Dronex 2023
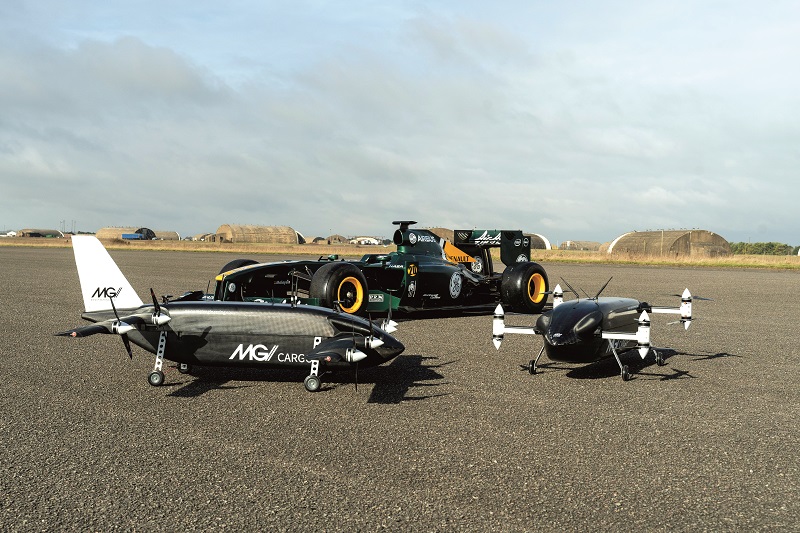
Rory Jackson presents his pick of the products on offer at this year’s trade show for UAV professionals
The DroneX trade show and conference returned to the ExCeL in the London Docklands in September this year, bringing with it around 200 exhibitors and 100 speakers dedicated to showcasing and discussing the latest in uncrewed aerial technology advances.
This year’s event was co-located with Helitech Expo and Advanced Air Mobility Expo, with many companies exhibiting mission-critical solutions for vehicle engineering for uncrewed, crewed and optionally piloted systems. Among the new UAVs and components for commercial, defence and emergency services applications were a wide variety of innovations across aircraft designs, propulsion and avionics, about which follow some first-hand details.
MGI Engineering attended the show to unveil two UAVs it has designed and manufactured in-house. The company was founded as an engineering consultancy by Mike Gascoyne, a former Formula One designer and engineer for various teams.
“Since our founding of Lotus Racing [subsequently renamed Team Lotus] in 2010, we’ve concentrated a growing amount of our r&d on VTOL aircraft engineering, combining that with our knowledge of aerodynamics, lightweight materials, and CFD modelling and FEA tools from Formula One to make the two UAVs, which we’ve named the Mosquito family,” said Fraser Harris.
“Both UAVs have the same body, but one is built with a tilt-wing design for fixed-wing flight and VTOL transitioning, the other has fixed rotors for a multi-copter configuration.”
The Mosquito Tiltwing has two pairs of tilting wings – one forward, one rearward – each of which has two motor-propeller drives, for a total of eight across the aircraft. The Mosquito Fixed-Rotor also has eight motor-propellers, but its drives are distributed on four tilting rotor arms, a coaxial motor-prop pair integrated at the end of each arm, in an X4 coaxial quadcopter architecture.
Both UAVs have a payload capacity and empty weight of 20 kg, and are configured to run with batteries. MGI aims to supply the aircraft for cargo delivery missions, particularly in remote locations or emergency relief operations. The Mosquito range will be expanded in future to include platforms with payload capacities of 100-500 kg.
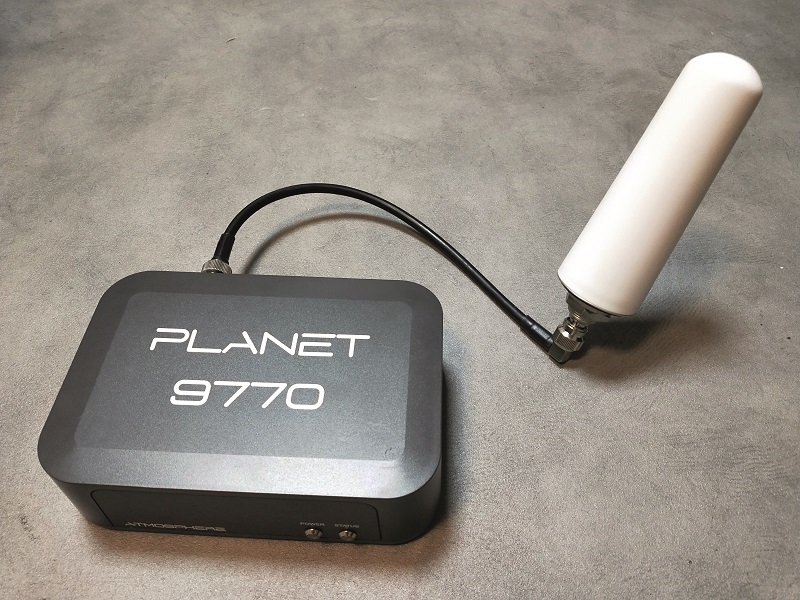
J Perkins is a UK-based distributor of small engines for UAVs and RC aircraft, and exhibited powerplants from a range of international manufacturers including Futaba, Swiwin, Zenoah and Stinger Engines.
“From Stinger, we’re showing their twin boxer unit, a 125 cc two-stroke which produces about 12 bhp, and weighs 2665 g,” said Paul Bardoe.
“It’s been developed for reliability rather than absolute peak power, so it’s designed for smooth throttle transitions and easy tickover. It runs on a standard petrol-oil mix, has an integrated ignition module for spark ignition on the back, and typically you’d install a 27 in[68.5 cm] diameter propeller with maybe 10-12o of blade pitch on the front.”
