Seasats Lightfish USV
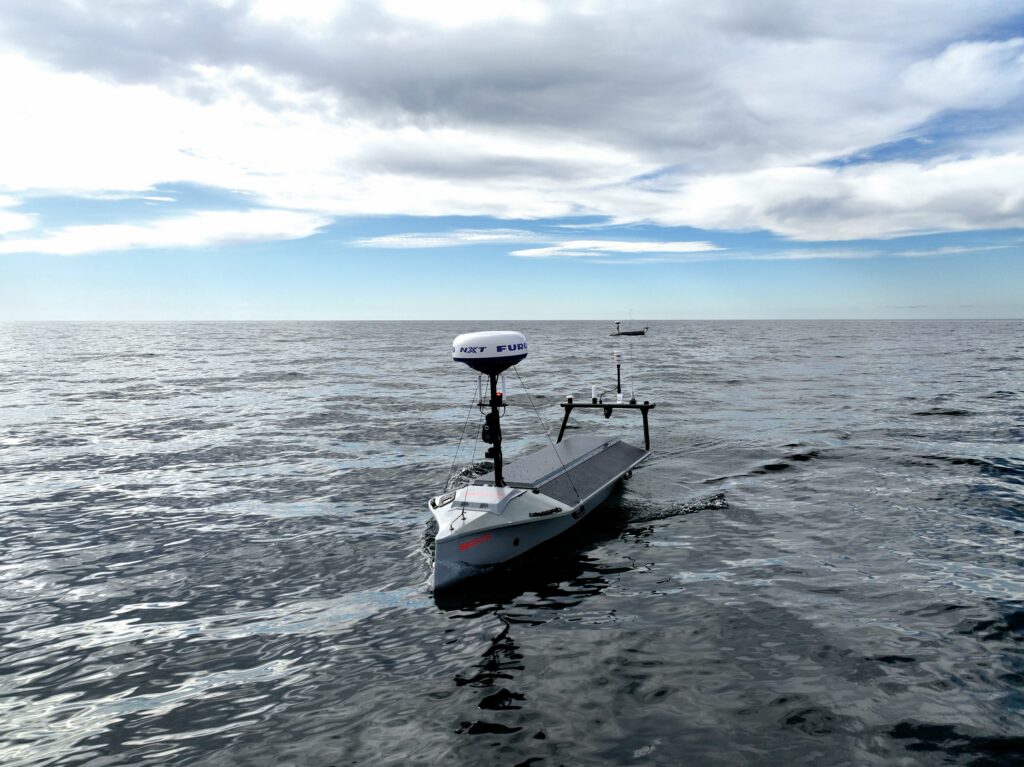
(All images courtesy of Seasats)
We know the way
Rory Jackson investigates a company working to prove the Pacific Ocean can be crossed with a small, reasonably priced survey USV
Autonomously crossing the world’s great oceans is a challenging undertaking, but one made easier when uncrewed systems engineers have a large budget to work with, as the last few years have proven. But managing such stable, fault-free and persistent operations with a USV that anyone could afford is another matter altogether.
The Pacific Ocean is Earth’s largest body of water, but a small number of USVs have managed to cross it, including those from Australia’s Saildrone in the west and the Boeing-Liquid Robotics Wave Glider in the east. These USVs have significantly lower prices and operating costs than traditional, crewed research vessels, which often run into hundreds of millions of US dollars per unit.
As we write, a very different platform is poised to achieve its first Pacific Crossing; one that comes at a fraction of the price of its headline-grabbing counterparts – the Lightfish USV from Seasats, based in California.
Given the sheer size of the ocean and the severe weather phenomena that can hammer vessels sailing it, many question whether a $200,000 USV could manage a trans-Pacific crossing. Such skepticism is precisely what motivated Seasats’ journey, which began in January when it launched one of its Lightfish USVs from the port of San Diego.
As Seasats CTO Dylan Rodriguez tells us: “We advertise the Lightfish as a persistent platform, so we have to be able to demonstrate that persistence. I’ve also previously worked for some of our competitors, where we all shared the frustration of using components or seeing vehicles that couldn’t do what their makers claimed they could do.
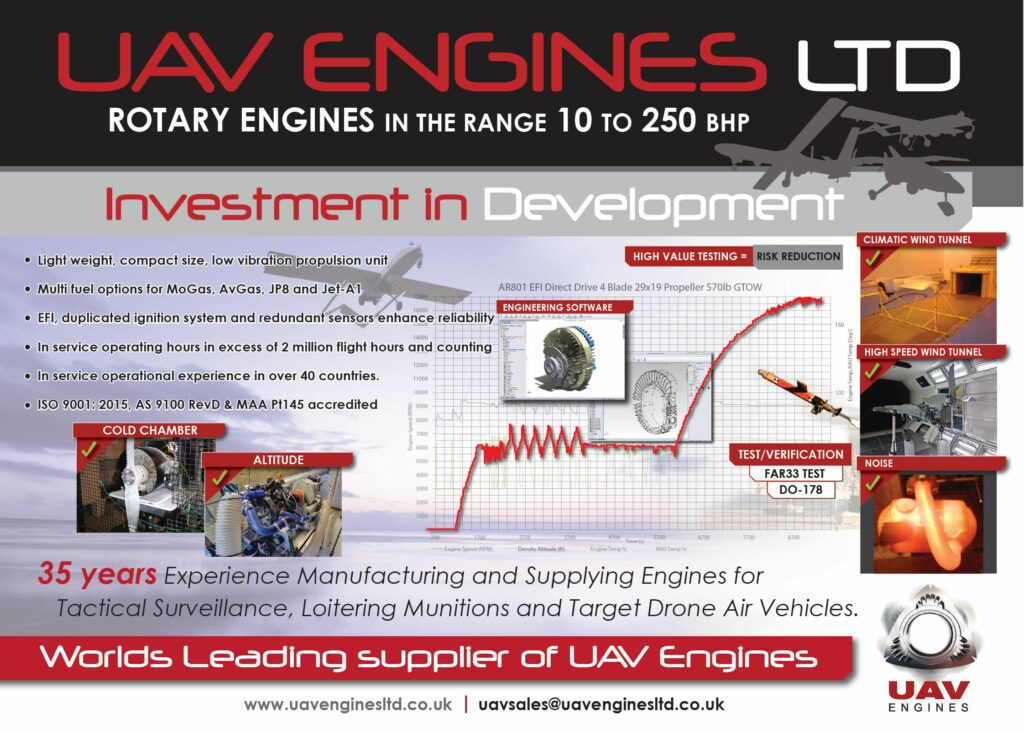
“So, internally, it has been really important to everyone here that we don’t just make claims of what Lightfish can do – we have to show it.”
Max Kramers, head of vehicle design at Seasats, adds: “Our users are the kind who want to send a USV far out into the middle of the ocean to collect and stream video and hydrographic data for them, and to not have to constantly watch it for potential dangers. At the price point we’re offering, we are receiving interest from people who need USVs but didn’t even know they existed before us.”
