Professor Alan Wilson
Motion Capture
Peter Donaldson discusses animal biomechanics and robotics with Alan Wilson, Professor of Locomotor Biomechanics at the Royal Veterinary College, London
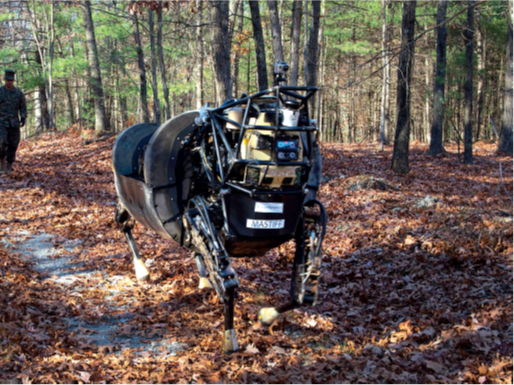
(Courtesy of Boston Dynamics)
Although he describes himself as more of a physicist than an engineer, Prof Alan Wilson has always loved building things. His recent repertoire includes multi-copter UAVs, a manned light aircraft and multiple sensing and tracking packages – all as tools in his quest to learn more about how animals move.
Through this work, he has developed views on the strengths and weaknesses of UAVs as research tools, along with considerable insight into the technology of legged robots. He has also collaborated with robotics design company Boston Dynamics.
The path to his current position at the nexus of biomechanics and robotics took him through studies of maths and sciences at school in his native Glasgow, Scotland, and international competition in middle- and long-distance running.
Along the way, he also developed an enthusiasm for building model aeroplanes and electronic devices, as well as for what he calls “fiddling with mechanical stuff”. From this combination emerged a keen interest in physiology.
“I was always on the mechanistic side of biology; that’s physiology,” he says. “I have an interest in how stuff works and an inherent confidence that I can make anything. Obviously that’s been proved wrong on a regular basis, but who doesn’t take the back off the TV and wonder why they’ve got a few bits left over afterwards? I’m a serial dismantler and re-assembler.”
When the time came to go to university, also in Glasgow, he applied for engineering as well as veterinary degree courses, and the vets said yes, he recalls. The veterinary degree allows for an ‘intercalation’ year in which to study other sciences, so Wilson took a physiology degree along with courses in sports science and computer science, which included programming in Fortran 77, C and other languages. He immediately followed these with a PhD in orthopaedic biomechanics.
Gauging bone
“I spent a lot of time sticking strain gauges to bone and talking about implant design, sitting alongside engineers doing finite element modelling of bones, and measuring stuff,” he says.
“Biology is a hard environment to measure in. Bone is highly anisotropic, bodies are full of salt and water, so implants corrode, and there’s the challenge of waterproofing electronics, particularly in moving bodies.”
That was particularly important to his work in sport, including studies of greyhound and racehorse locomotion, for example. “Eventually, if you’re interested in sport, running, speed and athleticism, you really ought to look at the cheetah,” he says.
The chance to work with cheetahs came through his mentor, the late Professor Craig Sharp. “Craig was one of these omni-competent people – he was a squash player, held the record for running up Mt Kilimanjaro, and was exercise physiologist for the British team for four Olympics,” he says.
Decades earlier, in Kenya, he had measured their maximum speed at 64.3 mph (103 kph) That was a two direction average measured using a stopwatch, the Radio Kenya time signal, a Land Rover, a piece of meat and a cheetah. “It was classic derring-do,” Wilson says. “And that was just a pet cheetah, so they must go much faster in the wild when they are really trying, we thought.”
Cheetah hunting speeds
With more advanced technology, the opportunity came in 2012 to get a better picture of cheetah performance in the wild.
“At that point, we were building small GPS trackers and putting them on birds to look at aerodynamic interactions in flocks,” Wilson says. “So we took some bird trackers, built them into more substantial boxes and put them on some wild cheetahs.
