SeaTrac SP-48 USV
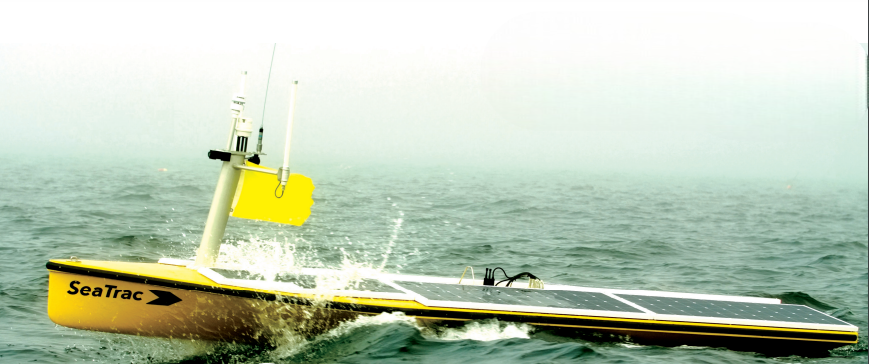
Sea fellows
Rory Jackson investigates a cost-effective and sustainable alternative to crewed survey vessels
While environmental data is important for tracking and analysing climate change, it is also used in a range of applications other than climate science. These include planning for offshore construction projects, predicting earthquakes and their magnitudes, and monitoring and protecting marine wildlife. Therefore, the ability to collect environmental data from widespread ocean locations at low cost is in high demand across a range of markets.
USVs naturally make a better fit for such work over crewed vessels. Keeping a crew safe and happy for potentially months on the ocean mandates making a ship large enough to maintain stability on rough seas, and to also contain kitchens, bathrooms, sleeping quarters, and so on. This necessitates huge construction and operating costs, with the latter involving vast quantities of fuel consumption, running strictly counter to the environmental nature of much ocean data collection.
Massachusetts-based SeaTrac Systems has designed and built its SP-48 USV as an ideal alternative to crewed survey vessels, being considerably more cost-effective, sustainable and transportable – saving crews from the dull, dirty and dangerous months of work at sea that is needed to satisfy market demand for ocean data.
The SP-48 is constructed as a flexible, payload-agnostic platform for operating a large and versatile mixture of survey sensors, communications relay devices, and more.
Up to 70 kg of capacity for payloads is available on the 4.8 m long, 275 kg (empty weight) monohull USV, powered by a battery that can recharge at sea via solar panels on its top deck – a capability that can enable months of operation.
SeaTrac was founded roughly seven years ago by Jigger Herman and Buddy Duncan, who met in MIT’s naval architecture department in the 1980s and bonded over a mutual experience in different forms of competitive sailing, as well as their passion for innovation.
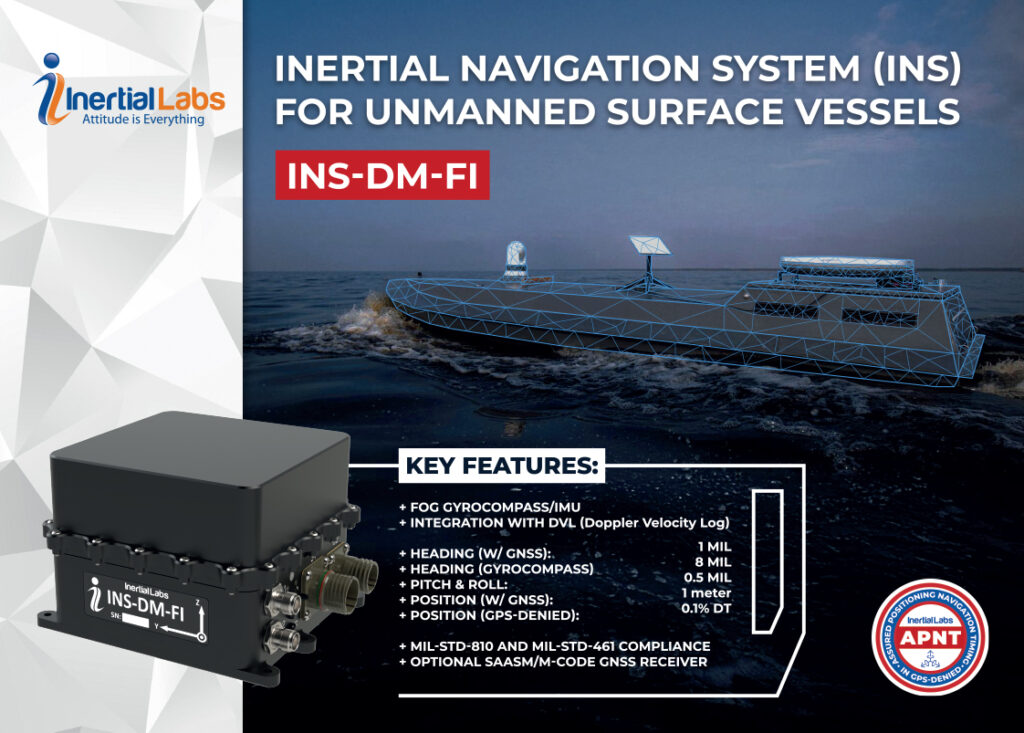
Subsequently, they collaborated on a range of projects, including racing sailboat engineering, which inspired them to develop an automated, CNC fabric-cutting machine, subsequently building a large company around producing and selling them, not only for use in carbon-composite manufacturing but also in a range of cloth-based industries.
The duo would go on to develop and commercialise smart home automation technologies (about 10 years before the iPad and other tablet computers appeared), and most recently they were drawn to the challenge of engineering low-cost, versatile USVs. This happened partially through learning of navy interest in the idea and partially out of a fascination with the Liquid Robotics Wave Glider, wondering if they could make something more cost-effective.
“Buddy and Jigger went through a customer-discovery process early on with some local stakeholders, including environmental groups like Woods Hole Oceanographic Institute [WHOI], to understand what prospective USV customers were trying to do: what data they were trying to collect and what their ideal USV platform would look like,” says Hobie Boeschenstein, director of business development and operations at SeaTrac.
“Based on those discussions, they agreed on a reasonably simple configuration for a sensibly sized USV, with solar panels recharging a battery pack to store up energy and power an electric propulsion motor, not just for sustainability but because they knew that making something work consistently on the ocean is hard, and you can’t build simplicity into something that was complicated from the outset.