Bardoe added that a version of the engine is coming with an integral BLDC starter/generator for generating electricity at 12-14 V on its aircraft to power the electronics and charge the batteries, as well as restarting the engine in mid-flight when needed.
Semai Aviation exhibited its Dynotis range of motor-propeller test rigs, of which there are five standard versions, with further models customisable on request. The Dynotis model on display was Semai’s ST-751, which is suitable for cycling motors up to 120 V with up to 75 kg of thrust, 60 Nm torque, 300 A of current and 100,000 rpm speeds.
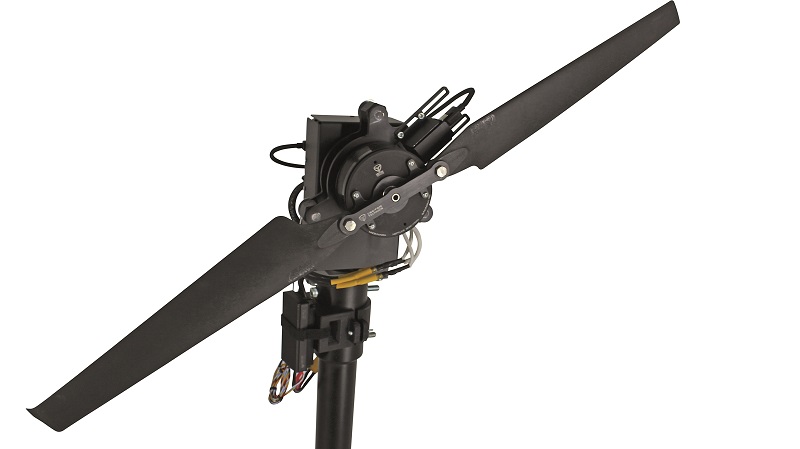
“The stands come with our software system, which calculates key motor-prop performance values coming from the test stand such as rpm, thrust, torque and voltage, then downloads all that data in real time onto the user’s computer, allowing them to gain independent and correct analyses on motor and propeller efficiency,” said James Ewan Alptekin.
“That way, before supplying or flying a UAV, manufacturers and integrators, can verify whether a given motor or prop is suitable for use on it, as well as if it’s the most energy and aerodynamically efficient choice.”
Each Dynotis test rig comes in two models: a static model in which the stand is meant to be run while stationary, and a dynamic test model mounted on a test vehicle and moved forwards along smooth, straight terrain.
The latter is configured (in both hardware and software) to function as if a UAV is in a wind tunnel, given the ambient air interplaying with the propeller, for companies seeking to avoid the expense of owning or hiring a wind tunnel.
Co-located at the Thales stand was Atmosphere, a manufacturer and integrator of Iridium-based satellite comms terminals.
“We have developed a range of products compatible with the Iridium Certus 100 constellation of satellites, which deliver 40 times the transmission bandwidth of legacy constellations,” said Jean-Marc Gaubert.
The company’s latest terminal is its Planet 9770 UAV-L, which enables up to 88 kbit/s mid-band throughput. As its name suggests, it is built for UAVs weighing 700 g, and can be supplied without its enclosure for OEM integrations.
Also installed in the system are a GNSS receiver and a SMARC processor to support edge computing or compression of data pre-transmission.
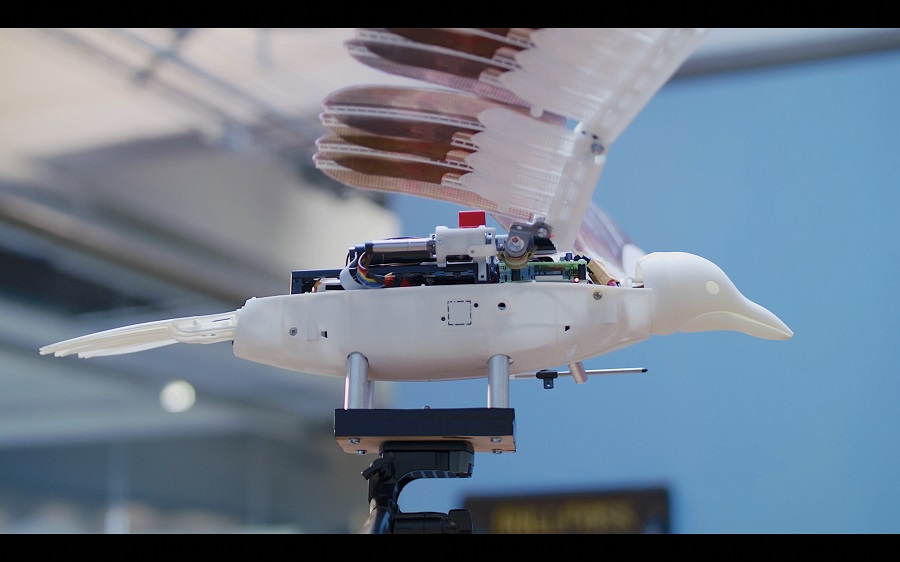
Flygildi debuted a prototype of its Silent Flyer UAV, a biomimetic aircraft shaped like a bird that is being developed to fly using flapping wings. By blending in among avian fauna, and flying without noise-generating jet engines or rotors, the company anticipates applying the UAV in covert operations across intelligence, security and wildlife monitoring.
“The wing-flapping prototype is currently undergoing indoor testing, to optimise the wing-flapping pattern for maximising the propulsion efficiency,” Peter Holler said. “We also use a version with non-flapping wings to optimise the aerodynamics by exploring variations of aerofoils and shapes of the main wings and tail in open-air flight tests.
