Oceanology International 2024
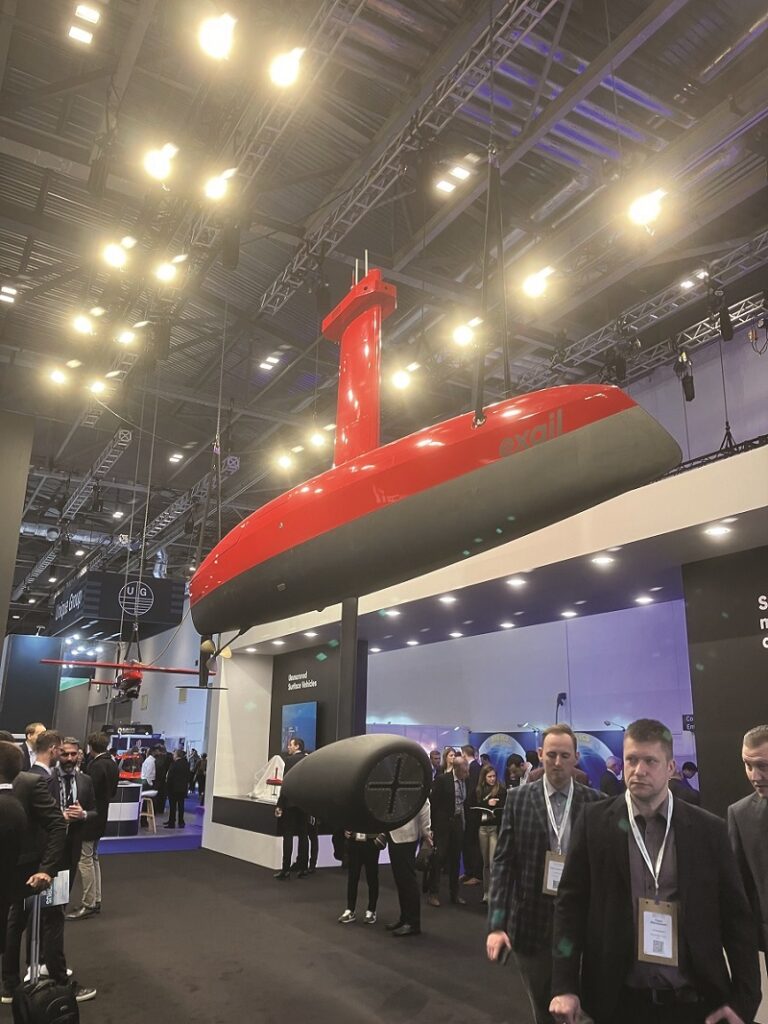
(Image courtesy of the author)
Peter Donaldson reports from the leading forum connecting marine science and ocean tech communities
Oceans 10
Oceanology International 2024, staged on 10-12 March at London’s ExCeL, was a busy event that showcased many new and innovative sensing, communications, navigation, positioning, robotic control and energy storage systems for use on and around uncrewed vehicles. As the industry increases its activities in offshore resource exploitation, from oil and gas support to renewables such as wind and wave energy, as well as ocean exploration and mapping of the surf zone, artificial intelligence (AI) is coming to the fore.
Blueprint Subsea presented its range of acoustic sensors including Oculus multibeam imaging sonars. Deployed on ROVs, AUVs and poles, Oculus multibeam sonars are designed to provide high-quality images for both navigation and inspection applications.
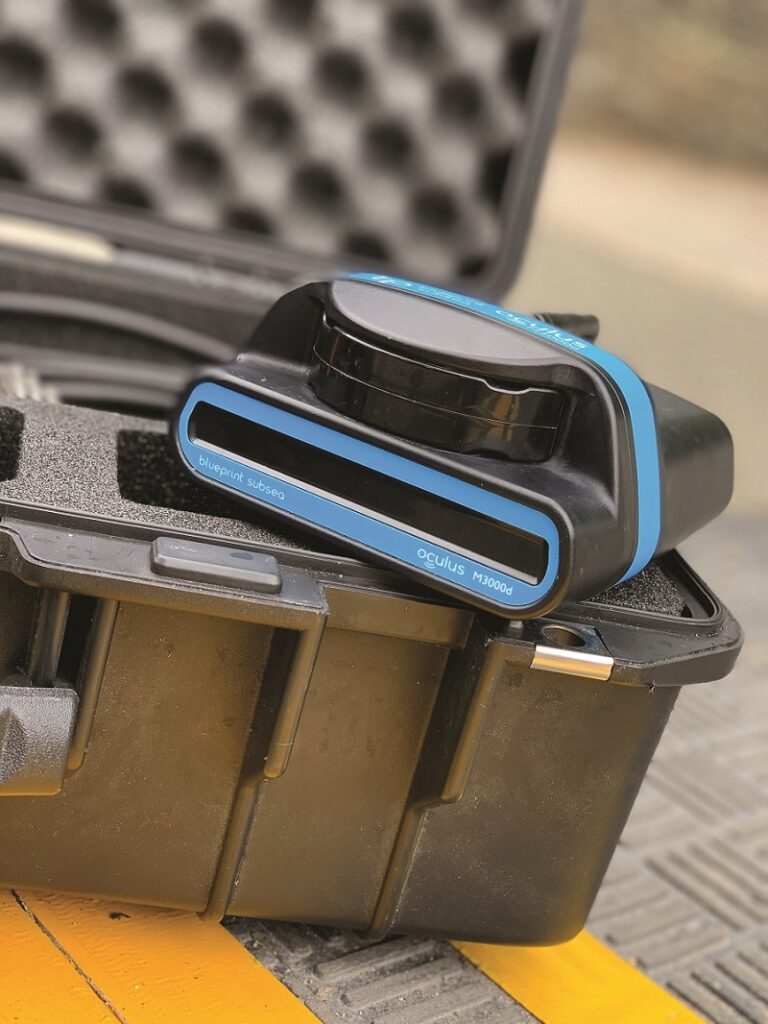
With models with depth ratings of 500 m, 1,000 m and 4,000 m, the sonars cover frequencies from 375 kHz to 3 MHz, and are available in single- and dual-frequency variants, and offer operating ranges from 0.1 m to 200 m.
Blueprint quotes horizontal and vertical apertures of 130° and 20° respectively, angular resolutions down to 0.25°, and range resolutions down to 2 mm, with update rates of up to 40 Hz.
The system can also be used to create detailed 3D images, with the caveat that the sonars have to be mounted in pairs. This has been done by a team of scientists at Stevens Institute of Technology, which fixed two of the sensors orthogonally on the front of a BlueRobotics BlueROV2 vehicle.
One of the sonars was tasked with capturing data in the horizontal plane to measure range and bearing, while the other was oriented on the vertical plane to capture data in elevation. Combining the data generated by this pair of sensors allowed the team to generate 3D point clouds, facilitating detailed mapping of what the firm describes as a congested underwater landscape. Interpretation of the data was assisted by the use of advanced perceptual algorithms.
