Oceanology International 2022
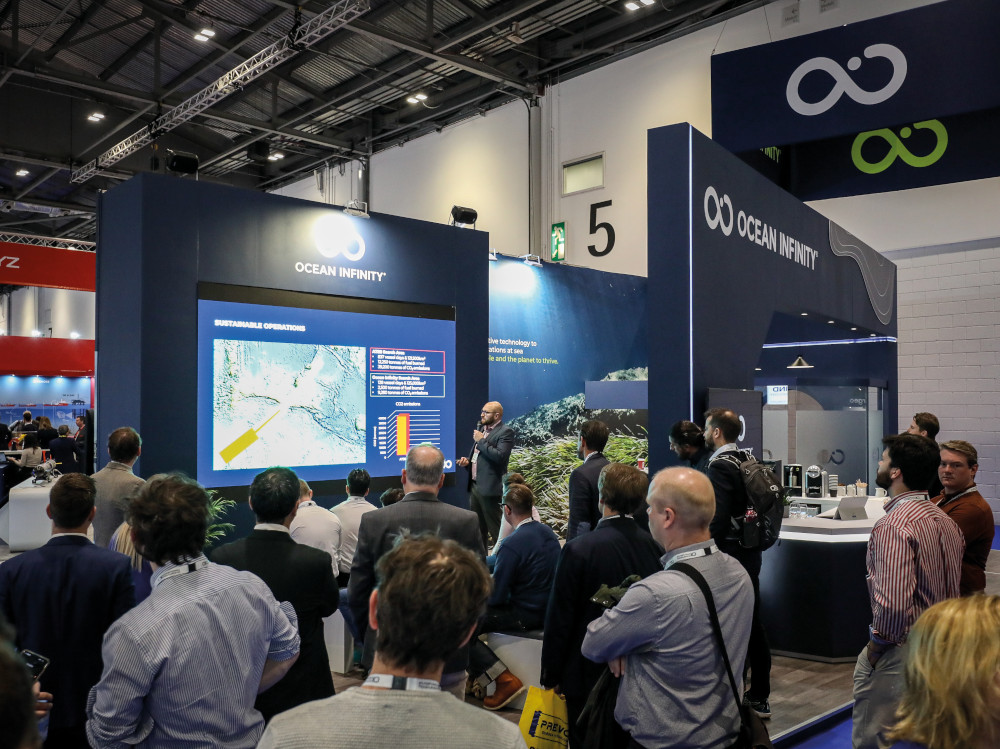
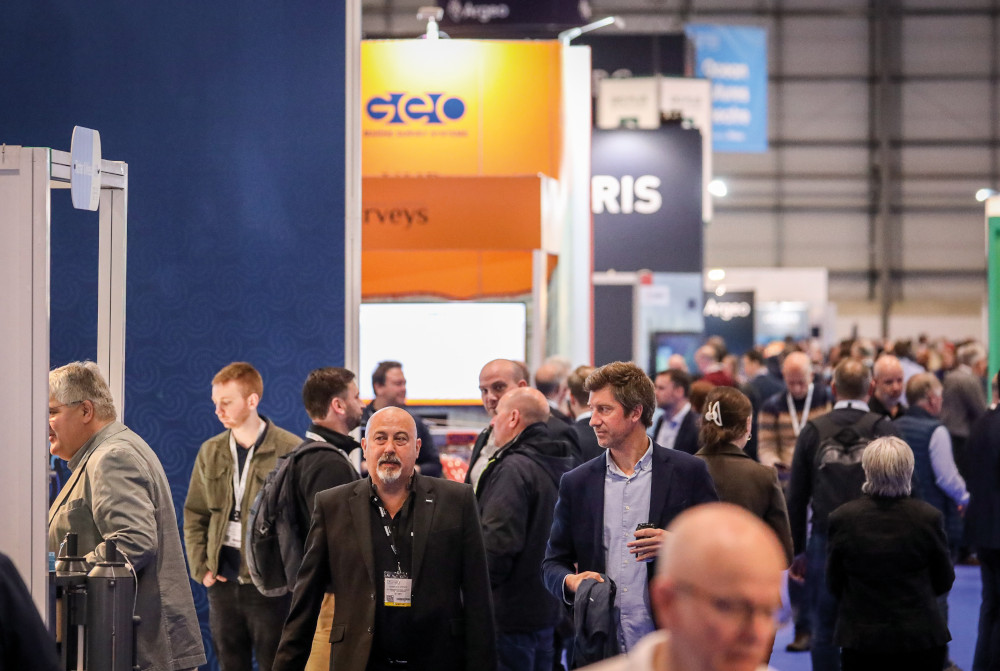

Into the blue
Rory Jackson reports from this show with his selection of the latest mission-critical products and technologies for the autonomous and uncrewed marine world…
With most lockdowns now ending, people are returning not only to streets and airlines but also the seas, and the return of Oceanology International to the ExCeL in London’s Docklands heralded a wave of new products for the Blue Economy. Although 4 years had passed since the last OI London, one thing remained the same: among the 440-plus exhibitors from 70 countries, USV and UUV technologies dominated the ocean survey solutions, with environmental monitoring and precision undersea mapping being of critical importance.
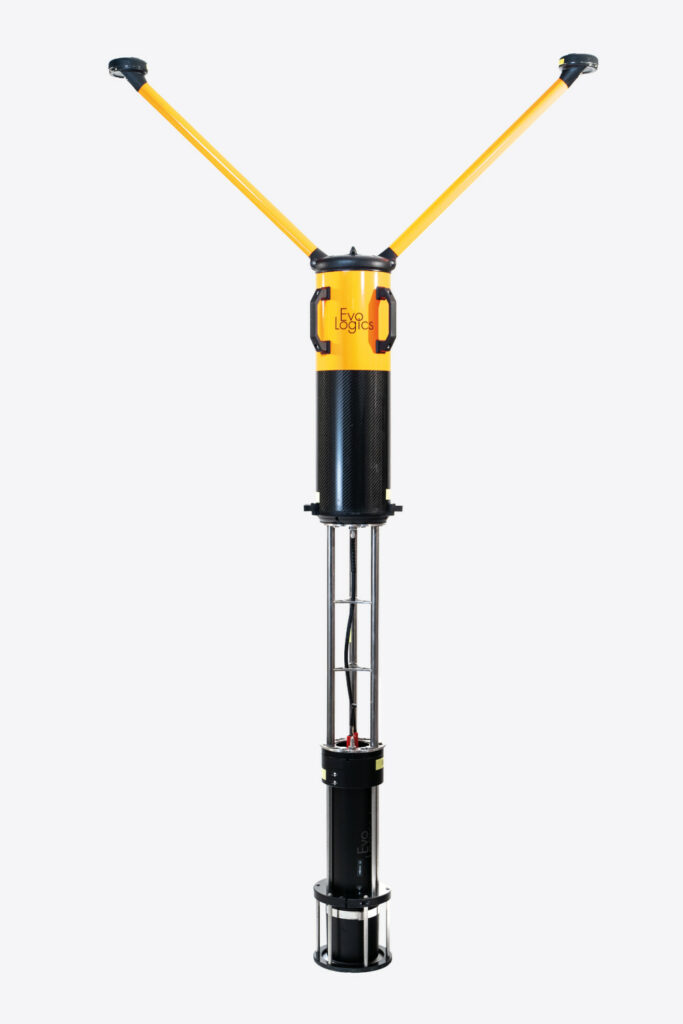
Subsea OEM EvoLogics showcased its range of underwater vehicles and technologies, and unveiled its new USBL buoy system. This was originally developed in-house as a tool for its own engineers to get accurate position data on underwater targets during field operations.
“It’s a turnkey unit that integrates a USBL transceiver, a battery, a flotation pod, a dual-antenna GNSS for georeferenced positioning, and a wireless comms unit, as well as an onboard PC running SiNAPS 2, our positioning software,” said Maria Pleskach.
“It takes less than 5 minutes to deploy, and the wi-fi access point allows remote operation and observation of the buoy, as well as live monitoring of the positioning data it produces, from the end-user’s GCS. It also collapses into three sections in order to fit into a small standard case.”
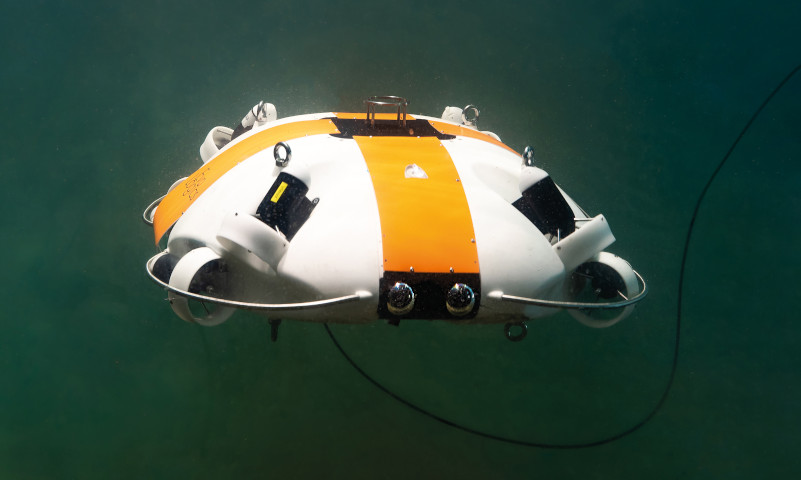
The company also exhibited its penguin-like Quadroin AUV, which is now commercially available and is continuing its environmental work measuring ocean eddy currents on behalf of the Moses Initiative (as featured in UST 42, February/March 2022), thanks to its faster speed during survey than is typical for UUVs of its size (up to 5 m/s).
