Steel E-Motive robotaxi
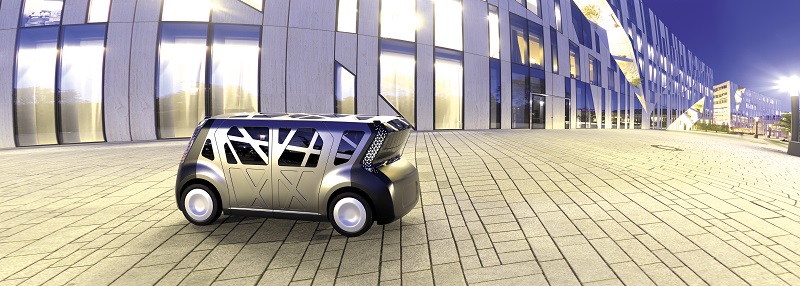
Rory Jackson reports on this project that uses different steels to produce an autonomous, eco-friendly taxi that meets stringent road safety regulations
Follow this cab
Market analysis of the trends affecting the future of personal mobility predict that consumer ownership of vehicles will decline over the decades to come, with the use of public or shared transportation services to grow in its place. That indicates a potentially enormous market for sustainable, autonomous commuter transport.
We have reported on different robotaxi solutions over the years that aim to serve such a market, although to date they have been limited in their use to tightly controlled and fenced-in campus-like areas or events.
A major reason for that is that road safety regulations list an exhaustive number of tests that have to be passed before an autonomous vehicle can be allowed to operate commercially on public roads. They go beyond the SAE levels of autonomy and ISO 26262, and not all OEMs are necessarily well-practised in how to make a robotaxi comply with such standards.
However, a new robotaxi project aimed at meeting not only road safety regulations but expected future environmental and mobility-as-a-service (MaaS) demands has emerged in a partnership between automotive group WorldAutoSteel and engineering consultancy Ricardo. While the latter is well-known among automotive engineers, the former is a research consortium of the world’s 18 largest automotive steel producers, spanning East Asia, Europe and the Americas.
As George Coates, technical director at WorldAutoSteel, explains, “We fund research projects aimed at defining attributes for steel that make it a compelling choice for various automotive applications. That involves regular collaboration with impartial research institutes and universities to publish detailed, open-source guidelines on how to form what we call advanced high-strength steels [AHSSs], how to join them, and how to adjust maintenance practices and tooling for them, while incurring minimal extra costs wherever possible.
“Every 5-8 years, we ask members to contribute additional funds for a research project that takes maybe 3 years, with blank-sheet designs for an automotive application use case for AHSSs. It results in a comprehensive, standards-compliant vehicle concept, the complete details of which are published so that anyone can copy and manufacture it.”
WorldAutoSteel has completed five such projects so far, lessons from which have informed various standard automotive manufacturing practices. Its sixth and most recent is the Steel E-Motive (SEM). It is the consortium’s first design for an autonomous robotaxi, and has been created with Ricardo as primary consultant.
True to its word, this August WorldAutoSteel will publish all the CAD files, data and engineering reports relating to the SEM so that any OEM interested in recreating or even bulk-manufacturing the vehicle can do so without paying a licence fee.
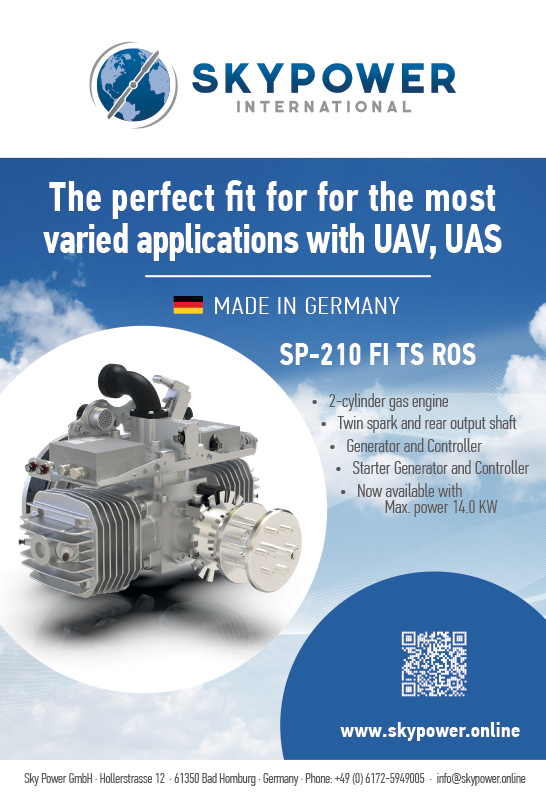
The Steel E-Motive concept
As Coates observes, “In the past few years, car ownership has fallen considerably among younger people throughout much of the world, and continues to do so. That means MaaS will be needed in centres of large populations, and full autonomy without manual fallback controls will create opportunities for making packaging and occupant space more efficient. But that in turn creates major challenges for crash safety.
“We investigated other MaaS vehicles and robotaxis, and found that a lot of them weren’t clear as to whether they incorporate a passive safety structure.
“Some spoke about their use of active safety systems through Lidars, vision and radar, and how the autonomy systems could always manoeuvre to avoid an accident using those sensors, but if you talk to any regulatory agencies, none of them have any interest in relaxing crash safety standards.
