Robotnik RB-WATCHER
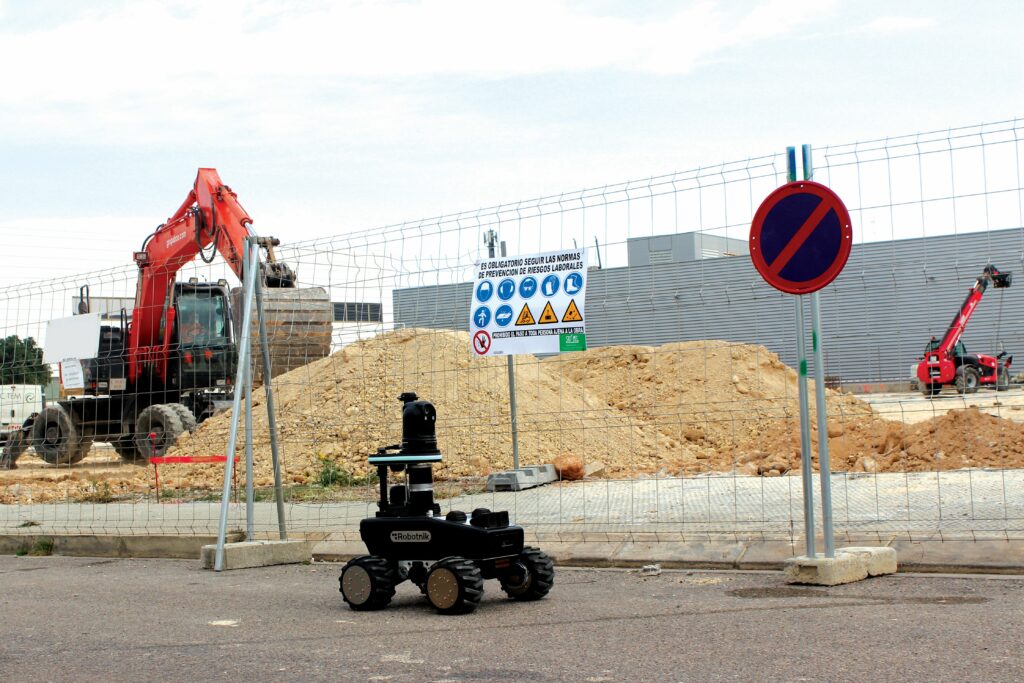
(All images courtesy of Robotnik)
One to watch
Rory Jackson meets a robot designed to navigate and inspect the inside and outside of industrial facilities safety
As uncrewed systems transition away from being little more than one-off science experiments and evolve into serious industrial tools that are as essential to industrial facility workers as a screwdriver, they are being designed with tougher reliability and ruggedness to withstand the environmental and impact risks of functioning everywhere from chemical plants to power stations and oil rigs.
The latest system from Spain-based Robotnik, the RB-WATCHER, integrates a plethora of sensors on a ruggedised body to navigate and inspect the inside and outside of industrial facilities safely, with little risk from indoor or outdoor hazards or single points of failure.
The RB-WATCHER measures 904 x 731 x 614 mm and weighs 73 kg when empty (its weight capacity for payloads being 50 kg). It moves at 2.5 m/s (9 kph) in its typical industrial-inspection missions and has a five-hour operating endurance; these capabilities coming from a 4WD, battery-electric powertrain. That mounts to a body rated to an IP54 protection level, meaning the bulk of the UGV is secured against limited dust ingress and from low-pressure waterjets coming from any direction.
Robotnik has more than two decades of experience in engineering robotic systems, including developing uncrewed mobile systems and robotic manipulators. That experience and the design specifics of the RB-WATCHER are key to how it is now racking up real-world commercial successes as a high-end industrial inspection robot with several users (and many others in the pipeline).
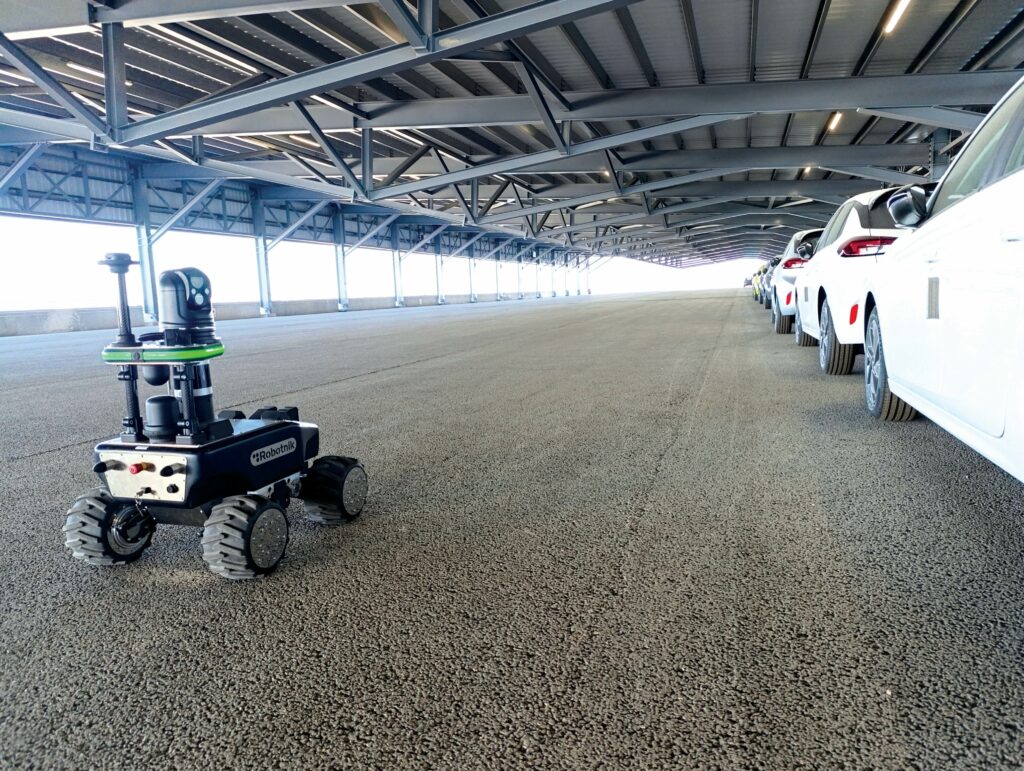
Development of the RB-WATCHER began in 2018, as a specialised derivative of a predecessor platform, the RB-SUMMIT, which was created (and is still sold by Robotnik) as a multipurpose UGV just over 15 years ago.
“We were searching for new, more imperative use-cases and we found a particularly strong market demand [from people] in the electrical energy sector here in Spain, who saw a valuable niche for autonomous robots in regular inspections,” says Marta Millet Pascual-Leone, robotics business development manager at Robotnik.
“We held a period of consultation with them for a long time, trialling different robot configurations, and using different sensors and subsystems – including different Lidars, cameras, GNSS technologies and algorithms for autonomous navigation.
“That enabled us to profile the needs of the ideal robotic platform for not just that use-case, but general inspection use-cases.”
That profiling included key lessons on engineering the robot for electrostatic safety in electrical environments, and also for minimal vibrations and maximum environmental ruggedness against the variables specific to both the indoor and outdoor sections of the customer’s facilities.
