Aant Farm TPR72
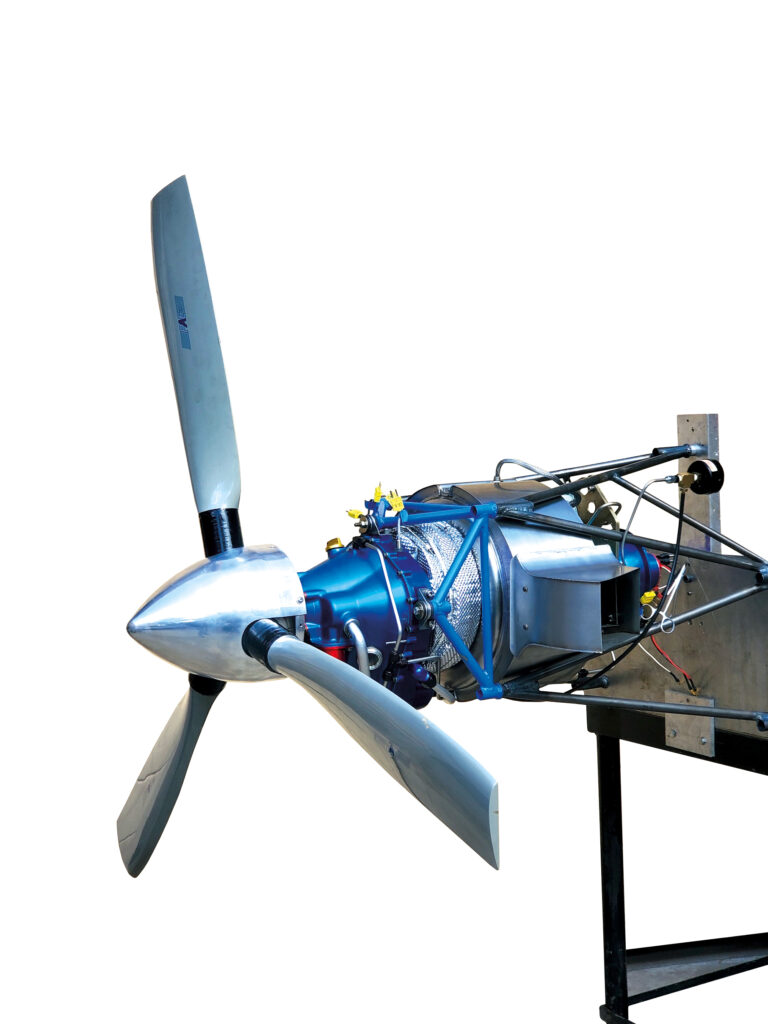
Recuperating heat from exhaust gases gives this microturbine an edge over gasoline engines for heavy UAVs, as Rory Jackson explains
Heat treatment
Although turbine engines offer benefits to fuel-powered UAVs in terms of efficiency, reliability, lifespan and noise, their uptake in the UAS industry has been slow relative to reciprocating and rotary engines. The reason for this is their fuel efficiency. When turbine designs are scaled down from those intended for crewed aircraft to something more appropriate for UAVs, their fuel efficiency drops by around two-thirds, meaning far shorter ranges, lower payload capacities or higher fuel bills.
Much of that drop comes from the clearances and blade tip leakages in a downsized turbine – or ‘microturbine’ – being proportionally bigger compared to those in a ‘normal’ sized turbine. That drop is unavoidable, barring some major advance in manufacturing technology.
However, as companies such as UAV Turbines (issue 11, December 2016/January 2017) and Turbotech (issue 31, April/May 2020) have shown, the loss of fuel efficiency in a microturbine can be compensated for, using a heat recuperation system in which exhaust gases preheat the charge air before it enters the combustion chamber.
Doing so means a far lower fuel-to-air ratio becomes sufficient for producing the temperature needed to drive the turbine and hence the propeller.
Aant Farm is the latest contender on the scene in this respect. The Arizona-based company is a derivative and descendant of M-DOT Aerospace, which was founded by Bryan Seegers in 1989, sold to Chase Capital Partners in 2011, and renamed Azmark Aero Systems before being sold again to Imaginetics in 2016.
Imaginetics allowed the engineering division to be spun off into Redline Turbine Systems, which now develops some of the world’s smallest turbomachines and where Seegers serves as chief scientist.
In 2020, he saw a growing market for a reliable uncrewed aircraft engine running on heavy fuel, and decided to use Redline’s existing hardware and IP to develop a modern version of its TPR60 turboprop. Thus was Aant Farm founded by Seegers and his partner Dave Weier, who now provides technical and operational leadership for the company.
The result is the TPR72, a 30 kg turboprop measuring about 905 x 707 x 381 mm, and designed to deliver up to 72 kW (96 bhp) from its gearbox-driven propeller. The engine flow path is similar to that of the Pratt & Whitney Canada PT6 engine family, with an inlet that can face forwards or backwards for pusher or tractor configurations; for simplicity, we will treat the air intake here as the ‘front’ of the engine. The system runs on JP-4, JP-8 and Jet-A, with further testing planned for evaluating its performance on JP-5 and diesel.
With UAVs getting larger, and demand for heavy fuel compatibility (and efficiency) rising, the time is ripe for more companies to create recuperated microturbines that can provide the efficiencies and TBOs needed to make heavy UAV operations profitable.
Aant Farm has also completed the design and started fabrication of the TA65-1, a version of the engine that replaces the gearbox with a brushless high-speed alternator. Also set to weigh 30 kg, it is designed to produce 60 kW from the main alternator and a further 5 kW from its starter/alternator. As the former solution is much further along in development however, the main focus here will be on the TPR72.
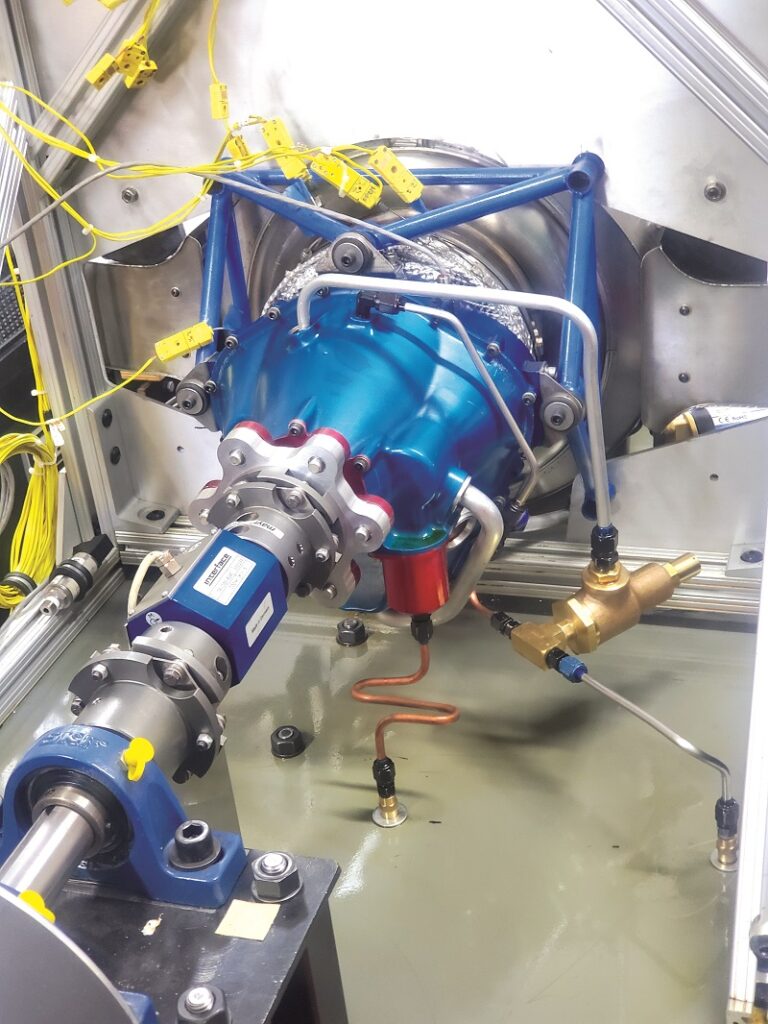
Development history
Aant Farm’s origins date back to 1990, when M-DOT Aerospace was contracted by the US Army MICOM (now the Aviation and Missile Research, Development and Engineering Center) to design, fabricate and test an ultra low-cost turboprop for uncrewed vehicles that had used a Sundstrand (now Pratt & Whitney) expendable turbojet as the gas generator core.