“Robotaxis are going to operate in mixed-mode traffic, surrounded by people driving cars and trucks, so there are always going to be crashes. So we set out to create something that could be used in commercial deployments by 2030-35, meet global road safety regulations and make architectural allowances for the kinds of sensor integrations that are likely to be standard by then.”
From the outset therefore, WorldAutoSteel and Ricardo chose to design the Steel E-Motive to be used as an SAE Level 5 autonomous vehicle, without an onboard driver or attendant, and combining the highest levels of autonomy with the highest levels of physical safety. To that end, the two vehicle designs that have emerged from the project – SEM1 and SEM2 – have a passive crash safety structure designed to protect its occupants should the active safety systems prove lacking.
The SEM1 is the more developed of the two in terms of the core engineering and NVH and crash modelling, while the SEM2 is effectively an expansion of the SEM1 aimed at using as many common parts as possible, to show that a larger vehicle can be made and operated with minimal extra costs; development of the SEM2 will continue through to 2024.
Neil McGregor, project lead at Ricardo, says, “The SEM1 is just over 4 m long and is sized at somewhere between a Volkswagen Polo or Golf for inner-city journeys, and with four seats set in two rows. It features a body in white [a term for a car body’s frame once it’s joined together but before chassis sub-assemblies, powertrain or trim components are integrated] with a weight of 282 kg.”
The SEM2 has more space and comfort for longer journeys, such as from home to airport, so it has six seats, with three rows of two. Both vehicles have their forwardmost row of seats rear-facing, as studies indicate this makes ride-sharing feel more comfortable and communal in the vehicles.
“Both the SEM1 and SEM2 are battery-electric,” McGregor says. “The SEM 1 has a 75 kWh pack with a front electric drive unit, while the SEM2 is 92 kWh for longer range and has front and rear electric drive units for a bit more control given its higher mass and therefore inertia.”
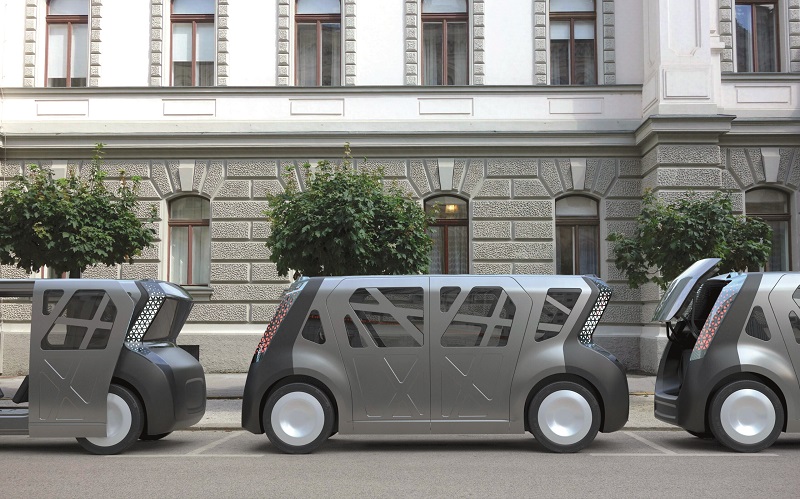
Using the SEMs
WorldAutoSteel’s initial research included discussions with organisations including automotive OEMs and start-ups to gather feedback and hence gain an insight into how best to develop the SEMs, to deliver autonomous vehicles they would want to adapt for their own production.
“The MaaS providers could be present-day OEMs, as many of them are investing in the autonomy space, and several Tier 1s are making the same movements,” Coates says.
“Elsewhere you have start-ups like Canoo and Waymo that are positioned to be OEMs as well as service providers, but in most cases we anticipate that the providers will outsource manufacturing to OEMs, who have the production knowhow.”
WorldAutoSteel and Ricardo expect the biggest markets for the SEMs and other robotaxis to be congested cities with the highest populations, where vehicle ownership costs are highest, and zero and ultra-low emissions zones are expected to make using and owning personal vehicles more expensive.
To minimise fleet managers’ barriers to operation, pre-operational checklists for the SEM1 and SEM2 comprise standard procedures such as inspecting tyre condition, battery health and coolant fluids – much like conventional taxi and truck fleets – before giving them the green light to start carrying passengers.
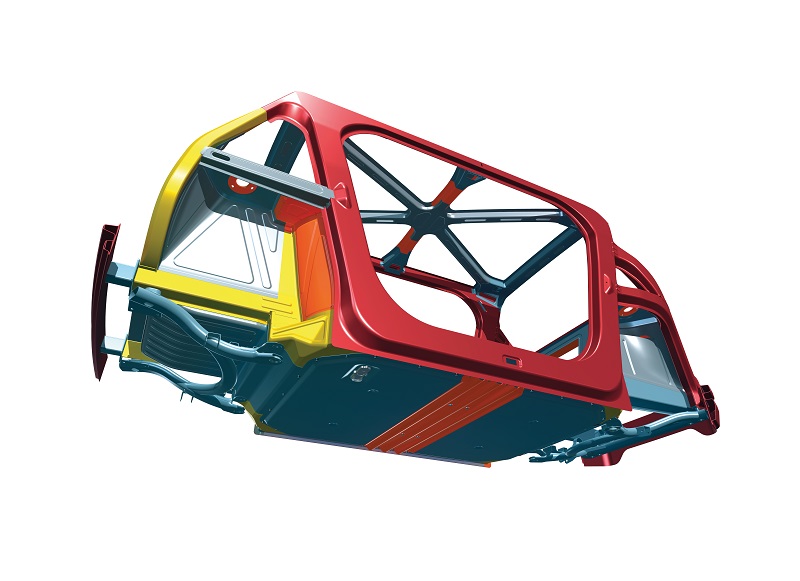
Autonomy coverage
For 360o situational awareness, the recommended sensor integrations include 10 HD cameras distributed about the corners and bumpers of the SEM1, with four short-range Lidars placed at the four corners of the roof to provide better range and shape information than cameras.
