Seaber YUCO
Missions in miniature
This micro-AUV has some advantages over traditional versions, as Rory Jackson found when tracing its development
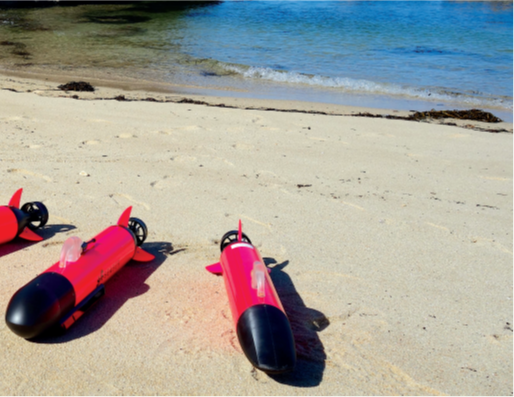
(Images courtesy of Seaber)
As reported before in this magazine, shallow waters prove something of a sticking point for the otherwise widening reach of uncrewed systems. Coastlines and lakes are typically under-surveyed compared with deeper seas and oceans, as they have trickier currents, greater collision risks, higher turbidity and less space for launching and recovering AUVs.
Also, the chances of biofouling and impacts from sudden, harsh waves make it impractical to use fixed buoys and so on in these environments, while crewed vessels pose an unacceptable carbon emissions risk to them. A new type of autonomous vehicle is therefore needed.
The market gap that these regions of water pose is steadily being addressed through the development of two new kinds of uncrewed vehicles. The first are amphibious ground vehicles such as the Copperstone Helix and Bayonet 350 (see UST 29, December 2019/January 2020 and UST 45, August/September 2022), the other is a miniaturised offshoot of the traditional autonomous UUV, increasingly referred to as a micro-AUV.
This new class of vessel is being defined by a number of successful commercial and scientific missions, many of which have been achieved by the YUCO, the signature offering from maritime robotics company Seaber. It is rated to a depth of 300 m, has a maximum endurance of 10 hours, and although its physical parameters change according to the range of payloads it can integrate, it is about 100 cm long, 12 cm wide and weighs 8 kg, with typical operating speeds of between 2.5 and 6 knots.
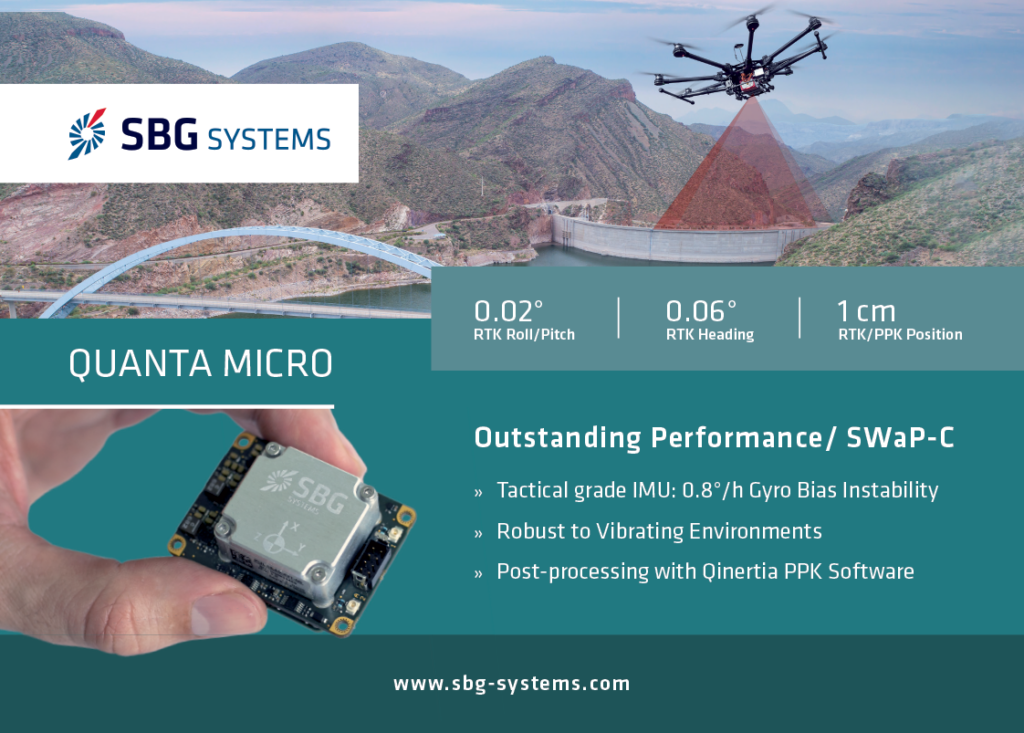
The formation of this team, based in Brittany, France, and its micro-AUV came about through the realisation of some fundamental issues affecting the traditional AUV market – and much broader ones than just the question of coastal and lake surveys.
“Our CEO and co-founder, Vidal Teixeira, had led various companies in the past, and across them he worked quite a bit with autonomous systems and in ocean physics and other waterrelated technologies,” explains Luc Simon, business development manager at Seaber.