“Engineering the Silent Flyer has come with challenges in finding highly energy-dense batteries, power-dense actuators for the wings for climbing flight and agile manoeuvring, as well as a control system which has the logic to handle the complex aerodynamics created by the wings flapping.
“Some solutions are unusual for the UAV industry. For instance, some load-bearing parts are additively printed from titanium and aluminium, which helps save the weight budget for batteries and payloads.
“While the current prototype is equipped with an array of PID controllers to control its attitude, the evolving control system will be based on machine learning techniques, trained by wind tunnel data using laminar airstreams and stochastic airflow disturbances. So the controller can learn which actuations achieve which attitude corrections.”
Although some parameters are not yet defined, Flygildi anticipates the Silent Flyer will be able to fly at 55 kph, carry up to 200 g payloads, and take off and land without ground infrastructure.
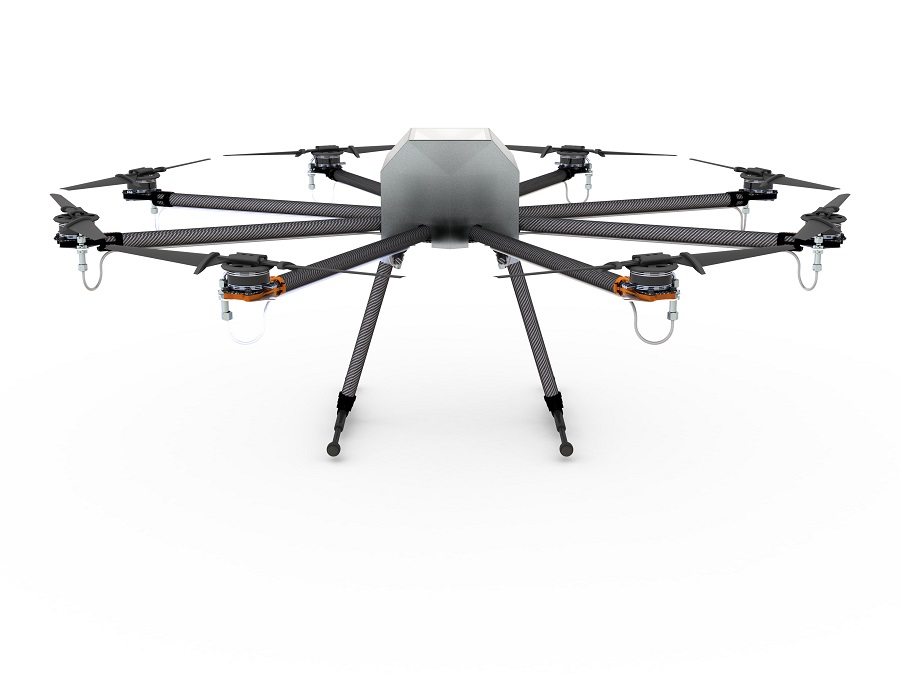
CAV Systems exhibited at DroneX to show and discuss its anti-icing technology for UAV propellers, which the company has previously supplied to general aviation aircraft, and is now scaling it to suit the much smaller geometries, higher speeds and hence faster ice accumulation rates of UAS props.
“Our solution is a mechanism that an aircraft operator or a UAV’s autopilot can turn on when an icing situation is encountered in flight, such as a very cold cloud or freezing precipitation,” explained Brock Harden.
When activated, CAV Systems’ solution pumps a de-icing, glycol-based fluid out to the propeller, which flows and spreads across the blade by centrifugal force. The fluid prevents ice-cold droplets from freezing on the blade, instead forcing them to remain liquid. As a result, the water will be shed from the propeller as it spins, instead of accumulating as ice.
“Integrating our solution can be achieved by working with propeller manufacturers or UAV OEMs,” Harden continued. “The technology is at the mid-to-late prototyping stage at the moment, and there are some more steps we want to take to see if we can optimise it further, in terms of how the fluid delivery is performed, and in using market-ready components.”
We met Delphys Dynamics at the event to learn about its flying saucer-shaped ADIFO (All Directions Flying Object) UAV.
“Its shape allows it to fly in all directions with the same aerodynamics, and to perform sudden lateral translations and sudden yaw rotations at very high speeds – something not really possible with any other aircraft design,” explained Razvan Sabie. “It can also accelerate very quickly. Combined, these qualities lend it towards various high-speed transportation applications.”
A scale model was displayed at the company’s stand, although Sabie said the full-scale ADIFO prototype is about 1.5 m in diameter. The airframe has four electric, vertically disposed ducted fans in the saucer-shaped airframe, as well as three small tilting jet engines.
When tilted horizontally, the engines’ shrouds conform with the hull shape, and achieve intake and exhaust using vents at the sides of the craft for horizontal forward thrust. The vents also act as effector vanes or nozzles for yaw, roll and pitch. The fans provide stabilisation during transition, as well as some extra manoeuvrability during flight.
