UMEX
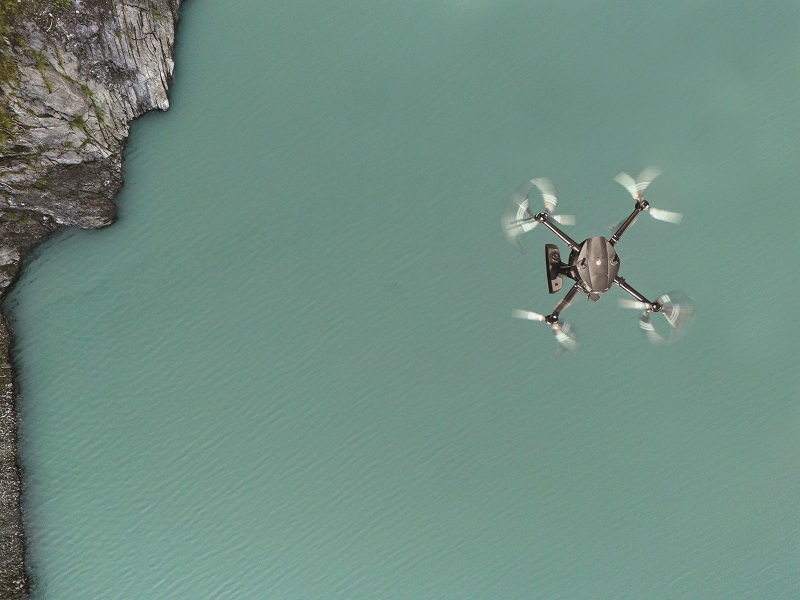
Peter Donaldson presents an in-depth report on the range of defence-grade uncrewed systems technologies on display
The sixth edition of the Unmanned Systems Exhibition (UMEX) and Simulation and Training Exhibition (SIMTEX), and the conference accompanying them, ran on January 22-25 at the Abu Dhabi National Exhibition Centre. The largest version of the expo yet, UMEX featured a range of new products and updates for defence-grade uncrewed systems operations, a selection of which are discussed here.
We last featured Xer Technologies’ X8 UAV in our 44th issue (June/July 2022), and the company exhibited the hybrid-electric multirotor at UMEX for applications such as de-mining operations and public safety, through the integration of high-end electro-optical/infra-red (EO/IR) sensors, ground-penetrating radar (GPR) or radioactivity detection and other sniffer-type sensors.
“Xer has successfully integrated the Sierra-Olympia Ventus OGI methane gas-detection sensor, and the X8 flies such payloads on a regular basis for customers in Australia, Southeast Asia, Europe and North America,” said Kristofer Skantze of Xer Technologies.
“The Xer X8 is capable of flying 2.5 hours with a 3 kg payload, or with 7 kg for one hour. It has been tested with payloads in -20 C conditions, as well as in 40 C and heavy winds.”
Xer Technologies developed most of the key parts of the UAV in-house, including some of the engine parts, its engine monitoring and control electronics, the power-management unit (PMU), the control software and the heating system to enable flights in very cold weather, with extensive tests and optimisations of a cooling system to enable high-temperature flights.
Its software engineers focused on designing its GCS software to be able to remotely monitor engine data, and on creating flight analytical software and simulation software for pilots to train on.
Volz has combined its proven, proprietary, 11-bit CAN protocol with the widely used DroneCAN (formally known as UAVCAN), integrating the latter into the firmware of its DA 15-N-CAN servo actuator. “The two CAN protocols do not interfere with each other in the servo, as one is using the 11-bit CAN mode and the other is using the 29-bit CAN mode,” explained Volz’s Mark Juhrig.
“This allows customers to now use the DA 15-N with any of several flight-control computers and autopilots on the market compatible with the DroneCAN GUI, especially the open-source ones.
“That means the customer can modify actuator parameters – for instance, the control-loop gains – through the DroneCAN-compatible autopilot, and also through any CAN interface supported by the DroneCAN GUI.”
The company plans to add DroneCAN to the solutions across its actuator portfolio in the future, commenting that several other Volz actuators’ electronics are currently undergoing redesigns to enable integration of CAN interfaces.
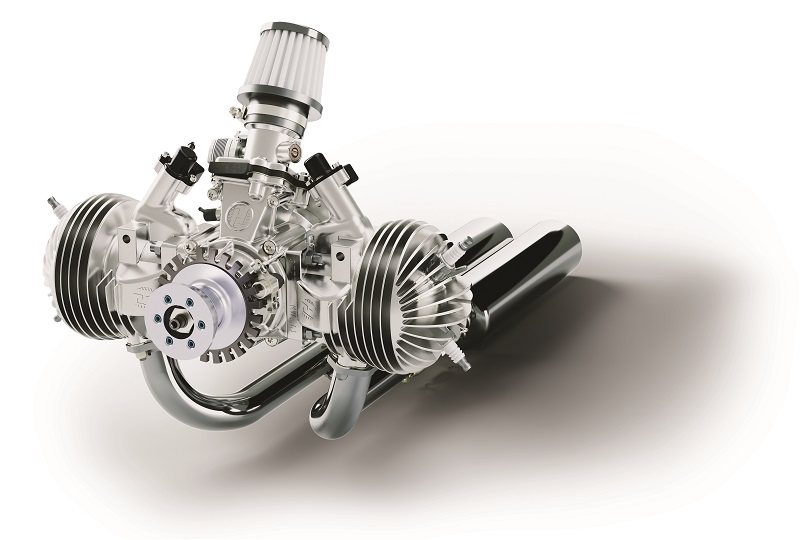
Hirth continues to develop its 4202 heavy-fuel engine – an 11.5 kg, two-stroke, two-cylinder boxer, air-cooled and spark-ignited with dual ignition plugs. Each cylinder has a 54 mm bore and a 40 mm stroke and the engine produces a maximum power output of 11 kW.
