UAVs
Multiple-choice questions
As the diversity of UAV types continues to grow, Rory Jackson quizzes developers on their different approaches to design
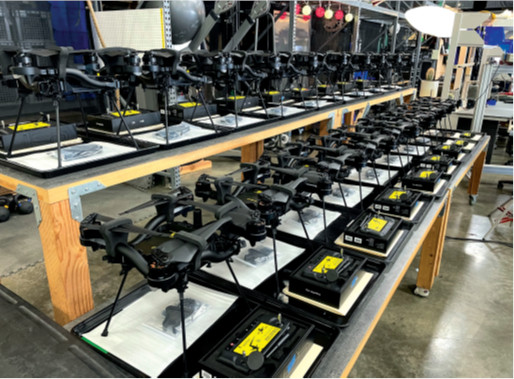
a more tightly integrated version of its wellknown
Alta X
(Courtesy of Freefly Systems)
In the 8 eight years since we began reporting on UAV developments, we have seen the technology evolve into dozens of different classes and types of craft for gathering data, logistics missions, emergency services and much more. It is a diversity that must overwhelm a newcomer to the industry – even two craft of the same size and weight can look strikingly different from one another for practical reasons.
To illustrate the breadth of systems that must be considered when researching and evaluating the state of the industry and the options available, we have spoken with a range of companies to examine the differences in UAV architectures.
Cinematography
Almost any professional aerial footage (as well as a lot of high-speed terrestrial footage) in movie and television productions nowadays was probably filmed using equipment from Freefly Systems. Since its founding in 2011, the US company has worked on advancing solutions for quality cinematography taken from UAVs and other moving platforms, and this year it unveiled its second original aircraft for that purpose.
“Our new Astro UAV is in many ways a smaller and more fully integrated repackaging of our Alta X, for users who want to transport our systems around the world more easily,” explains Tabb Firchau, president of Freefly Systems. The first Astro comes with a 61 MP Sony a7R IV camera (capable of up to 240 MP stills or 4K video), and it can fly with that for 25 minutes. Other versions will have sensors such as the Wiris Pro or FLIR Duo Pro R.
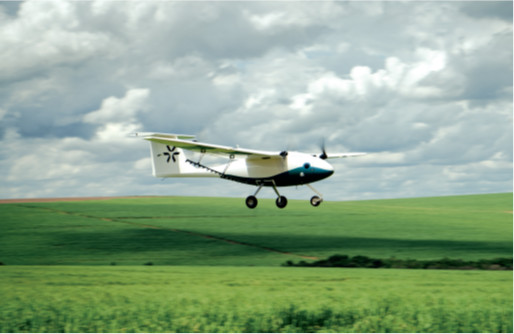
customer deliveries will start next year
(Courtesy of Pyka)
The Astro’s batteries have been designed to integrate 21700 lithium-ion cylindrical cells and Freefly’s proprietary BMS. It also uses Auterion’s Skynode avionics and connectivity suite, Freefly having designed and validated its own hardware in-house to conform to the Skynode’s reference designs.
“For our cycle-life tests on the Astro’s subsystems, we simulated drop tests, where a robot would drop the Astro over and over to see if the legs, booms or other parts would break,” Firchau adds. “We also redesigned our motor controllers to make them much faster, which is crucial for driving very large propellers for the platform’s size while still having high control during extreme filming manoeuvres.”
Agriculture
Over the years, we have observed that UAVs built for crop spraying make for larger and heavier designs than most on the market, and Pyka’s Pelican aircraft is no different. This all-electric fixed-wing UAS has an 11.5 m wingspan and measures 6 m in length, with a payload capacity of up to 317 kg.
“Our company has been building full-size airframes for around 5 years now, and our technology and designs are essentially at full maturity and ready for type certification,” says Garrett Rini, mechanical design team lead at US-based Pyka.
“The Pelican weighs 272 kg empty and 600 kg full with a 340 litre spray tank. We use a system of swappable battery packs in the nose, with endurance not being much of an issue as agricultural spray aircraft typically land quite often to refill their other tanks with fertiliser or pesticide chemicals.”
Up to 13 kWh of batteries are installed on the crop spray variant of the Pelican, with a future version to be designed for cargo deliveries that will integrate bigger batteries and have a larger fuselage to accommodate them and a heavier payload.
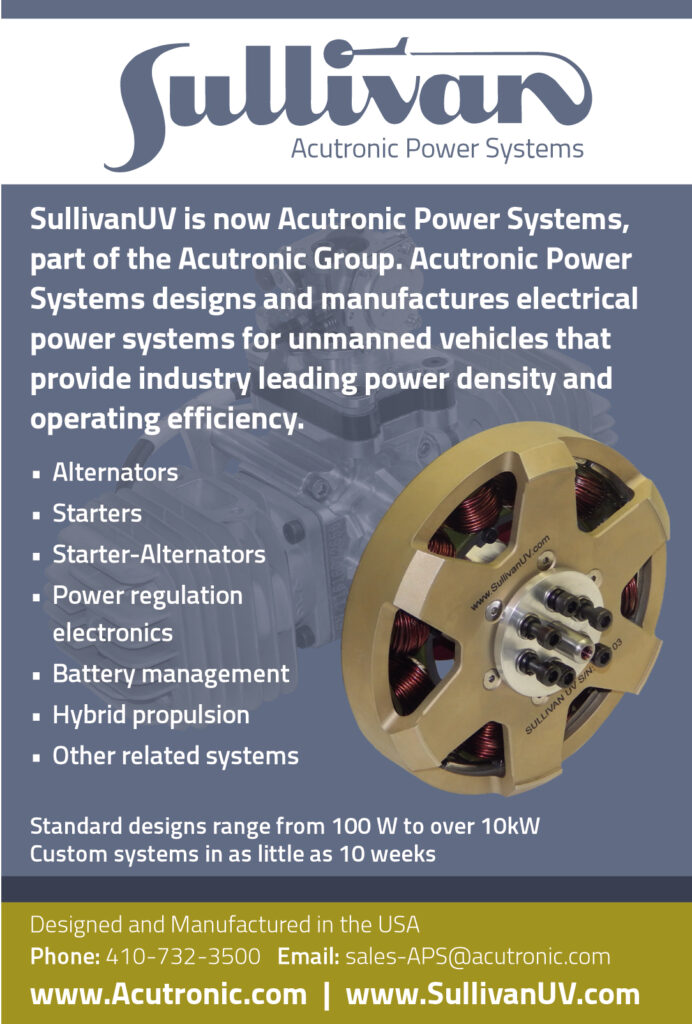
The aircraft has three 25 kW electric motors, which drive three carbon composite, fixed-pitch tractor propellers, one sitting on the tail and the other two on the wings. Future versions will have four such motors, powering four propellers: two in front of the wing and two in the back of the wing.
