Propellers
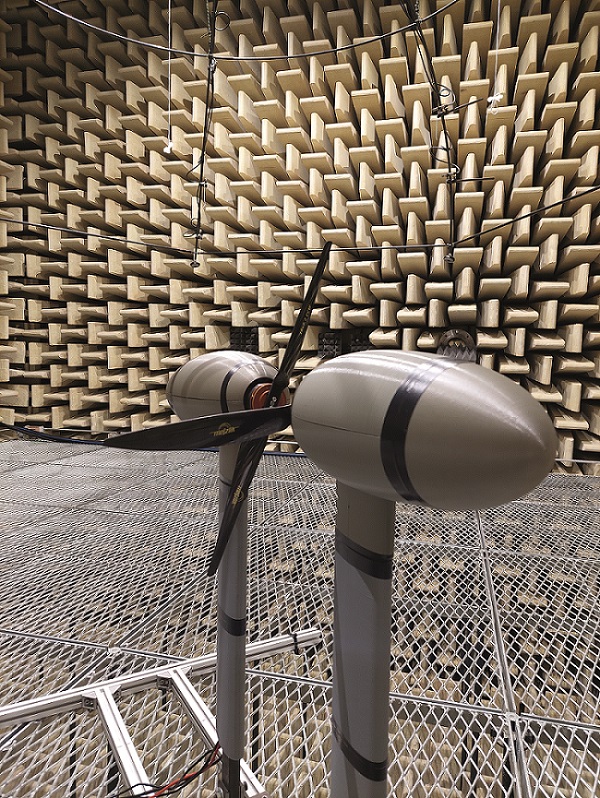
(Courtesy of Mejzlik)
Upward and onward
Rory Jackson finds out how prop suppliers are meeting the growing demands from OEMs for products that generate greater lift and with longer lifespans
Uncrewed systems have evolved over the past few years, leading to commercial, high-end UAV manufacturers attracting investment and setting up partnerships with organisations in markets including logistics, energy and defence.
These operators need increasingly large uncrewed fleets, with similarly large inventory requirements to suit their cargoes and payloads. The same applies to USVs and UUVs, although perhaps not to the same extent. At the same time, the burgeoning eVTOL industry has spawned hundreds of companies designing aerial taxis, ambulances and other aircraft with distributed lift systems reminiscent of UAVs, and they will all be expected to be aerodynamic and energy-efficient.
That puts significant pressure on propeller researchers and manufacturers, who are being asked by uncrewed and autonomous system OEMs to discover new ways of supplying products that generate lift and propulsion with smaller carbon footprints and greater lifespans than ever, and to enable these new classes of vehicles to be scaled up.
Air taxi manufacturers in particular want ever-larger propellers – with diameters of about 2-3 m – to ensure enough lift can be produced without needing prohibitively fast prop tip speeds, as these would create unbearable levels of noise for the passengers, not to mention losses in energy efficiency.
Furthermore, the air taxi industry’s determination to reach market readiness as quickly as possible is pushing lead times for large propellers, with prototyping now expected in some circles to take only 6 months compared with the 2 or 3 years it can take in general aviation.
These eVTOL propellers also feature much more complex designs than have been seen in more typical autonomous aircraft. UAVs for delivery and inspection, for example, use more advanced props now than 5 years ago, using scimitar shapes, upturned and downturned winglets on blade tips, and even featherlike serrations on trailing edges. Also, a wide variety of resin and fibre systems in the propeller structures achieve different combinations of structural, aerodynamic and loading properties.
But as air taxis will carry multiple passengers per flight, their props are almost certain to come with innovations such as leading-edge protection, internal structures using foams and other fillers, and potentially up to 100 layers of carbon fibre.
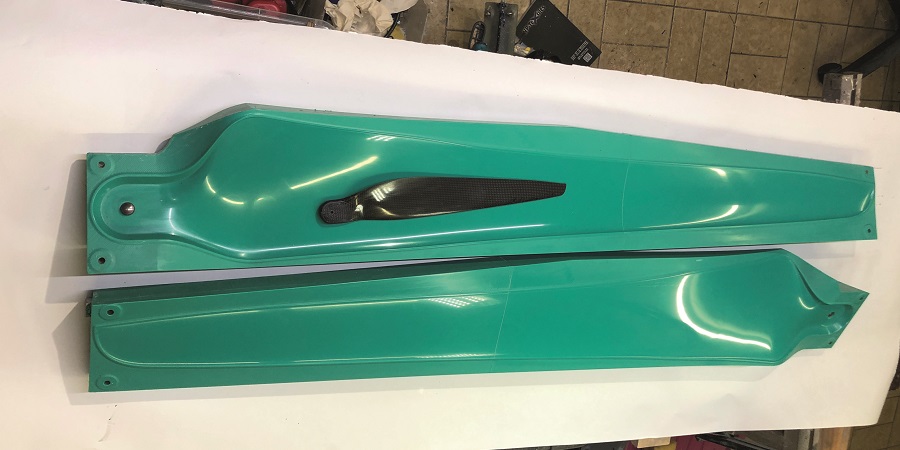
(Courtesy of MagCAD)
And as might be expected from the safety case, greater testing and scanning of props are anticipated. With that in mind, UAV propeller manufacturers have adopted validation techniques from general aviation and incorporated them into their design and production processes.
Materials and manufacturing
Propellers these days are made from many different types of material, including various kinds of wood, metals and polymers as well as composites of them. Each has its place in the airborne and maritime worlds – for instance, wooden propellers are popular in missions where there is a risk of explosions, such as gas facility inspections or gas leak detection, where metal or carbon props might produce a spark and hence ignite any gas present.
However, carbon composite is the most prolific material by far, with carbon fibre props being practically ubiquitous in uncrewed systems around the world.
Certified carbon fabrics are now especially important for self-driving transport vehicles such as eVTOLs and autonomous water taxis, as well as uncrewed aerial freight vehicles and medical logistics UAVs that might have similar or even higher safety requirements.
And with uncrewed systems now being held to the same safety standards as commercial and general aviation aircraft, propeller manufacturers are expected to keep close track of parameters such as the shelf lives of prepregs and resins to ensure their materials are not just safe when purchased, but safe through to the point of use.
