Professor Barry Lennox
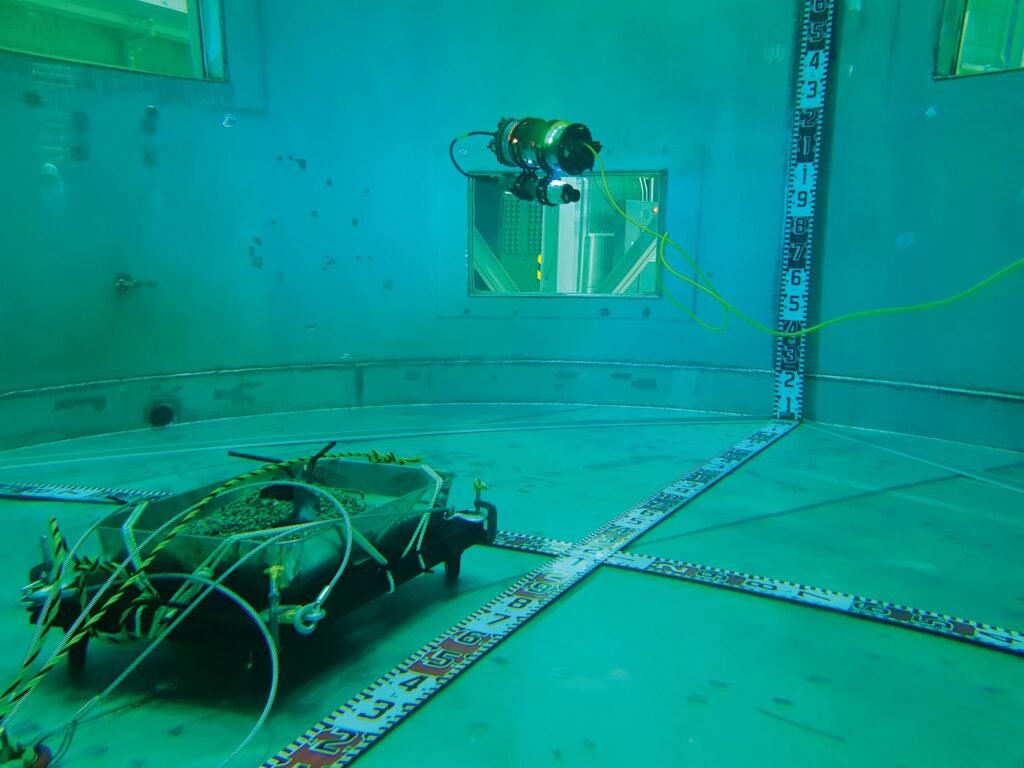
(Image courtesy of the University of Manchester)
Rad-hard robotics
Control systems expert Barry Lennox guides Peter Donaldson through his role in developing robots that make nuclear decommissioning safer and cheaper
Decommissioning nuclear power plants is an immense task. The estimate for the Sellafield facility in Cumbria is £136 billion over more than a century. During the last 14 years, Barry Lennox, professor of applied control at the University of Manchester, has dedicated himself to developing robots that can save users time and money while reducing risk.
Lennox was born in 1969 on the Wirral Peninsular across the River Mersey from Liverpool – close to the home ground of Tranmere Rovers football team, which he is still tribally obliged to support.
While most of Lennox’s secondary school years were spent at the local Neston Comprehensive, between the ages of 11 and 13 he lived in the Shetland Islands (“great fun”), north of Scotland, as his father worked in the oil industry.
Computerised guidance
A mathematics teacher, Mr Dawson nurtured Lennox’s enthusiasm for the subject, which dovetailed with his passion for the emerging personal computers. Later, it was a larger computer, which the local council brought to the school in a van, that helped him choose a career path.
“You entered the subjects that you liked and the grades you were getting into the computer, and it suggested what you should do,” Lennox recalls. The computer suggested chemical engineering, and he chose Newcastle University because it was satisfyingly far away from home while still in the north of England.
A year spent travelling followed graduation, after which he took a job with a construction engineering company. He didn’t enjoy it and returned to education, pursuing a PhD in control systems, offered to him by Gary Montague, one of his former lecturers at Newcastle. Lennox earned his doctorate in 1996.
A career in academia followed, much spent in the field of control systems and condition monitoring at the University of Manchester. In 2002, Lennox was involved in creating a successful spin-out company, Perceptive Engineering, providing process control solutions.
In 2011, he was offered the research chair position in nuclear decommissioning and robotics by the Engineering and Physical Sciences Research Council (EPSRC). “Part of my PhD focused on nuclear and there are lots of potential opportunities for control systems in robotics, so I accepted,” he says.
Nuclear debut
The first challenge his team tackled at Sellafield was the inspection of a highly contaminated pool in the basement of one of the buildings. There was too much radiation for personnel to enter the water and the floor immediately above the pool was out of bounds for similar reasons. The only access was through a room two floors above where there were 6 in-diameter pipes leading down to the pool.