“We captured 500 hunts in the end, and found that cheetahs hunt at about half maximum speed. We never saw them go as fast as Craig did because – it’s obvious when you think about it – manoeuvrability is highest at low speed,” he notes.
“A cheetah at its top speed is generating a lateral acceleration of 13 m/s2 – which is massive – and it has a turn radius of 65 m. In other words, it could not turn around on a football pitch. Velocity squared hurts, be it a fighter jet or a running animal.”
Wilson’s team also looked at the escape space for an impala being chased by a cheetah, which is a maximum-rate turn because it is where the two animals are most evenly matched.
“It comes down to the equivalent of a performance envelope in fighter aircraft: the velocity/acceleration envelope it can operate in and hence where it can get to in a given time. In an aircraft it would be measured in seconds, but with a cheetah you break it up by strides, because a stride is an actual break for a running animal in which it can make a manoeuvring decision.”
Legged robots
Wilson’s first contact with robotics came in the late 1990s with a visit to the MIT Leg Laboratory, where he met Marc Raibert, author of the seminal 1986 book Legged Robots That Balance and founder of Boston Dynamics.
Preoccupied with sensors and instrumentation, particularly accelerometers, at a time when an accelerometer cost around £1000, he was impressed by the new technology in use. “I remember visiting MIT and seeing a little Murata MEMS gyroscope and thinking, ‘Wow, what could you do with a gyroscope like that?’ Such things didn’t exist in our realm.”
Wilson’s collaboration with Boston Dynamics included becoming involved in the Cheetah robot built for the US Defense Advanced Research Projects Agency, which ran at a record speed of 18 mph on a laboratory treadmill in 2012.
While impressive for a legged robot, that speed is nothing like as fast as its feline namesake. Wilson says the major challenges with legged robots are in the areas of power consumption and control, which animals have had millions of years to evolve.
In terms of power consumption, legged robots have a long way to go to match animals. Boston Dynamics’ Big Dog robot, for example, uses a 15 bhp (11 kW) two-stroke engine to drive the pump that provides the pressure for its hydraulic actuators, and as the concept of a 15 bhp dog suggests, it consumes about 20 times the power of an animal of the same size, Wilson notes.
Elasticity and control
“Muscles are good at generating lots of force in a single stroke,” he says.
“You have a single actuator that can be powerful, damping and elastic, changing its properties in a fraction of a second. So you can have a lot of control and amelioration of energy in the system.
“Animal and human legs are very elastic, and muscles are very good at storing energy. You can jump off a table, and run down a hill quite efficiently and quickly. You might hurt the next day, but that’s just showing how much energy you are dumping.
“So biological systems have an advantage here, but robotics has always gone for classical control, which means control of position. So you make your robot rigid, as the last thing you want is for it to be elastic in any way, because then you can’t predict motion.”
However, he adds that engineers can measure motion accurately with MEMS IMUs to enable corrective inputs.
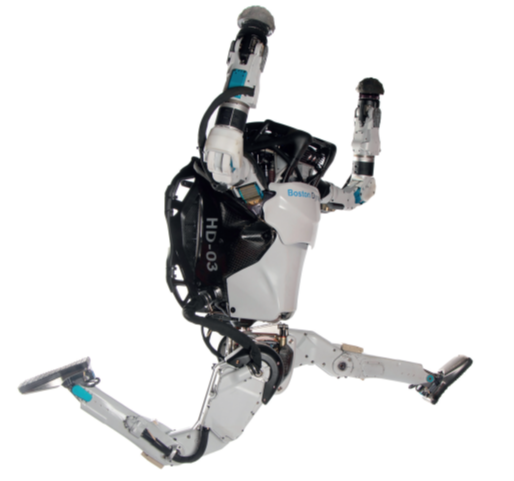
(Courtesy of Boston Dynamics)
He compares the control problem to the one that faced SpaceX in the development of rocket boosters that can land vertically. Noting that each rocket motor is on the equivalent of a Stewart platform – which uses six hydraulic rams to generate realistic motion in aircraft simulators, for example – he explains that controlling them is non-trivial, because there are orientations the platform cannot take up owing to geometric limitations.