There are many different techniques for making carbon propellers, starting with the cutting of carbon fabric. This can be performed manually, automatically or semi-automatically, and with different tools from scissors to ultrasonic blades, lasers and waterjets.
The subsequent installation, impregnation and curing of layers into the mould can then be similarly carried out in a range of permutations of manual and automated methods, with some approaches such as compression moulding and bladder moulding having been applied in UAV propellers that need to work at particularly extreme altitudes and in harsh environments.
In general, however, carbon propellers are labour-intensive to make, so mass production has been difficult to achieve. Some prop suppliers however are taking alternative routes towards achieving the bulk outputs that the uncrewed systems market is requesting.
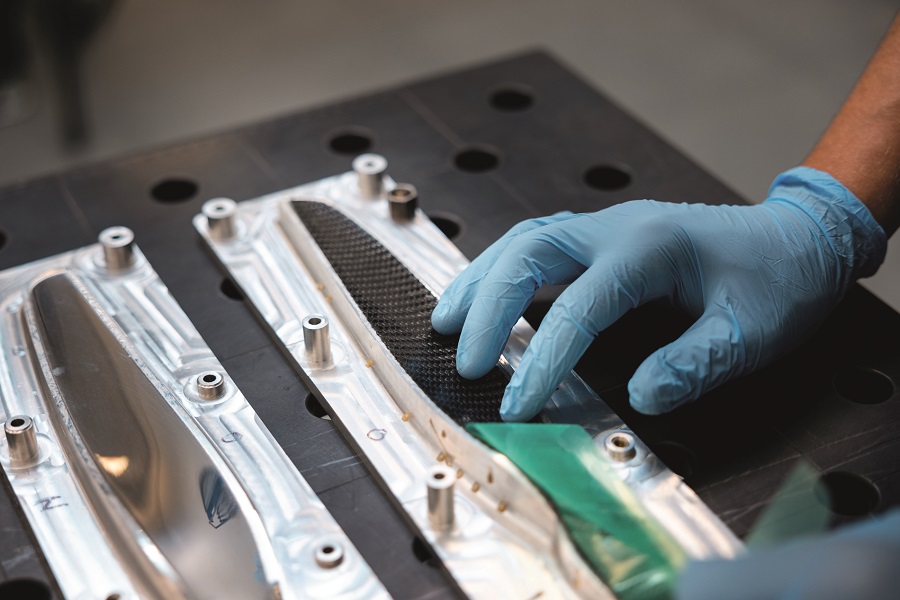
(Courtesy of Mejzlik)
One approach, inspired by the automotive and crewed aerospace industries for instance, forgoes the conventional wet layup in favour of a hot-press system. Here, prepreg carbon fibre sandwiches a foam core inside a metal mould, with high compression and heat then being applied. Going with this process stands to take a supplier’s typical 7-hour cycle time for the wet layup and autoclave sequence down to 30 minutes, as well as reducing the overall production costs by 50%.
The use of a metal mould and the hot-press technique is critical to these improvements. Whereas fibreglass moulds had previously been used, which allowed only one propeller to be made per mould and per day, now multiple props per mould per day can be produced, and with greater precision and repeatability.
Also, the hot-press machine’s degree of compression can be regulated to within 0.05 mm, which can be pre-programmed and automated over a timed period. That is key, as different epoxy resins will have differing curing cycles over time, compression and temperature.
That means the hot press can be closed to the exact and correct degree needed to squeeze the epoxy optimally and thereby distribute it evenly across the breadth of the fibre. It can also be done as the resin is being heated to the temperature at which it achieves the necessary liquefaction for being manipulated in this way.
The hot-press process consists of around 40% manual work – cutting the fibre, layering it with resin and preparing the layers in the mould – and 60% automated or semi-automated pressing and curing.
The repeatability of the process and consistency of propellers made using it also saves time in the design and validation processes, as key tasks such as balancing and validation are inherently accelerated. The precise control of the hot press is such that, after curing, propellers can be trimmed using a CNC machine to any tolerances required, something that conventionally would be done by hand.
As might be guessed though, the hot-press approach requires much more expensive tooling than conventional methods, so it might be more sensible to use it only for high-volume production such as 200-300 props at a time, and opt for wet layups with glass fibre moulds or less expensive methods for smaller batches.
It should not be assumed however that just because this method and others are taken from elsewhere in the composites world that any composites manufacturer can be contracted to design and produce batches of an ideal propeller. Most general carbon fibre parts manufacturers do not have the necessary understanding to optimise propeller fluid dynamics, mechanical properties or testing techniques, so it falls to specialist suppliers to feel their way towards taking the best from both worlds.
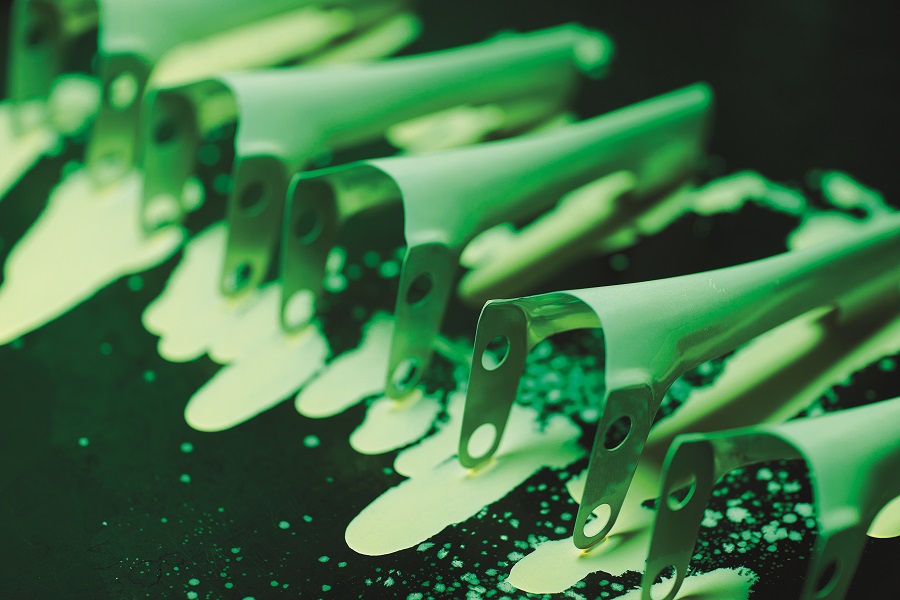
Propeller protection
Given the need for propeller safety among regulators, and longevity among buyers and users, considerable r&d in recent years has gone into protection systems capable of ensuring that UAVs and other uncrewed systems can keep flying amid impacts on or exposure to erosion of their prop blades.