The watercraft has hence become a cost-effective choice among both budget-constrained and wealthy organisations, with 30 units in service as of writing.
The 3 m-long, 1 m-wide, electric monohull boat is built from composites and solar panels to hit key mechanical and power capacities for persistent endurance. If pressed, Seasats can construct upwards of 20 units in a month.
The Lightfish
Looking down at the Lightfish, one sees square solar panels covering much of the top deck, flat down the centre, and angled on the port and starboard sides to better capture sunlight, as well as a mid-frontal mast and rear mast for mounting instruments such as antennas, lights and video cameras.
Beneath the deck hatch, Seasats installs a lithium-ion battery with up to 4 kWh of energy at the centre of buoyancy, a cold combustion generator that serves as a range extender in front (in addition to the solar cells above), and payload electronics behind.
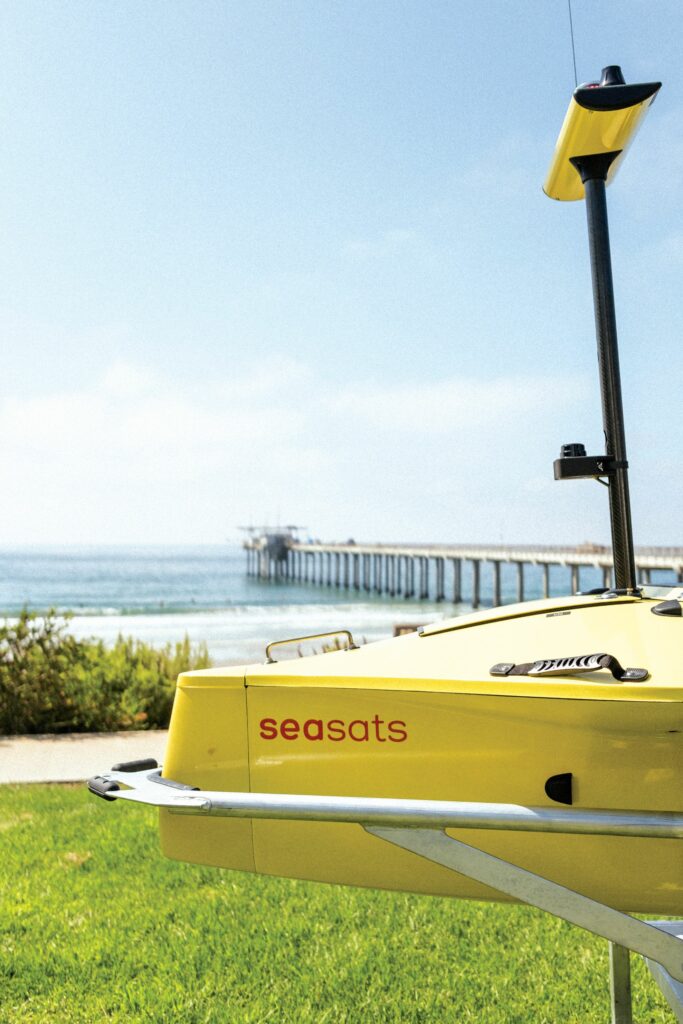
Further across the boat, one finds a single electric motor propeller and rudder combo installed at the rear, enabling up to 4.5 knots of speed, with control electronics, including an independent backup GNSS tracker, inside the bow. A retractable keel for added stability is integrated underneath.
Up to 50 kg of payload mass can be installed, with up to 200 W over 5-28 V that can be allocated to powering them, including EO/IR cameras, SIGINT systems and EW devices on deck, and active and passive sonars below deck. Depending on how much payload (and added battery) mass is installed, the Lightfish typically weighs 132-192 kg.
“We have made sure Lightfish only needs four to six people to pick it up on their shoulders and walk it down a beach for launching into the waves. We’ve seen too many ocean platforms that are trailer-only, so their points of entry and recovery are limited to where you can find slipways,” Rodriguez says. “And if you do have a crane or slipway then one person is enough to do it all.”
Journey’s preparations
Seasats has previously managed a journey from San Diego to Hawaii in summer 2024, before reaching just past 2300 miles (3700 km) across the remaining Pacific – roughly halfway between Japan and Hawaii – before being scuppered by a typhoon.
“We lost the boat, but streamed all the telemetry. Admittedly it was exciting watching 80 knots of wind battering the USV at certain moments, and watching the sea state go up through IMU readings, though with a recovery being impossible, we didn’t get to do a full autopsy,” Kramers notes.
“We found the likely problem was an intake to one of our air-breathing generators; then tested it in various ways. Although we can’t go into too much detail, we corrected that potential issue, and changed a few more things around to sense and take precautions of other risk factors. The ocean always has a say, but we’re quite happy with this revision.”
Such design changes have now been made across all Lightfish units. As with the first attempt, the current one is being made with a stock Lightfish USV using no special enhancements or integrations to ensure a successful crossing is possible with any of the units leaving the factory.
The USV launched from Dana Landing in San Diego using a boat ramp that Seasats has used many times for tests. A launch cradle has been built in-house around a dolly designed to house individual finished Lightfish units.
For launching both tests and commercial operations, Seasats rolls one of these cradles out of its workshop and into a van before driving it to the designated ramp for deployment, where the cradle is walked into the water and the USV is decoupled from the dolly to slide away by itself.
Rather than supply a physical checklist of manual tests or inspections required before deployment, the user interface (UI) contains a pre-launch checklist detailing 10-12 items, such as ensuring the hatch is secured, the backup tracker is working, the cellular radio is sending and receiving normally, and so on.
Automated checks are always running in the background, as is a dedicated error display window for indicating any potential causes of concern, with the UI functioning via the web browser on any computer, tablet or phone for ease of access and mission monitoring. An audit log window provides a timeline of subsystem tests, checks, commands and other actions performed by monitoring and operations staff.
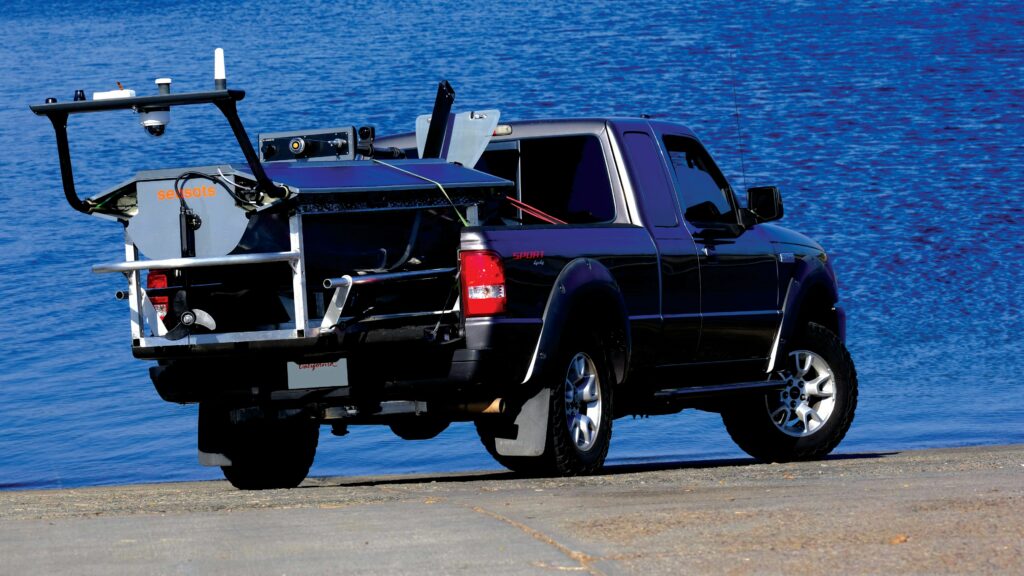
View from the bay
The Seasats team can monitor the USV’s progress from its facility in San Diego, or from any device that can log into the web portal for its GCS software or UI (the public UI can be viewed freely at track.seasats.com).