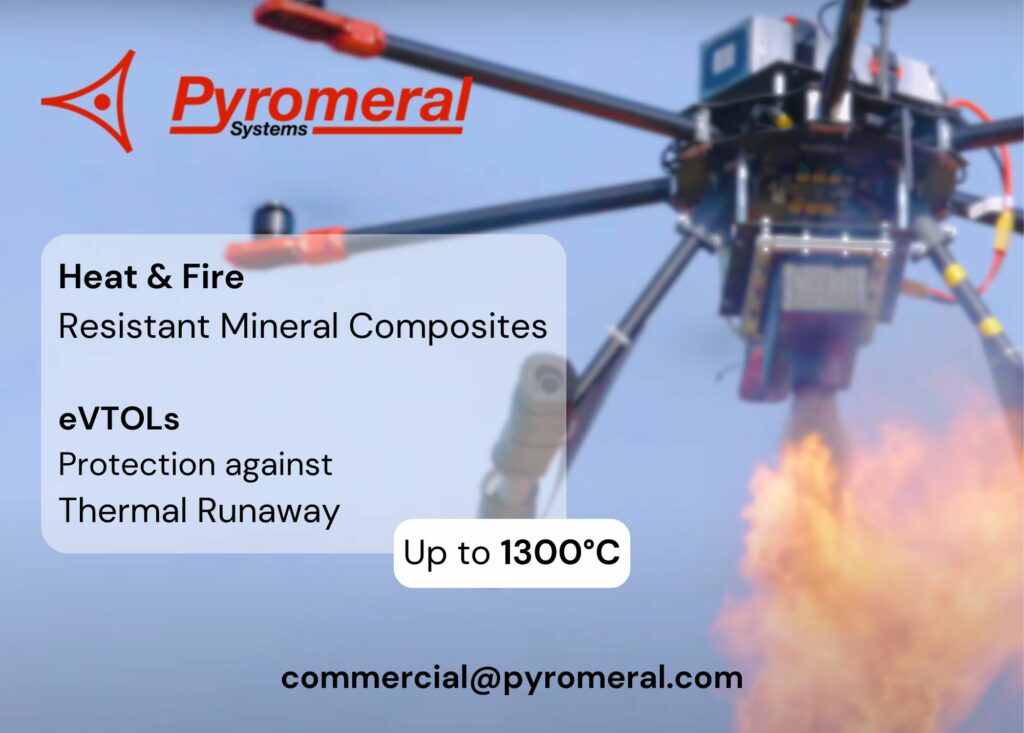
For those subsystems that needed to be placed outside of the IP54-rated shell of the UGV’s body, sourcing appropriately weatherproofed components (that would not break the bank) would prove a particular challenge for Robotnik’s engineers.
While one might assume that optimising indoor navigation was the only significant challenge facing Robotnik’s software developers, the outdoor navigation also presented numerous hurdles to success due to issues such as the changing nature of outdoor conditions presenting unpredictable sources of interference, and the clustering of concrete and metal structures hindering GNSS and other sensors.
The result of tackling all of these obstacles was a prototype of what is now the RB-WATCHER, which was deployed and trialled by the customer. Thanks to the developers engineering it to successfully navigate and endure consistently in both harsh indoor and outdoor industrial environments, the customer renewed the contract and added 10 more units.
“With that, we had the data and confidence to profile the UGV in such a way that we could then extrapolate any necessary design tweaks to slightly modify this system for other, similar use-cases and industries, such as inspections in other types of energy companies, airports and other industrial places,” Millet adds.
From the summit
As indicated, the RB-SUMMIT operated for years prior to the conception of the RB-WATCHER. Originating as an r&d project, it found particular use as a platform for universities and research organisations to trial and integrate technologies relating to outdoor navigation.
“When we decided to embark fully on the industrial inspection use-case, we spent the first three or four months doing tests with the most important sensors in our own facilities,” Millet says.
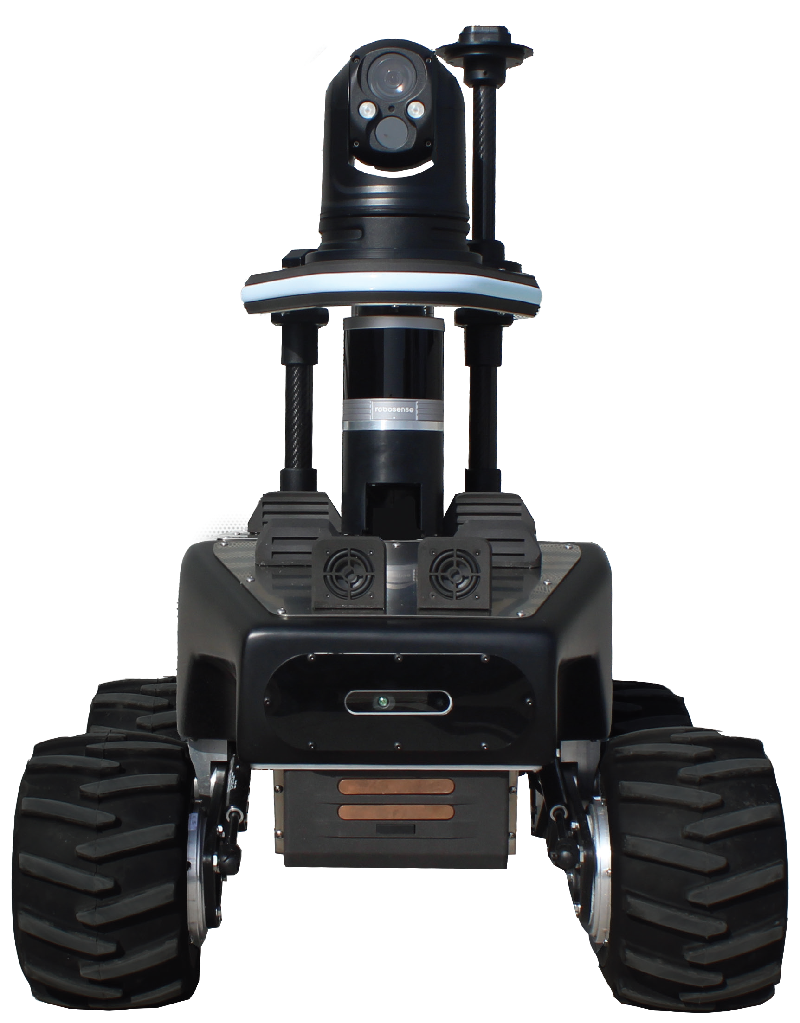
“For example, we integrated many different possible camera gimbals. The ‘right’ camera head had to give thermal data, while also balancing for several other performance specifications, but after those first three or four months we realised the electric motors we were using weren’t good enough.
“They were 24 V systems, and we needed 48 V to have enough power. Luckily, we’d already been researching how we might upgrade the batteries from 24 V to 48 V packs, which meant the whole powertrain could be upgraded together with reasonably simple power integration.”
Those developments and several others took place within the one-year consultation period, with the customer subsequently ordering 10 more units of the finished prototype, as mentioned. Robotnik additionally updated and re-released the RB-SUMMIT with some fine-tuning lessons learned via the RB-WATCHER to make the Summit viable as a commercial inspection solution.
