IAC AV-21
Racing certainty
The Indy Autonomous Challenge has created a hotbed for advances in uncrewed vehicle technology, as detailed by Rory Jackson
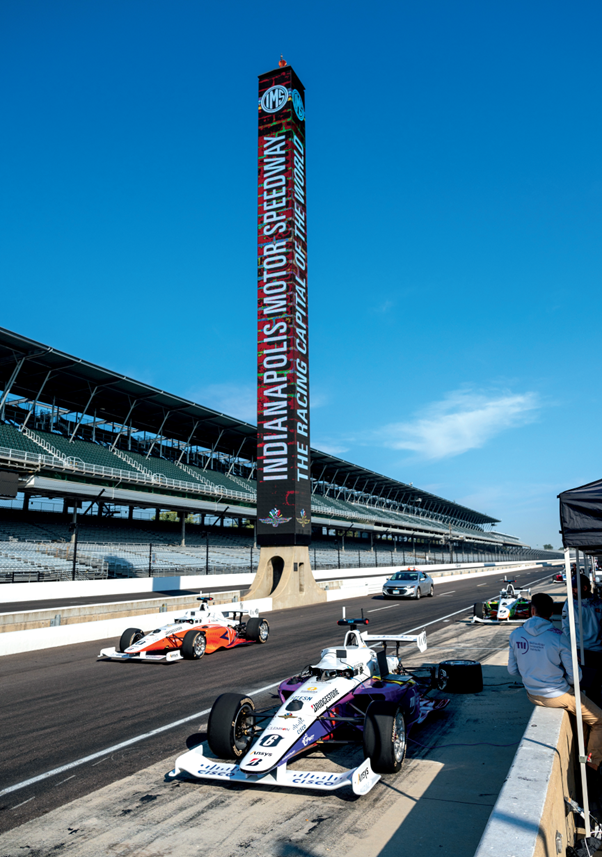
(Images courtesy of IAC unless otherwise stated)
Competitive motorsport has, for over a century, motivated countless innovations that have filtered through to safer, more comfortable and more efficient automotive solutions. Small wonder then that many of the world’s major vehicle OEMs, transport authorities and industry stakeholders advocate investment and engagement in motorsport as a means of achieving industrial and engineering advances.
That knowledge was what motivated the state authorities in Indiana to meet with the heads of the Indianapolis Motor Speedway (IMS) and the Energy Systems Network (ESN) in 2017. The groups sought to brainstorm how the IMS’ history and recognition, together with the Indianapolis motorsport industry, could be used to foster a new wave of advanced technology development in Indiana.
As electric racing was already the province of Formula E, the groups instead felt they ought to focus on autonomy, which they agreed was the next breakthrough in automotive innovation.
Investigations into past prize competitions aimed at encouraging autonomous innovations followed, particularly the DARPA Grand Challenges of 2004 and 2005. By 2019, Indiana, the IMS and ESN had begun talking with a range of universities as prospective competitors, and companies who might be sponsors, partners or suppliers.
Discussions with universities also established what the general state and focus of driverless autonomy projects were, and therefore how to regulate an autonomous racing contest to ensure a fair and achievable competition.
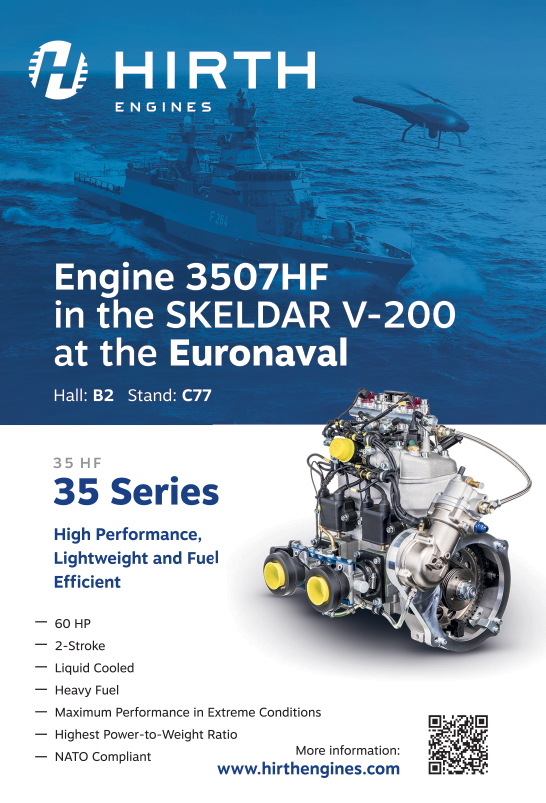
So it was that in May 2019, just days before the Indy 500, a workshop of 30- 40 industry, academic and government organisations gathered to design and format a prize competition that is now known as the Indy Autonomous Challenge (IAC).
As Paul Mitchell, president of the IAC (and president and CEO of the ESN) recounts, “That workshop defined the blueprint for the rule sets we have now. For instance, it was decided early on that we would standardise the race hardware – teams would not build their own racecars.
“That was very unlike the DARPA contests. Those events saw experimentations with autonomous Hummers and motorcycles, and Stanford University won in 2005 with a modified Volkswagen Touareg. But you can’t really do that with racecars. One, it’s not easy to fund and build a racecar; and two, it’s not safe to run a bunch of them at the same time on a track when they’re operating on self-driving software stacks.
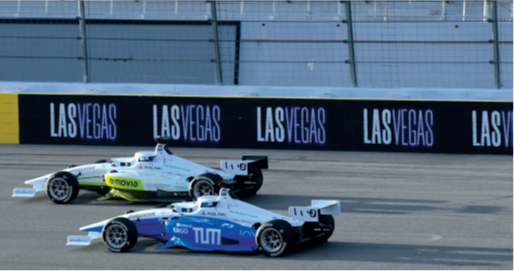
“So we determined that, at least in these early years, the competition should focus on the software elements of autonomy.
The teams would be responsible for the software driver that would pilot these vehicles, and the vehicles would be fixed with a common hardware set-up. So not only are all the teams using identical machinery but everything from tyre pressure to downforce has to be common across the board.”
The machinery takes the form of the AV-21, a racecar issued with all the necessary subsystems for autonomous navigation, path-planning and collision avoidance. It is an open-wheel, single-seat vehicle with the front wing, rear wing and sidepods typical of IndyCar and Formula racing. It is 4876 mm long, 1930 mm wide (with a 2971 mm wheelbase), 1156.5 mm in height and has a kerb weight of 726 kg.
Rather than being a blank-sheet design, it is a modification of the standard-issue chassis for Indy Lights, the NTT IndyCar Series feeder championship, much like Formula Two and Three are to Formula One. It has been developed in collaboration between Parma-based Italian constructor Dallara Automobili and Dallara USA in Speedway, Indiana.
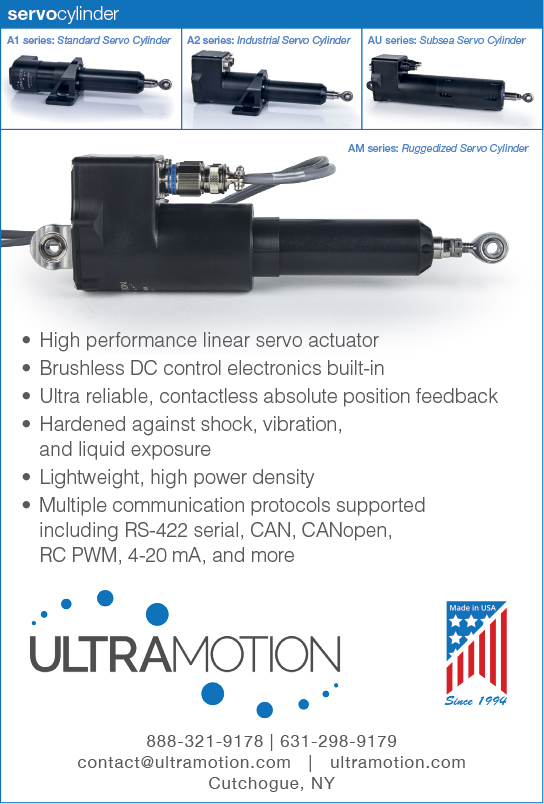
With the backing of industry and academia, the IAC was officially announced in October 2019, with a $1 million prize up for grabs. The first real-world on-track testing began in spring 2021, using AV-21s supplied to teams that made it through an initial all-virtual competition, in which their software algorithms competed in simulated races.