The impacts and erosion can come from more than bird strikes during flight or gravel flying about during take-off. Even rain and particles of dirt in the air are enough to cause hazardous erosion to the leading-edge profiles of propellers, threatening their structural integrity, aerodynamics and practical lifespan.
This erosion is so problematic because the leading edge of carbon fibre props typically represents a point of structural weakness, where a process of delamination and eventual rupturing of the material’s outermost layers will occur. That means a near-total loss of lift by the blade, probably leading to a propulsion failure and ultimately a crash.
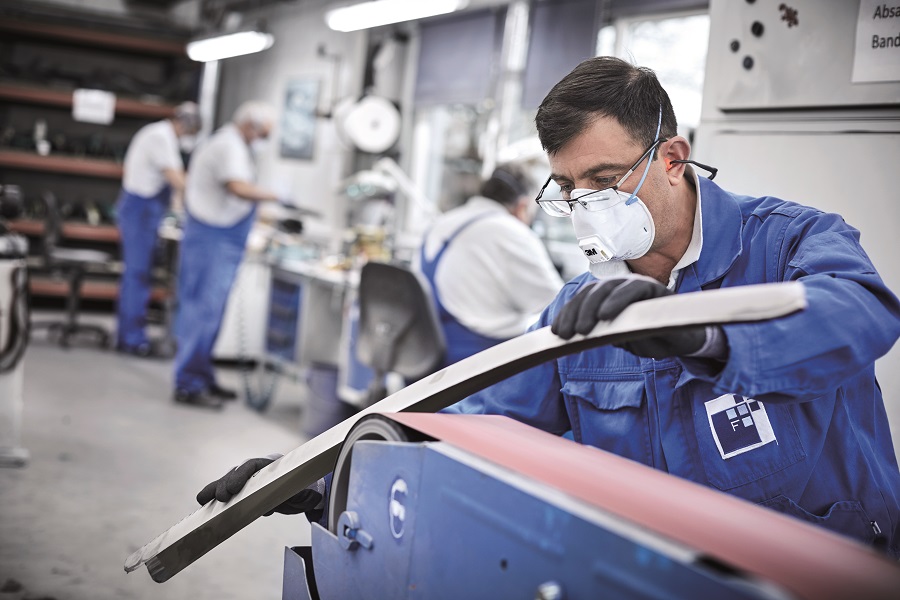
(Courtesy of Fichtner & Schicht)
The optimal protective material for propeller blades depends highly on an uncrewed platform’s working environment. In a desert for instance, rubber would probably be the longest-lasting and most comprehensive protection against sand and gravel. Alternatively, in a wet, dust-free, freshwater environment such as a reservoir, titanium would be best.
So far, the optimal solution being adopted for UASs is an electroformed nickel-cobalt alloy that is custom-designed to suit both the outer aerodynamic profile and inner mounting profile for each propeller.
This is a solution taken from crewed aircraft in defence and general aviation, particularly among some successful high-end military UAVs, and its mechanical and chemical properties are such that it is the second-best solution available for both desert and wet environments – it has about 98% of rubber’s effectiveness and 97% of titanium’s qualities.
That therefore makes it ideal for the many real-world operating areas where uncrewed systems have to withstand a combination of moisture and dirt. It also combines the flexibility of nickel with the hardness of cobalt to result in something that can be mounted over propellers to provide sufficient physical safeguarding without being too brittle to function as part of an aerofoil.
These parts are produced in galvanic tanks, with the nickel and cobalt distributed through an electrodeposition process onto stainless steel mandrels shaped like the propeller blade surfaces they are intended to mount on. The mandrel is highly polished to ensure that the nickel-cobalt layer growing around it does not adhere to it too strongly to be lifted off.
This solution wins out over alternatives, owing to qualities such as high geometric customisability thanks to the nature of the electroforming process. For instance, bending or forming a metal sheet to fit precise aerodynamic tolerances over a blade tip is extremely difficult by comparison, and even if aerodynamically optimal geometries can be achieved this way, doing so would weaken the metal sheet and hence the degree of protection gained.
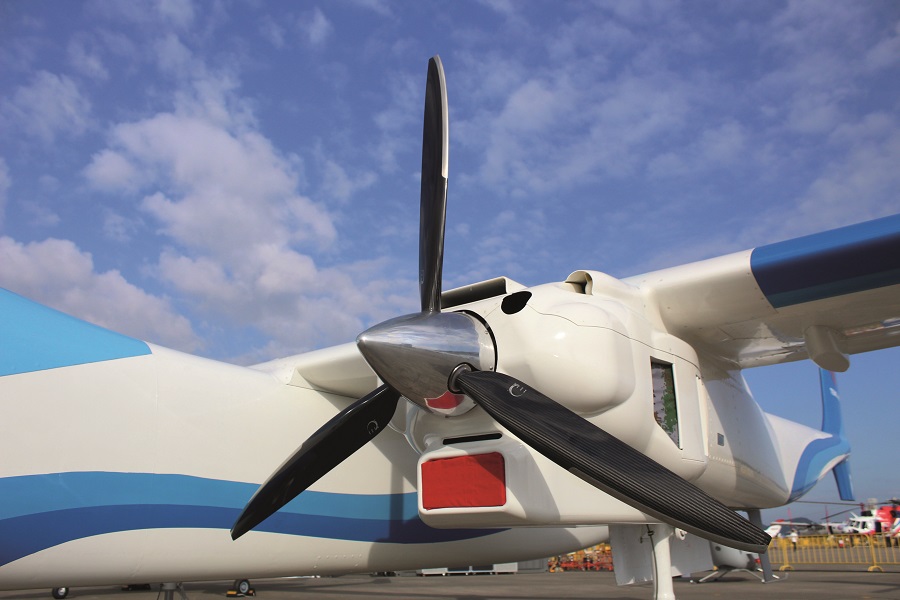
(Courtesy of Xoar)
The customisability of electroformed blade protection also extends to the material’s thickness. It can be varied to have, say, a thicker layer of material extending forwards from the blade tip, and a thinner layer running back along the blade chord, where material is needed primarily to ensure a broad contact area between the blade and its protection system for adhesive to be applied.