“You need a platform that enters life as simple in order to keep it simple later on, by minimising things like moving parts that can break, subsystems that require huge expertise or training from users, or components that are difficult to maintain.”
Seven years on from the start of r&d, the two friends’ SP-48 USV is in use by researchers at WHOI, NOAA, Princeton University and other leading research bodies across the US, with a range of potential customers in the commercial and military space also evaluating the use of this unit in the near future.
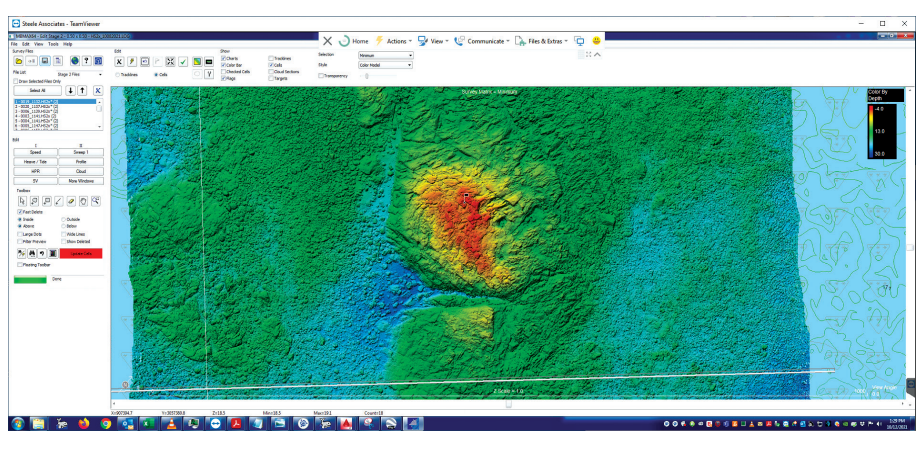
Design evolution
Herman and Duncan first began thinking about USV concepts in 2015, a process that naturally drew upon their education in naval architecture and experience in sailboat engineering.
SeaTrac Systems was officially incorporated in 2017, and the pair rapidly began work on the first development prototype shortly afterwards, with the aforementioned goal of a simple, solar-recharged boat in a small form factor that could be transported by shipping container to different areas.
By 2018, the first prototype had been built in a garage (with the founders helped by their children) with hand assembly and sanding. That went through two years of operations with WHOI, the Massachusetts Office of Coastal Zone Management, and other groups, to identify what could be improved.
The concept for the SP-48 soon followed, slightly larger than the first prototype, to facilitate higher solar-power generation (and enabling more payload capacity). It was also longer and had hydrodynamic optimisations, which meant that as well as generating more solar energy, it consumed less energy as it moved due to lower drag, and it could still fit in a standard, 20 ft shipping container.
“They also took into account how end-users mount their instruments,” Boeschenstein says. “The first prototype was a straight hull, with instruments bolted at the bottom, and they noticed that, whether it was an acoustic Doppler current profiler [ADCP], a sonar or profiling sondes, ocean-data survey instruments tend to have a rounded form factor, and average around 10 in in diameter.”
So, the founders determined that incorporating a moon pool would be valuable for integrating such instruments, as well as submerging and retrieving them from the water. The SP-48 thus features a moon pool as the primary payload bay, with standard bolting patterns on the bottom for easy installation or removal of instruments or the fairings that enclose them, either for easier mounting or reduced drag.
Another payload bay has been designed behind the moon pool for topside instruments. To ease payload integration the USV’s architecture includes three 12 V power supplies, three 24 V supplies and three 39 V connections, as well as several comms buses.
The SP-48 has remained outwardly unchanged since its unveiling as a second prototype in 2020, albeit with minor incremental changes as repeated trials and missions unearthed which sections would break first. Most of the changes, as Boeschenstein recounts, relate to fasteners, seals and keel design (for easier launch and recovery, and compatibility with underwater sensors).
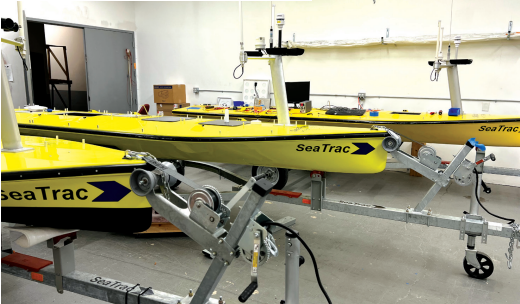
Structure and layout
The SP-48 is a somewhat flat monohull at 42 cm draft, with considerable subsystems packed in defined areas across the hull for a SWaP-optimised platform. Atop is a mast for antennas and sensing instruments, besides six solar panels and a plethora of hatches for accessing subsystems below deck.
“Under the bow hatch we have a main electronics enclosure; under the next hatch along the USV’s length we have our battery assembly, with the moon pool right behind that; and then we have a larger hatch, which we call the payload hatch behind,” Boeschenstein says.
“That has different options for mounting equipment. You can put in different kinds of plates and brackets to support instruments of varying sizes up to about 4 ft long and 2 ft wide. Behind the payload hatch are the propulsion and steering assemblies, which are accessible via a stern hatch.”
The boat is constructed broadly from three pieces: a hull piece bonds to a deck piece, with a separate moon-pool piece bonding within those at roughly the centre. All three are largely made from pieces of fibreglass composite with foam core material. Hull-part manufacturing is largely outsourced to a strategic partner, with assembly performed in-house; a process that includes SeaTrac’s engineers cutting hatch holes, mounting fasteners, and installing subsystems as required before the hull and deck get adhesive-bonded together.