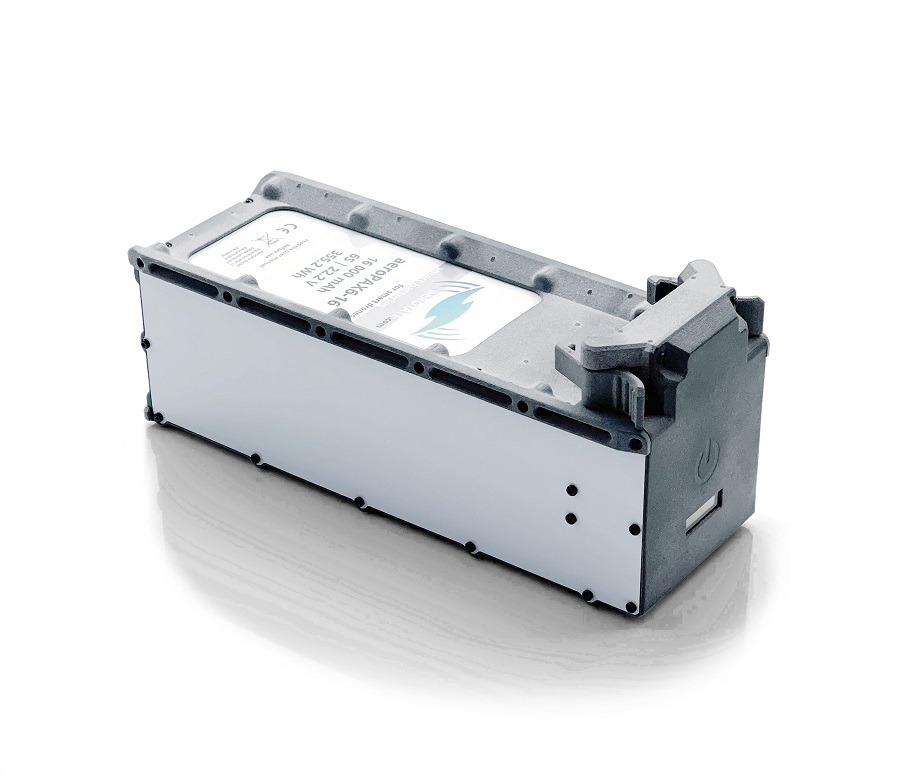
Also attending the show was aeRotate, a producer of battery packs with integrated BMSs, to showcase its aeroPAX6 Smart Battery.
“This battery is programmed to communicate via DroneCAN, enabling it to be plug and play with any Ardupilot-based flight controllers,” said Johanna Glutting.
“The BMS provides a hot-swap ability for parallel battery set-ups, while also monitoring and logging data on cell voltages, cell temperatures, SoC and other parameters.”
The aeroPAX6 is a lithium-polymer battery pack with a quick-swap adapter, making it possible to swap the battery within seconds. It has a 16,000 mAh maximum capacity, 266.4 kWh nominal storage, 22.2 V DC nominal supply, up to 60 A continuous discharge current (250 A peak) and weighs 2138 g.
The pre-charge circuitry prevents sparking when users power up their UAVs. Additional software functions include a ‘storage’ mode, which can be activated to preserve the health of the battery during long periods of inactivity.
Piran Advanced Composites displayed a number of parts on its stand as examples of different geometries, thicknesses and complexities it can produce using its carbon composite manufacturing capabilities.
“One of the UAV markets we’re able to supply to for instance is HAPS or HALE aircraft,” said Marcus Royle. “You can see here several examples of the level of lightweight carbon fibres we use, which make our parts suitable for HAPS and their structural components.
“Typical lightweight composites used in motorsport, automotive and conventional aerospace would be around 200 g/m2 per layer. Thanks to a very specialised supplier we’re partnered with, we can go down to 20 g/m2 per layer.”
The company’s resin systems cover a broad range of industry-standard components, with some key knowhow lying in the combination of standard resins with a range of prepreg materials and less-often used lightweight fibres.
Airvolute attended the expo to showcase its DroneCore 2.0 autopilot, which can be built around Cube’s Orange+ flight controller or its Blue H7, along with an Nvidia Jetson Orin NX to enable AI support of UAV navigation and mission planning.
“As well as designing it for mass manufacture, we’ve also optimised it for light weight and redundancy,” explained Lukas Palkovic. “It weighs 153 g, and while the Cube is the primary flight controller, an STM32H7 FMU is also installed as a secondary or back-up autopilot, although that latter unit can also be used as the primary autopilot if the user wishes.
“It also integrates a network switch for Ethernet, as well as several USB UARTs, and MIPI camera ports. A wi-fi module is also integrated on board, and in general we’ve designed the whole product with an open source architecture and a high level of modularity.
“The integrators can therefore perform their own redesigns, like replacing our connectors with their preferred connectors or integrating various adapters, which usually need separate boards. The same can be done with the power distribution board. Now, everything can be placed in one unit with minimum cabling.”
Palkovic added that the DroneCore 2.0 comes with Airvolute’s software features, which at the moment include visual odometry, support for different gimbals and automated gimbal pointing and tracking. Other features will be added as the company’s software library set grows.
“That frees up developers’ attention to concentrate on optimising their UAVs for user applications, rather than getting lost in writing software for lower-level functionalities,” he noted.
The DroneCore 2.0 measures 119.5 x 51 x 41 mm. As well as the various CAN, Ethernet and serial buses available to the Cube, STM and Nvidia computers in the system, it also features Airvolute’s DroneCore power distribution board.
This has a power switch and power sensor as well as four motor power pads (each designed for 30 A of continuous current, 50 A peak), an LED driver for four WS2812B-type strips, and DC outputs of 3.3, 5 and 18 V. The standard power distribution board is offered as a default, although as the interface is open source, it can be customised into a form or architecture better suited to the needs of a specific UAV.