A 60 ft electrically powered boom system for spraying is installed beneath the Pelican’s wings; it features variable-speed rotary atomisers and a proprietary high-speed centrifugal pump. As well as delivering the chemicals, the system enables the UAV to adjust its flow rate and droplet size during flight, to optimise the efficiency and precision with which the chemicals are distributed.
To date, the aircraft has been delivered to customers in Costa Rica and Brazil, with further deliveries later this year to a new customer in Honduras. In total, Pyka has more than 200 orders and options for the Pelican, to be delivered from 2023 onwards.
For other users needing heavy payloads in agriculture (among other applications), ZenaDrone has developed its ZenaDrone 1000 UAV for carrying payloads of up to 40 kg.
“It’s a customisable and hence multifunctional UAV, constructed fully from carbon fibre, and although it looks like a multi-rotor at first glance, it has eight electric motors for VTOL that rotate through 90º for transitioning into and out of forward flight,” says Simon Henry, business development manager at ZenaDrone.
“This is our first aircraft, and it’s going into production now. It’s battery-powered for a flight time of an hour, and we have a charging pad we’ve developed in-house that also charges it in an hour.”
To enable better data gathering and processing, the entire central section of the fuselage is hollow, which leaves room for custom integration of payloads and associated computers and cabling. The underside of the nose can be removed for easy installation of camera gimbals such as EO/IR and hyperspectral.
ZenaDrone has also developed AI capabilities, including the use of machine learning to develop facial recognition software and vehicular number plate detection for security customers.
“We also have extensive AI support for agricultural inspections,” Henry adds. “For instance, our systems can identify crop diseases through hyperspectral imaging very early on, and we’ve also developed an automated system in which, upon landing, the ZenaDrone attaches a sprayer to spray the specific area of land to cure the diseased area.
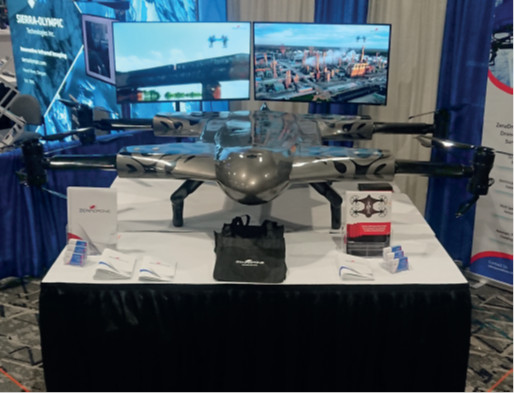
and utilise AI to scan and analyse the condition of crops
and livestock
(Courtesy of ZenaDrone)
“We also have a seeding machine, not just in agriculture but for reforestation too. And through AI we can also help in livestock management, first by detecting and identifying animals from the sky, and then with IR sensing to gauge their health and judge if their body temperatures are OK.
“We also have a geo-tagging system for counting and tracking animals and delivering live updates on their positions to their farmers, which would be important in areas where there are problems with rustling.”
ZenaDrone is also working with other aerial survey customers, including in inspections of wind farm blades and the development of aerial cleaning capabilities, by mounting a telescopic robotic arm payload under the ZenaDrone 1000 to replace the dangerous, traditional approach of suspending human cleaners from helicopters to clean turbine blades.
The next-generation version of the ZenaDrone will be gasoline-electric and be capable of up to 4 hours’ endurance. This hybrid-powered tiltrotor is anticipated to be unveiled later this year.
Mapping
The introduction of UAVs as a tool for faster, safer, and less costly mapping is enabling greater awareness of topographical assets, disaster zones and widespread infrastructure without the use of expensive and potentially dangerous aircraft such as helicopters, or very lengthy and labour-intensive ground-based surveys. It can also mean high-speed targeted delivery of urgent light-to-medium weight packages such as medical supplies, industrial repair tools and disaster relief equipment.
However, a desire to avoid paying for these new streams of data and capability in the form of increased harmful greenhouse emissions and energy bills is gradually pushing the UAV industry away from pure IC engine power and towards more emissions-efficient solutions.
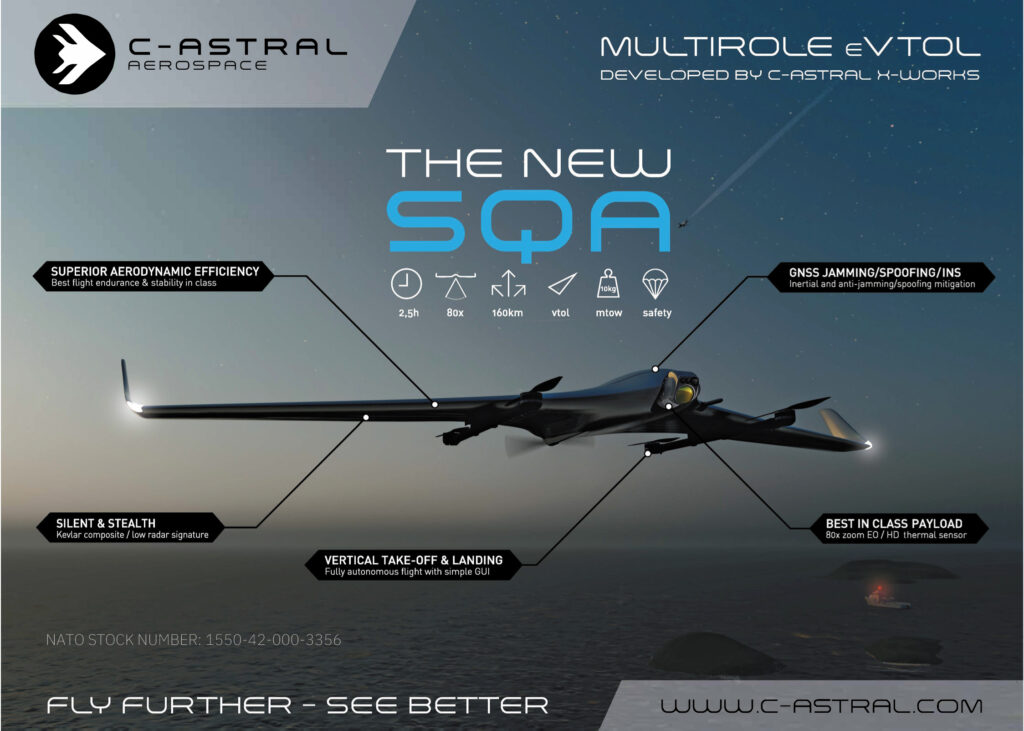
IC engine hybridisation can help greatly in this regard, although for those wishing to go even further in emissions reduction, proton exchange membrane (PEM) fuel cells offer an ideal compromise solution, unlocking range-to- weight ratios typical of some fuel engines in tandem with the advantages of zero emissions and low maintenance needs of a battery-electric powertrain.