Lennox’s team developed a robot that could pass through the pipe to inspect the pool, which was used later to inspect the Magnox swarf storage silos elsewhere on the Sellafield site.
“Through this application we instantly understood the difficulties of performing very routine inspections when a human can’t enter the facility and the access ways are very limited. There are very few situations when you can simply open a door and walk in,” Lennox says.
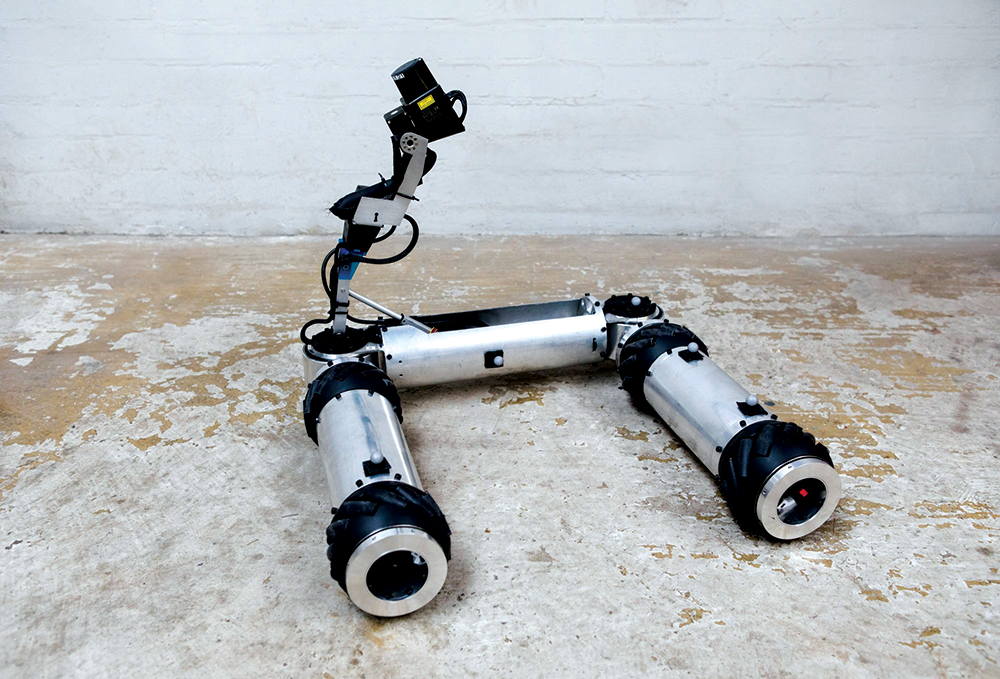
(Image courtesy of the University of Manchester)
“We’ve had to design ground-based, aerial and aquatic robots that can fit through 6 in holes. In the case of aerial drones, we designed them so they had rotors that folded for deployment and retrieval. Our ground-based vehicles had to be reconfigurable.
“Maintenance and retrieval are also difficult, and often can’t be done, so if a robot gets stuck then it could potentially block a passageway for years. This is a problem that they have had in the clean-up of Fukushima Daiichi.”
Also, the likelihood of radioactive contamination makes it unlikely that once deployed, a robot could be brought back into the lab for maintenance or repair, he notes, as some of the material is mobile and likely to stick to its internal mechanisms. In high-dose environments, the gamma rays can damage the electronic systems enough to render the robot useless, although exactly when it will fail is unpredictable.
“This is typically a stochastic process, so a robot could die very quickly or last longer,” he adds.
Radiation hardening
Hardening a robotic vehicle against radiation can be relatively straightforward, but involves trade-offs. The simplest solution is to place all the electronic components into a metal box called a vault, he says – an approach that was used on the Juno spacecraft that NASA sent to orbit Jupiter.
“Radiation in deep space is quite different from what you get on a nuclear facility. In space, larger particles are a bigger problem than gamma and can do more damage, but they are easier to stop. The main problem for nuclear robots is that gamma radiation means the casings to shield the electronics need to be thick, so they can weigh enough to make the robot impractical. We determined that for a very simple mobile robot we would need 20 kg of tungsten to protect it. This was mainly to protect the small processing board,” says Lennox.
As some electronic components that are tolerant of radiation are available, his team is developing a robot to exploit this attribute. This machine will use carefully selected encoders to provide the control computer with position feedback and feature a field-programmable gate array (FPGA) developed in Japan, which can operate at very high dose rates.
