Maritime Robotics
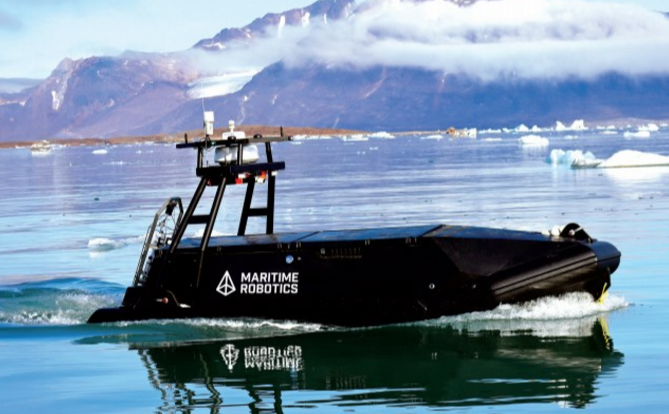
Rory Jackson discovers a Norwegian company that has gained the right to operate its USVs fully uncrewed
Earlier this year, Norwegian USV developer and manufacturer Maritime Robotics made headlines for establishing the world’s first uncrewed freight route, running between its headquarters in Trondheim and its production facility in Vanvikan.
The concept and challenges of autonomous shipping have been talked about in conference rooms and expo halls, and even explored in real-world applications such as the well-known Yara Birkeland container vessel (also developed and operated in Norway, by Yara International ASA). But, while that 3,200 t vessel must still operate with three crew members onboard, Maritime Robotics has achieved the right to operate its USVs fully uncrewed.
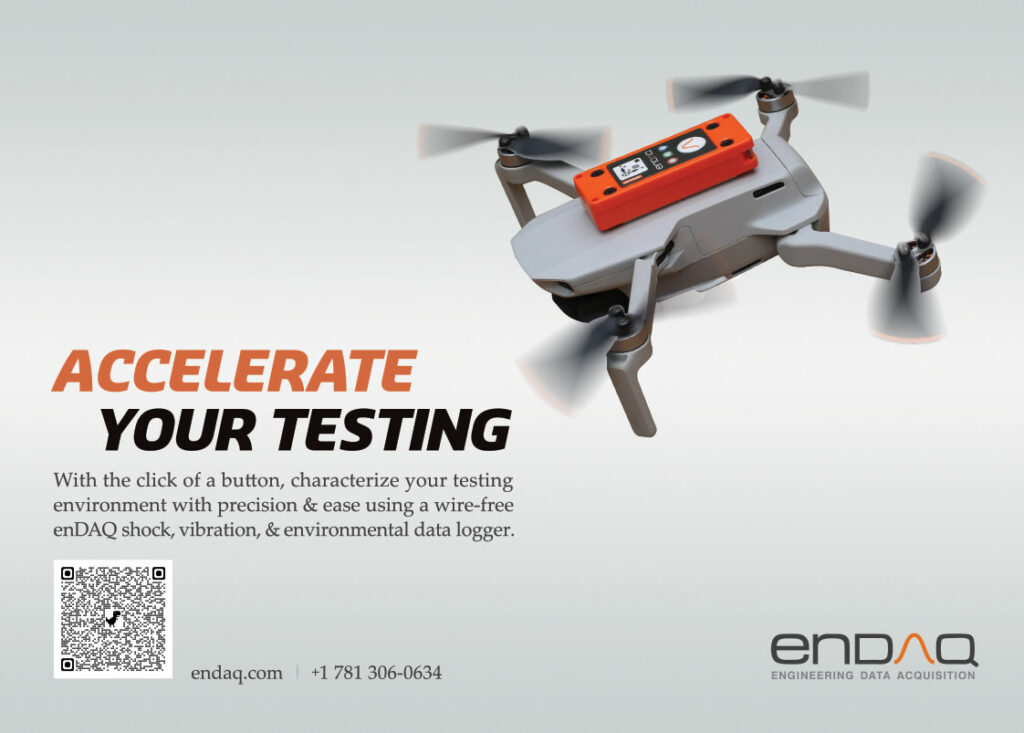
As redundant as the term ‘uncrewed USV’ might be, many of our readers will know firsthand how challenging it is to convince regulators to trust autonomous systems without a human physically onboard to take direct, manual control.
Indeed, it was the scale of the challenge that formed much of the motivation for Maritime Robotics to attempt such an operation in the first place.
As Eirik Hovstein, vice-president, defence & security at Maritime Robotics explains: “The main idea of this project was in fact to take on the authorities, their safety standards and inspectors, and see if it was possible to satisfy them with our technological capabilities.
“Our facilities in Trondheim and Vanvikan sit across the Trondheim Fjord [Trondheimsfjorden] from each other, and we typically have a lot of crewed traffic between those two, including boats with passengers, every day.
“Crewed boats must be very large, costly and polluting to carry a whole crew, rather than USVs, which are made only as big as needed to carry a cargo payload, so there was a great opportunity for cost and emissions savings by switching to a USV freight route.
“But, honestly, a bigger motivator than those actual, practical benefits was that we’ve heard so much talk about uncrewed water transport and uncrewed maritime logistics, and we wanted to see for ourselves if we could stop talking about it and actually do it.”
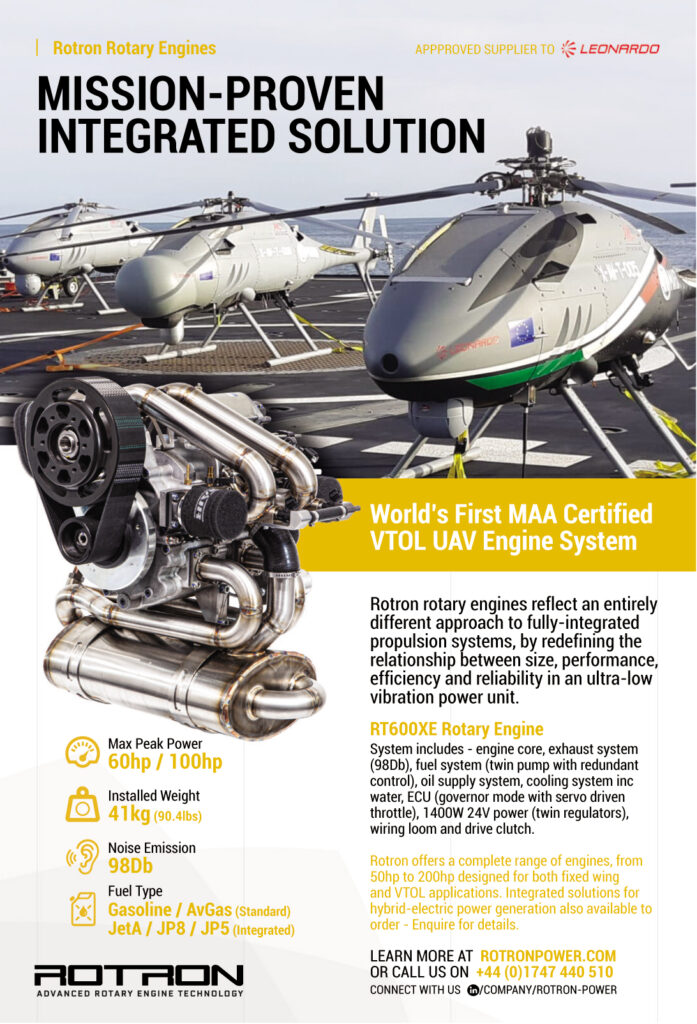
Maritime Robotics quickly formed a project team that included Hovstein, Eirik Moholt, the senior product manager for the Mariner USV (the testbed and proving platform for the uncrewed freight route) to cover the technical side of the work, and a PhD candidate at Maritime Robotics who specialised in the legislative side of autonomous maritime logistics.