The company argues that this has the potential to transform the way subsea inspections are conducted through offering a cost-effective, efficient, and safe approach.
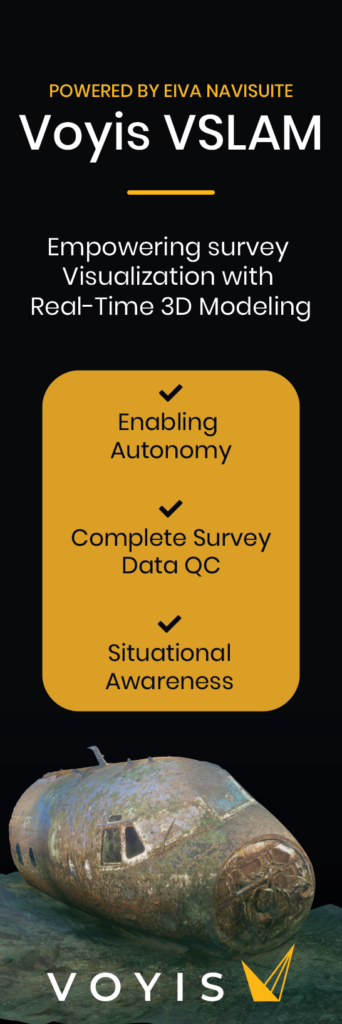
Blueprint also showed its StarFish sidescan sonars, and its SeaTrac ultra-short base line (USBL) positioning system. The latter is used to track multiple uncrewed underwater vehicles and the new D010 diver tracking beacon.
“The system features depth and geo-fence alarms, as well as a diver-distress alert cord on each beacon, helping to drastically improve topside situational awareness and diver safety,” says Rachael Reader.
Robosys promoted its new AI autopilot for small, survey USVs in the 3-6 m size range. Most of them have electric drives with their own communication protocols, which traditional, commercial, off-the-shelf autopilots were not designed to work with, according to Nigel Lee.
“We have taken our Voyager AI software, and integrated it with a hardware autopilot capable of working with analogue and digital steering and propulsion systems,” he says.
He adds that Robosys can configure the autopilot for any vessel out there now with the latest technology, and it is not limited to the smaller vessels. For example, the team is currently integrating the system into Acua Ocean’s 13.5 m, hydrogen fuel-cell-powered USV, which uses a steerable electric drive from RAD Propulsion. It is also compatible with TQ bus and TorqLink, as well as ESC and CAN bus-control systems.
The autopilot has to ingest data from the vessel’s navigation systems and sensors to work the steering and propulsion systems. Robosys’ Voyager AI software capability comes in here, with the ability to make the same decisions as a human.
“That is what we are doing, particularly when we follow the COLREGS – the rules of the road (RoRs) – at sea. It’s very much about machine learning and a rules-based architecture, particularly when it comes to the COLREGS.
“If you just try to use a neural network or learning at the edge through unsupervised learning, there is the potential to learn errors because you will learn from mistakes that are made, as opposed to applying the rules correctly, which is what I do as an officer of the watch at sea. So we use a mixture of rules-based and machine-learning techniques to react correctly within a dynamically changing environment. In addition, Robosys details the RoRs in force to deliver Explainable AI (XAI)-based COLREGS.
Robosys has also integrated the Computer Vision Sea AI Sentry perception system into its VOYAGER AI in conjunction with a software version of its USV AutoPilot for a 30 m tug in India.
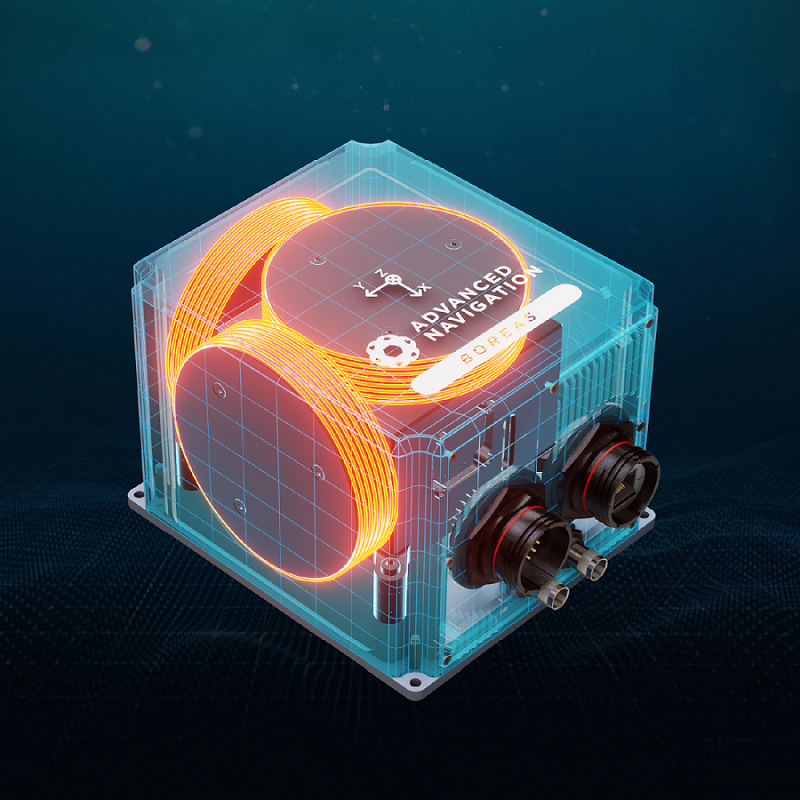
Advanced Navigation discussed its AI-enabled inertial navigation systems (INS), including fibre-optic gyroscopes (FOG) and micro electro-mechanical (MEMS) gyroscopes. The company’s AI fusion neural network helps to reduce drift to a minimum, so the INS keeps track of the host vehicle’s movements for longer in GNSS-denied environments.
“What the AI is doing is tracking and removing the sensor errors far more accurately,” says Xavier Orr.
He says traditional navigation systems rely on an algorithm developed in the 1960s, known as the Kalman filter, for guidance and navigation. However, it faced limitations in correcting certain errors in the process of determining an object’s position, such as biases, scale-factor errors, instabilities and noises.
“The Kalman filter will have a predefined level of uncertainty associated with each one of those pieces of information. As things change within that platform and the sensors have different levels of performance, you’re not modelling that fully,” he says.
“Advanced Navigation’s AI fusion neural network is able to learn the unique dynamics of the vehicle,” he says. “For example, if you’re on a train, you start with a factory learned model and it learns the specifics of that particular train over time. The models are trained on hundreds and thousands of hours worth of real field data, and continue to learn and fine-tune the physics model in the field. This allows the system to track sensor errors far more accurately and also reject erroneous data very well.”
The end result is that the company’s less costly MEMS gyroscopes achieve performances comparable with other FOGs on the market, while the performance of its FOGs is similarly elevated. With AI enhancement, INS can retain a sufficiently accurate position for the vehicle for much longer, increasing from the realm of minutes to that of hours for a MEMS INS.
