduct the inspection correctly. You do have to press an ultrasonic tool a fair bit for it to work, and that’s another benefit of our articulating thruster design: we can push forwards quite significantly with our rotors,” Korol notes.
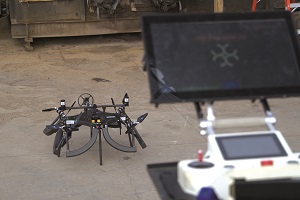
In-flight mechanics
Some past designs we have seen for solutions aimed at using UAVs for physical work (particularly on high-rise structures), such as painting or coating applications, would feature a pusher propeller (powered by an electric motor) extending from the back of the multirotor. This would ideally enable forward motion in a linear manner, without requiring the UAV to pitch down, hence enabling a level mode of contact, as well as sustained pressure against a wall via the thrust from that pusher prop.
“We have considered those kinds of designs, but they didn’t really appeal to us,” Korol says. “We’ve found that solutions like that, which dance around the core issue of drones needing to tilt around in order to move, ultimately mean that once a bit of wind comes in while you’re conducting some kind of physical work, the UAV and autopilot naturally resist the push and pull of that wind. They have no choice but to tilt around, to lose accuracy, to lose stability and contact; it’s just not going to work.
“We’ve seen dozens of projects like that, which try to engineer around that problem and maybe see some success in lab situations, but practically speaking, the real world has too much wind and too much precision force requirements.
“Frankly, until you dive deep into the challenge and do a total rewrite of how your flight-control architecture works, to isolate the motors and allow them to act separately from the airframe, you’re just going to keep bumping into the same problem.”
A variety of configurations have been used and iterated upon by Skygauge’s team. Currently, two rotary servos hold up each coaxial rotor pair, and tilt them around their respective axes using what Korol terms “a four-bar linkage”, enabling them to pan and tilt as a gimballed camera might, without modifying their position in the airframe. Each servo pair and motor pair operates independently of the others, enabling different adjustments, based on the aforementioned sensor data feeds.
“Programming those systems to all work correctly across different wind conditions was extremely challenging, especially getting the servos to tilt the rotor pairs in correct responses against wind and torque numbers. We do in-house testing and validation, where we strap each UAV down and run it through every conceivable permutation of articulations, with laser measurements to check that it is, for instance, tilting its rear-right thruster exactly 30° when we want it tilting 30°,” Korol notes.
“An undervalued part of this whole challenge was the stiffness we needed out of the airframe. We had to engineer all the carbon composite and aluminium parts across the body, over many iterations, to absolutely minimise flexing of any part of the assembly, because if the airframe starts flexing, it changes the positions and dynamics of the drone considerably. The end result is that we get less than a millimetre of deviation from its position in any direction.”
Cable management was another key development challenge. “There are no slip rings for now, thankfully; slip rings can be tough to work with. But routing of the cables for every motor and servo is important, and many of our early failures in our design iterations, particularly during stress testing, would come from wires getting sheared and chewed on the corners of subsystems,” Korol recounts.
“Since then, we’ve made a lot of provisions in the mechanical design to keep that from happening, and to make it easier to inspect and replace cable harnesses quickly too. Thankfully, we’ve not had another wire-jacket failure like that in quite some time.”
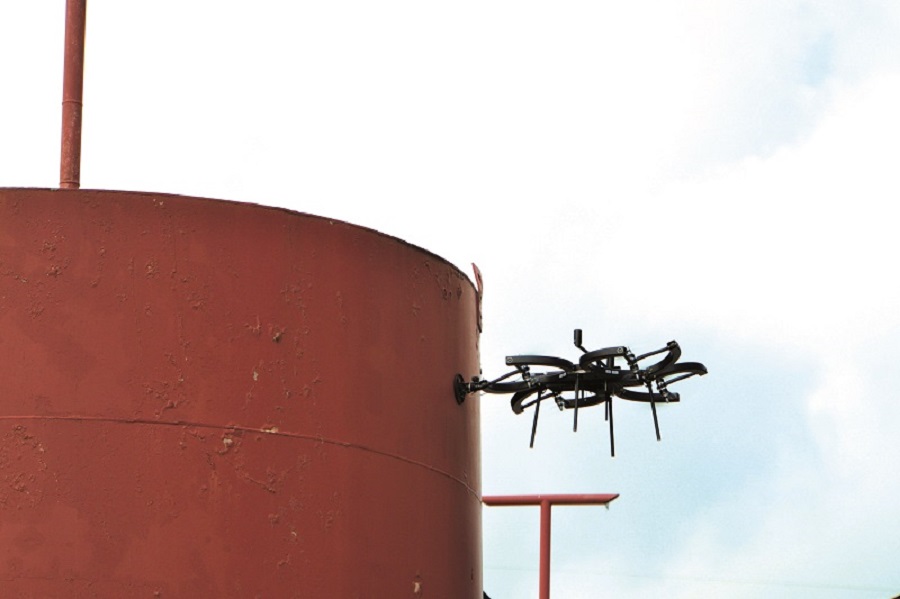
Swap and relaunch
Typically, the UAV keeps flying until the battery’s state of charge (SoC) drops enough to merit landing. In addition to the aforementioned laser rangefinder and camera for forward measurements, a second, downward-pointing pair of laser and camera sensors are used to ensure safe landings (the laser can also enable altitude measurements if the path to the ground is clear of objects).