Rodriguez developed the majority of the UI’s initial architecture, with a particular focus on keeping its layout and functions as simple and user-friendly as possible, such that any non-engineering personnel could use it.
“Because Lightfish is a solar boat, planning out the route was a lot like planning routes for a sailboat race. There are different aspects, different things across different aspects of the ocean that you want to avoid, and others you want to take advantage of,” Kramers says.
“On our first trip from San Diego to Hawaii, we just drew a straight line and stuck to it to demonstrate that our vessels can do that. Our customers can always keep it simple and do that too, but this time we wanted to optimise more, so we checked weather patterns because cloud cover is something you want to avoid, and it being winter in the northern hemisphere at the moment, directed the route further south than we did last time.
“The benefit is that we get more energy extracted via solar per day and, yes, we travel a fair bit longer distance-wise, but it still makes the trip significantly faster.”
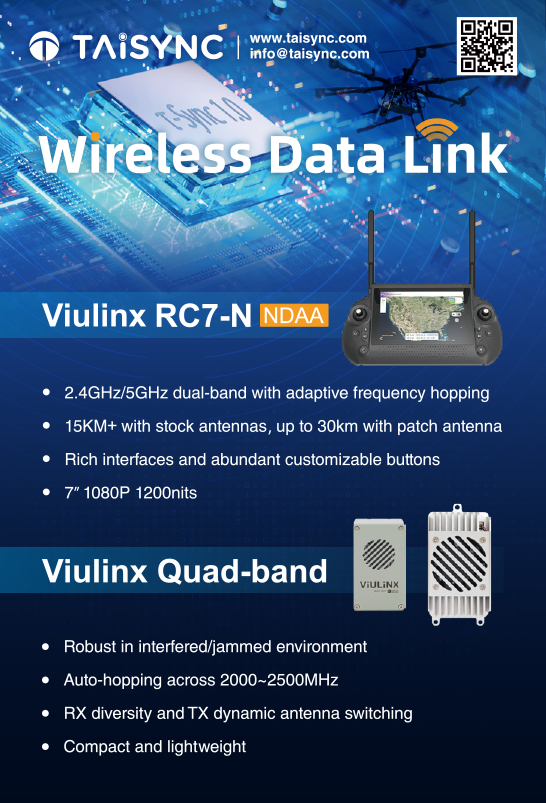
Not long after deployment from San Diego, the USV quickly turned south before taking a south-westward curving trajectory towards Hawaii. It successfully crossed through Waikiki in Hawaii during the week starting March 3, some slight acceleration orders having been sent to the USV so that it could take part in a US Naval event there.
After departing the archipelago, the vessel will follow a route engaging in a westerly line towards Guam (to showcase the boat for US Navy personnel there, as it did in Waikiki), following which it will turn northwards in the direction of Japan.
The waypoints were plotted manually, although Seasats may in future engineer AI-powered means for automating survey route plotting in the event that further ease of use could be achieved.
Balance of power
In addition to viewing and adjusting the route where necessary through an on-screen map of the Pacific, the company scrutinises all possible health and performance parameters of the Lightfish as it travels. Of these, the most critical is a plethora of power sensors that track power telemetry for every subsystem.
A detail-dense analytics screen that Rodriguez shares with us displays a pie chart of average power consumption for every onboard electrical or electronic device, as well as power generated by the solar and generator systems.
In total, 24 slices of the pie were shown, including low-voltage devices such as an Ethernet switch and a USB hub; naturally, the two power-generation systems occupied slightly more than 50% of the circle.
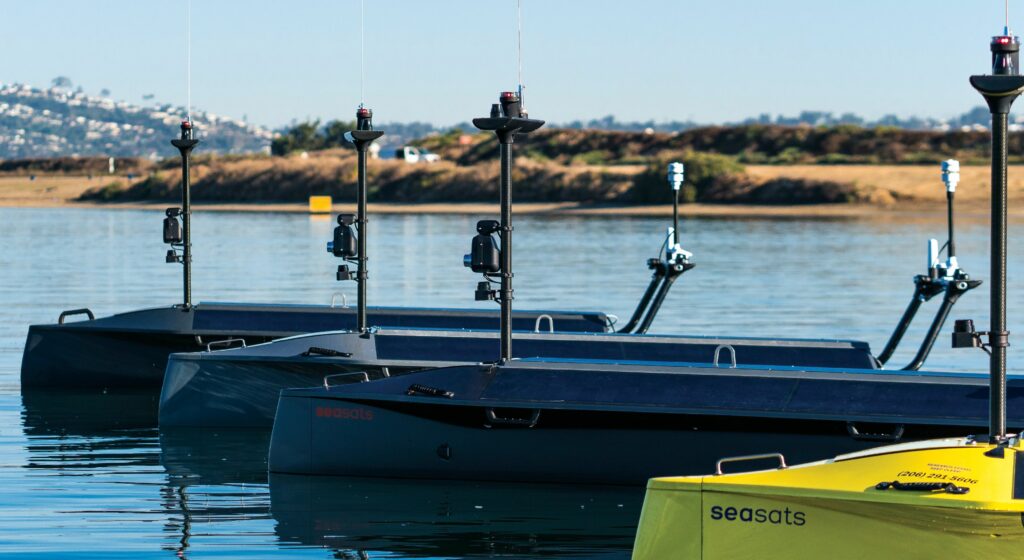
The page also showed numerous configurable graphs plotting power usage or generation over time for individual subsystems, and some for multiple subsystems against one another, such as clusters of data from the BMS, as well as time charts showing when certain devices (such as the bilge pump and the different BVLOS communication devices) were activated or deactivated.
A dropdown box in the top-right enables the user to set the length of time over which averages and stats are shown (running from the prior five minutes to the past several days or weeks), and aggregates for high-level stats such as power balance over the selected time period also display persistently on this page.
Sunshine and alcohol
As the USV travels, its thrust and rudder motors typically consume the most power of any subsystems. A single COTS Torqeedo motor pod propels the boat forwards. Seasats has trialled many of that company’s solutions.
