RigiTech Eiger UAV
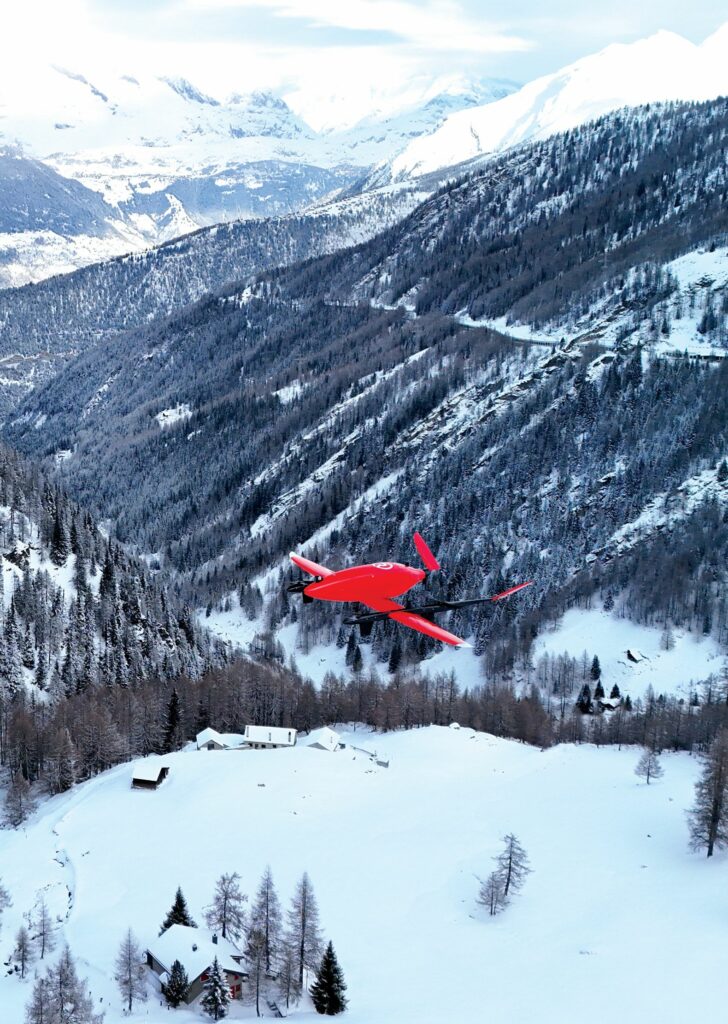
(All images courtesy of RigiTech)
The needs of the many
Making UAV logistics work takes more than just repurposing an off-the-shelf drone. It takes engineering a spacious UAV and a multi-dimensional cloud GCS portal from scratch. Rory Jackson interviews RigiTech to learn more
With the advent of uncrewed logistics solutions in air, and on land and sea, it pays to understand there are fundamental differences between what logistics operators need of their UAS, and what conventional UASs (designed most often for imaging-based work) bring to the table.
For one, buying an imaging UAV is easy and straightforward, whether mapping the spread of a wildfire, inspecting power lines, surveying for coastal erosion or simply photographing scenic views or videoing a wedding. Such UAVs can practically be bought off-the-shelf.
Logistics UAVs cannot be bought this way, however. Those designed specifically for logistics are nowhere near as prolific, and one may try to purchase and
re-engineer an imaging drone for logistics work, but the software inside and around it will remain unsuitable for logistics.
As Adam Klaptocz, CEO of Switzerland-based Rigi Technologies SA (RigiTech) says: “Almost all drone software, especially for aerial photography, is based on a principle of ‘One UAV, One Pilot’, so the GCS software in one handheld tablet connects to one multirotor, you do one of various mission profiles in your repertoire, and that’s it.
“Drone delivery, however, means flying the same route back and forth five days a week, and covering many different routes across an organisation. You can’t have one person monitoring every delivery drone. It just isn’t scalable.
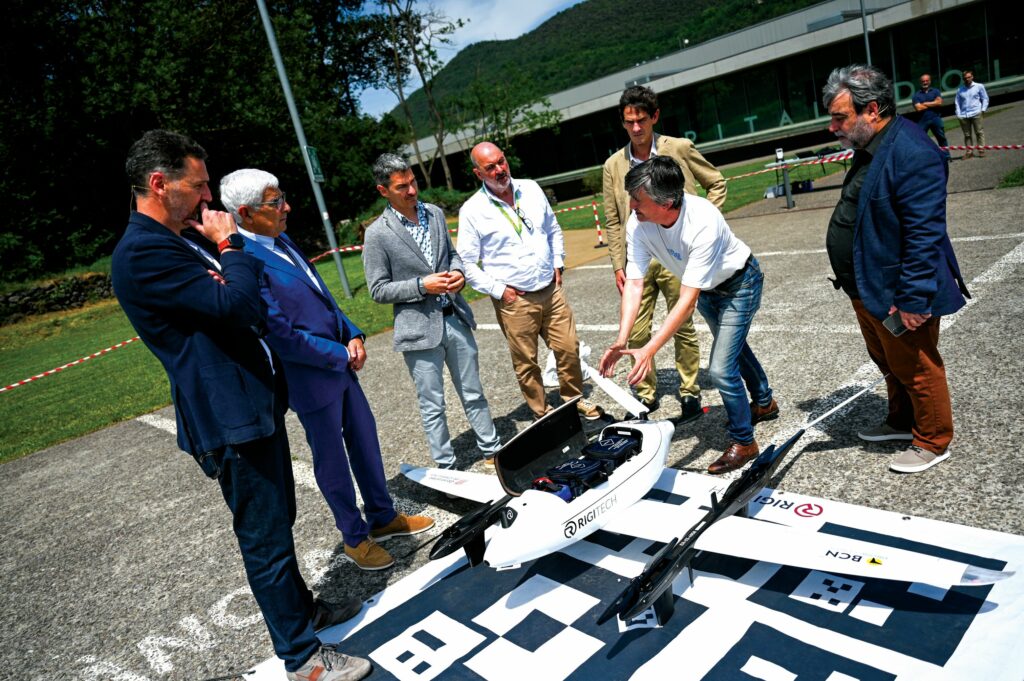
“You need something far, far more autonomous, such that entire fleets can deliver while monitored by a single supervisor, but also configured so multiple people can interact with the same UAV. A dispatcher fits one package after another into each UAV, the receiver takes it from their UAV, technicians on the ground maintain each returning UAV, and air traffic control [ATC] manages all the aircraft in the air. It’s many individuals, interacting with many drones.”
Addressing this ‘many-to-many’ problem and making drone delivery as straightforward as acquiring a Parrot or DJI toy are what motivated RigiTech to develop its UAS, starting in 2018 under the shadow of Mt. Rigi (hence the company name). That development work resulted not only in its Eiger UAV (also named for a Swiss mountain), but also its RigiCloud solution, encompassing the logistics operator’s GCS, UTM system, regulatory compliance wizard, and fleet management and maintenance portal.
RigiTech’s three co-founders pool copious experience from other UAV organisations, with Klaptocz having spent a long tenure in product engineering for Sensefly since its early days. He and now chief business officer David Rovira became introduced to uncrewed logistics through humanitarian work, during which they met Oriol López (now CTO, who was working for Médecins Sans Frontières).