The team subsequently approached Norway’s maritime regulation authorities, the Norwegian Coastal Administration (NCA) and the Norwegian Maritime Authority (NMA) to query the necessary paperwork, USV modifications, risk analyses, visitations and so on that would be needed for permits to carry out the freight route on a routine basis.
Beyond the will to tackle a big challenge, the company had another vital motivation for gaining this approval, as Moholt explains: “A key technical motivation came from the fact that Maritime Robotics is expanding like crazy, if we may say so, and as a consequence we decided to move the manufacturing of our smaller USVs, the Otters, from the Trondheim side to the larger and more production-appropriate Vanvikan facility.”
This meant relocating a massive inventory of tools, machine parts and stationery that are vital to the Otter production personnel from one coast to the other, with all the ensuing fuel, boat crew and large boat maintenance costs – unless these duties could be delegated to smaller, more efficient USVs instead, of which Maritime Robotics unsurprisingly had many in stock.
“The CEO literally asked us why we were whining about the costs and logistics of moving everything when we had an autonomous fleet ready to go. He even took some inspiration from how Boeing builds its planes at one facility before flying them to another for retrofitting,” Moholt says.
“It might not have been cost-effective to go through all the approvals just for this one route, unless we took Eirik’s [Hovstein’s] perspective that it was a chance to prove-out a model for future uncrewed freight operations, and also it means accruing a huge wealth of new testing and maturation hours for the Mariner USV by getting it to do these transport routes.
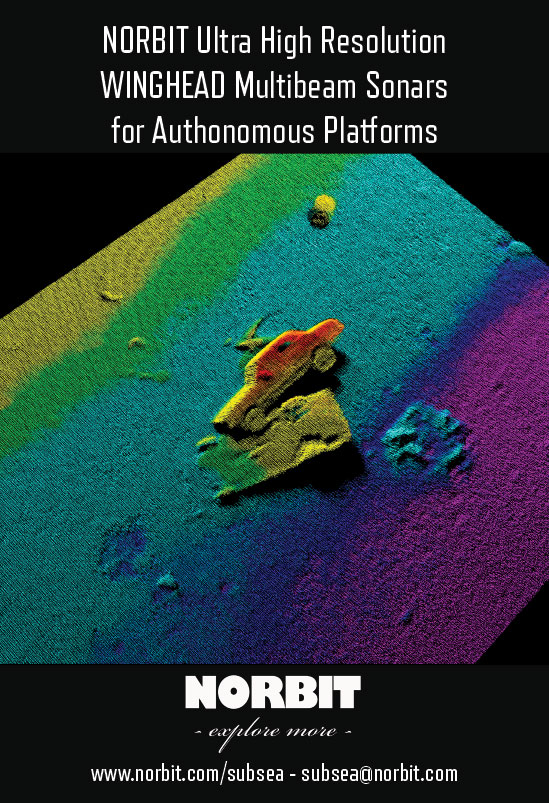
“We would have been out testing the Mariner at least once a week anyway; testing new software, custom hardware integrations, all year round. But, with the freight route, we get plenty of testing done, even more test hours than usual per week, and simultaneously move all the assets for the Otter manufacturing over to the Vanvikan facility.
“We’re using the testing for something really useful now and getting more value out of the whole thing.”
Maritime Robotics sees widespread use-cases for operations similar to the Trondheim-Vanvikan route elsewhere, including locally, with multiple remote islands dotting the coasts around Trondheim, the population of each one varying from two to upwards of 20 people.
Today, such islands only receive mail (including deliveries of medicine and internet-purchased commodities) once per week, so the flexibility and low cost of a USV compared with delivery boats could enable a higher quality of life for such communities with lower overheads.
“On top of that, Trondheim and much of northern Norway are home to many Michelin-quality restaurants, who rely on frequent but small deliveries of fresh ingredients, plus tools for the gathering or preparation of food, and other items,” Hovstein says.
“Thirty to 40 years ago, there were a lot more small transport boats operating, so it was possible for restaurants, home groceries and other small batches of goods to be cost-effectively delivered when needed. A lot of that has since been displaced by business models centred around huge freight vessels, which help their owners to be profitable, but can’t dock at or serve small community harbours. USVs can though, and they can handle pretty much any hard weather too, night and day, which could mean a new era of flexibility, emissions and convenience in marine deliveries.”
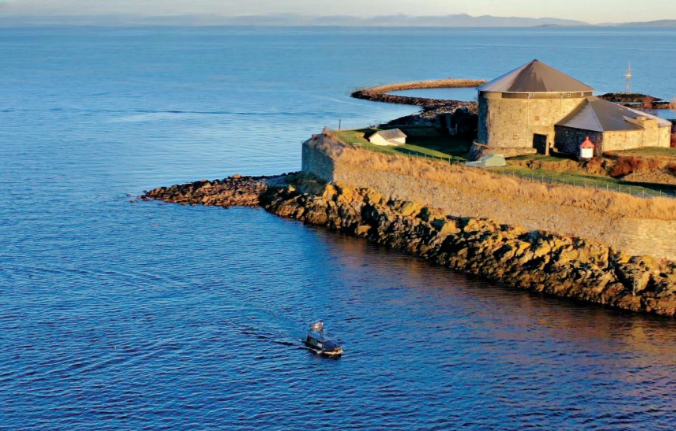
The Mariner USV
First detailed in Issue 39, the Mariner is a 5.9 m long, 2.06 m wide and 2.7 m tall (50 cm draft) vessel. It runs on a 195 bhp Yanmar diesel engine with both water-jet and electric thruster propulsion, with a typical operating endurance of 50 hours.
Its hull and superstructure are built from polyethylene, a low-maintenance material that does not corrode from seawater and exhibits very high impact resistance.