“Testing multiple motor pods simultaneously for six months in a fast-paced environment is hard, but very much necessary to guarantee a six-month endurance, so we have saltwater tanks at our shops, and motors, servos – essentially everything new that’s to go into the boat. They all get submersed and run in those saltwater environments at different duty cycles for their lifespan,” Kramers says.
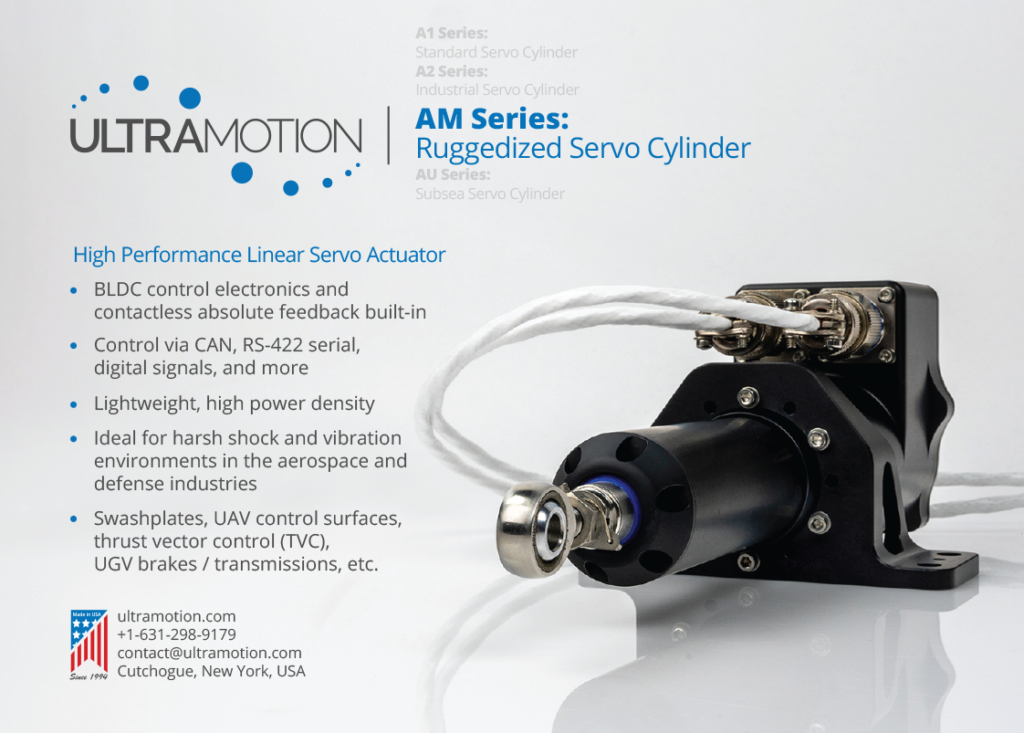
“IP ratings are self-certified and, frankly, a lot of companies stretch their stats, so it’s pretty crucial to do our own component validation before we opt to integrate and sail with them.”
Through such testing, Seasats validated and installed its rudder servo, a device operating on a stainless steel gear train and brushless DC motor (built and supplied by an undisclosed company).
Through that <500 g device, the USV manufacturer achieves a long-lived rudder-steering capacity over multi-month operations (an impossible proposition for hobby-grade servos), as well as over 1300 n/cm of torque for harsher sea states.
As mentioned, most of the USV’s in-operation energy replenishment comes from its solar panels – nominal solar generation being 415 W – with the power analytics screen enabling users to make ad hoc adjustments to vehicle speed or subsystem activations if something onboard is consuming excess energy.
“We use a custom-built, flexible, monocrystalline, silicon solar panel,” Rodriguez says.
Kramers adds: “We also have our supplementary methanol generator. It weighs around 9 kg, provides about 125 W continuously, and fits nicely in the Lightfish. The tank the supplier provides can carry up to 30 kWh of fuel. It is a cold combustion engine, and it essentially runs on hydrogen, but the hydrogen is suspended in methanol.
“That can be used when we’re doing multibeam echosounder surveys, given that those types of sonars are very power-hungry; and there’s other payloads too that need the generator’s level of power output, whether it’s EW jamming [electronic warfare], towfish, or so forth.”
Staying durable
Naturally, the USV’s long endurance at sea depends not just on robust power but also on a strong hull, and Seasats has chosen a particular fibreglass-epoxy composite for Lightfish’s outer shell – a durable and lightweight material ideal for weathering ocean environments, as well as an easier choice than aluminium if the USV were to remain portable for hand carrying and launching.
“The marine environment is a really hard thing to deal with. There are hydrostatic loads and hydrodynamic loads, both of which can be very difficult to predict, and so we went through several iterations on the USV’s hull structure, as well as the subsystems before reaching our current design,” Kramers says.
As for ensuring subsystem survival against the ravages of the ocean, Rodriguez adds: “The last company I worked at was Ocean Aero [featured in Issue 9] for five years. That platform was submersible and an amazing piece of engineering, but if you make something submersible, you make it expensive and hard to disassemble.
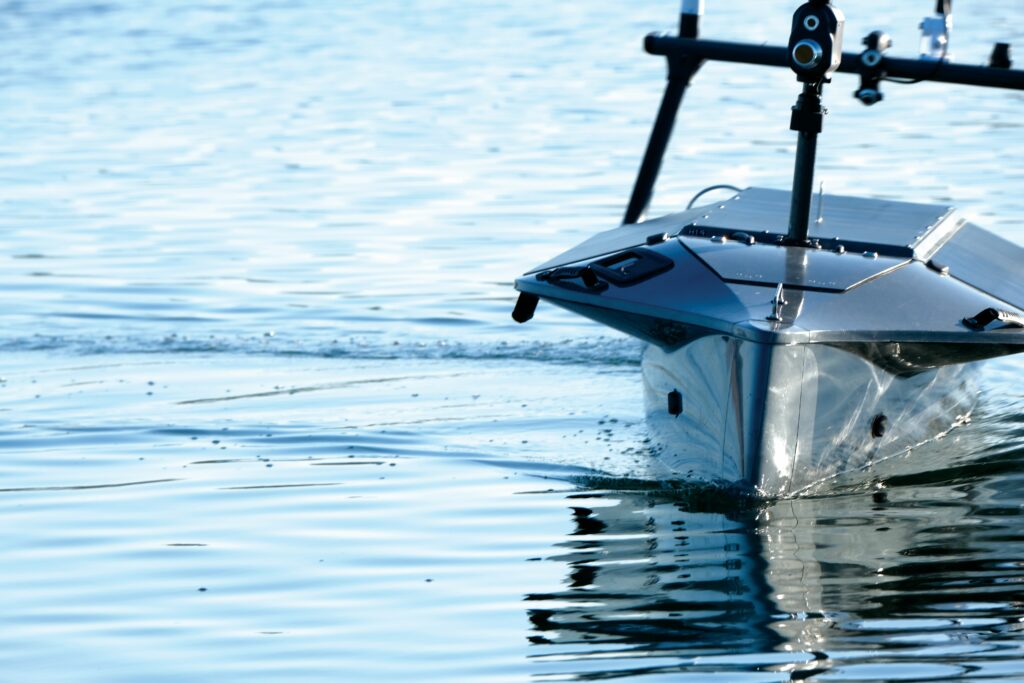
“Engineering is often a series of compromises, and with the Lightfish there’s been some optimisation that we’ve worked very hard on, so that all the subsystems are sufficiently water-proofed, but not a huge pain to take apart and not expensive.”