“Meanwhile, our fishlike Poggy AUV will provide a slower and more stable glide, and we’re now also in the early prototyping stages of an upcoming miniROV hybrid UUV. That will be aimed at customers who want to hover really close to inspection targets for using equipment such as cameras or manipulator arms,” Pleskach added.
We also caught up with VectorNav for an update on the progress of its Tactical Embedded series of IMU and INS products, which was originally unveiled in 2020.
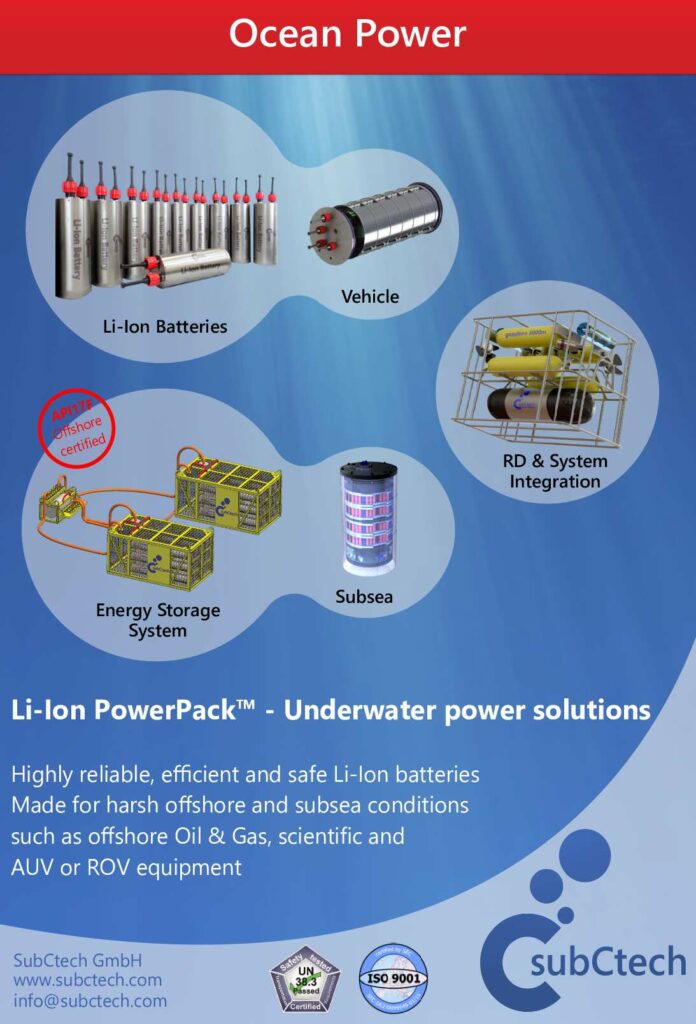
“We are happy to report that all three models are being used by a number of customers across various applications, and the feedback so far has been highly positive,” said Jeremy Connell. “These INSs offer the same performance as our full-sized Tactical Series but in a much more compact form factor – that’s 0.05º of accuracy in heading and down to 0.015 in for pitch and roll.”
Comprising the Tactical Embedded series is the VN-110E IMU and AHRS, the VN-210E single-antenna GNSS/INS and the VN-310E dual-antenna GNSS/ INS system, which provides heading measurements via GNSS compassing in addition to INS heading. The three systems each weigh just under 15 g, and all three measure 31 x 31 x 12 mm.
“The trade-off is that the Tactical Embedded navigation and positioning solutions don’t have the ruggedised IP68-rated housing of their larger, heavier Tactical Series counterparts, and also don’t come with ready-to-use plugs, just a 20 pin-out connection point,” Connell added.
“They are designed for integration onto end-users’ PCBs, enabling tactical-level navigation to be integrated directly into the vehicle’s electronics, which was not previously possible. This reduces the overall size, weight and power of vehicle, and provides cost benefits in larger volume purchases.”
French subsea technology company Notilo Plus was in attendance to promote some of the latest advances in its Seasam ROV. These include a new underwater GNSS capability for enhancing the accuracy of underwater inspections. “It had been challenging in some of our inspection jobs to get the position of the Seasam when underwater and geo-tag the data we were collecting from its various onboard sensors,” said Alexandre Arnaud.
“So we took another of our autonomous platforms, the Navigator USV, and plugged a USBL system into them. That gives us a precise position of the Seasam when underwater, as well as a GNSS referenced map of the camera imagery that’s been captured by the Seasam.
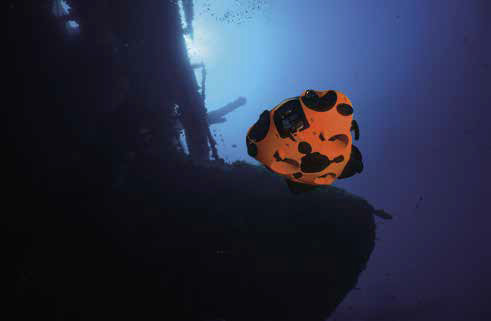
“That will be incredibly useful for customers who need to perform regular surveys of important assets, such as environmental protection groups who want to go back and check how a particular coral reef or population of fish is doing, or ship owners who want to gauge how the condition of their hulls are changing over time.
“To monitor these changes even further, our Notilo Cloud online platform can also be used to automatically analyse survey results and create comprehensive reports.”
The Seasam measures 55 x 45 x 23 cm and weighs 9 kg in air. It is powered by swappable batteries that provide 1.5 hours of endurance (upgradeable to 4 hours).
This power goes to thrusters that provide 2 knots of maximum forward speed and 1 knot of maximum lateral speed, as well as to a 1/2.8 in CMOS Sony IMX290 low-light camera sensor and two 1000 lumen LEDs to enable clear colour imagery. The vehicle’s DVL enables consistent distance-holding from assets it inspects (such as ships’ hulls) to ensure consistent levels of detail and collision avoidance.
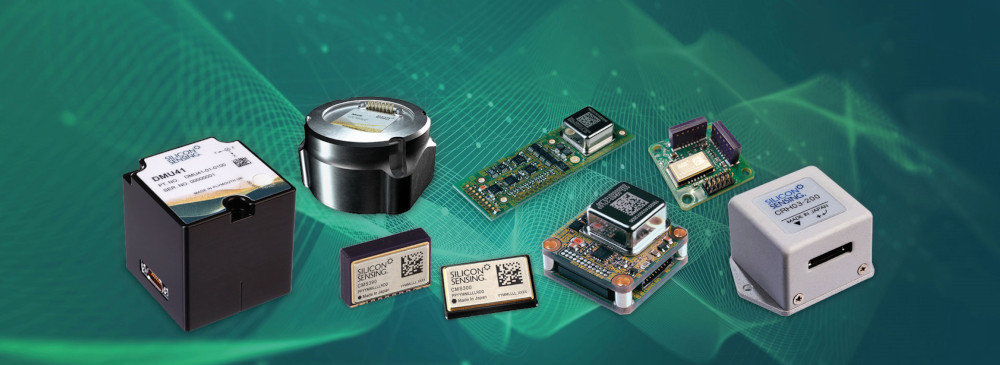
Silicon Sensing displayed a number of its latest inertial MEMS devices and products for the autonomous vehicles market. The first of these is the DMU11, which is positioned as the company’s low cost, six degrees-of-freedom IMU for high volume applications.
“The DMU11 has three gyroscopes as well as six accelerometers – two per axis for dual redundancy,” explained Katie Howard. “It integrates three of our CMS300 MEMS Combi-sensors, each of which contains a dual-axis MEMS accelerometer, and a single-axis gyroscope.”
The Combi-sensor has a digital dynamic range of up to ±300°/second, a bias over temperature of up to ±50 mg (at 10 g of acceleration), and a bias instability of no more than 10º/hour. It draws 8 mA of current on a 3.3 V input, weighs 0.6 g, and measures 10.4 x 6.7 x 2.7 mm.
Its gyroscope is constructed using the company’s proprietary vibrating ring structure technology to provide high quality scale factor correction as well as sustained performance over a wide range of temperatures and inertial rates.
Onboard processing for each Combi sensor is provided through an ASIC installed beneath its gyroscope, and the fully calibrated IMU processing occurs on the OEM PCB that the Combi-sensors are mounted on.
“For higher performance applications, we have our DMU41, which we unveiled last year and is about to enter production,” Howard added.
“It uses essentially the same sensor technology as our field-proven DMU30 high-performance IMU but with slight improvements in gyro balancing, futureproofing, a 50% size reduction, and other areas including end-user configurability so that customers can now tailor the format of inertial data outputs.”
The DMU41 measures 50 mm3 and consumes up to 125 mA on a 12 V supply. It contains one CRH03 gyro per axis, one PinPoint gyroscope per axis and two Gemini accelerometers per axis (six of each in total) to give bandwidth and error compensation redundancy. Its dynamic ranges are ±490°/second for its gyro outputs and ±10 g for its accelerometers. Also, the gyros’ bias over temperature are ±7º/hour, while the accelerometers’ are ±1.7 mg.