Success of the SBIR Phase 1 of this work led to a Phase 2 award to create a new centreline design, designated the TPR80-1, and a prototype of this engine was produced and tested. “At the time though, the team behind the IAI RQ-5 Hunter Short-Range UAS programme [the development plan by which that uncrewed aircraft was scheduled to become the US Army’s short-range UAV for division and corps commanders] was looking for a heavy fuel engine,” Seegers recalls.
“So we designed our engine to fit their aircraft’s cowl, and related packaging constraints defined the prop size and speed for the engine and gearbox, to the point that the Hunter became the original intended platform for the productionised TPR80.
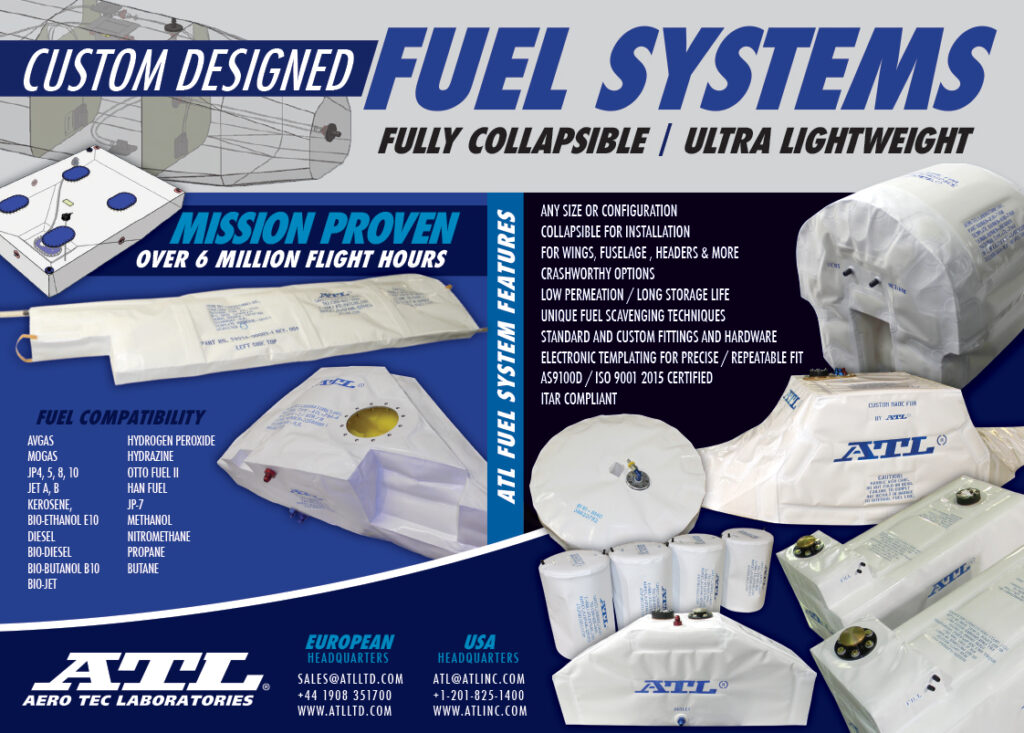
“Both simple-cycle and recuperated versions of the engine were designed but, owing to SBIR Phase 2 funding limits, we were only able to bring the simple-cycle version to the testing stages of that project. Since then, I’d wanted to pursue development of the recuperated version.
“My decision to restart development came in 2018, when I saw an Air Force Research Laboratory SBIR solicitation for a 50-100 bhp turboprop. I knew I could leverage our existing IP and hardware, bring in private money and come out way ahead of the government programmes.”
What followed was a hardware-heavy development programme to modernise and optimise the overall engine, with Seegers and Weier drawing on their experience in solid modelling, cycle analysis, stress analysis, turbine and compressor aero design and rotor dynamics. The pair also brought in John Dodge, an aerodynamicist whose work extends back over 59 years to the original General Electric TF39 high-bypass turbofan.
Four complete TPR72 engine sets plus spares have been produced to date (three of which had been assembled at the time of writing). The spare parts include centrifugal impellers, turbine rotors, alternator rotors and ancillaries such as oil pumps.
“While this approach is more expensive than building a single prototype, it affords parallel development paths that, in turn, compress the schedule,” Seegers says. “Serial number 001 is on the dyno stand, and we’re using it to develop the starting fuel supply schedule and test the lubrication system.
“Engine serial number 002 is instrumented for thermodynamic performance testing. Prototypes 003 and 004 aren’t assigned for testing just yet. We’re keeping them aside principally for any airframe manufacturers who want to flight test a TPR72 at short notice.”
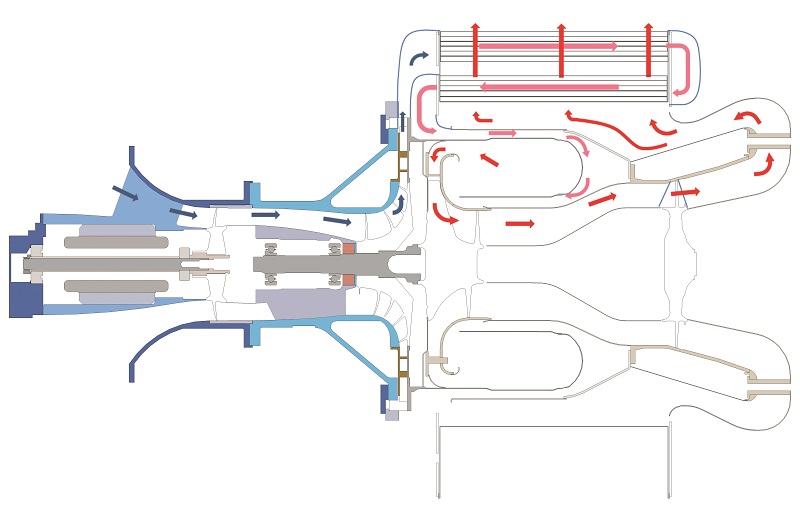
Operating stages and principles
As with many aircraft gas turbines, the TPR72 is designed mainly around a gas generator core that consists of a compressor, recuperator, burner and turbine, thereby generating hot gas via the Brayton cycle of compression, combustion, and turbine expansion. The resulting hot combustion products that still have useful energy can be sent directly through a nozzle for pure thrust (akin to a turbojet) or to an additional turbine stage for further expansion and additional power extraction.
In Aant Farm’s case, the outgoing hot gas drives a single-stage axial turbine, which in turn drives either a gearbox input pinion for the TPR72 or a 60 kW high-speed permanent magnet alternator for the TA65-1. The TPR72 can be regarded as a two-spool turbine, with the high-pressure spool in the core, gas generator section, and the low-pressure spool in the rear power extraction section. At full rated power, the core shaft turns at 96,000 rpm, the power extraction turbine at 76,000 rpm.
During operation, air first enters the engine through a bellmouth inlet on the front, where it is drawn in by and passes through a first compressor stage (referred to as an axial zero stage) where it is compressed at a ratio of about 1.5:1. Aant Farm notes that adding an axial compressor stage in front of the centrifugal stage has the same effect as a turbocharger on a piston engine, supercharging the engine core to increase the compression ratio and mass of airflow.