“I worked with him back then, and there came a moment where he realised that offering an AUV of around or less than 50 kg was logistically a massive enabler for organisations with maritime interests.
“Around that time, normal AUVs were priced at e200,000-1,000,000; in fact, many still cost that much. And such vehicles weigh hundreds, sometimes thousands of kilos. When AUVs are that expensive and difficult to work with, you’re so paranoid about risk that, one, you’re awfully hesitant about acquiring an AUV, maybe taking years between initial enquiry and purchase; and two, you’re so cautious about deploying it that you can take years to get the value back from it in data terms.”
Teixeira surmised that a far lighter and less costly AUV (within a e30,000-50,000 budget) would reach a far wider range of users, and enable far more regular collection of data on a wide range of critical environmental and commercial assets.
It also envisioned a micro-AUV improving the average quality of marine data. Compared with ROVs and buoys, the ability of AUVs to move dynamically across all three axes of movement and rotation, and capture spatially rich data – while also moving at great range from their place of launch and intelligently navigating within metres of key points of interest – would make them far superior.
Teixeira therefore gathered as many seasoned engineers as possible from the world of maritime robotics, as well as a few from terrestrial robotics companies.
Development history
Seaber was founded in July 2020, and work progressed rapidly over the next 9 months, having started beforehand with the first blueprint drawings and going to the first prototype deployments in water before the year was over.
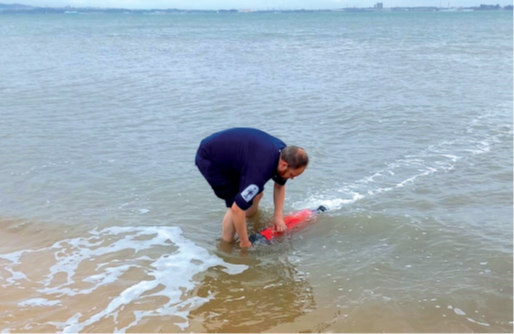
“What was key to our short development timescale was to avoid the trap of being an r&d company making on-request prototypes, but instead target a finished offthe- shelve solution,” Simon recounts.
“We were going to make a single product, encapsulating all our efforts to respond directly to what we saw as the lake and coastal market’s demands.
And if the market declined it, then we’d discard our work and start again from a blank sheet. One thing we weren’t going to do was pour billions of investor capital into something huge and heavy that could supposedly do everything for everyone but was impossible to deploy.”
To serve its target market, Seaber decided early in development on a maximum depth rating of 300 m, as well as sufficient thrust, speed and manoeuvrability (relative to the concept AUV’s size) to counter the strong currents it would face in shallow waters.
“We were – and are – targeting organisations who own only the sensors for marine surveys, and were not using AUVs for the reasons I’ve described. They were too costly, too complex and required too much dedicated training, bureaucracy and infrastructure,” Simon explains.
“We offer the YUCO as a means of enhancing the range, duration and autonomy with which they can deploy their sensors, and indeed we’ve found all our customers are those who are using AUVs for the first time.”
Ease of use was therefore another critical key aspect of Seaber’s engineering strategy: end-users can be fully trained in using a YUCO over a 4 hour videoconferencing session. This is illustrated not only in the low part count involved in the maintenance and disassembly of the YUCO but also in its ancillary systems such as the company’s SeaPlan GCS software and SeaComm recovery tool.
“We especially wanted one approximate vehicle design and profile, no matter what the payload. We therefore don’t put the payload in the dry section but in the wet section, and it’s always based on really small sensors, as that’s the way the market is going,” Simon comments.
“Five years ago, it would have been really complex to launch this product, because the sensors and electronics
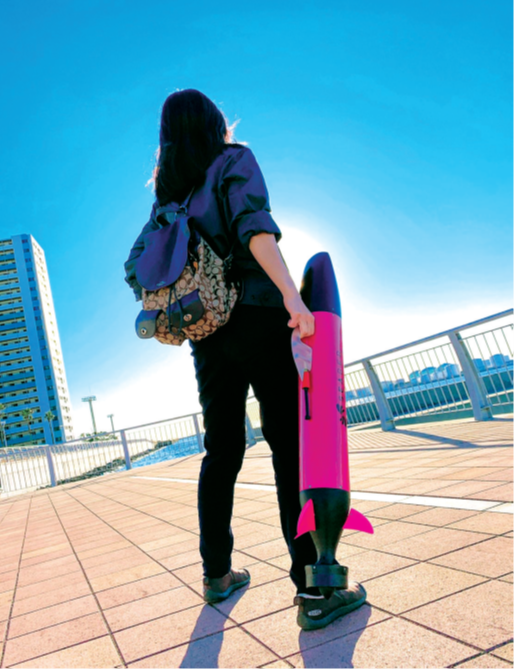
would have been too big and too powerhungry, and would have had to be kept dry at all costs.”
In the 6 months following the first deployments, Seaber conducted exhaustive water tests before taking on trial projects in partnership with various companies, not just to showcase what its technology could do but also to gather r&d data on how the early YUCO performed in different waters and missions.
“The Jerico European Research Program in Ireland with the Marine Institute there was our first real validation of what was by that time – autumn 2021 – the complete, off-the-shelf YUCO.