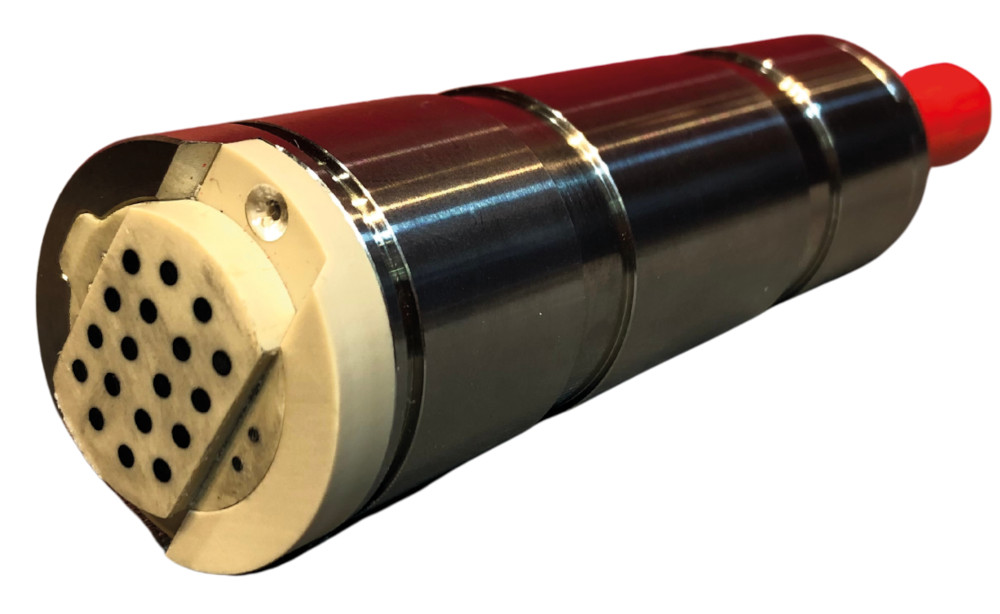
ANB Sensors discussed an advanced type of pH sensor it has developed, which it says stands to make a considerable difference for the large and fast-growing water quality data market.
“Existing, conventional pH sensors are built with glass and are very fragile, and on top of that they rely on lengthy calibration before use,” explained Carl Clemans.
“Our sensors don’t need calibration, just a quick wipe of the transducer is enough to refresh the chemical inside, and allow a further 15,000 measurements until the next wipe. Its onboard algorithms, arrangement of electrodes and chemical engineering enable self-calibration. We have 10 patents that effectively encapsulate how we’ve done this.
“Our founders spent 6 years developing the technology, released it commercially for the ocean market last year, and at this show we’re unveiling an updated version they’ve engineered to provide a wider salinity range so that it can also be used in freshwater zones.”
Clemans added that by forgoing traditional glass diode designs, ANB’s pH sensor maintains reliability through to its 15,000th measurement, whereas conventional pH sensors suffer significant degradations in accuracy and reliability over time, with no visibility to the end-user.
The sensor measures to 0.05 pH, with a resolution of 0.01 pH and a range of 2-10 pH. It is available in different versions depending on depth rating, and an enclosure-less OEM version also available.
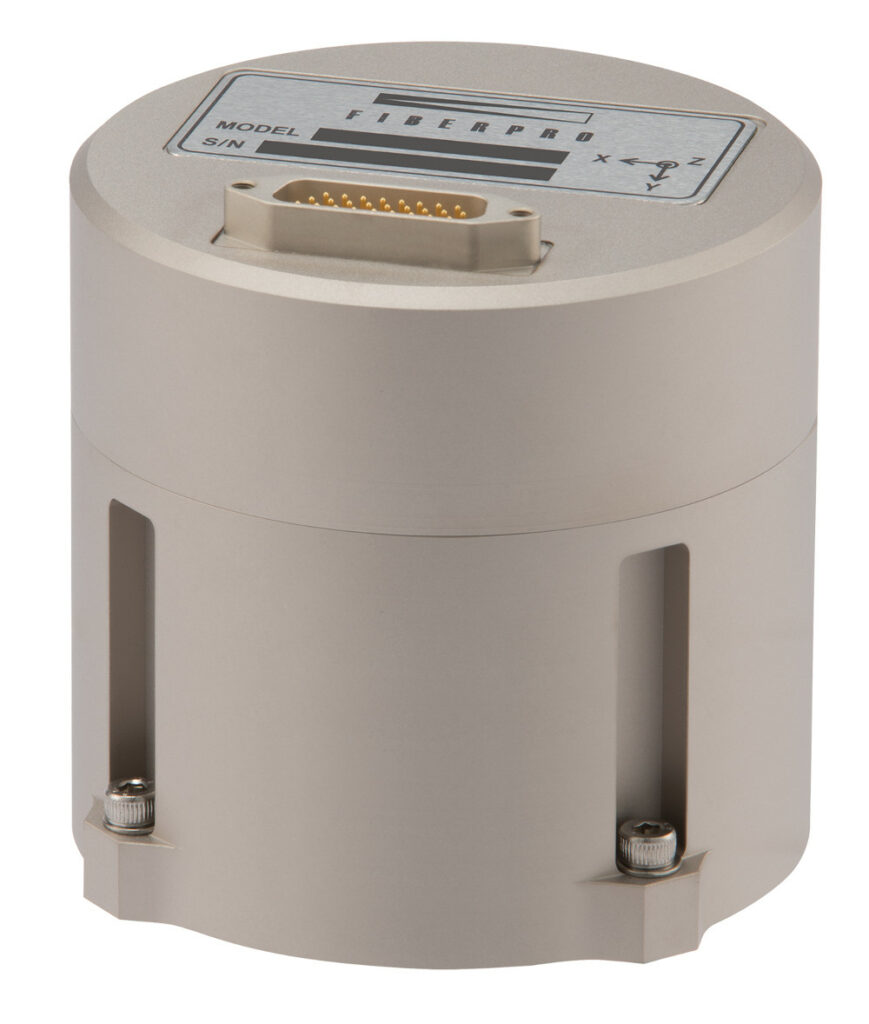
FiberPro exhibited several of its newest fibre optic sensors, including the FI 200 C, its high-performance tactical grade FOG IMU solution.
Richard Ryu said, “FOGs in general are critical for applications where the highest possible accuracy is needed in terms of angular rate and velocity, and there are two ways of designing FOG IMUs: open loop and closed-loop.
“Closed-loop FOGs are typically more expensive but offer the higher performance of the two approaches. However, we’ve focused on maintaining a performance advantage while bringing the price down to levels closer to those of open-loop systems.”
This price optimisation has been achieved primarily through the company’s investments in vertical integration processes, in order to design in-house most of its core parts for mass manufacture. It has also secured bulk purchases of FOG subsystem componentry through its supply chain partners, and automated its assembly lines to bring down input costs wherever possible.
“We’ve focused on positioning this product as a high-performance, low-cost solution, with low voltage and power consumption for an overall low burden of ownership,” Ryu added.
The FI 200 C weighs 790 g, measures 84.5 mm tall and 88.9 mm in diameter, and consumes 5.5 W at normal operation on a power input of 5 V. Its accelerometers measure accelerations to a range of ±10 g, has an in-run bias stability of 15 μg, and a bias repeatability of 2 mg. Its gyros have a measurement range of ±490º/second, a bias stability of 0.5º/hour, and an angular random walk of 0.025º/hour.
The standard product’s acceleration and gyro data is typically output at a rate of 400 Hz, although a 1000 Hz option is available on request.
Applanix, a Trimble company, spoke with us about the latest updates to the Trimble CenterPoint RTX real-time correction service for GNSS positioning augmentation, which expand its benefits into the maritime realm.
“While CenterPoint RTX corrections have been used for real-time landbased applications for the past 10 years, CenterPoint RTX had until recently been just a post-processing service for marine applications, principally for correcting mapping and imaging data after capture,” said Rick Morton. “But we’ve now rolled it out as a real-time marine correction solution for enhancing vehicles’ navigation and survey accuracies in-field.
“And as well as correcting position data to 2 cm horizontally, it also delivers accuracy to within 5 cm vertically. That’s very important for the applicability of the service to USVs and other marine vessels, because it gives you direct real-time information about the kinds of waves and heaving a boat is dealing with, and hence if your ocean survey asset should be recalled and recovered to prevent damage.”
Trimble CenterPoint RTX delivers real time corrections without the end-user needing to set up base stations (as is often the case with RTK processing) and at the time of writing, the satellite-based correction service was available to USVs up to 200 km offshore across most of the world’s continents. Morton added that it can still work beyond these distances, and some customers are trialling the extent to which it continues working.
“As well as being useful for persistently surveying oil rigs, wildlife habitats and other critical offshore assets, we’re seeing more and more small USVs going into very dangerous areas on behalf of wider ranges of clients,” he said.
“So it’s important for all operators to know exactly where their USV is at all times and to track the kinds of environmental conditions it’s dealing with.”
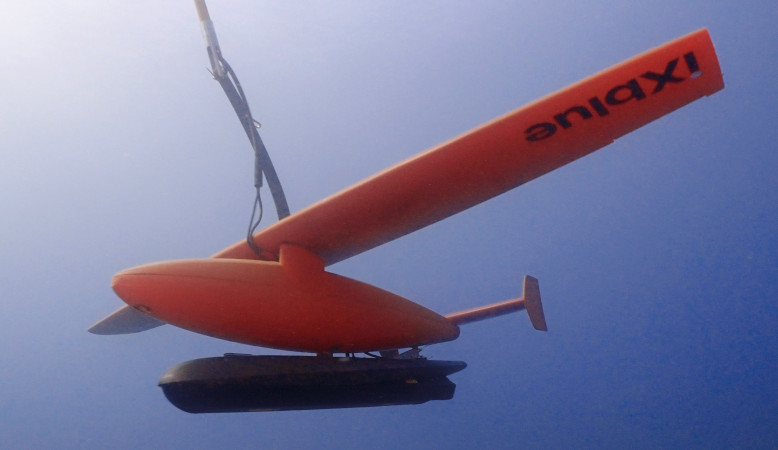
Also at the show was iXblue, which exhibited a range of solutions across hydrographic survey, autonomy, navigation and underwater positioning. One of these was its new FlipiX sensor tow vehicle, which expands the survey capabilities of the company’s DriX USV (see UST 25, April/May 2019).