While Robotnik can customise the RB-WATCHER to suit customer needs, this is rare among the units being output from its manufacturing plant and is usually for specific clients who want an especially large batch of UGVs.
“This year, we’ve manufactured between 30 and 35 units of the standard version of the RB-WATCHER,” Millet says. “It’s true that the software is constantly being updated, most often for things like camera or other subsystem providers sending firmware updates, which means we have to do minor updates on our end.
“The principal idea is to have the same sensors and electronics for all our RB-WATCHER clients because, by and large, those subsystems are components that have been validated to do these types of operations in these types of hazardous environments over many years of tests and commercial operations.”
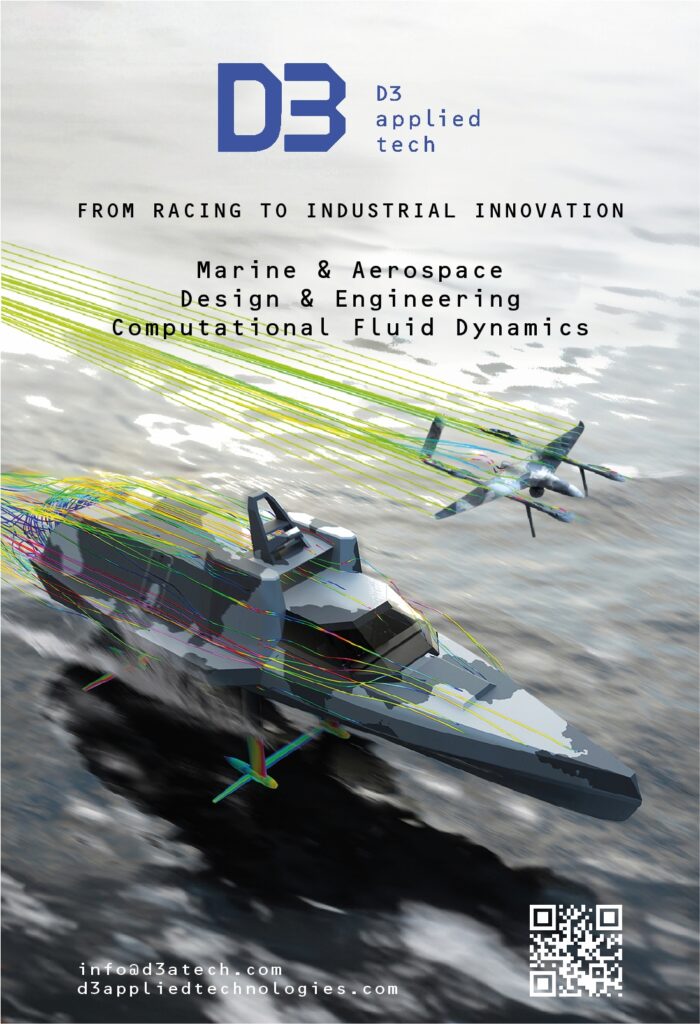
Naturally, Robotnik will aim to optimise the custom versions it provides to the best of its ability, but these will inevitably have individual differences that are not as tried, tested and validated as the standard RB-WATCHER.
Hence, the company tends not to call them RB-WATCHER when it ships them, preferring to give them new names or codes to differentiate them from the standard-issue UGV.
Watching the Watcher
Millet gives a rundown of the RB-WATCHER’s subsystem layout. At the highest point on the 904 mm-tall UGV is the RTK-GPS antenna, ensuring its ability to maintain a line-of-sight link with GPS satellites.
That antenna stands atop the rear of a raised platform over the UGV’s body, with this platform also mounting a gimballed inspection module, which integrates EO/IR cameras in a pan-tilt configuration.
Underneath the inspection module is a 3D Lidar, which is key to localisation, as well as detecting and dynamically navigating around obstacles. That Lidar sits atop the RB-WATCHER’s body, inside of which are the UGV’s core components. Among these are its computers, its IMU, its batteries and weatherproofed fans for cooling the electronics.
On the front of the body is a RGBD (red, green, blue and depth) camera, which provides several navigational functions, most importantly the detection of (and navigation towards) the system’s automated charging station. As a consequence, the lower front also features contacts for docking with it. Lastly, four wheels sit around the body, each driven by an in-wheel electric motor.
Metal and fibreglass
The RB-WATCHER’s outer body is made from fibreglass composite pieces, reinforced internally by an aluminium frame, which also serves as a chassis for mounting the internal subsystems on a plate. This aluminium plate also secures mechanically to the body at the rear for added rigidity.
Aluminium was chosen for the interior structural material as a compromise between several key operating requirements. One is that it provides for effective heat extraction and dissipation, with the fans blowing air throughout the body to cool the metal as it conducts heat from the electronics. Another was weight, as a heavier robot consumes more battery energy and hence suffers from reduced operating endurance.
The last requirement was stiffness, particularly to prevent any flexing or reverberation that could allow the upper inspection module to vibrate or sway; a key risk when operating outdoors where the system may periodically drive over gravel or sand.
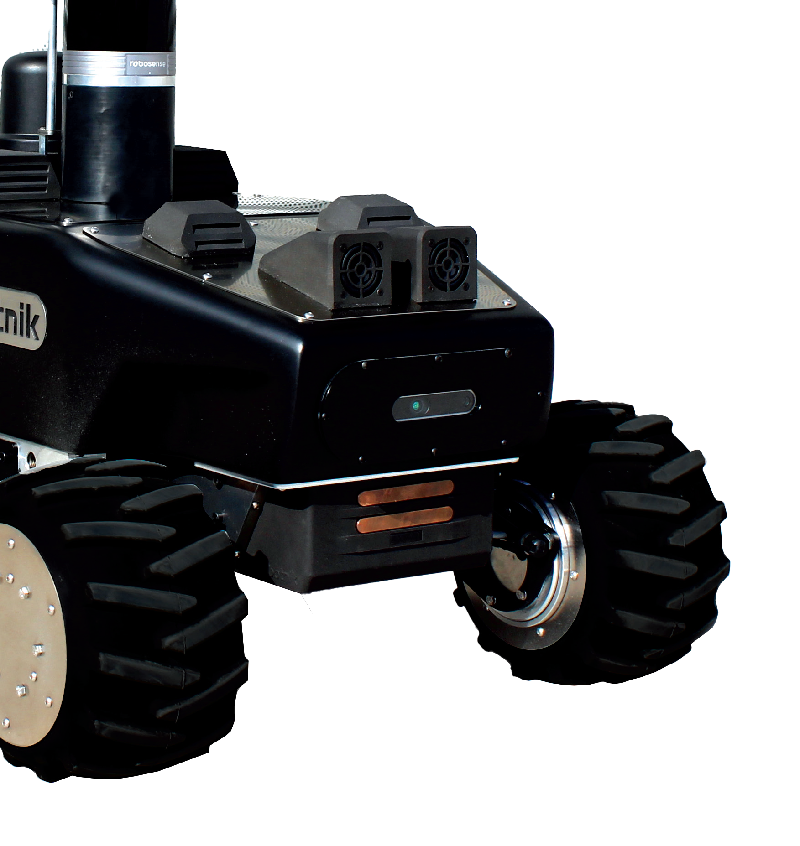
“As for fibreglass, that made more sense than carbon fibre as a body material, because we’re trying to offer a less pricey alternative to the very expensive UGV systems currently making the biggest movements into industrial inspection, like the four-legged robots you’ve seen before,” Millet explains.