For several years, Doosan Mobility Innovation has kept this growing market in mind as it developed its long-range, heavy-lift multi-rotor UAVs around its proprietary PEM fuel cell ‘powerpack’ systems, offering the latter as a system for other UAV systems integrators as well. Most recently, it has gone further and developed a fixed-wing, VTOL-transition UAV aimed principally at the medium-mile logistics and survey sectors.
Doosan’s new UAV, the DJ25, is a VTOL-transitioning craft that was developed in collaboration with JOUAV, using one of the latter’s gasoline engine-powered fixed-wing VTOL-transitioning platforms and replacing the IC engine with the former’s fuel cell system.
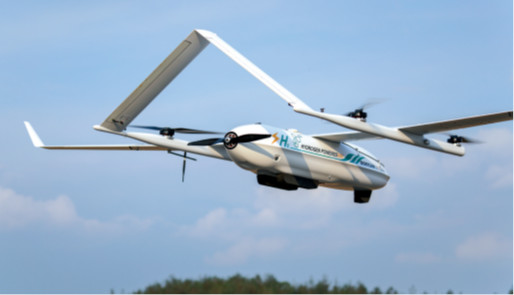
and endurances up to 5.5 hours while carrying 5-6 lb
payloads
(Courtesy of Doosan Mobility Innovation)
“Using hydrogen gas as the fuel, it flies for up to 5.5 hours, with about 5-6 lb of payload and no emissions, greenhouse gases or noise from the power unit,” said Soonsuk Roh, manager at Doosan Mobility Innovation. “Our main target during development has always been to match our fuel cell unit to the form factor of lithium batteries, so that UAV makers could use it as a drop-in replacement for battery packs.”
This meant that Doosan specifically had a small fuel cell powerpack, the DM15 (see page 68 for more details), in its portfolio as a solution for fixed-wing VTOL-transition UAVs, which only need high power during take-off and landing, as opposed to a multi-rotor which needs to constantly draw high power for hovering.
The hydrogen power unit enables a maximum payload capacity of 3.5 kg. The airframe’s wingspan is 4.28 m, it has a length of 2.09 m from nose to inverted vee-tail, while sitting 0.686 m tall. The craft weighs 27.5 kg when empty (assuming a 10.8 litre hydrogen tank), and its MTOW is 31 kg.
As standard, the craft will also integrate a hybrid battery system for regulating and stabilising the fuel cell’s voltage output as well as providing power if the fuel cell suffers a fault. It is typically a 2600 mAh pack consisting of two 384 g lithium-ion modules and measuring 117 x 45 x 33 mm.
The fuel cell’s energy on the DJ25 normally comes from a 10.8 litre Type 4 tank made from carbon fibre with a polymer liner. It weighs 4.3 kg and is certified to DoT standards in the US, AC418 standards in South Korea, TPED in Europe, WorkSafe standards in Australia and ISO 11119-3 by the CSA Group.
The hydrogen gas is pressurised to 350 bar in the cylinder. The check valve for enabling discharge (and preventing backflow) of gas is also CSA-certified for use in the US, Canada, Europe, and parts of Asia, and includes a pressure sensor as well as a thermal and pressure-relief device for safe automatic discharge of hydrogen in the event of its temperature exceeding 110 C.
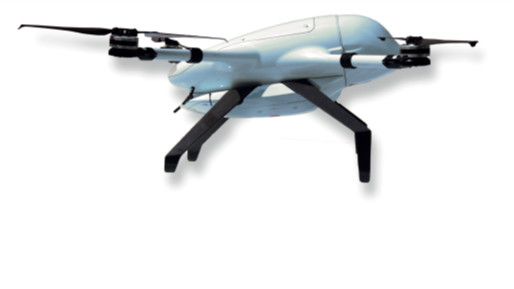
fluid dynamics of a beluga whale, hence its name
(Courtesy of EuroLink Systems)
Inspection and survey
Since 2016, Inspired Flight has been producing UAV systems designed primarily for survey and inspection applications across government and commercial operations from its headquarters in California. To improve the ROI of these applications through longer flight and greater payload capacity, and to continue doing so as a US DoD-approved Blue UAS vendor, the company has developed and recently unveiled its latest aircraft, the IF1200A.
“The IF1200A is an iterative update to our pre-existing IF1200, which had been our flagship product for the past 18 months,” says Marc Stollmeyer, director of product at Inspired Flight. “It has major improvements over its predecessor in several key categories, the first being flight time: we can fly for up to 44 minutes, or 85% longer than the IF1200, without significantly changing the UAV’s form factor.”
The IF1200A measures 165 x 154 x 77 cm when deployed, and folds down to 48 x 50 x 47 cm. The system also conforms to the Part 107-specified MTOW of 25 kg with a payload capacity of 9 kg, maintaining a 25-minute flight endurance while doing so. “And with a 9 kg payload, we can fly for 40 minutes,” Stollmeyer adds.
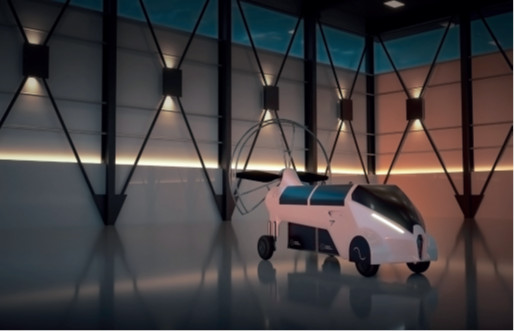
flight tests to prove out its capability to
fly for 800 km with a 100 kg payload
(Courtesy of Animal Dynamics)
To enhance the hexacopter’s endurance without piling on excessive weight or increasing the system’s size, the company’s engineers switched to much larger propellers (from 18 in diameter to 24 in) to enhance aerodynamic efficiency, as well as switching to more power-efficient electric motors.
“We’ve also overlapped the drives: the IF1200’s motors were all upward-facing, but on the IF1200 A, the clockwise-turning propellers are mounted under their motors, and the counter-clockwise propellers are mounted atop the motor arms,” Stollmeyer explains. “That helps a lot with keeping the UAV’s form factor compact and weight-efficient while using bigger props.”
The craft’s battery capacity has also been increased by 42%, from 22 to 32 Ah, and the electric motors have been customised to achieve higher power efficiency. They also feature screens over their apertures to keep dust out of their windings and enhance their MTBFs.
Inspired Flight has run them at full throttle on test benches without burning them out and plans to continue testing them for their full 1500 hour MTBFs, not only to validate them internally but also to provide fully detailed and accurate maintenance manuals for their customers.