“You cannot take it from one position and move it to another by whatever route you fancy; there are only a certain number of prescribed routes you can follow,” he says.
“The animals I work on are designed particularly for running and walking, to oversimplify somewhat. A horse weighs about half a ton, yet it has skinny legs that are very strong but elastic. That matters, because if you take a straight strut of a leg and put a large load on it, it will buckle or break, while an elastic leg will stretch the mechanical impulse out over time.
“Springy legs are inherently complex in some respects, but they also perform quite simple movements quite economically. It is a matter of versatility versus specificity in structural design that animals have had rather a long time to refine.
“It’s something that the robotics world is coming to terms with, because it is a much harder system to control and it requires much more in terms of real-time control.”
Kicking a dog
Wilson comments that the really impressive thing about Big Dog in demonstration videos is when people kick it to try to knock it over.
“You don’t know what your body motion is going to be until it happens, and then you don’t know what compensation you have to make until you see where you are going,” he says. “So you sense motion and then act to compensate.”
The robot takes several cycles to recover, but Wilson argues that this is a good thing as it reduces the loads on the legs. “By no means is it a good thing to correct within a stride, because that means you apply forces that might exceed mechanical limits. Say you just push harder; that’s great until the leg breaks or the foot slides.”
Many legged robots use hydraulics because of the need to apply a wide range of force levels responsively to legs moving at low cyclic frequencies, such as 1 Hz, for which electric motors are not so good.
“Hydraulics are lovely things, they deliver remarkable amounts of energy very quickly and with quite exquisite control. The downside is that you throw away a lot of energy in doing so.
“Take a hydraulic ring main at 3000 psi. You are probably going to dump a quarter of the energy in the control valves, and much of the rest in the actuator. Any hydraulic system spends a lot of energy making oil hot, but you get some work out of it in the end!”
Actuator technology is an area of robotics where there is a lot of room for improvement. “The perfect actuator is certainly a long way away from existing,” Wilson says.
Airborne science
Much of the science he does involves tracking animals in the wild, particularly in the open spaces of Africa where the use of aircraft is essential, along with aerial survey work. It encompasses creating instrumentation packages placed on animals (miniaturised to record without affecting their locomotion or behaviour) and sensor suites for various multi-copter UAVs and a Groppo Trail manned light aircraft.
He has also used quadcopters for PIX4D survey work, which combines photogrammetry and CAD. That makes computer reconstruction of the environment – “anything from game trails to trees and other obstacles” – much easier.
UAV pros and cons
He says using quadcopters for his work has limitations such as licencing issues, noise, lack of range and the cost of the higher-end systems.
“Where I work in Africa, turning up with a UAV is instant trouble for a variety of reasons, from natural government concerns about security issues to the general public being a nuisance with them and the fact that they could substantially disturb wildlife,” he says.
“If you film elephants with a UAV, a quadcopter 100 m away will disturb them, probably because it sounds like a swarm of bees.”
For these reasons, he and his colleagues built the Groppo Trail from a kit, equipped it with a sensor suite including a Lidar that can be operated by the pilot, and he flies it himself on surveys and tracking missions.
One area where UAVs shine in his animal tracking work though is as platforms to relay the signals from GPS equipped collars, which are typically fitted with LoRa radio modules that transmit very small volumes of data.
“I only need the last bit of the GPS position because I know it’s in the southern hemisphere, and I know it’s within 100 km of where it was yesterday,” he says. “So I can transmit 40 to 60 km over LoRa from an aircraft or a UAV.”
He reports that a growing number of masts are being built to carry LoRa WAN services in support of anti-poaching operations. “Using a bunch of UAVs is easier than setting up masts, so as radio platforms they have a lot going for them, and they are especially useful in the low infrastructure environments where I work, which are utterly vast.”