After touchdown, the battery can be removed and replaced by hand in a matter of seconds, the pre-flight steps can be repeated, and the UAV can launch again and continue measuring until the job is done. Operators, by convention, will also regularly inspect the UAV’s mechanics and their integrity during those brief landings, discerning for potential issues such as excess dirt or debris about the thrusters or servos, which could hinder performance.
“Once that’s done, we pack up the drone, and we’re able to issue a report to the client. That’s more or less created automatically via our team, and it shows the client all the information on metal thickness on every point that has been measured, as well as an overall summary of the inspection and any points of concern detected within the structure,” Korol says.
“Issuing data reports as a product of the overall uncrewed aerial solution [UAS] is commonplace across the UAV industry now, but one of the big differentiators we’ve tried to create with our reports is traceability. Inspections today are not very traceable. Like I said, reports often get lost purely through administrative error.
“But our ultrasonic waveform scans, showing the full picture of what is inside the metal, are digitally recorded and made available so that inspectors can even go back and reinterpret the information, or cross-reference it with other information, at any time.”
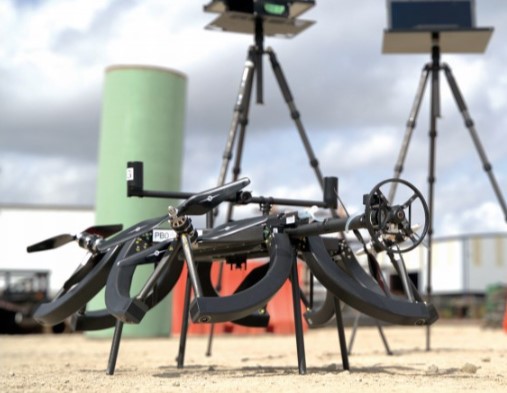
Future applications
Looking to the future, Skygauge is eyeing three principal directions of technological development that it plans to pursue. The first is diversifying its UAS offerings into new applications, and accordingly, new payloads.
“You can see fairly evidently that the bulk of work until now has been on the core technology behind the drone. It took us six years to go from building the first prototype to getting it to where it was successfully flying its first commercial application, but inside the last 12 months we’ve essentially optimised three new payloads. So that’s six years to go from zero applications to one, and then one year to go from one to four,” Korol summarises.
“It solidifies our determination that this UAV design isn’t a one-trick pony or built too specialised into one niche. It’s really a modular design capable of taking on different applications.”
Among the wider missions to be increasingly handled by Skygauge’s UAV are paint thickness inspections, for which one UAV has been sold to an unnamed South Korean client already (specifically for gauging paint on ship hulls). Others are scrubbing applications for removing rust from surfaces, as well as repainting and coating applications, which are currently under development in Skygauge’s laboratories.
Going forwards, these alternate applications will include activities such as pressure washing, industrial welding, concrete inspections, and the application of protective coatings against threats such as lightning or corrosion, and other work traditionally done at height by human hands.
Those types of mission, taking longer and requiring more weightlifting than ultrasonic inspections, are likely to make use of a tether and power converter for running power to the UAV from the grid, although Skygauge is also open to hybrid-electric or hydrogen fuel-cell power to enable the necessary lifting and endurance capacity.