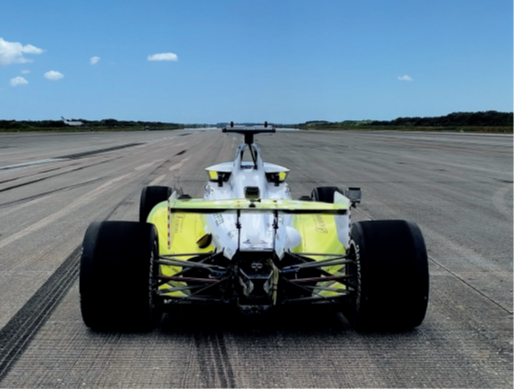
At the time of writing, the IAC had hosted nine teams formed through 21 universities from around the world. The first official live racing event took place in October 2021, with teams competing on the basis of time trials at IMS, in which TUM Autonomous Motorsport from the Technische Universitat Munchen emerged as the winner.
In January 2022, as part of CES, the IAC held the world’s first head-to-head driverless race, debuting a wave of innovations in autonomous highspeed passing which, along with the $150,000 grand prize, was won by Team PoliMove, representing the Politecnico di Milano and the University of Alabama.
These, combined with setting the world autonomous land speed record of 192.2 mph (309.3 kph) during AUVSI Xponential in April 2022 and spinning out the autonomy start-up drive blocks from TUM, have cemented the IAC’s mission to foster innovations in driverless systems through motorsport.
To better understand the systems at the heart of these innovations and competitions, we present here a deep dive into the AV-21, and the many high-end technologies that have been integrated together in and around its chassis to make it one of the most powerful tools in existence for pushing the limits of intelligent autonomy.
The AV-21’s development history
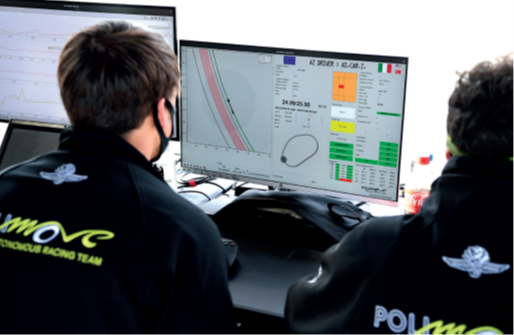
Although based closely on the IL-15 chassis, creating the AV-21 was not a simple copy-and-paste exercise but a complex process that depended on several key commitments.
The first came in the summer of 2019 from Clemson University, which as Mitchell explains has a programme in its Department of Automotive Engineering that poses a prototype vehicle design challenge to a cohort of graduate students each year.
“They’ve done projects for many of the major automakers – for example, a reimagined BMW Mini – but in 2019, Clemson decided it would develop the blueprint for the IAC race vehicle,” he recounts. “That was really helpful, because the students were able to continually run and advance that programme from autumn 2019 through to spring 2021.
“That freed us up to engage with industry leaders like Luminar and others, who would later become our most valued suppliers and whose hardware was essentially being designed into the form factor of a racecar by the Clemson University team.”
The IL-15 was chosen because it has a format familiar to the crews and technicians at IMS, one that would draw eyes more readily than stock cars and sportscars. That encouraged Dallara to collaborate with Clemson, the former providing the chassis, aero and NVH work, and the latter providing expertise on designing, sourcing, integrating and planning powertrain modifications and autonomy-related sensors and computing.
Dominic Coffey, design engineer at Dallara USA, says, “We started in April 2020 by exporting the CAD files of the IL-15 to Clemson’s people, including the monocoque, suspension, parts of the drivetrain we could supply, and aerodynamics models they could use.
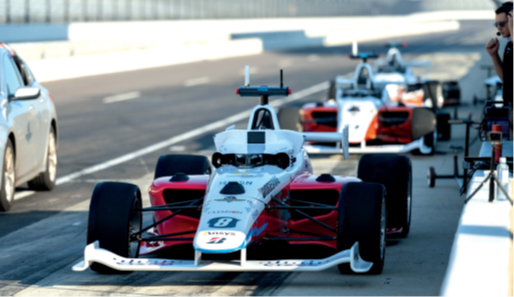
“Before long, we were having a weekly drivetrain development team meeting, a systems integration team meeting, an electronics meeting and so on with Clemson. We’d review their designs, and coach them on what might work or not – particularly in terms of installation and maintenance – to arrive at a solution that satisfied all the engineering requirements.”
Autonomous racing requires very specific features that can be quite different from traditional motorsport, according to Dr Robert Prucka, who was faculty lead for Clemson’s role in the project and is Clemson University’s Kulwicki endowed professor in motorsport engineering.
“We swapped the stock AER engine for one from Honda to better meet autonomous racing requirements,” he says. “One interesting target was that we wanted the vehicle to operate at the lowest ground speed possible, which is opposite to traditional motorsport engineering but critical to start mapping out a new track safely.
“We built a function to replicate a low-speed ‘track walk’, just like professional drivers do before a race. The AV-21 has a minimum speed of around 19 mph without slipping the clutch, about 50% lower than what would have been achieved with the original engine. That forced us to investigate engines with low valve overlap without sacrificing a lot of peak power.
“The engine also has to be incredibly reliable and tolerant of operating without pre-heated oil and coolant, since we knew there would be many quick stops and starts as teams developed their algorithms. We did not want an engineer to have to accompany each engine at all times, so the teams have maximum flexibility to develop their vehicles on their own timelines.”
By autumn 2020, with some consultation along the way from AutonomouStuff, designs were being finalised and approved for manufacture so that first integrations of critical components such as the drive-by-wire systems from Schaeffler Paravan could be performed.
“The bellhousing, which connects the gearbox to the engine, was another crucial manufacturing focus, and we designed it from scratch because we opted for a non-standard engine,” Coffey explains. “The IL-15 comes with an AER turbocharged four-cylinder engine, but we chose a Honda four-cylinder instead, so engine installation took a lot of attention.”
Initial builds started in spring 2021, with the first fire-ups at Juncos Racing’s facility in Indianapolis in March, and the official AV-21s started to be assembled and finalised soon after. The first test run of the AV-21 took place around the end of March, with deeper, extended track tests taking place through to the autumn in the lead-up to the first official IAC race at IMS in the October.

Meanwhile, the teams’ software development ran in parallel with Dallara’s and Clemson University’s vehicle development. They began programming using the initial AV-21s directly at the Juncos facility in May 2021, with algorithmic refinements continuing through the summer. This approach gave the teams the freedom to code and iterate with their own individual vehicles.
Mitchell says, “Initially, some teams had to share vehicles, but that actually led to a lot of collaborative troubleshooting between them, and between them, us and Dallara. That in turn led to breakthroughs in hardware and software engineering that were key to the car being capable of higher and higher speeds autonomously.
“By August, the AV-21s were running autonomously at IMS at 100-plus mph, and their capabilities progressed exponentially beyond that month by month, not just in terms of safe speed limits but proficiency in steering, braking – and, by January this year, passing as well.”
Most recently, the racecar has had an engineering ‘refresh’ of several of its subsystems, mainly the powertrain and software components.
The AV-21’s anatomy
The biggest architectural changes on the AV-21 versus the IL-15 were made to accommodate sensor mountings and to perform throttle, steering and braking by wire.
“The throttle was relatively easy to change, as it’s just computer-controlled, but the steering rack had to be modified to accept the Space Drive from Schaeffler Paravan, which also provided the brakes, run – as is standard on the IL-15 – along with a crank arm and motor for electronically actuating them,” Coffey says.
“As you move back in the cockpit, you find AdLink’s board for edge computing, Luminar’s Lidars, the GNSS antennas mounted on top, and radars on each side. Beneath those is a fire extinguishing system that’s been useful for safety reassurance, especially regarding the batteries, and the main autonomy computer systems are mounted on top of the batteries and extinguishers.”
In addition to the cockpit housing the side and forward radars, as well as the Lidars (three each), six cameras here provide for additional object and colour awareness, and one GNSS antenna mounts into the skin of each sidepod (with some work going into mounting them aerodynamically) with the other two GNSS antennas atop the roll hoop.
