Solar power
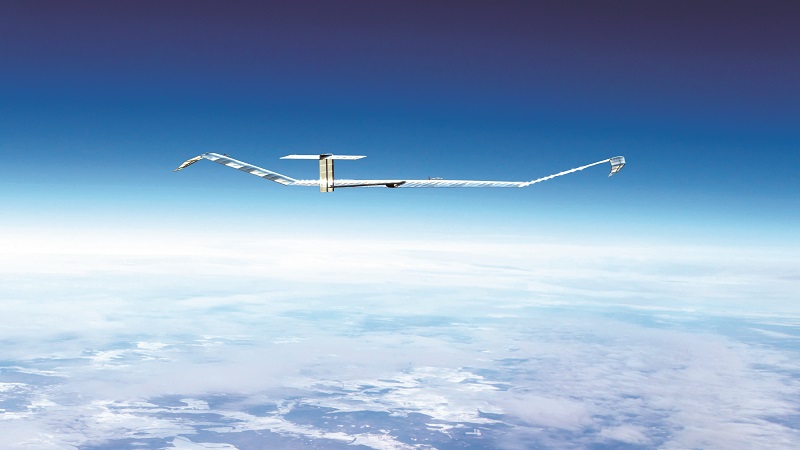
Travelling light
Saving weight in uncrewed systems is only one benefit of solar power, writes Rory Jackson, who reports on advances in the technology
Many UAVs and USVs now come fitted with solar panels covering much of their surfaces. The interest in solar energy comes from more than it being a potentially limitless source of green power; for uncrewed systems it extends autonomy in a practical sense.
For many electric UAVs for instance, the bulk of hands-on maintenance has been reduced to swapping a fresh battery into the chassis (repairs and overhauls notwithstanding). But if a UAV can land in a field and sit while being recharged by sunlight then maintenance technicians don’t need to lift a finger. Much like satellites or the uncrewed systems on Mars, the vehicles can take care of themselves thanks to their solar panels.
The most prominent examples of autonomous systems using solar cells include high-altitude, long-endurance (HALE) pseudosatellite platforms. The Airbus Zephyr and BAE Systems’ PHASA-35 projects are perhaps the most widely known of these, the former having set a new world record for autonomous flight endurance last summer thanks to its specific selection and integration of solar cells. Several more HALE UAVs are now also being developed by other companies.
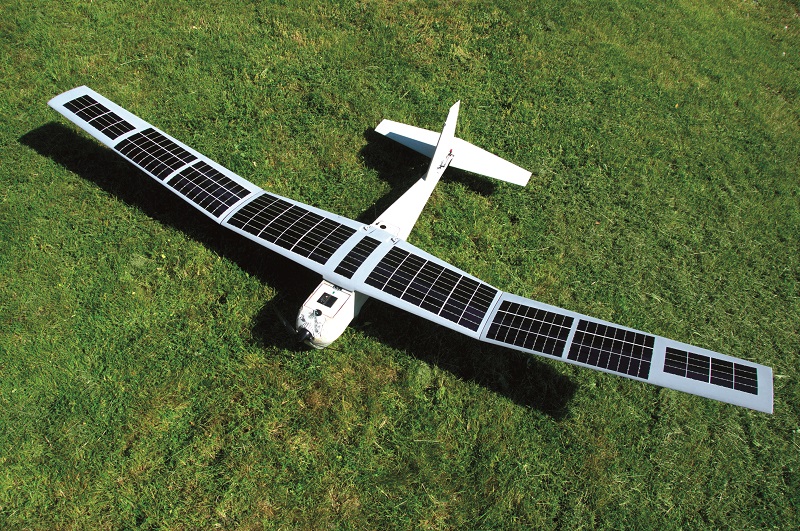
(Courtesy of Microlink Devices)
These aircraft are intended to fly in the stratosphere for around a year at a time, where light interference will be minimised during the day, and lift is maximised by using a very large, high aspect-ratio wing to provide plenty of area for photovoltaic (PV) cells to be integrated as a less weighty source of power than batteries. Trying to supply them with energy from batteries alone for 365 days would soon render them unfeasibly heavy.
Similarly, long-endurance USVs from companies such as Saildrone, Mayflower and AutoNaut (see UST 38, June/July 2021; UST 42, February/March 2022; and UST 12, February/March 2017 respectively) are packed with solar panels for replenishing their batteries while sitting relatively stationary in mid-ocean.
While weight reduction is less mission-critical for sea vessels, the space saved in their hulls by exchanging battery volume for thin solar panels enables more electronics hardware for research, mapping and comms relay missions, enhancing the usefulness of these vehicles and the return on investment from their voyages.
Beyond these, however, there is a wide and growing array of short to medium endurance electric uncrewed systems that are at least partially solar-powered. This has come from PV technology advancing and maturing to the point that it is not only accessible to smaller companies from a cost perspective, but also worthwhile for enhancing performance, with the most important performance parameters varying according to the use case.
Multi-junction cells
Power density (wattage relative to volume) and specific power (wattage relative to mass) remain the most critical factors for high-end, long-endurance users considering installing solar cells on their uncrewed systems.
Both specifications tie in with solar conversion efficiency – that is, the amount of sunlight transmitted into the cell and turned into current, rather than being reflected or lost as heat. While there are multiple layers in a solar panel, including outer layers of highly transparent glasses, encapsulant polymers and metallic back sheets – and the adhesives used in between – at the centre of all of them is the PV semiconductor cell, which carries most of the specifications that will define an end-user’s decision on whether to mount solar cells.