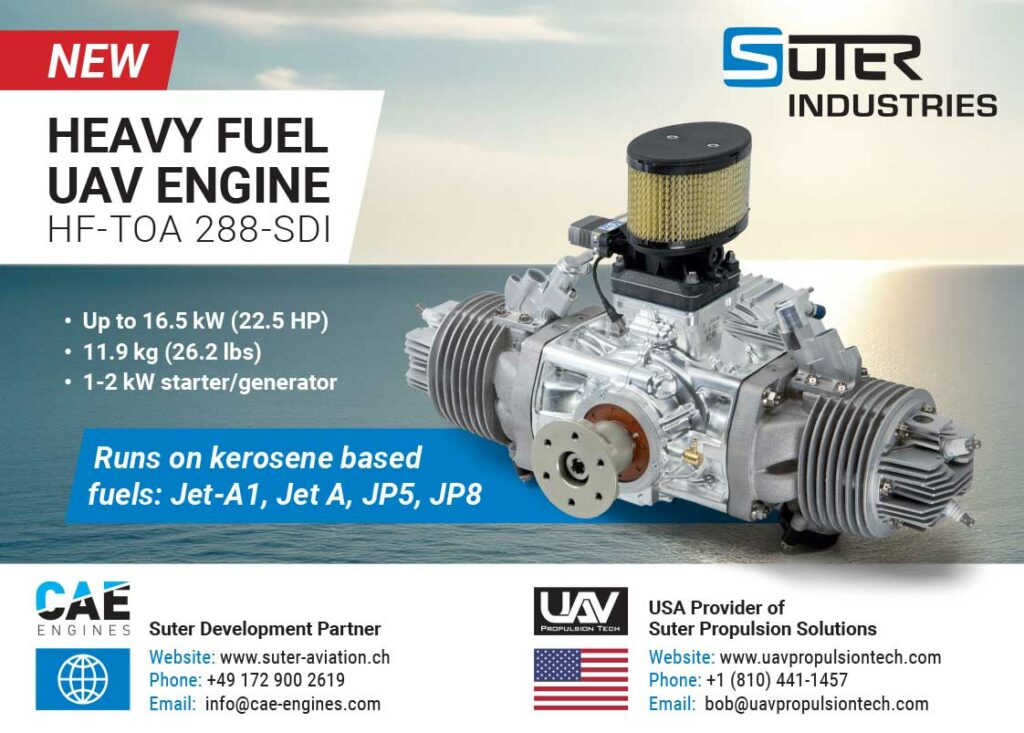
“It took a long time to narrow down to the contract manufacturers for our fibreglass composite parts we use, but we’re now very happy with their consistency. The exact same hull and deck pieces get delivered every time, even when we’re scaling up or down our orders, and our people in our workshop are able to get them prepped and rigged very quickly into a fully assembled unit each time without any surprises,” Boeschenstein says.
“The whole assembly process for a single SP-48 can be completed from start to finish in just under four weeks if we push ourselves, and we’ve always placed a lot of emphasis on being able to do that reliably and consistently.
“Buddy and Jigger put a lot of work into organising and optimising our production process plans, our jigs and fixtures, our tools, our training processes and other key inputs to make sure that when we’re building a USV in one part of the workshop there is no-one left with just a tape measure, trying to figure out where they’re meant to put a hole.”
Instead, the team’s fixtures are designed to be laid down on hull pieces, and those then register where a feature is meant to be, such that holes and hatches get cut into the exact same spot and dimensions every time, with no misreading of tape measures and no wrong measurements or other manufacturing errors.
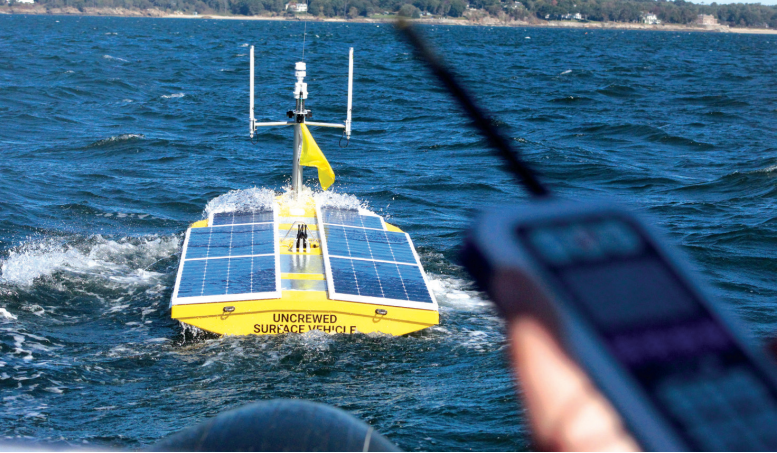
Solar electric boat
The solar-panel cells are made from a standard, widely available, high-efficiency crystalline silicon. The full panels are custom-built with a total panel rating of 816 W at 1 kW/m² solar generation.
That power runs from the six panels into the battery in parallel (so that if one is shaded, the others continue to function) via SeaTrac’s power-management system, built with customised charging boards. The battery is monitored via SeaTrac’s own in-house developed BMS, which controls the charging and discharging rates.
The batteries are engineered for a 39 V nominal voltage (with the 39 V supply ports interconnecting seamlessly with the battery bus). Floatage above or below that nominal level is minimised by virtue of the pack being composed of lithium iron phosphate cells – one of the more stable cathode chemistries.
“As one of the safer chemistries, it may have a slightly lower energy density than some others used in uncrewed systems, but it doesn’t quite suffer the same certification or clearance issues that higher energy, more unstable chemistries do,” Boeschenstein explains.
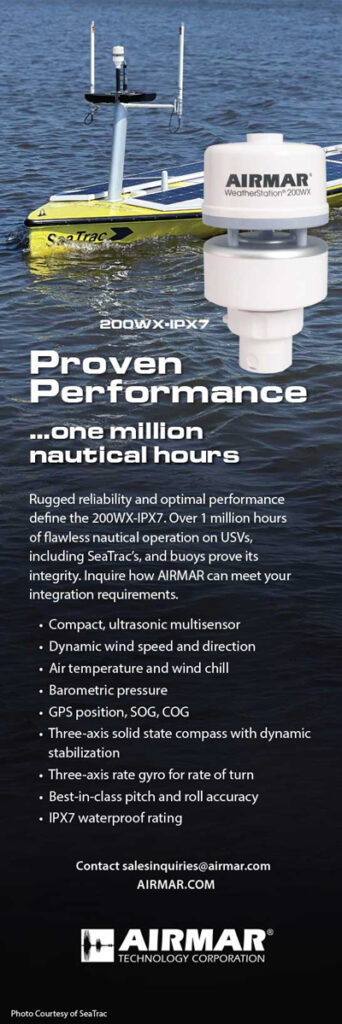
“That means it’s easier to get it shipped, moved by truck or approved for bringing it into some kind of base, so choosing that battery composition was a very conscious choice.”
Up to 6.75 kWh can be stored in the pack; a sizeable quantity, intended to offset times when lengthy periods of low sunlight occur across mission durations – the team having calculated expectations of average solar energy input against average power output to define battery requirements during development stages. The team is also in the process of releasing an enhanced capacity pack, which will offer 11.5 kWh to provide extra power when needed.