Atop the structure, deck hatches open to enable access to a cavity for installing payloads, such as sensors for a moon pool module, as well as space for additional batteries. Naturally, this space can also be used for cargo.
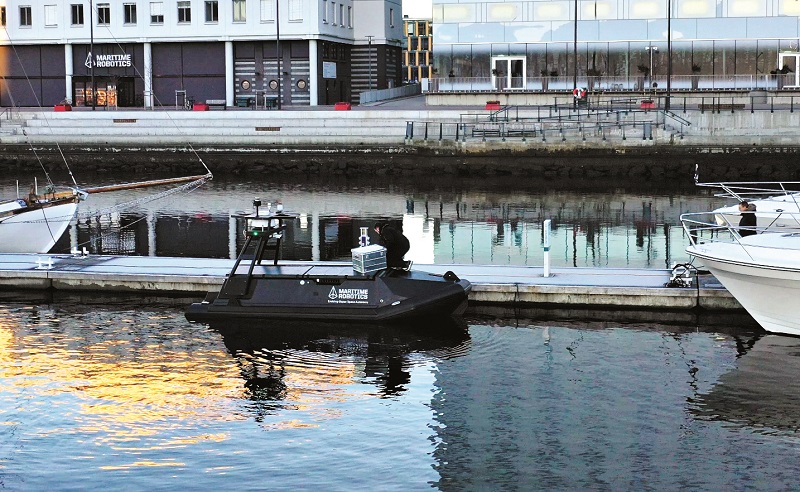
checks are needed before the USV can deploy
Be prepared
Hovstein and Moholt give significant praise to the NCA and the NMA for being prepared that a USV manufacturer would one day come forward to get an uncrewed freight route authorised.
“They had a very proactive approach in how they responded to us, and very much wanted our use-case to function as a demonstrator for other USV manufacturers and operators to follow,” Hovstein says.
“The biggest risk they focused on, of course, was collision with crewed boats, as the risk to human life is always prioritised in regulators’ metrics.
So, a lot of their rounds revolved around verifying that the situational awareness of the Mariner and our control room were always either as good as or even better than that of a human on deck, so that things like larger boats or small kayakers could always be detected at range.”
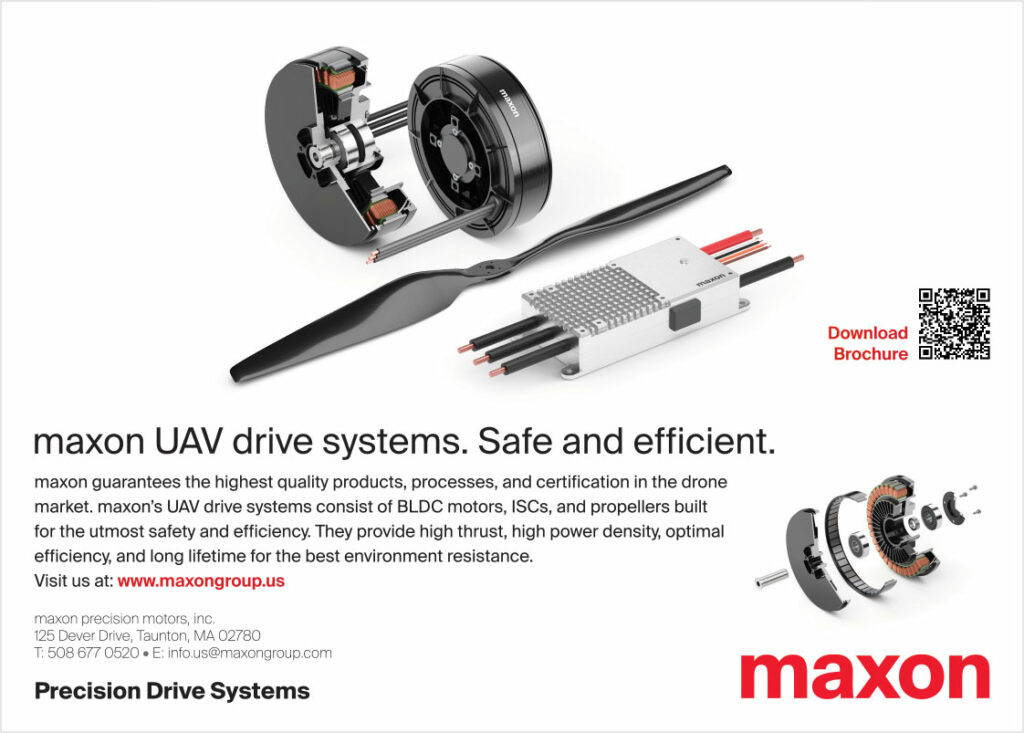
This involved demonstrations by Maritime Robotics, with Moholt and his fellows deploying Mariner USVs for NCA and NMA agents several times over, and talking them through its various functions and subsystems.
Often, this involved following the USV on a safety boat, which enabled proving of the system at sea, including showing its perception sensors, decision-making algorithms, and data links, all functioning in real-world maritime traffic and weather.
“We showed them the sensors were working both on the VCS [vehicle control station] interface and in our control rooms at Trondheim and Vanvikan. In fact, they were very familiar with the sensor technologies we used for autonomous perception, because you’ll find pretty much all of them on Norwegian passenger boats too,” Hovstein notes.
“In the Norwegian winter, before 10 am and after 3 pm, it is dark. Boat and ship captains here know you can’t sail using eyes alone. They are permitted to move at 30 knots in complete darkness, and they use instruments like camera, radar and GNSS to do it. Cameras can verify the presence and positions of lighthouses more scientifically than human vision, and we can even install microphones on the USV to detect audio cues like ship horns.”