Wilson was made a Fellow of the Royal Society of London in April 2020 for his outstanding contributions to science. “In career terms, that’s probably the biggest box you can tick from a science point of view,” he says. “I am very fortunate to have a job I enjoy very much, and hope to continue my research for a long while yet.”
He comments that instrumentation is becoming a “well-grazed field” but adds that there is still novel work to be done, particularly in understanding legged robot control. “Control is a very broad term, from control through structure to control through active instrumentation.
“I will carry on with the aviation side of things, with the flight research that’s going on in the lab. “The term ‘legacy’ sounds a bit over the top, but an important part of my role is to mentor and develop the next generation so they can deal with all the things we couldn’t do.”
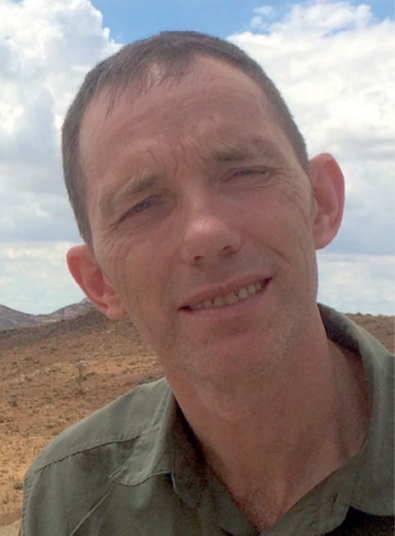
Professor Alan Wilson
Born in 1964, Alan Wilson attended the Glasgow Academy in his native city, going on to study veterinary medicine and physiology at Glasgow University, graduating in 1987.