Six short-range radars positioned low at the four corners of the vehicle body and beneath the door apertures enable high-resolution proximity and velocity information on nearby objects, and both a long-range Lidar and radar at the rear bumper provide safety-critical velocity details on objects approaching from the rear (where crashes are traditionally most likely to come from).
On top of the roof, a GNSS antenna enables periodic position checks. A satcom antenna will deliver health and navigation data to fleet managers (potentially in a similarly intermittent manner, as comms congestion and multi-pathing could hamper attempts at constant connectivity) as well as any kind of ad hoc swarm arbitration system that might be used to ensure taxis are distributed sensibly across cities.
“Those kinds of sensors are increasingly supplied as COTS systems, and will be quite mainstream by the time this vehicle or derivations of it are adopted into companies’ manufacturing lines,” McGregor says.
“What’s less mainstream is thinking about how the body structure affects how smoothly robotaxis can operate, so we’ve deviated from standard automotive designs to make something that regulators as well as passengers will actually approve of.”
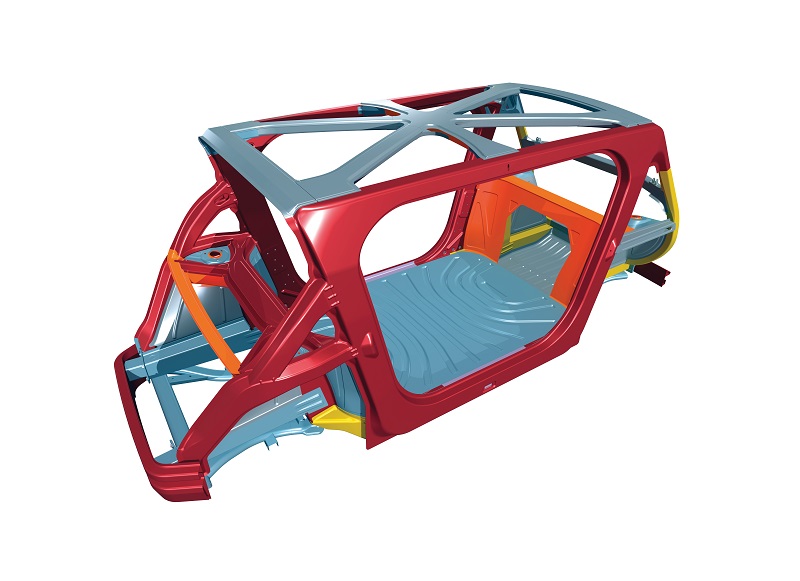
Steel in motion
For instance the B-pillar, usually a central support structure between the front and rear doors, has been taken out of the body and recreated in the doors themselves, which open in a scissor-type motion to about 1 m width. That enables a sufficiently wide space for passengers to enter and exit smoothly – a critical consideration in the absence of someone overseeing who goes in and out of the vehicle.
The body structure itself is made from five AHSS material groups. Each of them plays a particular role in structural support and crash safety depending on its zone, the direction in which crashes will come from, and how vehicle dynamics will play out in each crash.
Specifically, the A, C and D-pillars, along with the doorsill and roof rail, are press-hardened steels, available in tensile strengths of up to 2000 MPa. These are hot-formed by heating them, inserting them into a die and press-forming them, and in the SEM1 they are chosen to give minimal intrusion into the passenger compartment during a crash.
“We use press-hardened steels where we need to form shapes that can’t be achieved through the less expensive process of cold-forming,” Coates explains.
“And when press-hardened steels are rapidly cooled after press-forming, they form martensitic steels – very high-strength materials with tensile strengths of about 1500-1900 MPa,” he says. “We use them in some anti-intrusion beams and panels, in front of and behind the passengers, to minimise intrusion during an impact and reduce the risk of serious injuries to the occupants.”
The floors and longitudinal beams are made from dual-phase, complex-phase, and third-generation steels that have been optimised to be as formable as possible while still retaining mechanical strength. The roof rails and console are made from high-strength, low-alloy, bake-hardenable steels.
Overall, around 200 different steel structural parts are assembled to comprise the SEM1’s body structure and enable it to meet the various regulatory crash safety tests.
“One of the biggest technical challenges for instance were the frontal crash tests,” McGregor recounts. “There are four front-load cases or tests that the car had to meet, one being a frontal full-width barrier [FFB] crash to see if the car could decelerate and crumple gently during an impact with a rigid barrier, and if the airbags and seatbelts would do their jobs.