“It isn’t just work at height that we will be focused on,” says Korol. “We are also investigating strong possibilities to use our UAV in locations with confined-space entries. On industrial sites, that means going into small manholes, tanks or places where oxygen is restricted. Inspecting those sorts of places is a hazard to human life, but it’s still done by hand.”
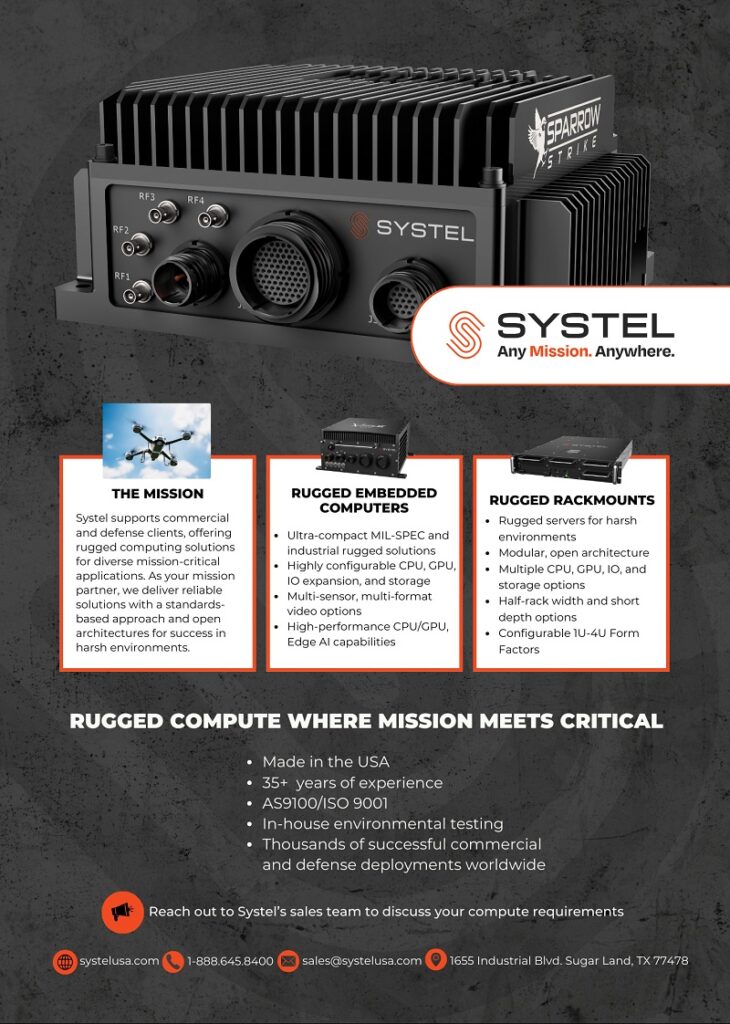
Skygauge is confident of being able to send its UAV to perform such inspections. The main pillar of success in those applications will naturally be its software and reporting systems. This forms the second area of future technical development, as the company aims to provide a cloud-based storage and computing solution for clients.
A robust cloud architecture would also enable a comprehensive fleet implementation and management system for industrial managers to remotely oversee their uncrewed inspection tools.
“Customers could thereby have multiple Skygauge UAVs and multiple payloads, all centralised and scheduled through a single cloud-based piece of software, which could form their one point of contact with the product to really simplify everything from flight planning to reports and analyses,” Korol adds.
“And, of course, enabling that simplification means taking the hands-on work out of flight preparations, so developing drone-in-a-box solutions for installations of UAVs as residents is definitely the last part of the puzzle.
“That, along with more advanced computer vision for smarter flights through hazardous pipe- or pylon-heavy locations, and maybe the integration of mesh radios so they can communicate and coordinate together as a swarm, will really achieve the uncrewed workforce in the sky that we’re envisioning.”