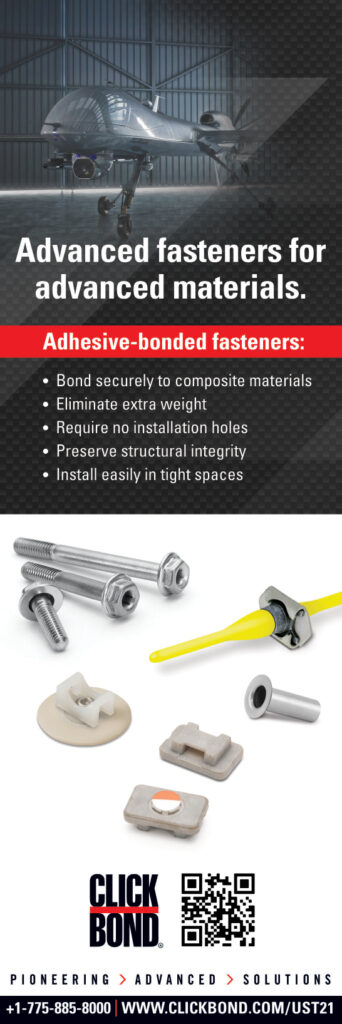
Behind the cockpit is the Honda engine. Coffey notes that this was supplied and essentially remanufactured by 4 Piston Racing, in Danville, Indiana, with Dallara doing considerable work to insulate it given that the car was originally designed for the housing and NVH of a significantly different power unit.
The Clemson team and their partners positioned these systems to minimise blind spots and to allow redundancy with multiple sensor types. A primary goal of the vehicle’s design was to make sure that no single team gained an unfair advantage through the perception systems chosen. To achieve that, engineers made sure the sensing modalities – that is, Lidar, camera, radars – had overlapping fields of view, so that teams could choose to use the sensors that best aligned with their experience.
A centrifugal clutch system is fitted behind the engine shaft, and is the reason the car has been able to operate without a clutch pedal. It is similar to a torque converter and had previously been used in an IMSA (International Motor Sports Association) Series. Behind it is the stock gearbox.
This clutch achieved multiple objectives for the vehicle. Not only did it greatly simplify the control of vehicle launches from the pit area, but its compact size allowed for the newly specified engine to be slightly longer than what the vehicle was initially designed around. That produced significant cost savings and made the vehicles easier to operate.
Mitchell adds, “All these systems are proven in modern automotive vehicles, and it was all possible because industry stepped up to sponsor us – some of our suppliers have contributed six-to-seven figures’ worth of equipment to the programme.”
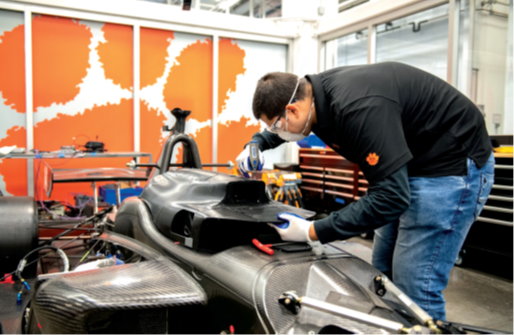
(Courtesy of Clemson University)
Structure and materials
Given the attributes of the Indy Light chassis in terms of strength, aerodynamics, downforce and so on, the AV-21 shares much in common structurally with it. The ‘safety cell’ (a misnomer given the absence of a driver) is a composite structure consisting of two carbon fibre layers sandwiching an aluminium honeycomb core, while additional aluminium bulkheads sit fore and aft of the tub shape. A pedal bulkhead sits at the front, while a dash bulkhead sits just inside the cockpit cover.
The monocoque and nose are made with essentially the same materials and bulkheads, as is the rear attenuator where the rear wing mounts. The bodywork itself is carbon fibre with a cloth core material – Coffey comments that this is a system called TNT400, and likens it to a black cotton. It sits between the carbon fibres as they are cured, after being wicked with resin.
Mitchell notes that on top of achieving the right structural strength, aerodynamics and NVH characteristics, integrating all the sensors inside the cockpit of a pre-existing racecar without having them come loose, become misaligned or break during autonomous operations at 190 mph was a challenge that no other team has undertaken.
Especially important to tackling that was the cockpit cover, which represents the largest focal point of Dallara’s custom body work on the AV-21. This had to enclose the various sensors used for real-time navigation and path-planning without ruining the aerodynamics of the car.
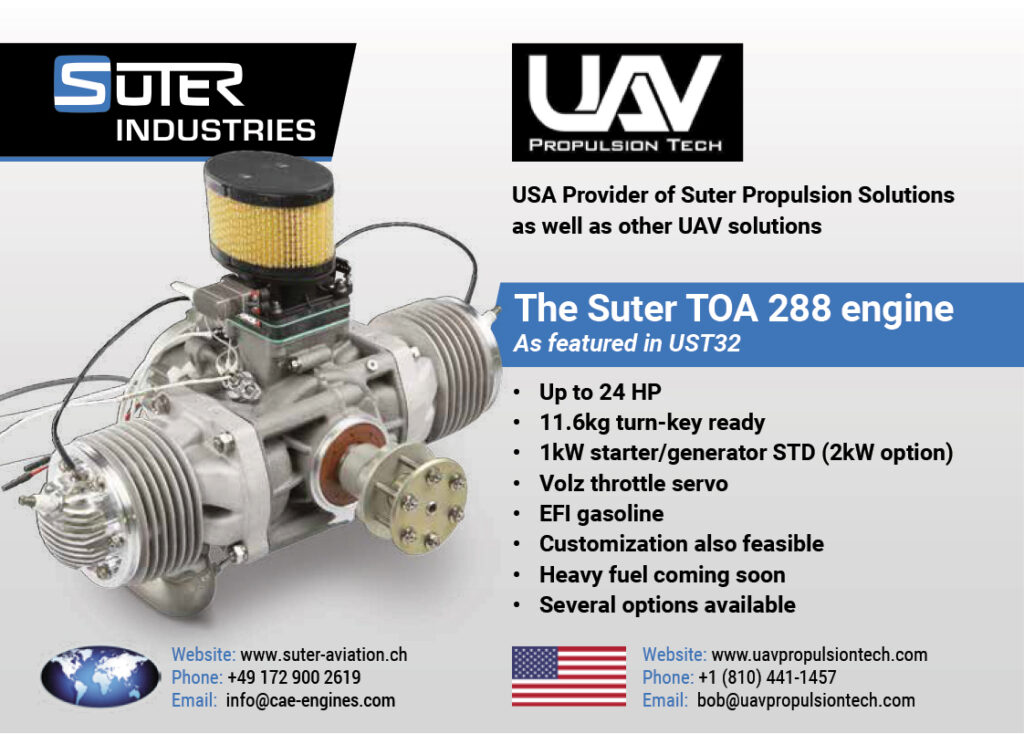
Of the cover, Coffey adds, “We worked very closely with Clemson University to make the cover both rugged and easily serviceable. Ideally, we, the suppliers and the teams would prefer to ‘set and forget’ the electronics, but that turned out to be impossible, so we had to do a lot of work between tests and races that required popping the top off.
“To integrate the GNSS atop the roll hoop, we bought some carbon aero fairings and made a whole assembly out of that, which turned out as a very elegant solution to mounting all those parts securely and aesthetically. And once all the navigation systems were located, Clemson made an aero surface in CAD to go on top of them, with a lot of CFD work from our aero department in Italy going into optimising that for manufacture.”
The structure also includes a support strut under the forwardmost Lidar to retain the cockpit cover at higher speeds. It is visually reminiscent of the FIA halo, but is positioned and designed carefully to avoid impacting the Lidar’s FoV. “All these modified structures that are unique to the AV-21 are made like the bodywork: carbon fibre sandwiching TNT400 as a core,” Coffey adds.
In addition, the GNSS mounts on the sidepods and the front of the monocoque are multi-jet fusion-printed using PA12 Nylon, as are the mounts for the side radars beneath the cockpit cover.
Navigation systems
Of all the navigation sensors on board the AV-21, Lidars are generally the most important in terms of sensing critical data for decision-making. Mitchell says, “Right now, our use of cameras is limited at higher speeds.
“Part of the reason for that is the computing time taken to communicate and interpret camera data, and hence make an optimal decision based on it. The efficiency of the Lidar at high speed is crucial to that. The radars meanwhile are especially useful for measuring the radial velocity of objects around the car.”
The six cameras used are Mako G-319Cs with a maximum resolution of 2064 x 1544, a spectral range of 300 to 1100 nm, and a maximum frame rate (at full resolution) of 37.6 fps.