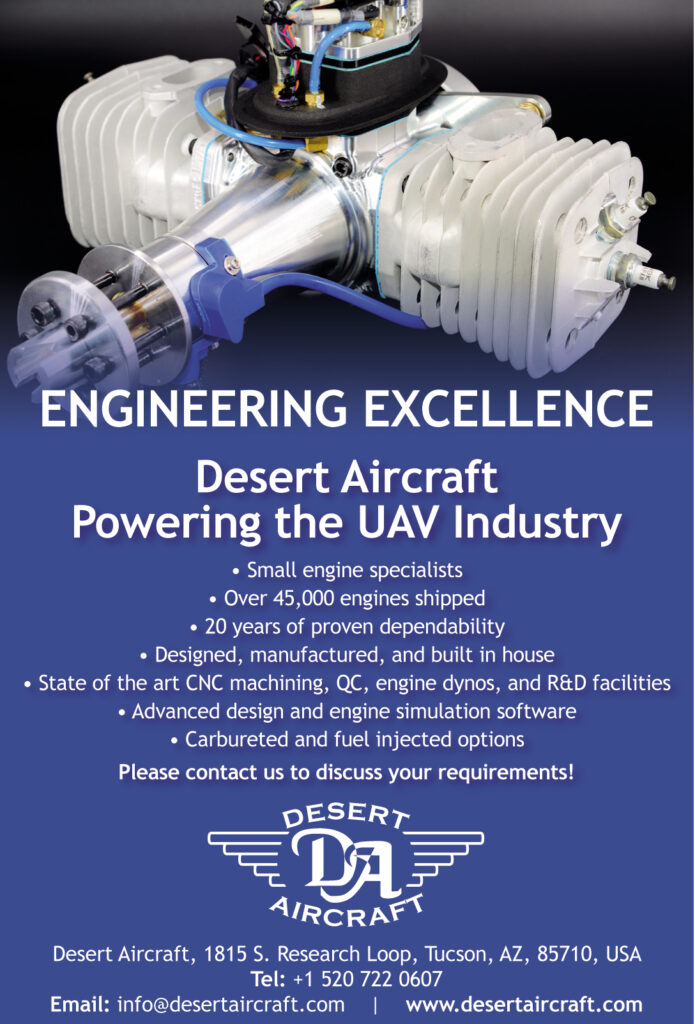
Frontline resupply
We reported on the ongoing development of Animal Dynamics’ Stork UAVs in issue 33 (August/September 2020) for risky frontline resupply and ISR platforms for defence users. The crafts’ bio-inspired paraglider design and open airframe are intended to lend them the highest possible wing-to-body ratio and hence the greatest weight-to-body ratio for optimised logistics capabilities.
As per its plans, the company has progressed from its 25 kg MTOW platform, the Stork ST25, to its much larger system, the Stork STM UAV, prototyped and currently in-flight tests.
Jonathan Page, analyst, and researcher at Animal Dynamics, says, “The STM can carry 135 kg across distances of 400 km. We’re defining user requirements in order to set development targets, and we’re going to carry out demonstration flights in the middle of next year, with production anticipated by 2024.”
The STM can also fly for 800 km with a 100 kg payload. Unlike the smaller ST25, which flies on an electric motor, the heavier Stork will use IC engine propulsion, enabling a 60 kph cruising speed (double that of the lighter craft). The ST25 meanwhile is now in production after being approved by the UK’s Military Aviation Authority.
Medical aid
As the search for bio-inspiration in aircraft designs continues, some UAVs now mimic sea creatures to achieve superior aerodynamics.
The first Beluga quadrotor UAVs from EuroLink Systems, unveiled last year at the Monaco Yacht Show, are designed for various duties for the luxury boating market, such as emergency delivery of defibrillators and other lifesaving medical supplies, wide-area surveillance of dangerous waters and pre-docking inspections of coasts and harboursides.
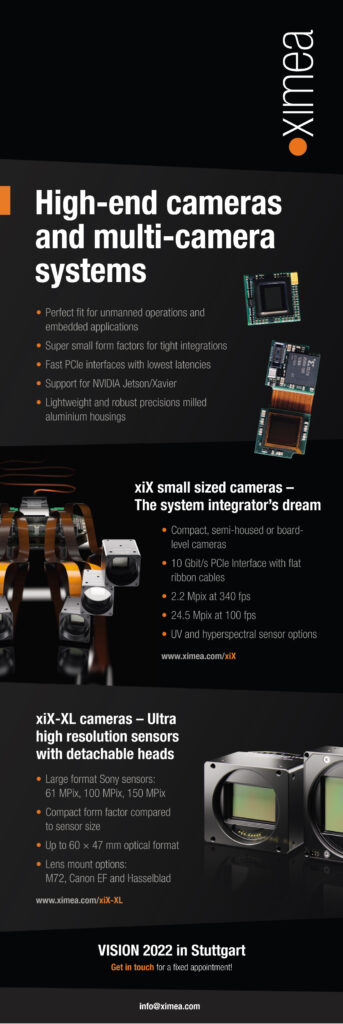
Marta Lapiana, COO at EuroLink Systems, says, “Since then we’ve expanded the Beluga product line into a family of multi-mission quadrotors, and for now we have a particular focus on critical aid missions such as high-speed sanitary blood transportation, search & rescue, and disaster area surveillance. However, last-mile logistics, precision agricultural mapping and other missions for public and defence users can also be handled with our different mission configurations.”
As standard, the Beluga measures 980 x 630 x 450 mm, and has a MTOW of 10 kg. Its aerodynamic design – which resembles the body of a beluga whale, hence its name – has wing-shaped rotor arms and can cruise at up to 110 kph; it also has a flight endurance of up to 60 minutes when carrying a 1.5 kg payload.