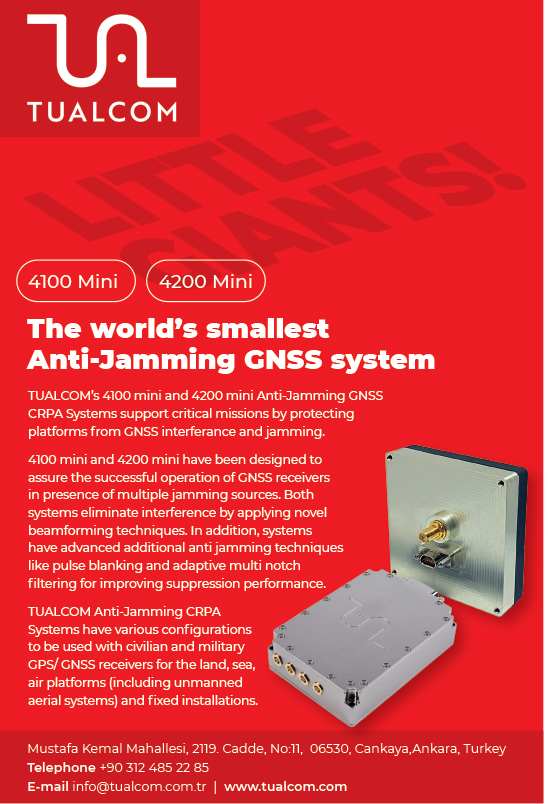
“Even tougher was a SORB [small overlap rigid barrier] test, where the SEM1 hits a barrier at 64 kph but only 25% of the vehicle’s width makes contact with it, so high strength and stiffness are needed for it to ‘bounce’ off the barrier – that’s a conflicting requirement on the physics of the structure with the FFB test.”
The front of the SEM1 therefore features longitudinal ‘crush rails’ that are made from dual-phase steels that crumple in a manner acceptable for FFB test requirements, while above those sit a vertical dash brace made from 1900 MPa press-hardened steel that minimises intrusions of metals or other items into the passenger compartment or battery during crush loads. Behind the dash brace is another 1900 MPa press-hardened steel component: this is a front strut brace tested to support SORB-type load barrier reactions.
“That section alone took about 300 CAE crash modelling sessions to optimise its design,” McGregor says, “We believe it is a world first to design a vehicle this small that can pass a SORB test with good safety ratings and minimal intrusions, but if autonomous robotaxis are to pass muster with safety authorities then it has to be done. Such was the scale of the development and simulation that we published a technical journal on all of it at the SAE Japan conference.”
In addition to the mechanical strength in this and the other sections across the SEM1, the project partners spent considerable effort identifying ways to remove weight to ensure the vehicle could run for extended periods on its all-electric powertrain without being energy-inefficient or slow. The result is that the vehicle’s top speed is actually 130 kph, which is capped by software for safety on city roads.
“Each grade of AHSS has different minimum thicknesses, and parts such as body panels, fenders and doors can go down to 0.6 mm, which really helps save weight,” McGregor says.
In addition, the battery is designed with a unique carrier frame that, unlike conventional enclosures, dispenses with a cover in favour of bolting it underneath the SEM1 frame’s floor. This, with other and smaller measures, saved 37% of the weight compared to conventional sealed battery packs without affecting safety.
This also makes it easy to inspect the modules and cells visually. So, if an intrusion into the pack should still occur, instead of discarding the whole pack (as is common practice), only the damaged module needs to be replaced.
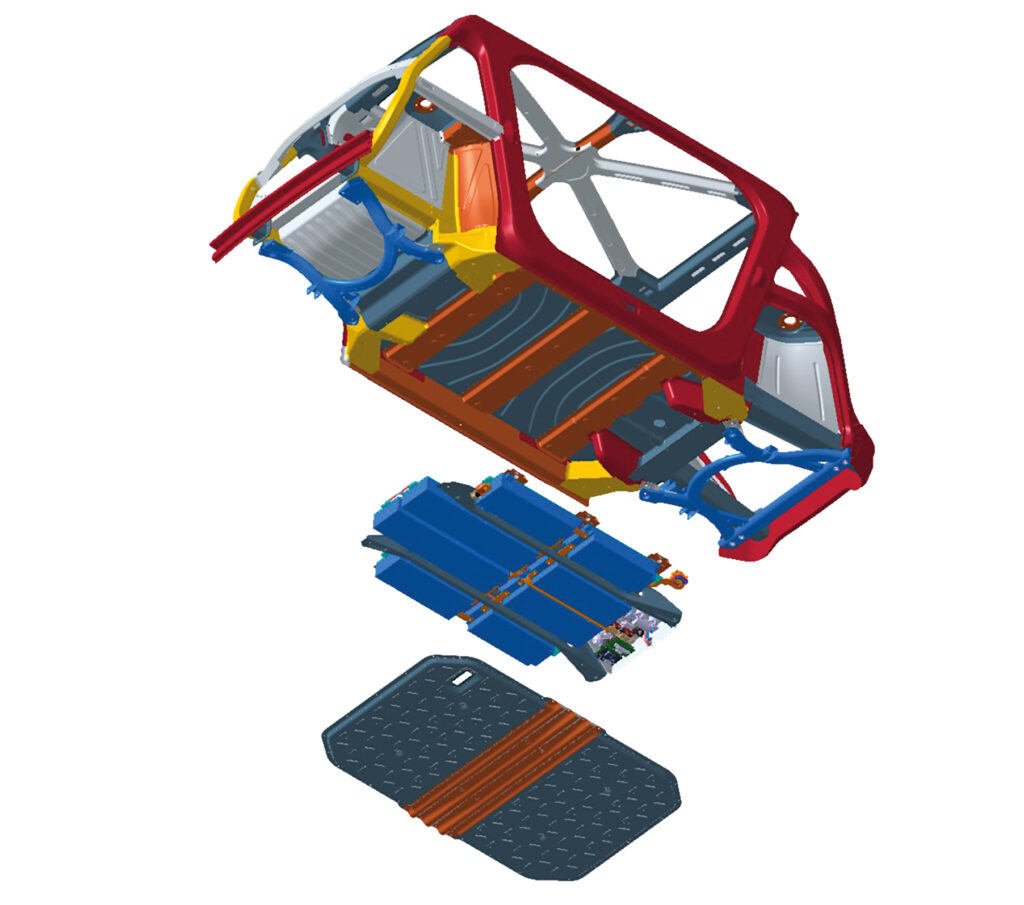
Maintenance strategy
Ricardo used in-house modelling software to simulate timelines of 24-hour duty cycles for the SEM1, including artificial traffic and rush hours, and found that a single charge should be sufficient for operating from 6am to 6pm.