López specialised in how UAVs could perform logistics for villages located in hard to reach areas. The three men subsequently led UAV experiments in Peru’s most jungled areas and quickly discovered that a lifesaving parcel, typically needing a six-hour riverboat journey to reach its patient, could be delivered by drone in 10 minutes.
Rapid development of a solution with the ideal infrastructure around it followed, including hiring its now lead cloud software architect, to achieve the cloud server-based concept for fleet management, flight clearances and so forth that could make UAV logistics practical, traceable and seamless.
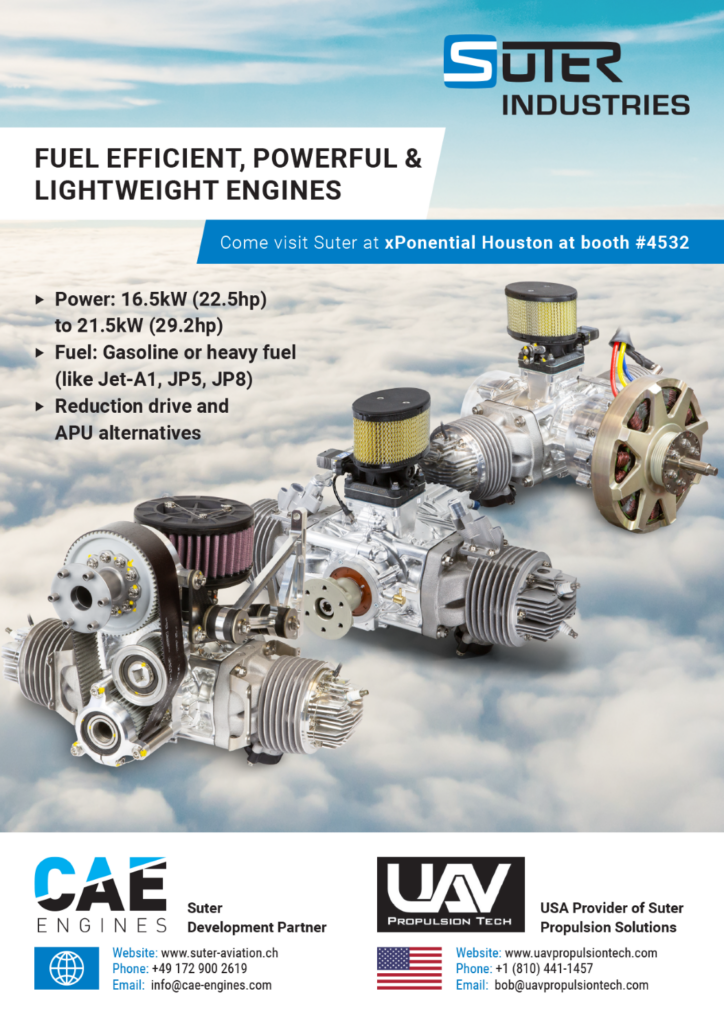
As well as critical software development over time, the co-founders (at their headquarters in Lausanne) focused on rapid iteration of the ideal aircraft, including getting to test flights as quickly as possible, to learn what engineering was needed to make a long-lasting UAV that could fly routes effectively.
“Within the first month of founding the company, we were test-flying an off-the-shelf VTOL drone in Tanzania, and it could carry 2 kg and fly 100 km,” Klaptocz says.
“Now, six years later, we have an aircraft that carries 3 kg, so very similar specs on the surface – specifically, a 104 kph cruising speed, 22 kg MTOW and 268 cm x 164 cm x 42 cm dimensions. But Eiger and that test drone are worlds apart in terms of safety, reliability and intelligence, not to mention how we can manage it.
“We did test flight programs in Italy, Portugal, Tanzania, and all sorts of places to refine the hardware and software, and it was in 2022 that we brought Eiger to market. We now ship the UAV worldwide, along with paperwork for flight clearances and training and CONOPS manuals.”
Volume versus weight
Designing the Eiger was largely a packaging exercise, fitting subsystems around a 15 litre empty space – the delivery drone’s cargo hold.
“When we talk about payload capacity in this industry, it almost always falls onto the metric of weight, which is something of a brute force number, derivative of motor and prop lifting power,” Klaptocz says.
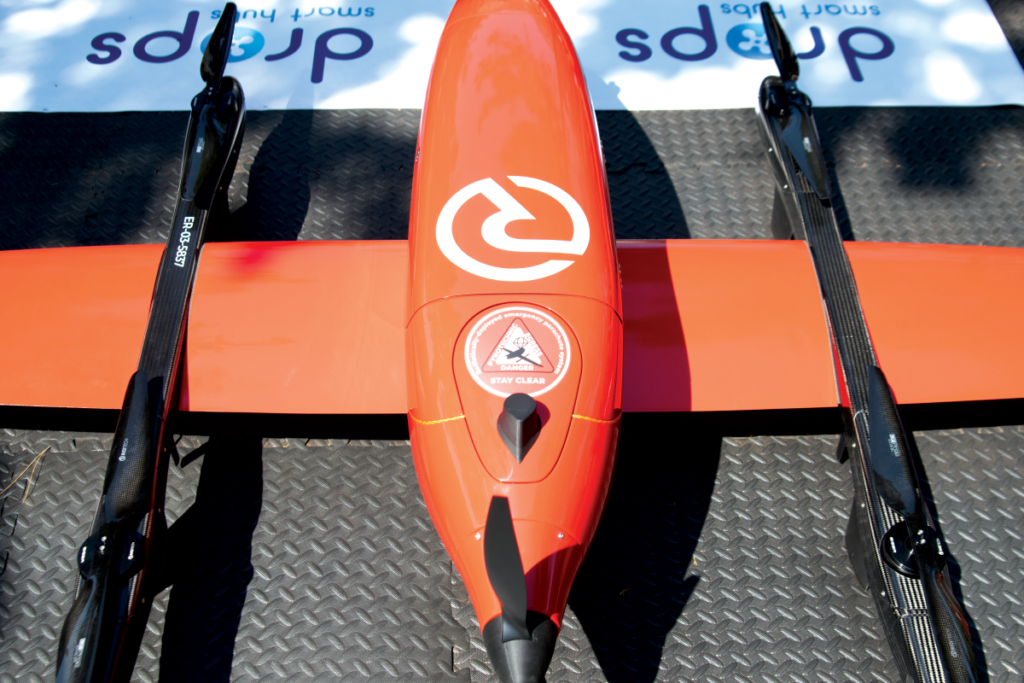
“But optimising for aerodynamic efficiency at a certain point gives you sleek, thin airframes. Those are fine for carrying a camera gimbal, because that’s a dense, concentrated ball of weight. But, for package delivery, what you really need is space: you don’t use Maseratis to deliver freight; you use vans and 18-wheel trucks. So payload volume has been much more important and practical for us than weight capacity.
“We’ve had customers demand 5-10 kg of capacity, but then when they actually put their blood vials or first aid kits into the drone, it’s more like 1-1.5 kg with space left over. When it comes to logistics, having 5 kg of payload capacity in a tiny area is not as good as 3 kg in a spacious area.”
While constraining around volume, RigiTech prioritised three targets. First (in no specific order), performance was key to ensuring a good cruising speed and range, such that within one hour of flight endurance, the UAV could fly its 3 kg payload out to 50 km and return along the same distance safely.
“We did a decent amount of aerodynamic studies and optimisations for weight, CoG and so on, so that the aircraft would fly well,” Klaptocz says. “It’s not the fastest or longest-endurance UAV out there, but people understand this solution works well and gets emergency packages to where they need to go, with a good but still safe speed.”