The test consisted first of several short deployments and then a longer mission stretching multiple lengths of Galway Bay,” Simon recounts.
“The latter was a 15 km mission, with occasional surfacing halfway along the bay. The institute’s operators literally went for a coffee while the AUV was working, then went to the pre-planned recovery point 300 m away.
“The YUCO was right on time; they retrieved it, extracted three-and-a-half hours of data, and that was it. On its first try, our finished product had proven that it could be programmed and deployed entirely by oceanographers who had mostly never used an AUV before, and be trusted to gather detailed data fully autonomously, so that its operators could do something other than slaving away in the water.”
Anatomy of the YUCO
All the standard-issue parts of the YUCO are housed in the rear section, known informally as the ‘never-open section’, which occupies about two-thirds of the vessel’s total length.
Simon explains, “We know that when something is going to be submerged, we want as far as possible to prevent any chance of interactions with the internal electronics, O-rings or anything like that, because it’s just going to create the risks of water ingress into the hull. We wanted the routine with this AUV to be: you pick it up with its embedded payload, deploy it, retrieve it, clean it and store it again.”
The top of the never-open section has a translucent mast containing the YUCO’s antennas for wi-fi and GPS, as well as an array of LEDs for visibility, and a connector for charging the battery and inserting a ‘key’ tool for switching the AUV on and off.
This section’s hull is water-tested and sealed to give the 300 m depth rating; materials and the design are optimised for hydrodynamics and mechanical rigidity. In addition to the battery, the inside holds all the main control electronics, receivers for wi-fi and GPS, and the AHRS for navigation (including Seaber’s navigation algorithms). About the hull are a single rear thruster and three fins displaced at 120º to each other, which enable the YUCO to dive, ascend, spiral and turn.
On the front of the rear sections are four protrusions. One is a pressure sensor that measures the YUCO’s distance from the surface, another is a data comms connector for the payload section.
“It’s important to us that the payload isn’t just powered by the AUV but synchronised to its navigation measurements, and that everything it measures can be read and analysed by the SeaPlan software, as well as being recovered via the interface it provides,” Simon comments. “Working with a separate dedicated storage for the data that has to be re-synchronised after downloading is really painstaking.”
Also inside the dry section is a system for maintaining the centre of balance when the payload is changed. Seaber is considering patenting that so cannot disclose it publicly for now.
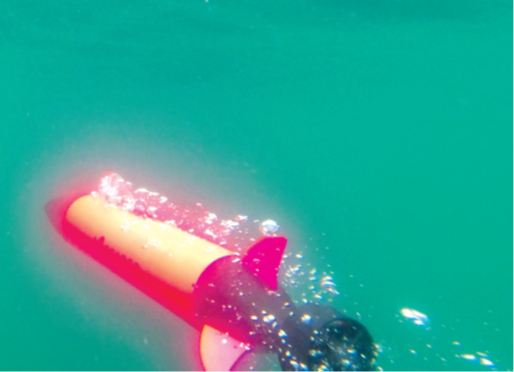
“And if necessary, for instance if a customer has made a custom payload of their own, there are mounting points on the front for them to add counterweights, so even then the enduser’s modification work can be kept external to the dry section to keep them from opening the never-open section,” Simon adds.
In contrast to the rear, which is identical on every YUCO, the front sections take many different shapes, up to 50 cm in length, depending on the sensor being installed. The back part of this front section is commonly the ‘main’ cylinder that has numerous inlets and contains the DVL and payload, while the very front is a nose that can be open or closed (depending on the need for water-sampling flows). It can be empty or contain a secondary sensor such as a GoPro camera.
“The front is very variable, but as long as the nose is neutrally buoyant it can be of different shapes. It is fairly long too, but the AUV remains quite manoeuvrable.
That is how we’ve been able to use different things such as CTD sensors, multi-parameter sondes, sidescan sonars, and underwater cameras and LEDs.”
Hull production
Different IP ratings are given for the various components in the YUCO, for splash-proofing, water ingress, pressure resistance and others.
To validate internally that the hull is capable of the depths Seaber has set as a hard target, the company has its own pressure test bench, which it uses to check that the YUCO can survive the pressure at up to 450 m depths over its lifetime (to guarantee a margin of safety for continuous operations at 300 m).
The YUCO hull’s main elements are carbon composite and high-density plastics. The design engineers have
avoided exposing any electronic couplings between the different materials, to prevent rusting or biofouling from algae or barnacles, but aside from that, few anti-biofouling measures have been taken, given the low risk of it when using carbon or plastics.
“We work with local suppliers for most of the hull,” Simon comments. “We designed everything in-house and then advised on the appropriate thicknesses of materials, with most of our design work being carried out using SolidWorks.”
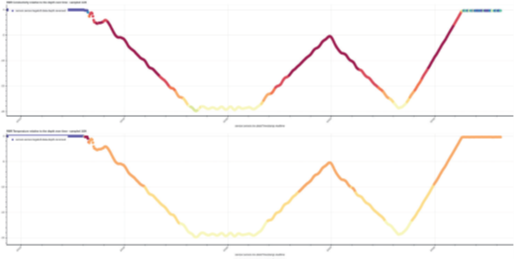
No YUCO is ever in the water for more than a day (with one or two breaks as well during each day, given the endurance limits), so there is insufficient exposure to the water for biofouling to accumulate.