Using carbon instead of fibreglass might have doubled the price of RB-WATCHER. Additionally, fibreglass serves as a sufficiently safe and robust material in many environments, including those with electrostatic and chemical risks, which some carbon fibres might not have guaranteed.
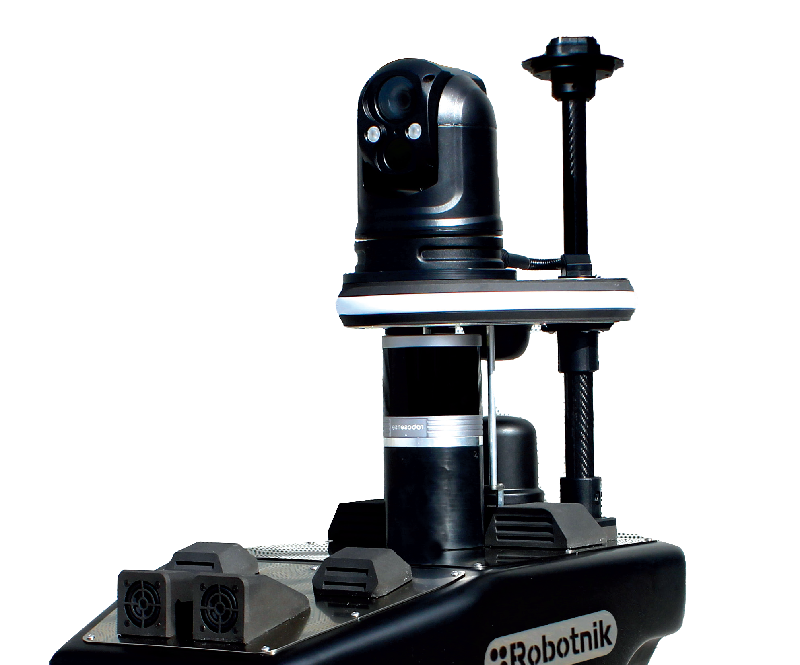
Navigation systems
As with the structural materials, the choice of 3D Lidar (from a few routinely used models) for sensing and avoiding obstacles depends on numerous factors. While these include perennial qualities such as price, the most important Lidar performance parameters are resolution and vertical FoV (all Lidar choices having a 360o horizontal FoV).
Optimising the former means that the 614 mm-wide robot can move effectively between objects and around corners without needing cumbersomely wide paths to avoid collisions. Maximising the latter is critical to ensuring the UGV can sense the ground ahead in detail, including hazards that the RGBD camera may find hard to detect, such as potholes.
Both Robosense’s Helios and Velodyne units have been used as the RB-WATCHER’s Lidar to fit these requirements.
The RGBD is a stereo camera, with Intel RealSense systems being used as of writing, although Zed stereo cameras have also been used. Again, price is a key factor in component selection, but as a critical source of navigation inputs, operational stability was also vital.
“The RGBD camera must be turned on and off many times over the robot’s lifespan, and in some camera designs this can provoke instability, but RealSense has proven quite stable so far where others failed. Its frame rate and FoV also worked very nicely for our needs,” Millet adds.
RTK-GPS is used for centimetric accuracy in georeferencing the inspection data taken (where GPS signals are available), with the quality of corrections playing the biggest part in system selection. Meanwhile, the IMU was chosen for being a precise and auto-calibrating system; a crucial requirement of the UGV’s autonomous 3D localisation working persistently.
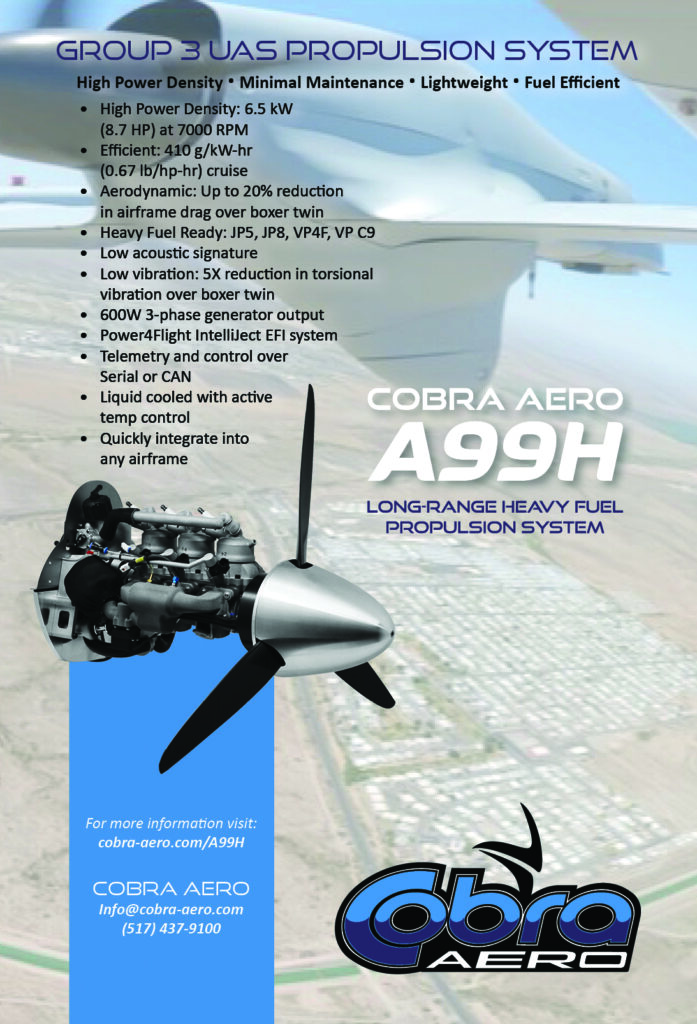
That localisation process is not SLAM. While it is performed in real time, the map within which RB-WATCHER localises is either derived from GPS data when outside or from an embedded dataset that is generated before its autonomous inspection work officially begins.
“The robot comes with a remote controller, so that someone can connect it, trigger the mapping procedure via a web browser, and control it as it collects data via its Lidar and RGBD camera for a 3D map of the facilities it is to inspect and the routes it is to take,” Millet says.
Compute
Data from the GPS, IMU, Lidar and stereo camera all feed into an off-the-shelf Intel i7 CPU model and board chosen for its high RAM and SSD storage capacity (typically, a system between the 10th and 12th generation is used).
That CPU processes the navigation inputs to generate movement decisions for the powertrain and the inspection head to go through preplanned mission objectives, such as GNSS waypoints and inspection targets.
In addition to using ROS as middleware, Robotnik works with Energy Robotics for an upper layer of software that collates and interprets both the navigation and inspection data coming from the RB-WATCHER, with cloud-based processing for those requiring intelligent analytics of the data (although initial processing of all data is done at the edge as standard).
“The RB-WATCHER’s onboard software originally came from the RB-SUMMIT, before being developed for key needs like inspection packages particular to industrial users,” Millet says.