“People might find that hard to believe, but when you look at the duty cycle for taxis, you find there are a lot of lulls in demand throughout the day,” McGregor says. “For instance, there’s a big drop-off in passengers from mid-morning to midday.
“That means it’s also easy to find a 20-minute window for an SEM1 to return to the depot and be cleaned of waste and wear that passengers will inevitably leave behind. It also provides an easy opportunity to fast-charge some energy back into the pack to operate for longer. So, with that kind of opportunity-based maintenance, range anxiety isn’t an issue for us.”
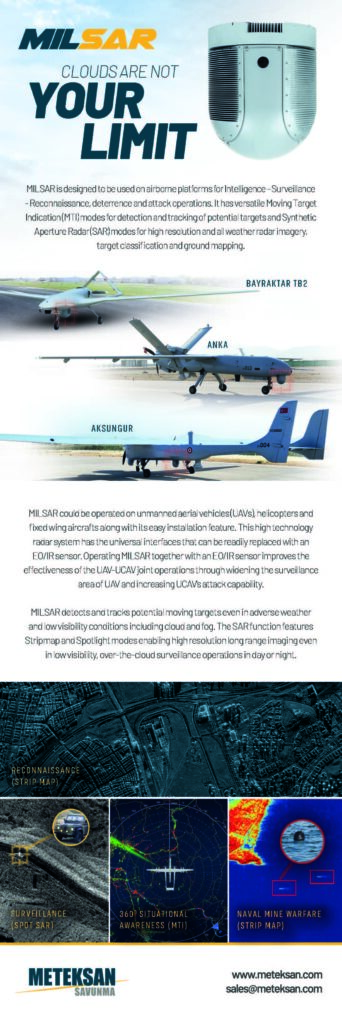
Coates adds that conservative projections for gravimetric energy density through to 2030 have been overlaid onto the duty cycle simulations, and further support the project’s claims that the SEM1 (and by extension the SEM2) are configured optimally in terms of weight and energy for transport duties on modern roads.
Future of the project
Sustainability over the lifetime of the SEMs is a major focus for the project’s partners. Much of the programme has for instance explored how to minimise scrap, with re-use of scrap metal in the fabrication processes potentially enabling 90% use of the steels; conventional automotive production often yields rates as low as 50%.
On top of that, the project identifies various ways to reduce greenhouse gases across the life cycle of the SEMs by 86% (by 2035, compared with theoretical 2020 figures). These include decarbonising steel production by using hydrogen and electric arc furnaces in place of coal, coke and gas, and developing autonomous vehicle control systems to smooth real-world drive cycles and optimise energy use.
Although the cost of transitioning to a green economy are significant, WorldAutoSteel and Ricardo plan to continue their r&d into how interested parties might make viable commercial operations out of the SEM vehicles. “For instance, we have a project with Michigan Tech University, where researchers are evaluating how the SEM2 could be adapted for transporting goods instead of people,” Coates notes.
“Buying vehicles in bulk is expensive, but if fleet owners can use SEM2s for logistics or last-mile deliveries during the off-peak hours for transporting people, that would greatly increase the hours per week the vehicles can generate revenue and the speed at which they break even on their investment.
“As for the OEMs, those who understand how many variations and specialisations of steel there are consider it to be as tailorable as carbon composite,” Coates says. “Our portfolio currently has 64 grades of AHSS; by contrast, the last time WorldAutoSteel did a big project like this, only 27 existed, and that programme concluded in 2010.
“That goes to show just how much product development there’s been over the past 13 years, and how much more we could do for different requirements in future mobility.”