To prevent degradation of its appearance from the action of seawater or ultraviolet radiation, some minimal coating is used for protecting the paint, and the screws for securing the hull parts are titanium and stainless steel.
“As far as in-house manufacture goes, we’re now able to make up to four units a week, although we’ll ramp that up in the future,” says Simon. “We plan to keep production not just within France but local to Brittany, to stay true to our low-carbon philosophy.
“The shape of the mast has also been iterated to improve the YUCO’s hydrodynamics and aerodynamics as it moves through the water or at the surface. It also serves as a handle for carrying and protecting the connector to start and charge the YUCO.”
In addition to hydrodynamics, each fin has been designed with rupture points about halfway up their heights and running lengthways, so that if there is a strong shock against any of them, the top of the fin will break off. That dissipates the impact’s energy and prevents the shock running through to the hull, which could spring a leak that would threaten the internal electronics.
Navigation
At present, all the main applications targeted by Seaber do not require USBL acoustic aiding, and as LBL requires external elements such as buoys or seafloor pylons, this latter approach has been avoided.
The sole acoustic navigation system on board is an A50 DVL from Water Linked. In addition to sensing the YUCO’s distance and speed over the seafloor, it was chosen for being, as Simon states, “The smallest and most cost-effective on the market.” Each unit measures 66 mm in diameter and is 25 mm tall, consuming 3 W to measure velocity accurate to 0.1 mm/s and altitudes of up to 50 m above the seabed.
“As well as obviously improving navigational accuracy, the DVL helps us to compensate for currents and in autonomously avoiding obstacles such as boulders on the seafloor. You can program altitudes and inclines that you want the YUCO to avoid, to help it avoid bumping against things coming up from below.”
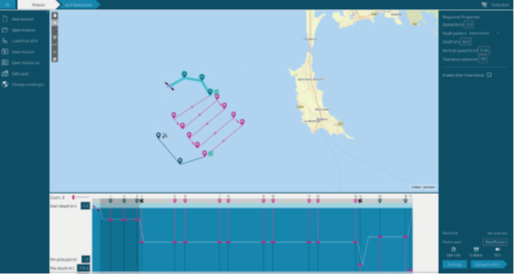
The company has also avoided installing FOGs, as they could triple the YUCO’s unit price. Instead, an AHRS using an industrial-grade IMU has been developed, following experiments aimed at benchmarking the performance of every MEMS accelerometer, gyroscope and magnetometer the company could acquire (as well as every combination of the sensors it could make).
The AHRS and DVL, along with a pressure sensor for depth and GNSS updates for surface positions, are integrated as Seaber’s INX (Intuitive Navigation eXperience). Proprietary algorithms for sensor fusion and processing of data for refined accuracy have also been developed.
“We take just the raw data from each sensor and run it through our own maritime algorithms, because generally most INSs use algorithms aimed at surface or above-surface vehicles,” Simon explains. “Standard-issue Kalman filters and other algorithms are therefore not optimised for an AUV going underwater for many minutes at a time.”
“We record and store all the navigation data at a rate of 20 Hz and make it available to the customer in case they really want to go into thin levels of detail on what their YUCO has been up to underwater. And any update to the navigation software or middleware can be uploaded over wi-fi; we don’t want users to have to recover, let alone open, their YUCO to update it.”
Power
The thruster is an electric motor system based closely on the reference design behind Blue Robotics’ T200, Seaber having selected it for its reputation as a low maintenance system and being easily disassembled and cleaned. The system has a maximum power output of about 600 W, running on 7-20 V with 76 mm-diameter prop blades, and steering is handled by three servo motors operating the fins.
“We also provide spare propellers and replacement fins for maintaining the powertrain, but to date we’ve not seen any fins broken by the work our clients do,” Simon notes.
Energy of 600 Wh is stored in an IATAcertified lithium-ion battery, although an NiMH battery with 200 Wh is also available for customers to transport the YUCO by air more easily. As indicated, the pack sits on a plate that is actuated forwards or back on a rail to keep the centre of buoyancy in the middle of the vessel.
“We’ve prepared the electronics to run on any bus, with various voltages and comms protocols depending on what customers want and how the electronics are optimised in the future,” Simon adds.
Payloads
Five versions of the YUCO were available at the time of writing. The YUCO-Physico was previously discussed in UST 42 (February/March 2022) in relation to its nose cone integrating AML Oceanographic’s AML-3 sonde for water quality measurements.
Its name signifies that up to three sensors can be inserted at once, for gauging parameters such as sound velocity, conductivity and turbidity. At 123 cm long, it is the lengthiest YUCO so far.
Meanwhile, the 112 cm YUCO-CTD uses RBR Global’s RBRlegato sensor for detailed conductivity, salinity and temperature measurements.
The other three models are all 98 cm long. For bathymetric surveys and mapping, the YUCO-Scan integrates the 680 kHz sidescan sonar from DeepVision, the engineering of Seaber’s INX being vital for accurate geo referencing and hence stitching of acoustic imagery taken from this payload.