A PhD in anatomy from Bristol University followed, focusing on the mechanical basis of tendon injury. Remaining at Bristol University, he worked as a postdoctoral research associate and then as a lecturer, moving to the Royal Veterinary College in 1996. He is a director of the Company of Biologists, a non-profit publisher that supports and inspires the scientists.
UPCOMING EVENTS
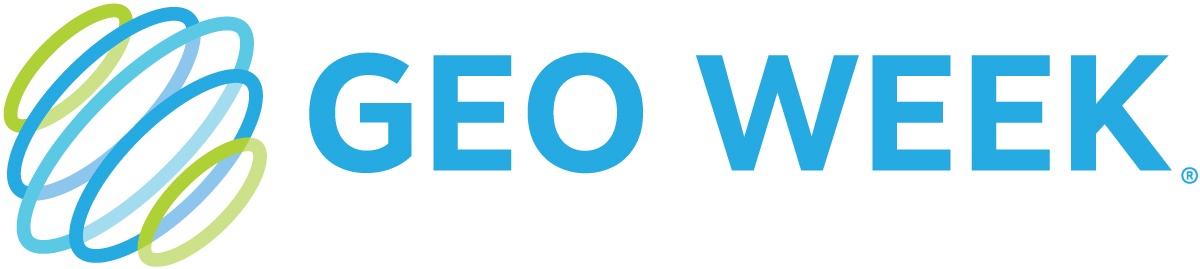