The side radars are Aptiv MRRs with detection ranges out to 40 m and range rates accurate to ±0.3 m at a 30 ms
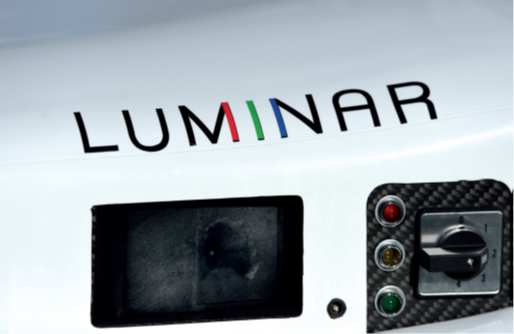
update rate, while the frontal radar is that company’s ESR 2.5, which measures up to 174 m ahead of the vehicle and updates every 50 ms.
Positioning, velocity, and attitude (heading, pitch and roll) estimates for navigation and control are produced using VectorNav Technologies’ VN-310 dual antenna GNSS/INS (with two being used for redundancy). Its VN-310 RTK positioning solution is also used, owing to its ability to enable centimetric accuracy.
Mitchell says, “VectorNav may be best known as a supplier to aerospace customers, but the robustness and precision it manages at high speeds works great for our racecar. At high speeds and harsh environments, there’s great cross-compatibility between aerospace and road technologies.
“As another example, Luminar’s been a great supplier to us and to automotive OEMs, but they’re also working with Airbus on Lidar for helicopters right now. So there’s great potential to be realised by the autonomous and assisted-driving and -piloting worlds talking together.”
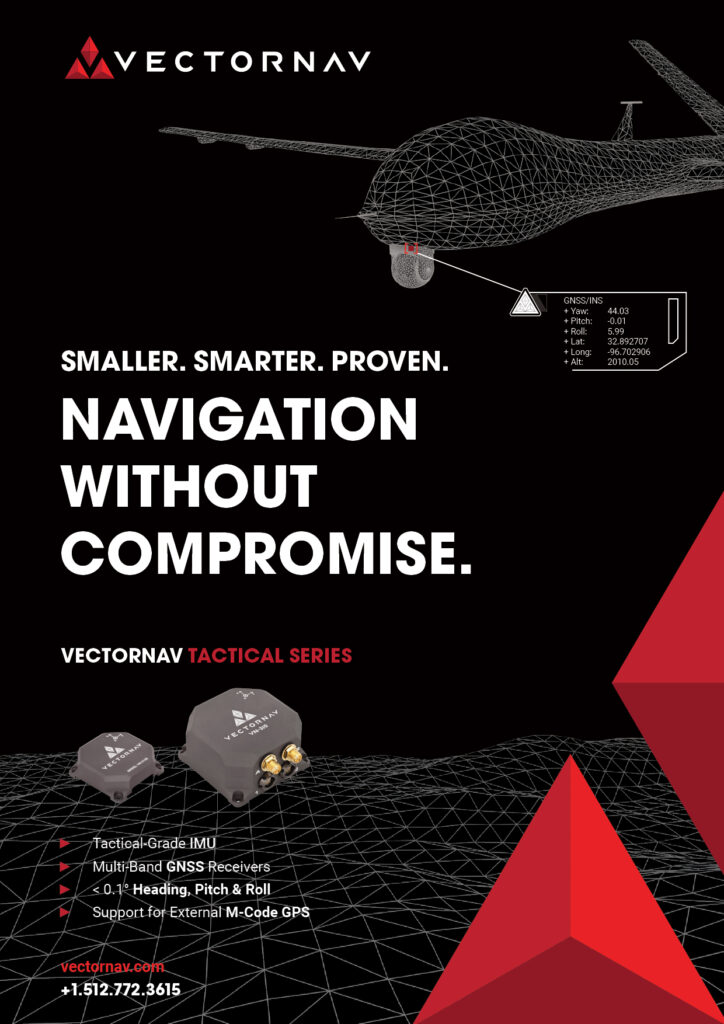
The Luminar sensor is the Hydra H3, a 1550 nm time-of-flight Lidar with a maximum detection range of 500 m, range precision accurate to 1 cm, a 120º horizontal FoV and a scan rate of 640 lines/second.
“The Lidar range requirement was determined by the need to sense an object on the track in time to perform a double lane change and hence avoid a crash,” explains Dr Prucka. “As the vehicle travels at nearly 85 m/s, the system needs to be able to see about 250 m ahead of the vehicle at all times.”
Aaron Jefferson, vice-president of product at Luminar, recounts, “We saw the IAC early on as this perfect incubator for new STEM innovation and graduates, as well as the kind of proving ground for our product. It’s high speed but controlled, and it reveals if or how the units might perform as we believe they do.
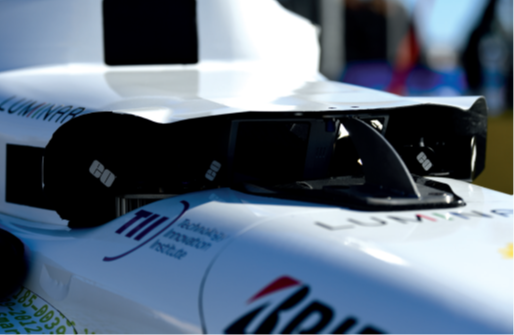
“Lidar has been around a long time, but until the IAC came along, there’d not been a great degree of trialling Lidars for automotive applications. High-speed mobility in particular was still a highly untested field, so our CEO didn’t hesitate when offered the opportunity to have our technology in the AV-21.”
Although the teams are given the same hardware, they are responsible for their own use of the Lidar from a software development standpoint, and how its data is ordered and fused with that coming from the cameras, radars, GNSS and IMU. Mitchell adds though that teams took different approaches early on in terms of whether the Lidar was merely a companion sensor to quantify what the cameras and radars saw, or whether it was a lead sensor driving decision-making.
“When we started in October 2021 at IMS, the teams weren’t ready to do passing, but we put large pylons on the track to force them to do obstacle detection and avoidance in a kind of autonomous slalom,” he explains. “That forced them to show they could use Lidar, although theoretically they could have done it with just camera and radar.
“As soon as we got to vehicle-to-vehicle passing though, the Lidar became absolutely essential, and Luminar’s tech was crucial to providing high-speed data and a form factor compact enough to fit into a race cockpit.
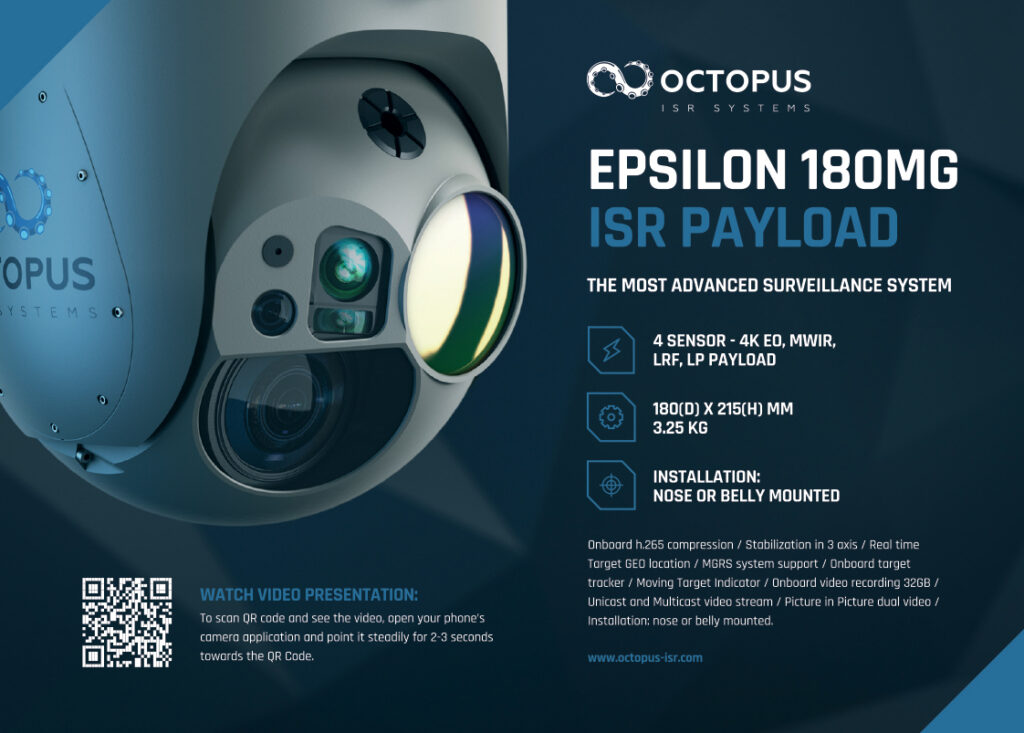
You can’t have a large, rotating device like a Lidar hanging off of a racecar doing 170 mph, it needs to be built into the skin of the vehicle. Lidars have to fit into the aerodynamic and aesthetic profile of production vehicles too, and they have to be capable of handling very high speeds and vibration.”