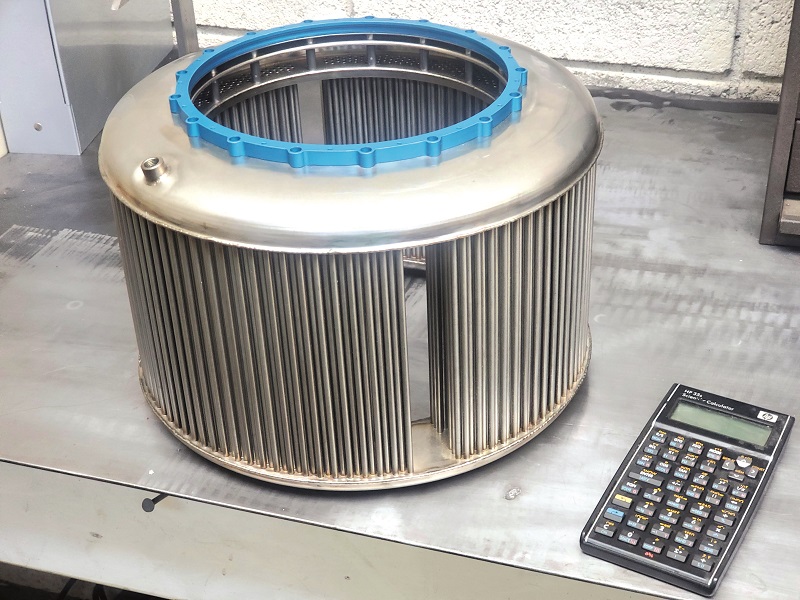
The air then enters a second centrifugal compressor stage, where it is further compressed as it is directed radially outward and sent through a diffuser to the entrance of the heat recuperation system.
In principle, the recuperator is similar in concept to Turbotech’s solution. It consists of metallic microtubes that channel the compressed air towards the burner while crossing paths with the hot exhaust gas in order to transfer the exhaust’s heat into the intake air.
“Our recuperator is nearly identical to another one we’d developed 10 years ago for the IARPA Great Horned Owl engine programme [a research effort aimed at producing a quiet fuel-hybrid powertrain for UAVs to minimise their acoustic signatures when flying ISR missions],” Seegers explains.
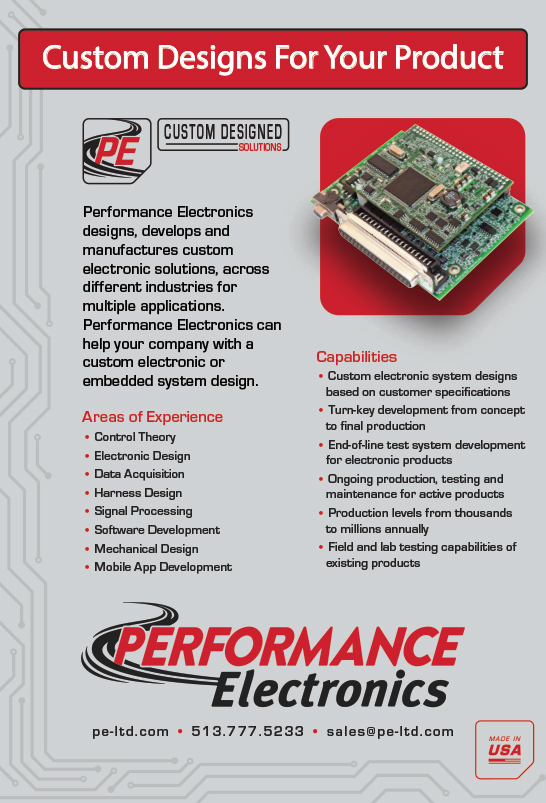
“The compressed air travels first through the outer tube bank, then down around the aft tank head where it is redirected towards the front again through the inner tube bank. During both passes it is heated by exhaust gas that is travelling radially outward across the tubes.
“The heated air then travels radially inward and first enters the plenum that surrounds the annular burner before entering the burner itself. In the burner, the air is mixed with fuel and burned. For ignition, we use a conventional low-tension exciter and semiconductor igniter plug.
“After igniting, the gas once again changes direction and travels to the left into the outer transition duct that directs the gases inward, through the vanes of the nozzle for the gas generator turbine,” Seegers says.
The hot gas then enters and drives the gas generator turbine, powering the compressors and starter/alternator in the core. The starter/alternator is mounted on the high-pressure core spool.
After exiting the gas generator turbine rotor, the hot gas then enters the power turbine nozzle and rotor, where it expands further to power the gearbox, or in the case of the TA65-1, the main alternator.
Finally, as stated earlier, gas exiting the power turbine is directed radially outward across the recuperator tubes before being collected and directed out of the engine through the exhaust ducts.
Much of the design throughout the engine follows standard practice for gas turbines. For instance, both engine shafts are mounted on ceramic-hybrid bearings that are jet-lubricated with Type II turbine oil, the gears are cut from alloy steel before being carburised and further heat-treated for high strength, while the rotors are cast in an undisclosed high-temperature alloy, having been designed for a cycle life of minimum stress and temperature.
The static housings are predominantly machined assemblies, made from 6061 T6 aluminium in the colder sections and a nickel-based alloy in the hotter section. The two front housings are 6061 dip-brazed assemblies, while the rear housings are nickel-based welded and furnace-brazed assemblies.
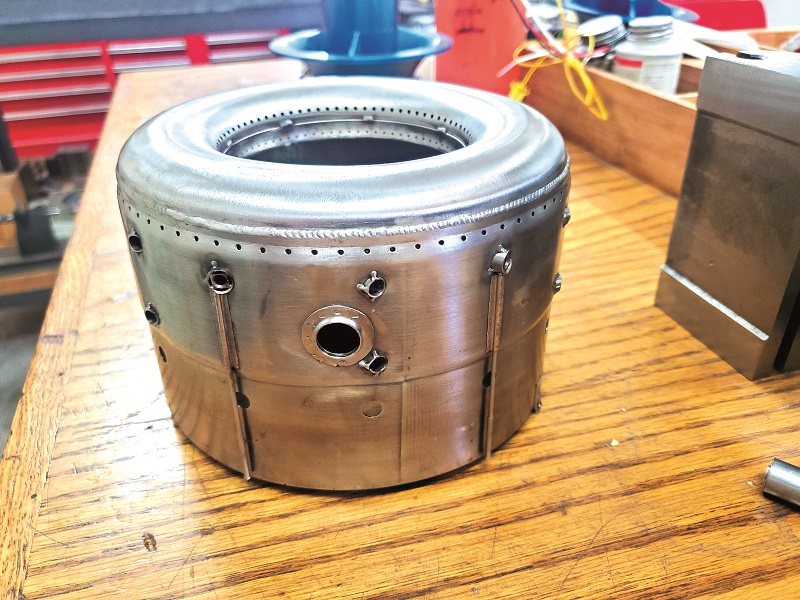
“Our choice of dip brazing and the subsequent heat treatments provided us with the quickest route to a complex monolithic part for our prototype engines,” Seegers says. “However, in series production we’ll switch to investment casting, as that will probably be a less expensive approach.”
Like the TPR80-1, the TPR72 features a patented air-blast fuel nozzle design. As a result, the six nozzles require very little fuel pressure beyond that needed to overcome the compressor exit pressure in the burner.
As mentioned, maximum continuous power (at sea level in standard day conditions) is 72 kW to the propeller, plus 5 kW electric from the starter/alternator driven by the gas generator. As altitude increases though, the power output falls and the fuel economy increases.