Explaining something of the FlipiX’s development history, Guillaume Eudeline said, “Customers needed the ability to make heavily detailed multi-sensor surveys, the kind that take multiple outings and sensor reconfigurations across multiple missions, but they wanted to do it all in a single USV deployment.
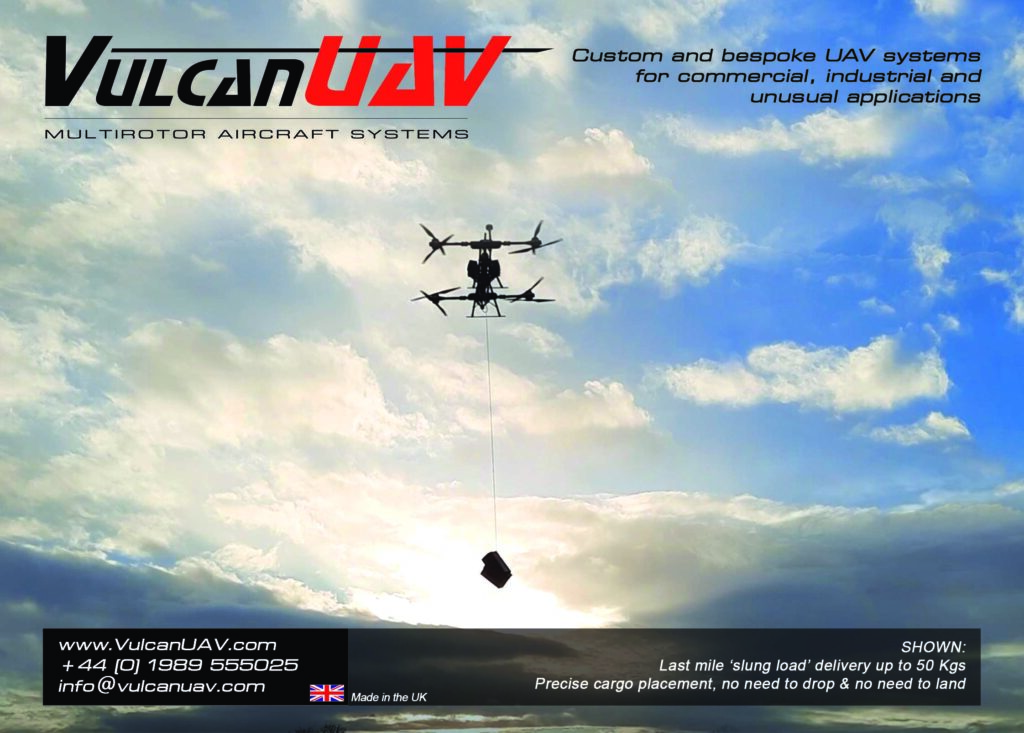
“The DriX is capable of using a great many sensors from the surface, but on top of that our customers wanted the sensors to go deeper below the surface in order to get more detailed and accurate hydrographic data. So we had no choice but to develop a new remotely operated tow vehicle [ROTV], which is the FlipiX.”
In typical operations, a FlipiX is towed behind the DriX at speeds of 3 to 7 knots, so that the latter can use its sensors for depths down to 50 m. The FlipiX can ‘swim’ down to 50 m while running sidescan sonars (the EdgeTech 4205 being the most popular choice at present) as well as a single magnetometer.
“We are also developing a frame that will attach to the FlipiX and hold several magnetometers simultaneously for wider magnetic field survey capabilities,” Eudeline added.
The ROTV autonomously holds its altitude to ±10 cm and also maintains pitch and roll to within 1º of error. Altitude-holding is achieved using data from an onboard altimeter and buoyancy adjustments from an auto-depressor.
The FlipiX is designed to be positively buoyant normally; the auto-depressor is essentially a bottle that contracts in response to external pressure. Pitch and roll are held owing to the FlipiX being constructed similarly to a fixed-wing aircraft, with wing flaps that adjust for its ‘flight’ manoeuvres through the water.
Meanwhile, the umbilical running from the ROTV to the USV transmits data from the FlipiX to the DriX in real time, and the latter’s data link delivers all the data to the end-user, for them to view in their GCS via iXblue’s HMI software. The cable also sends power from the DriX to the FlipiX.
“Of course, end-users also need precise geo-referencing of the FlipiX’s sonar and magnetic data,” Eudeline noted. “For that, we’ve installed our Gaps USBL system on the DriX to gauge in real time the position of a beacon on the FlipiX relative to the USV, and combine that data with the DriX’s GNSS updates to stamp the FlipiX’s survey data accordingly.
“Overall, this makes the FlipiX a part of the DriX autonomous solution, with the USV running the ROTV in a mode of ‘supervised autonomy’ in order to capture a huge body of data from the
surface to the subsea environment.”
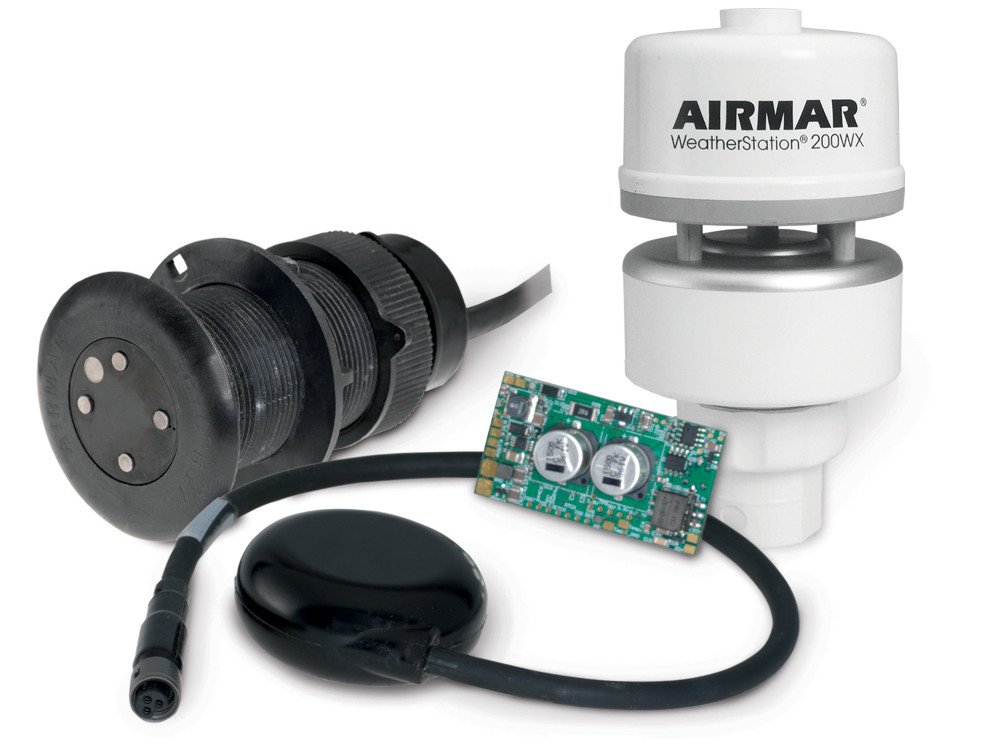
Airmar told us about three new products it said are of critical importance to autonomous marine vehicle manufacturers and operators.
The first is its 200WX-IPX7 WeatherStation multi-sensor, named for its IPX7 rating, indicating that it can endure the harshest weather and sea conditions; this is rare among such solutions. The system measures barometric pressure from 300-1100 hPa, wind speeds from 0 to 40 m/s, wind direction accurate to ±3º (at 10 m/s wind speeds) and other parameters.
“It is also uniquely suited to mobile applications, as it integrates GPS position with a three-axis accelerometer, rate gyro and magnetometers to compute pitch, roll and heading,” said Steve Boucher. “It can measure speed over ground, as well as apparent wind speed and the direction of a moving platform. Dynamic true wind speed is derived from the apparent wind speed, the speed of the vehicle, and vehicle heading.
“It’s also fairly small and lightweight – just 300 g – which makes it easier to mount than some other weather stations out there.”
The company also showcased its new 200m Mini Altimeter Kit. It is a derivation of Airmar’s range of existing transducer technology, and can be fitted to autonomous vessels for measuring height off the seafloor up to 200 m. The transducer is pressure rated to 1000 m.