“This opens it up to a whole broader spectrum of capability,” Orr says.
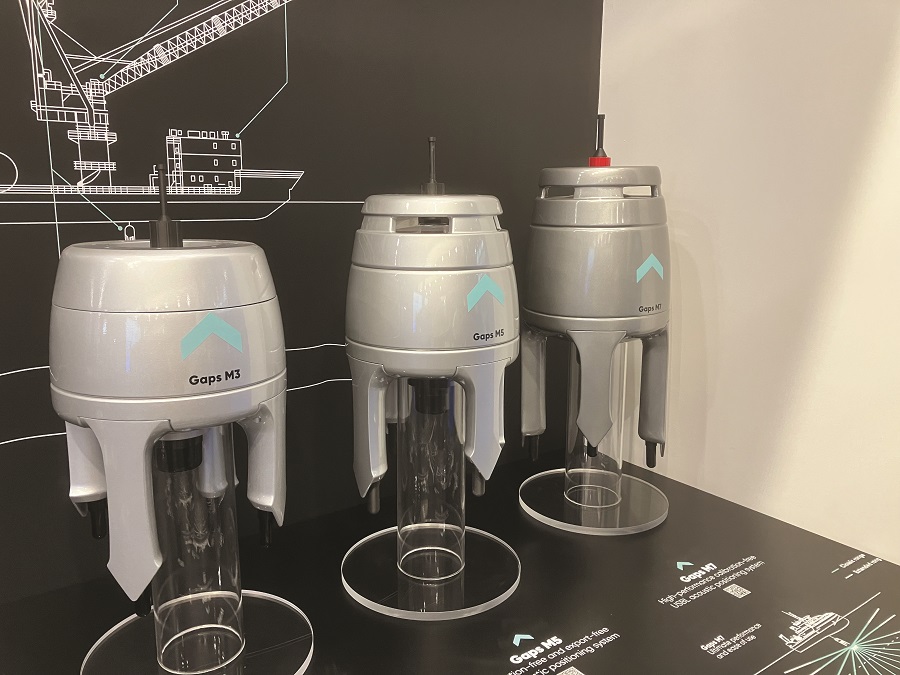
Exail presented updates to its Gaps ultra-short baseline (USBL), pre-calibrated, underwater positioning and communications system, new generations of which have been developed every five years or so since the company began working on it in 2004, according to Exail’s Paul Urvoas.
USBL systems track vehicles by emitting an acoustic ping, to which cooperating vehicles respond with an identity coded ping. Receiving these responses through several channels, the Gaps unit works out the responding vehicle’s position.
“We measure time difference of arrival for the distance and phase difference for the bearing,” he says. “We also compensate the acoustic ray bending that depends on sound velocity profile.”
Urvoas says the latest generation consists of three products. The top-of-the-range Gaps M7 can track cooperating vehicles down to 7,000 m deep using lower frequencies than before, and it contains a high-performance inertial navigation system (INS).
Gaps M7 has a stated positioning absolute accuracy figure of 0.06% of the slant distance, with a circular error probable (CEP) of 50%. This accuracy covers the higher offshore requirements and is achieved without any in-field calibration, thanks to its embedded high-grade INS.
“With this, we are taking on deep sea exploration challenges and future applications like deep sea mining and 6000 m class autonomous underwater vehicles (AUV).”
Gaps M5 is similar, but uses an attitude and heading reference system (AHRS) instead of an INS to reduce cost, returning a positioning accuracy of 0.2% of the slant distance (CEP50).
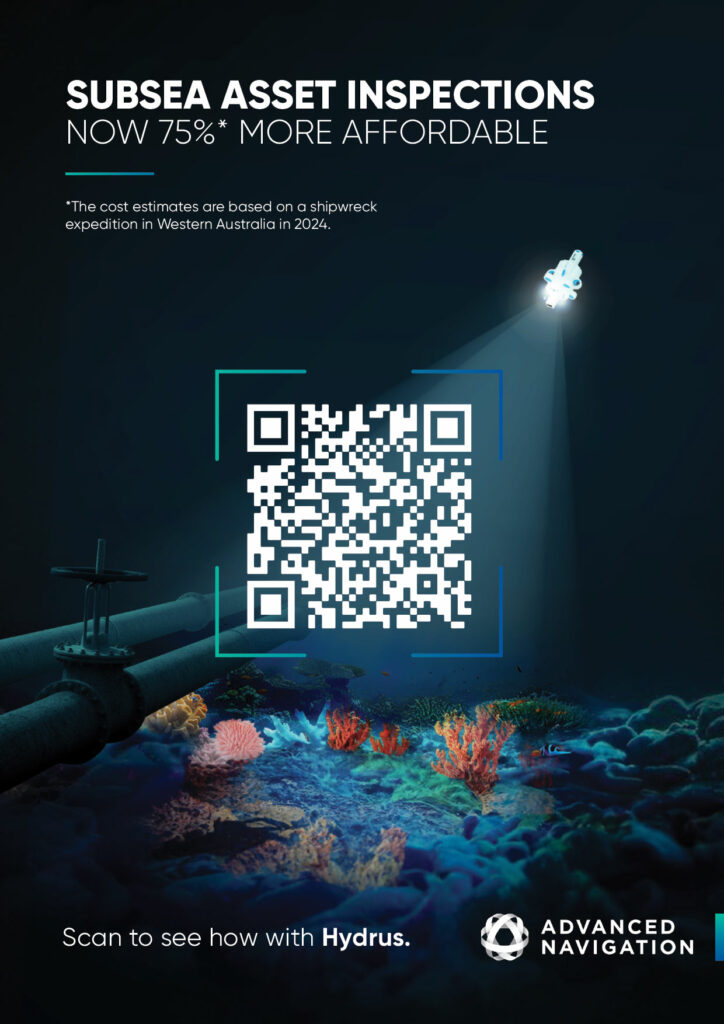
Finally, the smallest, lowest-cost Gaps M3 does not contain an inertial sensor as it is intended for permanent installation on vessels equipped with a gyrocompass, vertical reference unit and motion sensors. Its compactness makes it very adapted to uncrewed vehicles as well, Urvoas says.
A new feature on all Gaps models is acoustic telemetry to communicate with up to 15 subsea vehicles simultaneously.
“This will open up new applications such as autonomous seabed mapping, operating several AUVs at the same time and controlling data of the subsea net.”
Fiberpro launched its new fibre-optic gyroscope (FOG) technology-based FN 200C, a single-box system that serves as an inertial navigation system (INS), a motion reference unit (MRU) and an attitude and heading reference system (AHRS) at the same time. The FN200C determines position, velocity, vertical and horizontal displacements, and absolute orientation (heading, pitch and roll) for any platform on which it is mounted.