Second, safety was a vital consideration, particularly since Eiger flies BVLOS. To comply with the relevant standards, the aircraft’s subsystems include multiple means of detecting other aircraft and the aforementioned backup, parachute and FTS hardware to prove extra layers of safety to regulators.
“Fundamentally, our aircraft is big. It is almost 3 m wide and weighs 22 kg. If this UAV falls from the sky, you’re not just losing a med pack, you’re dropping 22 kg from the air and possibly sending it at around 100 kph,” Klaptocz notes.
“So, even if the regulations didn’t exist, we just do not want this aircraft falling from the air, so redundancy and safety are built-in to ensure escalating levels of reaction to different scales of failures, so even if it starts falling it does so in a safe and controlled way. If the airspeed sensor gets blocked, the computer system realises, compensates with GNSS inertial data and keeps flying steadily.
“If a wing breaks, which hasn’t happened yet, it switches to multicopter mode, and algorithms detect for a safe landing spot to guide it down.”
The third target was automation. As part of the many-to-many solution, both Eiger and RigiCloud integrate significant automatic behaviour, such that flights and deliveries do not break down due to one of the many persons involved across the stages of a given delivery failing to manually check a given box. The GCS interface is also designed to contain huge amounts of pertinent information, but also to ensure that what each person initially views in their main display panel is as simple as possible. Discussion of these behaviours and information are presented later in this feature.
Eyes on Eiger
The Eiger UAV is fully-electric and designed as a fixed-wing aircraft with a pusher propeller and quadrotor VTOL motors mounted on twin booms. This has been chosen as a practical and conventional airframe configuration, which would minimise the number of onboard moving parts to effectively just four servos (two wing ailerons and two ruddervators across the outboard vee-tail) for both safety and reliability.
The lion’s share of safety-critical subsystems sits at the back, where they are most protected in the highly unlikely event of a CFIT. Going from the pusher propellor forwards, one immediately finds a parachute concealed under a cap, and then a backup computer, which triggers the parachute’s rapid pyrotechnic deployment in emergency situations (RigiTech having determined that a spring-launched parachute would not grant a satisfactory speed of unfurling and descent slowdown).
“The backup computer provides further redundant control functions for safe emergency landings, and has its own backup battery as a short-run power source for itself and other subsystems, in case even the main battery should fail,” Klaptocz says.
The back of the UAV contains a secondary GNSS radio, and most importantly the autopilot computer, a downward-facing Lidar for autonomous precision landing and a flight termination system (FTS), which cuts power to the motors as a last-resort safety measure (FTSs are expected by many to become a requirement for certification in the near future, although the exact nature of their termination function may depend on the flight area and application).
Underneath the central payload bay are boards and cable management for the Eiger’s power distribution, as well as the aforementioned main battery. That is a 48 V, 1 kWh, 22,000 mAh Li-ion module which slots in and out of its compartment; that plus the hinged hatch covering the cargo hold make for largely tool-less maintenance and cargo loading between fights.
In the nose, RigiTech installs the ‘onboard computer’ (handling some alternate, non-continuous safety functions to the autopilot), comms and navigation systems, an FPV camera for regulatory compliance and a downward-facing camera for autonomous precision landing.
“The airframe is mostly composites, both carbon and fibreglass, but optimised for cost, as well as weight and structural strength, which results in there also being several plastic, rubber and metal parts,” Klaptocz says.
“Making an integrated system means being sensible about what materials you use in each place, both for the sake of the UAV and your manufacturing processes. There’s some structural foams in the UAV as well for extra weight-saving, but what you see from the outside is pretty much all composites.”
Software ecosystems
The UAV’s three interconnected computers may serve different functions during standard operations, but for emergency situations they are programmed to back each other up, briefly taking over and performing similar software functions as each other. Comms and navigation sources are similarly redundant. If all else fails, a parachute with a dedicated computer and power source deploys to slow and control a fall towards the ground.
“The need for safety is why we have waves of backups to ensure four or five things kick in before an issue becomes truly serious. It’s also why we have a three-month continuous software cycle, spending two months investigating and developing new algorithms to detect new failures, followed by one month of testing to refine it, so we don’t add any bugs to the system,” Klaptocz says.
RigiTech’s software encompasses several stacks and codebases across different platforms. Eiger’s autopilot, for instance, is a low-level microcontroller for flight-critical functions, largely programmed in C++. Its backup computer runs a separate codebase written from scratch (also in C++), and the onboard computer is Linux-based and runs the higher-level, non-critical (but still important) functions, having been programmed via a combination of C++, Python and other languages.
“Then there’s a cloud system, which is server-based and hence uses a lot of server-based technologies, with its back end based on Node.js and a lot of Javascript-type coding,” Klaptocz says.
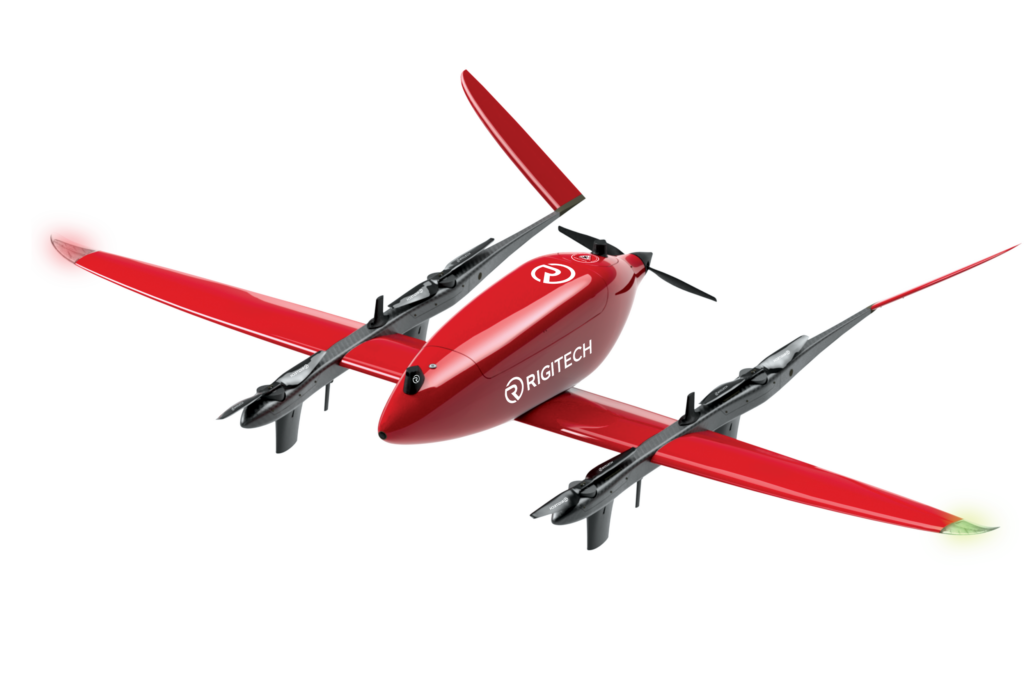
Hence, the company’s software solutions bridge together different programming languages and concepts from embedded code that runs standalone on singular processors to embedded Linux architectures, which run multiple interconnected algorithms in multiple languages, and its cloud, which runs varied services on different servers and architectures, linked by different infrastructures including (but not limited to) Google Cloud.