The materials at the top end provide the highest commercially available solar conversion efficiency. Continuing to lead the way are multi-junction materials, which incorporate different semiconductors that are individually optimised for conversion efficiency at different wavelengths of solar energy.
The most prominent productionised example for UAVs remains a triple-junction cell combining indium gallium phosphide (InGaP) with gallium arsenide (GaAs) and indium gallium arsenide (InGaAs). Collectively these materials provide more than 90% external quantum efficiency (the ratio of the number of charge carriers collected by the solar cell to the number of photons of a given energy shining on the solar cell from outside) over wavelengths of 450-1200 nm, and a typical power conversion efficiency of 28.5% in AM0 (zero atmosphere) and 30% in AM1.5 (terrestrial atmosphere).
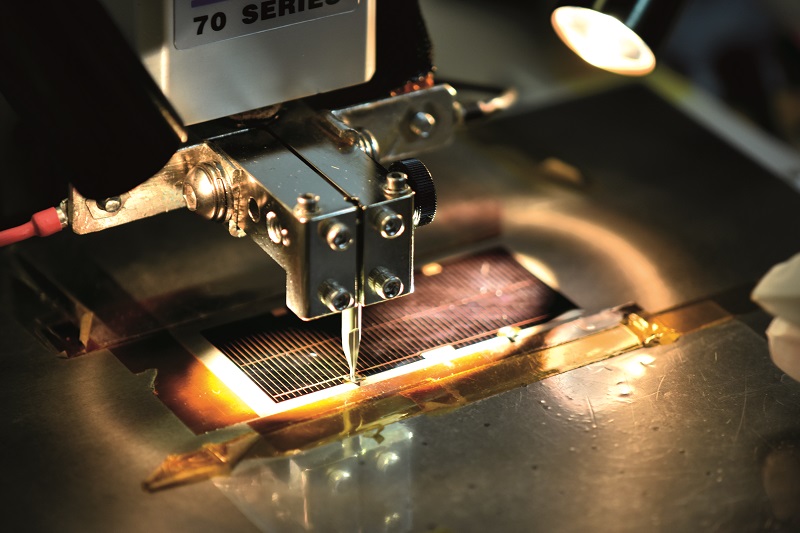
(Courtesy of Microlink Devices)
This solution also comes with a mass density of 250 g/㎡, a power density of 390 W/㎡ and a specific power of 2200 W/kg in AM0, and is highly encapsulated for ruggedisation against UV light, ozone and very low temperatures. Other multi-junction cells are of course available, particularly among those used by spacecraft, but they are often many times heavier.
Multi-junction panels are however among the most expensive, given that adding more semiconductors to a panel increases development and manufacturing costs, but interest in them nonetheless extends beyond their use in the stratosphere. For instance, some military users are expressing interest in integrating multi-junction solar onto their low-altitude small UAVs for a more persistent power supply and range extension during border patrols and similar work.
Elsewhere, the imminent boom in small satellites for applications such as telecoms, navigation and mapping will drive demand for highly efficient solar panels to power their dense electronics. Of course, these will mean changing their protection systems, doping systems and material thicknesses to account for issues such as outgassing or high levels of radiation in outer space.
But as their extensive hardware will come with a minimum power requirement, the ability to install more solar power for less weight will reduce the cost of launching them into orbit, which remains the major expense for this new space industry.
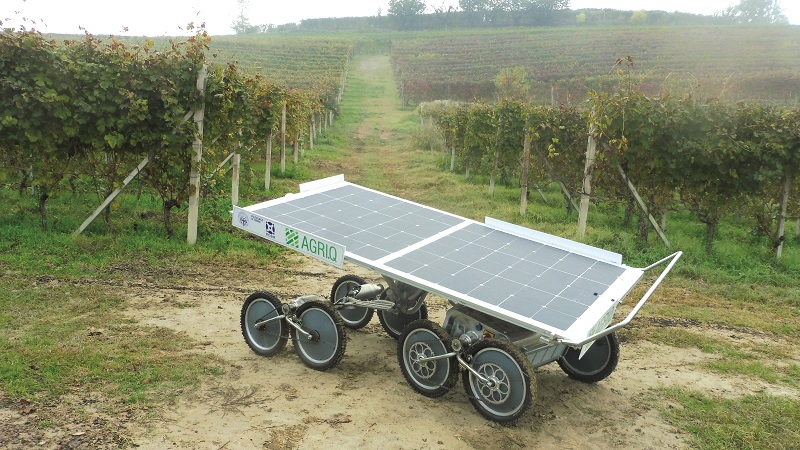
(Courtesy of Solbian)
Single and dual junction
At the present absolute limit, the world record for solar conversion efficiency is 47.1%, which was set in 2019 by scientists using a six-junction cell at the National Renewable Energy Laboratory, in Golden, Colorado.
However, given that the number of junctions directly increases the cost of solar cells, innovations in dual and single-junction cells have been key to widening accessibility to solar power across the uncrewed market.
Crystalline silicon PV cells generally remain the most affordable option, by virtue of being easy to work with and mass production by several suppliers. They range in solar conversion efficiency from sub-10% in commercial products to 25-27% in laboratories, and remain popular among USV manufacturers for their greater moisture resistance than some more expensive materials based on GaAs or CdTe (cadmium tellurium). The more sensitive a cell is to moisture, the thicker and heavier its encapsulation has to be, countering any weight advantages.