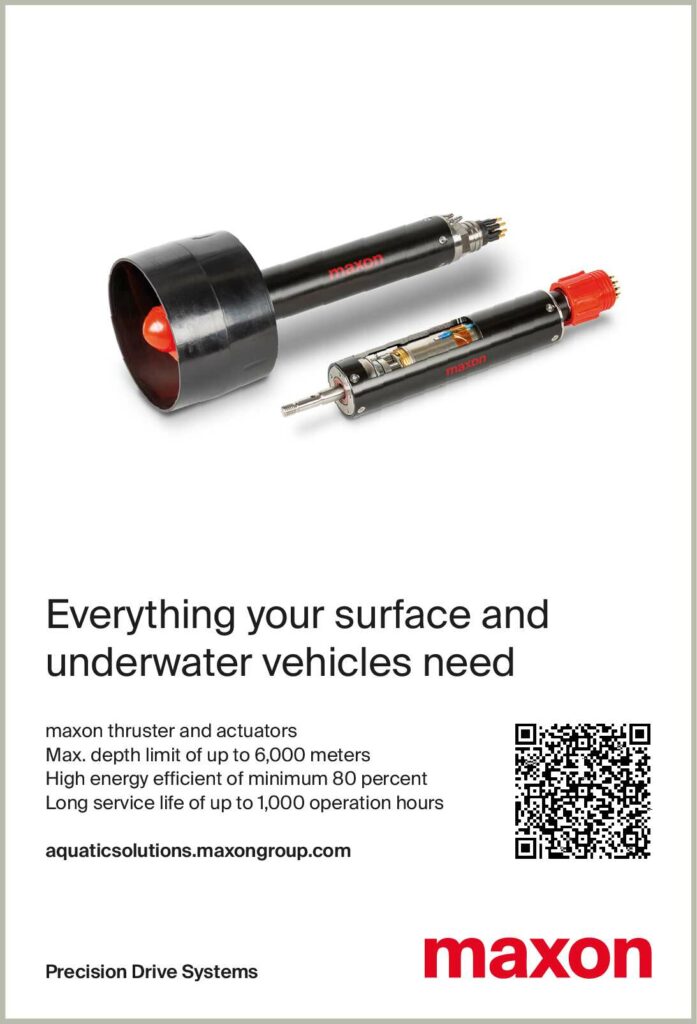
“The 200m Mini Altimeter Kit is an integrated altimeter with a 200 m range in a cylindrical package,” Steve Boucher added. “This integrated solution is targeted at USVs and smaller ROVs.”
Lastly, the company discussed its dual-axis electromagnetic velocity log (EVL), the DX900+, which is designed as a smaller and more cost-effective alternative to Doppler-based systems.
“Electromagnetic speed logs work by having an electromagnet in the centre of the sensor that projects an EM field into the water, and four pins around the sensor periphery in contact with the water,” Boucher said. “As water flows over the sensor, small voltages are induced, and by measuring the induced voltage between the fore and aft pins, and between the port and starboard pins, we can compute speed along both the x and y axes.
“It’s accurate at both low and high speeds, and we’ve been able to manufacture our EVL at price points around 15-20% of comparable DVLs, and in small form factors too.
“While DVLs can measure speed through the water at some known distance for the sensor, pulse Doppler technology is inherently much more expensive. But for applications where water velocity measurement at the sensor’s surface is acceptable, USV, ROV and AUV makers can save production costs by using an EVL instead.”
Voyis was at the show to explain its developments and capabilities in specialised multi-sensor payloads for AUVs, beginning with its IVER4 Recon.
“Our Recon payloads effectively take our camera and laser systems, and incorporate them with the right tubeshaped hull diameters and connectors to integrate with existing AUVs,” said Adam Riese. “We’re displaying the version we made for the IVER4 AUV from L3Harris, but we’ve also packaged the same technologies in different ways for the REMUS 100s, 300s and 600s now supplied by Huntington Ingalls Industries, and other AUVs from OceanScan.”
The Recon payloads will typically use an EO camera for taking still colour photography and a laser line-scan for generating 3D point clouds in real time. Also, a high-intensity strobe light system will be installed to ensure colour imagery can be captured up to 10 m away.
“We produce the 3D laser data on board the AUV in real time, which can be really useful for a range of purposes – for instance, pipeline tracking and following can be performed autonomously,” Riese noted. “Similarly, the images are saved in colour in real time, and they can be input to the main computer to perform object detection, classification, SLAM and other AI capabilities.”
Voyis has also integrated sidescan sonars from companies such as Wavefront into its payloads for applications such as mine countermeasures, debris surveys around wind farms, and pipeline health inspections and analyses.
Hexagon exhibited GNSS positioning and navigation solutions at the show, including OEM7700 and OEM7720 OEM GNSS receiver cards from Novatel, and LD8 and LD900 GNSS multi-constellation and multi-frequency receivers from Veripos.
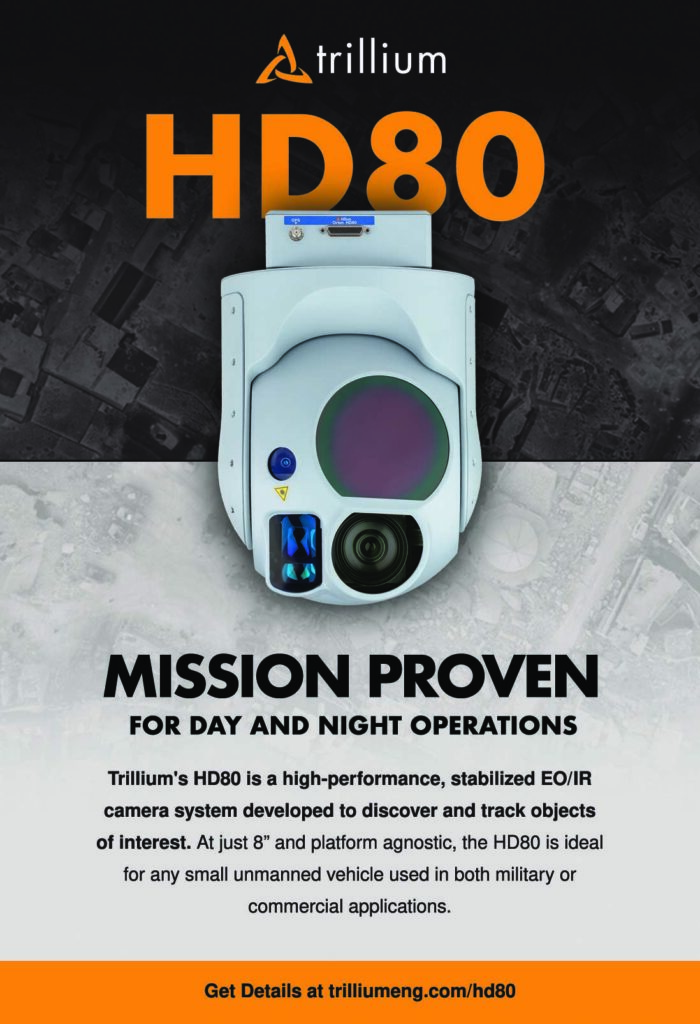
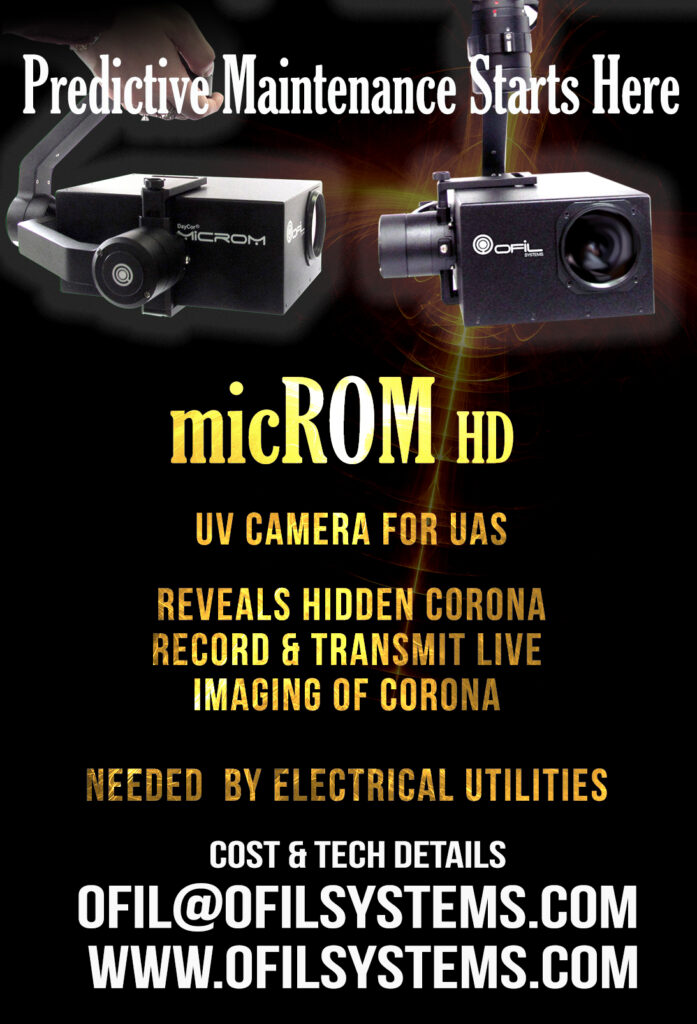
“The OEM7 series of cards are multiconstellation and -frequency, and can be used across diverse application areas including autonomous marine vessels,” said John Fleming.
“These solutions also incorporate Novatel’s SPAN GNSS+INS technology, which has been refined over several years to provide a deeply coupled sensor data to support a precise six degrees- of-freedom solution. SPAN technology is IMU-agnostic and can scale with different IMU hardware solutions including those from Epson, Honeywell, KVH and others,” Fleming added.
Both the OEM7700 and 7720 can track all satellite constellations including GPS, GLONASS, Galileo, BeiDou and India’s NavIC, as well as satellite-based augmentation systems (SBAS) such as QZSS. Each system produces readings accurate to 1 cm with RTK processing, up to 60 cm accuracy when using SBAS, and can be integrated using comms protocols including USB, CAN bus and Ethernet.
The OEM7720 differs from its counterpart in being a dual-antenna system to provide a GNSS heading solution. It consumes 2.3 W compared with the OEM7700’s 1.3 W, but in exchange the vessel outputs heading information to 0.08º accuracy (antenna baseline 2 m).