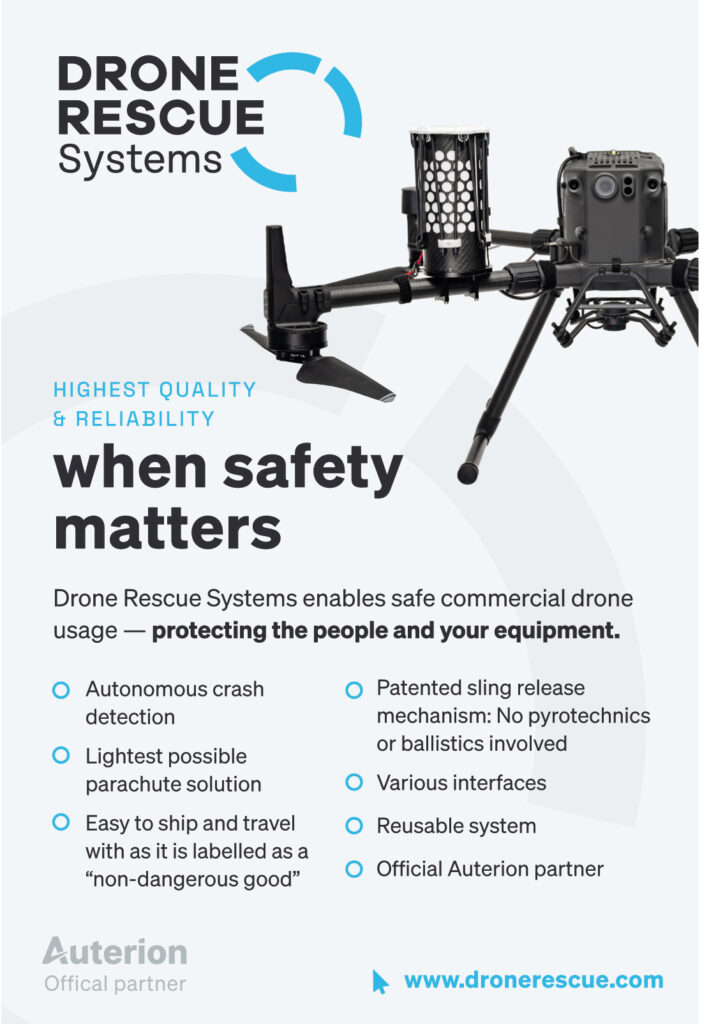
“We carried out some detailed and lengthy studies with the University of Rome to identify what would be the most aerodynamically efficient shape for a quadrotor body,” Lapiana says. “Most are just cube bodies with tubular rotor arms – very inefficient shapes – but ours is engineered to really reduce the impact and drag of air. Belugas are giant animals, but they’re shaped to move really fast and elegantly through fluid.”
The Beluga also integrates as standard an FPV camera, configurable as 1280 x 720, 1920 x 1080 (1080p) or 3840 x 2160 (8 MP or 4K UHD), and a radio data link with 20, 30 or 40 km of effective maximum range.
“We have several configurations of the UAV though,” Lapiana adds. “The white Fast Transportation version comes with a detachable cargo bay, the black Surveillance and Rescue version has a modular payload bay for swapping payloads such as EO/IR, Lidar and hyperspectral in and out, and the grey camo-print Military model is US Blue UAS-approved, using only components made in the US or allied nations.” All the variants are interoperable via the same control software and use a modicum of shared parts for maintenance ease.
“In the future, EuroLink plans to develop a tethered version for persistent semi-stationary surveillance, and a submersible version that can perform maritime surveys above and under the waterline – we look forward to returning the Beluga to the sea,” Lapiana says. “We are also developing biomimetic propellers with serrated trailing edges inspired by the speed and silence of owl feathers.”
ISR
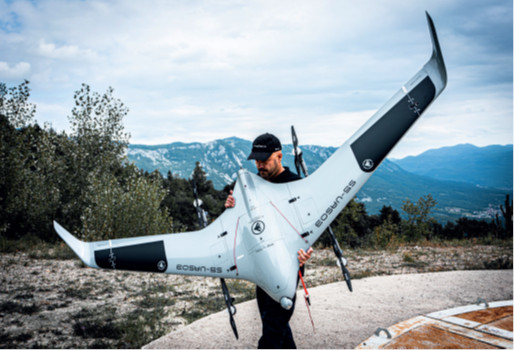
improved aero and VTOL transitioning
(Courtesy of C-Astral)
In issue 11 (December 2016/January 2017) we featured C-Astral’s Bramor UAV, a blended-wing body aircraft designed for long-range persistent surveys, and the Slovenian company has now unveiled its next-generation system, the SQA eVTOL UAS.
“We had a very long run with the Bramor – over 13 years and selling the system in 72 countries – and the SQA is the next evolution in the C-Astral ecosystem,” says Marko Peljhan, director and CEO of C-Astral.
“Based on many years of user feedback, we’ve designed it as an electric VTOL-transitioning machine with detachable twin booms and a MTOW of around 10 kg. It can also carry powerful ISR payloads, including an EO/IR system with an 80x optical zoom for the day sensor and an 8x optical zoom for the IR sensor.”
A lot of r&d went into optimising the aerodynamics and balance between the VTOL and cruising modes. As a result, the SQA can cruise at 61-108 kph, and in normal operation can take off and land in wind speeds of up to 29 kph.
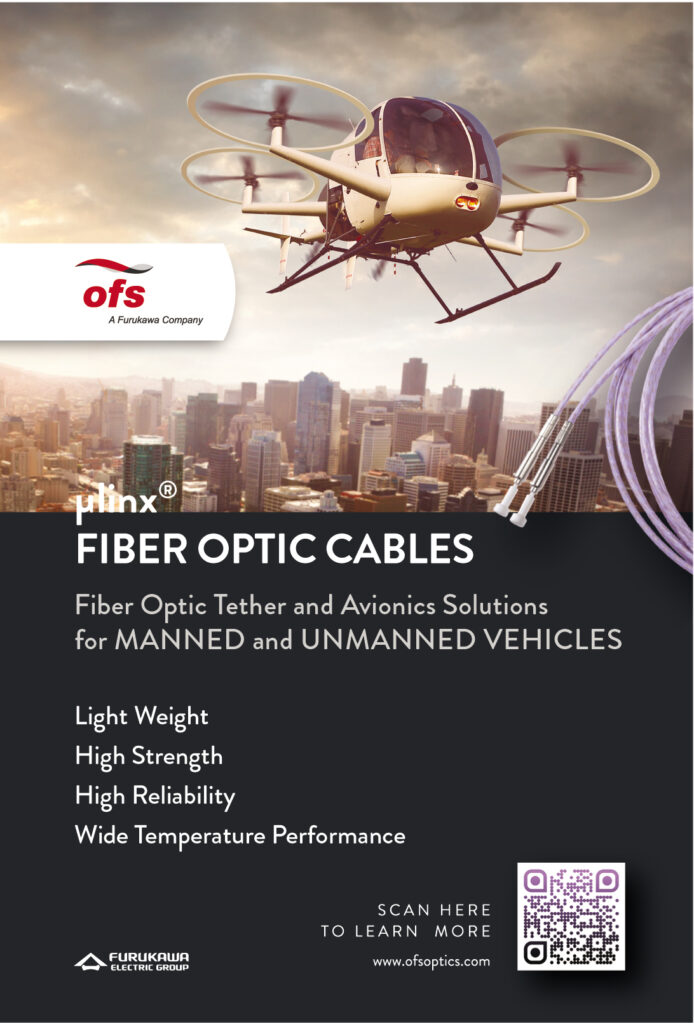
It flies for up to 2.5 hours on its battery, although the company has calculated that this figure will rise to 3.5-4 hours once the packs are switched from lithium-polymer to lithium-ion chemistry and the BMS is updated. These upgrades will be available in the SQA Mk 2, to be released later this year.
The first production and deliveries of SQAs began this May, with UVS Canada, Purdue University and Arctic UAV and Leonardo as its launch customers.