FN200C is an IP68-rated version of an all-new generation of ruggedised, EMC/EMO-shielded, fully integrated, high-performance, strapdown system, says Richard Ryu.
Ryu says the FOG-based IMU ‘FI200C’ inside the FN200C box is a closed-loop sensor that uses feedback to minimise drift. “Of course, in very long operations there will still be some drift, but compared to open-loop solutions there is a huge difference,” he adds.
One feedback mechanism is an integrated optical circuit (IOC) chip. In a FOG, rotation of the sensor causes a phase shift between the light beams travelling in opposite directions within a fibre-optic coil. This phase shift is proportional to the angular velocity of rotation. By enhancing optical coupling, the IOC chip mitigates the effects of noise, drift and other sources of error in the FOG’s measurements.
While similar performance products cost about €40,000 to €50,000 on the market, the FN200C is priced at 25-40% less than its competitors, Ryu says.
A further advantage, he stresses, is lead time. The company has invested heavily in its production facilities and now aims to deliver products within four to six weeks, instead of the industry typical six months to a year.
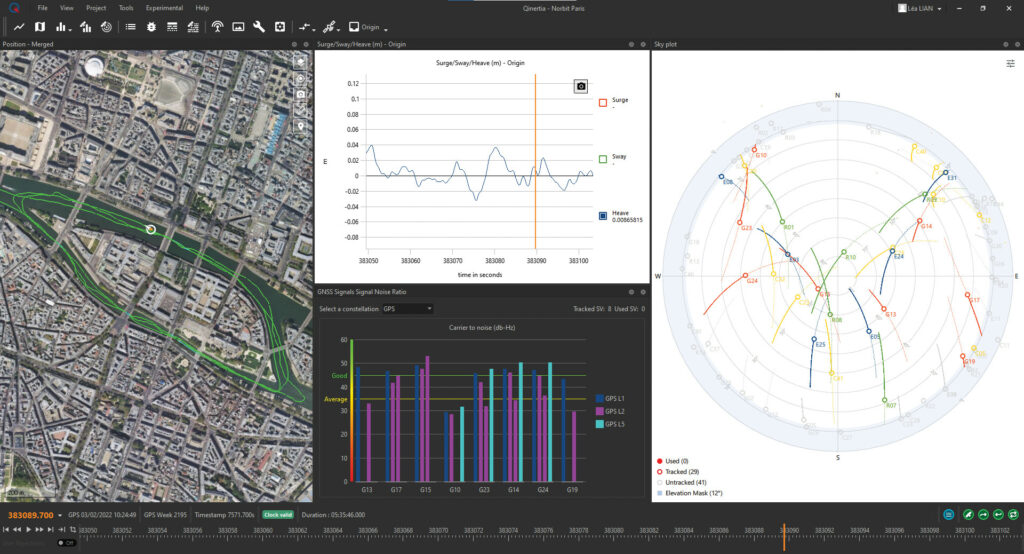
SBG Systems has launched the latest version of its Qinertia post-processing kinematic (PPK) software for surveyors. PPK is used to minimise errors in GNSS positions to achieve centimetre accuracy. Qinertia 4 was launched in December and, according to Florian Ollier, offers significant new features over the previous version.
He highlights the brand-new Geodesy engine, which integrates an extended network of continuously operating reference stations (CORS) consisting of more than 5,000 SmartNet base stations for GNSS error correction.
A Geodesy engine is the algorithmic component of a software suite, responsible for processing GNSS observations and calculating precise positions on the Earth’s surface. It also runs models related to the Earth’s shape and gravity field, and handles various reference systems, such as WGS84 and ITRF, and transformations between them.
It also handles error correction and mitigation, and supports advanced positioning techniques plus integration with GNSS receivers and data-processing systems.
The engine comes with a set of versatile tools and an extensive selection of coordinate reference systems, enabling surveyors to use essential official systems and transformations, as well as custom ones for specific requirements.
The software automatically ignores satellites with low signal strength and allows the user to select which ones to ignore.
One of the most important features of the PPK is the forward-backward processing, says Ollier. This processes GNSS data in the normal forward-time direction to calculate the receiver’s position. It then starts again at the end of the data-collection period and returns to the beginning to estimate the receiver’s position from the last observation back to the first. This step helps to detect and correct any biases or errors that may have accumulated during the forward processing.
“Qinertia is a powerful and easy to use post-processing software that really improves the accuracy of your data,” he says.
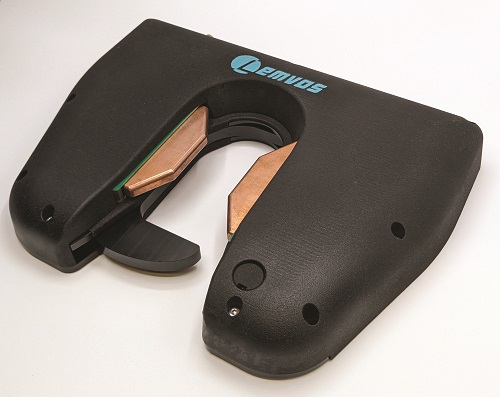
Lemvos, founded in 2022, presented its DockMaster automated docking and charging system for electric USVs up to 6 m long at the show. The company is also developing a family of USVs that are intended to operate unattended for up to six months at a time.
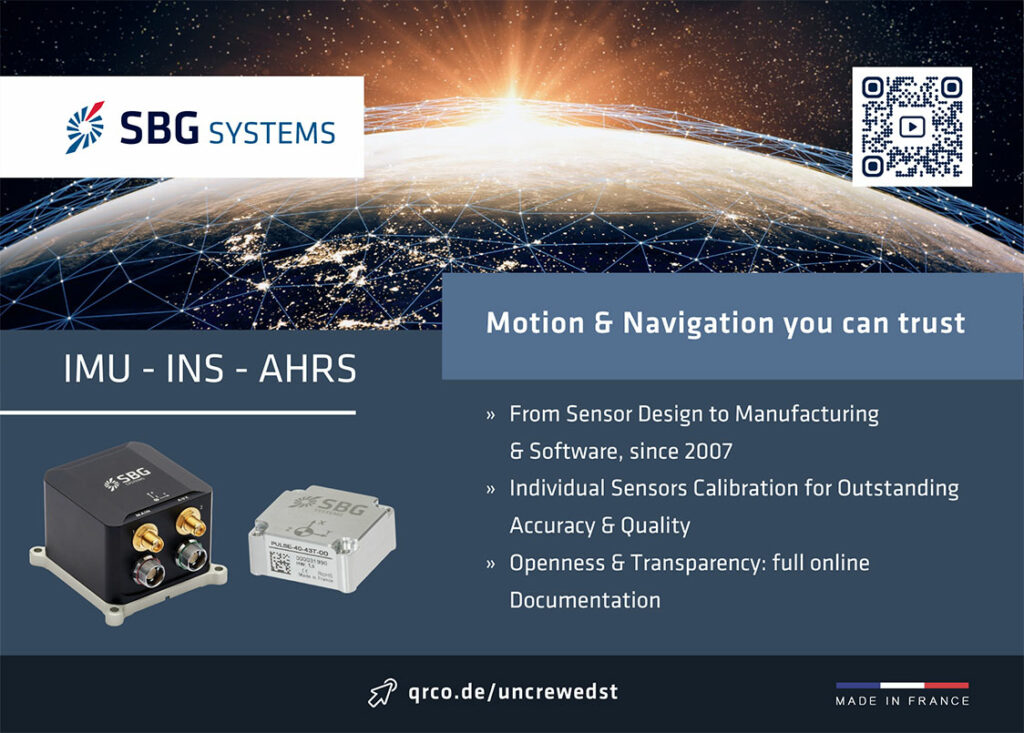
“We wanted the ability to dock the vessel and undock it without having anyone physically there,” says Daniel Severinsen. “We looked around for docking systems that don’t need a person there, but there was really nothing on the market.”