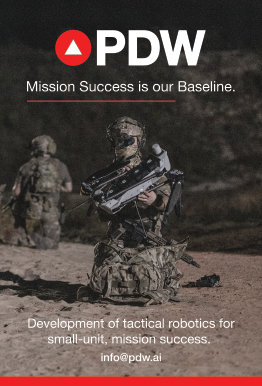
Also, perovskites (a range of calcium titanium oxide minerals) are on the cusp of being used in some commercial pilot solar product runs, partly as they are the solar cell technology that is advancing the fastest. While single-junction perovskite cells exhibited only 3-4% efficiencies in 2009, now they are capable of around 26% in laboratories, and dual-junction perovskite-silicon PV cells have come very close to 30% under test conditions. They also have desirable properties in terms of light absorption, long carrier diffusion lengths, a bandgap that can be tuned, and tolerance of any defects.
They are also able to match the efficiency of crystalline silicon cells while being three orders of magnitude thinner, making them particularly viable for installing on aerodynamic surfaces. Just as interesting are tests in ageing chambers indicating that perovskites could maintain their intrinsic stability for around 20 years. In essence, there is so much r&d going into perovskites that the principal challenge they pose to solar manufacturers is which of the innovations coming from laboratories they would like to commercialise first.
Perovskites themselves are a very broad category of material combinations. Dozens of them are being researched – too many to be listed here – but they include methylammonium lead trihalide, formamidinium lead trihalide and germanium tin alloy-based perovskites.
Typically, the structure of a perovskite cell consists of an electron transporting layer (ETL), a hole transporting layer (HTL), an anode and a cathode. Various sub-categories of the cells are defined by the ordering and architecture of these layers, as well as further variations without an ETL, without an HTL, and with the aforementioned perovskite-silicon tandem structure.
In any case, nothing used in perovskites is especially scarce (apart from their trace amounts of lead), and this abundance is highly appealing from a supply chain perspective. Meanwhile, the thin, flexible, efficient nature of perovskite cells makes them increasingly promising for powering uncrewed vehicles as well as IoT and other applications; the first perovskite PV-powered building came online in Lublin, Poland, in 2021.
Production processes
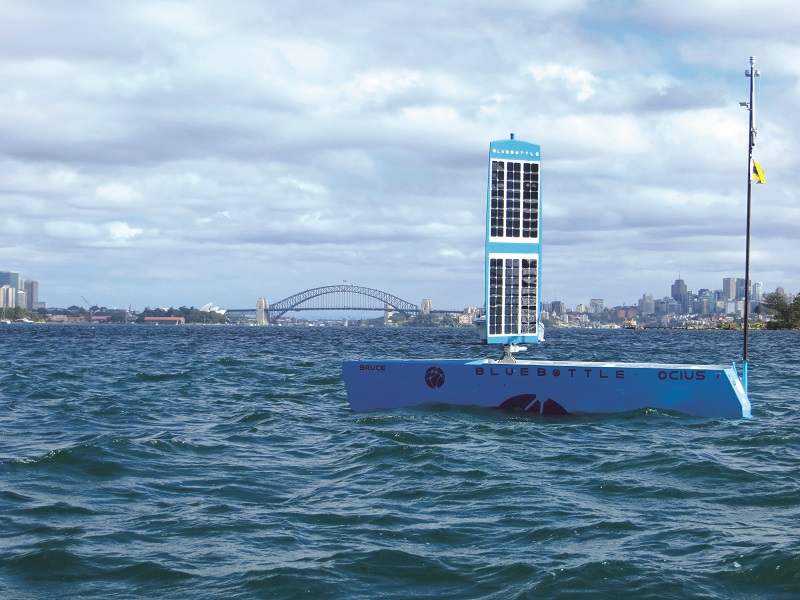
(Courtesy of Solbian)
In the uncrewed sector, there are a few solar manufacturers investing in research and machinery for integrating perovskites into their production chains. One of them is an organisation that also uses a highly flexible (physically and electrically) microgroove-based structural design that, on top of enabling an angular surface to solar cells for better absorption of light from different angles, lends itself to the deposition of other materials with beneficial properties on top of and within the grooves.
While these other materials were once regarded mainly as insulators, this design approach can use practically any materials of interest to solar cell producers. Before manufacture, the constituent materials used in perovskites are in a wet form, which enables them to be used flexibly in well-understood and easily controllable coating methods, such as blade coating, spray coating or slot die coating.
The company has therefore built a printing machine in a pilot manufacturing facility to deposit perovskite inks. Once applied, the wet materials flow evenly across the microgrooves and are then dried to form the PV crystal structure.
Through these material and design selections, it aims to deliver a product optimised for the ratio of price versus solar conversion efficiency as a primary target, with ¢10 per watt at low-volume production and ¢5 per watt achievable at mass production, with anticipated efficiencies of 10-16% based on commercially viable technologies. By comparison, crystalline silicon tends to hover around ¢20/W, and thin-film copper indium gallium selenide around $0.50-1.00/W.
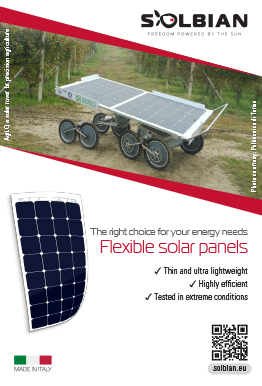
Naturally, these manufacturing advantages also apply to other solar cell materials, be they single-junction perovskites applied to a substrate or dual-junction systems of perovskite on silicon. And although much of the growing use of solar across uncrewed systems has been single-junction systems, more manufacturing of dual-junction cells is expected, for the spacecraft industry in particular, as they can be more easily manufactured to reduce the solar absorptance – the fraction of total incident solar radiation absorbed by a cell – than other materials.