“To be exact: at full power [100% shaft speed] the power output to the propeller falls from 72 kW at sea level to 46 kW at 15,000 ft,” Seegers explains. “Specific fuel consumption however improves, from 0.375 to 0.369 kg/kWh. That increase in fuel economy is mainly due to the increase in the compressor pressure ratio that occurs as the temperature of the inlet air decreases with altitude. An additional effect comes from the need to operate at higher throttle settings at higher altitudes due to the reduced air density, as higher throttle settings mean higher pressure ratios.”
Regarding the operational altitude limits, Seegers says, “The burner is designed to have a re-light capability up to 20,000 ft, so there’s no reason why the engine could not operate to 25,000 ft. We don’t want to predict performance at this altitude though until we know more about the engine through testing.”
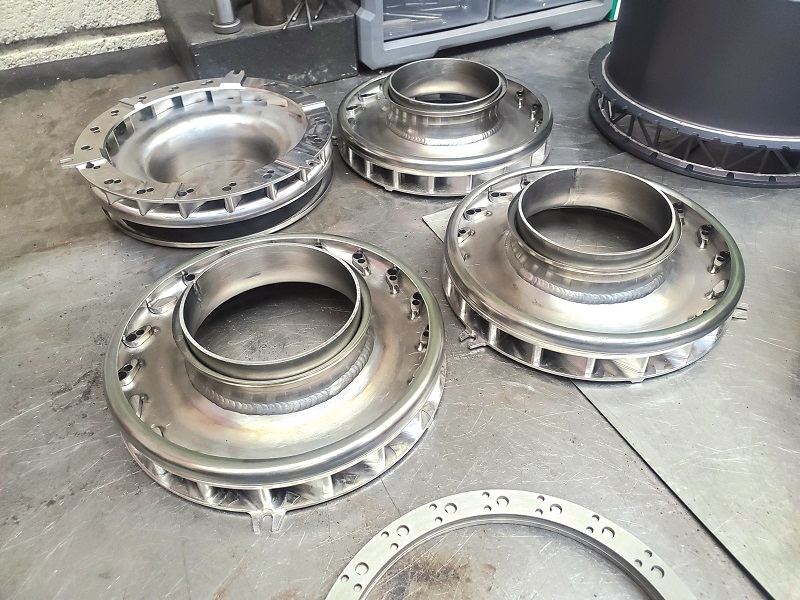
Engine management
The ECU remains in development, but is expected to feature start sequencing and speed governing of both spools, as well as alarms and automated shutdowns for turbine overtemperature, overspeed and low oil pressure.
“Our plan is to develop an analogue unit for anything crew-rated in order to simplify the certification process,” Seegers says. “In the nearer term, we’re working with Integrated Solutions for Systems, in Alabama, which is developing a digital controller for small gas turbines that we hope to test soon.”
Turbine manufacturing network
From the onset of the TPR72 programme, Aant Farm has aimed to have sufficient internal manufacturing capabilities to insulate itself from long lead times from suppliers. As a result, it has capabilities across five-axis CNC milling, CNC turning, grinding, sheet metal compound forming, TIG welding, dynamic balancing, tensioned carbon fibre winding and some heat treating at its Arizona facility.
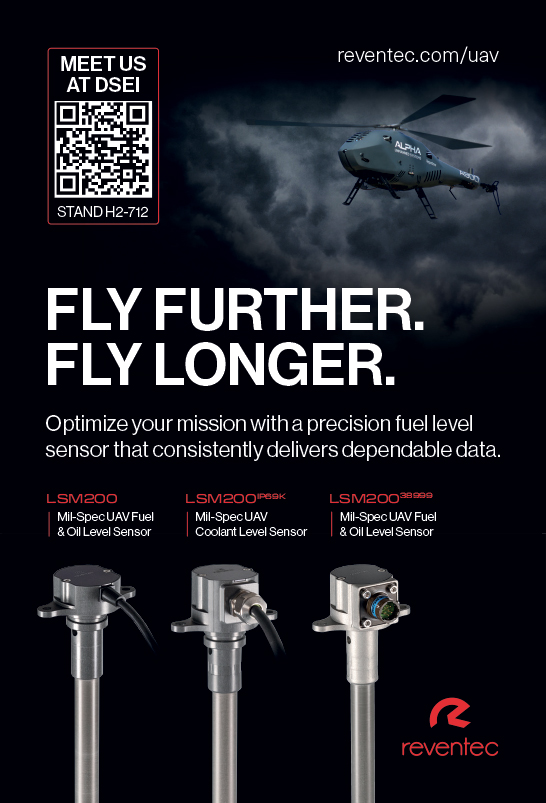
However, it does subcontract some highly controlled processing and parts to its supply network. A prime example of this is Mezzo Technologies, a company based in Louisiana that specialises in the design and development of microtube recuperators. Mezzo assisted Aant Farm in the original performance trade studies behind the recuperator in the TPR72 and TA65-1, and then provided the laser welding services for the microtube core assemblies.
“We also have High Temp Metals in California as our supplier for a number of critical hot-section materials including Inconel alloys 718, 625 and X-750,” Seegers says.
“Also very important is Bescast, in Ohio, which produced the investment castings for both our turbine rotors. We sent them our CNC-machined blue wax patterns for those parts, and they sent us back finished castings.
“When it comes to rotor systems, you almost always have to use a high-performance nickel or cobalt-based superalloy, which has to be vacuum cast and which is why you need a company like Bescast.”
Much of Aant Farm’s future brazing is set to be provided by fellow Arizona company Joined Alloys, which specialises in highly controlled vacuum furnace brazing and vacuum heat treatment.
Lastly, Seegers cites Metalcraft as another key company (also based in Arizona), which provided some critical services. “When we decided to switch our impeller material from an aluminium forging to titanium billet, we knew we would need outside help with machining the parts,” he says. “Metalcraft have a lot of experience with titanium, and they specialise in machining it.
“They’ve supplied numerous such parts for Honeywell’s gas turbine engines over the years, so we knew they’d be able to provide the titanium components at the quality we needed.”
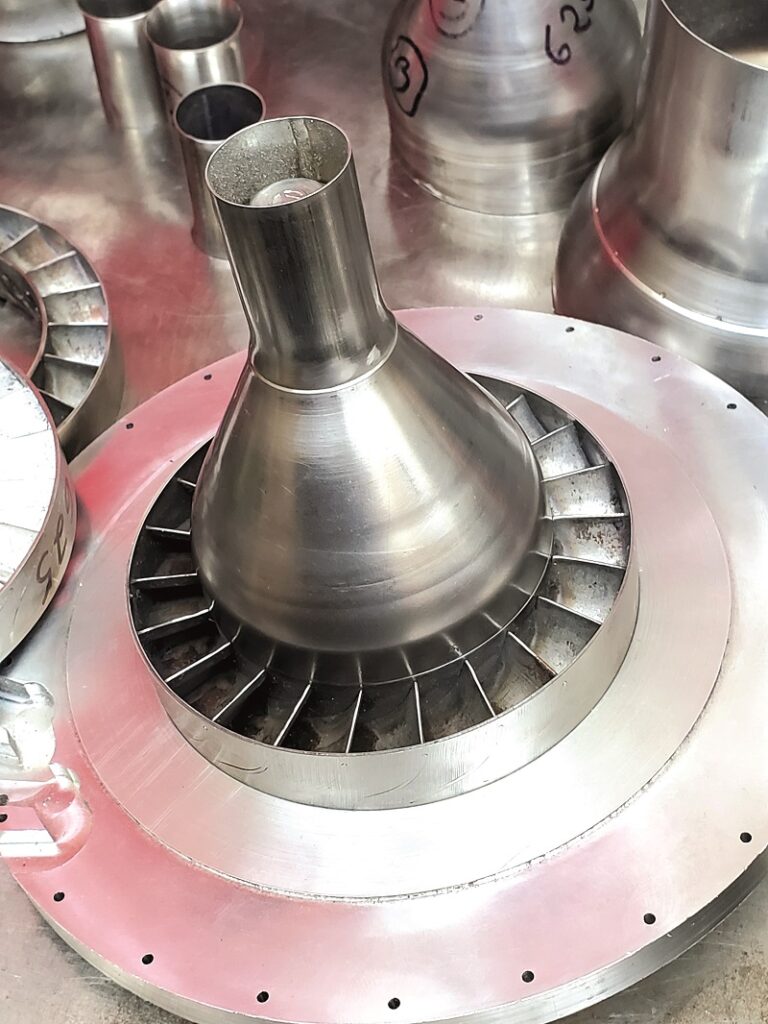
Heat recuperator
As mentioned, Aant Farm’s recuperator design has been inspired largely by a recuperator that was designed and developed for a previous engine aimed at the IARPA Great Horned Owl programme. The system has a multi-pass configuration, in which the outgoing air from the compressor exit makes two passes through the exhaust flow before entering the burner, first from front to back through the outer tube bank, then from back to front through the inner bank.