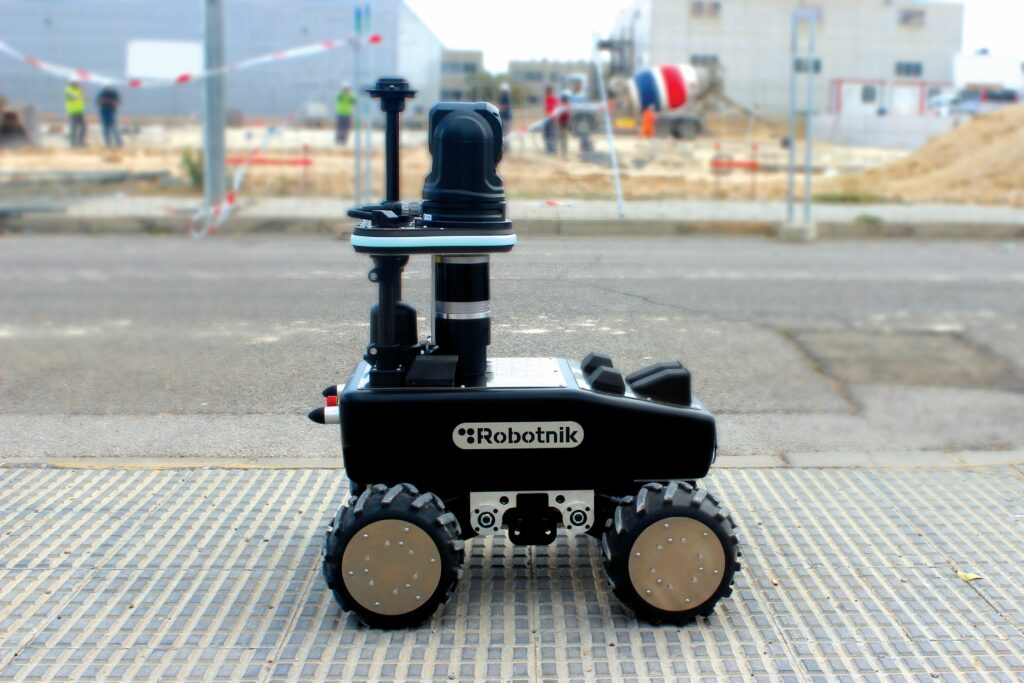
“We mainly used open-source tools,as well as algorithms developed and stored following the wide range of r&d projects we’ve taken on over the years. The final algorithms used in the RB-WATCHER were created by extrapolating the best lessons and code for this use-case from each of these.”
Powertrain
The RB-WATCHER runs on four electric motors, each integrated inside its respective wheel and outputting 500 W at the UGV’s 9 kph normal operating speed. This configuration avoids the need for a gearbox that would take up weight and volume inside the small robot body, and it also enables skid-steering by way of torque vectoring. The RB-WATCHER can thus turn on the spot, maximising its nimbleness in potentially cluttered indoor floor spaces.
“The tyres around the wheel are the same rubber, deep-tread items we used on the wheels of the RB-SUMMIT for many years. As that UGV was a multipurpose system, which needed to be able to move in different terrains, environmental conditions and inclines, it made sense to use exactly the same tyres on the RB-WATCHER, which may drive through sandy, uneven outdoor spaces, or dirty or wet indoor spaces,” Millet adds.
“The motor-control drivers we chose after testing many different units, with reliability being one of the most important traits we were after. We eventually chose a unit that exhibited very consistent communication with the CPU; not just to make sure the driver was receiving control output commands for the motors, but also to be certain that the CPU could always monitor the motor controllers and make sure they’re working correctly, making it a closed loop.”
The battery is built around lithium iron phosphate (LFP) cells; a cathode chemistry used in Robotnik’s previous battery-electric solutions for its touted safety and electrical stability benefits. The pack in the RB-WATCHER is designed for a 48 V output bus and it is sized for 15 Ah of energy capacity.
Robotnik chose this chemistry and formed its pack design around several other key capabilities it needed. For instance, optimising its ability to recharge quickly would minimise downtime; conversely, fast discharging was important as the motors can occasionally request a very high current – for example, when moving on surfaces with poor grip or on inclines (with the UGV able to move on inclines of 80% or 38.66°).
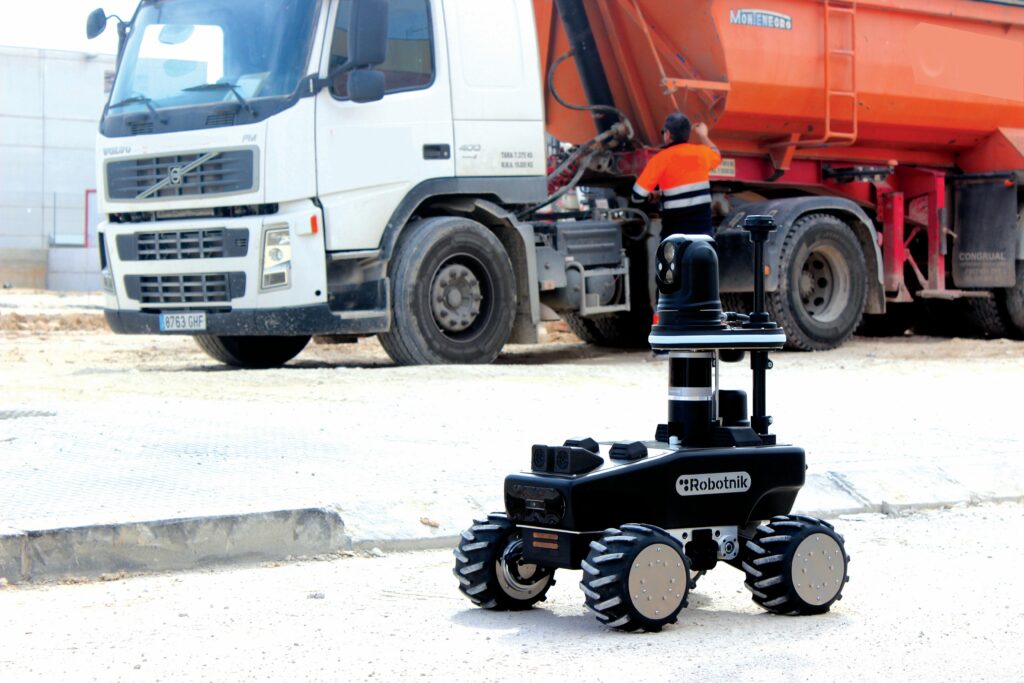
“With the C-Rates the pack can achieve, the RB-WATCHER’s battery can go from empty to a full state of charge in about two hours, which then gives it four to five hours of runtime,” Millet says.
After driving into the charging station (with the front of the RB-WATCHER’s body fitting into its receptacle), conductive contacts on the front of the UGV connect with contacts in the station. Magnetic sensors in the charging station confirm whether the connection has occurred successfully, and if it has, power starts being transmitted to the robot, typically at 600 W.
“The charging station design, as well as the charging control software, are generally the same across all our robots, with small adaptations for application-specific needs; for instance, the
RB-WATCHER’s charging station needs to be covered to protect against direct contact from rain, as many users want to place it outdoors,” Millet adds.