The YUCO-PAM (passive acoustic monitoring) uses the Porpoise recorder from RsAqua, with sampling rates of up to 384 kHz and up to 4 Tbytes of storage for detecting human-made noises such as ships or pile driving, or those from marine mammals including seals and dolphins.
Lastly, the YUCO-Carrier is offered as an open variant of the YUCO, for users to embed their own sensors or sondes in the wet payload cone. It can be customised to up to 45 cm with variable geometries on request.
“As long as you equilibrate properly and make a dedicated nose cone, you can implement as many different payloads as required,” Simon explains. “And as the payload sections have similar power and comms modes they can be swapped without issue.”
SeaPlan intelligence
Pre-deployment programming and recovery of mission data are performed on the YUCO via wi-fi on the SeaPlan GCS mission planner. The GCS also connects persistently to the YUCO via wi-fi.
The YUCO’s computer architecture consists of a main central board, with distributed lower-level boards allocated to different subsystems, including dedicated microprocessors for the INX, the payload and some other parts.
This robustness of processing and data handling enables some key capabilities for the end-user. As the YUCO executes programmed waypoints, the operator receives visualisations of not just the AUV’s longitudinal and latitudinal position but also its depth along the programmed route, which is shown in a separate display (consisting of just the y and z axes) below the GCS area map.
That allows the user to set geo-fences for the YUCO in terms of depth below waves and altitude over the seabed, with minima and maxima configurable for both. Also, templates for navigational patterns such as spiralled loitering, 3D zigzagging or floating at the surface for gathering data can be dragged and dropped onto or between different waypoints.
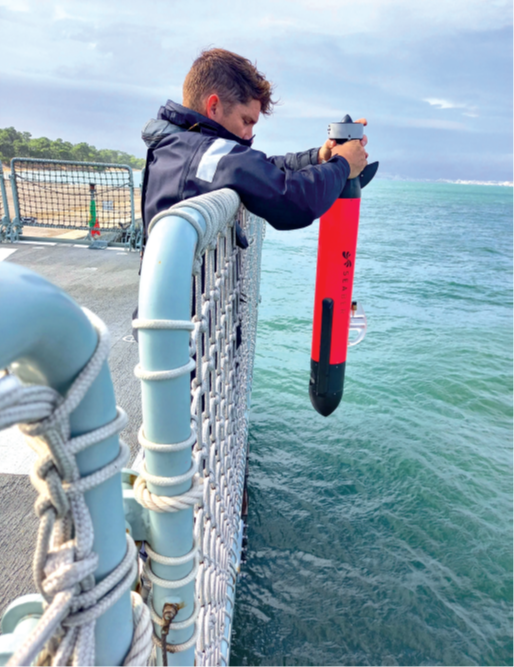
“It’s also a single drag-and-drop button to tell the YUCO to surface for a GNSS reading, or to keep its sidescan sonar on for a given length of travel,” Simon comments. “You can also copy and paste any set of waypoints for easily repeated survey patterns. That means end-users pretty much never need more than one session to become proficient in using the vessel.”
The operator can also adapt its end-ofmission behaviour according to which type of vessels or area it is to be called back to. These adaptations include selecting whether the YUCO is to be recovered from a small vessel, a big vessel or even from the shore, setting the most appropriate return and waiting behaviours to minimise the risk of a collision.
For example, if recovery is set to “No nautical means”, meaning a manual beach or shallows recovery is to be performed, it will simply navigate along the water’s surface to the assigned GNSS point without its usual avoidance of the seabed.
“And because it’s a small AUV, launching is easy. You can just drop it off the side of a big vessel, and then our handheld SeaComm unit can remotely trigger the mission to begin or to make an emergency return, over the YUCO’s radio antenna from up to 4 km away,” Simon adds.
Radio antennas are installed to ensure external comms needs, with the GNSS antenna under the centre dorsal fin.
Internal comms between the payload and dry sections can be configured for Ethernet, UART, or RS-232. An external satcom module can also be installed for open ocean applications.
Future plans
With the YUCO now matured and in production, Seaber is preparing to continue making new modular variations and technological capabilities available.
“One area we are working on are acoustic capabilities in terms of position aiding and underwater communication,” says Simon. “That will open up a wide range of new uses and application scenarios for the YUCO, such as anything needing launch or recovery from mobile platforms on or offshore.
“We have also received widespread interest in the integration of many new sensor types, and on that front an announcement will be made towards the end of this year.”