“Today’s UAV software is more or less ‘here’s a .exe, you put it on your autopilot, and off you go’. Our software is a bit more complex, to the point that when you update one system it runs updates on other systems, and all of that has to work together, and ensure continued compliance and safety across UAVs and deliveries,” Klaptocz says.
Connected couriers
To ensure the software can both guide and remotely track the UAVs, each Eiger integrates two GNSS receivers, the nose-mounted module’s antenna (nicknamed the rhino horn by RigiTech for its protruding, dark shape) that integrates an airspeed sensor for added telemetry and precision localisation aiding.
To keep the UAVs at a safe distance from other aircraft, the navigation hardware suite integrates traffic awareness systems, which include transponders for ADS-B In (with an option for a TSO-certified ADS-B Out), FLARM and remote ID, with the software for intelligently processing their data running in the frontal onboard computer.
“We have got four different comm links, including a main 4G modem, a backup 4G in the rear, one satellite modem and a 2.4 GHz radio, useful in the context of drone ports – which can co-ordinate three or four drones deploying simultaneously from the same place – plus a ground-based radio system and two mobile network systems connected to two different computers, so the loss of one data link never takes down a cascading network of other links,” Klaptocz explains.
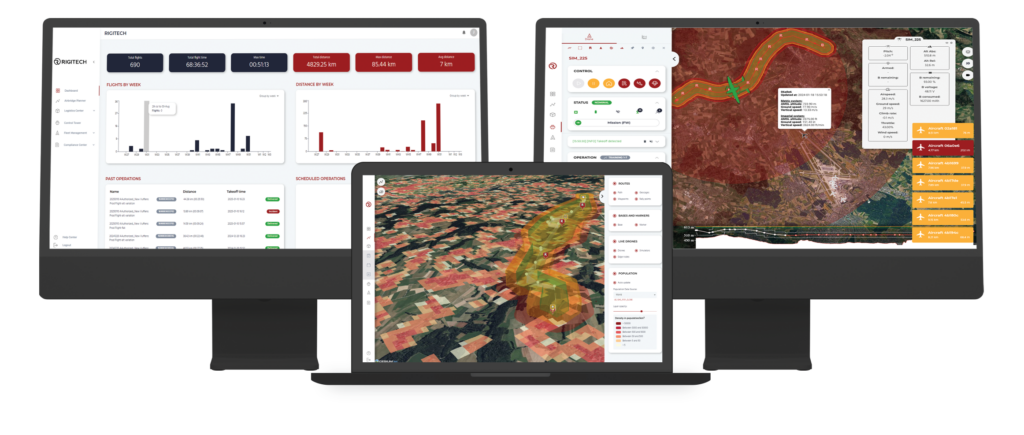
“All those modems, transponders and GNSSs mean we have 14 antennas distributed across each aircraft: four for comms protruding down from each of the two VTOL motor booms, three for GNSS up from the fuselage – one for the transponder – one for remote ID, and one for adding external modules.
“That may sound ridiculous, but connectivity and positioning are critical. Having that many antennas, precisely distanced from each other across the airframe, means that when Eiger is on the ground, in the air, tilted left, right, up or down, there’s no shadowing or polarisation losses keeping the many managers and technicians involved from tracking the drone when they need to.”
Extensive computer simulations based on first principles of RF engineering informed initial antenna placements, including correct shielding and ground planes across the airframe, with third-party laboratories providing further insights (via anechoic chamber, etc) for optimisations in the final UAV designs.
Buzzing the tower
Navigation, transponder and ATC data are delivered through these data links on the UAVs and the ground, and displayed on a map in a Control Tower panel in the GCS dashboard (which, being native to the cloud, contains cloud-hosted panels for pre-flight checklists and part maintenance schedules, remotely accessible by individuals with the appropriate logins and permissions).
“That means dispatchers loading packages on the ground can confirm they’ve done visual checks, the person in the operating centre can confirm they’ve checked for safe airspace and weather conditions, and other checks of that nature can happen, before the remote operator activates the launch sequence,” Klaptocz says.
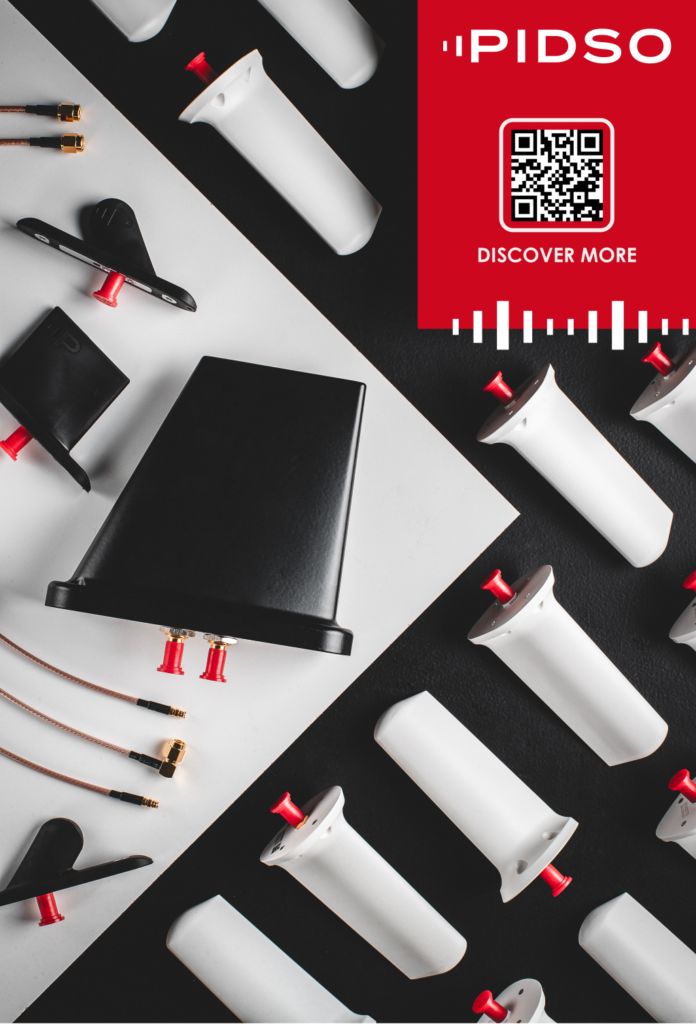
“Our traffic data includes real-time addition and pinging of any aircraft’s ADS-B, FLARM or remote ID data onto the display map. Receiving that data and sending it to the cloud is somewhat easy, but a lot of work went into the UAV and into the cloud to make sure we could display the data in a useful, ATC-inspired way that’s cleaned-up for visual ‘noise’. We engineered for interfacing with multiple air traffic data providers and arbitrating between them, so each aircraft is displayed with one definite position, based on multiple confirmatory sources.”
For added analysis, the Control Tower map can be toggled to show distances between the Eigers and non-controlled aircraft (calculated in real time by a function in the RigiCloud), and tracks of non-controlled aircrafts’ last reported positions over the prior 30 seconds, to then make estimations of whether those other air vehicles pose any reason for concern, with automated warnings and other responses within the software based on ASTM standards for detect-and-avoid.
Furthermore, since all operator software lives on the cloud and is permanently connected to the internet, RigiTech has developed an API, which, in addition to enabling map data, ATC information, weather reports and more to feed into RigiCloud, allows the user to export data to others, such as their own fleet-management solution (should they wish to continue using it), other UTM solutions or authorities, or potential partners and customers.