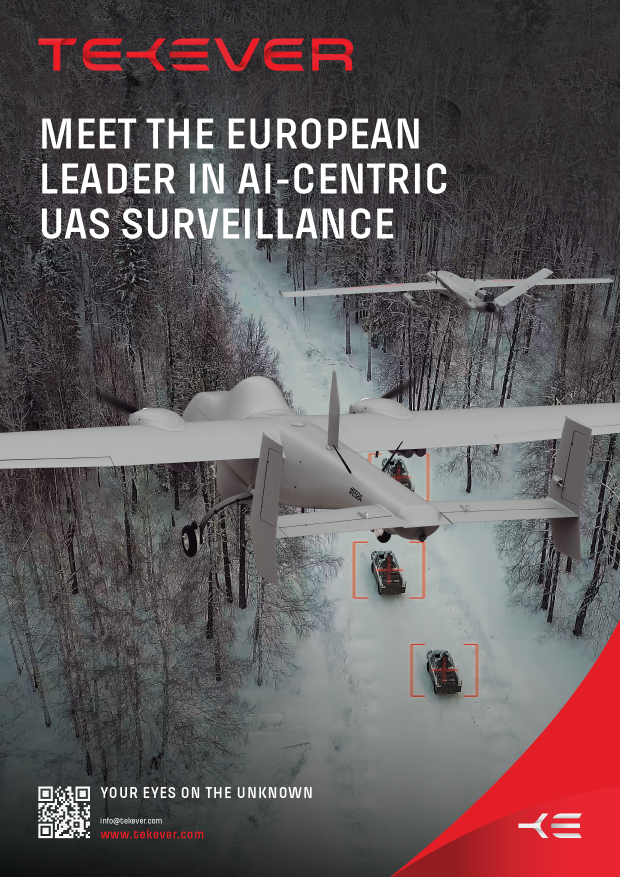
The robot will be low-cost, but will not have the level of functionality typically found in other modern robots.
“It will probably just be able to drive a camera into a radiation facility and move around. We hope to be able to equip it with radiation-tolerant Lidar to automatically avoid obstacles, Lennox says.”
However, the idea that radiation will kill robots is, for the most part, a significant misconception. “This is true in some cases, but there are many examples where radiation levels are relatively low in nuclear facilities – at least for a robot. The radiation limit for a nuclear worker in the UK is 20 millisieverts (mSv) per year effective dose. In our tests, we have found that electric systems can typically withstand about 50 Sv, so considerably more than a human. The 50 Sv figure does vary, depending on the device and when and where it was manufactured, et cetera,” he adds.
Potential with legs
In Lennox’s view, the improvements achieved in the functionality and costs of legged robots are among the most exciting developments of recent years.
“Robots such as Boston Dynamics’ Spot offer huge potential in the nuclear industry because they are quite robust and can move around complex environments,” he says.
“Since robots cannot typically be used once and returned to the lab for further work their cost is very important. It is now possible to buy legged robots that can be used for demonstration and trial purposes.”
He says their interfaces are now intuitive enough for non-roboticists to operate them, which is important because research scientists are frequently not allowed to deploy robots on nuclear sites. Their physical placement into contaminated areas has to be done by nuclear-trained personnel.
Co-operation between research scientists and nuclear professionals is well established, however, as the operation of the Lyra tracked vehicle developed for use at the Dounreay nuclear site in Scotland demonstrates.
“This robot had to be designed so that it could be deployed by nuclear staff, although once deployed we were allowed to drive it,” Lennox says.
Lyra had to be able to fit into a 1 m-high, 100 m-long tunnel, require no maintenance, and be equipped to take video images and collect radiometric data as it moved. Development and testing took about 12 months, while deployment lasted about two weeks, with interruptions due to COVID, Lennox recalls.
“The deployment was very stressful. I was the driver many times and was aware that if I crashed it, or got it stuck on debris, the robot would create a blockage in the tunnel for years,” he says.
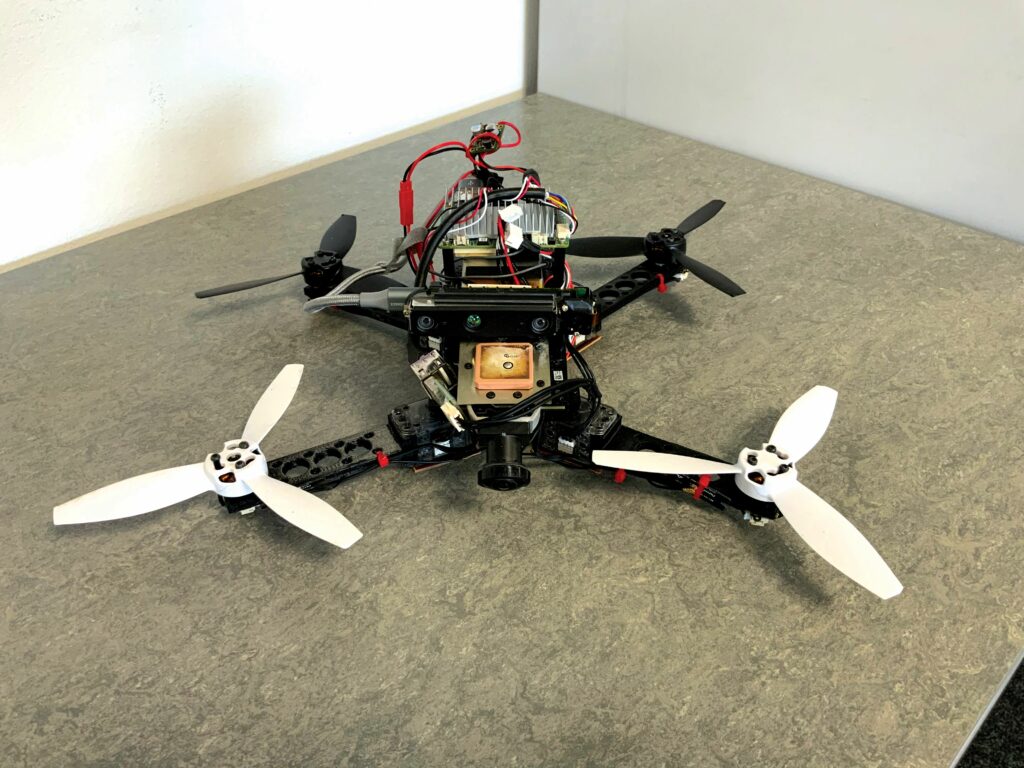
However, the mission was successful. “The Nuclear Decommissioning Authority estimated that the robot saved them about £65,000 and, more importantly, about 2250 hours of higher-risk operations involving personnel in PPE, including airline suits. The cost of the time reduction has been estimated at £4 million to £5 million.”