As an example, an autonomous helicopter might have up to 1.5 mm of nickel-cobalt electrodeposited on its propellers’ blade tips, and 0.25-0.3 mm elsewhere. For vehicles working in extreme environments and with critical safety requirements, the tip protection might be 5 mm thick.
For small UAVs, less protection thickness is needed of course, with variations stemming from the use case and how strenuously the payload must be protected. However, 0.25- 0.3 mm is probably the minimum thickness physically possible; any thinner and the material can suffer microfractures while being removed from its mandrel.
It follows that this type of erosion protection can be mounted around the whole blade or simply over the tip, covering the front third or half of a blade, where most of the erosion will take place. That saves on material costs and weight – many adhesive tapes are sufficient to safeguard the middle and rear regions of prop blades in most cases.
While these nickel-cobalt protection systems are not cheap to produce, they can significantly lower overall operating costs. Aside from helping propellers to last longer, their required mean time between inspections runs into the thousands of flight hours.
As well as keeping prop blades safe against physical strikes, protecting them from icing-up becomes increasingly important as more missions in colder climates are requested. To that end, installing resistance wires inside a propeller’s materials looks to be one of the most promising preventative approaches for uncrewed systems working in such conditions.
For this, an electrical interface is needed between the propeller and the onboard power system, to enable current to run through the wires in the prop blades. The wires act as resistors, converting effectively all the current into heat as commanded by their control system.
Testing methods
Naturally, as more stages of propeller manufacturing become automated, quality control becomes easier, with mistakes in resin distribution or heat regression during curing becoming rarer as computer control largely eliminates human error.
Meanwhile, testing methods for prototyped or finished propellers are also being improved in order to satisfy regulators and investors for uncrewed systems that such vehicles’ propellers are robust, professional-grade components.
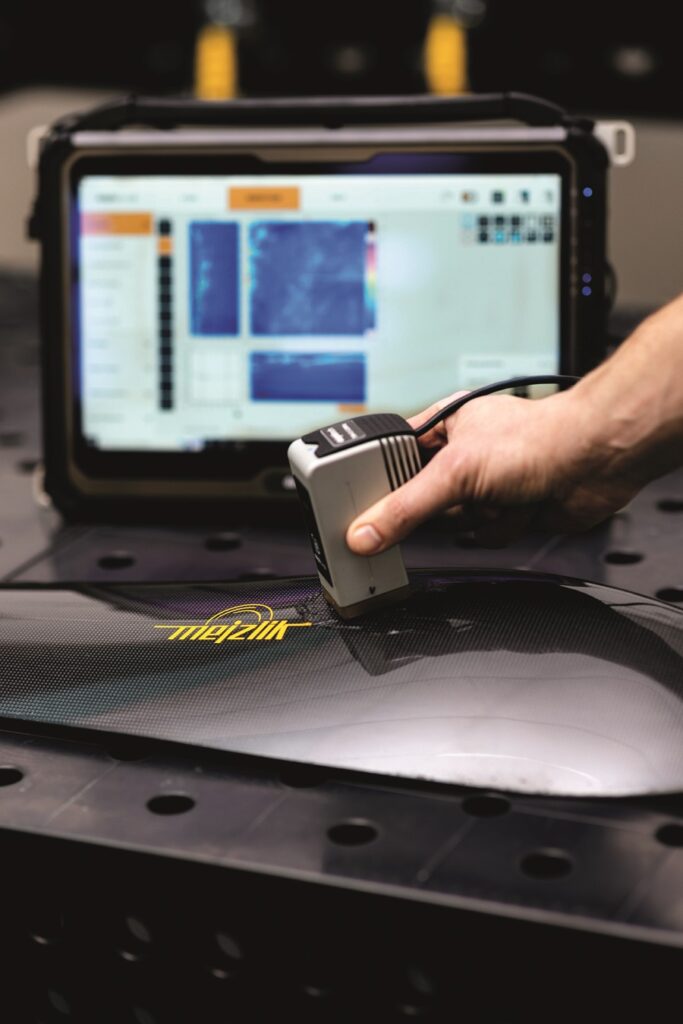
(Courtesy of Mejzlik)
For instance, 3D scanning of propeller profiles can reveal a lot of information about how precise the manufacturing processes are, where mistakes are being made, and how closely or consistently manufacturing tolerances are being met. It can also provide a vital insight into the properties of newly simulated and prototyped propeller designs, and examine how robust new designs are in real-life compared with, say, FEA.
In addition to well-established laser scanner systems, blue-light sensors are used to inspect some propellers. The sensors work by projecting a pattern of narrowband blue light across the surface of a part to filter out any potential interferences from ambient light, then use stereo cameras to capture that pattern and recreate the 3D shape of the part by recognising any distortions in the projected pattern created by the part’s profile.
The result is akin to a real-world FEA map, with heat maps of propellers showing where composites are thicker or thinner, smoother or twisted, and accurate to around 0.005 mm. The maps can also be produced for very small propellers as well as very large ones, from diameters of around 5 cm up to 5 m.
If 3D scans do not go deep enough for some suppliers, ultrasound machines can be an alternative. They are costly but they can be of critical help in unearthing visual subsurface data about the integrity of props, revealing bubbles in the resin system or areas where the layers of fibre have not connected together optimally.