Key specifications
- Skygauge UAV
- Dimensions: 90 cm x 90 cm x 40 cm
- MTOW: 7 kg
- Payload capacity: 2 kg
- Endurance: 10 minutes
- Operating flight speed: 2 m/s (1 m/s in ascent and descent
- Maximum flight speed: 5 m/s
- Maximum thrust: 14 kg of force
- Battery capacity: 200 Wh
UPCOMING EVENTS
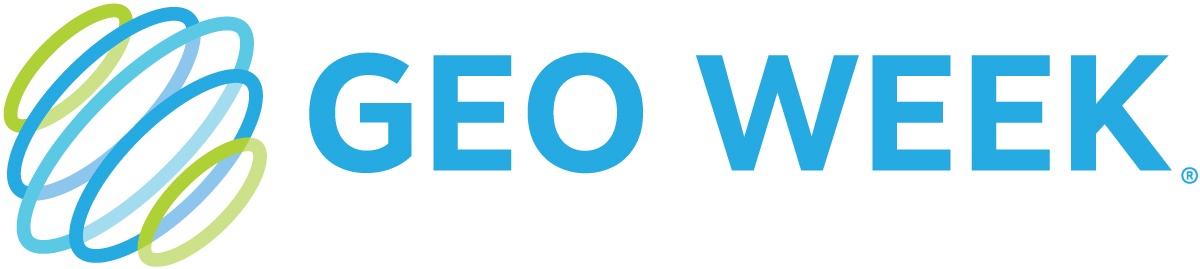