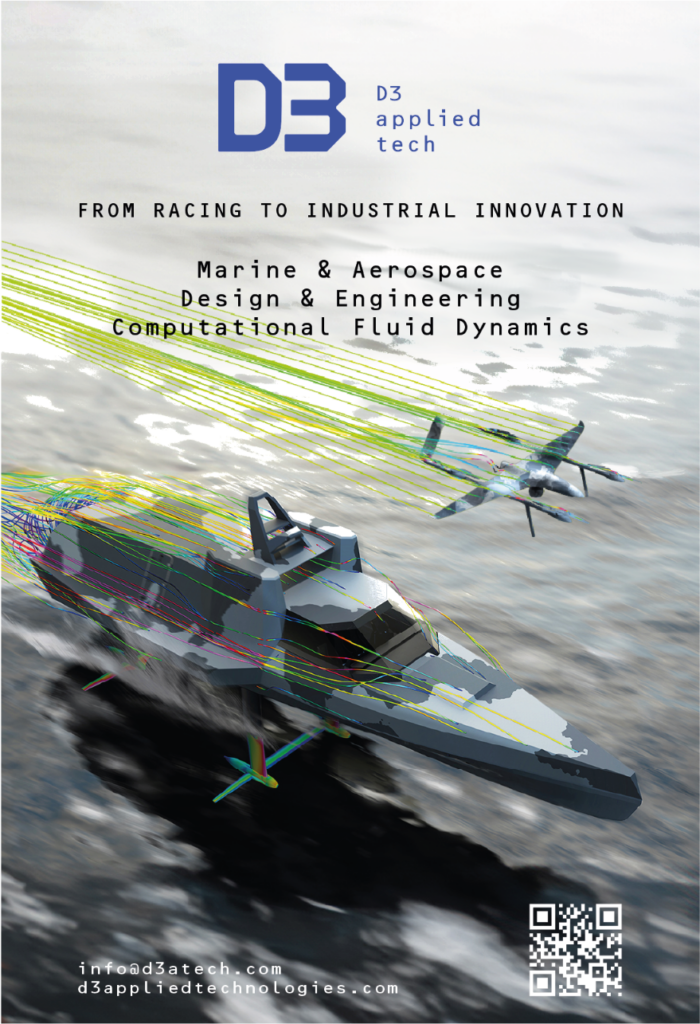
Selection and testing of sealing solutions formed much of the company’s optimisations. Within the Seasats office one can find a two-storey, vertically disposed PVC pipe, which the team will periodically fill with salt or fresh water for high-pressure submergence testing of different housings and sealing agents (as well as key components such as marine connectors).
“That pipe has proven its worth with the USV’s non-submerged components too. We’ve found antennas whose manufacturers advertise them as IP68, but they aren’t at all able to survive up to 30 minutes in 1.5 m depths of fresh water in the PVC pipe, which ‘IP68-rated’ is supposed to mean,” Rodriguez explains.
“It might sound like an exhaustive level of testing, but you can see that without it we could’ve sent 20 boats around the world that were doomed to lose their comms links as soon as they got rolled over by waves for the first time.”
In addition to the chemical hazards of the ocean, biological hazards are also a perennial concern for persistent maritime platforms. While many anti-biofouling approaches exist, Seasats has opted for a copper-coating treatment across much of the Lightfish to protect against buildups of algae and barnacles.
A physicist at sea
As Lightfish maintains its course to Hawaii (or Guam or Japan, depending on the time of reading) a prudent selection of navigation systems provides a first layer of aiding data that keeps it on track. Specifically, an IMU and GNSS receiver have been chosen off-the-shelf to maximise precision within the bounds of Seasats’ affordability philosophy.
The second layer, however, is a software-derived aiding source that is unique to the company, which Rodriguez refers to as its onboard physics model, and he cites it as a key part of how Seasats provides GNSS-denied navigation to those various government organisations among its prospective customer base.
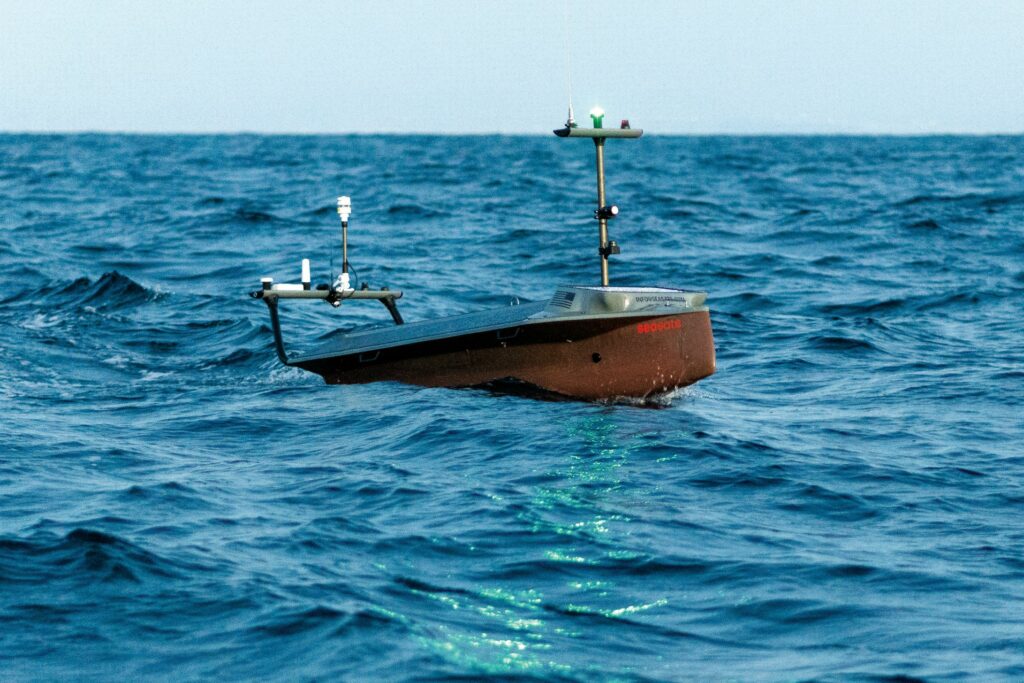
Development of the model began alongside the design of the Lightfish’s first physical prototype, as part of the company’s internal simulations to inform CAD work ahead of real-world sailing tests. Access to that simulator is now given to each customer to simulate their missions using digital twins and observe how toggling power loads or other parameters may benefit mission runs.