Hexagon also featured GNSS PPP correction services from both Veripos and Novatel through its Apex and TerraStar portfolios. These provide real-time positioning at the centimetre level, which is essential for marine navigation and positioning, particularly for autonomous and uncrewed marine vessels.
Apex corrections from Veripos were developed specifically for offshore applications such as dynamic positioning and hydrographic surveying. Depending on options selected, they can also use satellites from GPS L1 and L2, GLONASS L1 and L2, BeiDou B1 and B2, Galileo E1 and E5b, and QZSS L1 and L2.
Inertial Labs discussed in detail its latest r&d in SLAM development for the autonomous and smart vehicles space, and the potential it holds for the uncrewed world.
“Our systems have grown increasingly more versatile over the years in terms of what they can use in enhancing the performance of the navigation solution,” said William Dillingham. “Whether it’s velocity readings from an air data or wind speed sensor, information from an onboard encoder or one of the many other aiding sources we can accept, every bit helps and we want to use this data tactically.
“Having our own calibrated IMUs and using various readily available GNSS receivers helps considerably. On top of that, we’ve recently started working with a lot of different optical sensors and Lidar scanners, and that’s moved us into developing low-cost integrated payload solutions for the topographic survey market.
“That, combined with everything going autonomous and the growing affordability of sensing components, drove us to work on making a low-cost system that could enable highly accurate and intuitive navigation and surveying solutions through combined inertial systems, cameras and Lidars.
“Such a solution is going to be critical for autonomous mobile robots in the e-commerce world, inspection USVs populating harbours and shipyards, and much more.”
To that end, the company is experimenting with sensor combinations such as its RESEPI. This is a combined dual-antenna GNSS-INS system with a built-in data logger and integrated Lidar, camera and comms systems engineered for real-time and post-processed generation of point clouds for surveyors’ analyses. The aim is to devise a means for performing real-time navigation with the sensor combination.
Tests of these platforms will then be followed up with algorithmic work for optimised sensor fusion. This solution will output raw data that end-users could use to develop SLAM models tailored for their autonomous vehicles. These payloads would also give the architecture for partners to develop onboard obstacle avoidance and recognition and response algorithms.
The company also displayed its INS-U, a new GNSS-aided INS integrating a U-blox GNSS receiver in an IP67-rated enclosure. It has been designed for VTOL-transitioning UAVs as well as fixed-wing platforms, and is now commercially available.
“The INS-U has an embedded air data computer [ADC] that calculates velocity in the absence of GNSS, and we’ve worked with a number of companies to ensure it performs well in mission-critical situations for both GNSS-enabled and GNSS denied environments,” Dillingham said.
“We offer different air data pressure sensors that customers can select for their ADC, as per their application.
Depending on the airspeeds and altitudes customers want to fly at, they can choose the more expensive, sensitive and higher resolution of the two sensors to maintain accurate readings in the absence of dense pressure data, or the less expensive option if they intend to fly at lower altitudes and higher airspeeds.”
We met RTSYS, who had travelled from France to showcase its line of AUVs.
“The Comet-300 AUV was the first of our vehicles, which we released it in 2015,” said Corentin Troussard.
“It’s equipped with sidescan sonar, interferometric sensors for bathymetry, as well as up to seven water quality sensors, a video camera and light, and acoustic comms systems for real-time monitoring of its position, speed, heading and battery energy from the surface.”
Its RACAM acoustic modem was developed in-house, and is also deployed on the company’s handheld sonar (for use by divers) and on its second AUV, the NemoSens. That is an 895 mm-long and 124 mm-diameter AUV that weighs about 9 kg in air and carries similar sensor types to the Comet-300. It has a top speed of 8 knots, an endurance of just over 10 hours, and a maximum operating depth of 300 m.
The Comet-300 meanwhile is the larger counterpart to the NemoSens. It weighs 32 kg in standard configuration, is 1900 mm long, and can operate for 12 hours if running at 4 knots, up to a maximum endurance of 20 hours, and can also dive down to 300 m.
“All our systems can communicate with each other and with the surface thanks to our acoustic positioning system,” Troussard added. “And they can correct their survey routes for drift in real time, to within 5 m of constant accuracy.”
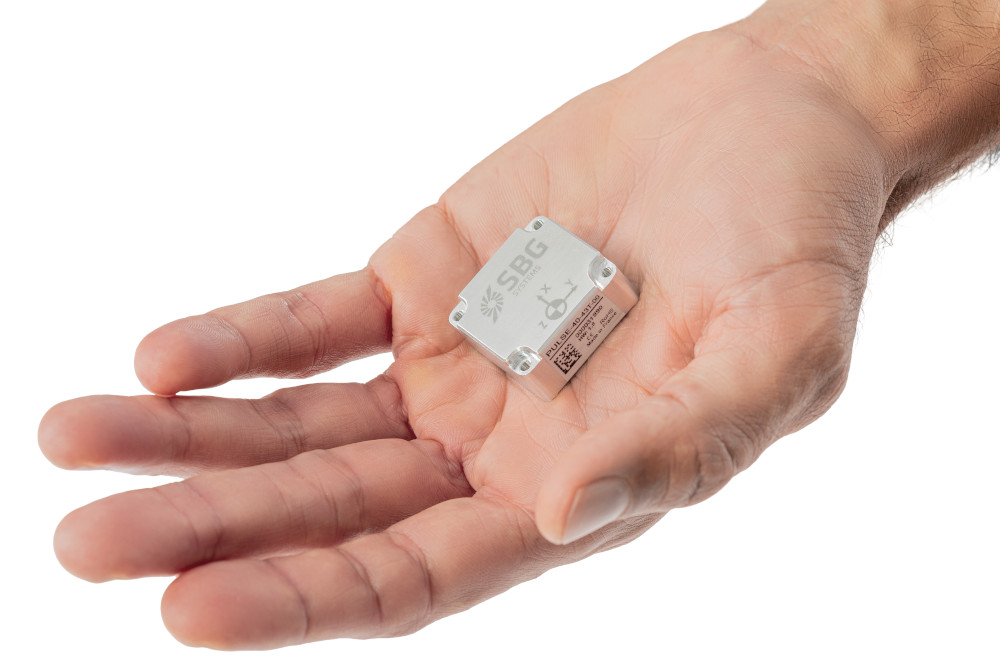
SBG Systems displayed its range of navigation and positioning products, including its newest solution, the Pulse-40 IMU.
“It’s a very small MEMS-based system that optimises performance against size, outputting raw IMU data for the end-user to use with their own algorithms in order to get the kind of navigational, survey or camera-pointing output they want,” explained Christophe Nicolopoulos.
The Pulse-40 weighs 12 g and consumes 0.3 W on power inputs from 3.0 to 5.5 V. It measures 30 x 28 x 13.3 mm, although it must be installed on an end-user’s PCB for data processing, via a UART serial interface that allows an output data rate of up to 2000 Hz (or a baud rate of up to 4 Mbit/s).
Its accelerometers enable a measurement range of up to 40 g and a bias instability of 6 μg while its gyroscope has a range of 490º/second. However, a version with a 2000º/second range can be available depending on export controls.
“For more complete solutions, including Kalman filters and additional algorithms for vehicle operations and mapping, we recommend our Ellipse, Ekinox or Apogee series, which are now well-proven for navigation and other autonomous functions,” Nicolopoulos added.