Autonomy and automation
Rather than all of RigiTech’s software being a complex ecosystem of separate modules, the overall logistics solution involves intricate interplay between the cloud, GCS and UAV portions of the company’s UAS offering.
For instance, the alert and warning displays for when non-controlled aircraft get too close are largely in the cloud, but the algorithms triggering the UAV to take regulation-compliant avoidance manoeuvres (including route recalculations) are installed in the onboard computer.
“That’s very important, because it’s fundamentally the UAV that needs to get out of the way, and we never want it to not do the avoidance behaviours because of a dropped data link or faulty modem,” Klaptocz says.
“But you can see why we need to control and define both the cloud intelligence and the drone intelligence, as well as the connectivity systems and the embedded computers, to create a solution where all the alerts and avoidances and so on mesh together as part of a sliding scale. Some software lives on the drone, some on the cloud, but all of it follows our plan. Anyone who makes just one or the other is going to hit a wall at some point when trying to do uncrewed logistics fleets.”
The UAV flies waypoints stored internally (whether preprogrammed briefly or long before a given flight), adhering to numerous rules, geocages, and multiple layers of warnings and corrections in the event of deviations. For RigiTech’s systems in Europe, each BVLOS route must be approved under the Specific Operations Risk Assessment (SORA) methodology, which involves examining each route, kilometre by kilometre, to evaluate the airspace to be traversed, the population to be flown over and other factors.
“Based on the ensuing risk level, each route falls into a SORA class, and if it’s too high, you can’t fly, which then entails going around certain airspaces or populated areas,” Klaptocz says. “So, designing a 50 km delivery route is actually quite complicated. It can take weeks, even months – and there’s consultants who will charge tens of thousands of euros to design a SORA for you – but to save our customers that time and money, we’ve built an auto-planning tool into RigiCloud.”
The auto-planning tool stores considerable SORA-relevant data, including that on worldwide terrain to account for elevation and CFIT risks, worldwide airspace-segmentation data, including airports, and global population data (including specific population distribution data for certain countries, such as Switzerland, France and Luxembourg).
This data is ingested by the tool’s auto-planning algorithm, as needed, to plan a route between pairs of specified takeoff and landing points. The population data toggle is programmed so the end-user can specify a maximum number or concentration of people that their central aviation authority permits sub-25 kg UAVs to fly over.
“That automates the route generation, avoiding highly populated places, whether the user’s fleets can fly over a mountain or are required to fly around it, and it also automates the geocage around your route, basically giving you your whole SORA in one click, ready for submission to EASA, instead of taking six months of work,” Klaptocz says.
Safety landings
RigiTech’s autonomy algorithms also define exact equations for which paths to follow to avoid mid-air collisions and make course corrections. Returns to base are generated onboard the UAV, such that no-one needs to manually select a new chain of waypoints, or open a guidebook on air traffic or public safety to determine where it cannot go on its new path.
Those algorithms have been optimised over time to account for edge cases, such as calculating the route needed if (or when) the operator changes their mind mid-return and requests that the UAV reinitiate its mission.
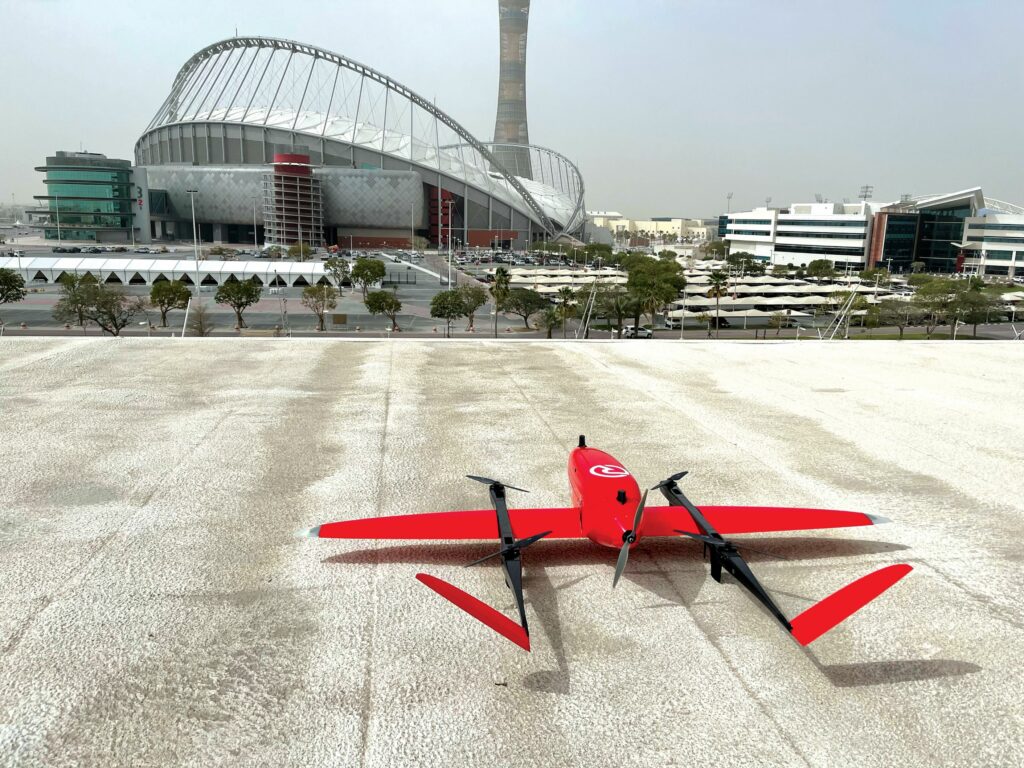
“If the fleet manager needs a UAV to return home, they just click a button on the interface and Eiger plots a regulation-compliant return path,” Klaptocz says. “Yesterday, we released a battery SoC estimation and prediction algorithm, so if it determines that it just won’t have the battery energy to return home, it selects a prudent safety landing spot from a predefined map of them and engages in an autonomous landing onto that.
“All of that together was key to making sure no one operator needs to look at any one UAV to the exclusion of others. Our overview, whether you’re selecting a map showing their geographical spread, or a table of them listed with real-time health parameters, allows you to see at least four or five Eiger UAVs at once, and if one has an issue, a prescribed safety behaviour kicks in, limiting the need for fleet managers to step in.”