“The 4202 now integrates our new proprietary CWI [Continuous Wave Injection] cylinder technology, which we’ve developed for running efficiently on kerosene,” said Peter Lietz at Hirth.
Development of the new cylinder took about 3.5 years, particularly to optimise for kerosene combustion. FAR 33 tests on the 4202 are complete, as are FAR 33 tests for the petrol version, Hirth’s 4201 engine (FAR33, EASA CS-E and EASA Part 21 being the main standards guiding the engine’s development and validation).
“We are also working on simulations using test and operation data from this and our other engines to improve all our products in terms of performance and fuel consumption,” Lietz said.
Key simulation tools used by Hirth include GT Power for CFD and FEM analysis, and 3DX from Dassault for mechanical design.
Going forward, Hirth is evaluating making further heavy-fuel versions of its current and future engine portfolio, particularly in its 20-30 hp power range, as well as at 50 hp. It is also working on a new ECU design to meet future UAV certification guidelines, which are being shaped.
“Power improvements and cleaner, more efficient combustion are additional big goals for 2024,” Lietz noted. “New materials and production processes will support these, and make our engines lighter, and new fuels such as SAFs [sustainable aviation fuel] will merit rounds of testing and verification to see how they can meet future market demands.”
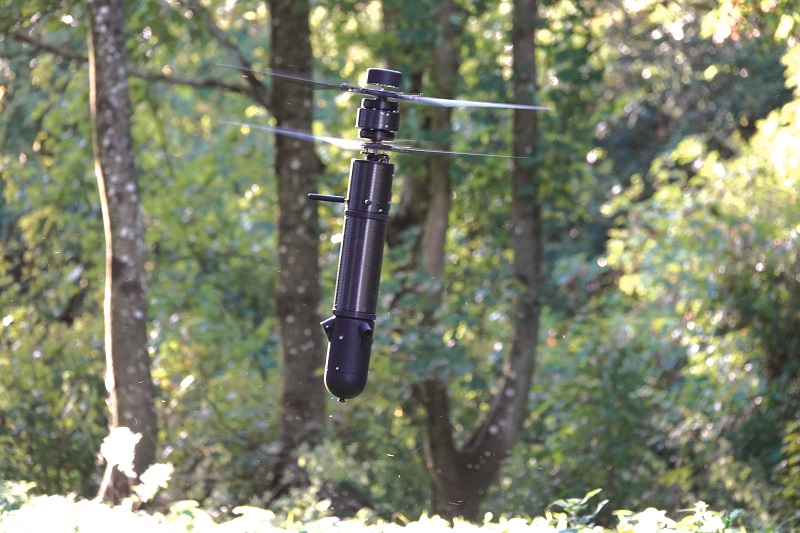
Overwatch Group showcased several kinetic and non-kinetic capability solutions, including the newestUAV-specific kinetic payloads from its Overwatch Energetics division.
“The tendency is for operational technicians to repurpose an existing munition, such as a mortar or grenade, and roughly hitch it onto a UAV for dropping or single-use delivery. We are focused on developing very specific munition classes for rapid and reliable integration onto any uncrewed system – aerial, ground or maritime – with arming and safety sequences benchmarked to comply with applicable NATO STANAGs,” said Overwatch Group’s James Hayward.
“While some munitions need rifling or high kinetic energy from a barrel to arm them, you rarely get that luxury on a UAV. Our solutions adopt a mechanical and electronic interface, providing data and power to the warhead. It can then either be decoupled and dropped, or the whole system can descend as a sacrificial unit for a tactical precision strike.”
Overwatch Energetics’ focus on solutions up to 2 kg has been informed by the payload capacities of those tactical UAVs currently in operation, but they are scalable for larger platforms.
In addition to various weight classes, four core munition effects are offered. One is an anti-armour payload with a shaped charge for penetrating rolled, homogeneous armour that is thicker than 180 mm. Another is a high-explosive fragmentation product with a 30 m-diameter effective area. The third is an anti-structure system that creates overpressure to demolish buildings, and the fourth is a multi-use inert round for cost-effective training missions.
The group also displayed and discussed its next generation of uncrewed systems being developed by its aerospace division, which it plans to reveal more on as the year progresses.
UAV Tech Private Ltd showcased its M165 Logistics Drone, designed for defence, emergency response or commercial delivery end-users seeking safe and timely aerial transport of payloads weighing up to 30 kg across long distances and at high altitudes.