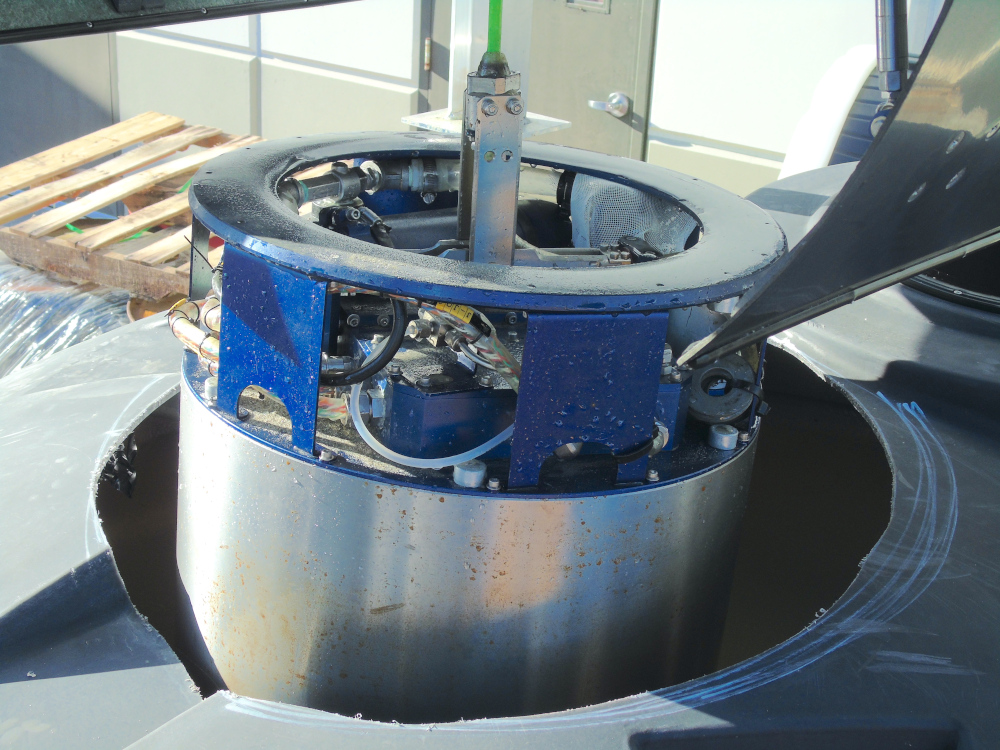
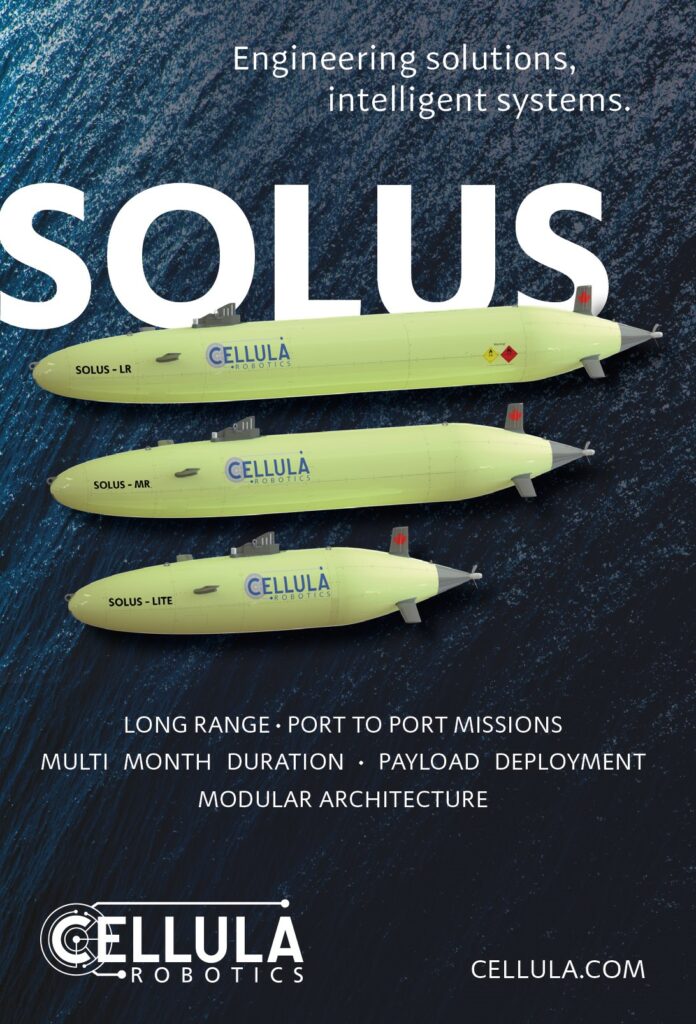
We caught up with Cellula Robotics, whose hydrogen-powered Solus-LR (Long Range) AUV we previously covered in detail in UST 30 (February/March 2020), to learn about an upcoming new vehicle the company is developing.
The new model, the Solus-XR, is expected to measure 12 m in length and 1.5 m in diameter. It will be the Canadian OEM’s longest-endurance platform yet, with an onboard powerplant constructed around redundant hydrogen fuel cells enabling at least 5000 km of range between refuelling stops if it’s operating at an average speed of 3 knots.
Manoeuvring will be aided by mechanically deployed thrusters that will provide hovering capabilities and pitch and roll when necessary, and retract back into the hull when not needed, so that the XR’s hydrodynamic profile is optimised.