“To house the tubes, we’ve used our in-house 100-ton press for compound-forming the tank pressure heads, mainly via rubber pad and matched die forming,” Seegers explains. “Those parts are then TIG-welded to the core header plates to yield a complete assembly.”
Throughout the recuperator’s design process, thermal efficiency has been prioritised over strength-to-weight ratio, as the design is already intrinsically stiff. Seegers notes however that a more applicable parameter than strength-to-weight might be “ratio of weight to effectiveness”.
In this context, ‘effectiveness’ is used to refer to the ratio of actual heat transferred from the hot exhaust gases flowing about the recuperator microtubes to the intake air inside of them, to what is theoretically possible with the given high and low temperatures.
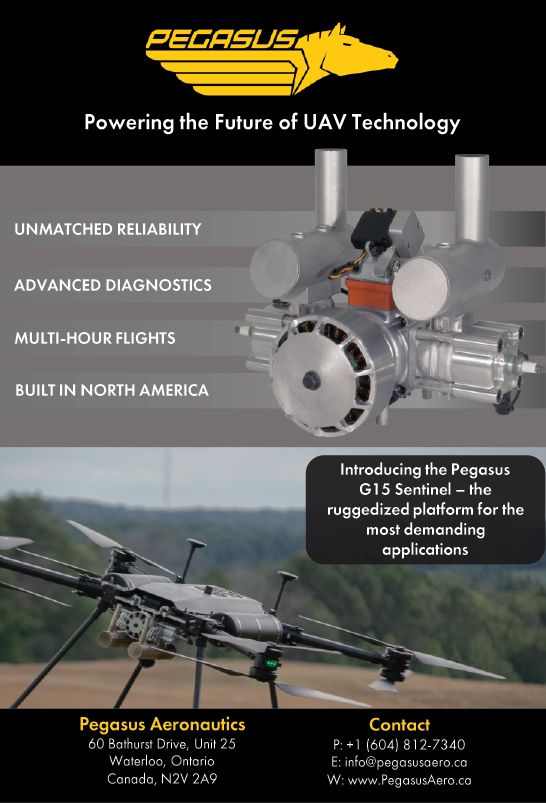
High effectiveness hence means more heat transferred and therefore better efficiency. However, as a heat recuperator becomes more effective, its mass tends to increase exponentially. For example, increasing a plate-fin recuperator’s effectiveness from 85% to 90% could double or triple its total mass.
“There’s a calculation known as the Breguet Range Equation, which essentially uses an aircraft’s mass, its lift-to-drag ratio, its fuel load and the efficiency of its powerplant to calculate range,” Seegers explains.
“The equation can therefore be used to evaluate the merit of additional tube mass in a recuperator versus the resultant reduced fuel burn. We looked at several mission profiles and chose our effectiveness based on lower tube mass.
“So if we make the recuperator a little less effective, maybe it consumes 7-8 kg more fuel over a given mission, but surplus fuel weight burns off during the mission. Excess recuperator mass on the other hand does not – in fact it compounds the weight problem by requiring a further increase in airframe structural mass in order to carry the extra weight of the recuperator core.”
To strike the right balance therefore, lower weight has been purposely prioritised over higher effectiveness, although modifications have been made to the engine cycle to compensate for that. The exact effectiveness of the recuperator, as well as the exact overall engine pressure ratio, are proprietary, although Aant Farm says values have been selected to minimise maintenance and to optimise efficiency and engine mass for 5-8 hour missions.
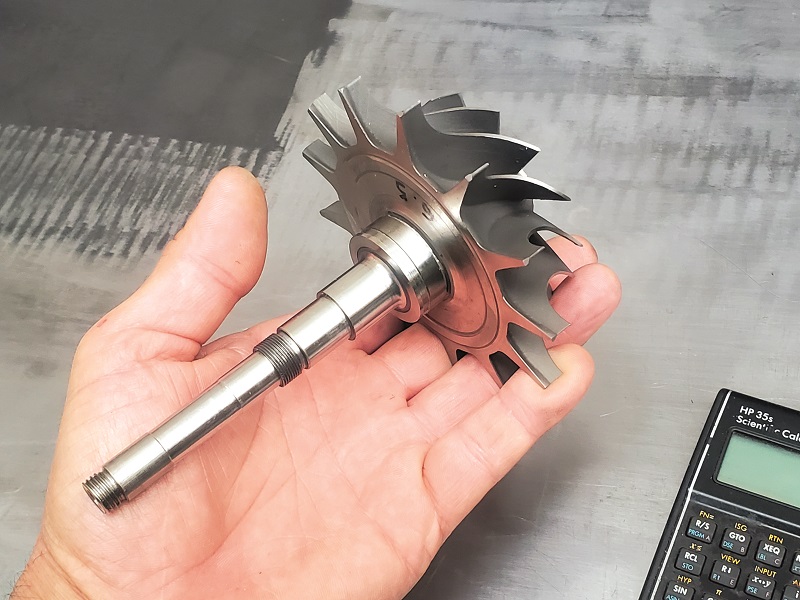
Exhaust
The exhaust ducting is made from Inconel 625, although the company anticipates substituting 300-series stainless steel in the future to reduce cost. A key point here is that exhaust temperatures are lowered once heat is removed by the recuperator, so super-high temperature alloys are not wholly necessary.
“We will also probably install baffling in the future to properly distribute the exhaust along the microtubes from front to back,” Seegers adds. “We plan to incorporate that into the next design iteration based on testing of the current design, both with and without baffles. If the difference proves minimal, we won’t use them.”
While noise generation from the exhaust is not yet a major concern, future hot-flow path design iterations might incorporate tuned metal fibre felts to attenuate noise. This is something Seegers and Weier have designed for business jets, APUs and research engines.
“The compressor inlet is currently the source of most of the engine noise,” Seegers notes. “In fact, depending on customer needs, we may offer a tuned inlet attenuator.”