“The synergy between the M165’s three lifting surfaces and hybrid powertrain, consisting of octa-quad, X8-configured electric motors for take-off and landing – as well as a 29 hp internal combustion engine for forward flight – ensures the M165 can efficiently cover up to 300 km with 30 kg payloads,” said Moukthik Kiran Reddy of UAV Tech Private Ltd.
The India-based manufacturer has focused its development on advanced materials to enable reliable performance across difficult environments, and a modular design for integration of different sensors and payloads.
Its autonomous navigation and in-flight obstacle avoidance are powered by an embedded sensor-fusion algorithm stack that can use GNSS, Lidar and cameras for real-time situational awareness.
“Presently, in its advanced testing stages, the M165 is on track for full commercial release by the close of 2024,” said Reddy.
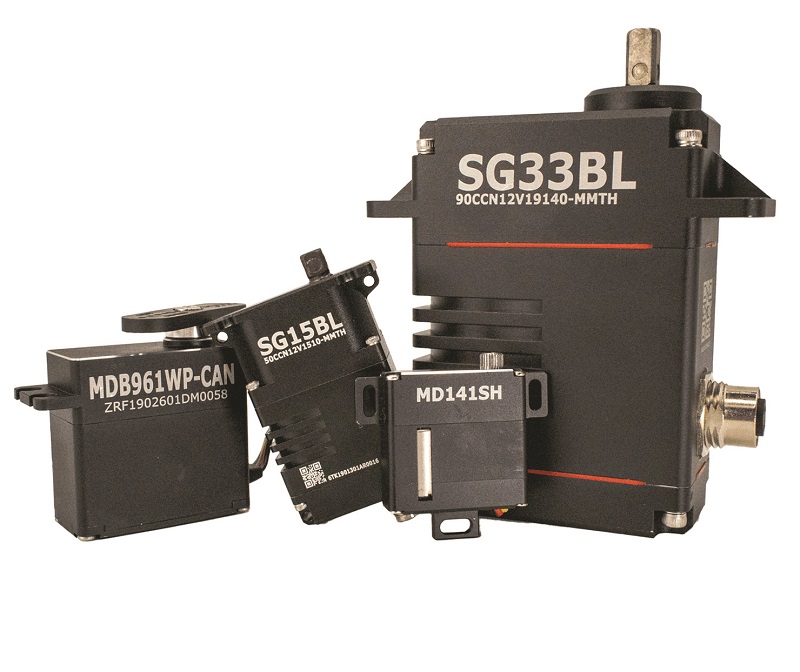
Hitec spoke with us about updates to its SG Series of actuators, including its SG10BL, SG15BL and SG20BL servos, which now have hardened steel gears and hardened aluminium cases, giving them greater durability and longer life.
“Greater strength in the gears equates to slower wear in the gear train, slowing the development of gear slop, and maintaining the level of positional accuracy and repeatability over the service life of the servo,” said Hitec’s Shawn Spiker.
“A stronger case enables greater resistance to internal and external forces upon the servo; that equals less motor stress for extended service life of the brushless motor in the servo. Both improvements lend to a longer lifespan for the servo.”
Hitec reported that its investment in equipment over the past five years has increased its manufacturing capacity, and supplying servos with hardened components has improved several processes, feeding into better r&d and production results.
“Among these are material inspection and testing equipment at the mass production level. Hitec has acquired the machinery necessary to test the tolerances and hardness of every gear-train component prior to assembly in our SG Series servos,” Spiker noted.
“The specified level of hardness, absence of material defects, and correct tolerance for a smooth and tight gear mesh is ensured prior to assembly.”
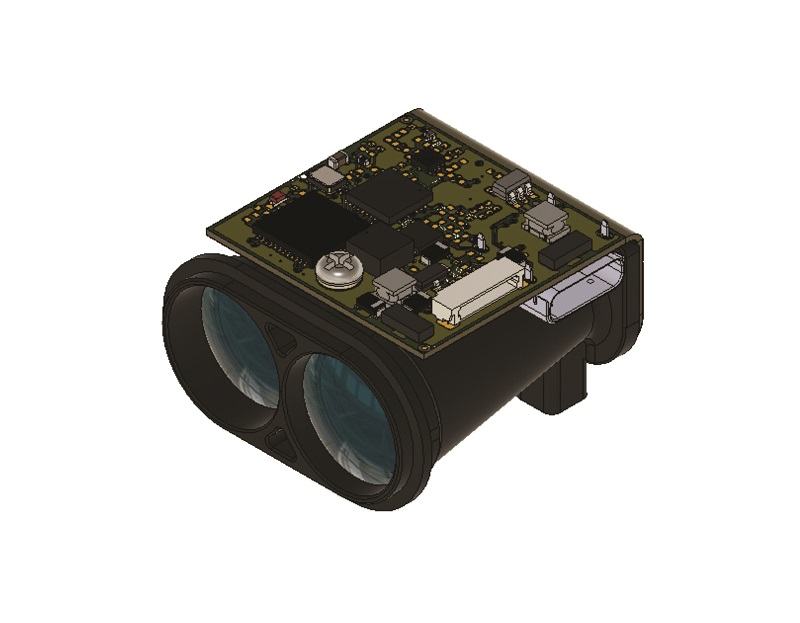
We came upon LightWare walking around the event and learned that it is developing a line of long-range Lidars tailored for integration with gimbals, to include ranging capabilities in camera systems for intelligence, surveillance and reconnaissance (ISR) applications.