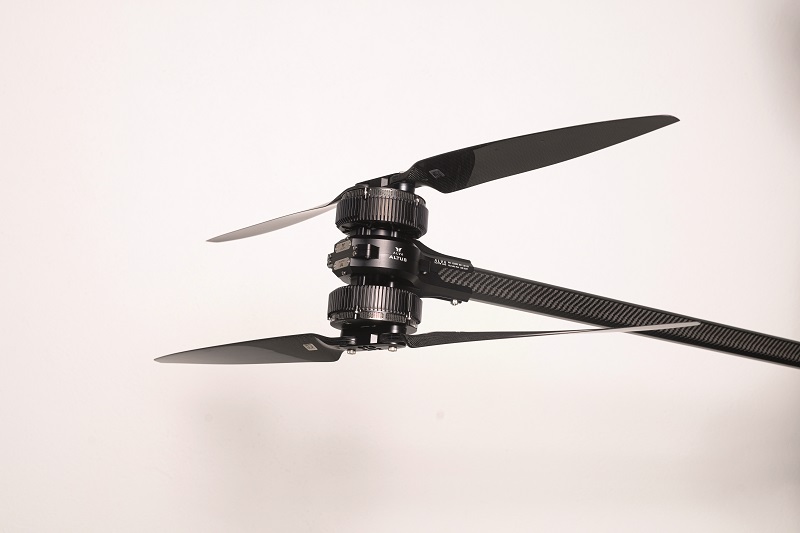
Electric motor manufacturer Alva Industries announced the second generation of its Altus X60 electric motor series, the company’s flagship product family that uses its patented FiberPrinting technology for constructing e-motors with ironless stators.
“We’ve done a lot of harsh and abusive testing on the motor, including 24/7 test rig cycling and simulations of uneven loading during high-speed and oscillation flights, the biggest cause of motor failures in UAV flights,” said Anton Frantzen. “Based on the test results, we’ve pinpointed and implemented several areas of improvement.
“Those include structural changes to enhance the lifespan against fatigue, along with some design changes to make manufacturing easier. For instance, the stator housing used to be assembled from two components – the cooling and bearing housings – joined with an adhesive. But now they’re manufactured as a single piece, which simplifies things a lot.”
Both the Uno and Duo versions of the X60 were previously tested to a maximum of 1000 hours, and Alva Industries anticipates this figure being revised upwards, the exact new figure to be determined via testing.
“We’ve also done some redesigns at the system level to make the motor housings weatherproof under any normal rain or thunderstorm conditions, including an extension to the housing that allows the motor to seal around the rotor arm or boom, to prevent water ingress into the motor or UAV,” Frantzen added.
The X60s can also now incorporate accessories. A port has been designed into the motor housing to power and interface over CAN with navigation and warning LEDs, among other devices.
The company also now designs motor housings for integration with 40 mm-diameter rotor arms, or rotor arms with octagonal cross-sections measuring 25 x 38 mm. Previously they could only mount directly onto 30 mm-diameter arms (now covering all industry-standard multi-rotor arms).
Hydrogen Craft Corporation exhibited for the first time at DroneX to showcase its two hydrogen PEM fuel cell products: a 1.7 kW unit weighing just under 2 kg, and a 550 W unit weighing about 800 g, which are also used in a range of UAVs the company manufactures.
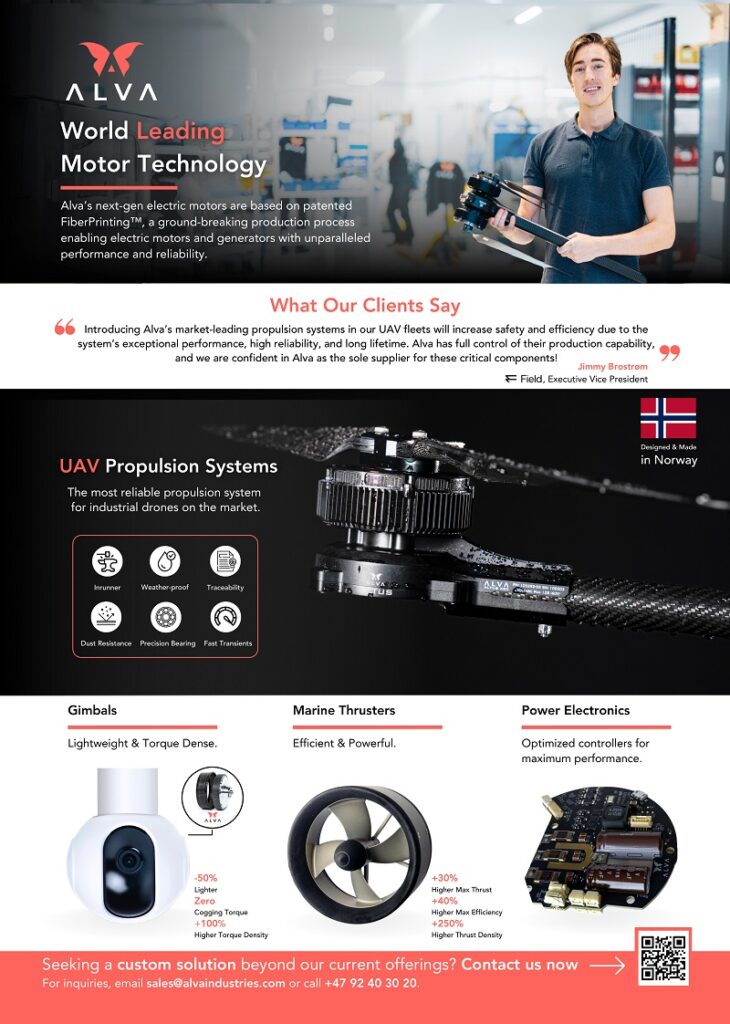
“Historically, air-cooled fuel cells have suffered from critical engineering challenges which affect their operating performance,” Haili Liu told us. “For instance, as well as being sensitive and fragile, they have very long re-activation times if they’ve been left standing for a long time, due to the exposure of the proton exchange membrane to the air.
