MEMS timer
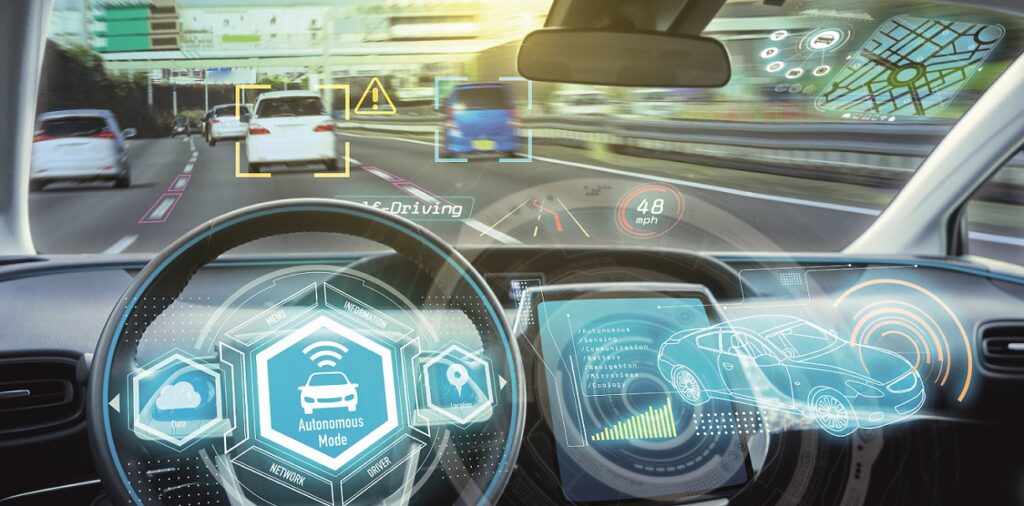
Driverless cars
A differential oscillator is providing more accurate timing for autonomous vehicles (writes Nick Flaherty).
The oscillator, developed by SiTime, uses a MEMS architecture to provide more accurate timing than existing oscillators that use quartz crystals.
As automotive safety systems integrate more sensors and cameras, they are generating an explosion of data that is crucial for safe, autonomous operation.