For even deeper analysis of propeller quality, some suppliers are contracting companies who X-ray props and rotors for the general aviation market. Ultrasonic scans only penetrate until they meet some resistance, in the form of an air bubble or similar. X-rays on the other hand provide views all the way through a propeller, although there is the trade-off here in the higher expense of the machinery and the necessary protection systems around the testing chamber.
And for anyone seeking a more practical approach to validating propellers’ longevities, some companies are investigating the robustness of available composite and protection materials using ballistics testing, for example by firing flurries of particles at props, both with and without nickel-cobalt edge protection.
The tests indicate that nickel-cobalt protection can safeguard propellers’ structural integrities and aerodynamic profiles enough to theoretically multiply their lifespans by a factor of 14, while increasing their weights by only around 10%.
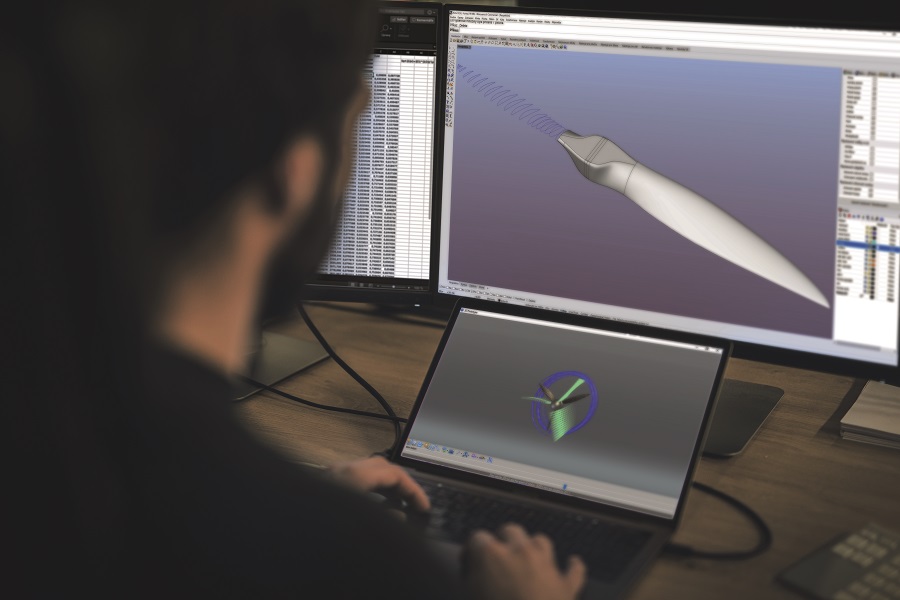
(Courtesy of Mejzlik)
In practical terms, most propellers available these days will last until their UAV platforms crash, but with the prominence of professional-grade craft across defence, government and commercial work, a real increase in prop lifetimes from around 100 hours to more than 1000 will be vital to ensuring uncrewed systems are viewed (and certified) as high-end industry tools and vehicles.
Also, more industry-standard physical tests – such as compression, stress rupture, fatigue and stress-corrosion testing – can be applied to propellers, while laser or blue-light scanners can run inspections of them to identify how the materials and coatings respond to different applications of forces, wear and other inputs over time.
Some prop makers are even borrowing the approach from manned helicopters of running tensor meters inside their blades to collect data on how the propellers bend and twist across their blade lengths in response to winds, strikes or other stresses. Such projects open up valuable insights into how prop mechanics and lifespans could be enhanced.
These collective improvements in manufacturing and testing could result in up to a threefold increase in overall production costs. But the real net outcome is a lower total cost of ownership and price per flight given that they will result in an increase in lifespan of more than 10 times per propeller, so long as vehicle OEMs ensure all the other onboard components and software do their job in ensuring safe operations until a platform’s next repair or overhaul date.
Simulation tools
While propeller testing approaches are becoming more varied and in the number and precision of their data points, the maturity of propeller technology is such that advances in simulation tools and methodologies are critical to unlocking the kinds of step-improvements in prop efficiency that could pose a breakthrough for autonomous systems and manufacturers.
However, while the benefits of distributed lift systems such as multi-rotors and VTOL-transitioning craft are closely understood across the autonomous space, the design rules, dynamics and heuristics are not yet captured in a single, universally applicable, high-fidelity CAD or CFD software solution that new aircraft developers can use when beginning the design process for a new vehicle.
Finding the optimal rapid, design-order tool suite for early concept work is therefore extremely challenging, with programs such as SolidWorks, STAR-CCM+, OverFlow and more potentially being appealing choices, with various advantages and disadvantages to solve the many issues that can be faced at the outset of a new vehicle’s r&d.
For example, and as discussed, eVTOL aircraft manufacturers have to contend with significant lead times when prototyping new propellers. It becomes even more challenging for them when designing more complex thrusters such as ducted fan arrangements, which could make for highly efficient propulsion systems.
As a result, some new programs are aimed specifically at simulating ducted fans for VTOL-capable air taxis and UAVs. Their aim is not necessarily higher fidelity or lower error in simulation results, but more in the sense of modelling at a faster rate and more intuitively, to save time in their use and the training requirements for getting the best from the software.
In addition to simulating individual prop, rotor and thruster designs, other projects are investigating how all-new distributed lift configurations – with motors, wings and propellers arranged in entirely untested permutations – can be optimised for qualities such as energy efficiency, noise, speed and structural resilience. One such project, publicised in mid-2022, investigated a UAV with tilting fixed wings and multiple rotors along its wings’ leading edges, looking at different positions of its motors with respect to its wings.
Conclusion
Well-established production and testing processes from the aerospace and automotive worlds are being deployed to enhance propellers in the rapidly maturing uncrewed vehicles industry. At the same time, software engineers are using a wide variety of algorithmic approaches and engines to perform their CFD work as well as optimise their quality control and validation of prototype and production propeller units.
As a result, many high-quality propeller solutions are becoming available to uncrewed vehicle OEMs.
Acknowledgements
The author would like to thank Tomas Mejzlik Jr at Mejzlik, Markus Tack at Fichtner & Schicht, Nicole Wan at T-Motor, Leo Ko at Xoar International, and Willem Anemaat at DARCorporation for their help with researching this article.