Specifications
- SEM1
- Robotaxi
- Battery-electric
- Single-speed front electric drive
- Four passengers
- Dimensions: 4095 x 1880 x 1850 mm
- Energy: 75 kWh
- Top speed: 130 kph
UPCOMING EVENTS
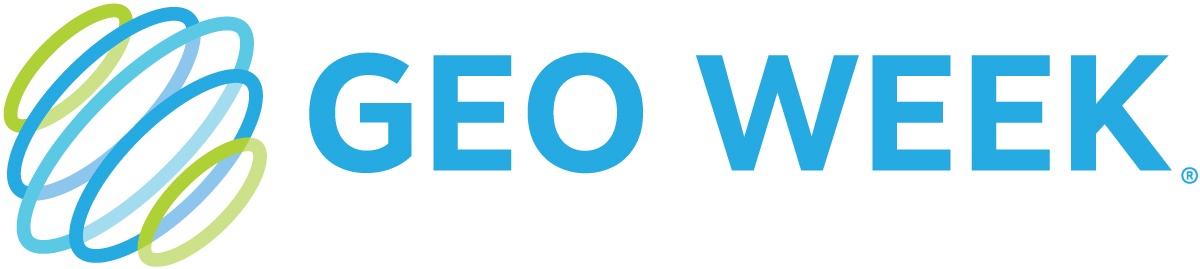
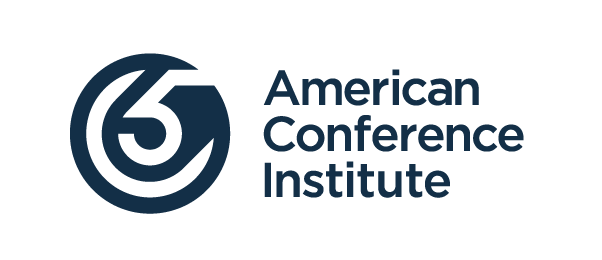
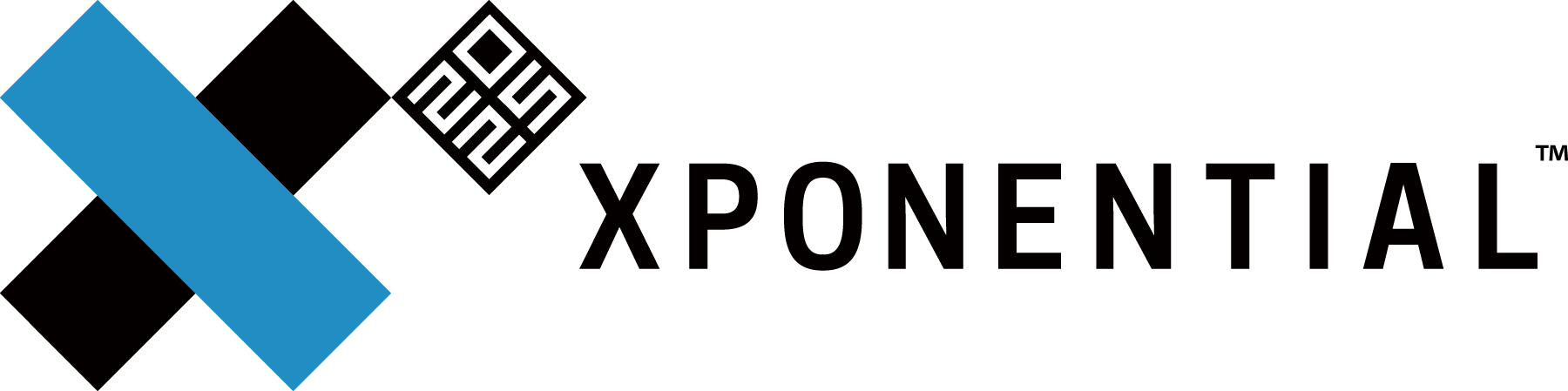
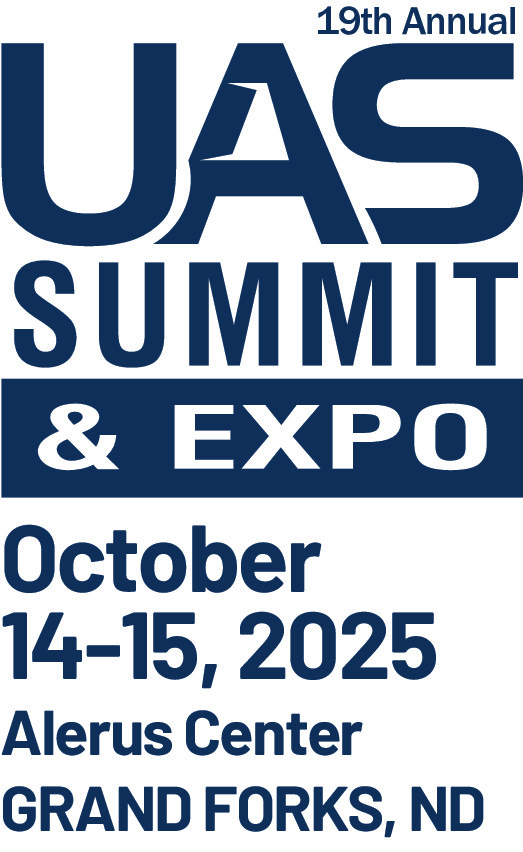
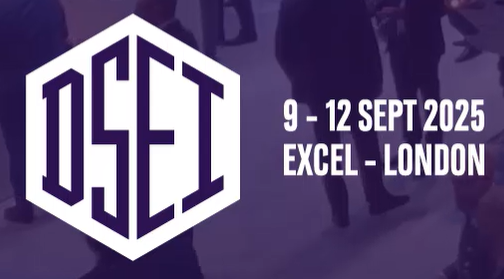