“In our collective heads, we anticipate that missions with the SP-48 should last between six to nine months before it becomes practical to bring it back to shore, so we can clean off biofouling and perform any other required servicing,” Boeschenstein says. “We’ve run several deployments of two months at a time – the longest so far – and on each occasion the USV came back with just a few barnacles and a full battery.”
Belt-driven thrust
A single propeller sits under the USV near the stern, made from anodised aluminium for corrosion resistance, and it is driven by a belt connecting up to a 1 kW brushless electric motor within the hull (which typically runs no higher than 500 W, except when sudden bursts of speed might be needed).
“The belt system came from Buddy and Jigger’s past work in automated cloth-cutting systems. Their gantry-controlled cutting machines all ran extremely reliably on belt drives, with very aggressive cycles of moving back and forth, so they developed a lot of experience with those sorts of drive systems,” says Boeschenstein.
Subsequently, the pair and their team determined that both alternate approaches of directly driving the propeller with the electric motor and using a gearbox instead of a belt would require the USV to have a larger form factor in the water.
Hence, the goal of size-optimised packaging won out, particularly since the founders possessed a close understanding of how to make belt systems that were highly efficient and reliable amid aggressive use.
“We also iterated on the propeller design, especially after running tests in and around seagrass beds when they’d tend to bloom the thickest, ending up with a geometry that minimises the tangling of weeds, fishing lines, and virtually anything else we might run into, inspired a little bit by fishermen that have to go out into marshlands and avoid getting tangled with debris,” Boeschenstein adds.
“Lastly, we’ve embedded some motor behaviours into our autonomy stack that has helped successfully shed everything that’s gotten caught in our prop blades during our deployments in the Gulf of Mexico over the last year.”
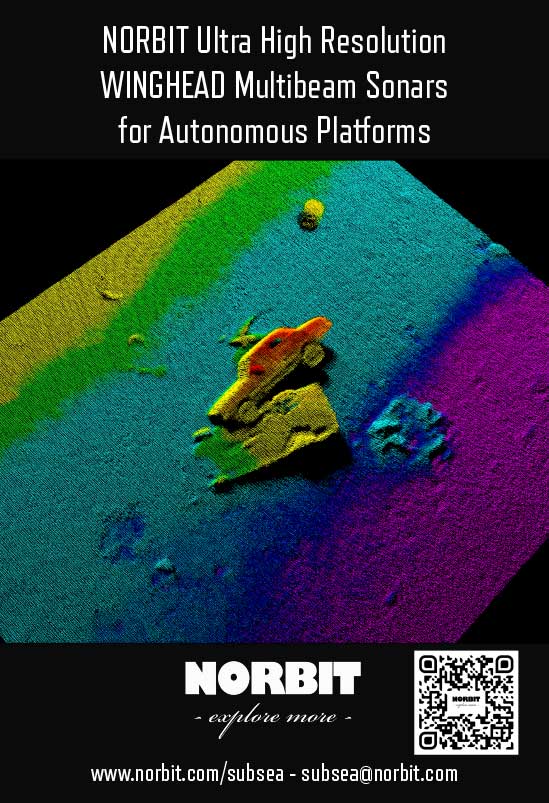
Distributed autonomy
The autonomy computing system consists of a distributed network of microcontrollers (including the BMS, power-management system and other low-level controllers).
A Windows-based computer, primarily for payload support, serves as something of a main interface, specifically for integrating, configuring and running payloads. That payload computer connects with the network of low-level controllers so they can share data.
“That connection also allows the USV to be operated using a different operating system; through an API and implementation of a backseat driver, we can enable commands to be passed to the network through the payload computer,” Boeschenstein says.
The founders built the base boat electronic system and software from the ground up, not only for the inherent safety of a distributed architecture, but also to have control over development and modifications to any part of the system, ensuring they could make changes to accommodate customer demands and move towards certifications.
The USV’s standard, marine-grade GPS provides a primary feed of satellite navigation signals into the autonomy control system, while a backup GPS is also installed for redundancy if the main system drops. A more advanced, high-accuracy GNSS can be installed for precision survey missions, such as multibeam sonar mapping.
“For missions like that, we can add in a Trimble Applanix INS and high-accuracy differential GPS to get very precise location data,” Boeschenstein says.
As a final situational awareness aid to the operator, four 1080p, continuous zoom cameras sit on the mast, although many other solutions can be installed, such as Teledyne FLIR thermal imagers for surveillance in low-visibility conditions (an M364C camera from that company having previously been integrated on an SP-48 for work with Task Force 59, the US Navy’s premier uncrewed r&d fleet).
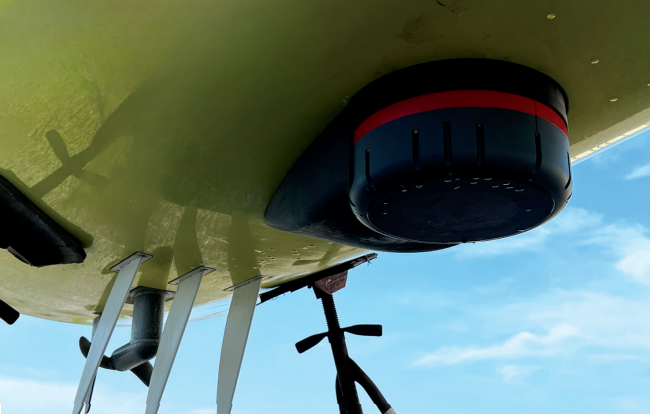
Ocean data
As well as those cameras, a wide array of payloads have proven compatible with the USV and valuable to SeaTrac’s end-users. For instance, the first multibeam sonar that the team integrated was Norbit’s iWBMS H-N, a widely used system for high-quality seafloor mapping at an efficient power draw, which suited the USV’s form factor closely.
“We’ve also used the R2Sonic 2020 multibeam and gotten good data with that one too. We are quite agnostic to echosounders, so long as they physically fit our moon pool and their overall SWaP makes sense within what our USV can offer,” Boeschenstein says.
The moon pool offers a cylindrical volume with a maximum diameter of roughly 10 in, but SeaTrac is open to customising sensor housings to fit payloads elsewhere on the USV.
SeaTrac has integrated Teledyne Marine’s Workhorse Monitor ADCP as its primary tool for current-measuring missions, although Nortek’s Signature 1000 has also been operated for some customers.