Examples of propeller manufacturers and suppliers
CANADA
Aerovate | +1 807 474 1641 | www.aerovate.ca |
CHINA
Anyang Hawk Aviation | +86 372 5931 122 | www.falconhobby.com |
T-Motor | +86 791 8855 6889 604 | www.tmotor.com |
CZECH REPUBLIC
Fiala Prop | +420 732 682 554 | www.vrtule-fiala.cz |
Mejzlik Propellers | +420 775 099 706 | www.mejzlik.eu |
DENMARK
Copenhagen Subsea | +45 70 22 11 62 | www.copenhagensubsea.com |
FRANCE
Helices E-Props | +33 4 92 34 00 00 | www.e-props.fr |
GERMAY
Fichtner & Schicht | +49 5252 9354 0 | www.fi-sch.de |
MagCAD Propeller Development | +49 4050 0167 83 | www.magcad.de |
MT-Propeller | +49 9429 9409 0 | www.mt-propeller.com |
INDIA
Albatross Flying Systems | +91 80 28 44 44 66 | ww.albatrossflyingsystems.com |
Robu.in | +91 020 68197600 | www.robu.in |
ITALY
FP Propeller | +39 0532 732470 | www.fp-propeller.com |
GT Propellers | +39 0541 693399 | www.gt-propellers.com |
NEW ZEALAND
Airmaster Propellers | +64 9 833 1794 | www.airmasterpropellers.com |
SPAIN
Helices Aerobat Propellers | +34 617 772273 | www.aerobat.es |
SWITZERLAND
Hydromea | – | www.hydromea.com |
UK
CJR Propulsion | +44 2380 222032 | www.cjrprop.com |
Dowty Propellers | +44 1452 716000 | www.dowty.com |
Rockwood Composites | +44 1626 240026 | www.rockwoodcomposites.com |
Teignbridge Propellers | +44 1626 333377 | www.teignbridge.co.uk |
USA
APC Propellers | +1 530 661 0399 | www.apcprop.com |
Blue Robotics | – | www.bluerobotics.com |
Culver Props | +1 573 364 6311 | www.culverprops.com |
DARcorporation | +1 785 832 0434 | www.darcorp.com |
Hartzell Propeller | +1 937 778 4200 | www.hartzellprop.com |
Ivoprop | +1 562 602 1451 | www.ivoprop.com |