AI introduction
While AI is heading for ubiquity in robotic vehicles, its use in radioactively contaminated environments is typically kept at a low level, limited to tasks such as obstacle avoidance, Lennox notes, freeing operators to do other things.
“Ideally, we don’t want the operators getting worried about hitting a wall. It can be stressful deploying a robot in a radioactive environment and the more low-level functions that we can take away from the operator, the better,” he says.
Even as AI improves, human operators will remain central to robotics in the nuclear industry, although the balance between them will change, he argues.
“As robots are deployed with greater regularity, the confidence that industry has with them will improve, and it is possible that more AI will be deployed. It is many years away, but technology could reach the point where an operator could open a door and tell the robot to clean up a facility, and then close the door and come back two weeks later, allowing them to complete other more complex tasks that require a human.”
In the near term, Lennox believes the role of autonomous systems, including those incorporating AI, will expand, particularly in the case of UAV systems used to inspect tall structures. “As confidence grows with this technology, they will be allowed to do more and more.”
Together with Rob Buckingham, director and lead for robotics at the UK Atomic Energy Authority (UKAEA), Lennox is working to further AI in the field through the Robotics and Artificial Intelligence Collaboration (RAICo).

Based in Cumbria and led by Kirsty Hewitson, RAICo aims to support the nuclear industry in its development of robotic systems. RAICo unites researchers and application experts from the university, UKAEA, the Nuclear Decommissioning Authority (NDA) and Sellafield to co-operate on the development and deployment of robotic solutions on the Sellafield site, the decommissioning of the JET fusion reactor in Culham, and across the NDA’s nuclear estate.
Lennox acknowledges many people he has encountered through his education and career as mentors. These include his PhD supervisor, Montague, and Professor David Sandoz, who taught him about control systems and their commercialisation, Richard Taylor, professor of nuclear engineering at Manchester University, fellow members of the UK Government’s Committee on Radioactive Waste Management (CoRWM), and his RAICo collaborator, Rob Buckingham.
As a mentor himself, Lennox sometimes faces the delicate task of advising young engineers about working in an industry that divides opinion. After all, they will be the ones who tackle what Lennox sees as the next frontier for robotics in nuclear decommissioning.
“I tend to highlight that whether someone is supportive or not of nuclear energy, there are considerable robotic challenges in the nuclear industry, which are focused on cleaning up nuclear waste that was created many years ago and needs to be safely processed,” he says.
Future manipulation
“Most of the initial applications of robots have been in characterisation. This is relatively straightforward in some respects because you are just trying to understand what materials are there and you don’t need to touch anything,” he says. “The next stage is more difficult and involves manipulating radioactive materials – moving them into storage drums or just moving them from one location to another. And, if possible, doing this automatically.”