Severinsen describes the system as an electrically operated latch that is mounted to the front of the vessel, which latches itself to a pole on the dock to secure the USV mechanically. The system lets the boat roll, pitch and move vertically to cope with tides and waves, and withstands tensile loads up to 5 kN, he says. “That’s plenty for a USV up to around 6 m, depending on weather conditions.”
Fitted to the bow of a monohull or on a bracket between the hulls on a catamaran, the latch is a slam-closed system, he says. “You drive the vessel in, and the latch slams shut and it’s secure, and then to release it you send a signal to an electrical actuator in the latch.”
The dock itself is V-shaped to provide alignment guidance. Charging is by a low-voltage DC system that supplies current through the pole to a pair of copper contacts integrated into the latch.
“The charger is quite smart,” says Severinsen. “It applies about 2-3 V continuously. Then, when it sees there’s a boat connected, it goes up to the full voltage to start charging, and the charging curve is programmable for the battery type and voltage. We can charge up to 3 kW on a 48 V system.”
DockMaster development is complete and the system is entering production.
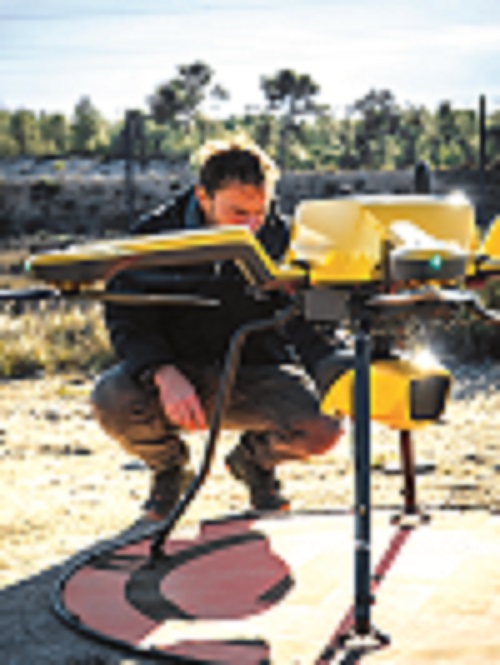
Yellowscan showcased its new Navigator bathymetric Lidar, carried by a Clogworks Dark Matter hX Gen 2 heavylift hexacopter.
Nassim Doukkali says the UAV equipped with the sensor can fly at up to 120 m above ground level and map the ground, the water surface and below the surface in shallow water in 3D.
“One of the main purposes of the system is to map coastal areas where a boat cannot go with a sonar because of rocks or waves,” he says.
Riverbed mapping is another key application, where water can be very shallow and the Lidar’s ability to penetrate vegetation is potentially very useful.
“With our system, you can map up to two Secchi of water depth,” says Doukkali.
This is a reference to a Secchi disk, which has alternating black and white quadrants, and is used to measure water turbidity. The Navigator Lidar’s green (532 nm) laser penetrates water to twice the depth at which a standard Secchi disc disappears as it is lowered in. In really clear water, the disc disappears at about 9 m.
“It’s a Class 3B visible laser, so it could be dangerous for the eyes at up to 30 m,” he says.
The Lidar operator is provided with safety glasses, and the team applies straightforward safety procedures to ensure nobody is within 30 m while it is working.
The Navigator attaches to a Gremsy universal mounting and it is powered by an internal battery, although it can draw power from the UAV instead, saving 400 g. With the battery, Navigator weighs 4.1 kg and runs for about 45 minutes.
The unit has an integrated IMU/GNSS from SBG, so a survey-grade GNSS antenna must be mounted on the UAV to achieve the system’s 3 cm accuracy and precision. The IMU is used to measure the angles at which the laser is transmitting to allocate 3D coordinates plus GNSS position for each laser shot.
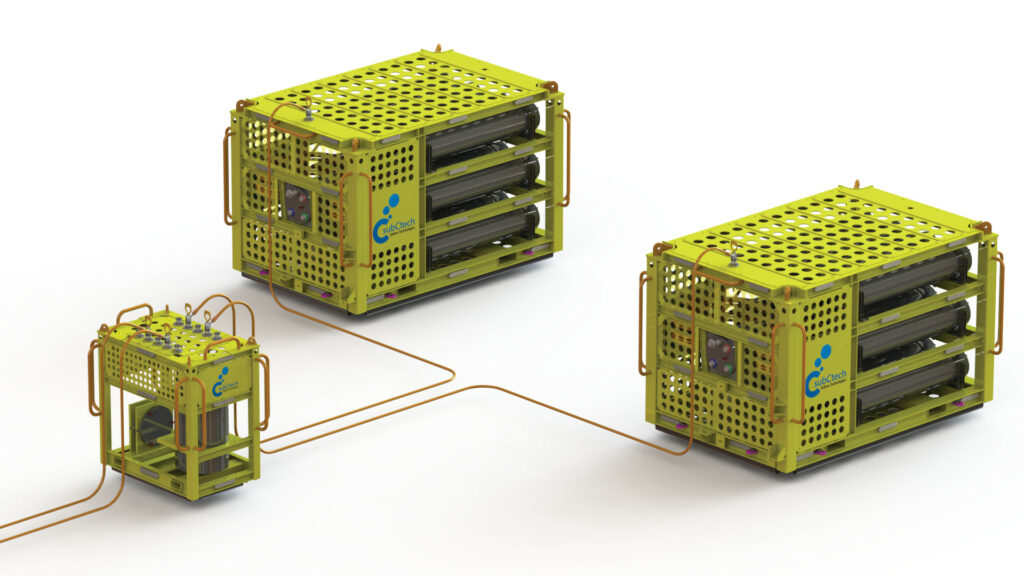
1 MWh are designed as back-up power sources, storage for renewables, and to feed docking/charging stations for ROVs and UUVs
SubCtech, a developer of lithium-ion batteries for use in underwater applications ranging from uninterruptible power supplies for energy infrastructure to running sensor networks, powering UUVs and providing energy storage for renewables, showed off a new battery in the megawatt/hour (MWh) capacity range.