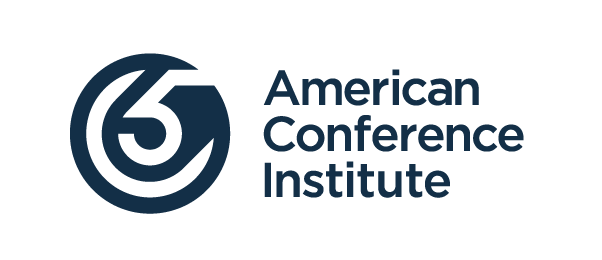
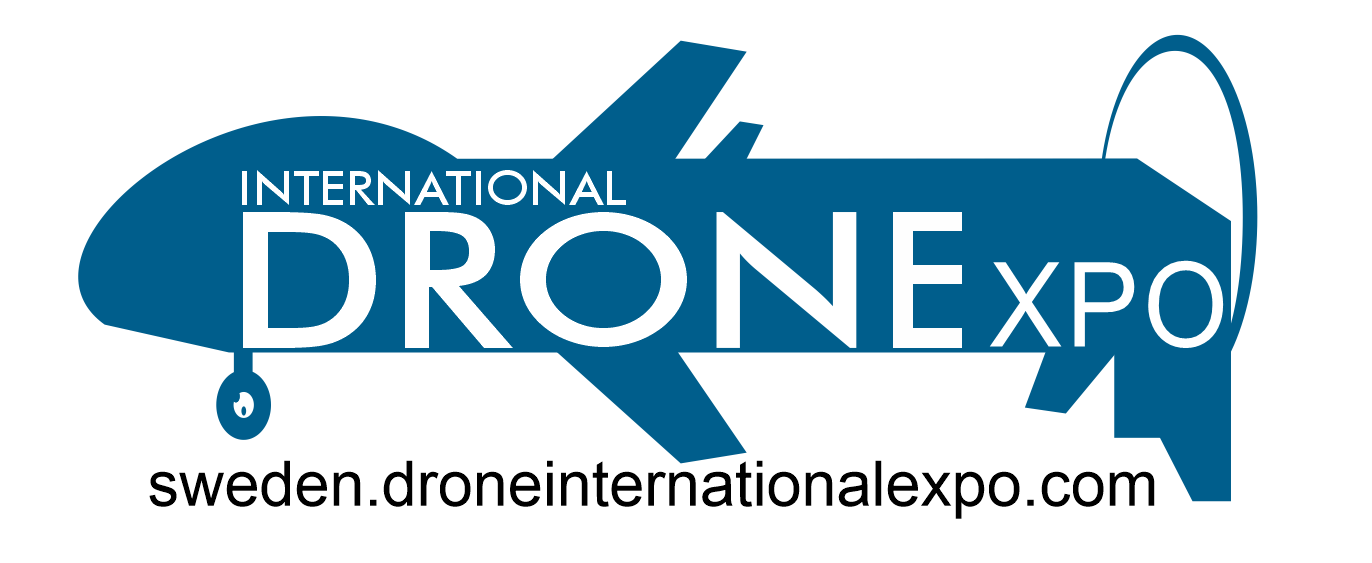
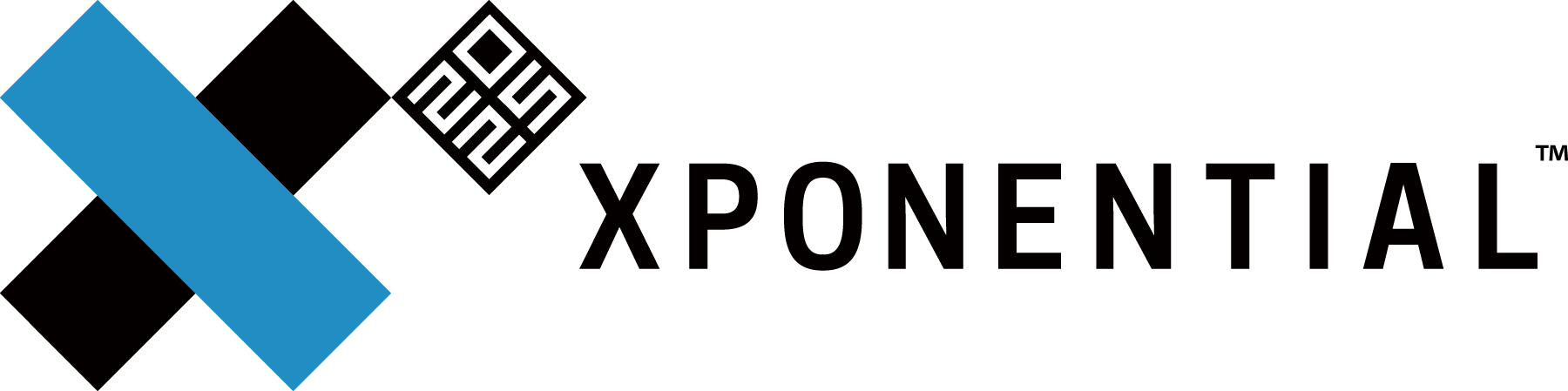
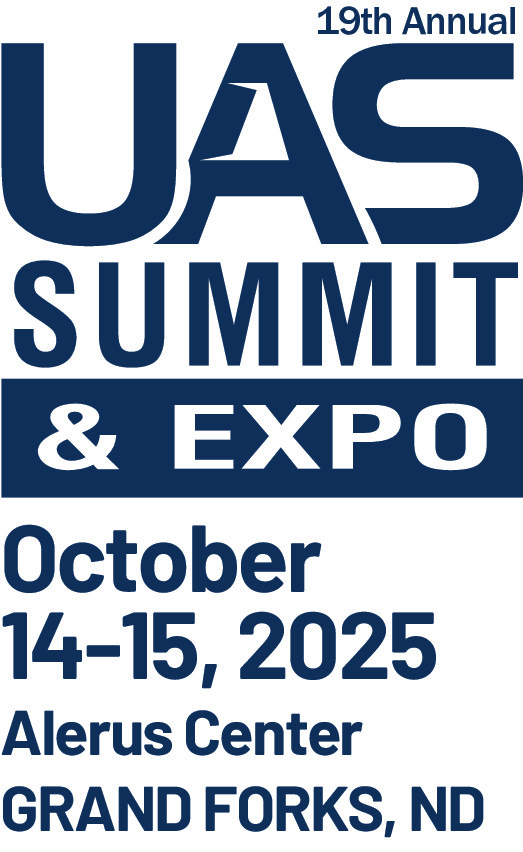

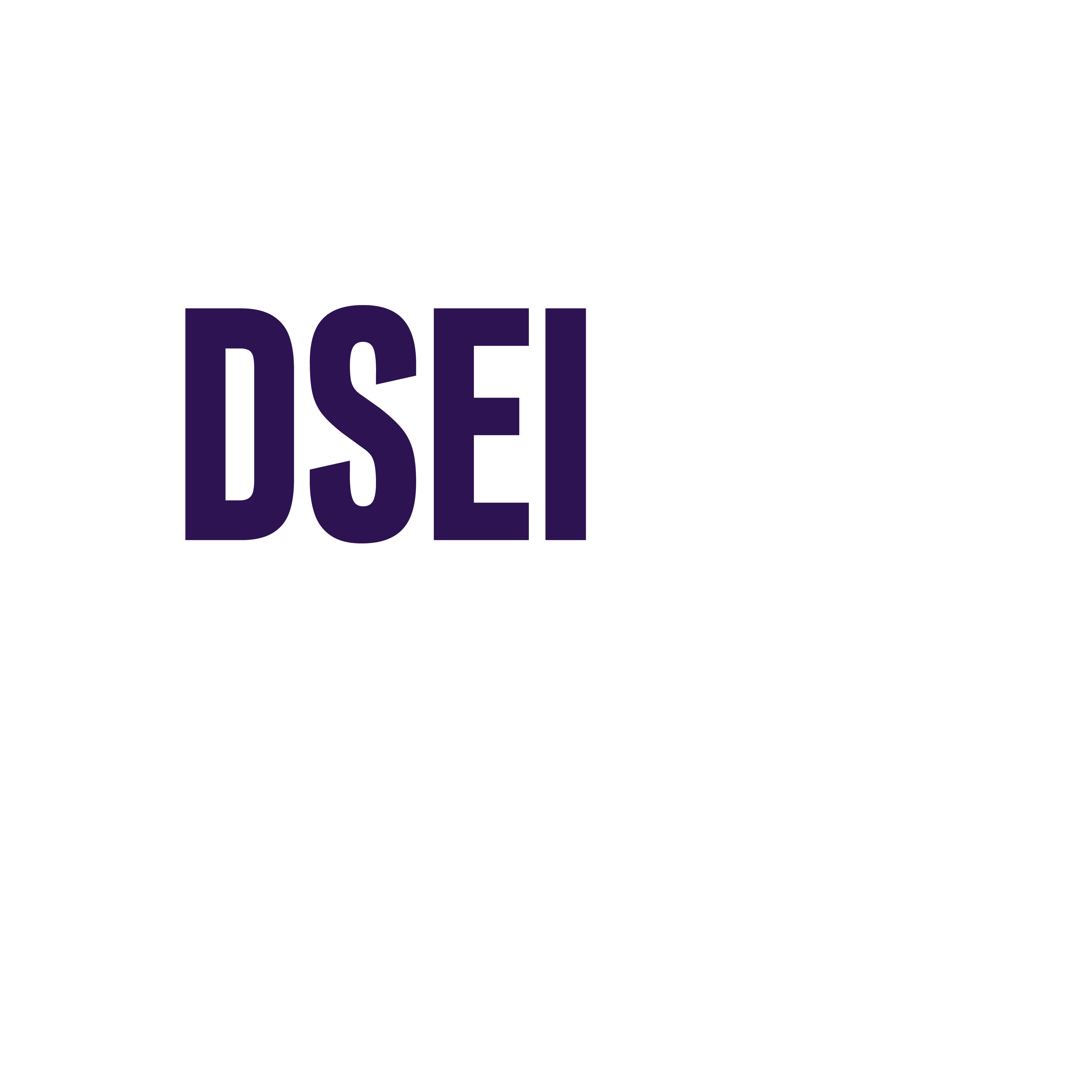