“The upcoming GRF-series will employ 905 Nm technology and comprise three variants: a 250 m, a 500 m and a 1000 m solution,” said Nadia Nilsen of LightWare.
The GRF-series is designed to be lightweight and compact, like LightWare’s commercially available microLiDAR sensors, while enabling longer-range Lidar operations among uncrewed systems customers without being cost-prohibitive or mechanically unviable for integration in both small and large gimbals.
“Achieving longer-range capabilities with 905 Nm technology presents significant challenges, primarily due to atmospheric attenuation affecting the laser beam,” Nilsen noted.
“Overcoming that necessitates meticulous control over beam divergence, and higher output power to optimise the signal-to-noise ratio, all while adhering to stringent eye-safety standards.
“While achieving longer ranges is easier with 1550 Nm technology, adopting it brings prohibitively high costs, limiting its use to scenarios where it is absolutely essential.”
The GRF-250 will enter full-scale production in July, followed by the GRF-500 in October. Meanwhile, the GRF-1000 is scheduled for launch in February 2025. LightWare has extended the warranty period for all its products from 12 to 24 months, which will also apply to the new GRF-Series.
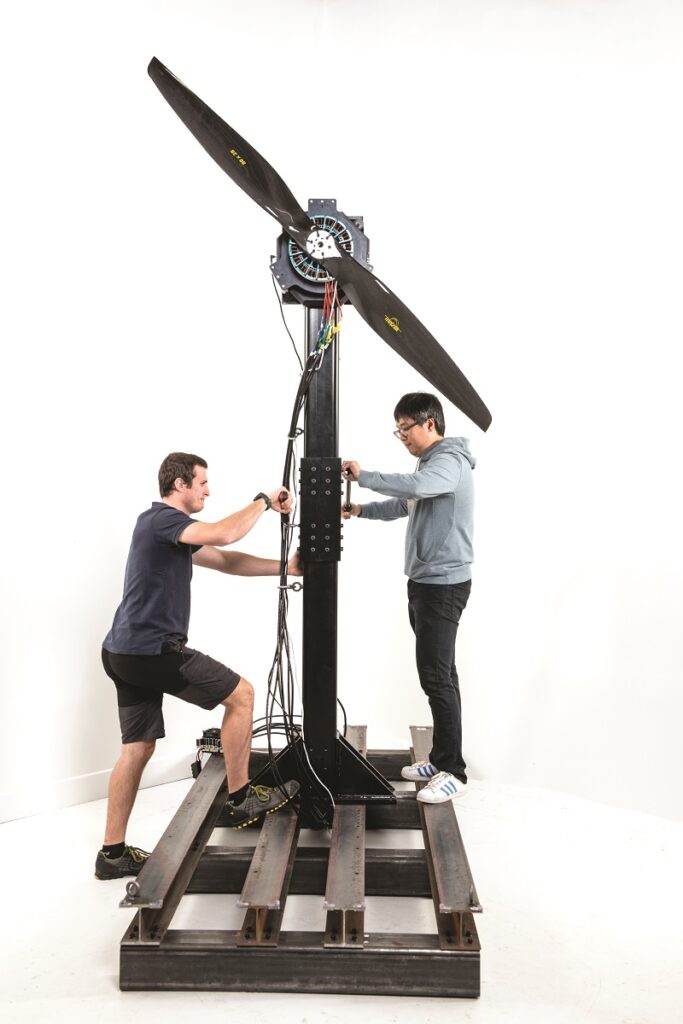
Tyto Robotics travelled from Canada to Abu Dhabi to showcase (among other products) the Flight Stand 500, its newest professional thrust stand for testing big, brushless electric motors and propellers. The stand was designed for testing the propulsion systems of heavy-lift UAVs and eVTOL-type air-taxis, and it can measure up to 500 kg of thrust force and 1500 Nm of torque.
“One of the key features of the thrust stand is that it is compatible with CAN ESCs,” said Tyto’s Lauren Nagel.
“When dealing with very large BLDC [brushless DC] motors, CAN compatibility is indispensable. The current rating is also customisable. Users can choose from 100 A, 200 A or 500 A, which is useful because the current sensor should be matched to their actual current draw to ensure maximum measurement accuracy.”
The stand can also be controlled remotely from any computer on the end-user’s network, enabling their technicians to keep a safe distance when running tests at high power.
“As with our other tools, the stand has a 1000 Hz sampling rate, which opens the door for many types of dynamic tests, like torque ripple, current analysis, vibration analysis and reaction time analysis.”
The system comes with a Python API, allowing users to control the stand via Python, an in/out API for connecting additional sensors, and a replay feature where users can upload flight-controller data and replay their flight with their propulsion system on the stand.
Tyto started developing the Flight Stand 500 after some customers said its previously largest stand, the 150, was not big enough, despite measuring 150 kg of thrust force and 150 Nm of torque.