That means they can avoid exceeding operating temperature limits for longer, and therefore, although they will lack the conversion efficiency of a triple-junction cell, their efficiency over their lifetime in space may well be superior. Multi-junction cell production chains can thus be expected to become more widespread, particularly perovskite-silicon dual-junction panels, as their coating and deposition methodologies mean they can be introduced into the production processes behind silicon cells, to enhance the resulting panels’ efficiencies, without changing very much at the factory level.
There are various manufacturing methods for more conventional multi-junction solar materials, as opposed to crystalline silicon, which can be assembled layer by layer using straightforward mechanical approaches.
These correspond mainly to differences in PV materials and combinations. Most follow a general pattern of cutting wafers of solar semiconductor from a large ingot and then carrying out chemical vapour deposition (CVD) of additional layers, such as secondary or tertiary-junction solar cells, anti-reflective protections, and back metals.
The InGaP-GaAs-InGaAs triple-junction cell for instance relies on a method called metal organic CVD, in which a release layer is deposited on a GaAs substrate, and then the solar cells and back metal are deposited on top. After that, the lattice-matched PV cells can be lifted from the substrate thanks to the presence of the release layer, and electrical and glass components can be added to the face of the PV cells to complete the panel. Moreover, the GaAs substrate can be reused multiple times, saving costs and reducing the environmental impact.
Other forms of vacuum coating besides CVD are also used. For instance, one of the perovskite-focused approaches alluded to earlier is to use ‘sputtering’, a process in which atoms are ejected from a solid target material as a result of being bombarded by high-energy particles.
This is a complex approach, but enables the highly controllable consistency and stoichiometry between material layers needed for optimising performance and longevity of thin-film solar cells at scale.
In future, solar manufacturers will face a trade-off between mass-scale, low-cost production and smaller-scale, bespoke production. The uncrewed sector tends towards short production runs and small batches of vehicles, so the ability to tailor PV panels for different wing geometries, bus voltages and operating environments is key.
Design and testing
Developing a new solar panel first requires information on the body of the uncrewed system. This is the ‘substrate’ on which the solar cells are to be laid, and therefore knowing the exact type of plastic, aluminium or composite is key to understanding the electrical conductivity, thermal properties, chord dimensions and many other factors affecting the shape and composition of the panel.

Finer detail can then be derived. For example, data on a vehicle’s bus voltage requirement directly informs the electrical design of the solar cells, particularly how many cells need to be connected together in series or parallel to build up to that voltage, while still meeting the geometrical requirements as defined by the properties of the craft’s body. By extension, that affects the manufacturing process, as the deposition timings, angles and material selections must be changed accordingly.
Panel manufacturers can then experiment with prototypes or samples of the requested material, for instance small pieces or strings of it to show prospective customers what they would receive from larger versions. It can then be tested to evaluate how it will perform under the most severe conditions it might experience over its lifetime.
Some of the steps that PV panels and samples are put through will seem familiar, such as thermal cycling from -50 to +60 °C to simulate the temperatures in the stratosphere, followed by inspecting the adhesives, interconnection points and the cells themselves for damage, as well as some power cycles to see how general performance has been affected.
The cells will also undergo deflection and deformation, potentially while integrated on wing structures similar to those the customer wants to use, to predict how their performance and lifetime could be affected by the mechanical aspects of the platform and operating environment.
Beyond these though, solar panel testing procedures and equipment can be quite unique. Electroluminescence, for one, is an important tool for gauging physical damage to solar cells: by forward-biasing the cells, with visible red or IR light for example, they can be made to luminesce like an LED.
Some solar manufacturers will therefore ‘light up’ their cells, and using an HD or IR camera they can closely measure the impact of damage on the cells’ photovoltaic performance.
Also, directly measuring the solar conversion efficiency, absorptance and other factors relating to the transmission of light through a cell can be performed using sunlight simulators, using lamps that can be controlled to emit different portions and wavelengths of the solar spectrum, unlike sunlight, which changes constantly during the year.
Naturally that also gives the ability to blast cells with UV light to gauge the survivability of different panel layers at higher altitudes and orbits. Other environmental survivability tests might then follow depending on the exact use case, such as damp heat testing to gauge humidity resistance if the uncrewed vehicle is to operate in such areas.
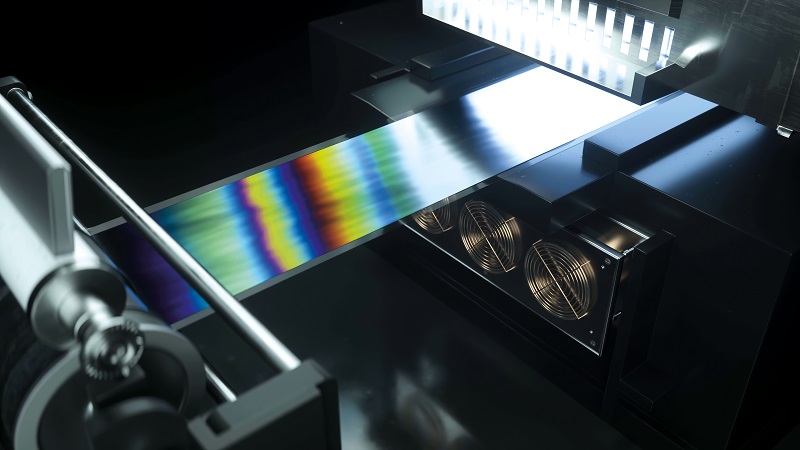
(Courtesy of Power Roll)
Ancillary systems
Work is also ongoing in power management and controller systems. These are key to collecting and distributing power, and therefore towards getting as much current and efficiency from the panels as possible.