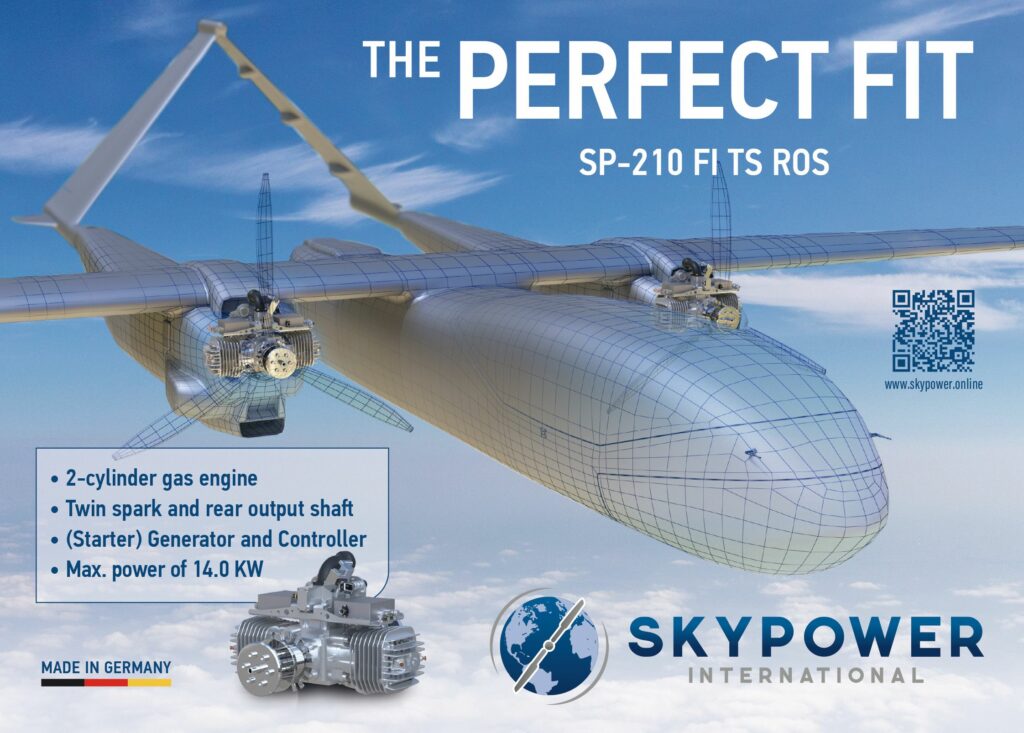
The safety landing paths and points (called ‘rally points’ internally) are specified by operators, selected along the route after it has been generated, with open fields and parking lots often being acceptable emergency landing places. Several must be chosen at regular distances, given that one of the riskiest causes for an emergency landing is the loss of fixed-wing flight, and switching to multicopter mode entails a significantly shorter flight time, given the power needed by the four lift motors.
The user must define their autonomous safety behaviour – how the UAV will react to different faults or hazards. For instance, if a strong weather pattern is detected (as can be done via ADS-B In), it can choose to return home, land at a rally point or continue its mission.
“When it comes to the landing itself, a lot of people say they do vision- or Lidar-based landing, but if you want reliable landing, which lands 100% of the time and not just 80-90% of the time, that’s actually a huge amount of work,” Klaptocz notes. “We wrote all of our own vision- and Lidar-based landing algorithms from scratch, such that our system uses a dozen different markers to triangulate its descent robustly, regardless of any situation-specific variables that might throw off less well-engineered landing software.”
SAIL away
RigiTech continues to develop Eiger’s place within the SORA framework. As of writing, the UAV is classed under Specific Assurance Integrity Level (SAIL) 2, enabling it to fly low-risk routes, as defined by the EU, although the company is working on gaining clearances to fly SAIL 3 medium-risk routes.
“We’ve measured the MTBF of all our critical components, and our engineering is definitely compatible with SAIL 3. We’re working with our regulator in Switzerland and with those of our clients, so that in the coming months we will have a SAIL 3 update package for Eiger that all of our customers will be able to use, and that’ll include that MTBF data,” Kaptocz says.
In addition to expanding into new markets (including its first few launch customers in the US, to be announced soon), RigiTech is pursuing its ultimate goal of more automation and less hands-on involvement by humans.
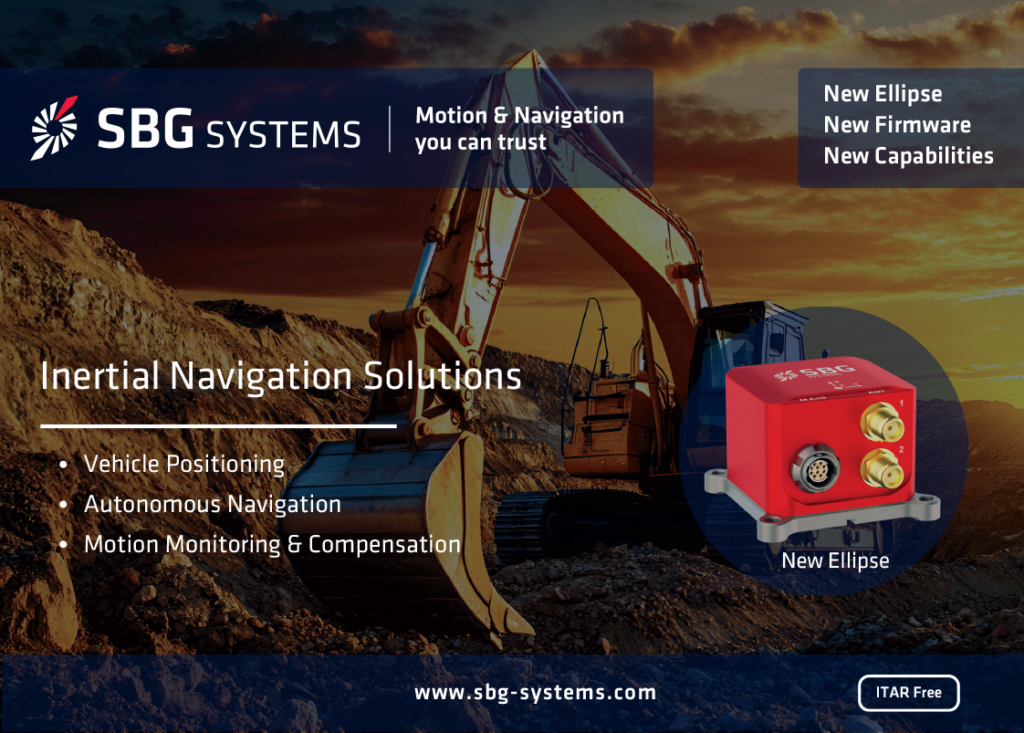
The company notes that some of its customers no longer even touch the drone on a day-to-day basis. Hospitals and clinics load and unload their Eigers, and perform battery replacements.
“There are ways to further automate the ground-related aspects of the UAV, such as placing camera arms around some landing points for remote – and maybe even machine-automated – visual checks, because removing the need for direct human involvement is the essential business case by which logistics can scale,” Klaptocz says. “We will achieve a lot of that through software, as well as a few new hardware products we’ve got cooking in our pipeline.”