The Solus-XR will be capable of sprint speeds of greater than 8 knots, and it will displace 10,000 kg. Included in this displacement will be two large modular payload ‘cartridges’ – one installed under the forward part of the hull and one under the rear. These are being designed to make field-swapping of mission sensor packages quicker and easier than traditional engineering approaches allow.
“Also, the suction anchor will be available as one of the options for those modular payloads,” said Jacqueline Nichols.
UPCOMING EVENTS
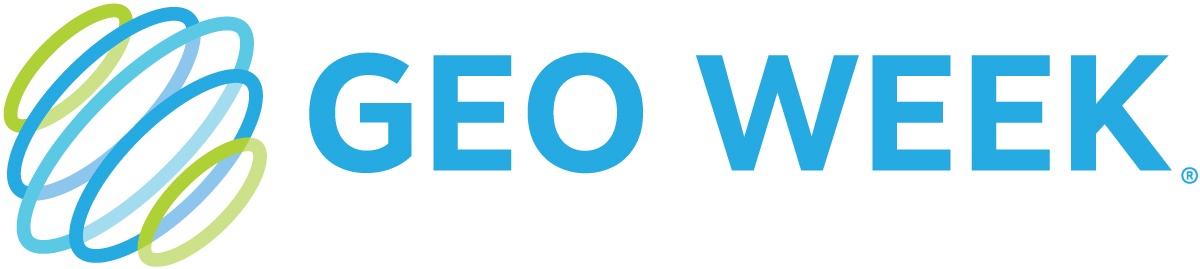
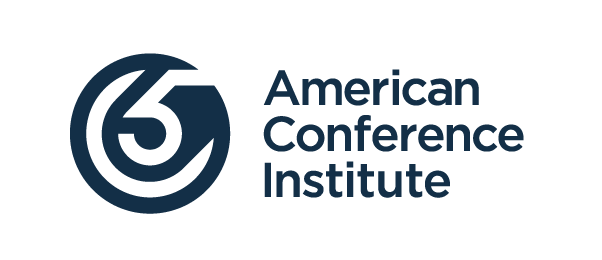
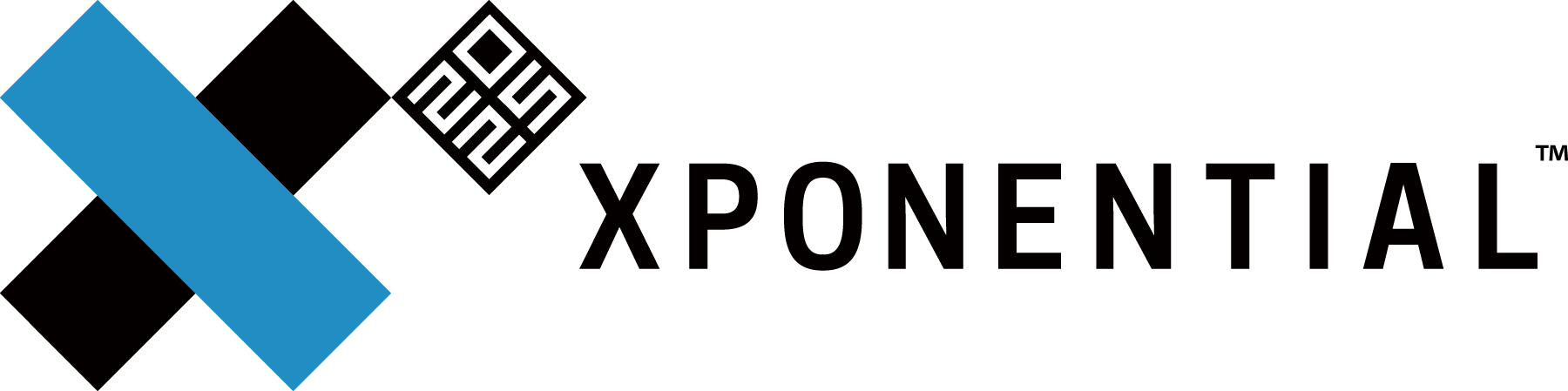
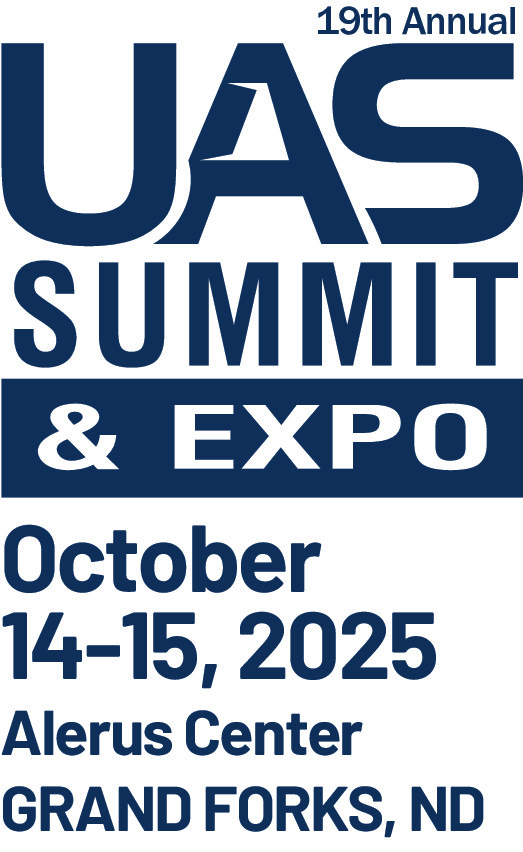
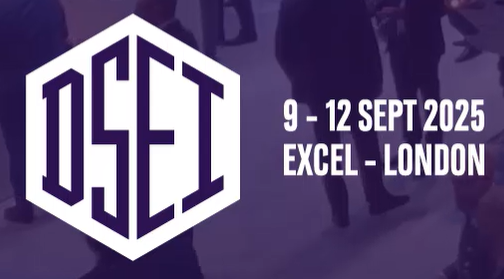
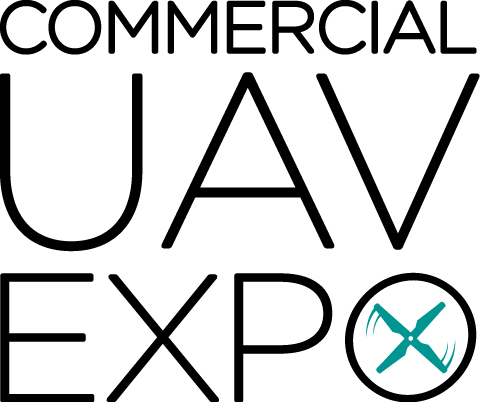
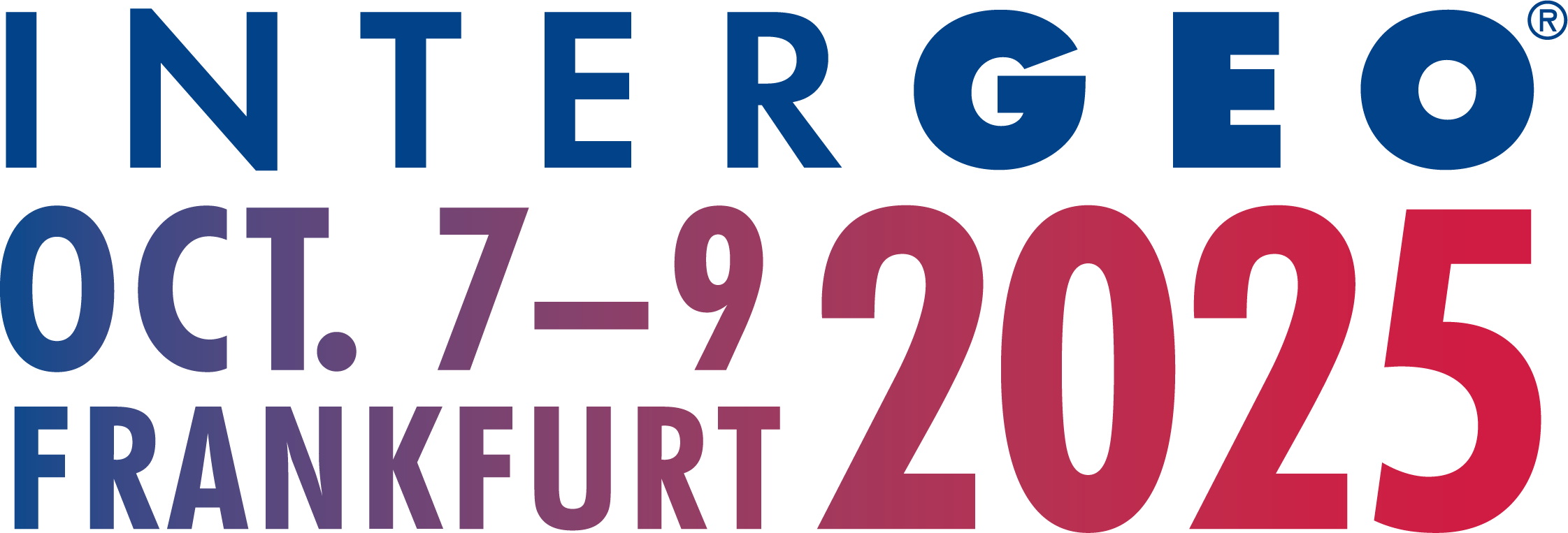
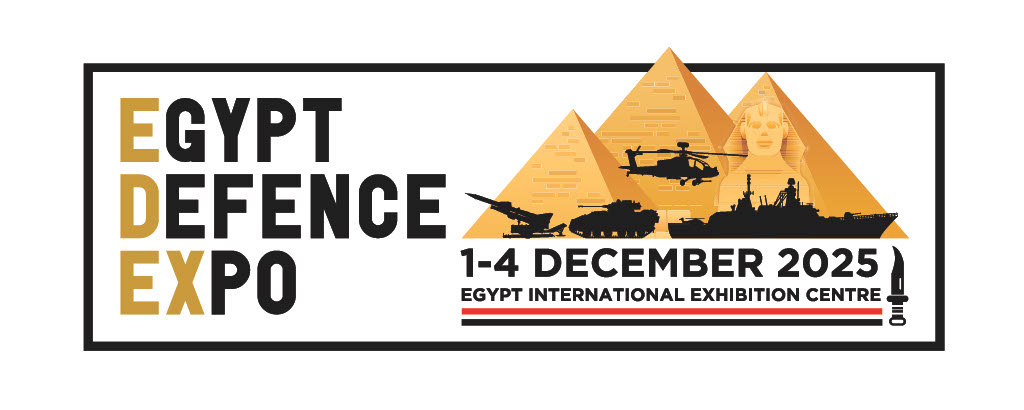
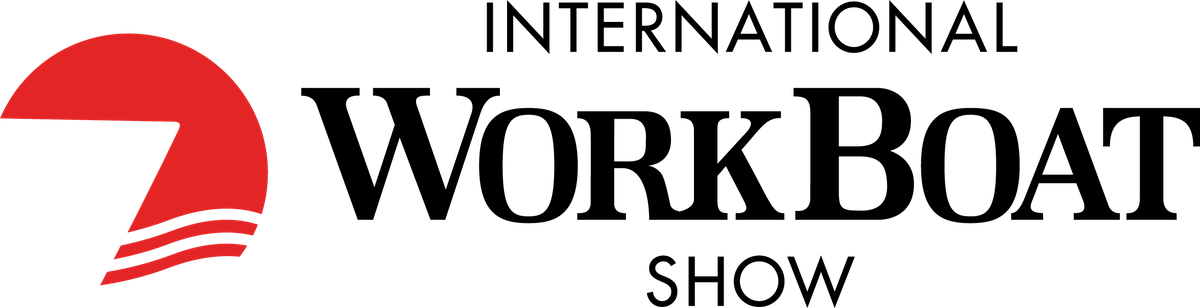
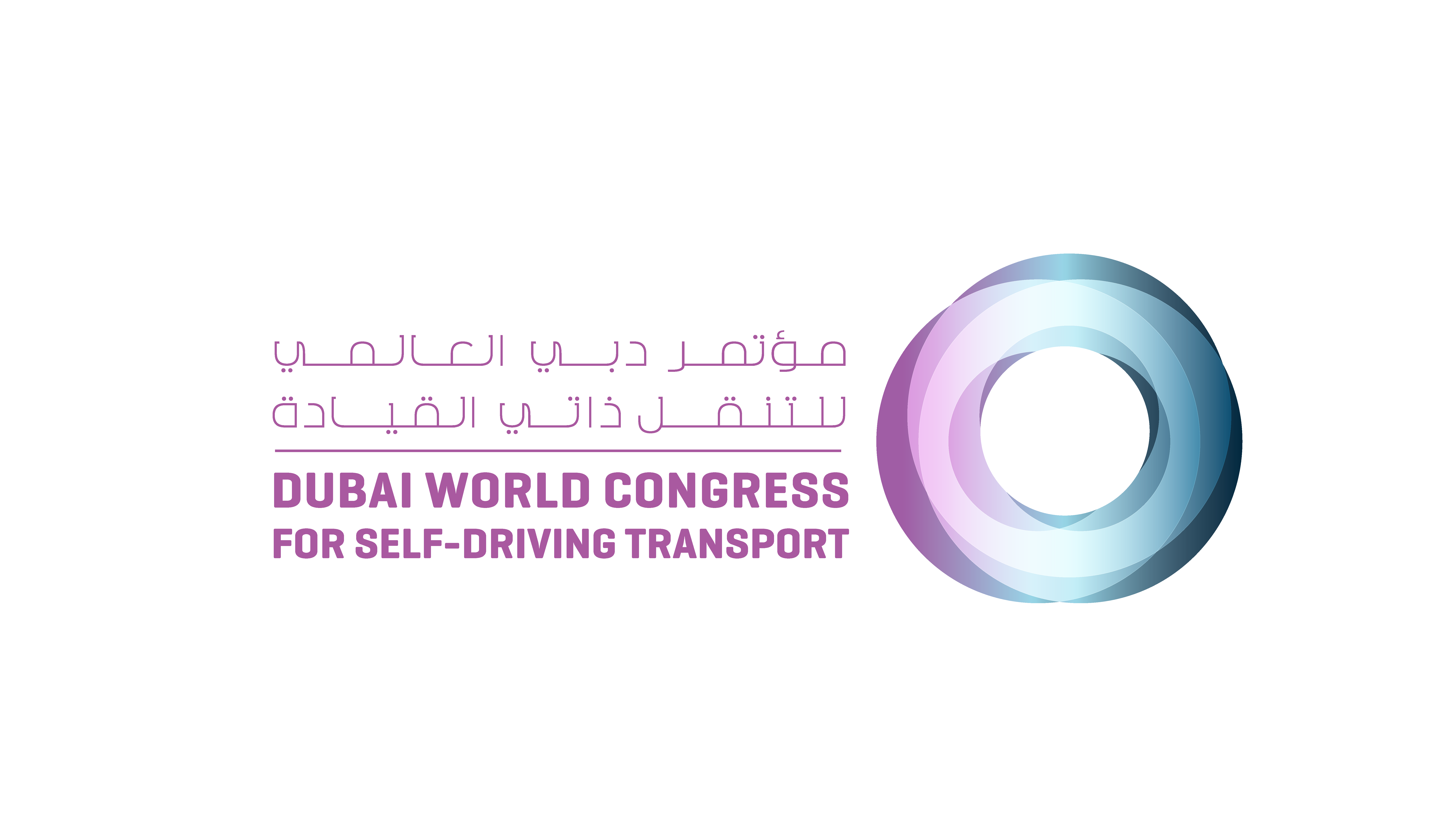