“We have completed many hours of rigorous testing, and we expect the first unit to ship this summer,” Nagel said.
Exail showcased the Phins 9 Compact, a high-performance inertial navigation system (INS) for all types of UUVs, with a particular engineering focus on performance, reliability and SWaP efficiency.
Maxime Le Roy at Exail told us: “The Phins 9 Compact has dimensions of 88.9 x 130 mm, and doppler velocity logger (DVL)-aided position accuracy of 0.1% TD (travelled distance), with a heading accuracy of 0.07°, a pitch-and-roll accuracy of 0.01° and power consumption of less than 7 W.
“It has been designed for new-generation AUV manufacturers and e-ROV operators who are looking to save power without compromising on data-processing capabilities, and it will be commercially available in July or August.”
The Phins 9 Compact has been built around Exail’s UmiX 40 compact FOG IMU, which, in addition to its north-finding fibre-optic sensor, integrates miniaturised, in-house accelerometers that are designed for high dynamics. It features new, custom-built FOGs.
Exail anticipates the Phins 9 Compact serving subsea navigation applications in a wide range of aquatic missions, including survey-grade coastal and offshore seabed mapping, inspection repair and maintenance (IRM), and defence.
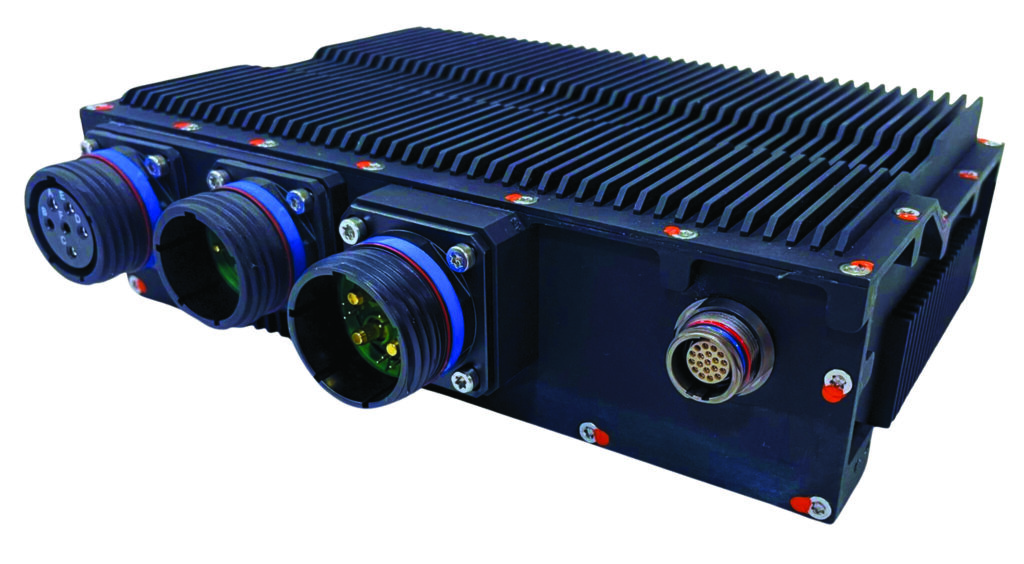
VISIONAIRtronics promoted several new systems, particularly two products for power management in its latest generation of high-power UAVs.
Its 2 kW Generator Control Unit (GCU), a configurable, multi-channel AC/DC solution, is designed for 60-150 kg, VTOL-transitioning hybrid UAVs using 60 V, 12-14 S lift batteries (which could not always be charged onboard due to voltage incompatibilities), although manufacturers with platforms of 150-1500 kg have adopted it more rapidly.
“The 2 kW GCU is designed with a modular approach for diverse aircraft configurations, including helicopters, multirotors, fixed-wing and VTOL-transitioning craft; its smallest host aircraft weighing around 80 kg,” said Ben Tschida of VISIONAIRtronics.
“It can be configured for single-output, dual-output or triple-output, and with many different combinations of voltage and power levels to efficiently and safely power different groups of onboard systems; for instance, PDUs [power distribution units] further distributing and converting into different voltages.”
VISIONAIRtronics also showcased its 1.8 kW PDU, designed around two of its 900 W PDUs to cater for higher-power UAV manufacturers. Presently, they are separately controlled, but an upcoming revision will arrange them in a master-slave configuration, enabling control via a single interface.
It features three inputs – ideally one from a ground control unit (GCU), and one or two separate battery inputs – ensuring redundant input power to securely provide power to the PDU.
“With six configurable outputs, the PDU has four redundant and two non-redundant outputs, which are programmable in terms of voltage. End-users can read all the data on, say, voltage and current per output and input, as well as temperature and error messages,” Tschida said.
The 2 kW GCU and the 1.8 kW PDU are housed in IP67-rated machined aluminium enclosures, and they can operate in environments from -40 C to 55 C, and at altitudes up to 10,000 m.
“Both are built around power converters and PCBs that we’ve designed in-house from scratch, with solid-state controllers, such that if a microcontroller fails, the product will continue to function until it is powered off or disconnected from batteries,” Tschida said.