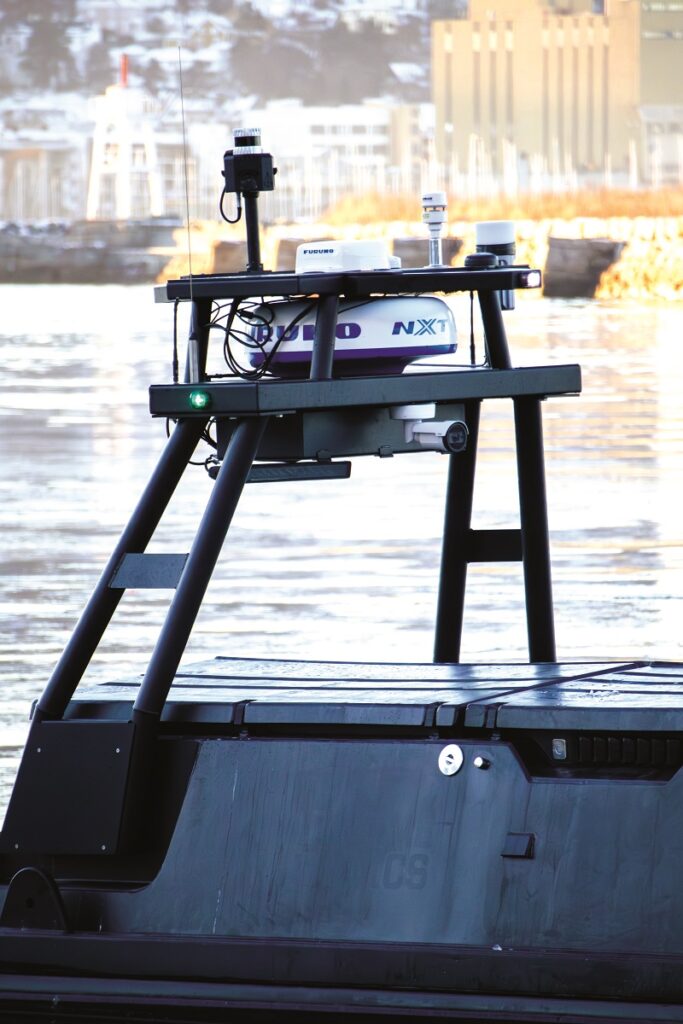
Engineering redundancies
Maritime Robotics made sure the Mariner is compliant with DNV CG 0264 on autonomous ships (despite being meant for far larger vessels), which involved engineering redundancies for power, propulsion, communication and computing.
Each of these subsystems therefore has at least one form of backup to take over in the event of failure, and if propulsion or steering should specifically suffer a fault, the USV is configured to throttle down so that position drift is minimised and the vehicle may be retrieved.
“A big help is that the Mariner has dual propulsion as standard. It is built with a water jet and electric thrusters,” Moholt explains.
“If our local express ferry gets its jet clogged up with something, for instance, it stops and starts drifting. If ours gets clogged, the thrusters can keep the USV in place while the operator analyses whether it’s best to drive home on the electric thrusters or stay in place and wait for human intervention, or even radio out to other boats or authorities over VHF to alert there is a USV with lost control nearby.
“Top that with the six battery banks onboard the Mariner and we always had enough energy to try something else in response to the authorities’ ‘what if’ queries and scenarios.”
The Norwegian authorities also required multiple redundancies to cover for cascading data-link failures, so a triple-redundant communications system is installed onboard to ensure persistent telemetry and control, including remote intervention by engineers monitoring the USV.
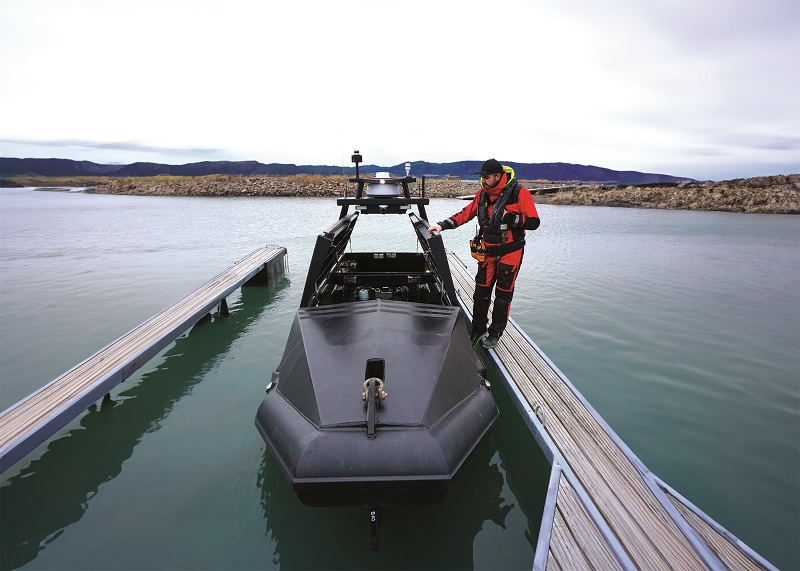
At Trondheim
Operationally, a key part of gaining permissions involves fully understanding the necessary risk analysis before commencing a day’s uncrewed sailing. Much of this was already part of Maritime Robotics’ usual practices, such as checking for decent weather, and the absence of swimmers and heavy water traffic.
“Additionally, we have to make sure we have extra staff on hand in case the operator tasked with monitoring the USV becomes incapacitated,” Moholt notes.
“It’s all exactly the same as good seamanship on a crewed boat. We also have to test all of the sensors, carry out maintenance inspections of the vessel’s parts, and validate that the engine fuel and oil are good to go, but if you’ve ever operated a crewed vessel or an uncrewed vessel in a reasonably professional manner, none of it should be surprising.”
As of writing, the company is conducting logistics across the Trondheim Fjord in an ad hoc manner, without a fixed or minimum number of runs per day. Depending on the number of Mariner USV stock available, multiple deliveries can be carried out by an individual unit in a single day.
Usually, one crew will be located in Trondheim with a VCS laptop to load and launch the Mariner. Once the risk and maintenance inspections have been completed, and the USV can be triggered to begin sailing towards Vanvikan, the crew notifies the Vanvikan control centre, whose crew is then given control of the vessel, although both continue to monitor it.
Control logic
The largest item shipped by the Mariner currently is the main body of the Otter USV, which is roughly 2 m long, 1 m wide and tall, and fits inside the larger USV’s cargo hold (and well within its 400 kg payload capacity).
As the USV transports cargo, both crews at Trondheim and Vanvikan monitor its activity, performance and health. As mentioned, the receiving crew is typically the one in control, but in the company’s control logic, each VCS in-the-loop can be assigned a number corresponding with its prioritisation in the hierarchy of computers.
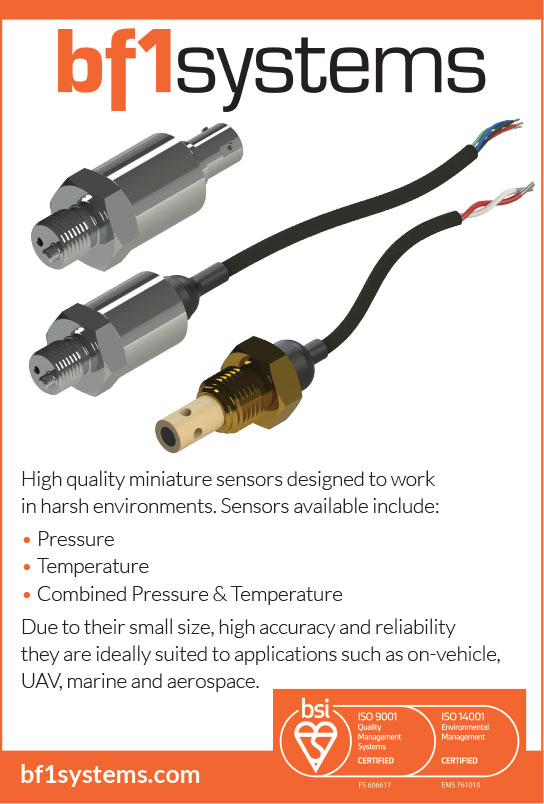
“The main control-room user at the receiving end will always have the highest number, and the second-highest will often be a secondary control station next to that user, which isn’t actively being used but serves as a backup, and then operators at different locations, including the mission start area, get their numbers,” Moholt says.