“The same physics model inside our simulator is also constantly running inside Lightfish, so, for instance, if its main computer knows it is applying half power to the motor, then it knows how fast it should be travelling through the water and the local weather. Similarly, it can track for steering impacts from the rudder and roll or heave through the IMU,” Rodriguez explains.
“So, if it sees a significant divergence between where the GNSS claims its position to be and where it knows it should be, it can first alert the operator that there might be spoofing or jamming going on, who can then trigger the USV to use the physics model as the primary navigation data source. At that point it becomes 100% autonomous, as in not even using external aiding data for navigating anymore.”
Knowing that persistent remote monitoring and tracking of autonomous assets remains a critical requirement for most users, the USV is equipped with a cellular modem for terrestrial BVLOS comms, Iridium Certus and Starlink radios for satellite-based data links, and an Iridium short-burst data (SBD) radio conventionally used for sending small packets of emergency telemetry or alerts.
As well as the redundancy entailed by integrating four different data links, the cellular modem is keyed for two telecoms providers. Lightfish is also programmed with a system of failovers and prioritisations for its different comms technologies, intelligently sending varying sets of information over different radios as required.
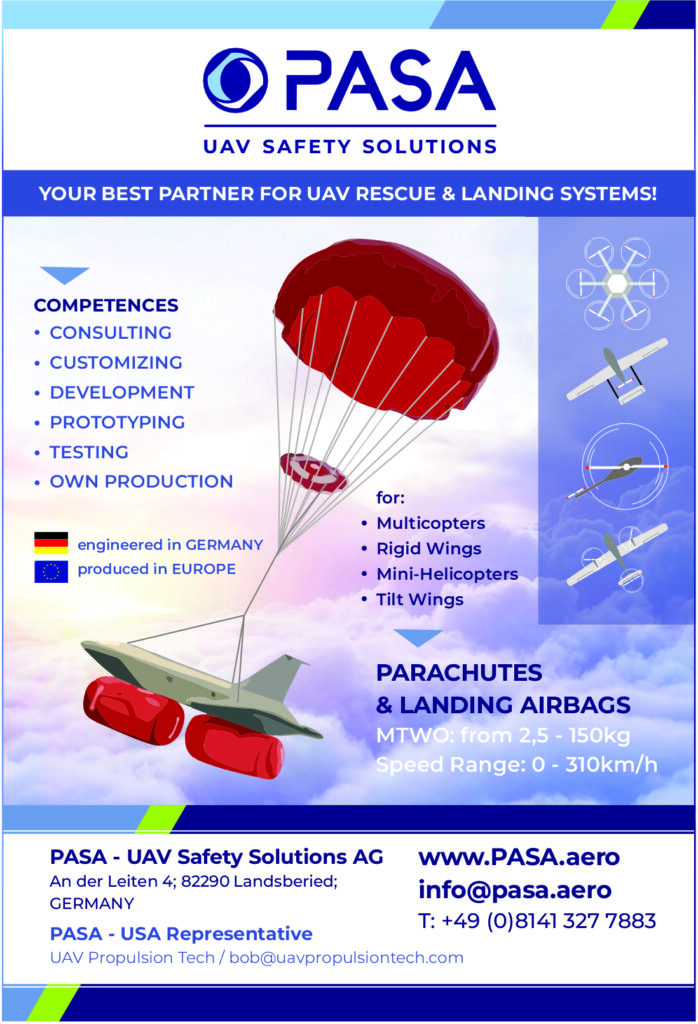
“Obviously, you can’t send nearly as much data over SBD as you can with Starlink, but all of that plus the backup tracker ensures you could have a power failure or the Iridium constellation could crash out of the sky, and end-users would still be able to see where the platform is and probably still be able to send it commands,” Rodriguez says.
Tomorrow is tomorrow
The exact landing point in Japan is undecided, although doing so can be decided ad hoc depending on weather conditions and discussions with local authorities and partners.
Once the journey is complete, Seasats will recover the USV and analyse it as standard for any necessary maintenance or repairs, as well as evaluating for any performance gains that the boat could be updated for (although only minor changes, such as adjustments for added biofouling resistance, would be expected at this point).
Afterwards, rather than undertake a new specific, non-customer journey, Seasats anticipates focusing on growing as a company, having raised a new round of funding in February.
“We are going to be hiring new people and expanding our team, potentially to launch new, larger classes of USV, and to continue expanding our manufacturing, with big gains to be had in cost optimisation, consistency and quality control,” Kramers says.
As Rodriguez continues: “Not every customer asks to have a USV delivered to them within two days, but there are those who want an international-sized survey done next month. That’s only going to be possible with boats on the shelf, and right now there’s four Lightfish on our shelf.
“Even though production has a slight edge right now, we’re aiming higher. Once the Pacific crossing is complete, and we’ve shown what we can do, I’m really excited at the thought of being able to send our USVs all over the planet – to have Lightfish gathering data from the Arctic to the Indian Ocean, across the Pacific and the Atlantic, as both main and support survey vessels.
“I don’t know what keeps Max and the others up at night, but that’s what does it for me.”