UPCOMING EVENTS
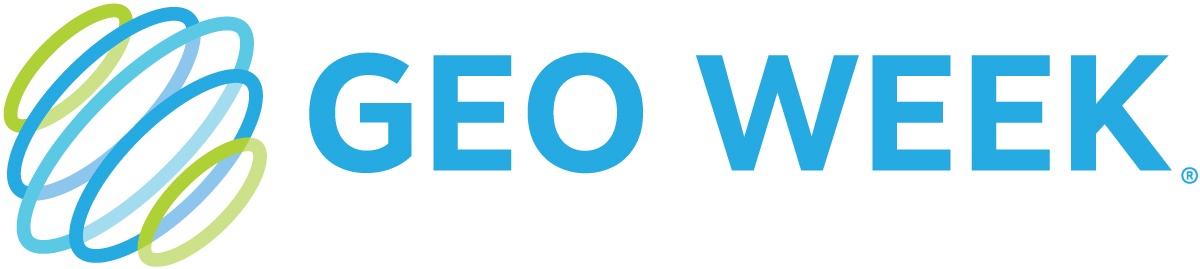
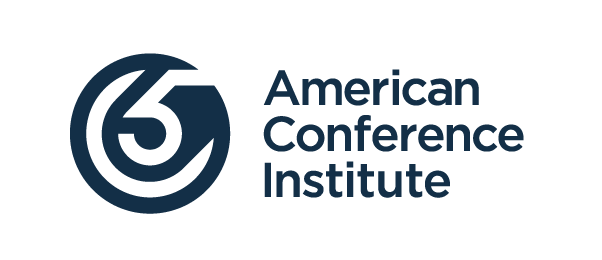
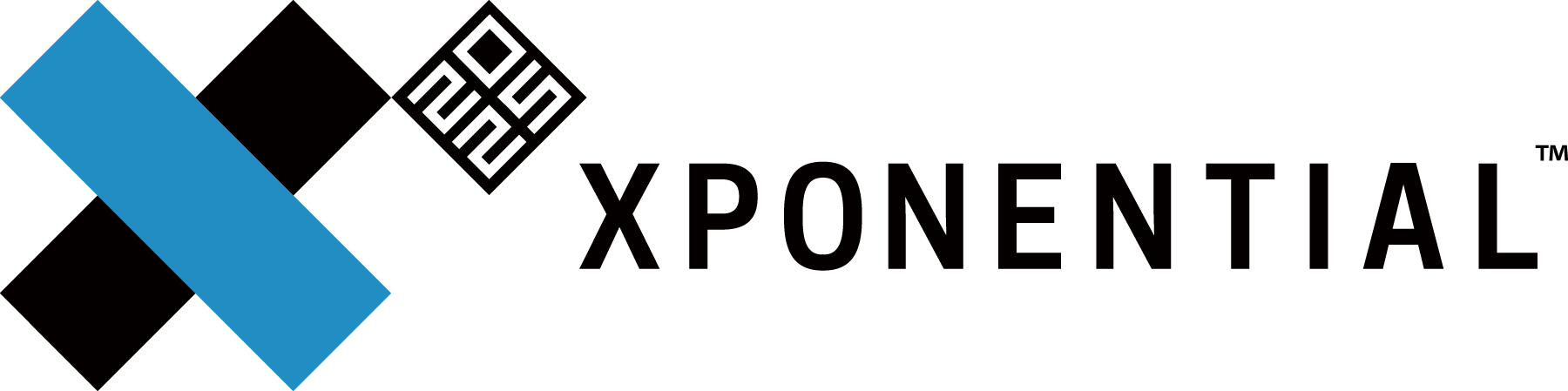