Inspection devices
As Millet explains, the EO/IR gimbal atop the UGV is used solely for the inspection missions prized by the end-user, and it never becomes necessary for navigation.
The choice of inspection camera primarily came down to size; too large a sensor head on top of the UGV, and the resulting vibrations and inertia would have been detrimental to stable image capture (as well as stable movement).
“And, of course, it was equally fundamental that the gimbal had very fine pan-and-tilt control for accurate, shake-free imaging,” Millet adds.
Going for a very high-quality thermal imager was also important, as IR photography was expected to be the most important part of the robot’s inspection work, revealing cracks, degradation and hotspots in industrial assets to an extent that EO cameras cannot match.
Lastly, getting consistent data output and communications from the cameras to the UGV was especially vital during the engineering process, given that this forms the first step towards achieving real-time monitoring and analysis of the inspection information it generates (the next steps of remote data links and operator systems are discussed later).
A ring of LEDs integrated inside the platform on which the gimbal sits provides visibility for the EO camera in low-light conditions, as well as giving different condition-specific light signals to nearby personnel; for example, when recharging or detecting signs of a fault. It also helps personnel watch out for the robot and avoid colliding into it in areas of high foot traffic or vehicle traffic.
Robotnik tested various LEDs for electromagnetic compatibility, software compatibility and electrical stability before choosing and integrating the ideal components.
In addition to the two cameras and the LEDs, a microphone is installed on the RB-WATCHER; something our avid readers will know is used for audial detection of gas leaks, malfunctioning electrical systems and other potentially dire anomalies in industrial facilities.
“Choosing microphones is certainly easier than choosing Lidars and thermal cameras, given that microphones are a long-established technology, but getting the microphone right in the RB-WATCHER still meant getting a very tight integration for good data delivery,” Millet says.
A speaker is also installed for the UGV’s operator or crew to transmit audio warnings, where appropriate.
“People might think microphones and speakers are a lot cheaper than Lidars and cameras, and that there would be lots of options for us to choose from, but that’s not exactly the case. We needed IP65-rated systems; waterproof and weatherproof, and capable of communicating via USB or Ethernet with our CPU,” Millet says.
“That narrows down the options significantly. We also needed their firmware to be compatible with our software, including the ability to trigger either the mic or speaker from the operator’s HMI with good consistency and low latency. That includes enabling users to trigger automated audio recording when there are signs of a machine or infrastructure item failing. So, only after testing many systems did we find good fits for both.”
Communications
Inside the UGV’s body is a multipurpose router, designed for 4G, 5G, wi-fi, Bluetooth, and GPS receptions and transmissions. More conventional radio systems had been tested previously, but were found to give significantly slower latency in real-time communications and monitoring.
Most often, 4G and wi-fi are used for remote monitoring and control signals from the end-user’s preferred command centre (such as the onsite office of the safety inspector), while Bluetooth is used for the handheld remote controller.
That router was chosen for its tight size (and hence its ability to fit inside the RB-WATCHER’s body, along with the other electronics mentioned), as well as efficient power consumption, not to mention the many comms standards listed above (with 5G SIM card compatibility also being important for future real-time inspection data-streaming in areas without wi-fi).
“Those many standards meant we had to integrate many different antennas in the early designs of the RB-WATCHER, which meant an impractical cluttering of antennas, which was risky for working inside and around industrial assets, and also a great deal of wiring that had to be stuffed inside and routed throughout the robot,” Millet recounts.
“But now, we’ve found and integrated a six-in-one antenna module that communicates across all of the router’s bands. It’s a dome-shaped device we install behind the Lidar; the only receiver it doesn’t connect with is the GPS, as the GPS antenna has to be on the upper part, and the six-in-one module was too large to install at the top.”
Operator systems
The Bluetooth-linked remote controller is actually a PlayStation 5 handset, given the plethora of context-sensitive and reconfigurable key bindings it provides.
“Our HMI software for monitoring, pre-programming and controlling the RB-WATCHER is based in a web browser, so it can be run from any desktop, laptop, tablet or smartphone,” Millet says.
“In principle, the HMI software uses the same core software as all our robots, but it has also been re-engineered with plug-ins specific to the inspection use-case. That has been key, for example, to operators being able to monitor the different camera inputs.”
The RB-WATCHER’s HMI software comes with a task sequencer for end-users to intuitively plot and schedule different inspection tasks in their desired geographical and chronological order. Another plug-in enables the location of the robot to be shown or shared in Google Maps, while others provide for visualising data from the robot in ways that industrial safety officers might need in order to make actionable reports from the gathered survey information.
“We also had to develop a REST API [which conforms to the representational state-transfer (REST) architectural style], so that when certain customers in the industrial space don’t want to use our interface, or maybe prefer to run our HMI from their own facility management software, that API can facilitate it. We have also used MQTT APIs that have worked well and tend to integrate smoothly with IoT devices.”
Future
While the RB-WATCHER has been available for a few years now, Robotnik’s engineers are continuing to optimise and update the system, most recently releasing a new version of the HMI with a cleaner layout and greater ease of reconfiguring the alarms, monitoring tasks and other automated behaviours.
“We’re exploring new ways to update the robot, including contactless, wireless charging technologies, ways of integrating more cameras in different locations across the body, and the potential for integrating gas-detection sensors and even robotic manipulator arms,” Millet says, alluding to Robotnik’s long-running portfolio of mobile manipulators for industrial applications.
“We automate tasks with robotic arms all the time, including one project with an RB-SUMMIT using an arm in agricultural r&d, and we’re interested in how we could get a future version of the RB-WATCHER to start handling manual maintenance tasks with an arm of its own. But we want to accomplish lots of r&d to make something that works reliably enough to meet industrial safety standards, so it’s not something you’ll see from us within the next few months.”