“We’ve carried over many of the Bramor’s features, including integration with our command, control, comms and planning software that sits at the heart of our C4 system, while using new avionics and associated firmware,” Peljhan adds. “We’ve also spent the past 4 years developing our own data link [the Astral- Dynamic DDL] using a proprietary protocol, although we still integrate comms from many of the top radio hardware providers such as Microhard, Trellisware, Commtact and Silvus.”
Wide-area surveillance
Thailand is responsible for almost 300,000 sq km of exclusive economic zone and more than 3200 km of coastline, making persistent surveillance as well as search & rescue capabilities critical maritime priorities. Natural disasters such as the 2004 Sumatra- Andaman earthquake and tsunami, as well as more man-made ones such as chemical leaks and oil spills, also demand quick humanitarian responses and disaster relief capabilities.
In addition, economic and infrastructure developments require versatile aerial platforms to conduct precise 2D/3D survey and mapping at minimum costs. As a result, UAV development is high up on Thailand’s national agenda.
For example, the Swiftlet is a multi-purpose UAV developed by the Royal Thai Air Force and the National Research Council of Thailand. It is categorised as a fixed-wing tactical UAV, and has a 5.5 m wingspan and a 100 kg MTOW. It is based on a modular design, a composite structure and current uncrewed technologies. It has an endurance of up to 10-12 hours compared with the 6-8 hours of previous iterations of its design.
Cobra International, a Thailand-based composites manufacturer, has been able to use its knowhow to reduce the Swiftlet’s weight considerably, which has been key to the craft’s endurance, by using a CNC-machined carbon sandwich material for the internal structures, with glass and carbon-fibre reinforced PVC foam sandwich skins. The Swiftlet prototypes were made by using a combination of wet layups and vacuum bagging, with some parts infused and some parts using pre-pregs. As a result, the composite airframe weighs about 32 kg, or one-third of the craft’s MTOW.
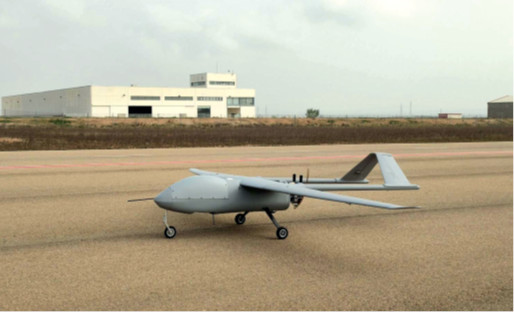
by the Royal Thai Air Force and the National Research
Council of Thailand
(Courtesy of Cobra International)
“The Swiftlet is the fifth UAV we’ve worked on at Cobra,” says Danu Chotikapanich, CEO of Cobra International. “The r&d project has been so successful that it will probably lead to industrial production of Swiftlets.
“Plans have been made with the r&d team to introduce a more efficient engine and to improve the consistency, precision, durability and finish of production airframes with our composite facilities and equipment. “And the project we worked on before this was a VTOL-transitioning UAV called the VETAL, for Thailand-based HiveGround.”
The VETAL is designed for large-scale surveying and mapping, particularly in crop monitoring missions for the vast plantations of Southeast Asia and elsewhere. It has machine learning (ML) visual data processing to enable analysis of parameters such as canopy area and height calculations, crop yield estimations, weed and disease detection, automatic fertilisation requirement calculations – both type and quantity – and automatic planning of the spraying pattern.
HiveGround’s use of ML also extends to offering pre-launch flight planning functions such as automated route mapping, swarm mission control, mission progress comparison and 3D flight area volume calculation.
The VETAL is a flying-wing design with a 1.3 m wingspan and measuring 1 m long and 0.7 m tall. Its battery gives it a maximum endurance of 60 minutes and a top speed of 108 kph, with a payload capacity of up to 800 g.
In addition to RTK and PPK processing of its GNSS data for precision mapping, it integrates a 2.4 GHz data link for live telemetry, as well as 5G and 4G cellular link options. A GCS 4G tablet is ruggedised to the MIL-DTL-810G standard, and comes with the company’s HGMC GCS software. HiveGrid‘s embedded fleet management software is also available.
Summary
With all the solutions investigated here, it might seem peculiar that the singular term ‘UAV’ is used for vehicles that can be fixed-wing or rotary, STOL or VTOL, tail-sitter or tilt-rotor, mechanical or bio-inspired, and weighing from 25 to 2000 kg.
We now see different uncrewed terrestrial vehicles being referred to as AUGVs, Q-UGVs, AMRs, self-driving cars and so on, and underwater systems as ROVs, micro-AUVs, LUUVs and XLUUVs. In light of this, it makes sense to develop a new taxonomy to describe the far larger and more diverse UAV ecosystem.
Whether that leads to reclassifications such as XLUAVs or uncrewed tiltrotors styled as UTRs, or more creative approaches, remains to be seen. There is no doubt though that, much like the design and engineering presented here, the best framework taken will be that which the market finds most helpful and appropriate.