The initial application is for a customer who needs a backup power supply to close pipeline valves, says Mike Naismith. However, enquiries are coming from other industries, including local storage for wind or wave energy, and from operators of underwater vehicles who want to be able to charge them without bringing them back to the surface.
“Our first customer now is in the process of bringing it in the water as we speak, and they’ve got two of them because they want to have them as a larger backup system. When one is being charged, the other one is operating on the seabed.”
The client also wants to be able to charge it underwater with renewable energy. “So that’s our next step on the development side: to push innovations in the energy market.”
Naismith says this explains why SubCtech has made its core battery technology scalable. To create the 1 MWh class battery system, the company took up to 12 batteries of about 100 kWh capacity, connected them together and mounted them in an underwater skid with a weight of around 23 t.
SubCtech builds its batteries to withstand the pressures encountered in the ocean at depths of 6,000 m and more, building the enclosures from titanium or duplex steel for the subsea industry. The company also makes all of the main components, including the battery management system, but excluding the cells. The industrial-grade cells are very reliable, and the BMS controls all operating conditions for maximum safety and reliability.
“Our batteries, particularly the large MWh energy storage systems, are the only fully international certified battery system in the industry. It is a simple and reliable way to save on equipment and maintenance costs, as well as to reduce the CO2 footprint at the same time; for example, by replacing long tiebacks and reducing vessel deployments,” says Naismith.
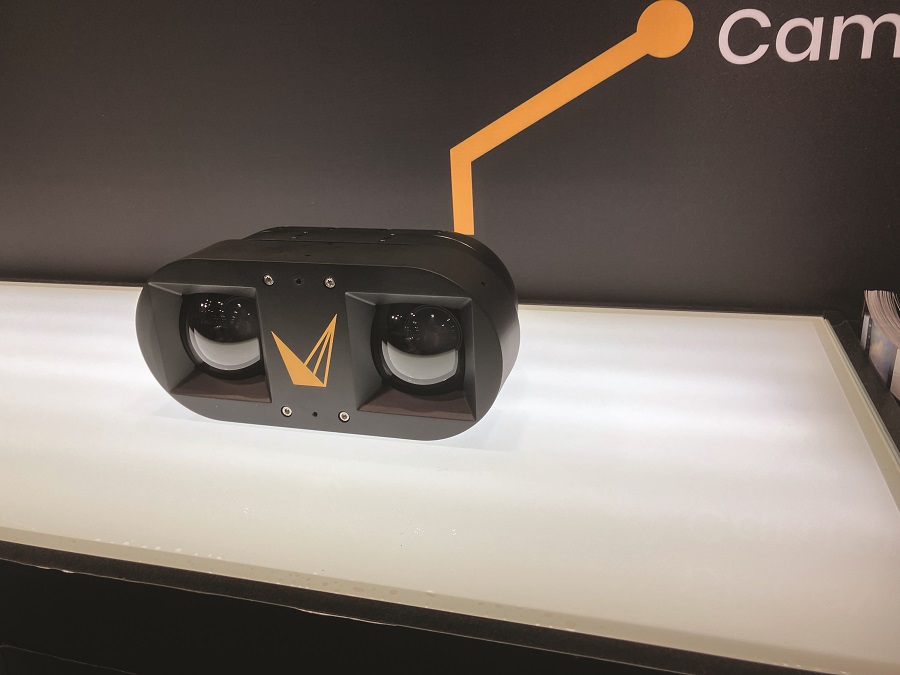
visual simultaneous localisation and mapping (VSLAM) software to create accurate, detailed models of underwater objects, supported by high-res images and 4K video
Voyis showed off its Discovery family of high-resolution, underwater vision systems for uncrewed vehicles. It includes the new, 300 m-rated, shallow water version of the Discovery Stereo camera, which joins the 4,000 m-rated version and the mono Discovery camera.
Both stereo cameras come with visual simultaneous localisation and mapping (VSLAM) capability, developed in cooperation with sister company EIVA.
“That’s what is going to bring real-time, 3D modelling capabilities,” says Patricia Sestari. “So the stereo cameras now provide high-resolution stills images, 4K videos, and real-time 3D modelling for positioning and quality control.”
The VSLAM capability is powered by EIVA’s NaviSuite.
“The Discovery stereo camera has been out there, being used commercially, for over a year, and what was lacking was real-time feedback to understand the model being created in real-time,” says Sean Elmer.
“Prior to the EIVA launch, we relied on ROV pilots and survey project managers, creating very rigid and structured survey lines and plans to make sure they covered everything they needed to make an accurate 3D model,” Elmer says.
“Now they can see the model being created in real time, and understand if there are any areas they’ve missed and can fill the gap.”
A good camera with large, sensitive sensors is essential to make the most of the VSLAM software and for 3D modelling, Elmer says.
“Being able to expose a global shutter for a millisecond, let’s say, to capture enough light to produce a usable image is very important – that coupled with very powerful LED lights,” he adds.
The domes, lenses and sensors of all the cameras are identical, but the 4,000 m-rated versions have titanium bodies, while the 300 m camera is housed in aluminium.
“With the 300 m-rated camera, we are seeing more use for it on inspection class and smaller vehicles, since the system is neutrally buoyant,” Sestari says.