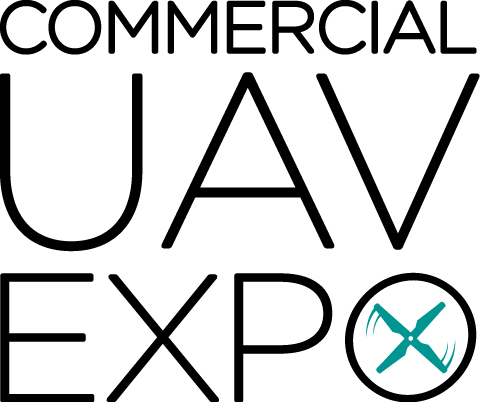
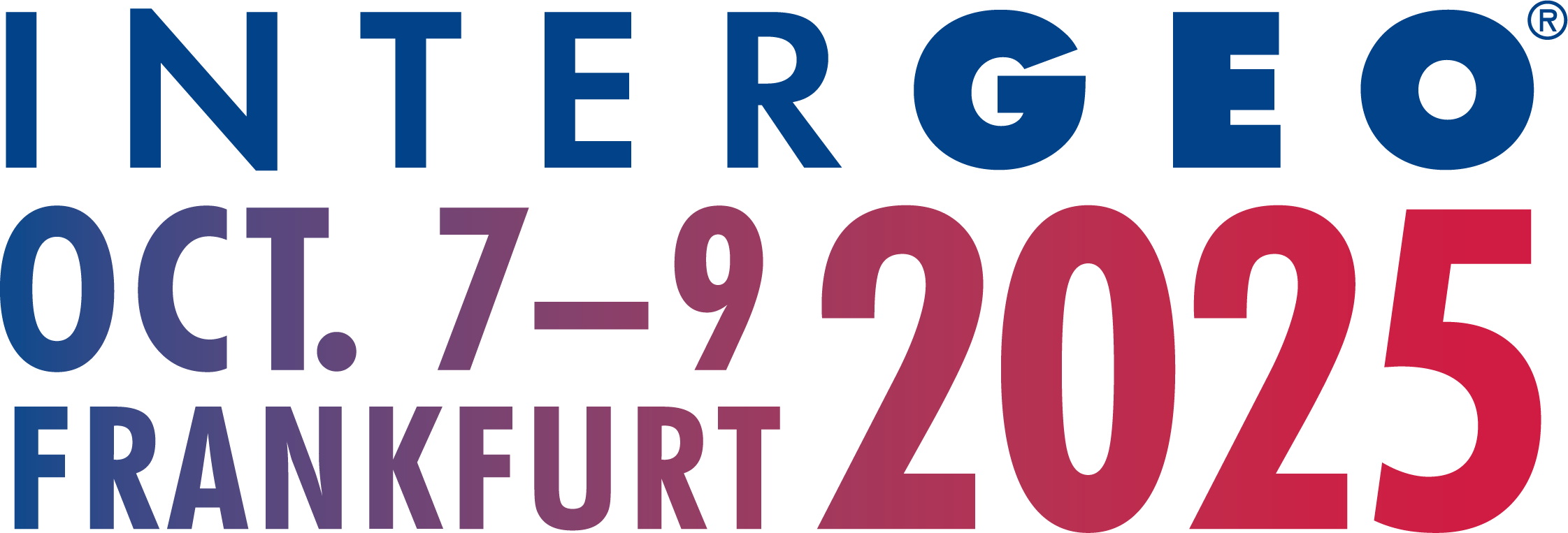
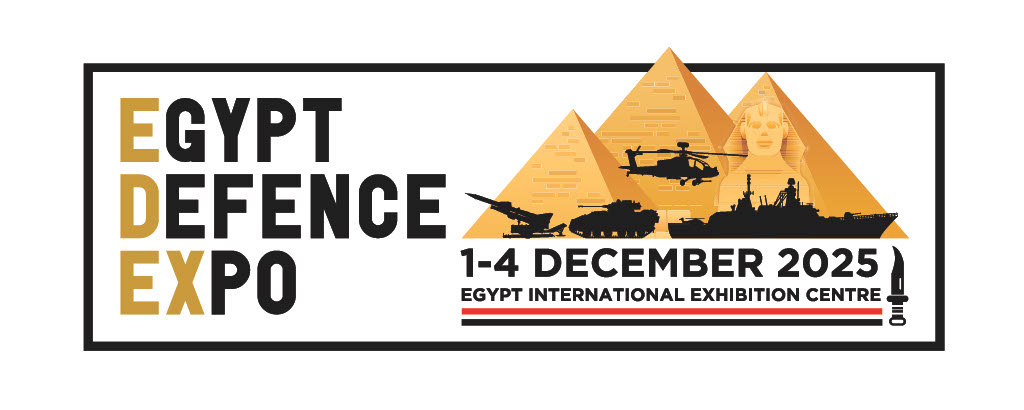
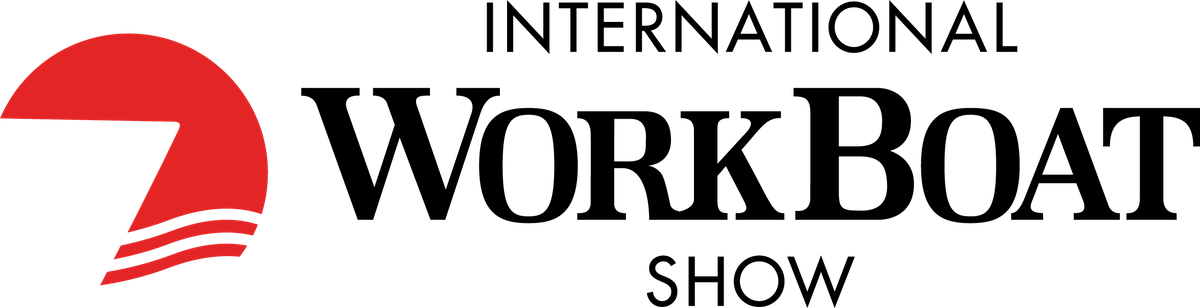
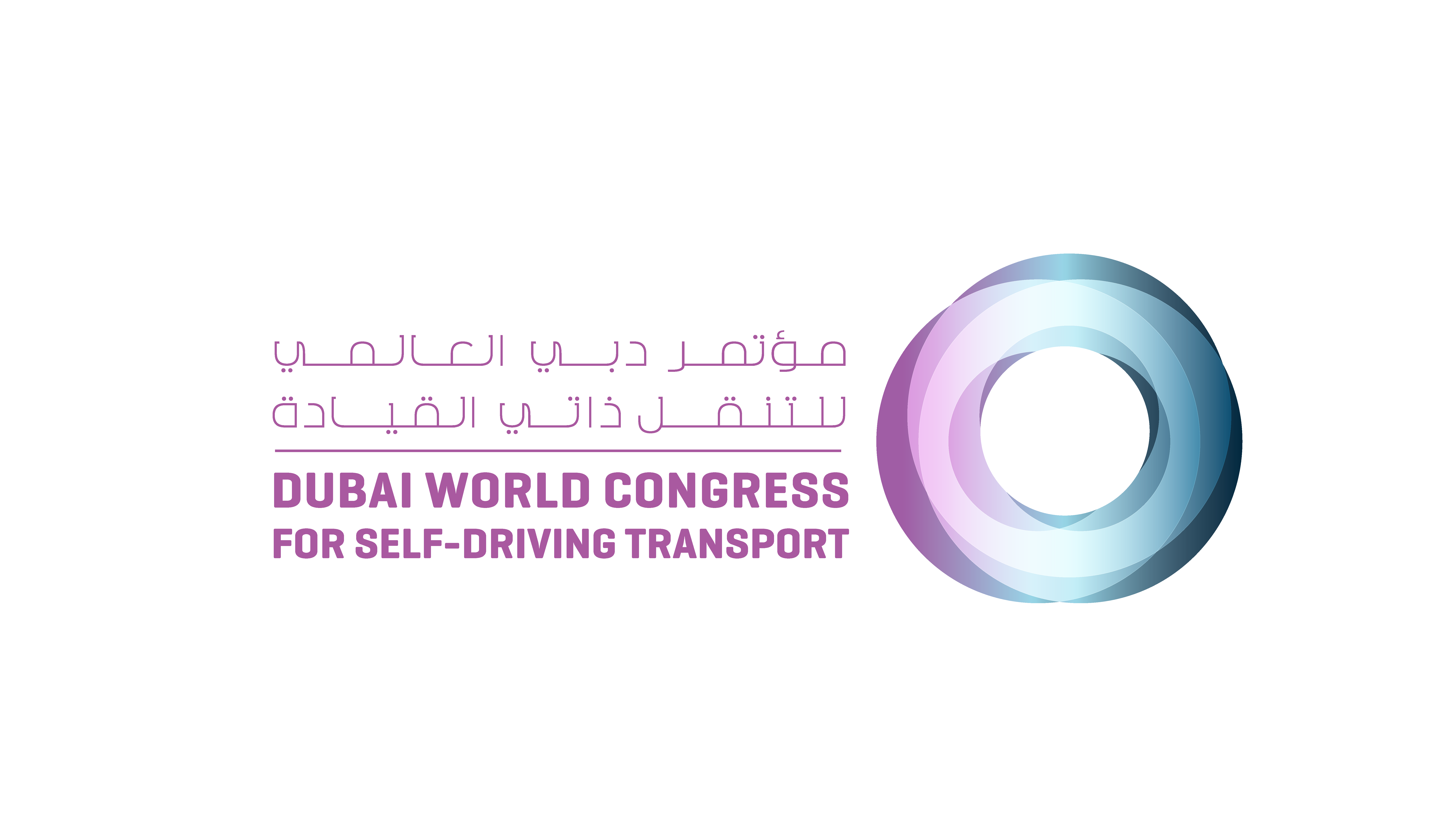