KDE Direct | – | www.kdedirect.com |
Maxx Products International | +1 847 438 2233 | www.maxxprod.com |
McCauley Propeller Systems | +1 316 831 4021 | www.mccauley.textron.com |
NorthWest UAV | +1 503 434 6845 | www.nwuav.com |
Sensenich | +1 813 752 3711 | www.sensenich.com |
Whirlwind Propellers | +1 619 562 3725 | www.whirlwindpropellers.com |
Xoar International | +1 626 679 1158 | www.xoarintl.com |
UPCOMING EVENTS
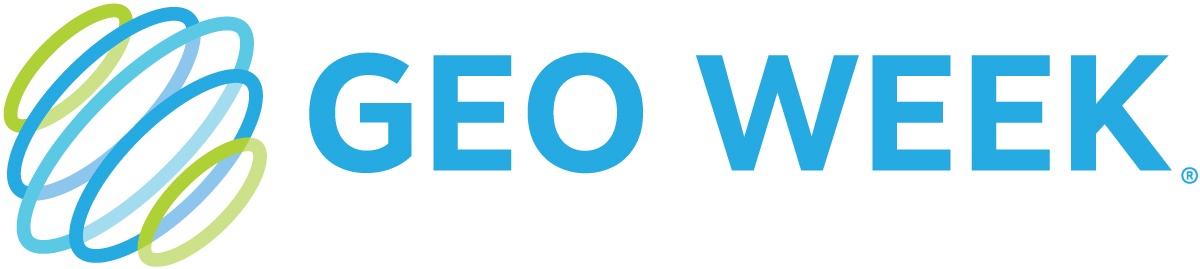
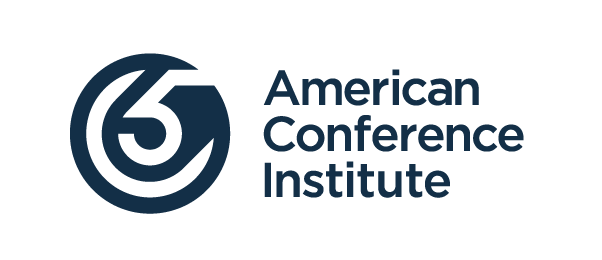
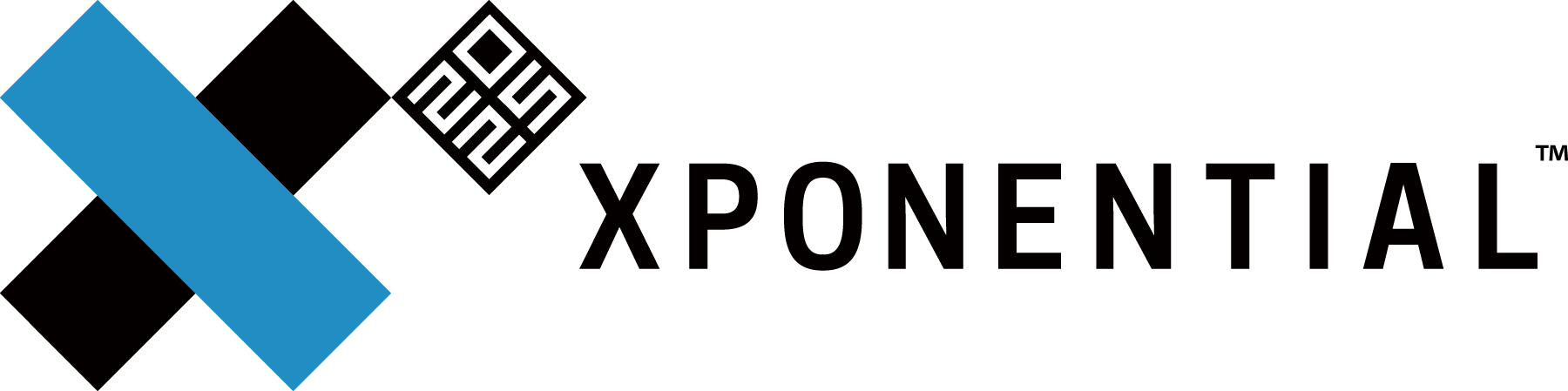
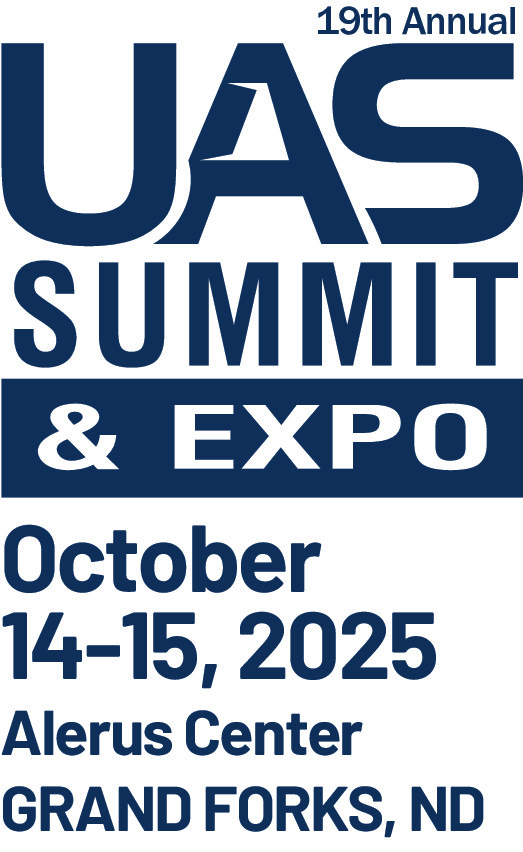
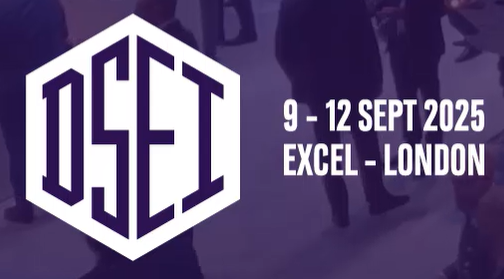
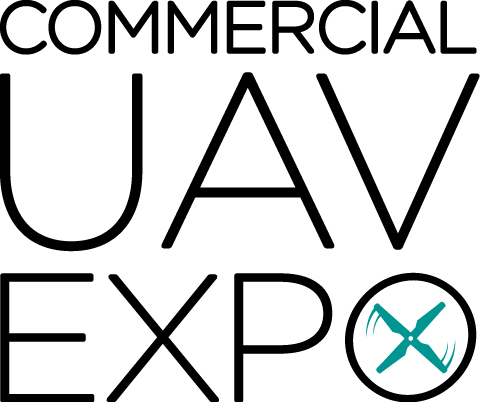
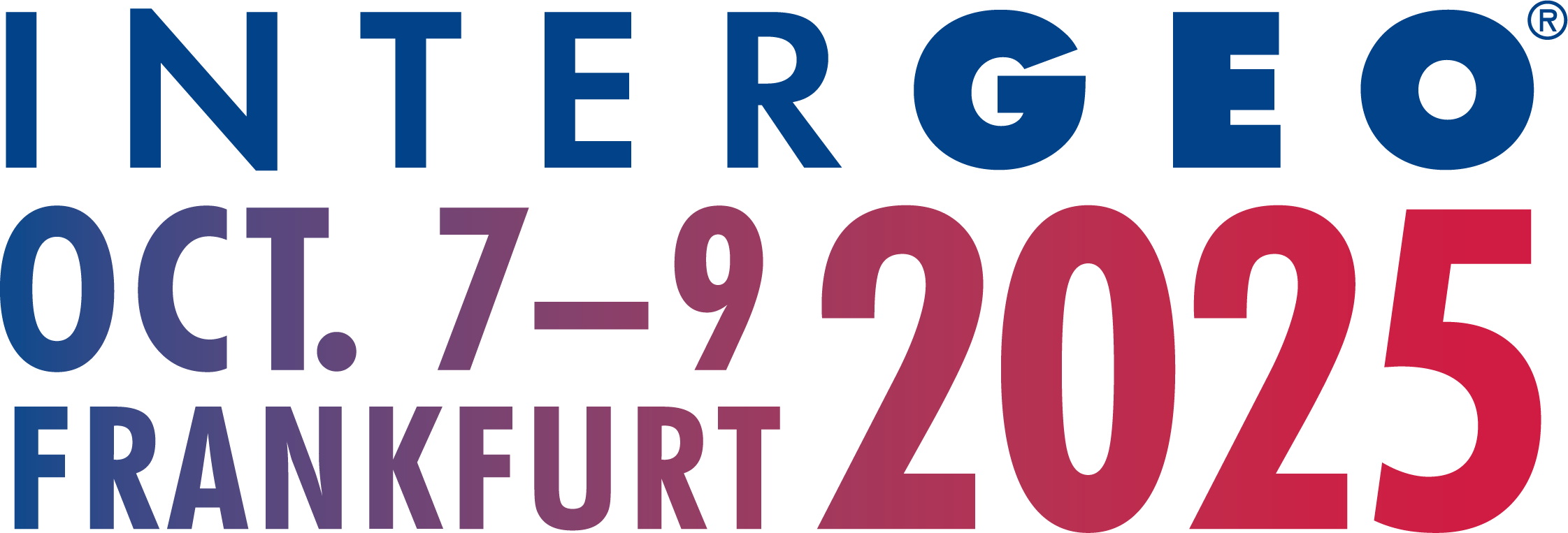
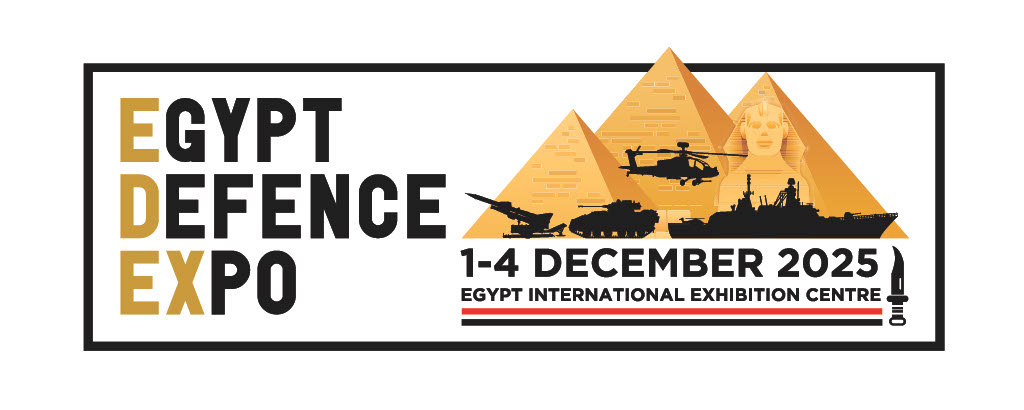
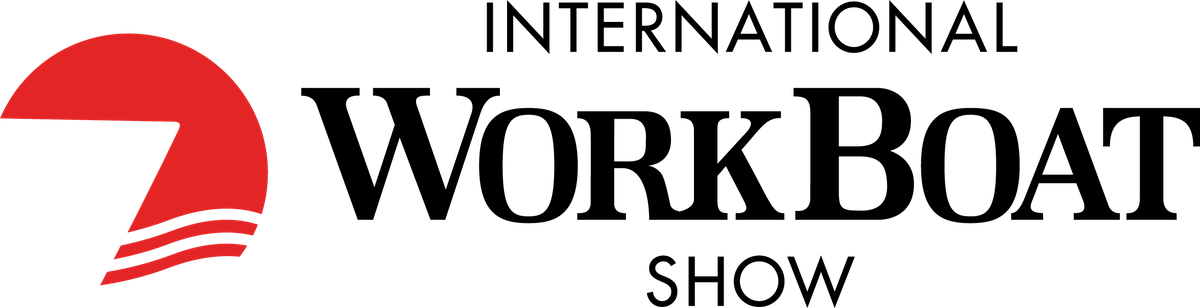
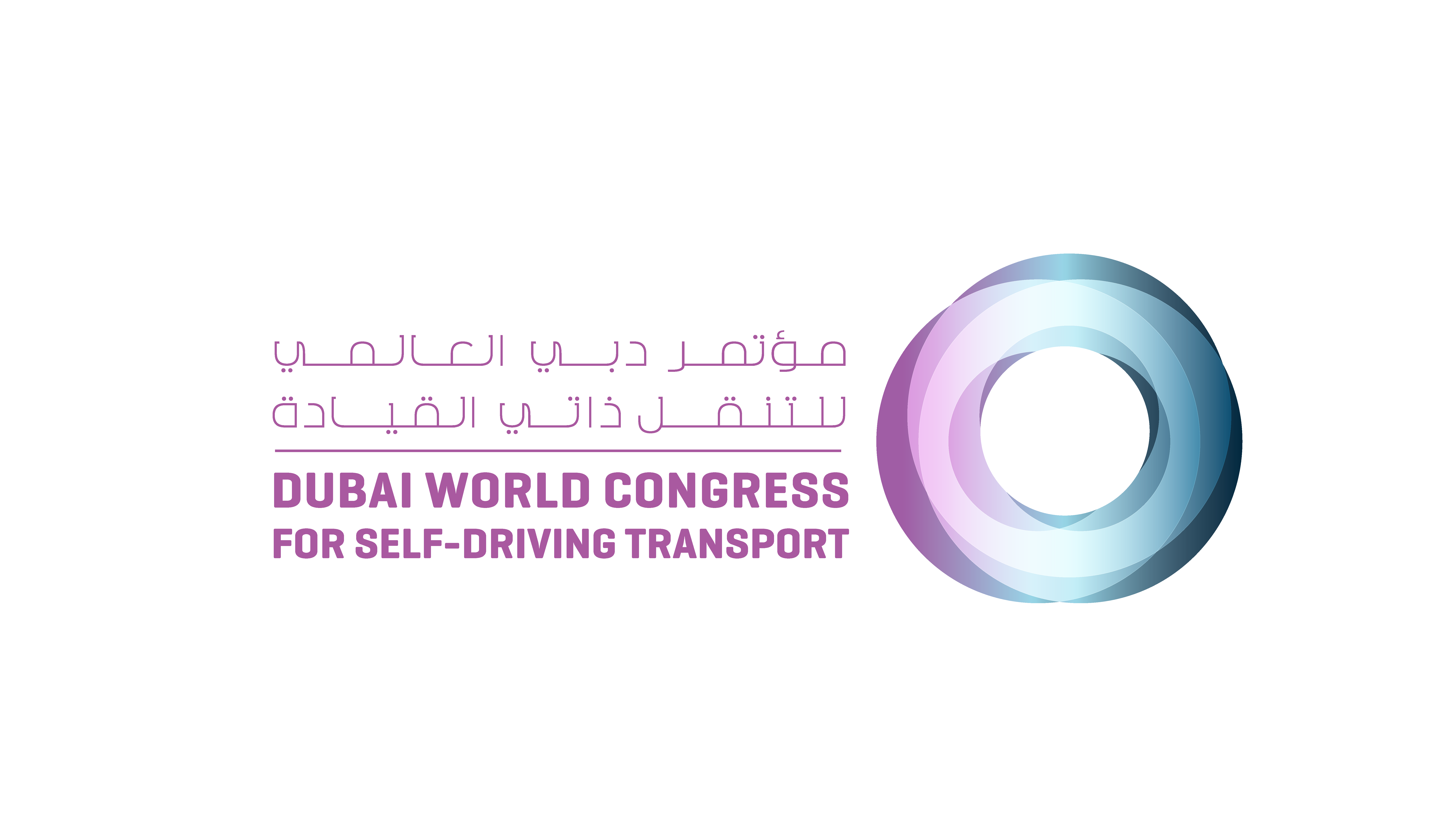