A typical vehicle generates 2 Tbytes of data each hour, according to the Automotive Edge Computing Consortium, but that is set to increase to 20 Tbytes per hour by 2025. All that sensor data must be transferred at very high speeds within the in-car network, even in the most demanding environments, to enable the central processing unit to make timely decisions for a safe, reliable journey.
Timing technology is one of the weakest links in vehicle electronics. Quartz crystals provide a timing signal, but they are susceptible to vibration and shock, extreme temperatures, and exhibit performance degradation over time.
The MEMS oscillator, built in silicon, uses a differential structure to cancel out internal noise and provide a typical jitter of 150 fs (femtosecond, a million billionth of a second) and ±30 ppm stability. Parts with a stability of ±25 ppm or better are also possible with the architecture, providing a signal from 1 MHz to 920 MHz.
The differential output drivers include LVPECL, LVDS, HCSL and low-power HCSL. A proprietary FlexSwing output driver performs like LVPECL but provides independent control of voltage swing and DC offset.
The oscillator is designed to interface with chipsets that have non-standard input voltage requirements without requiring external source-bias resistors.
UPCOMING EVENTS
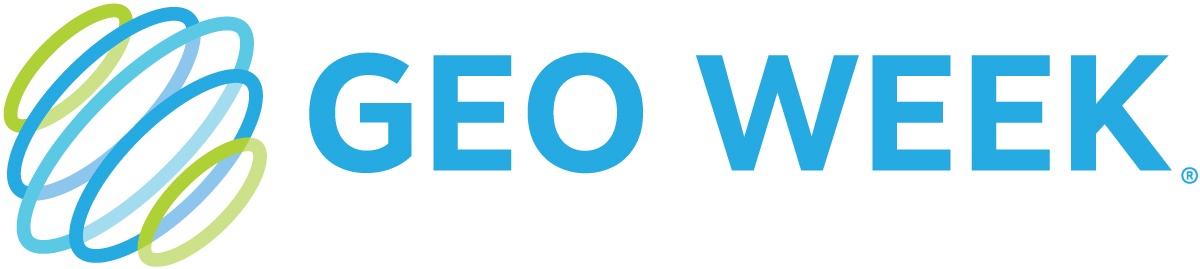
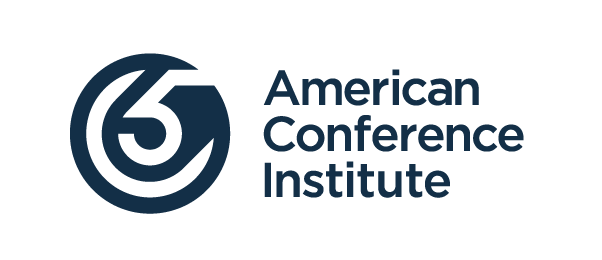
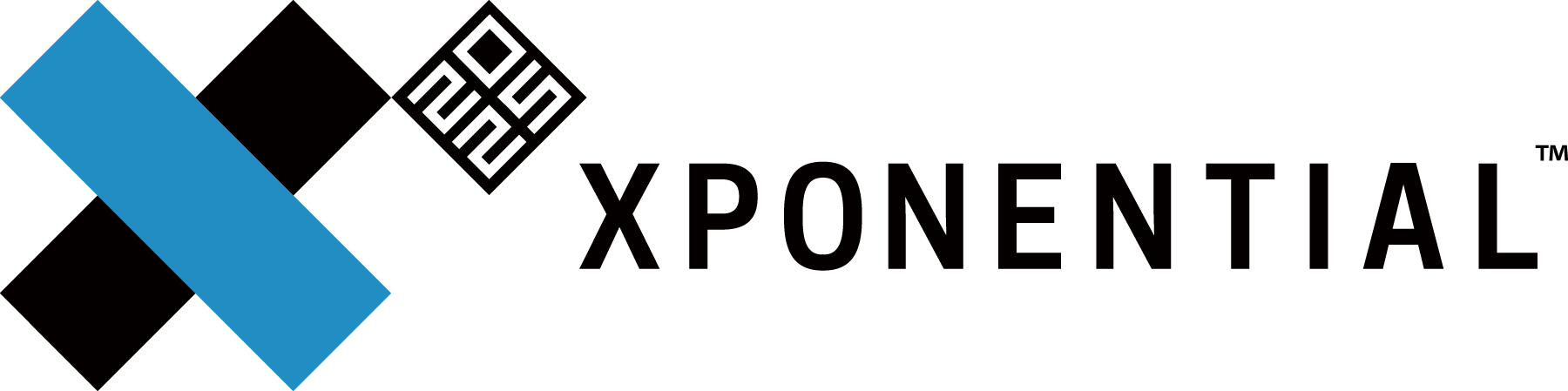
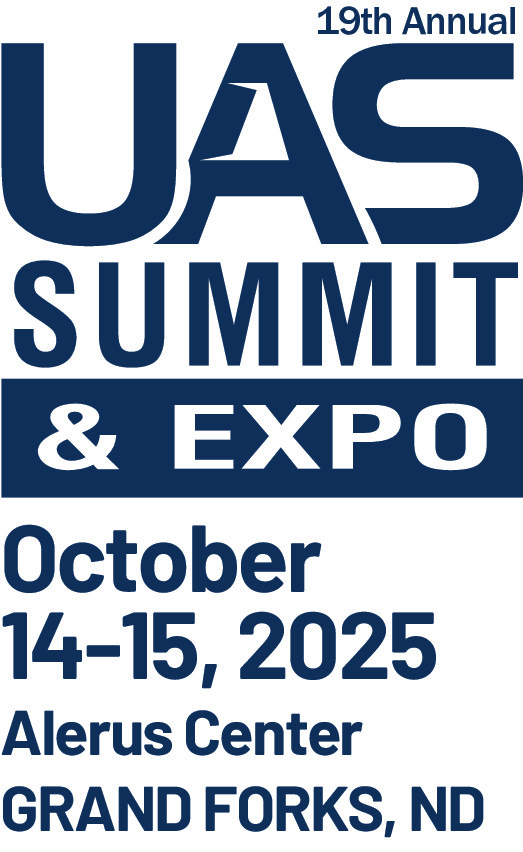
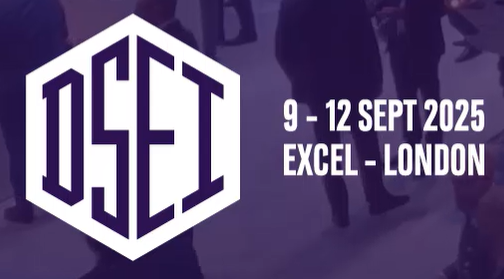
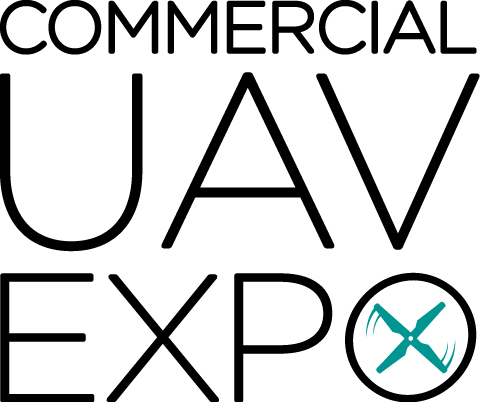
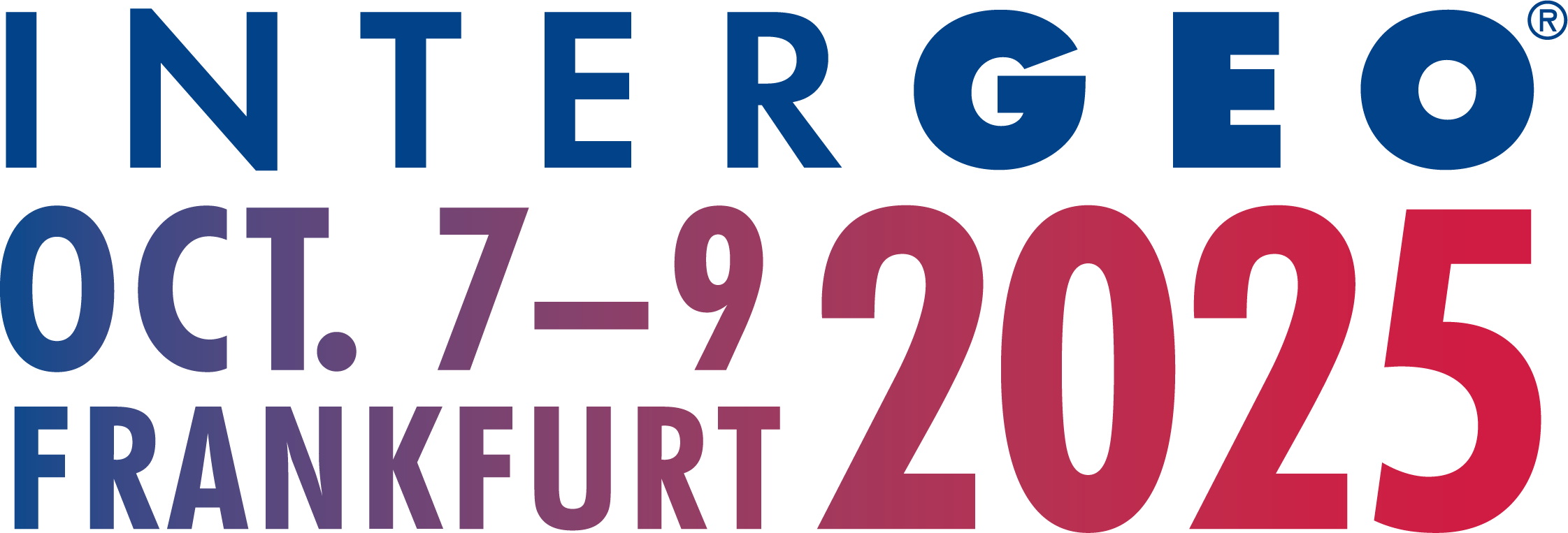
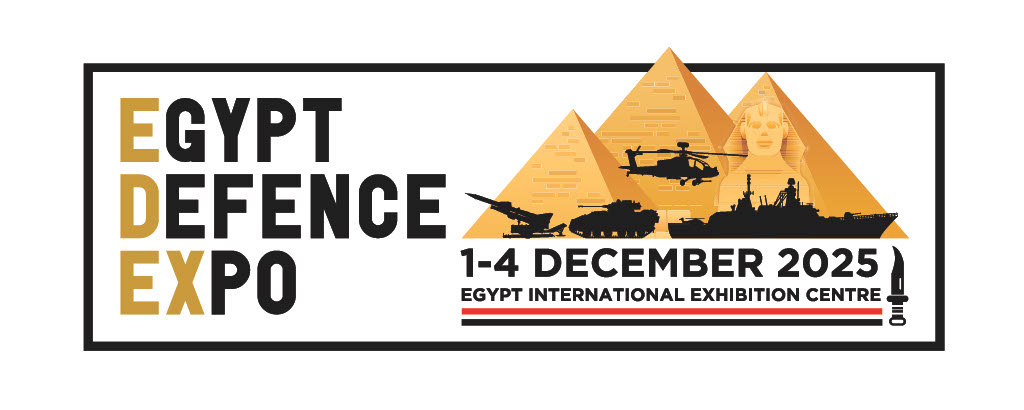
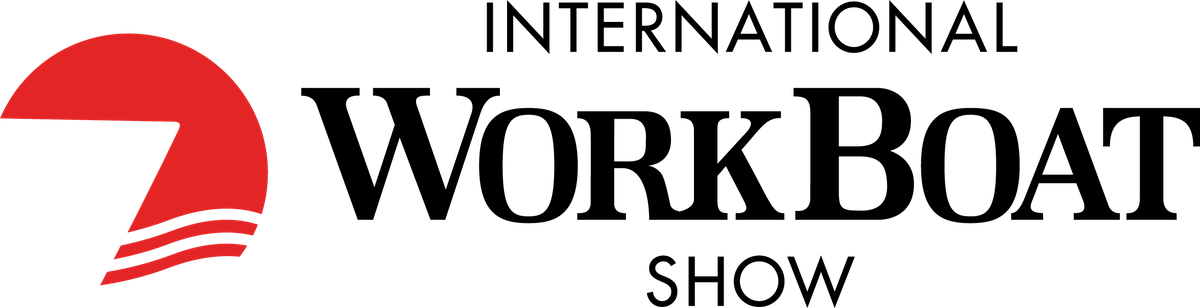
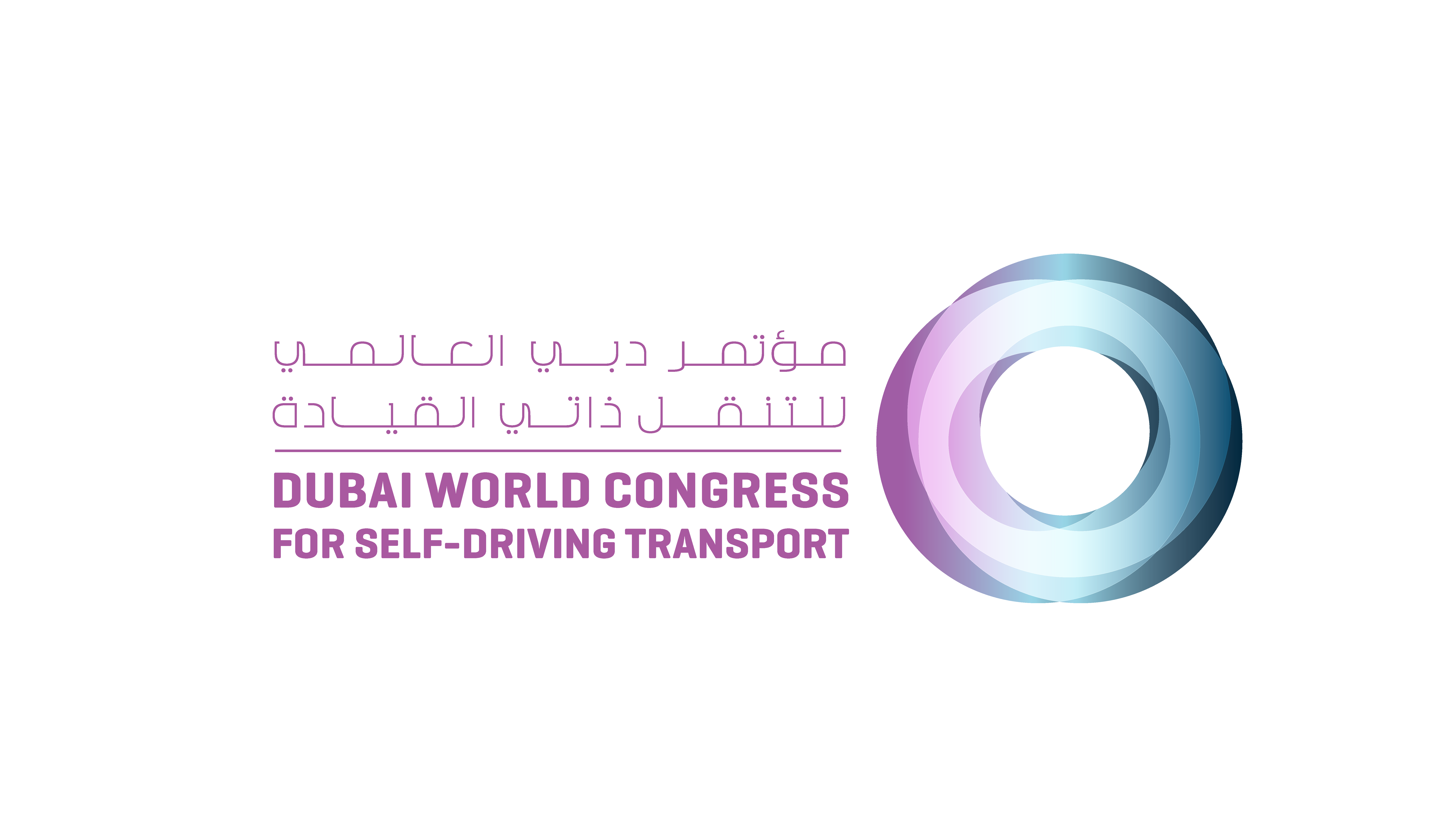