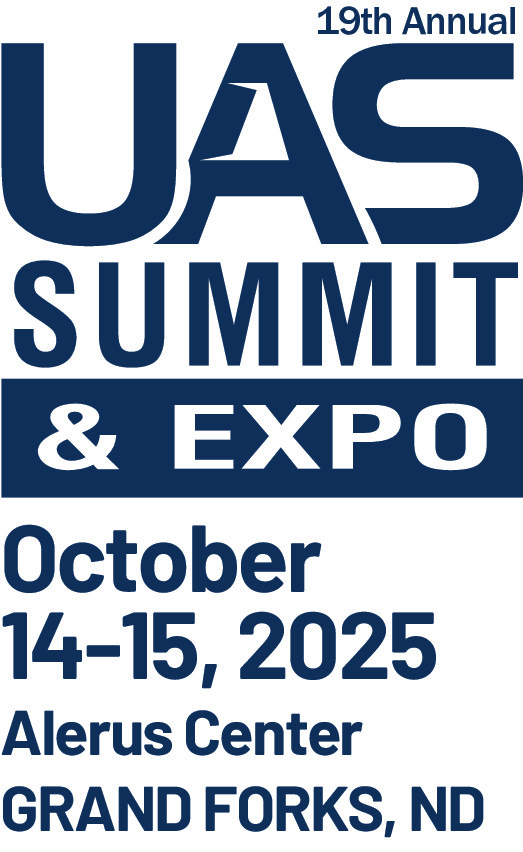
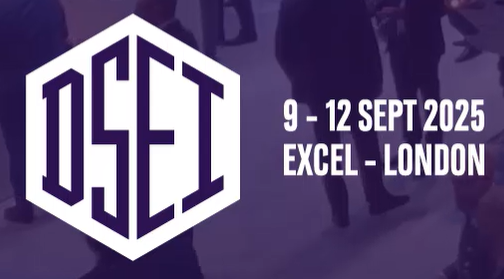
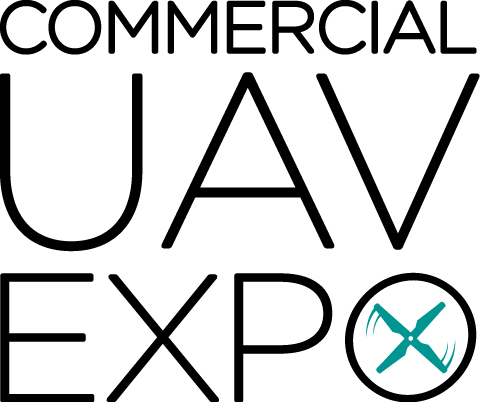
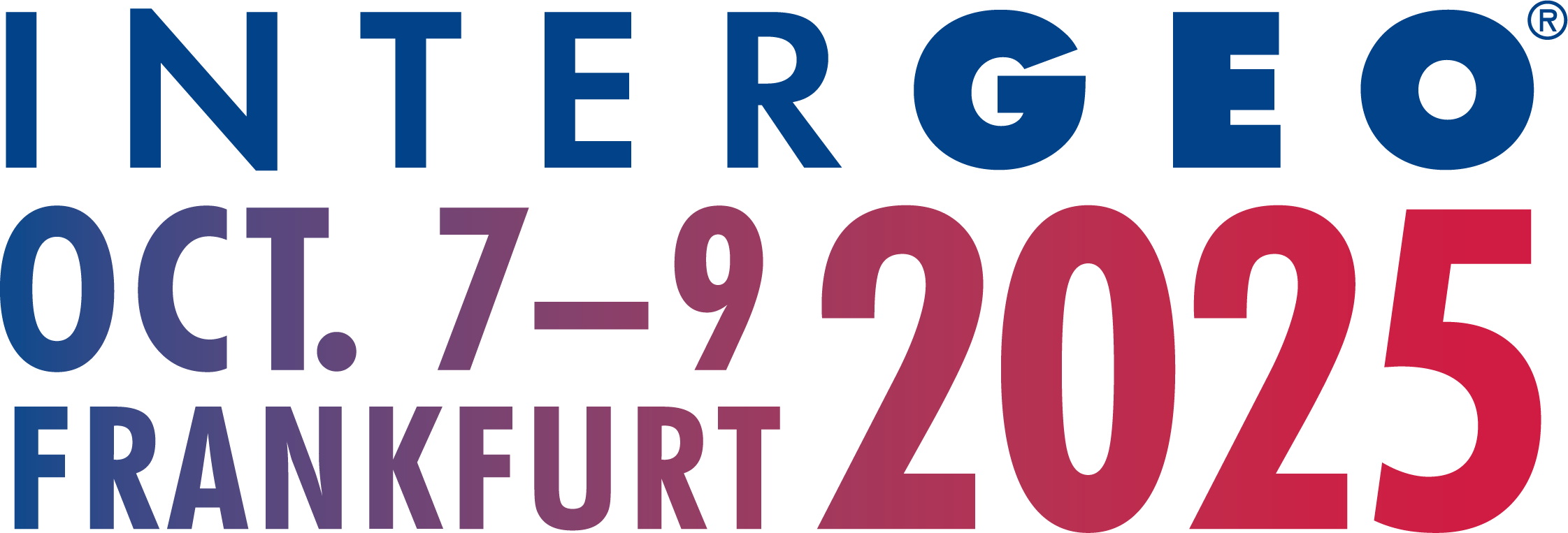