Specifications
Micro-AUV
Depth rating: 300 m
Weight: 8 kg
Length: 98-123 cm
Diameter: 12 cm
Speed: 2.5 to 6 knots maximum
Endurance: 6 to 10 hours
Some key suppliers
DVL: Water Linked
Payloads: RBR
Payloads: DeepVision
Payloads: AML Oceanographic
Payloads: RsAqua
Thruster: Blue Robotics
UPCOMING EVENTS
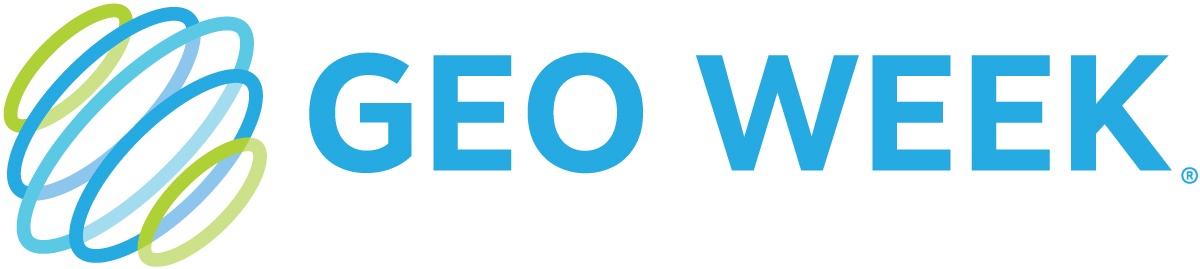
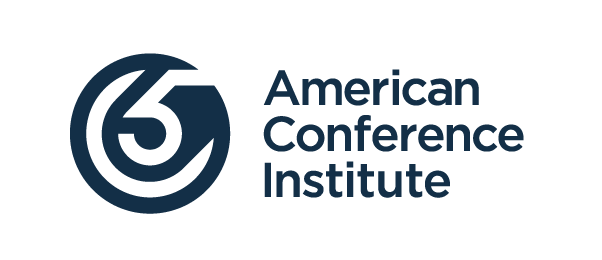
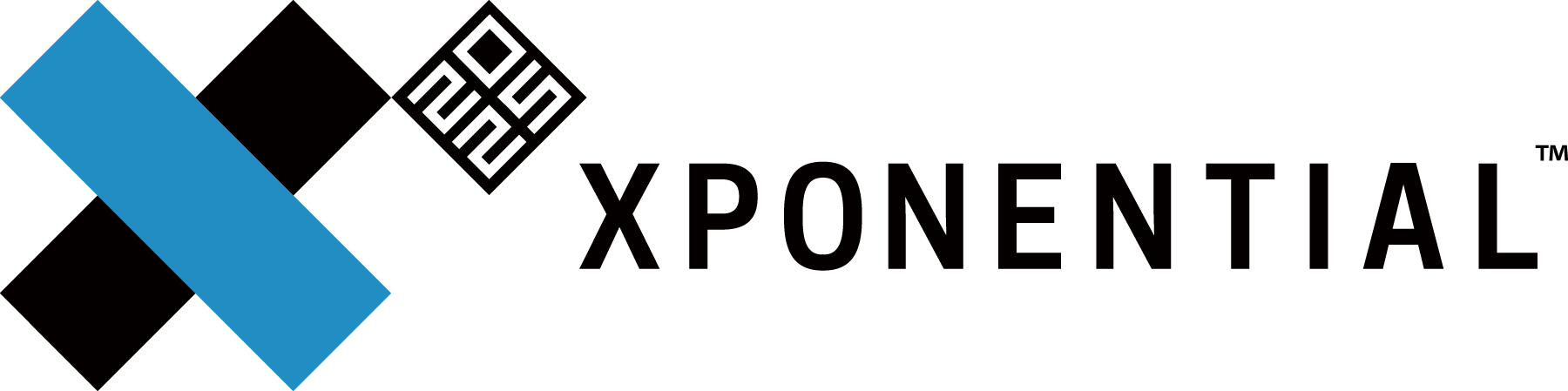
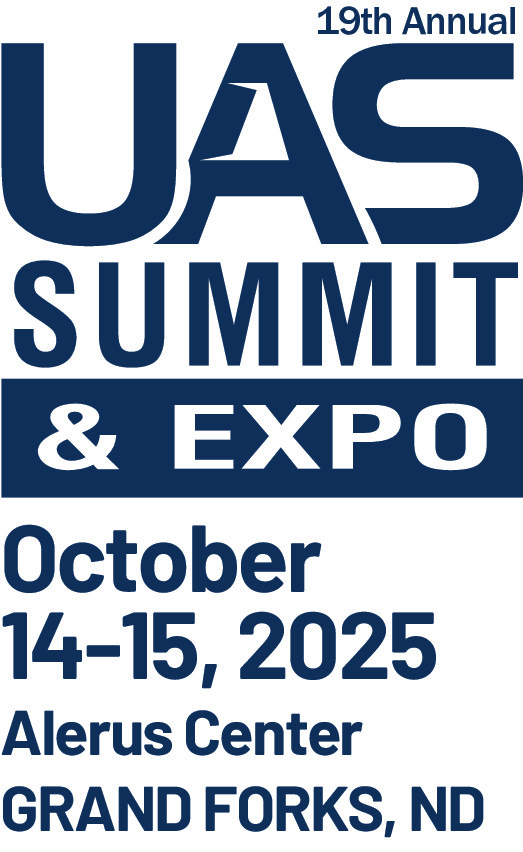