UPCOMING EVENTS
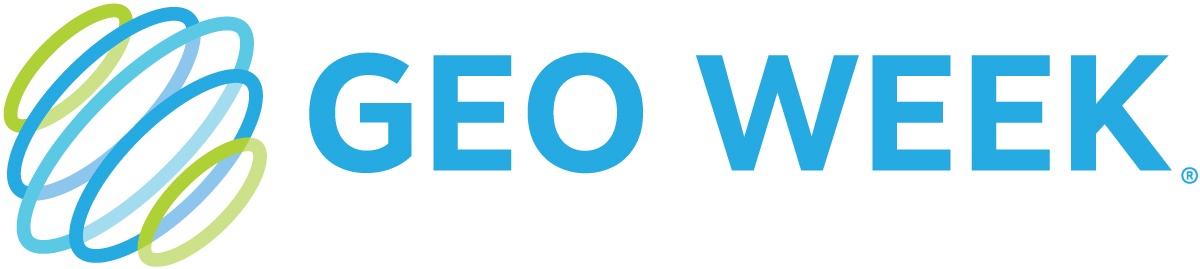
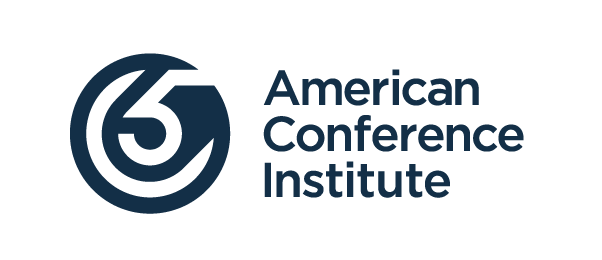
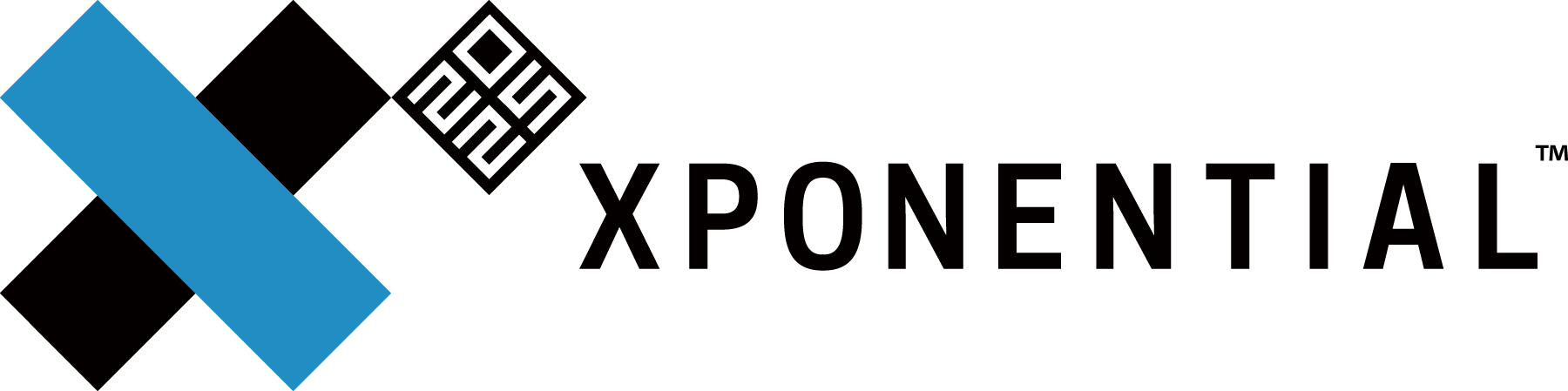
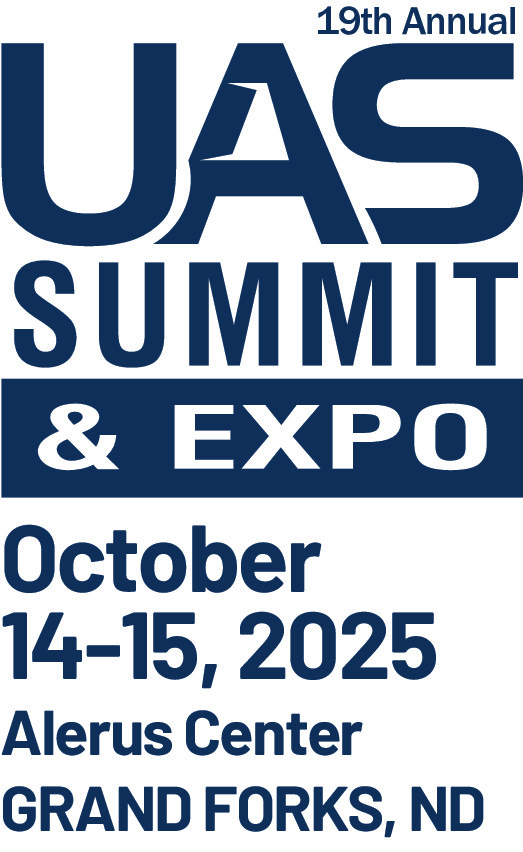
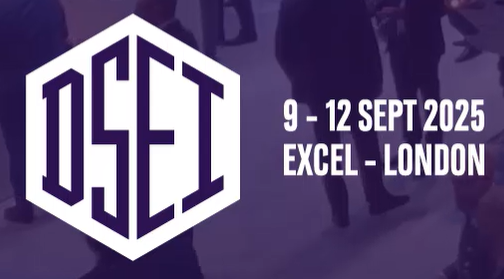