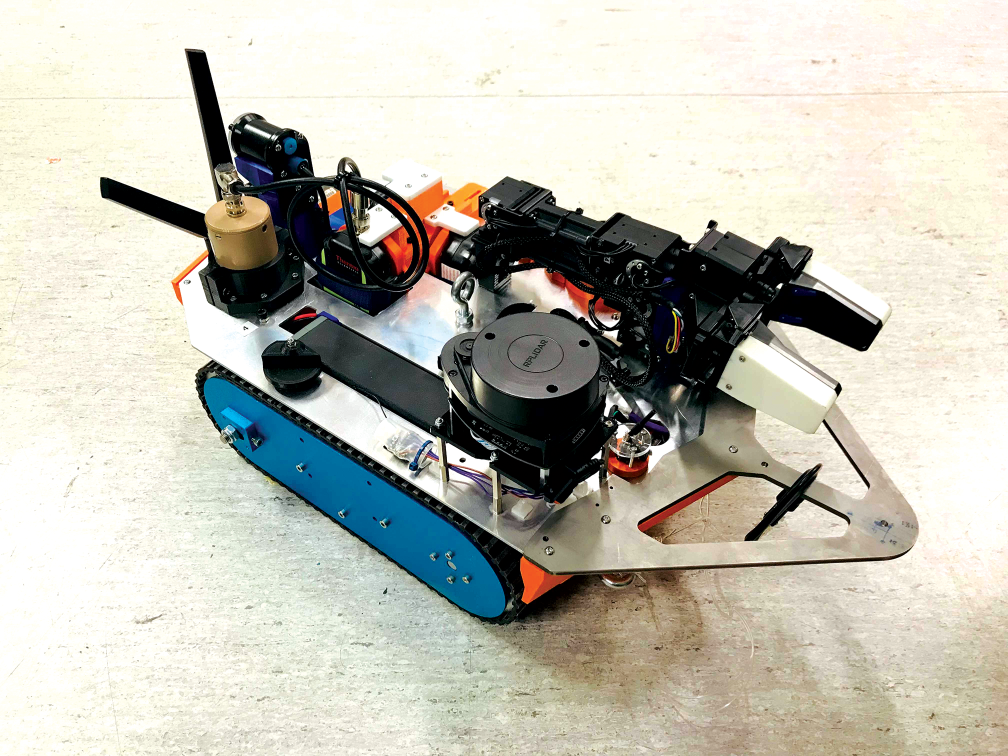
(Image courtesy of the University of Manchester)
His remaining ambition is to see RAICo become a long-term success. “If we get it right it can become a shop window that demonstrates the potential of developing and applying robotic systems into a highly regulated sector.”
Formerly a keen cyclist and hillwalker, Lennox is currently recovering from a stroke he suffered in 2024. “Walking to the local coffee shop can now be a challenge, but