Key specifications
Dimensions: 731 x 614 x 904 mm
Empty weight: 73 kg
Payload capacity: 50 kg
Speed: 2.5 m/s
Enclosure rating: IP54
Maximum endurance: 5 hours
Operating temperature range: -10 C to 45 C
Maximum slope: 80% or 38.66°
UPCOMING EVENTS
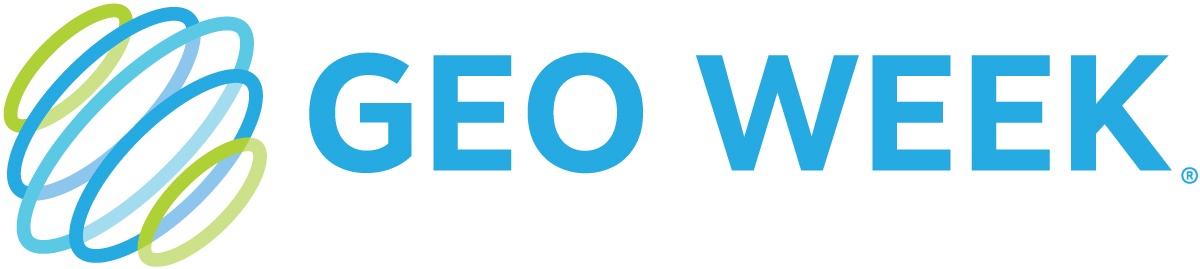
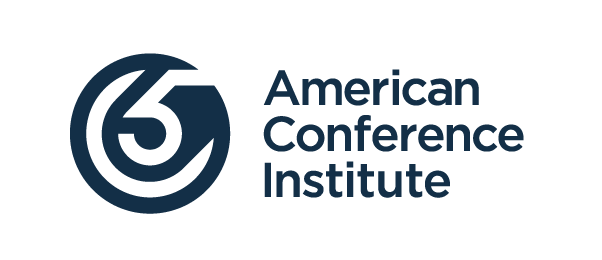