UPCOMING EVENTS
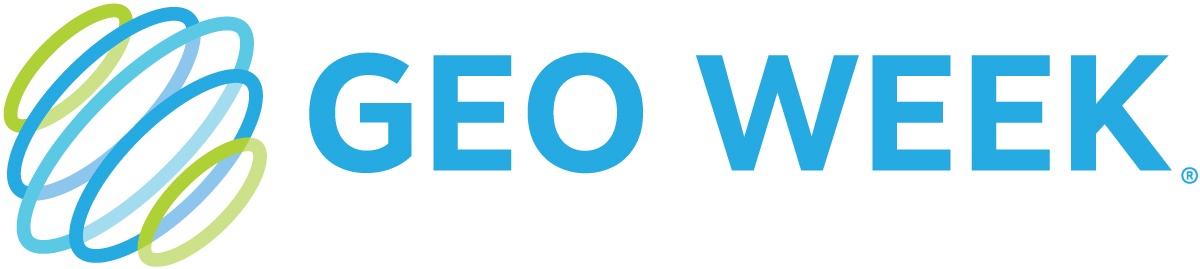
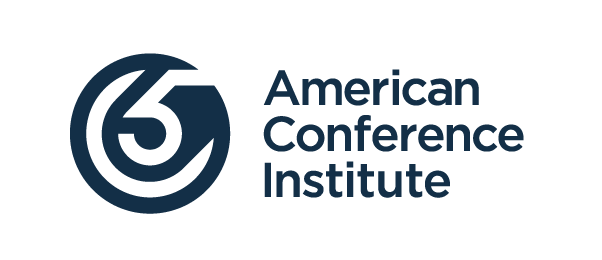
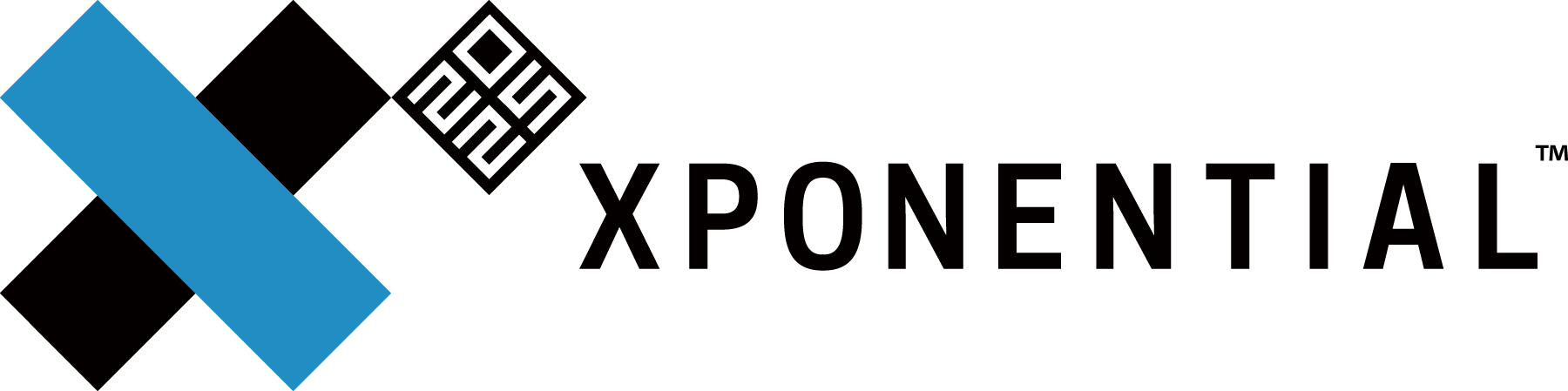
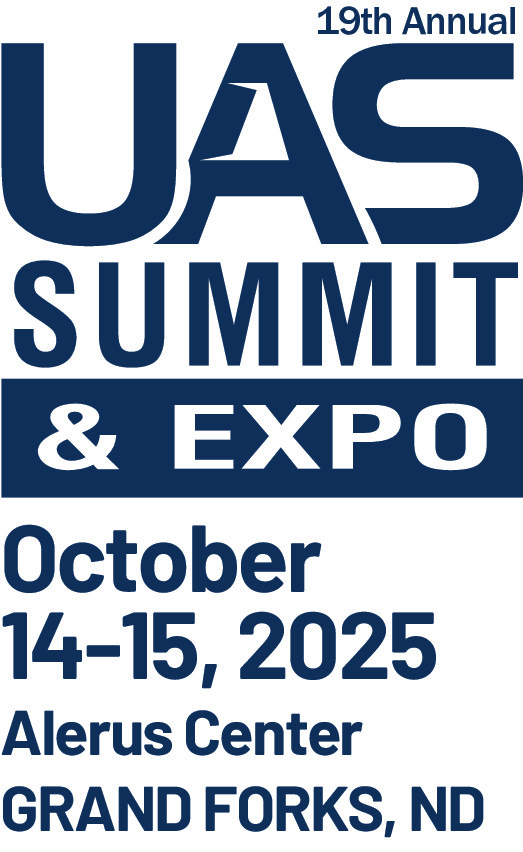
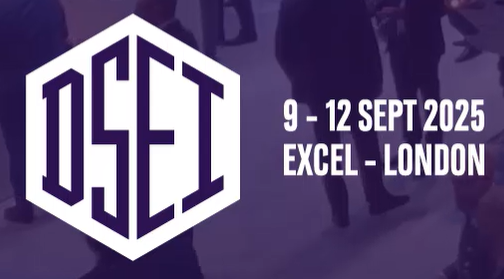