As an automotive-grade Lidar, the Hydra H3 has been designed to optimise resolution at range, to prevent different types of road accidents. To function accordingly, Luminar chose an architecture that combines a spinning polygon mirror with a vertically tilting mirror in order to direct the laser towards areas of interest as needed.
“The architecture and design of the sensor is key to getting the range we need with the 25 W power consumption we have, and the FoV means three of them can cover 360º around the vehicle so they can determine out to 200 m if they have free space for any kind of manoeuvre,” Jefferson notes. “You might not need that on the track – even at 180 mph, or 80 m/s, you have room to manoeuvre in less than 200 m, but there’s no minimum in terms of seeing something adjacent to the car.”
The laser itself is a Class 1, eye-safe beam. It has a 26º vertical FoV and a 120º horizontal FoV for producing 3D data on where objects are, how far away, how quickly they are being approached, and what road and lane boundaries there are.
Data on these and other factors is output in a format designed to ensure the teams can use the sensor effectively for path planning and decision-making in real time.
“The Hydra sensors are expensive, but we felt it was really worth donating them to the IAC,” Jefferson says. “While the pylons [Mitchell] mentioned were actually pretty huge, if we’re to safely achieve faster speeds and more kinds of passing in the future, we need to be able to recognise something as small as a tyre, a slick or a part that’s fallen off one of the other cars.”
Onboard autonomy and computation
As announced in October 2022, as part of the AV-21’s recent technology refresh it has been upgraded to use the Autera from dSpace as its main computer, the primary reason for the upgrade being some connectivity issues that could not be resolved through the previous computer.
The Autera has also been designed specifically for users engaging in data driven r&d for autonomous driving applications – another factor making it a good match for the teams – logging up to 50 Gbit/s onto a 64 Tbyte storage drive. Its CPU is a 12-core Intel Xeon for up to 24 GHz clock speed, and sufficient space for 32-512 Gbytes of RAM.
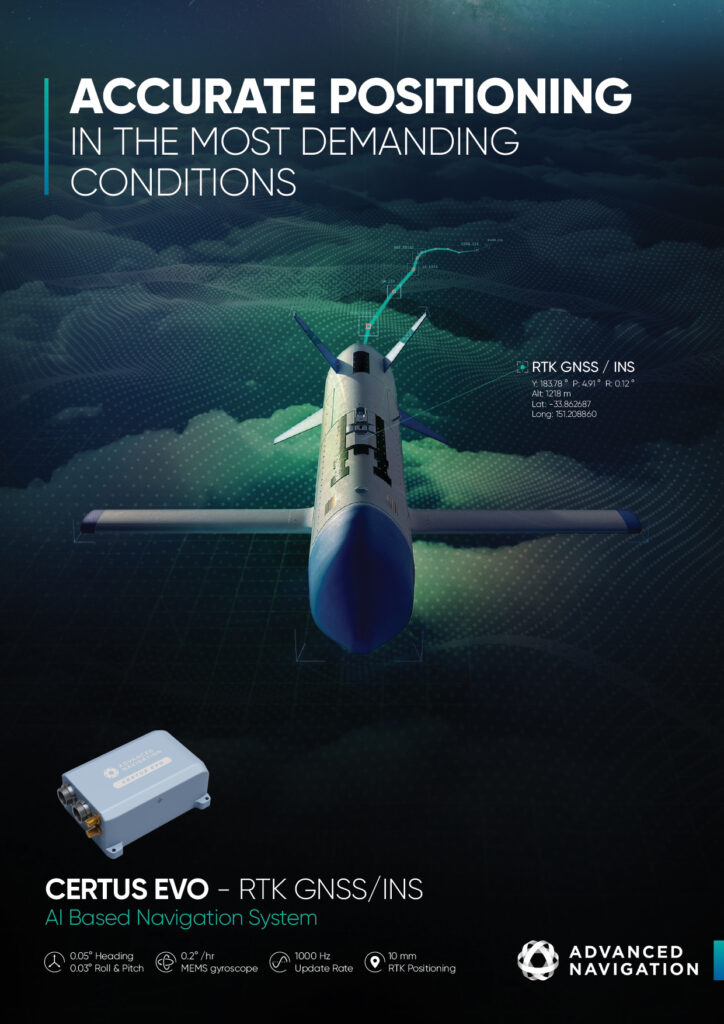
It features two USB 3.0 ports, two for USB 2.0, four for 10 Gbyte Ethernet and another four for 1 Gbyte Ethernet, with several additional multi-I/O channels and one for audio, covering the gamut of sensor data feeds needed to qualify as an autonomous driving computer. It also comes with slots for CAN FD, as well as interfaces for the different Ethernets’, raw data, and additional GPUs or FPGAs as hardware accelerators.
And for surviving high speeds and vibrations, the system is tested to the EN 60068-2-6, EN 60068-2-27 and EN 60068-2-64 standards for shock and vibration. It is sized at 330 x 376 x 156 mm and functions on 10-30 V supply inputs.
Also, the GPU is an Nvidia Quadro RTX 8000 with 4608 cores, 96 ROPs and 48 Gbytes of onboard memory.
“Outside of the main computer, on the low-level controllers’ side, we made a number of operational changes that helped our teams in two key ways,” says Andrew Keats, technical operations manager at the IAC. “One was to speed up their turnover of the car, because normally you have to shut the whole thing down and bring it back up between updates, but with our controller changes that’s no longer the case. The other was that they now get so much more data from the engine control unit and its lower-level sensors that they didn’t have before.”
Mitchell adds, “That turnover improvement was also critical because we have way more practice days than most motorsport – at least 10-20 track days per team – and renting the track plays hell with teams’ budgets, so
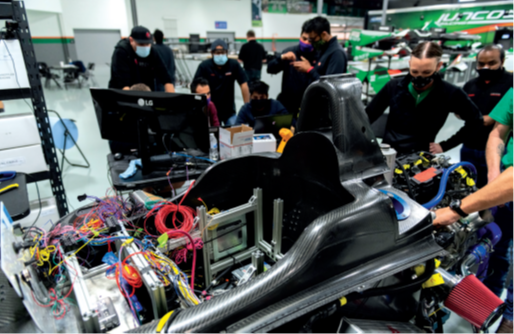
(Courtesy of Clemson University)
maximising uptime is everything to them.”
As for Schaeffler Paravan’s Space Drive drive-by-wire system, it is triple redundant and supplies peaks of 60 A per motor controlled (30 A continuous), with a cycle time of 10 ms. As well as having two CAN bus interfaces, two FlexRay ports and two LIN bus interfaces, it also has a DTC connector for automotive diagnostics and eight digital I/Os, two of which have timer functions.
According to Dr Prucka, “These systems incorporate a separate electrical circuit and several levels of redundant sensing to make sure the vehicle will stop in case the autonomous systems fail or the vehicle loses communication with race control.”
Connectivity and comms
Also key to control is New Eagle’s Raptor software platform, which Keats explains is vital to both safety and general operation of the full system. “It includes and controls a switch that has several stages to power-up different levels of the system,” he says. “It also has a program on the back end where race control goes through to access the car, which is quite standard for a lot of racetracks.”
Dr Prucka adds, “The New Eagle system continuously checks that all the other electronics are communicating, and it can take over control to perform an emergency shutdown if the vehicle loses contact with the autonomous computing system.”
The main transceiver on the car is Cisco’s URWB (ultra-reliable wireless backhaul) FM4500 MOBI, which transmits and receives at 5.1 to 5.8 GHz as well as at 4.9 GHz with OFDM modulation. It is built around an 880 MHz CPU, a 2 x 2 MIMO array and two Ethernet ports, and supports roaming connectivity on vehicles moving at up to 225 mph.
Of the URWB’s selection, Keats notes, “We went with that partly to have our own fine control over the network. The problem with 5G right now is that consumer-grade systems aren’t that reliable, and industry-grade is still prohibitively expensive, but the FM4500’s fluid mesh allows us great flexibility with the stationary infrastructure we set up at the track to enable constant telemetry between the cars and the teams.”
Mitchell adds, “It’s an ultra-low latency wi-fi system, which can even be used for vehicle-to-vehicle comms. That can be important in some approaches to road autonomy, although we have yet to go with a high data load configuration for things like live video streaming. Small data packets are all we need for control and data telemetry.