“We have also had Seaview Systems’ SVS-603HR wave-height sensor working onboard, which we used to measure things like maximum wave heights and periods of waves,” Boeschenstein adds.
Additionally, AML Oceanographic’s water-quality measuring sondes have been used, particularly the AML-3, which judges depth and two other parameters of the end-user’s choosing, such as turbidity, pH or chlorophyll.
These have sometimes been hard-mounted to the hull, but nowadays the team will more often integrate them into a specially made winch, designed and engineered by SeaTrac, primarily for running sound-velocity profiling simultaneously with multibeam echosounder work.
“The winch uses a non-powered tether to keep it simple, as a tether can be run much longer if you aren’t running power and comms through it, and it also means we don’t run into reliability issues with things like slip rings that can break,” Boeschenstein explains.
“AML also supports a wireless charging solution that we use. When the USV completes its cast, the winch hoists the sonde up to proximity with the charging emitter, we collect the data it has amassed over wi-fi and the sonde gets recharged while dumping data, so it’s ready for another mission without any technicians needing to physically handle anything shore side during that process.”
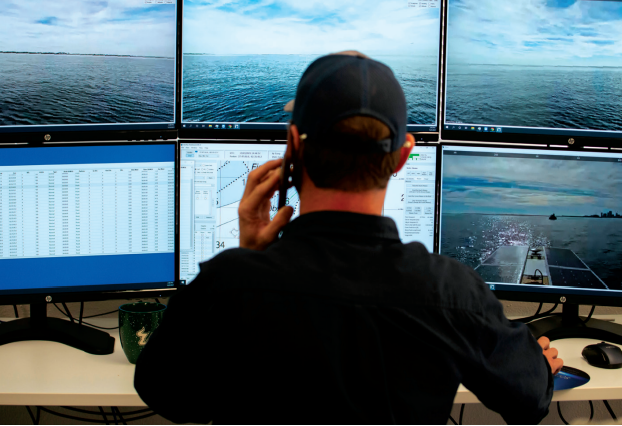
Data links
Given that the USV may spend multiple months at sea per mission, data-link security via a plethora of comms systems is paramount.
“As they say in the navy, two is one, and one is none, so redundancy is everything for communications as far as we’re concerned, because you can’t predict when something will go down,” Boeschenstein says.
“The base boat comes configured with a 916 MHz data link for LOS connections, and that’s primarily used with a handheld GCS that we first use to drive the boat off a trailer, away from the dock, and potentially through a busy channel for deployment or recovery. But, for the rest of the way, it is critical that the USV can work on its own without needing people to intervene.”
On top of the LOS RF connection, the USV integrates two cellular connections – a primary and a backup – as well as an Iridium SBD (short-burst data) system; the latter functioning as a backup (albeit a slow, high-cost one) for emergencies, particularly when cellular links go down, delivering small, periodic updates on where the boat is and if it still functions.
“When you get out of cell range, primary satellite communications is handled by an Iridium Certus 100, which provides a good BVLOS connection to the SP-48, with high enough data rates to maintain a good position lock and to send commands much faster than SBD, as well as receiving some low-definition pictures from the cameras every five to 10 pictures,” Boeschenstein adds.
“Hence, the Certus becomes our primary data link for most offshore missions, as cell networks don’t work far into the ocean, except maybe in a few networked parts of the Gulf of Mexico. We also have a battery operated tracking solution on the USV, so if it stops and all comms links drop for some reason, that gives a GPS ping for us to understand, without fail, where the boat is.”
For passing vast amounts of data quickly, Starlink High Performance Dishes have been installed on a few customers’ boats, although, at 100 W, this system draws significant power (particularly compared with the Certus’ 8-10 W), so it is used sparingly when integrated.
As of writing, SeaTrac is about to integrate a Starlink Mini for the first time. Though a lower-bandwidth system, its SWaP stands to make it a more sustainable fit to the SP-48’s power budget. SeaTrac has also integrated and successfully operated a Silvus high-broadband radio for Task Force 59, to function as part of its mesh radio network.
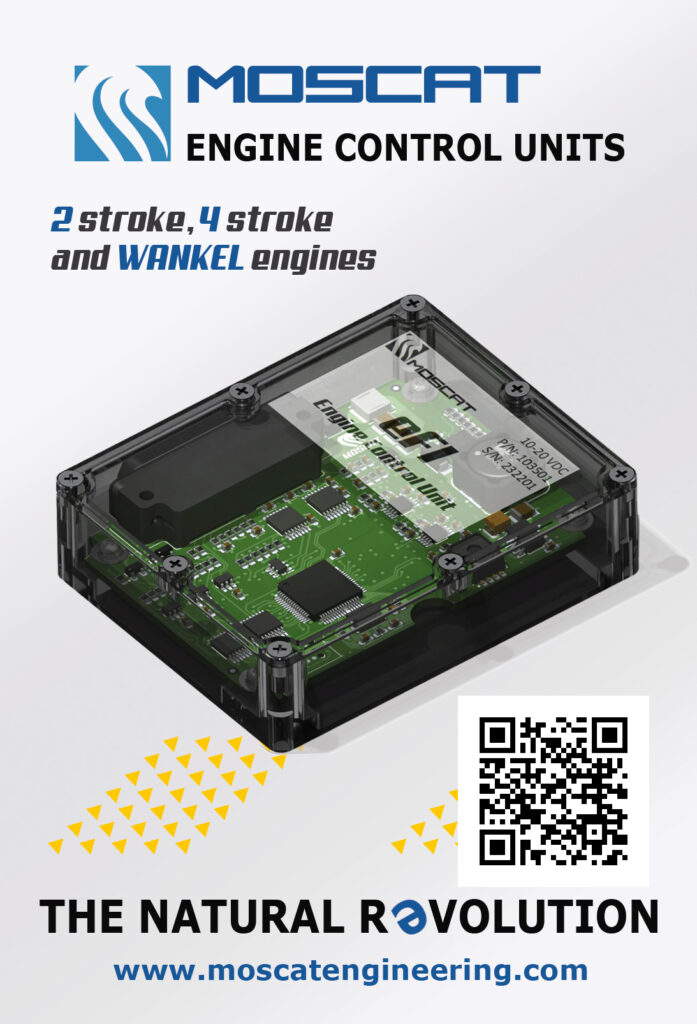
Future
Having sold many units, SeaTrac is determined to move on from building and operating single SP-48s to operating them as fleets or swarms, given their low cost and easily manufacturable nature.