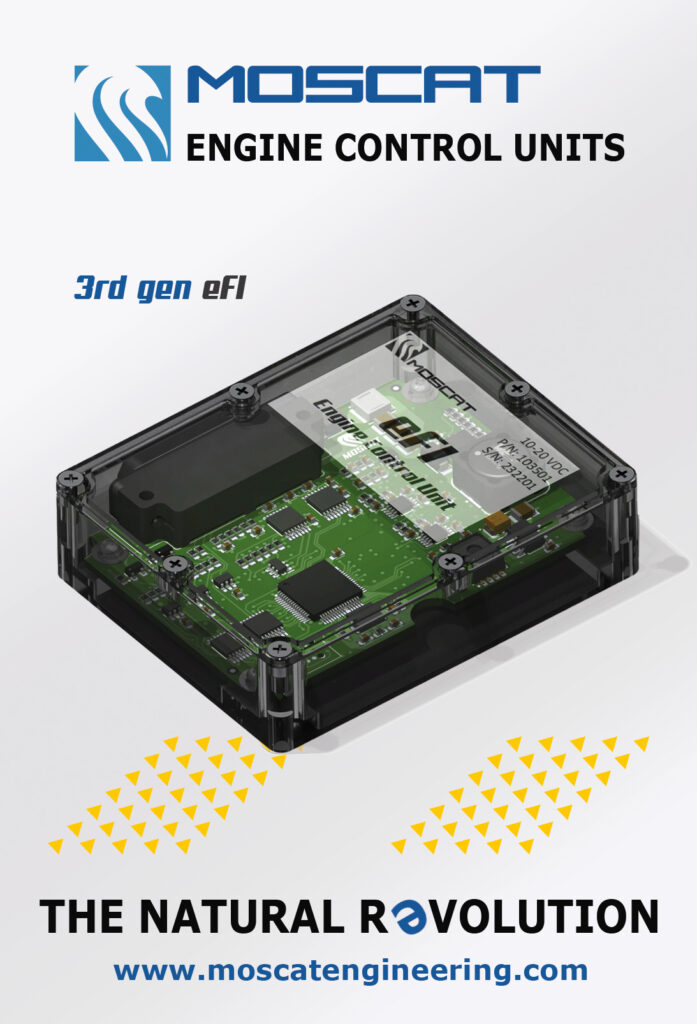
Alternators
As mentioned, the TPR72 has a front-mounted starter/alternator bolted directly to the gas generator bearing housing. It features 12 stator poles and four neodymium rotor magnets, which are bonded directly to a steel core shaft and then over-wound with pre-tensioned unidirectional carbon fibre tow.
“Different versions of the starter alternator are offered; we’re currently testing 50 V and 450 V units,” Seegers comments.
Although still at the concept stage, the TA65-1 turbo-alternator will feature a 60 kW liquid-cooled main alternator (as well as the same 5 kW starter/alternator as in the TPR72) in place of the gearbox and propeller.
That main alternator is of a slotless design, directly driven at 76,000 rpm by the power turbine. “To help minimise losses, Hiperco 50 is used in the core stack, and litz wire is used in the windings, which are directly cooled by the heat transfer fluid that flows axially down the stack,” Seegers notes.
At the time of writing, both the main and starter alternators were designed to operate to 20% overspeed. The alternator is predicted to be 96% efficient, and will deliver its 60 kW maximum continuous power at 708 V AC (RMS).
Gearbox mechanics and lubrication
The gearbox design is nearly identical to that on the original TPR80, and in fact uses gearsets left over from that programme. The overall design philosophy has been to produce a reduction drive with the lowest possible parts count, using as many commercially available parts and production processes as possible, to give a minimum life of 3000 hours and maximum flexibility in the available reduction ratios.
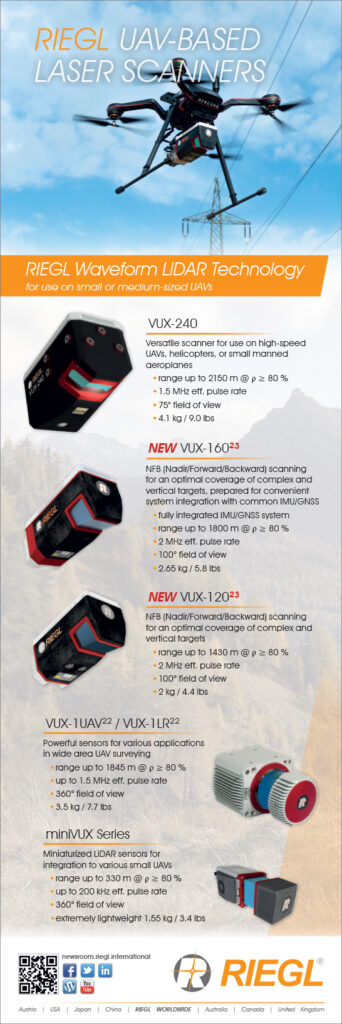
“We chose a two-stage design with twin layshafts that one might call a twin star-gear arrangement,” Seegers comments. “Two stages instead of one make for a gearbox with less frontal area.
“All the gears are made from hardened and ground alloy steel. The teeth are first cut using a gear hob, then through-hardened for the highest possible bending strength, and finally carburised for maximum surface hardness and contact stress resistance prior to precision grinding of the involute profile.”
The gearbox has a reduction ratio of 22:1, as per the TPR80’s original sizing for the Hunter UAV programme. Gearbox (and therefore power turbine) speed is sensed by a threaded monopole sensor that reads gear tooth passing frequency on the left bull gear (the larger of the two spur gears; the pinion is the other, smaller spur gear).
The gearbox is a wet-sump design, meaning that the oil is contained in the gearbox housing rather than in a separate oil tank. A 2 gallons/minute gerotor oil pump is driven by one of the layshaft gears and delivers oil to the engine through a standard 3-micron filter element.
“All the gearbox bearings are COTS,” Seegers says. “The axial turbine shaft runs in a pair of its own high-speed, ceramic-hybrid spindle bearings, and there are six more bearings inside the gearbox – two for each of the two layshafts – and a pair for the output propeller shaft.
The propeller shaft runs on tapered roller bearings so that it can take the 1P cyclic loading and gyroscopic loads the propeller generates “They’re cheaper than the ceramic bearings, and they’re beefier too,” Seegers says.
“Also, the layshaft bearings are radial contact bearings. Like the roller bearings they’re not high-speed, so they’re not expensive.”
The oil pumps were built to Aant Farm’s specification by WireTech, a wire EDM company in Arizona. As Aant Farm wanted full integration of the pump into the gearbox, the TPR72’s pump has no COTS elements; the entire pump has been fabricated for this one application and is designed to integrate specifically into the space internal to the gearbox.
“Lastly, the gearbox housing is machined as two halves, also out of aluminium billet, but as it has no non-line-of-sight parts, no brazing is needed. Again, we’ll probably switch to investment castings for series production, as it could save $400-500 per unit,” Seegers adds.
Future plans
Aant Farm anticipates developing an upscaled version of the TPR72 as a replacement for general aviation piston engines running on 100 octane low-lead gasoline. In the process of upscaling, it is likely that some consolidation will be done to reduce the parts count.
“We’ve seen what some successful aviation turbine engine companies are doing out there, and also what is happening in general aviation, with 100 octane low-lead gasoline having a questionable future,” Seegers comments.
“A 224 kW Jet-fuel burning diesel like the Continental CD300 weighs 264 kg. The Rolls Royce 300 turbine has the same maximum power rating but weighs 91kg. That’s a difference of 173 kg, which is weight you can’t burn off, reduces payload capacity, and adds to landing loads.
“We therefore think there is a market for a powerplant somewhere under 224 kW for OEM and retrofit aircraft. There are microturbines with more power than the TPR72, but given where the UAS industry and general aviation seems to be going, we might try to leapfrog the competition,” Seegers says.
“All commercial aviation and light aircraft OEMs are going to find 100 octane low-lead gasoline becoming rarer and more expensive, so a heavy-fuel engine like ours with low cost over lifetime could fill a huge gap across uncrewed and crewed aircraft fleets alike.”