While solar cells have varying relationships and architectures with regard to controllers, inverters, grids and other load-relevant systems, MPPT (maximum power point tracking) controllers are emerging as a popular energy management and extraction device among USVs in particular, for their ability to adjust impedance levels and optimise the power transfer efficiency from cell to battery.
Currently, bus voltages for uncrewed vehicles tend to range from 12 to 100 V, and many MPPT controllers are available for such voltages.
But as time goes by and advances in e-mobility increasingly filter through, UAVs and USVs operating on 400-800 V are likely to become more and more common, especially in mapping and intelligence missions which come laden with Lidars, cameras and other power-hungry electronics.
Then there are self-driving road vehicles, with solar-electric driverless cars and trucks likely to become prominent as awareness of thin-film, low-cost PV cells grows among EV makers.
MPPT controllers for such high voltages are in much shorter supply than those for 12-100 V though. Higher voltage MPPTs as well as boost rate controllers to increase the voltages coming from solar panels will be key to bridging the gap between solar technologies and autonomous vehicles in every realm.
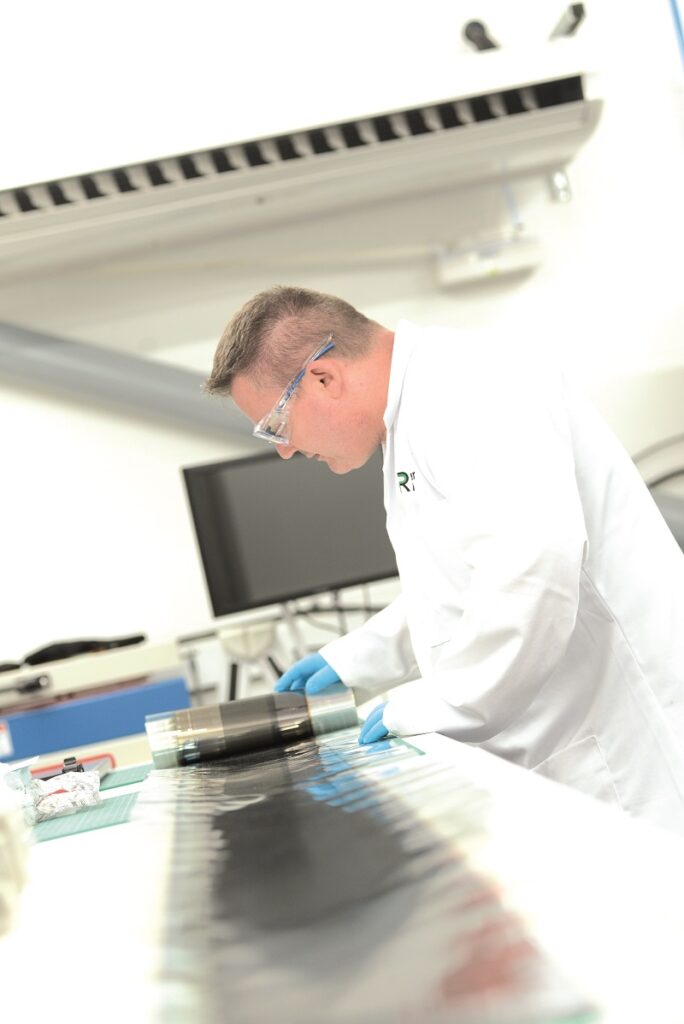
(Courtesy of Power Roll)
Future prospects
Although modern solar cells have matured in many ways, incremental improvements are still being made. Soon, for instance, an InGaP-GaAs-InGaAs material with a 29.5% conversion efficiency in 25 °C and AM0 conditions is to be released, with increases to 30.5% potentially coming in the near future.
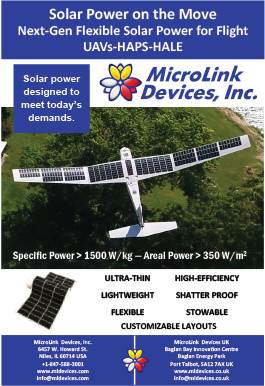
Further ahead, some research organisations that were once focused entirely on photovoltaics are now looking towards thermophotovoltaic (TPV) cells, which can convert heat flux into electricity. They are similar to PV cells but tuned to the thermal radiation spectrum.
While technically that is also possible by using heat engines (usually at lower expense and higher efficiency), TPV panels offer a thinner form factor that could potentially allow the absorption of waste heat generated by IC engines, PEM fuel cells, batteries and electronics, as well as applications such as steam turbines or solar farms.
Thermal radiation falls closer to the IR portion of the EM spectrum than to visible light, so TPV cells need different bandgap materials than PV panels. Research is therefore looking to identify ways of improving their efficiencies, which at the moment cannot reach viable double-digit figures without multi-junction layers. Other factors are lowering their costs and cooling them without affecting the amount of heat reaching them.
While the challenges are significant, the market is likely to be enormous for both recaptured energy and energy storage through TPVs, to the extent that it might one day occupy an equal level of commercial interest to solar cells.
Acknowledgements
The author would like to thank Mark Osowski of Microlink Devices, Luca Bonci of Solbian and Don Scott of Power Roll for their help with researching this article.
Many thanks as well to Tom Markvart, Head of the Centre for Advanced Photovoltaics, Czech Technical University in Prague, Czech Republic, and Emeritus Professor of Energy Conversion, University of Southampton, UK, for his peer review of this article.