“We’ve tried different 5G systems, but we found that performing smooth handoffs between our antenna towers was a real challenge with 5G. So the Cisco system works great for now.”
Powertrain and drive
The drivetrain has received the most attention throughout the IAC’s technology refresh in the lead-up to the next race.
The AV-21’s K20C engine is a 2.0 litre four-stroke built largely from aluminium, spark-ignited, turbocharged and featuring four cylinders, each with an 86 mm bore and 85.9 mm stroke. In standard configuration it provides up to 306 bhp continuously (228 kW, although during PoliMove’s record run the engine sustained a 500 bhp peak) at 6500 rpm. It has a 9.8:1 compression ratio, and maximum torque of 400 Nm is achieved at 2500 rpm.
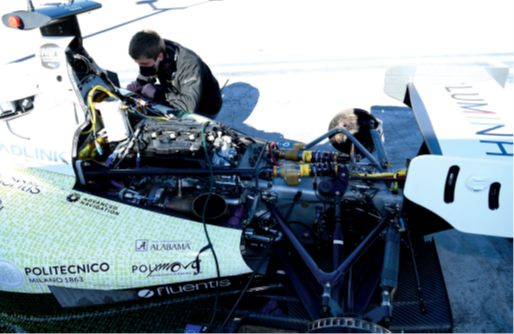
“For this season, we put a bigger turbo on the car that will give teams an extra 100 bhp, along with a different fuel pump that raises the capacity of fuel we can send to each cylinder,” says Keats. “That means in total the AV-21 now puts around 473 bhp at the wheels.”
The engine forms a stress member and hence a structural part of the car, with the only real dampers being in the suspension, limiting the extent to which engine noise can be filtered out. That had a great bearing on how the IAC’s partners and teams immunised their sensor data inputs. “That’s a key part of how this application pulls out and resolves edge cases that appear only sporadically at best in commercial or consumer vehicles,” Keats says.
Although changing the engine from that in the standard IL-15 car meant making considerable adjustments to the K20C to fit it into the structure and resonances of the AV-21, the IAC still chose the new engine, primarily because it made for far easier maintenance and servicing than the old one. That was a critical factor in checking
and replacing the cable harnesses for the sensors and controls that are key to safe autonomous driving, in addition to being slightly less expensive and not particularly different in speed and power.
Coffey says, “The changes to the K20C included switching to a dry sump, as that made for a flat oil pan fitting under the engine that attaches to the monocoque, with an oil tank and reservoir system off the front of the engine. That switch also ensured a similar overall powertrain weight to that in the Indy Lights car.
“Then we built a trunnion to connect the gearbox and bellhousing to the monocoque, above the engine, as well as an aluminium bracket to connect the front of the K20C to the monocoque. It’s similar to installations used in some Formula series.”
He adds that the dry sump is 7075 aluminium, the engine bracket is 6061, and the trunnion is 4130 steel. “We initially drew all of them in CAD, although for the trunnions we first installed one on the car and used it as a weld-jig, before building a weld-jig off that and then using it to make parts that matched for all the cars.”
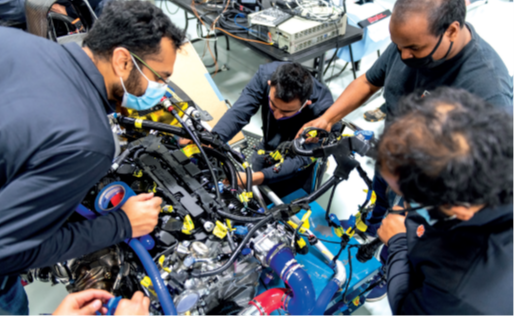
(Courtesy of Clemson University)
The air intake is located on the left side of the car, as is the intercooler, which required some redesign, as the K20C’s throttle sits on the right, and now the intake plumbing runs through the bellhousing. More recently, the engine cover has been redesigned to make room for the bigger turbocharger.
Engine control (including throttle and shifting) takes place through the Motec ECU, which Keats comments is a particularly flexible COTS unit used in vehicles from street cars to professional racecars, which teams could therefore use to design their data flows and engine management strategies according to their preferred approach.
Also, during dynamometer testing, the IAC’s engineers carried out a lot of programming through the ECU to flatten the torque curve and hence make the powertrain handle more like the electric UGVs and road vehicles most of the teams were more familiar with.
“And for autonomous gear shifting, the ECU tracks the efficiency and where in the power band the engine is running, so that teams don’t have to dig in and calculate it for themselves using the CPU,” Keats says.
The transmission is the IL-15’s stock six-speed sequential arrangement made by Ricardo. The Clemson University team selected gear ratios that would allow for good vehicle performance over a wide range of ground speeds, since achievable racing speeds were completely unknown when the vehicle was being designed.
When a gearshift is requested, the engine controller manipulates the engine throttle plate simultaneously with a pneumatic shift solenoid to automate the process in less than half a second.
And while the stock fuel systems are used, the battery system is a lithium-ion racing pack from Braille that runs through a DC-DC to supply power to the computers and sensors. “Originally we had a set-up of four lithium-ion race packs at the bottom of the chassis, but using only one keeps it simple and lightweight, and it works just fine for the electronics,” Keats says.
Future plans
Despite PoliMove having hit the 192.2 mph record earlier this year, the IAC anticipates the AV-21 achieving 200 mph eventually, with particular benefits expected to follow for the commercial automotive world.
“Getting full autonomy to work on highways has been a major technological bottleneck for years now, but if you can achieve full autonomy at speed, you can increase the safety and efficiency with which freight and people are moved across a country,” Mitchell says.
“With the software intelligence and speed our teams are unlocking, and the massive body of data we’re filtering back to our subsystem providers, we’re confident of uncovering ways to achieve commercial autonomy at 70, 80, probably 100 mph in the near future. We’re going to keep refreshing and enhancing the car each year, as it’s important that we gather and evaluate data using cutting-edge systems and technologies.”
Beyond this, the IAC anticipates future versions of the AV-21 – most likely an AV-24 in 2024 at the earliest – continuing the teams’ investigations into how new automotive and powertrain technologies can be used in autonomy stacks.
These include the interaction between autonomous drivers and aerodynamics, low-carbon propulsion systems and high-voltage switching systems.
“A lot of that is also not very different scientifically to the new world of eVTOL UAVs, air taxis and autonomous helicopters,” Mitchell says. “We are proving out a lot of new tech at ground speeds that also need to be proven safe at high airspeeds, so it’s interesting to watch how discussions evolve between our worlds and theirs.”
As of September 10 this year, the teams participating in the race have begun on-track testing, with the second official IAC race event due to take place at the Texas Motor Speedway on November 11 and the next head-to-head autonomous challenge confirmed for January 2023 at CES.