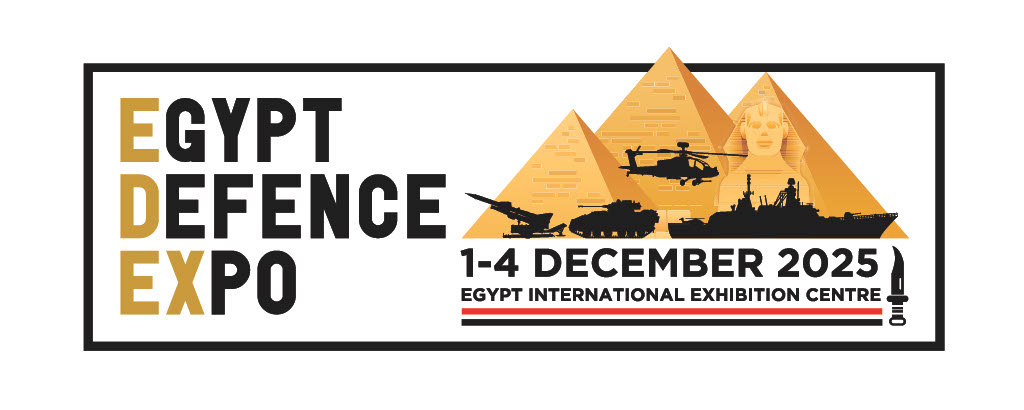
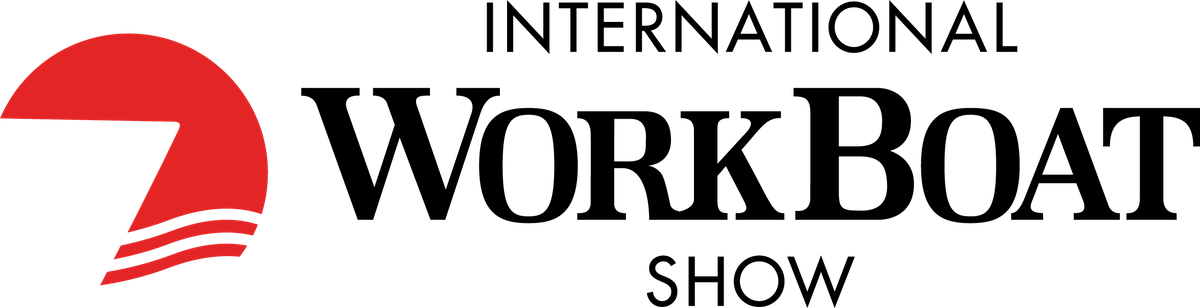
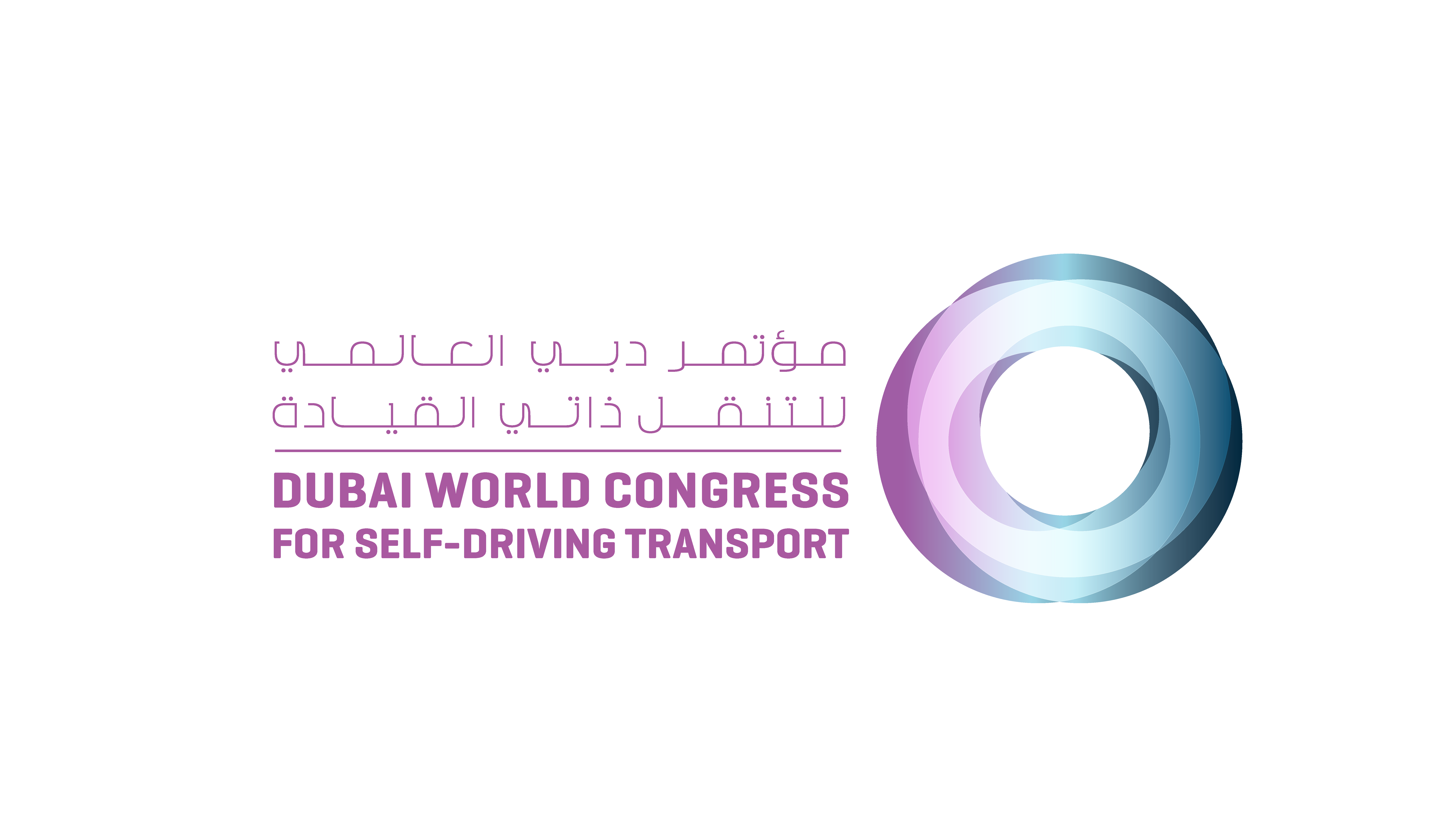