Some examples of solar power-related suppliers
FRANCE
ASCA SAS | +33 240 384 000 | www.asca.com |
GERMANY
Gochermann Solar Technology | +49 410 390 4488 | www.gochermann.com |
ITALY
Solbian | +39 011 966 3512 | www.solbian.eu |
LITHUANIA
Metsolar | +370 650 69905 | www.metsolar.eu |
UK
Oxford PV | – | www.oxfordpv.com |
Power Roll | +44 191 543 9254 | www.powerroll.solar |
Solar Technology International | +44 168 477 4000 | www.solartechnology.co.uk |
USA
Ascent Solar Technologies | +1 720 872 5000 | www.ascentsolar.com |
Envision Solar | +1 858 799 4583 | www.envisionsolar.com |
MiaSole | +1 408 940 9658 | www.miasole.com |
MicroLink Devices | +1 847 588 3001 | www.mldevices.com |
Osazda Energy | +1 505 218 7228 | www.osazda.com |
Rocket Lab USA | – | www.rocketlabusa.com |
SunPower | +1 800 786 7693 | www.sunpower.com |
UPCOMING EVENTS
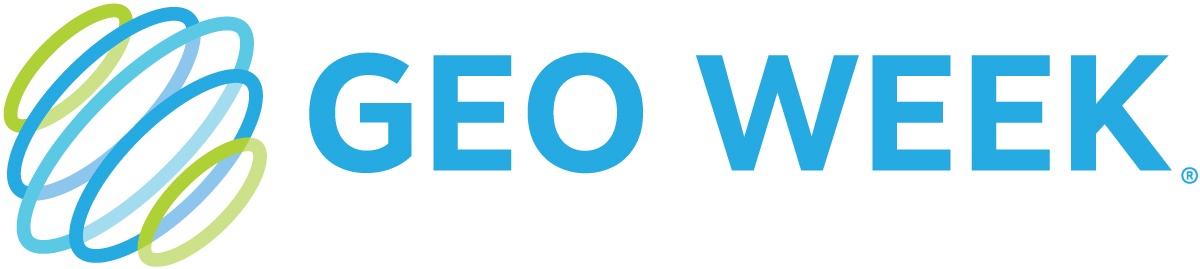
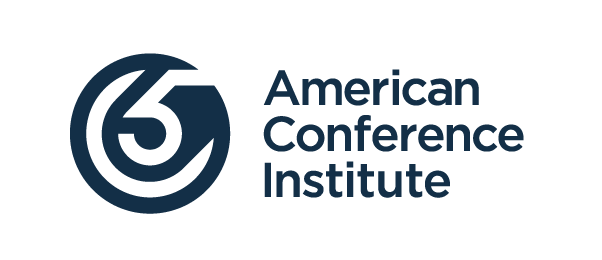
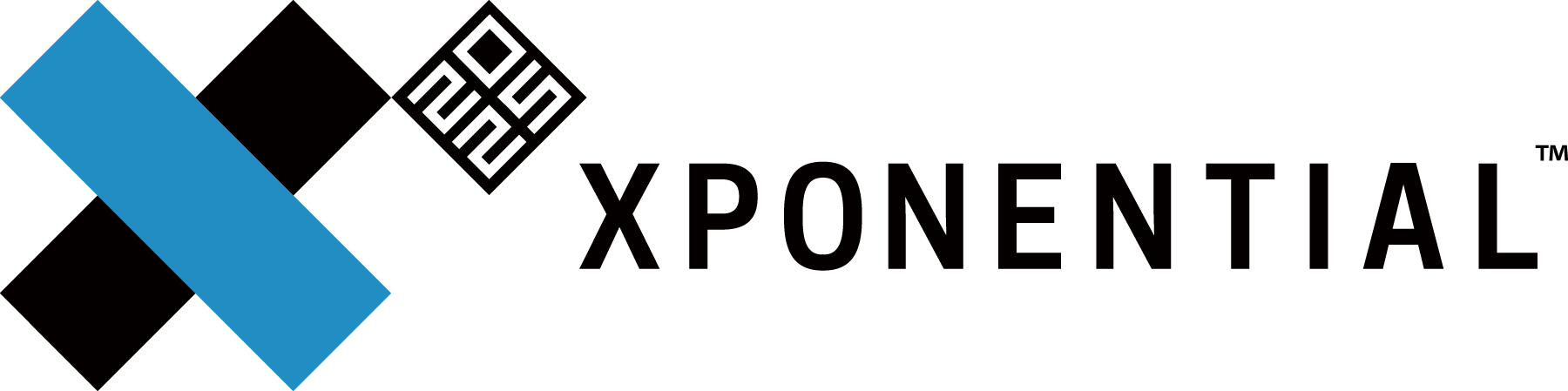
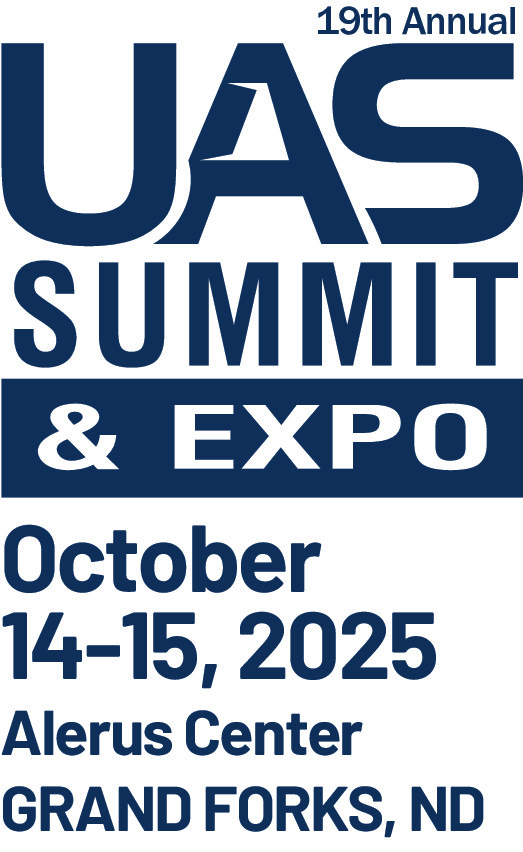
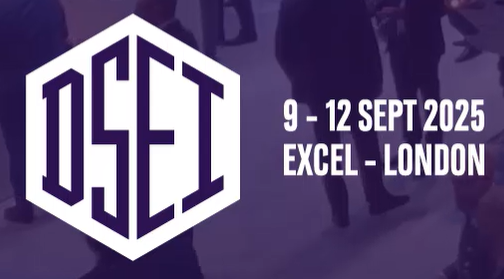
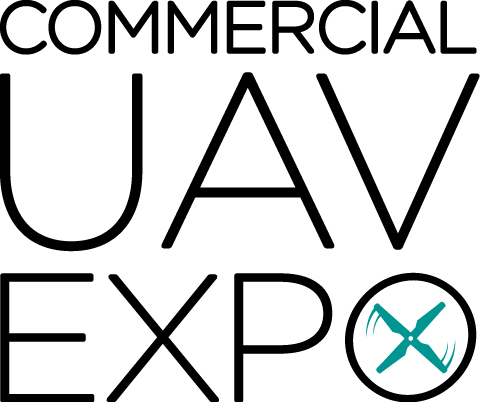
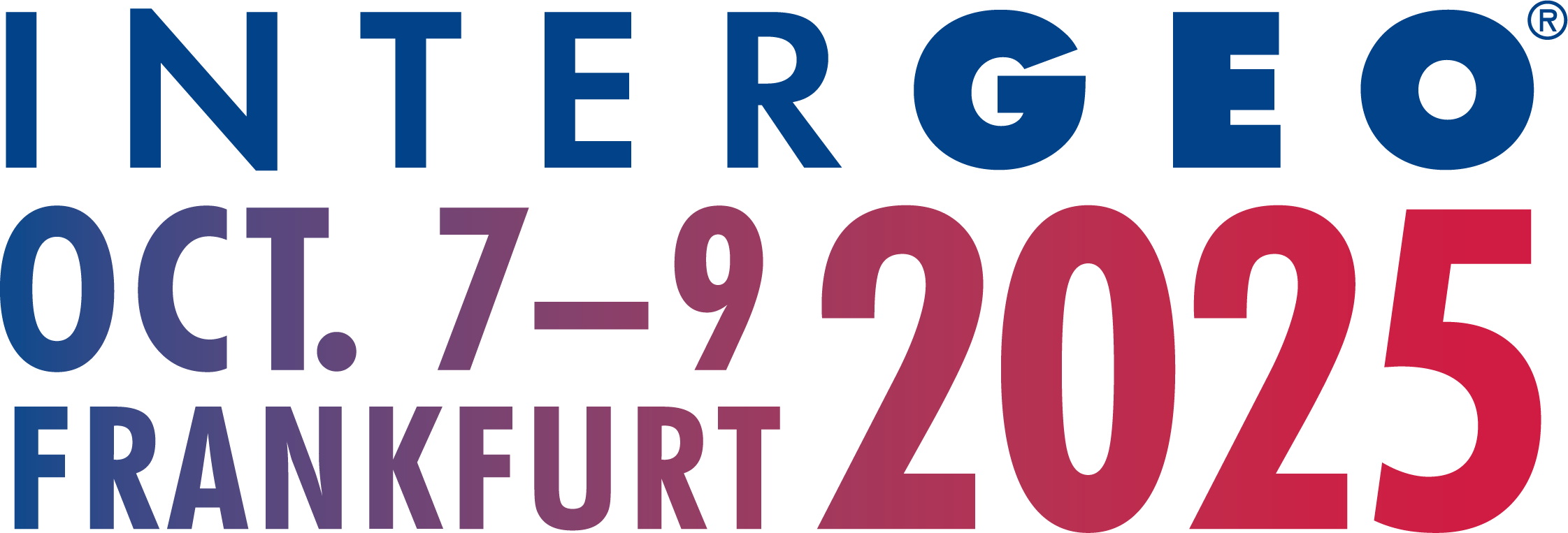
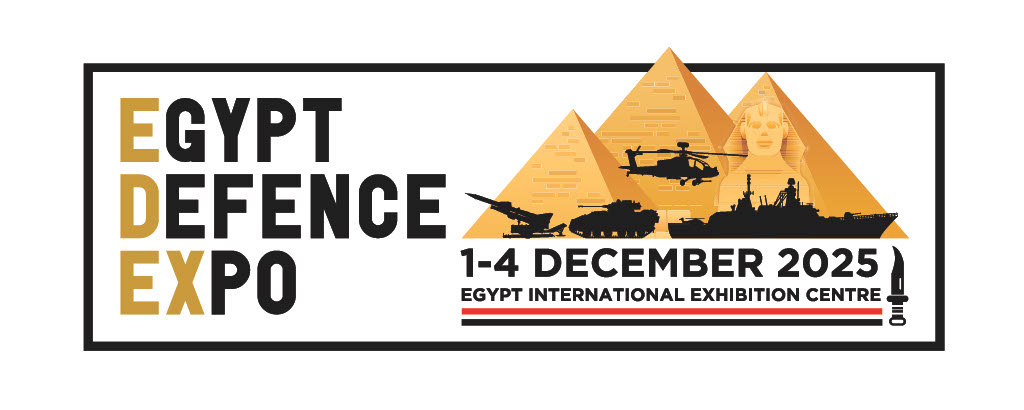
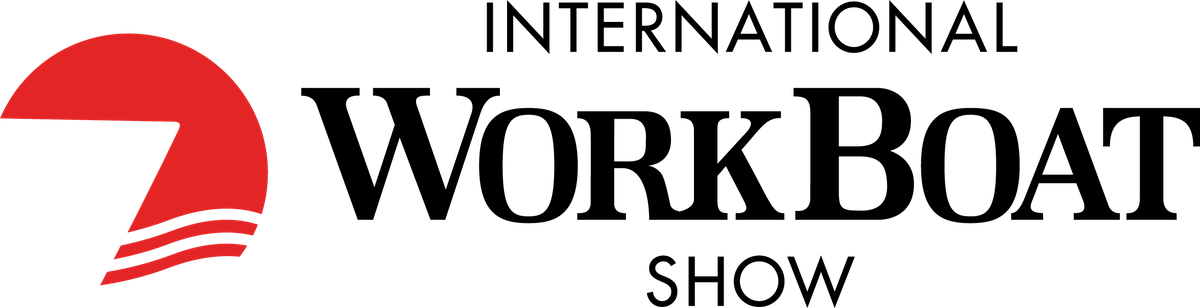
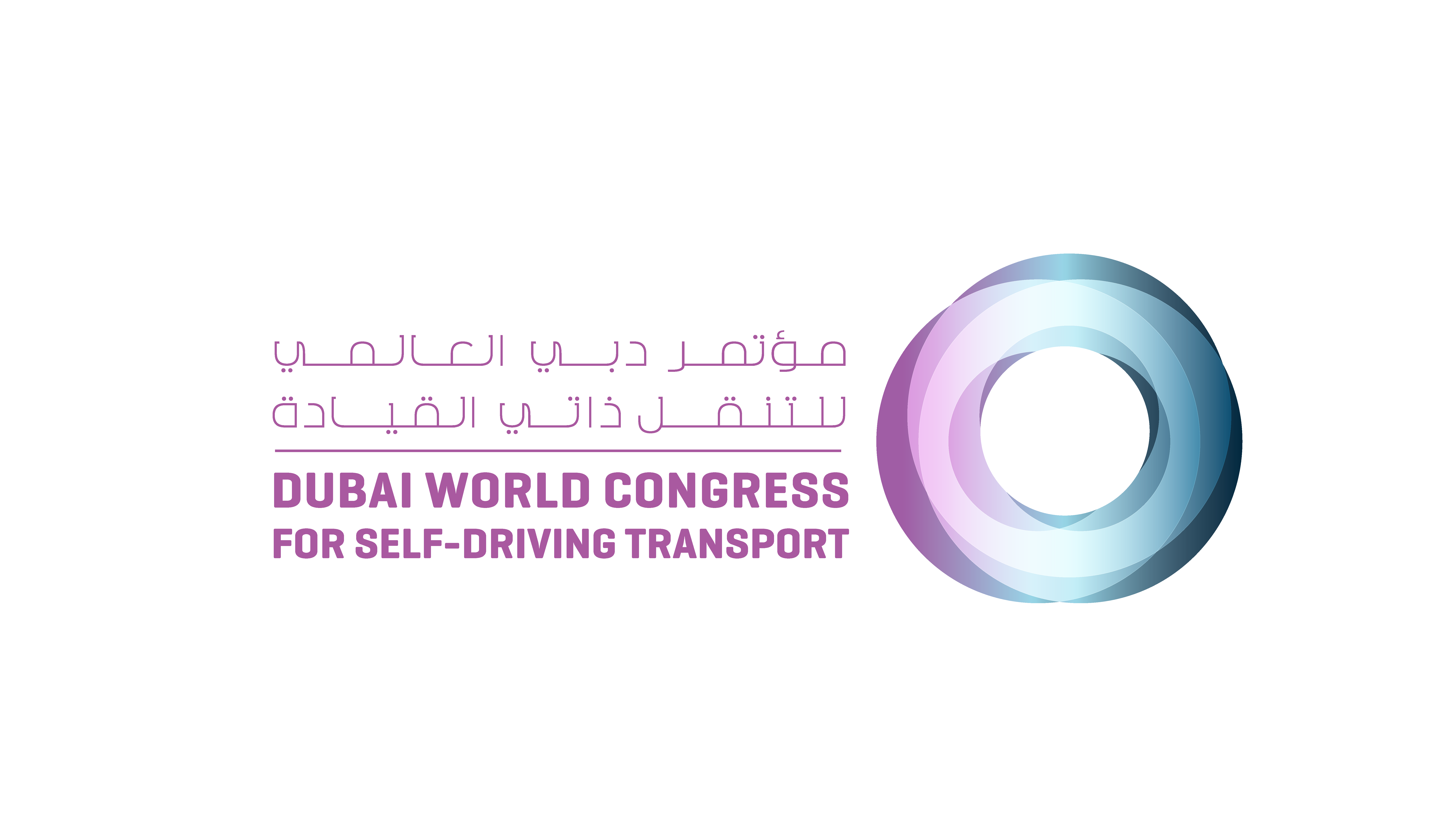