“The higher-number computers can relinquish control to lower-ranked users as the need arises, but control cannot be seized from anyone unless they relinquish it, so defining higher and lower users, or ensuring end-users do so clearly on their end, is a key part of our CONOPS.”
The comms arrangement ensuring triple-redundant control and monitoring connections includes maritime broadband radio (which serves as the primary data link), 4G cellular radio, and a satcom system such as Starlink or Iridium.
Some customers will also integrate Iridium short burst data (SBD) as an entirely standalone backup method for sending very small packets of information akin to SMS messages, particularly in the event that propulsion and all comms go down, and either the USV must ping its condition and location in short form or the user wants to send very simple emergency commands.
“We’re not restricted to those,” Moholt adds. “The main architectural focus of all our vessels is modularity, so we’re working to avoid putting any restriction on what the customer can use, whether it is data links or something else.”
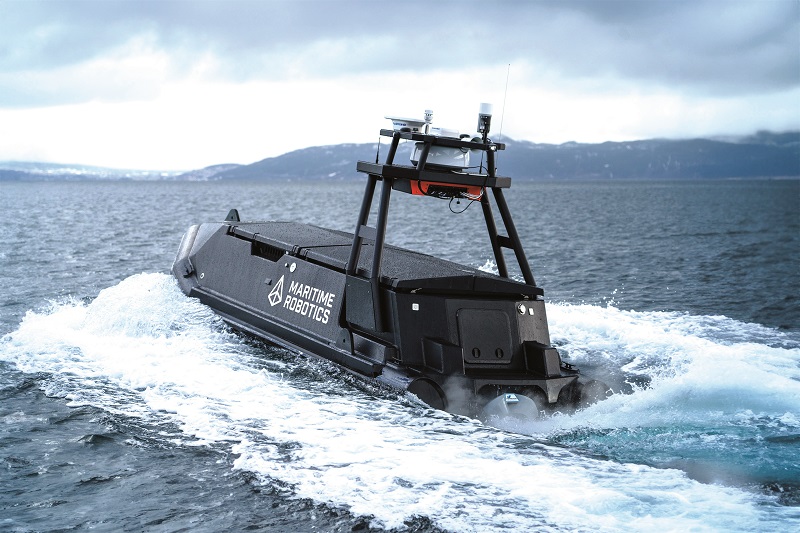
Post operation
Once the USV arrives at the receiving dock in Vanvikan (or Trondheim if a return journey is being performed), one operator in the port-side crew closely monitors its docking activity (and may perform this manually if they choose), while a second crew member ropes and moors the Mariner to secure it for offloading.
“We are now capable of auto-docking – admittedly, this is our first time mentioning that publicly – and we’re developing some proprietary subsystems around that to autonomously moor or lock the USV in place, such that the operator could be in Australia and the whole thing would be done autonomously,” Moholt says.
“That can be further developed to integrate something like a charging or refuelling station, so those aspects of maintenance can be made autonomous also.”
He notes that Maritime Robotics does not use robotic arms because saltwater can play havoc with electric motorised joints and other moving parts. Maintenance tasks following or between deliveries are minimal (a very deliberate objective of the Mariner’s design and engineering), particularly as the USV’s powertrain is built to provide five full working days of endurance at a 6 knot top speed on a single fuel tank.
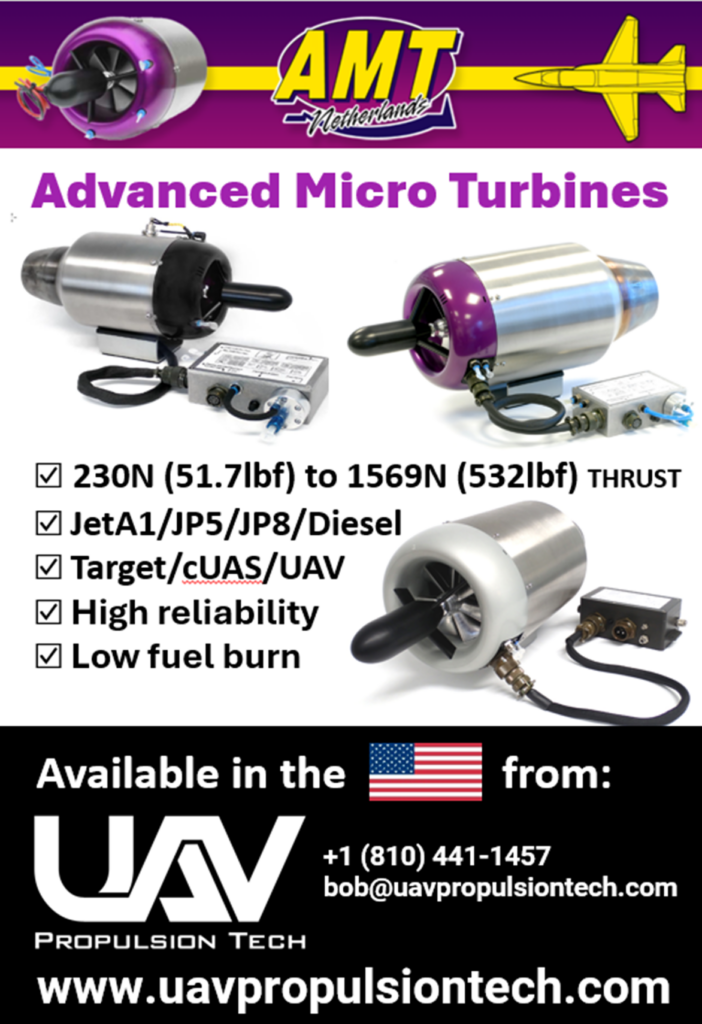
Hence, refuellings are rarely performed more than once per week, and typical maintenance consists of visually inspecting the oil tanks and engine belts, and scanning for signs of wear and tear; such checks can be done dockside.
Other parts have been engineered for easy replacement, such as the onboard computer, which can come in a Pelican case for easy lifting out from inside the deck hatch (and lowering in of a new one).