Key specifications
Eiger
VTOL-transitioning
Fixed-wing/quadrotor hybrid
Battery-electric
Cloud-based GCS
Dimensions: 268 cm x 164 cm x 42 cm
MTOW: 22 kg
Payload weight capacity: 3 kg
Payload volume capacity: 15 L (45 cm x 16 cm x 21 cm)
Cruising speed: 104 kph
Maximum gust resistance: 15 m/s
Maximum flight range: 100 km (80 km with max payload)
Maximum endurance: 59 mins
Maximum altitude: 3000 m AMSL
UPCOMING EVENTS
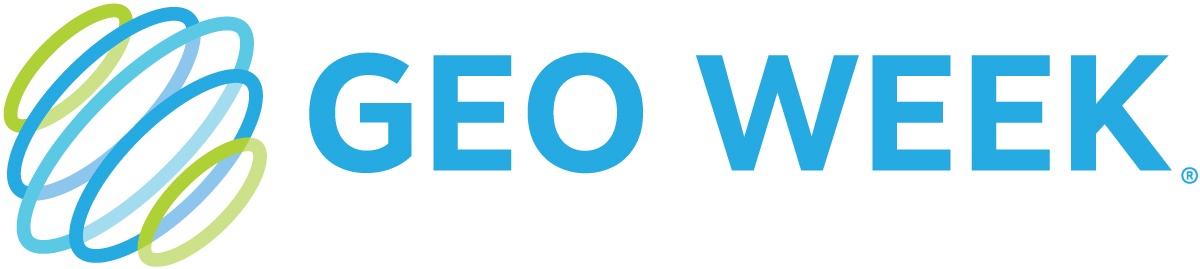
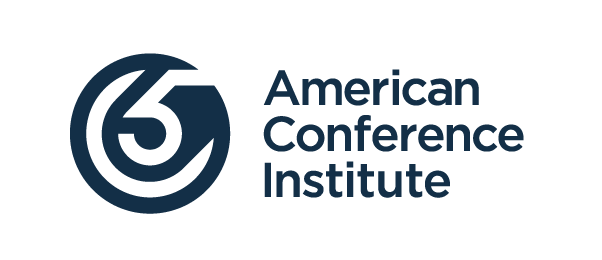
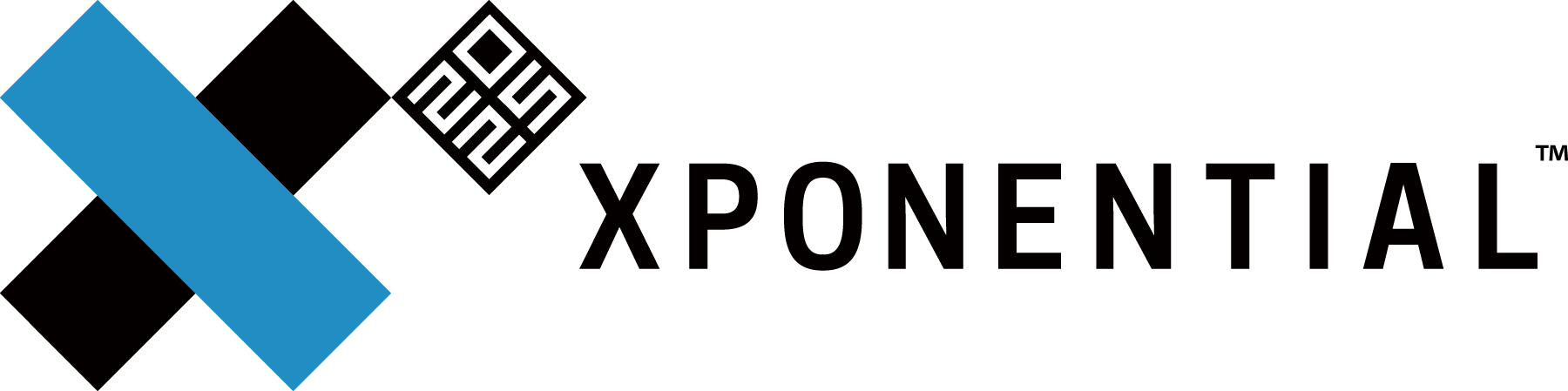
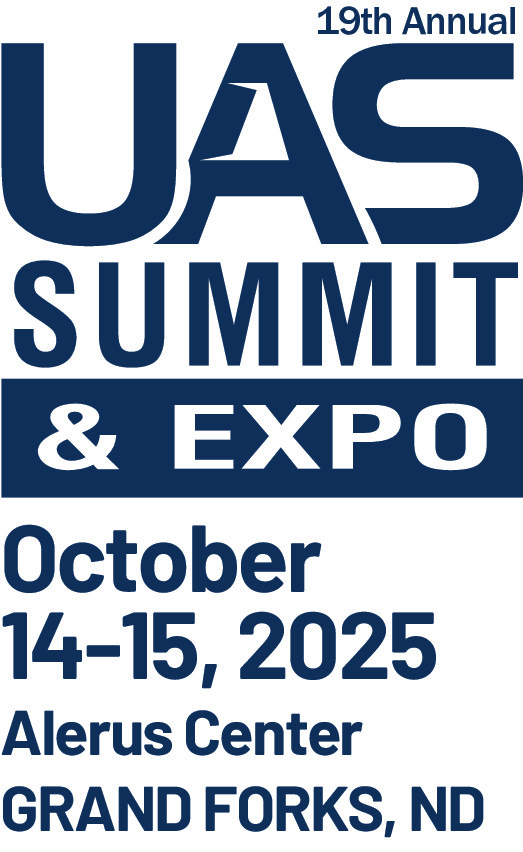
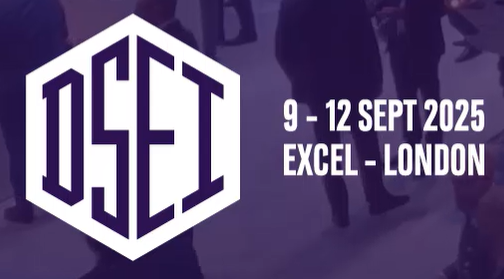
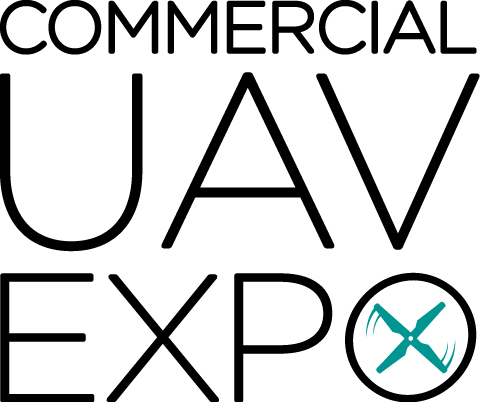
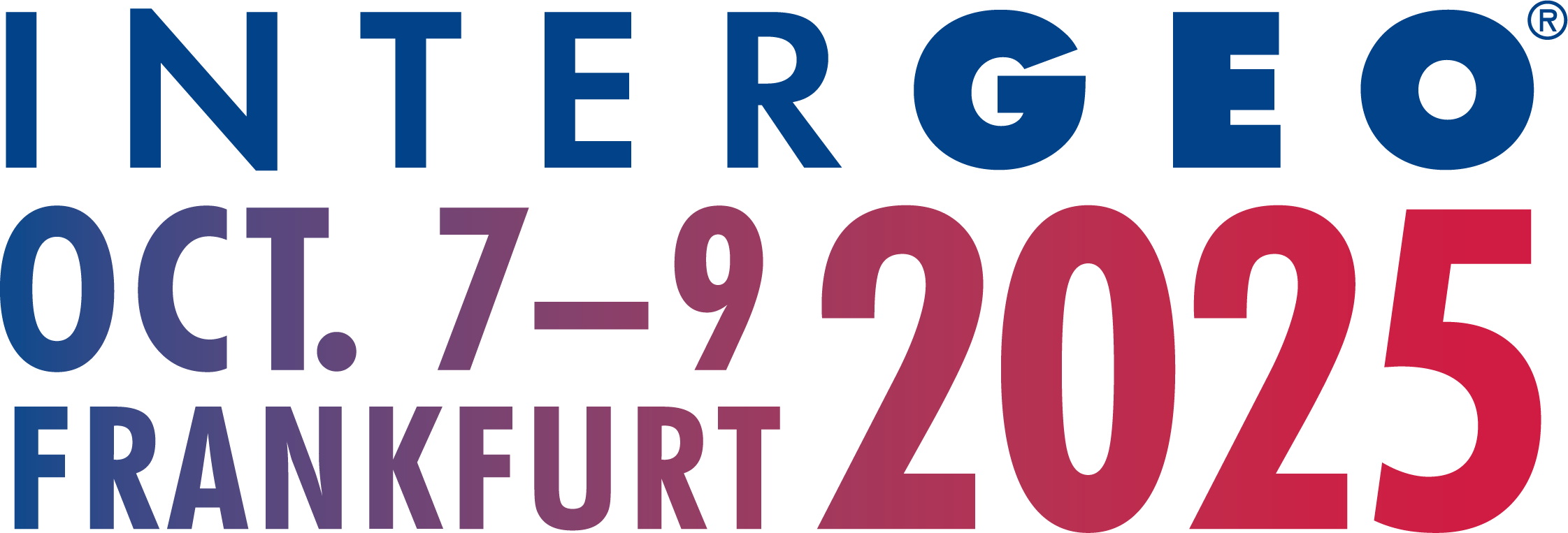
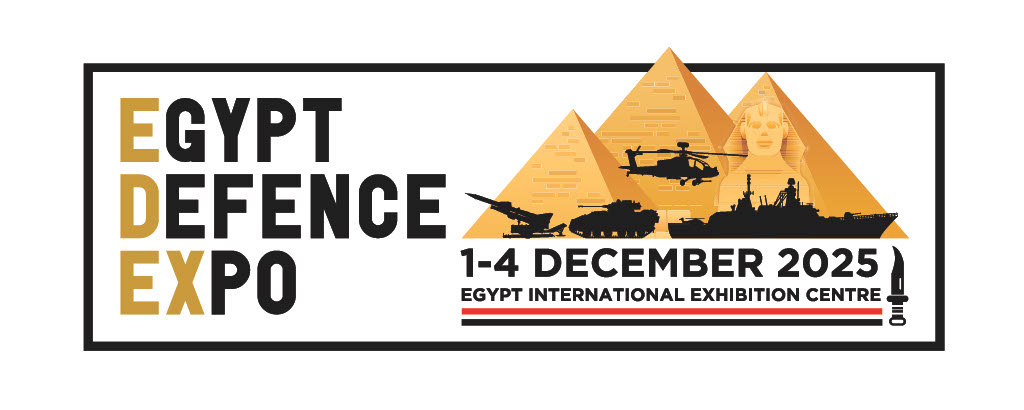
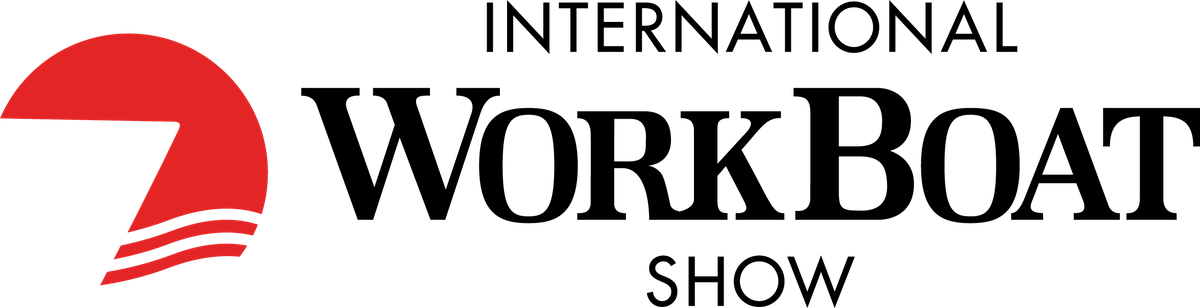
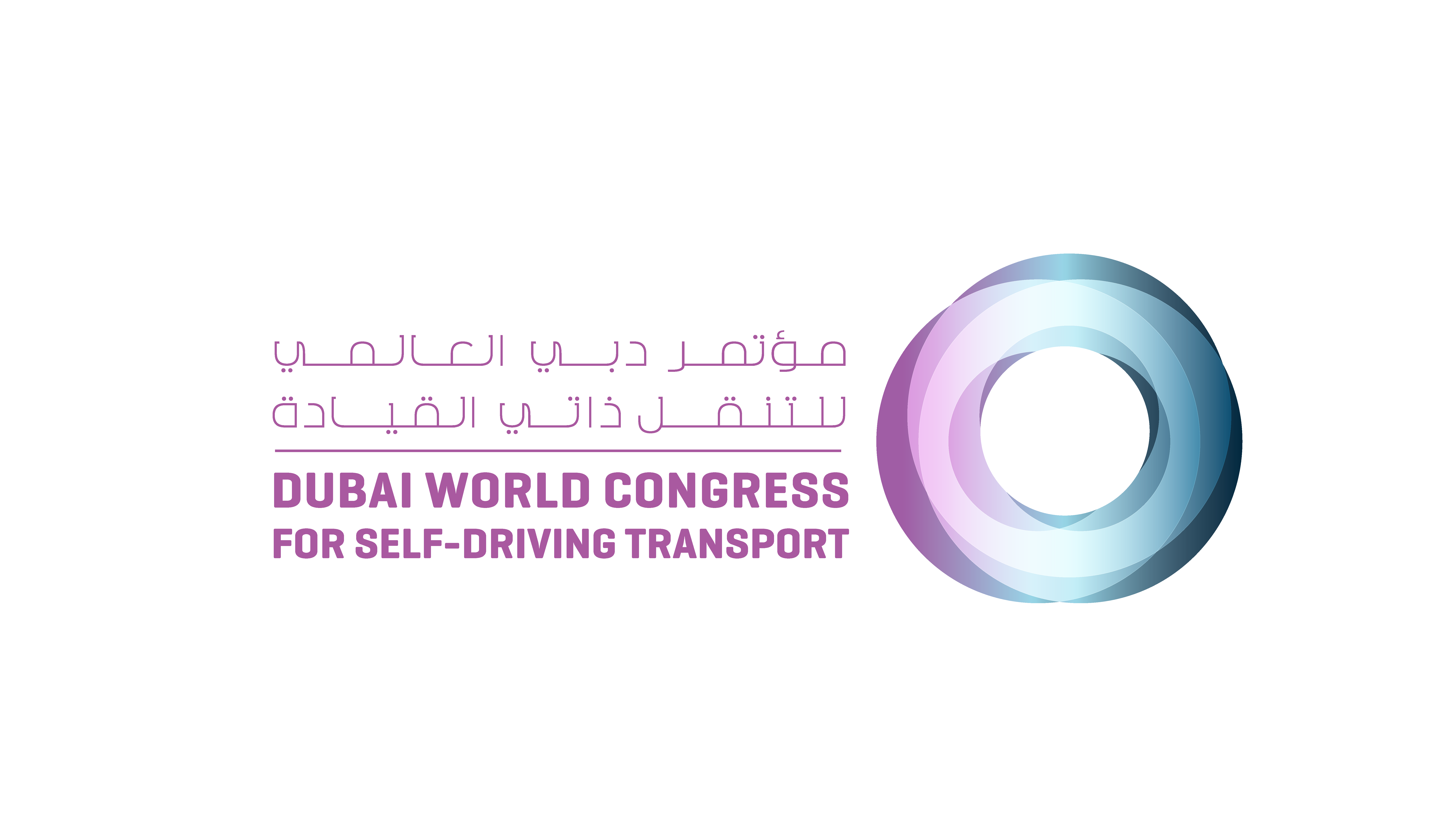