“You can survey huge areas at scale by having several of these USVs working together, to get a real, big picture of the environmental state of the oceans instead of looking through a straw at our planet’s giant, systemic problem areas,” Boeschenstein says.
“To me, that’s a really exciting prospect: gaining so much operational efficiency. Having one operator watch one boat 24/7 is easy, but most of the time nothing is happening. There is minimal incremental cost for deploying one, two, three or more of these.
“We’re not burning any fuel, and personnel are more than capable of monitoring larger fleets of USVs, especially if they’re intelligently working together to create a grand view of what is happening in the ocean.”
Key specifications
- SeaTrac SP-48
- USV
- Monohull
- Solar-electric
- Length: 4.8 m (15.9 ft)
- Width: 1.4 m (4.6 ft)
- Draft: 42 cm (1.4 ft)
- Empty weight: 275 kg (606 lb)
- Payload capacity: 70 kg (154 lb)
- Maximum speed: 5 knots
- Nominal endurance: six to nine months
Some key suppliers
- INS: Applanix
- Multibeam echosounder: Norbit
- Sonar: R2Sonic
- ADCP: Teledyne
- ADCP: Nortek
- Wave height sensor: Seaview Systems
- Additional sensors: Airmar
- Water data sensors: AML Oceanographic
- HD cameras: Axis
- Thermal cameras: Teledyne FLIR
- Satcom: Iridium
- Satcom: Starlink
- Winch/profiling system: SeaTrac winch with AML-3 or AML-6 instruments
UPCOMING EVENTS
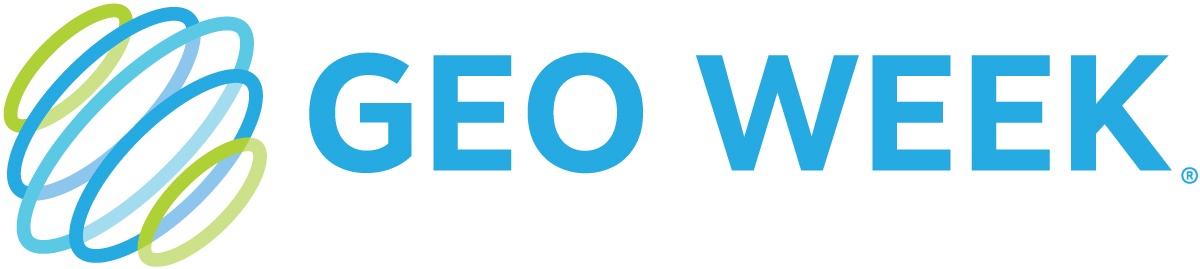
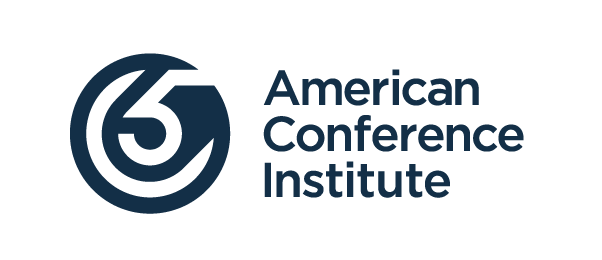
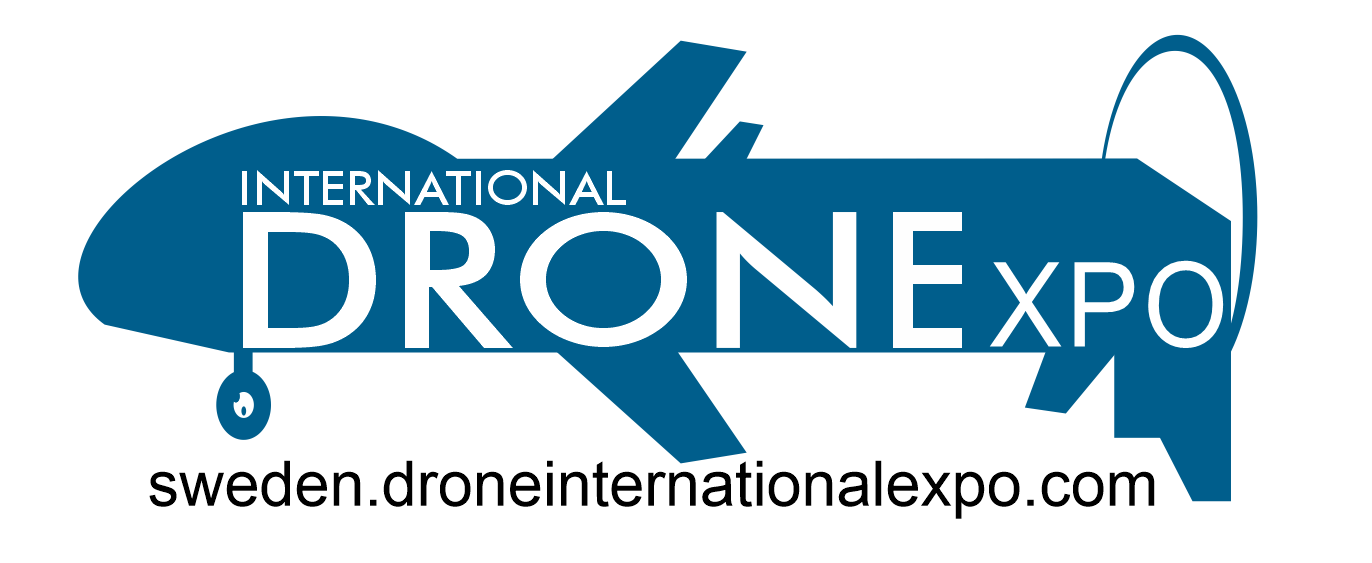
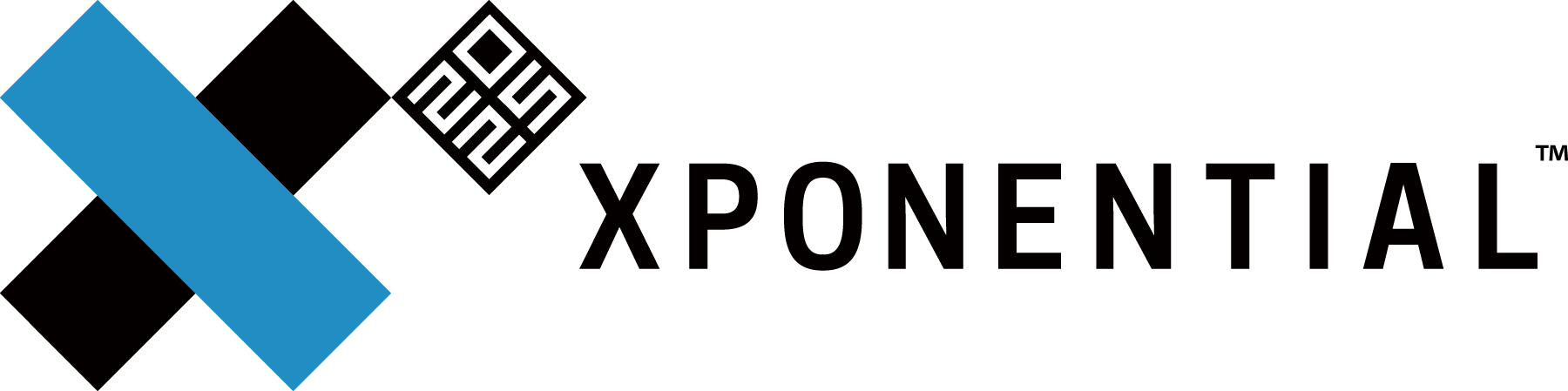
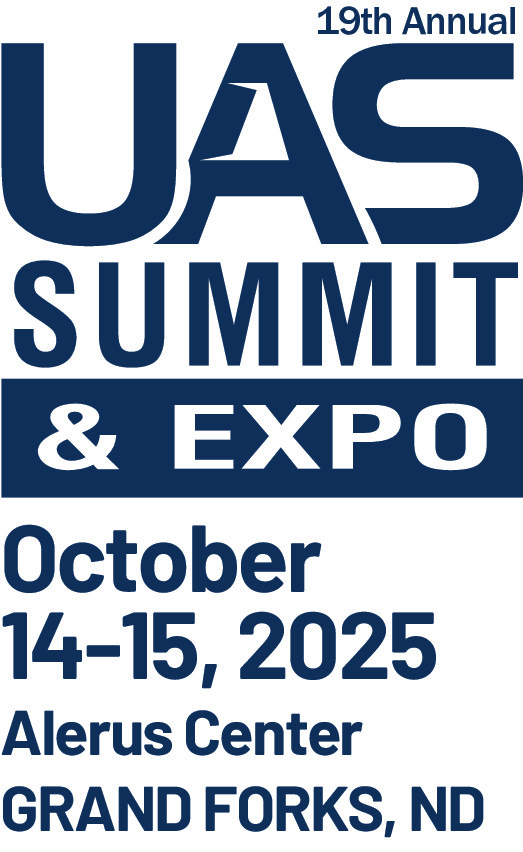

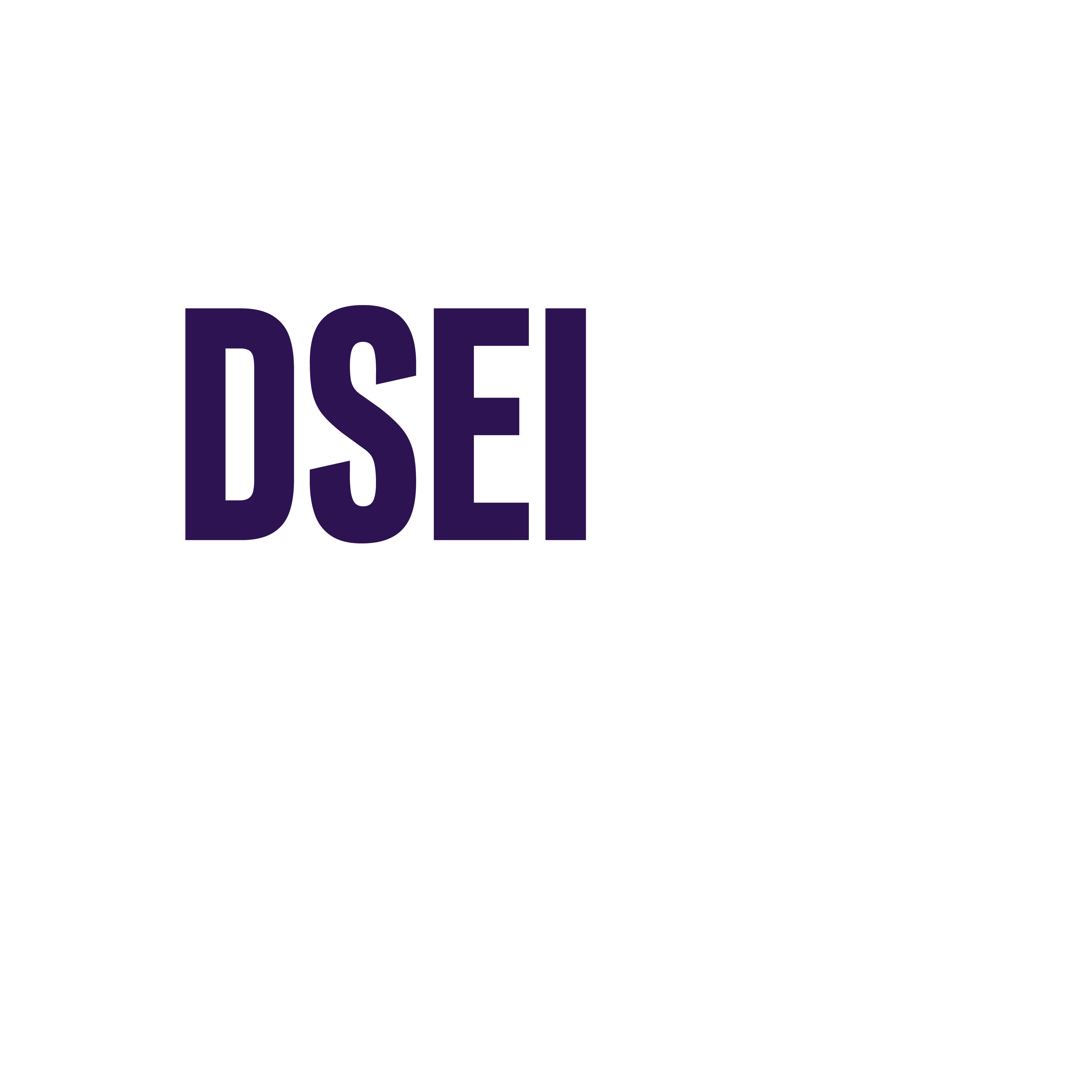
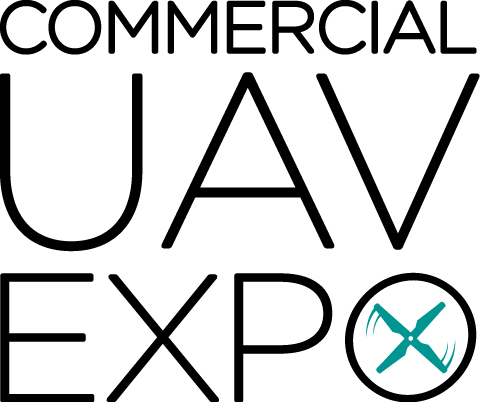
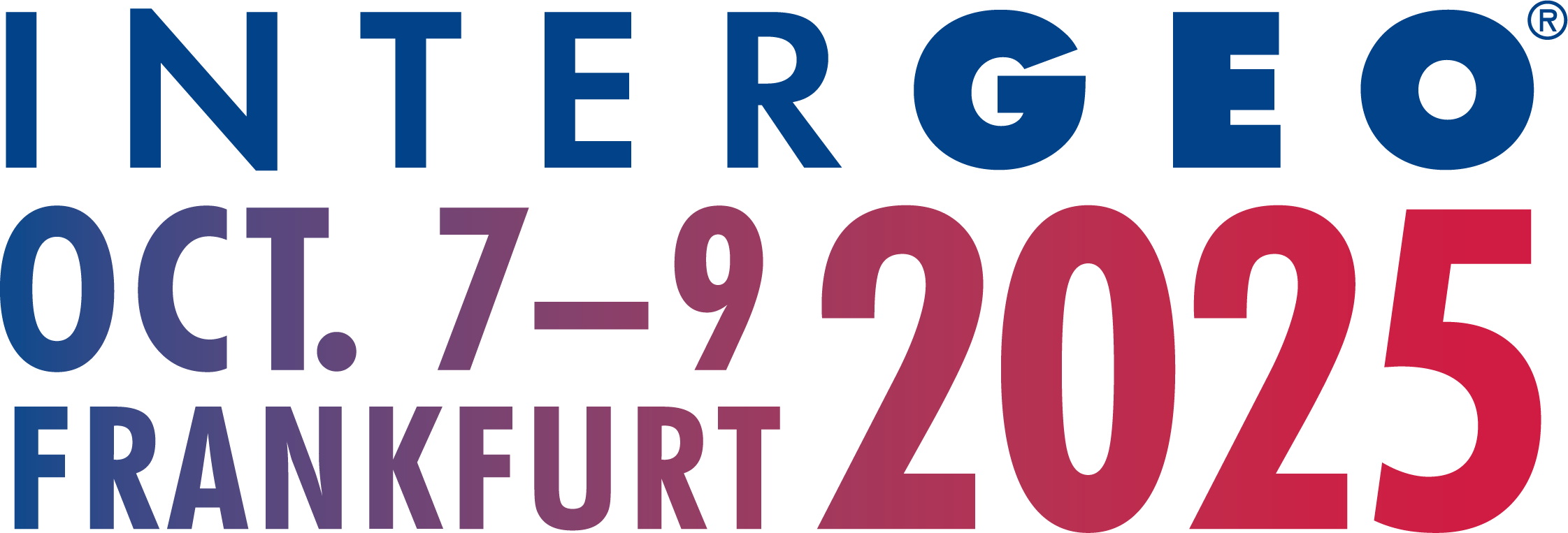
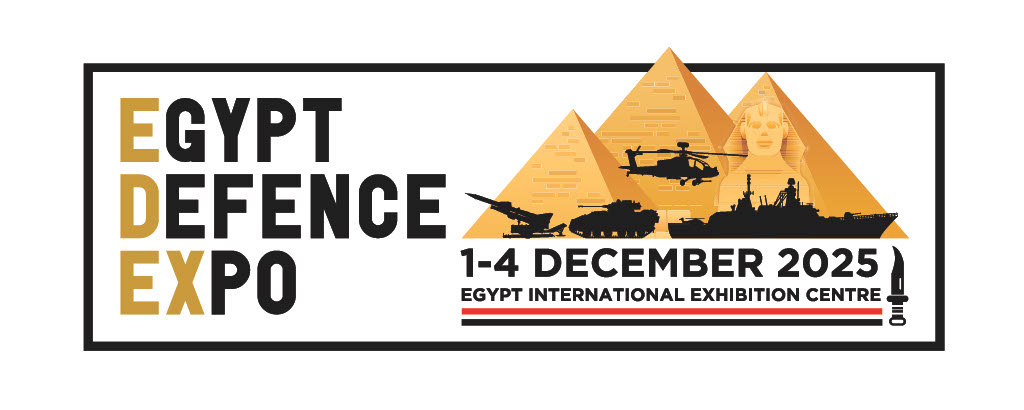
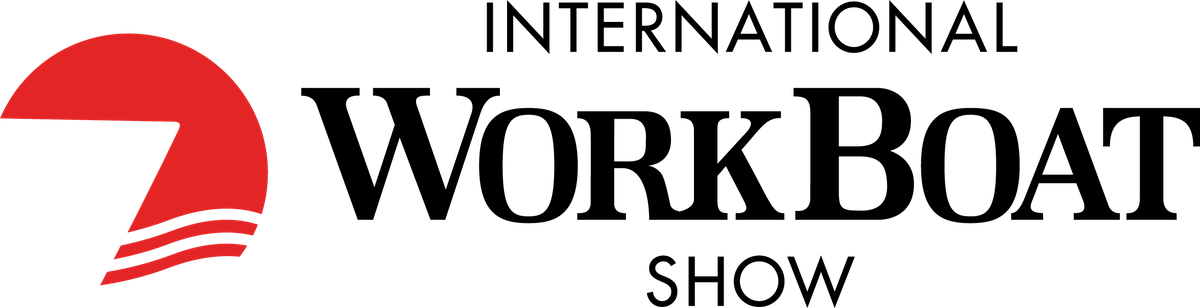