“I’ve done lots of maintenance on small vessels, and I hate it, so we’ve designed for a wide, open space inside the hatch where operators can easily see everything in the powertrain that needs to be inspected,” Moholt explains.
Hovstein says: “Of course, there is increasing impetus to remove the diesel engine and go all-electric, because then it would just remove all the belts, all the oil changes – just so, so many points of servicing and repair – and the operational flexibility would be greater, because most of the ‘remote’ locations we would try to deliver to will have accessible electricity for spot charging.”
Moholt concurs, adding: “For sceptics who fret about range anxiety, going far or quickly with a diesel boat means drinking an awful amount of fuel. You’re really not as free or independent as you think when running on fuel at sea.
“But USVs don’t even need to go quickly; they can move at a gentle 3 knots, make their destination in a known timespan, and even recharge at sea if solar panels or wind turbines are installed onboard. We think there’s going to be a lot more electric USVs in logistics as time goes on.”
The future
Maritime Robotics plans to continue optimising its USV designs as end-users make their requirements clearer, with modularity to remain at the forefront of its engineering priorities.
“Again, this operation is partially being carried out as a proof-of-concept. Since we’re an OEM, there is no reason [why] we couldn’t design and build a totally new USV in a design and volume specific to an end-user’s exact requirements if they have a decent idea of what they need, or wanted to sit with us to talk through their needs,” Hovstein explains.
He says there are two major autonomous ship projects ongoing in Norway, the aforementioned Yara Birkeland and the Basto Fosen VI ferry (discussed in Issue 32), which are gradually reducing their crew complements in operation and approaching fully uncrewed sailing.
“But both of these use-cases rely on inputs and produce outputs that connect to more remote locations, which don’t have the infrastructure to work with big ships, but could easily use a system of USVs,” Hovstein says.
Moholt adds: “In the project with Ørsted [briefly discussed in Issue 56], we also configured the autonomy so that their USV would follow their crewed vessel at a fixed bearing and distance.