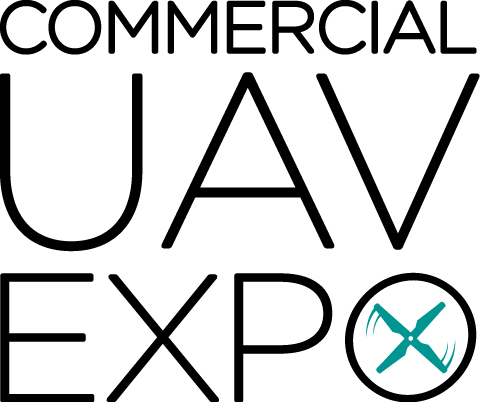
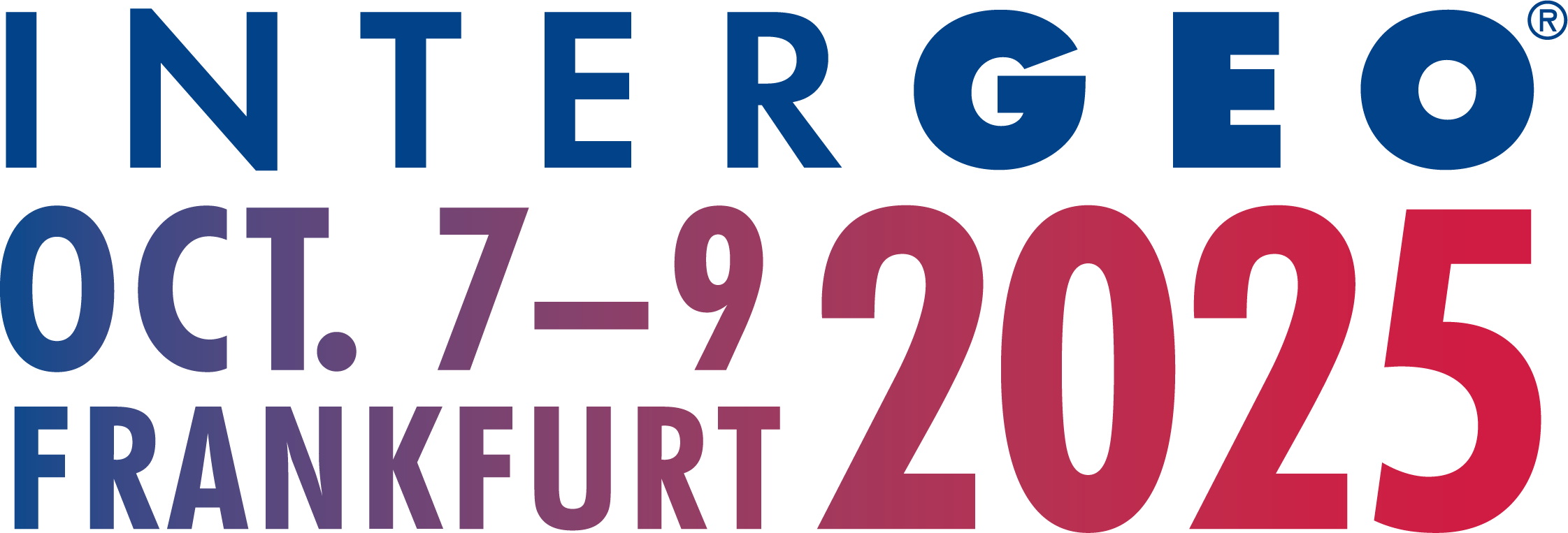
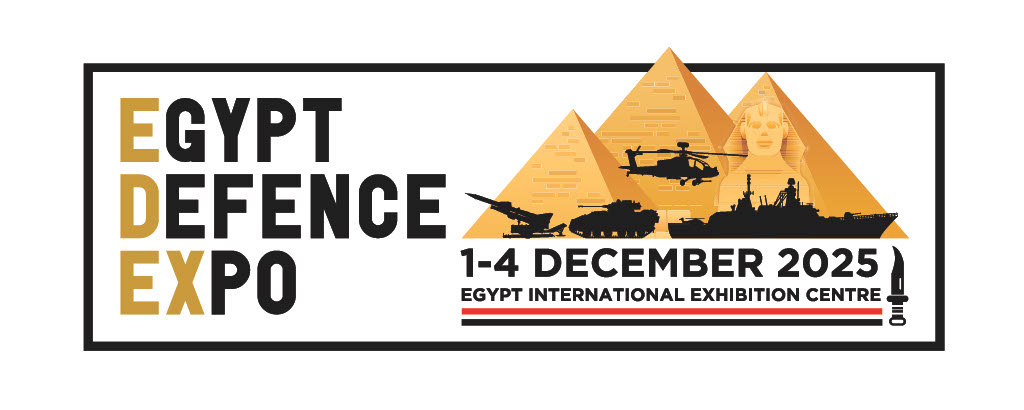
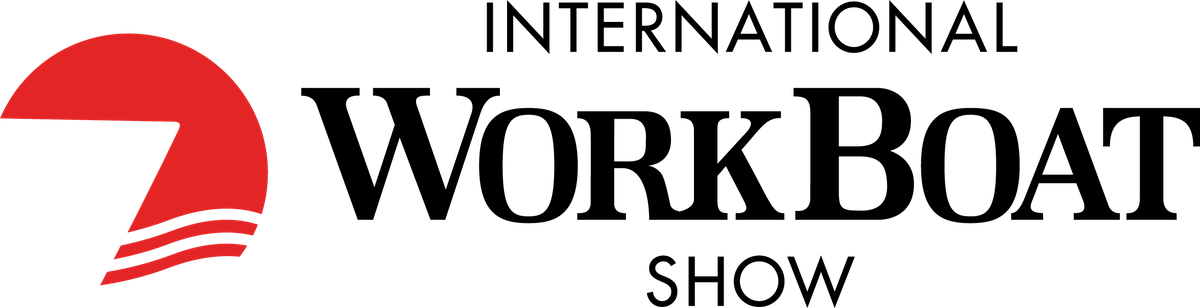
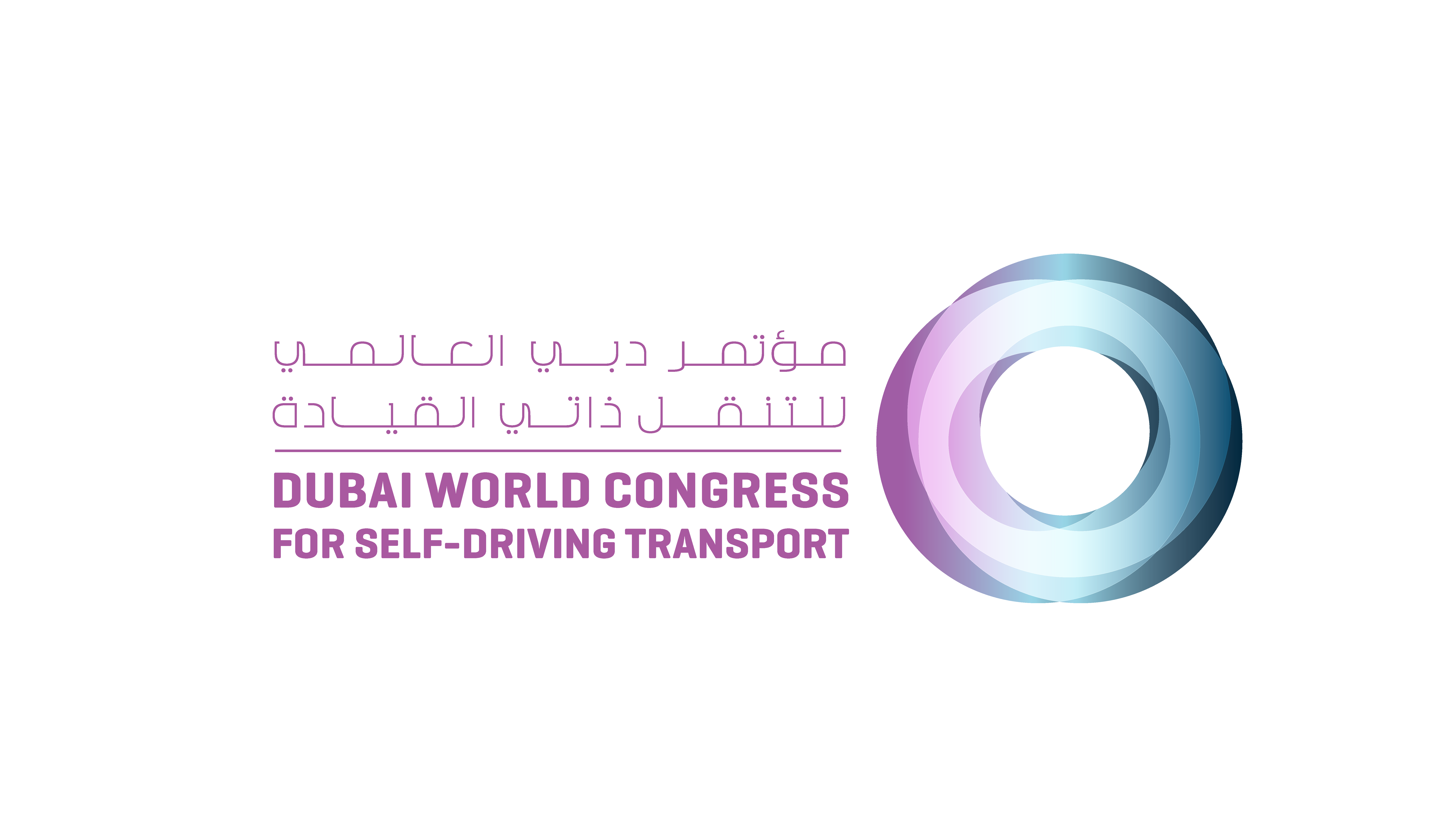