Key specifications
Weight: 132-192 kg
Top speed: 4.5 kts
Practical endurance: six months
Theoretical endurance: Infinite
Payload capacity: 27-50 kg
Payload voltage: 5-28 V
Payload peak power: 200 W
Max range without solar: 575 nm (estimated; actual figure may be higher)
Some key suppliers
Motors: Torqeedo
Satcom: Iridium Certus
Satcom: Starlink
Short burst comms: Iridium SBD
UPCOMING EVENTS
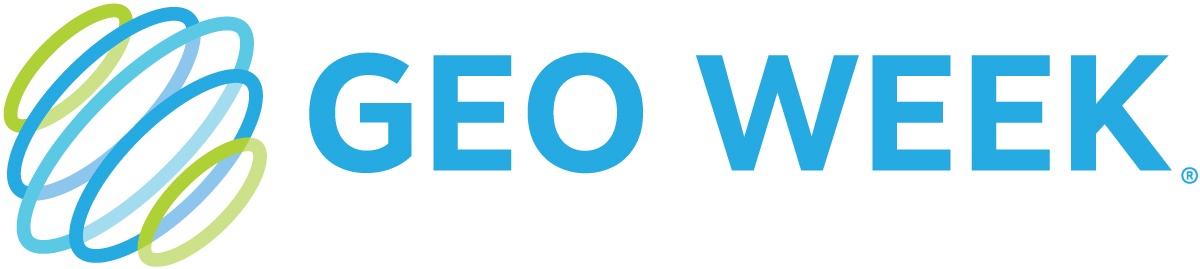
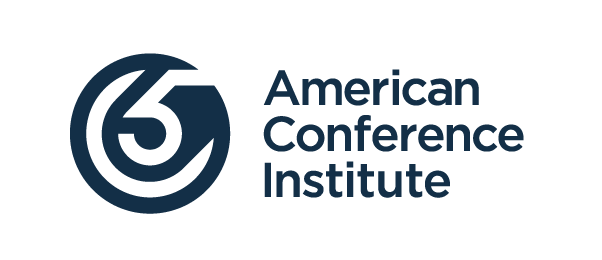
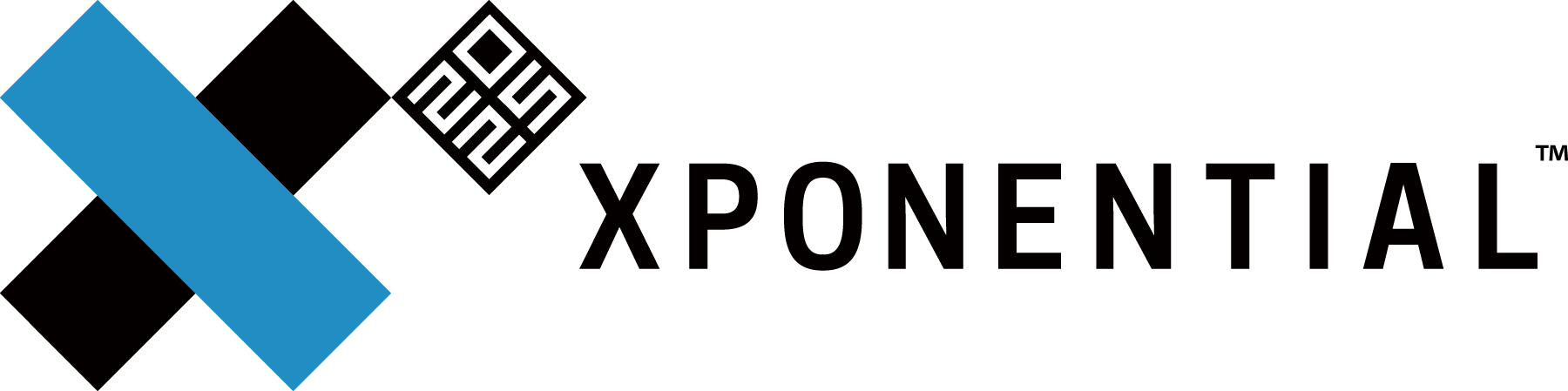
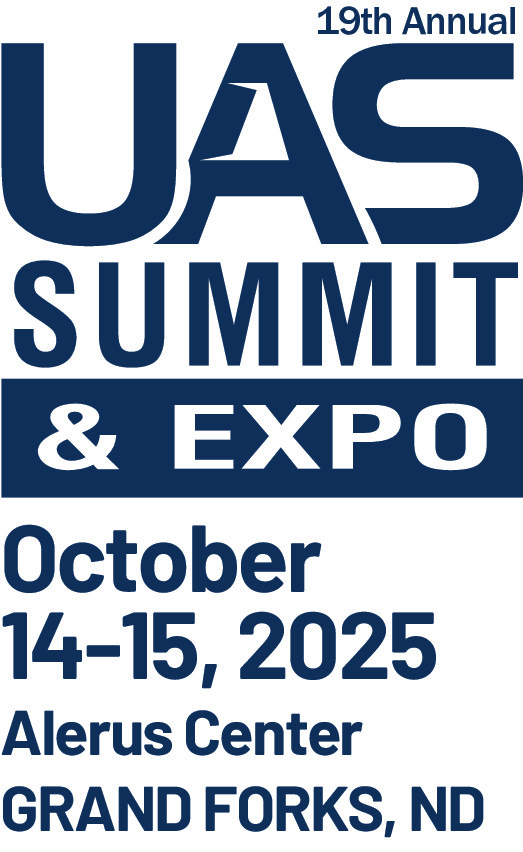
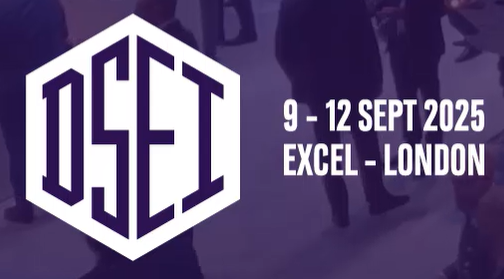
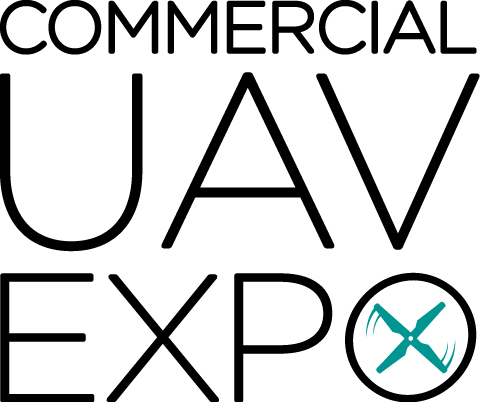
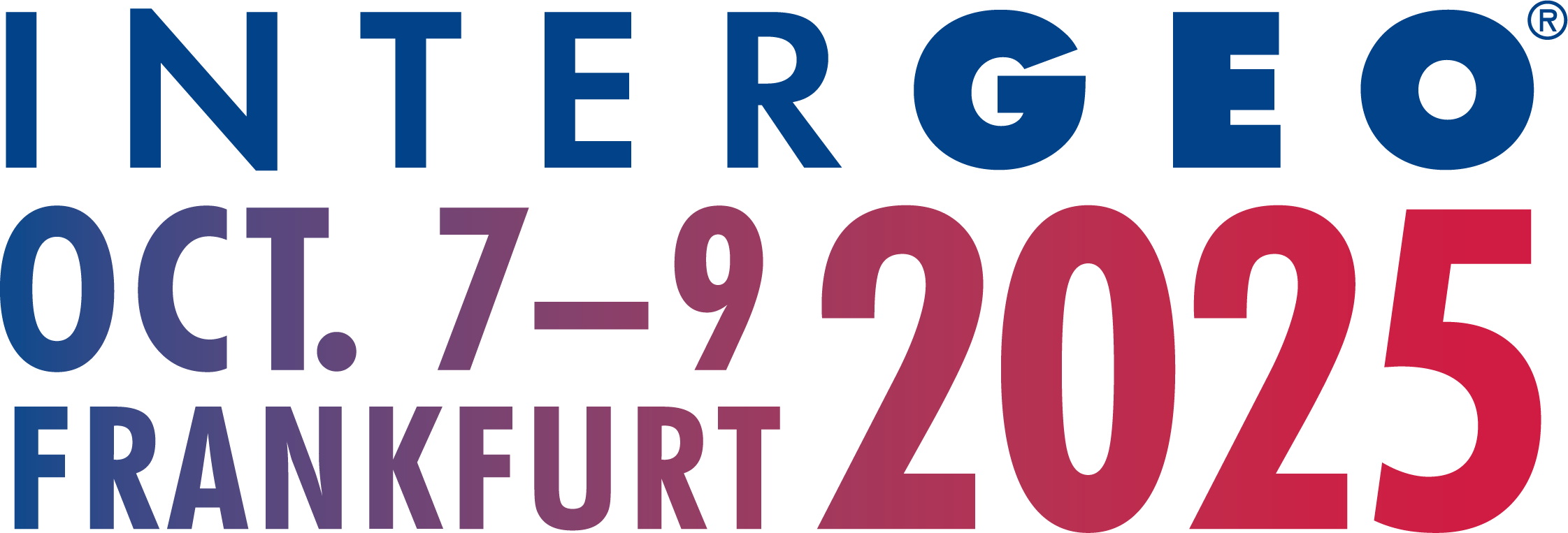
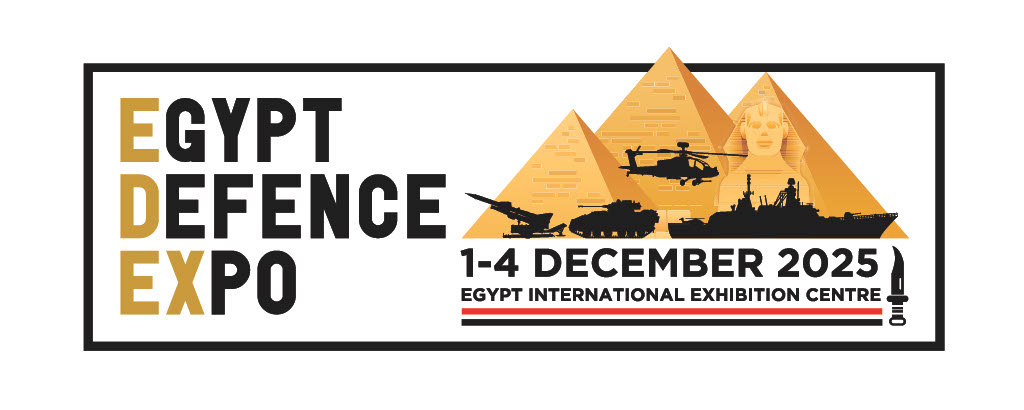
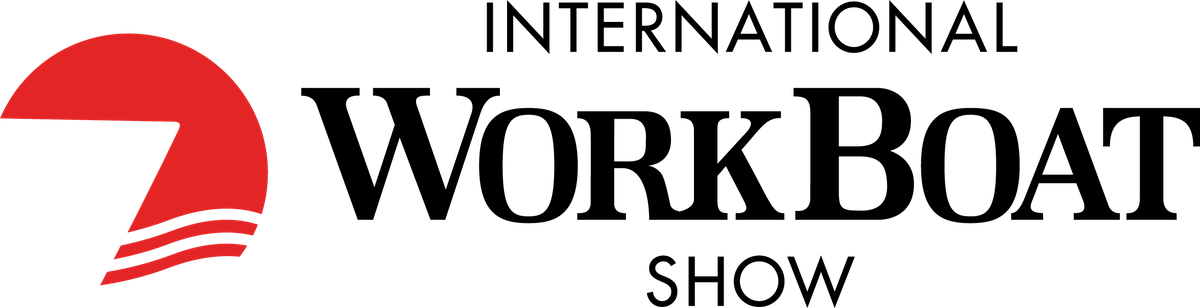
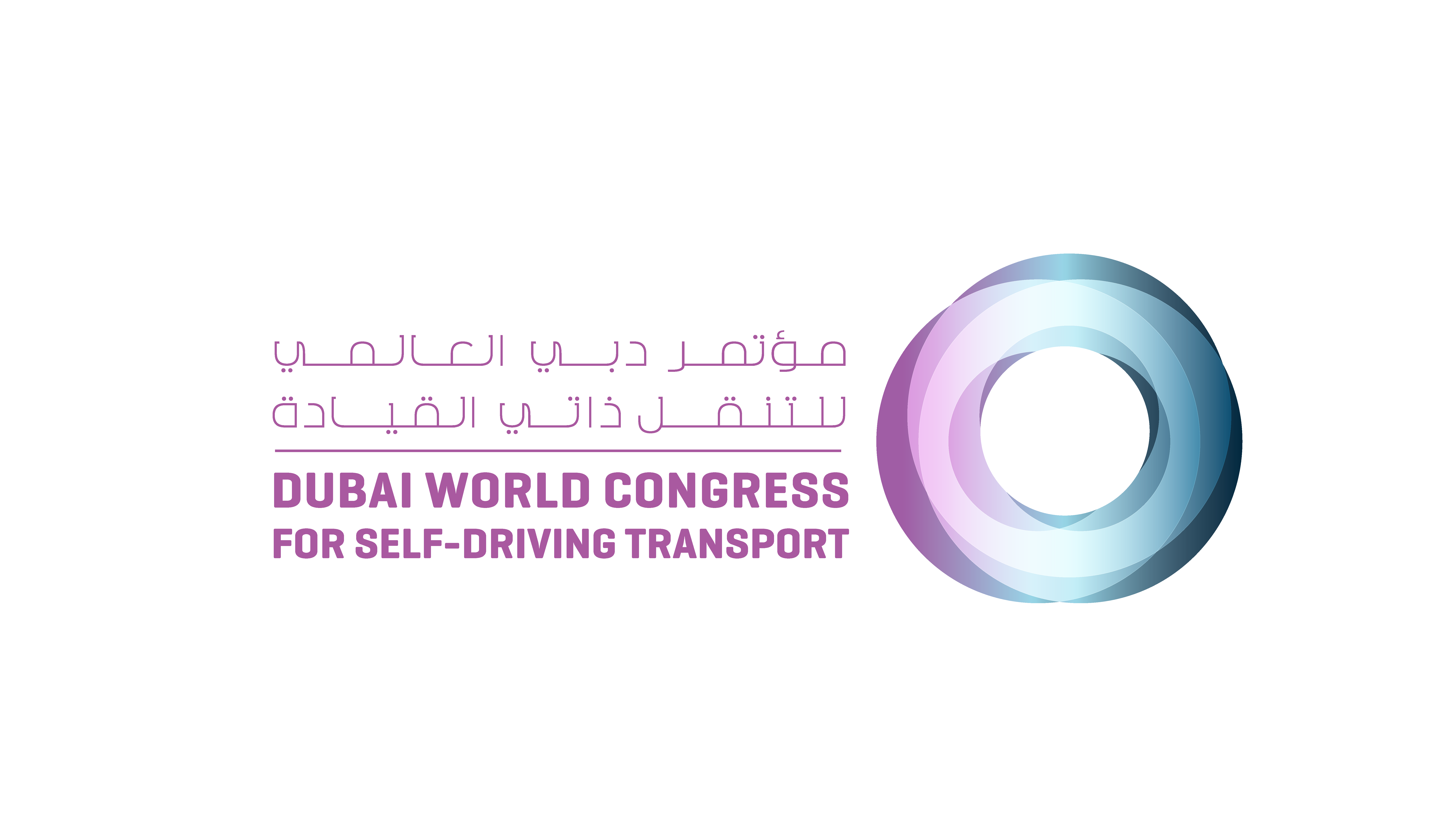