“That, plus a lot of work we’ve been doing behind closed doors to develop our patented formation control technologies, means we could fairly easily organise fleets and networks of delivery USVs across varying waterfronts and waterways, with their own collision avoidance and autonomous speed adjustments taking care of much of the edge cases.”
Key specifications
- Mariner USV
- Length: 5.9 m
- Width: 2.06 m
- Height: 2.9 m
- Draft: 80 cm
- Dry weight: 2000 kg
- Top speed: 24 knots
- Endurance: 50 h at 4 knots
- Payload capacity: 400 kg
Some key suppliers
- Diesel engine: Yanmar
- Electric thrusters: Torqeedo
- Water jet: Hamilton Jet
- Multi-beam sonar: Kongsberg
- Multi-beam sonar: Norbit
UPCOMING EVENTS
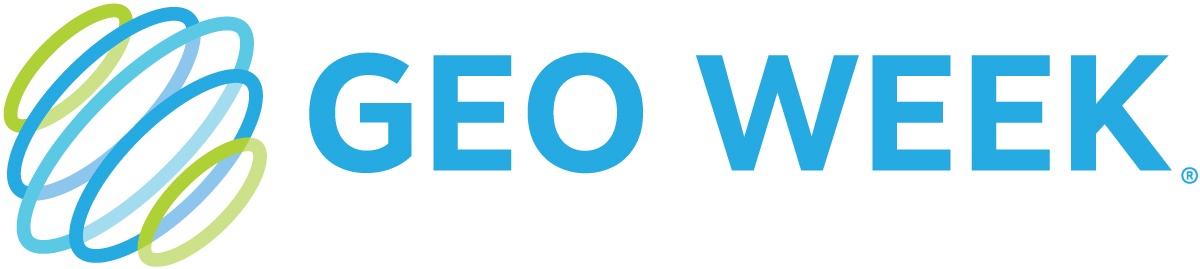
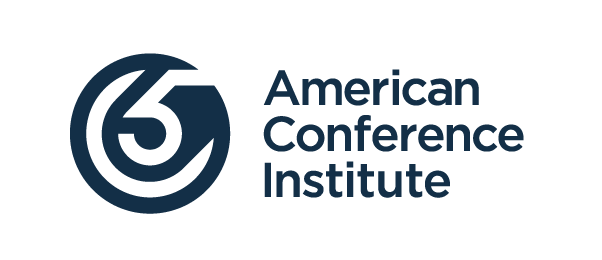
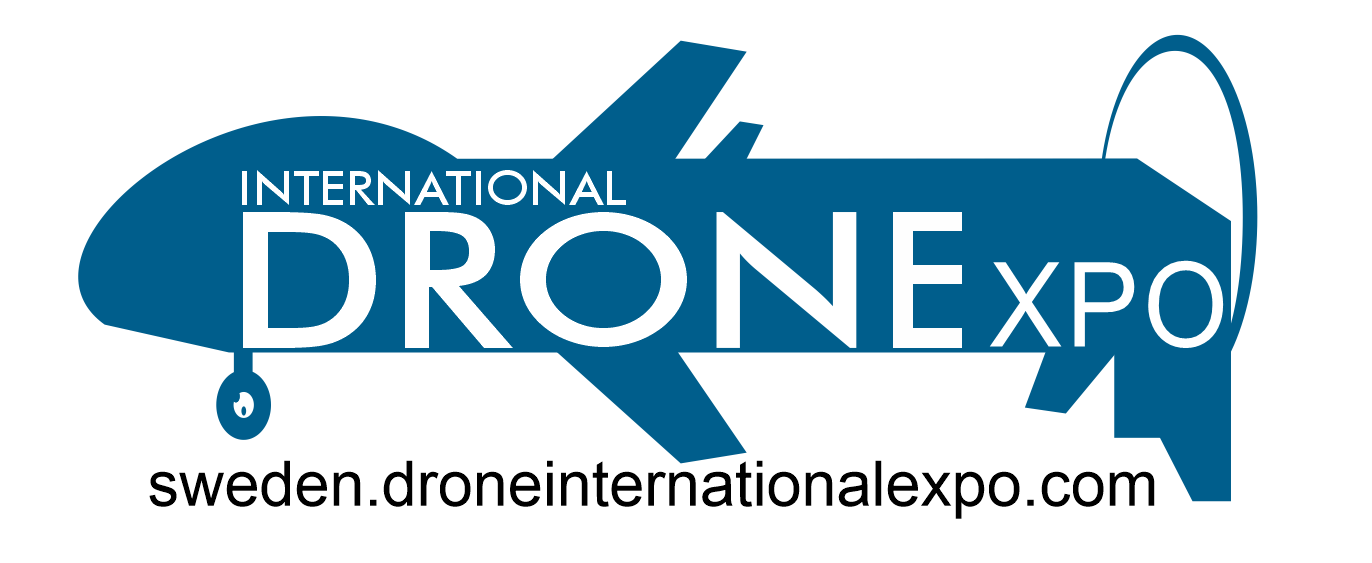
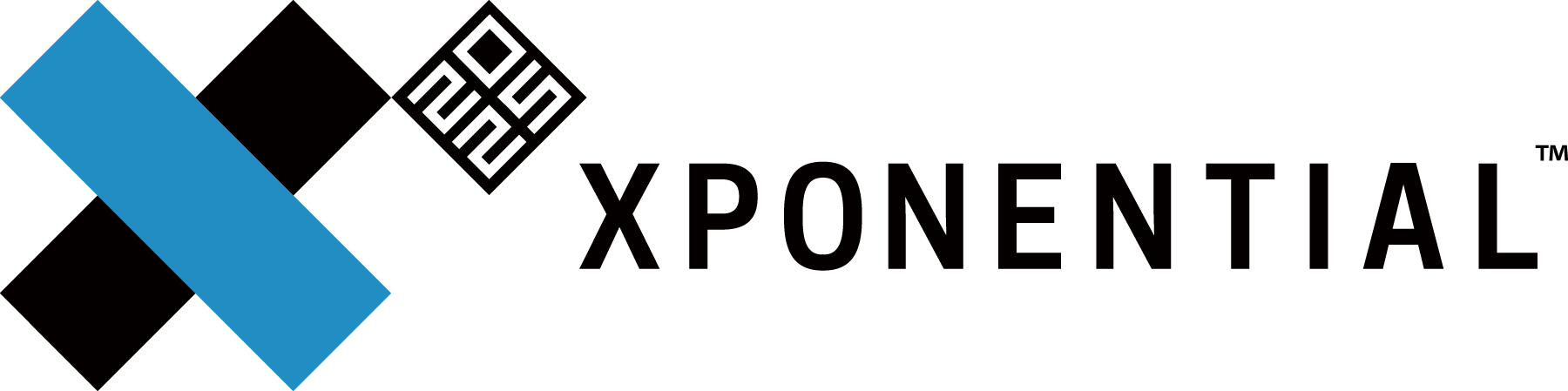
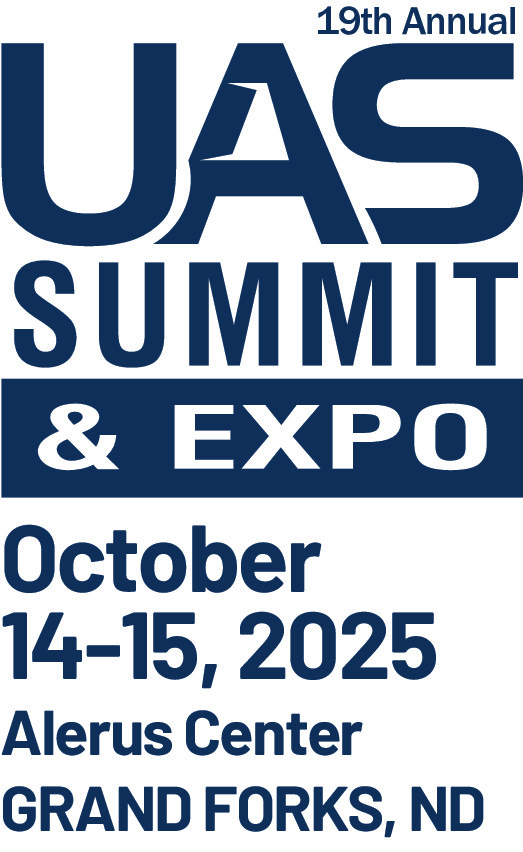

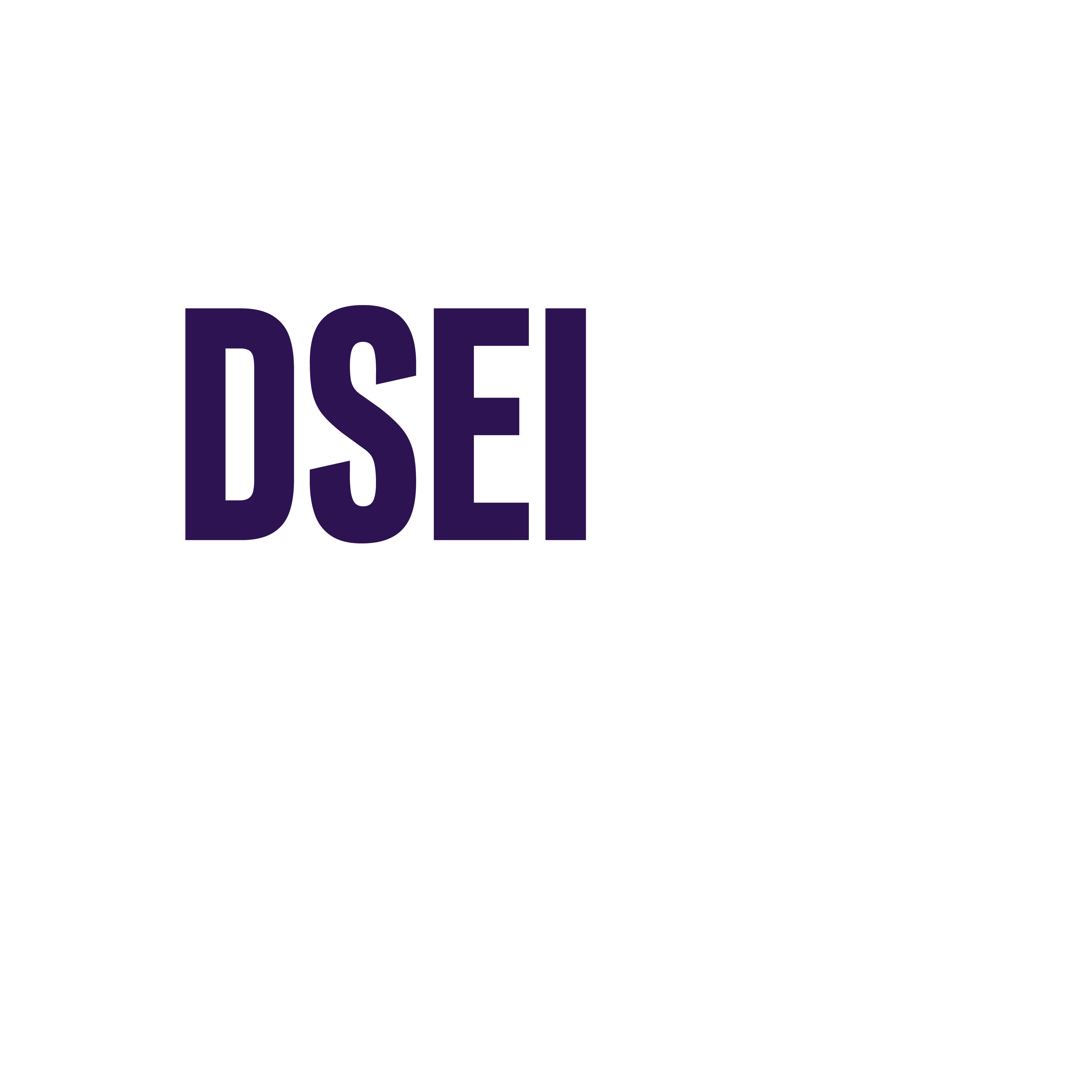
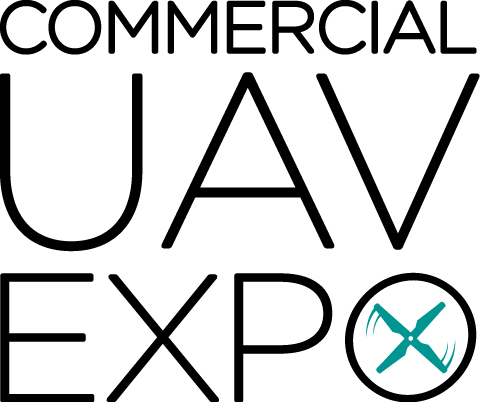
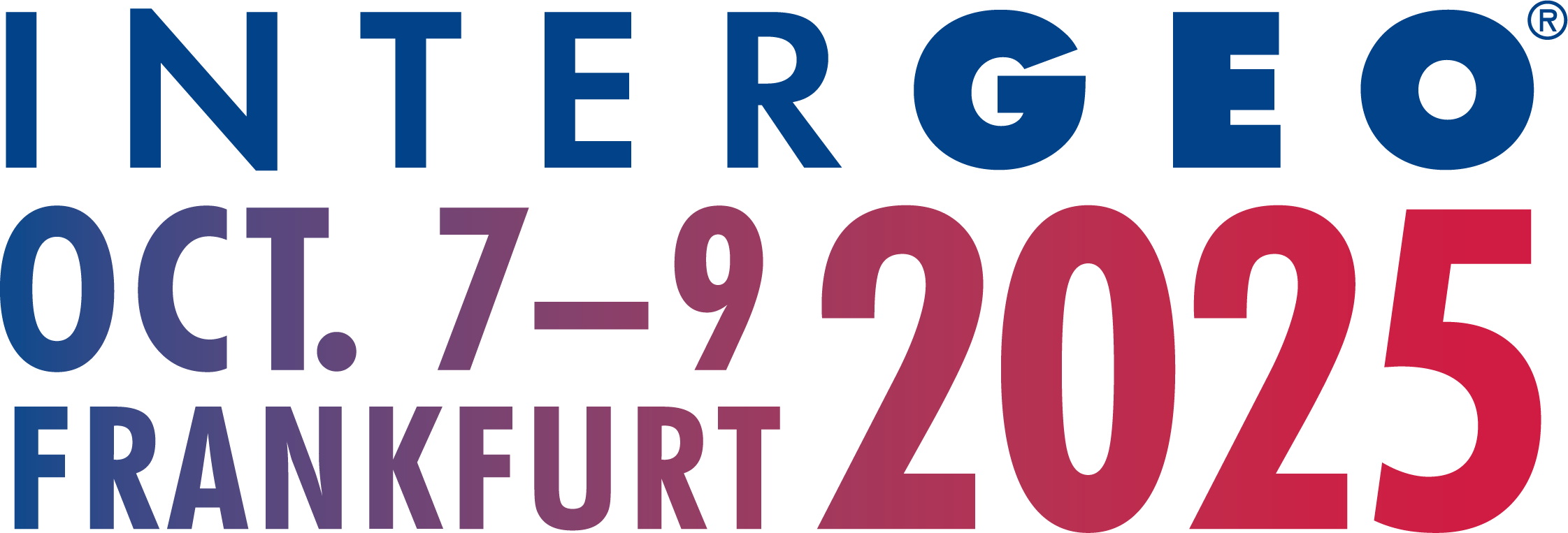
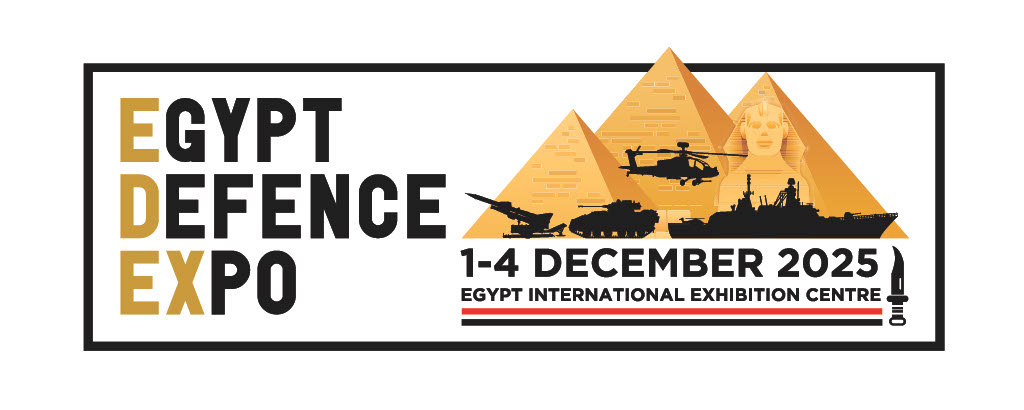
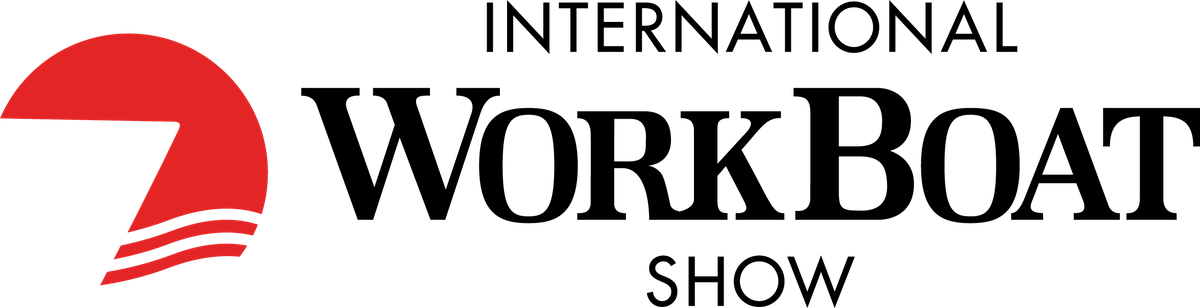