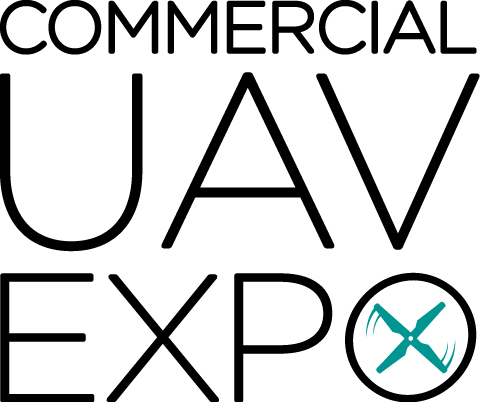
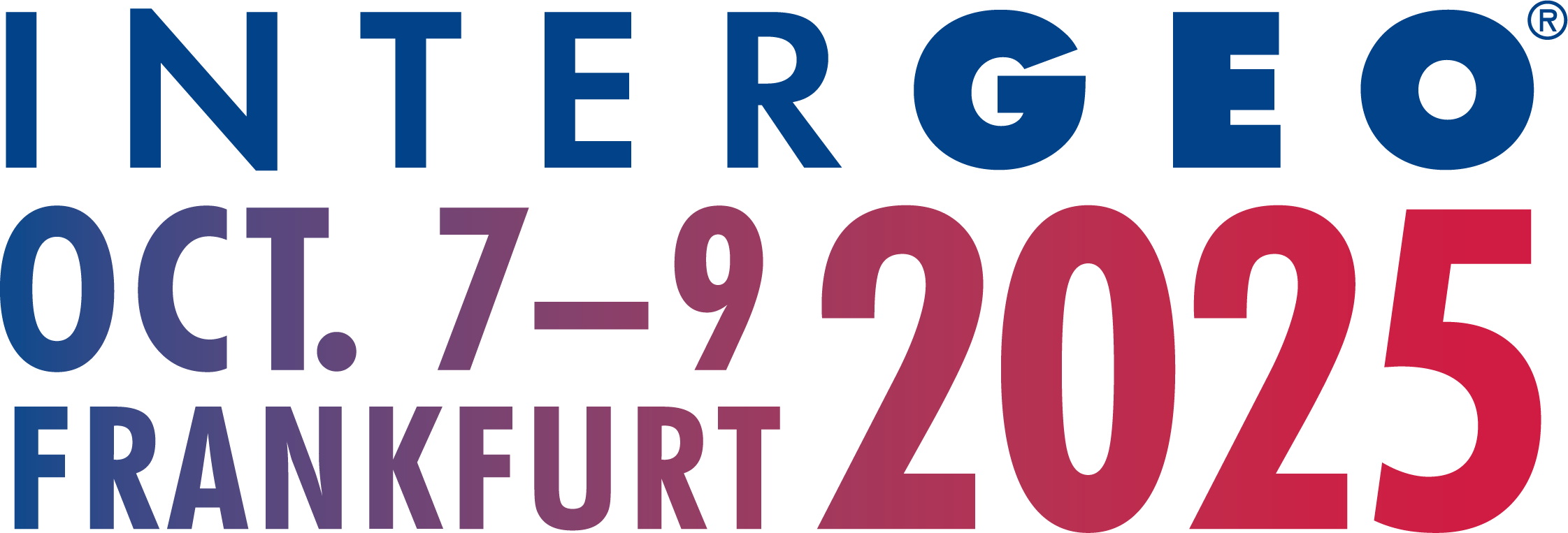
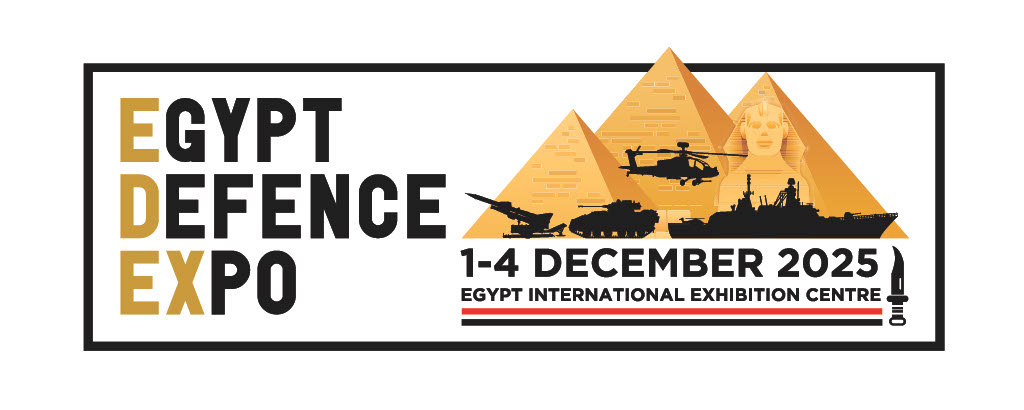
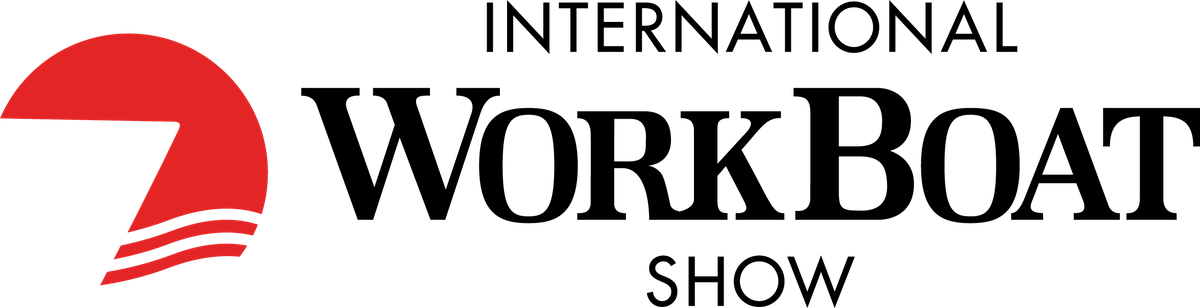
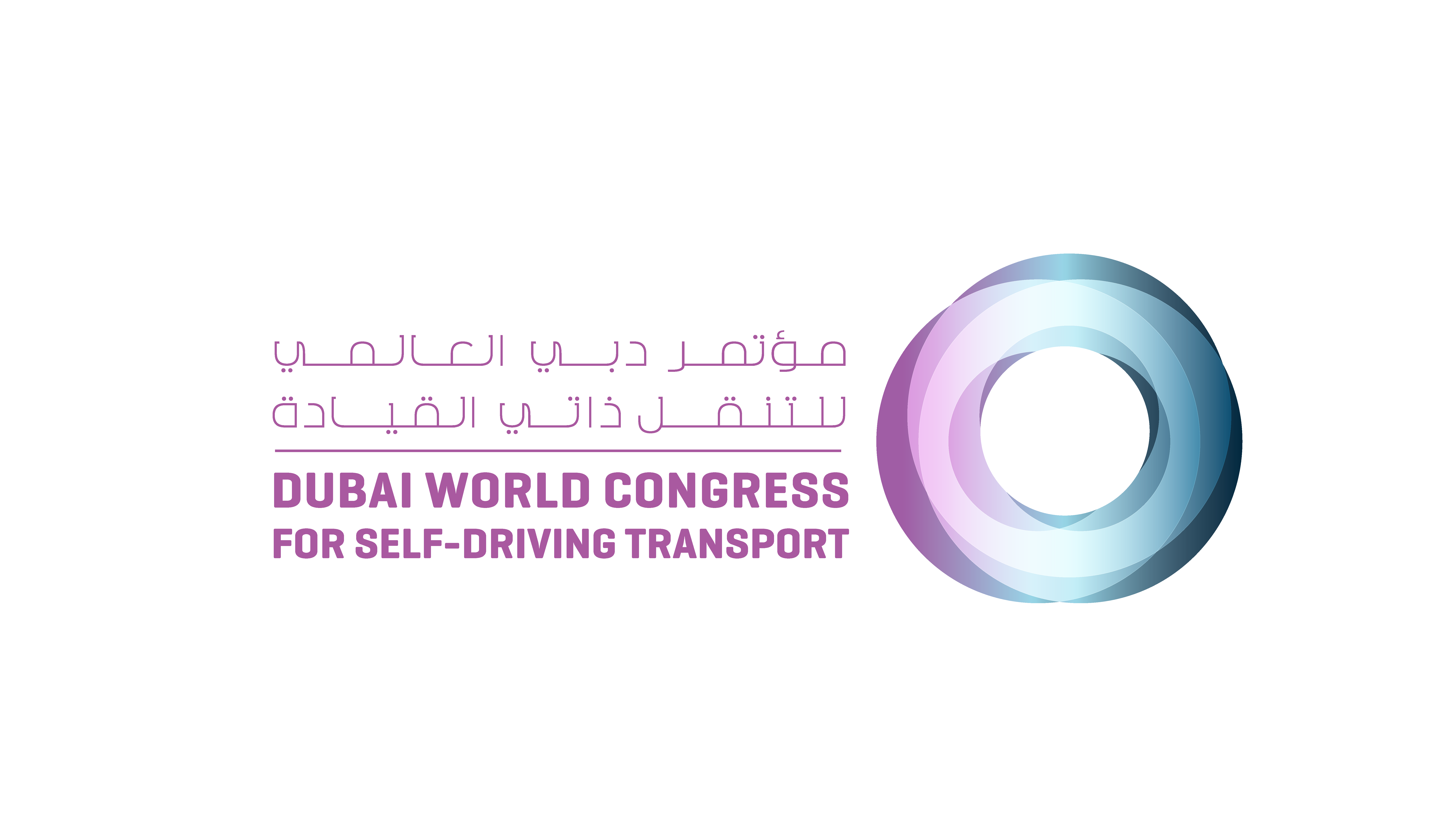