Specifications
- TPR72
- Turboprop
- Heat recuperator
- Fuels: JP-4, JP-8, Jet-A, Jet-A1 (JP-5 and diesel yet to be tested)
- Total weight: 30 kg
- Maximum power output: 77 kW total (72 kW at propeller, 5 kW at alternator)
- Maximum prop speed: 3410 rpm
- Attitude limits: ±45o pitch, ±30o roll
- Flight ceiling: to be confirmed; 25,000 ft expected
- TBO: 3000 hours expected
Some key suppliers
- Oil pumps: WireTech
- Alloys: High Temp Metals
- Investment castings: Bescast
- Brazing: Joined Alloys
- Machined titanium: Metalcraft
- Manufacturing and IP services: Redline Turbine Systems
- Microtube welding: Mezzo Technologies
UPCOMING EVENTS
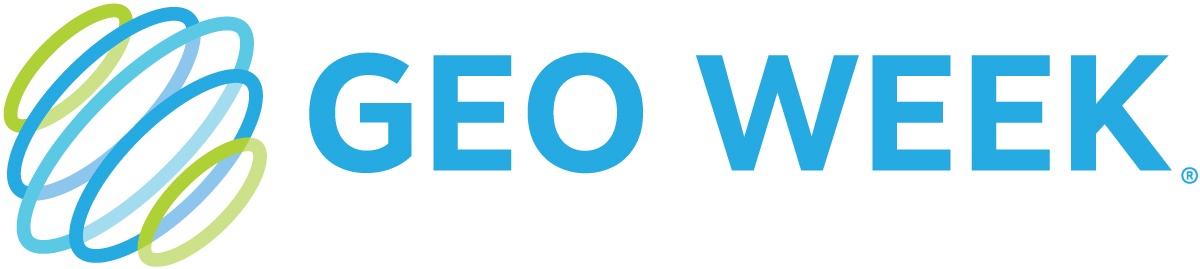
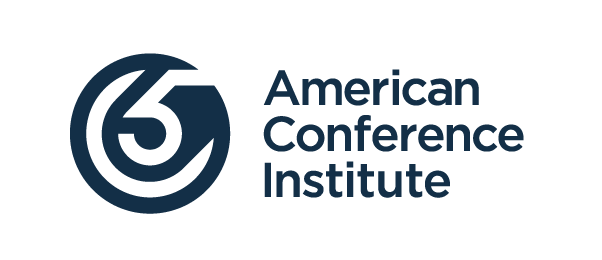
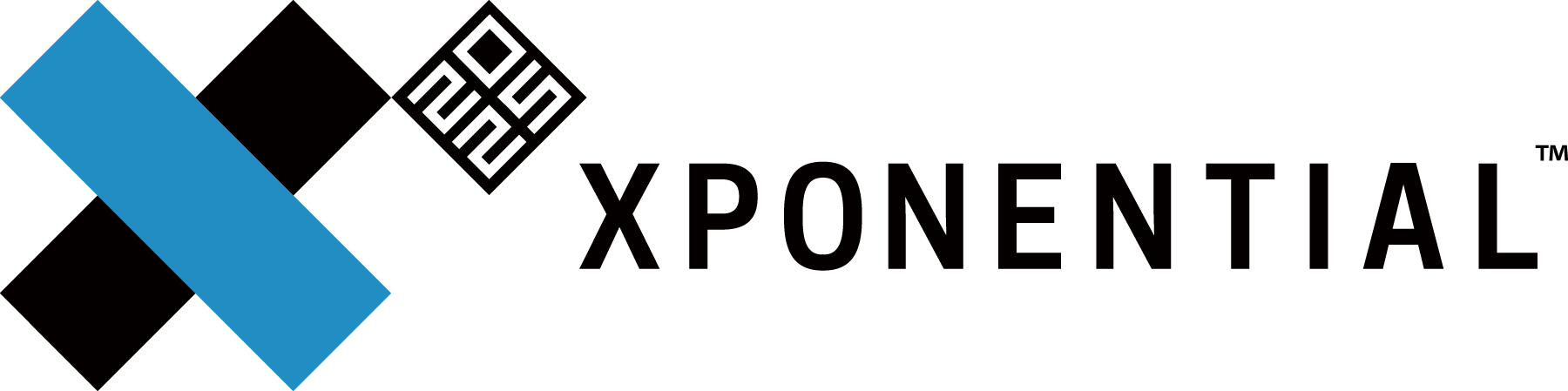
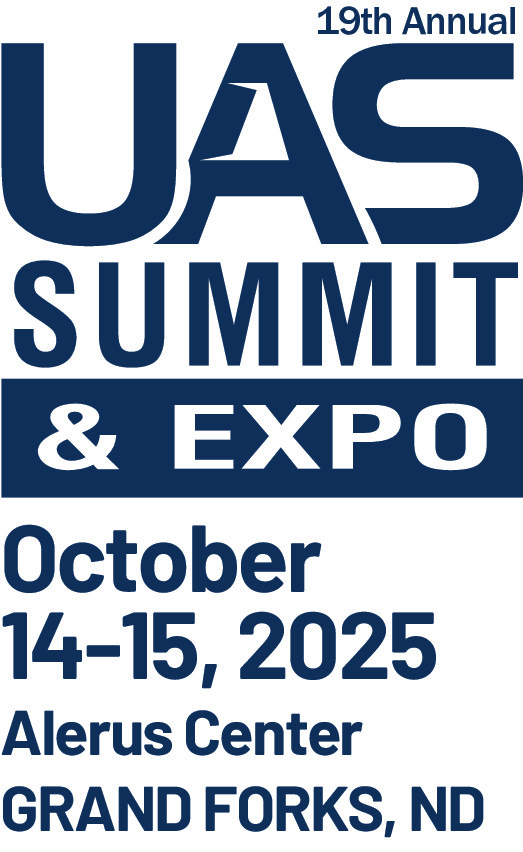
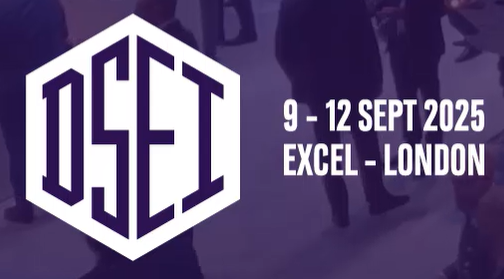
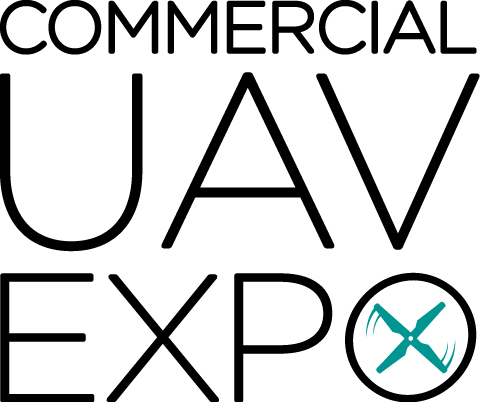
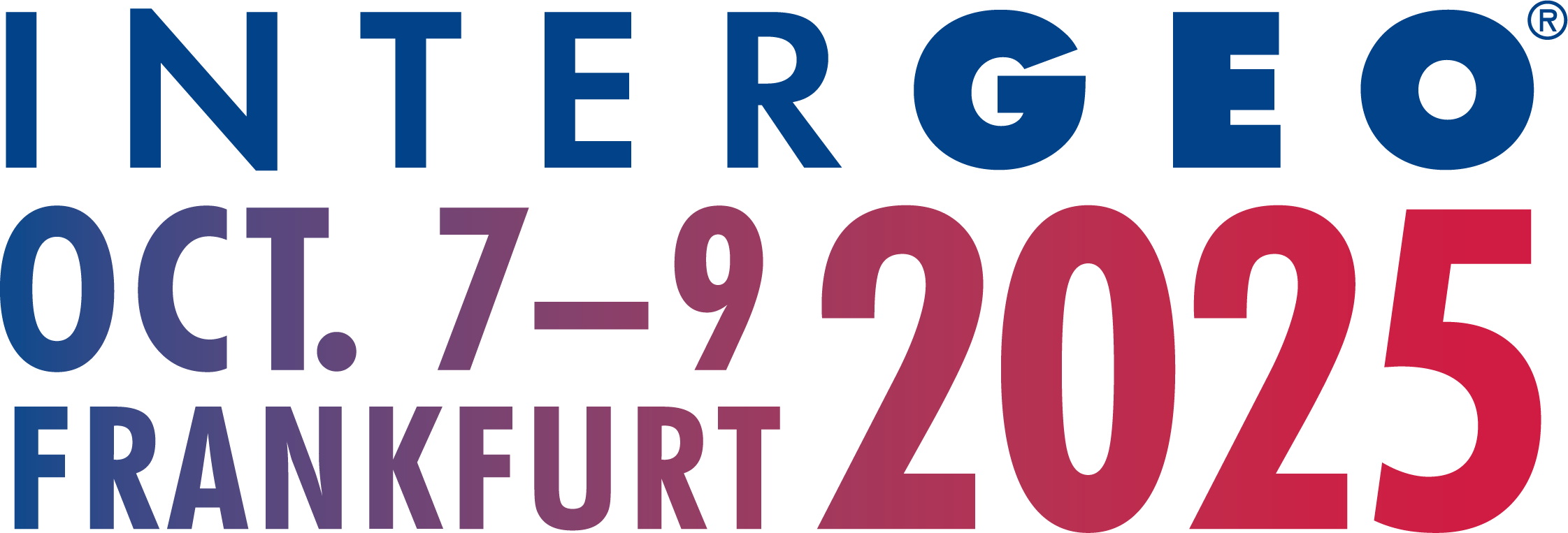
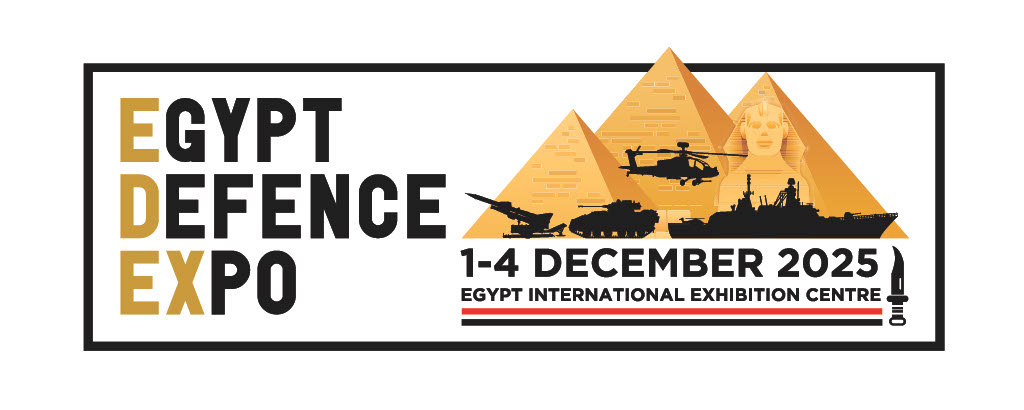
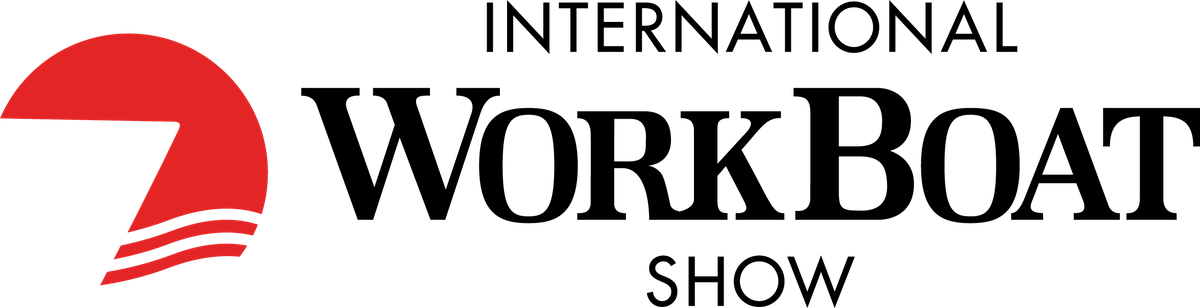
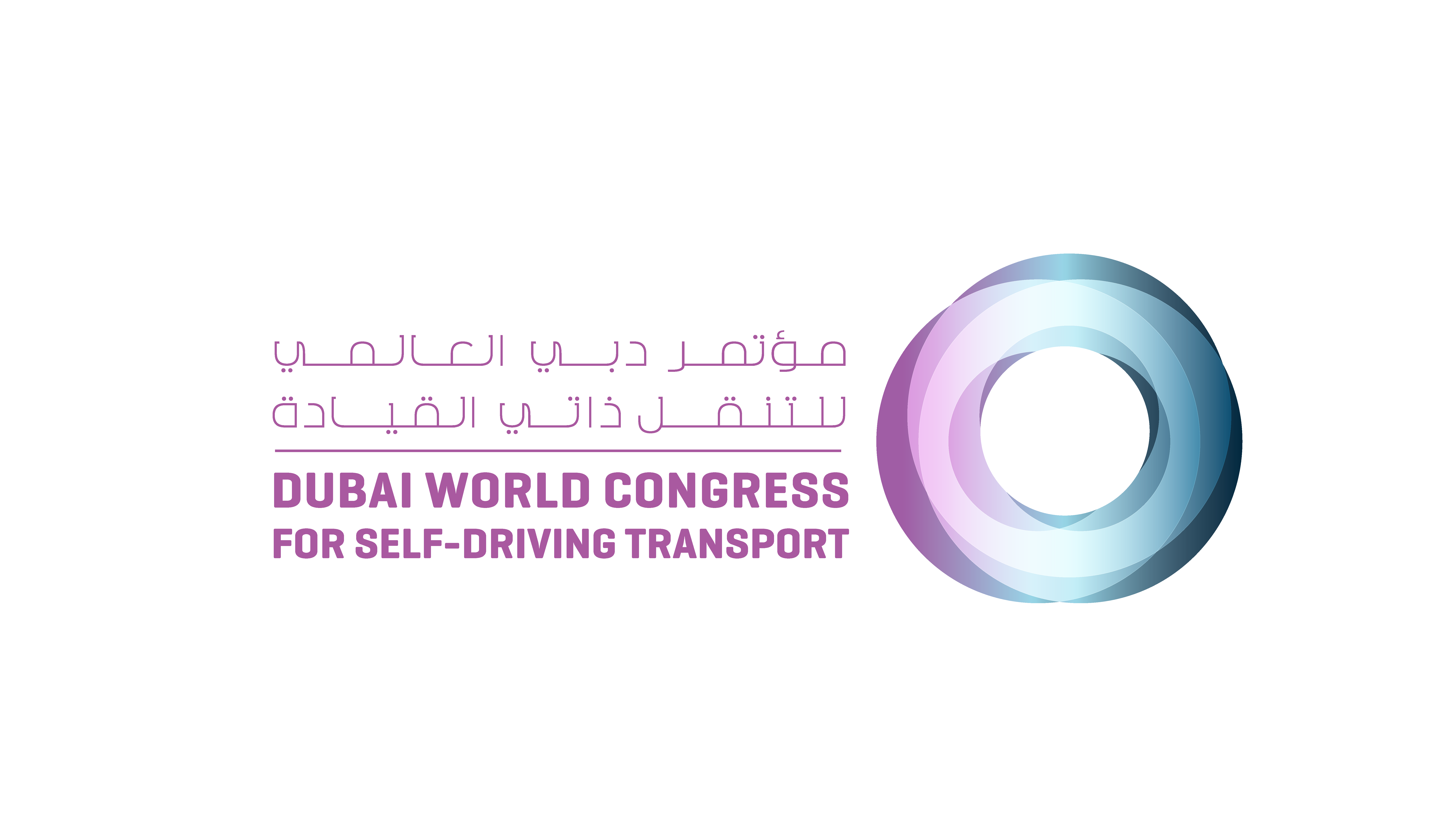