Some key suppliers
Chassis: Dallara
Vehicle assembly, test and maintenance services: Juncos Racing
Early systems integration consultation: AutonomouStuff
Engine: 4 Piston Racing (remanufactured Honda Performance engine)
Battery: Braille
Cooling systems: PWR
Lubricants: Valvoline
ECU: Motec
Engineering development tools: New Eagle
Drive-by-wire systems: Schaeffler Paravan
Anti-stall clutch: ZF
Transaxle: Ricardo
Tyres: Bridgestone
GNSS-IMU: VectorNav
Cameras: Allied Vision Technologies
Lidar: Luminar
Radars: Aptiv
Networking systems: Cisco
Local wireless infrastructure: Prism Systems
Cloud computing: Microsoft
Cloud hosting: AWS
Main computer: dSpace
Edge computing system: AdLink
GPUs: Nvidia
Base vehicle software: Apex.AI
Connectivity software: Real-Time Innovations
Simulation systems: Ansys
Simulation systems: SVL Simulator
Specifications
AV-21
725 kg
4876 x 1930 x 1156.5 mm
2971 mm wheelbase
Four-stroke engine
Top speed: 192.2 mph (309.3 kph)
Maximum continuous power:473 bhp
Maximum Lidar detection ran ge: 500 m
GNSS positioning accuracy: 1 cm + 1 ppm RMS
UPCOMING EVENTS
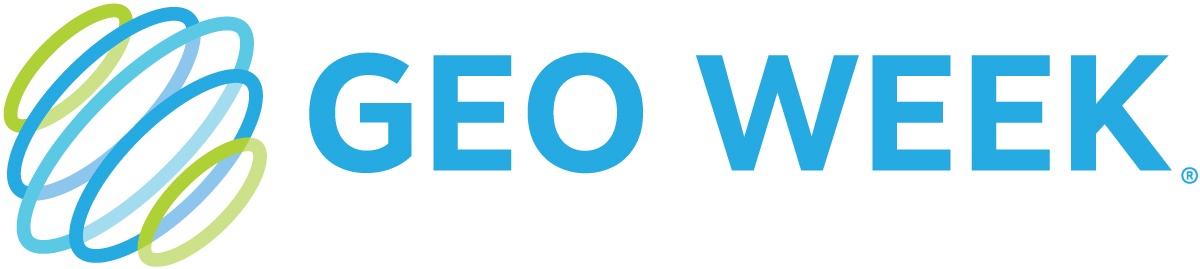
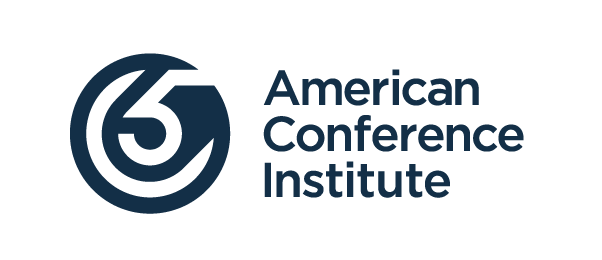
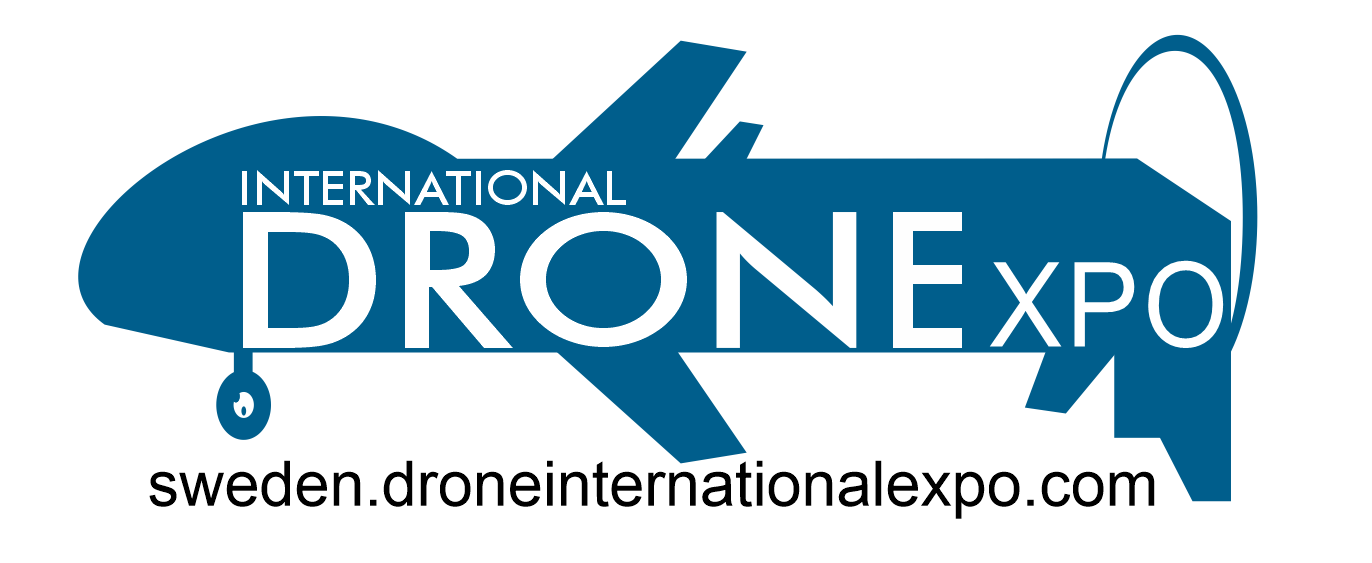
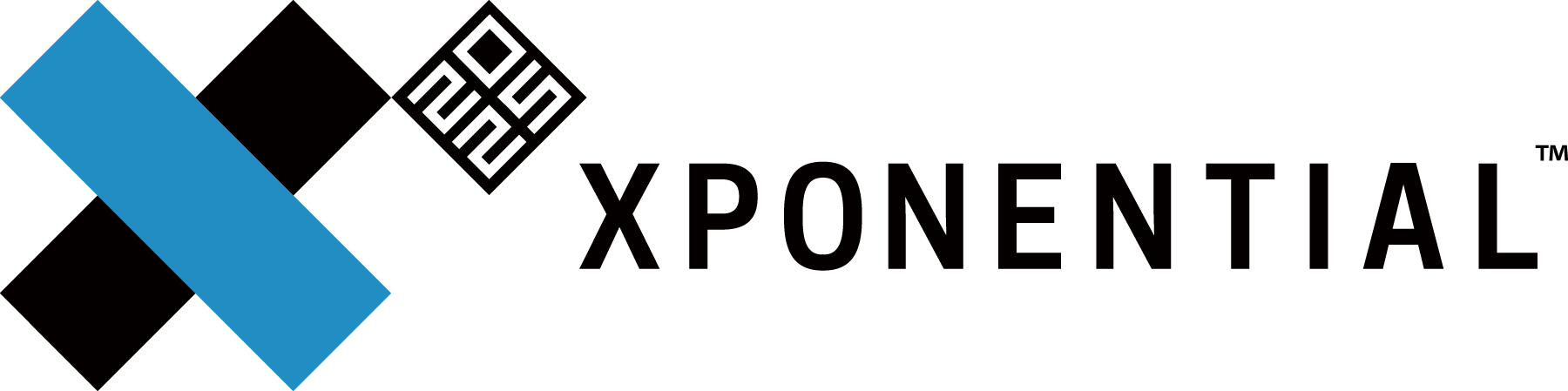
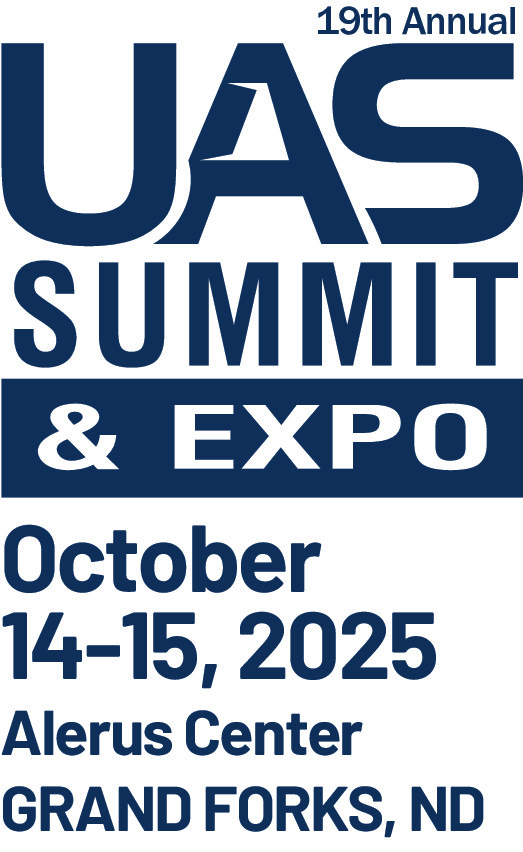

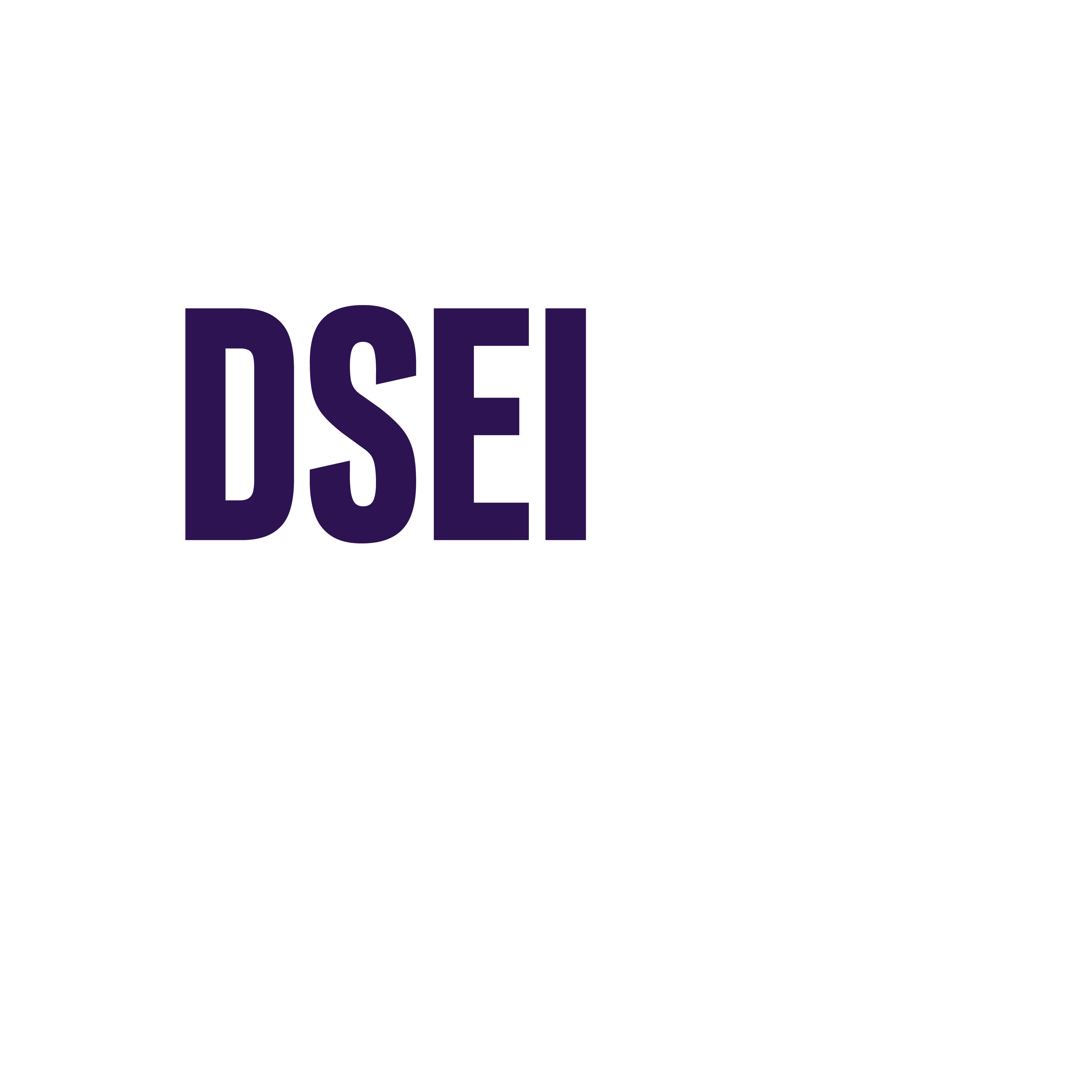
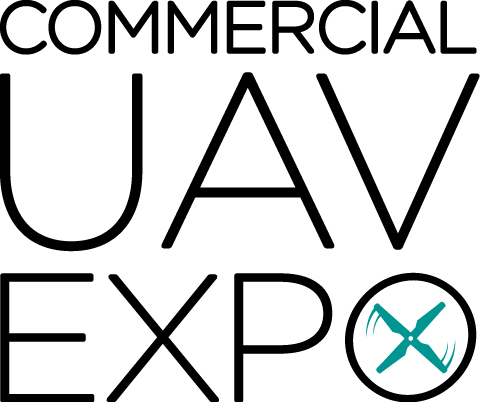
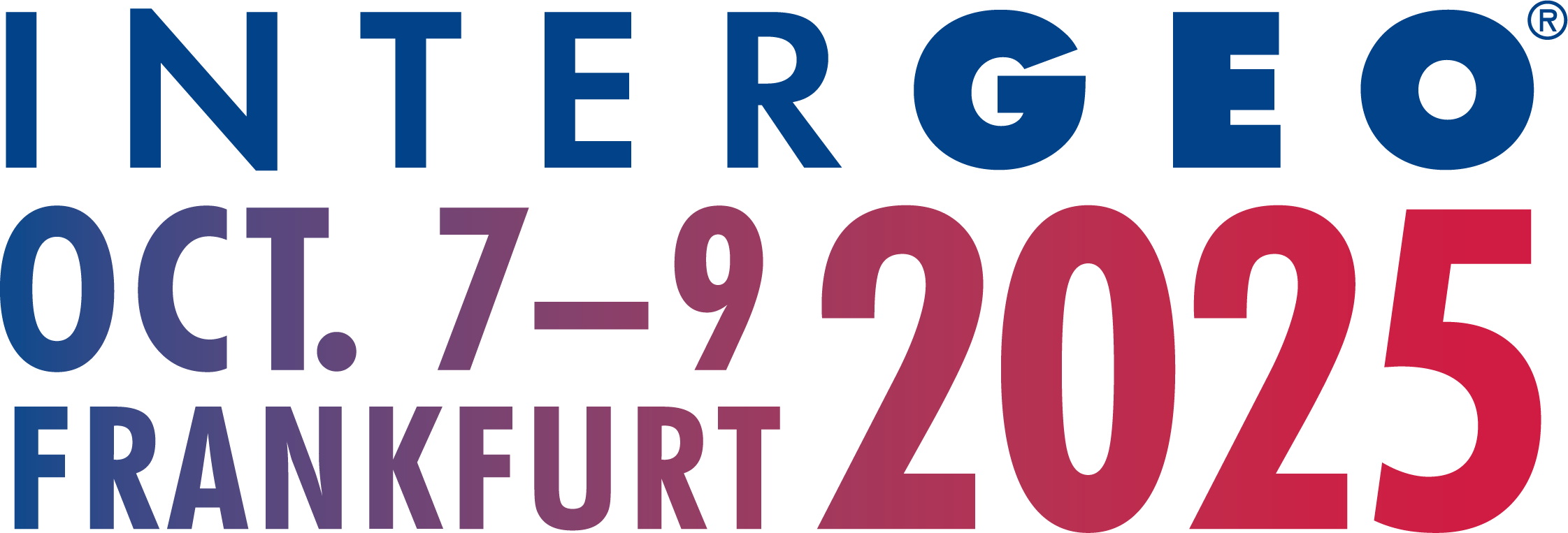
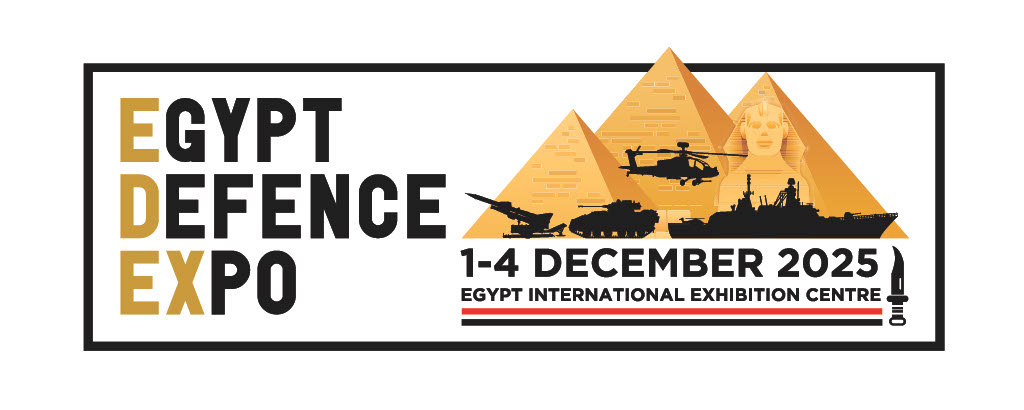
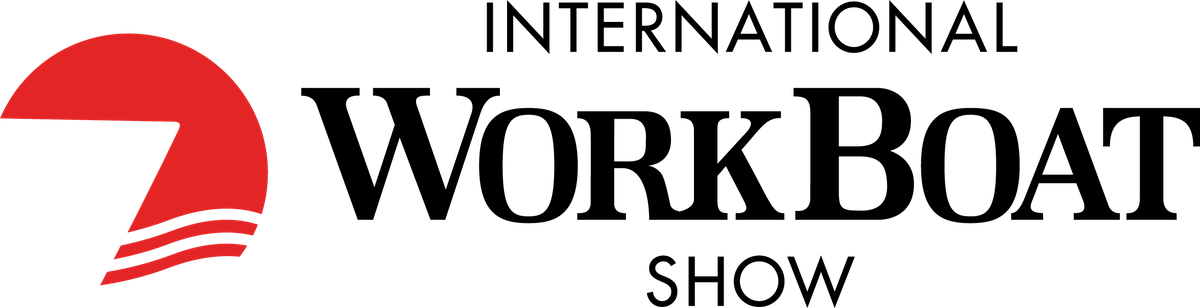