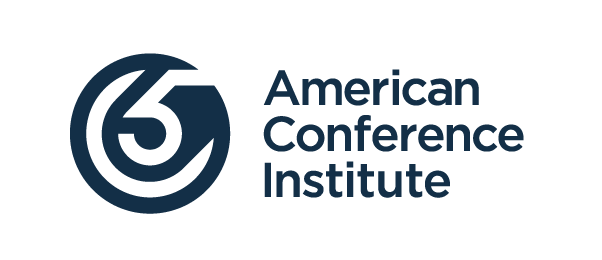
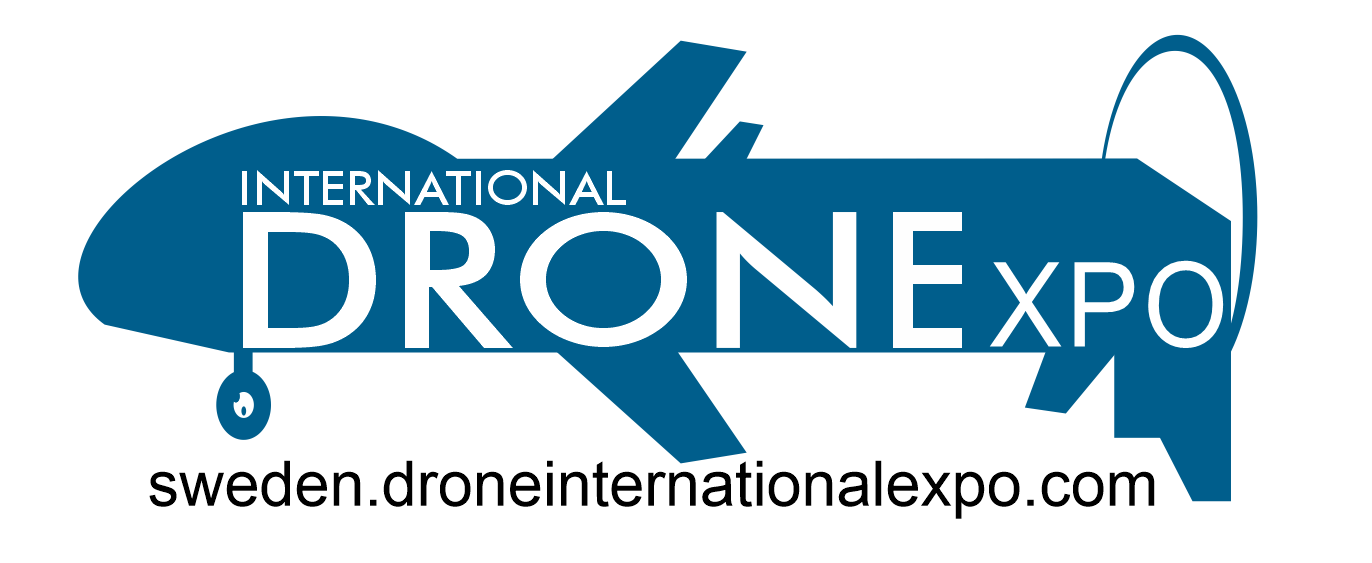
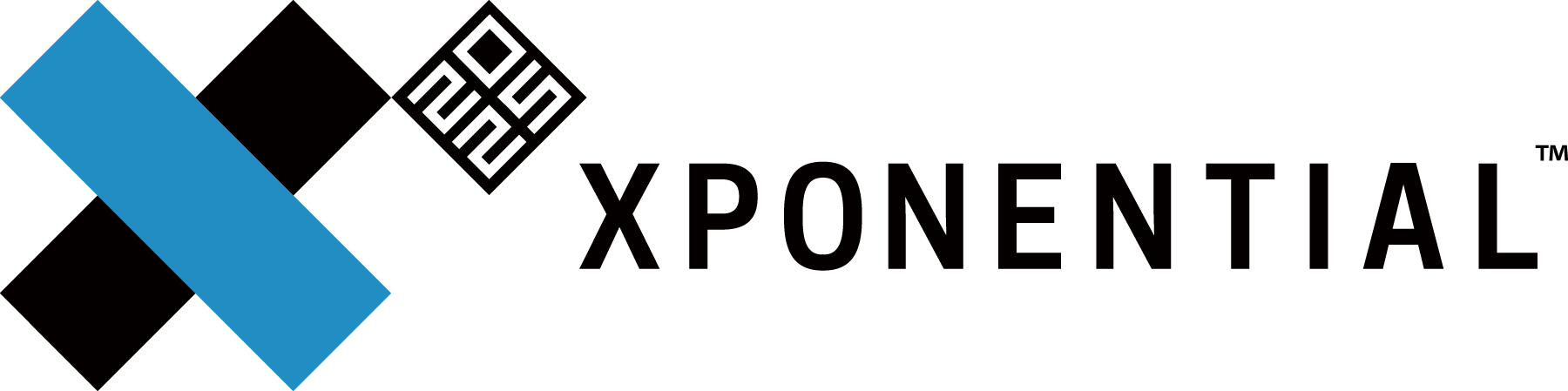
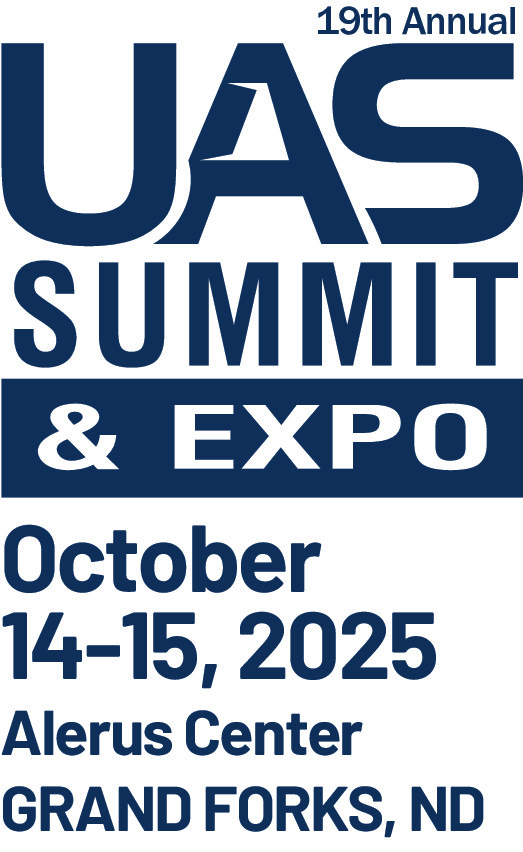

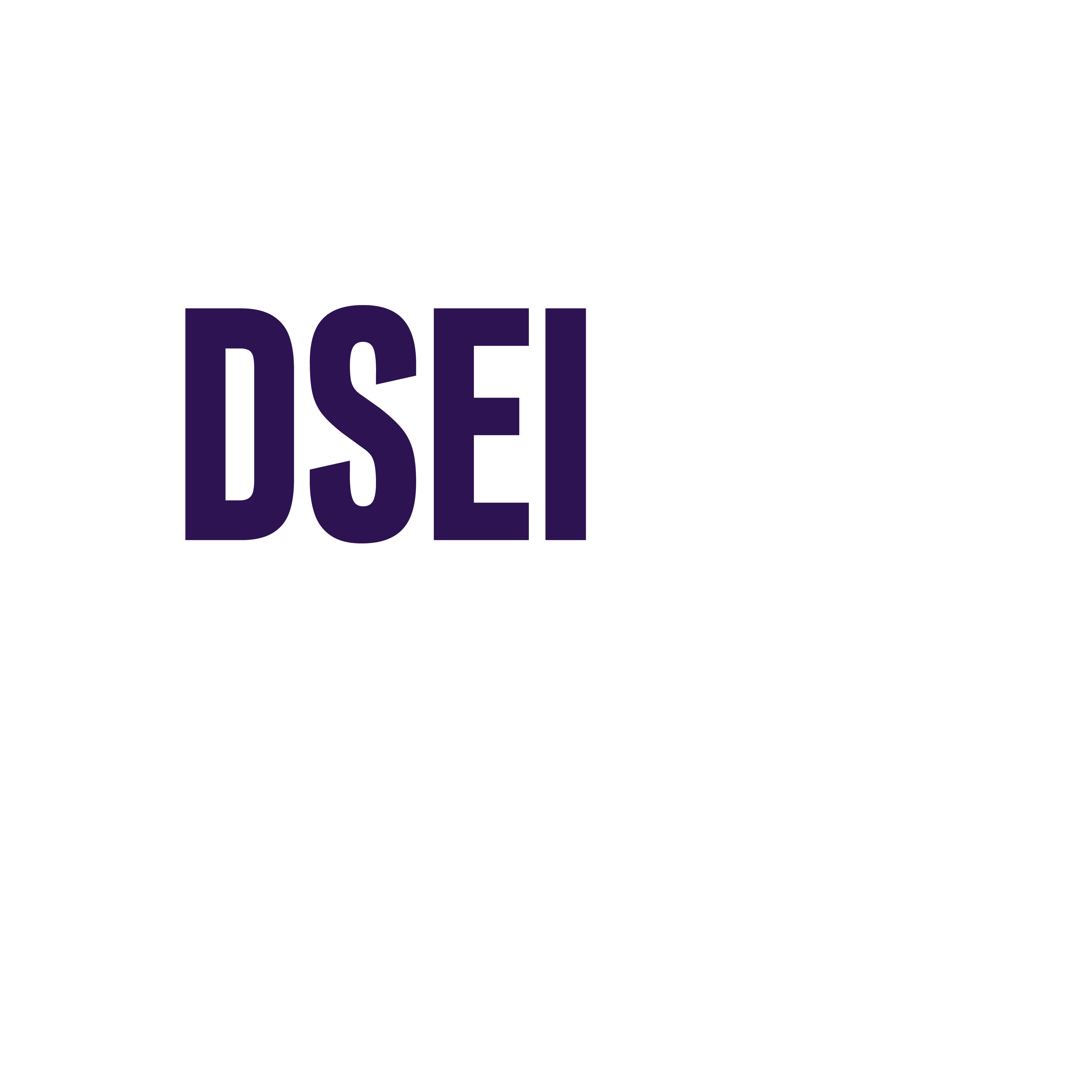
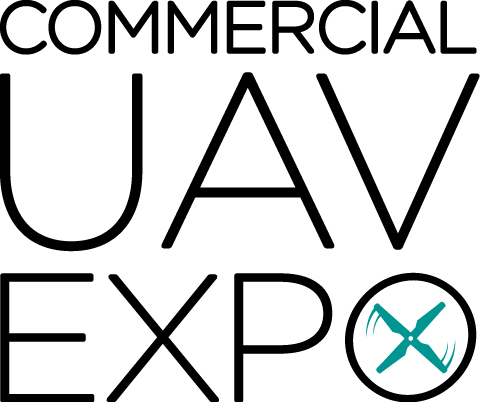
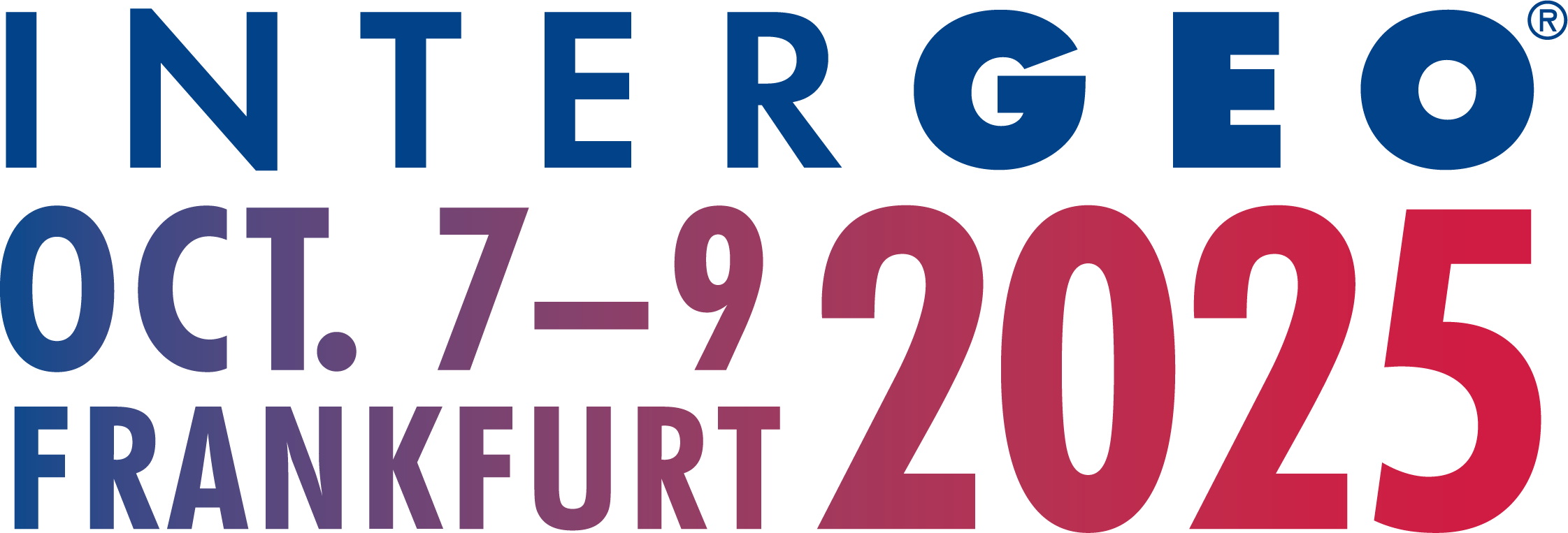
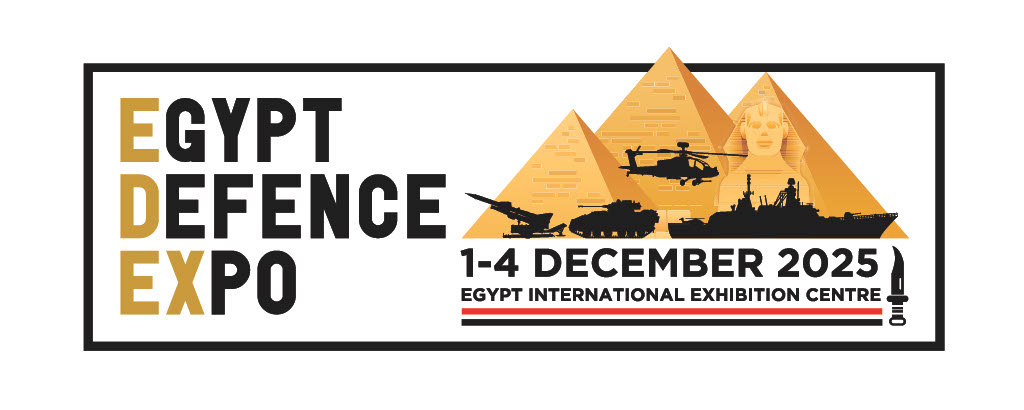
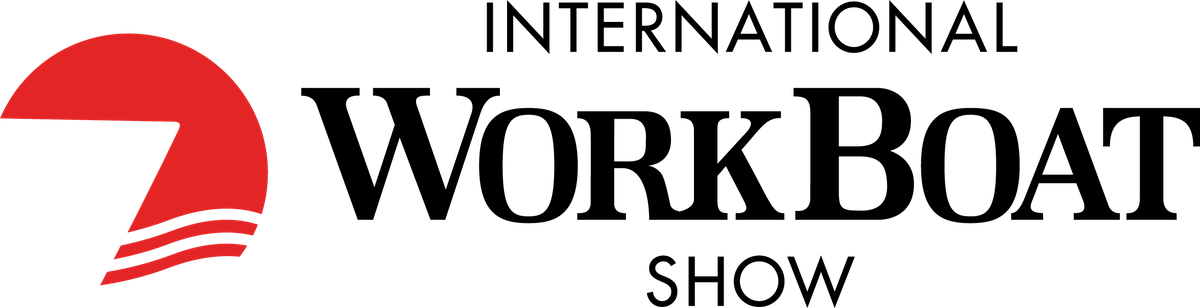