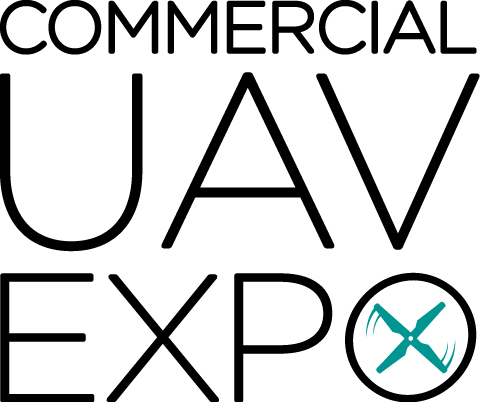
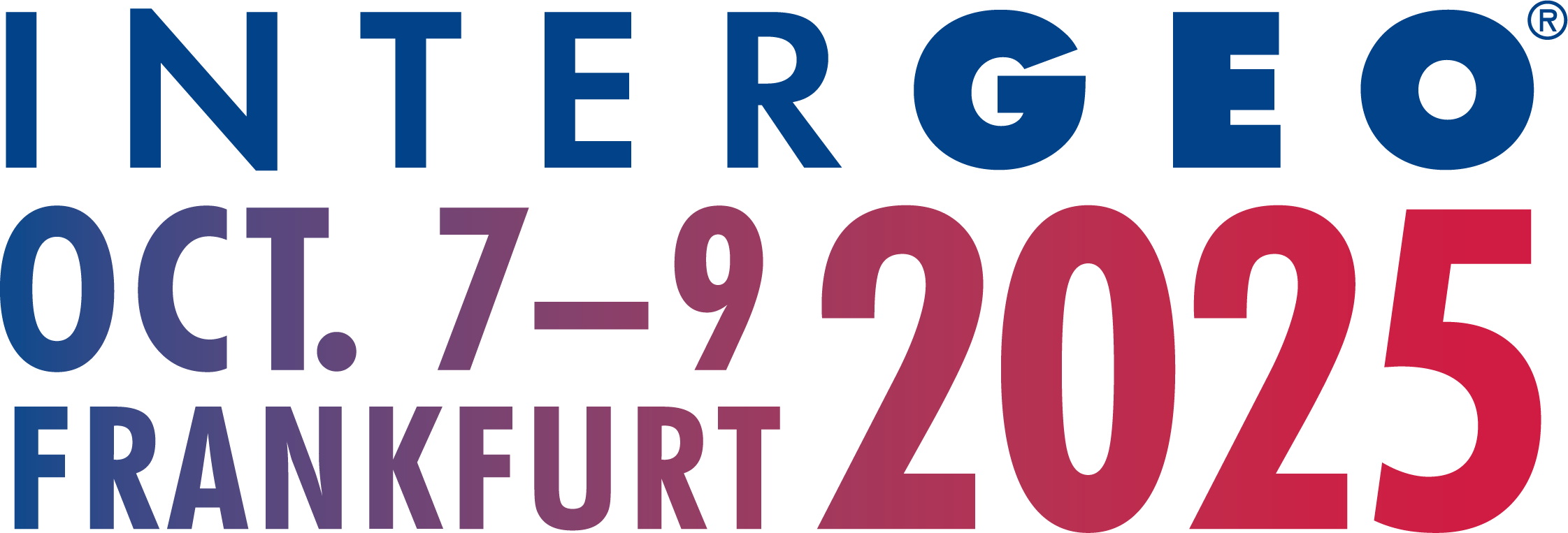
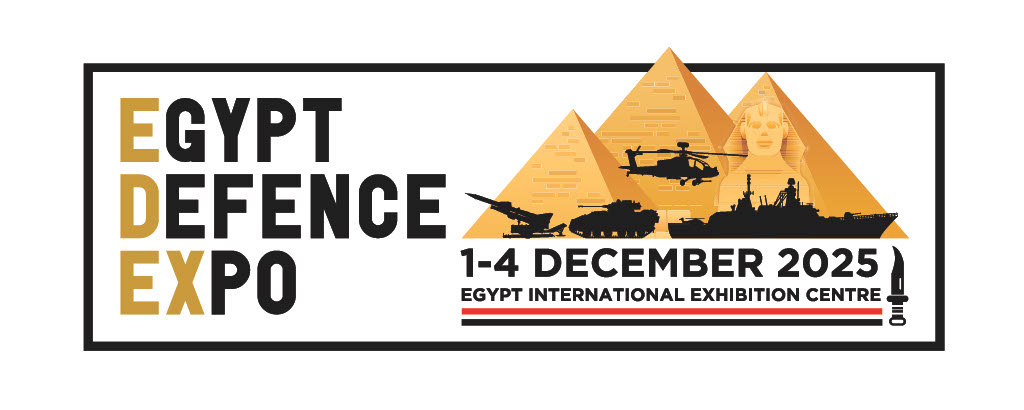
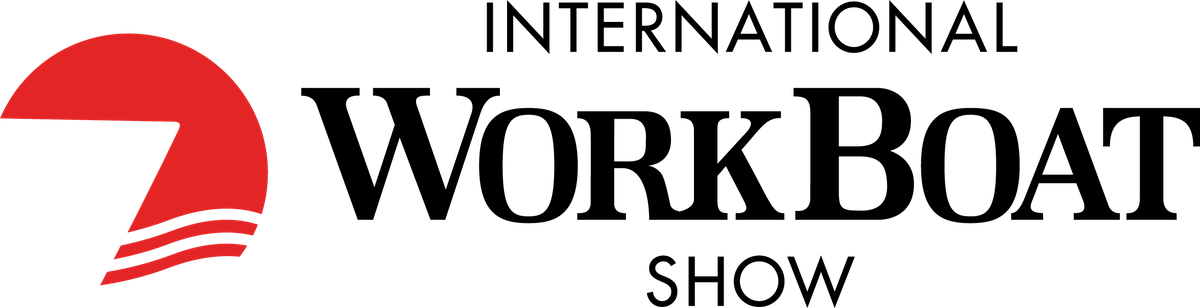