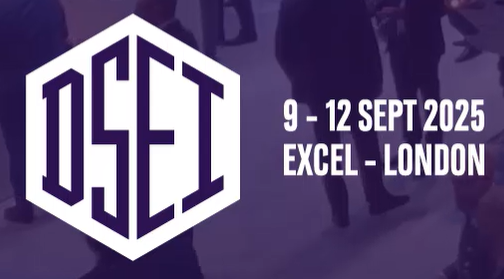
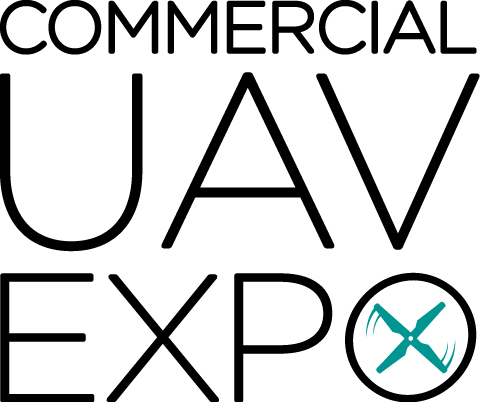
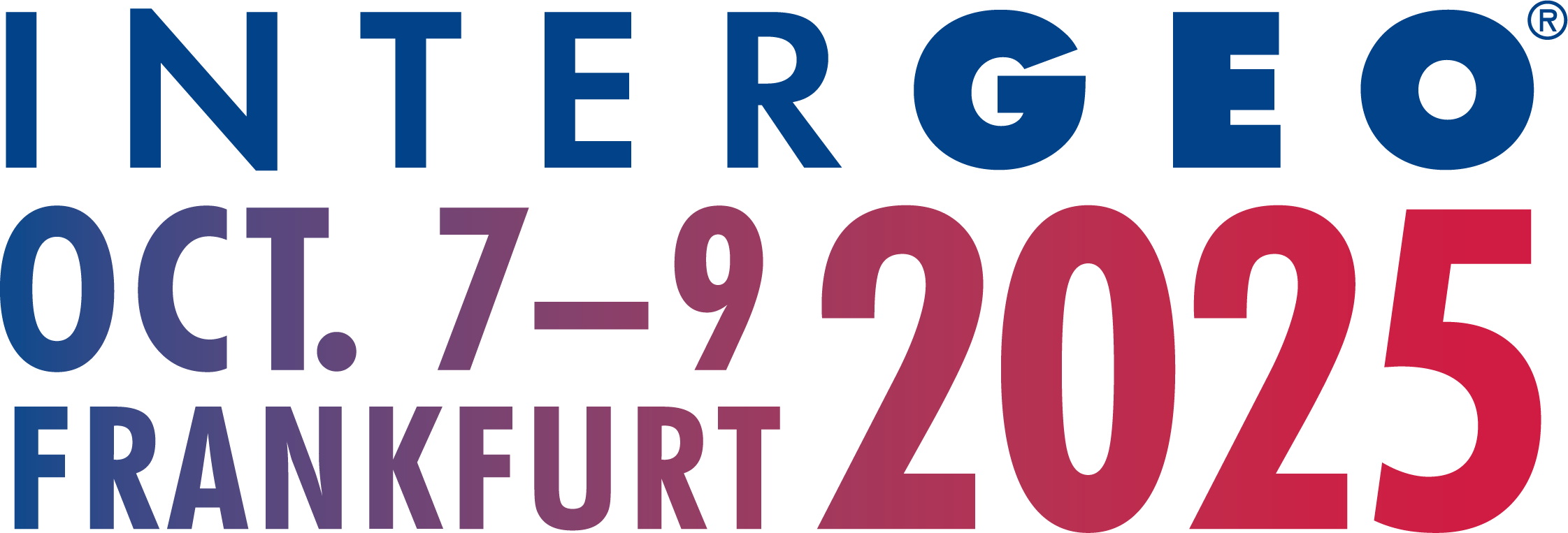
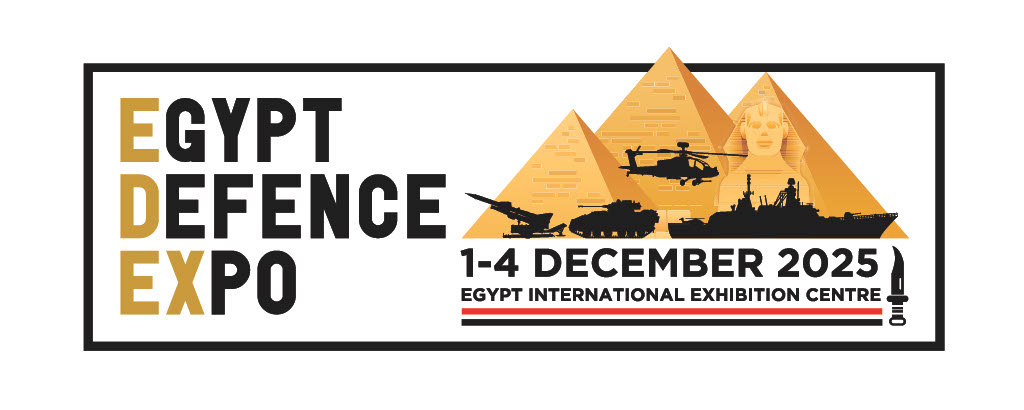
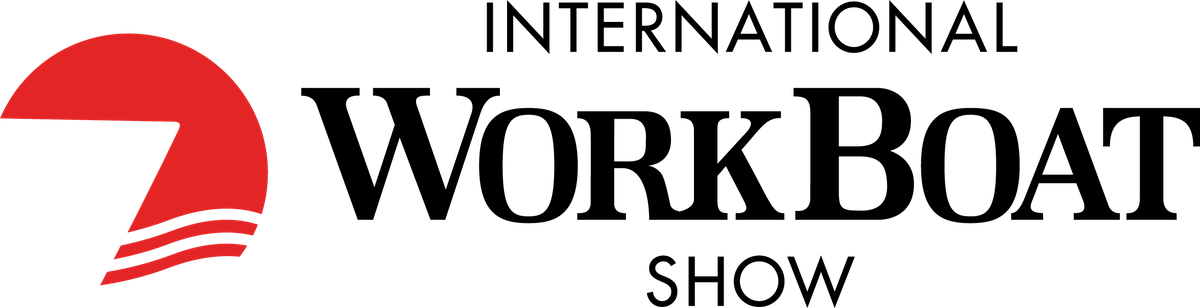
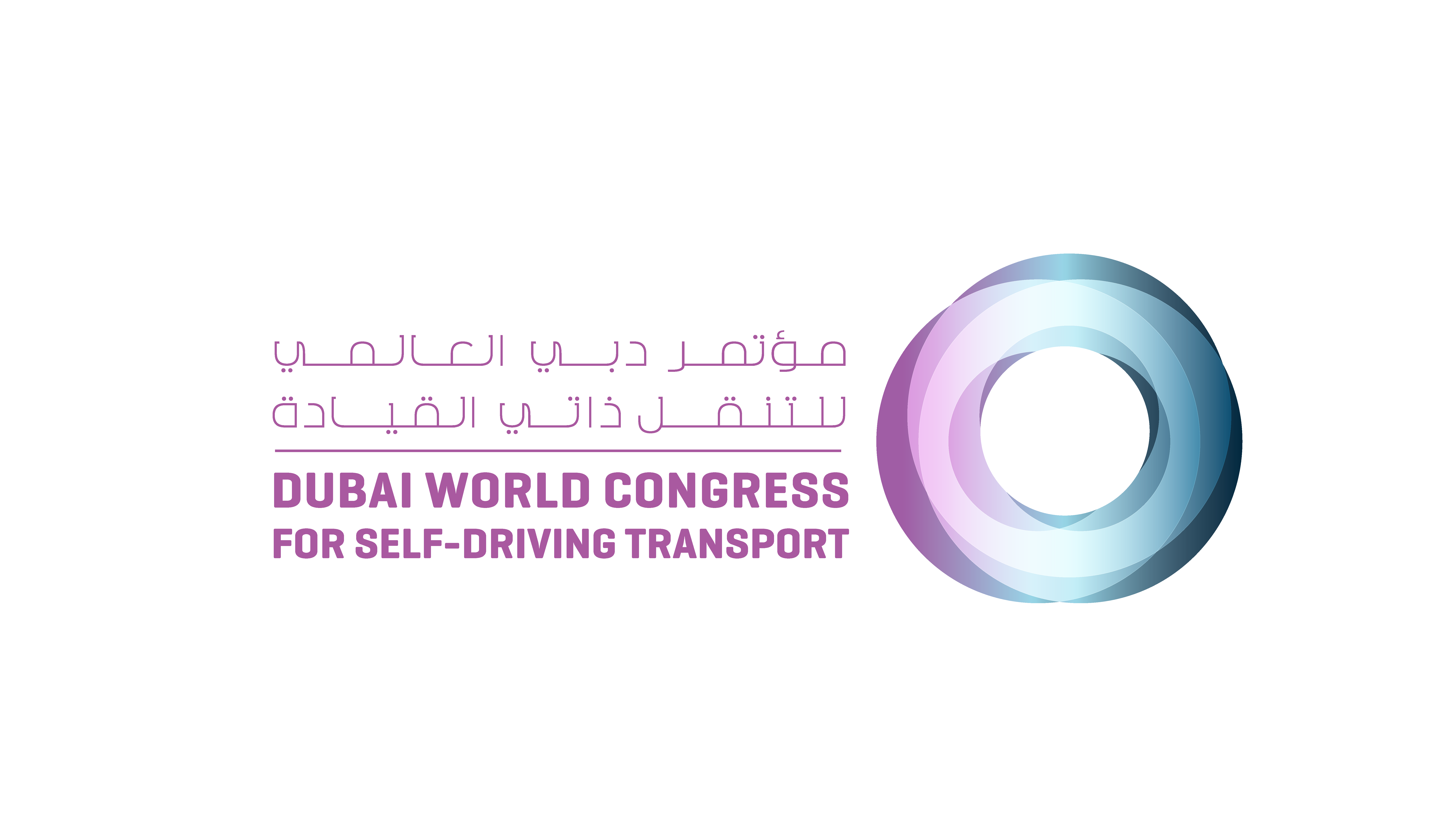