I still have hopes that I’ll be able to walk up all the Wainwright hills in the Lake District.”
Professor Barry Lennox
Barry Lennox is professor of applied control in the School of Electrical & Electronic Engineering at the University of Manchester. He held the Engineering and Physical Sciences Research Council (EPSRC) chair in nuclear decommissioning in 2012-14, and holds a Royal Academy of Engineering (RAEng) chair in emerging technology (2019-29).
He is a fellow of the RAEng, a senior member of the Institute of Electrical and Electronic Engineers (IEEE), a fellow of the Institution of Engineering and Technology (IET), and the Institute of Measurement and Control (InstMC), and a chartered engineer.

Lennox received a BEng in Chemical Engineering and a PhD in control systems from Newcastle University, and before being appointed a lecturer in control systems at the University of Manchester in 1997, he worked as a research associate and fellow at Newcastle and Monash Universities.
UPCOMING EVENTS
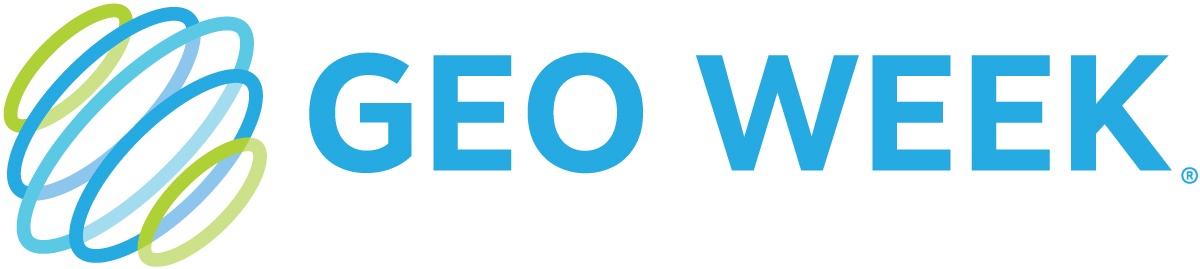
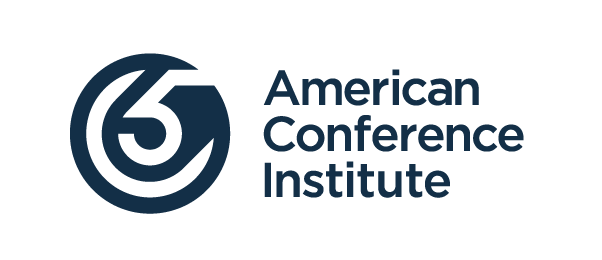
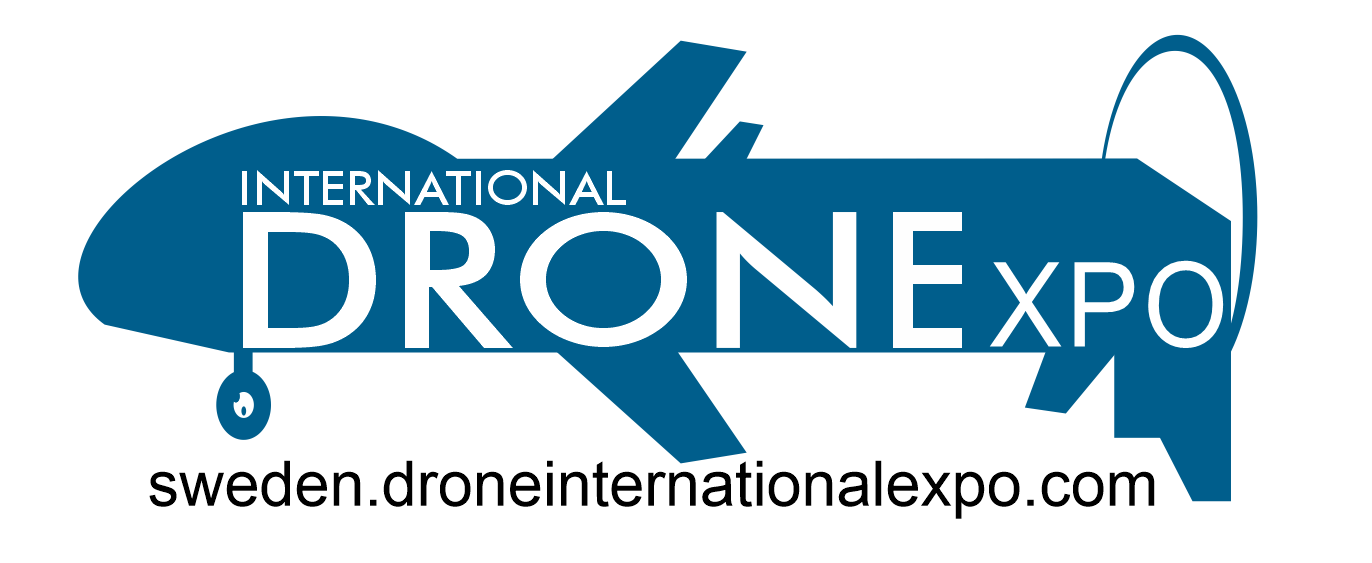
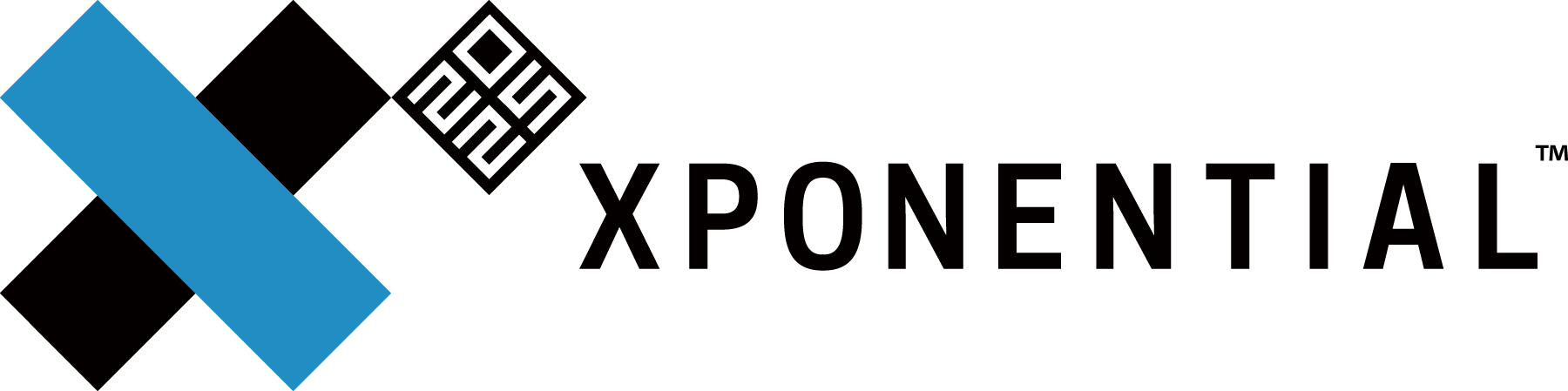
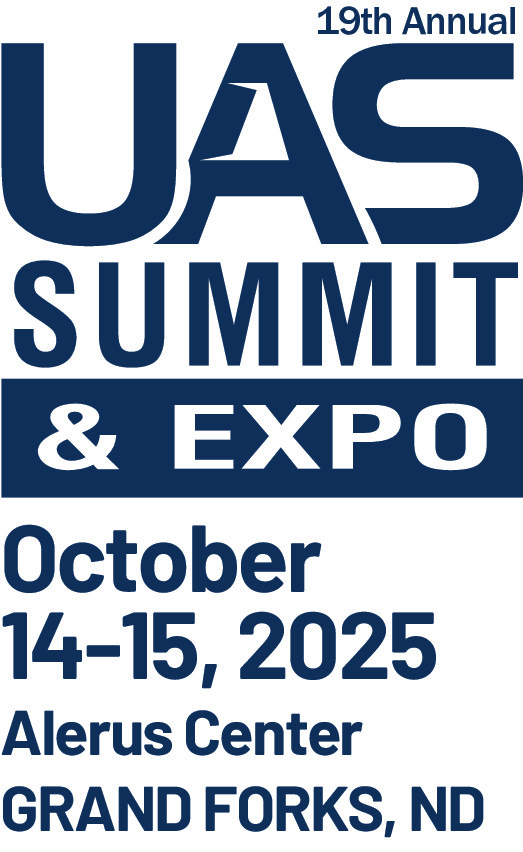

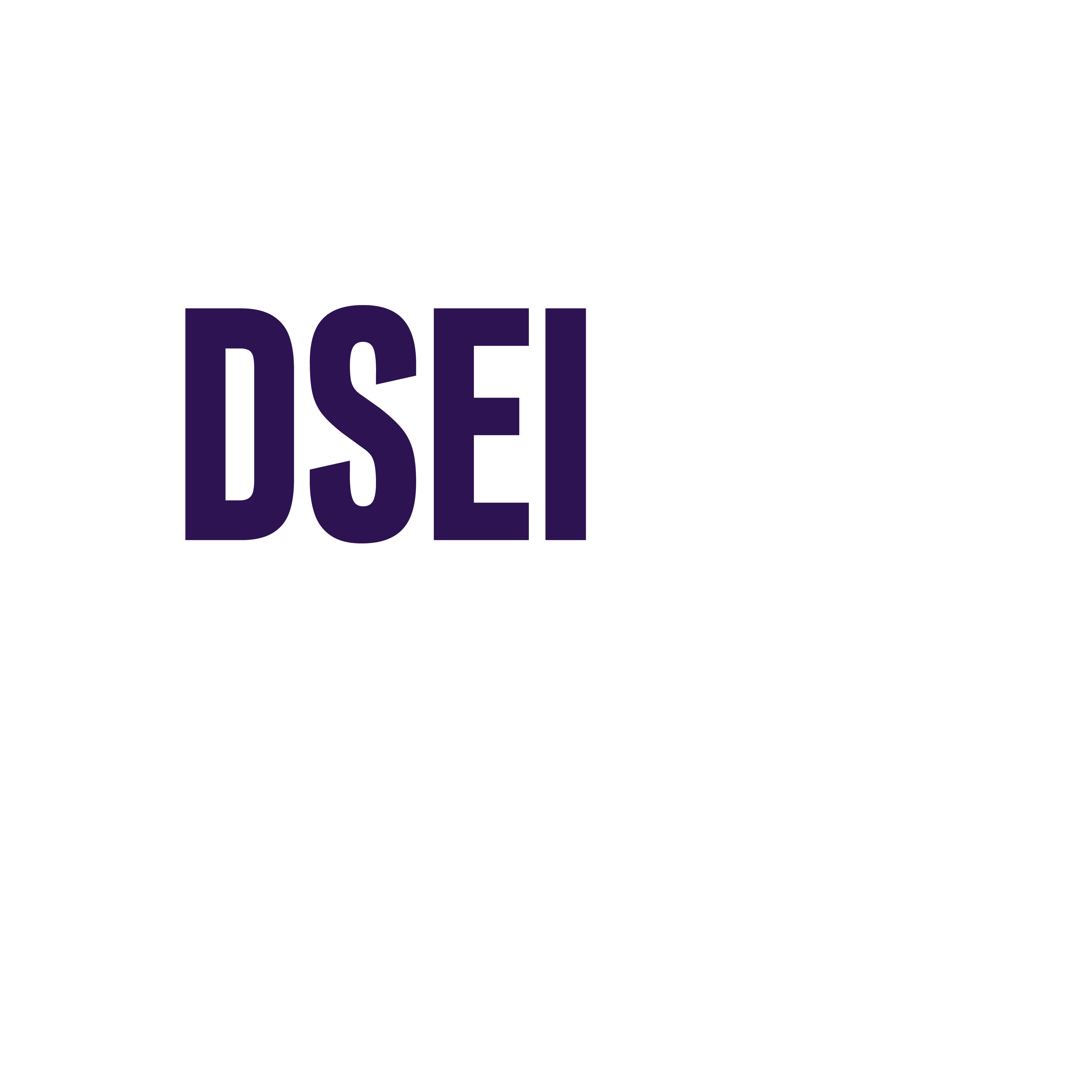
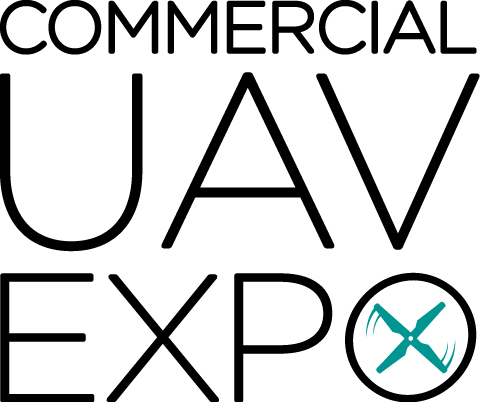
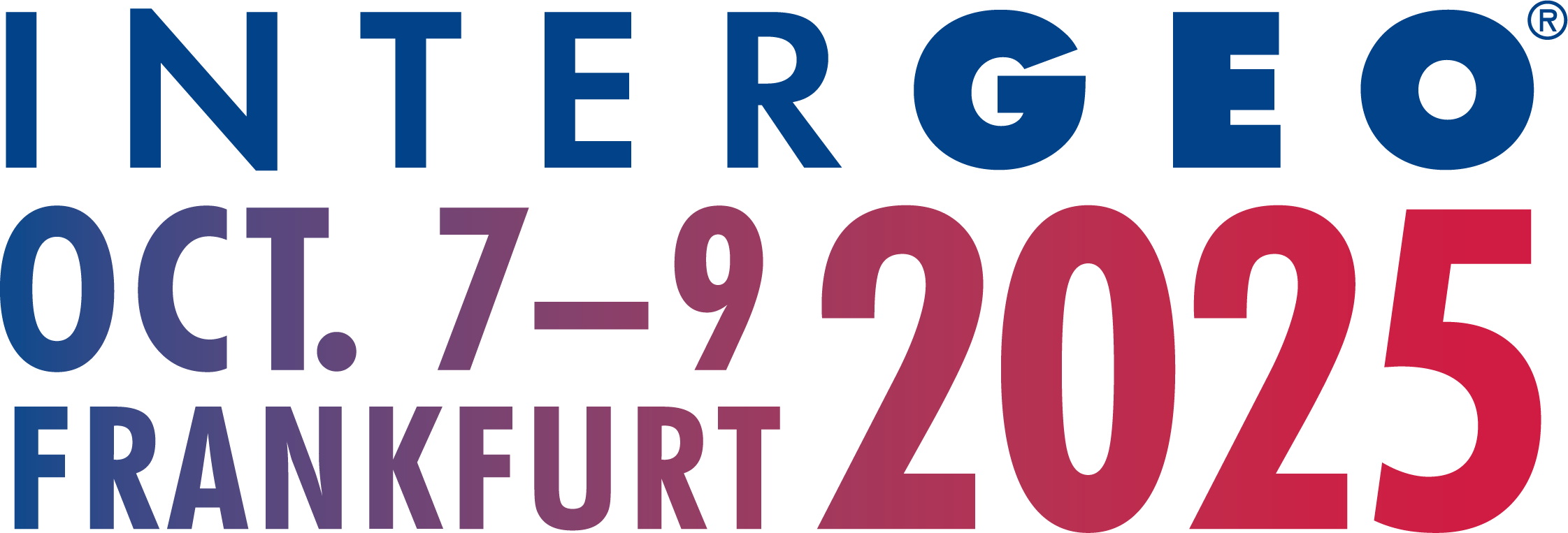
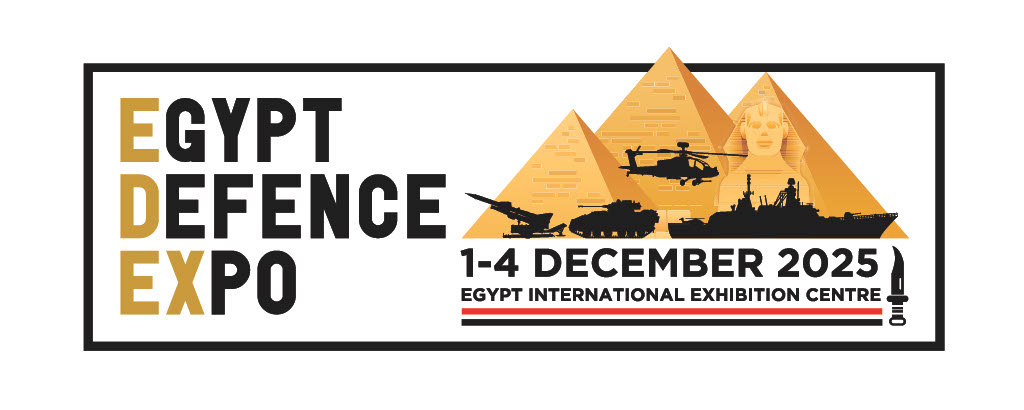
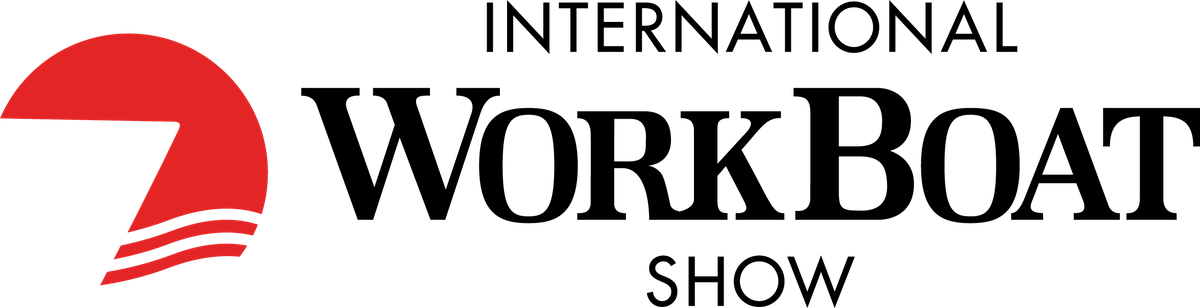