“That causes the PEM to dry out, so re-starting it takes at least several minutes. When you compare that to batteries, which work almost instantly, you realise that’s a serious hurdle to the practical use of air-cooled PEMFCs and a big reason why they’re not used in a widespread way, despite being at least three to four times more gravimetrically energy dense than batteries.”
Since its founding in 2017, Hydrogen Craft Corporation has therefore focused its r&d on the catalyst-coated membrane level of its fuel cell technologies, resulting in the creation of material layers within the stack that manage its internal water channels differently to other fuel cells. The layers preserve the ambient humidity about the MEA for long periods between operations of the PEMFC.
“Last year, we achieved a 1.8 second start-up time with our fuel cell products, which was verified and certified by the Shanghai Auto Testing Centre,” Liu added. “That’s a key reason why our UAVs powered by our fuel cells are now regularly flying in power grid and oil pipeline inspections.
“Our next goals are working towards lighter fuel cells as well as HT-PEMFC [high temperature PEM fuel cell] technology. We believe the latter is going to be the future for eVTOL taxi powertrains, and we’ve started collaborating with COMAC [Commercial Aircraft Corporation of China], supplying hydrogen powerplants to their eVTOL programme.”
UPCOMING EVENTS
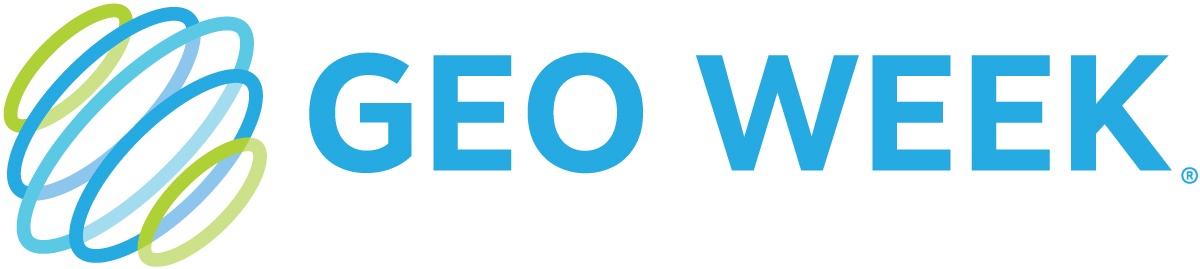
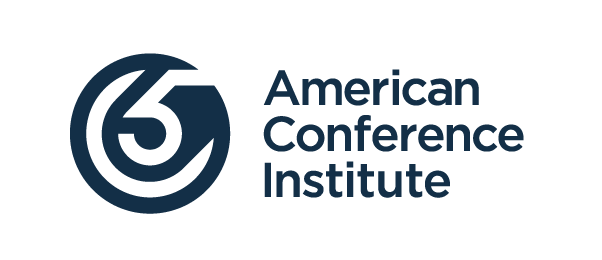
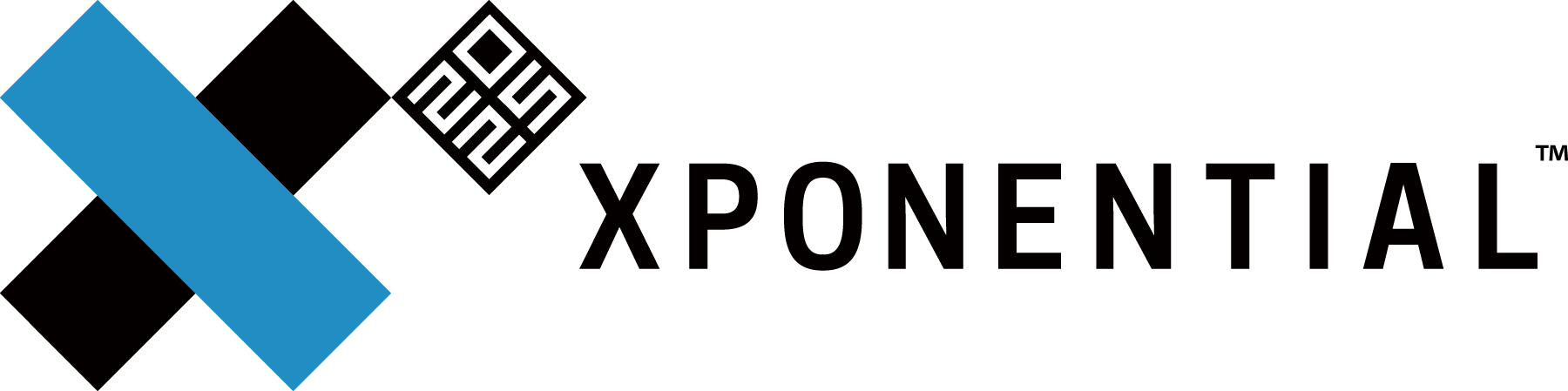
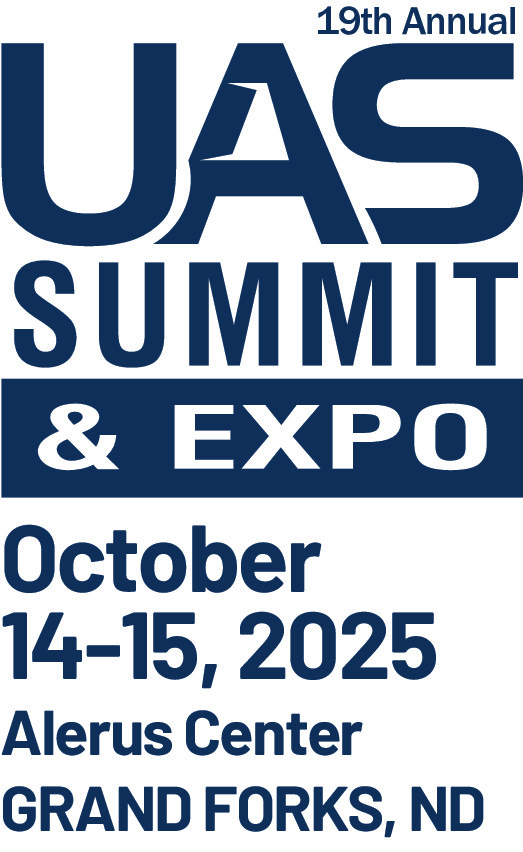
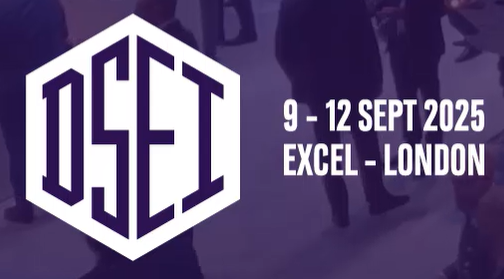
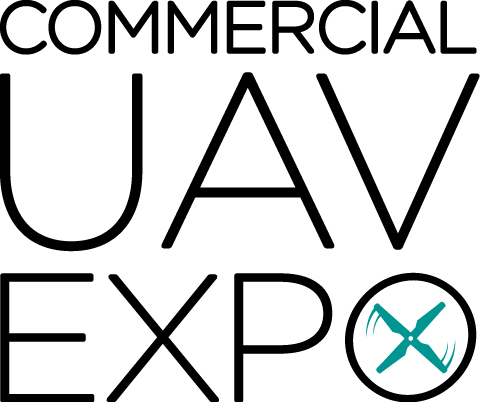
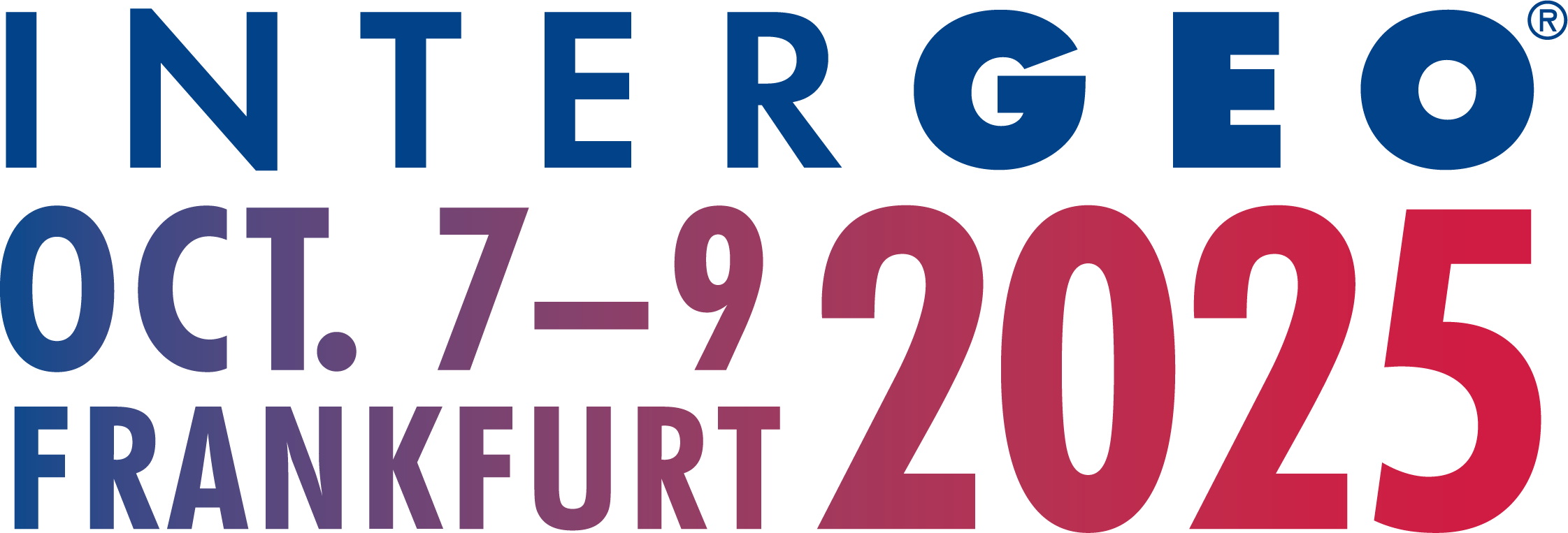
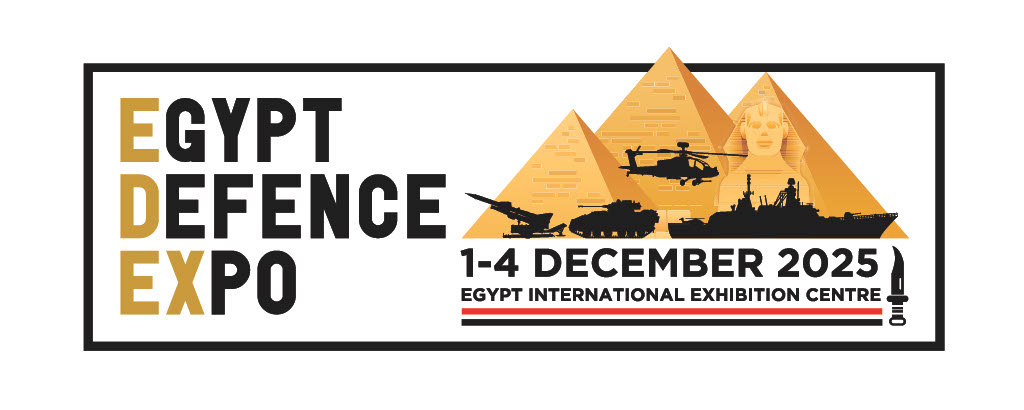
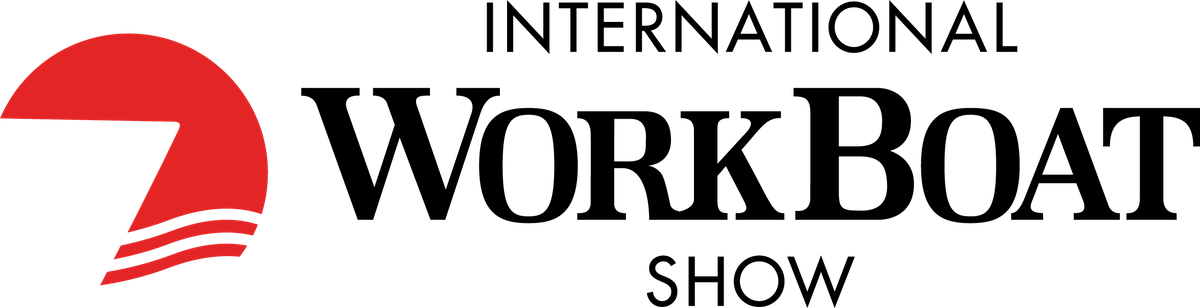
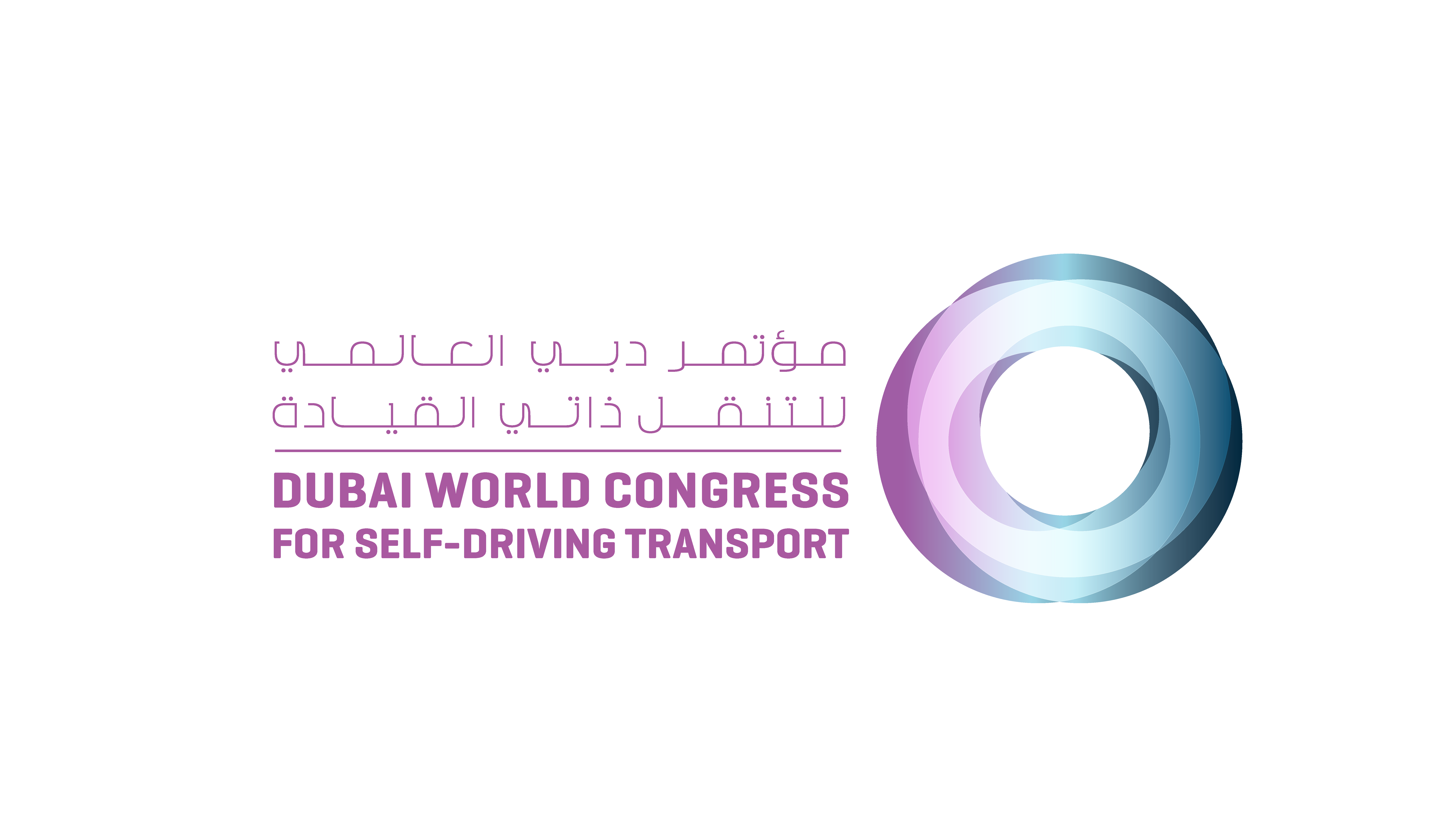