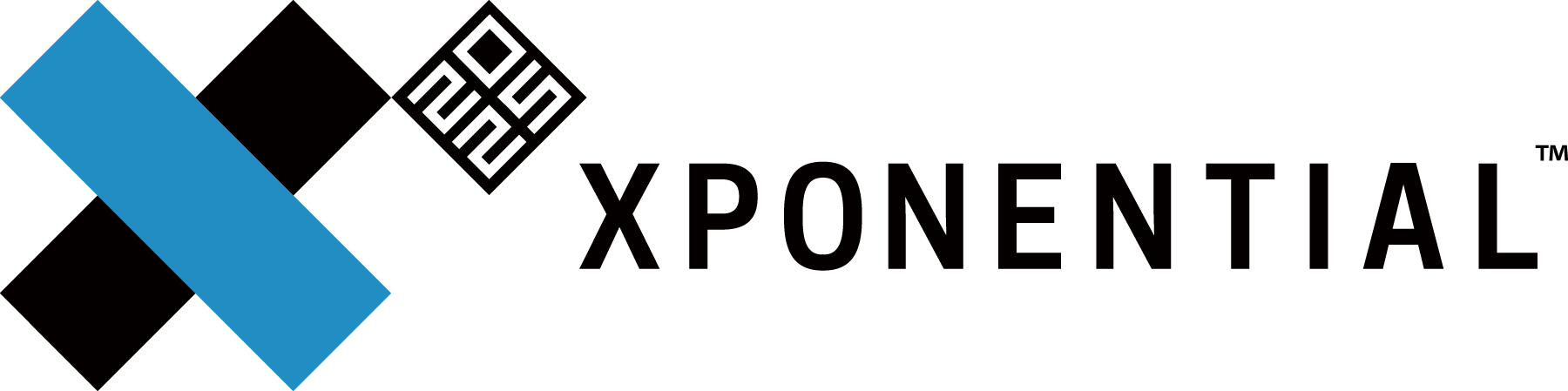
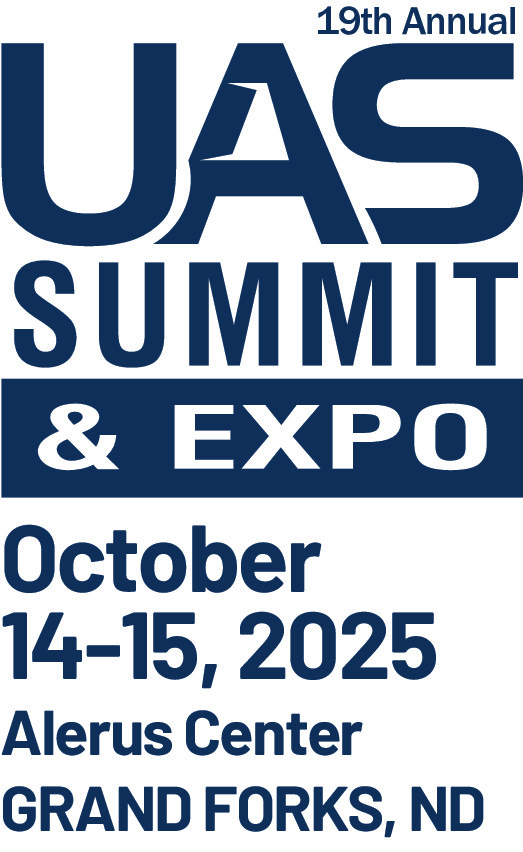
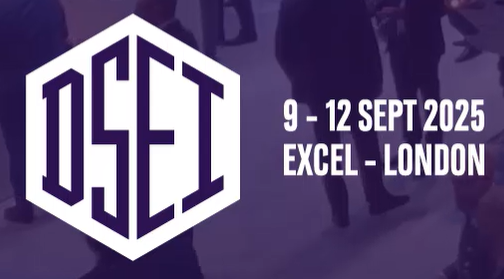
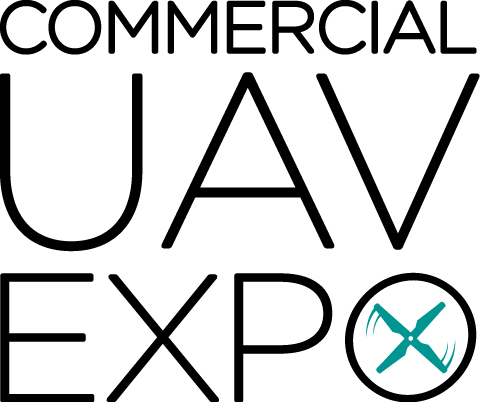
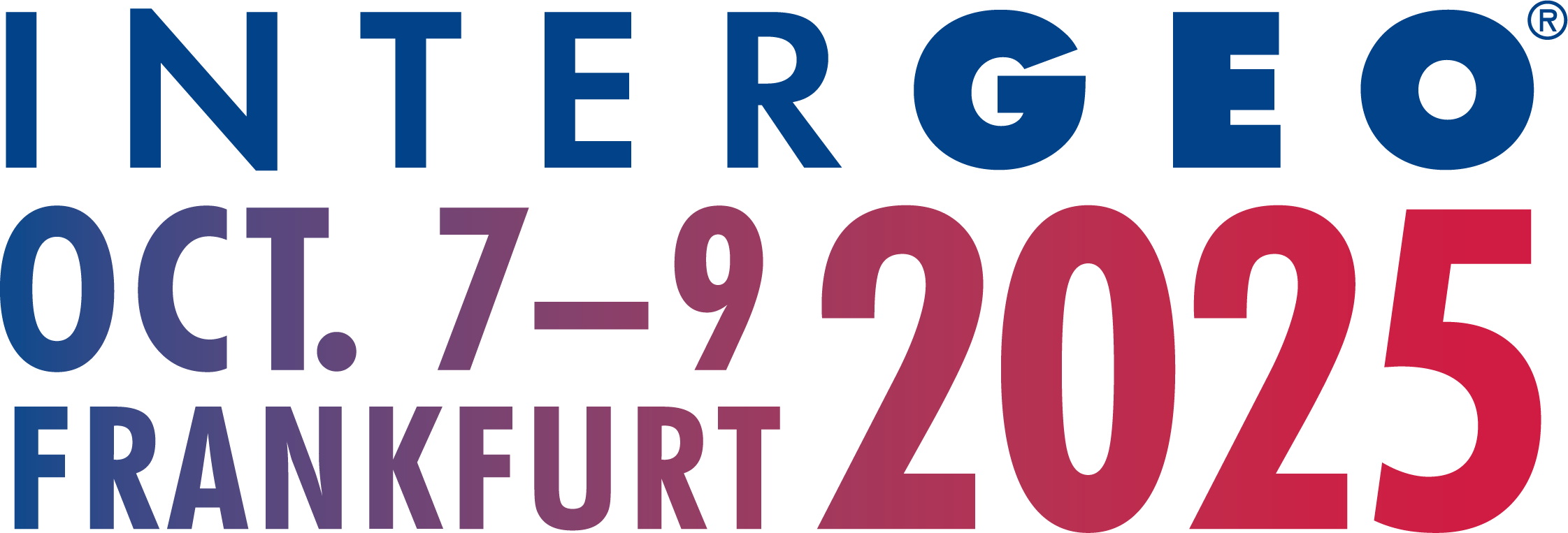
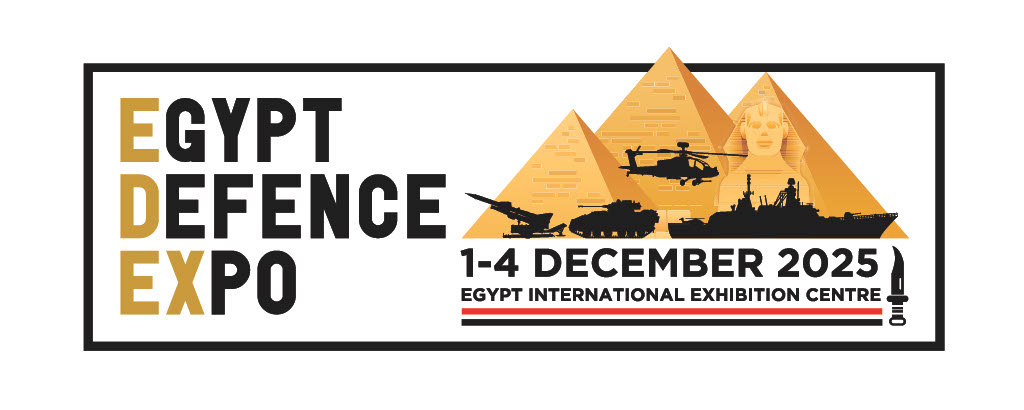
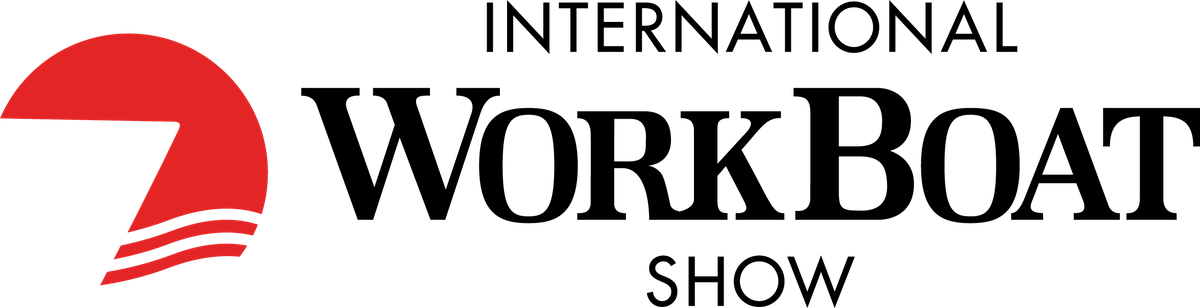
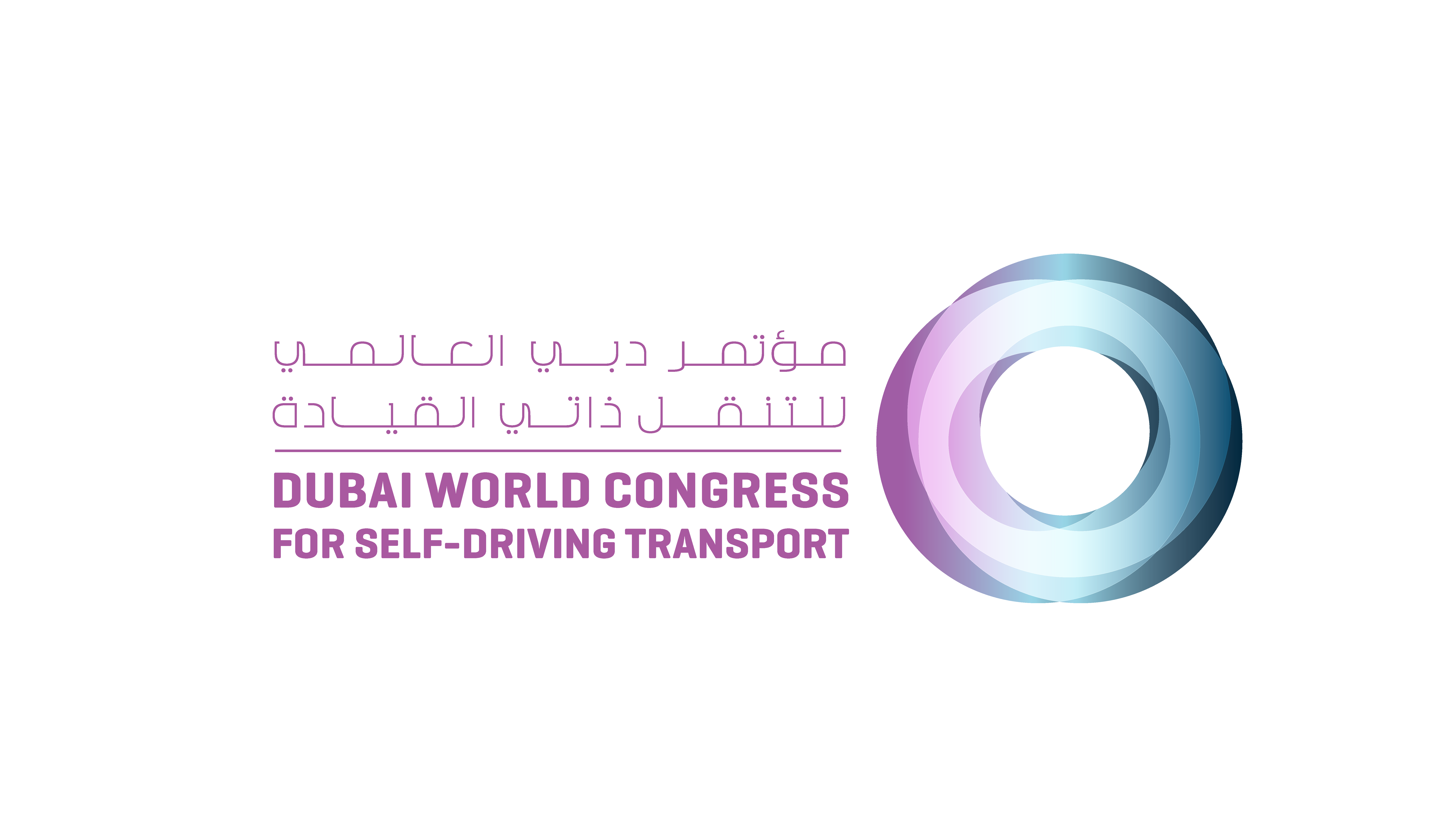
